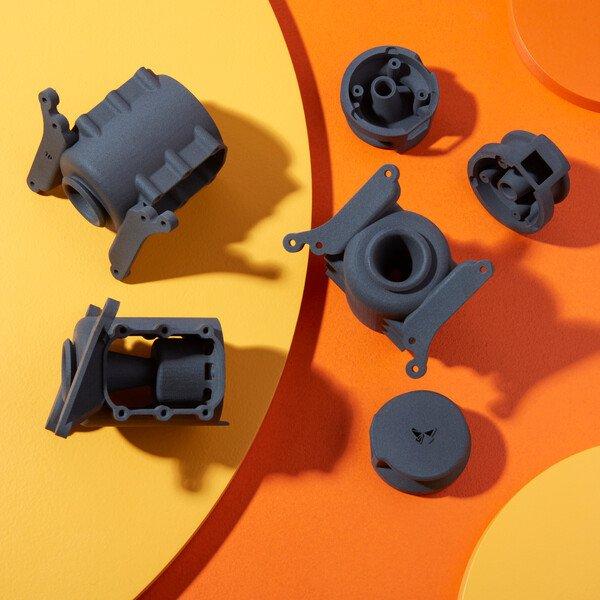
Pièces finales imprimées sur la Fuse 1
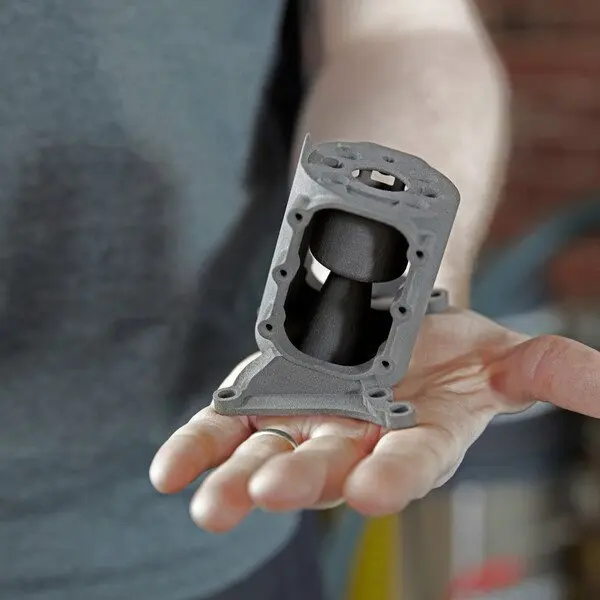
Un purgeur de capteur IR imprimé sur la Fuse 1 avec Nylon 12 Powder
Construire la Fuse 1 a été un vrai défi d’ingénierie. Intégrer une performance de niveau industriel à une imprimante 3D SLS (frittage sélectif par laser) de bureau minimaliste a nécessité des années de travail d’ingénierie et de conception.
L’un des outils utilisés pour réaliser des prototypes a été la Fuse 1 elle-même. Mais le recours à l’impression 3D ne s’est pas arrêté au prototypage. Aujourd’hui, toutes les Fuse 1 livrées aux clients contiennent plusieurs pièces de production imprimées directement sur la Fuse 1 avec Nylon 12 Powder.
L’utilisation de l’imprimante SLS Fuse 1 pour le prototypage et la création de pièces finales offrait trois avantages principaux selon Seth Berg, le responsable du programme d’ingénierie supervisant la Fuse 1 :
- La liberté de créer des pièces complexes sans structures de support internes.
- L’allègement de la chaîne logistique en prototypant et en créant des pièces finales en interne.
- L’élimination de la sous-traitance afin d’obtenir une solution économique pour la production en série limitée avec un matériau en Nylon 12 Powder éprouvé et polyvalent.
Prototypage SLS et production en interne : Imprimer un purgeur de capteur IR
Seth Berg nous parle de l’impression de pièces finales sur la Fuse 1
Quand les utilisateurs installent leur nouvelle imprimante Fuse 1 et unité de post-traitement Fuse Sift, ils ne savent peut-être pas que cinq pièces différentes ont été imprimées sur une Fuse 1. Parmi ces cinq pièces, le purgeur du capteur IR illustre parfaitement le type de pièces idéales pour la production en série limitée à l’aide de l’impression 3D SLS.
L’un des principaux obstacles lors de la création de la Fuse 1 a été de mesurer et d’équilibrer la température à l’intérieure de la chambre de fabrication. Seth Berg savait qu’il était confronté à l’un des ses derniers obstacles avant l’expédition de la Fuse 1 : son équipe et lui avaient besoin d’un purgeur de capteur IR sur mesure afin de réguler convenablement la chaleur à l’intérieur de la baie d’impression. Étant donné que la précision de la température était extrêmement sensible à l’intérieur de la chambre d’impression, l’équipe s’attendait à devoir fabriquer des douzaines de prototypes avant de trouver les purgeurs de capteur IR qui fonctionnent correctement et la perspective de devoir sous-traiter ou utiliser un moulage par injection n’était pas idéale en raison du nombre de prototypes nécessaires. C’est pourquoi l’équipe s’est tournée vers ses unités test de la Fuse 1, alimentées en Nylon 12 Powder, pour créer des prototypes des pièces et produire ces dernières. « Nous avions besoin d’une technologie d’impression 3D qui ne nous limitait pas en matière de géométrie ou plaçait des points de contact de support sur les surfaces sur lesquelles nous voulions un écoulement fluide de l’air. Le frittage sélectif par laser était vraiment la seule option d’impression 3D qui allait réussir ça pour nous », a déclaré Seth Berg.
C’est pourquoi l’équipe a pu travailler en utilisant les premières unités de production de la Fuse 1 pour concevoir, tester et, au final, fabriquer des composants sur mesure à grande échelle afin que nous puissions commercialiser la Fuse 1. Au fil du temps, les concepteurs ont commencé à créer davantage de pièces : des poignées de portes, des poignées IR, des poignées pour la Fuse Sift, le tout en interne sur leurs unités test de la Fuse 1. Aujourd’hui, toutes les Fuse 1 livrées contiennent plusieurs pièces de production imprimées directement sur la Fuse 1. « Nous avons rigoureusement testé ces pièces. Nous avons près de 50 imprimantes au siège que nous utilisons en continu pour imprimer ces pièces. Nous les avons testées dans le cadre d’une application d’impression réelle pendant des milliers d’heures », a déclaré Seth Berg.
Après des douzaines de prototypes du purgeur de capteur IR, l’équipe s’est mis d’accord sur un design final. Les membres de l’équipe sont passés sans difficulté du prototypage à la production en série limitée sur les mêmes imprimantes Fuse 1. Avec des milliers de pièces imprimées chaque semaine, la chaîne de production de la Fuse 1 a confirmé le fait que la machine était prête à être expédiée. Seth Berg ajoute : « Chez Formlabs, nous pensons à l’accessibilité des produits du point de vue du prix, afin d’en faire un produit que vous avez les moyens d’acheter, mais également du point de vue de la maintenance. La pire chose qu’il puisse se produire est d’arriver le matin et de voir que votre impression a échoué. C’était réjouissant de voir la Fuse 1 en action à la fois en tant que moteur central du prototypage et en tant que machine de production à temps plein. »
En raison de la capacité d’agencement dense de la Fuse 1, la chambre de fabrication est capable de contenir 12 purgeurs de capteur IR par cycle d’impression. Pour les pièces plus petites, telles que la poignée du capteur IR, ce nombre passe à 60 pièces par cycle d’impression. Bien que l’impression 3D en interne ne soit pas encore pertinente pour la production en série de millions de pièces, de multiples machines travaillant en tandem sont une excellente solution pour les lots de petites et moyennes tailles. La poignée du capteur IR nécessite 22 g de poudre pour imprimer, ce qui coûte 2 $ par pièce. Le purgeur du capteur IR principal utilise 70 g de poudre, coûtant ainsi environ 7 $ par pièce.
Selon Seth Berg, « avoir la Fuse 1 en interne a réellement permis d’obtenir un purgeur de capteur IR qui fonctionne plus efficacement, parce que nous avons pu créer des itérations plus rapidement et tester davantage de modèles. Nous avons ensuite pu passer directement à la production en utilisant le même matériau. » Cela signifie que l’équipe n’a pas eu à modifier ou peaufiner les tolérances entre le prototypage et la production.
Seth Berg
Disposer de la Fuse 1 en interne a réellement permis d’obtenir un purgeur de capteur IR qui fonctionne plus efficacement, parce que nous avons pu créer des itérations plus rapidement et tester davantage de modèles. Nous avons ensuite pu passer directement à la production en utilisant le même matériau.
Sans la Fuse 1, Seth Berg affirme que l’équipe aurait été forcée de sous-traiter le frittage sélectif par laser pour ces pièces. Il ajoute que « si nous n’avions pas la Fuse 1 en interne, nous aurions sous-traité les pièces imprimées par SLS à un atelier de composition et nous aurions payé plus tout en devant attendre plus longtemps pour recevoir ces pièces. La Fuse 1 imprime en interne des pièces imprimées par SLS finales de qualité industrielle pour une fraction du prix et du temps normalement nécessaires. »
Seth Berg déclare que son équipe « est tellement convaincue que ces pièces fonctionnent pour notre application que chaque Fuse 1 que nous expédions possède des pièces qui ont été imprimées sur la Fuse 1. » Le purgeur du capteur IR, la poignée IR, la poignée de porte et le couvercle de l’aimant de verrouillage ont tous été développés grâce à la Fuse 1.
Nylon 12 Powder pour pièces finales
Le premier matériau de Formlabs lancé pour la Fuse 1 est Nylon 12 Powder, un matériau efficace conçu pour le prototypage fonctionnel et la production finale d’assemblages complexes et de pièces durables qui est doté d’une stabilité environnementale élevée.
Tandis que les autres procédés d’impression 3D peuvent être utilisés pour les pièces finales, l’impression SLS offre un ensemble de propriétés différentes qui rendent avantageuse l’impression de pièces pour la Fuse 1. Tout d’abord, les pièces SLS ont tendance à être plus durables, en particulier quand elles sont manipulées ou utilisées tous les jours. En comparaison avec les matériaux de stéréolithographie, les impressions en Nylon 12 Powder offrent une durée de vie optimisée, un faible fluage, ainsi qu’une meilleure résistance à l’usure, aux produits chimiques et aux UV. « En fin de compte, il existe de nombreux types de pièces finales différentes, mais la quasi-totalité d’entre elles doivent être solides, elles doivent résister à la fois aux températures et aux chocs. Le nylon est un matériau qui trouve réellement le juste équilibre entre toutes ces différentes propriétés. Donc, si vous pouvez penser à une application pour laquelle vous voulez imprimer une pièce et l’utiliser, le nylon est presque à coup sûr une option adéquate », affirme Seth Berg.
L’une des caractéristiques particulièrement marquantes de l’impression par poudre SLS lors de la création d’un purgeur de capteur IR sur mesure a été la capacité à imprimer des pièces sans supports internes. Avec les autres procédés d’impression 3D, les fentes et les orifices internes nécessiteront des structures de support et les pièces devront être conçues en gardant ceci à l’esprit. L’impression SLS élimine ce problème en permettant à des pièces complexes d’être créées et utilisées tout en réduisant considérablement le temps nécessaire à la post-production.
Pour finir, Nylon 12 Powder permet à la Fuse 1 d’imprimer avec jusqu’à 70 % de poudre recyclée. Il s’agit d’un avantage considérable pour le prototypage et la production sur la Fuse 1, permettant ainsi aux équipes d’ingénierie de tirer profit de chaque gramme de poudre achetée. L’équipe de Seth Berg s’est rendu compte qu’il s’agissait de l’une des raisons essentielles pour lesquelles la Fuse 1 était une option de production avantageuse, affirmant ainsi que « toutes les pièces imprimées et installées sur la Fuse 1 sont imprimées avec 70 % de poudre réutilisée. C’est l’un des secrets qui font d’elle une option de fabrication compétitive pour nous en interne. » Il poursuit : « Et nous n’avons pas utilisé de la poudre recyclée uniquement pour les prototypes. Sur la ligne de production de la Fuse 1, toutes les pièces que nous imprimons utilisent 70 % de poudre recyclée. Cela inclut également les pièces finales. »
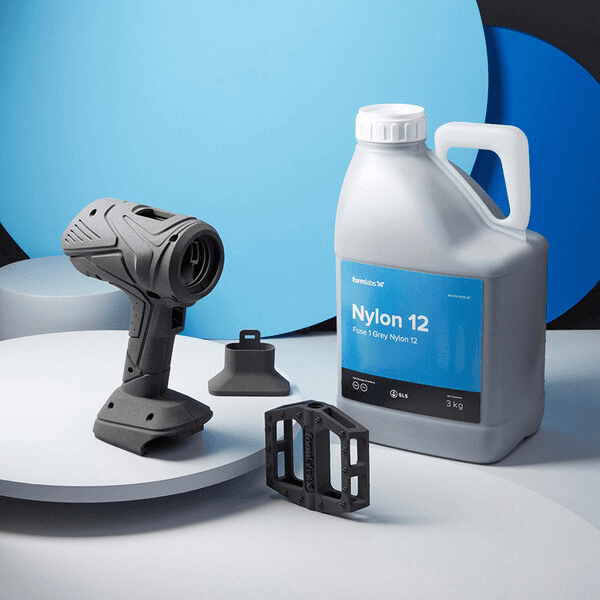
Nylon 12 Powder
Nylon 12 Powder est un matériau puissant conçu pour le prototypage fonctionnel et la production finale d’assemblages complexes et de pièces durables, doté d’une stabilité environnementale élevée. Nous avons préparé une publication couvrant les questions que vous nous avez le plus fréquemment posées.
La Fuse 1 : Désormais disponible
Formlabs est réputée pour concevoir des processus de fabrication additive rendant accessible l’impression 3D de qualité industrielle à des entreprises de toutes tailles. La Fuse 1 et la Fuse Sift donnent aux entreprises les moyens de maîtriser le processus de conception, d’imprimer en interne des pièces en nylon prêtes pour la production, d’augmenter le volume de production et de disposer de l’impression 3D par SLS de niveau industriel dans leurs ateliers, à un prix d’entrée de gamme. Tous ces concepts, la polyvalence de Nylon 12 Powder et les avantages uniques de l’impression 3D par SLS se sont rassemblés pour aider Seth Berg et l’équipe d’ingénierie de Formlabs à créer une meilleure Fuse 1.
Vous voulez savoir à quoi ressemble une pièce imprimée sur la Fuse 1 ? Demandez un échantillon gratuit dès maintenant.