ESD Resin a permis de passer du prototypage à la production de la Fuse Sift
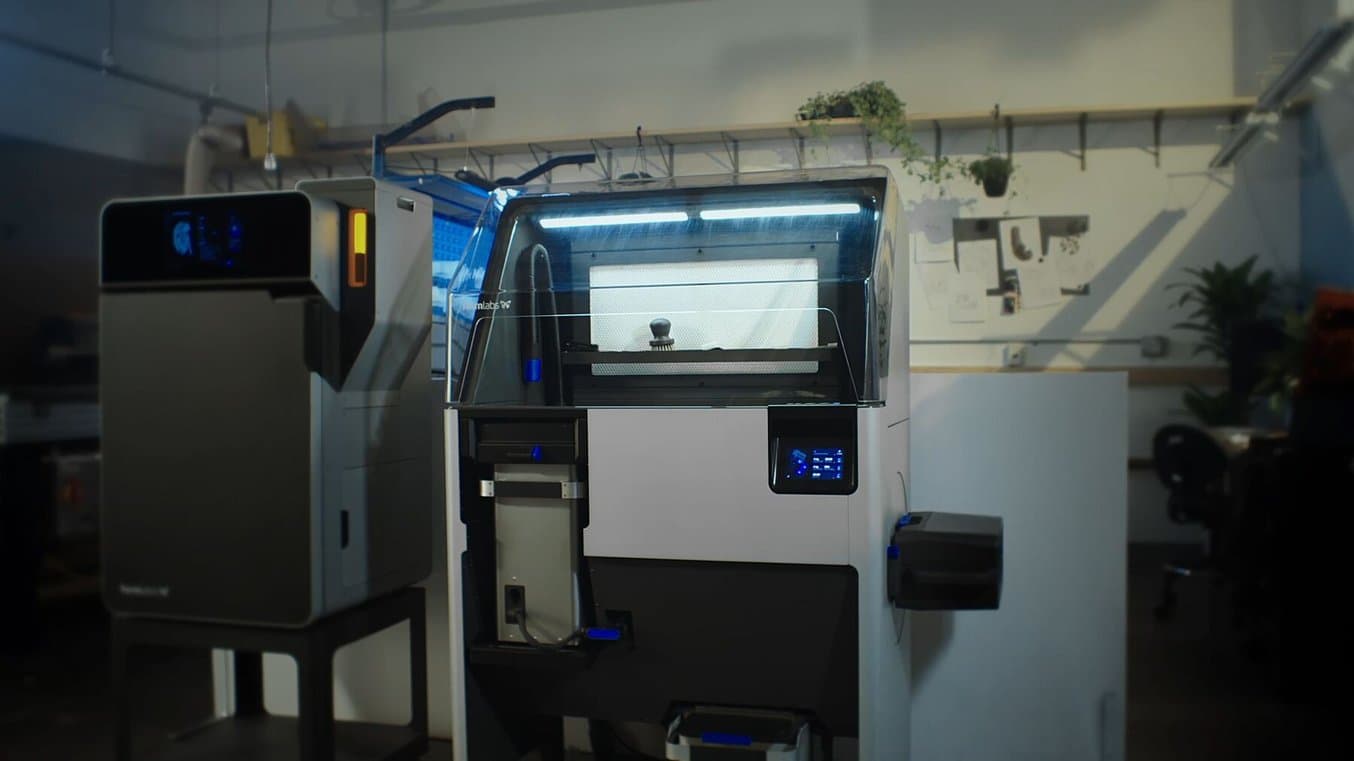
La Fuse 1 est aujourd'hui la solution de frittage sélectif par laser (SLS) la plus vendue sur le marché, mais il a fallu du temps pour passer à la production de masse. La Fuse Sift, l'appareil de post-traitement et de recyclage des poudres qui optimise le flux de travail SLS, représentait un défi de taille pour l'équipe d'ingénieurs de Formlabs qui a dû adopter des approches et des solutions uniques.
Concevoir les pièces destinées au système de confinement de la poudre sur les prototypes finaux de la Fuse Sift était particulièrement ardu. Les sous-systèmes de confinement de la poudre devaient pouvoir dissiper l'électricité statique générée par les particules de poudre en mouvement rapide, mais leur fabrication ne devait pas prendre trop de temps ni être trop chère.
Découvrez comment l'équipe de développement a pu réaliser rapidement et à moindre coût les prototypes des pièces de la Fuse Sift en utilisant une résine antistatique, ce qui lui a permis d'envoyer des unités prototypes aux bêta-testeurs.
Développer un flux de travail SLS complet
En 2019, Formlabs disposait d'un puissant prototype d'imprimante SLS, mais sans un système de post-traitement de haute qualité pour l'accompagner, l'imprimante ne pouvait pas vraiment être utilisée dans le milieu industriel. La plupart des clients SLS impriment leurs pièces finales dans des environnements professionnels et de fabrication, où le confinement des petites particules de poudre est de la plus haute importance pour maintenir un espace de travail sûr et propre.
Pour répondre à cette préoccupation, l'équipe Fuse 1 a commencé à développer la Fuse Sift, une station de récupération et de recyclage de la poudre qui permet de traiter les pièces sortant de l'imprimante Fuse 1. L'objectif de la Fuse Sift était d'offrir une solution de bout en bout et d'optimiser le flux de travail pour l'impression SLS. En 2019, les prototypes de la Fuse 1 et de la Fuse Sift étaient presque prêts pour les tests bêta externes, mais le contrôle de la poudre sur le prototype de la Fuse Sift n'était pas encore au point pour le lancement.
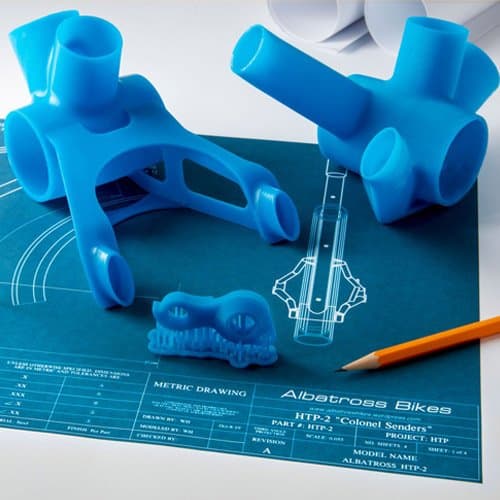
Comment trouver la clé du succès grâce au prototypage rapide et à l'impression 3D
Cet e-book couvre six études de cas réelles montrant comme des entreprises innovent et améliorent
les processus traditionnels grâce à l'impression 3D.
Une fois l'impression terminée, l'utilisateur retire la chambre de fabrication de l'imprimante Fuse 1 et l'insère dans la Fuse Sift, où les pièces peuvent être séparées du cake de poudre non fritté. L'air est aspiré à travers un filtre HEPA situé à l'arrière du capot pour maintenir une pression négative dans l'espace de travail et réduire le risque que la poudre ne s'échappe de la machine. Le cake de poudre non fritté provenant de la chambre de fabrication est tamisé et placé dans une trémie où il peut être mélangé avec la quantité appropriée de poudre fraîche pour recharger les cartouches de poudre.
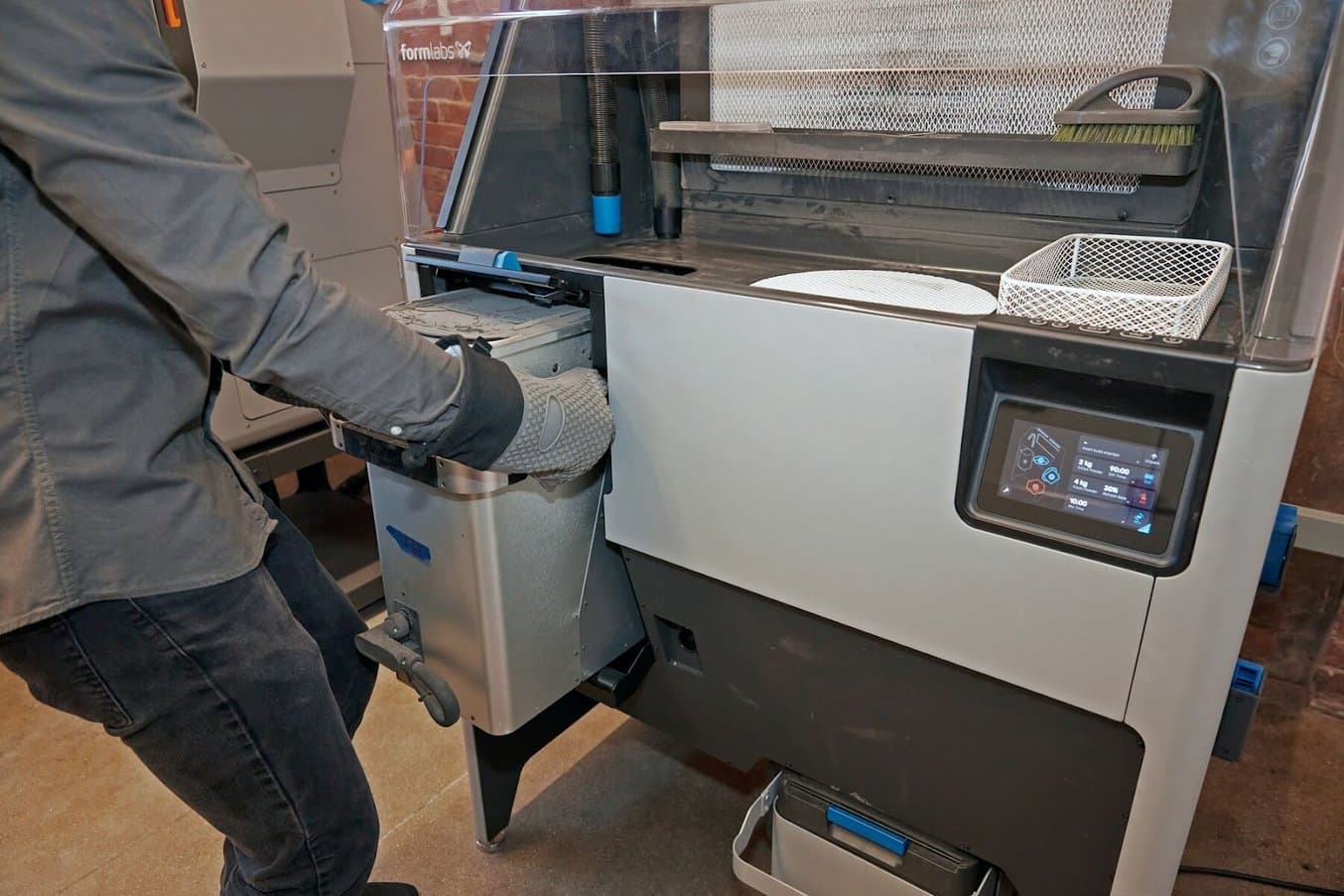
Questions relatives au contrôle et à la surveillance des poudres
« Nous avons longtemps planché sur le filtre HEPA, qui permet de retirer la poudre de l'espace de travail. Mais il y avait toujours cette couche de poudre qui se déposait sur le sol, et nous avons longtemps essayé de comprendre d'où elle venait. J'ai fait quelques vidéos, et il s'est avéré que pendant le dosage, des particules microscopiques de poudre de nylon sortaient de la cartouche. Au bout d'une semaine, la Fuse Sift, les cartouches et le sol étaient tous couverts de poudre », explique Larry Cheung, responsable de l'ingénierie mécanique au sein de l'équipe Fuse Sift.
L'équipe a évalué plusieurs options, comme un capot ou un boîtier qui contiendrait à la fois le système de dosage et la nouvelle cartouche. Mais comme la cartouche doit être pesée en permanence pendant le dosage pour garantir un mélange optimal de poudre fraîche et de poudre usagée, tout ce qui toucherait la cartouche fausserait le système de pesage et ne conviendrait pas.
« Puisque nous avions déjà un aspirateur, nous avons pensé l'utiliser pour garder l'espace de travail propre. Nous avons donc commencé à tester un prototype avec un répartiteur reliant les tubes du plan de travail et de l'orifice de dosage à l'aspirateur. Pour savoir si cela fonctionnait, nous l'avons imprimé avec Draft Resin et l'avons enveloppé dans du ruban de cuivre », explique M. Cheung.
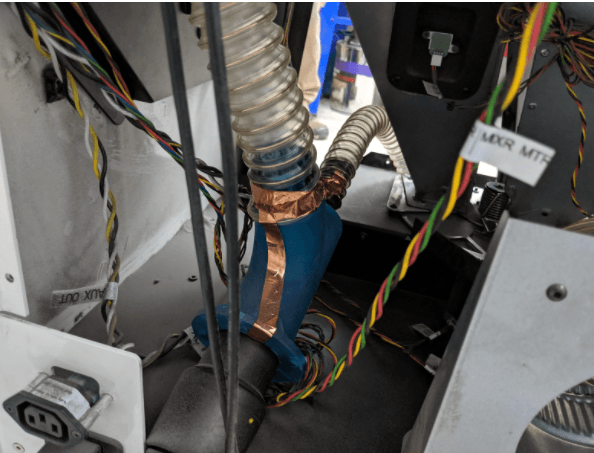
Premier prototype de répartiteur en Draft Resin avec du ruban de cuivre
Le ruban de cuivre, bien qu'il s'agisse d'une solution temporaire, permettait de dissiper toute décharge éléctrostatique provoquée par le déplacement de la poudre de nylon dans le tube. Ceci est très important, car les décharges électrostatiques peuvent présenter un risque pour les composants électroniques de la Fuse Sift et constituer une source d'inflammation potentielle pour la poudre de nylon combustible.
Larry Cheung
« Si des composants ne permettant pas de dissiper l'électricité statique sont utilisés, vous pouvez souvent sentir et même voir les chocs statique lorsque vous faites passer rapidement une tonne de poudre dans le système. Ces chocs constituent un vrai problème. Tous nos sous-systèmes sont mis à la terre, et nous ne pouvons pas permettre aux décharges électrostatiques de les traverser. »
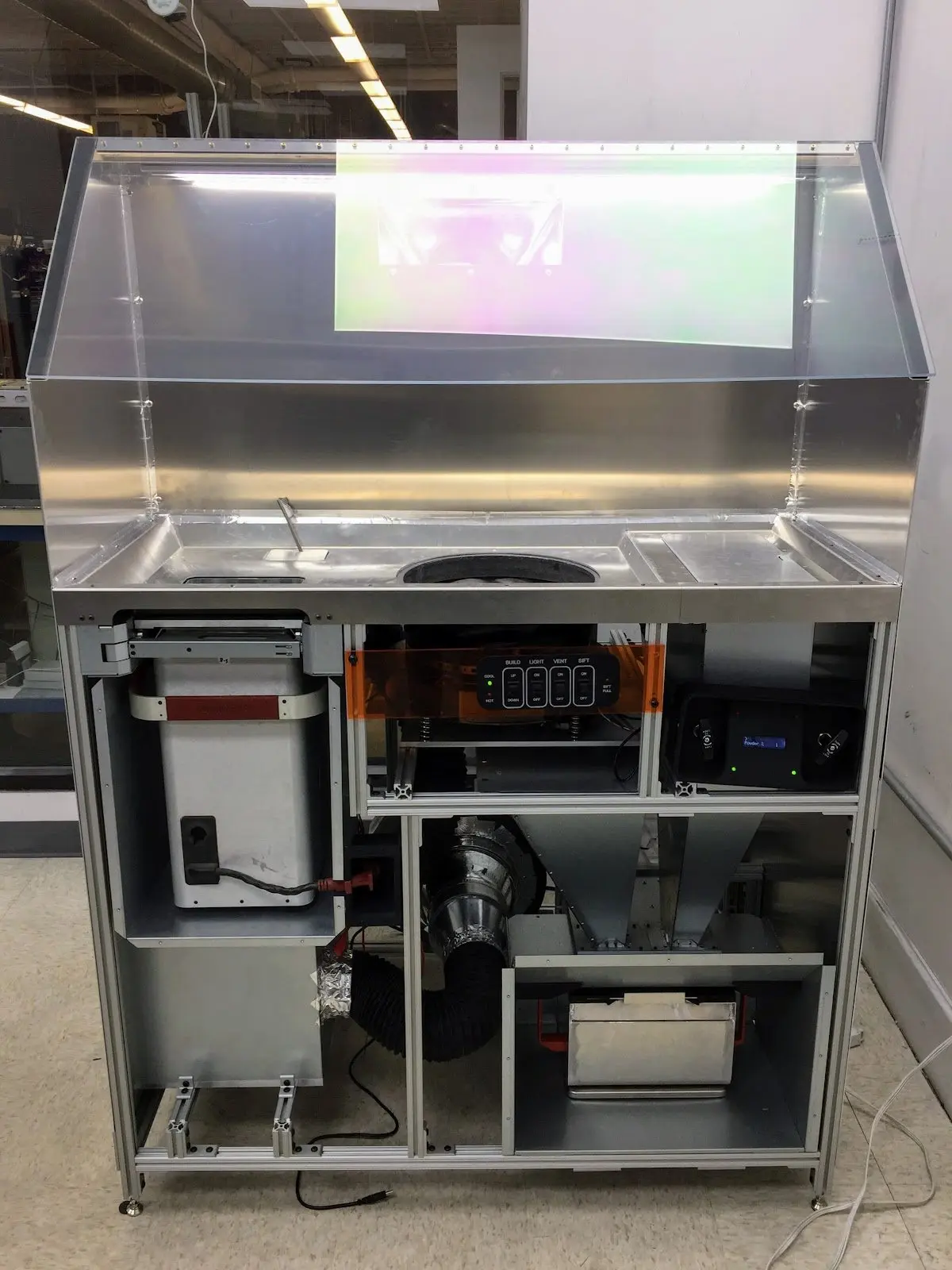
L'un des premiers prototypes de la Fuse Sift.
Les courants électriques statiques non contrôlés sont une préoccupation pour tout fabricant, et ont de multiples implications. L'une d'entre elles concerne la sécurité des employés : les travailleurs doivent être protégés des chocs dangereux lorsqu'il manipulent des équipements. Encore faut-il souvent déterminer l'origine de ces chocs, qui peuvent provenir de composants électriques ou tout simplement de l'électricité statique. Si l'on ne parvient pas à localiser la source d'un court-circuit, des lignes de produits entières peuvent être endommagées, ce qui fait perdre du temps et de l'argent aux fabricants.
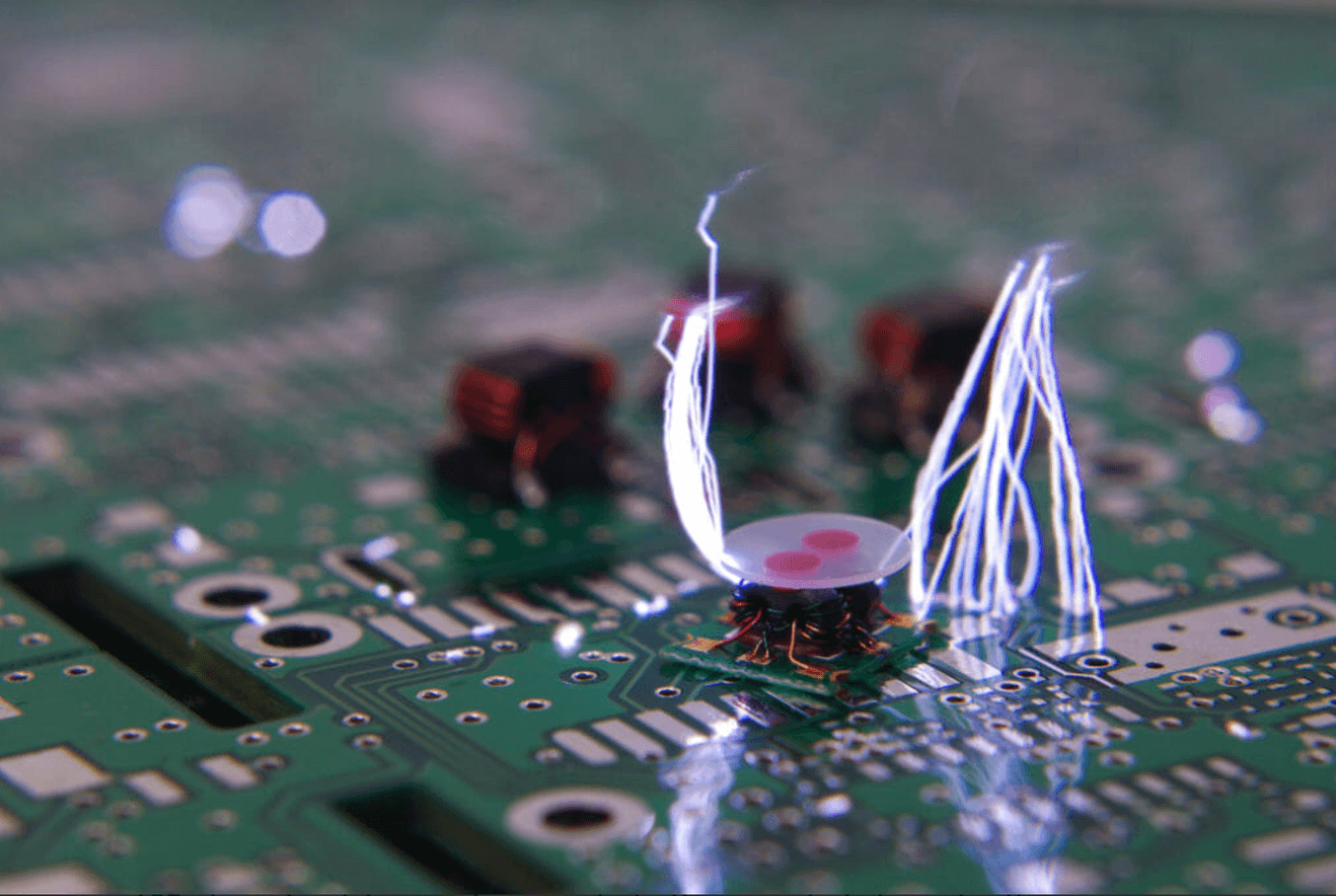
Des chocs statiques endommageant un circuit imprimé.
Dans certains cas, comme dans celui du client HAVEN de Formlabs, des charges électrostatiques incontrôlées ont court-circuité les composants électriques des produits finis, les rendant inutilisables. HAVEN a utilisé ESD Resin pour créer des gabarits et des montages antistatiques sur sa chaîne de montage et ainsi contrôler les décharges électrostatiques.
Il existe quatre types de matériaux liés aux décharges électrostatiques :
- Les matériaux conducteurs (par exemple le métal) permettent aux électrons de passer librement sur leur surface. C'est pourquoi les outils pour les composants électroniques sont souvent usinés en métal.
- Les dissipateurs (par exemple, ESD Resin ou d'autres plastiques antistatiques) permettent aux électrons de se déplacer vers un point de mise à la terre plus lentement qu'avec des métaux.
- Les matériaux antistatiques permettent d'éviter les charges triboélectriques, c'est-à-dire les charges électriques provoquées par les frottements ou les contacts avec un autre matériau.
- Les isolants empêchent ou limitent le flux d'électrons sur leur surface, ce qui signifie que des charges statiques peuvent s'accumuler et y rester longtemps, endommageant souvent tout circuit électrique en contact avec eux.
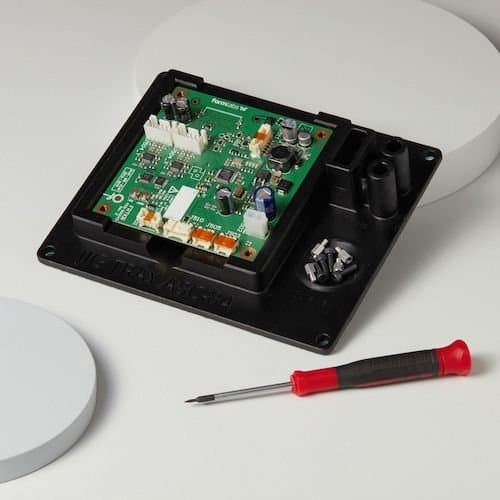
Comment ESD Resin permet d'optimiser l'impression 3D de composants électroniques
Phil Tsao, ingénieur en chef responsable de la qualité de l'air intérieur chez HAVEN, explique comment son équipe a utilisé ESD Resin pour réduire de 90 % le coût et les délais de production de fixations antistatiques.
Flux de travail traditionnels permettant d'éviter les décharges statiques
En général, les pièces finales destinées à des applications antistatiques sont fabriquées en métal ou en plastique antistatique. Le soudage, le moulage ou l'usinage sont autant d'options pour sous-traiter des pièces métalliques, avec des coûts et des implications variables. Mais pendant la phase de prototypage, les pièces métalliques personnalisées peuvent être difficiles et coûteuses à concevoir, à fabriquer puis à ajuster, et peuvent vite être rendues obsolètes si la conception est modifiée.
« Nous avons contacté quelques fournisseurs experts en cintrage et en soudage de tubes pour avoir une idée du prix et des délais de fabrication de cette pièce, pour une production à court et à long terme. Tous les devis indiquaient que la production coûtait extrêmement cher : de l'ordre de 40 à 50 € par pièce, même en cas de production de masse. C'était beaucoup plus que ce que nous avions imaginé ; de plus, nous aurions dû attendre des semaines avant de les avoir en main. En raison des contraintes de temps et de coûts, passer par des sous-traitants n'était tout simplement pas envisageable. C'est pourquoi le fait de pouvoir fabriquer la pièce en interne et l'obtenir immédiatement a complètement changé la donne », explique M. Cheung.
En plus d'envelopper une pièce imprimée en Draft Resin dans du ruban de cuivre, l'équipe a également essayé d'utiliser des sprays antistatiques ainsi qu'un procédé de revêtement par immersion pour tenter de recouvrir la pièce en résine SLA d'un matériau antistatique. Le problème de cette approche était que les revêtements antistatiques n'étaient pas très résistants à l'usure et qu'il était difficile d'obtenir une couche uniforme permettant d'obtenir des performances fiables. Heureusement, l'équipe Fuse Sift avait entendu des rumeurs selon lesquelles il ne fallait peut-être pas chercher bien loin pour trouver une solution.
Une solution toute proche
« Nous avons entendu dire dans le bâtiment que l'équipe des matériaux travaillait sur une résine antistatique, et nous avons contacté Kathy [Bui] (chef de produit en ingénierie) pour voir si nous pouvions imprimer quelques pièces pour les prototypes de la Fuse Sift », explique Cheung.
« Comme beaucoup de nos clients effectuent des tâches de conception et d'ingénierie avec nos résines, nous recevons beaucoup de questions sur la sécurité ESD, qui ont servi de base au développement d'ESD Resin. L'un des points forts de Formlabs est que, comme nous réalisons nos tâches d'ingénierie en interne, nous savons ce que les clients attendent de nos nouveaux produits. Lorsque Larry a décrit les défis auxquels l'équipe Fuse Sift était confrontée, nous nous sommes rendus compte qu'il s'agissait précisément du type de problèmes pour lesquels nous avions conçu ESD Resin : c'était donc l'occasion rêvée de tester notre matériau », explique Mme Bui.
ESD Resin, mise au point par l'équipe des matériaux, n'aurait pas pu arriver à un meilleur moment. Les prototypes de la Fuse 1 étaient prêts à être envoyés aux bêta-testeurs externes, et le prototype de la Fuse Sift devait les accompagner. Nous n'avions pas le temps d'attendre les pièces d'un sous-traitant pour le revêtement ou l'outillage. Pouvoir imprimer ces pièces en interne était donc essentiel pour que le test bêta se déroule dans les temps.
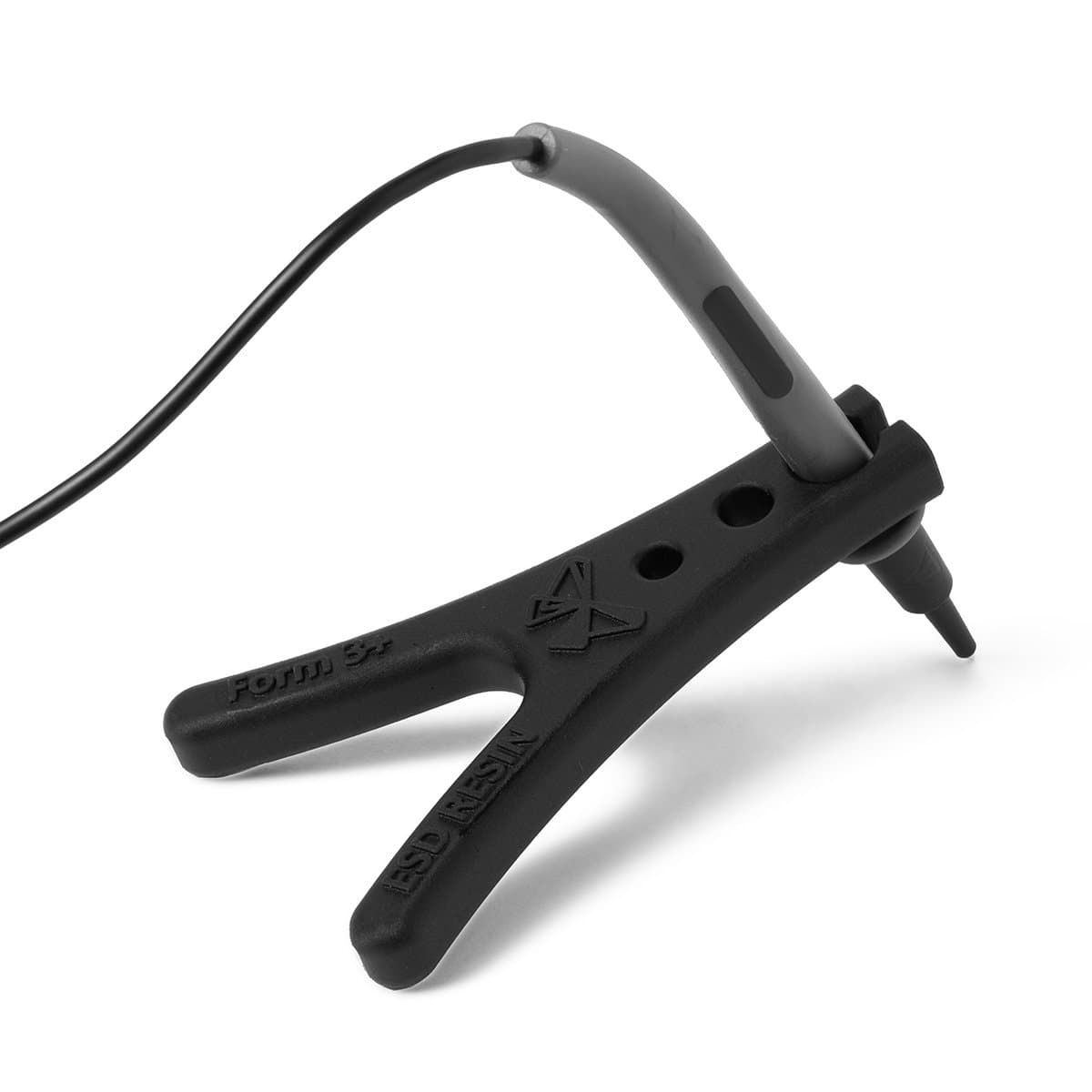
Commander un échantillon gratuit
Vous souhaitez essayer ESD Resin par vous-mêmes ? Commandez notre porte-sonde multimètre imprimé en 3D, antistatique et gratuit, pour votre établi électrique. Testez sa résistivité superficielle pour vérifier qu'il s'agit bien d'un matériau ESD.
Les pièces imprimées avec ESD Resin ont permis de réaliser neuf prototypes
L'équipe a imprimé neuf prototypes avec le matériau qui sera finalement commercialisé sous le nom d'ESD Resin. Les pièces ont été validées sur des prototypes finaux de la Fuse Sift, qui ont ensuite été envoyés à des fabricants sous contrat potentiels et utilisés pour des tests bêta internes et externes. À l'aide d'un résistivimètre de surface, l'équipe a constaté que les pièces imprimées avec ESD Resin dissipaient l'électricité statique et qu'elles étaient parfaites pour fabriquer les tubes dans lesquels circulent de grandes quantités de poudre de nylon.
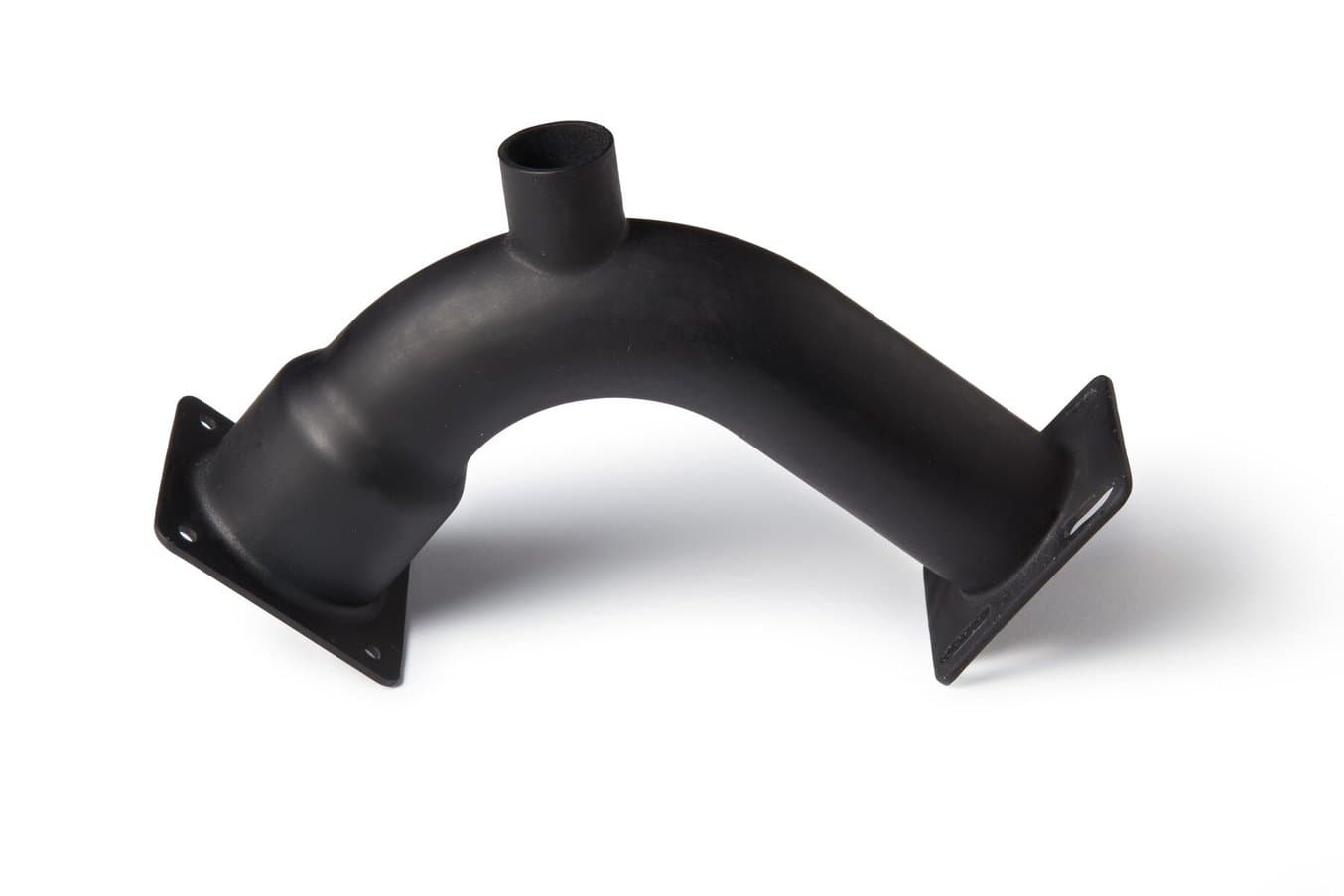
Le tube final de la Fuse Sift, imprimé avec ESD Resin
« Utiliser ESD Resin nous a permis de combler l'écart entre le prototypage et la production. L'impression 3D est le moyen le plus rapide de prototyper une pièce comme celle-ci, mais nous ne pouvions pas valider en toute sécurité les concepts du séparateur et du tube sans trouver un moyen de nous protéger des décharges antistatiques. ESD Resin nous a permis de concevoir et de valider notre concept en interne, sans avoir à dépenser des centaines, voire des milliers d'euros en outillage ou en pièces sous-traitées », explique M. Cheung.
L'utilisation d'ESD Resin de Formlabs a permis aux équipes Fuse 1 et Fuse Sift de passer plus vite à la phase de production, en évitant les coûts élevés et les longs délais qu'aurait entraînés la sous-traitance des pièces antistatiques. Pour un fabricant de matériel, le fait de pouvoir fabriquer des pièces antistatiques en interne permet de lancer un produit plus rapidement et de minimiser les risques.
« Si nous n'avions pas imprimé les pièces en interne, il aurait fallu plusieurs semaines et peut-être quelques milliers d'euros pour les fabriquer. Le fait de savoir qu'il était possible de les fabriquer nous-mêmes nous a permis de mieux planifier ; surtout que nous avions des délais à respecter pour les envoyer aux fabricants sous contrat », explique M. Cheung.