Cómo Unilever y Serioplast desarrollan nuevos diseños de botellas con moldes impresos en 3D
Unilever es una de las mayores empresas de bienes de consumo de alta rotación del mundo, por lo que está desarrollando constantemente productos nuevos de uso cotidiano, en ámbitos como el cuidado personal, la atención domiciliaria y la nutrición, entre otros. Es bastante probable que haya alguno de sus productos en tu hogar ahora mismo, ya que marcas como Dove, Domestos, Cif, Knorr, Axe (Lynx), Ben & Jerry's y decenas de otras marcas globales o locales son propiedad de Unilever.
Los bienes de consumo de alta rotación son un sector en el que la demanda constante de los consumidores fomenta una competencia encarnizada, por lo que las marcas tienen que innovar continuamente y adaptar las estrategias de sus productos a los cambios. Un área importante de innovación son los envases y embalajes; el diseño de una botella a veces puede afectar a la percepción de los clientes tanto como lo que contiene. Marcas como Unilever tienen que tener en cuenta factores como el consumo de material, el atractivo estético, la seguridad y la sostenibilidad de un amplio catálogo de tipos de embalaje y los productos que contienen. A pesar de eso, con las botellas "simples" de plástico, pasar de un diseño en la pantalla del ordenador a la máquina de llenado en la cadena de producción solía llevar muchos meses.
"Un fabricante de productos de consumo como Unilever debe estar en el mercado lo antes posible o antes que la competencia. Hay que ofrecer el mejor producto al mejor precio en el tiempo más corto posible a los consumidores. La impresión 3D nos ayuda a agilizar este proceso".
Stefano Cademartiri, propietario de CAD y Prototipado de Unilever
Descubre cómo Stefano Cademartiri, el propietario de CAD y Prototipado de Unilever, y Flavio Migliarelli, director de diseño para I+D de Serioplast Global Services, trabajaron codo con codo para poner a prueba la viabilidad de los moldes impresos en 3D para el moldeo por estiramiento y soplado de bajo volumen, con el fin de acelerar el prototipado y los ensayos piloto eliminando seis semanas de espera y reduciendo los costes hasta un 90 %.
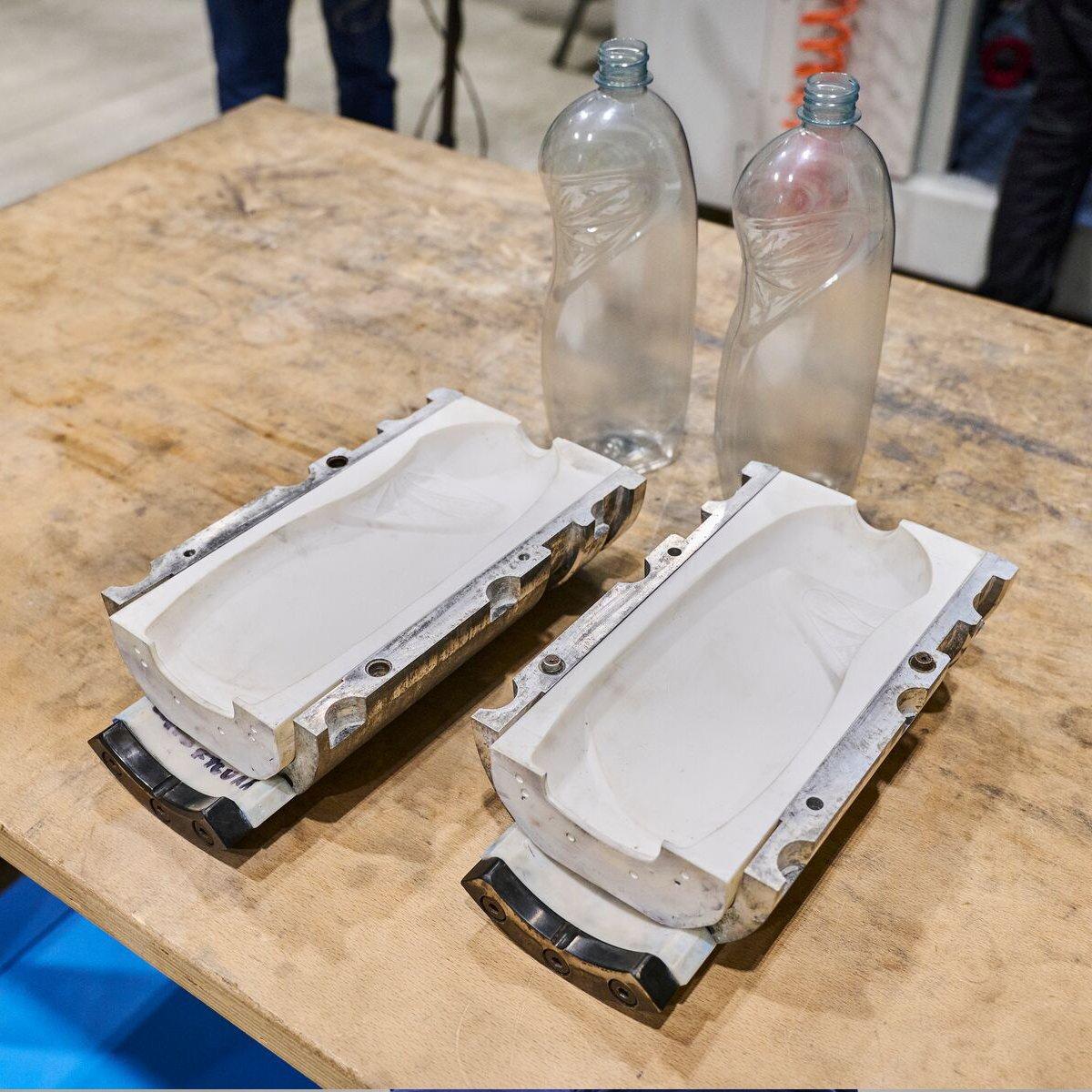
Moldeo por soplado y estiramiento rápido de bajo volumen con moldes impresos en 3D
Este libro blanco proporciona métodos y recomendaciones para usar en el proceso de SBM moldes impresos en 3D mediante SLA, para reducir los costes y los tiempos de espera durante la preproducción. Detalla el estudio de viabilidad que realizaron dos expertos del sector, Unilever y Serioplast. Los pormenores de este estudio abarcan desde consideraciones respecto al diseño y el proceso de trabajo hasta las condiciones de moldeo.
El proceso de trabajo tradicional para el desarrollo y el ensayo de nuevos diseños de botellas
El método más habitual para producir productos de plástico como los recipientes de comida y bebida, los envases de cosméticos y los embalajes médicos es el moldeo por soplado, un conjunto de técnicas de producción en masa rápidas y de eficacia probada para piezas de alta calidad con paredes delgadas. El moldeo por soplado tiene tiempos de ciclo muy cortos, que normalmente duran entre uno y dos minutos, y resulta extremadamente rentable para una producción de alto volumen. Se suele utilizar para producir millones de piezas idénticas con un precio por unidad bajo.
El moldeo por soplado consiste en inflar un tubo de plástico calentado, llamado paresón o preforma inyectada, dentro de un molde hasta que adquiera la forma deseada. Hay tres tipos de procesos de moldeo por soplado: el moldeo por extrusión-soplado (EBM), el moldeo por inyección-soplado (IBM) y el moldeo por soplado y estiramiento (SBM). El SBM se suele utilizar para producir recipientes de PET totalmente transparentes y de alta calidad, como las botellas de agua.
Serioplast es un productor global de envases de plástico rígidos para el sector de los bienes de consumo de alta rotación y es uno de los principales socios de Unilever a la hora de desarrollar y producir envases y embalajes para el mercado del hogar y del cuidado personal. "Producimos 4000 millones de botellas al año usando el PET, el polietileno de alta densidad y el polipropileno como materiales", dijo Migliarelli.
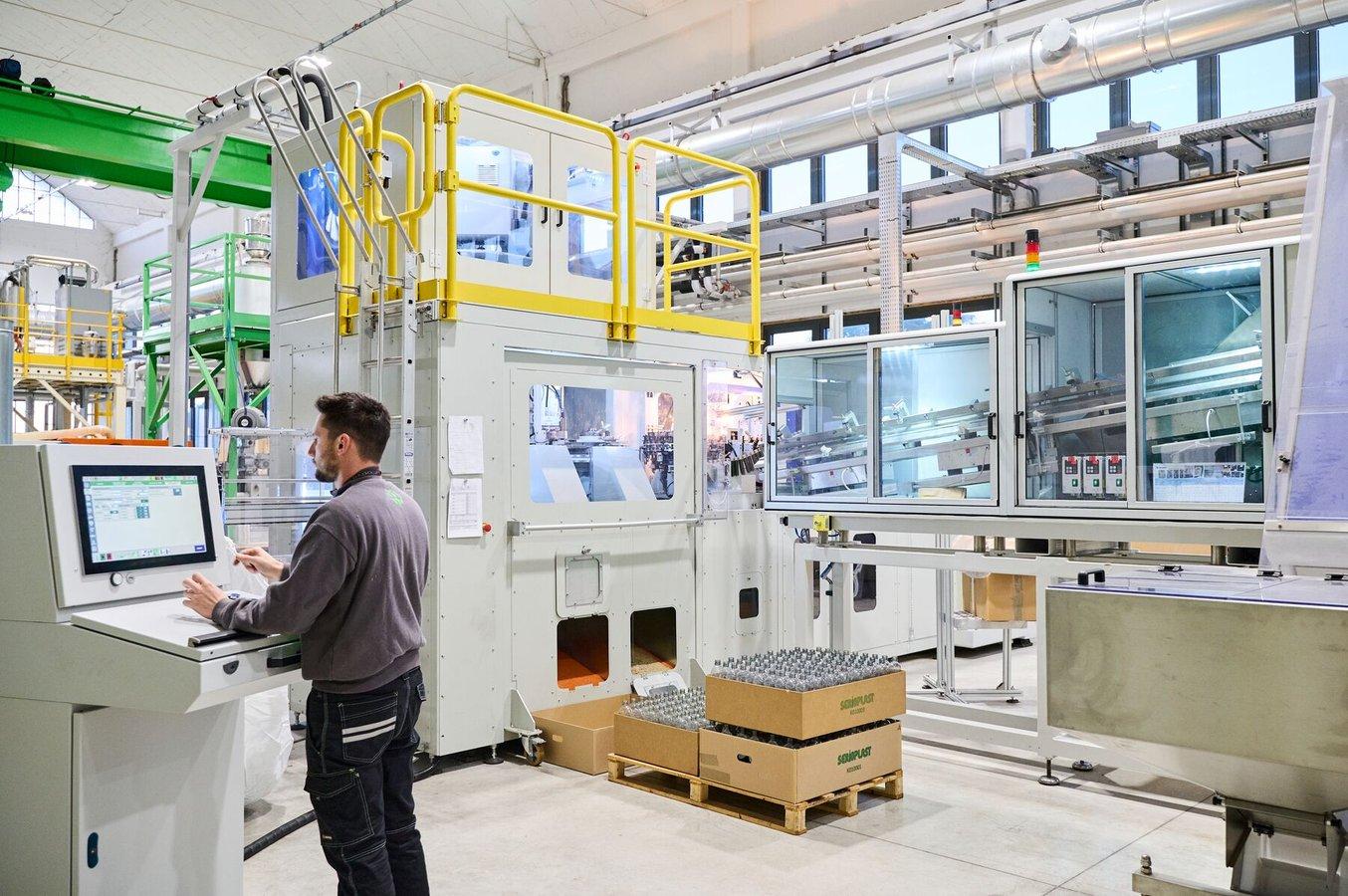
Una máquina de SBM de cuatro cavidades Seriomac UNIX de Serioplast en sus instalaciones de I+D en Italia. En colaboración con Unilever, desarrollaron un nuevo proceso de trabajo para usar moldes impresos en 3D en este equipamiento de fabricación industrial a gran escala.
Normalmente, Serioplast habría impreso directamente en 3D piezas que sirvieran como prototipos o las habría producido mediante moldeo por soplado. Antes, esas versiones preliminares impresas en 3D no representaban el tacto ni la transparencia adecuados de la pieza final, y no eran lo bastante fiables como para enviarlas a los consumidores. Sin embargo, fabricar muestras con la calidad de las piezas finales mediante SBM requiere utillaje de metal caro, lo que añade entre seis y nueve semanas de espera a una fase típica de ensayos piloto por la complejidad del proceso y por tener que externalizar la producción del molde.
"Tenemos que esperar entre seis y 12 semanas para dar a un cliente la muestra real, por lo que desperdiciamos muchas semanas solo en probar un diseño de botella nuevo. A veces resulta un proceso exigente y frustrante, porque es posible que haya que empezar de cero", dijo Migliarelli.
Los moldes para SBM se han hecho tradicionalmente de metal mediante mecanizado CNC, lo que requiere equipamiento especializado, software CAM y mano de obra experimentada. Por lo general, la producción de utillaje de metal se externaliza a proveedores de servicios que requieren esperas de entre cuatro y ocho semanas y puede costar entre 2000 € y 100 000 € o más, en función de la complejidad de la pieza y del número de piezas por molde. Incluso mecanizar un molde de metal in situ suele llevar seis semanas, ya que requiere varios pasos: un tiempo de espera para que llegue el pedido de materiales, la configuración de CAM y de la máquina, un pulido manual y esperar a que la máquina esté disponible.
Por lo tanto, moldear por soplado cantidades pequeñas de piezas para el prototipado y para ensayos piloto no ha sido viable económicamente con este método. Empresas como Unilever han tenido que prolongar sus plazos y tomar decisiones respecto al diseño final basándose en prototipos estéticos hechos con distintos materiales, que a menudo han hecho que el utillaje quede obsoleto y han llevado a pérdidas irrecuperables.
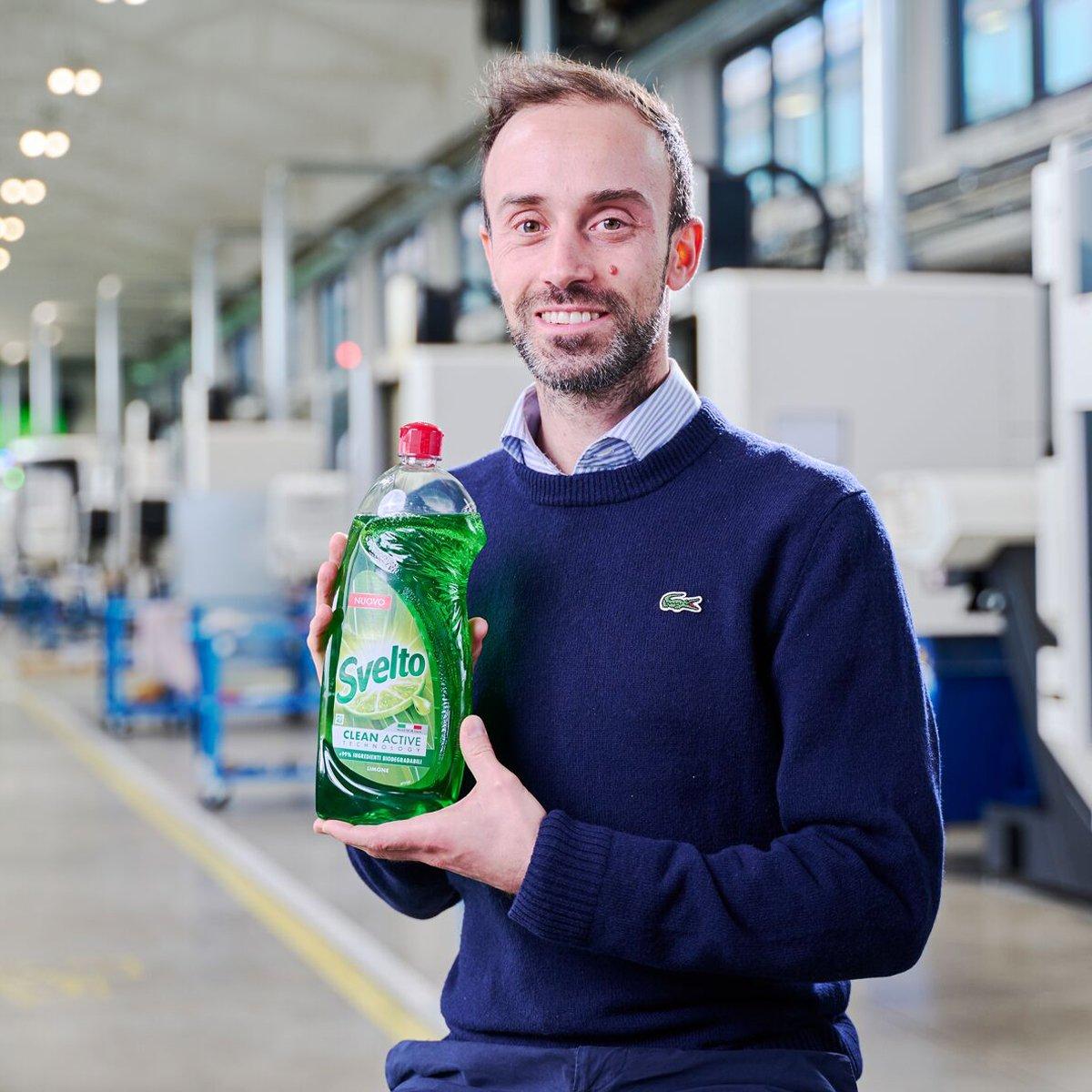
Reduce los costes y el tiempo dedicado a los ensayos piloto de embalajes con el moldeo por soplado rápido
En este seminario web, el experto en moldeo por soplado Flavio Migliarelli explicará el proceso de trabajo y el método paso a paso, además de hablar de las ventajas clave y las posibles aplicaciones de usar moldes impresos en 3D para realizar un moldeo por soplado y estiramiento rápido.
Moldeo por soplado de botellas reales, un 70 % más rápido y un 90 % más barato
La impresión 3D es una potente solución para fabricar herramientas con rapidez y con costes reducidos. Requiere muy poco equipamiento, con lo que se libera capacidad de CNC y tiempo de operarios expertos que pueden dedicarse a otras tareas importantes. Al contar con la impresión 3D en sus propias instalaciones, los fabricantes y los diseñadores de productos pueden introducir el utillaje rápido en el proceso de desarrollo de productos para validar los pasos de diseño y fabricación antes de pasar a la producción en masa. Los moldes impresos en 3D ya se utilizan en procesos como el moldeo por inyección o el termoformado para realizar iteraciones rápidamente, acelerar el desarrollo de productos y lanzar mejores productos al mercado.
La tecnología de impresión 3D por estereolitografía (SLA) es una buena elección para el moldeo. Se caracteriza por un acabado de la superficie liso y una alta precisión que la herramienta trasladará a la pieza final y que también facilita el desmoldeo. La Form 3L es una impresora 3D de gran formato que permite fabricar piezas y moldes de gran tamaño y al mismo tiempo es lo suficientemente compacta para una oficina.
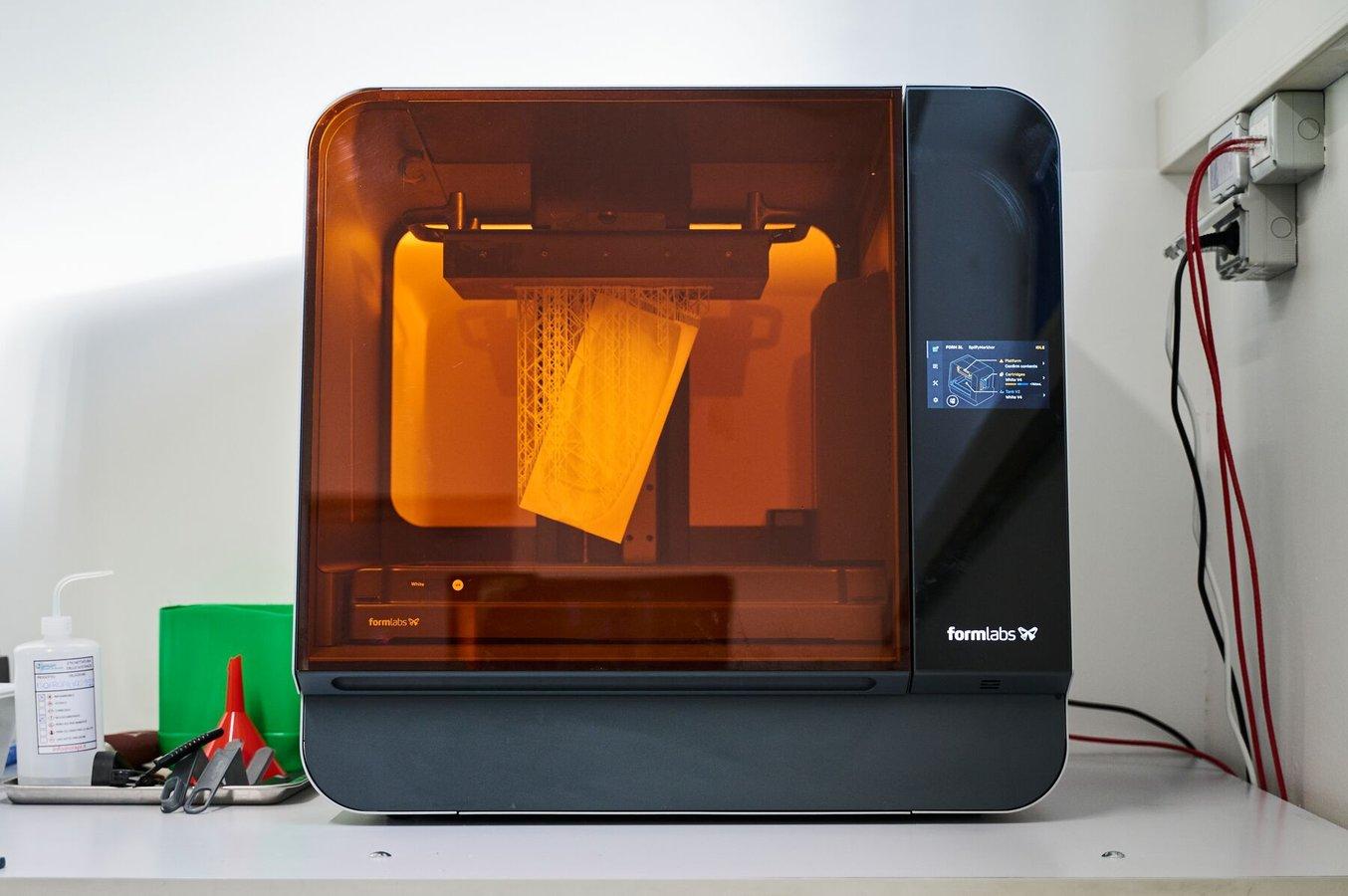
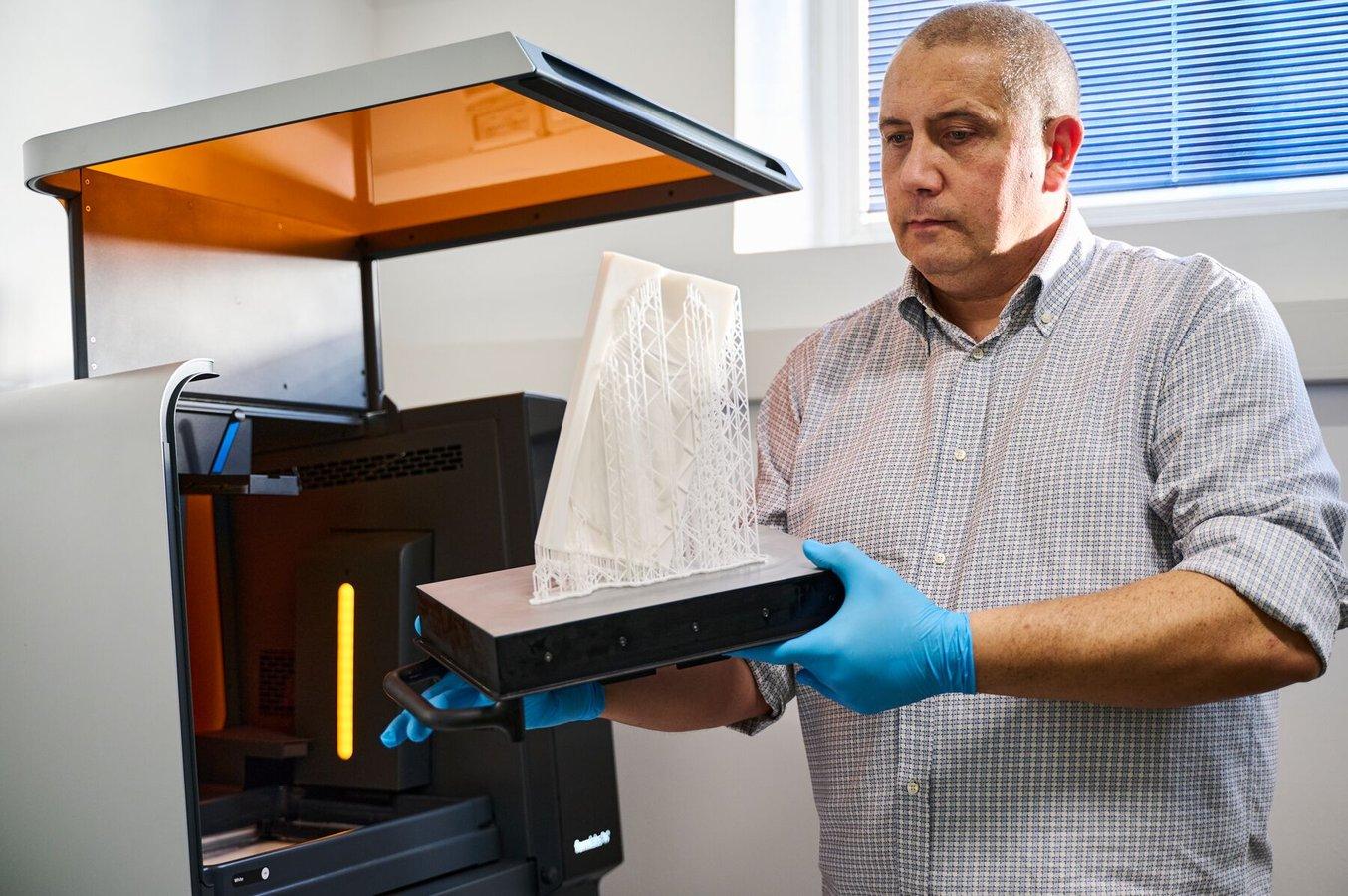
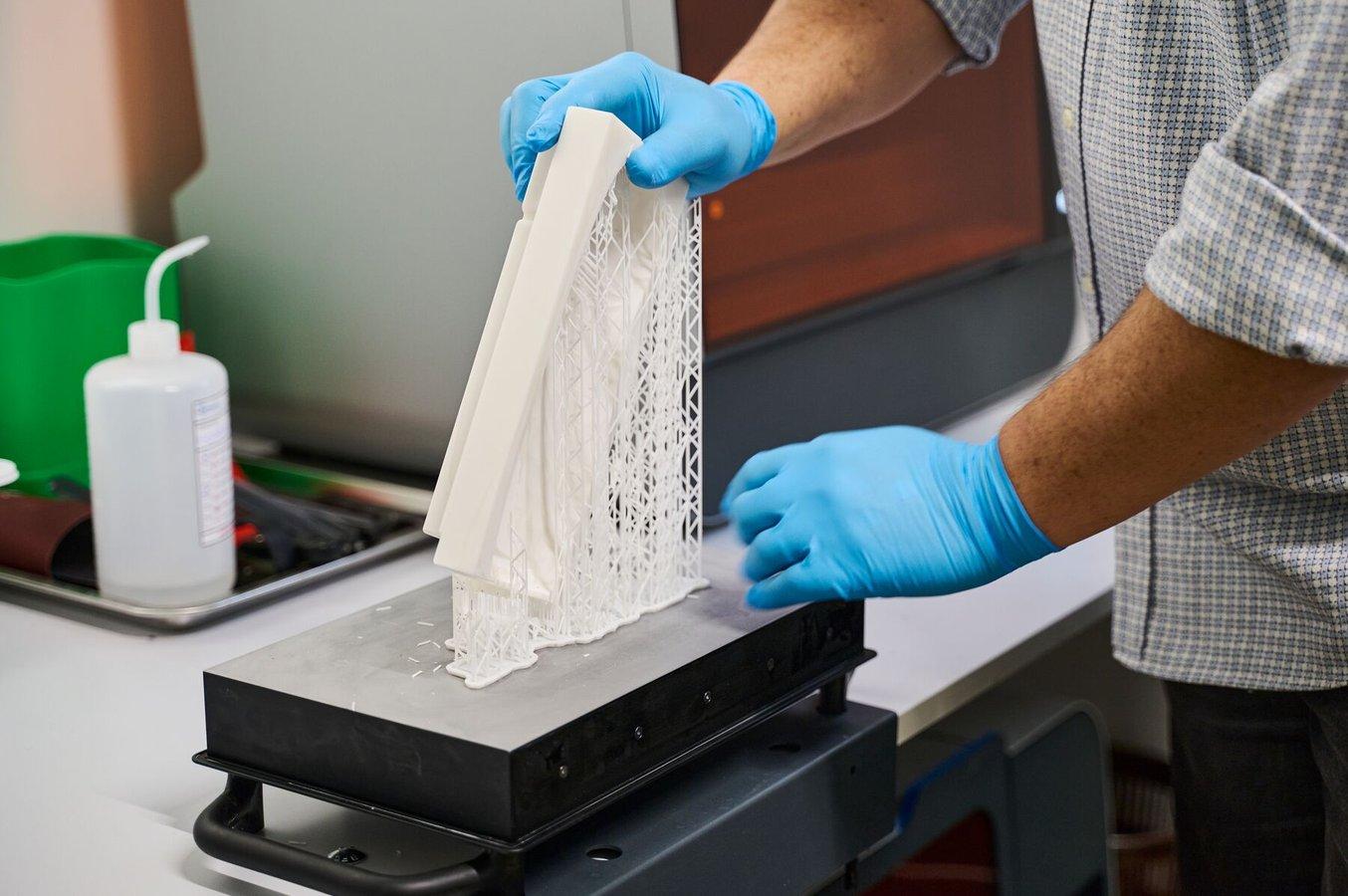
El molde se imprime en 3D en la Form 3L con la Rigid 10K Resin.
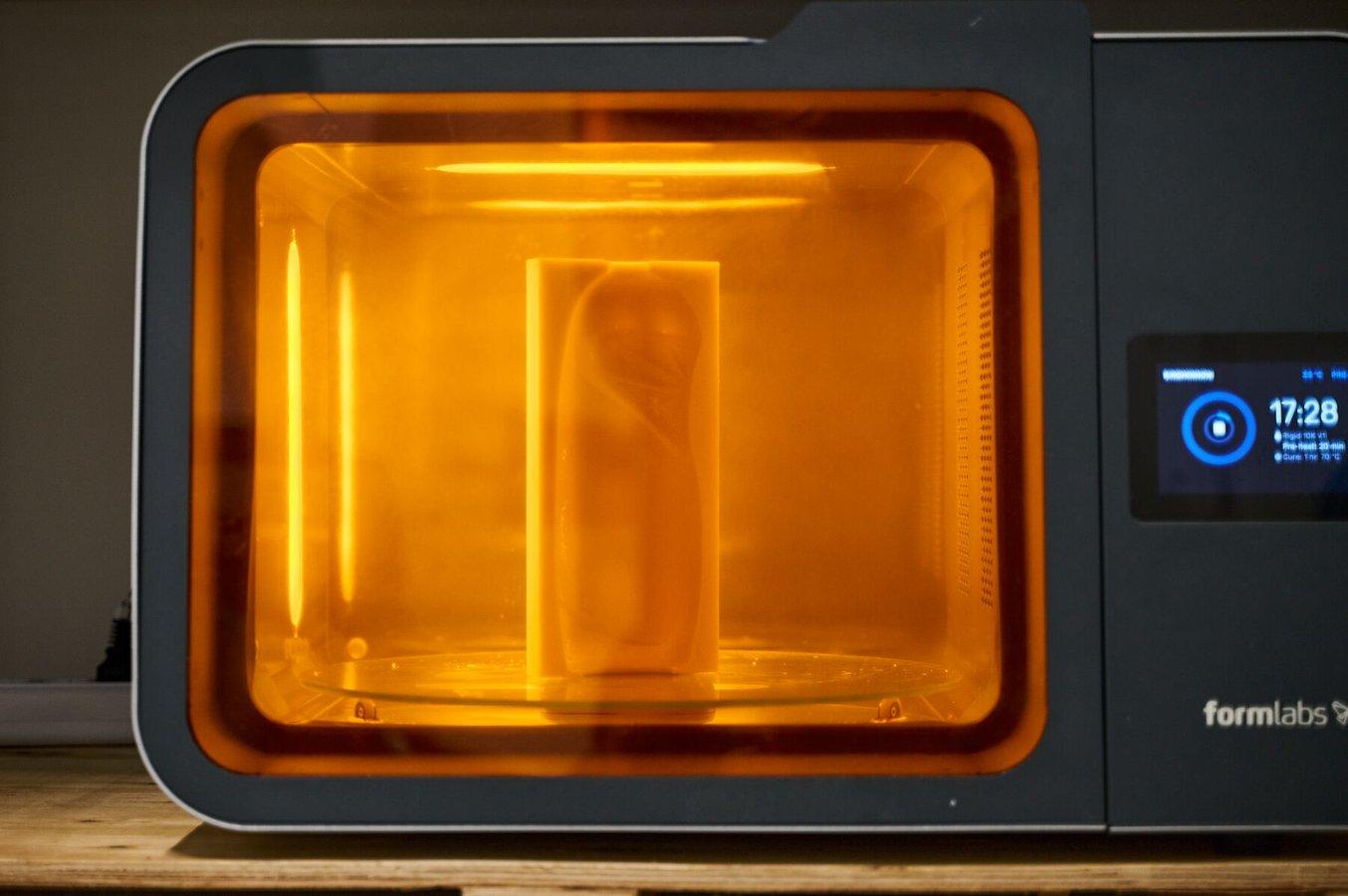
Después del lavado, se retiran los soportes y se poscura el molde.
Elegir el material correcto es crucial para producir moldes. Unilever y Serioplast necesitaban un material que pudiera soportar la presión interna y la temperatura del proceso de SBM y que mantuviera al mismo tiempo una buena precisión y estabilidad dimensional.
"Con la ayuda de los ingenieros de Formlabs, identificamos el material que nos podía dar la posibilidad de tener algunas botellas hechas con los materiales reales para llevar a cabo nuestras pruebas", dijo Cademartiri.
El material que recomendamos para el SBM es la Rigid 10K Resin, por su combinación de tenacidad, rigidez y resistencia térmica. Es un material con partículas de vidrio de calidad industrial con una temperatura de flexión bajo carga de 218 °C a 0,45 MPa y un módulo de tracción de 10 000 MPa. El utillaje impreso con la Rigid 10K Resin tiene una buena estabilidad dimensional y es adecuado para cientos de ciclos de moldeo por soplado, con una gran repetibilidad.
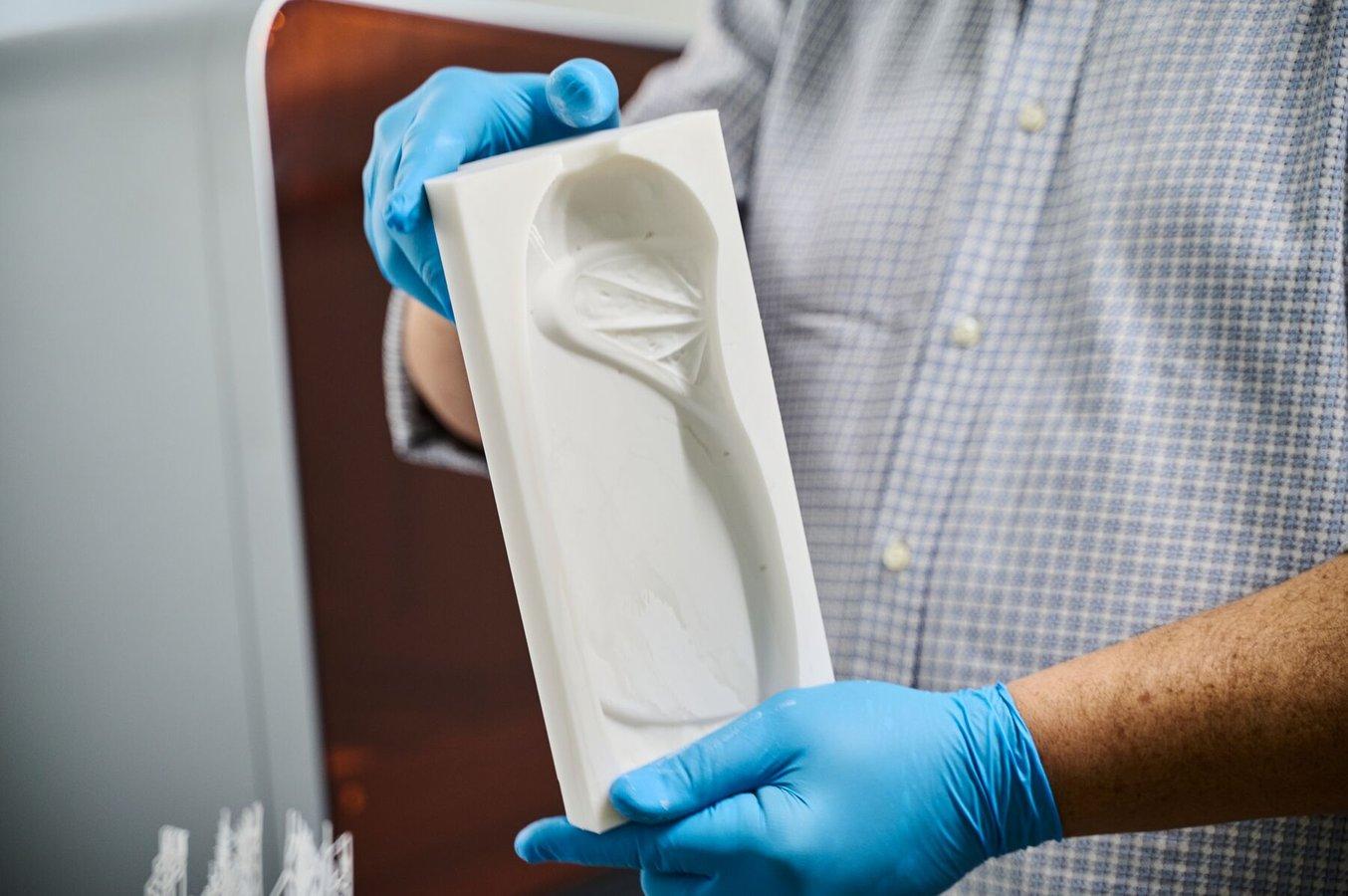
Al usar la Rigid 10K Resin, Serioplast fabricó moldes precisos con un acabado de la superficie liso, capaz de integrar detalles precisos, incluidos agujeros de diámetros tan reducidos como 0,5 mm. Posacabaron la herramienta con una máquina de pulido o un lijado manual para alcanzar las medidas importantes. Las superficies con texturas se incorporan en el diseño en CAD de la cavidad del molde.
"Tenemos detalles ajustados a medida para los moldes, sobre todo para botellas que tengan logotipos o cosas como un detalle en forma de limón, que requieren mucha precisión. La máquina de Formlabs, combinada con la Rigid 10K Resin, ofrece la posibilidad de tener detalles muy buenos que se puedan trasladar posteriormente a la botella real", dijo Cademartiri.
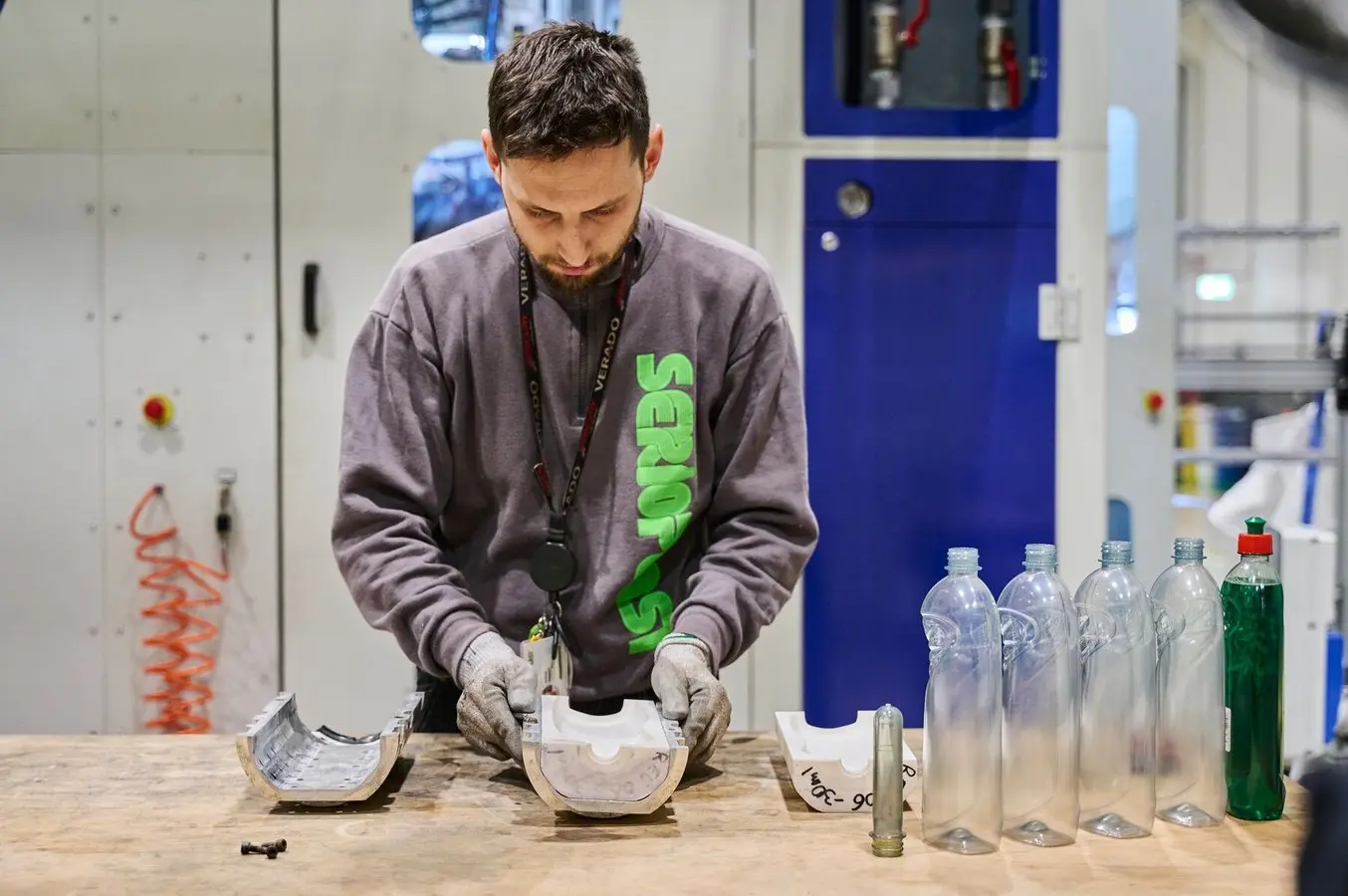
El molde impreso en 3D con la Rigid 10K Resin se pule a mano y después se ensambla dentro de un armazón de metal.
Con la impresión 3D SLA, se puede construir un molde en dos días. Los moldes impresos en 3D reducen el tiempo de espera para iniciar los ensayos piloto de seis a dos semanas, obteniendo al mismo tiempo piezas previas a la producción realistas que tienen una calidad muy cercana a la final y que se moldean usando el mismo material y la misma maquinaria que las posteriores unidades de producción final. Además, los moldes impresos en 3D permiten a los operarios realizar ensayos piloto con múltiples diseños al mismo tiempo.
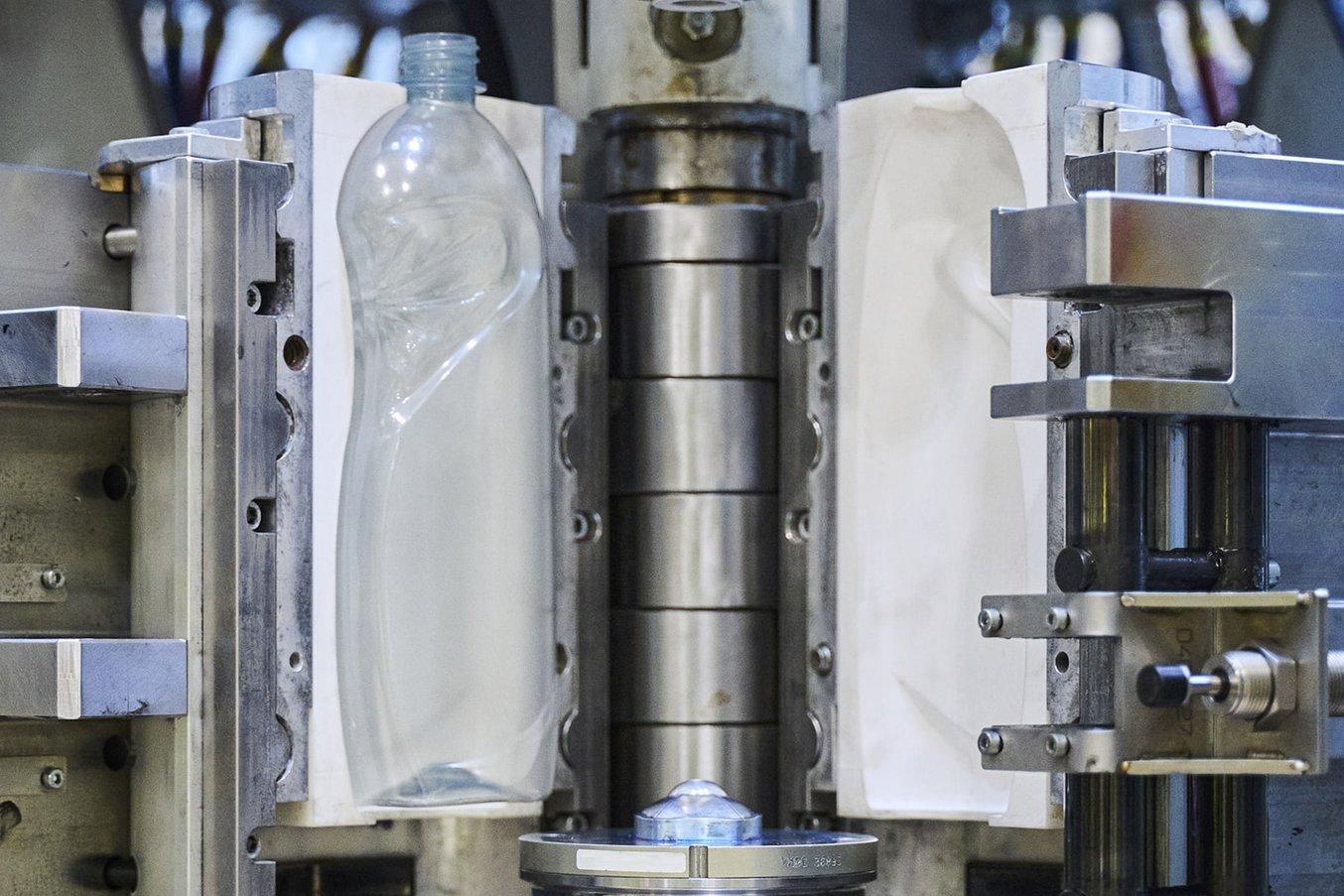
Molde impreso en 3D con la Rigid 10K Resin para una botella de 750 ml que Slice Design creó para Unilever, instalado en las abrazaderas que sujetan la cáscara del molde en la máquina. El equipo puede usar la misma ventana de proceso que con un molde piloto estándar, lo que permite someter a ensayo el proceso final de forma fiable.
"Con el molde impreso en 3D, utilizamos una disposición estándar dentro de unas abrazaderas que se colocan en la máquina de moldeo por soplado. Por eso, ahorramos mucho tiempo en el diseño de moldes y podemos gestionar nuestro horario de impresión 3D con mucha facilidad", dijo Migliarelli.
Producción de 200 unidades | Molde de metal mecanizado | Molde impreso en 3D |
---|---|---|
Equipamiento | Máquina CNC in situ o externalización | Form 3L Rigid 10K Resin |
Tiempo de espera para los ensayos piloto | 6-8 semanas | 2 semanas |
Coste de utillaje | 2500 - 10 000 € | 500 - 1000 € |
"Con el molde impreso en 3D, podemos ahorrar hasta un 70 % de tiempo y un 90 % de costes respecto al molde estándar. Anteriormente, [los clientes] tenían que esperar hasta 12 semanas para recibir la pieza de un único diseño, mientras que ahora podemos hacer cinco diseños".
Flavio Migliarelli, director de diseño para I+D de Serioplast Global Services
Realizar ensayos tan amplios es casi imposible con los métodos tradicionales. Haría falta invertir en un molde de metal para cada diseño sin las ventajas de economía de escala y los costes del utillaje nunca se recuperarían.
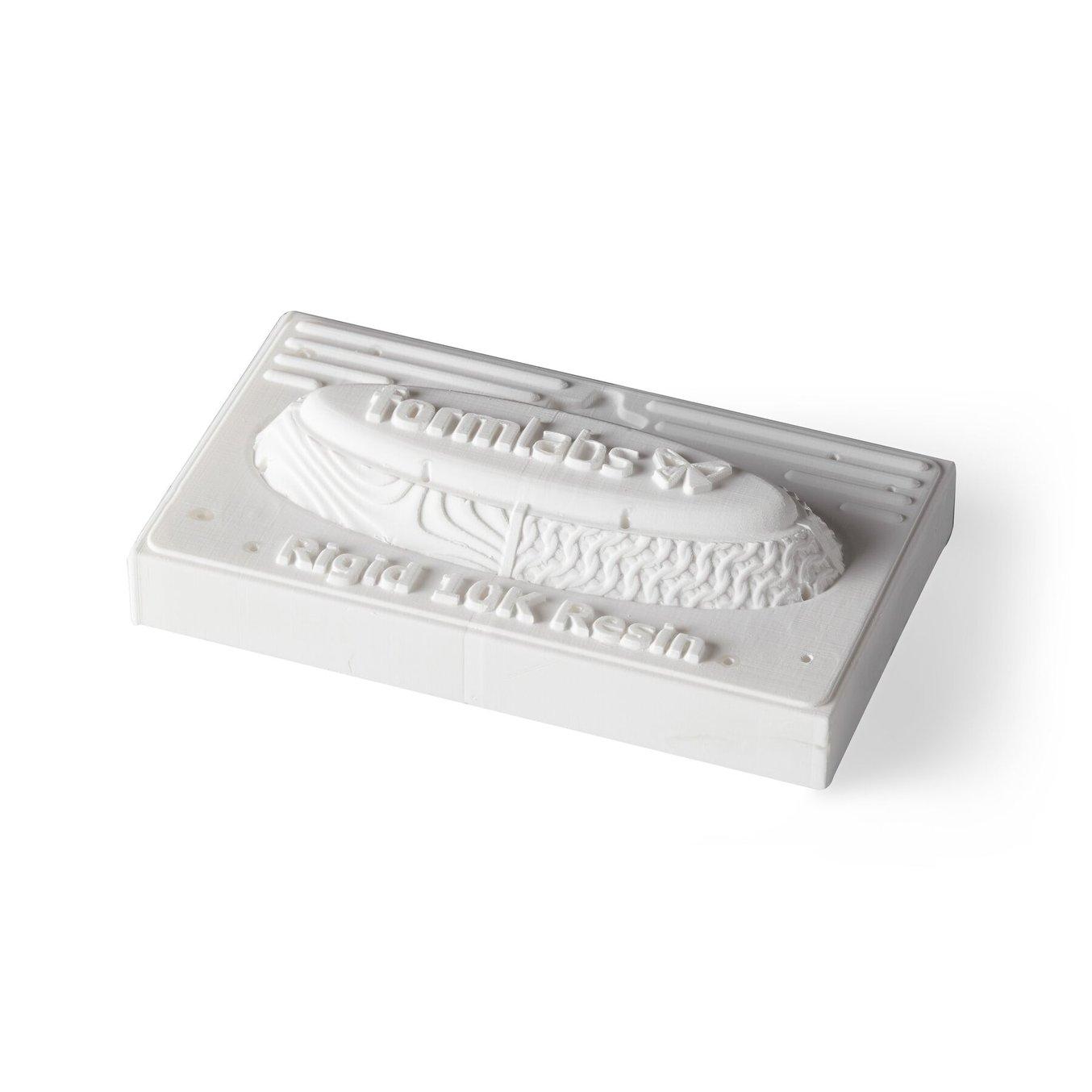
Solicita una pieza de muestra gratuita
Experimenta la calidad de Formlabs de primera mano. Enviaremos una pieza de muestra gratuita a tu lugar de trabajo.
Desde las pruebas con clientes a la configuración de la cadena de producción
Principalmente, las herramientas impresas en 3D se utilizan para producir muestras destinadas a pruebas con los clientes. Estas muestras representan al producto final en cuanto a la sensación que producen, su estética y su utilidad, y el consumidor las percibe como el producto real.
"Puedes tener una botella real antes de fabricar el molde real; así se puede identificar inmediatamente si el desarrollo está siguiendo el camino adecuado o si hace falta cambiar algo antes de cometer errores que salgan más caros.
Stefano Cademartiri, propietario de CAD y Prototipado de Unilever
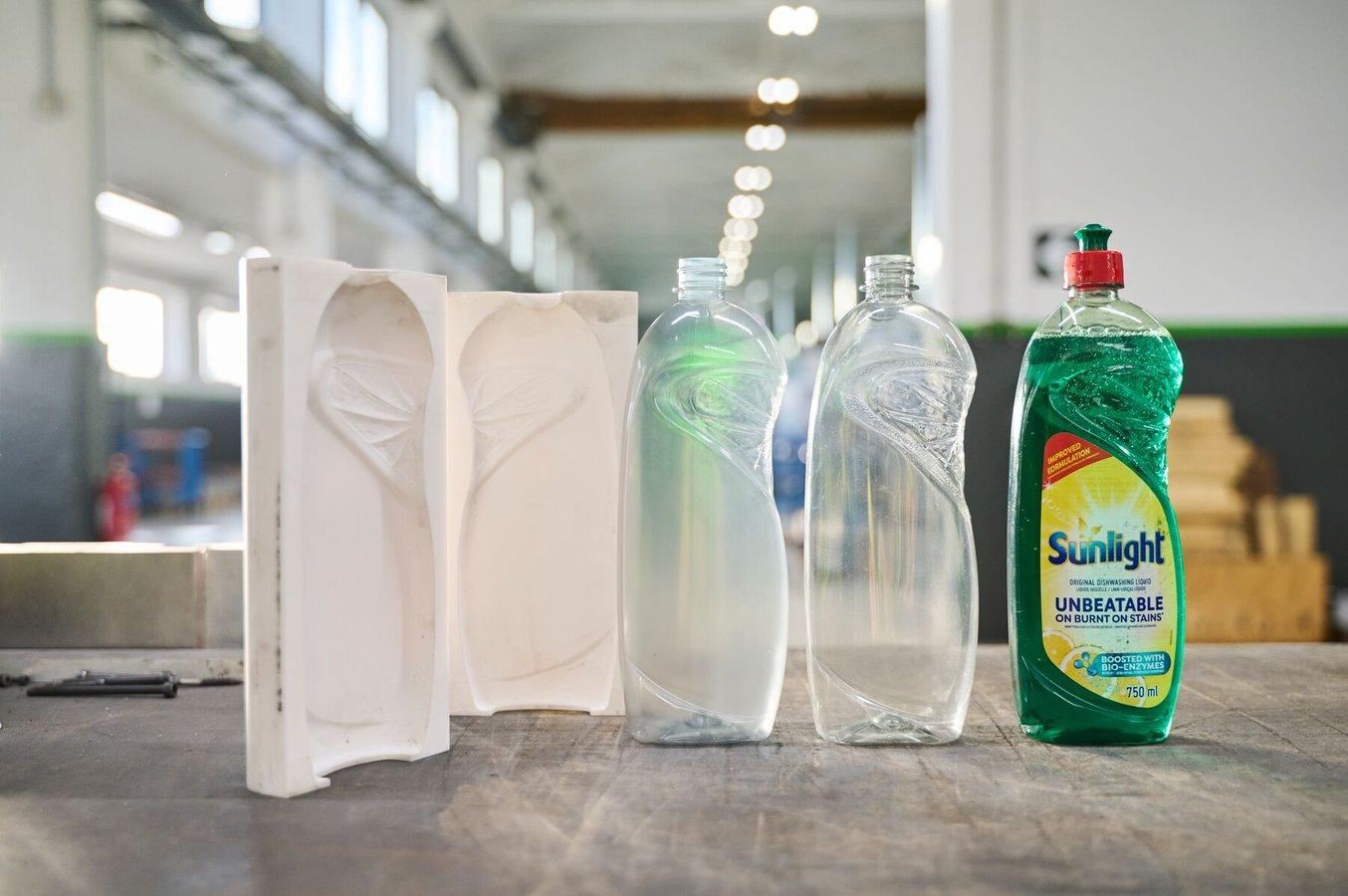
Las botellas producidas con una herramienta impresa en 3D son casi indistinguibles del producto final producido mediante procesos de utillaje de metal tradicionales. De izquierda a derecha: el molde de dos piezas impreso en 3D con la Rigid 10K Resin, una botella producida con un molde de metal y un prototipo de botella etiquetado para pruebas con los clientes.
Un uso secundario del molde modular es validar el proceso de SBM y la preforma de PET que se va a soplar, examinando las ventanas de proceso, el índice de estiramiento y la distribución del material que se puede alcanzar. Serioplast produce las preformas in situ mediante moldeo por inyección. Aunque algunas preformas están hechas a medida para una botella específica, suelen trabajar con elementos estandarizados que los usuarios no pueden modificar. El equipo de Serioplast quería comprender la gama de capacidades que estaban disponibles al utilizar esta preforma común. Conocer esta información ayuda a determinar si una preforma concreta es adecuada para moldear por soplado una botella específica antes de pasar a la producción.
Usamos la misma ventana de proceso que un molde piloto estándar. Esto es fantástico, porque podemos poner a prueba las ventanas de proceso finales y ver qué le ocurre a la botella. Hablamos de presiones de hasta 30 MPa, dando resultados buenos y fiables. También podemos decir que hay un calentamiento de en torno a 100 °C en la preforma sin que haya desgaste en la cavidad del molde impreso en 3D. Podríamos producir con mucha facilidad 100 o 200 botellas cada día. Podemos llegar hasta las 1000 con más tiempo", dijo Migliarelli.
La tercera aplicación de la producción de moldes rápidos es poner a prueba algunos aspectos de la cadena de producción en fases tempranas del proceso. Dado que las botellas moldeadas con moldes impresos en 3D son tan similares a las unidades de producción final, se pueden usar para realizar una validación primera de la cadena de llenado, como el movimiento de la cadena, el uso de los volantes de las máquinas de llenado de botellas, la colocación de los tapones o la actividad de la encajonadora robótica. Realizar ensayos piloto con la cadena de producción en las primeras fases del proceso permite a las fábricas prever la necesidad de piezas de recambio, preparar la cadena para una producción en masa y acelerar el tiempo de lanzamiento del producto al mercado.
Cómo lanzar mejores productos al mercado más rápido
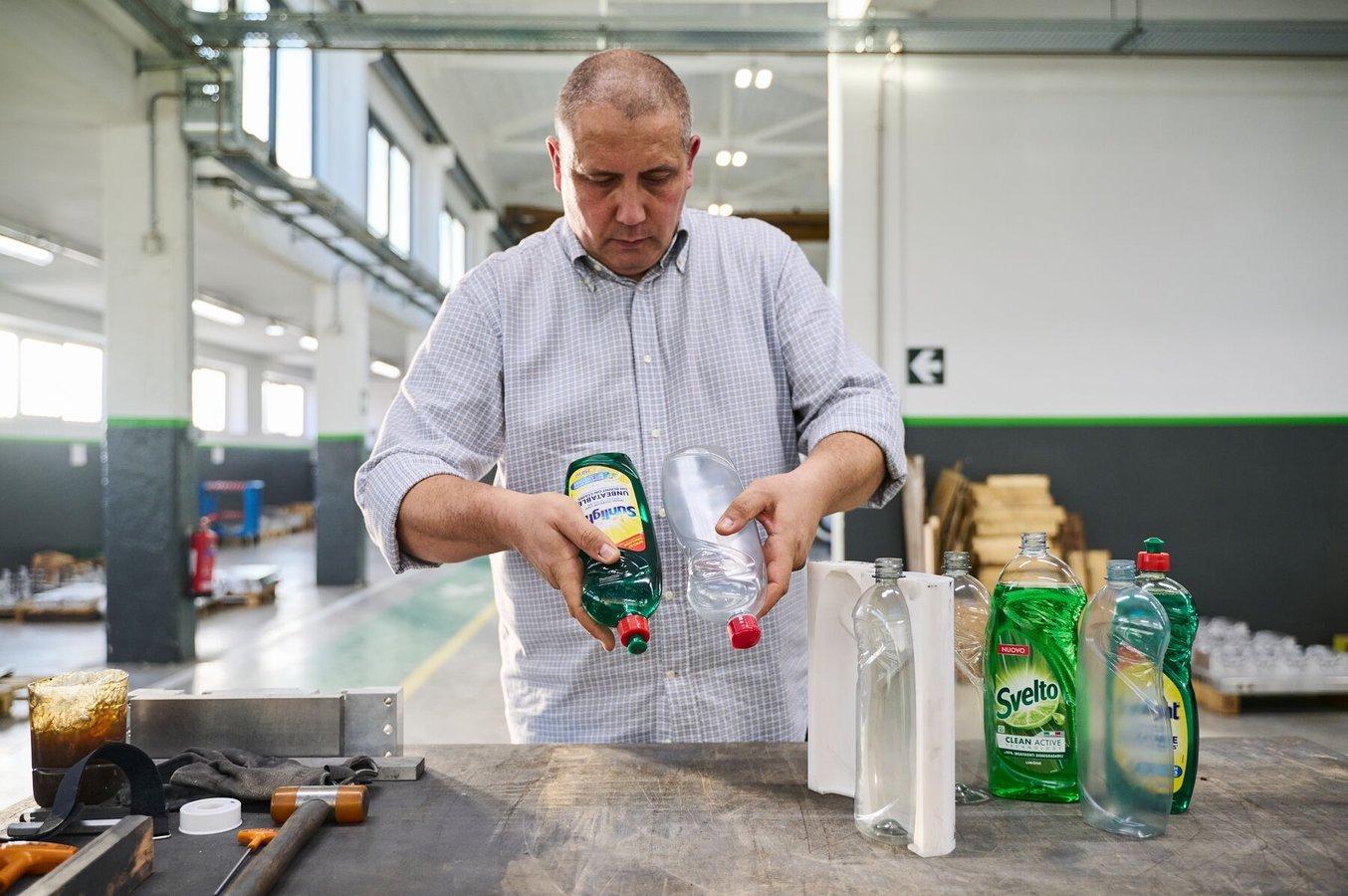
Cademartiri y Serioplast ya han puesto a prueba unos 15 modelos diferentes de botellas con el nuevo proceso.
Con las impresoras SLA de Formlabs y la Rigid 10K Resin, Unilever y Serioplast pudieron reducir los tiempos de espera hasta un 70 % y los costes de utillaje hasta un 90 %, para producir remesas piloto de 200 unidades en solo dos semanas.
"Formlabs ha sido un socio fantástico no solo por vender la máquina, sino también por apoyarnos a la hora de descubrir las propiedades de estos materiales. Esta colaboración me ha ayudado a identificar la posibilidad de iniciar este viaje con los moldes impresos en 3D", dijo Cademartiri.
El nuevo proceso de trabajo permitirá a Unilever lanzar productos mejores al mercado con mayor rapidez y reducirá drásticamente los riesgos y los costes asociados con el desarrollo de embalajes.
"El gran impacto que ha tenido la impresora 3D es la posibilidad de hacer que un sueño se haga realidad. Algo que está en la pantalla está en nuestras manos en un par de semanas. Un producto real con una botella real, con un tapón real y la etiqueta real", dijo Cademartiri.
¿Tienes dudas acerca de cómo utilizar una impresora SLA para el moldeo por soplado u otras aplicaciones de ingeniería y fabricación? Descarga nuestro libro blanco para conocer los detalles del proceso de trabajo, ponte en contacto con nuestros especialistas en soluciones o solicita una pieza de muestra gratuita impresa con la Rigid 10K Resin.