El futuro de las piezas de atrezo y los efectos de maquillaje: impresión en 3D de grandes piezas de atrezo y moldes con la Form 3L para la 2.ª temporada de Raised by Wolves
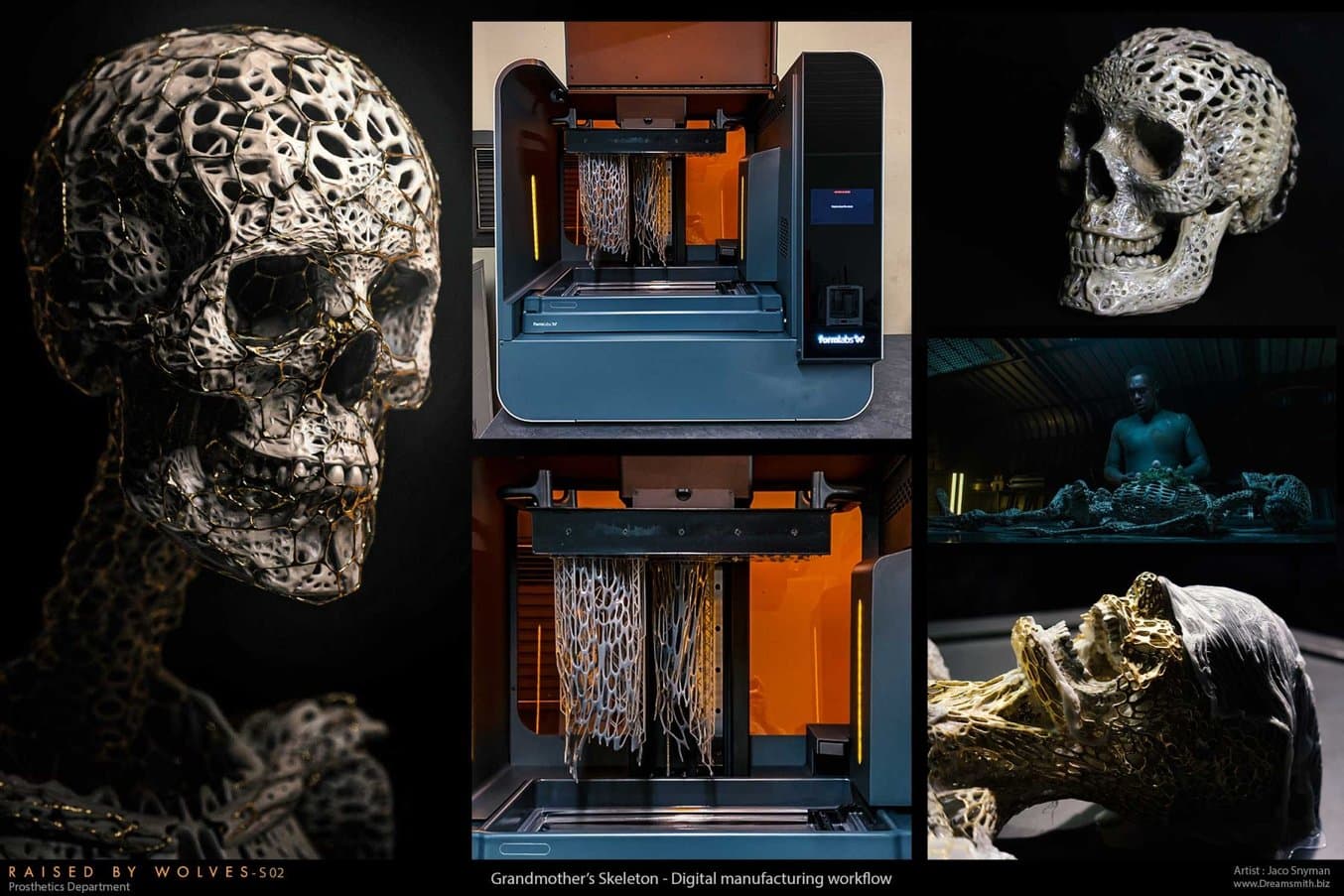
En 2020, entrevistamos a Jaco Snyman, fundador de la galardonada empresa de fabricación de piezas de atrezo y efectos de maquillaje con prótesis reales Dreamsmith Studio y jefe de diseño de prótesis de la serie de ciencia ficción Raised by Wolves. En su momento, Snyman nos habló de su proceso de trabajo para producir moldes impresos en 3D y modelos de uso final que se mostraron en pantalla en la primera temporada de la serie.
La serie de HBO Max, creada por Aaron Guzikowski y producida por Ridley Scott, gira en torno de dos androides, Padre y Madre, que tienen la misión de criar niños humanos. La serie estrenó su segunda temporada en febrero de 2022 con una gama aún más amplia de piezas de atrezo y prótesis fabricadas con la ayuda de la impresión 3D, esta vez impresas con una flota de impresoras de estereolitografía (SLA) de gran formato Form 3L.
Avance de la 2.ª temporada de Raised By Wolves
En este artículo, escrito por Snyman y su equipo, nos muestran cómo Dreamsmith utilizó la Form 3L para imprimir grandes moldes y modelos para dar vida a alienígenas, androides y otras piezas de atrezo del mundo apocalíptico de Raised by Wolves.
Revolucionando las piezas de atrezo y los efectos de maquillaje: cinco casos de estudio de la 2.ª temporada de Raised by Wolves
La impresión 3D promete ser una tecnología revolucionaria en el mundo cinematográfico, caracterizado por su ritmo frenético y dependencia de los plazos de entrega. Además de disfrutar de todas las ventajas de un proceso de trabajo digital, reproduciendo de forma fiable y precisa esos activos en el mundo físico, permite que los trabajadores se centren en tareas más creativas. Sobre el papel, esto es totalmente revolucionario y estábamos deseando incorporar la impresión 3D a nuestro proceso de trabajo. Desafortunadamente, como pasa con todas las tecnologías emergentes, hubo algunas dificultades iniciales.
Para que la impresión 3D nos funcionara, necesitábamos tres cosas concretas. Para empezar, necesitábamos que igualara los detalles que podemos conseguir con las técnicas tradicionales. También era necesario reproducir estos detalles a una escala lo suficientemente grande como para ser útil: un volumen de impresión lo suficientemente grande como para que entrara una cabeza humana completa, por ejemplo. Por último, tenía que ser fiable, precisa y fácil de usar. Con plazos cortos y limitaciones de presupuesto, los fallos y la resolución de problemas debían reducirse al mínimo.
Era extremadamente difícil encontrar una impresora que cumpliera todos estos requisitos y no fuera excesivamente cara. Las impresoras del mercado que podían conseguirlo todo a un precio asequible resultaban ser poco fiables, y las opciones más fiables eran incapaces de alcanzar un buen nivel de detalle a una escala útil. Tras unos años de prueba y error, nos resignamos a que, por el momento, la impresión 3D solo sería una herramienta más en nuestro arsenal y no la revolución absoluta que esperábamos. Entonces llegó la Form 3L.
La Form 3L cumplía todos los requisitos. Presenta un inmenso volumen de impresión de 33,5 × 20,0 × 30 cm con una resolución de 25 micras y cuenta con el apoyo del software PreForm, que hace que el paquete sea extremadamente fiable y fácil de usar. Todo esto, unido a la impresionante variedad de resinas, hace que la Form 3L sea una herramienta increíblemente potente, una herramienta que ha revolucionado completamente nuestro proceso de trabajo en dos cortos años.
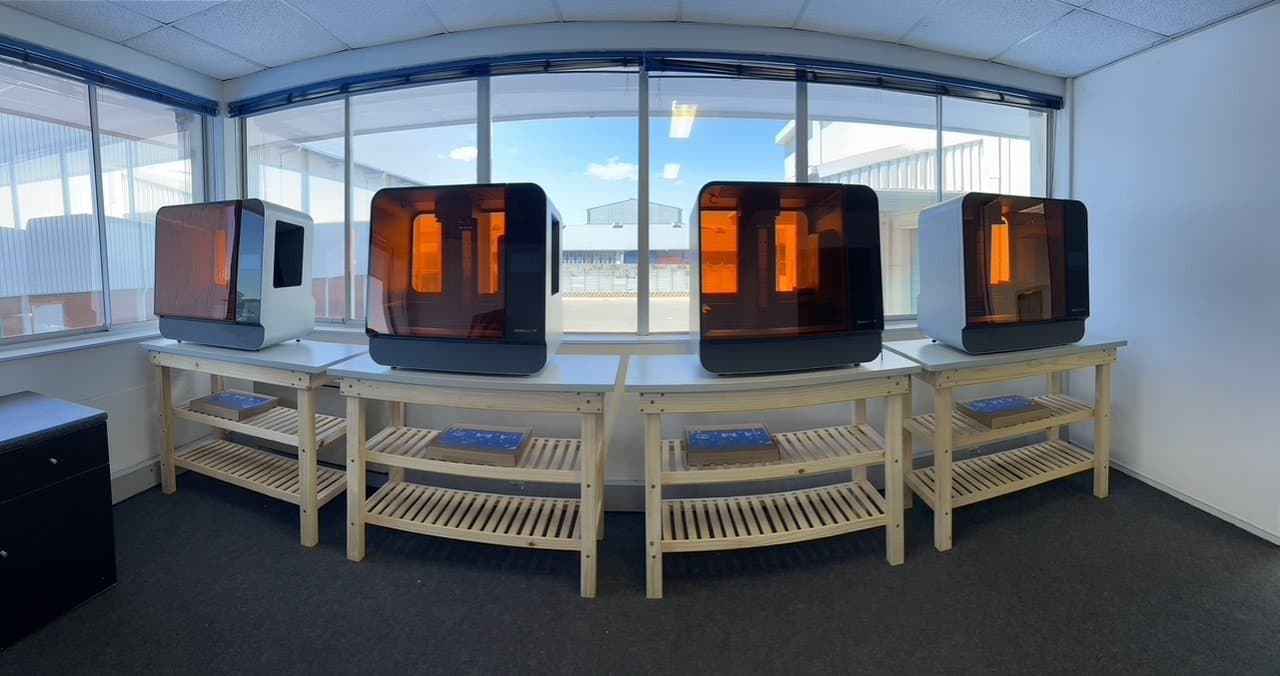
Impresoras 3D Form 3L en el espacio de trabajo de Dreamsmith en Cape Town (Sudáfrica).
Es difícil explicar exactamente el punto de inflexión que supone la Form 3L sin entrar en detalles sobre cómo ha afectado a nuestra forma de abordar los problemas creativos. En los ejemplos siguientes, desglosaremos nuestro proceso de trabajo y, con suerte, aclararemos por qué creemos que esta impresora concreta es tan revolucionaria en nuestro sector.
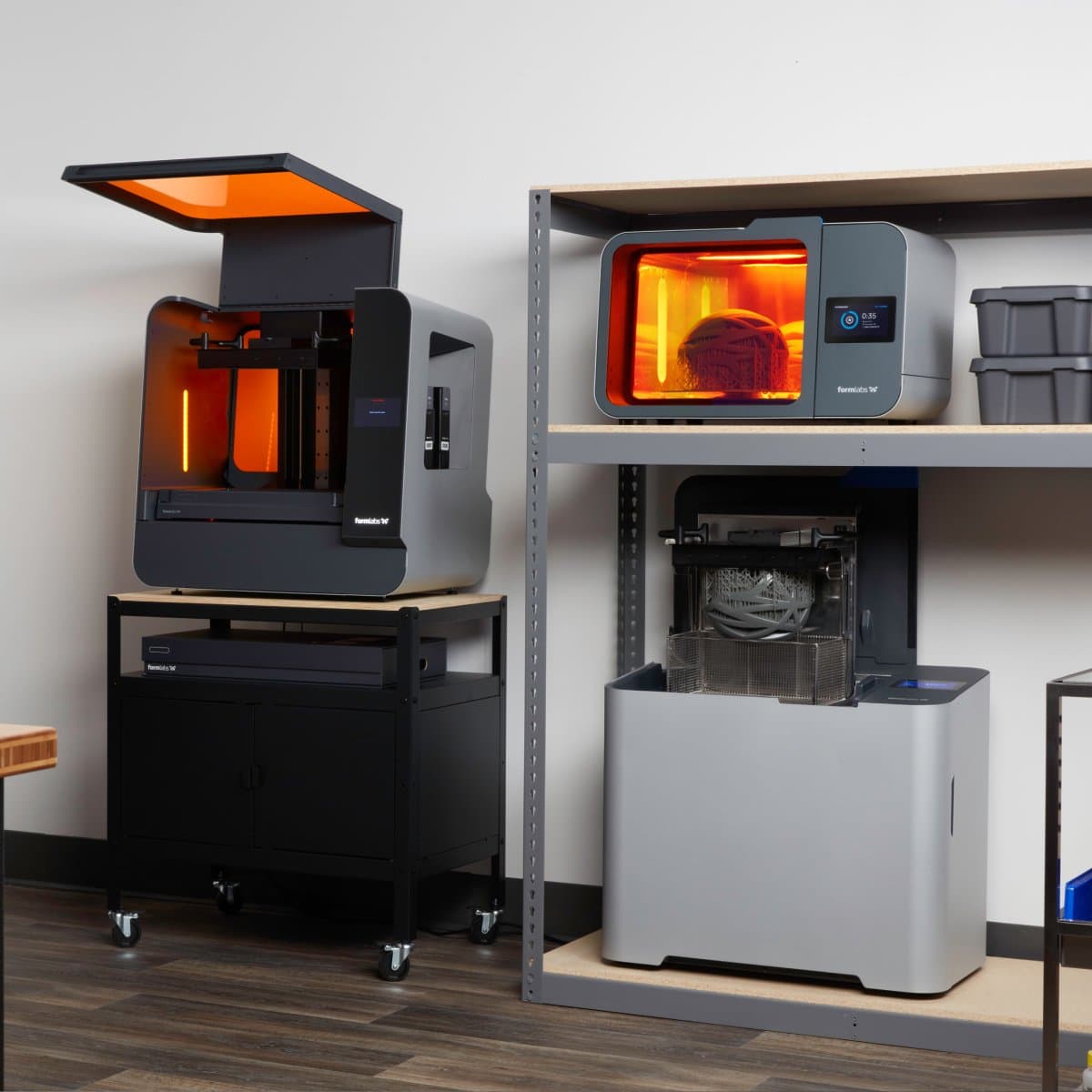
Demostración en directo de la impresora 3D de gran formato Form 3L
¿Quieres saber más acerca del ecosistema de la Form 3L y la Form 3BL, así como de las nuevas máquinas de posacabado de gran formato? En esta demostración, Kyle y Chris explicarán cómo realizar el proceso de trabajo completo con la Form 3L, incluido el posacabado.
N.º 1: Sustitución del molde real: maniquí de réplica de actriz
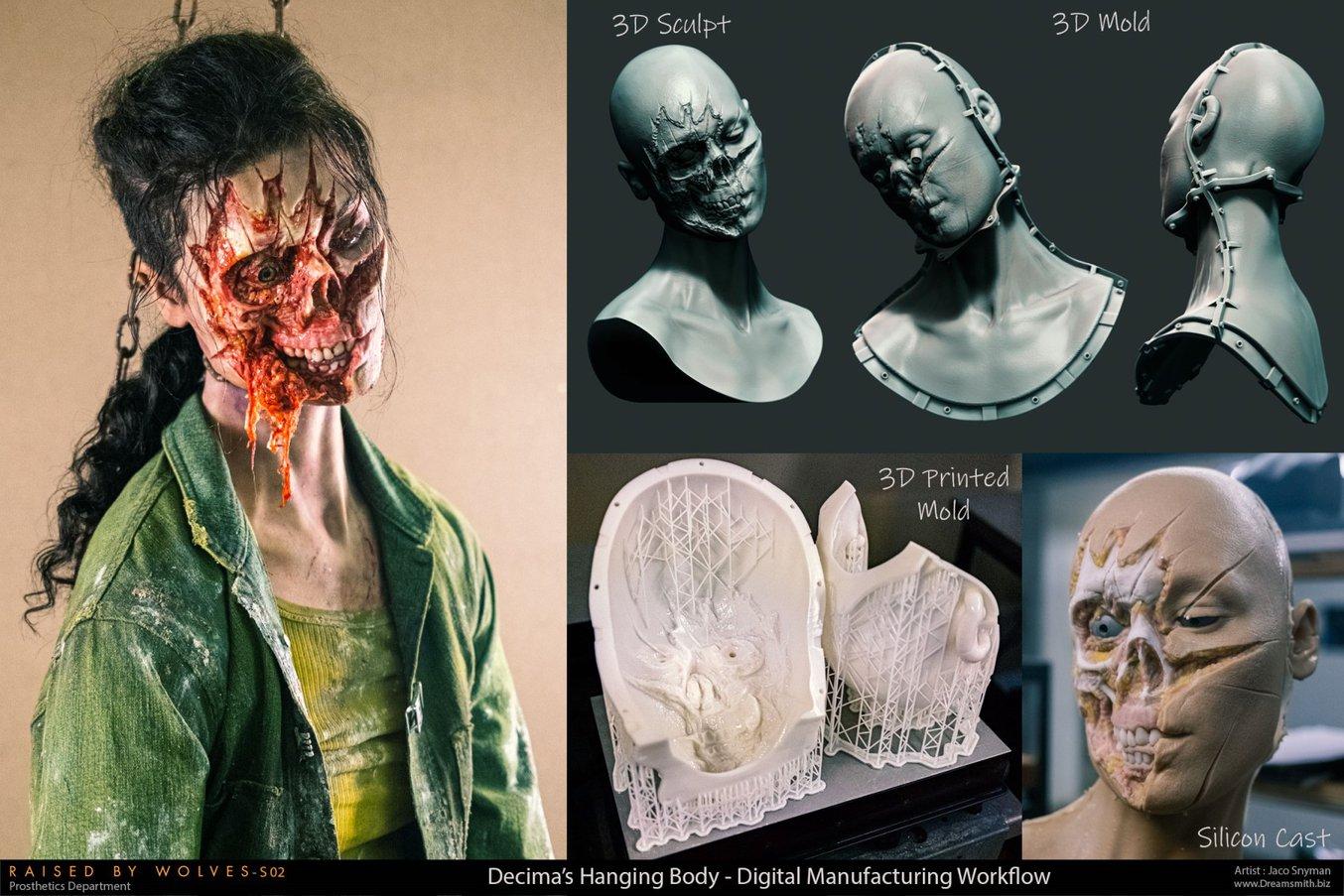
Realización de una réplica de silicona hiperrealista del rostro de una actriz, con moldes diseñados digitalmente e impresos en 3D en la Form 3L con la Rigid 10K Resin.
En este ejemplo, se nos encargó crear una réplica de silicona hiperrealista del cuerpo de una actriz. El problema era que tenía que estar colgada del cuello sin la mitad de la cara.
Siguiendo el modo tradicional, haríamos un molde real de silicona de la actriz cubriendo la cara de esta con silicona y vendas de yeso para crear un molde desechable de su rostro. A partir de este molde real, crearíamos un molde de arcilla sobre el que esculpiríamos a mano el resto de los detalles necesarios para la escena. En este caso, esto significaba alargar su cuello y eliminar partes de su cara.
Esta escultura de arcilla se moldearía después con resina epoxi y fibra de vidrio. A partir de este molde final, crearíamos la réplica de silicona definitiva de la cabeza. Habría sido un proceso de tres semanas que habría tenido que estar supervisado por al menos tres artistas y técnicos con experiencia, y la réplica de la cabeza seguiría siendo solo una pieza de silicona en bruto que tenía que pintarse y perforarse minuciosamente para colocar el pelo con el fin de lograr el hiperrealismo necesario. En total, este proceso habría durado aproximadamente un mes de principio a fin.
"La Form 3L puede imprimir todo el molde final de la cabeza con suficiente detalle como para que no se distinga de uno hecho mediante las técnicas tradicionales. Esto nos permitió digitalizar el proceso partiendo de un escaneo 3D muy preciso de la actriz. Evitó el invasivo proceso de escayola, por lo que todo resultó mucho más cómodo para la actriz."
Jaco Snyman, fundador de Dreamsmith Studio
Luego, pudimos utilizar ZBrush para añadir digitalmente otros detalles escultóricos necesarios. El proceso no comprende ninguna parte invasiva ni repetible y sigue siendo totalmente fluido, lo que nos permite hacer grandes cambios creativos con facilidad a medida que recibimos comentarios del director.
Después, diseñamos el molde digital, y el gran volumen de construcción de la Form 3L nos permitió dividir el molde en piezas más grandes para obtener un producto final con menos líneas de convergencia. El molde se imprimió durante la noche y, tras limpiarlo un poco, estuvo listo para procesarse al día siguiente.
Proceso paso a paso
Todo este proceso de trabajo puede realizarlo una sola persona en una fracción del tiempo que se hubiera necesitado en el pasado, lo que permite que los trabajadores se centren en el paso más importante en relación con el valor de la producción final: los toques finales. Este proceso de trabajo de mayor eficacia evita que vayamos apurados en las fases finales del producto, que es algo que casi siempre pasaba debido a lo laborioso que solía ser el proceso de trabajo tradicional.
Con este único ejemplo, es fácil ver por qué la impresión 3D puede ser tan revolucionaria. Podemos trabajar más rápido, ser más productivos y ahorrar en materiales y mano de obra tradicionales. La Form 3L hizo nuestro proceso de trabajo más rápido, más barato y mejor.
N.º 2: Creación de formas complejas: máscara de silicona
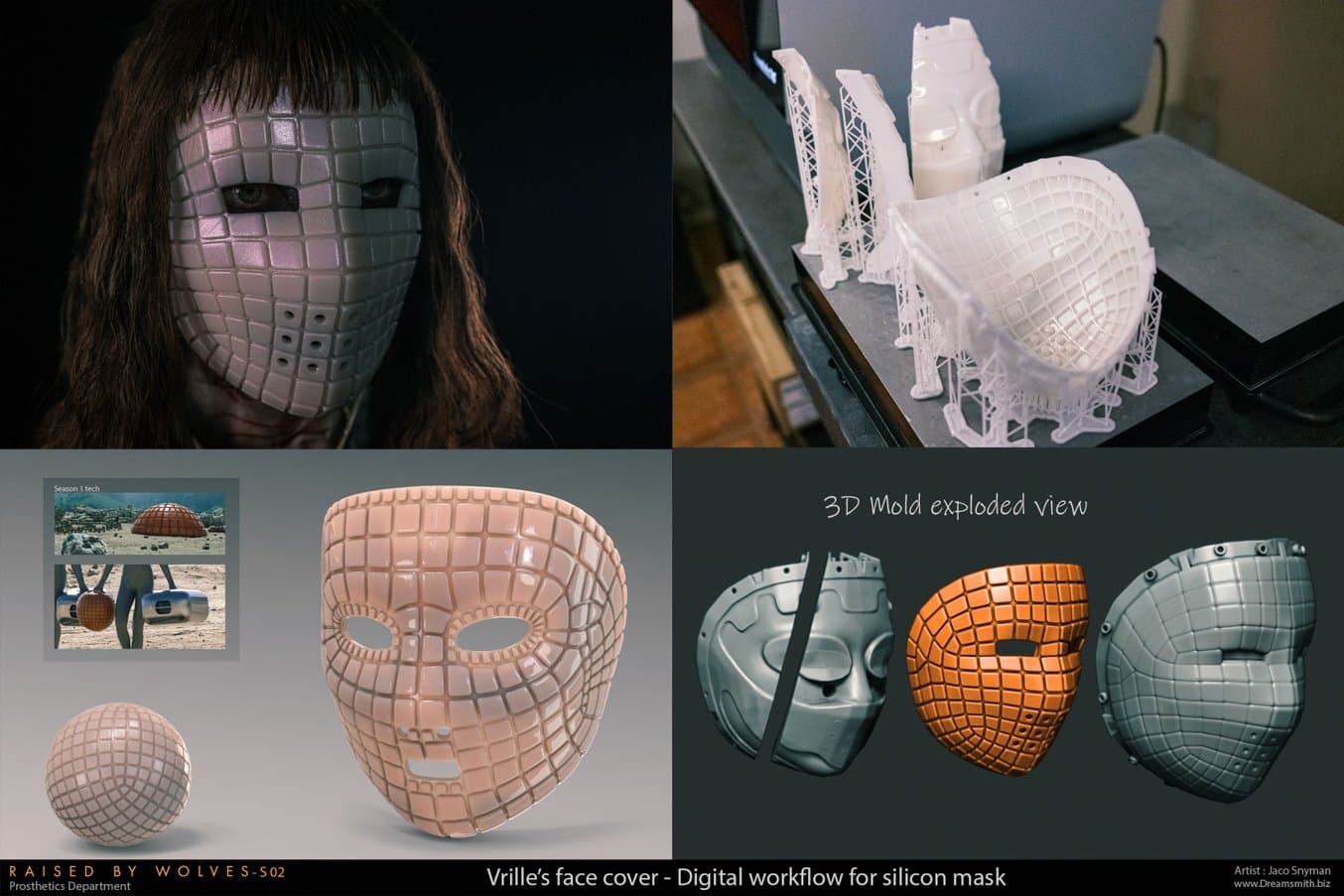
Diseño e impresión de una máscara de forma compleja y alto nivel de detalle con impresión 3D.
Hay ciertos elementos de diseño que se benefician enormemente del diseño asistido por ordenador (CAD). A veces, un encargo es simplemente imposible de crear a mano o es tan poco práctico y requiere tanto tiempo que sería imposible también. En el pasado, habríamos recurrido a la externalización de estas piezas a un taller de mecanizado o sencillamente habríamos rechazado el trabajo por completo. La impresión 3D siempre prometió resolver estos problemas, pero la tecnología tenía que mejorar hasta un punto en el que la calidad de impresión y la asequibilidad estuvieran al mismo nivel.
Para nosotros, la Form 3L supuso esta mejora. Ahora estamos mucho menos limitados por las técnicas de fabricación tradicionales y podemos lograr mucho más en nuestras instalaciones sin tener que recurrir a una costosa externalización. Nuestro mayor obstáculo ahora son los límites de nuestra creatividad ¡y nos encanta que sea así!
En el ejemplo anterior, teníamos un encargo que habría sido muy difícil de realizar sin la impresión 3D. La máscara de Vrille presentaba dos problemas singulares que resolver.
En primer lugar, debía combinar detalles orgánicos y geométricos: debía tener una capa exterior prístina de formas geométricas basada en la forma orgánica y asimétrica del rostro de la actriz.
En segundo lugar, había un problema de materiales: la máscara final tenía que ser de silicona, lo que requería la necesidad de un molde, ya que no podemos imprimir en silicona.
Proceso paso a paso
Este encargo concreto constituye un ejemplo de la necesidad de combinar distintos avances tecnológicos. Necesitábamos un escaneo 3D de la actriz, el software para crear el activo digital y diseñar el molde digital, y una impresora 3D lo suficientemente grande y precisa para imprimir el molde.
Si observas el desglose del progreso anterior, verás que pudimos encajar todo el molde en una sola base de impresión, lo que redujo drásticamente el tiempo de impresión. Los avances en los materiales de impresión también resultaron muy importantes. Al imprimir con la Rigid 10K Resin de Formlabs, el molde final fue extremadamente preciso, lo que dio como resultado la máscara final casi perfecta que se muestra más arriba.
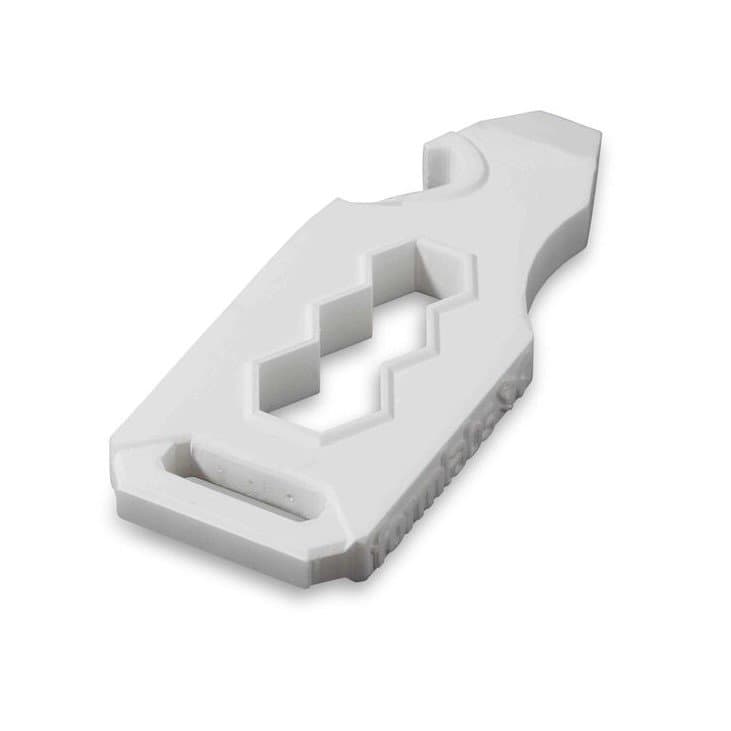
Solicita una muestra de impresión 3D con la Rigid 10K Resin
Experimenta la calidad de Formlabs de primera mano. Enviaremos una pieza de muestra gratuita a tu lugar de trabajo.
N.º 3: Impresión de formas imposibles: esqueleto biomecánico
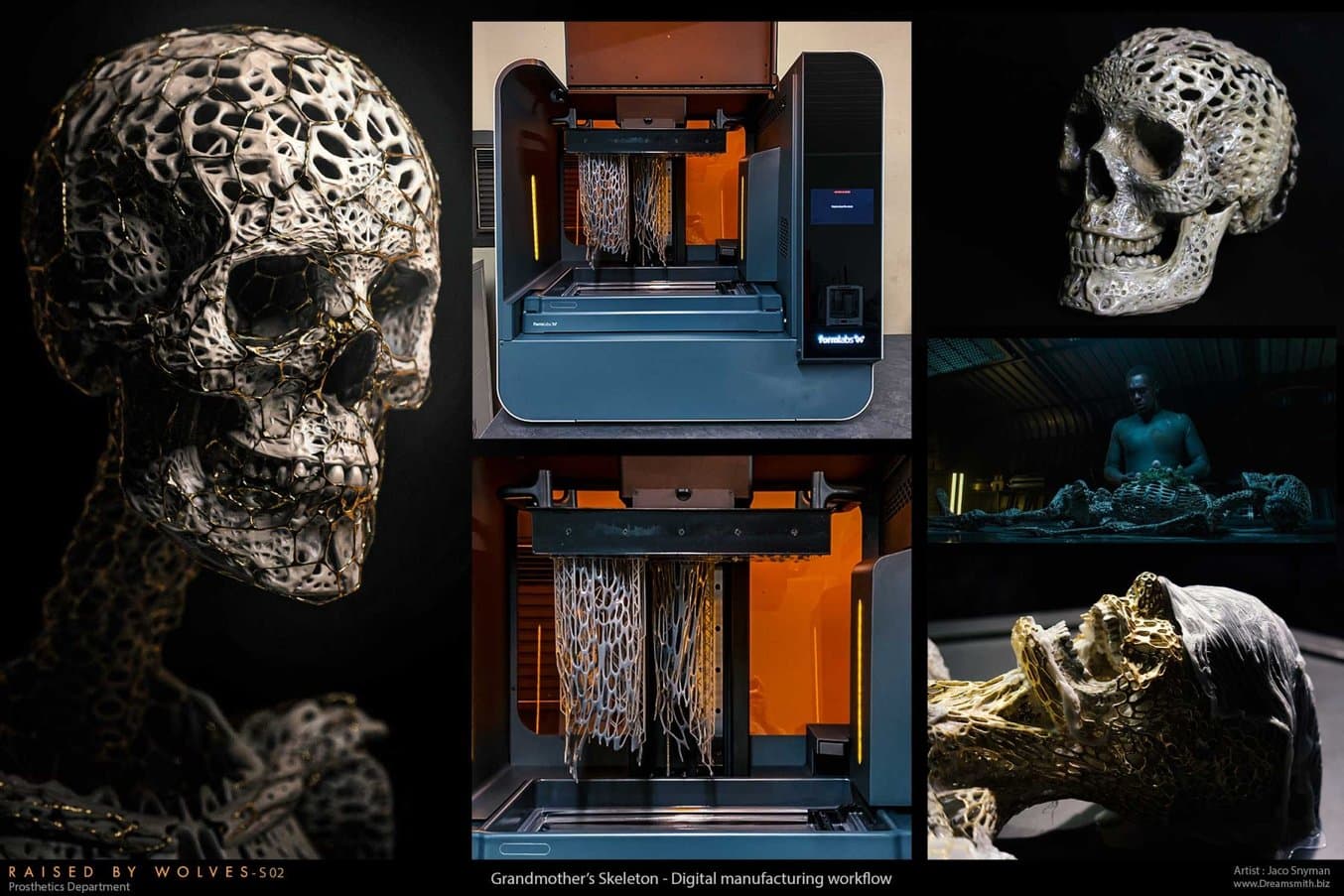
Forma orgánica de un esqueleto biomecánico de gran tamaño, impresa en 3D en la Form 3L.
Algunos diseños son más fáciles de hacer con la impresión 3D y otros solo pueden hacerse con ella.
Por ejemplo, el diseño anterior es de un esqueleto biomecánico de tamaño real. Una pieza de atrezo intrincadamente detallada con una fluidez geométrica que habría sido terriblemente difícil de esculpir en arcilla y básicamente imposible de moldear con las técnicas tradicionales.
El esqueleto de la Abuela es un ejemplo perfecto de un diseño creado únicamente porque podemos imprimirlo en 3D. Hace tiempo que se imprimen formas imposibles y engranajes entrelazados, pero necesitábamos ser precisos a una escala útil. ¡Necesitábamos un esqueleto de tamaño real! El volumen de impresión de la Form 3L nos permitió imprimir toda la pieza de atrezo en trozos prácticos a alta resolución.
Proceso paso a paso
Esta es una pieza de atrezo que habría sido práctica y económicamente imposible de crear sin el uso de la Form 3L.
N.º 4: Impresión rápida de piezas grandes: maniquí de réplica de actriz
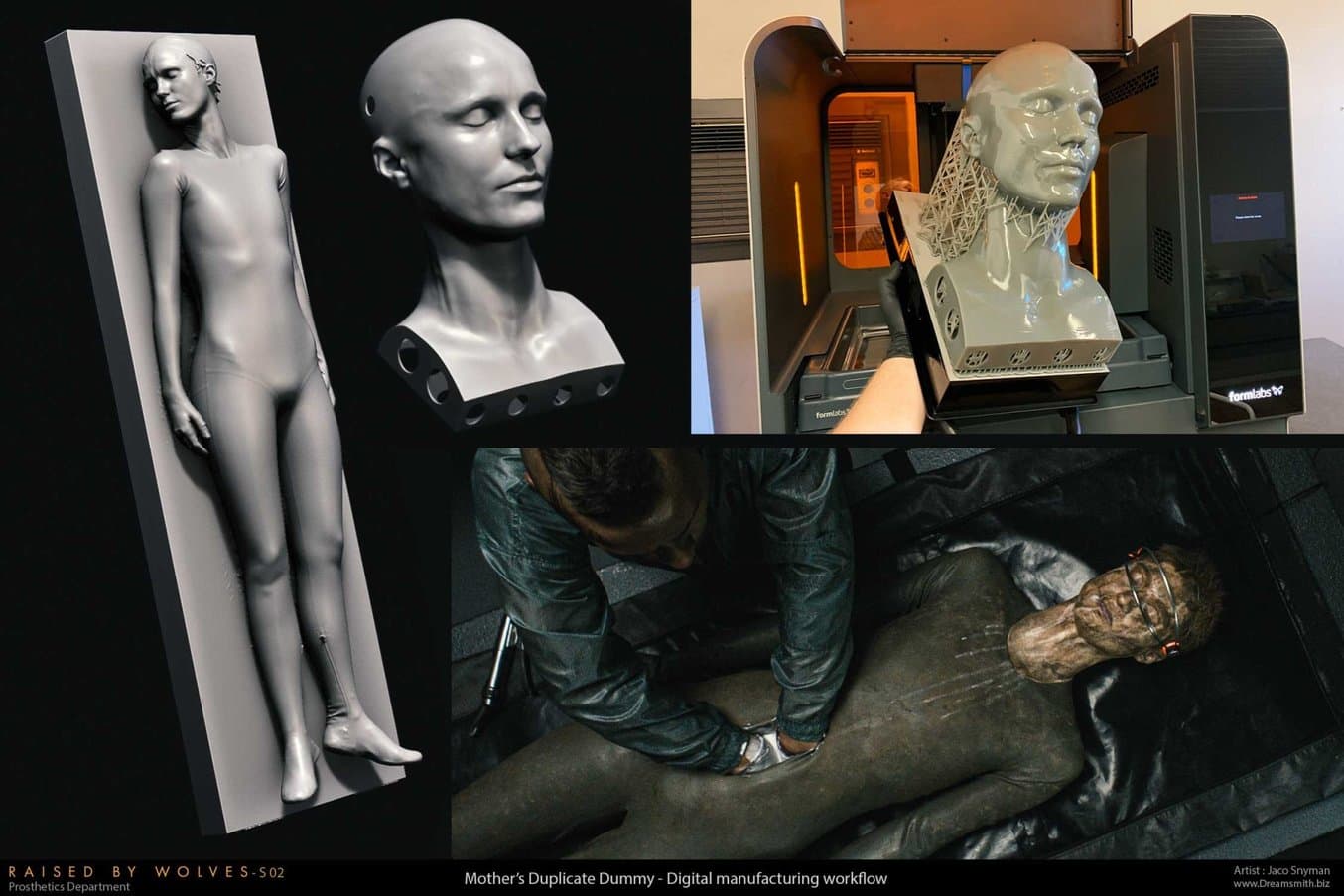
Cabeza de la actriz Amanda Collin, impresa en 3D en 12 horas con la Draft Resin en la Form 3L.
El tamaño es especialmente importante cuando se trata del volumen de impresión. Uno de nuestros requisitos al elegir una impresora era que debía ser capaz de imprimir una cabeza humana entera. Cada vez que divides algo en piezas más pequeñas estás aumentando el trabajo en el proceso de acabado. Cada unión o línea de convergencia del molde debe acabarse y retexturizarse con mucho cuidado para crear la pieza de atrezo final perfecta.
El maniquí de réplica de la Abuela mostrado anteriormente es el ejemplo perfecto. Pudimos imprimir su cabeza de una sola vez en la Form 3L, lo que nos dejó una réplica perfecta en resina del rostro de la actriz que pudimos pintar minuciosamente para lograr el máximo parecido.
Antes, este proceso habría llevado mucho tiempo, ya que implicaba un molde real, e incorporaba moldes de epoxi hechos a mano y un molde de silicona final. A modo de comparación, antes de tener acceso a la Form 3L, tuvimos que crear otro maniquí de réplica que llevó a todo nuestro equipo un mes de trabajo. Esta vez, pudimos imprimir el rostro de Madre y crear su cuerpo con mecanizado CNC en una semana, y obtuvimos la pieza de atrezo final pintada y lista para el rodaje en menos de dos semanas.
Proceso paso a paso
Es importante señalar que esta pieza de atrezo no habría aguantado un primer plano, se hizo especialmente para la toma final mostrada anteriormente. Esto nos permitió utilizar la pieza de resina impresa directamente desde la impresora; era lo suficientemente detallada como para mantenerse a esta distancia. Esto nos permitió ahorrar mucho tiempo, materiales y dinero.
Con las técnicas de moldeo y fundición tradicionales, este maniquí habría tardado lo mismo en crearse, independientemente de los detalles finales del producto acabado. La Form 3L hizo posible nuestro planteamiento de detalle medio: pudimos hacer una pieza de atrezo que respondiera especialmente a las necesidades de la escena. Esto nos permite prometer más en menos tiempo y a menor precio, algo de incalculable valor en el sector cinematográfico, donde los presupuestos son tan ajustados.
N.º 5: Procesos de trabajo híbridos: maquillaje del bioataque de Paul
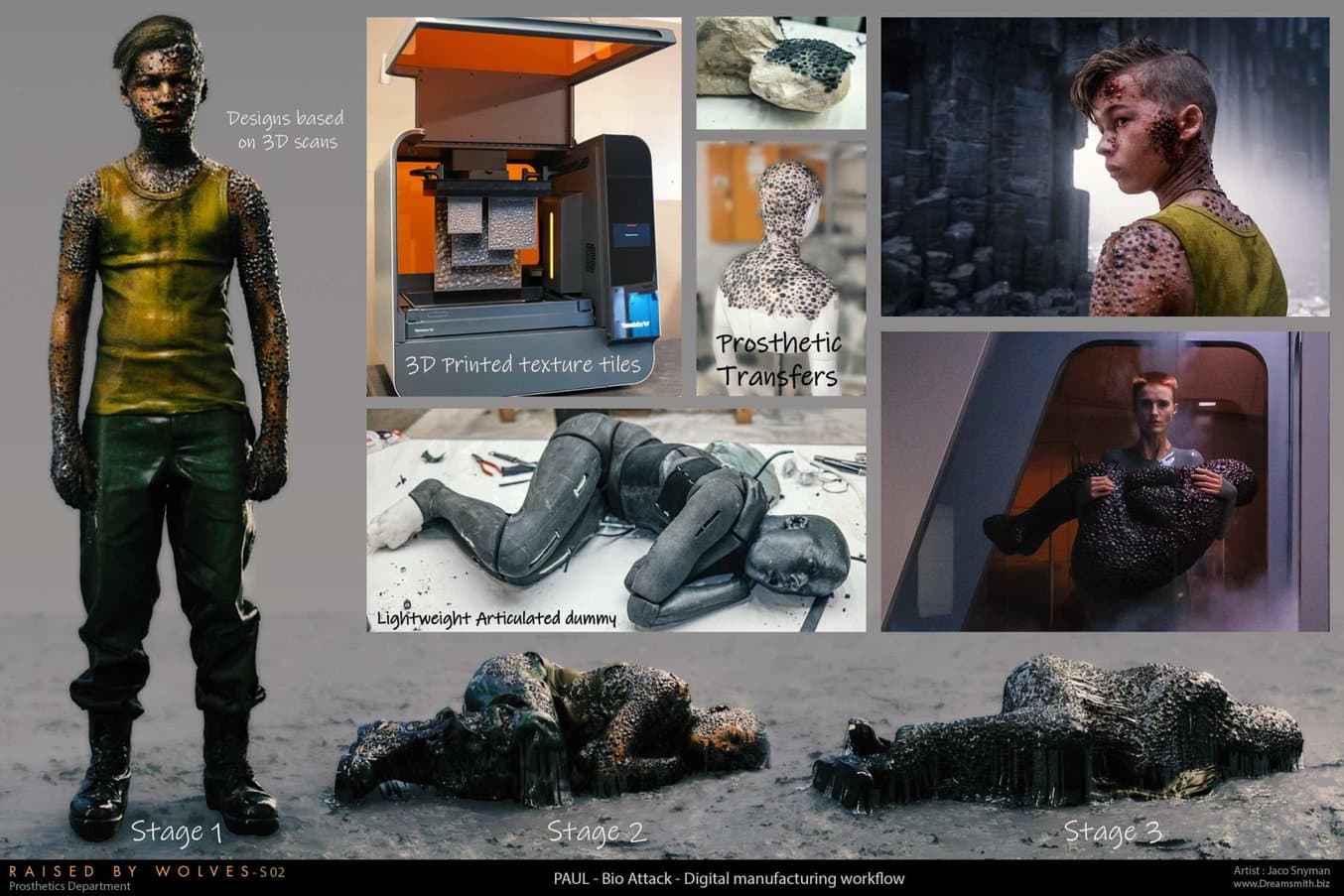
Combinación de cuadrados texturizados de impresión 3D con técnicas convencionales de fabricación de maniquíes.
La impresión 3D no siempre tiene que sustituir por completo las técnicas convencionales. Nos ha gustado tener la Form 3L a nuestra disposición y poder idear nuevos procesos de trabajo híbridos que aprovechan las ventajas de ambos métodos.
La crisálida de Paul ejemplifica cómo combinamos las técnicas de fabricación tradicionales y la impresión 3D para crear algo que habría sido muy difícil con cualquiera de las dos disciplinas por separado.
Jaco Snyman, fundador de Dreamsmith Studio
La crisálida requería una piel escamosa maleable que pudiera moverse con el maniquí articulado en su interior. Normalmente, esto requeriría un molde muy grande y caro, pero como las escamas son orgánicas y se pueden encajar como un puzle, tenía sentido fabricar la piel sobre el maniquí a mano, lo que eliminaba la necesidad de un molde caro.
No obstante, necesitaríamos una gran cantidad de cuadrados de textura escamosa para armar la crisálida. Para esta etapa del proceso, la impresión 3D era la solución evidente por su capacidad de reproducir detalles complejos con precisión y rapidez. Imprimimos una serie de moldes texturizados a escala plana de diferentes tamaños que pudimos usar para fundir cuadrados escamados de silicona. Luego, utilizamos los cuadrados de silicona para fabricar la crisálida.
Proceso paso a paso
La Form 3L con una variedad de resinas hace posible este tipo de procesos de trabajo híbridos y es una herramienta inmensamente poderosa cuando tenemos que resolver los problemas cotidianos propios del sector cinematográfico.
Detrás de las escenas de la 2.ª temporada de Raised By Wolves: conclusiones de Dreamsmith
La 2.ª temporada de Raised By Wolves fue un momento decisivo para nosotros: fue la primera vez que recurrimos considerablemente a los procesos de trabajo de impresión 3D. Muchos de los ejemplos anteriores solo se consideraron en teoría antes de que los intentáramos dentro del plazo.
Este suele ser un territorio plagado de errores y consecuencias imprevistas y, aunque nos encontramos con muchos de ambos, nuestra experiencia general con la Form 3L fue ejemplar y nuestra confianza en el equipo aumentó con cada proyecto satisfactorio.
La fiabilidad de la plataforma nos demostró que podemos seguir avanzando y aplicar lo que hemos aprendido a proyectos más grandes y exigentes. Desde entonces, hemos incorporado cuatro Form 3L a nuestro parque y, gracias a este aumento de la capacidad, hemos alcanzado un nivel de productividad que antes hubiéramos considerado imposible.
Este proceso de trabajo completamente digital nos permite trabajar a distancia. Podemos escanear, diseñar, esculpir y moldear en 3D prótesis de personajes completos y enviarlas a cualquier parte del mundo sin necesidad de que nuestro equipo se desplace físicamente ni que el cliente tenga que esperar a que lleguen los frágiles paquetes. Si quieres saber más sobre este servicio, no dudes en escribirnos a [email protected].
A partir de ahí, hemos aprovechado la experiencia que adquirimos trabajando en la 2.ª temporada de Raised By Wolves y, cuando llegue el momento, estaremos encantados de compartir algunas de las novedades en las que hemos estado trabajando desde entonces. Mirando ahora estos primeros experimentos y viendo lo mucho que dependemos actualmente de la impresión 3D, es evidente que la Form 3L ha revolucionado de verdad nuestra forma de trabajar.
Sigue a Dreamsmith en Instagram (@dreamsmith_) para estar al tanto de sus últimas producciones.
Gracias en especial a Jaco Snyman y Mathew Howard-Tripp por escribir este artículo y a nuestro socio comercial sudafricano BuildVolume.
Un vistazo al futuro: un proceso de diseño completamente digital para prótesis de maquillaje
Tras adoptar la Form 3L y experimentar con diversos materiales del catálogo de resinas de Formlabs, Snyman y su equipo han descifrado las claves para hacer moldes de maquillaje protésico para su actual proyecto secreto, que saldrá a la luz en 2023.
Pasaron a un proceso completamente digital para hacer efectos de maquillaje con prótesis, empezando por un escaneo 3D del actor, esculpiendo digitalmente el maquillaje protésico y empleando una técnica híbrida de fundición de silicona con una fina capa de silicona intercalada entre una cáscara impresa en 3D y una base corregida impresa en 3D.
Afirman que este método está revolucionando completamente su forma de trabajar, ya que ahora pueden producir prótesis de maquillaje en una sexta parte del tiempo y a un precio asequible. Otra de las ventajas es la posibilidad de escanear los rostros de los actores desde cualquier lugar del mundo, lo que facilita el trabajo a distancia antes de los apretados planes de rodaje.
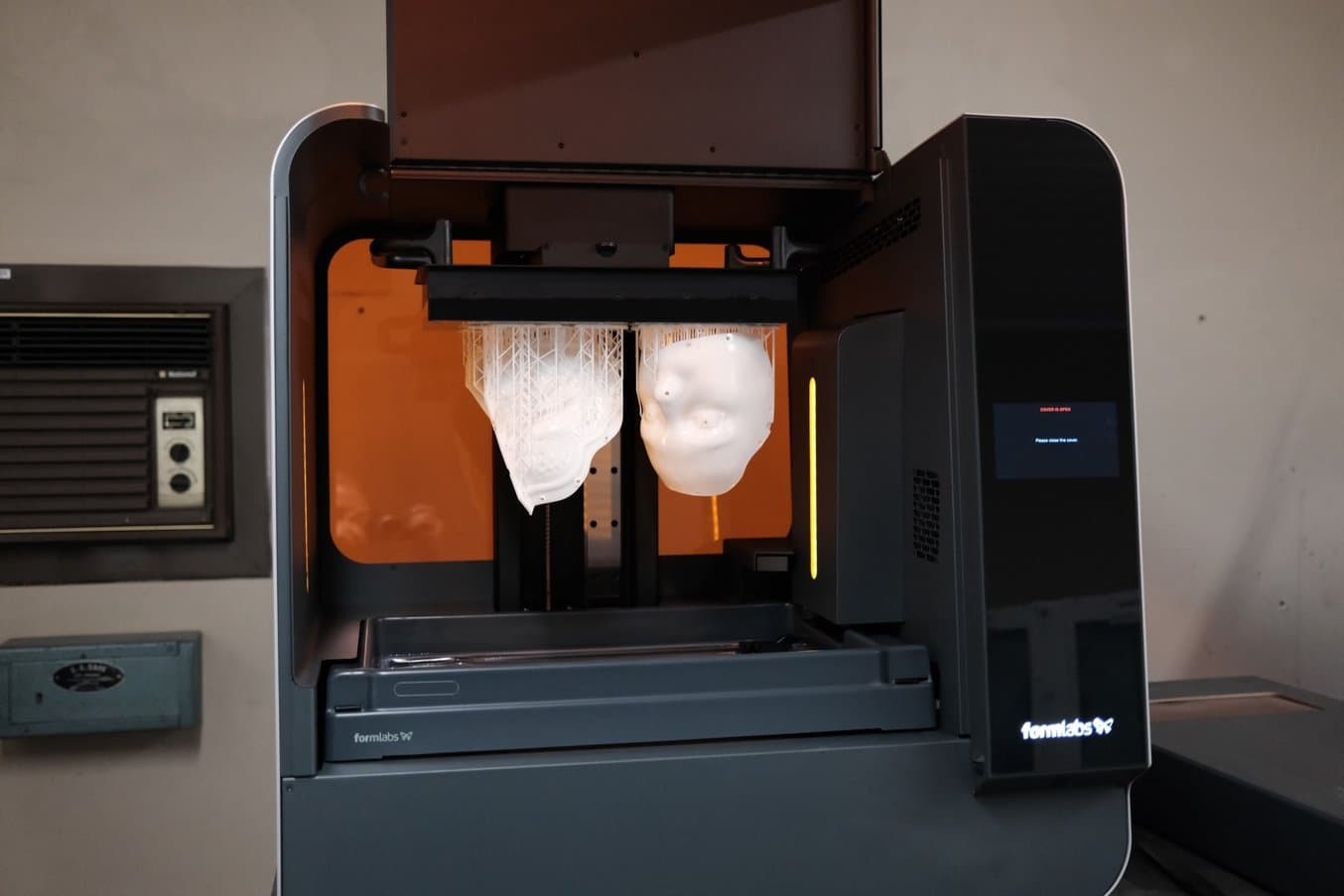
Experimentos con la Rigid 10K Resin y la impresora 3D Form 3L para hacer moldes de prótesis de maquillaje.
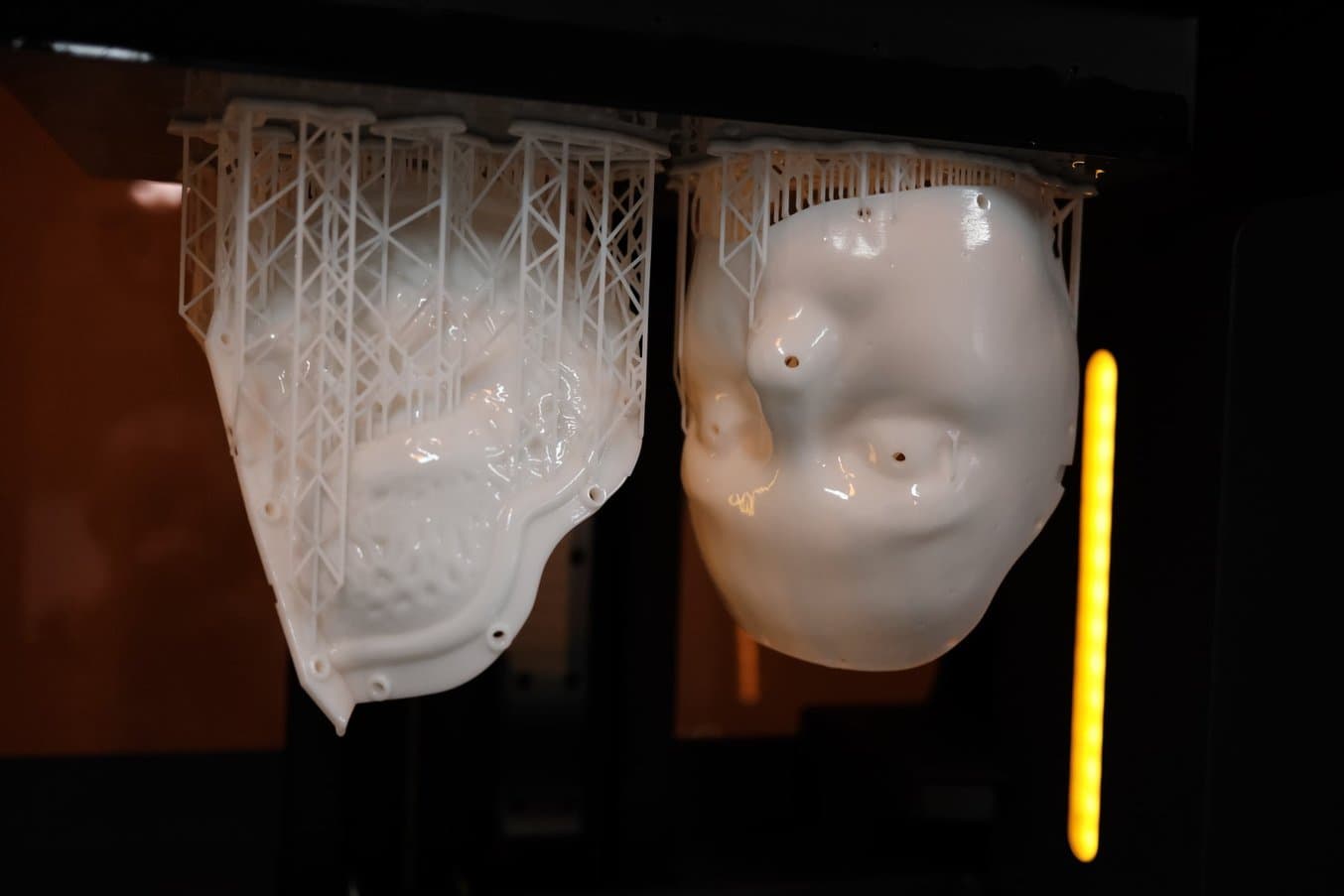
Snyman y su equipo trabajan sin descanso para descubrir todas las posibilidades de la impresión 3D SLA en la industria del entretenimiento. El equipo de Dreamsmith está encantado de seguir usando la impresión 3D en su proceso de trabajo en futuros proyectos. Permanece atento para ver sus próximos trabajos con la Form 3L.