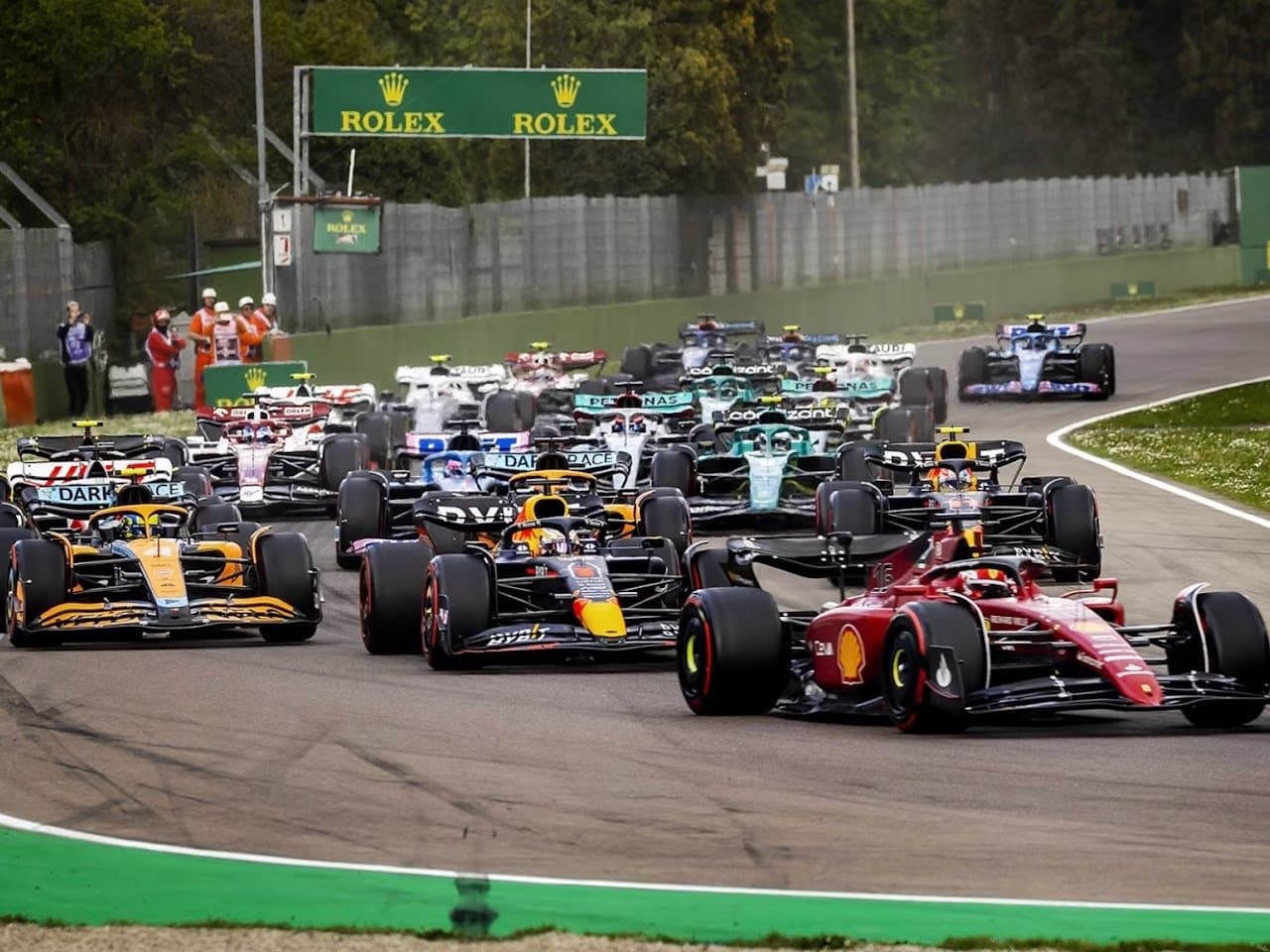
Foto cortesía de Formula1.com
A medida que símbolos de la automoción a escala mundial como la Fórmula 1 se vuelven más populares, crece la presión para hacer que todos los coches sean cada vez más rápidos y más potentes. Los equipos de Fórmula 1 ya incluyen a algunas de las mentes más brillantes de la ingeniería, pero a veces hasta estos equipos de primera línea recurren a expertos externos para alcanzar esos ansiados caballos de potencia.
Uno de esos expertos es Mackart Additive, una subcontrata de ingeniería y fabricación con sede en Staffordshire, en pleno corazón del Reino Unido. Gracias a sus más de dos décadas de experiencia con el diseño para ingeniería y la fabricación aditiva, Mackart ha podido llevar la impresión 3D más allá de los parámetros tradicionales del prototipado rápido. Alrededor de un 80 % de los proyectos actuales de Mackart son para equipos de Fórmula 1, clientes que no paran de buscar mejoras en cuanto a la ligereza, la potencia, la fiabilidad y la optimización aerodinámica de sus vehículos. El equipo de McCarthy ha destacado a la hora de imprimir en 3D herramientas complejas para componentes de plástico reforzado con fibra de carbono que están estableciendo estándares y nuevas expectativas que antes eran inalcanzables.
Mackart utiliza nueve impresoras de estereolitografía (SLA) de la serie Form 3 y la Form Auto, así como impresoras de modelado por deposición fundida (FDM) y materiales compuestos para fabricar utillaje de fibra de carbono y silicona, además de componentes de uso final impresos en 3D. Trabajando con el socio oficial de Formlabs Solid Print3D, Mackart ha expandido sus operaciones hasta alcanzar volúmenes de producción industriales.
"No vemos la impresión 3D como una herramienta de prototipado rápido, sino como un proceso de fabricación eficiente."
Steven McCarthy, director ejecutivo y fundador de Mackart Additive
Impresión 3D de utillaje complejo para piezas de fibra de carbono
McCarthy provenía del sector de la ingeniería aeroespacial, pero desde que fundó Mackart en 2016, la empresa se ha asociado con un amplio abanico de sectores, desde fabricantes de equipamiento de fontanería a titanes internacionales del sector automovilístico.
Uno de los materiales más comunes que se usan en el mundo de los coches de competición y que recientemente está pasando a ser de uso común en la industria automovilística es la fibra de carbono. Los componentes de los plásticos reforzados con fibra de carbono pueden soportar las altas temperaturas del circuito, al mismo tiempo que ofrecen una proporción entre fuerza y peso incomparable que potencia cada aspecto del rendimiento del vehículo.
Las piezas de fibra de carbono se suelen fabricar utilizando láminas preimpregnadas de tejido de carbono a las que se le aplica el volumen correcto de resina sin curar. A continuación, estas láminas preimpregnadas se laminan dentro o encima del molde y se curan con calor y presión en un autoclave.
Tradicionalmente, cada molde se mecaniza a partir de metal para soportar el calor y la presión del autoclave. Este proceso sustractivo tiene varias desventajas: puede ser derrochador, lento y caro, e inhibe el proceso de diseño iterativo. Al haber avanzado los materiales y el equipamiento, se ha convertido en una opción viable para crear herramientas duras para estas aplicaciones.
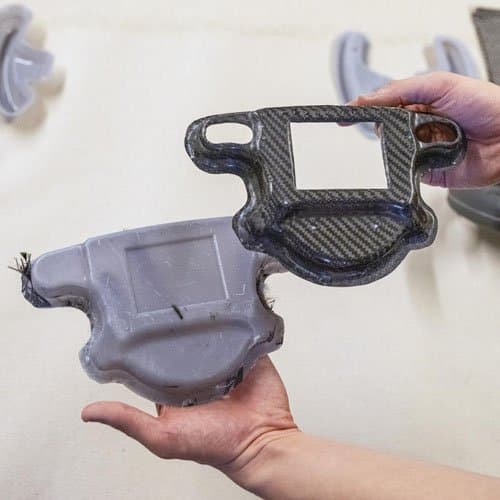
Fabricación de piezas de fibra de carbono con moldes impresos en 3D
Descarga este libro blanco con guías para diseñar moldes compuestos y directrices paso a paso para los métodos de preimpregnado (prepreg) y de laminado manual para crear piezas de fibra de carbono.
Combinación de tecnologías para utillaje de fibra de carbono
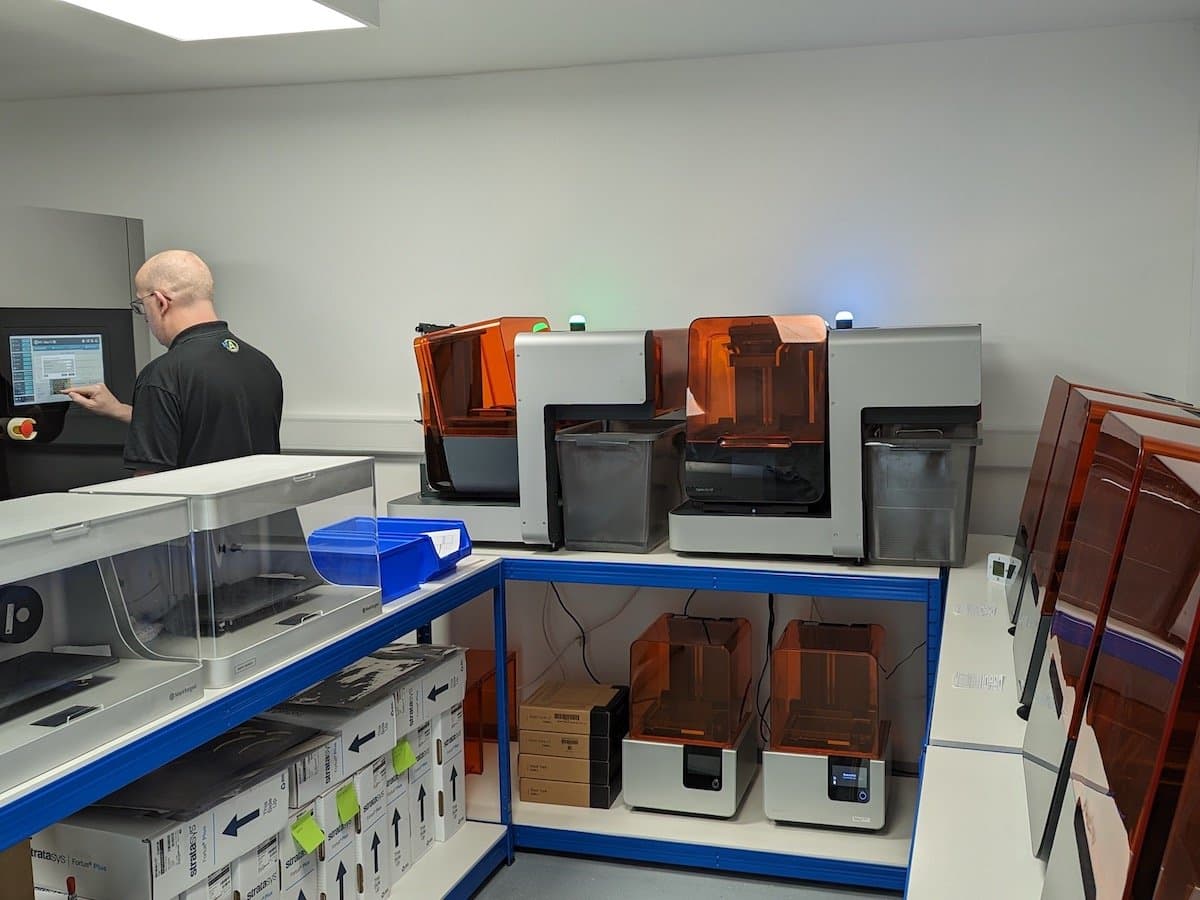
El laboratorio de impresión 3D de Mackart Additive combina varias tecnologías y procesos, que incluyen dos accesorios Form Auto, para crear piezas avanzadas para un amplio abanico de aplicaciones industriales.
La clave para fabricar con éxito utillaje industrial es optimizar el diseño y la orientación de la impresión, parámetros que el equipo de Mackart domina a la perfección. Diseñan y fabrican moldes y mandriles complejos de fibra de carbono utilizando una combinación de diferentes tecnologías y materiales de impresión 3D, cada uno de ellos elegido por sus atributos específicos.
Tras empezar usando la Grey Resin y después la Grey Pro Resin, el equipo comenzó a probar la Rigid 4000 Resin y la Rigid 10K Resin y descubrió que su acabado de la superficie liso y su rigidez daban los mejores resultados con las piezas de fibra de carbono de uso final. "Probamos herramientas de impresión única con la Rigid 4000 Resin y los resultados fueron excelentes. Lo inspeccionamos mediante metrología por láser y los resultados que presentaron en cuanto a sus medidas fueron excelentes. En algunos casos, las desviaciones respecto a la geometría hecha en CAD eran de micras", dice McCarthy.
El equipo produce a menudo herramientas de gran tamaño dividiéndolas en piezas más pequeñas y uniéndolas después con elementos de fijación cuidadosamente considerados. "Para herramientas más grandes que sobrepasan los volúmenes de impresión de la impresora, incluimos con frecuencia articulaciones que rebordes que favorezcan el ensamblaje. Podemos producir conjuntos de tres o cuatro componentes para obtener herramientas de cerca de 450 mm de longitud", dice McCarthy.
Comparación de tecnologías: Utillaje para piezas de fibra de carbono
Tiempo de espera | Ventajas | Inconvenientes | |
---|---|---|---|
Utillaje impreso en 3D | 1 semana | Libertad de diseño Control de los tiempos de espera/la cadena de suministro Rentable para volúmenes más bajos | Hay que considerar la dilatación térmica Limitaciones de tamaño Menor número de usos por pieza |
Utillaje hecho de forma tradicional | 3-4 semanas | Miles de usos por pieza Durabilidad Tamaño | Esperas largas Limitaciones de diseño |
Configuración de los parámetros y optimización del proceso
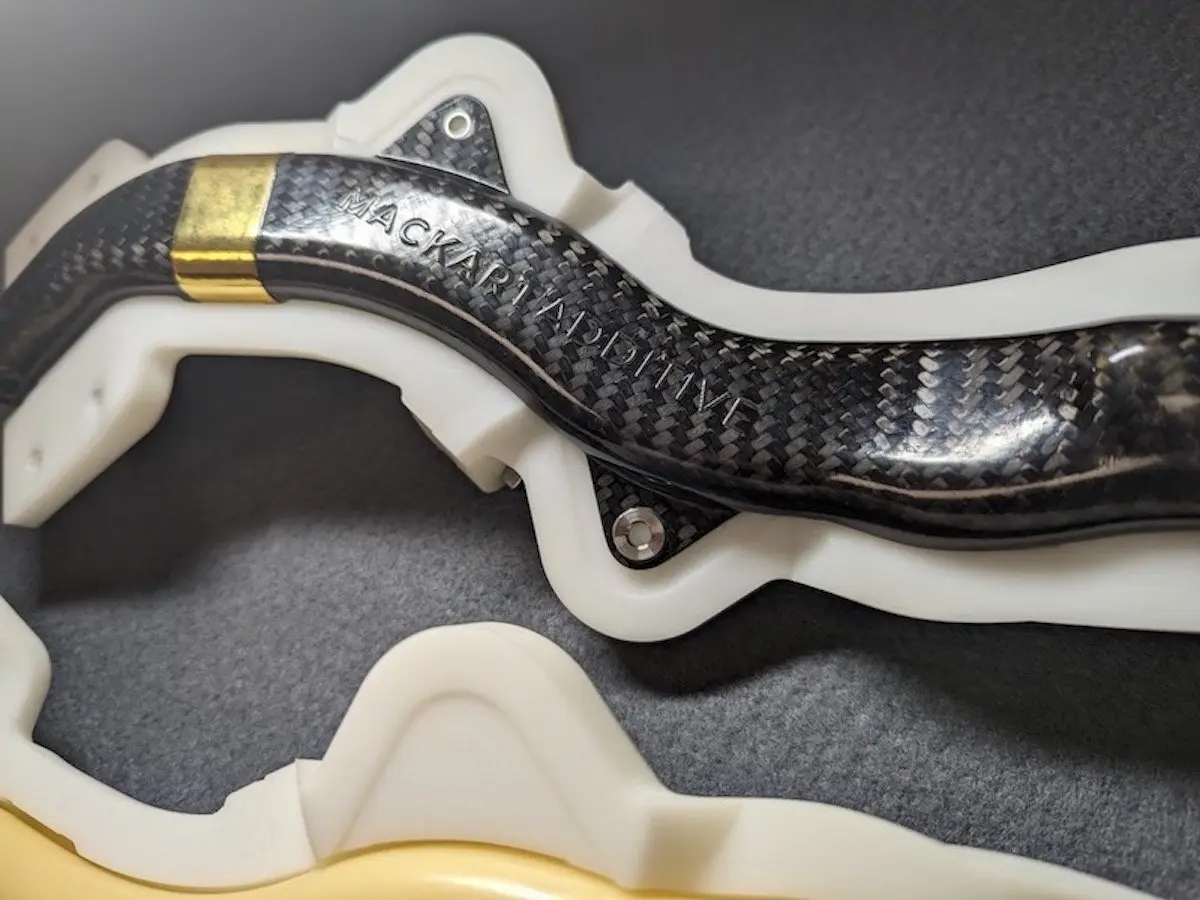
Este componente de conducto de fibra de carbono se fabricó con utillaje rápido impreso en 3D, incluida una carcasa exterior impresa en la Form 3+ con la Rigid 10K Resin y un mandril interno de molde impreso en una impresora 3D SLA de gran tamaño con un tanque profundo.
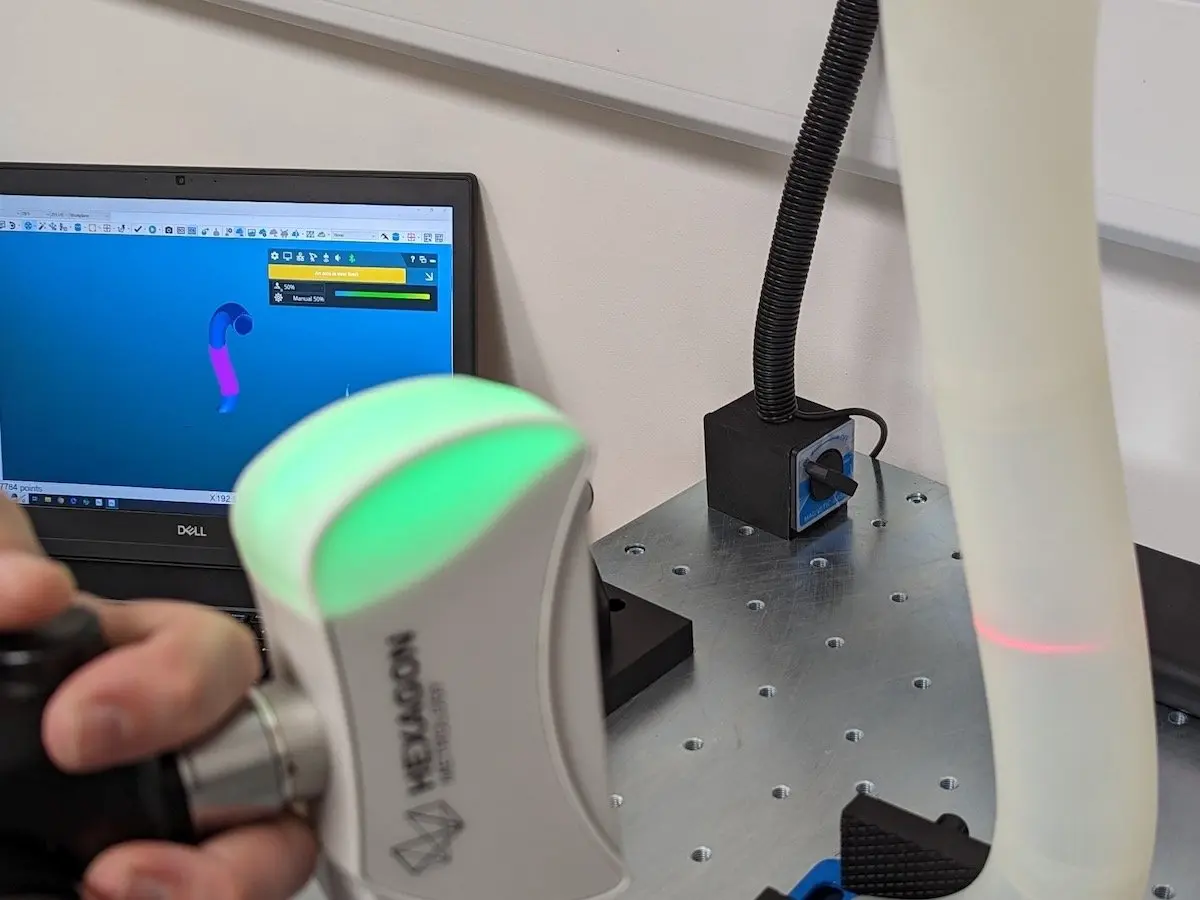
McCarthy escanea en 3D un mandril impreso en la Form 3 con la Durable Resin, que se utilizará en un proceso de fabricación con plásticos reforzados con fibra de carbono para crear un conducto de aire para un Fórmula 1.
Durante el proceso de curado en autoclave, las temperaturas pueden superar la temperatura de transición vítrea del material de la herramienta, pero el equipo ha descubierto que la Rigid 10K Resin funciona bien y que no se degrada ni pierde su precisión dimensional después de un uso repetido. "La Rigid 10K Resin es un material más duro y ofrece un acabado de la superficie ligeramente mejor. La verdad es que es un buen sustituto del aluminio", dice McCarthy. Para optimizar la superficie para interactuar con las láminas de fibra de carbono, el equipo de Mackart embellece ligeramente la superficie de las piezas del molde de Rigid 10K Resin para eliminar las partículas de vidrio que quedan visibles por el proceso único de conversión del fotopolímero de la Rigid 10K Resin durante la impresión.
El equipo también ha introducido en su configuración factores de compensación para la fluencia del material durante el proceso de autoclave, para que la pieza resultante de plástico reforzado con fibra de carbono se fabrique de acuerdo con las tolerancias establecidas. "Si no se vuelve muy complicado, podemos hacer que encaje perfectamente en las tolerancias. Con las herramientas grandes es todo cuestión de porcentajes", dice McCarthy.
Para la forma interna de componentes complejos de fibra de carbono como conductos o tubos se usan mandriles solubles de forma tradicional. Sin embargo, para componentes más pequeños (que cabrían dentro del volumen de impresión de la impresora) es posible producir mandriles extraíbles y evitar la complejidad y el tiempo que requiere la solución soluble de forma tradicional que produce el FDM. Mackart ha utilizado para ello la Durable Resin con gran éxito. Para los mandriles extraíbles de gran tamaño que sobrepasan el volumen de impresión de la impresora, Mackart recurre a su proceso interno de SLA en tanque profundo.
Lo importante son los detalles
La fabricación aditiva es perfecta para un sector como el de los vehículos de competición, donde cada incremento derivado del diseño, incluso de micras, puede suponer la diferencia de un segundo o de cruzar o no el primero la línea de meta. La circulación del aire alrededor del coche y dentro de él lo es todo.
"La impresión 3D ofrece una buena solución para el deporte automovilístico, ofreciendo un grado de libertad sin las restricciones típicas de los métodos sustractivos tradicionales. Al ser tan valioso el espacio en un coche de carreras, esa libertad geométrica permite a los equipos optimizar todo el paquete aerodinámico. Si no hubiéramos tenido la capacidad de manipular e incluir componentes rígidos de fibra de carbono en el coche sin renunciar a prestaciones (las piezas de fibra de carbono hechas a partir del utillaje impreso), es posible que no hubiéramos visto algunas de las mejoras de rendimiento de las últimas temporadas. Para poder producir herramientas que den acceso a este potencial hay que adoptar utillaje impreso en 3D optimizado por una técnica de diseño cuidadosa y bien desarrollada", dice McCarthy.
Anteriormente, la fabricación de geometrías relativamente complejas para plásticos reforzados con fibra de carbono mediante métodos de utillaje sustractivo hacía que fuera necesario incorporar material sobrante en los componentes para que hubiera un "desbarbado" en la fase de ajuste final. La precisión y la estabilidad de las herramientas de moldeo impresas en 3D han reducido en gran medida esta necesidad de material adicional. „Ahora se ha creado una expectativa de hacer las piezas bien a la primera y hemos conseguido eso repetidamente con los componentes con fibra de carbono que fabricamos. Lo que se nos da bien es hacer geometrías muy complicadas y precisas", dice McCarthy.
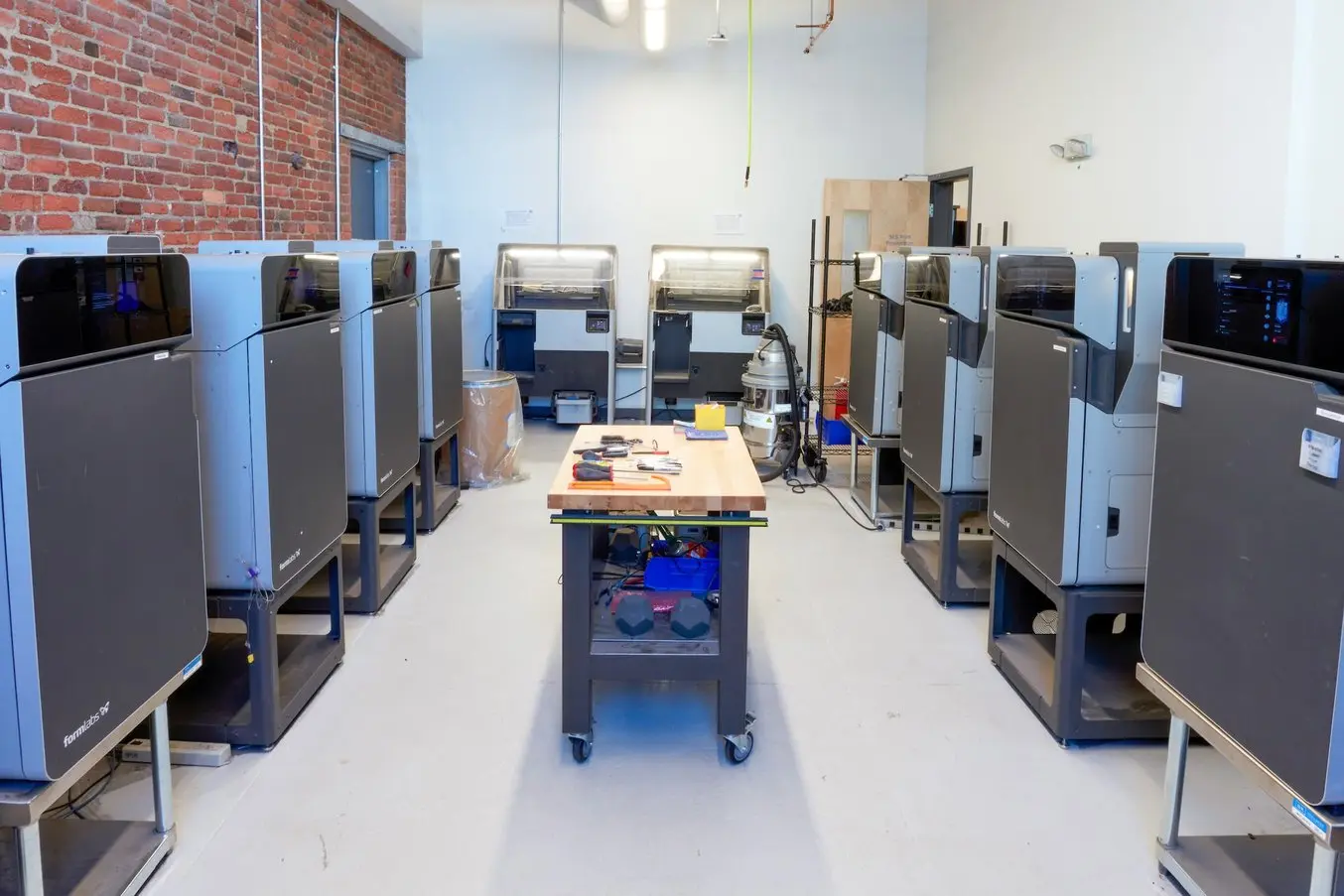
Gestión de parques de impresoras 3D
Gestionar múltiples impresoras SLA y SLS no tiene por qué ser complicado, ya que cualquier empresa puede poner en marcha un parque de impresoras SLA y SLS en solo uno o dos días. Esta guía repasará cuatro situaciones distintas de éxito con varias impresoras para ayudarte a establecer un proceso de trabajo eficiente para cualquier tipo de pieza o volumen de producción.
Cómo añadir un tercer turno a la jornada con la Form Auto
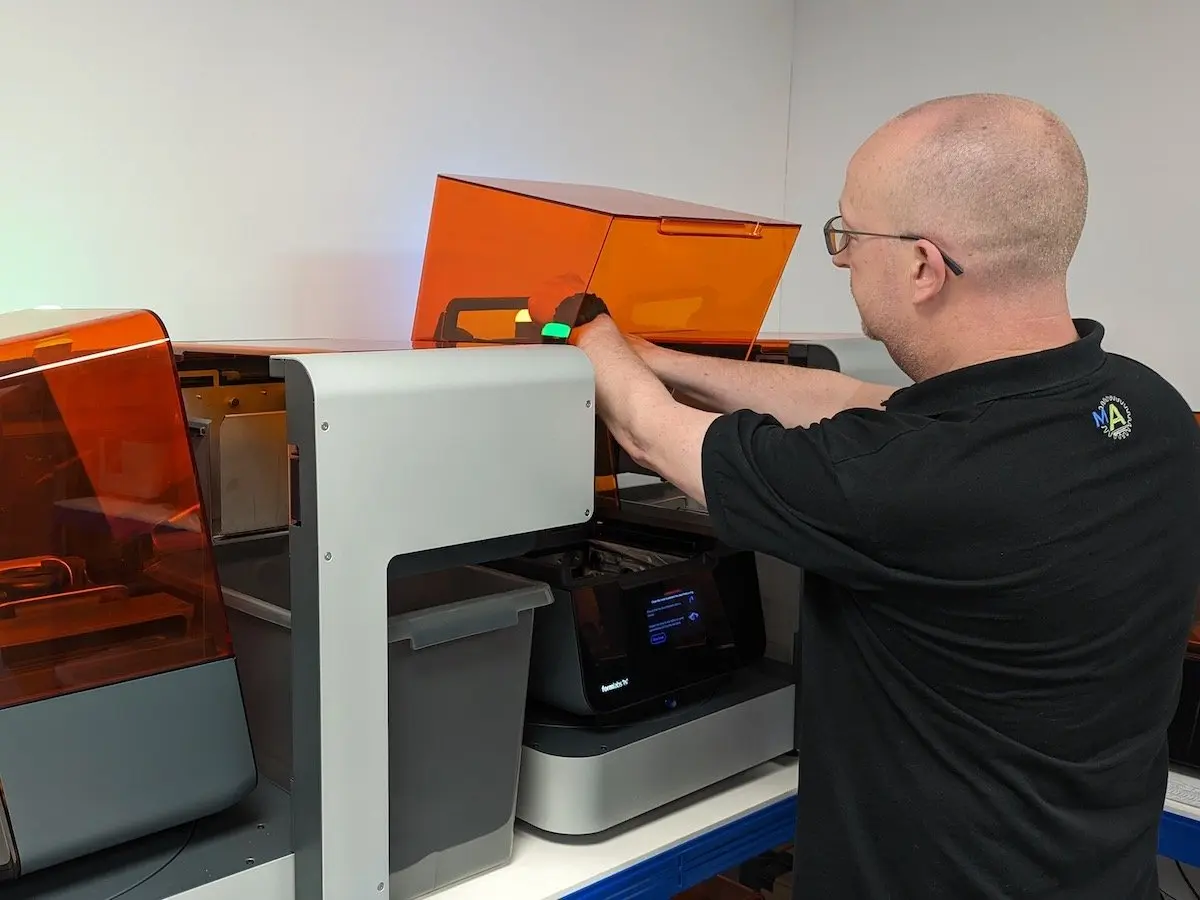
La Form Auto se puede incorporar en una impresora Form 3 o Form 3+ adquirida anteriormente, lo que permite a los laboratorios expandir su instalación de equipamiento a medida que crezca su negocio.
Mackart adoptó pronto el ecosistema de automatización de Formlabs, ya que empezó a utilizar la Form Auto a principios de 2023 y ha estado optimizando su proceso de trabajo de automatización desde entonces. "Hay una oportunidad para maximizar la capacidad, dado que la ventaja de la Form Auto es que se puede añadir un tercer turno a la jornada: el de la noche", dice McCarthy.
Se instaló la Form Auto en dos de sus nueve impresoras Form 3+ y está funcionando de forma continua, trabajando por la noche y durante el fin de semana para seguir imprimiendo incluso cuando el equipo se ha ido a casa.
"Con la Form Auto, puedes dejar las máquinas trabajando durante la noche y el fin de semana, sin tener que planear cambios de cartuchos, tanques o bases de impresión. Funciona bien y es estupenda para componentes pequeños y series de producción en lotes de tamaño medio, de hasta 1000 piezas y más".
Steven McCarthy, director ejecutivo y fundador de Mackart Additive
El equipo de Mackart siempre está trabajando en diversos proyectos, así que aunque siguen trabajando manualmente con algunas de sus piezas más nuevas y complejas, la Form Auto puede ocuparse de muchas de sus tareas repetitivas y reducir los tiempos de inactividad de la impresora. "Gracias a ello, nuestras esperas se han reducido y ha crecido la productividad", dice McCarthy.
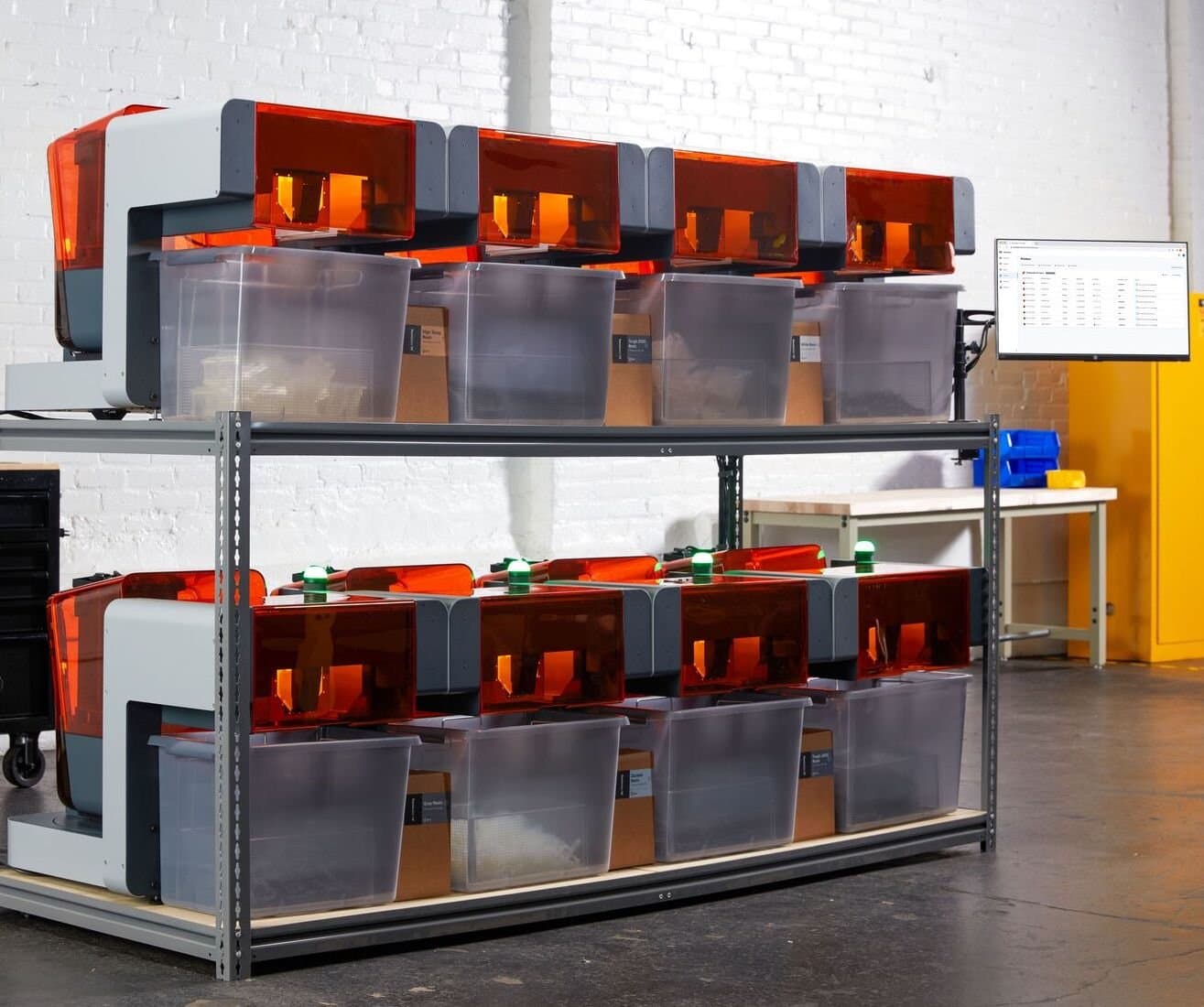
Presentamos el ecosistema de automatización de Formlabs
Descubre el ecosistema de automatización de Formlabs: desde una producción de piezas 24/7 que redefine el rendimiento y la productividad a un parque de impresoras 3D automatizado.
Cómo eliminar 10 000 £ del coste de las piezas de coches clásicos
Algunas de esas tareas repetidas son para piezas pequeñas que se deben producir en volúmenes mayores, como las piezas de coches clásicos. Normalmente, estas piezas se moldearían por inyección, pero muchas de estas herramientas se han perdido con el paso del tiempo y sus últimas existencias se han agotado. Esta situación hizo que un cliente pidiera ayuda a Mackart.
Estas piezas podían costar 0,20 £ cada una cuando sí se fabricaban. La impresión 3D hace que cuesten cinco o diez veces más, pero sin los gastos de crear herramientas nuevas, series de moldeo de inyección mínimas que no aprovechen toda la capacidad, los costes de instalación y, lo que es más, la incapacidad de amortizar ninguno de estos costes de producción de forma viable con cada componente.
Imprimir el componente en 3D ofrece ahora una solución muy viable. "Al imprimir estas piezas en 3D, se saca la amortización de todo el coste de producción con moldeo por inyección de la ecuación: diseñamos lo que haga falta mediante ingeniería inversa y el cliente solo tiene que comprar una unidad de la pieza, sin pagar 10 000 £ o más por una nueva herramienta de moldeo por inyección ni los demás costes adicionales relacionados con ese proceso. Después, se tiene la base para ofrecer un suministro de las piezas en las cantidades que el cliente necesite", dice McCarthy.
En el sector de la automoción, obtener una pieza o incluso una cantidad pequeña de ellas puede resultar tremendamente caro, por lo que restaurar y mantener coches clásicos se convierte en un lujo. Con la impresión 3D, Mackart puede ofrecer a los clientes precios reducidos independientemente de las cantidades. "Es una solución económica mucho más flexible, que es en lo que destaca la Form Auto. Llega ya lista, requiere un cuidado mínimo y se pueden producir 1000 piezas y solo habría que cambiar de cartucho de resina ocasionalmente", dice McCarthy.
Tras demostrar la viabilidad de su caso, Mackart quiere expandir su capacidad
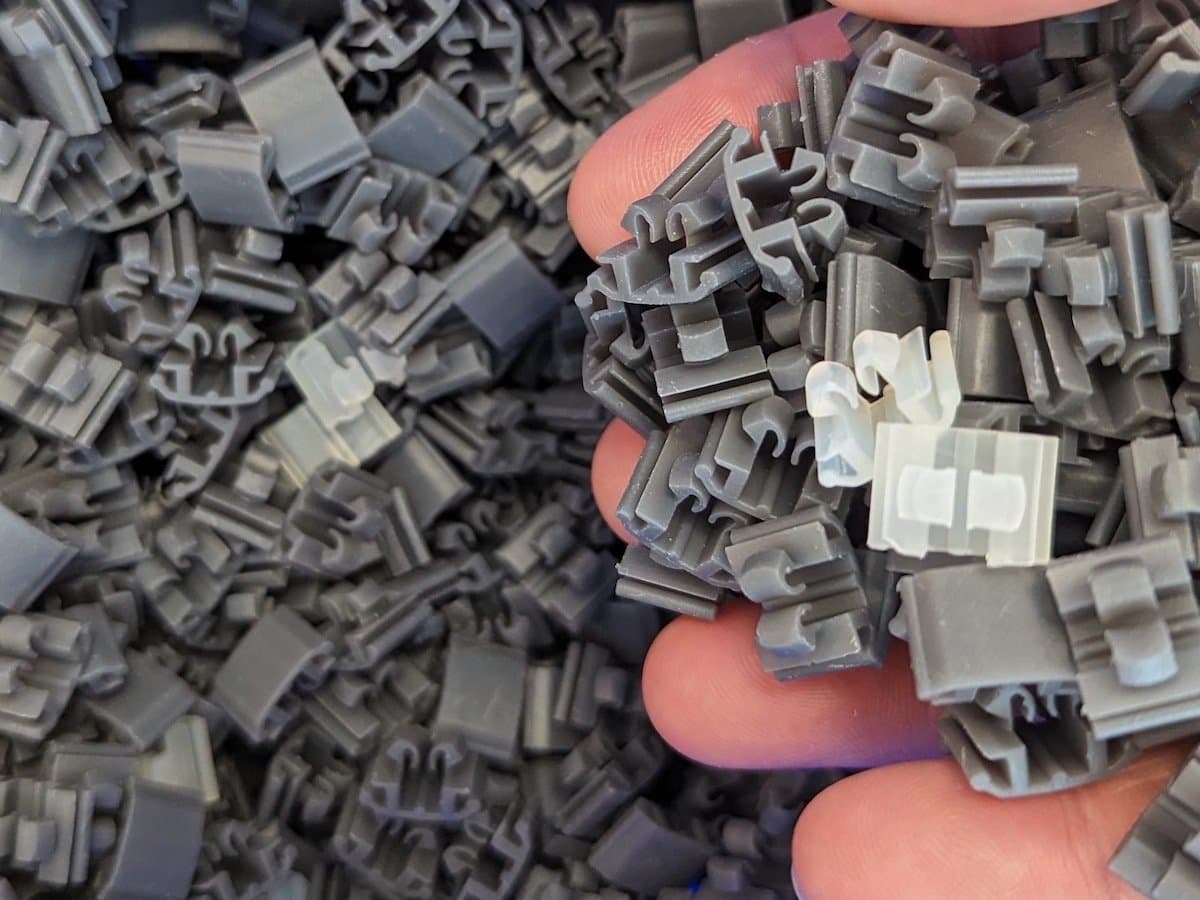
La Form Auto destaca a la hora de ayudar a Mackart a fabricar cientos o miles de piezas pequeñas, como estos remaches para el mercado de los coches clásicos.
Mackart se ha tomado el tiempo de optimizar sus procesos y asegurarse de que ofrecen diseños de alta calidad para sus clientes en un amplio abanico de sectores. Lo han conseguido utilizando diversas tecnologías que se complementan entre sí y aprovechando distintos métodos y materiales de impresión 3D en los casos en los que han sido los más apropiados.
Incorporar la Form Auto ha aumentado su capacidad y añadido un nuevo turno a su jornada en el que los trabajadores no tienen que estar presentes. A partir de esto, McCarthy confía en que al crecer la demanda, la empresa pueda usar su parque de impresoras 3D para acceder a nuevos sectores y acometer nuevas aplicaciones con la misma precisión y rendimiento que convierten a Mackart en un socio fiable para algunos de los mejores equipos de Fórmula 1 del mundo.
Estamos especialmente agradecidos a nuestro socio revendedor de Reino Unido Solid Print3D por sus consejos y su apoyo a Mackart con las soluciones de impresión 3D de Formlabs. Si quieres saber más acerca de las aplicaciones de la impresión 3D en el sector de la automoción, visita nuestra página de recursos o habla con nuestro equipo sobre tu aplicación específica.