Des pièces 3D dans des presses d'imprimerie : applications robotiques et pièces de rechange chez HEIDELBERG
Heidelberger Druckmaschinen AG est le premier fabricant mondial de presses offset. Il est présent dans plus de 170 pays et emploie près de 10 000 personnes dans le monde. L’entreprise fabrique une vaste gamme d’équipements et de technologies d’automatisation pour l’ensemble de la chaîne d’impression, des presses à grande vitesse aux machines de découpe et de pliage.
Il y a environ six ans, HEIDELBERG a ajouté une nouvelle technologie à ses flux de travail : l'impression 3D. Au départ, ils ont adopté cette technologie pour optimiser le prototypage et le développement de produits en réduisant les coûts et les délais. Mais aujourd'hui, l'entreprise imprime en 3D des pièces pour la production en série, fabriquant des milliers de pièces par an pour une quinzaine d'applications différentes.
Découvrez comment les pièces imprimées en 3D par frittage sélectif par laser (SLS) permettent de créer des applications robotiques légères et peuvent même remplacer les pièces en acier dans les machines à plier.
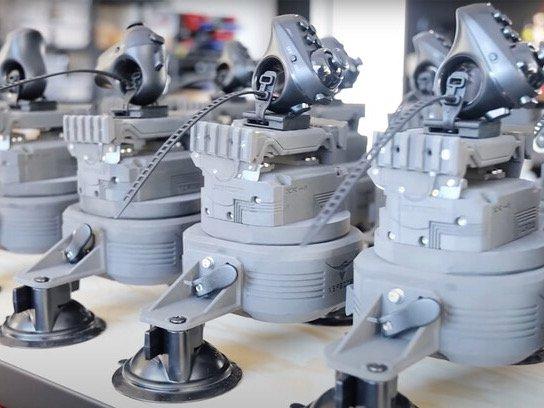
Test de résistance de pièces imprimées en 3D pour les applications finales
Ce livre blanc présente le matériel d'impression 3D et les solutions matérielles de Formlabs pour produire des pièces d'utilisation finale. Il documente les études de cas de divers utilisateurs et inclut les résultats de tests de résistance pour prouver l'adéquation des matériaux d'impression 3D aux applications finales.
Accélérer le développement de produits
« HEIDELBERG s'adresse à nous pour des projets liés à de nouveaux développements, en particulier pour les développements de composants et de sous-ensembles qui sortent du cadre de la fabrication conventionnelle », nous confie Joachim Krumma.
Après avoir travaillé pendant 15 ans chez HEIDELBERG dans le domaine du développement de produits et d'applications, M. Krumma dirige aujourd'hui CTS-3 GmbH, une société de conseil dans le secteur de la fabrication additive. L’entreprise collabore étroitement avec l’équipe de recherche et de développement de HEIDELBERG pour le développement de produits et pour le transfert de nouvelles technologies vers la production en série.
Une partie du développement se fait à partir de tests pratiques, ce qui permet d’évaluer directement le produit HEIDELBERG et ainsi de l’améliorer grâce aux commentaires en temps réel du client final.
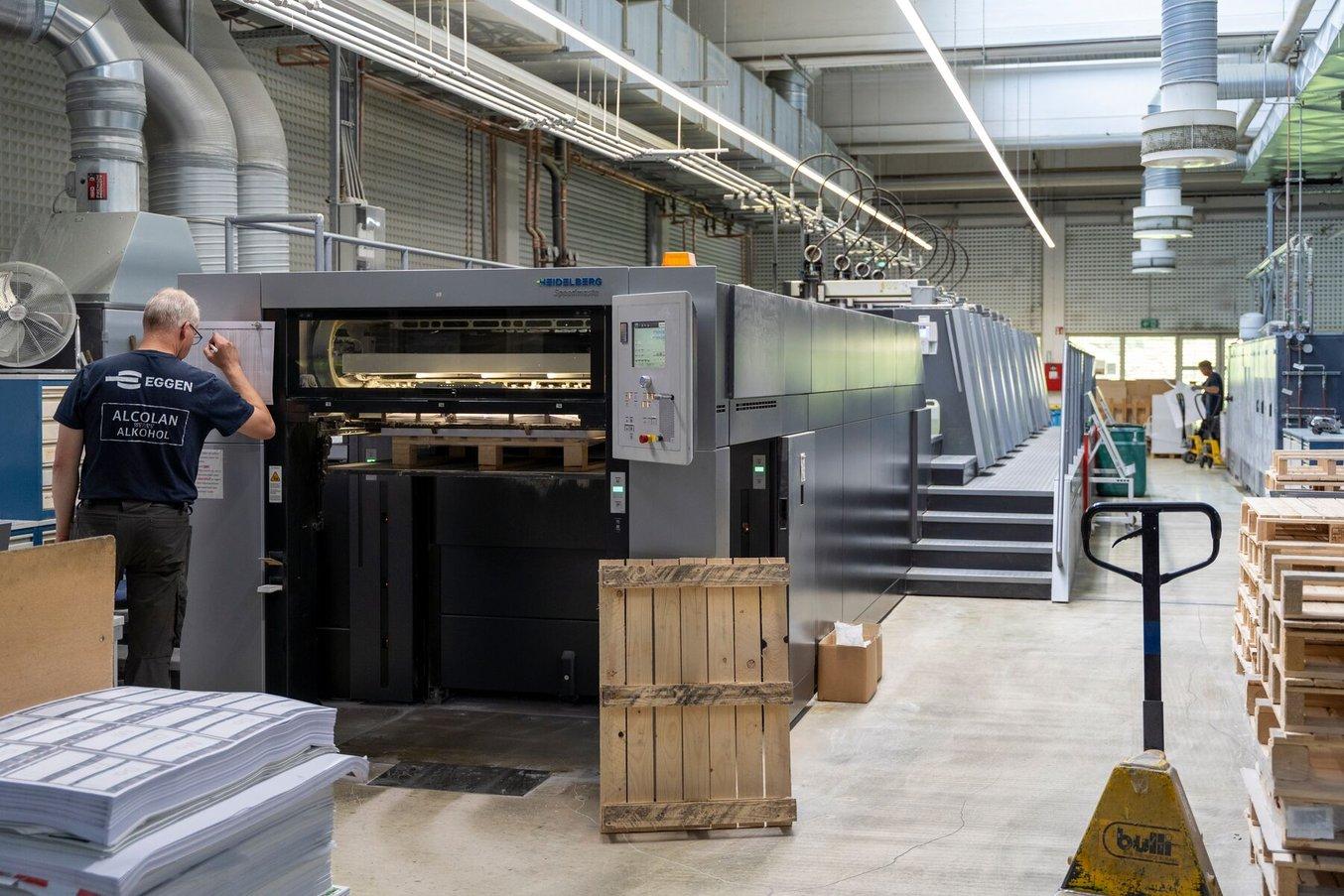
Meinders & Elstermann est une grande imprimerie offset située à Belm.
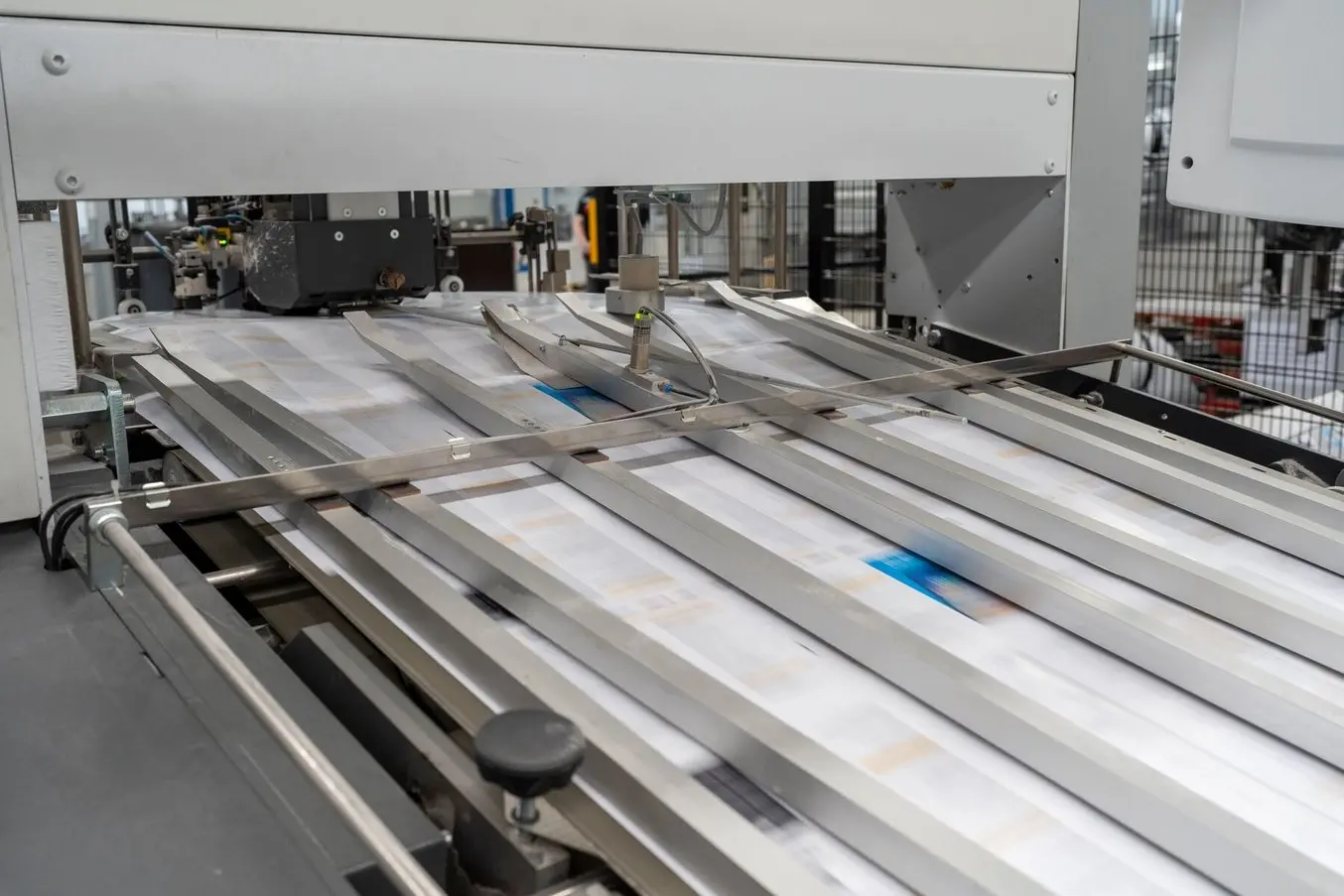
Les nouveaux produits HEIDELBERG sont testés et développés sur place.
« Meinders & Elstermann est une grande imprimerie offset située à Belm. Nous imprimons environ 100 à 120 millions de feuilles de papier par an. Nous disposons de quatre machines à imprimer HEIDELBERG dans l'atelier d'impression et de sept plieuses dans le département de finition des imprimés. Les machines que HEIDELBERG souhaite lancer sur le marché sont testées par nos soins et font l'objet d'un développement continu chez nous », a déclaré Klaus Harig, chef du département de transformation chez Meinders & Elstermann GmbH & Co. KG.
Les pièces imprimées en 3D sont utilisées ici pour un large éventail d'applications : il y a des pièces légères pour les robots de transfert, de nouveaux composants pour les plieuses, et des pièces de rechange pour les composants de machines qui étaient auparavant fabriqués en acier. Pour produire toutes ces pièces, l'équipe utilise une imprimante 3D SLS de la série Fuse, sur laquelle sont imprimées des pièces rigides en Nylon 12 Powder et des pièces flexibles en TPU 90A Powder.
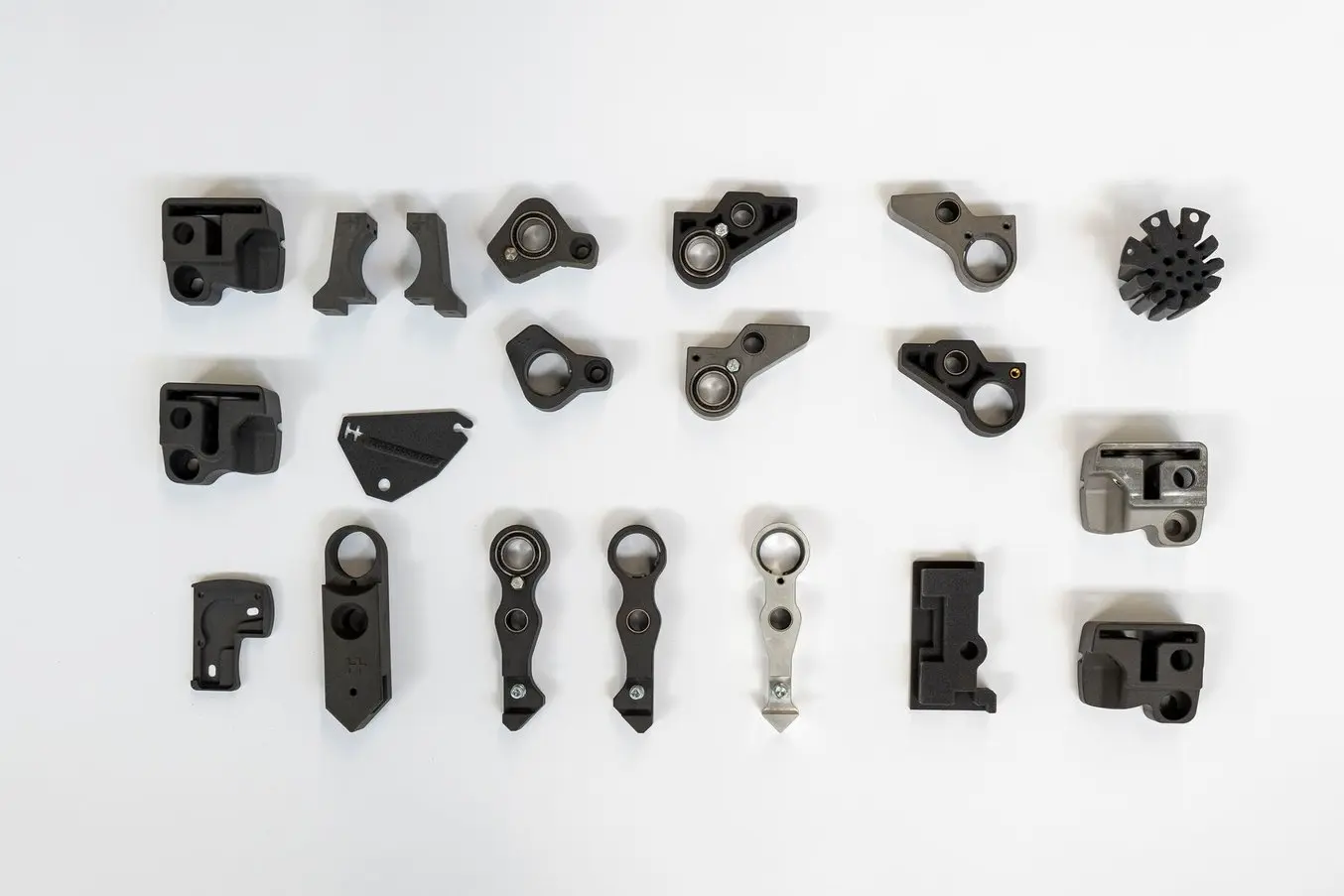
Chez HEIDELBERG, les pièces imprimées en 3D sont utilisées pour une large gamme d'applications, comme des pièces légères pour les robots ou des pièces de rechange pour les composants de machines qui étaient auparavant fabriqués en acier.
« Le point le plus important pour nous est la vitesse de l'impression 3D. Nous répondons rapidement aux exigences des clients, qui sont en constante évolution. Nous pouvons développer et produire de nouvelles pièces en un ou deux jours, alors qu'il nous fallait auparavant plusieurs semaines dans certains cas. C'est la raison pour laquelle l'impression 3D est parfaite pour nous. »
Joachim Krumma, Management, CTS-3 GmbH
Outre les délais réduits, l’entreprise peut également se réjouir de réaliser d’immenses économies. C’est particulièrement vrai dans les domaines du prototypage et de la production en série de pièces personnalisées et de petites séries de pièces finales. « Lors de la fabrication de pièces, nous avons souvent une réduction des coûts d’un facteur de 10 ou 20 par rapport à la production conventionnelle », explique M. Krumma.
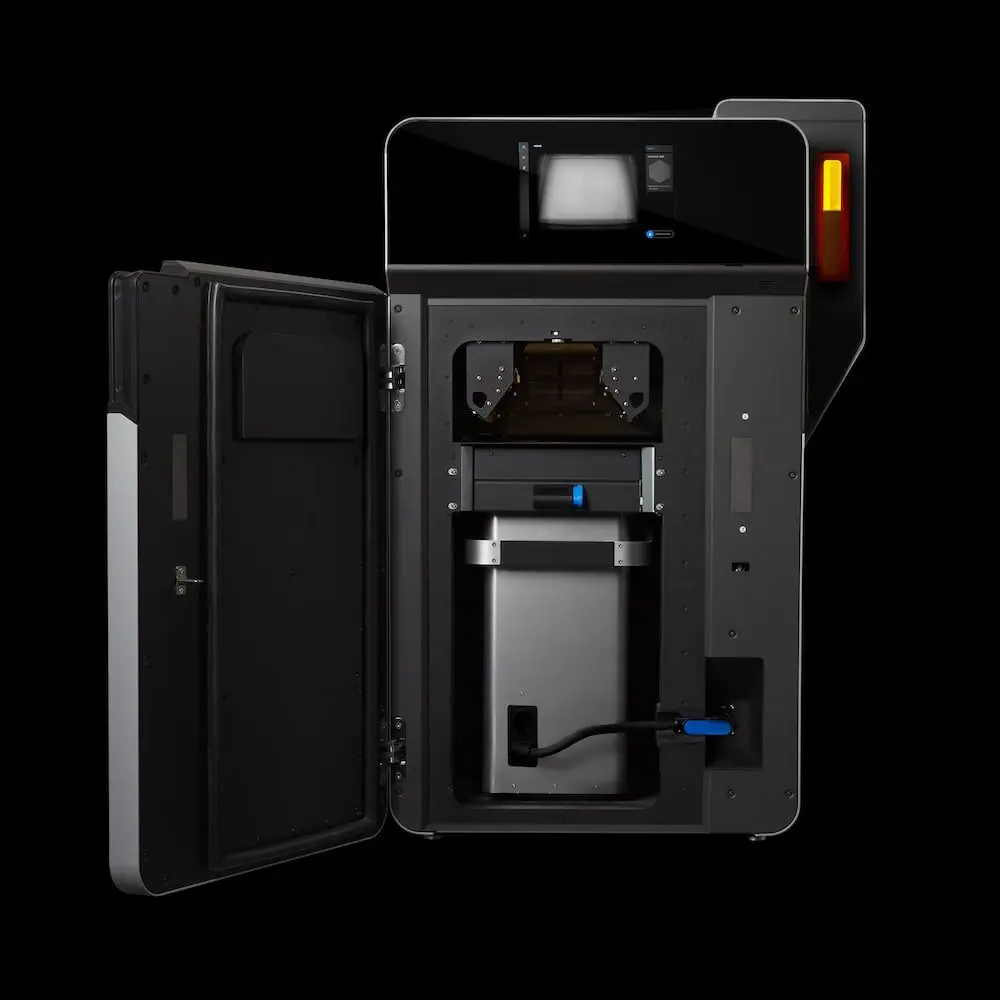
Produire rapidement des pièces SLS haute performance avec la nouvelle Fuse 1+ 30W
Regardez une démonstration détaillée de la Fuse 1 et de l’impression 3D SLS, réalisée par les experts Formlabs.
Pièces légères pour la robotique
Le titre de la machine comportant le plus grand nombre de composants imprimés en 3D revient à la P-Stacker, un système robotisé de pointe qui prend les feuilles pliées en paquets dans la plieuse et les positionne sur une palette.
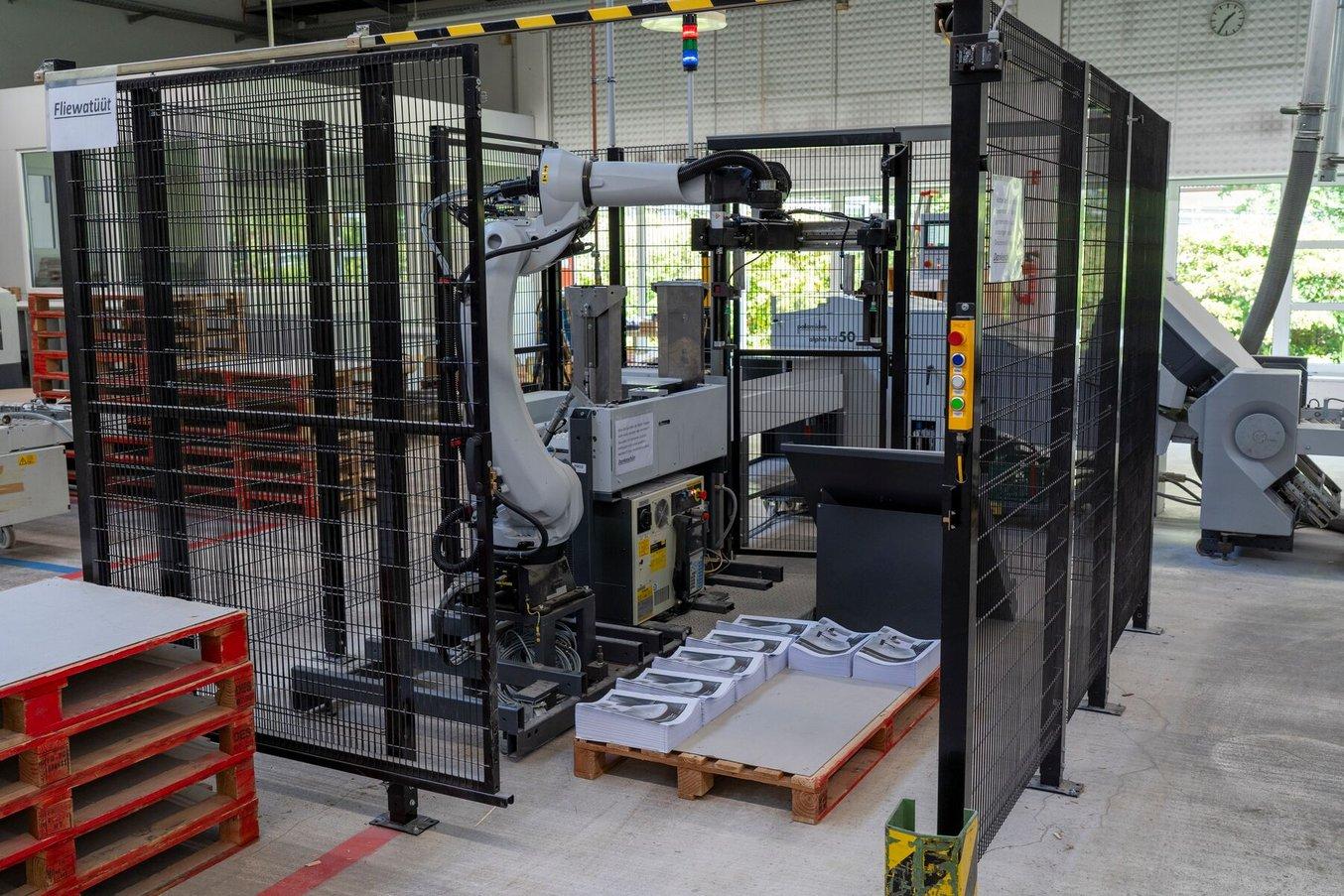
La P-Stacker s’occupe de la tâche fastidieuse d’empiler les paquets derrière la plieuse, ce qui soulage considérablement le personnel.
« Le robot peut empiler les palettes jusqu'à un mètre de haut. Selon sa vitesse de fonctionnement, il peut placer jusqu'à 18 000 feuilles par heure. Avant d'utiliser la P-Stacker, une personne devait déplacer chaque jour quatre à six tonnes de paquets sur des palettes », explique M. Harig.
De nombreuses pièces imprimées en 3D dans ce robot sont très complexes et remplissent plusieurs fonctions simultanément. Par exemple, il contient des joints et des supports qui permettent le mouvement des axes, le serrage des axes, l’effet d’aspiration pneumatique, la technologie des capteurs ainsi que le glissement des pièces.
« Le poids joue un rôle décisif, surtout dans les applications robotiques. Plus le poids est important, plus les pièces sont soumises à des contraintes mécaniques, ce qui affecte leur résistance à la fatigue. Nous avons déjà beaucoup de composants dans le système, ce qui signifie qu'il nous reste peu d'espace pour les assemblages et les pièces de grande taille », a déclaré M. Krumma.
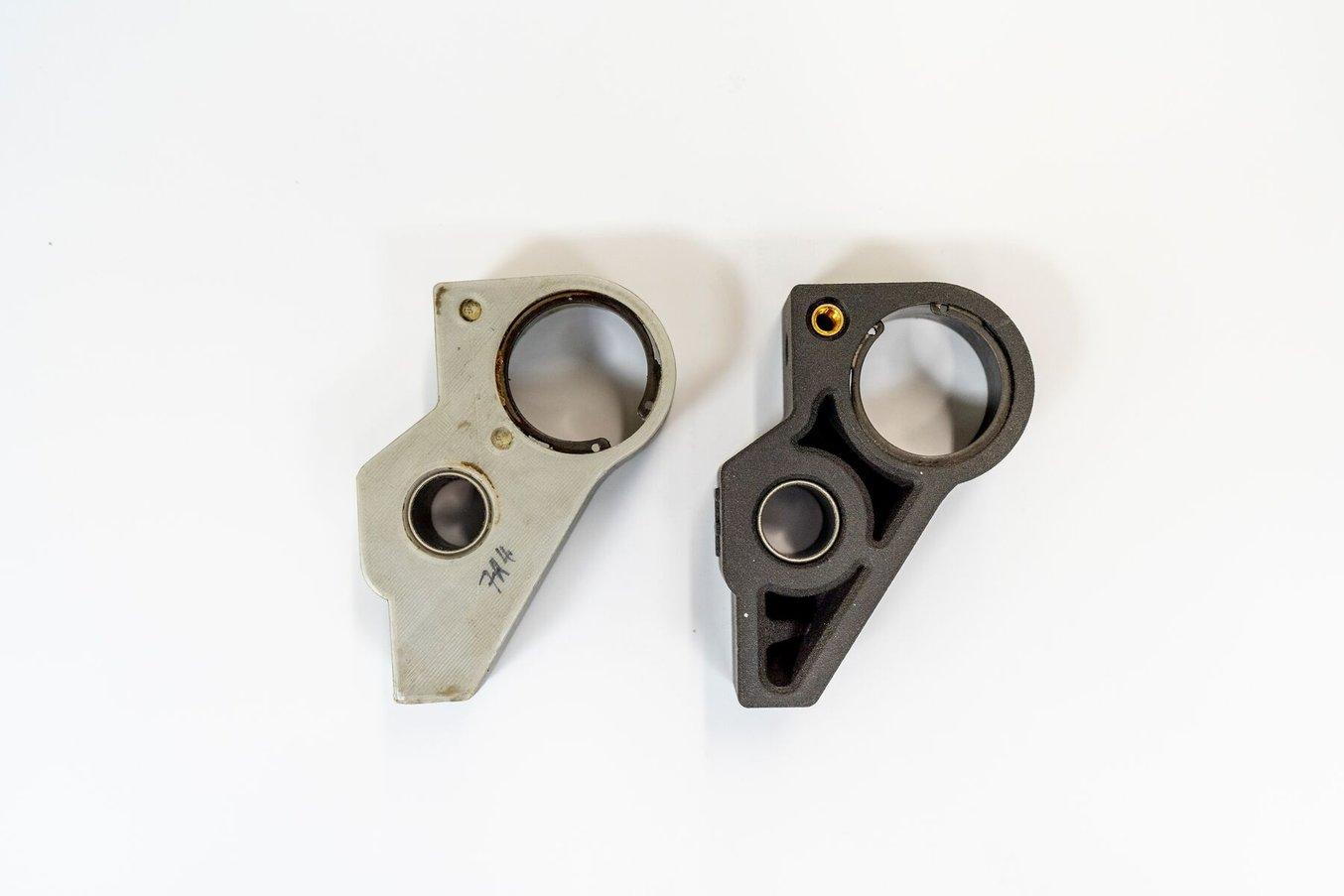
Les pièces en plastique imprimées en 3D sont plus légères que l'acier, et leur conception peut être optimisée en fonction des contraintes et des forces auxquelles elles sont soumises. La complexité accrue de la conception n'entraîne pas de coûts plus élevés, contrairement aux processus de fabrication conventionnels tels que l'usinage.
Il en résulte souvent des structures amorphes très complexes, car la conception est spécialement développée pour l'application considérée en fonction des contraintes et des forces en présence. Les pièces étant constamment utilisées, ces forces peuvent être considérables. Les pièces imprimées en 3D sont souvent combinées à d'autres composants, comme des roulements métalliques ou du téflon couvrant des pièces pour réduire la friction.
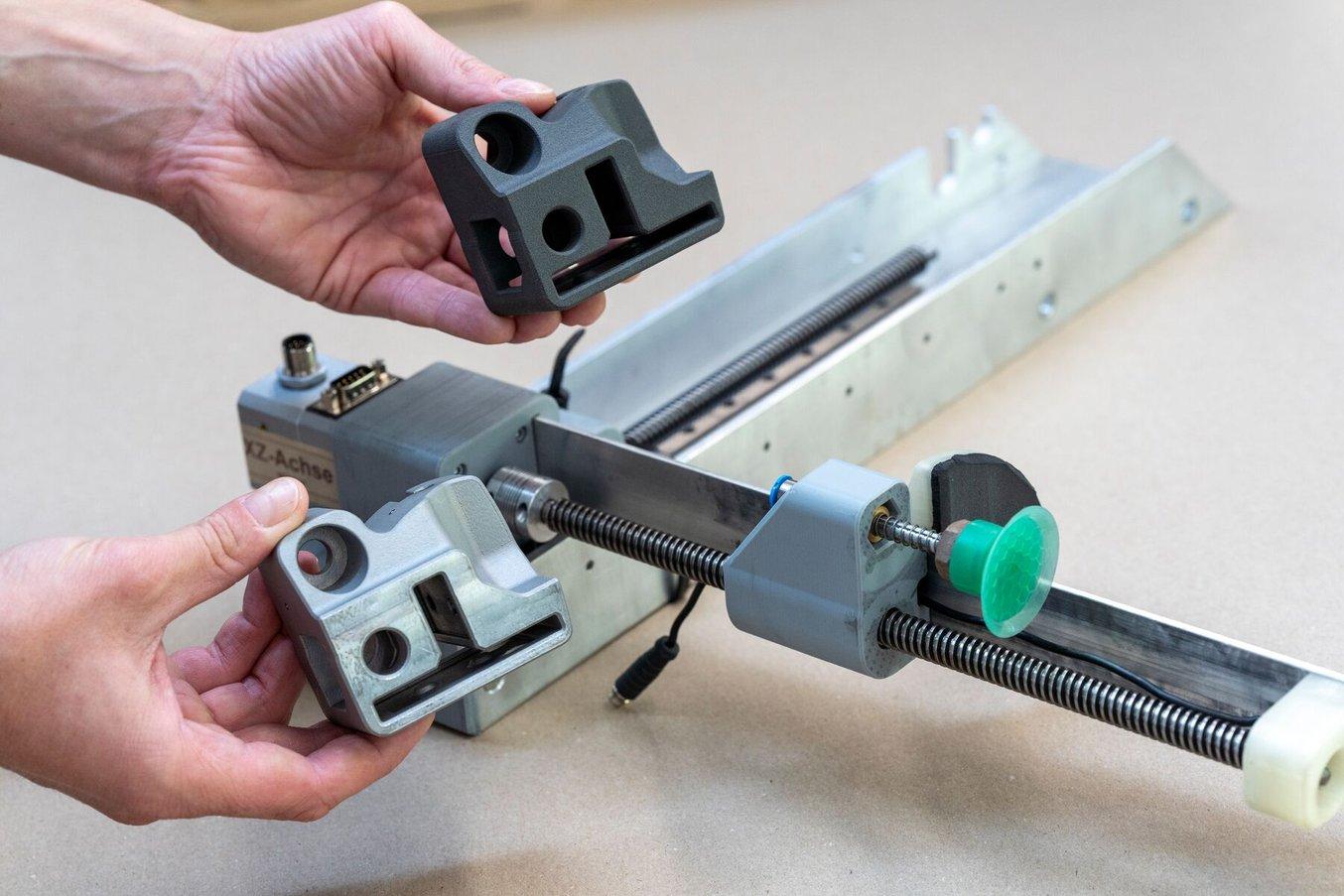
De nombreuses pièces imprimées en 3D sont très complexes et remplissent différentes fonctions. Les composants solides et durables sont fabriqués avec Nylon 12 Powder.
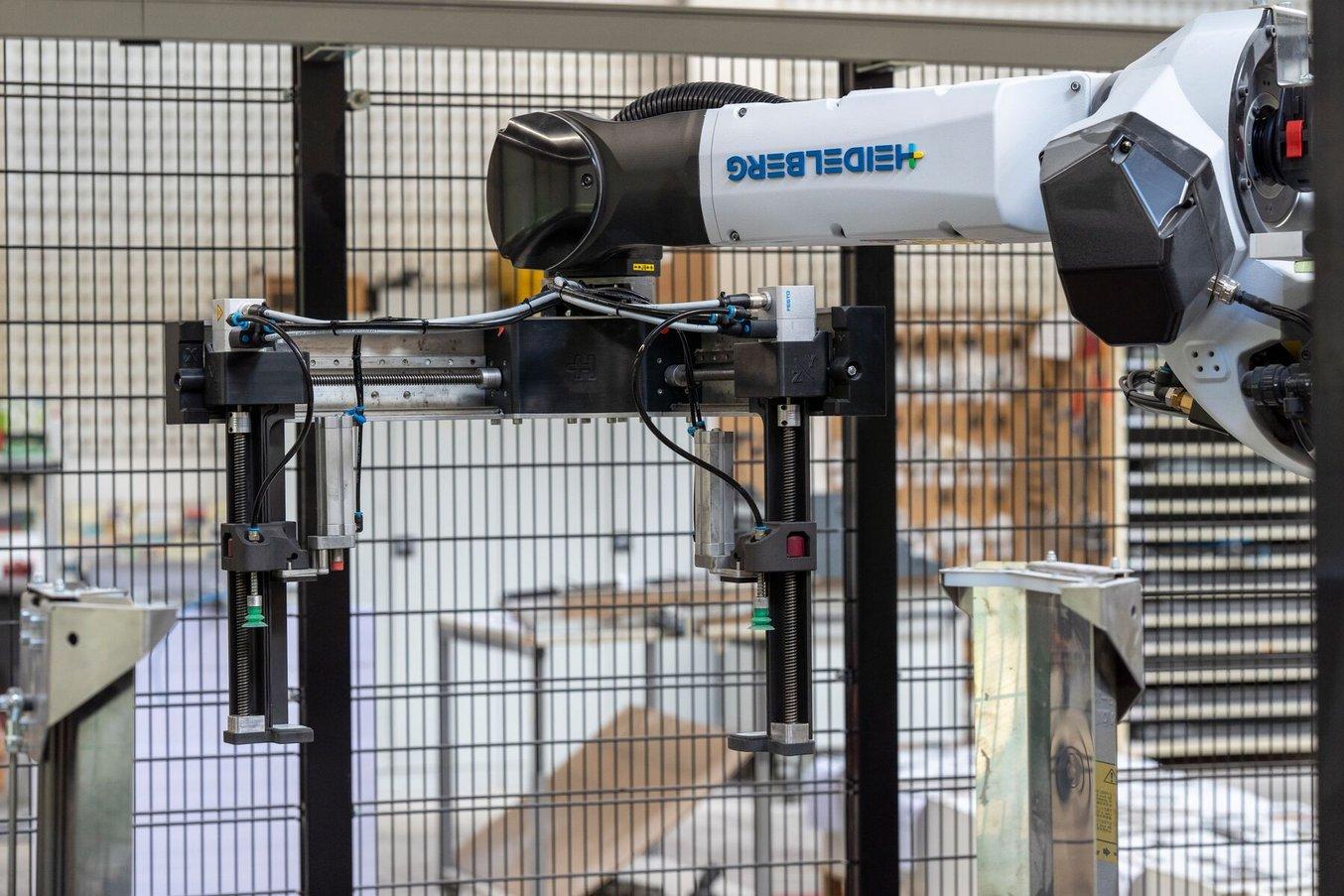
Le poids joue un rôle essentiel en robotique, car il augmente les contraintes mécaniques auxquelles sont soumises les pièces.
Nombre de ces formes complexes ne seraient pas rentables, voire impossibles à fabriquer avec des méthodes traditionnelles tels que l'usinage. Certaines pièces sont constituées de différents assemblages et composants, qui doivent être laborieusement assemblés, alignés et retravaillés. Si ces éléments étaient usinés, ils seraient beaucoup plus lourds et rendraient la densité des composants encore plus élevée.
« Même s'il était possible de fabriquer ces pièces de manière conventionnelle, l'effort à fournir serait énorme par rapport à l'impression 3D. L'impression SLS nous permet de reproduire des formes assez complexes. Nous pouvons ainsi simplifier certains composants et assemblages, car nous sommes capables de développer et d'imprimer des géométries très amorphes. C'est exactement ce que nous voulons. »
Joachim Krumma, Management, CTS-3 GmbH
Certaines pièces sont moins complexes, mais nécessitent tout de même une grande exactitude ou une grande précision. Cela comprend par exemple des pièces flexibles qui empêchent la contamination croisée, couvrent les bords tranchants, protègent les capteurs ou préviennent l'usure.
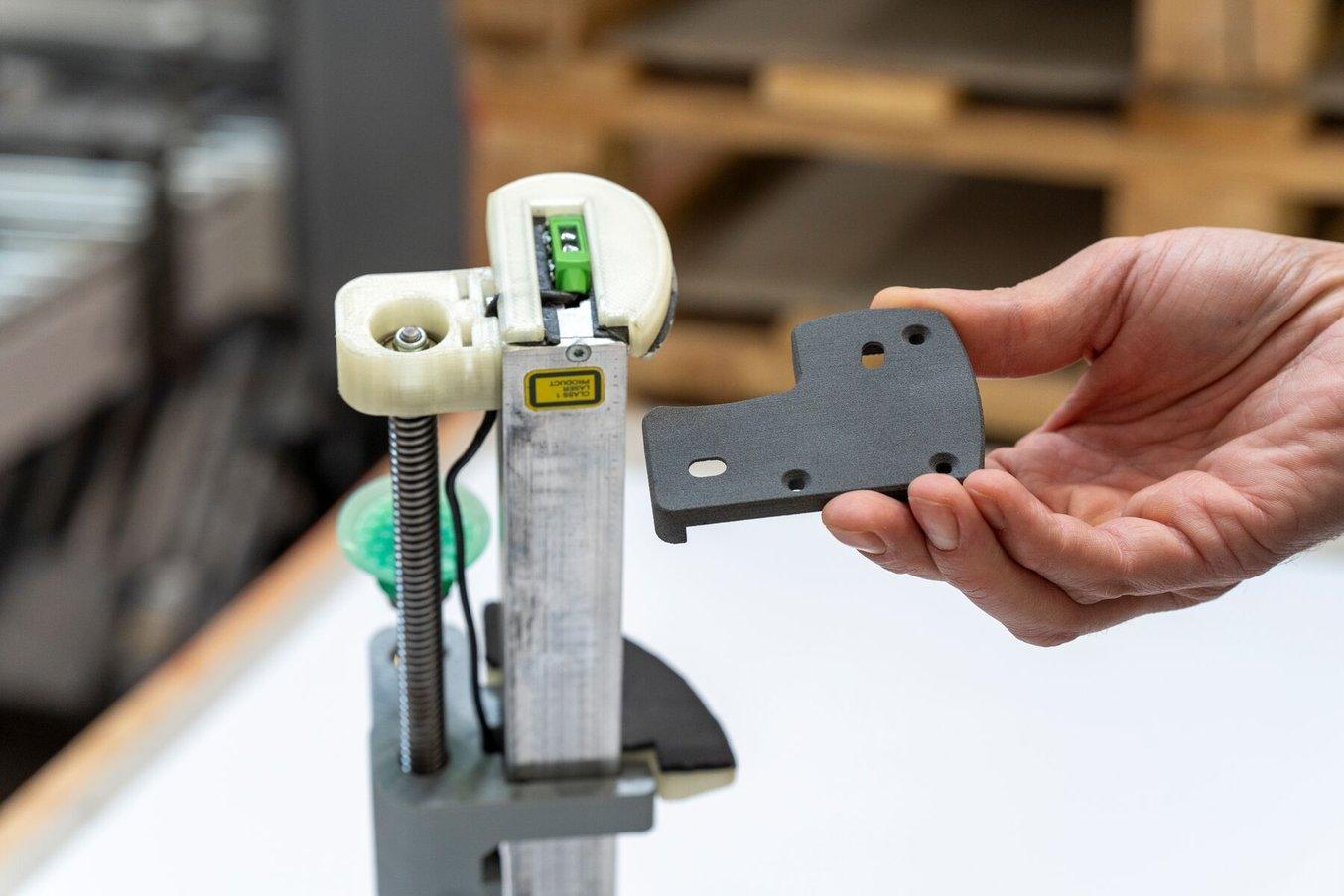
Une pièce flexible imprimée en TPU 90A Powder pour protéger les capteurs et autres outils de fin de bras.
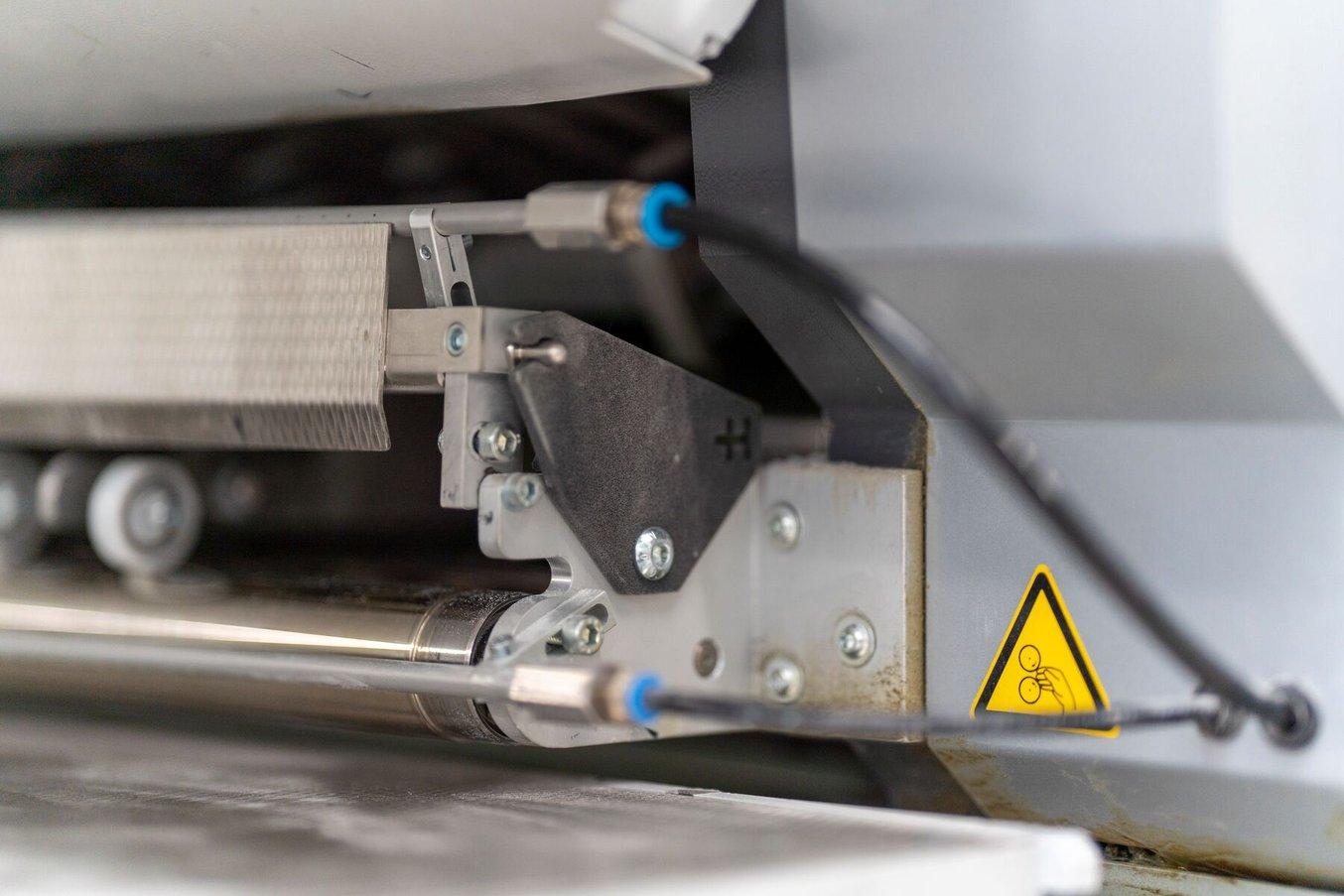
Les pièces flexibles sont idéales pour les composants encliquetables. En couvrant les bords tranchants, elles protègent également les opérateurs.
« Une pièce imprimée en 3D vient d’être installée dans notre robot ; elle permettra d’éviter les ruptures de câbles et devrait naturellement allonger la durée de vie de l’appareil. Nous pouvons ainsi garantir que nous ne serons pas confrontés un jour à une panne nécessitant le remplacement des faisceaux de câbles », explique M. Harig.
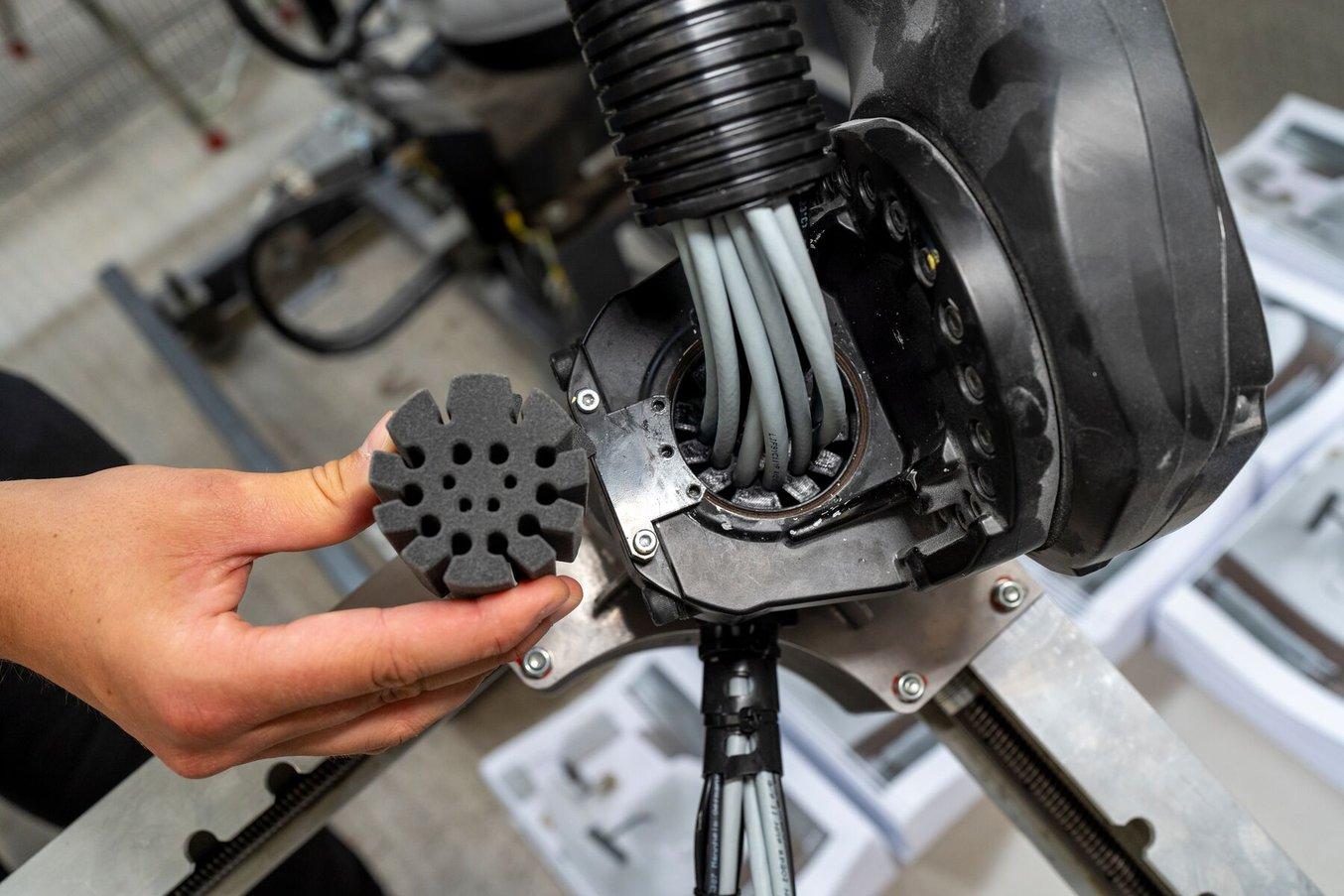
Ce guide-câble flexible produit avec une imprimante 3D SLS de la série Fuse permet une conception complexe et offre une solution durable à long terme pour protéger les câbles de l'usure.
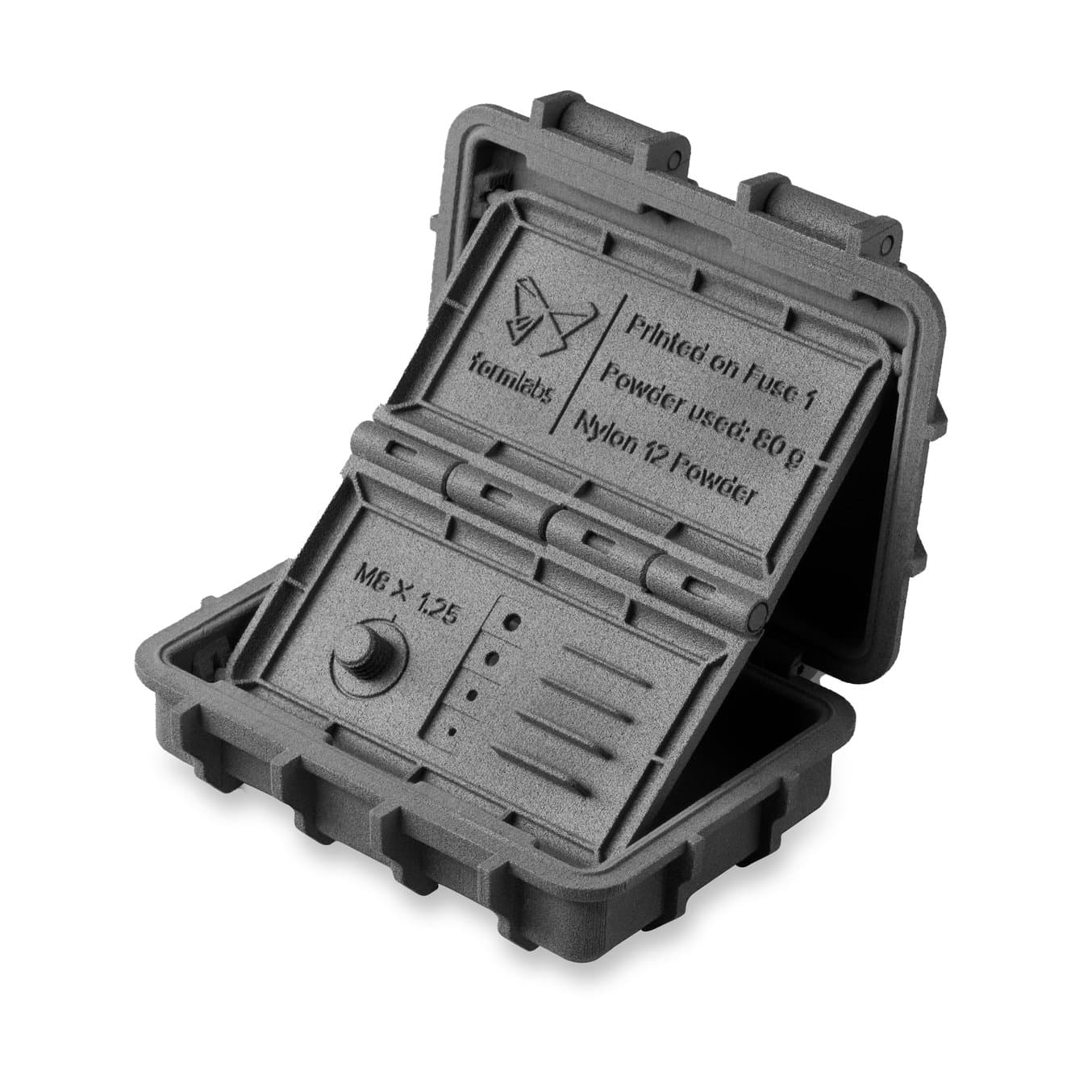
Commander un échantillon gratuit
Examinez et constatez par vous-même la qualité Formlabs. Nous vous enverrons un échantillon gratuit imprimé sur la Fuse 1+ 30W à votre bureau.
Des pièces de rechange qui remplacent l'acier
Minimiser les temps d'arrêt des machines est essentiel pour une entreprise d'imprimerie, car tout retard peut entraîner des délais manqués et rendre le matériel d'impression obsolète. Grâce à son vaste réseau de service à la clientèle, HEIDELBERG peut expédier 95 % des pièces de rechange dans les 24 heures vers n'importe quel endroit du monde. L’équipe voulait toutefois savoir si les pièces imprimées en 3D à la demande pouvaient offrir une solution pour créer des pièces en fin de série.
Dans l'une des anciennes plieuses de Meinders & Elstermann, M. Krumma a installé des pièces imprimées en 3D qui ont remplacé un certain nombre de composants initialement usinés en acier, par exemple des joints pour les rouleaux de métal pesant jusqu'à 13 kg. Les pièces se trouvent à l'intérieur de la machine, où elles sont exposées à un environnement extrêmement sale et huileux. Elles sont soumises à de lourdes contraintes mécaniques et physiques pendant une période d'utilisation prolongée, par exemple en cas d'arrêt d'urgence, où l'ensemble du système de la machine s'arrête en une fraction de seconde.
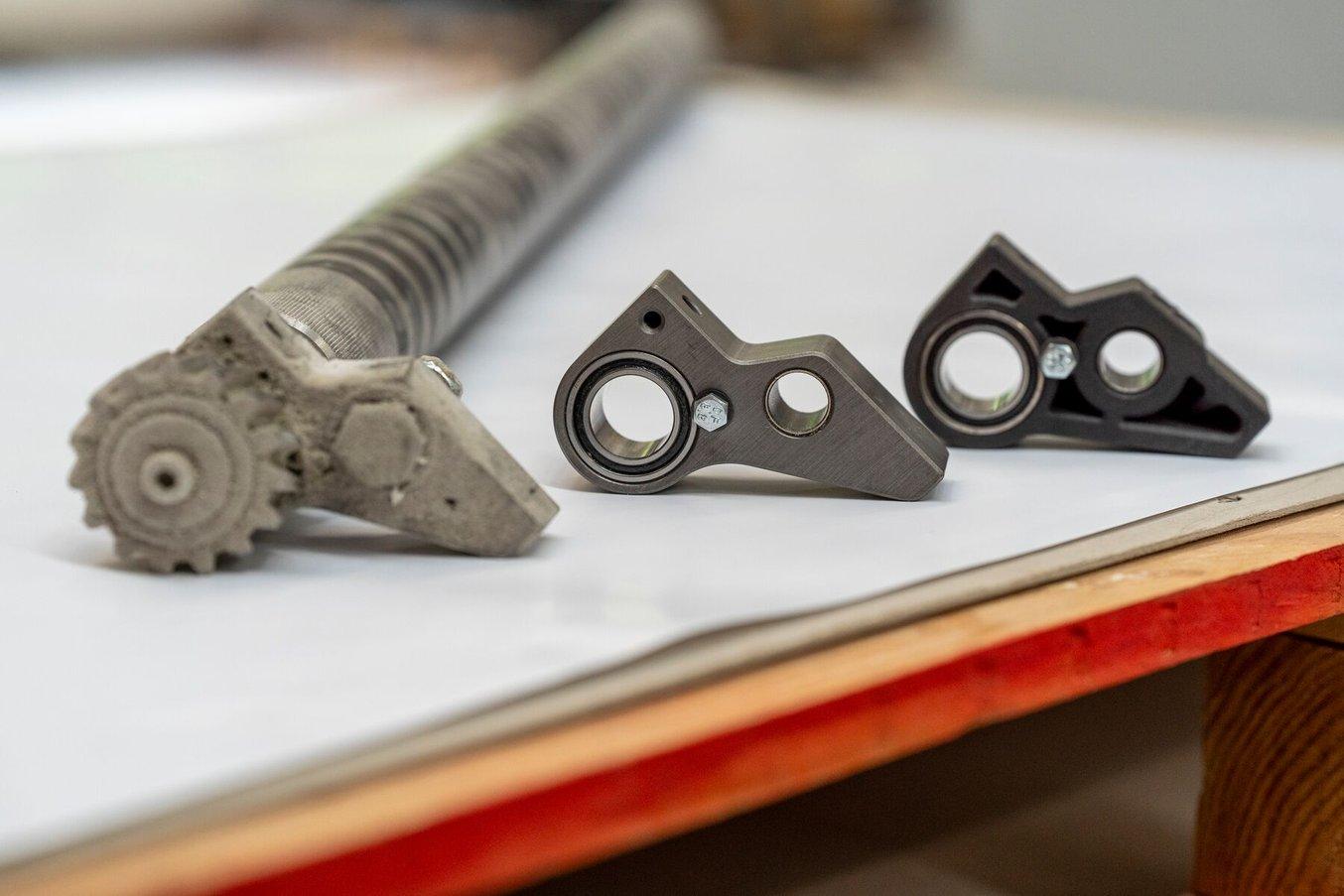
Les pièces de rechange imprimées en 3D sont assemblées avec des roulements et des composants métalliques antifriction.
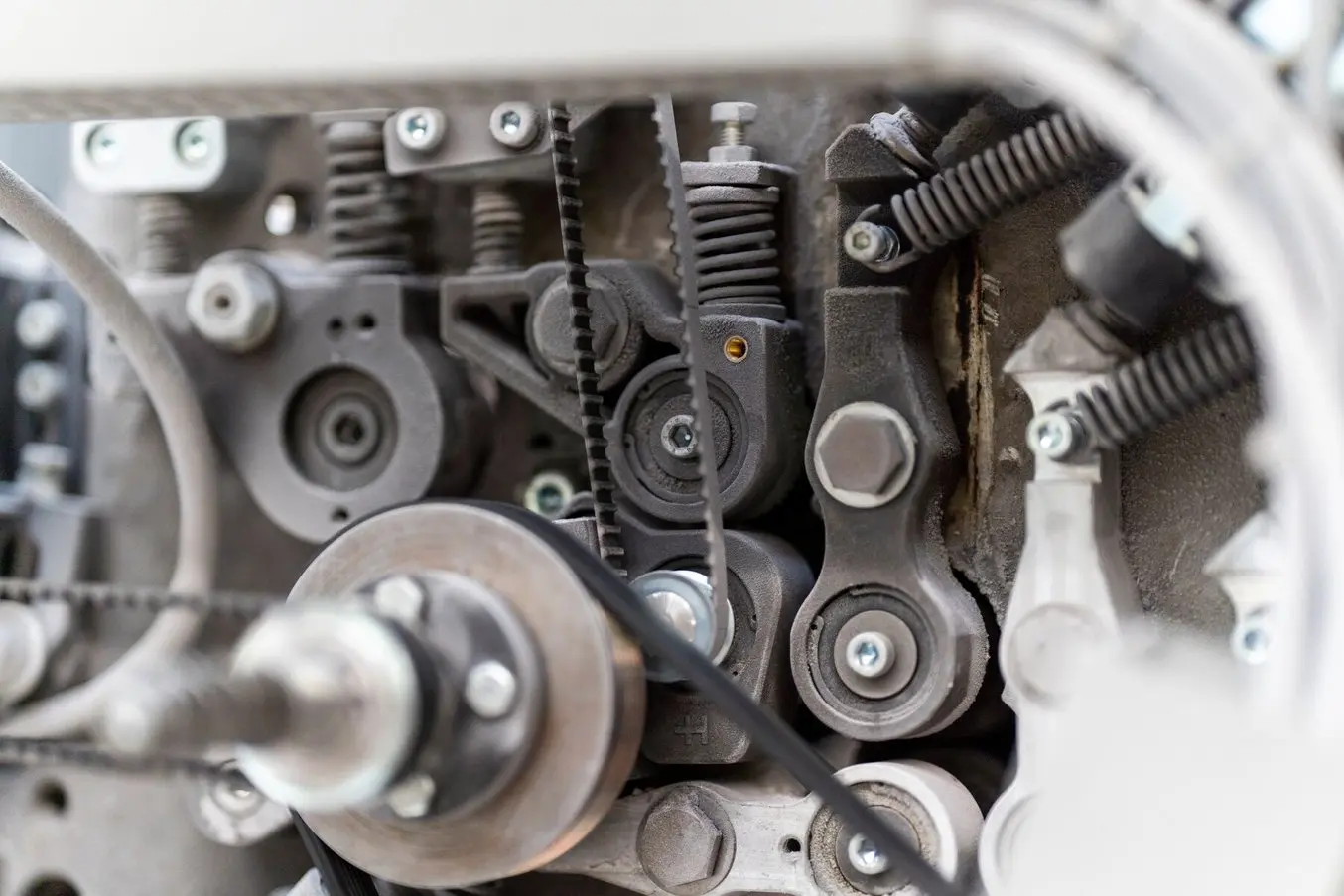
Les articulations maintiennent des rouleaux métalliques qui tournent à grande vitesse et pèsent jusqu'à 13 kg chacun.
« Ils doivent résister à une utilisation continue : deux équipes, cinq jours par semaine, avec une charge extrêmement élevée. Nous avons actuellement ces pièces installées qui sont dans les machines depuis plus de deux ans et demi. Cela n'était pas prévu lors de la phase initiale de développement. Néanmoins, nous avons bien observé ces pièces, et nous avons constaté qu'elles pouvaient résister à cette charge continue. »
Joachim Krumma, Management, CTS-3 GmbH
« Elles sont de toute évidence vraiment solides. J'ai moi aussi du mal à y croire, mais nous n'avons pas encore eu à remplacer de pièces dans nos plieuses », ajoute M. Harig.
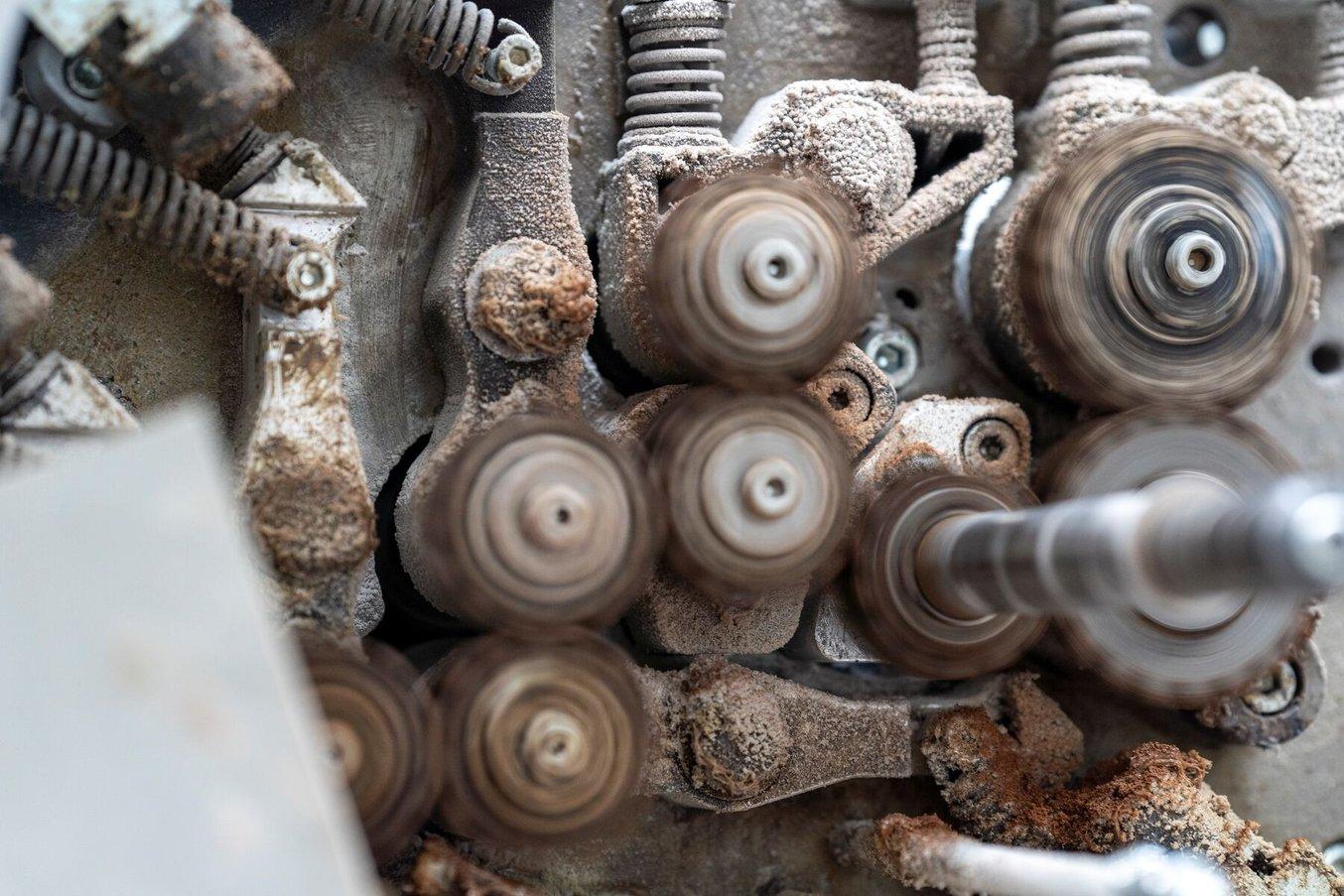
Certaines pièces de rechange imprimées en 3D sont depuis deux ans et demi dans une plieuse utilisée par deux équipes, cinq jours par semaine. Elles sont exposées à un environnement extrêmement sale et huileux.
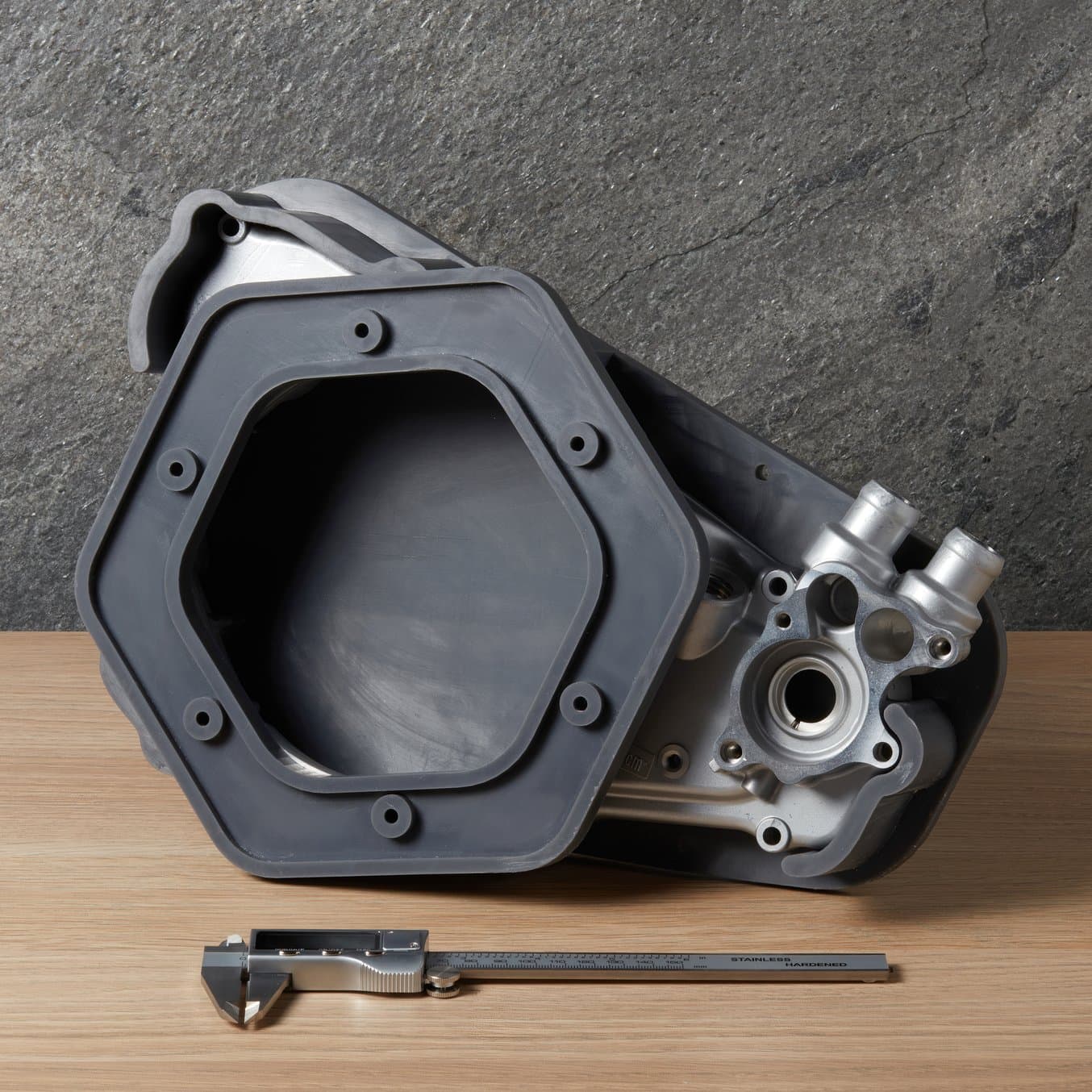
Comment imprimer en 3D des gabarits, des fixations et d'autres aides à la fabrication en interne
Ce livre blanc explique comment créer des gabarits, des fixations et d'autres aides à la fabrication en interne
Garder les imprimeries compétitives
« De nombreux clients optent pour des produits en ligne plutôt que pour des produits imprimés. Par conséquent, de nombreuses commandes que nous avions auparavant se sont taries. Les tirages sont de plus en plus courts et doivent être disponibles plus rapidement. Le seul moyen d'y remédier est d'utiliser de nouvelles machines. Il y aura moins d'imprimeries à l'avenir. Et ceux qui restent dans l'industrie doivent veiller à bien se positionner pour l'avenir », estime M. Harig.
L'utilisation d'imprimantes 3D et la collaboration avec des experts tels que M. Krumma et CTS-3 permettent à Heidelberg d'accélérer le développement de ses produits, ce qui rend ses clients plus compétitifs sur un marché en évolution constante.
« Si nous n'avions pas accès à cette technologie, en particulier à l'impression 3D SLS avec la série Fuse, les processus de développement seraient extrêmement longs. Les machines nous permettent de réaliser des étapes de développement très importantes en très peu de temps. Nous pouvons tester et rejeter ou développer des idées, et produire des pièces pendant la nuit pour les tester dans les locaux du client dès le lendemain. Sans cette technologie, le processus de développement ressemblerait presque à de la fabrication traditionnelle. »
Joachim Krumma, Management, CTS-3 GmbH
« L'impression 3D fait d'énormes progrès chaque année. Vous pouvez constater que ceux qui ne sautent pas dans le train en marche restent à la traîne. Le processus d'impression 3D s'est vite avéré avantageux par rapport à la production traditionnelle. Nous sommes curieux de voir ce que nous réserve l'avenir. » Nous avons vraiment hâte », a déclaré M. Krumma.