L’équipementier automobile international Brose se tourne vers l’impression 3D SLS pour produire des pièces finales
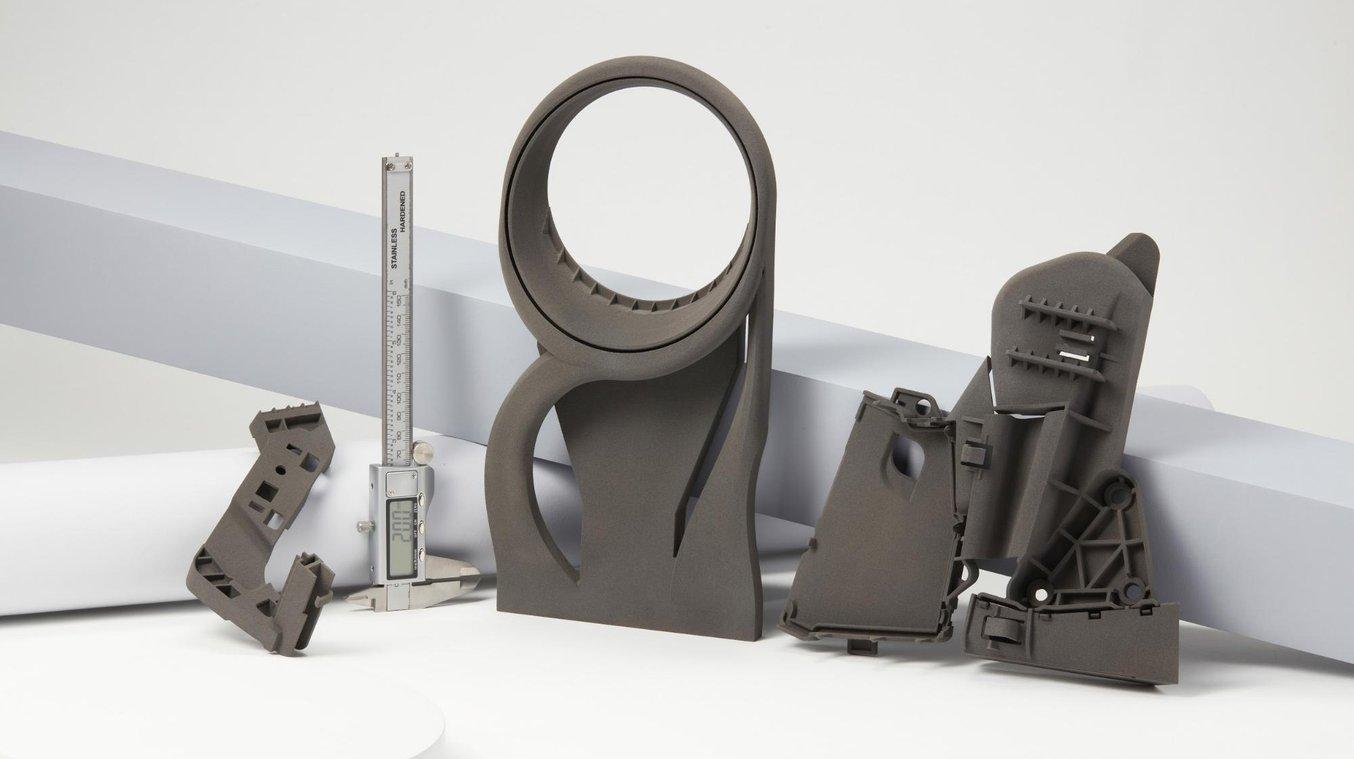
Dès que vous vous asseyez dans une voiture, il est pratiquement certain que vous interagissiez avec un produit Brose. Brose est l’une des plus grandes entreprises familiales d’équipementiers automobiles Tier 1 au monde. Cette société est implantée dans 24 pays, emploie 25 000 employés, travaille avec 80 marques d’automobiles, 50 fabricants de vélos électriques, et plus de 40 fournisseurs.
Un véhicule neuf sur deux produit dans le monde est équipé d’au moins un produit Brose, qu’il s’agisse de systèmes ou de composants mécatroniques, comme des structures de sièges, des composants de portière ou encore divers moteurs et entraînements électriques.
Brose est l’une des entreprises allemandes des plus innovantes. Elle se trouve en excellente position pour intégrer la fabrication additive à son processus de fabrication et ses produits. Elle utilise diverses technologies de fabrication additive pour le prototypage, l’outillage et les fixations, et son prochain objectif est d’appliquer ces technologies à la production en série. L’un des outils qui va leur permettre de le réaliser est la dernière arrivée dans leur parc d’impression, la Fuse 1, première imprimante 3D SLS industrielle d’atelier de Formlabs.
Cet article raconte l’expérience de Christian Kleylein, technicien de fabrication additive polymère en série chez Brose avec cette nouvelle machine, et la façon dont il prévoit d’utiliser l’impression 3D pour la fabrication en série.
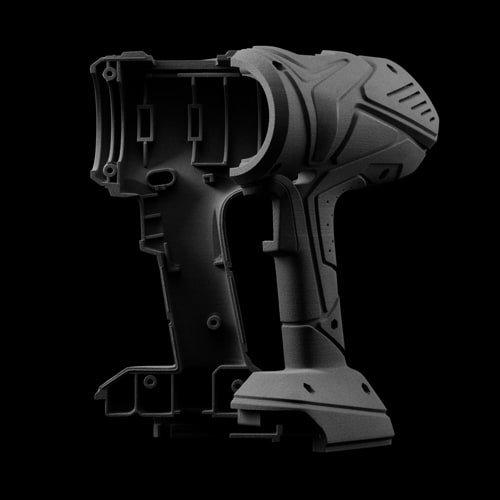
Introduction à l’impression 3D à frittage sélectif par laser (SLS)
Vous cherchez une imprimante 3D pour réaliser des pièces solides et fonctionnelles ? Téléchargez le livre blanc pour savoir comment fonctionne l’impression 3D SLS et les raisons de sa popularité pour le prototypage fonctionnel et la production de produits finis.
Utilisation de la Fuse 1 dans le contexte industriel
La fabrication additive est une compétence principale que Brose a développée récemment. Son centre de fabrication additive est un guichet unique pour la fabrication additive, le développement de produits, l’élaboration de matériaux et la validation. Il fournit des pièces dans le monde entier.
Son activité a commencé il y a plus de dix ans avec une première imprimante 3D par dépôt de fil fondu (FDM), rapidement rejointe par pratiquement tous les autres procédés existants, de la stéréolithographie (SLA) aux procédés de projection de liant, au frittage sélectif par laser, ainsi que par un vaste parc d’imprimantes 3D à métal.
Le parc d’imprimantes de Brose comprend plusieurs systèmes d’impression SLS, depuis les petits appareils de bureau jusqu’aux imposantes imprimantes industrielles traditionnelles. Brose a une vaste expérience de ce procédé et c’est l’une des premières sociétés à avoir acquis une Fuse 1 en Europe.
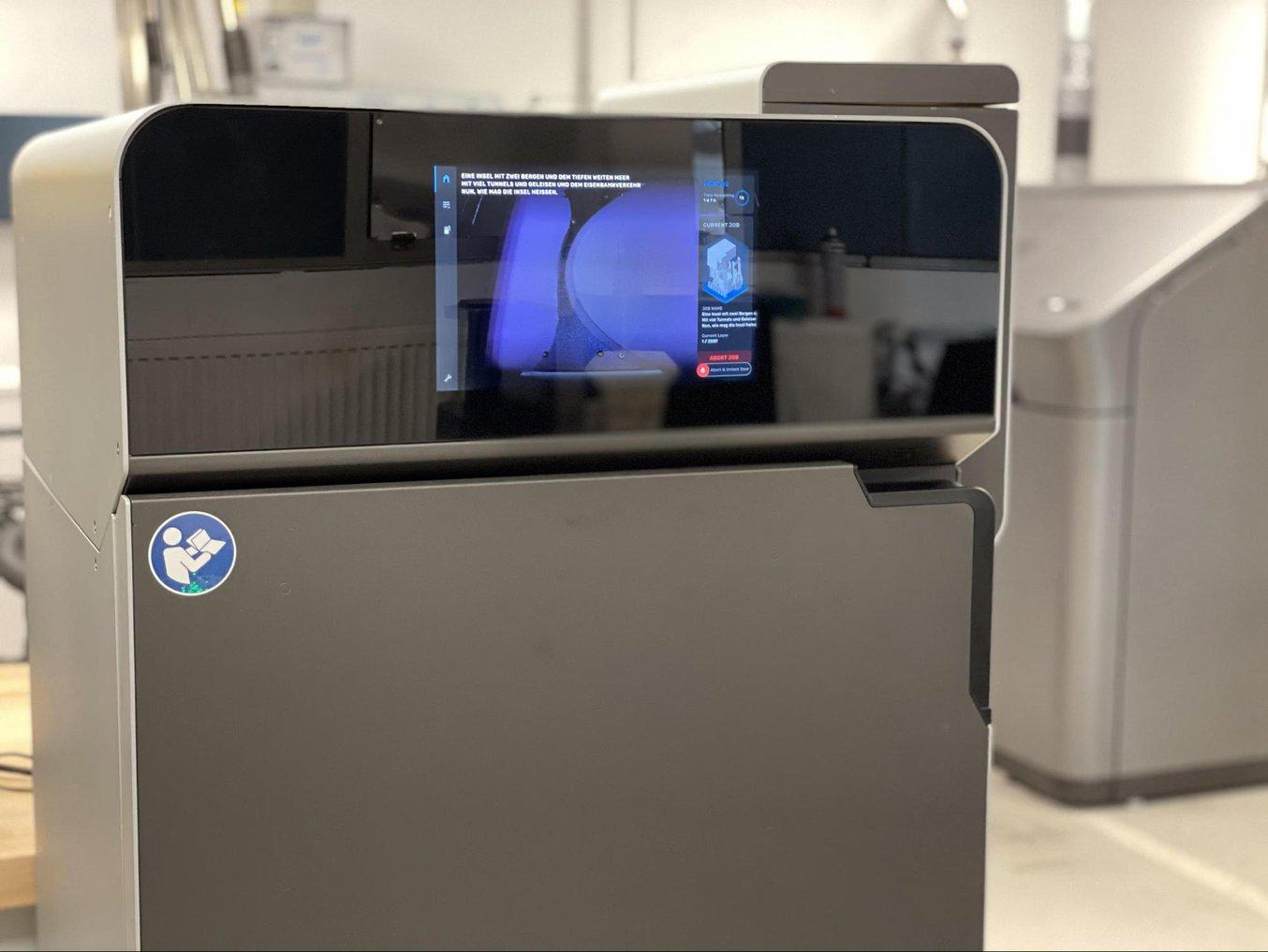
Le centre de fabrication additive de Brose est équipé de pratiquement tous les procédés d’impression 3D existants, et notamment de la Fuse 1, leur toute dernière acquisition.
Alors qu’il faut une semaine pour la mise en œuvre d’une grande machine, Kleylein a trouvé très simple celle de la Fuse 1.
« L'installation est très facile. Si vous disposez d’un local fermé avec climatisation, vous êtes prêt. L’appareil ne demande pas beaucoup de place, et c’est très appréciable. Un véritable étalonnage n’est pas nécessaire, il faut juste s’assurer que la machine soit de niveau. Vous la branchez, vous démarrez le processus de configuration et vous êtes prêt à imprimer », explique Kleylein.
« L’apprentissage est rapide. Il est probable que vous allez réussir votre première impression. Ensuite, vous pouvez commencer à faire des réglages et à mieux connaître l’appareil. »
Christian Kleylein
« Nous avons beaucoup essayé la Fuse 1. Nous avons imprimé de nombreux modèles avec l’épaisseur minimale, ou encore très fins et très longs. Les essais ont montré que, même lorsque les dimensions des pièces étaient décalées, elles déviaient toujours de la même façon. Dès que vous aurez optimisé le processus, vous allez obtenir des pièces avec l’exactitude dimensionnelle requise », explique Kleylein.
L’équipe a fait plusieurs essais d’impression sur la Fuse 1 pour tester les limites de l’appareil, allant de l’impression nocturne d’une pièce durant environ 12 heures à une chambre de fabrication complète de 1000 petites pièces qui a mis quatre jours à s’imprimer.
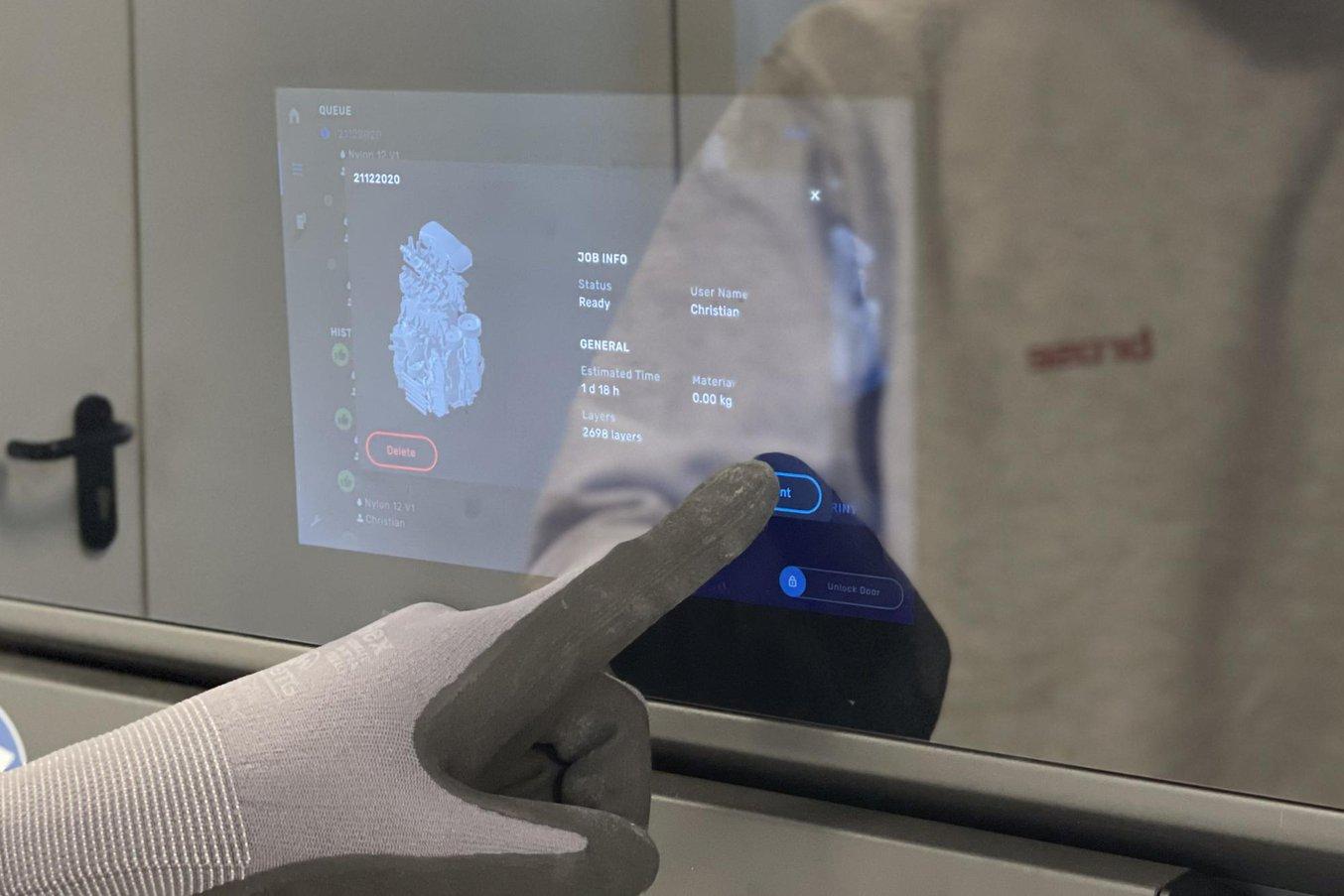
Le frittage sélectif par laser ne nécessite pas de structures de support parce que la poudre non frittée entoure les pièces pendant l’impression. Il est possible d’agencer de nombreuses pièces à imprimer de façon à maximiser l’espace de fabrication disponible.
« La finition de surface est très belle, très lisse. Les couches sont peu visibles. Vous pouvez utiliser les pièces directement en sortie d’impression, après avoir soufflé le reste de poudre à leur surface. Il est possible de réaliser beaucoup de détails très fins. Par exemple, lorsque vous imprimez des engrenages, les pièces sont bien rondes », ajoute Kleylein.
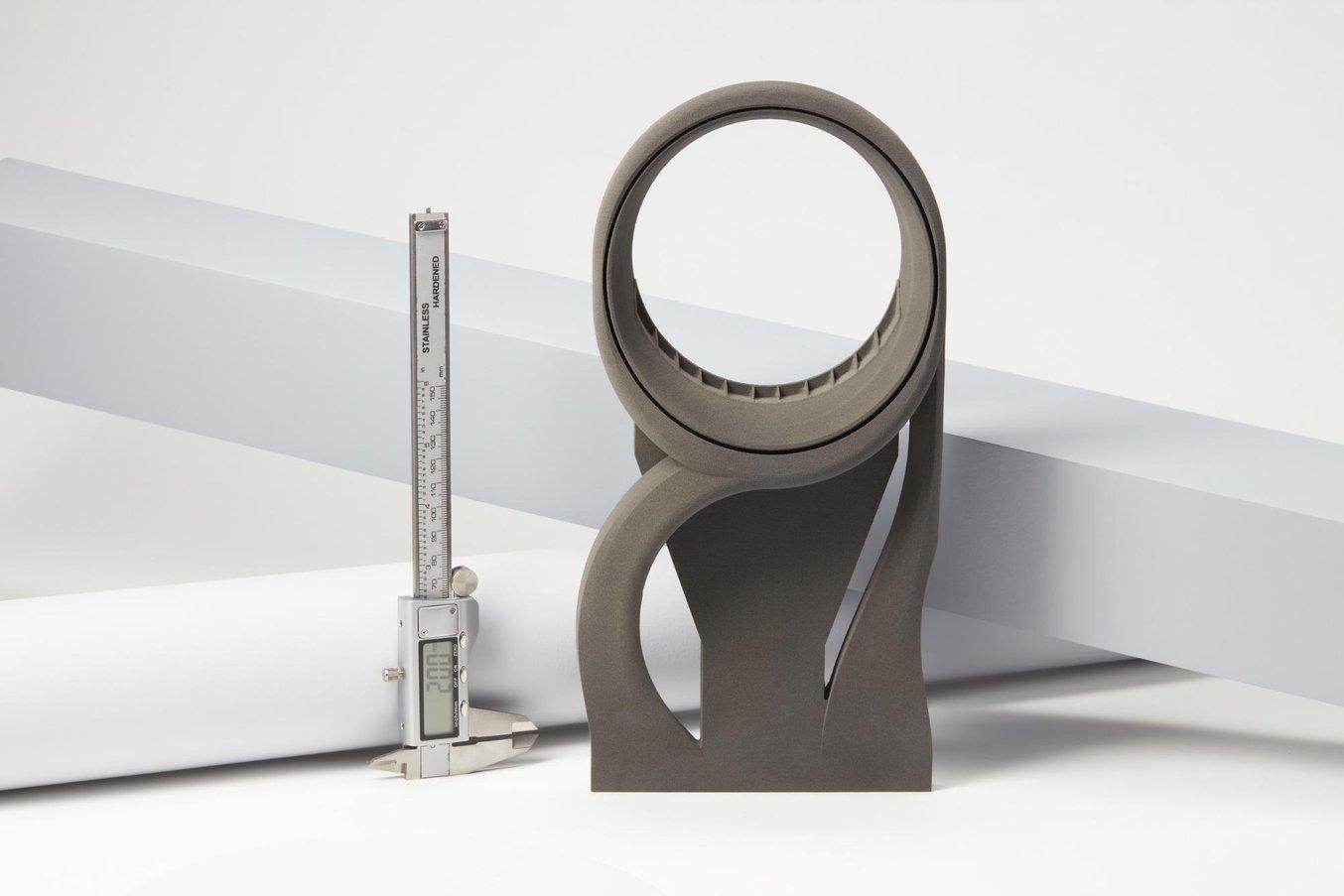
Un équipement de test de fin de ligne des appareils de Brose pendant l’assemblage.
Avec la Fuse 1, Formlabs vise à combler l’écart existant entre les appareils d’impression SLS d’atelier de niveau industriel traditionnels et les imprimantes plus petites à bas prix, en proposant une imprimante de haute qualité, compacte et non encombrante, au processus de travail complet et simplifié, le tout à un prix largement inférieur à celui des systèmes SLS industriels traditionnels.
« Elle doit plutôt être comparée à une imprimante industrielle qu’à une imprimante de bureau. Parce que Formlabs a son laser à fibre, il a développé son propre système de scanner optique et la déviation du faisceau laser est bonne. » explique Kleylein.
« C’est une machine. Ce n’est pas un jouet, c’est un véritable outil de travail. Si vous ouvrez le capot, ça fait industriel et ça fonctionne. Dans l’équipe d’essai, nous en sommes très contents. Vous pouvez très facilement l’utiliser dans le contexte industriel. »
Christian Kleylein
On pourrait penser que de grosses machines sont plus adaptées aux pièces automobiles, mais Kleylein trouve que le volume de fabrication de la Fuse 1 est suffisant pour la plupart de leurs modèles.
« 80 % des pièces que nous imprimons sont de la taille du poing, au plus. Nous pouvons donc toutes les imprimer sur la Fuse 1. Nous avons aussi de très grosses pièces et quelques-unes de taille intermédiaire, » déclare Kleylein.
« La vitesse d’impression est bonne, et elle sera sans doute supérieure après optimisation. Mais pour un début, la vitesse d’impression est suffisante et le volume de fabrication convient pour des applications précises, » ajoute Kleylein.
La Fuse 1 est accompagnée de la Fuse Sift, une station qui associe l’extraction des pièces, la récupération, le stockage et le mélange automatique de la poudre dans un seul appareil autonome.
« Auparavant, pour certaines machines, l’équipement de post-traitement venait en complément. Les gens devaient le concevoir eux-mêmes, même pour le mélange. [Fuse Sift] est un système intégré bien pratique. Avec tous ces ventilateurs qui extraient la poussière, vous pouvez réduire l’équipement personnel de sécurité au minimum. L’appareil tamise la poudre et bloque tout ce qui est trop gros dans le tamis. Vous n’avez plus qu’à recycler ces éléments. La poudre est mélangée ici et vous pouvez décider vous-même du taux de renouvellement. Si vous souhaitez obtenir certaines propriétés, vous n’utilisez que de la poudre neuve, un taux de renouvellement de 100 %. Sinon, vous pouvez même imprimer avec 100 % de poudre déjà utilisée. Vous l’introduisez dans le mélangeur, qui fait que la poudre est bien dispersée, » ajoute encore Kleylein.
Il trouve aussi que produire des pièces sur la Fuse 1 requiert peu d’interventions, juste un peu de temps pour préparer la nouvelle impression, entretenir l’imprimante et post-traiter les pièces.
« Vous pouvez la mettre dans un petit local, puis il suffit d’une personne à quart-temps pour la faire tourner. Le logiciel gratuit est également bon et le procédé d’impression est comparable à ceux des grandes machines. Sa préparation est donc rapide, » explique Kleylein.
« C’est facile et très bien pensé. Vous pouvez redémarrer l’imprimante en 30 minutes. »
Christian Kleylein
« Elle fait partie des appareils faciles à mettre en parc. Programmer les impressions est très simple, la machine peut donc tourner en continu. Pouvoir imprimer jour et nuit est un grand avantage. Il n’y a pas de place pour des appareils inactifs ici, sauf si la tâche d’impression n’est pas suffisante et qu’elle arrive à son terme pendant le weekend. »
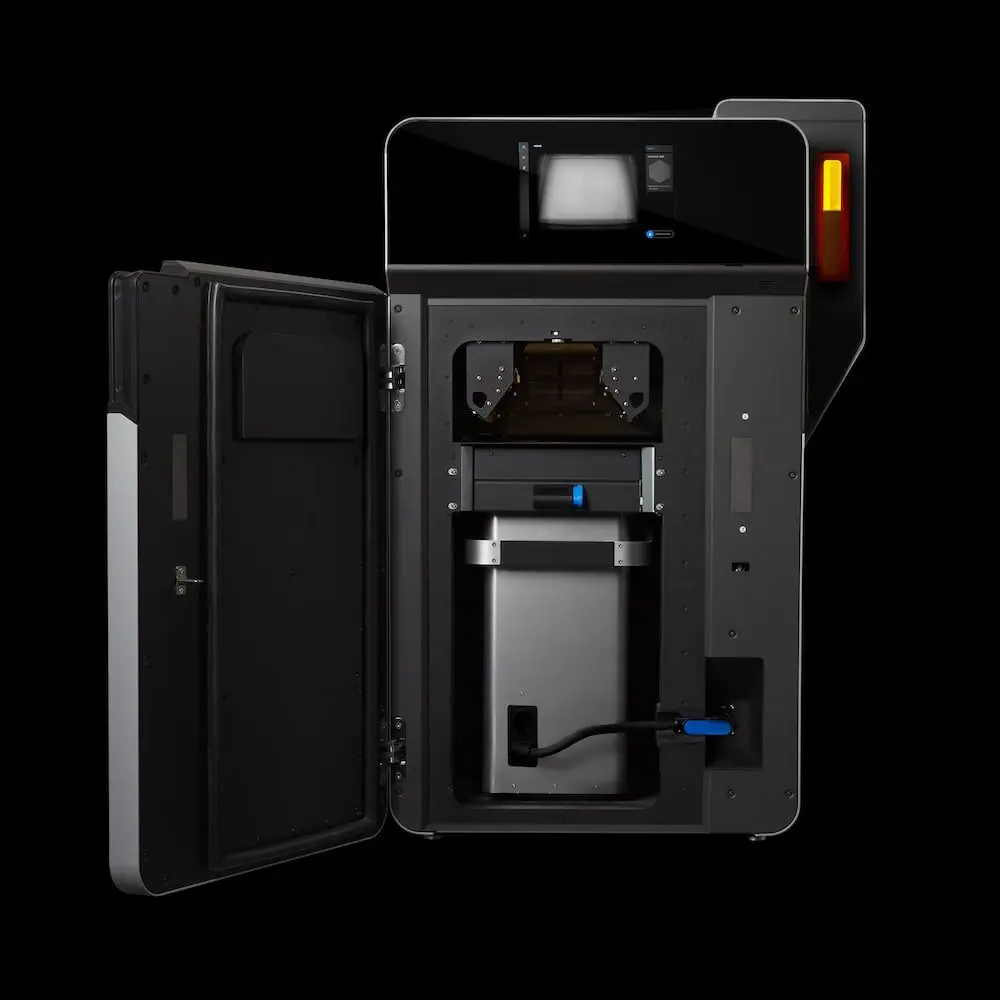
Démonstration Fuse 1
Regardez une démonstration détaillée de la Fuse 1 et de l’impression 3D SLS, réalisée par les experts Formlabs.
Frittage sélectif par laser pour des applications d’utilisation finale : pièces de rechange et pièces pour produits en fin de vie
Dans un premier temps, Brose prévoit d’utiliser la Fuse 1 pour le prototypage pour tirer parti de la rapidité d’exécution et du matériau Nylon 12 Powder, offrant des propriétés similaires à celles des matériaux actuellement utilisés en production. Mais l’équipe de Kleylein est également en train d’évaluer des pièces et de monter les premiers projets d’applications d’utilisation finale, les applications toutes désignées étant des pièces de rechange et des pièces pour produits en fin de vie.
Une fois qu’un modèle de véhicule est retiré du marché, les équipementiers ont toujours l’obligation de fournir des pièces de rechange. Traditionnellement, cela signifie essayer d’estimer la quantité de pièces qui seront nécessaires, les produire par moulage par injection et les stocker.
« C’est un grand gaspillage de ressources, de place et d’argent. Si nous les imprimons en 3D, nous n’avons pas à stocker les moules d’injection et les pièces pendant les 15 prochaines années. Il y a une forte demande de pièces de rechange et de pièces de produits en fin de vie. Les produits manquent toujours et nous avons un grand nombre de pièces moulées par injection. Si nous pouvons les agencer astucieusement et faire des impressions à forte densité, cela devient rentable, » explique Kleylein.
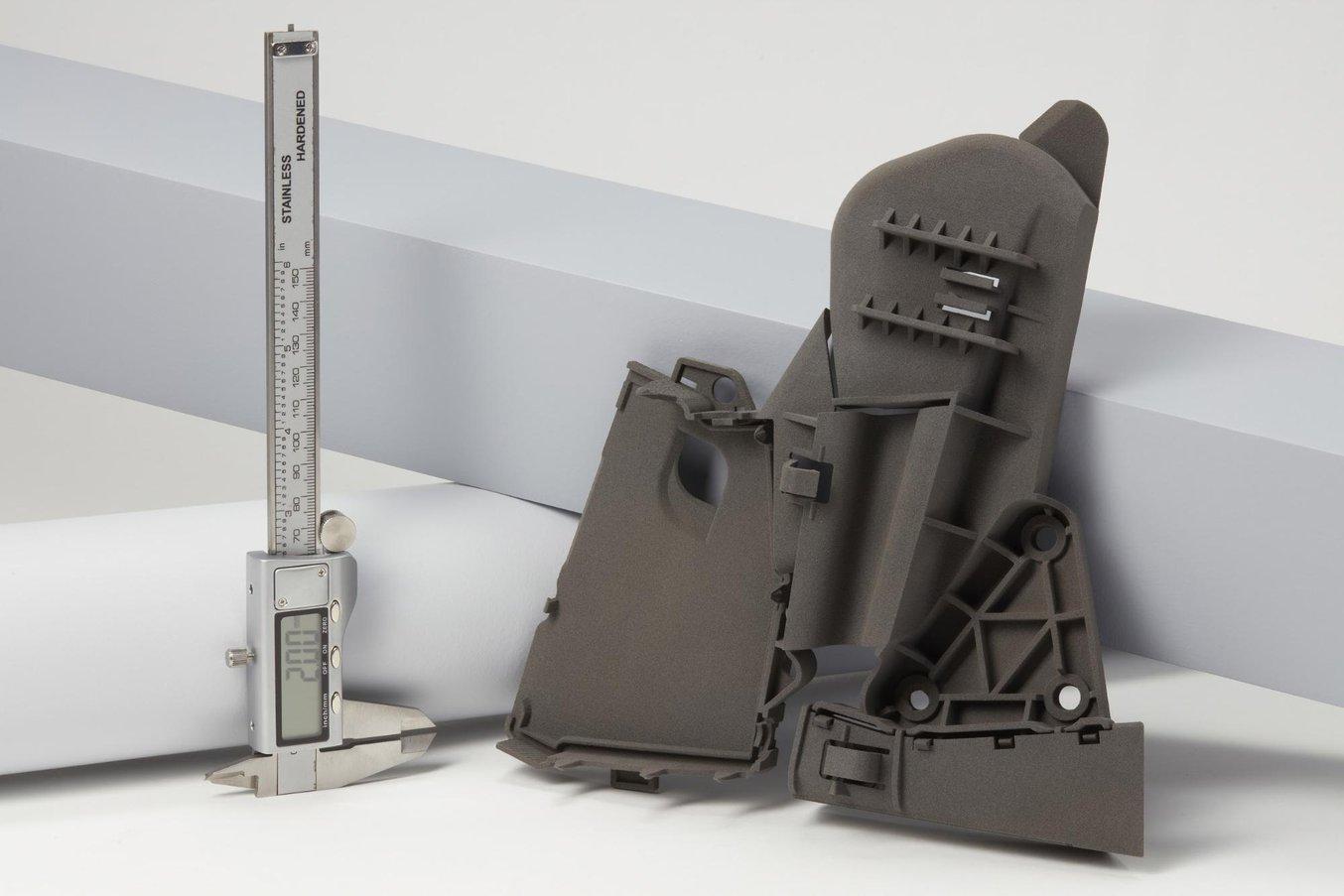
Une pièce de rechange d’un module de poignée de porte imprimée en 3D qui était habituellement moulée par injection.
« Dans le secteur automobile, il est important de fournir la plus grande qualité au meilleur prix possible. À l’heure actuelle, toute série de moins de 10 000 pièces par an peut être imprimée par SLS. »
Christian Kleylein
Le procédé SLS est idéal pour la production sous plusieurs aspects :
-
Il permet de fabriquer des pièces de grande qualité avec des propriétés similaires à celles de pièces moulées par injection.
-
Il peut être mis en œuvre dans un contexte de production.
-
C’est l’un des procédés de fabrication additive les plus propres et les moins gourmands en matériau, ce qui devient de plus en plus important en fabrication.
« Vous pouvez utiliser des polymères techniques pour la fabrication de pièces techniques, et vous n’avez pas besoin de supports. Le post-traitement est également très propre, la plupart de la poudre restant sur la pièce est enlevée avant de la souffler, » explique Kleylein.
« Certains clients de Brose sont très ouverts à ce procédé parce qu’ils apprécient que nous nous efforcions d’imprimer quasiment sans gaspillage. Nous pouvons réutiliser la poudre et non la jeter. Il n’y a pas non plus d’autre produit chimique à recycler. Toutes nos imprimantes SLS devraient fonctionner avec zéro déchet dès la fin de l’année prochaine
L’avenir du SLS en production de série
Bien sûr, le but final est d’utiliser le procédé SLS pour fabriquer les pièces de production en série de la prochaine génération de produits automobiles. Christian pense que cela va se produire dans un futur proche.
« Prototypage et pièces de rechange, c’est possible dès maintenant. À l’heure actuelle, au vu des avancées techniques, je vois cette production possible dans quatre à cinq ans. »
Christian Kleylein
Pour y arriver, il faut qu’il se produise deux choses : que la fabrication additive soit prise en compte pendant le développement de produits dès la phase de conception, et que les coûts des matériaux et des machines baissent.
« Le plus grand obstacle actuellement est de faire en sorte que le concepteur de produits soit conscient de ce qu’il peut réaliser par impression 3D pour qu’il prenne la décision d’imprimer la pièce en 3D. Vous ne serez jamais rentable avec des composants qui sont conçus pour le moulage par injection. Il vous faut concevoir spécifiquement pour ce procédé », déclare Kleylein.
« Il suffit de savoir combien de pièces vous prévoyez d’imprimer et quelle est l’efficacité des systèmes traditionnels de fabrication. Ceci posé, nous produirons une pièce avec le système le plus efficace disponible. Nous n’allons pas forcer l’impression 3D d’une pièce, mais si cela s’avère le meilleur système pour la produire, nous l’imprimerons, » déclare Kleylein.
En baissant le seuil d’entrée à l’impression 3D SLS, La Fuse 1 va jouer un rôle déterminant dans ce changement de mode de production. Brose a déjà prévu d’augmenter rapidement ses capacités d’impression 3D. Son deuxième centre de fabrication additive avec des plastiques est en construction aux États-Unis, et il va bientôt accueillir sa première Fuse 1.
« Il y a encore de grands défis à affronter, mais en regardant la Fuse 1, je pense que nous disposons d’un très bon produit, et à un prix très concurrentiel. »
Christian Kleylein