Comment l'impression 3D SLS permet de produire des véhicules spéciaux
MOSOLF Special Vehicles GmbH est un fabricant de véhicules spéciaux de premier plan basé à Kippenheim, en Allemagne. Avec près de 50 employés, la société produit environ 1000 véhicules spéciaux et d'urgence par an. Parmi ses clients, on trouve les polices régionales et la police fédérale, le secteur de la défense, la protection civile, les services d'assistance technique, les communes ainsi que les clients industriels qui ont besoin de véhicules présentant un haut degré de personnalisation et des performances supérieures.
Dans le secteur automobile, les composants sont principalement produits par des procédés de production de masse, tels que le moulage par injection, qui sont rentables pour des volumes de centaines de milliers d'unités. Cependant, les clients de MOSOLF ont besoin d'une large gamme de pièces personnalisées produites en petites séries, de sorte que le coût de l'outillage rend les méthodes de production traditionnelles économiquement irréalisables. Pour MOSOLF, l'impression 3D constitue une solution idéale.
« J'estime qu'actuellement, un véhicule de police sur trois [en Allemagne] contient des pièces fabriquées par fabrication additive. Chez MOSOLF, nous utilisons tellement l'impression 3D qu'aucun véhicule ne quitte notre usine sans une pièce produite grâce à cette technologie. Nous imprimons actuellement en 3D environ 5000 pièces par an, mais la tendance est à la hausse, ce qui signifie qu'il y a au moins trois pièces fabriquées avec cette technologie sur chaque véhicule. »
Carsten Busam, responsable de la planification des projets, MOSOLF Special Vehicles GmbH
Lisez la suite pour découvrir comment MOSOLF utilise l'impression 3D par frittage sélectif par laser (SLS) avec la série Fuse pour produire une large gamme de pièces finales pour les fourgons de police et autres véhicules spéciaux et d'urgence.
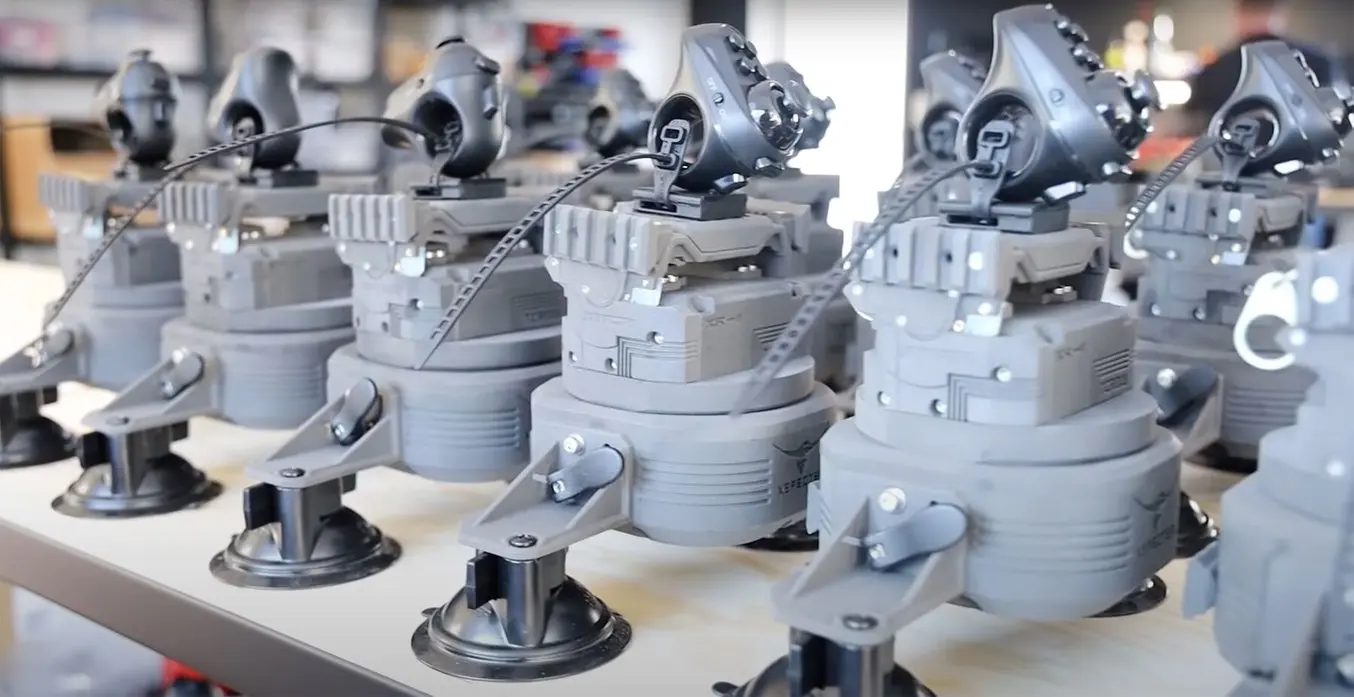
Le SLS pour la production finale
L'impression 3D pour la production finale n'est pas seulement accessible : elle est aussi plus abordable, plus agile et plus évolutive que jamais grâce à l'écosystème Fuse SLS. Comparez les méthodes de production, découvrez les prix des poudres en vrac et découvrez comment 15 fabricants utilisent actuellement les imprimantes de la série Fuse.
Des solutions personnalisées pour répondre aux besoins des 17 corps de police allemands
« Notre plus grand défi est la variété », a déclaré M. Busam. Chaque division des forces de police achète différents types de véhicules, dont chacun peut nécessiter des composants personnalisés en fonction de son usage spécifique. Les composants à intégrer peuvent également varier : par exemple, différentes forces de police utilisent des systèmes de radio ou de signalisation provenant de différents fabricants. Cela signifie que chaque véhicule nécessite une grande quantité de pièces faites sur mesure.
« Nous produisons des véhicules pour 17 forces de police en Allemagne, chacune ayant sa propre vision de l'ergonomie et de l'utilisation prévue. Par conséquent, les quantités sont généralement relativement élevées pour le modèle de base, mais si l'on tient compte du degré de personnalisation, elles diminuent à nouveau », a déclaré M. Busam.
L'équipe MOSOLF travaille sur des véhicules de série, c'est-à-dire des voitures, des camions et des camionnettes disponibles dans le commerce, qui sont adaptés pour répondre à des besoins spécifiques. L'équipe doit trouver l'emplacement idéal pour chaque élément requis, en veillant à ce qu'il soit ergonomique, robuste et esthétique. Dans le cas des modèles plus anciens, l'opération était plus facile car il y avait plus d'espaces vides où installer des composants, comme dans le tableau de bord ou la console. Les modèles plus récents donnent plus de fil à retordre.
« L'intérieur des véhicules comporte de plus en plus d'écrans et de moins en moins d'espace pour la maintenance. Bien qu'il y ait des compartiments pour ranger des objets ou recharger les téléphones, il est difficile de trouver de la place pour installer toutes les commandes. En particulier dans les véhicules dissimulés, où l'on ne devrait pas pouvoir voir qu'il s'agit en fait d'un véhicule de police », a déclaré M. Busam.
MOSOLF a commencé à utiliser l'impression 3D en 2016, à la suite d'une demande de la police bavaroise d'installer de nouvelles radios numériques sur l'ensemble de son parc de véhicules et de motos.
« Nous avons dû trouver une solution individuelle pour chaque véhicule et chaque moto. Si nous avions fabriqué toutes les pièces en tôle, le processus aurait été long et les solutions auraient été moins attrayantes. C'est pourquoi nous avons commencé à utiliser l'impression 3D. »
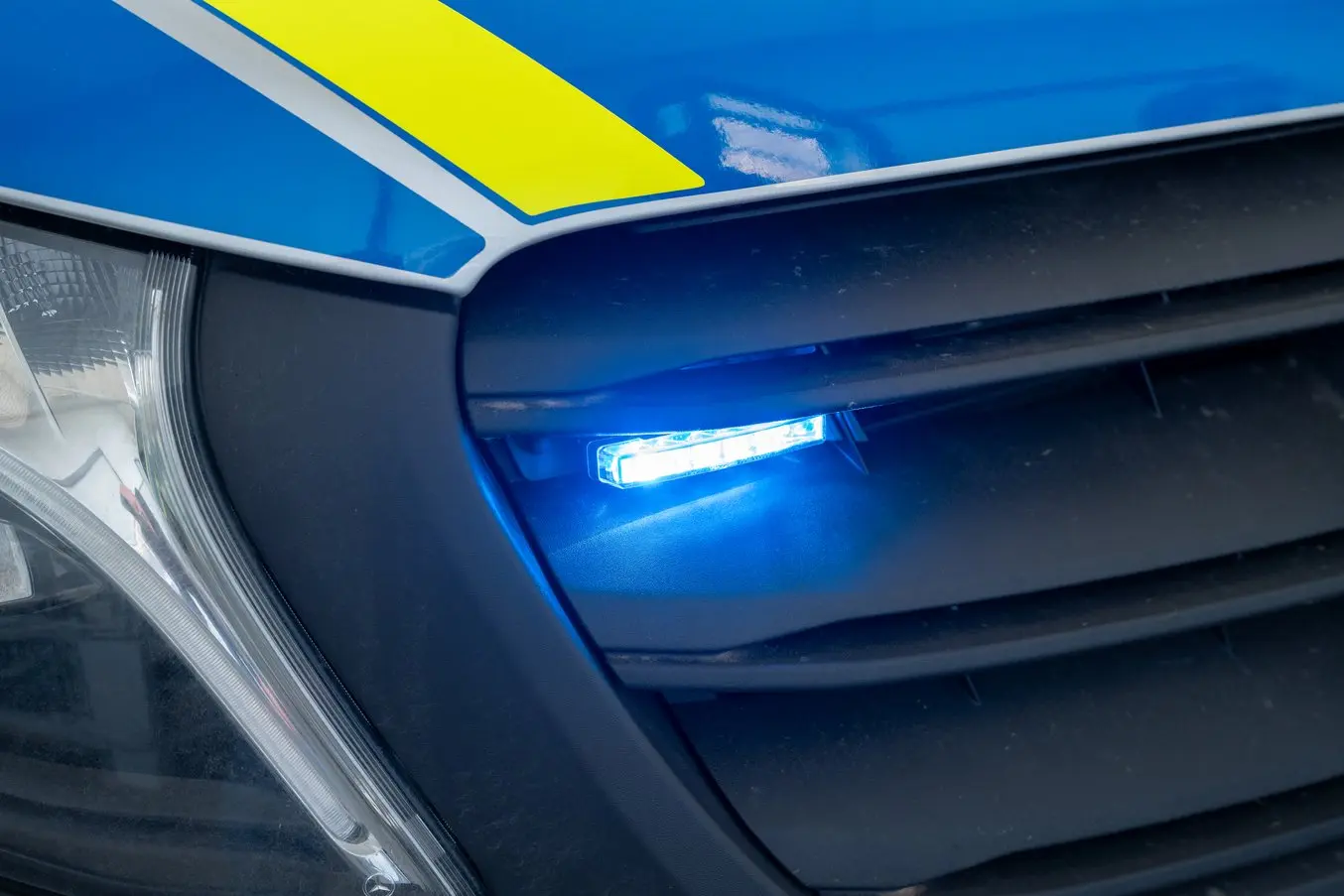
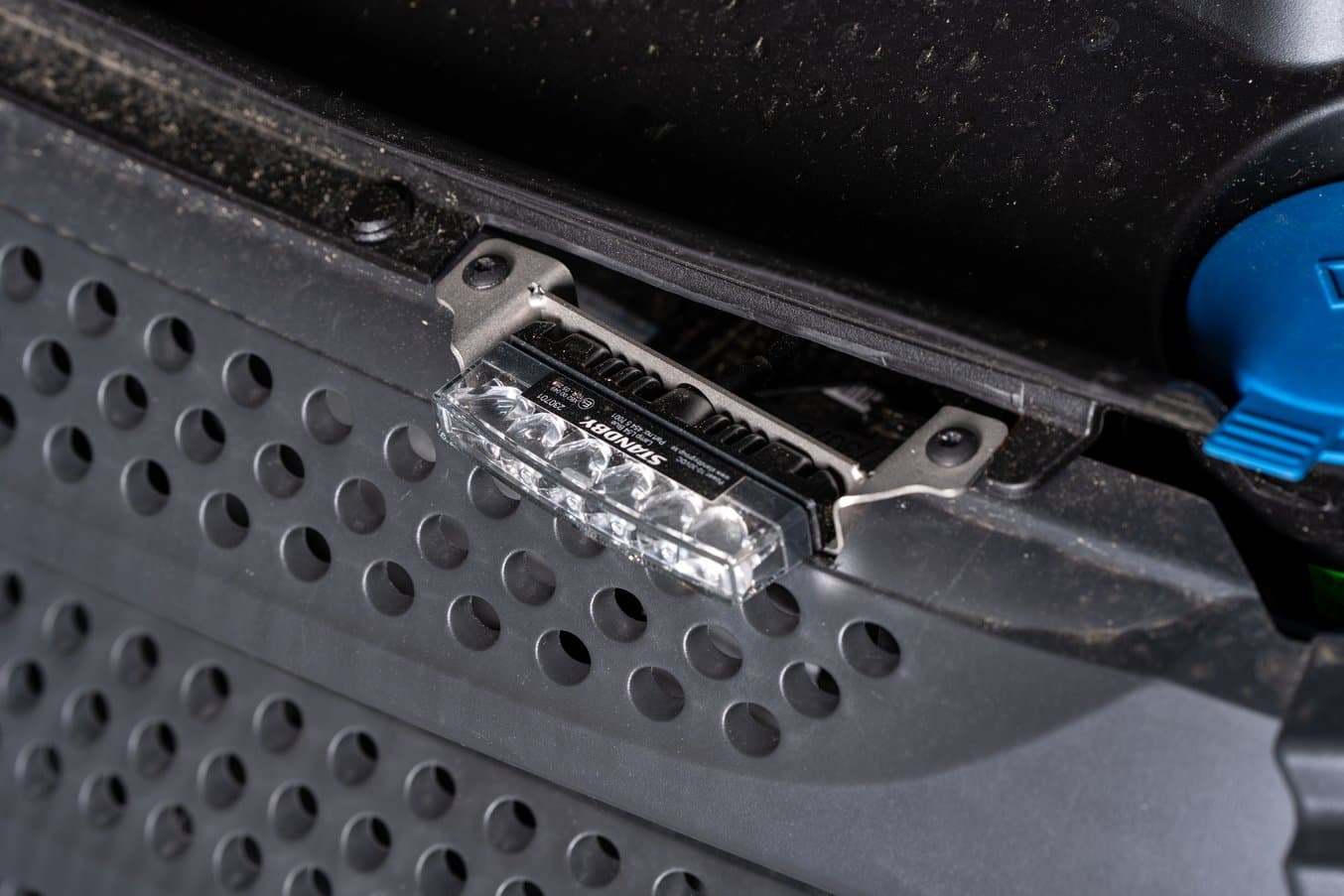
Support personnalisé pour les feux clignotants LED avant de fourgons de police. Auparavant, l'équipe utilisait le formage de tôles pour produire ces pièces.
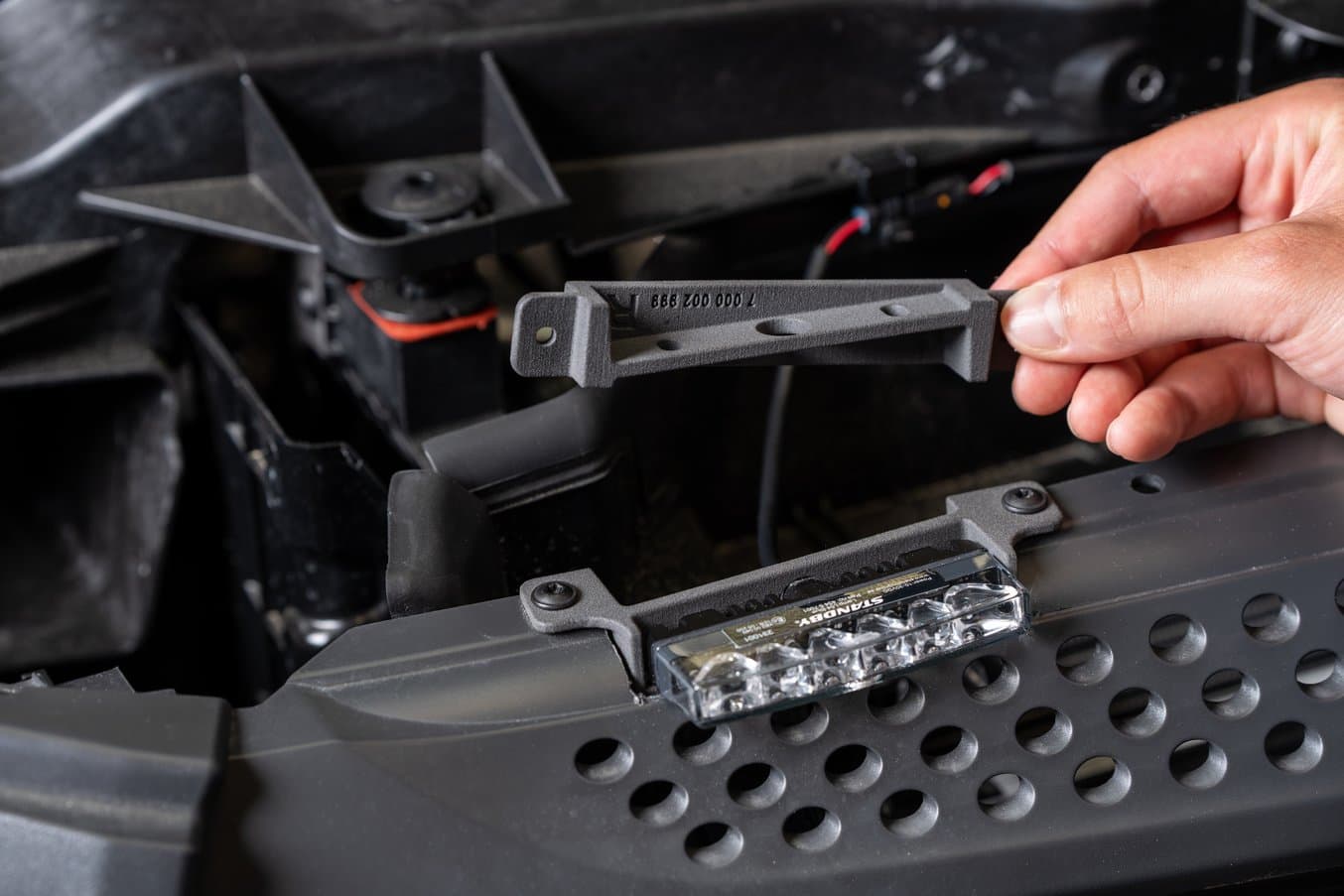
L'impression 3D SLS offre maintenant une solution nettement plus rapide, plus facile et plus rentable.
Dans un premier temps, l'équipe a produit les pièces en utilisant l'impression 3D par dépôt de fil fondu (FDM), qui était la technologie la plus abordable et la plus adaptée aux besoins de l'entreprise à l'époque. Cependant, les limites de cette technologie sont vite apparues : elle ne permettait pas d'augmenter la production à des volumes suffisants pour répondre aux commandes et les pièces n'avaient pas la qualité industrielle requise.
L'impression 3D SLS aurait été la solution idéale, mais le coût des appareils, qui avoisine les 200 000 €, les rendait inabordables pour les petites entreprises. Mais tout a changé avec le lancement de la série Fuse de Formlabs.
« L'impression SLS est parfaite pour MOSOLF, car elle garantit une excellente qualité, une grande précision, des performances matérielles élevées et la possibilité de produire de nombreux composants simultanément. C'est rentable, parce que le système entier est extrêmement abordable », a déclaré Gerhard Duda, PDG et fondateur de 3D-WERK Black Forest GmbH, partenaire de Formlabs, qui a travaillé avec l'équipe de MOSOLF depuis le début afin de trouver les meilleures solutions pour leurs applications.
« L'écosystème Fuse était parfait pour nous car il est le plus facile à gérer en termes de gestion et de flux de travail », a ajouté M. Busam.
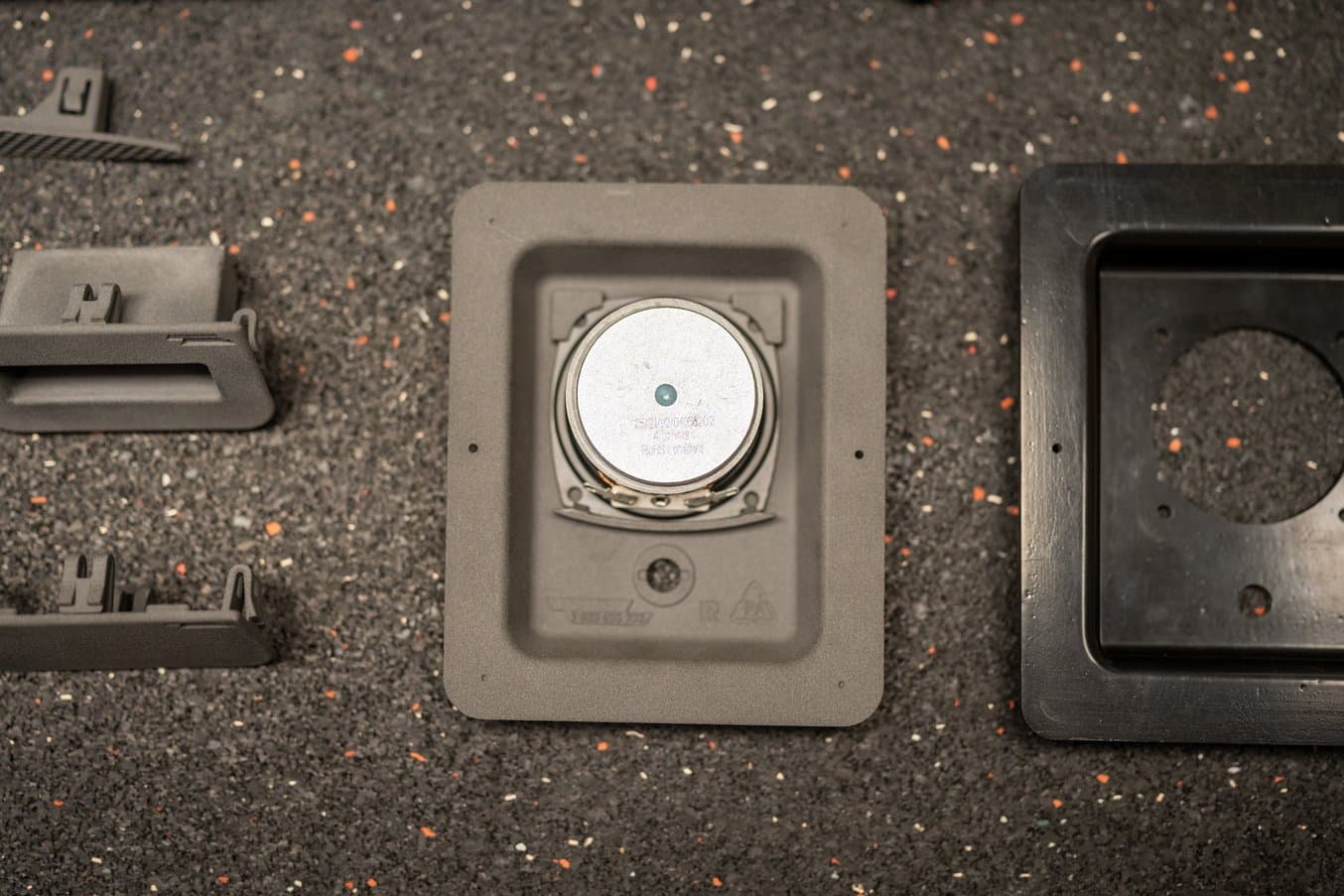
Ce couvercle de haut-parleur est conçu pour réduire les coûts de pré-installation de 70 %. Le corps du haut-parleur se connecte directement à l'insert, ce qui élimine le besoin de soudure ou d'attaches mécaniques.
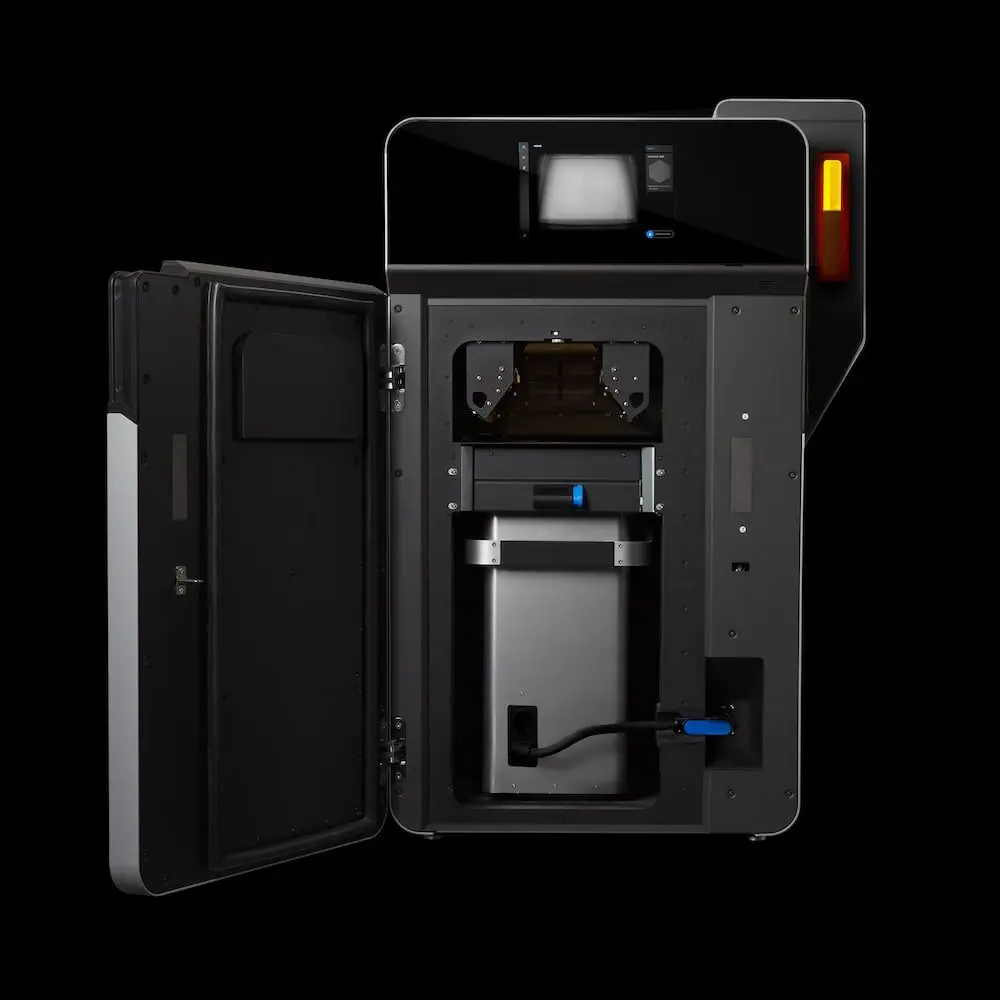
Produire rapidement des pièces SLS haute performance avec la nouvelle Fuse 1+ 30W
Regardez une démonstration détaillée de la Fuse 1 et de l’impression 3D SLS, réalisée par les experts Formlabs.
Des pièces finales personnalisées en 24 heures grâce à l'impression 3D SLS
Par rapport aux procédés de production de masse traditionnels tels que le moulage par injection, le thermoformage, ou le formage de tôles, le plus grand avantage de la fabrication additive est qu'elle permet de produire de petites séries de pièces sur mesure ou de pièces finales sans outillage coûteux.
« Nous utilisons la technologie SLS et en particulier la Fuse 1+ 30W pour divers composants, des conceptions les plus petites et les plus simples à la console complexe installée dans les véhicules. Nous avons largement adopté cette technologie, et la Fuse 1+ 30W répond à environ 80 % de nos besoins », a déclaré Tiberiu Morariu, responsable du prototypage, du design et de la conceptualisation technique chez MOSOLF.
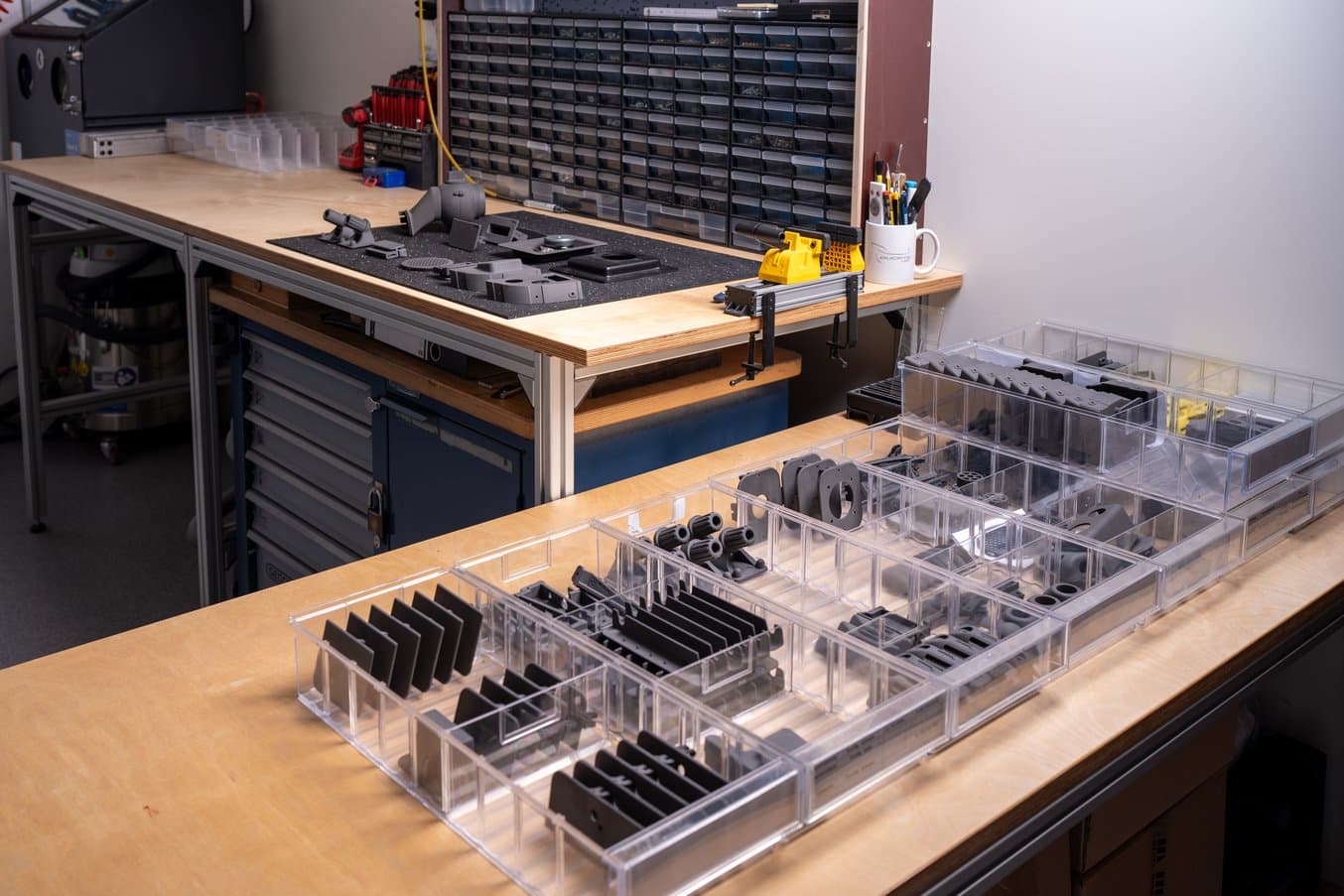
L'équipe de MOSOLF utilise l'impression 3D SLS pour produire des dizaines de conceptions personnalisées, des plus petits couvercles et boîtiers aux grands assemblages de plusieurs pièces et aux composants de tableaux de bord.
« Les exigences peuvent varier non seulement d'un État à l'autre, mais aussi d'un poste de police à l'autre. L'impression 3D permet de s'adapter plus facilement à ces différences. Vous pouvez rapidement changer de design lorsque vous passez d'un véhicule à l'autre. Même si le véhicule et la forme sont identiques, les systèmes installés peuvent être très différents », a expliqué M. Morariu.
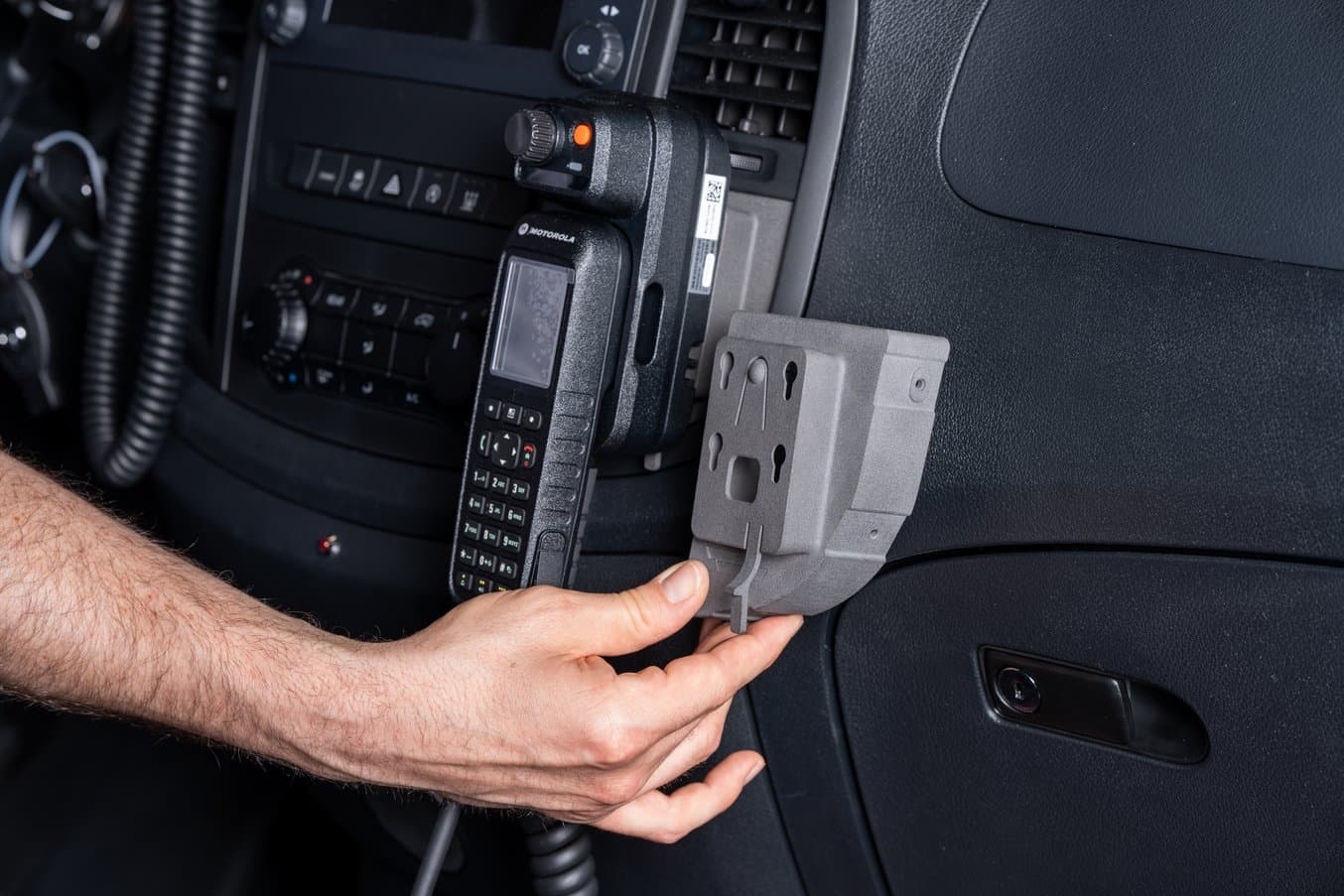
Le support de radio est un excellent exemple de personnalisation. Bien que la fixation à la console soit identique pour toutes les camionnettes Mercedes, l'ensemble peut facilement être modifié à l'aide de différents supports de radio provenant de diverses sociétés.
Cette polyvalence simplifie et accélère considérablement le processus de prototypage et de production, puisque les prototypes et les pièces finales peuvent être produits avec le même appareil.
« Pour un designer, il n'y a rien de plus agréable que de concevoir une idée, de la dessiner et de l'avoir entre les mains dès le lendemain », a déclaré M. Morariu.
« Le plus grand impact de l'impression 3D sur la production en interne est que nous sommes devenus nettement plus rapides dans de nombreux domaines. Avec les procédés traditionnels, nous avons des durées de livraison de quatre à six semaines, surtout si les pièces doivent être revêtues. Avec l'impression 3D, nous pouvons nous procurer des pièces pratiquement du jour au lendemain. Si nous n'avions pas accès à l'impression 3D, nos processus de travail seraient probablement beaucoup plus longs et compliqués, car nous devrions sans doute fabriquer et adapter chaque pièce plusieurs fois. »
Carsten Busam, responsable de la planification des projets, MOSOLF Special Vehicles GmbH
Impression 3D SLS | Formage de tôle | Thermoformage | Moulage par injection | |
---|---|---|---|---|
Délai entre la conception, le prototype et la pièce de série | 1 – 2 semaines | 6 – 8 semaines | 6 – 8 semaines | 6 – 8 semaines |
Délai de production des pièces finales | 1 – 2 jours | 6 – 8 semaines | 6 – 8 semaines | 6 – 8 semaines |
Autres facteurs | Aucun outil n'est nécessaire Personnalisation facile Liberté de conception Esthétique supérieure | Nécessite un outil Liberté de conception limitée Plus difficile à personnaliser Moins bonne esthétique | Nécessite un outil Liberté de conception limitée Plus difficile à personnaliser | Nécessite des outils coûteux Pas de personnalisation possible Moins de liberté de conception |
« De nos jours, les véhicules sont de plus en plus esthétiques, avec des intérieurs moins standards et des espaces de rangement de plus en plus dynamiques et sophistiqués. L'impression 3D joue un rôle clé dans la conception et l'ergonomie des véhicules, car elle offre des résultats que d'autres technologies, telles que le thermoformage ou le formage de tôles, ne peuvent pas toujours garantir. Pour ces formes compliquées, l'impression 3D est également la meilleure solution pour le raccordement au véhicule lui-même. Avec l'impression 3D, je peux concevoir plus librement, et je peux développer pleinement ma créativité en matière de design et de forme. »
Tiberiu Morariu, prototypage, design et conception technique, MOSOLF Special Vehicles GmbH
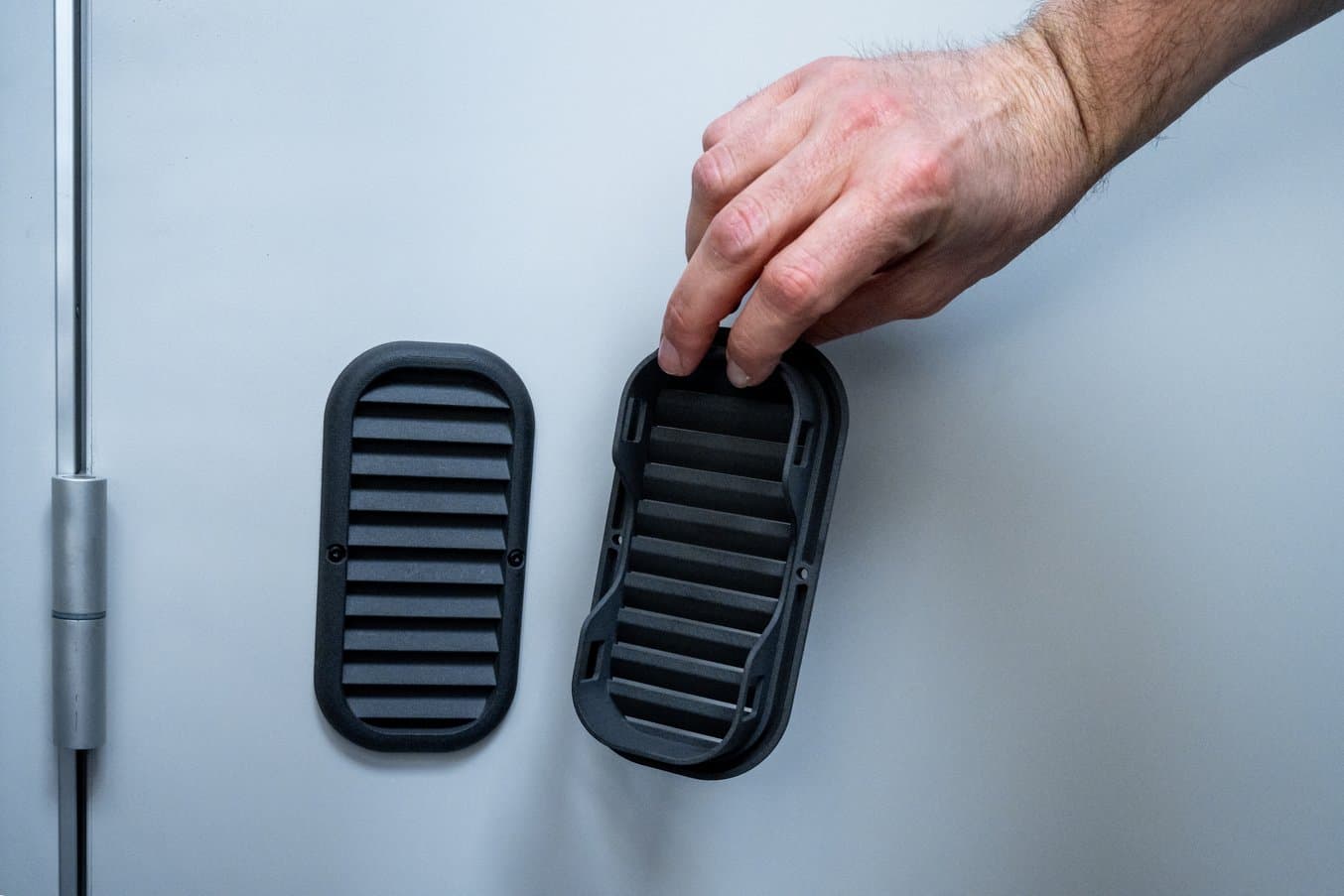
Cet évent est une valve à sens unique qui sépare les compartiments noir et blanc d'un véhicule spécialisé dans les enquêtes sur les incendies criminels. Il s'agit d'un assemblage de conception relativement complexe composé de trois éléments vissés les uns aux autres. L'équipe a d'abord essayé de le produire avec l'impression 3D FDM, mais s'est heurtée à des difficultés liées à la forme circulaire et aux parois fines. Elle s'est ensuite tournée vers l'impression 3D SLS, car elle offre une plus grande liberté de conception.
L'un des principaux avantages de l'impression 3D SLS est que les équipes d'ingénieurs connaissent les propriétés mécaniques des matériaux disponibles, tels que le nylon, largement utilisé dans l'industrie automobile pour la production de pièces intérieures et extérieures. L'équipe MOSOLF a une bonne connaissance des performances d'une pièce en nylon fabriquée par impression 3D SLS, ce qui lui permet de concevoir en tenant compte de la fonctionnalité et même de remplacer certaines pièces métalliques d'origine.
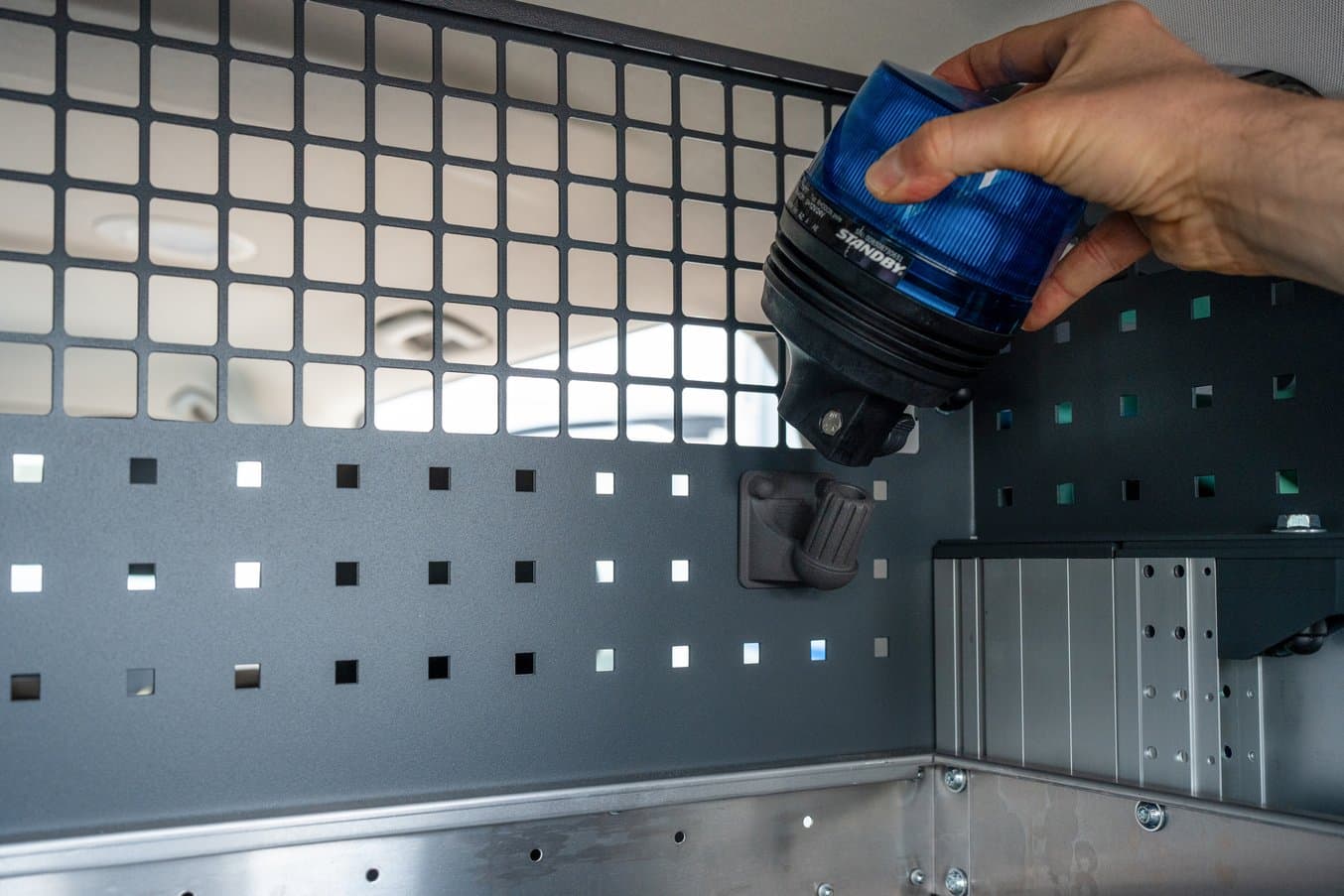
Fixation par clip pour une lampe de secours amovible dans le coffre.
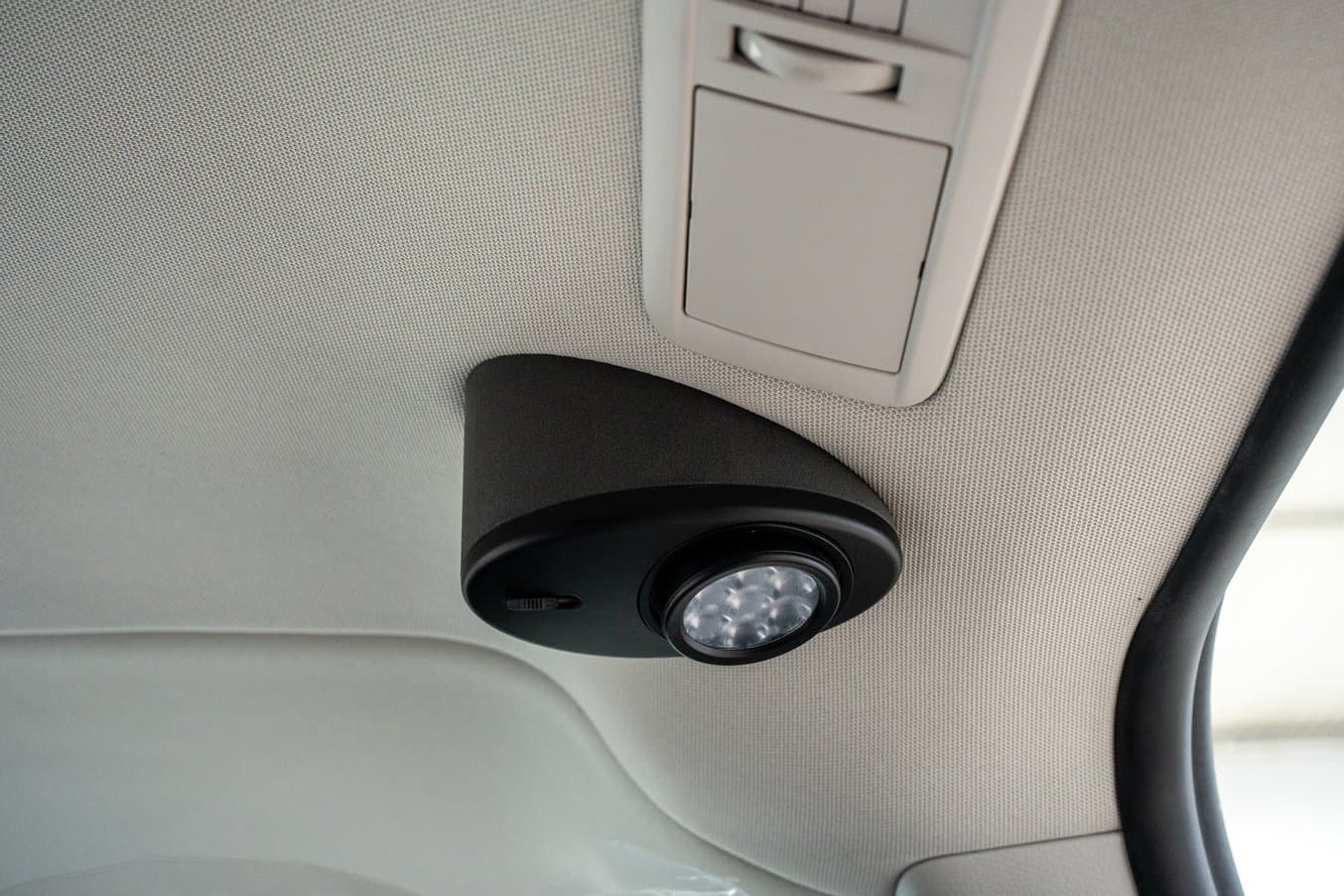
Boîtier et support pour un plafonnier.
« L'écosystème Fuse offre un matériau parfait : prêt à l'emploi, présent sur le marché depuis longtemps et testé de manière approfondie », a déclaré M. Duda.
Outre la durabilité, l'un des critères les plus importants pour les applications automobiles est la résistance à la chaleur. Avec les matériaux FDM, le PLA est hors de question, car sa température de fléchissement sous charge (TFC) n'est que d'environ 50 ºC à 0,45 MPa. L'ABS a une TFC de 90 ºC à 0,45 MPa, ce qui est mieux, mais reste à la limite ou en dessous de la limite pour de nombreuses applications. Avec une TFC de 171 °C à 0,45 MPa, Nylon 12 Powder de Formlabs offre une résistance à la chaleur nettement plus élevée, ce qui signifie qu'il n'y a pas de risque que des pièces fonctionnelles comme un support de radio tombent en panne lorsque la voiture chauffe sur le parking pendant l'été.
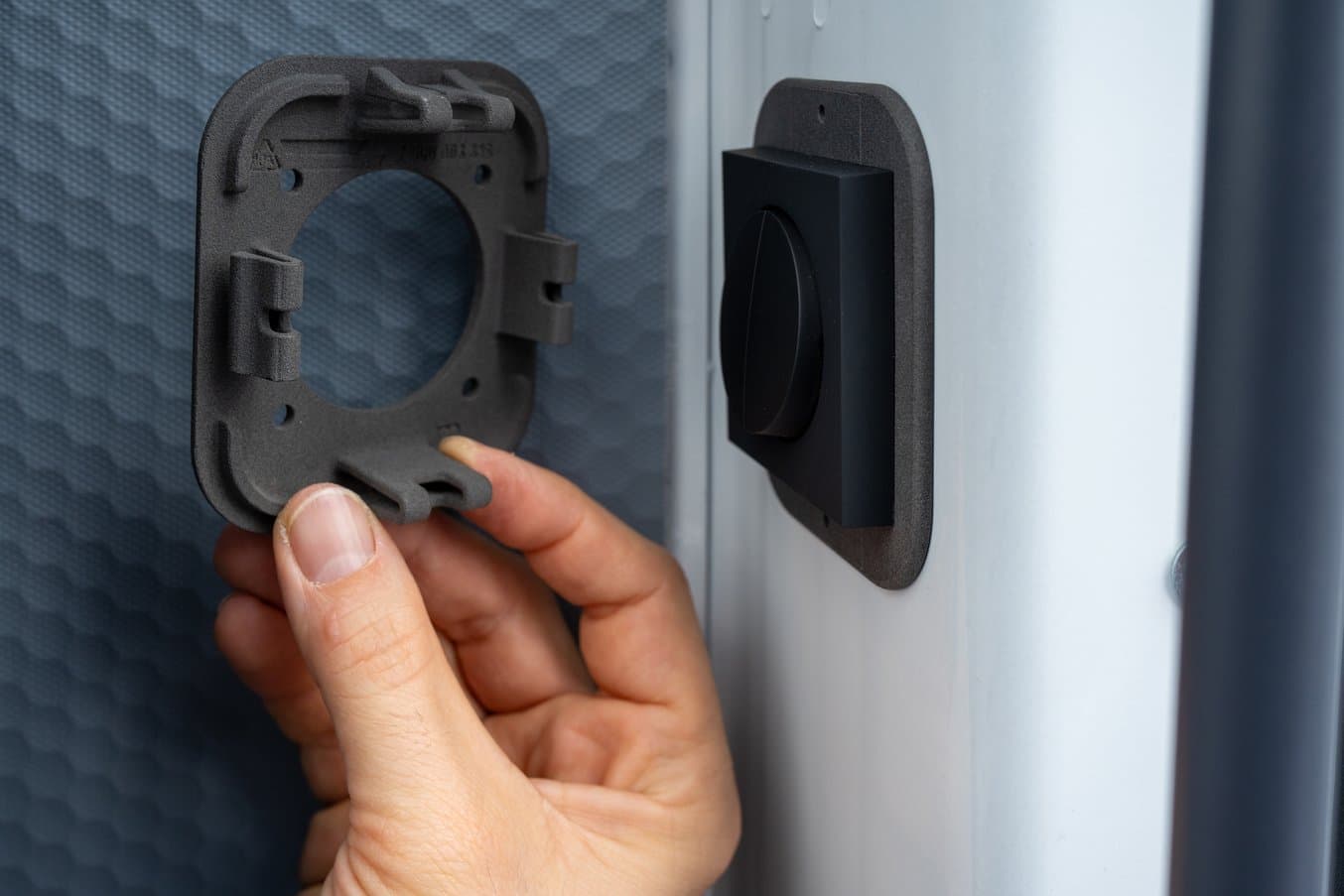
Boîtier de prise électrique.
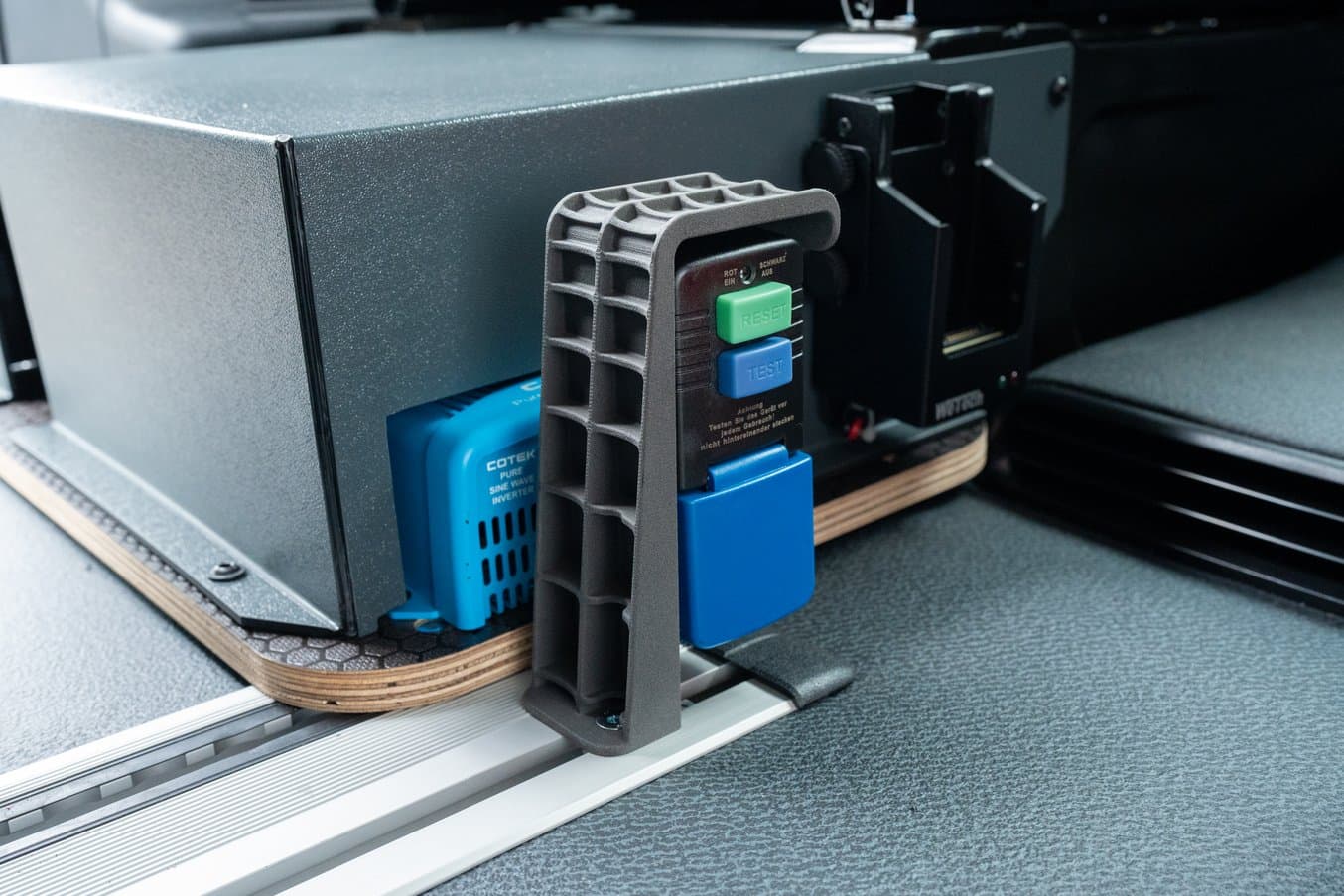
Couvercle de protection pour éviter tout dommage accidentel lors des déplacements en véhicule.
Dans certains cas, les véhicules sont loués par la police ou les forces d'urgence, puis revendus à la population civile ou à d'autres services une fois leur utilisation terminée. C'est pourquoi l'équipe de MOSOLF doit adapter ces véhicules sans les endommager ou les modifier de manière permanente, afin qu'ils puissent être restaurés dans leur état d'origine à la fin de leur cycle de vie. La fabrication additive facilite cette tâche : au lieu de modifier de manière permanente les composants existants, l'équipe les remplace par des pièces imprimées en 3D qui peuvent être remplacées ultérieurement.
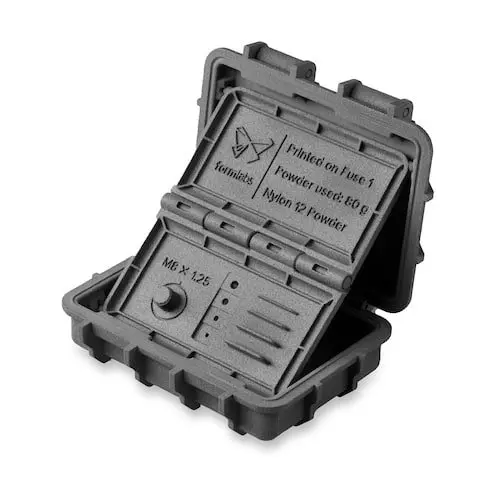
Commander un échantillon SLS gratuit
Examinez et constatez par vous-même la qualité Formlabs. Nous vous enverrons un échantillon gratuit imprimé sur la Fuse 1+ 30W à votre bureau.
Vers un avenir où les véhicules de police contiendront de plus en plus de composants imprimés en 3D
Fortes du succès de l'impression 3D SLS, les équipes de MOSOLF et de 3D-WERK envisagent désormais d'utiliser d'autres matériaux et d'autres imprimantes pour remplacer encore plus de pièces dans les véhicules spéciaux.
« Malgré des années d'expérience dans le domaine de la fabrication additive, je suis toujours étonné par les produits que nous avons conçus et imprimés nous-mêmes, grâce à la fonctionnalité et aux possibilités offertes par l'impression 3D », a déclaré Michael Ringwald, PDG de MOSOLF.