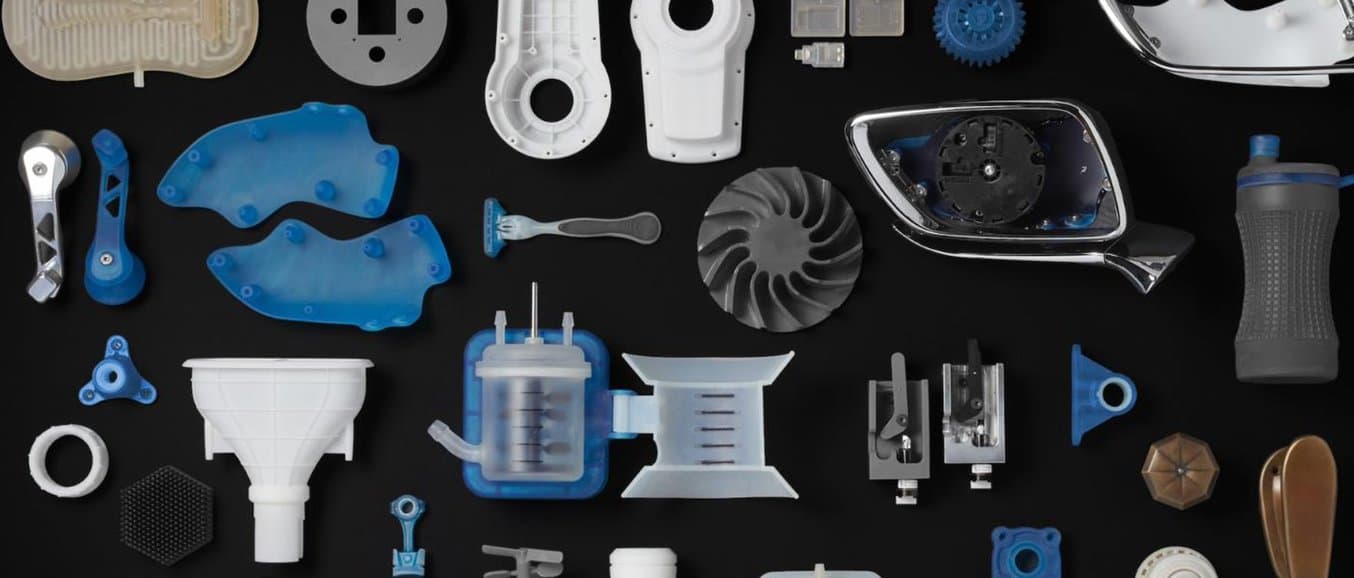
La fabrication additive, aussi appelée impression 3D produit des pièces tridimensionnelles à partir de modèles CAO, en déposant le matériau couche par couche jusqu'à fabrication complète de la pièce.
Alors que les technologies de fabrication additive sont apparues dans les années 80, le secteur industriel a connu son moment médiatique le plus fort au début de la dernière décennie, lorsque ses promoteurs ont déclaré que cette technologie trouverait un large usage pour des produits de consommation et réorganiserait toutes les activités, de Home Depot à UPS.
Comme cet engouement s'est calmé il y a quelques années, les technologies d'impression 3D professionnelles ont muri rapidement de plusieurs façons concrètes. Les progrès récents en appareillage, matériaux et logiciels ont rendu l'impression 3D accessible à une gamme plus large d'activités, permettant à un nombre croissant d'entreprises d'utiliser des outils qui étaient auparavant réservés à quelques secteurs high-tech.
Aujourd'hui, les imprimantes 3D contribuent à accélérer l'innovation et aident les entreprises de nombreux secteurs, dont l'ingénierie, la production industrielle, la dentisterie, la santé, l'enseignement, le divertissement, la joaillerie, l'audiologie et bien d'autres encore.
Cet article fait une présentation approfondie de cinq grandes tendances qui ont été déterminantes pour le secteur de la fabrication additive, et des perspectives d'avenir.
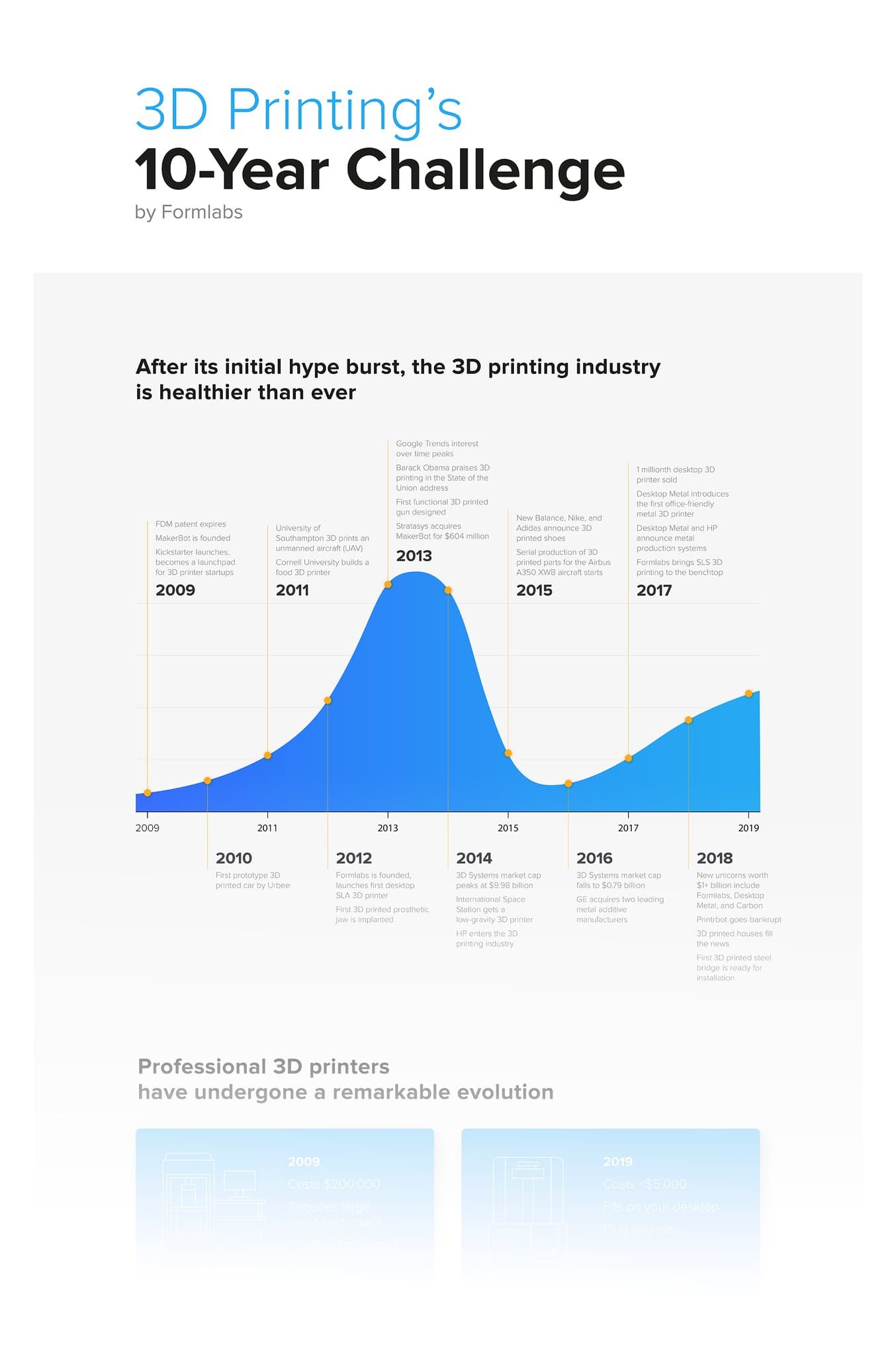
Téléchargez ce document infographique complet pour connaitre les changements du secteur de la fabrication additive cette dernière décennie.
Cet article a été initialement publié dans le rapport The Digital Factory. Téléchargez le rapport complet pour en savoir plus sur la transition numérique de la production industrielle. Inscrivez-vous au salon The Digital Factory, ayant lieu à Boston, le 7 mai 2019, présentant des responsables qui sont en train d'adopter des technologies de fabrication de pointe pour transformer leurs activités.
Présentation : l'état actuel du secteur de la fabrication additive
Le marché de l'impression 3D, totalisant 6 milliards de dollars de ventes en 2017, devrait croître à un taux de croissance annuel composé de 30,2 % pour atteindre une taille de marché totale de 22 milliards vers 2022.
- L'impression 3D a été omniprésente en prototypage et en développement de produits pendant des décennies. Maintenant cette technologie mature commence à entrer largement en production industrielle.
- L'amélioration de la technologie pour l'impression de pièces finales de haute qualité et la production de grands volumes, et la grande variété des matériaux font de l'impression 3D une technologie adaptée pour la production industrielle de petites et de moyennes séries, pouvant atteindre parfois quelques dizaines de milliers de pièces.
- En plus de la fabrication directe de produits finis, l'impression 3D offre des avantages indéniables en « production hybride », comme un intermédiaire par rapport aux processus traditionnels, notamment pour la fabrication de moules, d'outillage, de modèles, de fixations et de gabarits d'assemblage.
- Les capacités des imprimantes 3D, compactes et accessibles, ont augmenté, et, lorsqu'elles fonctionnent en parallèle, peuvent être plus avantageuses en coût et en flux de production que des machines industrielles onéreuses.
- Les fabricants cherchent à réduire l'intensité en main d'œuvre des processus de travail en fabrication additive, ce qui est essentiel pour amener l'impression 3D au niveau de la production à moyenne et grande échelle.
- L'investissement en fabrication additive a augmenté en flèche et les améliorations des procédés et des technologies ont fait baisser le coût par pièce.
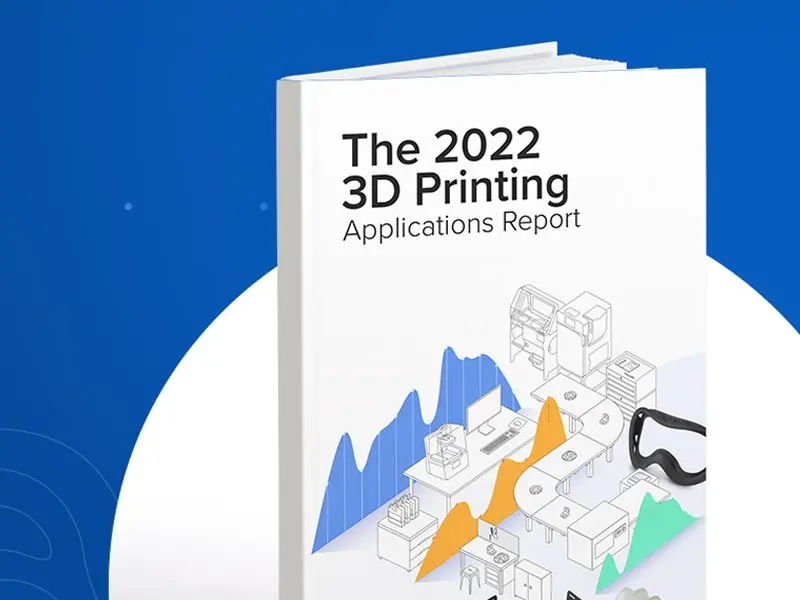
Le rapport 2022 sur les applications de l'impression 3D
Un rapport qui analyse les tendances passées, présentes et futures de l'impression 3D dans la fabrication industrielle.
Tendances marquantes en fabrication additive :
Systèmes compacts et modulaires pour le plastique
Pendant les trente premières années de leur développement, les imprimantes 3D ont été réservées aux grandes entreprises et bureaux d'études, de par leur coût et leur complexité. Au début des années 2010, grâce à un matériel intégré plus performant, l'expiration de brevets et le niveau de maturité technologique, des centaines d'entreprises sont entrées sur le marché et ont commencé à l'inonder d'imprimantes 3D. Une bulle s'est rapidement formée.
Le premier procédé disponible a d'abord été l'impression par dépôt de filament fondu (FDM). Ces imprimantes 3D, qui fondent du plastique et le déposent sélectivement, sont devenues accessibles financièrement aux consommateurs, mais leurs performances restaient limitées. Le pic d'intérêt est vite retombé et le rêve de voir l'imprimante 3D comme un outil indispensable dans chaque foyer ne s'est jamais réalisé.
En dehors de cette bulle de consommation autour de l'impression 3D, les technologies de la fabrication additive ont continué à progresser. Les imprimantes destinées aux professionnels de l'ingénierie, du prototypage et de la production industrielle commencèrent à dépasser des seuils critiques en termes de qualité d'impression, de fiabilité et de structure des coûts.
La deuxième technologie à apparaitre dans un format plus abordable, plus compact et plus facile d'utilisation a été la stéréolithographie (SLA). En 2013, Formlabs a rendue l'impression 3D professionnelle haute résolution disponible sur le marché avec la Form 1, vendue au prix de 3000 €. Auparavant, elle etait uniquement disponible via des imprimantes 3D dont le coût dépassait 80 000 €. Avec son offre très variée de matériaux fonctionnels, la technologie a élargi l'usage de l'impression 3D à la conception de produits et l'ingénierie, et aux secteurs du dentaire et de la joaillerie.
La troisième vague des techniques d'impression 3D fonctionnant sur un bureau (ou plus précisément à l'atelier, sur les paillasses) se fonde sur le procédé du frittage sélectif par laser (SLS), qui s'est avéré essentiel aux utilisateurs industriels. Contrairement à d'autres procédés de fabrication additive de bureau, le procédé SLS permet de fabriquer des pièces extrêmement robustes à partir de thermoplastiques comme le nylon, qui sont presque aussi solides que les mêmes pièces fabriquées en moulage par injection. La poudre soutient les pièces avant qu'elle soit fondue, ce qui augmente le nombre de pièces par impression, donc le débit de production, et permet un processus de traitement après impression moins intensif en main d'œuvre.
Jusqu'à il y a trois ans, les imprimantes SLS les moins chères coûtaient environ 200 000 € (et les systèmes industriels les plus grands, de l'ordre de plusieurs millions de dollars). Les imprimantes SLS d'atelier qui produisent des pièces en nylon sont maintenant disponibles à environ 10 000 €, rendant cette technologie beaucoup plus accessible et baissant significativement les coûts de production lorsqu'on prend en compte le coût de possession. Le procédé SLS en atelier peut s'étendre au-delà du prototypage et entrer dans le domaine de la fabrication des produits finis.
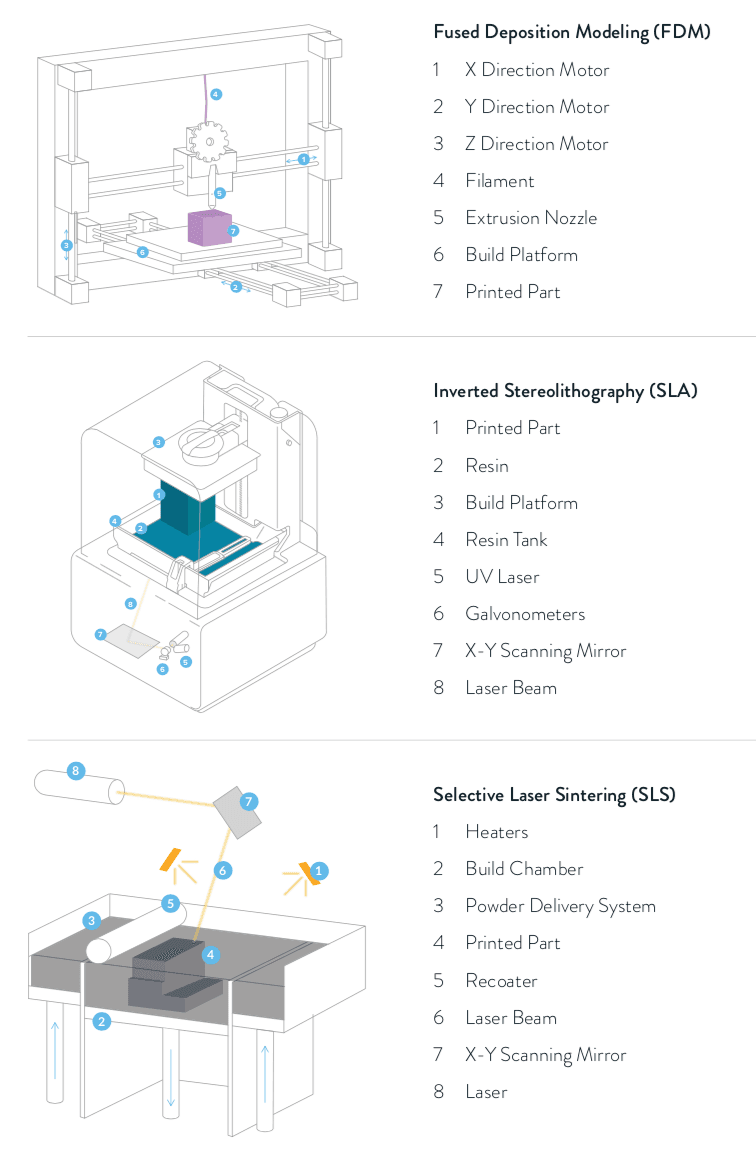
Les trois procédés les plus courants d'impression 3D Les imprimantes 3D FDM fabriquent les pièces en extrudant un filament thermoplastique préalablement fondu. Le procédé par stéréolithographie (SLA) polymérise de la résine liquide avec un laser. Le frittage sélectif par laser (SLS) utilise un laser de forte puissance pour fondre de petites particules de poudre de polymère.
Impression 3D en métal
Les métaux ont toujours été en tête sur le marché de la fabrication additive et l'investissement dans le marché de l'impression 3D en métal a énormément augmenté depuis plusieurs années.
L'impression 3D métallique donne aux pièces imprimées l'aspect haute performance d'objets en acier, en titane, en alliages de nickel et en aluminium, de formes peu communes, demandés par des secteurs à haute valeur ajoutée, tels que l'aérospatiale et la fabrication de dispositifs médicaux. Ces secteurs peuvent tirer tous les avantages de l'impression 3D en imprimant des pièces en métal, en particulier des pièces conçues par design génératif, avec des structures en treillis serré, qui diminuent la quantité de matériau nécessaire et le poids.
Les systèmes de fabrication additive traditionnels les plus courants sont la fusion sélective par laser (SLM) et le frittage direct par laser du métal (DMLS). Exactement comme pour le frittage sélectif par laser du plastique, ces procédés fabriquent des objets à partir de matériau en poudre, en le faisant fondre sélectivement à l'aide d'une source de chaleur. Mais le point de fusion des métaux étant plus élevé, ceux-ci requièrent des lasers beaucoup plus puissants et des locaux industriels.
Jusqu'à récemment, leur coût très élevés et leur complexité ont cantonné ces imprimantes 3D à métaux à une gamme très réduite d'applications à haute valeur ajoutée et à faible volume de production. Les prix des imprimantes DMLS et SLM commencent à 400 000 € et peuvent dépasser le million d'euros. Elles requièrent des opérateurs extrêmement qualifiés et des conditions de travail très contrôlées. Contrairement aux pièces fabriquées par SLS, les pièces métalliques fabriquées par frittage laser ont besoin de supports. Le traitement après impression nécessite beaucoup de main d'œuvre et certaines pièces doivent encore être usinées pour présenter leurs caractéristiques finales.
Le domaine de l'impression 3D de métaux a bénéficié d'un investissement actif ces dernières années. En 2016, GE a acquis deux entreprises leaders en fabrication additive de métaux, Concept Laser et Arcam. Plusieurs sociétés financées par capital-risque, notamment Desktop Metal, Markforged et Xjet, continuent à progresser sur des procédés d'impression 3D de métaux, qui promettent de réduire le coût par pièce et rendre le procédé accessible à plus d'applications.
Cherchant à bouleverser le marché par le bas de gamme, Desktop Metal et Markforged ont développé des systèmes compacts et accessibles, qui fonctionnent comme celui par FDM, mais utilisent des matériaux composites, à partir de poudre métallique liée à une matrice plastique. Après impression, les pièces sont soumises à un nettoyage et un frittage dans un four pour en éliminer le liant et fondre la poudre métallique, et obtenir ces pièces pleines en métal. Leur prix se situant autour de 100 000 € pour un système complet, ils sont bien moins coûteux que les systèmes traditionnels de fabrication additive en métal, fonctionnant avec des lasers.
Le deuxième système de production haut de gamme de Desktop Metal combine des matériaux éprouvés pour le moulage par injection métallique à une technologie similaire à la projection de liant pour faire démarrer son écosystème et réduire considérablement les coûts. La technologie par pulvérisation métallique de XJet utilise une suspension de particules de métal dans un liquide et l'évapore thermiquement pour fabriquer des objets solides en métal ou en céramique.
Ces technologies d'impression 3D métalliques ne sont pas encore à la portée des masses, mais elles vont élargir l'adoption de la fabrication additive par des secteurs de production de petites et moyennes séries de pièces métalliques, et moderniser le prototypage et les processus de développement de ces produits.

Les trois procédés les plus courants d'impression 3D Les imprimantes 3D FDM fabriquent les pièces en extrudant un filament thermoplastique préalablement fondu. Le procédé par stéréolithographie (SLA) polymérise de la résine liquide avec un laser. Le frittage sélectif par laser (SLS) utilise un laser de forte puissance pour fondre de petites particules de poudre de polymère.
Automatisation et procédures de travail continues
Contrairement à ce que l'on peut penser intuitivement, la main d'œuvre est le composant le plus coûteux de la plupart des processus de fabrication additive. Une imprimante 3D n'est pas une boite magique qui fabrique une pièce sortie de nulle part en appuyant sur un bouton. Les techniciens doivent sortir les pièces des imprimantes et réaliser plus ou moins de traitements après impression. Ces traitements peuvent aller d'un léger polissage à un lavage important au solvant, un traitement thermique, un polissage abrasif ou encore le dépôt d'un revêtement. Pour s'introduire dans les usines, les systèmes de fabrication additive doivent d'abord diminuer leurs besoins de main d'œuvre et s'insérer dans les processus de travail existant en production industrielle.
Les améliorations apportées aux processus de travail et à la technologie sont prometteuses sur le plan des réductions des coûts de main d'œuvre. Certaines imprimantes FDM à double buses proposent des supports solubles, facilement éliminés par bain dans des solvants. Certains systèmes SLA simplifient le traitement après impression à l'aide de postes de nettoyage et de post-polymérisation. Les impressions en SLS ne requérant pas de supports, le processus de traitement après impression tend à être moins intensif en main d'œuvre que d'autres. De plus, le volume d'impression peut contenir plus de pièces, ce qui réduit le besoin de manipulation par pièce. En fabrication additive métallique, les fabricants proposent des systèmes automatisés qui simplifient les processus de traitement après impression, notamment la manipulation et l'extraction de la poudre, le traitement thermique et le retrait des pièces.
De la même façon que les ordinateurs centraux ont été remplacés par des PC de bureau dans les années 80, les systèmes d'impression 3D centralisés laissent la place à des systèmes distribués. Formlabs, Stratasys, 3D Systems et Mass Portal ont tous introduit sur le marché des cellules d'imprimantes modulaires, compactes et automatisées, pour les matières plastiques. Des bras robotiques et des systèmes de portiques se chargent de retirer les pièces, réduisant le travail des opérateurs et permettant aux imprimantes de travailler 24 heures sur 24, pour produire en continu même la nuit. Des logiciels intelligents de gestion de cellules optimisent les queues d'impression, fournissent des commandes à distance et s'intègrent à des systèmes de gestion clients (CRM), de gestion globale intégrée (ERP) et de pilotage de la production (MES). Une série de capteurs détecte les erreurs d'impression et assure la protection des opérateurs. La modularité des systèmes présente également l'avantage d'augmenter la redondance, ce qui permet de répartir la charge de travail sur les autres machines lorsqu'un appareil tombe en panne, en éliminant tout arrêt de production.
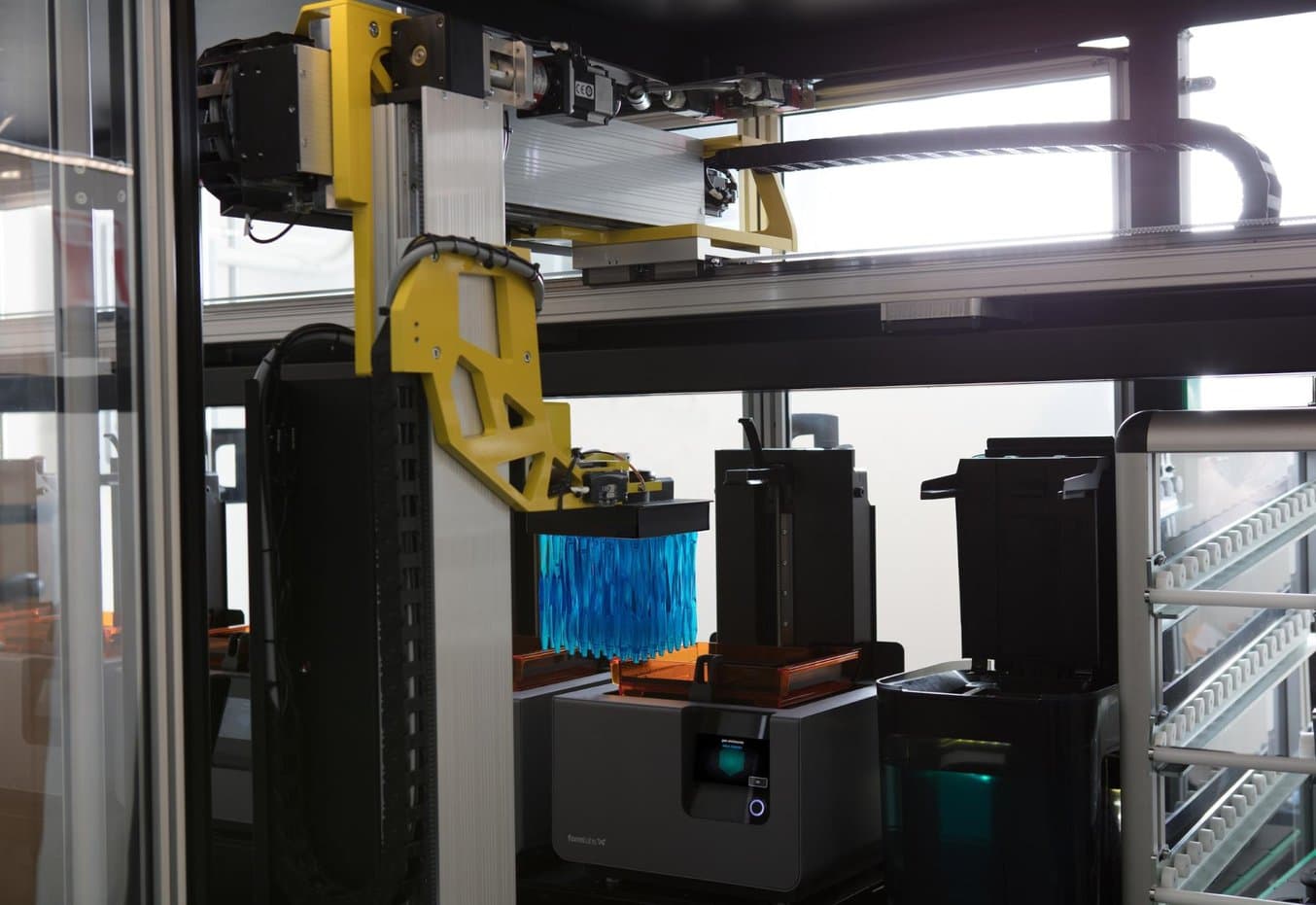
Form Cell est une cellule de production modulaire, développée par Formlabs, équipée d'un système de portique avec bras robotique pour retirer les pièces imprimées et les nettoyer sur un poste de lavage, avant de les placer sur une étagère pour subir des traitements après impression, ce qui économise considérablement le besoin de main d'œuvre.
Ces cellules automatisées continuent à modifier l'économie de l'impression 3D en transformant des groupes d'appareils de bureau en machines de production, à haut débit et à bas coût. De plus, elles permettent aux ingénieurs et aux concepteurs d'utiliser la même plateforme pour le prototypage et la fabrication, réduisant les processus coûteux de conception pour la fabrication et raccourcissant les cycles de développement de produits.
Les systèmes automatiques progressent et deviennent capables de traiter des pièces uniques de formes irrégulières, rendant envisageable à l'avenir l'automatisation d'autres aspects de l'impression 3D. Des robots pourraient être capables d'éliminer les supports d'impression, d'appliquer des apprêts et des produits adhésifs pour assembler des pièces conventionnelles et d'autres imprimées en 3D, faisant passer la « fabrication numérique » au stade de l'« assemblage numérique ».
Les avancées en termes de matériaux
Les systèmes de fabrication additive sont les couteaux suisses de l'outillage de production industrielle. Ils fonctionnent avec une large gamme de matériaux et, en passant de l'un à l'autre, un seul appareil est capable de produire des pièces pour de nombreuses applications différentes.
Parmi les meilleurs exemples de cette polyvalence, on peut citer les procédés d'impression 3D à base de polymères, comme la stéréolithographie (SLA). La même imprimante 3D SLA de bureau, compacte, peut produire des gouttières biocompatibles et des guides chirurgicaux dans des cabinets dentaires de petite taille, ainsi que des gabarits, des fixations et des moules résistants à la chaleur pour le secteur automobile.
D'autres matériaux avancés d'impression 3D permettent la numérisation de processus jusqu'alors analogiques. Des résines haute-température peuvent être utilisées en moulage par injection basse pression de plastique, mais aussi pour la fonderie de métaux mous comme l'étain. Bien que la qualité du moulage puisse ne pas atteindre celle de l'outillage d'usinage, les moules imprimés en 3D satisfont un besoin crucial en production de petites et moyennes séries, pour lesquelles le coût de l'outillage peut ne pas être recouvrable avec d'autres procédés.
Des pièces imprimées par SLA, SLS et FDM peuvent être utilisées pour fabriquer des gabarits et des fixations pour les lignes de production industrielle, remplaçant des processus d'usinage coûteux. Les PEEK, ULTEM et thermoplastiques techniques renforcés, utilisés en FDM, fournissent des pièces dont les propriétés mécaniques et la résistance thermique leur permettent de remplacer même des pièces en métal. Les nouveaux matériaux céramiques SLA présentent des propriétés exceptionnelles et prometteuses en terme de résistance thermique et d'inertie chimique.
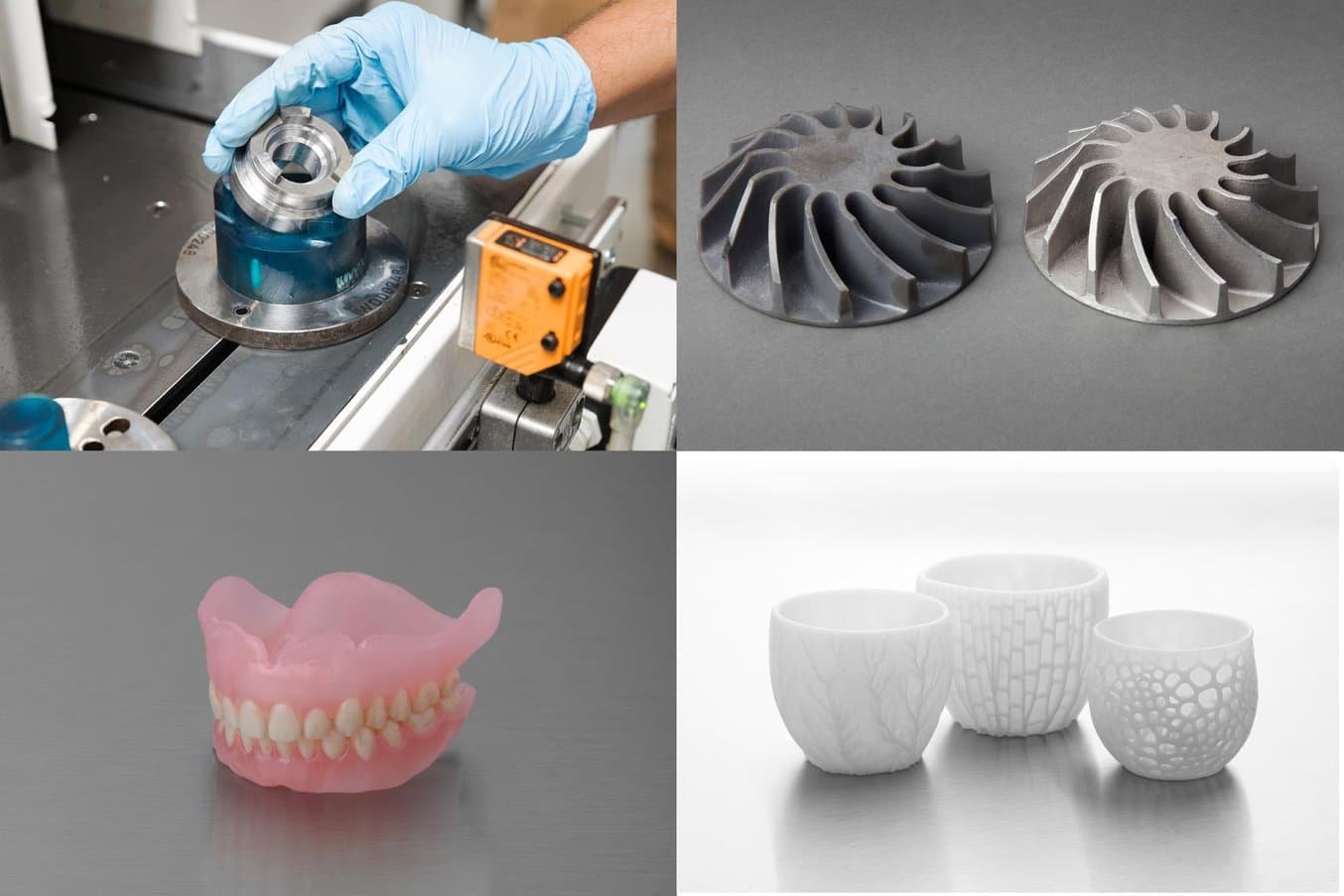
Quatre pièces produites avec la même imprimantes 3D SLA. De haut en bas et de gauche à droite : une fixation dans une ligne de production automatisée d'une usine automobile ; une pièce en métal coulée à l'aide d'un modèle imprimé en 3D ; une prothèse dentaire biocompatible ; de la vaisselle en céramique.
Optimiser la production industrielle
L'impression 3D n'est pas la panacée pour les besoins de la production industrielle. Jusqu'à maintenant, elle n'a eu de sens que pour des produits à haute valeur ajoutée, fabriqués en très petites séries et sur mesure. Pour la production à volume élevé, les méthodes conventionnelles restent plus rentables. Néanmoins, les facteurs économiques de l'impression 3D s'améliorent et le seuil de rentabilité du coût par pièce se déplace : il devient réalisable d'utiliser la technologie pour des applications de valeur ajoutée de moins en moins élevée et des séries de plus en plus grandes. Alimentée par l'innovation technologique et l'amélioration des propriétés des matériaux, la fabrication additive est destinée à s'étendre au-delà du prototypage vers la production de masse et de pièces finales.
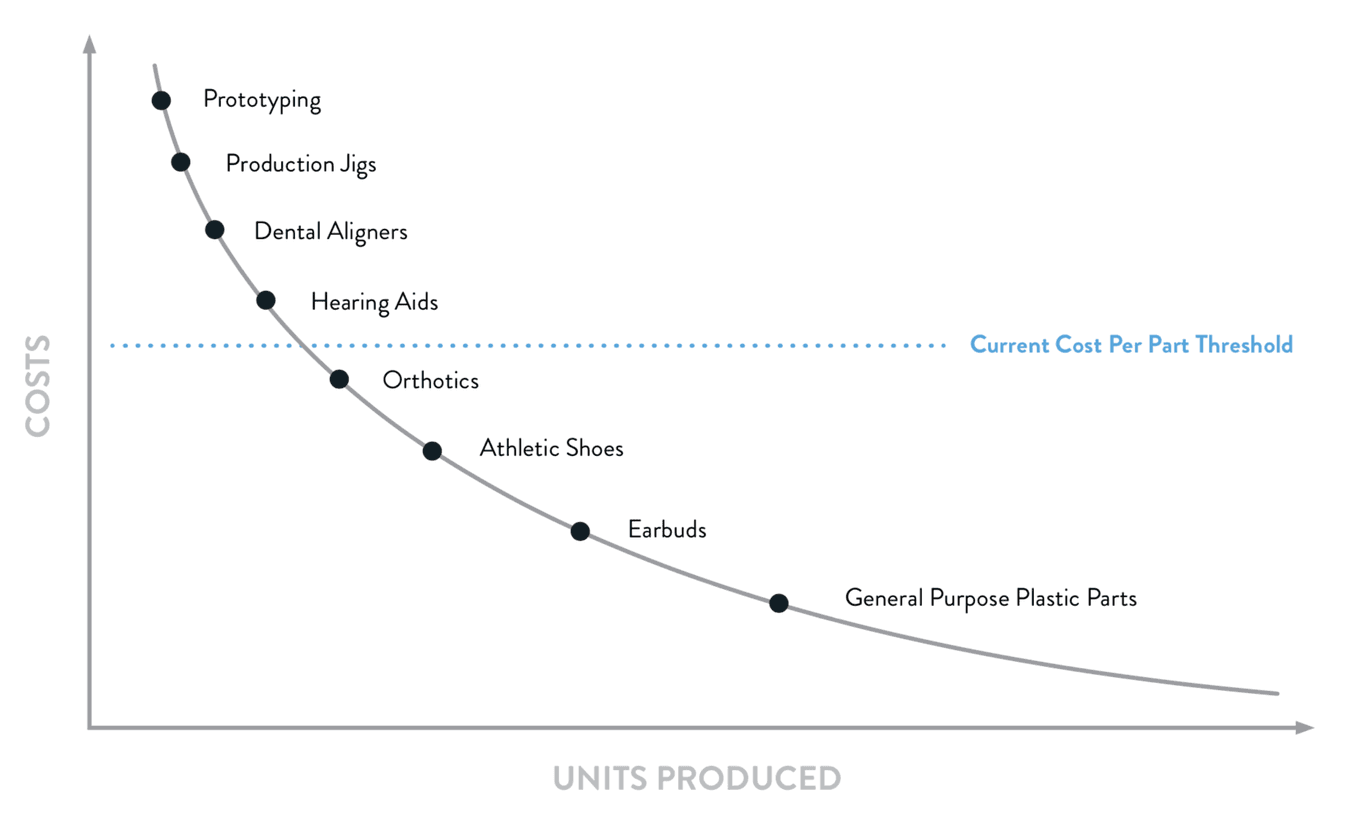
Les facteurs économiques de l'impression 3D s'améliorent et le seuil de rentabilité du coût par pièce en production industrielle se déplace : il devient réalisable d'utiliser la technologie pour des applications de valeur ajoutée de moins en moins élevée et des séries de plus en plus grandes.
Dans de nombreux cas, l'impression 3D devient une étape intermédiaire des méthodes conventionnelles de production industrielle, appelée aussi production hybride. Dans le secteur de la joaillerie par exemple, l'impression 3D fait aussi partie du procédé de fonte à modèle perdu. Les joaillers commencent par concevoir numériquement une pièce, puis l'impriment en 3D en résine spéciale pour la fonte à modèle perdu. La pièce imprimée est immergée dans un matériau réfractaire ressemblant à du sable, puis brûlée dans un four, exactement comme les modèles habituels en cire pour joaillerie, laissant un moule pour couler les métaux précieux.
Un processus hybride d'impression 3D permet aussi de produire des écouteurs personnalisés à un coût raisonnable. Le processus commence par un scan rapide et non intrusif du canal auditif du client à l'aide d'un scanner 3D. Un technicien travaille le fichier numérique pour produire un moule imprimable en 3D et l'envoie par Wi-Fi à l'imprimante 3D. Les pièces sont nettoyées après impression et un technicien coule du silicone biocompatible dans les moules, retire les coques imprimées en 3D puis s'occupe de la finition et du revêtement du produit final. L'impression 3D s'intègre parfaitement à ces processus autrefois artisanaux, même si aucune pièce du produit final n'est elle-même imprimée.
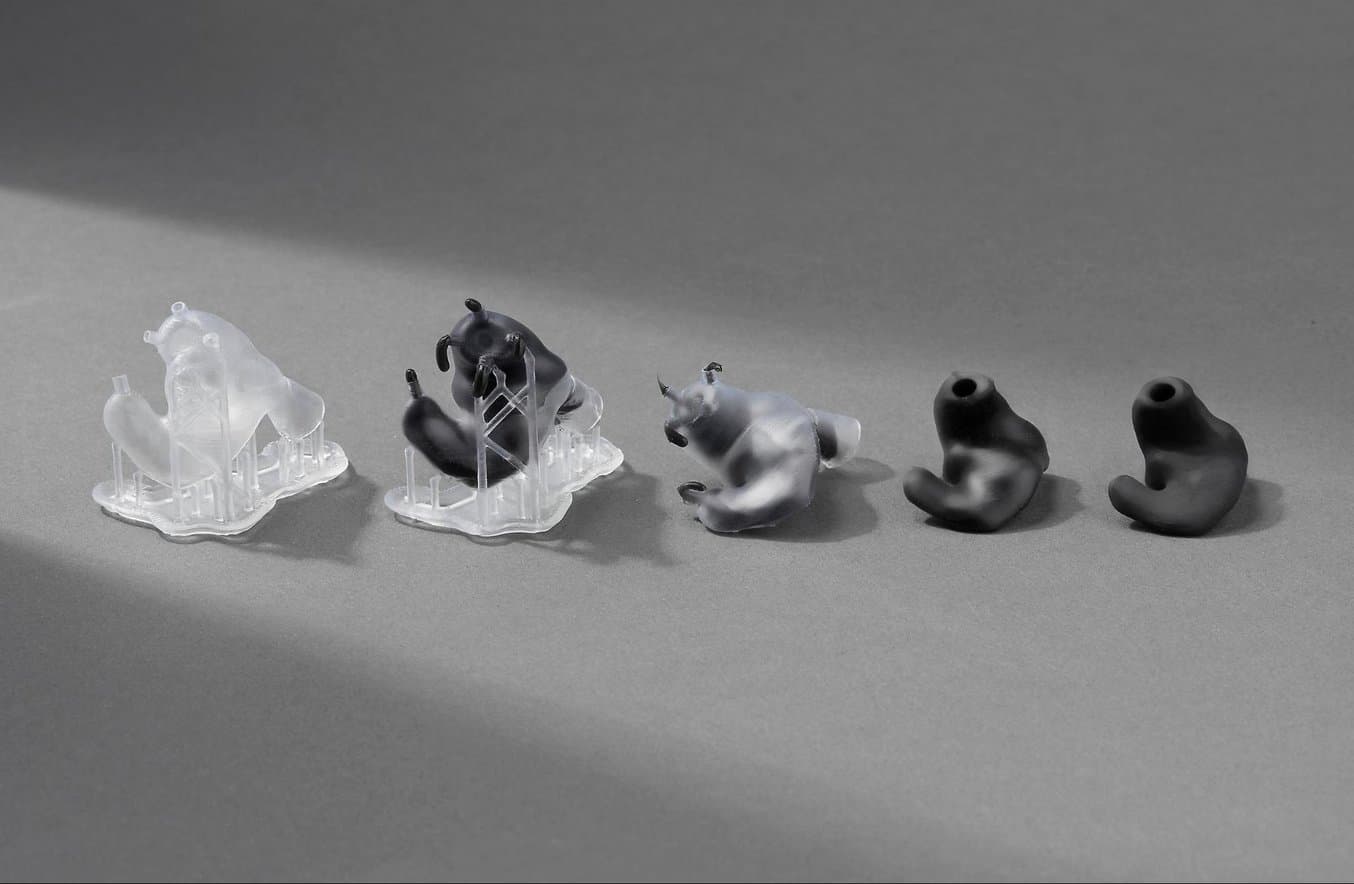
Les écouteurs sur mesure sont fabriqués en coulant du silicone biocompatible dans des moules creux imprimés en 3D. Chaque moule imprimé coûte entre 0,35 € et 0,50 € pour la résine et la production complète d'une paire d'écouteurs finie revient approximativement à 2,5-3,5 € pour le matériau brut (dont le silicone et la laque).
Des secteurs, comme la dentisterie, le fabrication de dispositifs médicaux et l'audiologie, adoptent rapidement l'impression 3D pour la production de pièces finies, adaptées au profil de chaque patient. L'impression 3D devient également la norme dans les cabinets et les laboratoires dentaires et va être de plus en plus utilisée pour fabriquer des gouttières et des appareils dentaires directement à partir de matériaux biocompatibles. En audiologie, la plupart des aides auditives sont déjà imprimées en 3D. Le marché médical, encore plus large, présente également un potentiel phénoménal. Par exemple, des pièces SLS biocompatibles et solides peuvent être utilisées pour produire des orthèses sur mesure et d'autres dispositifs en contact avec la peau.
Les coûts étant en baisse, la fabrication additive industrielle est destinée à intervenir aussi en fabrication de produits de consommation conventionnels. Dans les segments de plus grand volume du secteur des produits électroniques de consommation par exemple, le moulage par injection est encore l'unique moyen pratique de produire des pièces en plastique. Mais dans le large segment à volume moyen de ce même secteur, l'impression 3D a commencé à s'imposer. En utilisant la fabrication additive au lieu du moulage par injection, les fabricants en produits électroniques peuvent rationaliser la conception et la production, en gardant de la flexibilité, et d'atteindre des seuils de rentabilité avec le moulage par injection pour des volumes dépassant 10 000 unités, parce que l'impression 3D ne nécessite pas d'outillage coûteux.
Des fabricants de chaussures comme New Balance et Adidas ont annoncé pour les années à venir leurs projets de production de masse de semelles sur mesure, imprimées en 3D à partir de polyuréthane rigide (RPU). Là encore, l'impression 3D va être associée à d'autres méthodes de production industrielle. Elle permettra de fabriquer les pièces les plus critiques et les plus personnalisées du produits, laissant la fabrication des autres pièces à d'autres processus traditionnels et rentables.
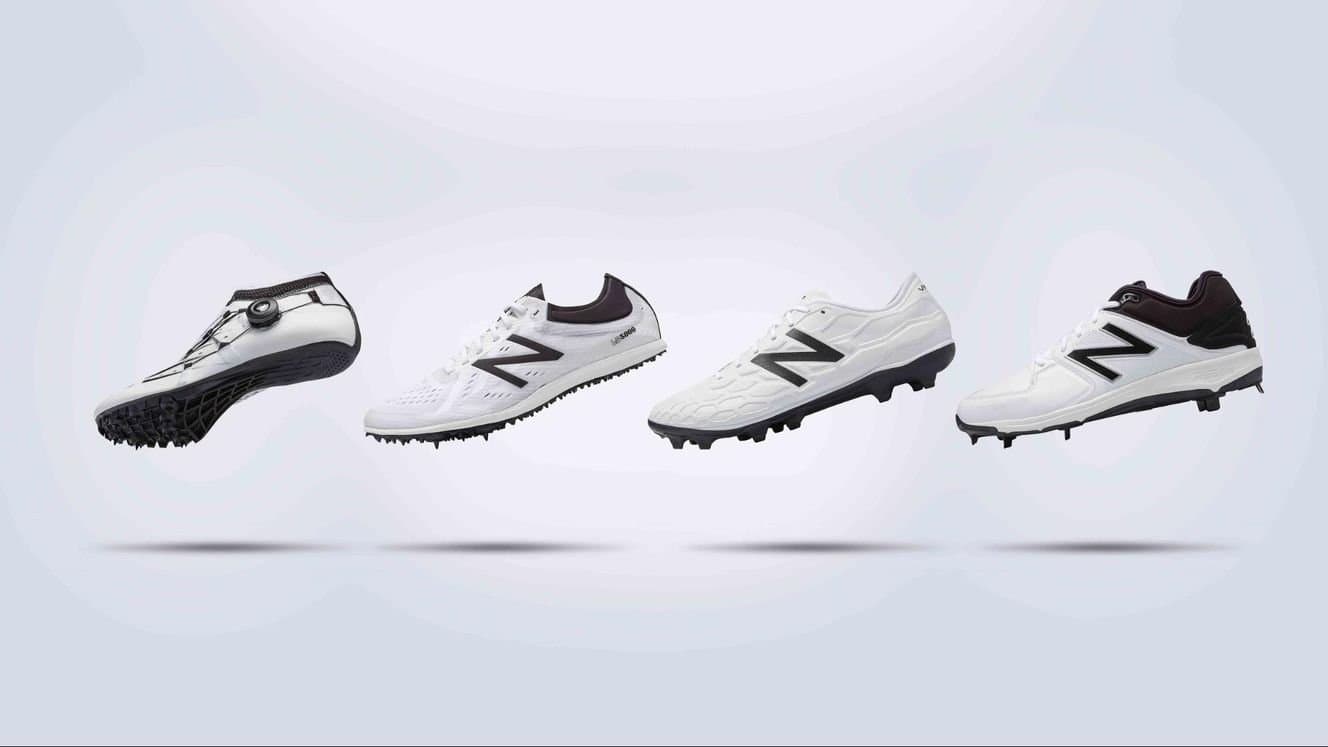
Concepts de chaussures avec des semelles imprimées en 3D par New Balance.
Découvrez comment l'impression 3D et les technologies numériques transforment l'ingénierie et la production industrielle
Téléchargez le rapport de la Digital Factory et écoutez le podcast pour en savoir plus sur la transition numérique de la production industrielle, l'intelligence artificielle, la robotique et l'automatisation. Assistez à la prochaine conférence The Digital Factory ayant lieu à Boston, le 7 mai, pour entendre des responsables innovants du secteur de la production industrielle numérique, et notamment le PDG de Align Technologies, le PDG de FedEx, le PDG de GE, le PDG de Desktop Metal, le responsable de production industrielle de Ford Motor et bien d'autres encore.
Les progrès rapides du matériel et des matériaux utilisés en fabrication additive et la baisse constante du coût par pièce permettent d'envisager de nombreuses applications à volume de production faible à moyen. Vous y verrez comment les fabricants leaders exploitent la fabrication additive pour économiser sur les coûts, réduire les délais de réalisation, et résolvent des problèmes complexes, du prototypage à la production.