Produire en série des systèmes de haut-parleurs professionnels grâce à l'impression 3D SLS
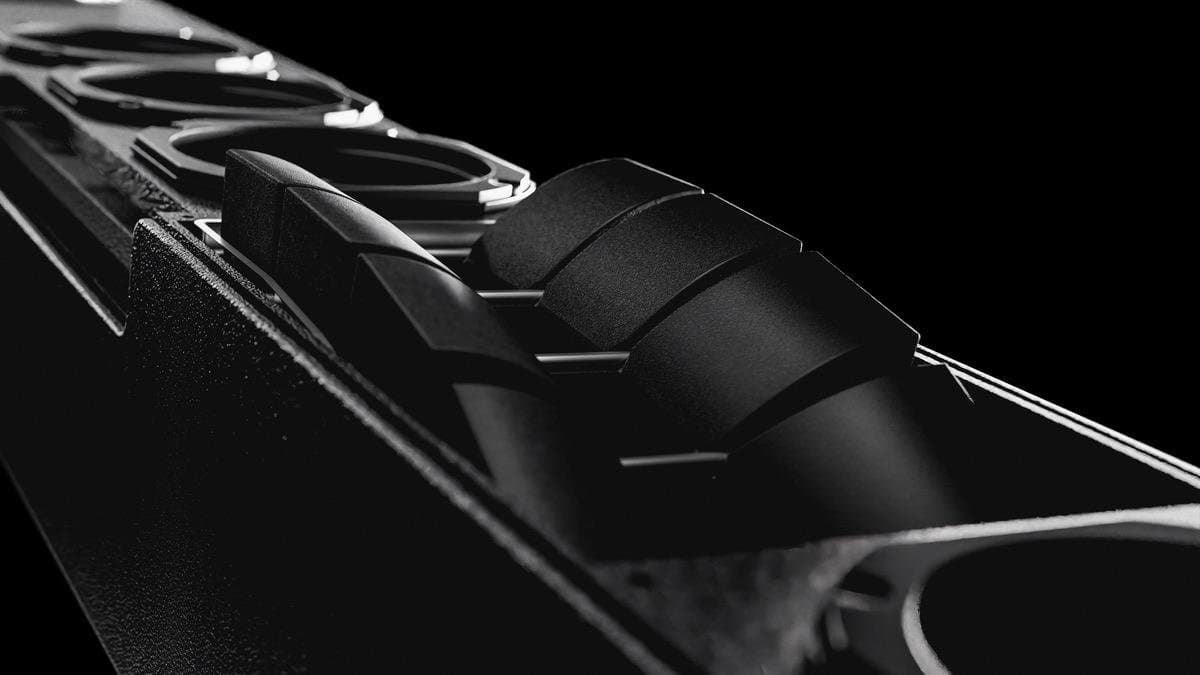
Les systèmes de haut-parleurs de Kling & Freitag ont pu se démarquer de leurs concurrents grâce au développement continu de leurs technologies, à leur conception moderne et à leurs applications polyvalentes.
Depuis 20 ans, ce fournisseur de systèmes sonores utilise la fabrication additive pour développer ses produits. Ils ne l'utilisaient d'abord que pour le prototypage rapide, mais plus récemment ils en ont tiré parti pour produire en série des composants de leur système de haut-parleurs innovant PIAM.
Dans notre interview, André Figula, ingénieur concepteur chez Kling & Freitag, parle de ses nombreuses années d'expérience avec la fabrication additive, des avantages de l'impression 3D dans l'ingénierie et de la façon dont elle continuera très probablement à stimuler l'innovation chez Kling & Freitag à l'avenir.
Plus de 30 ans d'expérience dans le développement de systèmes professionnels de sonorisation et de haut-parleurs
Kling & Freitag vise à impressionner ses clients avec un son de première classe et une large gamme de systèmes de sonorisation professionnels.
Fondée en 1991, l'entreprise Kling & Freitag fournit des systèmes de sonorisation innovants à de nombreux théâtres, stades et salles de concert dans le monde entier. L'entreprise propose également ses systèmes de haut-parleurs pour des festivals, des foires commerciales ou des événements en plein air.
En 2018, Kling & Freitag a achevé un de ses projets les plus prestigieux : améliorer le système acoustique principal de la grande salle de concert de l'Elbphilharmonie à Hambourg.
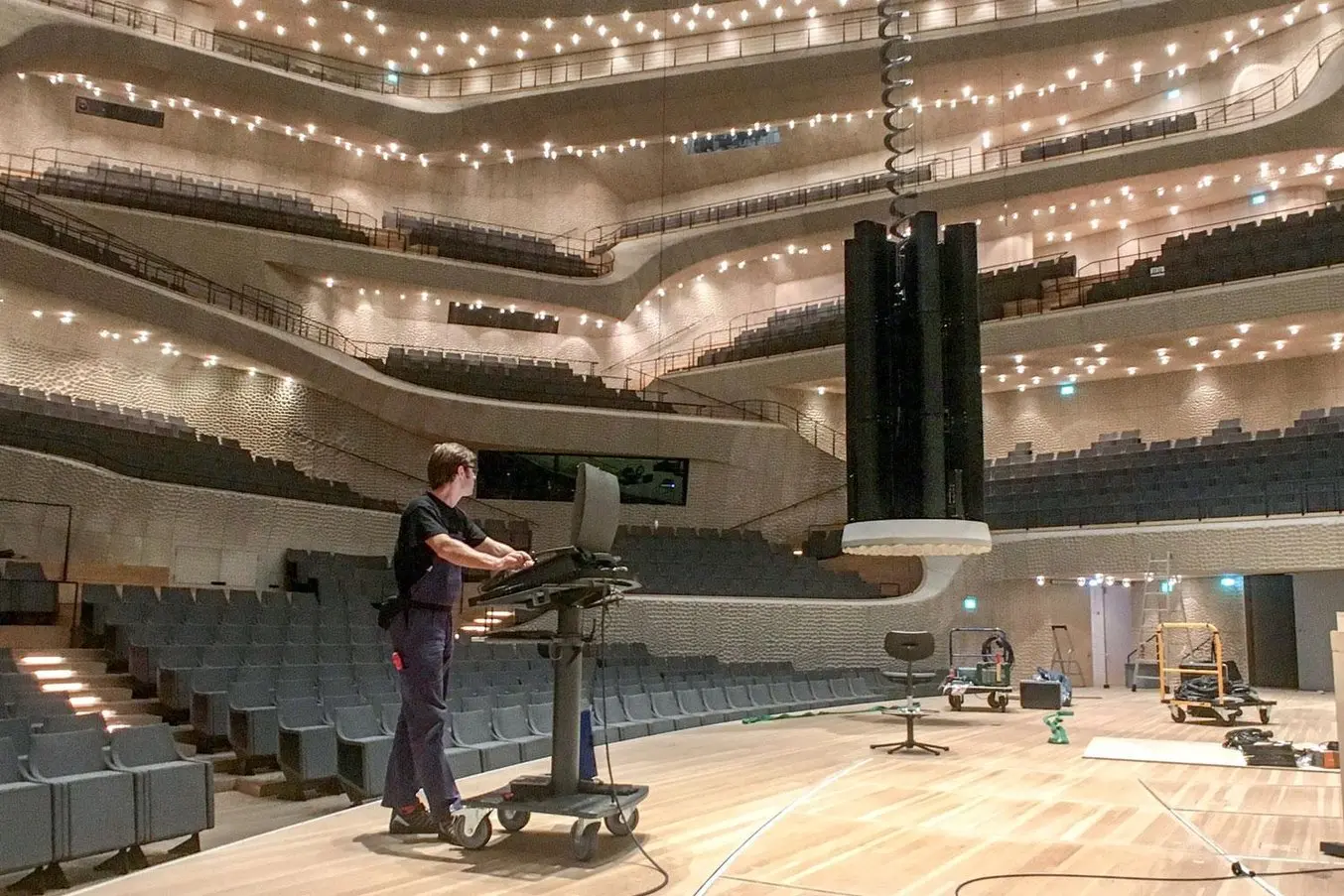
Le groupe d'enceintes VIDA L de Kling & Freitag, suspendu au plafond de la grande salle de l'Elbphilharmonie, offre à l'ensemble de la salle une excellente expérience sonore.
En plus d'être performants sur le plan sonore, les systèmes Kling & Freitag impressionnent également par leur aspect. Les composants des haut-parleurs, élégants et souvent à peine visibles, sont particulièrement appréciés lorsque l'entreprise travaille en collaboration avec des architectes.
De l'externalisation à l'adoption de l'impression 3D SLS en interne
Kling & Freitag a depuis longtemps recours à l'impression 3D. M. Figula a commencé à s'intéresser à la fabrication additive au début des années 2000. À l'époque, lui et son équipe fabriquaient encore manuellement ce que l'on appelle des cornets à haute fréquence afin de répondre aux exigences de leurs clients en matière de précision et de qualité sonore, ce qui leur prenait des semaines entières.
Cependant, les systèmes d'impression 3D SLS étaient encore si chers (plus de 200 000 €) que l'équipe a décidé de travailler avec des sous-traitants en fabrication additive pour créer des prototypes fonctionnels. Ils ont ainsi pu installer les prototypes directement dans les enceintes pour les tester, ce qui leur a permis d'économiser des semaines de travail tout en continuant à faire appel à la sous-traitance.
L'arrivée de la Fuse 1 de Formlabs a tout changé. Cette imprimante a réduit le coût de l'impression 3D SLS d'environ dix fois, donnant aux petites et moyennes entreprises comme Kling & Freitag l'outil parfait pour commencer à produire des pièces SLS en interne.
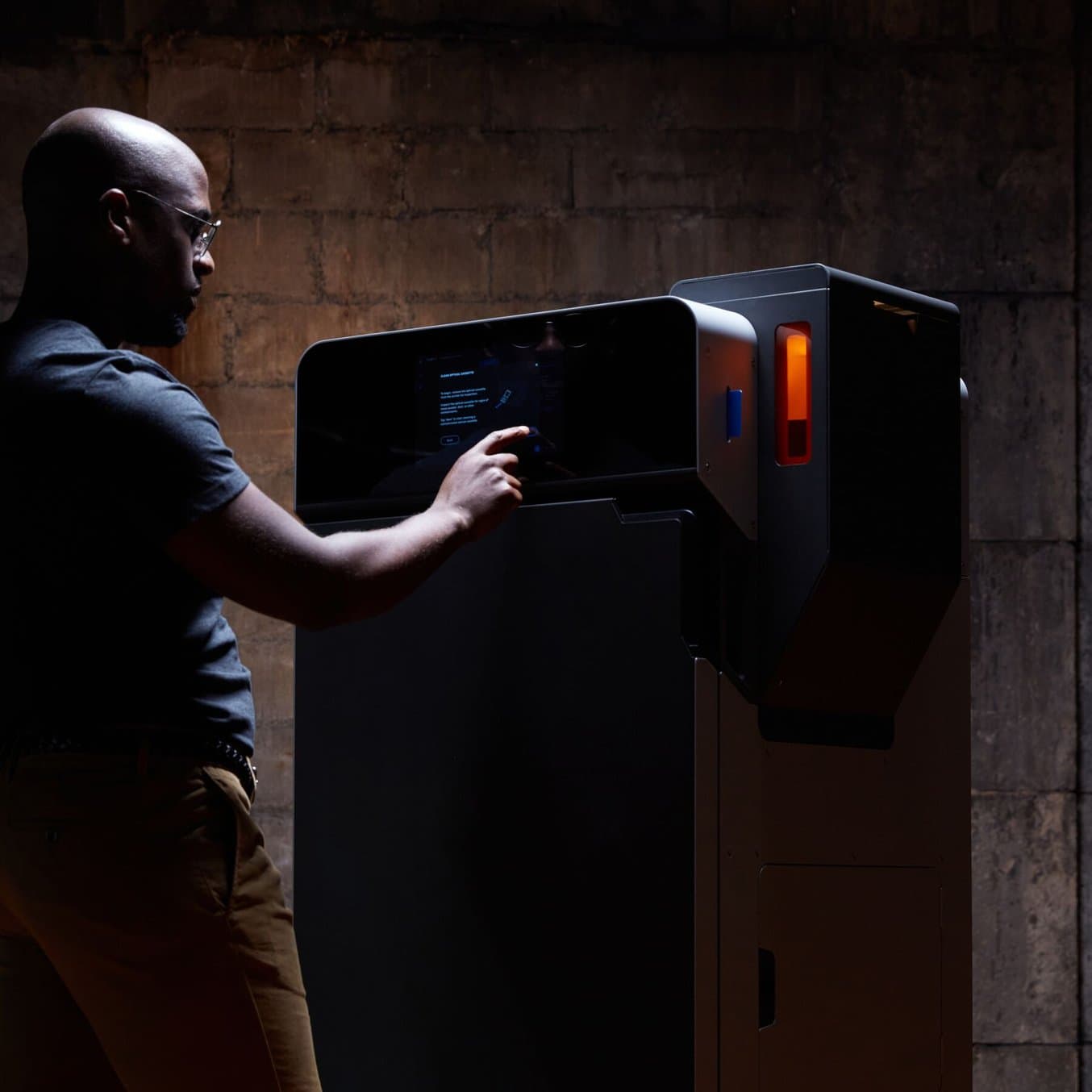
Externalisation ou internalisation : quand est-il judicieux d'adopter l'impression 3D SLS en interne ?
Dans ce livre blanc, nous passons en revue les avantages de l'adoption en interne des imprimantes 3D à frittage sélectif par laser (SLS) par rapport à la sous-traitance des pièces SLS auprès de fournisseurs de services.
Production en série du nouveau guide d'ondes avec la Fuse 1
Le haut-parleur à colonne PIAM est l'un des produits récemment lancés par Kling & Freitag. Sa caractéristique la plus unique est ce que l'on appelle le pavillon d'aigus ou guide d'ondes, composé de quatre réseaux de cornets mobiles qui peuvent être ajustés pour s'adapter à un environnement spécifique. Il est difficile d'obtenir une qualité sonore uniforme pour des lieux et des publics de taille variable. La mécanique sophistiquée du PIAM permet de constamment réajuster l'acoustique, ce qui garantit une distribution uniforme du son dans l'auditoire quel que soit le lieu dans lequel l'unité est utilisée.
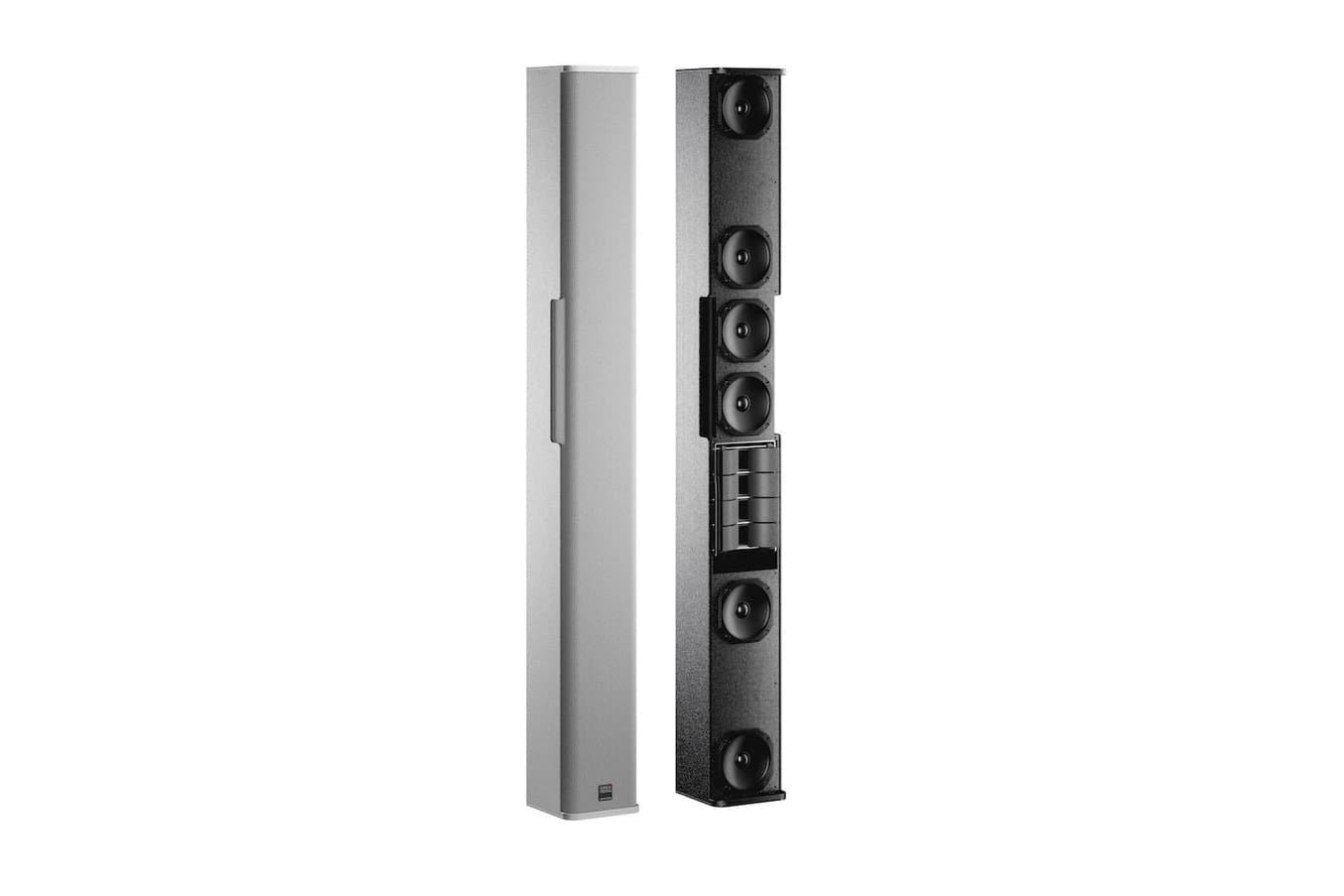
Quatre réseaux de cornets flexibles sont utilisés pour permettre une distribution réglable du son.
En raison de la complexité de leur conception, il aurait été extrêmement difficile et coûteux de fabriquer ces réseaux de cornets réglables en utilisant un processus de moulage par injection.
« S'il avait été adapté pour ce genre de pièces, le moulage par injection aurait probablement coûté autant qu'une imprimante 3D SLS de Formlabs. C'est pourquoi nous avons décidé d'acheter notre propre imprimante pour développer et produire en série nos guides d'ondes. »
André Figula, ingénieur concepteur chez Kling & Freitag
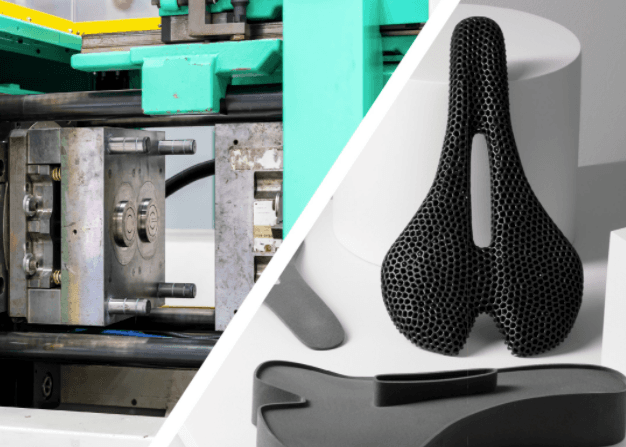
Impression 3D SLS ou moulage par injection : quand remplacer les pièces moulées par l'impression 3D ?
Ce livre blanc présente la dynamique des coûts pour des cas d'utilisation réels, et vous montre comment utiliser l'impression 3D SLS, le moulage par injection, ou les deux.

Chambre de fabrication entièrement remplie de l'imprimante 3D SLS Fuse 1, vue dans le logiciel PreForm.
Aujourd'hui, M. Figula et son équipe ont commencé à produire leurs guides d'ondes en série et font face à une demande considérable dans l'industrie audio professionnelle.
En outre, ils découvrent à la Fuse 1 de plus en plus d'avantages. Ils utilisent par exemple l'espace restant de la chambre de fabrication pour fabriquer des prototypes rapides d'autres composants, ce qui leur permet d'économiser beaucoup de temps et d'argent.
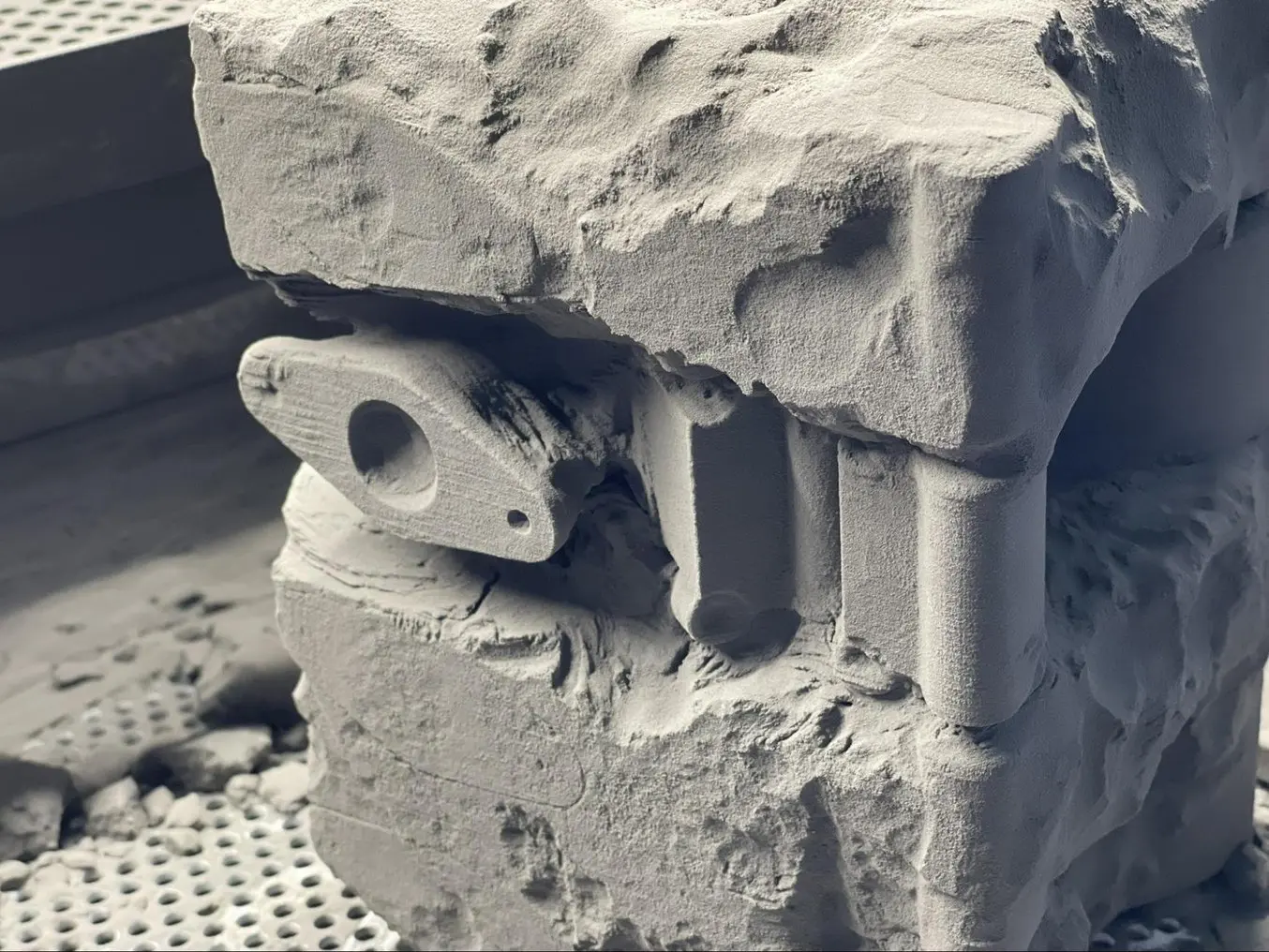
Un composant imprimé en 3D par SLS pendant le post-traitement avec la Fuse Sift.
La liberté de conception qu'offre la fabrication additive
Un autre avantage majeur de l'imprimante 3D SLS de Kling & Freitag est la flexibilité qu'elle permet dans la conception de nouveaux produits.
« Quand nous développons de nouveaux produits, nous pouvons réajuster les caractéristiques du prototype à chaque itération. Nous n'aurions pas eu une telle flexibilité avec le moulage par injection, et nous n'aurions donc pas obtenu les mêmes résultats ».
André Figula, ingénieur concepteur chez Kling & Freitag
La forme complexe du guide d'ondes ainsi que les nombreuses contre-dépouilles de la conception auraient également rendu le moulage par injection inadapté.
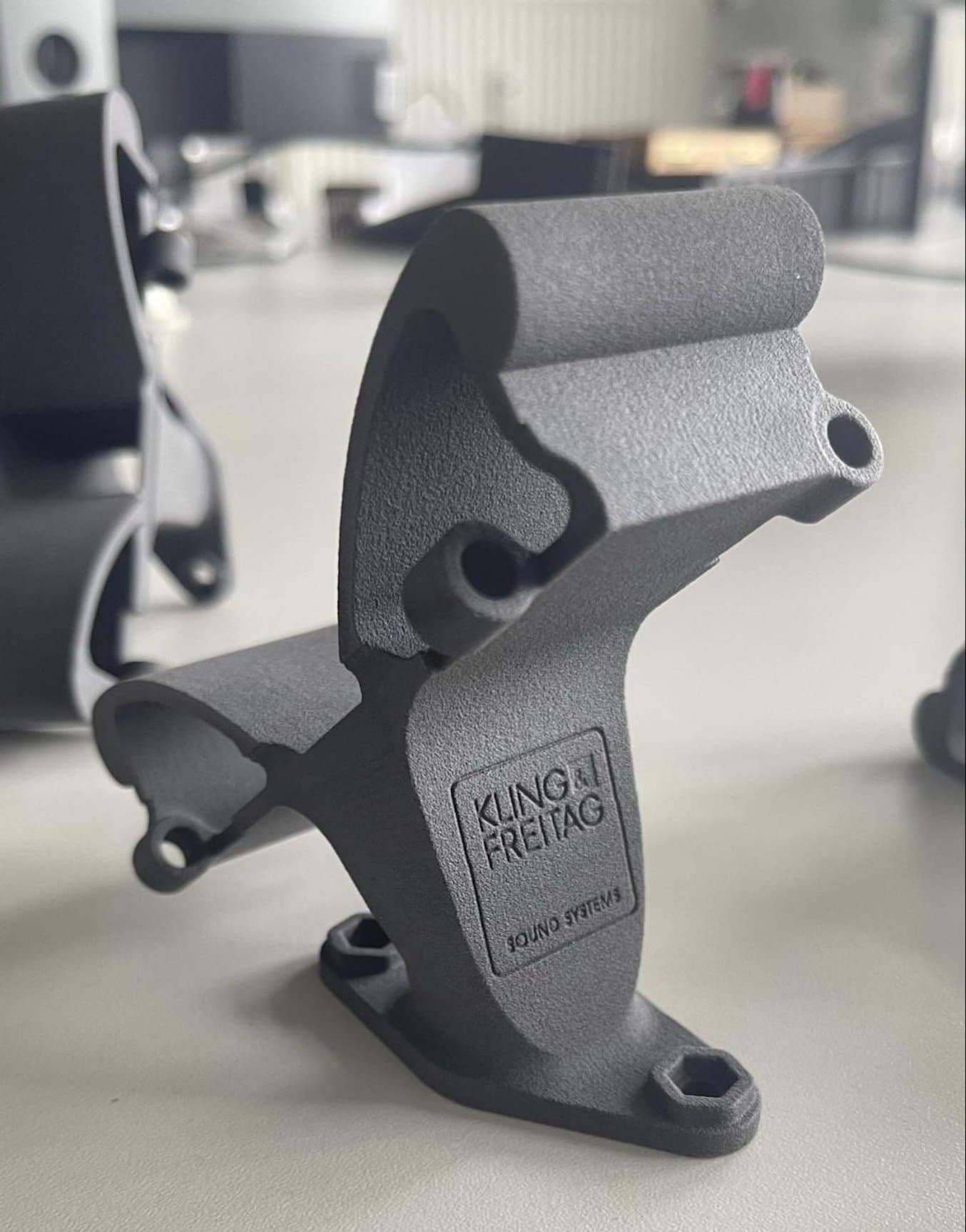
L'un des quatre réseaux de cornets innovants imprimés en Nylon 12 Powder..
« Nous n'aurions pas pu fabriquer le guide d'ondes de l'enceinte PIAM sans la Fuse 1. »
André Figula, ingénieur concepteur chez Kling & Freitag
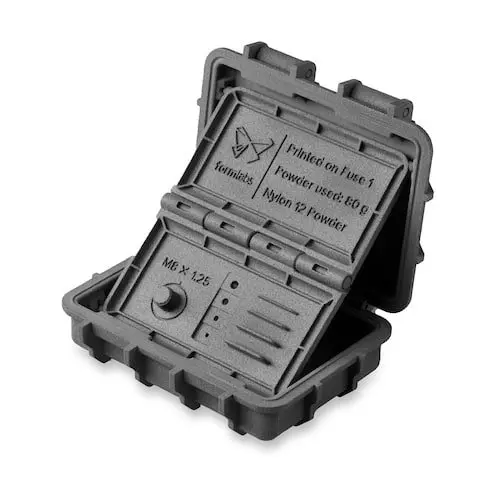
Commandez un échantillon SLS gratuit
Examinez et constatez par vous-même la qualité Formlabs. Nous vous enverrons un échantillon gratuit imprimé sur la Fuse 1+ 30W à votre bureau.
La prochaine étape : breveter des produits innovants grâce à la Fuse 1
Les imprimantes fonctionnent en continu chez Kling & Freitag. Elles sont principalement utilisées pour produire en série le nouveau guide d'ondes du système de haut-parleurs PIAM, mais aussi pour de nouveaux produits.
« Avec l'impression 3D, tout est plus rapide et plus abordable, et nous restons flexibles tout au long du processus de développement ».
André Figula, ingénieur concepteur chez Kling & Freitag
L'un de ces produits a été fabriqué à 100 % sur l'imprimante 3D SLS Fuse 1 et est sur le point de faire l'objet d'une demande de brevet.
« Si j'avais fait appel à des sous-traitants externes, j'aurais dû attendre environ huit semaines pour obtenir un nouveau prototype entre chaque étape d'itération. Maintenant, il me suffit de téléverser chaque nouvelle variante sur la Fuse 1 et, dans un délai relativement court, j'ai une pièce fonctionnelle », explique M. Figula.
Pour en savoir plus sur la façon dont la Fuse 1 peut aider votre entreprise à progresser dans le prototypage rapide et la production en série, contactez nos experts et demandez un échantillon de pièce gratuit.