Ubicado en pleno corazón de la industria automovilística del Reino Unido, Vital Auto es un estudio de diseño industrial con una amplia experiencia en el diseño de automóviles. La ilustre clientela de la compañía incluye a muchos de los principales fabricantes automovilísticos, como Volvo, Nissan, Lotus, McLaren, Geely y TATA, entre otros.
"Nuestros clientes suelen acudir a nosotros para intentar ir más allá de los límites de la tecnología disponible", nos dijo Shay Moradi, vicepresidente de Innovación y Tecnología Experimental de Vital. Cuando los fabricantes no tienen tiempo para experimentar por su cuenta, acuden a Vital Auto con cualquier desafío que implique convertir ideas, bocetos iniciales, dibujos o especificaciones técnicas en una forma física completamente desarrollada.
Sigue leyendo para descubrir cómo Vital Auto crea prototipos de alta fidelidad y concept cars, pasando rápidamente de una iteración a otra gracias a una serie de herramientas avanzadas, entre las que se encuentra su gran parque de impresoras Form 3L y Fuse 1.
El desarrollo de un concept car
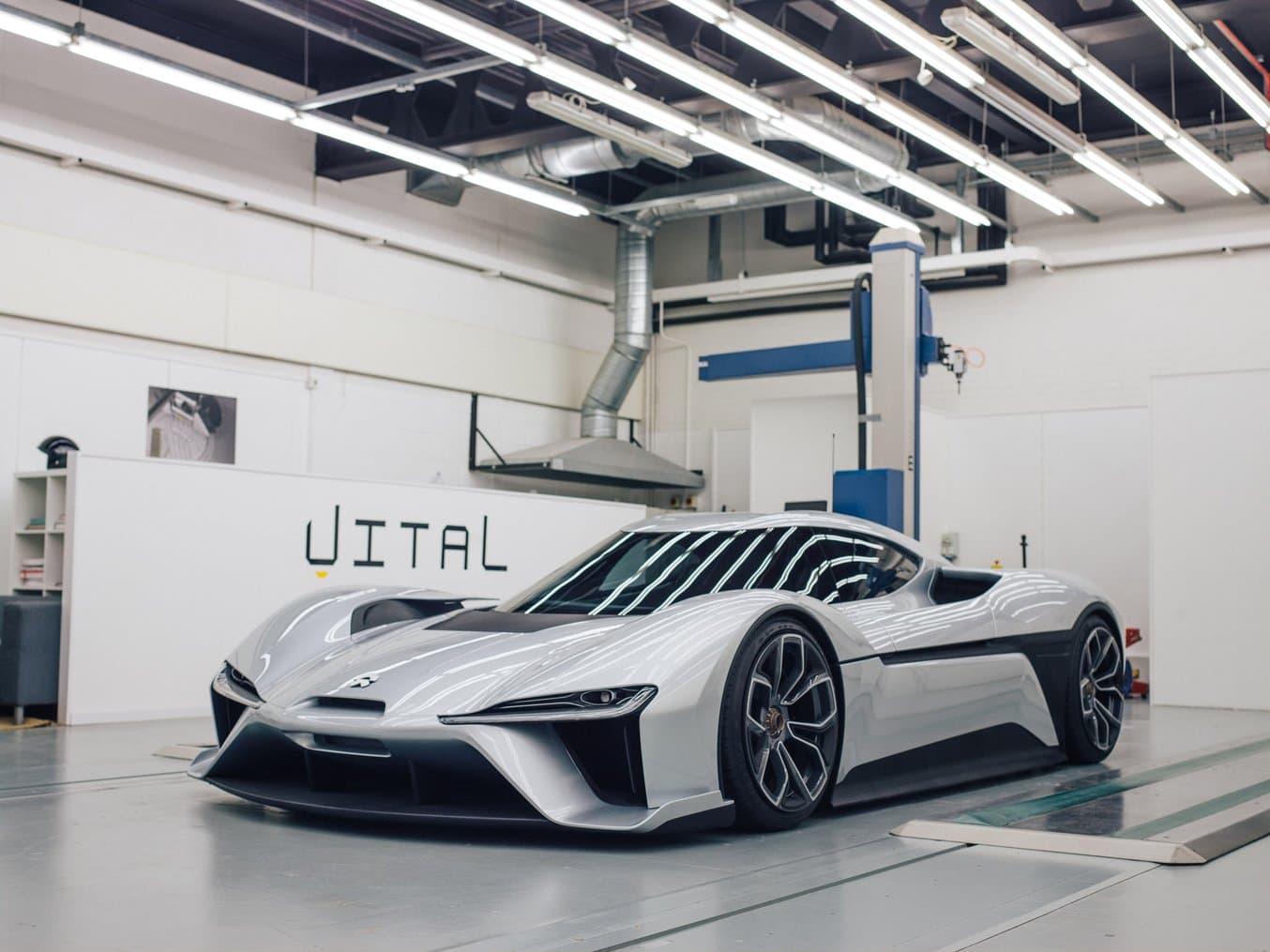
Vital Auto nació en 2015, cuando tres amigos decidieron dejar su trabajo para montar un taller en un garaje. Uno de los primeros contratos que la empresa acometió fue el concepto del superdeportivo NIO EP9, que encaminó inmediatamente al equipo hacia la producción de prototipos de vehículos de alta fidelidad extremadamente realistas.
En función de lo que solicite el cliente, el equipo puede empezar desde distintas bases, que abarcan desde un sencillo boceto en una hoja de papel hasta un vehículo ya diseñado. Desarrollan coches desde cero, diseñan todas las partes del chasis, todos los elementos exteriores e interiores, las aberturas y cierres y los elementos interactivos. Al trabajar de cinco a 30 personas en un único concepto, el proyecto típico podría durar entre tres y 12 meses.
En este tiempo, el típico coche de exhibición pasa por hasta una docena de iteraciones de diseño, que a su vez pueden incluir otras iteraciones de componentes más pequeños hasta que el diseño satisfaga las expectativas del cliente.
"En nuestro sector, es habitual tomar las propiedades virtuales de un producto como referencia a la hora de evaluarlo antes de lanzarlo al mercado. Sin embargo, creo que siempre habrá también un lugar para objetos fabricados físicamente. No hay nada mejor que la sensación de sostener un objeto en las manos con el peso adecuado las proporciones correctas y la dinámica de cómo el entorno físico cambia la percepción de ese objeto físico.
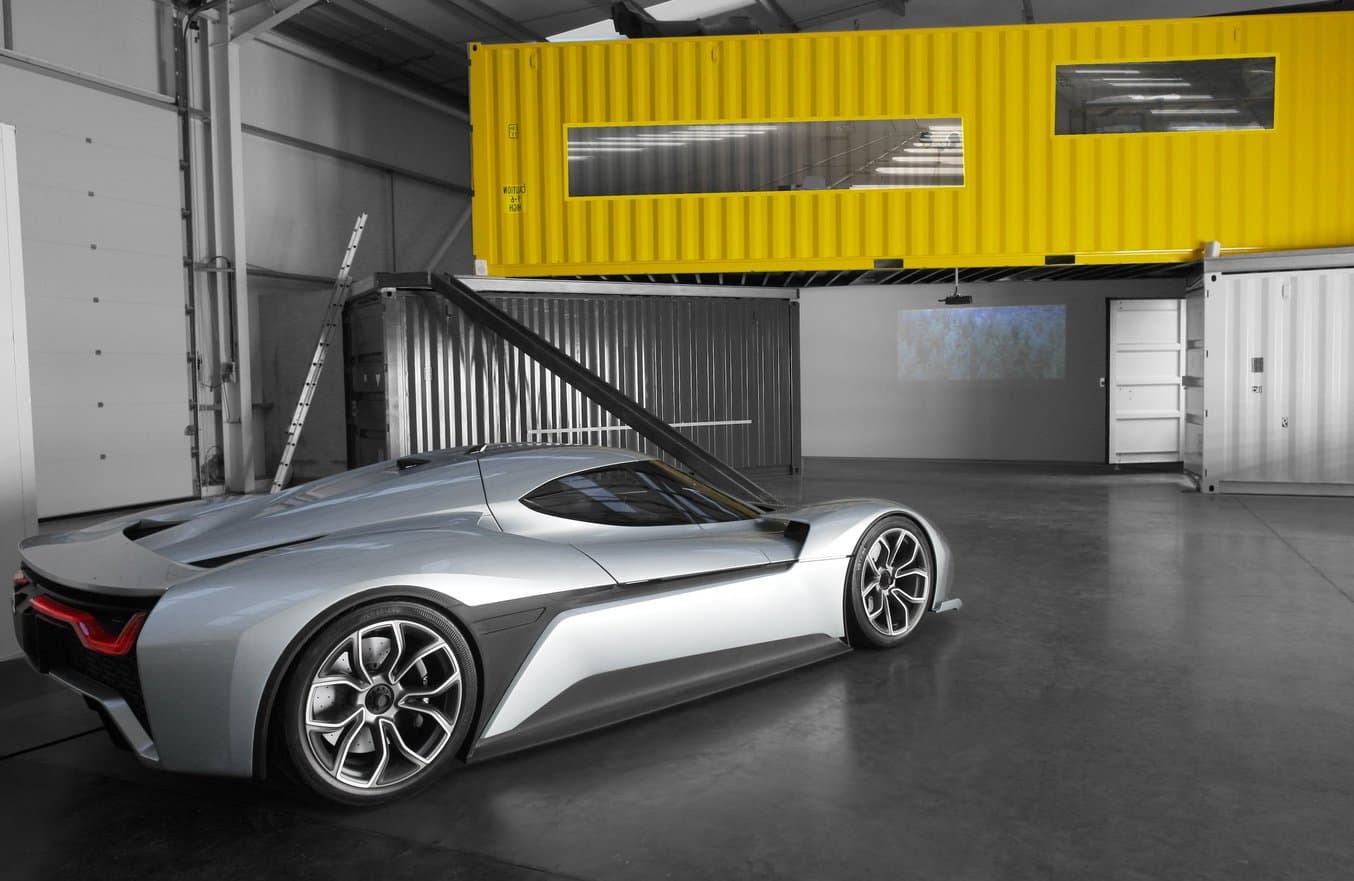
"La mayoría de nuestros clientes acuden a nosotros con una idea nueva e innovadora, algo que no se ha hecho nunca antes. Por eso, para nosotros los desafíos son nuevos cada día y no tienen fin", dijo Anthony Barnicott, ingeniero de diseño a cargo de la fabricación aditiva. "Estos desafíos pueden abarcar cómo producir un número concreto de piezas en un tiempo determinado, cómo fabricar un producto sostenible o cómo hacer una pieza que alcance un peso específico sin dejar de funcionar de la manera deseada".
Aunque, normalmente, los coches de exhibición se hacen únicamente fresando arcilla, el equipo también utiliza el fresado CNC de tres y cinco ejes, el moldeado a mano de chapa y de arcilla y compuestos de plástico reforzado con vidrio. No obstante, estos procesos tradicionales a menudo no son ideales para producir las piezas personalizadas que requieren los conceptos únicos.
"Hemos usado la impresión 3D desde el primer día. Queríamos incorporarla a nuestros procesos de fabricación no solo para reducir los costes, sino también para ofrecer a los clientes más diversidad en sus diseños e ideas", explicó Barnicott.
Actualmente, Barnicott dirige todo un departamento dedicado a la impresión 3D, que incluye 10 impresoras FDM de gran formato, tres impresoras SLA de gran formato de Formlabs y cinco impresoras SLS Fuse 1.
"En cuanto a la capacidad de todas esas impresoras, prácticamente desde el primer momento han estado funcionando al 100 % las 24 horas del día. Las utilizamos para todas las áreas de nuestros conceptos y diseños. Normalmente, usamos las Fuse 1 para nuestras piezas basadas en la producción y usamos nuestras Form 3L para nuestras piezas basadas en conceptos", dijo Barnicott.
Fabricación de diseños complejos a partir de múltiples materiales con la Form 3L
Utilizamos las Form 3L para cualquier cosa que requiera un acabado de la superficie de primera categoría. En el ámbito de la automoción, suelen ser elementos de interiores donde hay piezas que no están tapizadas con cuero, alcántara o algún otro tipo de material textil. Los materiales de Formlabs nos dan un acabado bonito y liso con el que pueden trabajar nuestros pintores, podemos usar las piezas recién salidas de la impresora y colocarlas directamente en un vehículo", dijo Barnicott.
Lo que más me interesa de las Form 3L es su versatilidad. La capacidad de cambiar de material en menos de cinco minutos y la diversidad de dichos materiales, ya que poder pasar de un material blando y flexible a uno que es duro y rígido no tiene precio".
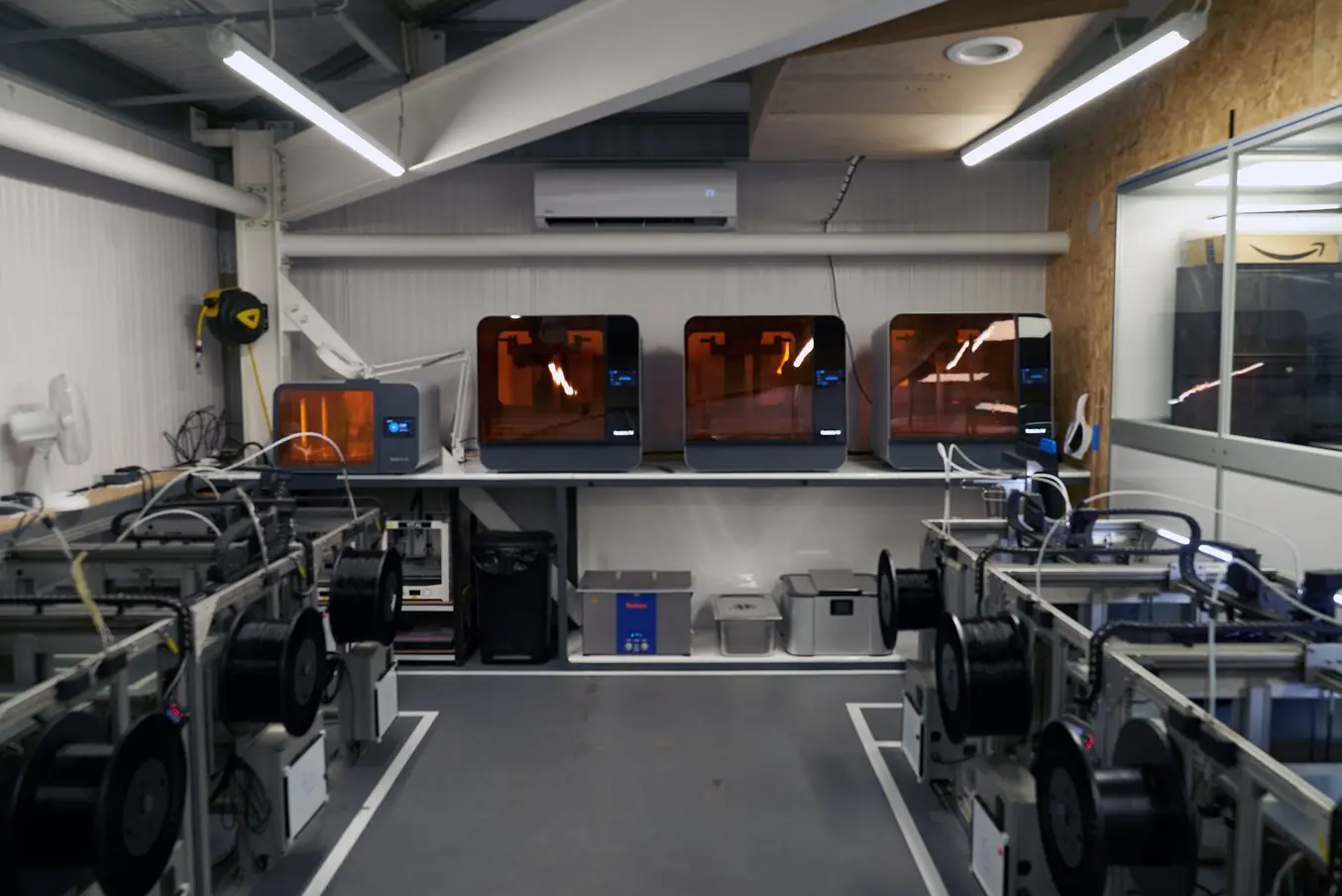
El equipo usa las Form 3L con múltiples materiales para una amplia gama de aplicaciones, como por ejemplo:
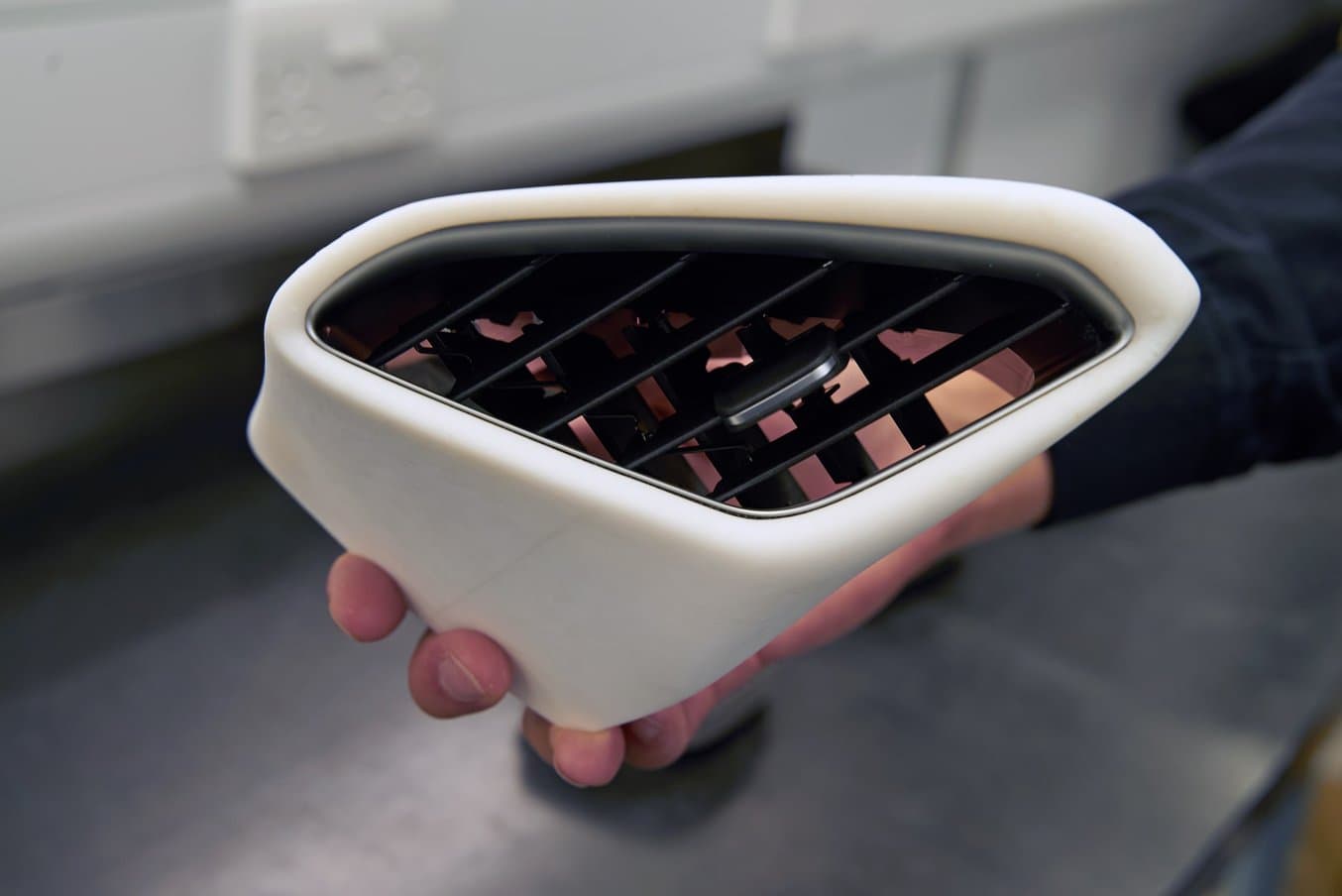
Orificios de ventilación
"Algo que nos plantean con frecuencia los clientes es encastrar un producto de otra marca en su propio diseño. Una vez, un cliente acudió a nosotros con un respiradero de otro vehículo que quería incluir en el interior del suyo. Utilizamos la tecnología de escaneado 3D para reproducir esta pieza de forma digital y después creamos una piel externa. En primer lugar, la fabricamos con la Draft Resin para poner a prueba el diseño y que el cliente pudiera verificarlo. A continuación, pasamos a la White Resin para crear una pieza lista para la producción".
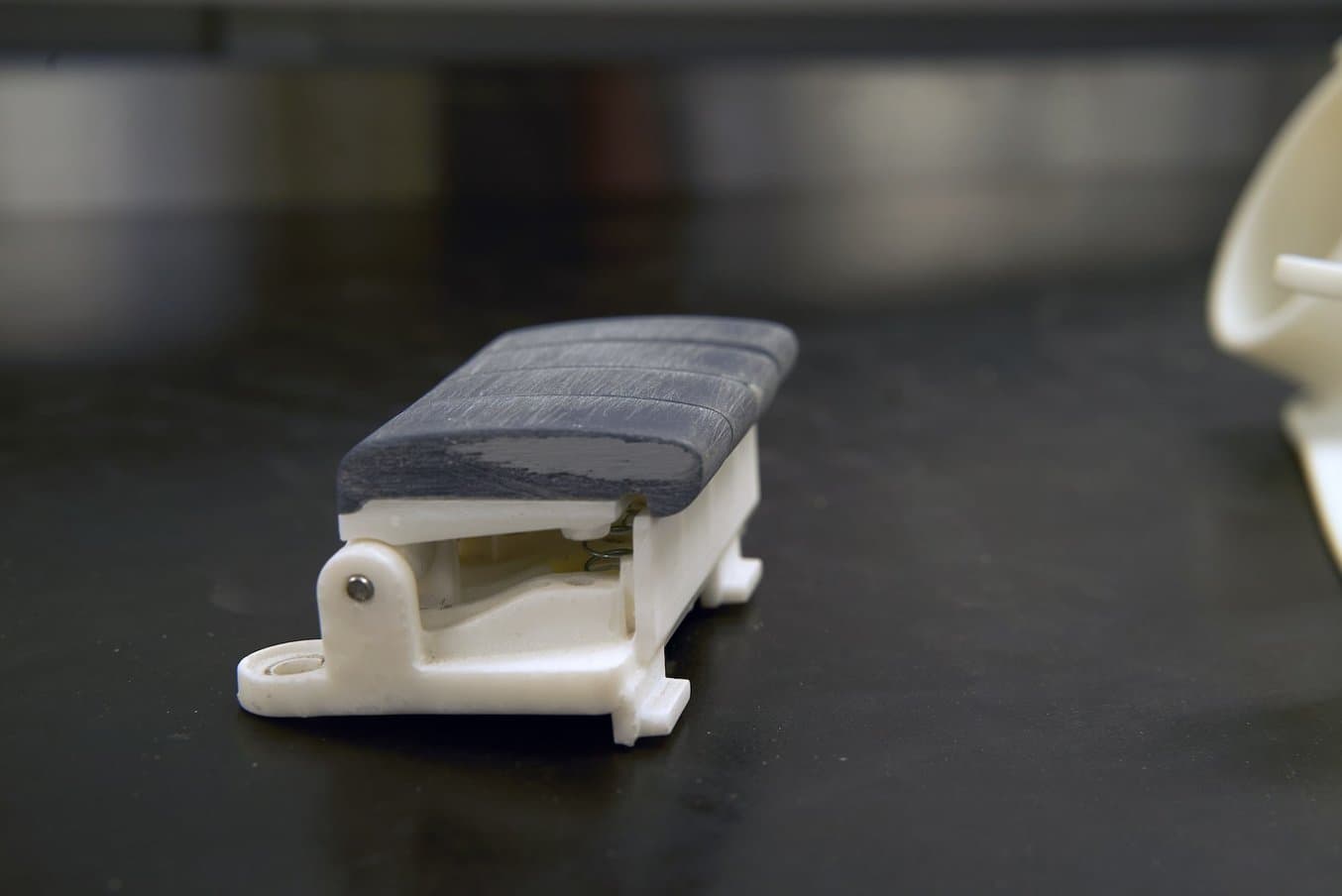
Conjuntos de interruptores
"Cuando trabajamos con diseños muy detallados, como los de pequeños conjuntos de interruptores, podemos utilizar varios materiales a la vez para obtener un producto mecánico que no solo funciona correctamente, sino que se puede usar en el mundo real. Combinamos materiales duros (como la Tough 2000 Resin) para la superficie superior con materiales ligeros y más asequibles para la parte interna.
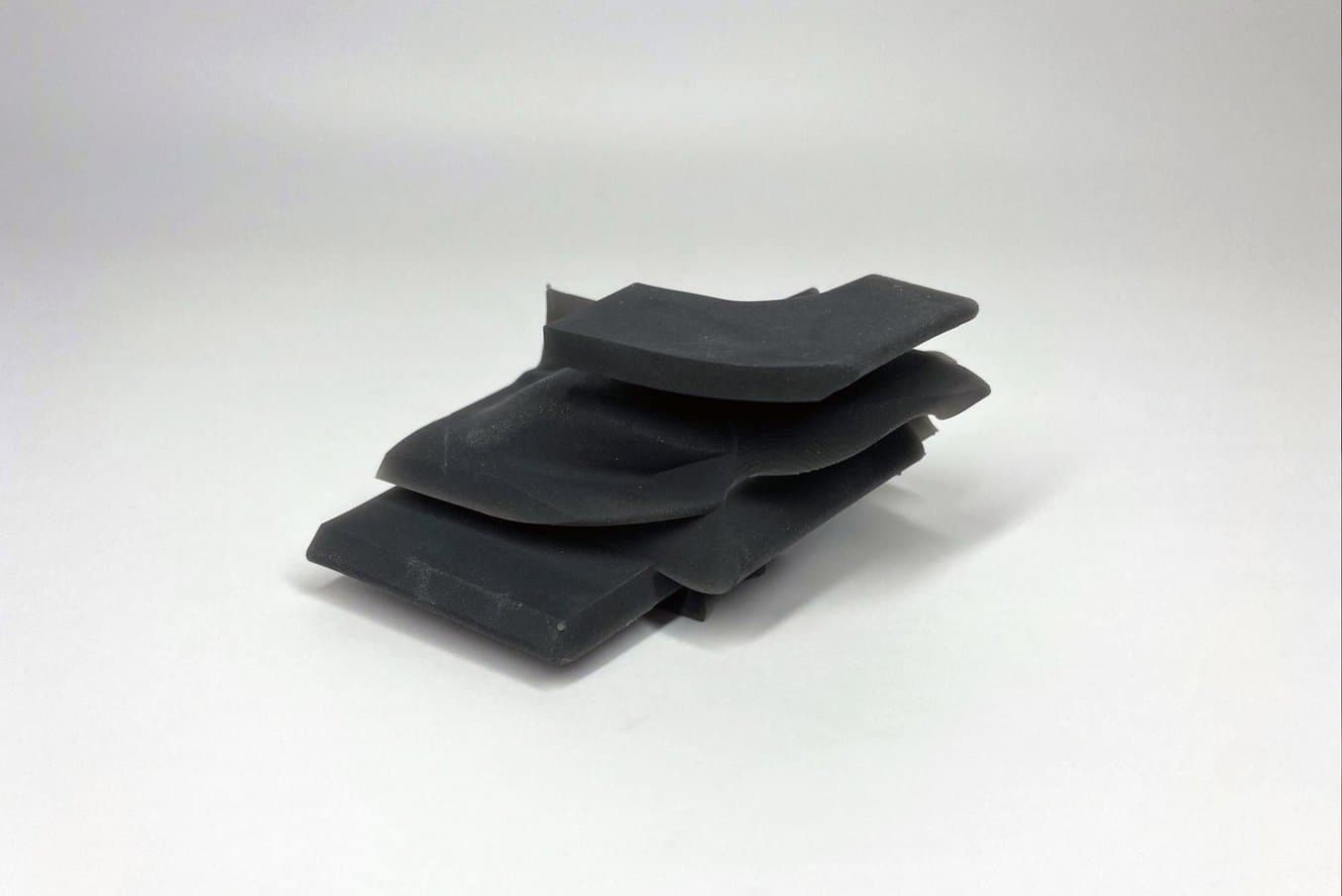
Juntas de las puertas
"Normalmente, las juntas de las puertas de los automóviles pueden resultar increíblemente caras de producir. Sencillamente, el único modo de fabricarlas es mediante moldeo por extrusión. Esto no solo tiene un coste de utillaje muy elevado, sino que además conlleva un largo plazo de producción. Pudimos experimentar con uno de los materiales más nuevos de Formlabs, la Flexible 80A Resin. La Form 3L nos permitió producir partes de esta junta de puerta por la noche para someter a ensayo diversas geometrías y se imprimió con un margen de error de 50 micras respecto al diseño real".
Disponer de la Form 3L da al equipo la capacidad de producir múltiples iteraciones de piezas en menos de 24 horas, en la mayoría de los casos. Acabaron comprando tres máquinas distintas para poder producir hasta tres iteraciones diferentes de una pieza al mismo tiempo, incluso con un material distinto para cada una de las tres. Después, pueden transmitir el ahorro que supone al cliente u ofrecerle un valor mayor, mostrando varias opciones de diseño por el mismo precio.
"Una de las maravillas de usar la fabricación aditiva es que minimiza el tiempo que inviertes en el proceso. ¿Qué se puede hacer en ese período que se queda libre? Nosotros lo vemos como una ampliación de las posibilidades con la que imaginar alternativas y ganar más bucles de iteración para el proceso", dijo Moradi.
"Hay muchos de nuestros actuales productos que sencillamente no seríamos capaces de fabricar sin nuestras Form 3L. Con algunas de las técnicas de fabricación más avanzadas, como el mecanizado CNC de siete ejes, sí que seríamos capaces de producirlos, pero el coste que supondría sería considerable", explicó Barnicott.
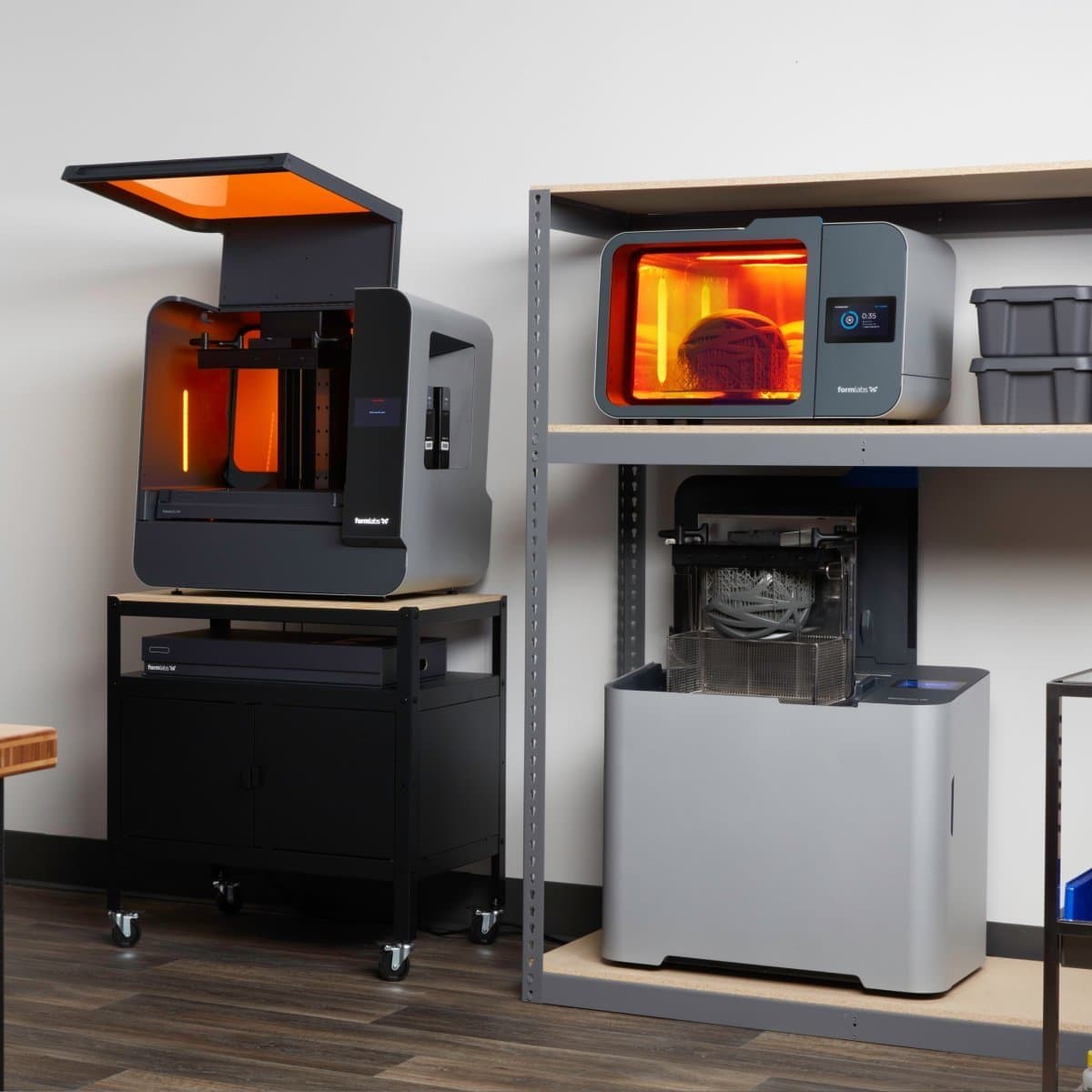
Demostración del ecosistema Form 3L
¿Quieres saber más acerca del ecosistema de la Form 3L y la Form 3BL, así como de las nuevas máquinas de posacabado de gran formato? En esta demostración, Kyle y Chris explicarán cómo realizar el proceso de trabajo completo de la Form 3L, incluido el posacabado.
Cómo complementar el mecanizado CNC de piezas mecánicas con la Fuse 1
La Fuse 1 fue nuestro primer contacto con la tecnología SLS. Al ser una empresa pequeña, es una tecnología que nunca creímos que podríamos tener en nuestras instalaciones. De hecho, no tenemos solo una Fuse 1, sino cinco de ellas. Lo que estas máquinas nos han permitido hacer es producir piezas mecánicas estructurales con mucha rapidez, no solo para el ensayo, sino para aplicaciones físicas reales de la mayoría de nuestros conceptos. Antes, este proceso se habría llevado a cabo mediante mecanizado CNC, en nuestro taller o externalizándolo, en función de la geometría, y habríamos tenido que esperar entre dos y cuatro días para tener las piezas en nuestras manos. La Fuse 1 nos permite ocuparnos de todo ello en nuestra propia empresa y tener las piezas listas en menos de 24 horas, en la mayoría de los casos", dijo Barnicott.
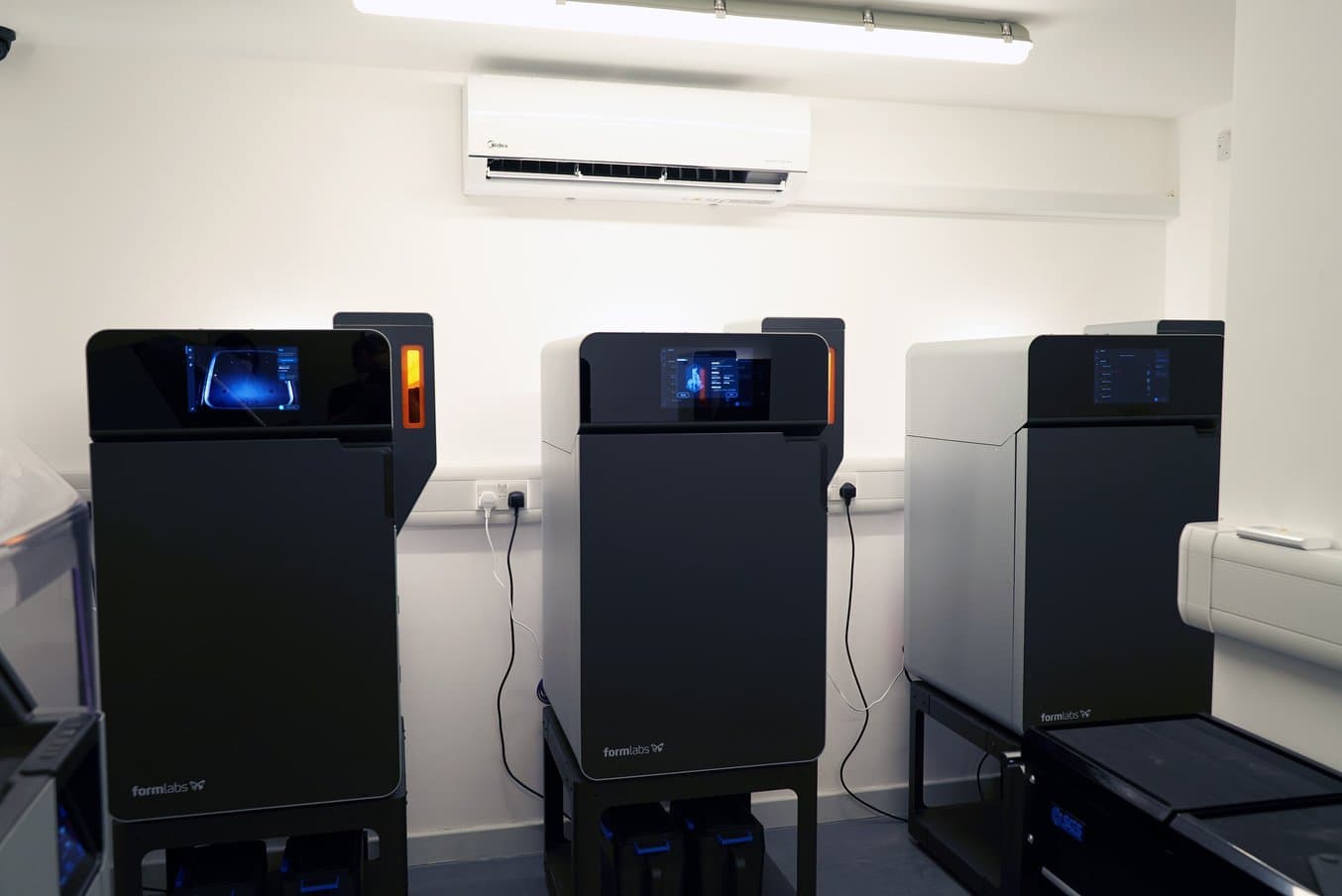
El equipo utiliza las Fuse 1 principalmente para fabricar piezas mecánicas como bisagras de puertas, piezas internas de tiradores, interiores de las puertas y aplicaciones estructurales. Pueden usar las piezas recién sacadas de la impresora, con un acabado mínimo. Estas son algunas de las aplicaciones para las que el equipo ha usado las Fuse 1:
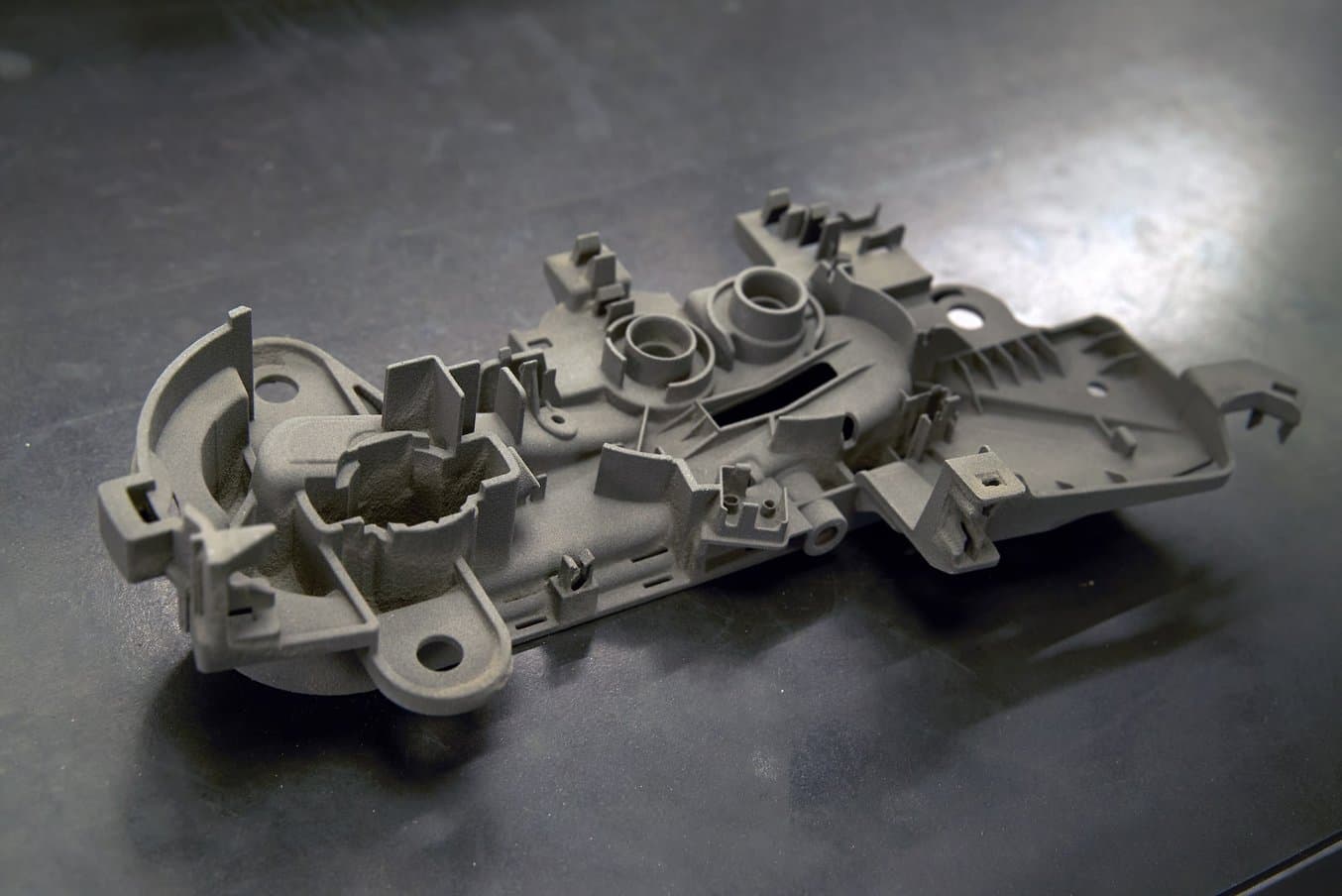
Conducto de aire
"Muchas piezas del interior de un automóvil pueden resultar muy difíciles de producir sin recurrir al moldeo por inyección tradicional. Son piezas como los conductos y respiraderos de aire internos, elementos que nunca se ven, pero que son caros de producir. Usamos la Fuse 1 para fabricar estas piezas. Nos ofrece una versatilidad mucho mayor en los diseños que incluimos en el vehículo y sin los grandes costes que tendrían normalmente".
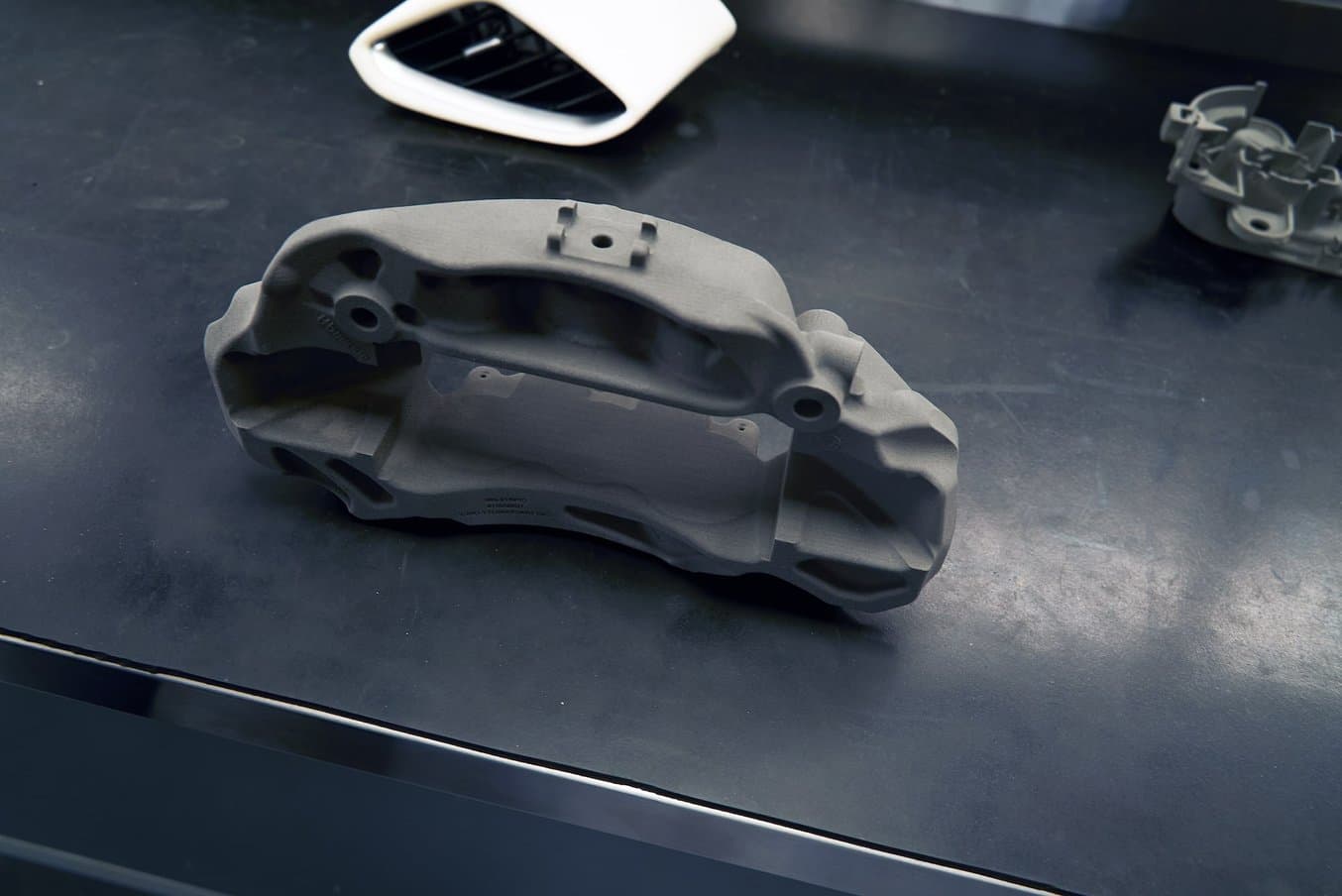
Galga de freno
"A veces producimos piezas simplemente porque el cliente quiere ver cómo queda su marca en ellas. Eso significa que tenemos que hacer una pieza con bastante rapidez para poder aplicarle su marca. Utilizamos la Fuse 1 para producir estas piezas, como las galgas de freno, y podemos incluir el logotipo en distintas zonas de la galga y en varios colores, para que el cliente lo evalúe.
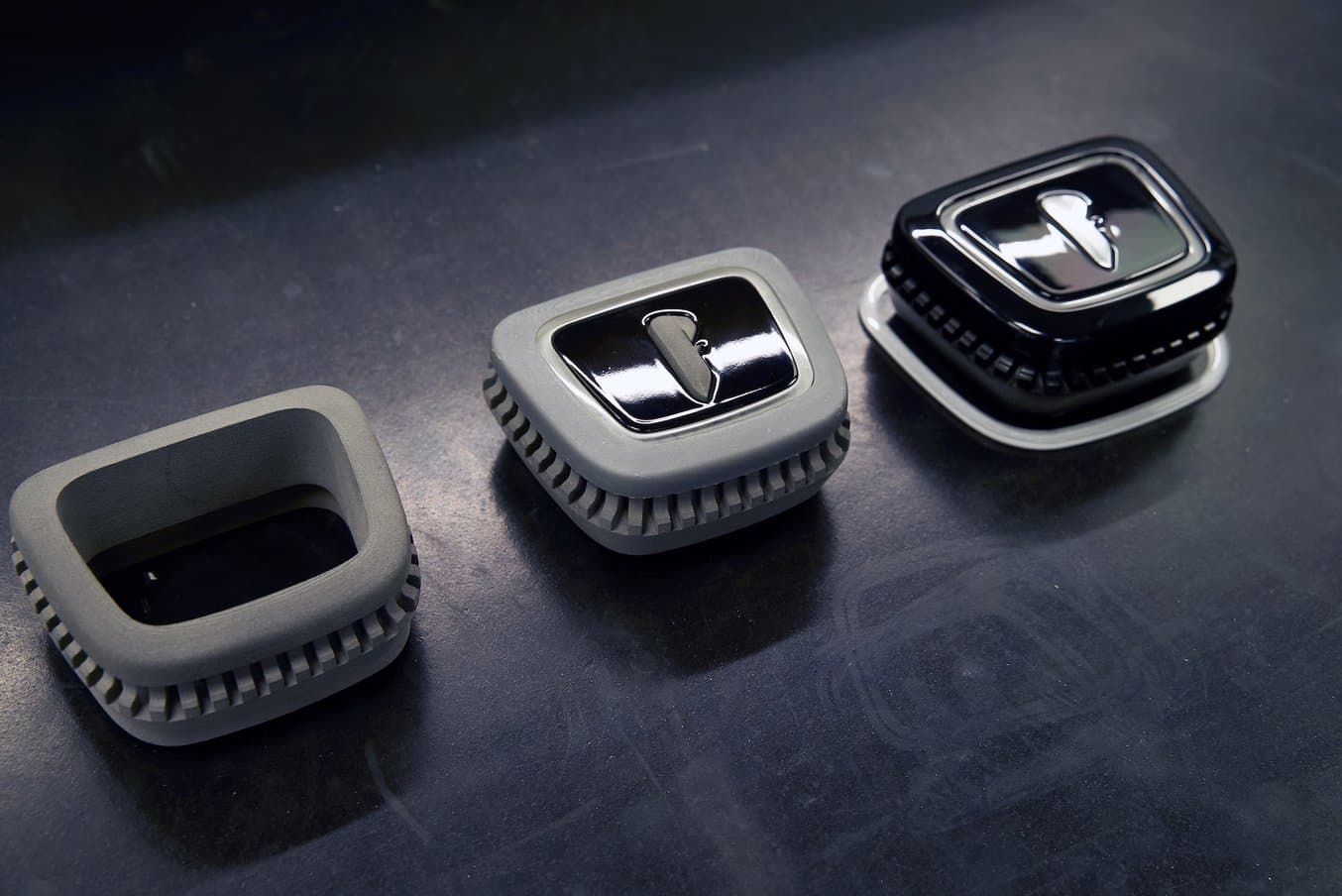
Concepto interactivo para un superdeportivo
"La impresión 3D nos ha permitido combinar materiales tanto de la SLA como el SLS para resolver las iteraciones de diseño de proyectos específicos. Esto nos permite producir rápidamente múltiples iteraciones combinando ambos procesos por las propiedades específicas de cada uno, con el fin de obtener un diseño final. De este modo, podemos hacer cualquier cosa, desde piezas mecánicas a piezas translúcidas, para comprobar su calidad óptica y su rendimiento".
Aunque con frecuencia se dice que la fabricación aditiva ha llegado para reemplazar a la fabricación sustractiva, el equipo de Vital Auto ve las ventajas de combinar distintas tecnologías para aprovechar sus mejores cualidades.
"Usamos ambas técnicas a la vez para que se complementen. Hay muchas piezas con las que usaríamos fabricación sustractiva y después usaríamos la fabricación aditiva para producir todos los detalles precisos. Esto nos permite disponer de un modo mucho más rentable de producir muchos de nuestros modelos de concepto.
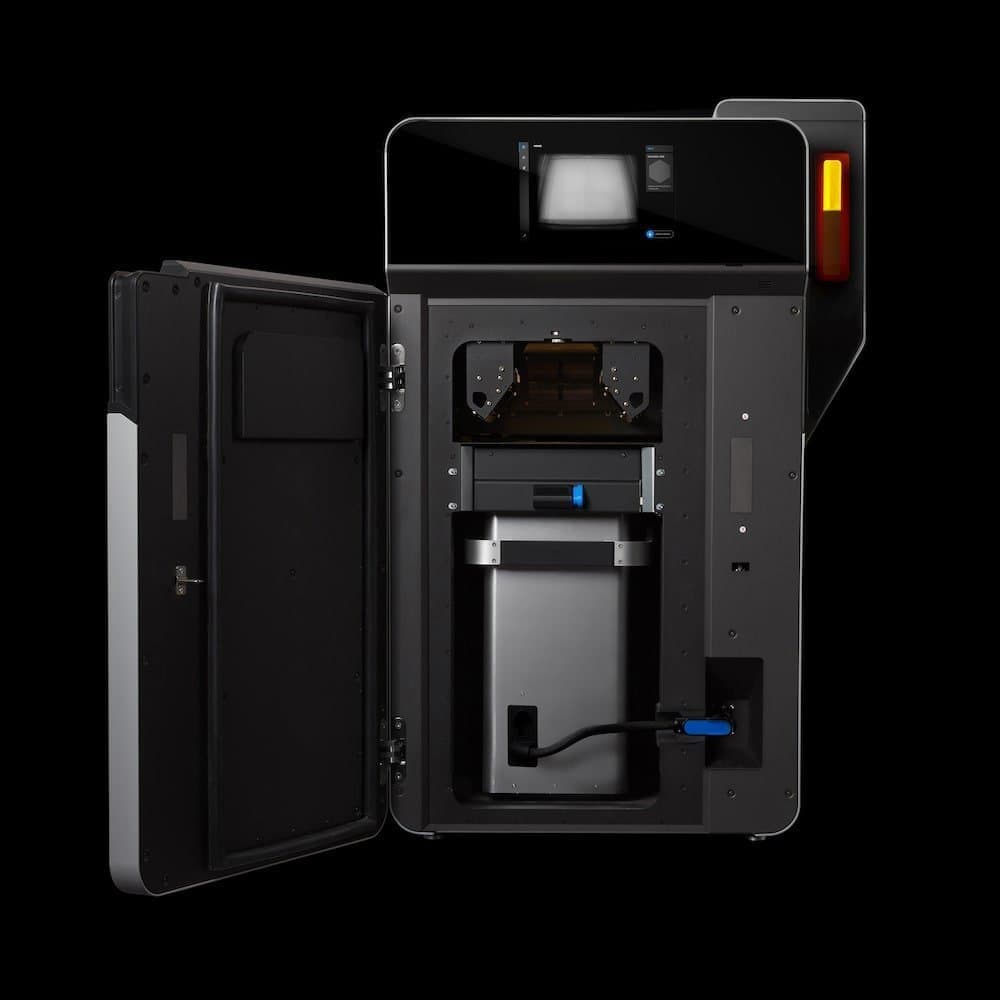
Demostración de producto de la Fuse 1
Ve nuestra demostración del producto para aprender más sobre el funcionamiento de la Fuse 1 y la impresión 3D SLS de la mano de expertos de Formlabs.
Creación de concept cars de alta fidelidad con la impresión 3D
"La progresión de la tecnología en la impresión 3D en los últimos diez años ha sido impresionante." Cuando yo empecé a producir vehículos especializados en pequeñas cantidades, algunos de los productos que fabricamos hoy habrían estado sencillamente fuera de nuestro alcance. Y ahora no solo soy capaz de producir esas piezas, sino que puedo producirlas de forma muy rentable y muy rápida", dijo Barnicott.
La impresión 3D ayuda al equipo no solo a crear mejores productos con mayor rapidez, sino también a atraer nuevas oportunidades de negocio. Descubrieron que muchos de sus clientes acuden a ellos porque quieren tener acceso a las tecnologías más punteras y fabricar sus componentes con materiales de vanguardia.
Hay ciertas cosas que simplemente ya no se pueden clasificar como tecnologías emergentes. La impresión 3D es una de ellas. Ha avanzado hasta un punto en el que todo lo que producimos es bastante bueno para usarlo en la fase de presentación final con todas las capas de refinamiento que le aplicamos. La impresión 3D pasado de ser casi una curiosidad a convertirse en parte totalmente imprescindible de lo que hacemos", explicó Moradi.