Formlabs a récemment publié un livre blanc expliquant l’utilisation de moules à injection imprimés en 3D pour le moulage rapide de petites séries, et a également organisé un webinaire gratuit. L’un des panels de discussion a réuni des experts du moulage par injection pour expliquer comment l’impression 3D permet en quelques jours, à partir d’une simple idée, de fabriquer des moules en interne à la demande pour produire des centaines de pièces.
Ce webinaire a eu beaucoup de succès et nous avons reçu une centaine de questions de la part des participants. Dans cet article, nous répondons à quelques-unes de vos questions les plus fréquentes sur le moulage par injection avec des moules imprimés en 3D.
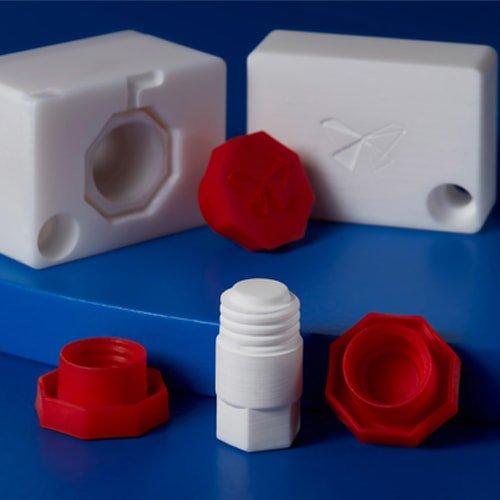
Le moulage par injection rapide en petite série avec des moules imprimés en 3D
Téléchargez ce livre blanc pour connaître les recommandations d’utilisation de moules imprimés en 3D dans le processus de moulage par injection afin de réduire les coûts et délais de production. Vous y trouverez des études de cas réels, réalisées chez Braskem, Holimaker et Novus Applications.
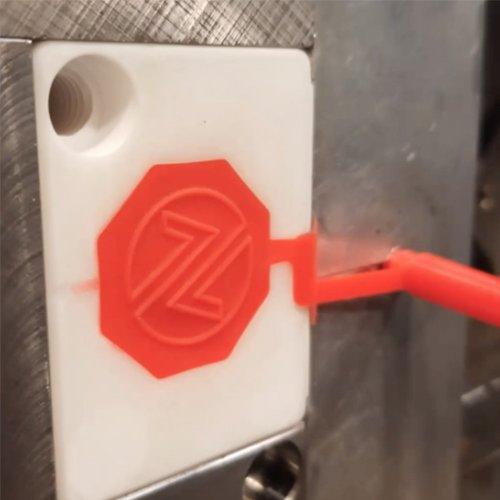
Comment fabriquer rapidement des moules à injection de petites séries
Regardez ce panel de discussion dans lequel des experts du moulage par injection vont expliquer comment l’impression 3D permet en quelques jours, à partir d’une simple idée, de fabriquer des moules en interne à la demande pour produire des centaines de pièces.
Équipement
Q : Pouvez-vous recommander une machine de moulage par injection ?
Le type de presse d’injection n’a pas d’influence notable sur le processus tant que vous pouvez régler les paramètres essentiels comme la pression, la température et la pression de serrage. Parmi les entreprises décrites dans notre livre blanc, Braskem et Novus Applications utilisent des presses entièrement électriques, respectivement Cincinnati Milacron Roboshot 110 tonnes et Sumitomo 50 tonnes. Les machines de moulage de bureau automatisées telles que celles produites par Babyplast sont de bonnes alternatives pour la production à grande échelle de petites pièces.
Si vous débutez dans le moulage par injection et que vous souhaitez tester ce processus sans trop d’investissement ni de maintenance, utiliser une machine d’injection de bureau telle que la Holipress ou la Galomb Model-B100 peut être judicieux.
Certains de nos clients ont également recommandé des systèmes Minijector, Morgan, APSX ou encore Micromolder.
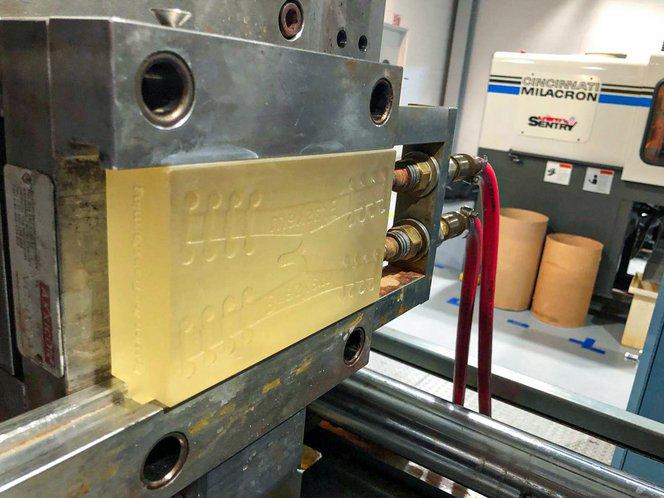
Les moules à injection imprimés en 3D peuvent s’utiliser tant sur des machines que sur des appareils de bureau de plus petite taille.
Q : Quels sont les matériaux d’injection compatibles avec les matériaux Formlabs ?
Pour l’injection dans des moules imprimés en 3D en matériaux Formlabs, nos clients ont utilisé une large gamme de thermoplastiques, parmi lesquels du PP, du PE, des TPE et TPU, du POM, de l’ABS et du PA. Un matériau à faible viscosité contribuera à réduire la pression d’injection et prolongera la durée de vie du moule. Le polypropylène et les élastomères thermoplastiques (TPE) sont faciles à injecter et résistent à un grand nombre de cycles. En revanche, les plastiques plus techniques tels que le polyamide permettront un plus petit nombre de cycles. L’application d’un agent de démoulage facilite la séparation de la pièce du moule, tout particulièrement pour les matériaux flexibles tels que les polyuréthanes ou les élastomères thermoplastiques (TPU ou TPE).
Récapitulatif du procédé
Q : Quelle est la durée de vie d’un moule imprimé en 3D et comment s’abîme-t-il ? Que signifie « petite série » ?
La durée de vie d’un moule imprimé en 3D dépend du modèle, du matériau d’injection et des conditions de moulage. Il ne faut pas s’attendre à ce qu’un moule polymère imprimé en 3D offre la même performance qu’un moule usiné en métal. Les dimensions critiques sont plus difficiles à obtenir, le temps de refroidissement est plus long car l’échange thermique est plus lent dans le plastique. Des moules imprimés en High Temp Resin ou en Rigid 10K Resin peuvent facilement se casser du fait de la chaleur et de la pression. Habituellement, la détérioration se manifeste sous forme d’une fracture de fatigue. On observe parfois un cisaillement en lamelles des coins ou d’autres éléments du moule, qui se détachent alors au démoulage de la pièce.
La plupart de nos clients réussissent à produire des centaines de pièces par moule, imprimés avec des matériaux à basse viscosité comme le polypropylène. Les plastiques plus techniques tels que le polyamide permettront un plus petit nombre de cycles. Cependant, il est possible d’imprimer plusieurs moules et de les changer plus ou moins facilement selon le système utilisé. Nous n’avons pas étudié l’impact de la durée de cycle sur la rupture des moules.
Q : Quels sont les résultats de la comparaison des procédés SLS et FDM avec le procédé SLA pour l’impression en 3D de moules à injection ?
La technologie d’impression stéréolithographique (SLA) est un excellent choix pour le moulage par injection. Elle se caractérise par une finition de surface plus lisse et une précision plus élevée que les deux autres procédés, ce qui se transmet à la pièce et facilite son démoulage. Les liaisons chimiques existant dans les impressions 3D produites par stéréolithographie les rendent denses et isotropes. Les moules fonctionnels sont d’une qualité impossible à obtenir avec le procédé FDM.
Q : Quelle est la différence de coût entre les processus avec moule en métal et moule imprimé en 3D ?
Les moules d’injection imprimés en 3D coûtent généralement de 25 à 250 € en matériau, en fonction de leur taille. Les moules à injection en métal standard peuvent coûter entre quelques centaines et plus de 10 000 euros. Cela dépend de leur taille, de leur complexité et du fait de disposer ou non de l’équipement CNC nécessaire à leur fabrication en interne, au lieu d’avoir recours à un sous-traitant.
En règle générale, l’utilisation d’un moule en métal devient plus rentable lorsque les volumes de production augmentent, le coût du moule étant divisé par le nombre de pièces produites.
Les économies générées par l’utilisation de moules d’injection imprimés en 3D peuvent être importantes. Pour produire les 6000 sangles de masques, Braskem a réduit ses coûts de 97 % par rapport à ceux générés par la sous-traitance de la fabrication d’un moule en métal.
Q : Pour des petits volumes de production, dans quelles circonstances le moulage par injection se justifie-t-il par rapport à l’impression 3D ?
L’impression 3D permet de produire des prototypes et des pièces fonctionnelles rapidement et à bas coût à partir d’une large gamme de matériaux. En général, nous recommandons d’imprimer en 3D des pièces et des prototypes pendant les premières phases de développement de produit, lorsque leur conception change souvent et qu’ils sont produits en petit nombre. Pour certaines applications, l’impression 3D peut aussi convenir pour des pièces finales. L’impression 3D permet aussi de réaliser des pièces complexes impossibles à fabriquer par moulage par injection.
Le moulage par injection avec moules imprimés en 3D est le meilleur choix lorsque vous ne trouvez pas de matériau d’impression 3D qui convienne, ou que vous préférez utiliser un thermoplastique standard. Lorsque vous avez besoin de centaines de prototypes identiques, il est souvent plus rapide d’imprimer un moule et de les injecter, plutôt que de les imprimer en 3D (en fonction de leur forme et du procédé d’impression). Les matériaux d’impression 3D étant plus coûteux, il peut s’avérer plus rentable d’opter pour le moulage par injection lorsque le volume de production augmente.
Q : Rencontrez-vous des problèmes de cristallinité des pièces en utilisant des moules imprimés en 3D ?
Nous n’avons noté aucun cas de cristallisation de pièces, ni reçu aucun retour sur ce problème de la part de nos clients.
Processus de conception
La complexité du processus de moulage par injection dépend largement de la complexité de la pièce à mouler et de la structure du moule. Certaines règles de conception contribuent à améliorer la précision dimensionnelle et à accroître la durée de vie d’un moule. Notre livre blanc donne des instructions de conception détaillées à suivre dans le cas de l’utilisation d’un moule imprimé en 3D au lieu d’un moule en métal.
Q : Quelle valeur est recommandée pour l’angle de dépouille ? Quelle est la profondeur recommandée pour un évent ou un orifice de drainage ? Sont-ils destinés à évacuer l’air ou à faire circuler le polymère ?
Nous recommandons d’ajouter un angle de dépouille de deux à cinq degrés lorsque cela est possible.
L’évent permet à l’air de s’échapper au lieu d’être piégé à l’intérieur. Nous recommandons une profondeur de 0,05 mm.
Q : Comment pouvons-nous éviter de gaspiller du matériau d’impression ? Qu’entendez-vous par amincir l’arrière du moule ? Cela revient-il à garder les parois de même épaisseur partout ?
Nous conseillons d’amincir les parois des moules de grande taille pour réduire la consommation de matériau. Diminuer la section transversale des parties qui ne supportent pas la cavité va réduire les coûts en matériau et le risque d’erreur d’impression et de déformation. L’épaisseur des parois des parties qui supportent la cavité doit être la même partout.
Q : Comment éviter les problèmes d’alignement et de plan de joint posés par les moules en deux parties ?
Lorsque c’est possible, nous recommandons de concevoir le moule pour qu’il soit plat d’un côté et avec l’empreinte du modèle de l’autre côté. Ceci réduira un éventuel décalage dans l’alignement des blocs et les risques de bavure. Si cela s’avère impossible, nous conseillons de post-traiter le moule imprimé : un fraisage mécanique ou un ponçage manuel facilitera l’ajustement des deux parties et évitera les bavures.
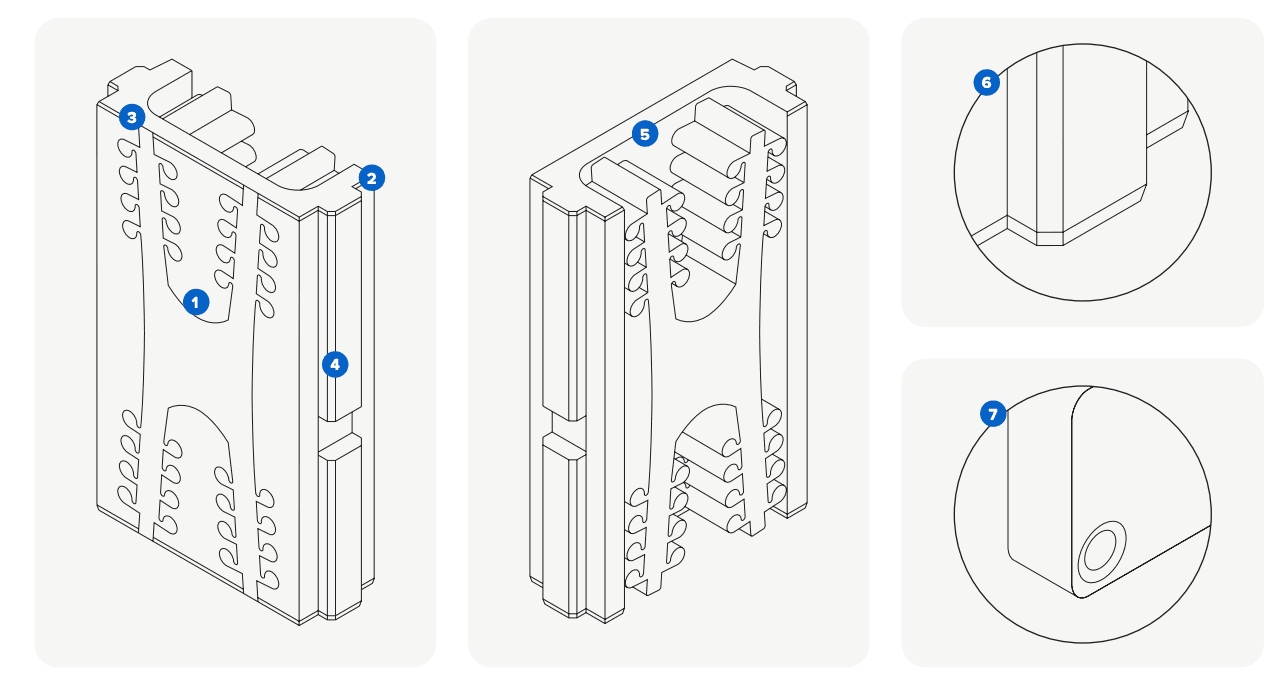
En plus de ces règles générales de conception des moules d’injection, il existe plusieurs façons de prolonger la durée de vie d’un moule et de garantir une bonne précision dimensionnelle. Téléchargez notre livre blanc pour connaître les recommandations en détail.
Q : Quelle peut être la finesse des détails du moule ?
Nous recommandons de suivre les instructions de conception pour la fabrication additive, exposées dans le guide de conception pour la Form 3 de Formlabs, téléchargeable ici. Il faut éviter les sections transversales trop fines : une épaisseur de surface inférieure à 1–2 mm peut se déformer sous l’effet de la chaleur. Des éléments en creux d’épaisseur inférieure à 0,5 mm peuvent poser des problèmes de définition, et des éléments verticaux inférieurs à 0,1 mm peuvent se casser.
Q : Est-il possible d’ajouter des tiroirs à des moules imprimés en 3D ?
Oui. Consultez l’étude de cas de Novus exposée dans le livre blanc.
Processus d’impression
Q : Quelles sont vos recommandations pour prendre en compte le rétrécissement des moules à l’impression ?
Imprimez un premier moule pour bien comprendre les écarts dimensionnels. Nous recommandons d’ajouter des marges de tolérance au modèle CAO pour compenser tout écart dimensionnel. Des ajustements manuels seront nécessaires en post-traitement. Un fraisage mécanique ou un ponçage manuel aideront à respecter les dimensions critiques, faciliteront l’ajustement des deux parties du moule et supprimeront les bavures.
Q : Comment éviter les traces de lignes de couche sur des impressions en creux ?
Nous recommandons d’imprimer avec l’épaisseur de couche la plus faible possible. La technologie d’impression stéréolithographique (SLA) est un excellent choix pour le moulage parce que les pièces produites présentent une surface lisse et une grande précision.
Q : Est-il possible d’ajouter une finition de surface, une texture et des motifs à des moules d’injection imprimés en 3D ? Cela se ferait-il au cours du post-traitement ou est-il possible d’imprimer directement sur la surface ?
Le procédé SLA est une bonne option pour texturer des pièces. Grâce à sa haute résolution, il peut reproduire des détails de petite taille et complexes. Les surfaces imprimées sans structures de support ne nécessitent généralement pas de post-traitement.
Q : Existe-t-il d’autres matériaux que High Temp Resin et Rigid 10K Resin pour le moulage par injection ?
Quelques clients, comme Holimaker, utilisent Grey Pro Resin. Ce matériau présente une conductivité thermique et une stabilité dimensionnelle moindres que High Temp Resin et Rigid 10K Resin, mais il est moins rigide et son allongement à la rupture est supérieur, ce qui lui permet de supporter plus de cycles avant de se casser.
Q : Quel est le processus de polymérisation pour High Temp Resin et Rigid 10K Resin pour cette application ?
Nous recommandons de post-polymériser la pièce en High Temp Resin avec ses supports pendant 120 minutes à 80 °C, puis de la chauffer à 160 °C pendant trois heures. Consultez le site d’assistance ici.
Nous recommandons de post-polymériser les pièces en Rigid 10K Resin avec leurs supports dans la Form Cure à 70 °C pendant 60 minutes, puis à 125 °C pendant 90 minutes pour augmenter leur température de fléchissement sous charge. Consultez le site d’assistance ici.
Q : Quelle est la taille maximum d’un moule fabriqué par ce procédé ? Cela fonctionne-t-il avec la Form 3L ?
Les moules en High Temp Resin et Rigid 10K Resin peuvent être imprimés sur la Form 3L, de volume d’impression maximum de 33,5 × 20 × 30 cm. Cependant, les moules de grande taille sont plus difficiles à imprimer et à injecter.
Conditions de moulage
Q : Les moules à injection imprimés en 3D sont-ils réservés aux processus basse température et basse pression ? Quelles sont les valeurs recommandées de température et de pression de l’injection ?
Diminuer la pression et la température contribuera à réduire le risque de rupture du moule et prolongera sa durée de vie. Cependant, c’est la conception du moule qui influencera le plus l’impact de la pression dans la cavité.
Dans les études de cas exposées dans notre livre blanc, Braskem a injecté des pièces à 230 °C et 5000 psi, et en ce qui concerne Novus Applications, la pression à la rupture était de 11 500 psi à 210 °C.
High Temp Resin présente une température de fléchissement sous charge (HDT) de 238 °C à 0,45 MPa. Rigid 10K Resin présente une température de fléchissement sous charge de 218 °C à 0,45 MPa et un module de traction de 10 000 MPa.
Q : Est-il recommandé d'utiliser des cadres en aluminium lorsqu’on utilise des impressions 3D comme inserts ? Peut-on utiliser des moules imprimés en 3D sans ces cadres ?
Oui. Les moules à injection imprimés en 3D peuvent être utilisés sans cadre en aluminium, mais il est recommandé de les placer dans un cadre métallique ou d’imprimer l’insert et d’usiner l’extérieur du moule afin de supporter la pression verticale et la chaleur de la buse d’injection.
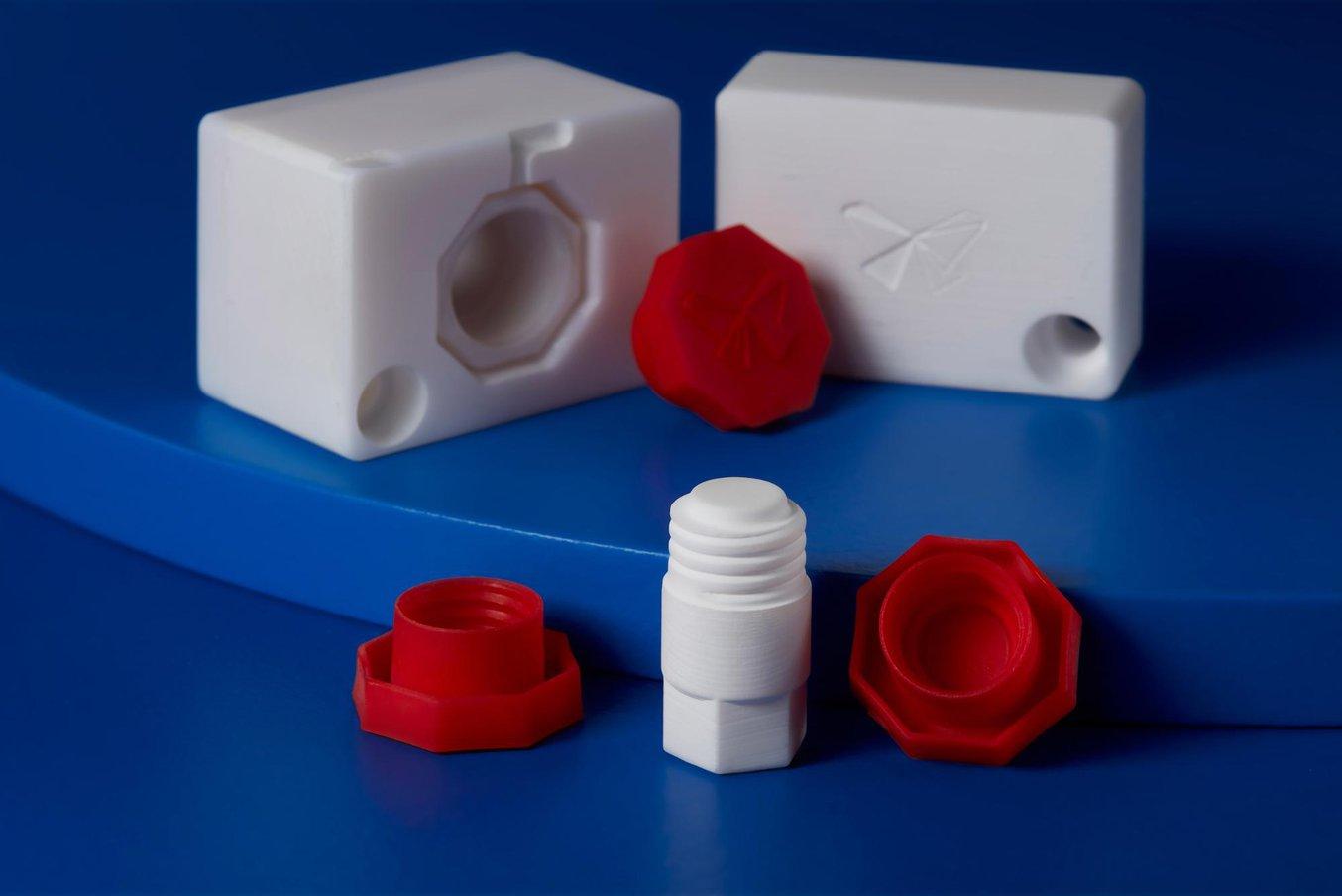
Il est possible d’ajouter un ou plusieurs tiroirs aux moules d’injection imprimés en 3D.
Refroidissement :
Q : Le refroidissement dure-t-il plus longtemps avec un moule imprimé en 3D qu'avec un moule en métal ?
Oui, le refroidissement est plus long pour le moule imprimé en 3D car la dissipation de chaleur s‘opère plus lentement dans les pièces en plastique. Placer le moule imprimé à l’intérieur d'un cadre métallique permet l’absorption partielle de la chaleur et réduit la durée du refroidissement. Une alternative pour réduire la durée de cycle est d’imprimer plusieurs moules en 3D et de les changer à chaque cycle.
Q : Comment faire pour refroidir la pièce ? Faut-il ajouter des canaux de refroidissement ?
Utiliser des plateaux interchangeables pour effectuer de nouveaux cycles pendant que les plateaux utilisés refroidissent peut accélérer le refroidissement et compenser la faible conductivité thermique d’un moule plastique. Les moules considérés dans les études de cas n’avaient pas de canaux de refroidissement, mais cela peut être une option. Refroidir à l’air comprimé en est une autre.
Démoulage
Q : Comment éjectez-vous la pièce ? Les moules imprimés en 3D nécessitent-ils l’emploi d’un produit de démoulage ? Pouvez-vous en recommander un ?
Dans notre livre blanc, aucun tenon d’éjection n’a été utilisé. Chaque pièce était retirée manuellement du moule. Prévoir des angles de dépouille et imprimer à faible valeur d’épaisseur de couche donnent une finition de surface lisse qui aide au démoulage. L’adhérence d’une pièce au moule dépend du matériau injecté et peut endommager le moule pendant la phase d’extraction, en particulier avec des matériaux flexibles comme les TPU et les TPE.
L’emploi d'un produit de démoulage peut être une bonne solution pour aider à extraire la pièce du moule. Les produits de démoulage prévus pour le silicone sont compatibles avec Grey Pro Resin, High Temp Resin et Rigid 10K Resin de Formlabs. Novus Applications utilise des produits Slide et Braskem le produit de démoulage de qualité alimentaire MR303 pour silicone de Sprayon.
Procédés connexes
Q : Faut-il envisager de traiter le moule par galvanoplastie pour augmenter sa durée de vie ?
Il est possible de traiter les pièces imprimées en 3D par SLA par galvanoplastie. Consultez le webinaire consacré à ce sujet. Nous ne sommes pas en mesure à cette date de confirmer que ce traitement allonge la durée de vie des moules imprimés en 3D.
Q : Les pièces imprimées en 3D avec des matériaux Formlabs peuvent-elles être utilisées avec d’autres procédés de moulage ?
Oui. Des ingénieurs et des fabricants de divers secteurs ont adopté l’impression 3D dans le cadre de plusieurs techniques de fabrication de moules. Consultez les ressources sur notre site présentant des articles sur l’emploi de moules et de modèles imprimés en 3D, notamment en thermoformage, moulage en silicone, moulage en sable et à modèle perdu, ou encore en laminage.
Vous avez d’autres questions sur l’utilisation de l’impression 3D pour le moulage par injection ? Téléchargez le livre blanc et regardez le webinaire pour connaître les recommandations et les études de cas réels, ou contactez directement notre équipe commerciale.