La resina antiestática permite a la Fuse Sift ir desde los prototipos hasta la producción
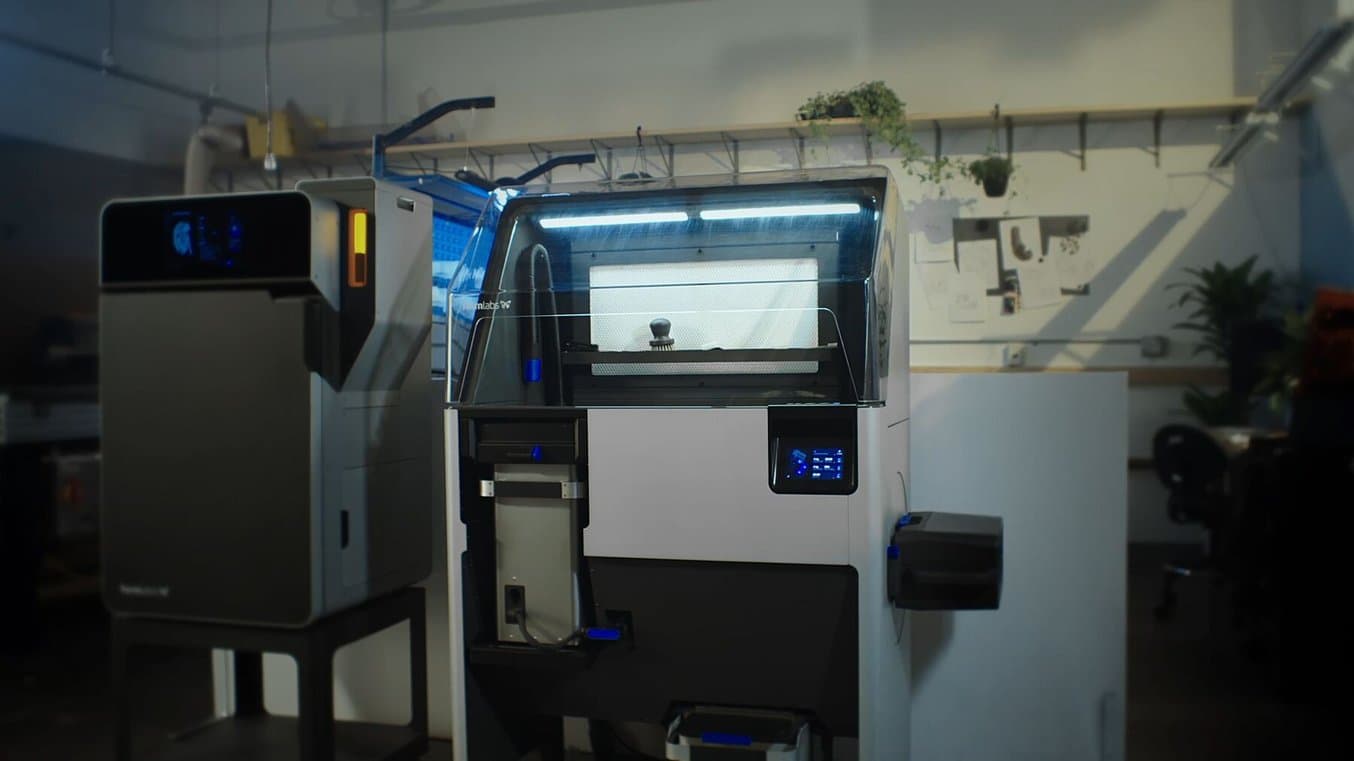
La Fuse 1 es actualmente la solución de sinterizado selectivo por láser (SLS) más vendida del mercado, pero el camino hasta la producción en serie ha sido largo. Crear la Fuse Sift, la máquina de posacabado y reciclaje de polvo que optimiza el proceso de trabajo para SLS, fue un nuevo desafío para el equipo de ingeniería de Formlabs e hicieron falta soluciones y enfoques únicos para conseguirlo.
Uno de esos desafíos surgió al diseñar piezas para el sistema de contención del polvo en los prototipos finales de la Fuse Sift. Los subsistemas de contención del polvo de impresión debían disipar la electricidad estática que generaban las partículas de polvo en movimiento, pero no podía ser excesivamente caro ni lento de fabricar.
Descubre cómo el equipo de desarrollo pudo crear prototipos para piezas de la Fuse Sift de forma rápida y económica con una resina antiestática, lo que permite al equipo enviar unidades de prototipo a los testers de productos en fase beta.
El desarrollo de un proceso de trabajo completo para el SLS
En 2019, Formlabs tenía un prototipo potente de impresora SLS, pero sin un sistema de posacabado de alta calidad que lo acompañara, la impresora no podía ser una verdadera solución industrial. La mayoría de los clientes de SLS imprimen piezas de uso final en entornos profesionales y de fabricación, por lo que contener las pequeñas partículas de polvo tiene una importancia fundamental para mantener el espacio de trabajo seguro y limpio.
Para abordar este problema, el equipo de la Fuse 1 empezó a trabajar en la Fuse Sift, una estación de recuperación y reciclado del polvo que procesara las piezas salidas de la impresora Fuse 1. El objetivo de la Fuse Sift era crear una solución integral con la que optimizar el proceso de trabajo de la impresión SLS. En 2019, los prototipos de la Fuse 1 y la Fuse Sift casi estaban listos para ensayos de beta externos, pero el sistema de control del polvo del prototipo de la Fuse Sift no estaba preparado para el lanzamiento.
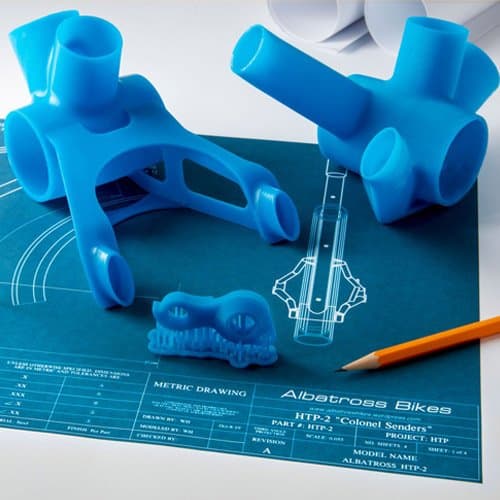
Cómo tener éxito con la creación rápida de prototipos impresos en 3D
Este libro electrónico muestra seis casos reales de empresas que fomentan la innovación y la mejora de
los procesos tradicionales con la impresión 3D.
Cuando completa la impresión, el usuario extrae la cámara de impresión de la impresora Fuse 1 y la introduce en la Fuse Sift, donde las piezas acabadas se pueden separar del bloque de polvo no sinterizado. Se hace pasar el aire por un filtro HEPA en la parte posterior de la superficie de trabajo cubierta para mantener una presión negativa en la zona de trabajo y reducir el riesgo de que el polvo salga de la máquina. El bloque de polvo no sinterizado de la cámara de impresión se filtra y se almacena en una tolva donde se puede dispensar junto con la proporción apropiada de polvo nuevo para rellenar los cartuchos de polvo para la impresión.
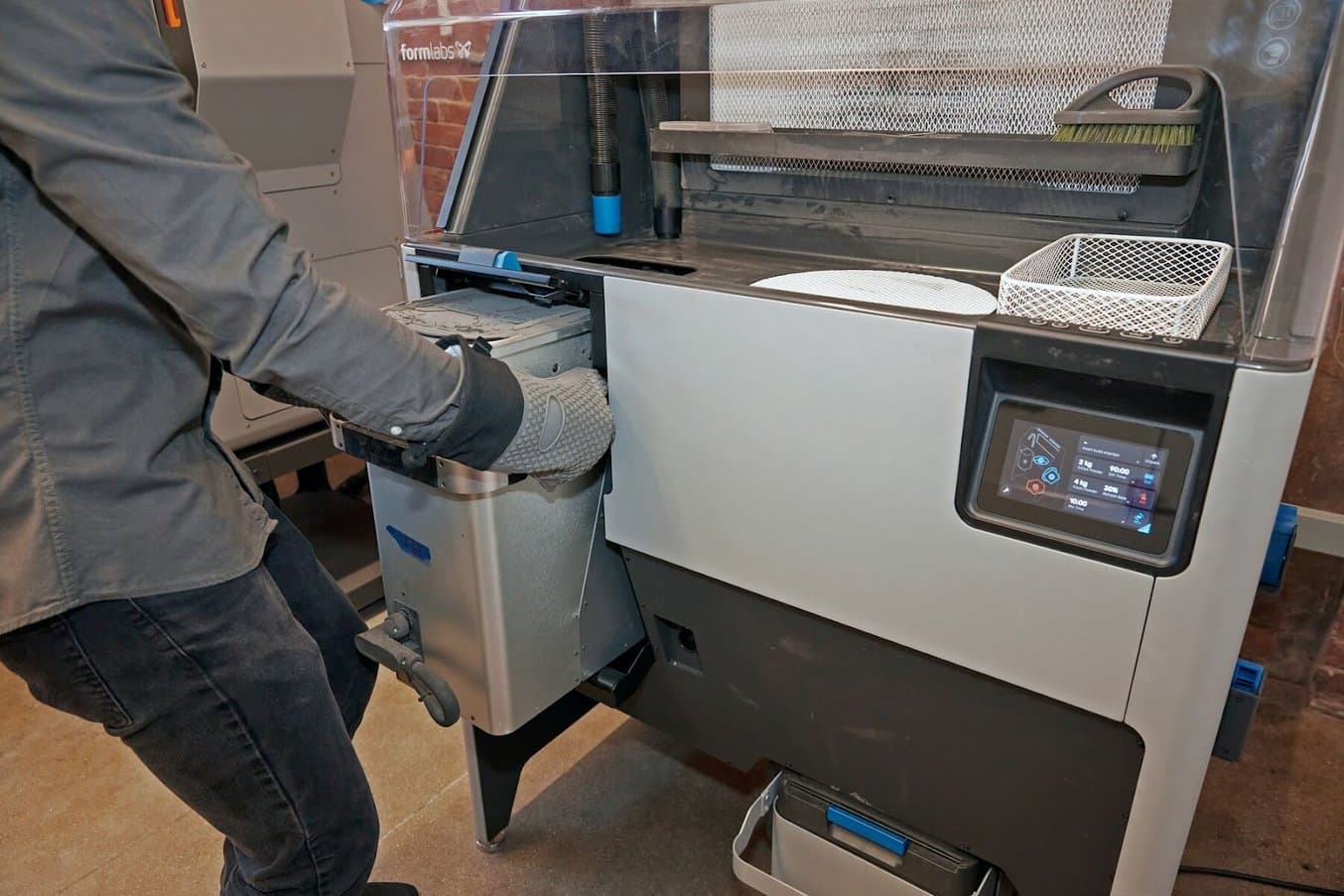
Problemas de control y monitorización del polvo
"Nos habíamos centrado mucho en el filtro HEPA, que era capaz de sacar el polvo de la zona cubierta. Sin embargo, seguía quedando una capa de polvo en el suelo y estábamos intentando averiguar de dónde venía. Grabé un par de vídeos y en ellos se ve que durante la dosificación, un surtidor de polvo de nylon microscópico surge del cartucho; pasada una semana, la Fuse Sift, los cartuchos y el suelo quedaban cubiertos de polvo", explica Larry Cheung, el director de ingeniería mecánica del equipo de la Fuse Sift.
El equipo evaluó un par de opciones, como una cubierta o una falda que envolviera tanto el sistema de dosificación como el nuevo cartucho. Pero el cartucho se debe pesar continuamente durante la dosificación para garantizar una mezcla óptima de polvo nuevo y usado, por lo que cualquier cosa que toque el cartucho afecta al sistema de pesado y no funcionaría.
"Se nos ocurrió que ya que teníamos un aspirador, bien podíamos usarlo para mantenerlo todo limpio. Por eso, empezamos a probar un prototipo con tubos de conexión en Y que fueran desde la superficie de trabajo y el puerto de dosificación hasta el aspirador. Para ver si funcionaba, lo imprimimos con la Draft Resin y lo envolvimos con cinta adhesiva de cobre", explica Cheung.
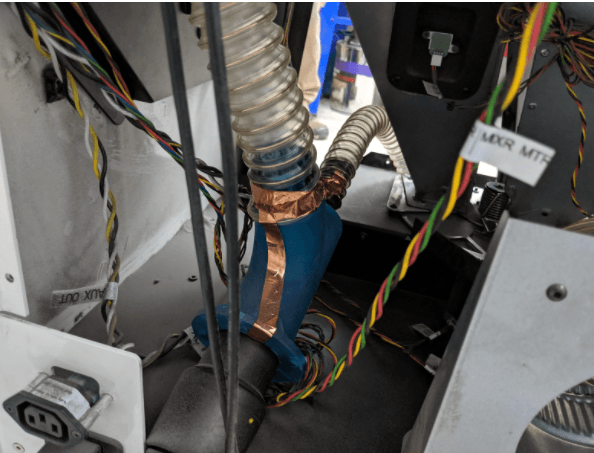
Primer prototipo del separador en Y, hecho con Draft Resin y envuelto en cinta adhesiva de cobre
La cinta adhesiva de cobre, a pesar de ser una solución temporal, tenía la importante función de disipar la carga estática provocada por el movimiento del polvo de nylon a través del tubo. Disipar esta carga de forma eficaz es importante para evitar descargas electrostáticas que pueden suponer un riesgo para los sistemas electrónicos de la Fuse Sift, así como una potencial fuente de ignición para el polvo de nylon combustible que circula por el sistema.
Larry Cheung
"Si se usan componentes que no disipen la electricidad estática, se pueden sentir e incluso ver choques electrostáticos cuando hay mucho polvo circulando a gran velocidad por el sistema. Por eso, las descargas electrostáticas son un verdadero problema. Todos nuestros subsistemas están conectados a tierra y no podemos permitir que los atraviesen descargas electrostáticas".
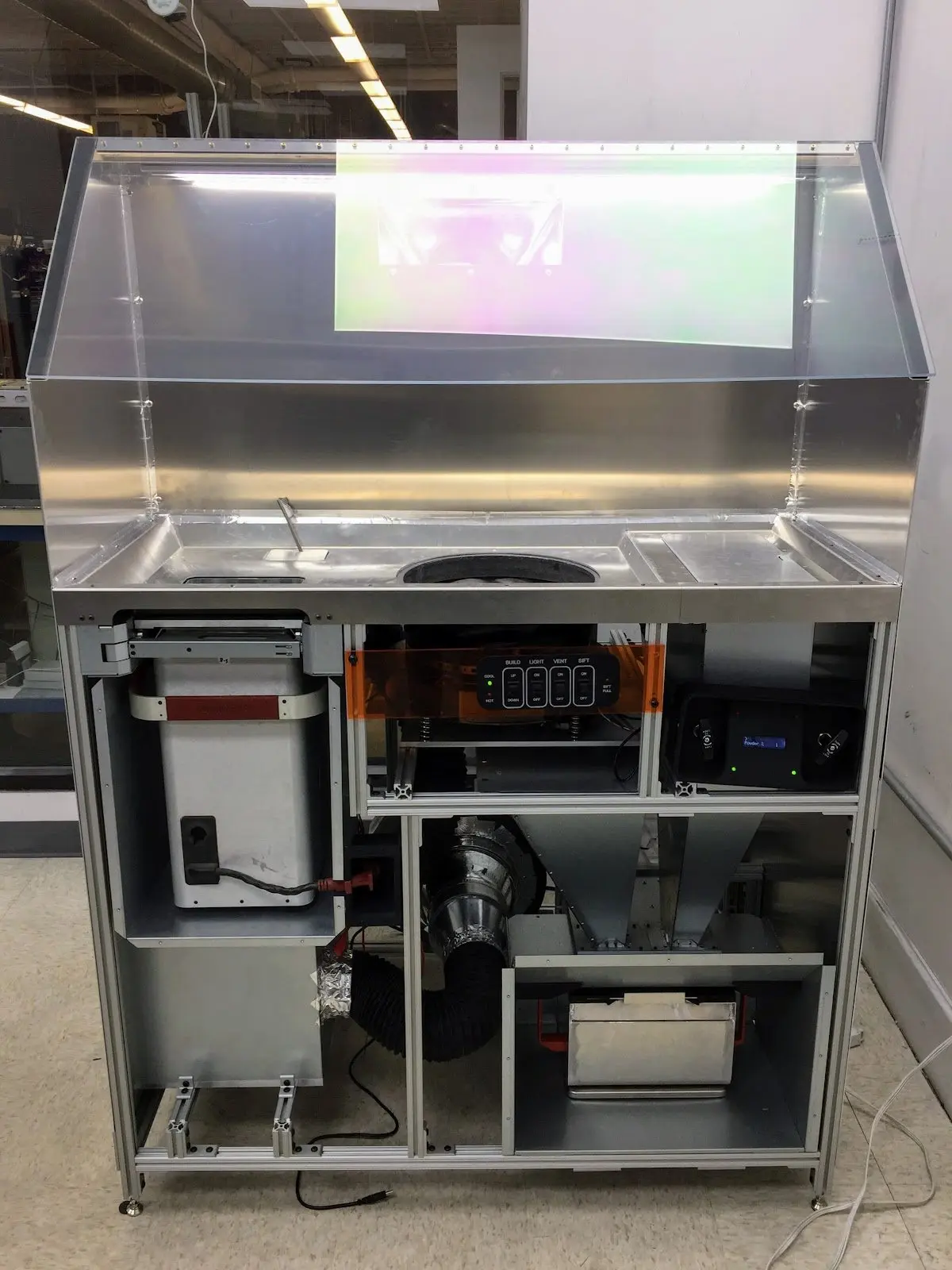
Uno de los primeros prototipos de la Fuse Sift.
Las corrientes eléctricas estáticas y no supervisadas son una preocupación para cualquier fabricante, con muchas ramificaciones. Está la cuestión de la seguridad de los empleados y la necesidad de proteger a los trabajadores de choques dañinos durante la manipulación del equipo. También está el dolor de cabeza que supone determinar de dónde provienen los choques: podrían provenir de componentes eléctricos o sencillamente, de la electricidad estática. No poder localizar la fuente de un cortocircuito puede hacer que líneas enteras de productos sufran daños, lo que le cuesta a los fabricantes tiempo y dinero.
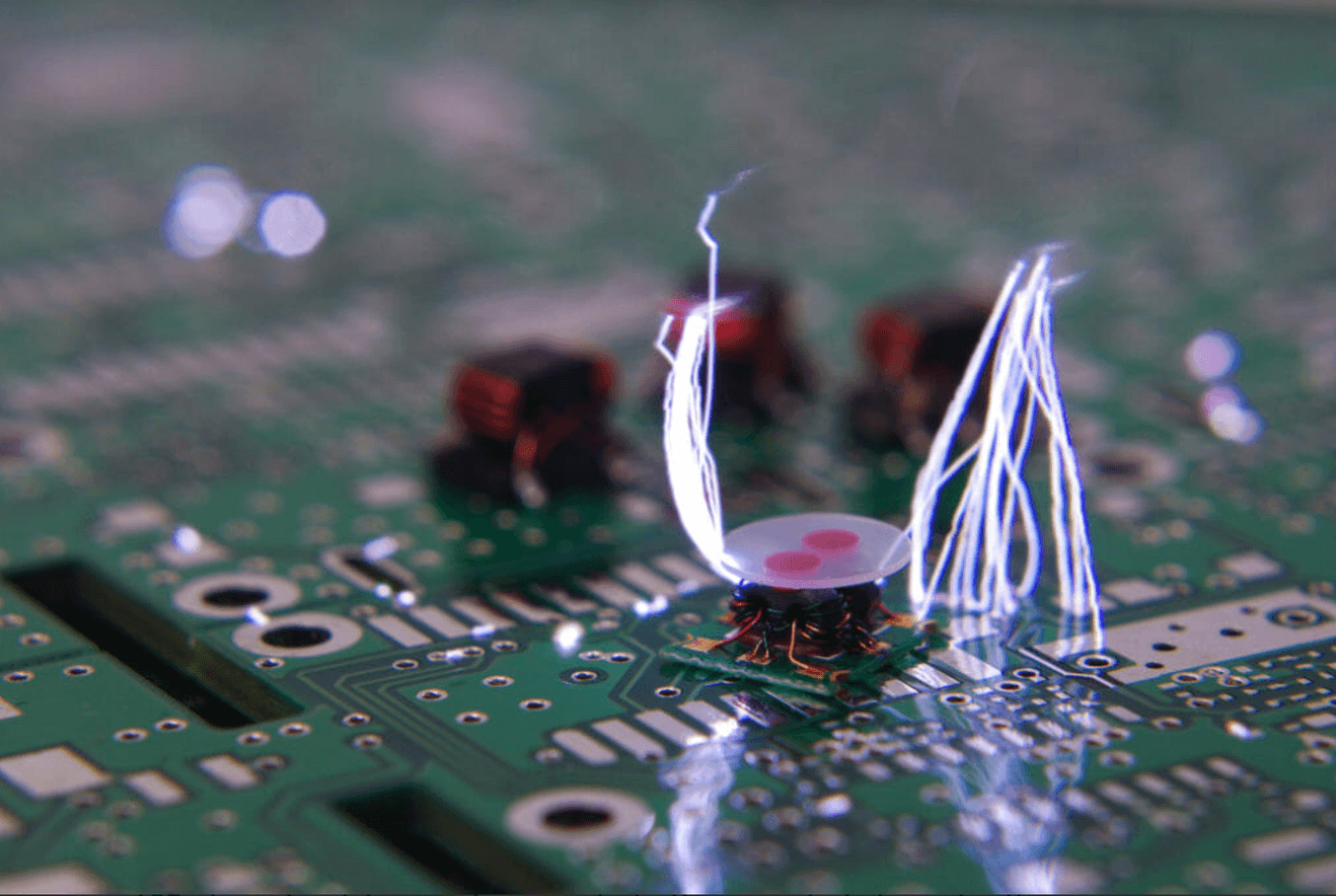
Choques electrostáticos destruyendo una placa de circuito.
En algunos casos, como le ocurrió a HAVEN, uno de los clientes de Formlabs, las cargas electrostáticas fuera de control pueden cortocircuitar los circuitos eléctricos de los productos finales, por lo que los clientes recibían un producto que quedaba inutilizado inmediatamente. HAVEN utilizó la ESD Resin para crear guías y fijaciones antiestáticas en su cadena de montaje y controlar las descargas electrostáticas.
Hay cuatro tipos de materiales relacionados con las descargas electrostáticas:
- Los materiales conductores (por ejemplo, el metal) permiten que los electrones recorran libremente su superficie, que es por lo que el utillaje para los componentes electrónicos se suele mecanizar a partir de metal.
- Los materiales disipadores (como la ESD Resin u otros plásticos antiestáticos) permiten que los electrones se muevan hacia un punto conectado a tierra a un ritmo más lento que el de los metales.
- Los materiales antiestáticos inhiben la carga triboeléctrica, es decir, la carga eléctrica que se acumular por la fricción o el contacto con otro material.
- Los materiales aislantes evitan o limitan el flujo de los electrones por sus superficie, por lo que las cargas estáticas pueden acumularse y mantenerse en ellos durante períodos largos de tiempo, que a menudo dañan los circuitos eléctricos que estén en contacto con ellos.
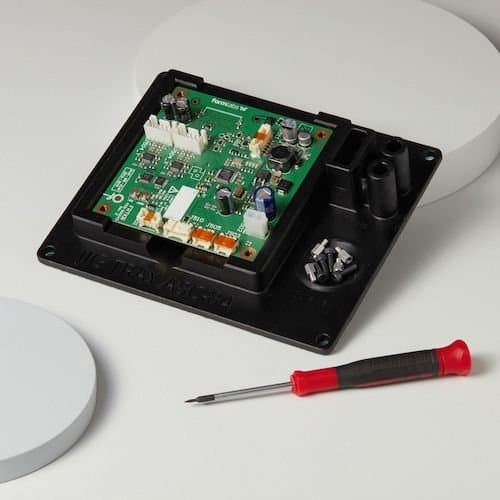
Cómo la impresión 3D con la ESD Resin optimiza la fabricación de electrónica
Phil Tsao, el ingeniero jefe de calidad del aire en interiores de HAVEN, nos cuenta cómo utilizaron la ESD Resin para reducir el coste y el plazo de producción de las fijaciones de producción antiestáticas hasta un 90 %.
Procesos de trabajo antiestáticos tradicionales
Normalmente, las piezas de uso final para aplicaciones antiestáticas se fabrican a partir de metal o de plásticos disipadores de electricidad estática. La soldadura, la fundición o el mecanizado son opciones para externalizar las piezas de metal con diversos costes e implicaciones. Sin embargo, durante una fase de creación de prototipos, las piezas de metal personalizadas son a veces difíciles y caras de diseñar, crear y ajustar, por no hablar de cómo pueden quedar obsoletas en la siguiente iteración.
"Nos pusimos en contacto con algunos vendedores que eran expertos en el doblado y la soldadura de tubos para hacernos una idea del precio y del plazo de elaboración de esta pieza para la producción tanto a corto como a largo plazo. Daba igual a quién le pidiéramos un presupuesto: eran extremadamente caras de producir, tal vez 40 $ o incluso 50 $ por pieza incluso con cantidades de producción en serie, que era mucho más de lo que esperábamos y además tardaríamos semanas en recibirlas. Debido a las limitaciones de tiempo y al coste, externalizarlo para nuestros prototipos simplemente no era una opción favorable. Por eso, poder hacer esto in situ y tenerlo listo inmediatamente fue algo revolucionario", nos explica Cheung.
Además de envolver una pieza impresa con la Draft Resin en cinta de cobre, el equipo también intentó utilizar aerosoles antiestáticos, así como bañar la pieza de resina de SLA en un recubrimiento disipador de estática. El problema de esta posibilidad era que los recubrimientos antiestáticos no eran muy resistentes al desgaste y era muy difícil obtener la capa uniforme necesaria para alcanzar un rendimiento fiable. Por suerte, el equipo de la Fuse Sift había oído rumores de que podía haber una solución más cerca de lo que pensaban.
Una solución cercana a casa
"Habíamos oído por el edificio que el equipo de materiales estaba trabajando en una resina antiestática, y hablamos con Kathy Bui (directora de productos para ingeniería) para ver si podríamos imprimir un par de piezas para los prototipos de la Fuse Sift", dice Cheung.
"Ya que muchos de nuestros clientes realizan trabajos de diseño de productos e ingeniería con nuestras resinas, no es raro que nos pregunten por la protección contra descargas electrostáticas, lo que fue la base del desarrollo de la ESD Resin. Una de las cosas buenas de Formlabs es que al hacer toda nuestra ingeniería en la empresa, a menudo necesitamos de nuestros productos las mismas cosas que nuestros clientes. Cuando Larry describió los desafíos que afrontaba el equipo de la Fuse Sift, resultaron ser exactamente el tipo de uso para el que habíamos diseñado la ESD Resin, de modo que nos lanzamos a aprovechar una oportunidad de predicar con el ejemplo", dice Kathy Bui.
La ESD Resin del equipo de materiales no podía haber llegado en mejor momento. Los prototipos de la Fuse 1 estaban listos para pasar a los testers externos de fase beta y estaba previsto que el prototipo de la Fuse Sift lo acompañara. No había tiempo de esperar a piezas de un proveedor de recubrimientos externos o de utillaje, así que poder imprimir estas piezas nosotros mismos esta crucial para que la prueba de fase beta fuera como estaba programada.
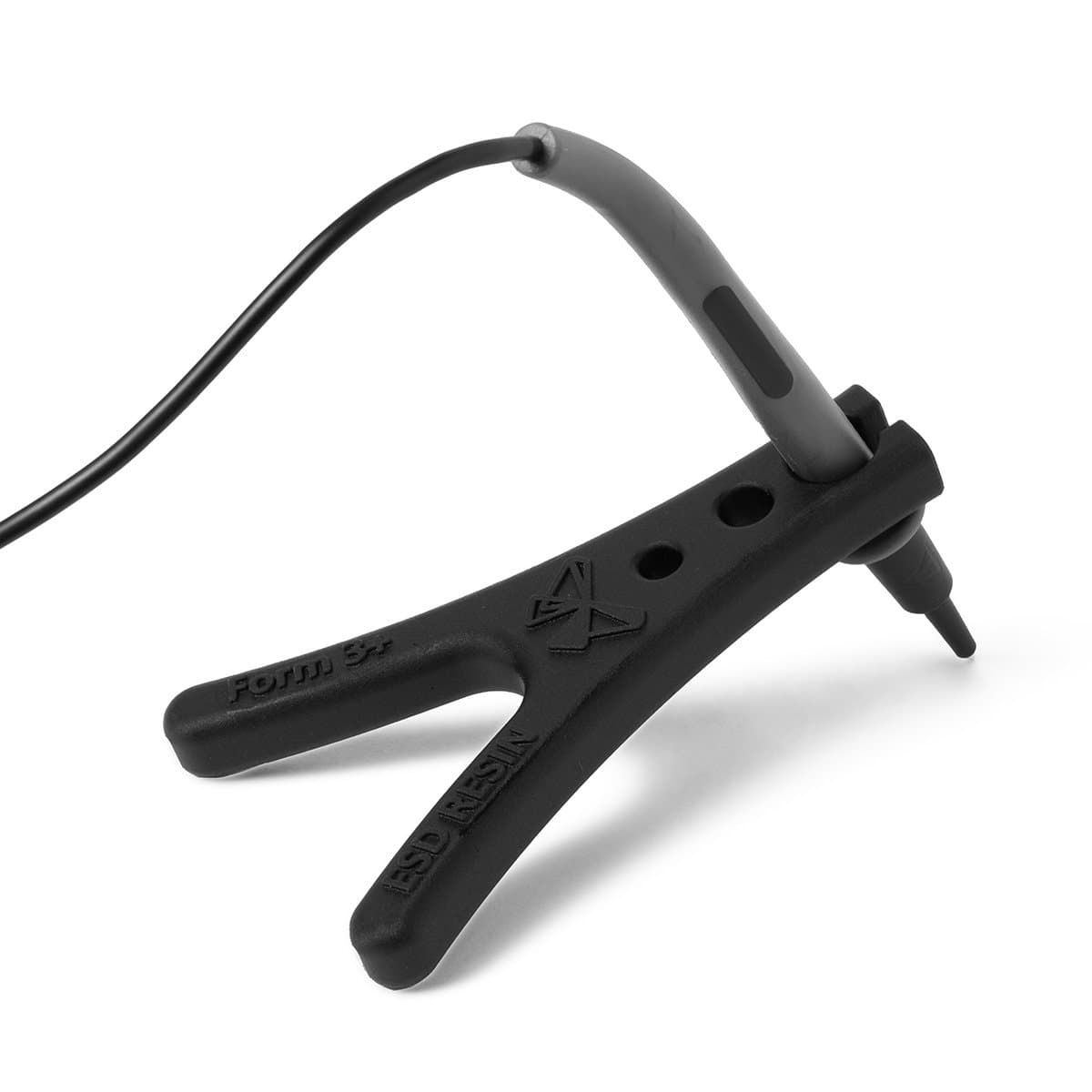
Solicita una muestra gratuita
¿Quieres probar la ESD Resin por tu cuenta? Solicita nuestro soporte antiestático de sonda de multímetro e impreso en 3D gratuito para tu mesa de trabajo eléctrica. Comprueba la resistividad de la superficie para validar su seguridad ante las descargas electrostáticas.
Las piezas de ESD Resin ayudan a completar nueve prototipos
El equipo imprimió nueve prototipos con el material que se acabaría comercializando con el nombre de ESD Resin. Las piezas se validaron con prototipos acabados de la Fuse Sift, que después se enviaron a potenciales fabricantes por contrato y se utilizaron para ensayos de fase beta internos y externos. El equipo utilizó un medidor de resistividad superficial y descubrió que las piezas impresas con la ESD Resin disipaban la electricidad estática y eran perfectas para conductos por los que circulara una gran cantidad de polvo de nylon.
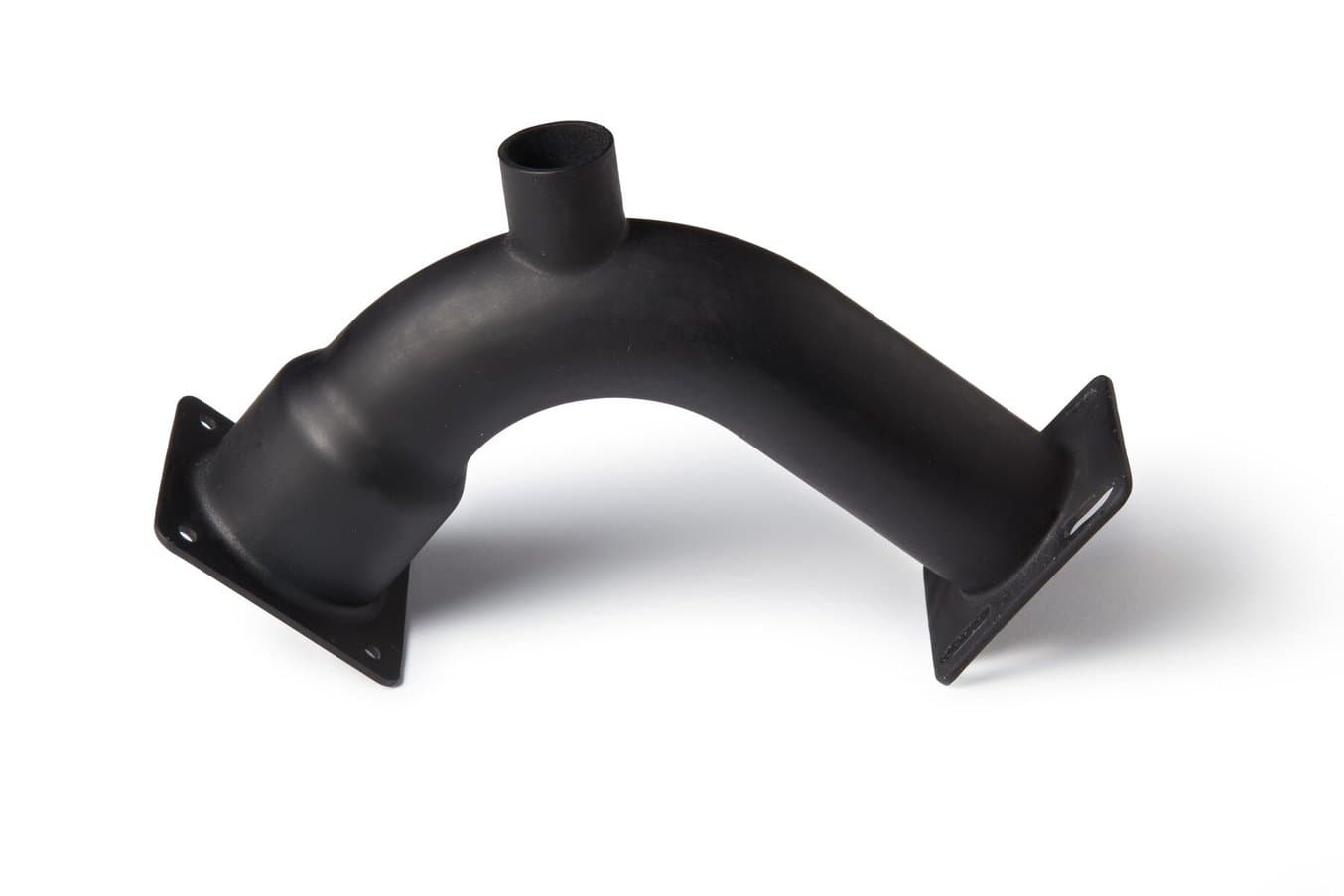
El tubo final del filtro, hecho con la ESD Resin
"Utilizar nuestra ESD Resin nos ha permitido salvar la distancia entre la creación de prototipos y la producción. La impresión 3D es la forma más rápida de hacer prototipos para una pieza como esta, pero no podíamos validar de forma segura el concepto del separador y los conductos sin una solución antiestática. La ESD Resin no ha dado las capacidades de diseñar y validar nuestro concepto in situ sin gastar cientos o incluso miles de dólares en utillaje o piezas externalizadas", dice Cheung.
Utilizar la propia ESD Resin de Formlabs permitió a los equipos de la Fuse 1 y la Fuse Sift acortar el camino hasta la producción evitando los costes elevados y los largos plazos de producción asociados a la externalización de piezas antiestáticas. Para un fabricante de equipos físicos, contar con las herramientas para crear piezas antiestáticas in situ suponía que este producto podría lanzarse más rápido y con un riesgo mínimo.
"Se no imprimimos esto en nuestra empresa, habría tardado en llegar un par de semanas y nos habría costado un par de miles de dólares. Saber que podíamos hacerlo nosotros mismos, especialmente cuando teníamos una fecha límite para hacerlo llegar a los fabricantes por contrato, nos permitió planificar mejor", dice Cheung.