Besoin de rapidité : Rome Snowboards accélère le développement de ses produits grâce à l'impression 3D SLS
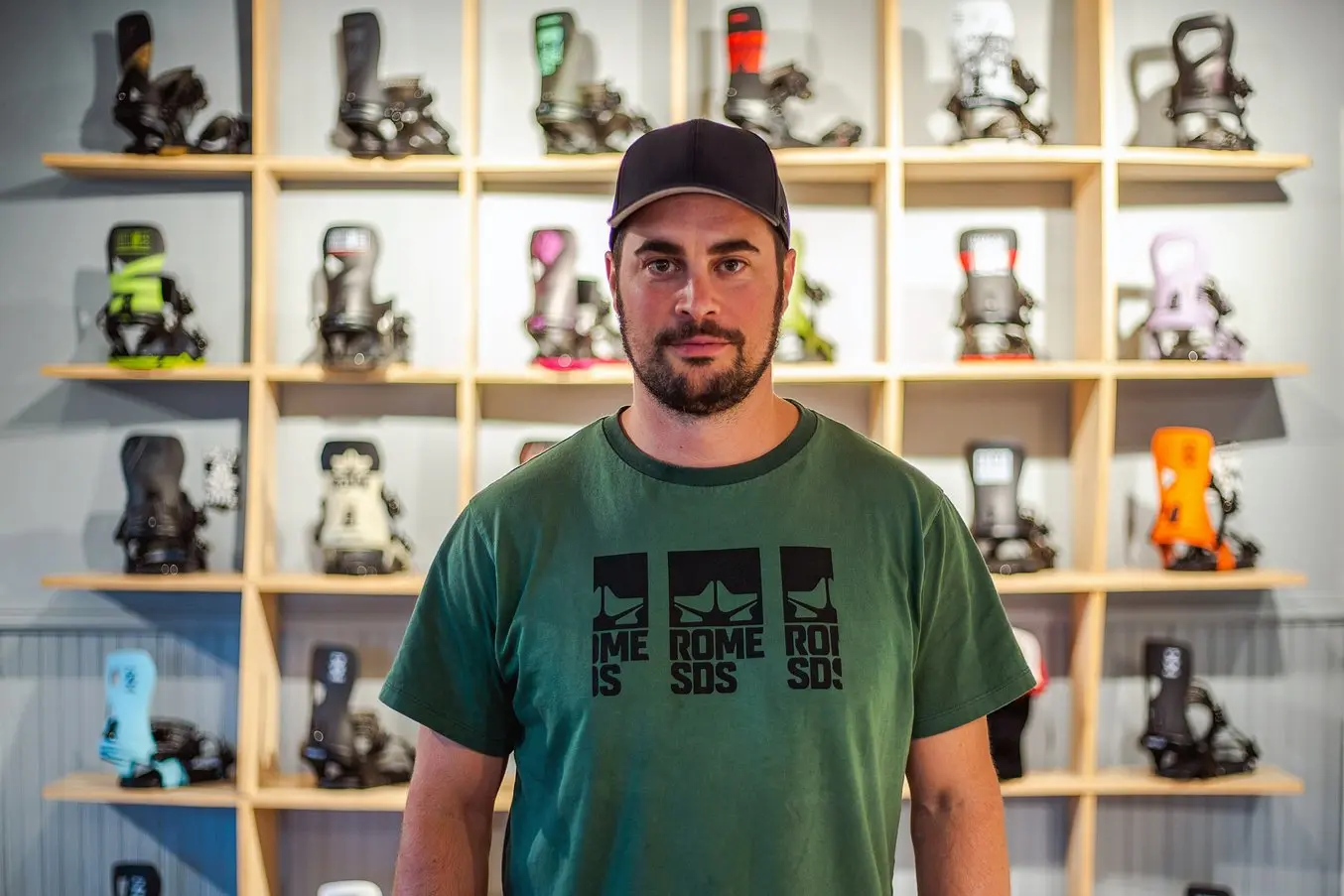
Justin Frappier, concepteur de produits chez Rome Snowboards, est en mesure de concevoir, de prototyper et d'améliorer chaque jour ses produits grâce à l'impression 3D SLS en interne.
Nous visons toujours à développer des produits innovants... Avec l'accélération du prototypage, nous constatons déjà un retour sur investissement positif après cinq mois à peine.
Justin Frappier, concepteur de produits chez Rome Snowboards
Depuis son invention dans les années 1960, le snowboard est associé à la rébellion : ses glisseurs jeunes et effrontés, ses vêtements amples et ses cascades tape-à-l'œil en font le petit frère punk des sports d'hiver traditionnels. Ses similitudes de style avec le surf et le skateboard attirent des sportifs de tous poils et contribuent à renforcer son image de contre-culture.
Le snowboard est né d'un désir de faire les choses différemment, et la fabrication de cet équipement reflète bien cet état d'esprit. Les fabricants de snowboards trouvent sans cesse de nouveaux moyens de faire glisser les sportifs le plus longtemps possible grâce à des équipements fiables, robustes et confortables, capables de supporter une saison complète sur les pistes. Pour accélérer leur processus itératif et développer constamment de nouvelles conceptions innovantes, les fabricants se tournent vers l'impression 3D en interne.
Rome Snowboards, une petite entreprise de dix personnes située à Waterbury dans le Vermont a une devise : All Ways Down (La glisse à tout prix). Cela décrit bien leur passion de la montagne et leur processus de développement : le concepteur de produits Justin Frappier est toujours à la recherche de nouveaux processus et de nouvelles méthodes pour créer des fixations et des bottes. L'objectif principal de Rome est de créer des équipements pour des randonnées plus longues et plus confortables, capables de résister à la torsion et à l'impact générés par les sauts, les pirouettes et les glissades. En adoptant une imprimante 3D à frittage sélectif par laser (SLS) Fuse 1 en interne, Rome Snowboards a pu innover plus rapidement et tester ses prototypes sur la montagne, ce qui permet un meilleur processus itératif. « Nous visons toujours à développer des produits innovants... Nous constatons déjà un retour sur investissement positif après cinq mois à peine, grâce à l'accélération du prototypage. », nous dit M. Frappier.
Rome Snowboards fabrique déjà certains des produits les plus respectés de l'industrie. L'entreprise a été récompensée par des spécialistes tels que White Lines, qui a sélectionné les fixations Vice de Rome pour sa liste des 100 meilleurs produits de snowboard en 2021-2022. « Il s'agit d'une fixation extrêmement polyvalente qui associe une technologie éprouvée et fiable à des caractéristiques haut de gamme... Rome a frappé dans le mille avec la dernière version de son best-seller Vice. »
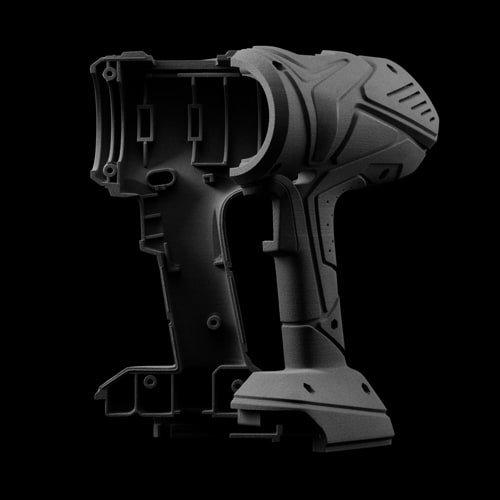
Introduction à l’impression 3D à frittage sélectif par laser (SLS)
Vous cherchez une imprimante 3D pour réaliser des pièces solides et fonctionnelles ? Téléchargez le livre blanc pour savoir comment fonctionne l’impression 3D SLS et les raisons de sa popularité pour le prototypage fonctionnel et la production de produits finis.
Le SLS : un saut dans l'inconnu
Avant la Fuse 1, M. Frappier et son collègue de l'équipe de conception de Rome réalisaient la majeure partie du travail de conception à la main avec des matériaux tels que l'argile, l'adhésif bondo et des pièces externalisées, qui devaient toutes être assemblées et post-traitées pour obtenir un prototype final ressemblant à une planche de surf. L'impression 3D était dans sa ligne de mire, mais ce n'est que lorsque le teaser de la Fuse 1 a mis en avant une fixation de snowboard imprimée en 3D que M. Frappier s'y est intéressé de plus près. « Cela fait probablement huit ans que je souhaite installer une imprimante 3D au bureau... J'ai pesé le pour et le contre de différentes imprimantes affichant différents prix, et la Fuse 1 m'a semblé vraiment bien adaptée, car elle comprenait à la fois la Fuse Sift et l'imprimante. Tout me semblait bien pensé », explique M. Frappier.
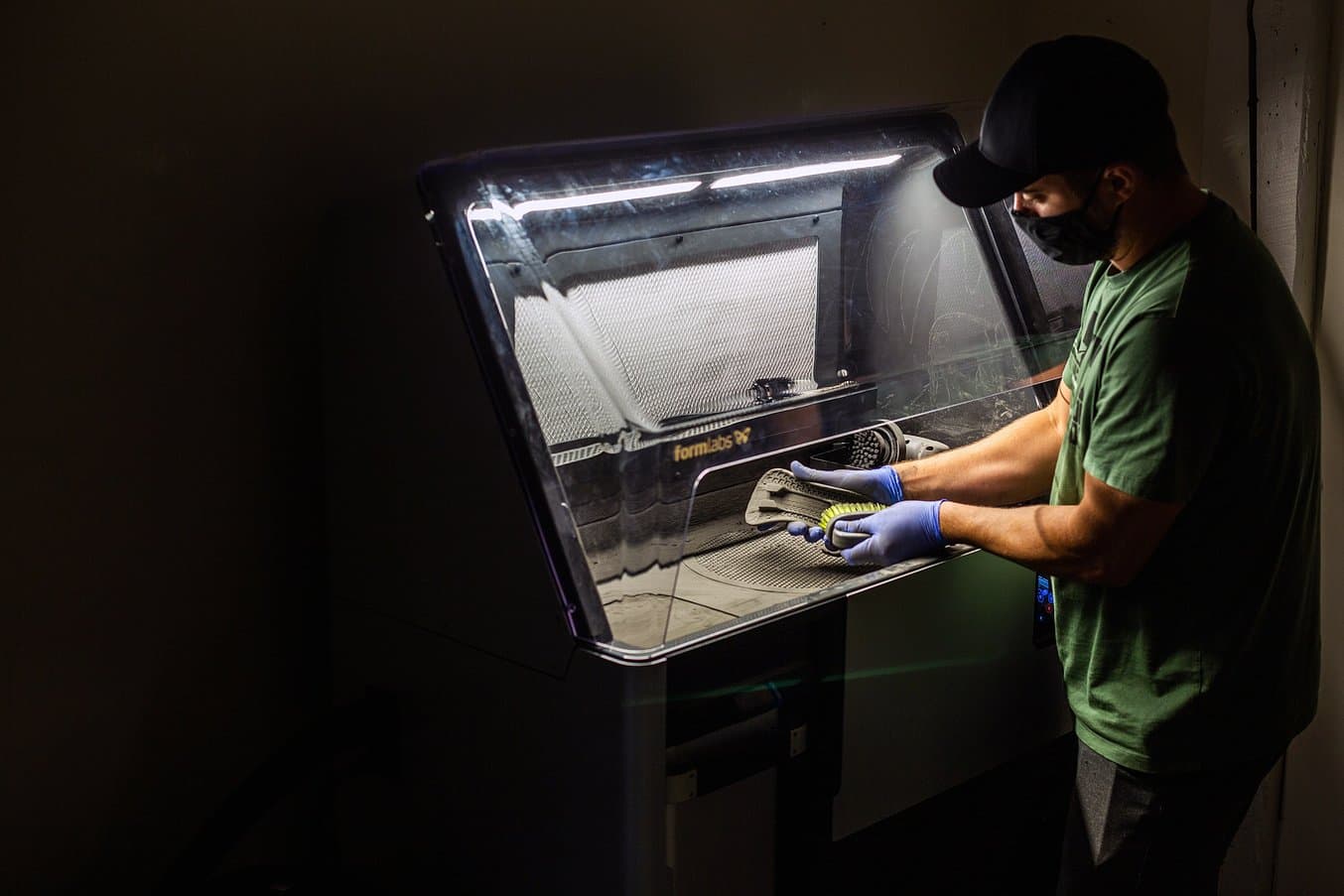
La Fuse Sift optimise le processus de post-traitement et de recyclage des poudres, libérant ainsi le temps de M. Frappier pour des tâches de conception qui demandent plus d'efforts.
Outre la sculpture sur argile, l'équipe a commandé des pièces imprimées en 3D de l'autre côté de la frontière, à Montréal. Bien que le coût ne soit pas exorbitant, les délais de production ont eu un impact sur leur capacité à concevoir à la vitesse souhaitée. « Nous étions en compétition avec d'autres entreprises, de sorte que la vitesse à laquelle nous développions nos produits dépendait de la date à laquelle nous pouvions obtenir des pièces », explique M. Frappier.
Pour de petites entreprises comme Rome Snowboards, connue pour ses fixations hautement personnalisables, les retards de développement peuvent avoir de lourdes conséquences et les désavantager par rapport à la concurrence. Leur force réside dans leur capacité à itérer, à obtenir rapidement des approbations internes et à créer des produits uniques dans le secteur, comme leurs technologies brevetées AuxTech, PivotMount et AsymWrap.
« Nous n'avons la Fuse 1 que depuis six mois environ, mais nous avons tout de suite compris l'intérêt de l'avoir en interne. Nous avons travaillé sur les boucles pendant environ six mois. Nous imprimions une boucle, l'assemblions, puis vérifiions son fonctionnement pour détecter les problèmes et les interférences. Cela nous a été très utile de pouvoir utiliser l'imprimante, imprimer une pièce, puis l'assembler le lendemain matin, la vérifier et la réitérer le jour suivant », explique M. Frappier.
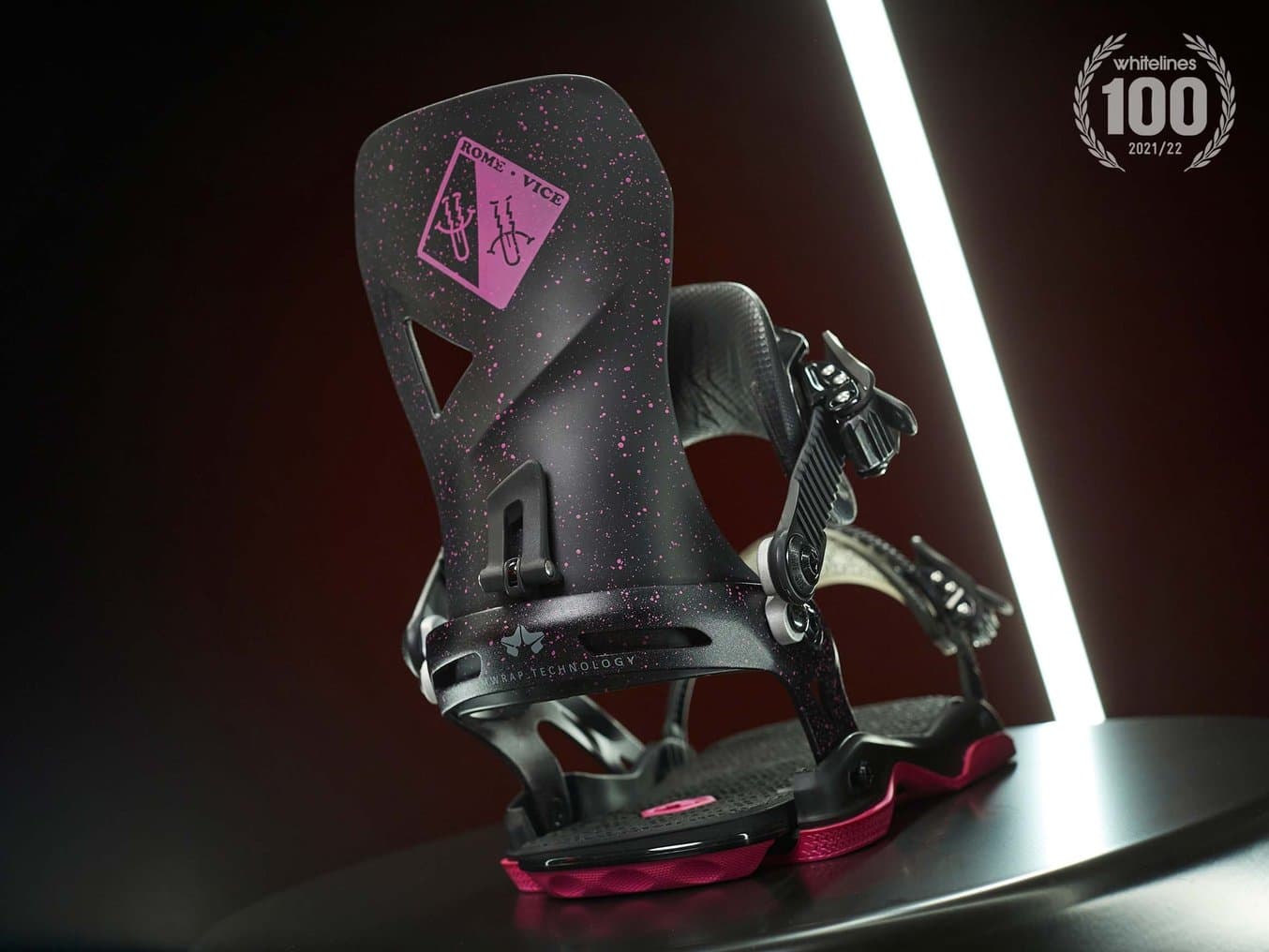
La fixation primée Vice, photographiée ici dans la revue White Lines. Photo courtoisie de White Lines.
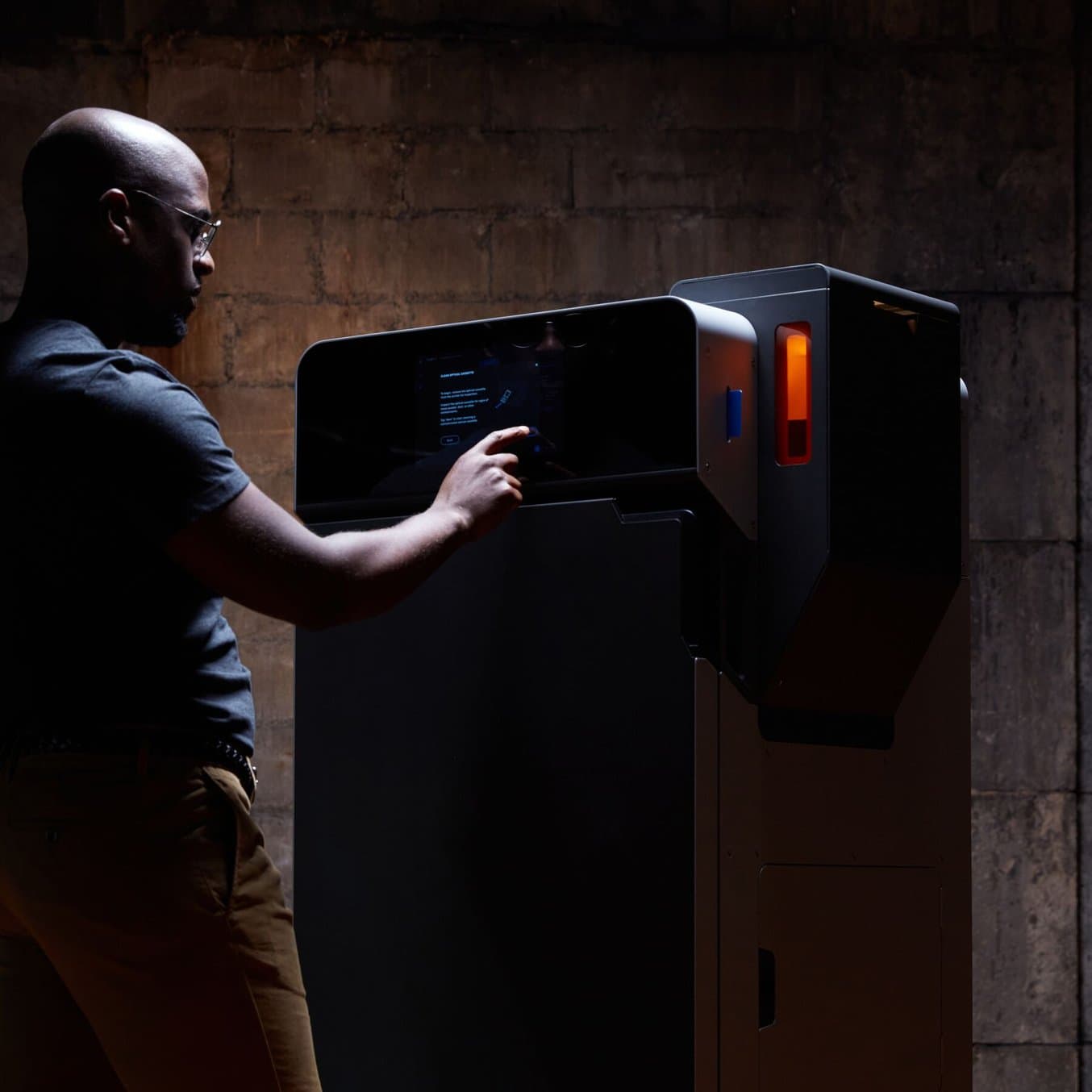
Externalisation ou internalisation : quand est-il judicieux d'adopter l'impression 3D SLS en interne ?
Dans ce livre blanc, nous passons en revue les avantages de l'adoption en interne des imprimantes 3D à frittage sélectif par laser (SLS) par rapport à la sous-traitance des pièces SLS auprès de fournisseurs de services.
Différents produits pour différents clients
Avec les produits Rome, les snowboarders peuvent personnaliser leurs fixations en ajustant plusieurs composants, ce qui leur permet de les adapter à leur poids et taille, à leur style de glisse et aux conditions du terrain. Cependant, la présence d'un aussi grand nombre de composants nécessite une conception plus complexe et des tolérances exactes afin que l'assemblage soit parfait. L'avis de White Lines indique que « l'arrière de la chaussure est construit à 100 % en nylon pour un niveau de flexibilité qui n'est heureusement pas trop rigide. N'importe quel glisseur pourra ainsi sauter sur le Vice et se sentir immédiatement à l'aise. »
Cette facilité d'utilisation est due au soin et au temps que l'équipe de Rome consacre à chaque étape de la fabrication. M. Frappier explique : « Nous essayons constamment de nous assurer que nos pièces sont parfaites et fiables. Même si nous avons plus de pièces et que l'assemblage est parfait, l'expérience client est excellente parce que la fixation a été conçue méticuleusement. L'impression 3D est idéale car elle nous permet d'affiner chaque pièce et de nous assurer qu'elle fonctionne parfaitement dans l'assemblage. »
Faible encombrement, grosse productivité
De nombreuses entreprises peuvent obtenir des conceptions de cette qualité en employant d'immenses équipes de concepteurs qui coopèrent entre elles. Rome n'a que deux concepteurs, ce qui leur donne plus agilité, mais peut rendre le travail plus intense. La Fuse 1 travaille à leurs côtés et permet d'imprimer toute la journée lorsque l'équipe en a besoin. Elle a été un argument de vente majeur lors de la recherche de sponsors. Sa taille et son prix accessibles en font une solution facile à intégrer, même pour les entreprises qui ne disposent pas de grands locaux ou d'un personnel nombreux.
Nous sommes une petite entreprise si on nous compare à d'autres fabricants de fixations. Nous ne sommes que huit à dix personnes dans le bureau de Waterbury, et le fait de disposer d'une installation complète d'impression 3D est tout simplement incroyable. Beaucoup de gens pensent que nous sommes une plus grande entreprise. C'est ce qu'il y a de bien avec la Fuse 1 : beaucoup de petites entreprises peuvent se l'offrir.
Justin Frappier, concepteur de produits chez Rome Snowboards
M. Frappier nous dit que lorsque les athlètes et les distributeurs d'équipement viennent visiter le bureau de Waterbury, leur réaction à la Fuse 1 est toujours extrêmement positive. « Lorsque les gens voient l'imprimante, ils sont époustouflés. Nous sommes en mesure de prendre des modèles et de leur montrer une pièce immédiatement, qu'il s'agisse d'athlètes ou de représentants de distributeurs d'équipement. Nous pouvons ainsi obtenir leur avis sur une pièce avant de l'envoyer à l'outillage », explique M. Frappier.
Des prototypes fonctionnels de plus en plus rapides
La ligne de produits 2022 de Rome ne sera pas produite en masse par impression 3D, mais cela n'a pas empêché l'équipe de réaliser des tests de validation finale très réalistes. Au cours de la première saison hivernale qui a suivi l'acquisition de l'imprimante, l'équipe de conception a décidé de procéder à des essais très fonctionnels. Ils voulaient pousser les prototypes jusqu'à leurs limites pour s'assurer que chaque boucle et chaque assemblage résiste aux conditions prévues et que toutes les pièces envoyées aux fabricants sont parfaites.
« Nous ne voulons pas perdre de temps et nous rendre compte trop tard que l'outillage utilisé n'est pas le bon. Cela nous rend plus efficaces », explique-t-il.
M. Frappier et ses collègues ont utilisé des fixations entièrement imprimées en 3D (à l'exception de quelques vis métalliques) dans les montagnes du Vermont, et ont augmenté leur vitesse à chaque descente. En testant la flexion, la résistance et la durabilité des fixations en montagne, M. Frappier peut réduire de plusieurs semaines le temps de développement habituel. Leur succès en tant que marque dépend de cet esprit d'innovation, et le moyen le plus sûr de tuer la créativité est que les équipes doivent attendre pendant des semaines des pièces provenant de fournisseurs extérieurs.
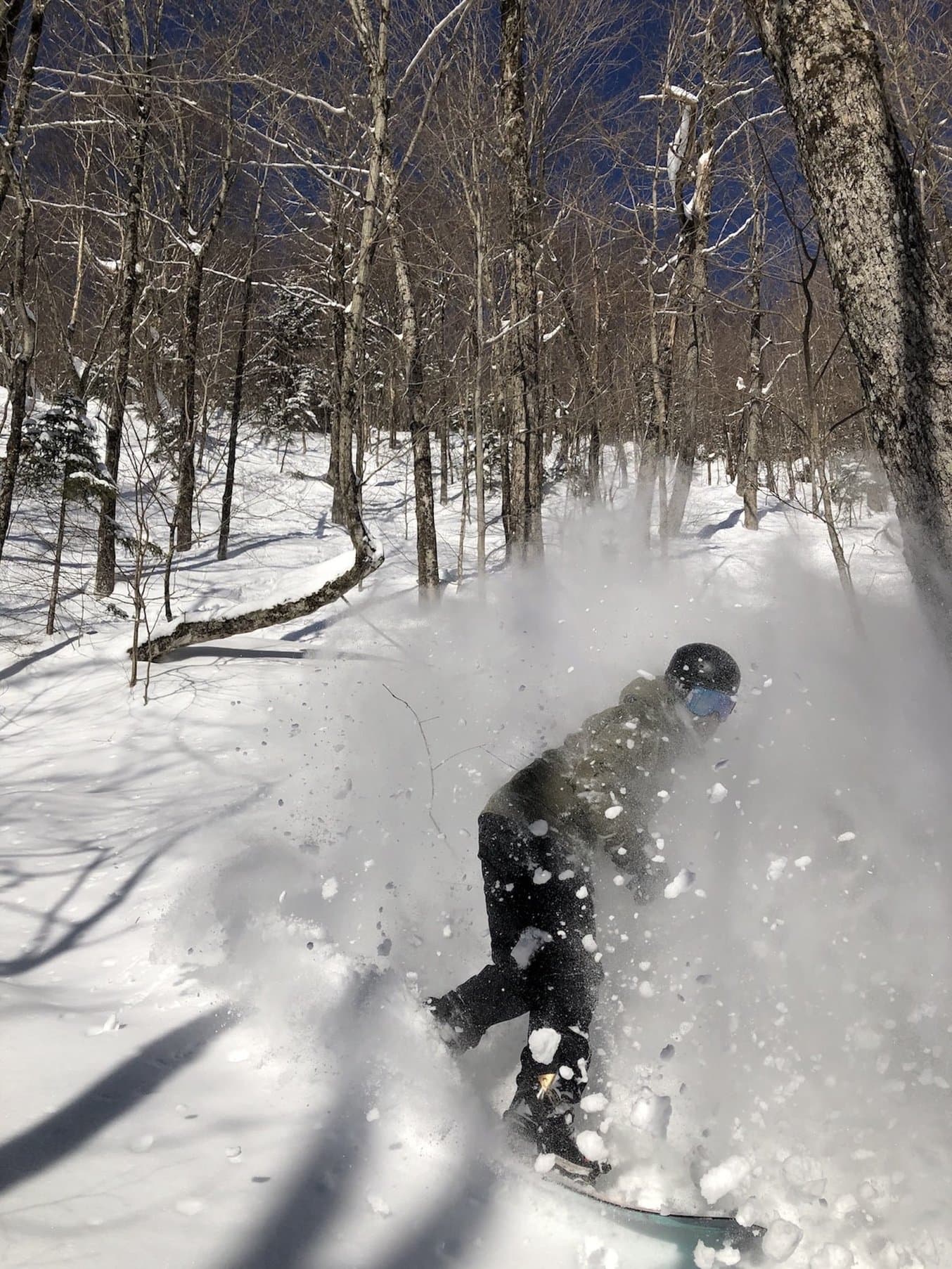
Le principal argument de vente était que nous pouvions directement utiliser les pièces imprimées. Nous n'avons jamais pu le faire avec d'autres pièces. La première fois, nous avons travaillé sur la plaque de base et les composants du châssis. Chaque itération était meilleure que la précédente. Désormais, nous pouvons imprimer, tester, et réimprimer le lendemain.
Justin Frappier, concepteur de produits chez Rome Snowboards
En donnant à son équipe de conception un contrôle total sur l'ensemble du processus de création, de test et d'itération, Rome Snowboards a pu continuer à repousser les limites de ce qui est possible en matière d'équipement de snowboard.
« Nous sommes à la pointe du secteur dans toutes les catégories. Nous essayons toujours de faire quelque chose qui n'a jamais été fait auparavant, et nous ne faisons que nous améliorer. Avec l'accélération du prototypage, nous constatons déjà un retour sur investissement positif après cinq mois à peine. », nous dit M. Frappier.
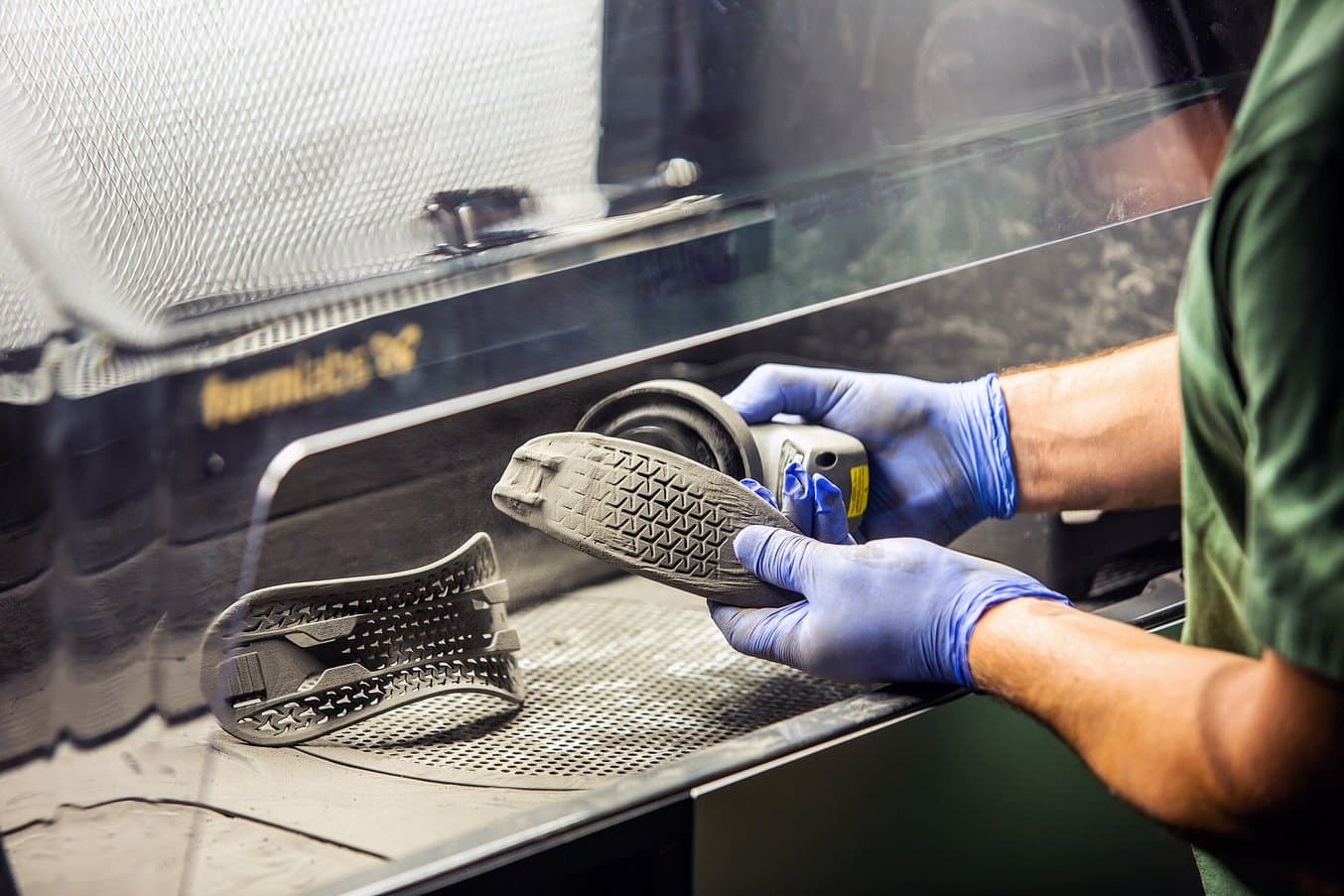
L'élimination et le recyclage de la poudre non frittée sont rendus faciles grâce au flux de travail autonome et optimisé de la Fuse Sift.
Les imprimantes de la série Fuse permettent aux concepteurs de tester le fonctionnement de leurs produits et de les faire évoluer sans avoir à attendre les pièces des fournisseurs. Pour Rome Snowboards, la Fuse 1 a considérablement accéléré le processus de développement et a permis à M. Frappier de faire glisser ses clients sur des fixations imprimées en 3D. Pour savoir si la Fuse 1 peut faire la même chose pour vos produits, commandez un échantillon ou lisez notre livre blanc comparant les pièces imprimées SLS en interne à celles imprimées par un prestataire de services.