Cómo Figure Engineering desarrolló un material de SLA avanzado para el Departamento de Defensa de EE. UU.
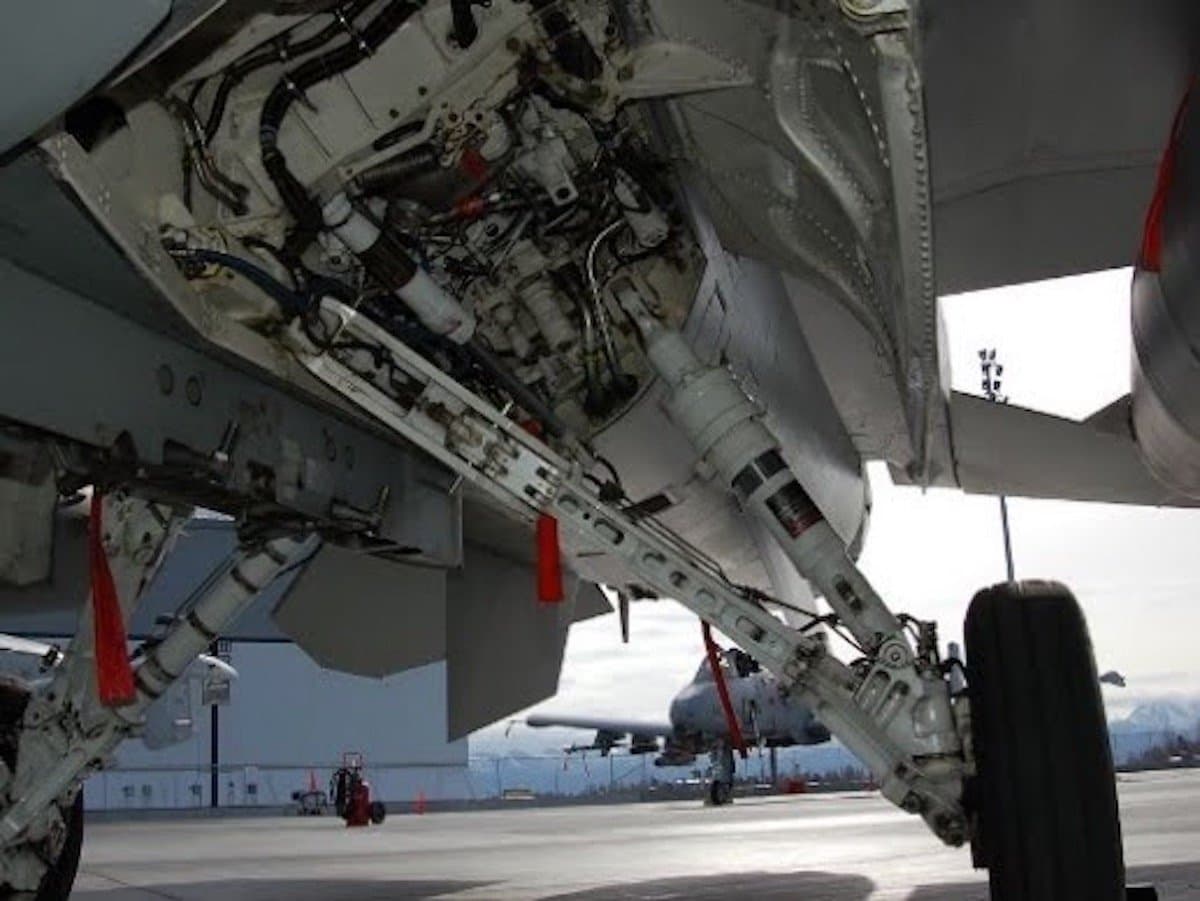
Por cada hora de vuelo que realiza un avión del Departamento de Defensa de Estados Unidos, se llevan a cabo unas 12 horas de mantenimiento. Aunque las operaciones de mantenimiento, reparación y renovación son necesarias para asegurar que cada aeronave funcione de forma segura y con el nivel de rendimiento más alto posible, a menudo se ven prolongadas por su carácter manual y los procesos tradicionales que se emplean en ellas.
El Departamento de Defensa siempre está buscando formas de mejorar estas operaciones y hacer que el proceso de trabajo sea más eficiente, y Figure Engineering, utilizando el nuevo ecosistema abierto de Formlabs, ha desarrollado una solución innovadora y asequible para hacerlo.
Figure Engineering ha aprovechado la velocidad de la impresora 3D de estereolitografía (SLA) Form 4 de Formlabs para desarrollar un nuevo material hecho específicamente para enmascaramientos y herramientas utilizadas en el proceso de galvanizado. El Editor de ajustes de impresión y el Open Material Mode han hecho posible que el cofundador de Figure Engineering Jonathon McDaniels y su equipo afinen su proceso de desarrollo de materiales y encuentren una nueva solución para un problema multimillonario.
Sucio, tedioso y peligroso: en busca de una solución avanzada
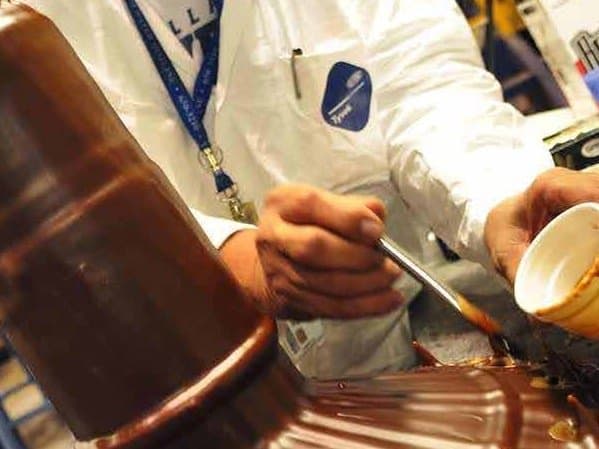
Pintar a mano con laca para enmascarar piezas que se van a galvanizar puede ser peligroso si los materiales que se usan son tóxicos, y cuando los operarios alcanzan sus límites de exposición, todo el proyecto tiene que detenerse, pudiendo dejar la aeronave varada en tierra durante más tiempo.
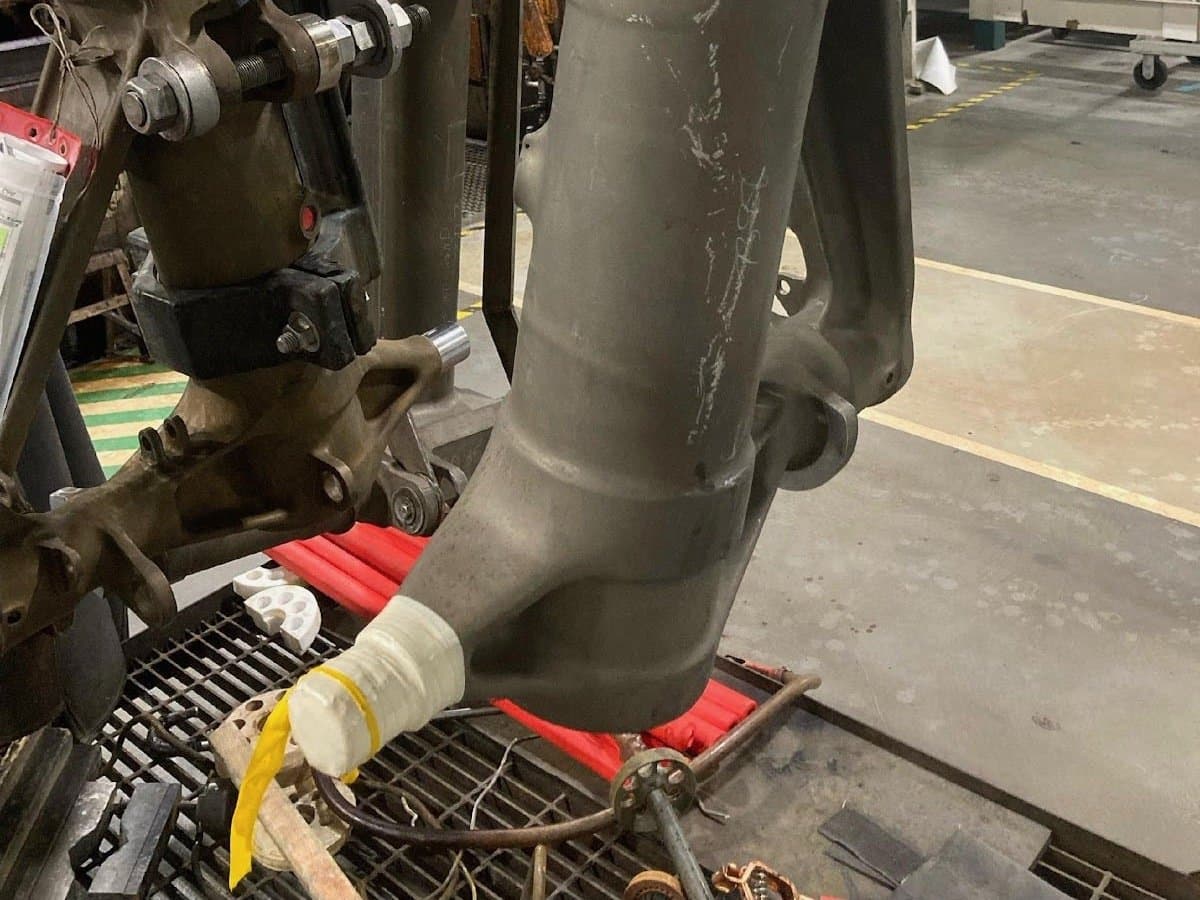
La aplicación de cinta adhesiva a mano para enmascarar ciertas áreas durante el proceso de galvanizado es lenta y laboriosa, y se debe repetir con cada pieza, lo que conduce a unos costes de mano de obra excesivos.
Figure Engineering desarrolla soluciones avanzadas de fabricación y mantenimiento, principalmente como contratista para las diferentes ramas del Departamento de Defensa, pero también para empresas privadas. En el caso de las aeronaves de la Fuerza Aérea, la Armada y el Ejército de los Estados Unidos, así como de las aerolíneas comerciales, Figure Engineering recibió el encargo de centrarse en áreas que se pasan por alto en el proceso de mantenimiento: el granallado adhesivo, la pintura, el galvanizado y los revestimientos.
Estas operaciones reciben el apelativo informal de "las tres D", por las palabras inglesas de lo que son: sucias, tediosas y peligrosas. Esa designación hace que sean menos visibles y conocidas que procesos como la sustitución del motor o las nuevas innovaciones en las puntas de las alas, pero pueden ser igual de importantes para el rendimiento general del aparato. Si los procesos tardan demasiado tiempo debido a procesos de trabajo poco eficientes, la preparación militar se puede ver afectada, los costes operativos crecen de forma considerable y, al involucrar con frecuencia productos químicos tóxicos, pueden afectar a la seguridad de los operarios.
Figure Engineering se especializa en encontrar soluciones innovadoras para hacer que estos procesos sean más seguros y eficientes y ha estado trabajando con talleres de la Fuerza Aérea de EE. UU. durante años. "Las mejores soluciones requieren mucha colaboración con el propietario del proceso, que es quien mejor va a conocer sus desafíos. En cuanto al proceso de galvanizado, este propietario nos decía: 'no puedo tener este avión listo lo bastante rápido y estamos generando mucho desperdicio'", dice McDaniels.
El problema: El proceso de trabajo del galvanizado de aviones
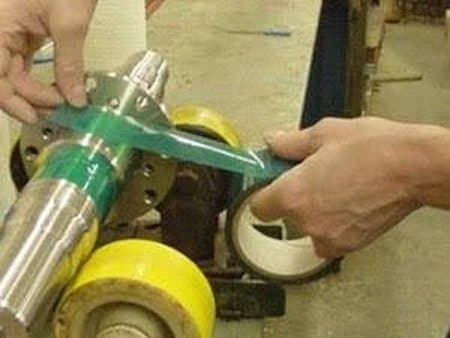
La cinta se aplica a mano.
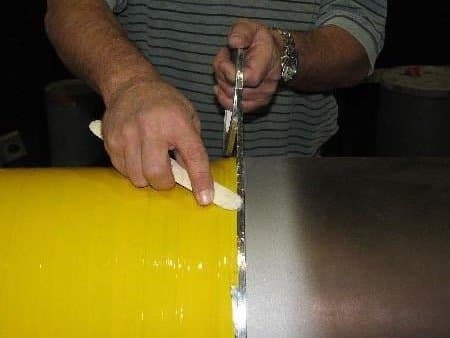
La cinta se recorta a mano.

Las piezas enmascaradas se sumergen en el baño de galvanizado.
Uno de los procesos más difíciles y lentos de mantenimiento, reparación y mejora de aviones es el galvanizado de componentes de gran tamaño para los trenes de aterrizaje. El proceso de trabajo incluye baños en productos químicos muy agresivos, así como horas de laborioso trabajo manual para enmascarar áreas que no haya que galvanizar, sea pintando a mano con una laca removible o cubriendo secciones de la pieza con cinta.
"La cantidad de trabajo manual que hace falta para que el recubrimiento acabe donde quieres que esté y que no esté donde no lo quieres es enorme, además de ser un proceso tedioso y caro. Los talleres de reparación querían una forma de reducir ese tiempo de trabajo manual y de crear máscaras que se pudieran sujetar o atornillar al aparato", dice McDaniels.
Sin embargo, cuando Figure Engineering comenzó a diseñar y crear prototipos de máscaras para galvanizado, se encontró con una complicada serie de problemas. "Cuando llevamos a cabo los estudios iniciales, nos encontramos con que no había nada que pudiera soportar los rigores del proceso de galvanizado. El material debía tener una gran resistencia química y ser muy duro: las piezas se caen continuamente o se golpean con martillos, por lo que deben ser bastante resistentes a los impactos", dice McDaniels.
Aparte del material, elegir el hardware de impresión adecuado también era un desafío. "Al principio, no nos cerramos a ninguna opción. Necesitábamos encontrar una impresora que fuera fácil de usar y fiable, y que además fuera de una marca conocida que obtuviera el apoyo de los distintos talleres", dice McDaniels.
Después de probar varias piezas de impresoras 3D de modelado por deposición fundida (FDM) y sinterizado selectivo por láser (SLS), el equipo se dio cuenta de que necesitaba piezas totalmente densas y no porosas. Los productos químicos utilizados en el proceso de galvanizado se podían introducir en las piezas impresas en 3D mediante FDM y SLS, y cuando se retiraban del baño, seguían supurando los productos químicos tóxicos en sus superficies. La respuesta fue la impresión con resina, y aunque Figure Engineering probó varias impresoras 3D, una de ellas destacó entre las demás.
"No tardó en quedarme claro que Formlabs era la empresa con la que quería trabajar. Un coste menor por un equipamiento de mayor calidad, que las impresoras sean muy fiables y que la marca sea muy conocida la convirtieron en la mejor opción".
Jonathon McDaniels, cofundador de Figure Engineering
McDaniels empezó con la Form 3+, modificando los ajustes de impresión y realizando iteraciones de una formulación de resina hecha a su medida con el Open Material Mode. Cuando llegó la Form 4, ese proceso de iteración se vio potenciado y el desarrollo de su formulación personalizada de resina se aceleró.
"Cuando se lanzó la Form 4, muchos de los problemas que teníamos desaparecieron de la noche a la mañana. La Form 4 era revolucionaria en cuanto a su capacidad de imprimir estos materiales tan difíciles. Después de todo, estamos llevando la fabricación aditiva con polímeros al límite para que estos materiales puedan soportar el proceso de galvanizado", nos cuenta McDaniels.
Desarrollo de materiales únicos con el ecosistema abierto de Formlabs
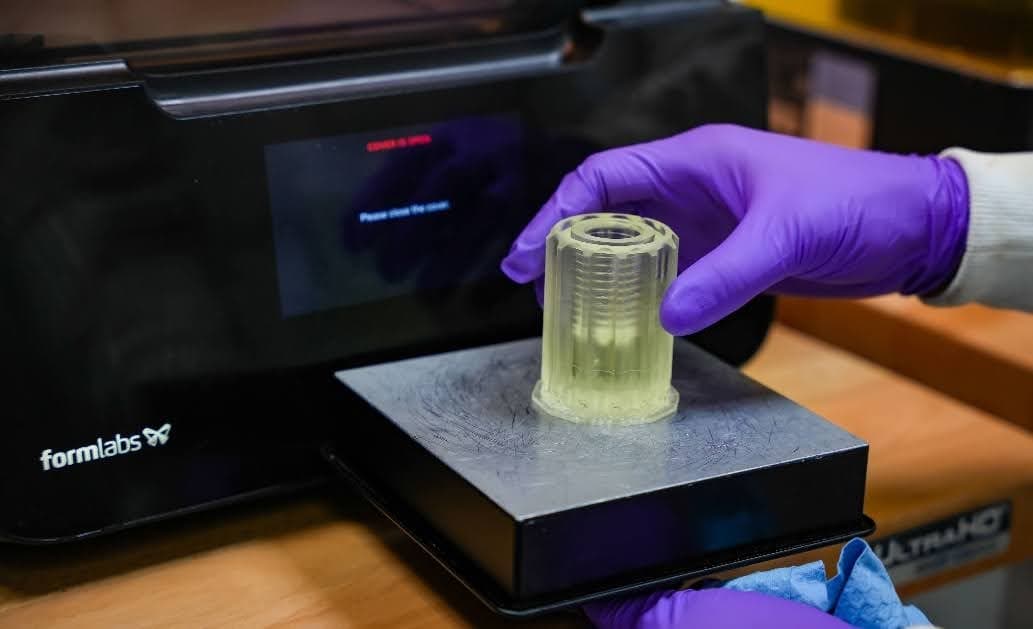
La Form 4 le dio a Figure Engineering el empujón que necesitaba: triplicar el número de iteraciones que podían probar cada día les dio una información más rápida y les permitió probar más parámetros de impresión en un período de tiempo más corto para encontrar la configuración perfecta.
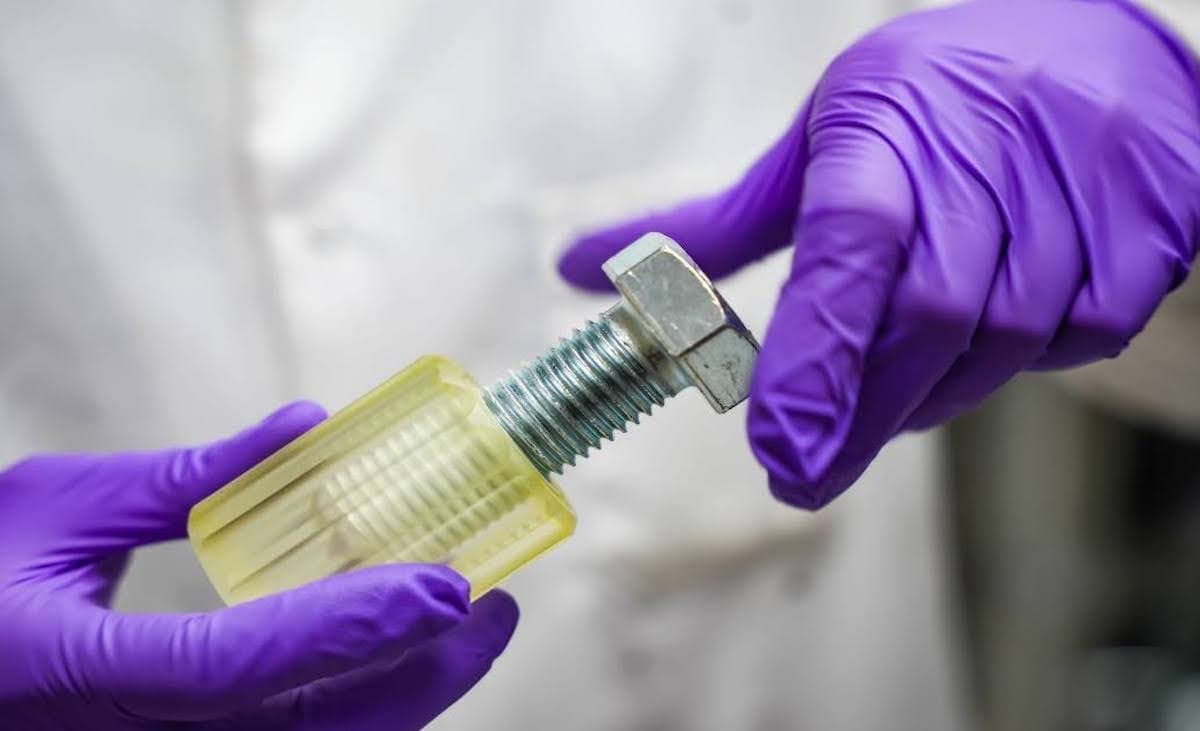
El material hecho a medida por Figure Engineering hizo posible crear herramientas de enmascaramiento muy resistentes a los productos químicos, fuertes y reutilizables, como esta herramienta que se puede enroscar directamente en un tornillo de gran tamaño que requiere galvanizado.
La gran velocidad de impresión de la Form 4 permitió al equipo de Figure Engineering realizar más del doble de ensayos que podían antes, pero fue el acceso a los ajustes de la impresora lo que hizo posible crear un material nuevo, totalmente funcional y avanzado técnicamente.
"No habríamos podido despegar sin el Open Material Mode y el Editor de ajustes de impresión", dijo McDaniels. Desarrollar materiales nuevos y afinar los ajustes de impresión requiere entender el efecto que cada ajuste tiene en el resultado. Por eso, la experiencia de McDaniels con la ingeniería química resultó útil en su trabajo con el equipo de Formlabs para afinar determinados procesos. "Modificar los ajustes de impresión fue bastante sencillo. Entender cómo funciona la impresora, cómo la resina rellena y da soporte a la primera capa y cosas por el estilo es algo que ayuda en el proceso. En cuanto tus números acaban dentro del intervalo correcto, todo empieza a imprimirse como debería. Cuando uno entiende eso, usar los ajustes se vuelve fácil", dice McDaniels.
Reducción del trabajo manual y los costes
Desarrollar una resina para hacer piezas que sirvan para enmascarar en el galvanizado requería características únicas, que no estaban disponibles en ningún sistema existente. Formlabs ofrecía a Figure Engineering una plataforma que usar como base para su investigación: una impresora 3D rápida y fiable, acceso a ajustes de impresión y a software, y un equipo implicado que estaba preparado para apoyar a McDaniels y sus compañeros y colaborar con ellos.
La formulación personalizada desarrollada por Figure Engineering ya se ha entregado a un taller mantenimiento, reparación y mejora de aviones de la Fuerza Aérea de Estados Unidos para su uso. Cuando las piezas de enmascaramiento ya están diseñadas e impresas, su implementación en el proceso de enmascaramiento reduce drásticamente el tiempo que lleva preparar los componentes de las aeronaves para el galvanizado. "En el fondo, el objetivo es lograr que los operarios pasen menos tiempo de trabajo manual en este proceso y que estén apartados todo lo posible de los baños químicos", dice McDaniels.
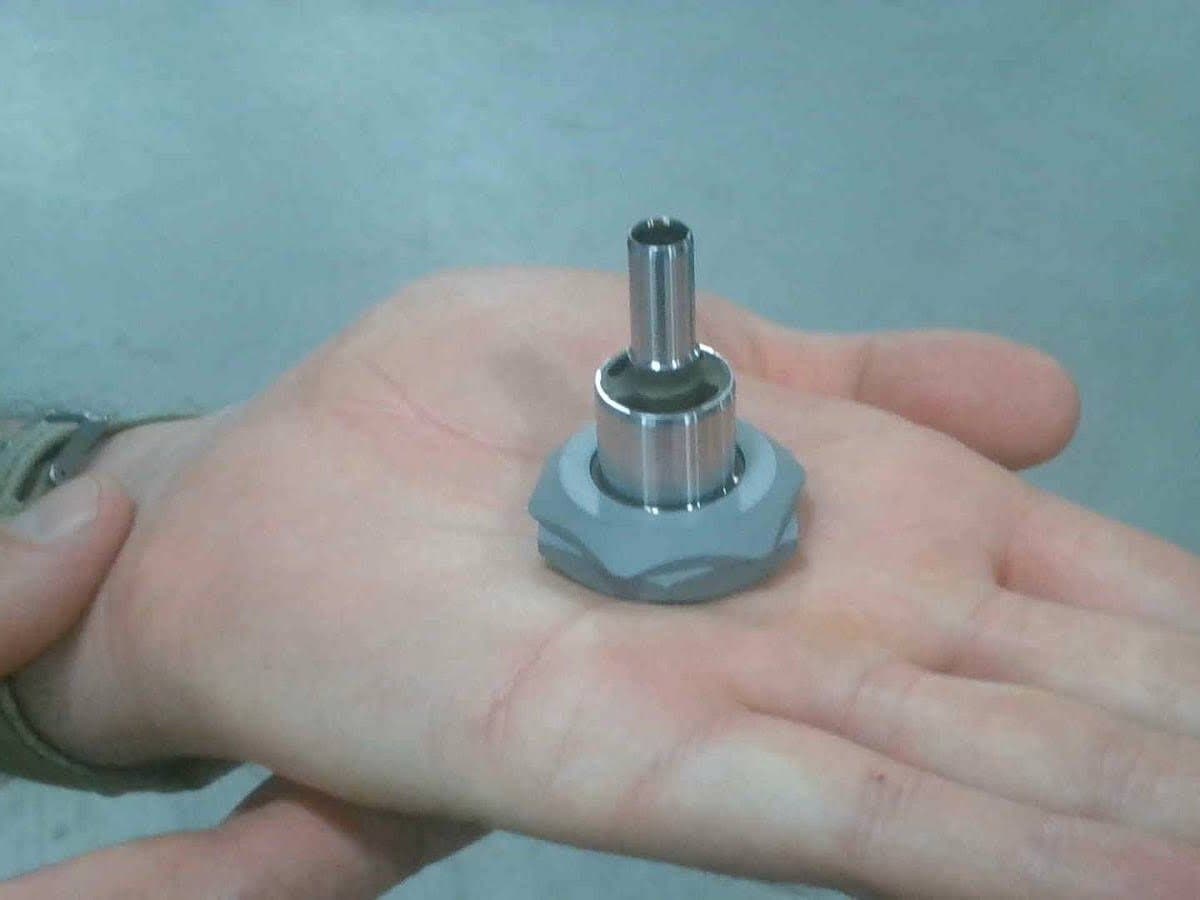
Crear una máscara a mano para este tornillo de metal costaba uno 250 $ por máscara, mientras que imprimirlas con elementos de roscado integrados usando Resist™hace que cada más cara solo cueste 5 $.
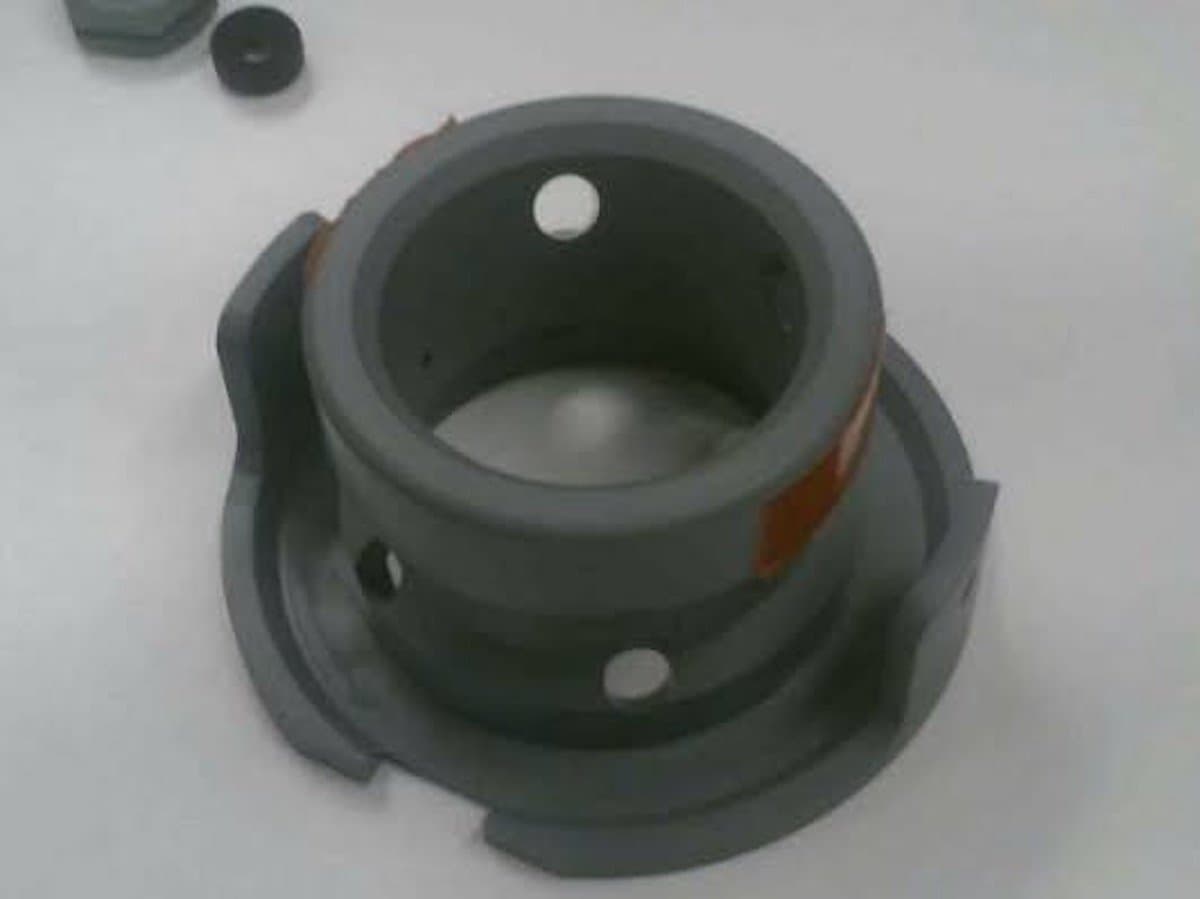
Esta pieza de gran tamaño tiene un coste de unos 550 $ en cuanto a materiales y mano de obra durante su aplicación, mientras que el proceso de enmascaramiento tradicional cuesta entre 2000 $ y 4000 $.
Cada pieza impresa en 3D se puede reutilizar en hasta 20 ciclos de galvanizado y solo pensar en las lacas y las cintas, que son de un solo uso, permite ver que los talleres de galvanizado gastan millones de dólares al año en laca y cinta de enmascaramiento. Aunque el diseño, la impresión y el posacabado de la impresión 3D pueden llevar tiempo, ese diseño se puede compartir entre departamentos, talleres o incluso distintas ramas de las fuerzas armadas, de modo que cualquier avión con un componente que requiera un galvanizado podría llegar a usar el mismo diseño e imprimirlo bajo demanda. Además, las máscaras impresas en 3D se pueden producir en lotes y almacenarse hasta el momento en el que hagan falta. El enmascaramiento es un gran cuello de botella en el proceso de galvanizado y pasar a imprimir las máscaras en 3D elimina ese cuello de botella.
Apuntando cada vez más alto
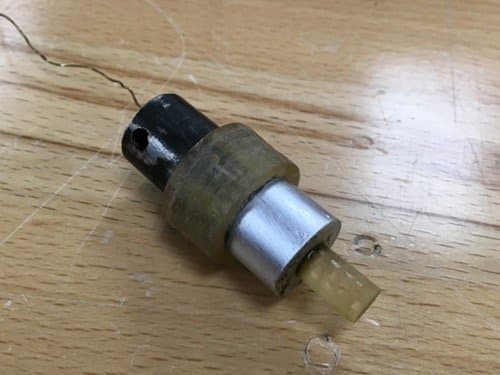
Fase 1: Viabilidad
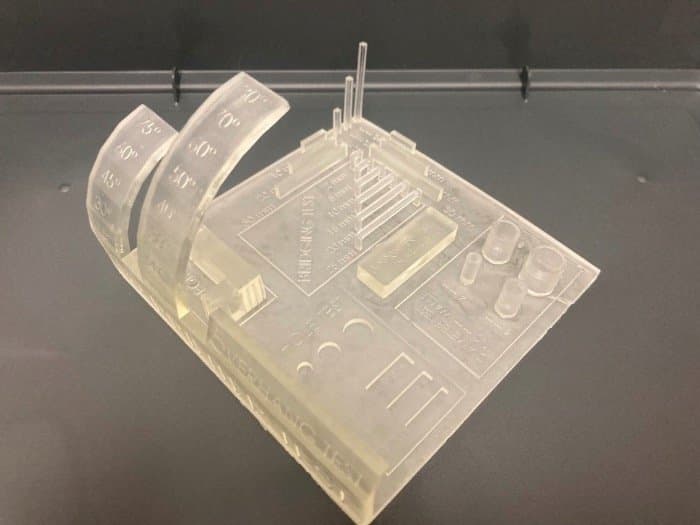
Fase 2: Desarrollo
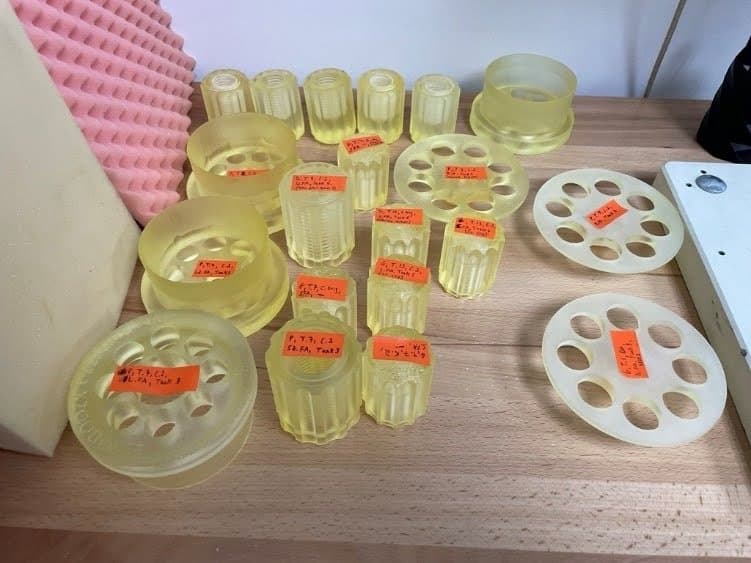
Fase 3: Primera demostración del artículo
La colaboración entre Figure Engineering y Formlabs ha demostrado que las soluciones a problemas grandes y complejos se pueden encontrar más rápido con el socio adecuado. La experiencia de Figure Engineering con la ingeniería química y su profunda comprensión del problema fueron cruciales, pero necesitaban algo más que solo una impresora 3D para llegar a la solución adecuada: necesitaban acceso a una plataforma de impresión potente y asistencia para utilizarla.
El ecosistema abierto de Formlabs y el Open Material Mode han permitido a McDaniels y su equipo crear un material y un proceso de trabajo completamente nuevos para el Departamento de Defensa, ahorrando potencialmente millones de dólares en materiales y costes de mano de obra y mejorando la seguridad de los técnicos en talleres de mantenimiento, reparación y renovación de todo el país. "Nuestro trabajo no habría sido posible sin el Open Material Mode", dice McDaniels. "De hecho, ha cambiado nuestra forma de pensar en proyectos nuevos en el futuro. Este no será el último material de impresión 3D que crearemos. Estamos trabajando con otras partes del Departamento de Defensa de EE. UU. e incluso con aerolíneas privadas comerciales. El Open Material Mode es nuestra vía para acceder a esas oportunidades".
Infórmate acerca del ecosistema abierto de Formlabs o pide una pieza de muestra gratuita para ver de primera mano la calidad de la Form 4.