Cómo XSPECTER combina las piezas de uso final impresas en 3D mediante SLA y SLS para fabricar el trípode de su cámara exterior
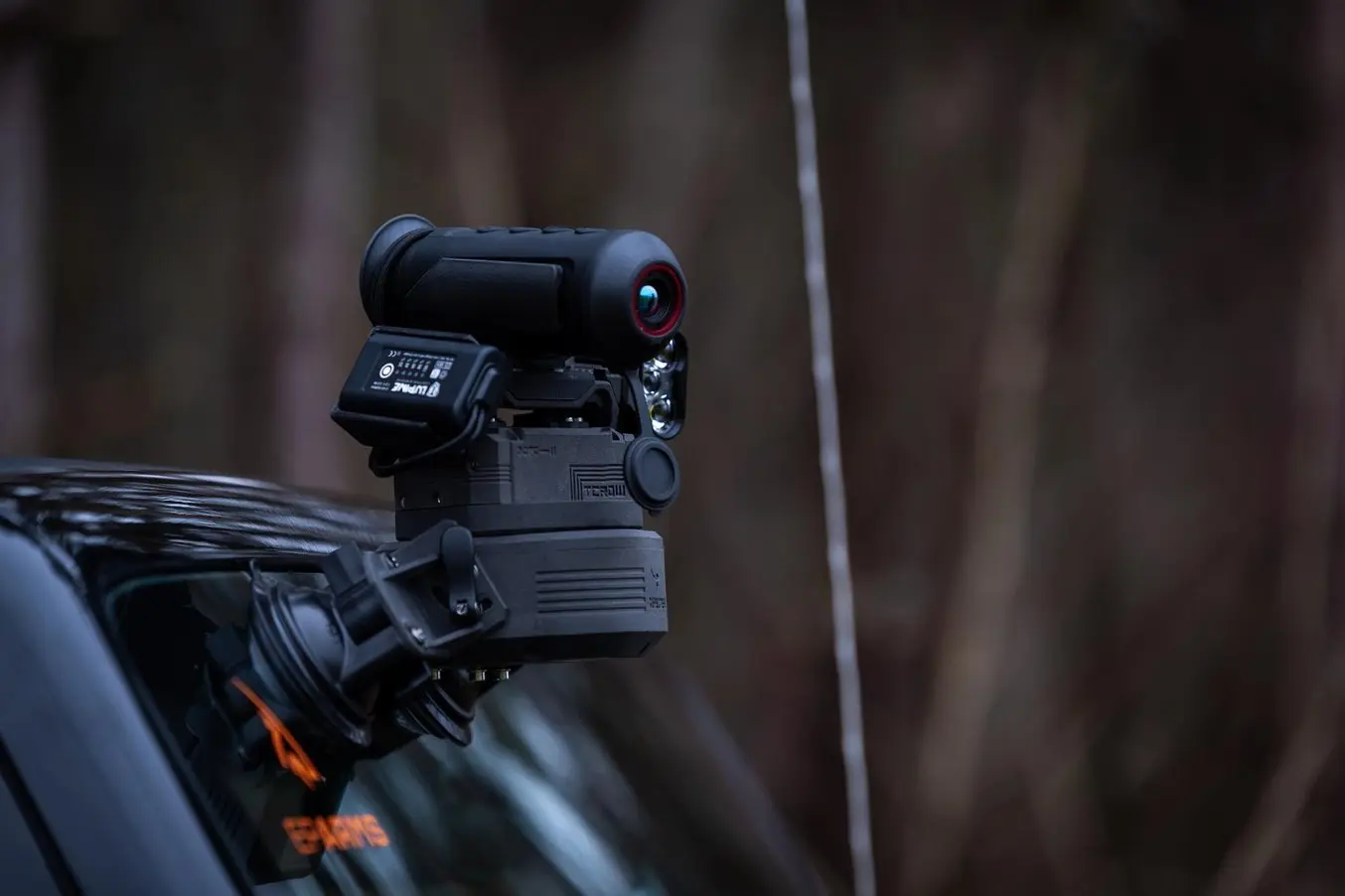
Con una idea innovadora y mucha motivación, muchos emprendedores ya han logrado llenar huecos en el mercado. Tras no poder encontrar nada similar, Matthias Mähler tuvo la idea de construir el primer prototipo de un trípode especial para cámaras de visión nocturna y dispositivos portátiles de imagen térmica.
Uno de los principales desafíos era poner en práctica un diseño de producto complejo, que habría requerido una inversión inicial de más de 100 000 € en utillaje si hubiera elegido el moldeo por inyección. Sin un conocimiento previo de cómo rendiría el producto en el mercado, esto habría sido muy arriesgado para una startup pequeña. Sin embargo, recurrir a la impresión 3D para desarrollar y después fabricar el trípode hizo posible evitar esta inversión tan cuantiosa. Ahora, su empresa XSPECTER fabrica su primer trípode de cámara completamente desarrollado de modelo T-CROW XRII in situ y lo está vendiendo con éxito a través de un socio exclusivo.
En una entrevista, Mähler nos contó cómo un producto acabado se puede fabricar utilizando una combinación de diferentes tecnologías de impresión 3D y por qué eligió este proceso.
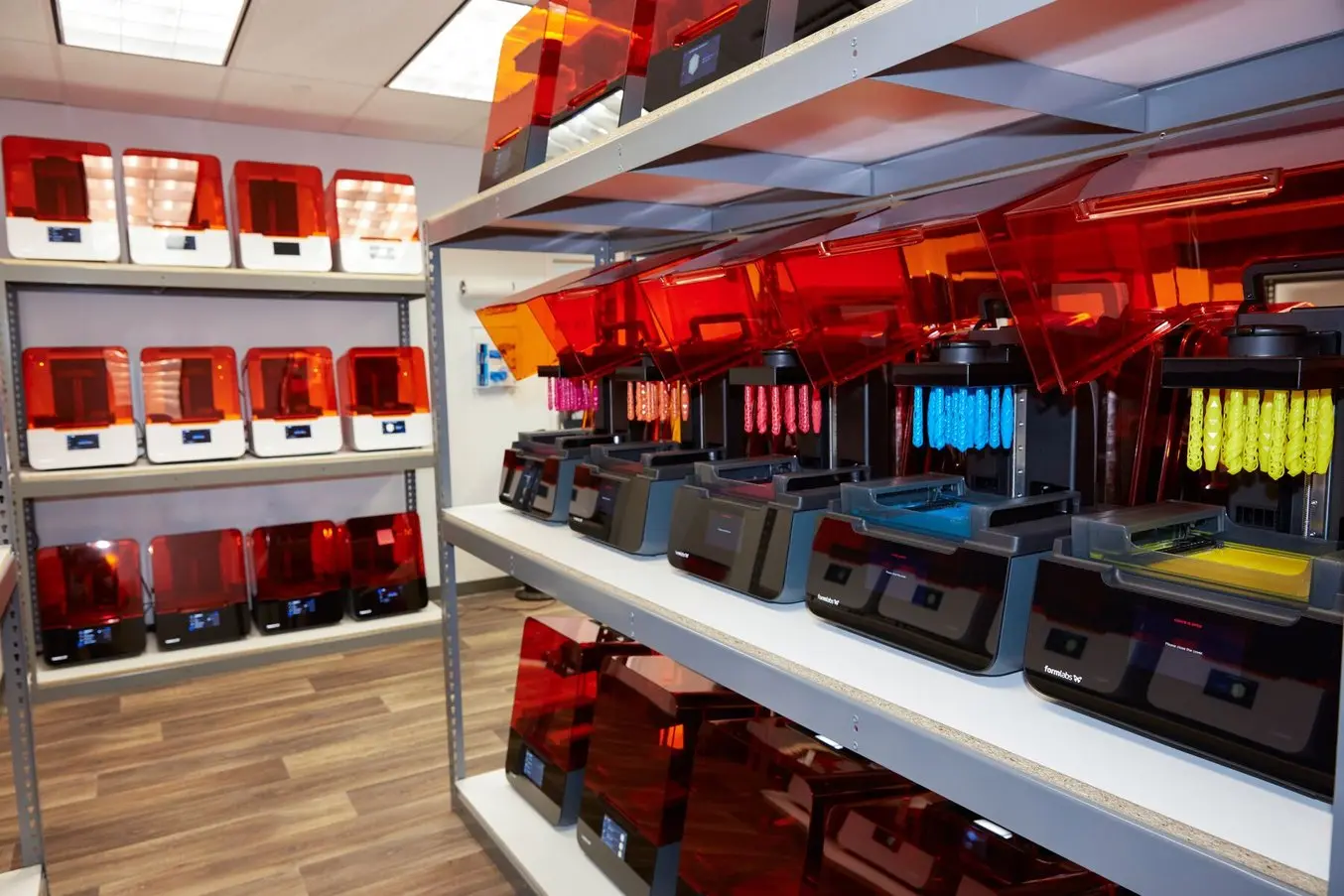
Cómo acceder a la producción de bajo volumen y la fabricación personalizada con piezas de uso final impresas en 3D
Ve este seminario web para conocer cómo puedes acceder a la fabricación personalizada y la producción de bajo volumen de piezas de uso final de forma rápida y rentable con la impresión 3D.
El desarrollo de un trípode de cámara controlable de 360°
Los aparatos de imagen térmica y visión nocturna son herramientas habituales para los cazadores, los pilotos de barcos y los trabajadores del sector de la seguridad. El problema es que los dispositivos no funcionan a través de cristal o ventanas. Cuando se conduce un coche por la noche, esto significa que los conductores tienen que sostener el dispositivo fuera de la ventana abierta con la mano o salir una y otra vez del vehículo.
Matthias Mähler, que además de emprendedor es cazador en su tiempo libre, buscaba una solución adecuada para montar sus aparatos en el exterior de su vehículo.
Tras darse cuenta de que no había ningún soporte ni trípode que sirviera en el mercado, decidió crear una solución él mismo. Empezó por crear el prototipo de un trípode controlable y estabilizador para dispositivos de visión nocturna e imagen térmica, que se pueden colocar en el techo o en la ventana de un coche utilizando ventosas o pies magnéticos.
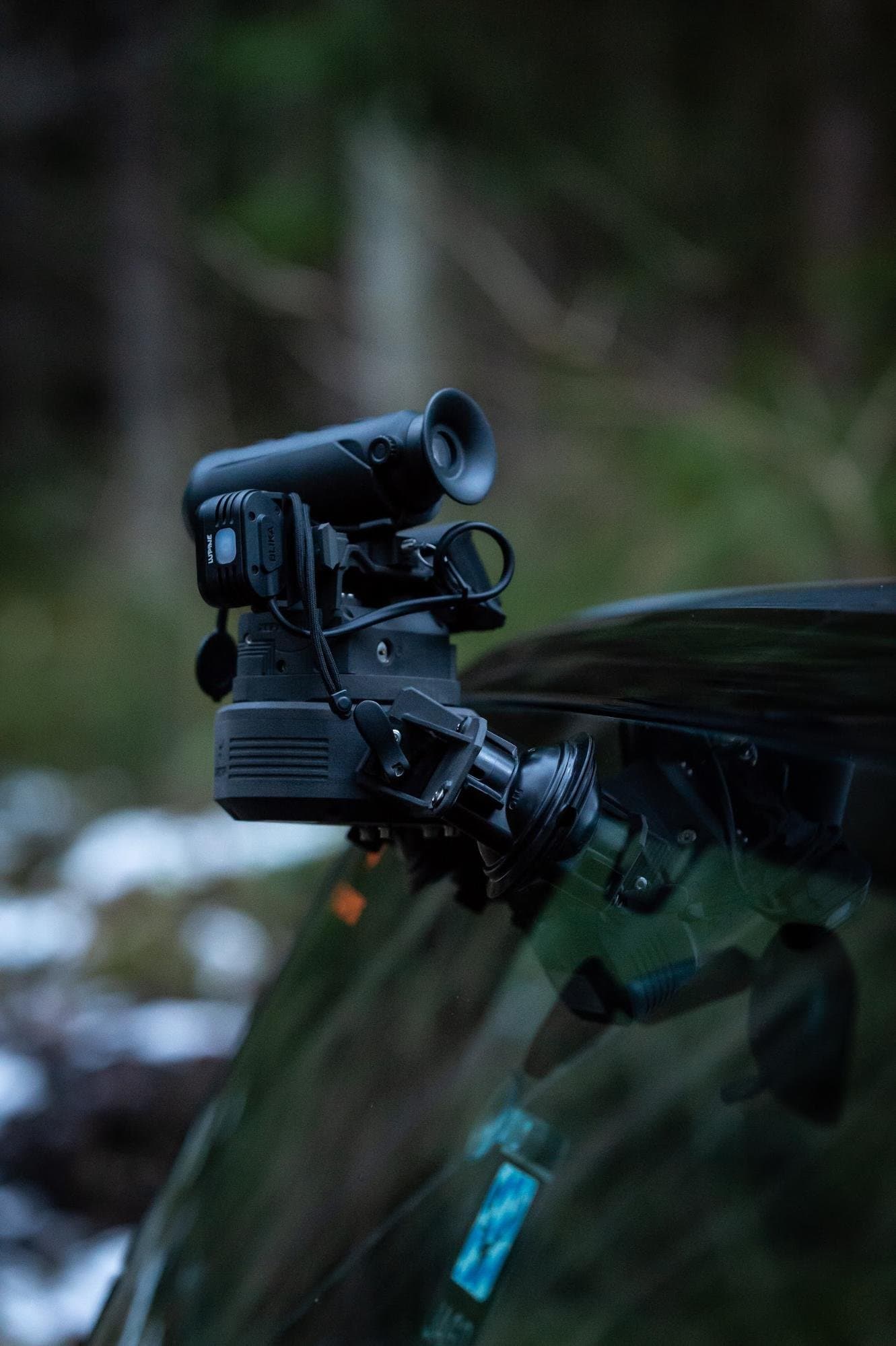
El T-CROW XRII con diferentes cámaras en la ventana del coche (izquierda) y sobre el techo del coche (derecha).
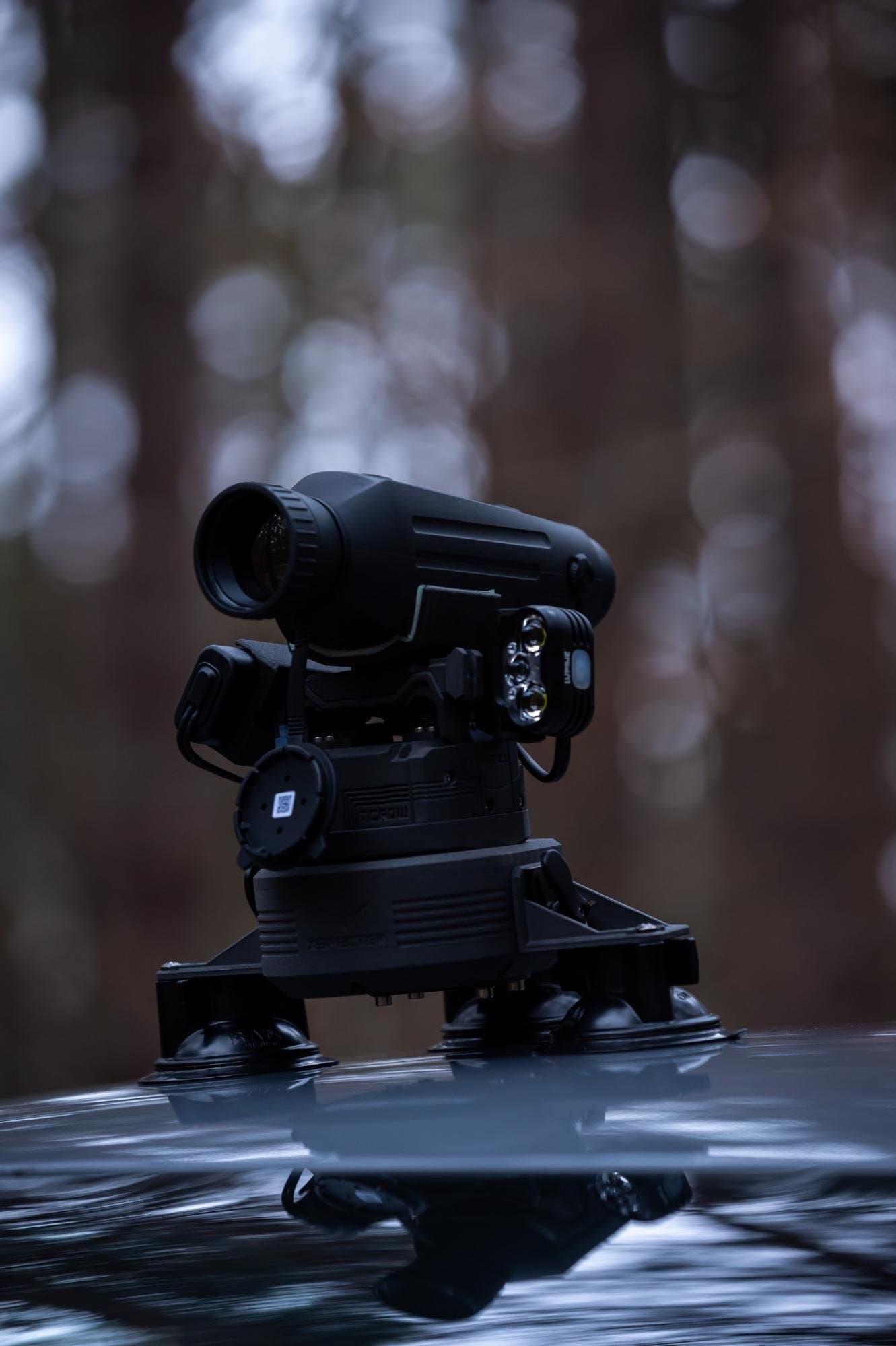
Con una rotación de 360° y un intervalo adicional de inclinación de 55°, el trípode T-CROW de XSPECTER permite rastrear animales y obstáculos con comodidad desde el interior del vehículo.
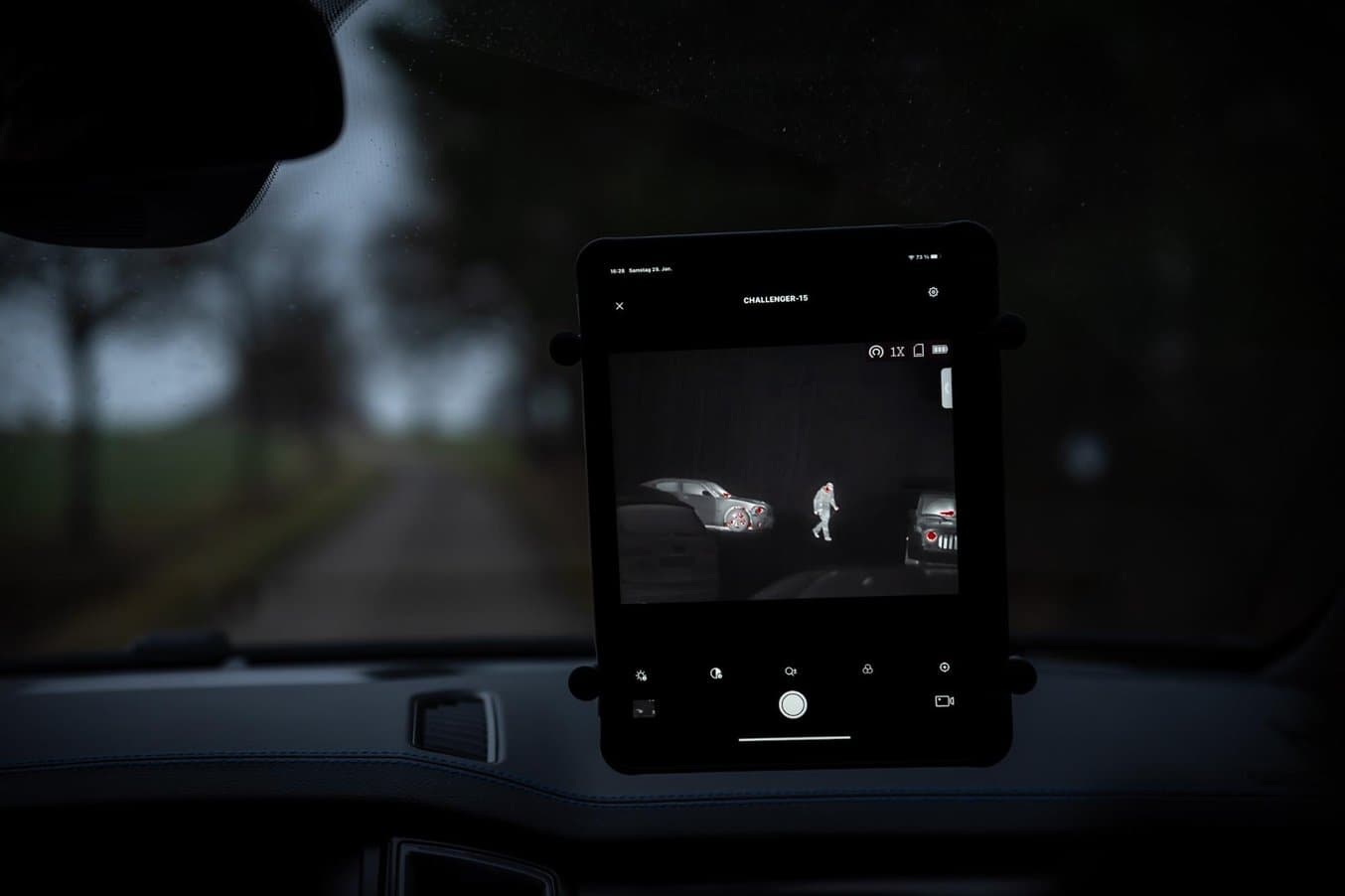
La imagen térmica en la pantalla de una tableta dentro del coche.
Desde los prototipos hasta la producción en serie
"La impresión 3D se integró en mi cadena de producción porque utilicé estas tecnologías para producir los prototipos. Funcionó tan bien que acabamos diseñando todo el producto utilizando diversas tecnologías de impresión 3D y seguimos produciéndolo con la impresión 3D hoy", dice Mähler.
Para empezar, Mähler realizó iteraciones de varios prototipos del trípode en colaboración con proveedores de servicios de impresión 3D en impresoras FDM. Una vez que el diseño preliminar del producto estuvo decidido, contactó con el socio de Formlabs AMPro 3D en busca de consejo sobre qué tecnologías y materiales de impresión 3D serían adecuados para la primera producción en serie.
"Lo adaptamos todo al proceso de SLS, porque el gran nivel de detalle y la ausencia de estructuras de soporte dan muchas más opciones en la impresión SLS. Pasamos casi directamente del prototipo a la producción en serie".
Matthias Mähler
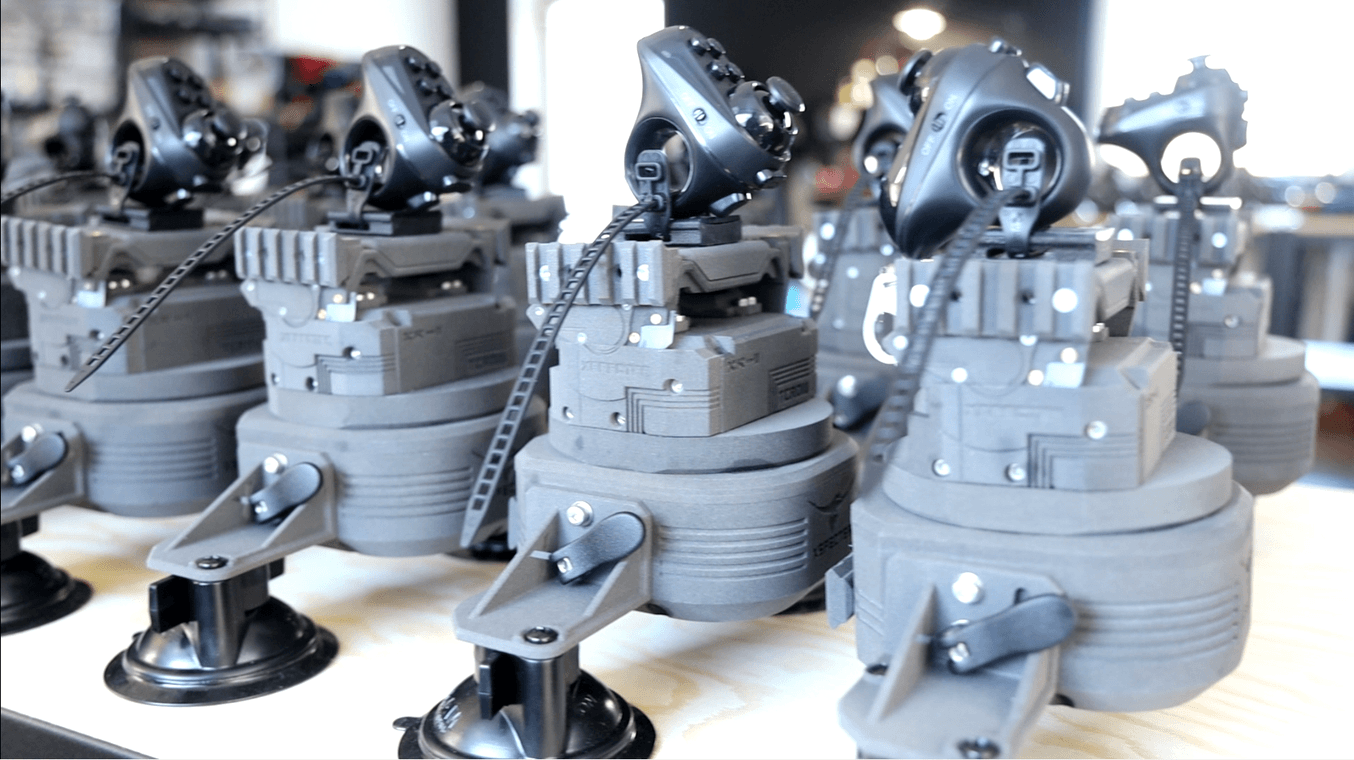
Un trípode T-CROW listo para su envío con el bastidor producido con el Nylon 12 Powder.
Eligió la impresora 3D SLS Fuse 1 y la impresora 3D SLA de gran formato Form 3L de Formlabs para iniciar la producción en masa de trípodes T-CROW utilizando piezas de uso final impresas en 3D.
"Creo que las impresoras 3D de Formlabs son realmente las mejores impresoras que están disponibles actualmente en el mercado en cuestión de su relación calidad-precio".
Matthias Mähler
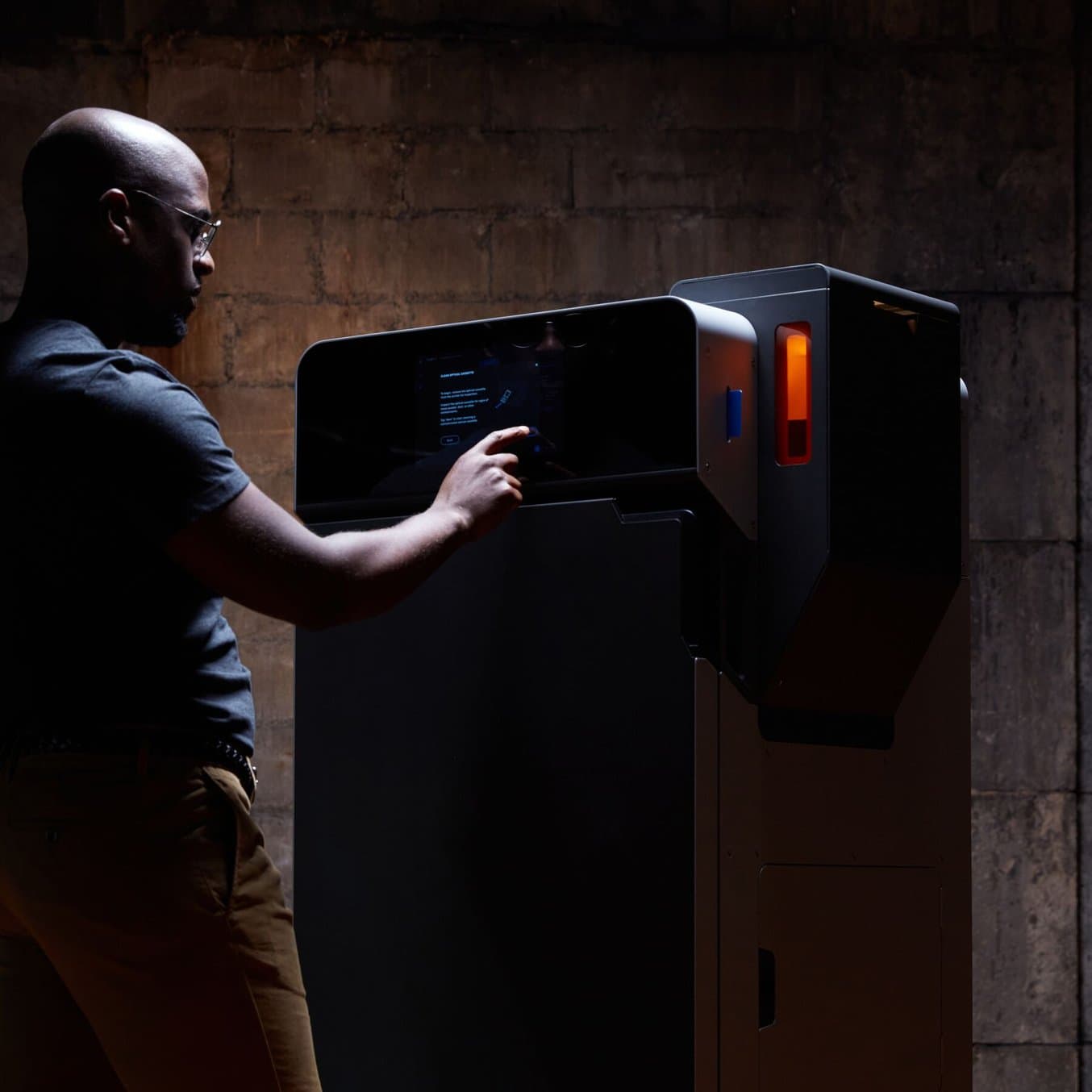
Externalización vs. internalización: ¿cuándo tiene sentido realizar la impresión 3D SLS en la propia empresa?
En este libro blanco, evaluamos la propuesta de valor de incorporar las impresoras 3D SLS en tus instalaciones, en comparación con la externalización de piezas de SLS a una empresa de servicios.
Producción en serie con una combinación de impresión 3D SLA y SLS
Para fabricar los T-CROW, XSPECTER utiliza una combinación de impresión 3D SLA y SLS para producir casi todos los componentes del trípode de cámara impreso en 3D, excepto los electrónicos.
La carcasa se fabrica en la Fuse 1. Gracias al material de Formlabs Nylon 12 Powder, la carcasa no deja de ser ligera y es resistente a los impactos del entorno. También es muy adecuado para fundir insertos roscados durante el ensamblaje.
Para los ejes y engranajes, XSPECTER utiliza su Form 3L y la Durable Resin. La flexibilidad, la resistencia a los impactos y la baja fricción del material permiten instalar ajustes de presilla, que son necesarios para el sistema de control de dos ejes.
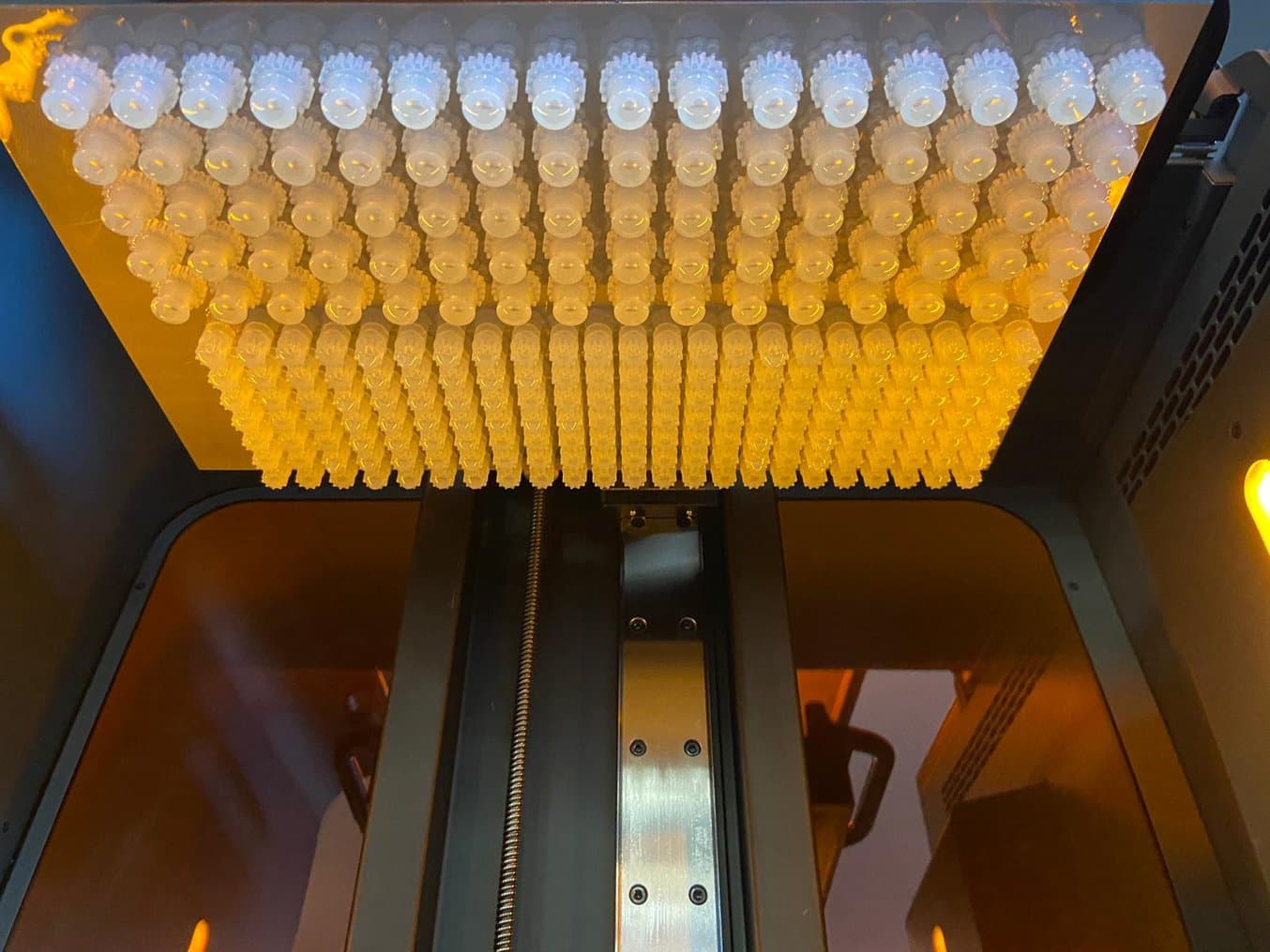
Engranajes para el T-CROW hechos de Durable Resin en la Form 3L.
Después de que todas las piezas se hayan impreso y posacabado in situ, se ensamblan utilizando los insertos roscados y están completamente preparados para su envío en tres días.
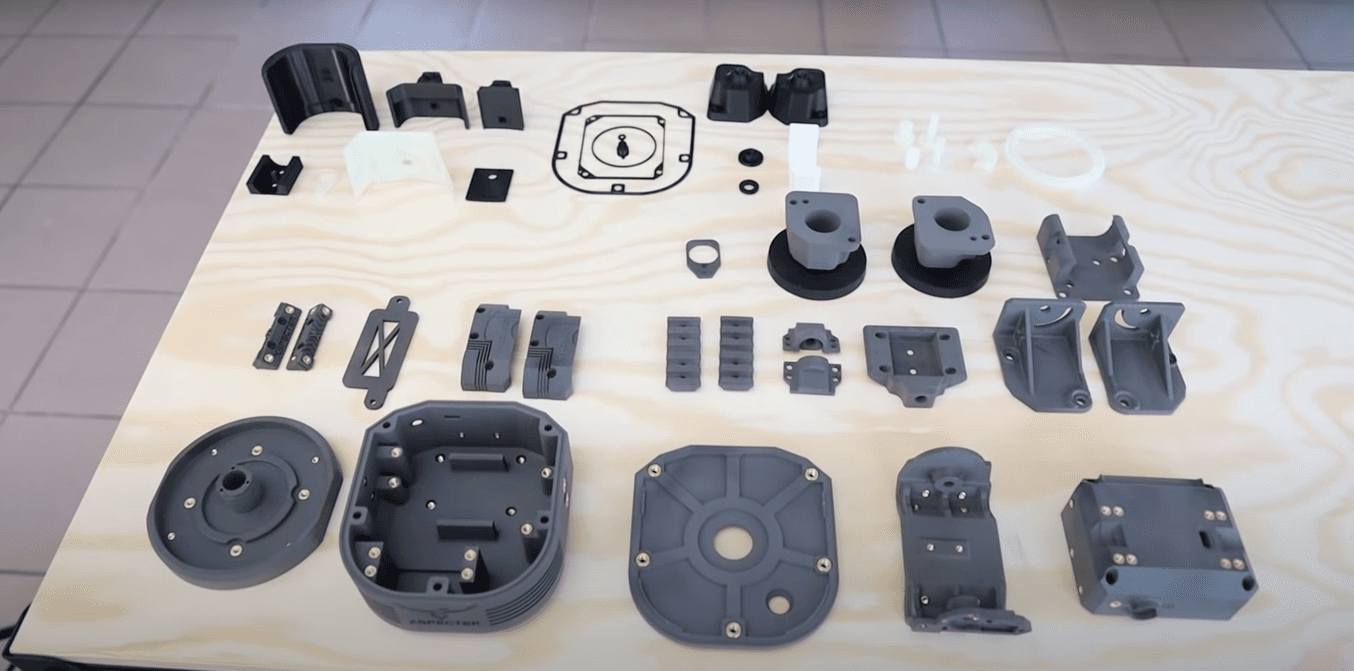
Todos los componentes impresos en 3D del T-CROW antes del ensamblaje.
"Con las impresoras que tenemos actualmente, podríamos producir 1500 T-CROW completos listos para enviar en un año", dice Mähler.
Flexibilidad de diseño gracias a la impresión 3D
Una ventaja fundamental y un factor clave a la hora de tomar decisiones para la producción mediante impresión 3D in situ es la enorme flexibilidad que se obtiene.
"Con la impresión 3D, simplemente tenemos más libertad de diseño que con los métodos convencionales como el moldeo por inyección. Llamamos a esto un producto vivo. Si encontramos un fallo de diseño o recibimos opiniones de los clientes, podemos implementar una nueva iteración de un día para otro. Eso no se puede hacer con ningún otro método".
Matthias Mähler
Un ejemplo de cambios de diseño de este tipo son los que se realizan al personalizar los adaptadores de cámaras diferentes para que los trípodes se puedan utilizar de forma universal. Los diferentes elementos de diseño se integran directamente en el bastidor impreso en 3D. Cuando se lanza una cámara nueva al mercado, Mähler puede realizar rápidamente los cambios correspondientes en su trípode T-CROW y venderlo.
XSPECTER también pudo ahorrar una ingente cantidad de tiempo y dinero reaccionando más rápido a los cambios en los proveedores de piezas concretas gracias a la flexibilidad de la impresión 3D.
"Una vez dejé de recibir el interruptor de encendido de nuestro proveedor original y me vi obligado a cambiar a otro. Para nosotros, eso significaba que había que agrandar la abertura del interruptor de encendido dos milímetros, un cambio que realicé prácticamente de un día para otro", explica Mähler.
Con un utillaje para impresión 3D que se presupuestó en 120 000 € para empezar, una modificación de ese tipo en el molde original habría requerido considerablemente más tiempo y dinero.
En mi opinión, la impresión 3D está marcando tendencia, especialmente si una empresa quiere incluir opiniones de los clientes en sus productos. Aunque ya estamos en una fase de producción en serie, seguimos desarrollando constantemente nuestros trípodes en función de las opiniones que recibimos".
Matthias Mähler
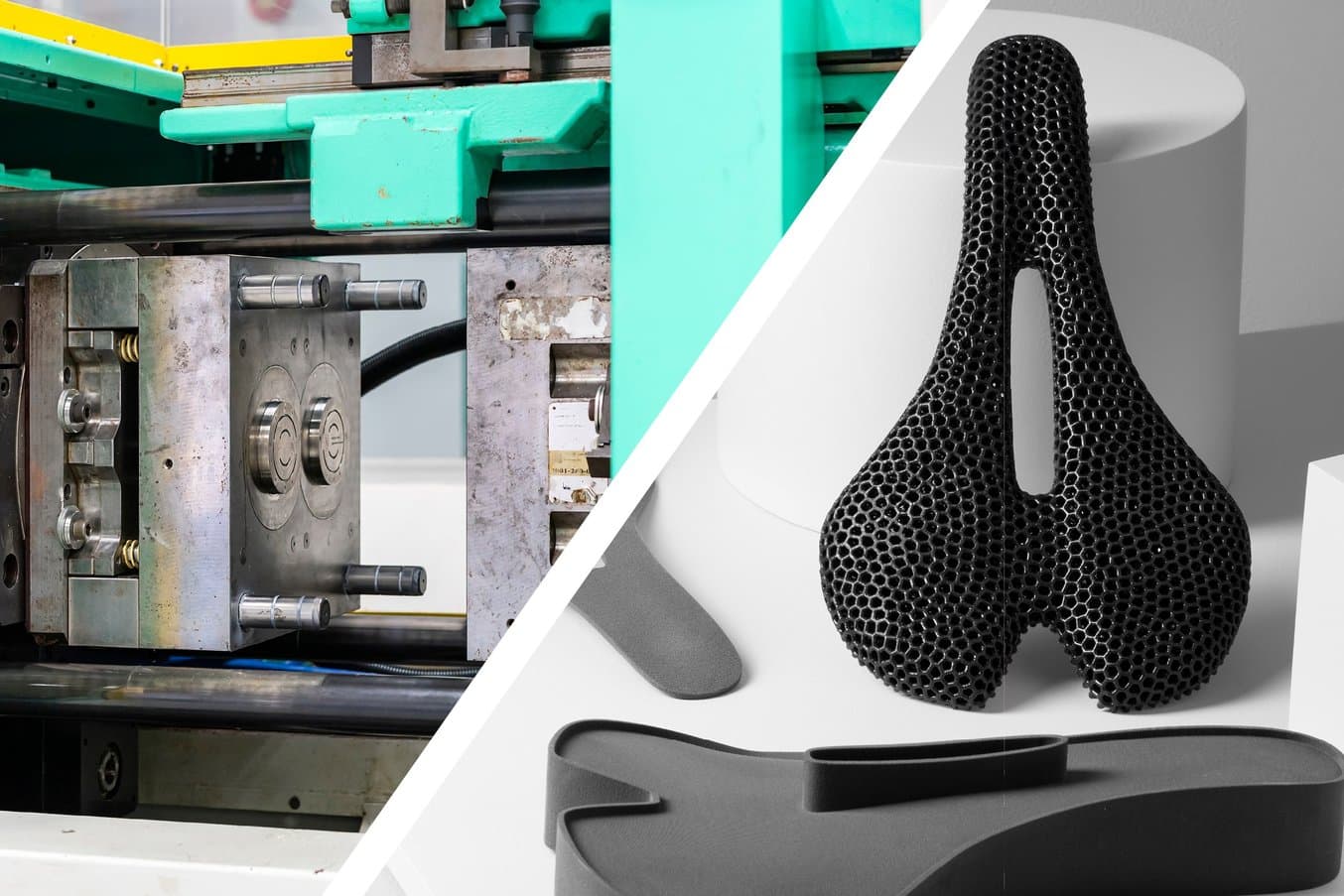
Impresión 3D SLS vs. moldeo por inyección: ¿Cuándo se deben reemplazar las piezas moldeadas con la impresión 3D?
Este libro blanco muestra los costes de casos de uso reales y ofrece recomendaciones para usar la impresión 3D SLS, el moldeo por inyección o ambos.
Dado que XSPECTER obtiene la misma cantidad por un coste por pieza más bajo con la impresión 3D que con el moldeo por inyección y su estrategia depende en gran medida de la flexibilidad de la impresión 3D SLS, Mähler no puede imaginar ninguna otra tecnología de fabricación para su producto en el futuro cercano.
Mientras tanto, Mähler ya está trabajando en su siguiente proyecto, llamado Sea-Crow: una variante marítima del trípode de cámara, que también incluye focos y sirve como ayuda para la navegación en el agua por la noche.