Comment la Fuse 1 a permis à BTI Gauges de s'imposer sur un marché automobile de niche
La moitié des entreprises américaines font faillite au cours de leurs cinq premières années d'existence, selon le Bureau des statistiques du travail des États-Unis. Face à des statistiques aussi défavorables, comment une nouvelle entreprise peut-elle garantir sa stabilité et sa pérennité ?
Pour Brandon Talkmitt, fondateur et propriétaire de BTI Gauges, la réponse à cette question réside dans l'impression 3D avec l'imprimante à frittage sélectif par laser Fuse 1. M. Talkmitt n'a pas seulement conquis un marché de niche, mais a réussi à transformer une activité secondaire en une entreprise prospère qui a survécu à la pandémie de COVID-19, aux problèmes de la chaîne d'approvisionnement mondiale et à l'augmentation des prix des matières premières.
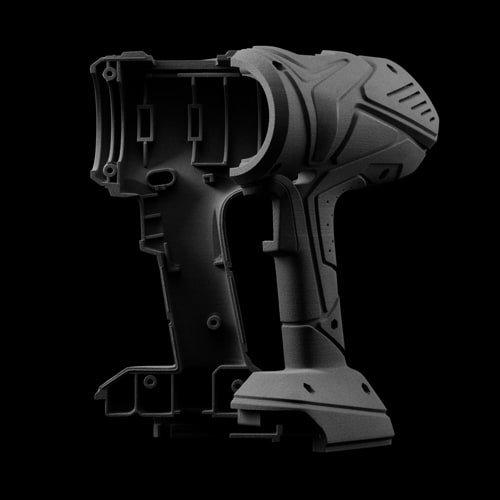
Introduction à l’impression 3D à frittage sélectif par laser (SLS)
Vous cherchez une imprimante 3D pour réaliser des pièces solides et fonctionnelles ? Téléchargez le livre blanc pour savoir comment fonctionne l’impression 3D SLS et les raisons de sa popularité pour le prototypage fonctionnel et la production de produits finis.
Trouver la faille
Comme beaucoup d'autres entreprises prospères, BTI Gauges est née pour combler un vide sur le marché. M. Talkmitt souhaitait personnaliser l'affichage de la télémétrie de sa voiture haute performance. Dans la plupart des voitures courantes, le tableau de bord n'affiche que des paramètres standard, tels que la vitesse et le nombre de tours par minute des roues (RPM). Cependant, dans les voitures hautes performances, les conducteurs ont besoin de beaucoup plus de données pour pouvoir rouler à des vitesses supérieures à 240 km/h. Avec une telle vitesse et une telle puissance, des éléments tels que la pression du liquide de refroidissement sont d'une importance vitale pour la sécurité. Pour obtenir toutes ces informations, les conducteurs ajoutent une série de jauges indiquant des paramètres tels que le rapport air/carburant, la suralimentation du turbocompresseur, la pression du liquide de refroidissement, etc.
« Compte tenu de la puissance de ces voitures, les pannes sont très fréquentes et les réparations très coûteuses », a déclaré M. Talkmitt. Pour éviter tout accident, les conducteurs doivent garder un œil sur les affichages afin d'éviter que le moteur ne devienne trop chaud ou en surpression. Plus il y a de paramètres à surveiller, plus les jauges encombrent le tableau de bord de la voiture.
M. Talkmitt a cherché en vain un instrument contenant plus de paramètres de performance : trop d'affichages sur le pare-brise auraient été une source de distraction potentielle. C'est pourquoi, comme beaucoup d'autres chefs d'entreprise, il a simplement créé ce qu'il ne trouvait pas sur le marché. « Je cherchais quelque chose et personne ne le fabriquait, alors j'ai conçu une jauge ronde unique avec un écran tactile qui affichait toutes les informations », nous a expliqué M. Talkmitt. Il a commencé par prototyper les boîtiers externes des jauges sur une imprimante 3D à dépôt de fil fondu (FDM) et les a testés lui-même, en soumettant les boîtiers à des environnements de forte chaleur à l'intérieur de voitures et de fours, et en modifiant la conception pour l'adapter à plusieurs modèles de voitures.
Une belle apparence, d'excellentes performances !
Son produit a tout de suite suscité l'intérêt d'une clientèle conduisant des voitures de course japonaises des années 1990, des Lamborghini, des Dodge Vipers et d'autres véhicules à hautes performances. Pour les passionnés qui aiment les belles voitures, il est dommage d'encombrer un tableau de bord avec de multiples jauges disgracieuses : un écran tactile unique et élégant était à la fois efficace et esthétique.
C'est là que M. Talkmitt s'est heurté à un autre problème. La finition de surface des pièces imprimées par FDM ne correspondait pas à l'aspect et à la sensation haut de gamme de la conception de la jauge. « Les lignes de couche visibles ne plaisaient pas à tout le monde », explique M. Talkmitt. « Nous avons dû les poncer et les remplir de mastic automobile. Ce fut un processus très ardu. »
M. Talkmitt a commencé à s'intéresser à plusieurs options d'impression 3D, notamment des imprimantes 3D à fusion sur lit de poudre coûteuses, des imprimantes 3D résine et une imprimante SLS compacte peu coûteuse. Mais entre les machines coûtant parfois un demi-million de dollars et celles présentant un système de matériaux ultra complexe, il n'y avait tout simplement pas d'options disponibles. Jusqu'à ce qu'il entende parler de la Fuse 1. « Lorsque j'ai reçu l'échantillon, je me suis dit : « Si seulement mes pièces pouvaient ressembler à ça ! » J'ai donc effectué quelques tests et j'ai établi quel type de chaleur elles pouvaient supporter. Nous avons procédé à la finition et à la peinture, et tout a fonctionné », explique M. Talkmitt.
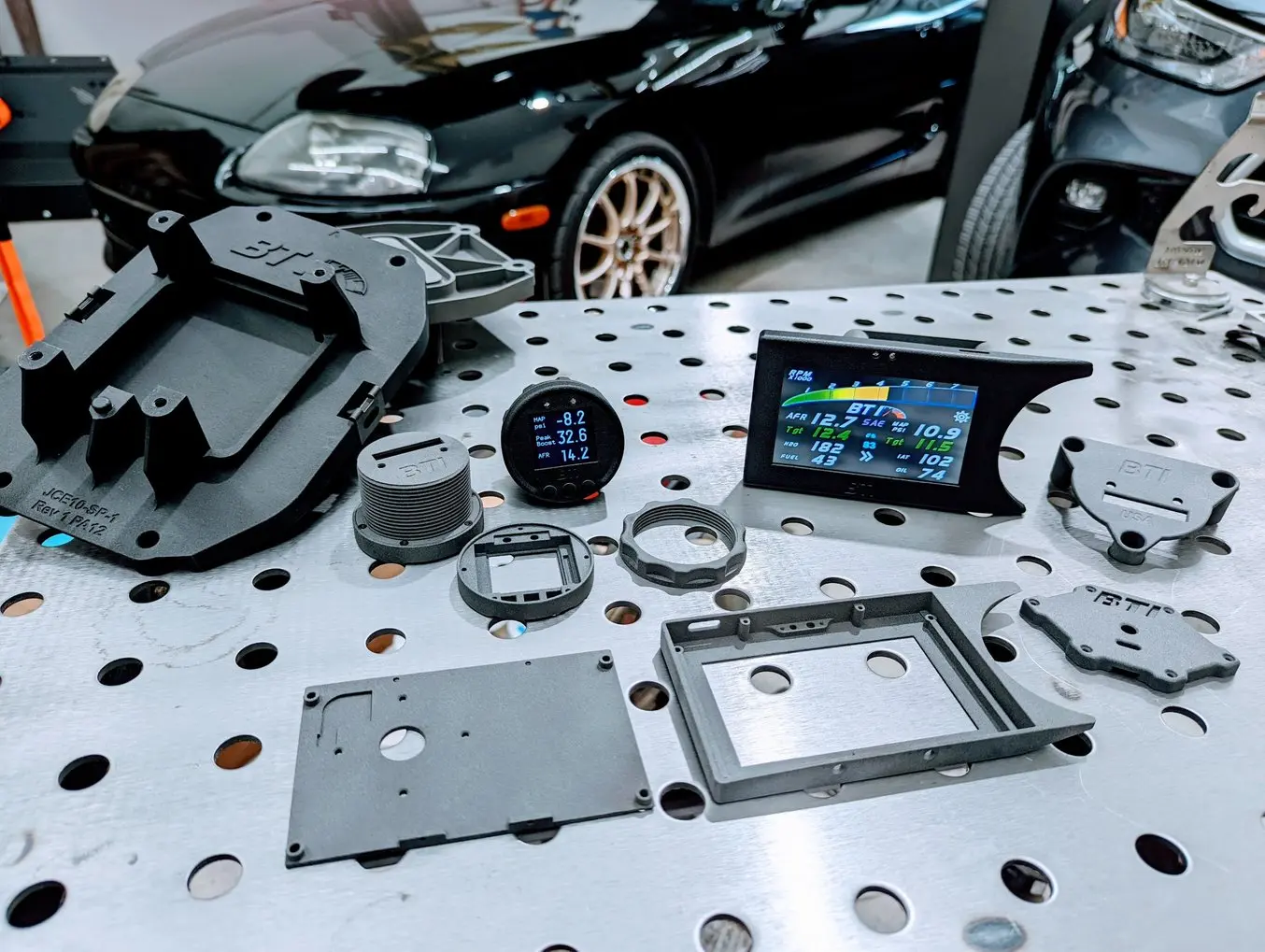
Une précision inégalée
Pour augmenter sa production avec la Fuse 1, M. Talkmitt avait besoin de plus que d'une belle apparence. Il fallait que les pièces soient toujours précises, même à des volumes élevés, et il disposait enfin d'une imprimante capable d'obtenir des tolérances étroites et reproductibles. M. Talkmitt a pu régler la précision de ses fichiers, sachant que la Fuse 1 pouvait imprimer avec précision les détails de sa conception.
« J'ai conçu un trou de 40 mm x 40 mm et maintenant, avec la Fuse 1, je peux imprimer une broche de la même taille qui s'adapte parfaitement. Nous réalisons des filets de vis et d'autres caractéristiques qui doivent être précises. Dans un environnement automobile, d'autres pièces se déformeraient, mais depuis que nous utilisons la Fuse 1, nous n'avons pas eu la moindre pièce déformée. »
Brandon Talkmitt
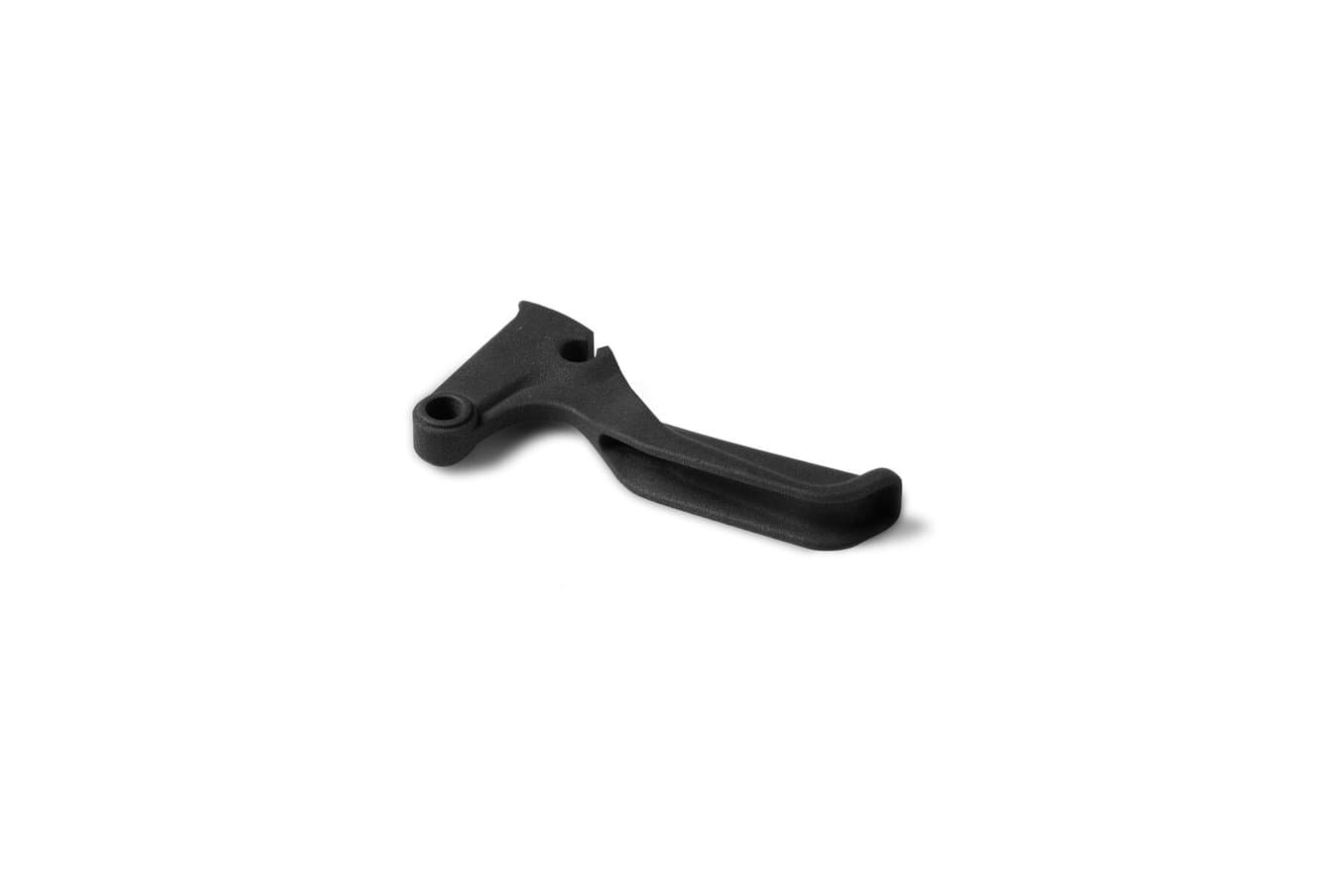
Commander un échantillon gratuit
Examinez et constatez par vous-même la qualité Formlabs. Nous vous enverrons un échantillon gratuit imprimé sur la Fuse 1+ 30W à votre bureau.
Production antifragile
Les pièces de ce type peuvent être fabriquées de diverses manières. Quel est donc l'intérêt de disposer d'une imprimante SLS en interne ? BTI Gauges a accompli ce que l'auteur Nassim Nicholas Taleb a appelé l'« antifragilité. » Les entités antifragiles sont non seulement capables de résister au stress et aux chocs, mais aussi de se fortifier, de s'améliorer et de devenir plus efficaces à la suite de ces événements. En raison des problèmes de chaîne d'approvisionnement des deux dernières années, BTI Gauges a dû faire face à plusieurs pénuries d'écrans tactiles et d'autres composants nécessaires à ses neuf gammes de produits. Pour un fabricant « fragile », ces pénuries auraient pu entraîner l'arrêt de la production, de la distribution et de la génération de revenus. Pour M. Talkmitt, elles l'ont obligé à se procurer de nouveaux types d'affichage, ce qui a eu une incidence sur le type de processeur, le circuit imprimé et la forme de la jauge elle-même.
En intégrant l'impression 3D en interne avec la Fuse 1, l'équipe a pu passer immédiatement à une nouvelle conception sans avoir à dépenser des milliers de dollars pour un nouvel outillage ou à gérer des produits désormais obsolètes. « J'aurais été enseveli sous toutes ces pièces en plastique, mais avec la Fuse 1, j'ai pu tout de suite apporter les changements nécessaires. Il m'a fallu 30 minutes pour modifier les fichiers. Sans cela, j'aurais sans doute des ennuis aujourd'hui », déclare M. Talkmitt.
M. Talkmitt n'a pas fait appel à des fournisseurs externes et a maintenu une intégration aussi verticale que possible. Le fait d'être confronté à plusieurs pénuries l'a poussé à mettre au point un inventaire numérique des pièces détachées afin de se prémunir contre de futures ruptures de la chaîne d'approvisionnement. Faire face à des pressions économiques hors de son contrôle a en fait renforcé son modèle d'entreprise, et l'a isolé des chocs futurs : la définition de l'antifragilité.
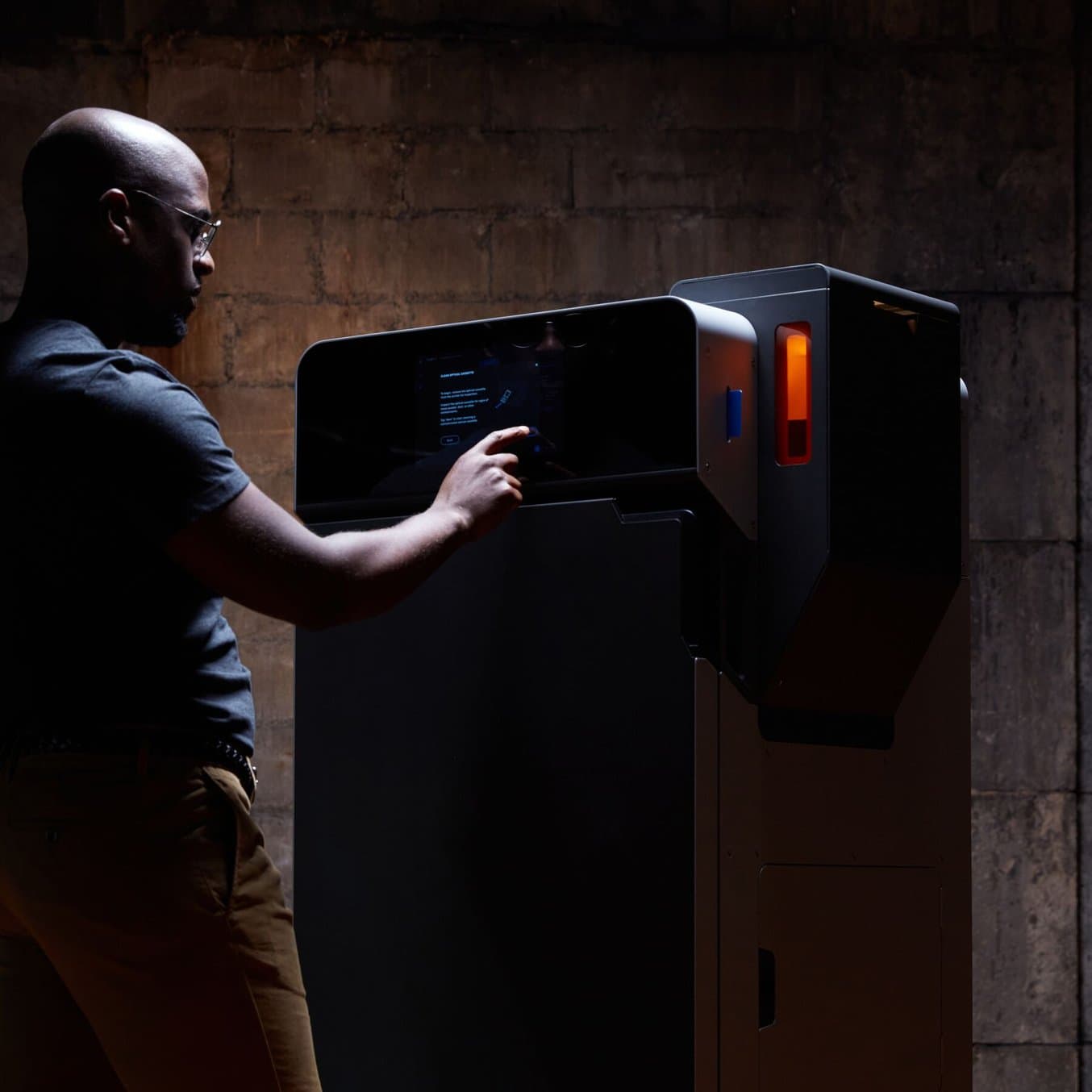
Externalisation ou internalisation : quand est-il judicieux d'adopter l'impression 3D SLS en interne ?
Dans ce livre blanc, nous passons en revue les avantages de l'adoption en interne des imprimantes 3D à frittage sélectif par laser (SLS) par rapport à la sous-traitance des pièces SLS auprès de fournisseurs de services.
Production à haut rendement
Pour que la production continue reste rentable et durable, M. Talkmitt s'appuie sur l'efficacité de l'ensemble du système de la série Fuse. Grâce à l'algorithme d'agencement avancé de PreForm, il est en mesure d'imbriquer les pièces les unes dans les autres afin d'augmenter sa densité d'agencement globale et de la faire correspondre le plus possible au taux de renouvellement de 30 % de Nylon 12 Powder. « L'un de nos produits est un outil de 4,3 mm qui nécessite deux pièces, l'une à l'avant et l'autre à l'arrière. Il y a un très grand espace entre les deux, alors je prends une autre pièce de 3,5 mm et je l'insère à l'intérieur. Nous pouvons remplir stratégiquement le volume d'impression et atteindre une densité d'agencement de 25 % », explique M. Talkmitt.
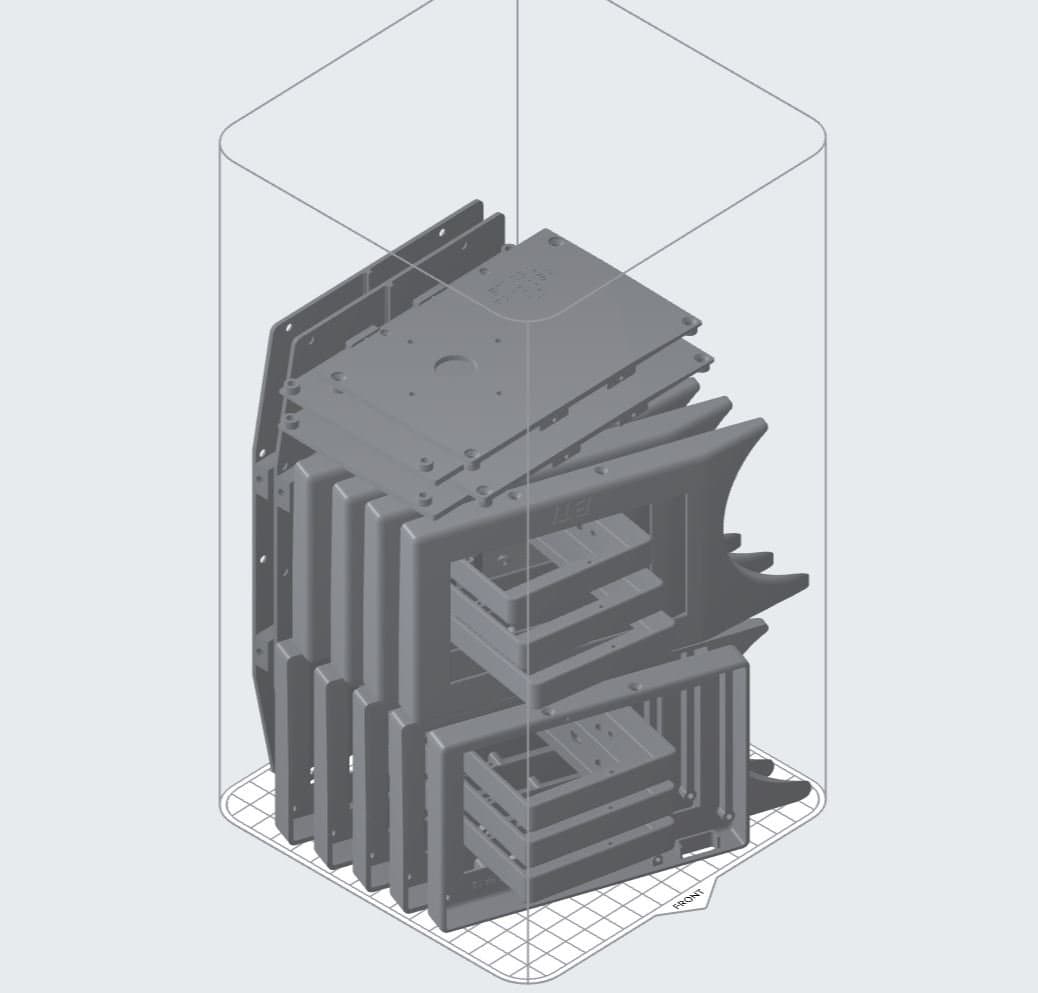
Une chambre de fabrication Fuse 1 affichée dans PreForm, avec des pièces imbriquées dans des pièces plus grandes (à gauche) et une pièce imprimée sur la Fuse 1 en phase de post-traitement (à droite).
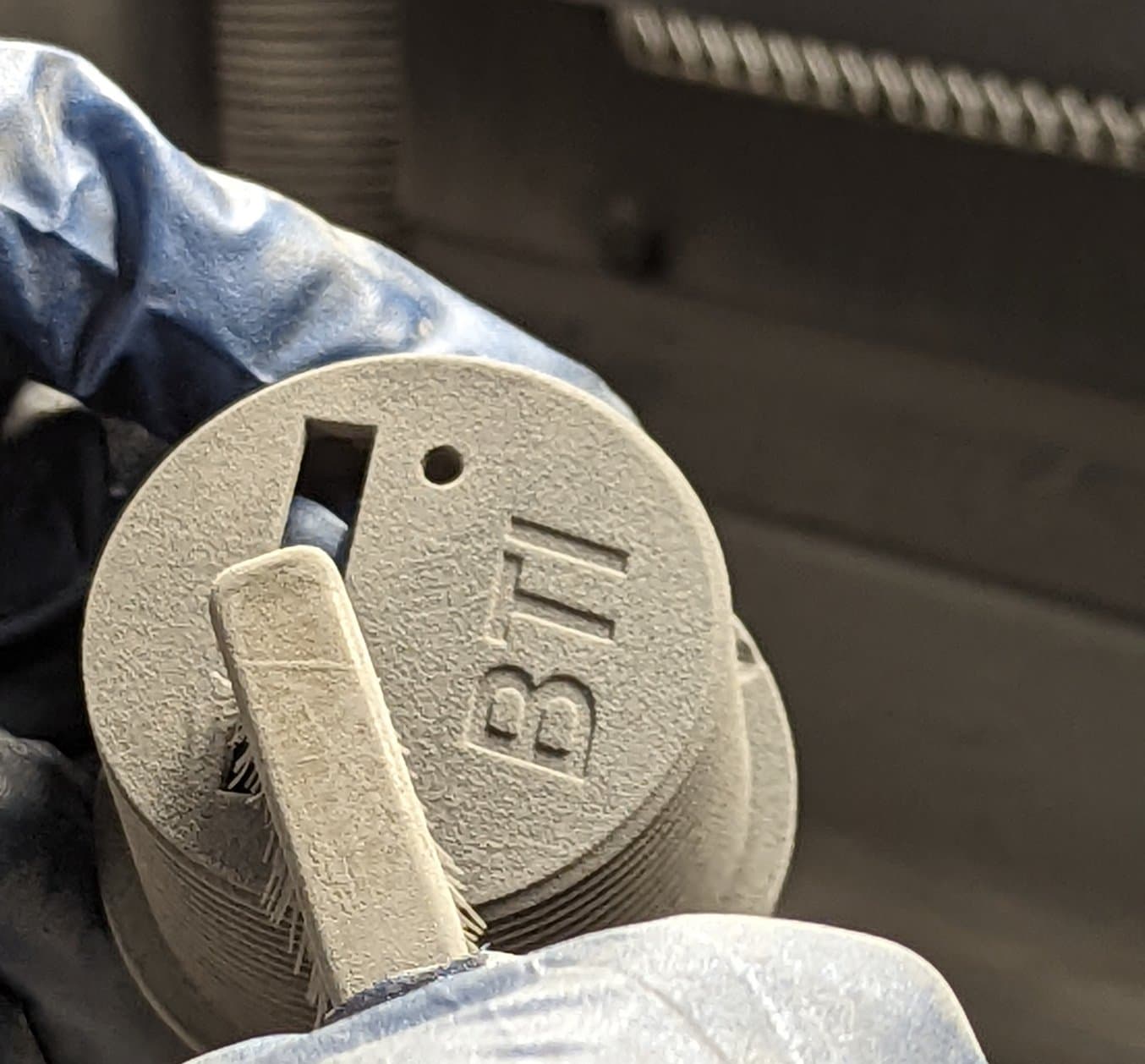
En agençant efficacement les pièces, M. Talkmitt peut profiter d'un flux de travail ne produisant presque aucun déchet, où chaque morceau de poudre est utilisé dans des séries d'impressions successives. Pour un petit fabricant, cette efficacité diminue le coût par pièce et accélère le retour sur investissement.
Le rendement élevé de la Fuse 1 a permis à M. Talkmitt de passer de trois imprimantes FDM fonctionnant sans interruption à des chambres d'impression de Fuse 1 remplies à pleine capacité une fois par semaine. Le flux de travail optimisé de la Fuse Sift permet à M. Talkmitt de consacrer moins de temps au post-traitement et plus de temps à la conception de nouvelles pièces et à l'accroissement de la notoriété de la marque. « Au fond de l'atelier, nous avons la Fuse 1, la Fuse Sift et la sableuse, tandis que la peinture, l'assemblage et l'emballage ont lieu dans l'installation de production. Les dimensions et l'encombrement de la Fuse 1 conviennent parfaitement au processus », explique M. Talkmitt.
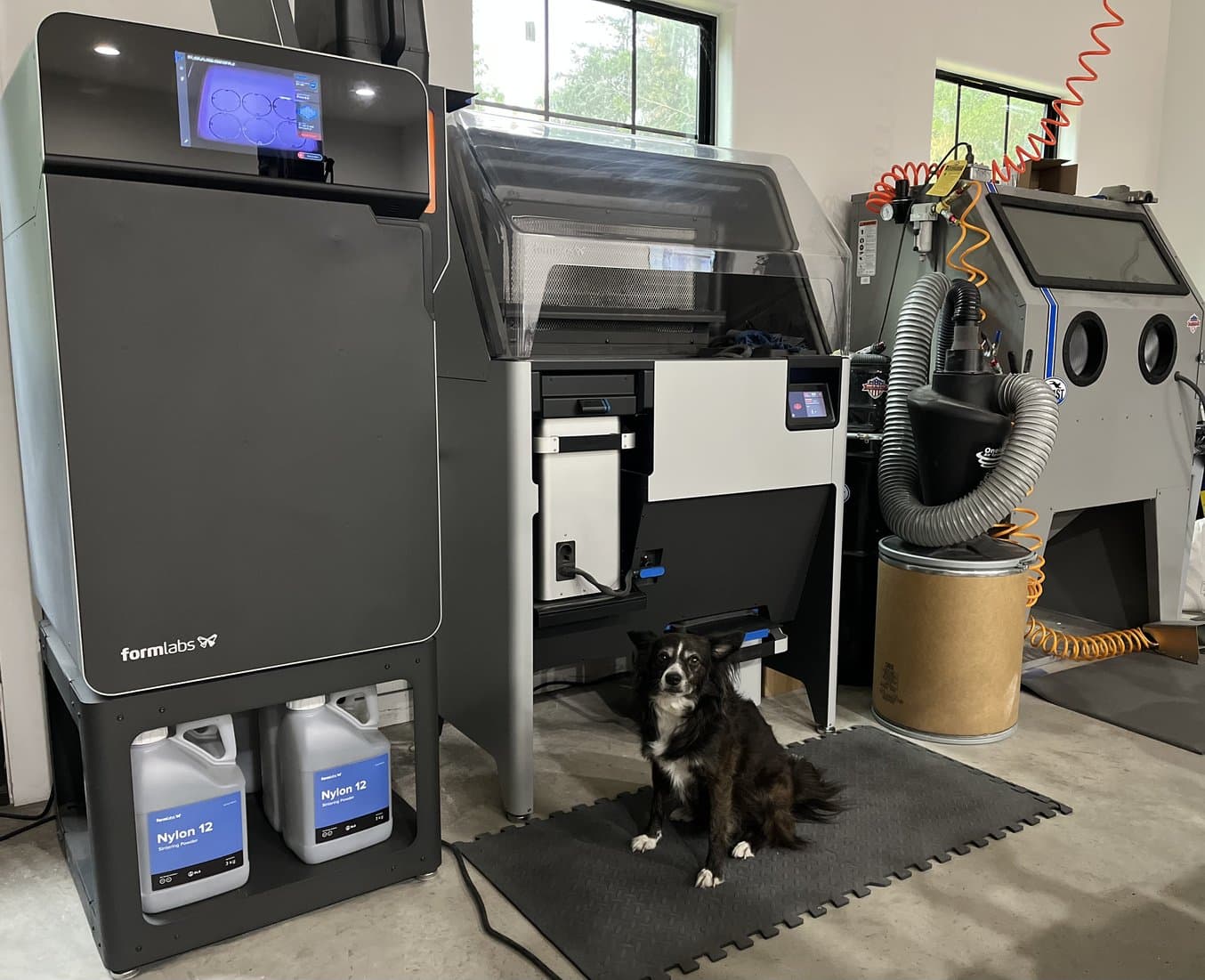
La Fuse 1 et la Fuse Sift offrent un encombrement accessible et un flux de travail optimisé qui peuvent s'ajuster facilement aux espaces de travail existants.
Continuer sur sa lancée
En tant que nouvelle entreprise, il est difficile de percer dans un secteur où les voitures sont régulièrement vendues pour des centaines de milliers de dollars. Il est pratiquement impossible de le faire en pleine crise mondiale, en cas de blocage de la chaîne d'approvisionnement internationale et en pleine tourmente économique.
En produisant en interne avec une imprimante SLS de haute qualité comme la Fuse 1, il a pu contrôler et sécuriser son processus de production, lui permettant de surpasser ceux qui dépendaient encore de la fabrication traditionnelle ou de fournisseurs externes. « Je le recommanderais à tout le monde. La Fuse 1 a changé la donne pour nous », déclare M. Talkmitt.