Ashley Furniture : D'une simple idée à l'impression de 700 pièces en 3D dans l’usine
Peu après qu’Ashley Furniture ait installé la première imprimante 3D stéréolithographique (SLA), l’un de leurs ingénieurs de production a eu une idée. Était-il possible de remplacer des chevilles de positionnement usinées par des pièces imprimées en 3D ? Ces pièces finales permettraient d’éviter les longs délais de réalisation et les quantités minimales de commande applicables avec l’externalisation.
La réponse était oui mais elle a donné lieu à davantage de questions.
Aujourd’hui, environ deux ans et une imprimante supplémentaire plus tard, ce sont 700 pièces imprimées en 3D qui sont utilisées dans l’usine d’Ashley Furniture à Arcadia, Wisconsin, au milieu des robots industriels et des fraiseuses à commande numérique à toute épreuve, de l’assemblage à la fabrication.
Les employés de l’entreprise entière continuent de poser des questions et de soumettre des idées et l’entreprise continue de croître.
Regardez cette vidéo pour apprendre pourquoi et comment Ashley Furniture, le plus grand fabricant de meubles au monde, a intégré de nouvelles technologies dans ses usines, de l’impression 3D à la robotique.
La recette du succès en fabrication
Ashley Furniture est le plus grand fabricant de meubles au monde et malgré les difficultés que représente la récession du marché du travail, l’entreprise a continué sa croissance.
« Nous avons augmenté la production de 10 % rien qu’à Arcadia, avec une baisse de presque 15 % de l’occupation du personnel, » a déclaré Vaughn Pieters, directeur principal pour les meubles de rangement.
Avec une culture qui encourage les employés à participer activement aux processus d’optimisation continue, Ashley Furniture se sert des technologies de pointe pour remplacer la main-d’œuvre et maximiser la valeur du personnel en puisant les optimisations de processus et les innovations auprès des personnes les plus proches du travail.
« L’automatisation nous a vraiment permis d’éliminer le côté lourd qui caractérisait la fabrication ces dernières 50-60 années. Nous n’avons plus d’employés assignés à ce travail lourd toute la journée. Nous laissons les machines s’en charger. Nous laissons les employés se servir de leur cerveau et essayer d’améliorer le processus, » a ajouté Pieters.
« Nous avons installé notre premier robot il y a cinq ans, et maintenant, vous pouvez voir lors de la visite de notre usine à quels autres postes nous avons intégré l’automatisation. L’impression 3D a suivi ce type de croissance aussi. »

Du prototypage en interne aux gabarits, fixations et outillage
Durant les 30 dernières années, Brian Konkel, ingénieur de production chez Ashley Furniture, a travaillé dans les départements conception, ingénierie et fabrication. Il a trouvé des opportunités de mise en œuvre l’impression 3D dans chaque discipline.
Avant d’intégrer l’impression 3D dans l’usine, Ashley Furniture avait déjà utilisé cette technologie en interne pour la fabrication de prototypes. En effet, l’entreprise a utilisé l’impression 3D durant des décennies, externalisant des pièces ici et là depuis les années 90. Cette expérience a débouché sur l’acquisition d’une imprimante à dépôt de filament fondu (FDM) peu onéreuse lorsque les volumes commandés ont commencé à augmenter.
L’entreprise a commencé à imprimer de plus en plus en interne, mais la qualité a commencé à poser problème. L’équipe a décidé de passer à la stéréolithographie à laser et a acquis l’imprimante 3D Formlabs Form 2.
« Nous avons réalisé que nous recherchions une surface de meilleure qualité et des tolérances plus serrées. L’impression 3D SLA sur la Form 2 nous a permis de créer des choses comme des éléments d’emboîtage élastiques pour différents composants de fixation, » a affirmé Konkel.
« L’une des qualités de la Form 2 est la variété des matériaux disponibles. Nous pouvons commencer à imprimer un composant, et si le matériau en question ne répond pas exactement à nos attentes, nous avons d’autres options en réserve. »
Les choses ont pris de l'ampleur une fois que l’équipe a introduit l’imprimante 3D Form 2 dans l’entreprise. Outre les modèles de prototypes, Konkel a trouvé des domaines où se servir de l’impression 3D pour la fabrication. Le volume d’impressions a tellement augmenté que six mois plus tard, l’entreprise a commandé une seconde imprimante.
« Actuellement, nous utilisons les deux imprimantes Formlabs au minimum 40 heures par semaine, » a précisé Konkel.
Le passage aux pièces imprimées en 3D pour la fabrication
L’impression des pièces était une solution rapide et à faible risque pour tester et mettre en œuvre des idées visant à booster l’efficience, qu’il s’agisse de gagner du temps et de réaliser des économies en créant des pièces de rechange en interne, ou de découvrir des solutions créatives qui ont fondamentalement changé l’organisation de l’usine.
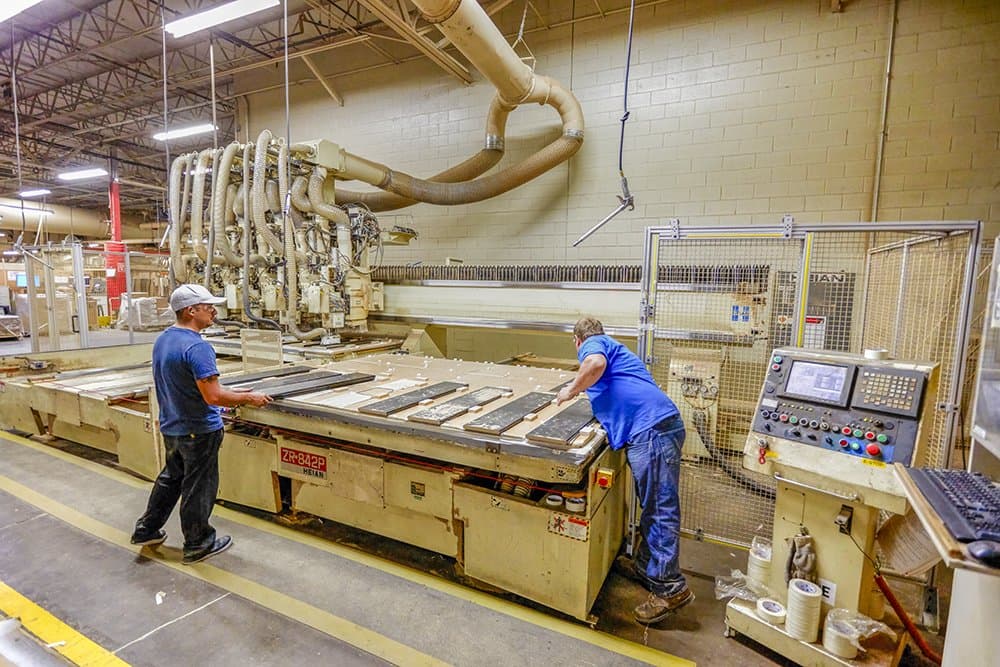
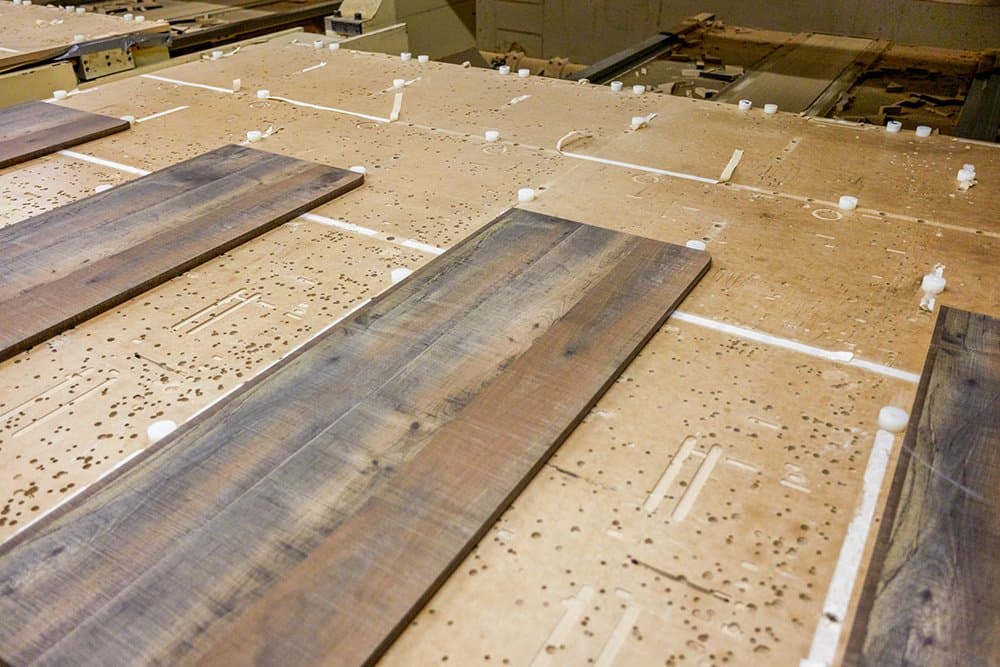
Rien que l’impression en 3D des chevilles de positionnement a permis de réaliser des économies de temps et d’argent considérables par rapport à l’externalisation des pièces en nylon.
« Avant, nous commandions [les chevilles] auprès d’un atelier d’usinage qui imposait une quantité minimale de commande très élevée, 1 200 pièces, et qui les fabriquait par enroulement sur un tour avec du nylon. Maintenant, nous sommes capables de nous passer de ce processus et de littéralement diviser le prix par deux, » a ajouté Konkel.
L’impression des pièces en interne a non seulement permis d’économiser des ressources pour l’externalisation, mais également du temps d’immobilisation pour les changements entre les tâches. Avant, un dispositif spécifique était créé pour chaque panneau. Désormais, les ouvriers utilisent une plaque de configuration pour déplacer rapidement les chevilles sur un simple quadrillage.
Comparaison des coûts : chevilles de positionnement
Externalisation auprès de l’atelier d’usinage | Impression 3D en interne sur la Form 2 | |
---|---|---|
Coût | Quantité min. de commande 1200 pièces, 8,80 € par pièce | Aucune quantité minimum, 5,20 € par pièce |
Délai de réalisation | 3 - 4 semaines | 15 h 30 min pour 16 pièces avec deux imprimantes |
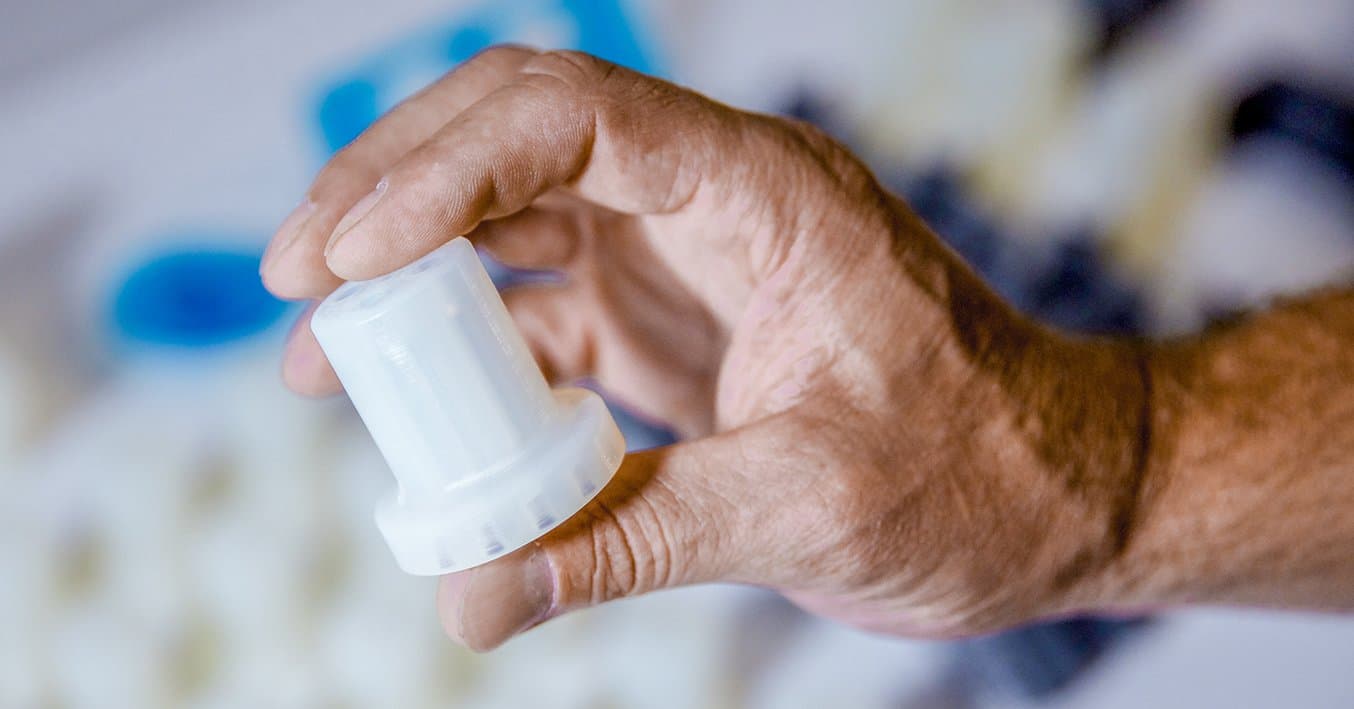
Un système universel pour montage d’assemblages
L’une des solutions les plus créatives de l’entreprise à ce jour est un système universel pour montage d’assemblages. De façon similaire au quadrillage de la table de découpe pour les chevilles de positionnement, l’équipe a créé un système de montage universel utilisant des pièces imprimées en 3D pour simplifier les ajustements entre les changements de produits. Il n’est donc plus nécessaire d’utiliser des ressources d’atelier d’usinage pour créer chaque système de zéro.
« Les pièces imprimées en 3D comblent les vides entre les différentes configurations », a ajouté Konkel.
Le système de montage universel de Konkel utilise des pièces imprimées en 3D pour simplifier les ajustements entre les changements de produits.
Désormais, après l’introduction d’une nouvelle unité de gestion des stocks, l’entreprise a uniquement besoin de modifier certaines dimensions sur des modèles solides existants pour concevoir et imprimer de nouvelles pièces afin d’adapter le système. À part cela, elle peut réutiliser toutes les configurations et géométries courantes. Les ouvriers chargés de l’assemblage suivent des guides d’instructions simples pour chaque changement, ils font glisser les actionneurs le long de rails verticaux pour les resserrer dans leur nouvelle position, et ils remplacent les anciennes pièces par de nouvelles pièces imprimées en 3D adaptées à la nouvelle configuration.
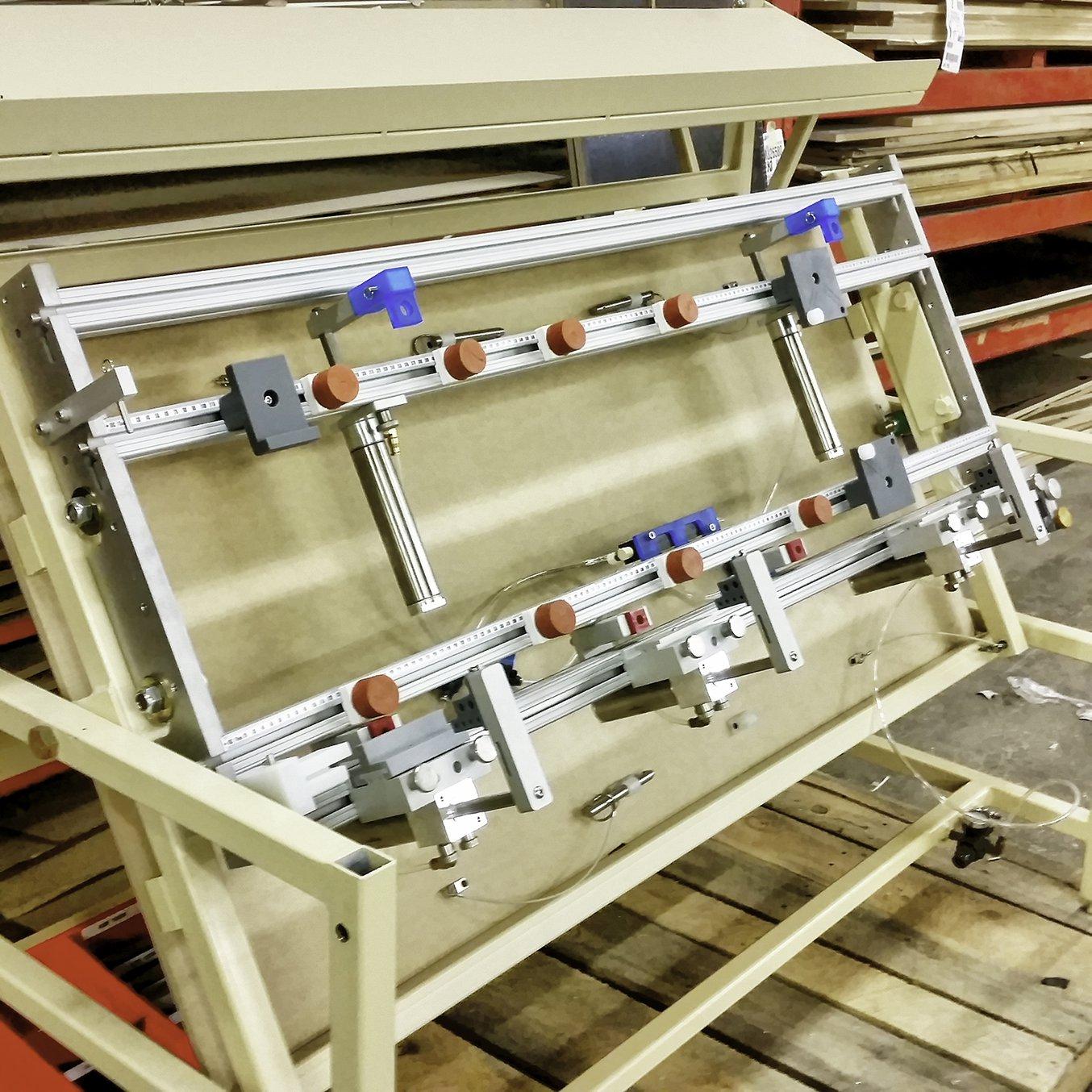
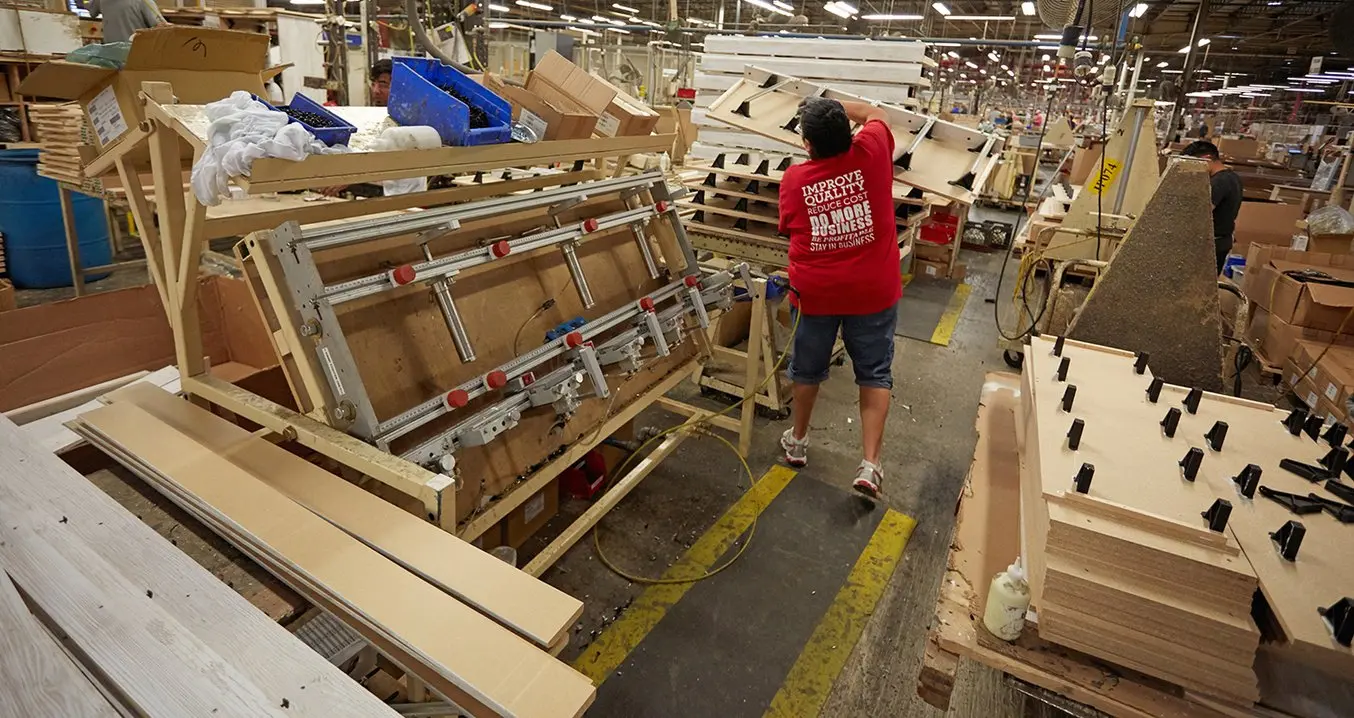
« Avec l’impression 3D, il est vraiment facile de remplacer [des pièces], mais nous avons été surpris par leur longévité ; certaines de ces pièces ont duré trois fois plus longtemps que ce à quoi nous nous étions attendus, presque neuf mois avant de devoir les remplacer, » a poursuivi Konkel.
« Par exemple, certaines de pièces sont utilisées une fois par minute, elles descendent et fixent un assemblage pour pouvoir le visser. »
Le système universel a considérablement réduit le temps de configuration dans la zone d’assemblage ainsi que l’empreinte du stockage des pièces de fixation d’origine qui pouvaient peser jusqu’à 200 livres (90 kg).
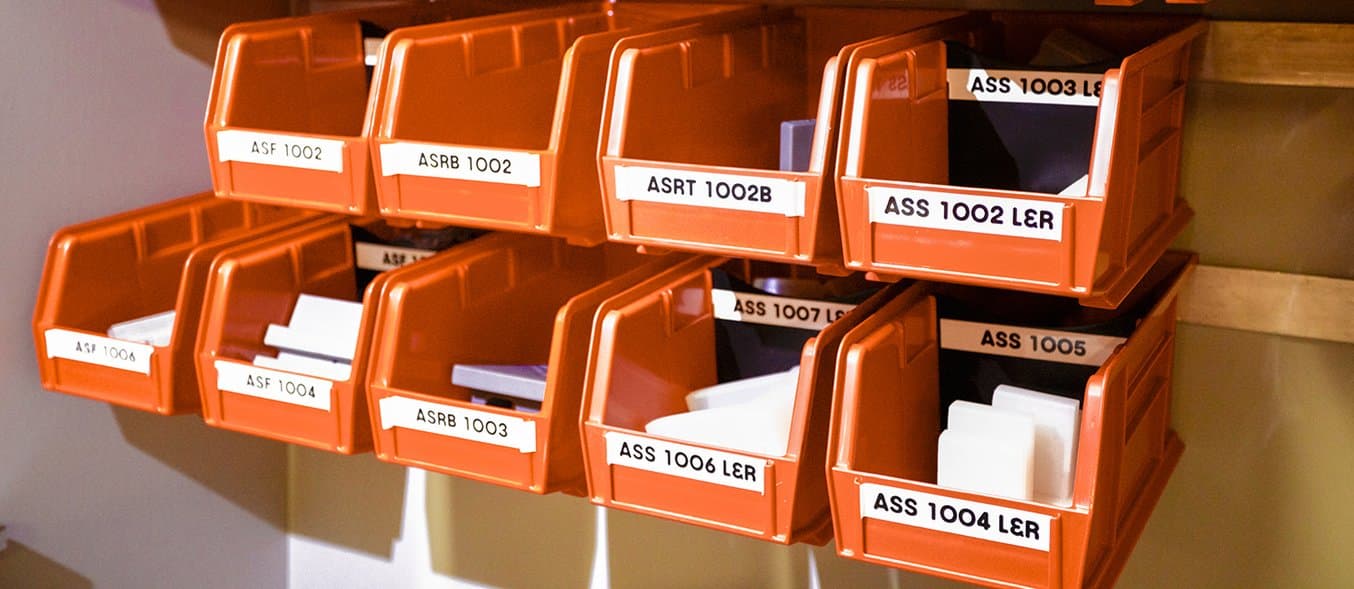
« Avant, nous construisions un gabarit à part pour chaque ligne de produits. En imprimant les pièces en 3D, il s’agit juste de remplacer des pièces pour nous adapter aux différentes unités de gestion des stocks. Nous avons littéralement remplacé des fixations de 3 pieds x 6 pieds (91 cm x 182 cm) par un simple système de bacs ; nous avons désormais un temps de configuration de deux minutes. », a ajouté Konkel.
« Cela permet aux constructeurs de gabarits d’éviter les tâches répétitives pour se concentrer sur des problèmes plus urgents, de quitter un rythme effréné pour l’étude d’éléments plus complexes. »
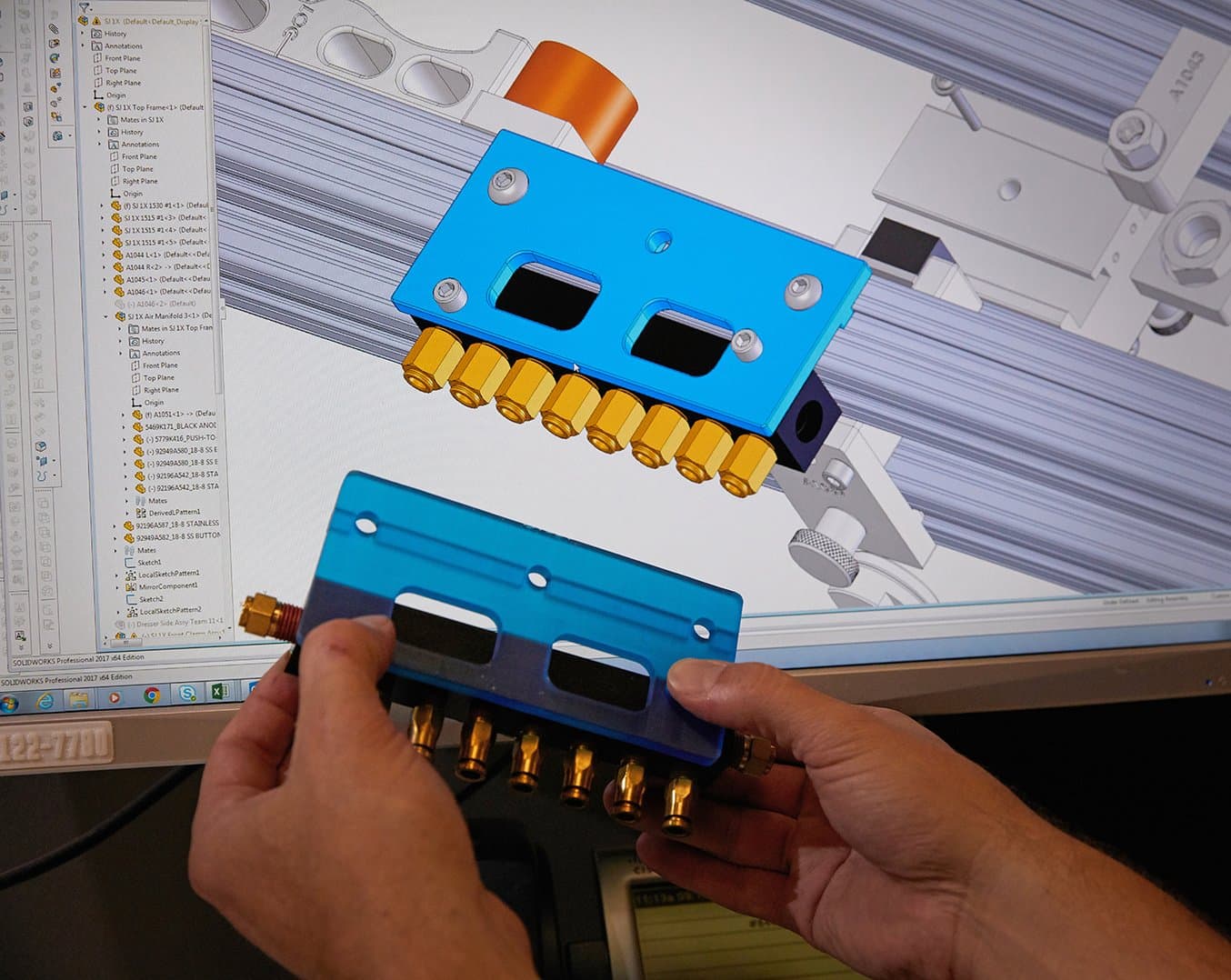
Outils sur mesure, et suppression de l’externalisation coûteuse pour les pièces de rechange
Nous avons réussi une amélioration facile et pratique avec une pièce de rechange. Il fallait remplacer une bague de retenue à vide pour une perceuse point à point mais il n’était pas possible de l’acheter seule. La seule option était d’acheter l’assemblage entier qui est très coûteux.
« L’entreprise ne voulait pas vendre la bague seule, nous aurions dû acheter la cellule entière pour 620 €, » a déclaré Konkel. « Au lieu de cela, nous avons pu réaliser un scan 3D de la pièce pour capturer la géométrie et imprimer une pièce de rechange pour moins de 1 € qui nous a permis de continuer à exploiter notre perceuse et de ne pas être obligés d’acheter l’ensemble complet. »
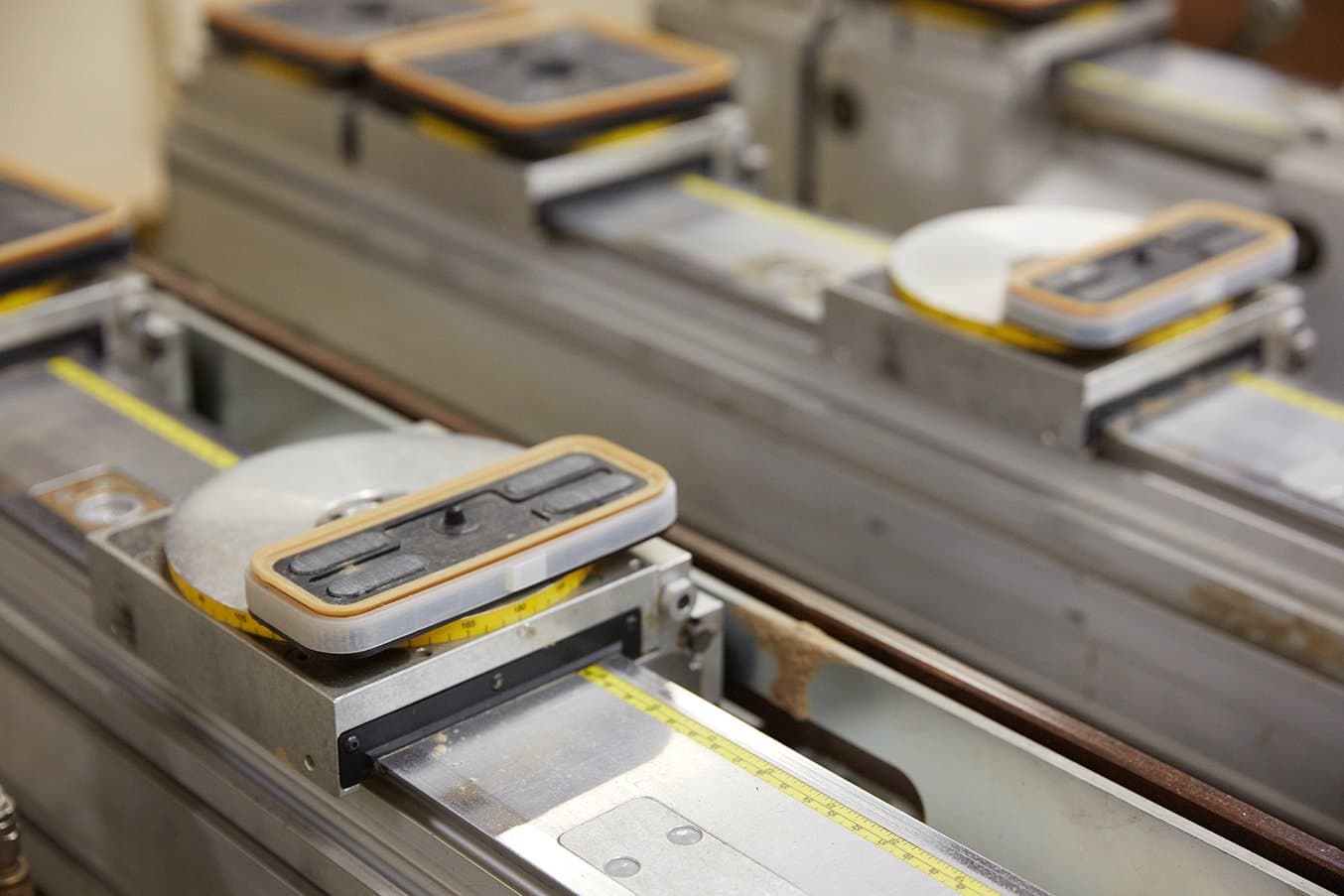
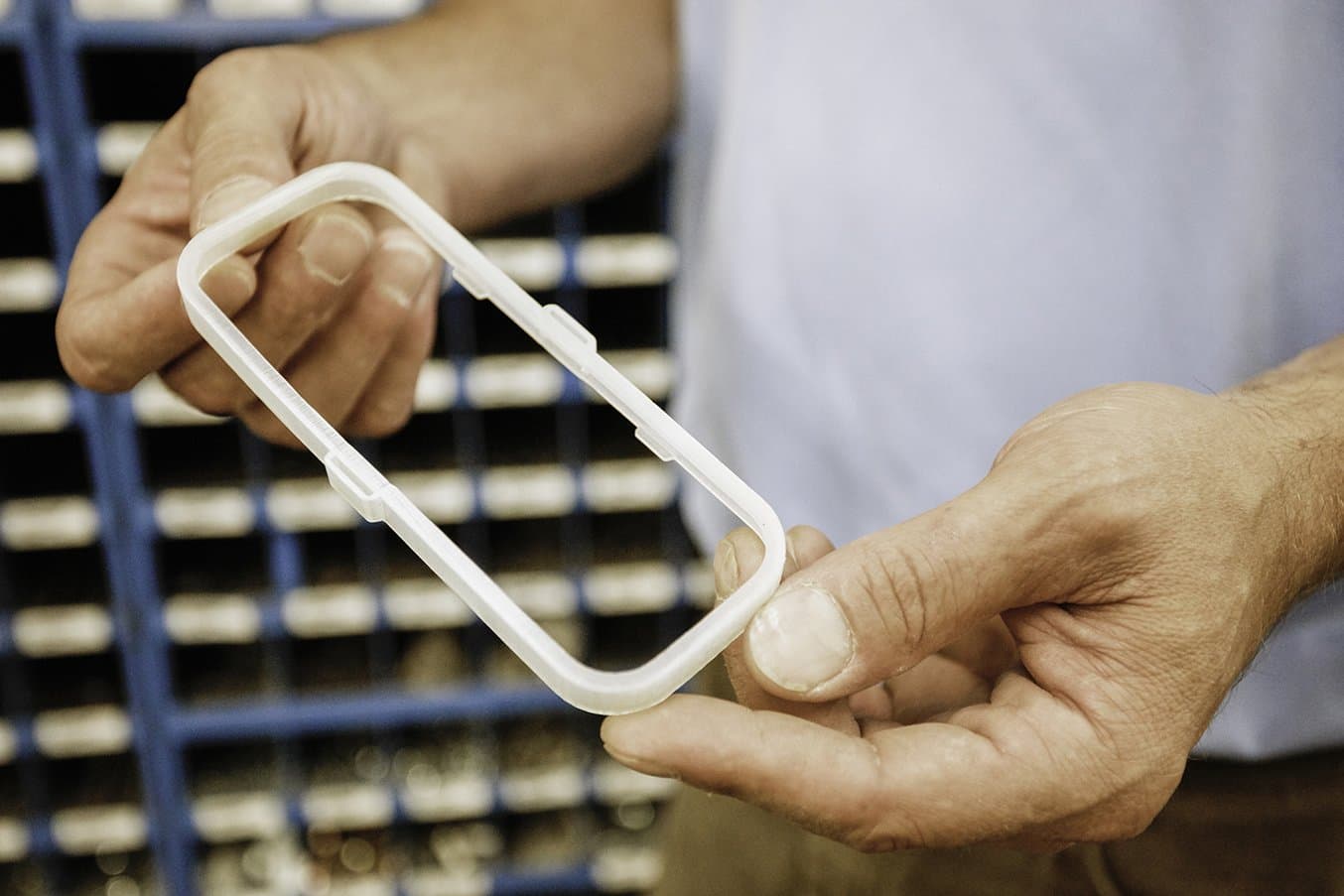
La Form 2 a également permis à l’équipe de créer des outils à main sur mesure comme un simple guide pour un pistolet à agrafes.
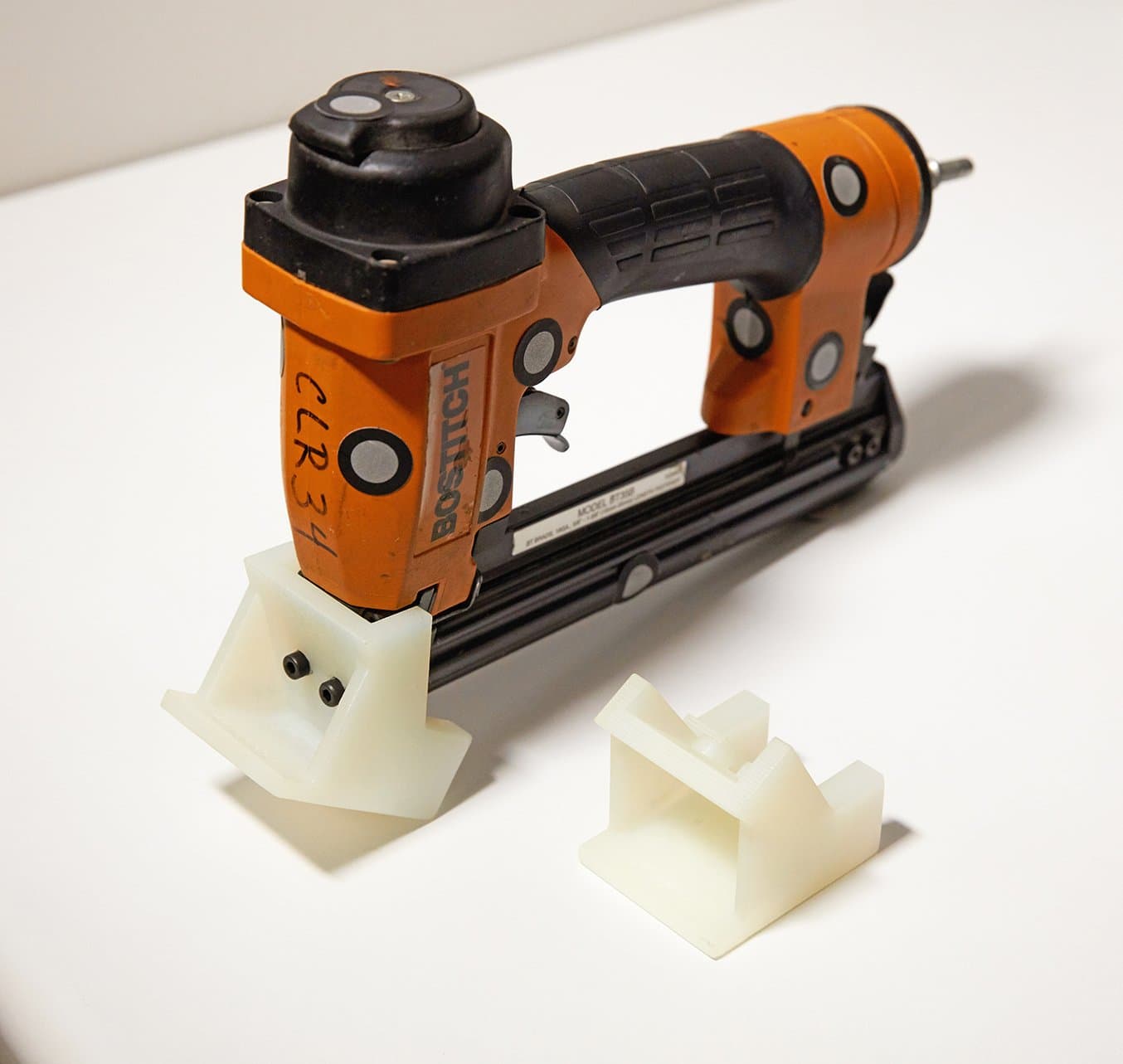
Explorez l’impression 3D pour la fabrication
Grâce à l’impression 3D en interne avec la Form 2, les employés d’Ashley Furniture ont davantage de moyens de résoudre les problèmes grâce à des solutions créatives et d’augmenter la productivité dans l’usine. L’équipe exploite les deux imprimantes 40 heures par semaine et l’entreprise continue d’explorer de nouvelles manières d’améliorer les processus.
« La Form 2 et la possibilité d’imprimer des pièces en 3D nous ont permis de nous éloigner de certains des processus traditionnels de développement des fixations et des outils, » a conclu Konkel.
« Cela nous permet de nous adapter rapidement à chacune de nos suggestions et à chacun de nos besoins et de créer des géométries que nous ne sommes pas traditionnellement en mesure de fabriquer ou d’usiner. Nous pouvons faire des choses qui étaient impossibles il y a quelques années. »