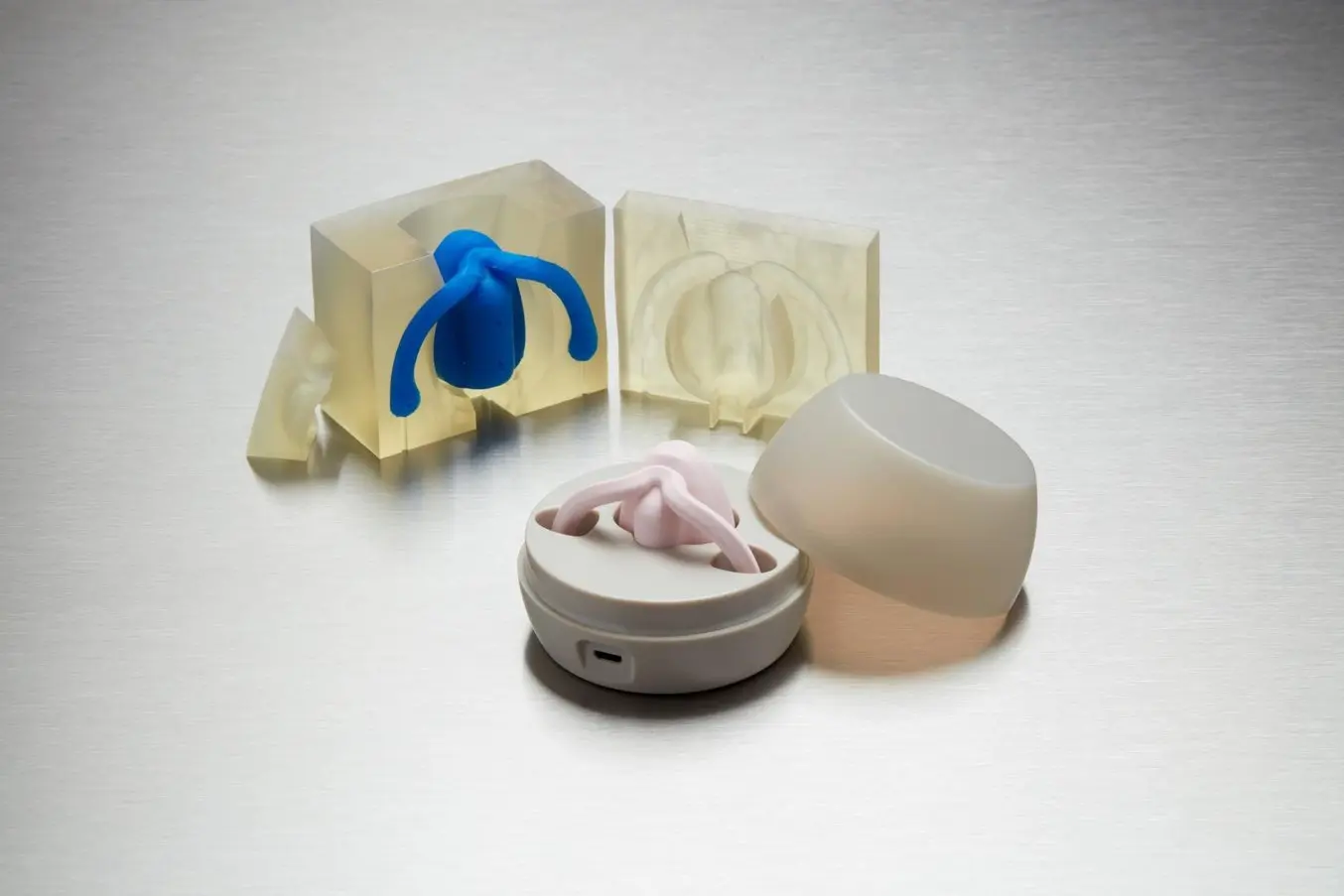
Le surmoulage et le moulage par insertion ont souvent tendance à être confondus l’un avec l’autre. Ce qui est compréhensible, puisque ces deux processus sont des types de moulage par injection utilisés pour créer des pièces structurellement similaires. Mais si on y regarde de plus près, on se rend compte que le moulage par insertion et le surmoulage sont bien distincts l’un de l’autre et que chaque technique a ses avantages propres.
De l’intégration d’éléments électroniques à l’amélioration de la prise en main des outils du quotidien, le surmoulage et le moulage par insertion offrent une foule d’avantages, mais on ne peut les exploiter que si l’on comprend bien ce qui singularise ces deux méthodes de fabrication.
Dans cet article, vous découvrirez :
-
Les bases du surmoulage et du moulage par insertion
-
Comment déterminer quelle méthode de fabrication utiliser et quand
-
Les applications les plus répandues du surmoulage et du moulage par insertion
-
Comment utiliser ces processus pour le prototypage
-
Comment réaliser des prototypes moulés par insertion avec des moules imprimés en 3D
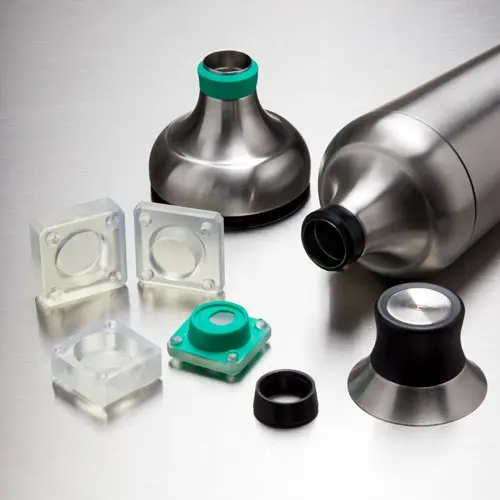
Moulage en silicone pour la conception de produits
Téléchargez ce rapport pour découvrir les études de cas des entreprises OXO, Tinta Crayons et Dame Products, qui illustrent trois mises en œuvre différentes du moulage en silicone pour la conception et la fabrication de produits, dont le surmoulage et le moulage d’insert.
Qu’est-ce que le surmoulage ?
Le surmoulage est un processus de moulage par injection en plusieurs étapes au cours duquel deux ou plusieurs composants sont moulés l’un sur l’autre. Le surmoulage est parfois appelé le moulage bi-matière car c’est un processus en deux étapes.
Premièrement, un composant de base (aussi appelé le substrat) est moulé et polymérisé. Les substrats surmoulés sont souvent faits en plastique. Ensuite, une deuxième couche est moulée directement sur la première afin de créer une pièce unitaire solide. Le surmoulage est fréquemment utilisé pour fabriquer des pièces en plastique présentant une poignée en caoutchouc. Le processus de surmoulage en deux temps d’une brosse à dents, par exemple, consiste à former une couche de base pour le manche en plastique, puis une couche superficielle de caoutchouc (pour améliorer la prise en main de la brosse à dents).
Matériaux fréquemment utilisés en surmoulage
Une large gamme de matériaux se prête au surmoulage, dont :
-
Acrylonitrile butadiène styrène (ABS)
-
Polyéthylène haute densité (PEHD)
-
Polyétheréthercétone (PEEK)
-
Nylon (Polyamide)
-
Polycarbonate (PC)
-
Polyéthylène (PE)
-
Polyétherimide (PEI)
-
Polytéréphtalate de buthylène (PBT)
-
Acrylique (PMMA)
-
Polyoxyméthylène (POM)
-
Polypropylène (PP)
-
Silicone (SI)
-
Élastomères thermoplastiques (TPE)
-
Polyuréthane thermoplastique (TPU)
-
Caoutchouc thermoplastique (TPR)
Avantages et limites du surmoulage
Le surmoulage offre de nombreux avantages. Il permet de fabriquer relativement facilement des produits composés de plusieurs matériaux et/ou couleurs. Le surmoulage nécessite aussi moins de main-d’œuvre (il est donc moins onéreux) comparé aux autres méthodes de fabrication où une pièce devrait être transférée dans un tout autre moule une machine. Le surmoulage réduit le besoin d’assemblage des produits car les pièces sont fabriquées directement l’une par-dessus l’autre, ce qui leur confère une durabilité globalement supérieure.
Le surmoulage est souvent la meilleure méthode de fabrication pour les productions en grande série et/ou les produits présentant de multiples couleurs et matériaux, mais cette technique comporte aussi quelques limites qu’il faut garder à l’esprit. À l’instar du moulage par injection, le surmoulage présente un coût d’équipement excessif. Fabriquer et modifier l’outillage métallique prend du temps et coûte très cher, et les machines d’injection bi-matière sont complexes à programmer. Cela signifie qu’il faut produire un grand nombre de pièces pour lisser ces coûts.
Conseil de pro : Imprimer en 3D des pièces ou des moules de surmoulage peut vous faire gagner du temps et vous éviter des coûts lors de la phase de prototypage.
Qu’est-ce que le moulage par insertion ?
Le moulage par insertion est une autre forme de moulage par injection lors de laquelle une pièce secondaire est formée par-dessus un substrat. La grande différence entre le moulage par insertion et le surmoulage, c’est que le moulage par insertion est réalisé avec un substrat préexistant (une base ou un composant interne). Une pièce préfabriquée (souvent produite dans un tout autre site ou fournie par une entreprise tierce) est insérée dans un moule, puis une couche secondaire est appliquée sur cet insert.
Le moulage par insertion est souvent utilisé pour ajouter une couche plastique sur un élément métallique, par exemple pour ajouter un manche en plastique à un tournevis en métal. On peut aussi utiliser le moulage par insertion pour fabriquer des tuyaux et des câbles isolés et autres produits semblables, ou pour intégrer des circuits électroniques dans des éléments en plastique.
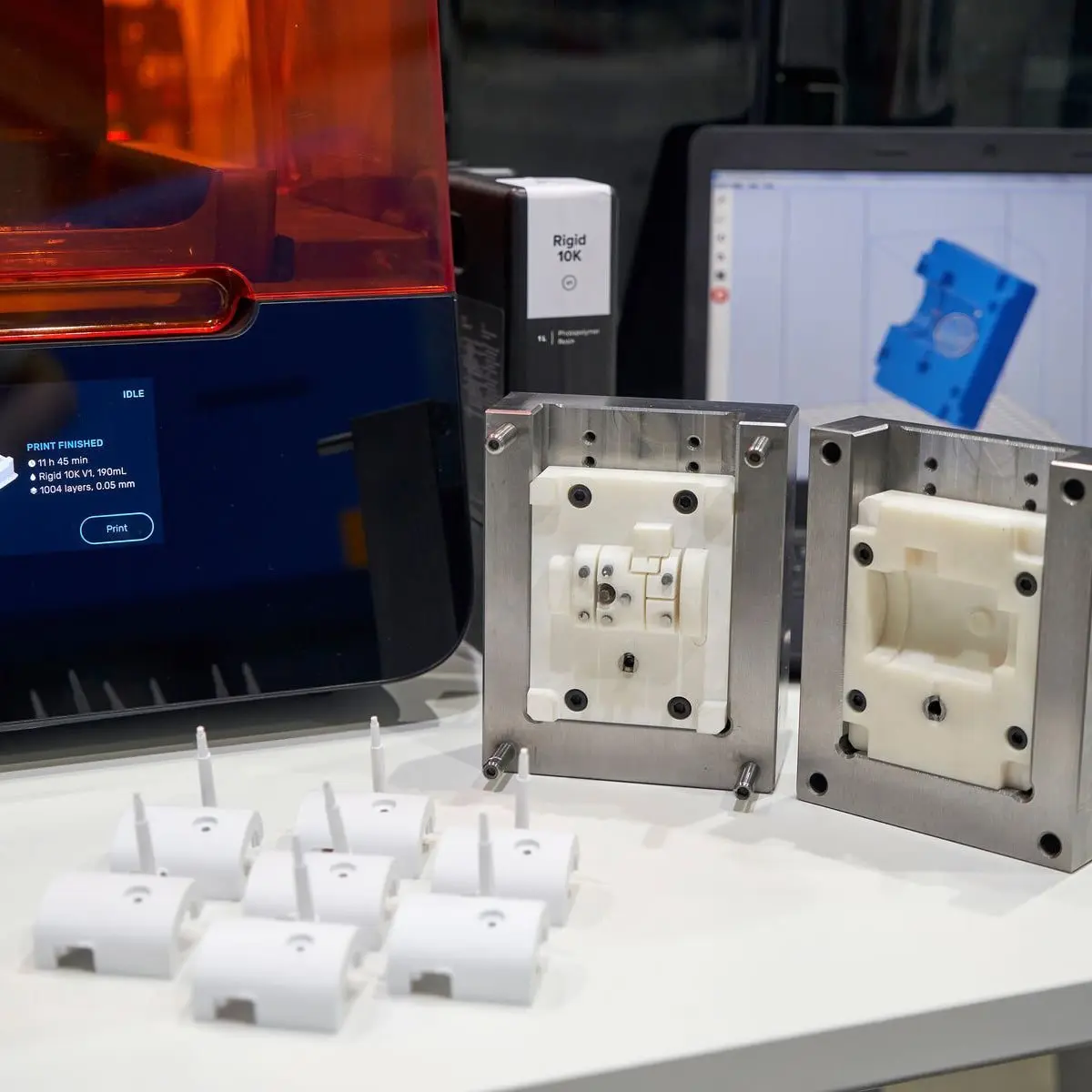
Le moulage par injection rapide de petites séries avec des moules imprimés en 3D
Téléchargez ce livre blanc pour savoir comment utiliser des moules imprimés en 3D pour le processus de moulage par injection, et ainsi réduire les coûts et les délais de production. Vous y trouverez des études de cas réels, réalisées chez Braskem, Holimaker et Novus Applications.
Matériaux fréquemment utilisés en moulage par insertion
Les mêmes thermoplastiques que ceux repris dans la liste concernant le surmoulage à la section précédente peuvent être utilisés pour former la couche extérieure ou superficielle du moulage par insertion.
Avantages et limites du moulage par insertion
Le moulage par insertion est utilisé pour créer des pièces robustes ne nécessitant pas d’assemblage, au même titre que le surmoulage, mais le moulage par insertion permet de le faire à l’aide d’une plus grande variété de matériaux. Par exemple, on peut placer des puces ou des câbles informatiques dans une gaine ou un boîtier plastique de protection. Mais l’avantage le plus impressionnant du moulage par insertion est peut-être le fait qu’il permet de créer des boîtiers plastiques (stérilisables) pour des dispositifs et implants médicaux qui sauvent des vies.
Cependant, le moulage par insertion présente des limites similaires à celles du surmoulage. Le prototypage peut devenir compliqué si l’on n’utilise pas d’imprimante 3D résine pour les séries de test. L’outillage doit aussi être réalisé de manière très précise car le substrat doit souvent être suspendu à l’intérieur du moule pour former le produit final.
Comment savoir si le surmoulage ou le moulage par insertion convient mieux à votre projet ?
Utilisez ce tableau pour déterminer quel procédé de fabrication se prête le mieux à votre projet :
Choisissez le surmoulage si :
-
La pièce finie peut être faite de thermoplastique et/ou de caoutchouc.
-
Le modèle fini consiste en plusieurs couches, matériaux (dans les limites de ceux repris plus haut) et/ou couleurs différents.
-
Vous fabriquerez à la fois le substrat et la couche secondaire.
-
La pièce finale n’a pas besoin d’être démontée ou désassemblée.
Choisissez le moulage par insertion si :
-
Vous utilisez un substrat préfabriqué.
-
Ce substrat est fait de métal, de câbles ou de pièces informatiques.
-
Vous souhaitez que la pièce finie soit monobloc.
Des pionniers adaptent constamment les méthodes de fabrication, donc il existe des exceptions à ces règles, mais le tableau ci-dessus est un très bon point de départ pour décider quel procédé utiliser. Gardez à l’esprit que ces deux méthodes de fabrication peuvent aussi être utilisées ensemble.
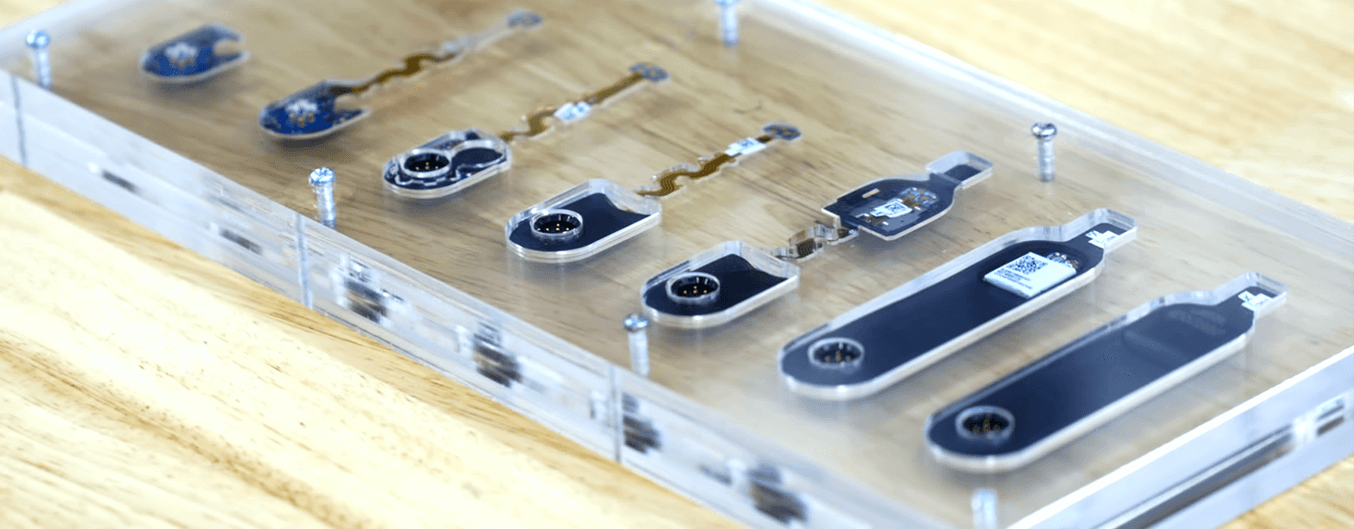
L’équipe ATAP de Google a produit un dispositif portable grâce à une combinaison de surmoulage et de moulage par insertion. Le dispositif portable est à la base un circuit imprimé rempli de composants. Ce circuit imprimé est encapsulé dans un système de moulage à basse pression qui le transforme en un bloc de plastique. Ce circuit imprimé et un câble flexible forment le sous-ensemble électronique qui est ensuite surmoulé dans un hybride d’uréthane thermoplastique (TPU) et de caoutchouc silicone. L’ensemble du circuit imprimé subit ensuite l’étape finale de surmoulage.
Applications du surmoulage et du moulage par insertion
Les fabricants utilisent le surmoulage et le moulage par insertion pour réaliser des produits à destination d’une grande diversité de secteurs. Voici quelques exemples de produits qui sont fréquemment fabriqués par l’un ou l’autre procédé, voire une combinaison des deux :
Produits de consommation
Quand vous êtes chez vous, regardez autour de vous et vous trouverez certainement plus d’un objet en plastique fait d’une seule pièce mais présentant des couleurs multiples. Vous pouvez être sûr que la plupart de ces objets ont été fabriqués par surmoulage. Ce procédé de fabrication répandu est utilisé pour tout fabriquer, des quilles de bowling aux pièces de jouets pour enfants en passant par les bacs de stockage et les conteneurs en plastique.
Les brosses à dents, les coques de téléphone portable et les clés USB sont souvent produites par surmoulage et/ou moulage par insertion. Le surmoulage est utilisé pour réaliser toute une variété de meubles en plastique bicolores tels que des escabeaux ou des chaises de jardin. Les boîtiers en plastique pour modules GPS et dispositifs de navigation sont, eux aussi, souvent fabriqués par surmoulage et moulage par insertion.
Industrie automobile
Les capteurs électriques, engrenages, fixations et autres pièces automobiles combinant des matériaux métalliques et plastiques ou du caoutchouc sont fréquemment fabriqués à l’aide du moulage par insertion. Le surmoulage, pour sa part, sert à créer des composants intérieurs bicolores robustes tels que des panneaux de portière et de tableau de bord, des poignées, des boutons et différents dispositifs de contrôle. Certains moteurs et batteries subissent aussi un procédé de moulage par insertion.
Secteur médical
L’industrie médicale fait un usage intensif de pièces surmoulées et moulées par insertion car les plastiques sont plus faciles à stériliser que des composants électriques ou informatiques. Les défibrillateurs, les câbles et les branchements médicaux sont souvent encapsulés dans du plastique après moulage par insertion, à la fois pour protéger les composants internes fragiles et pour rendre le dispositif final plus facile à nettoyer.
Les dispositifs médicaux tels que les pacemakers conçus pour être implantés dans le corps humain sont généralement fabriqués par moulage par insertion. Les usines recourent également au moulage par insertion pour produire toute une variété d’équipements vidéo utilisés en imagerie interne, tels que les caméras d’endoscopie et de colonoscopie.
Industrie électrique
Les câbles électriques sont rendus plus sûrs, et dans certains cas, imperméables à l’eau en leur ajoutant une gaine de caoutchouc par moulage par insertion. Les fabricants recouvrent souvent les composants de câblage avec du caoutchouc pour rendre les produits tels que les chargeurs de téléphone et d’ordinateur portable plus sûrs d’utilisation pour les consommateurs. Parfois, plusieurs câbles sont gainés dans la même couche de caoutchouc et d’autres fois, ces câbles sont séparés et différenciés par des couleurs contrastantes telles que le bleu et le rouge.
Industrie cosmétique
Le surmoulage et le moulage par insertion sont habituellement utilisés pour rendre l’emballage des produits cosmétiques plus attractif. Ces procédés permettent aux concepteurs de créer des emballages sur mesure présentant des textures de surface uniques et multicolores. Des produits tels que des poudriers, des pinceaux de maquillage et des flacons de parfum peuvent tous être fabriqués par surmoulage et/ou par moulage par insertion.
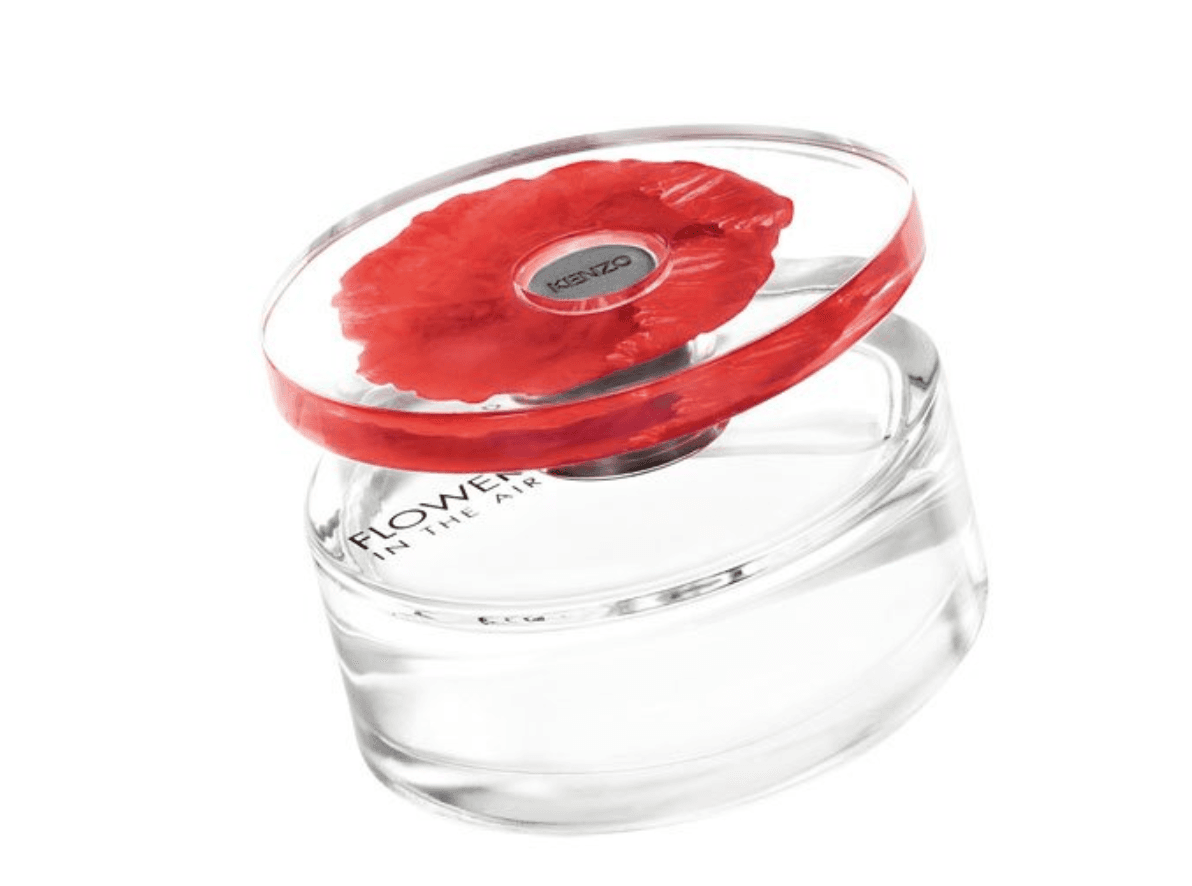
Flacon de parfum surmoulé créé pour Kenzo. (source de l’image)
Prototypage par surmoulage, moulage par insertion et impression 3D
Le prototypage est une partie cruciale du processus de développement de produits. Les concepteurs de produit et les ingénieurs ont besoin de tester les concepts et d’optimiser les éléments de conception qui n’ont encore jamais été utilisés. Mais l’inconvénient du prototypage, c’est qu’il peut très vite devenir très cher. Et si en plus, on dépend de sources externes pour la production des composants, il peut aussi prendre énormément de temps.
Certains des innovateurs les plus inspirés au monde surmontent ces difficultés de prototypage en combinant des procédés de fabrication tels que le surmoulage et le moulage par insertion avec l’impression 3D.
Des concepteurs du labo de projets et de technologie avancés de Google (ATAP) ont pu réduire les coûts de plus de 100 000 $ et réduire leur cycle de test de trois semaines à à peine trois jours en utilisant une combinaison d’impression 3D et de moulage par insertion. L’équipe Google ATAP a découvert qu’en imprimant en 3D des pièces de test plutôt que d’utiliser des pièces électroniques chères qui devaient être livrées par un fournisseur, elle a gagné du temps et de l’argent. Voilà juste une manière parmi d’autres dont les entreprises utilisent l’impression 3D en conjonction avec d’autres méthodes de fabrication.
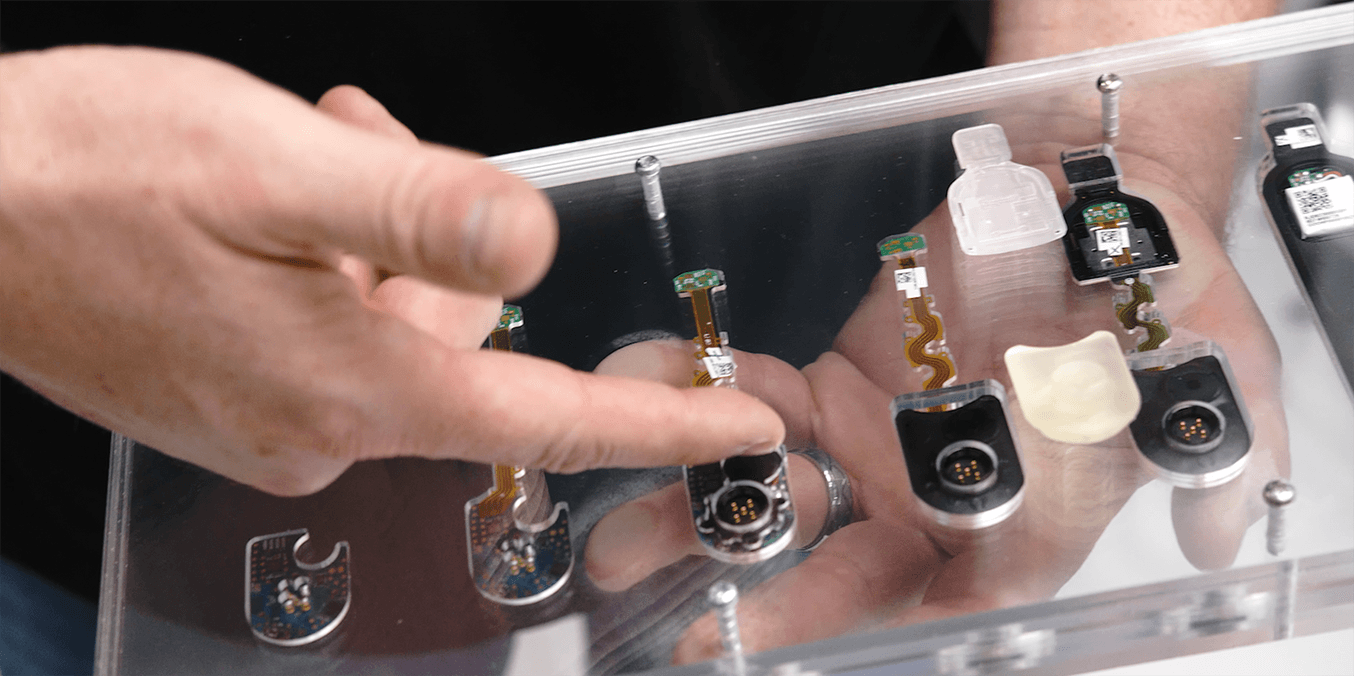
L’équipe ATAP de Google a utilisé des gabarits imprimés en 3D, ou des pièces de substitution, au lieu des circuits imprimés surmoulés pour le réglage initial de l’outillage en usine.
Dame Products est une start-up de Brooklyn qui conçoit des produits pour l’industrie de la santé et du bien-être. Ses employés utilisent le moulage par insertion de silicone pour encapsuler les composants internes de leurs prototypes bêta destinés aux clients. Les produits de la ligne réalisée par Dame Products présentent des géométries ergonomiques complexes, entièrement recouvertes d’un silicone aux couleurs vives sans risque pour la peau.
Les ingénieurs fabriquent des douzaines de prototypes surmoulés et moulés par insertion dans la journée en utilisant par roulements trois ou quatre moules imprimés par SLA. Pendant que le caoutchouc silicone d’un prototype est en phase de polymérisation, le suivant peut être démoulé et préparé pour le prochain remplissage. Les finitions et le nettoyage des prototypes démoulés se déroulent en parallèle. Quand un prototype est renvoyé à la société, l’appareil est désinfecté, la fine couche de silicone est retirée, et les composants internes sont réutilisés dans un nouveau prototype en version bêta.
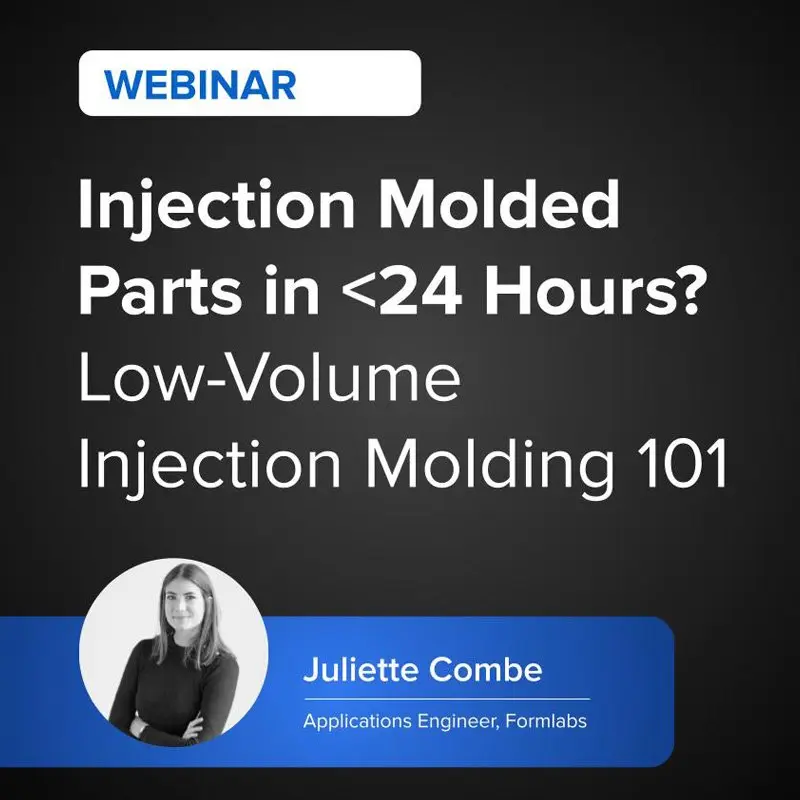
Des pièces moulées par injection en moins de 24 heures ? Le b.a.-ba du moulage par injection en petite série
Dans ce webinaire, nous vous montrerons comment des moules imprimés en 3D par stéréolithographie (SLA) peuvent être utilisés dans le processus de moulage par injection afin de réduire les coûts et les délais de fabrication et de lancer des produits plus qualitatifs sur le marché.
Guide étape par étape du moulage par insertion avec moules imprimés en 3D
Le guide d’instructions suivant peut être suivi pour encapsuler une pièce matérielle dans du silicone. Dans cet exemple, nous utilisons une combinaison d’impression 3D et de moulage par insertion.
Équipement et matériaux nécessaires :
-
Imprimante 3D SLA de Formlabs
-
Spatule et pince coupante Formlabs
-
Silicone liquide RTV en deux produits de qualité médicale : dureté Shore recommandée de 20 à 40 A
-
Seringues
-
Cartouche à époxy
-
Pistolet à époxy
-
Buse mélangeuse
-
Bâtonnets
-
Presses en C
-
Appareil à encapsuler (au choix)
Équipement et matériaux optionnels :
-
Colorant pour silicone
-
Vaseline
-
Source de vibrations
-
Ruban adhésif
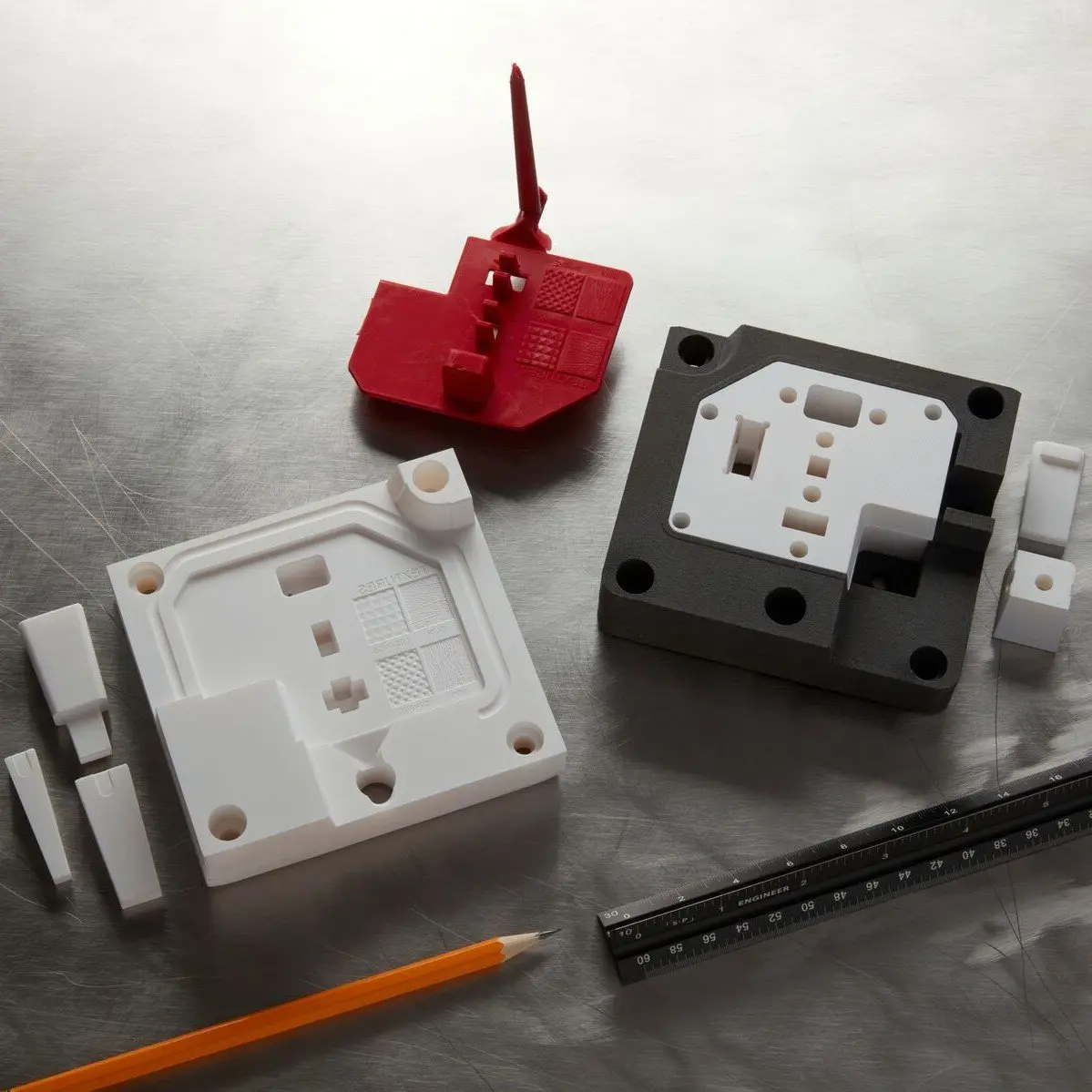
Guide de l'outillage rapide
Dans ce livre blanc, apprenez comment combiner l'outillage rapide imprimé en 3D avec des procédés de fabrication traditionnels tels que le moulage par injection, le formage sous vide ou la fonderie.
Méthode étape par étape :
1. Réalisez un moule pour plusieurs pièces avec Clear Resin de Formlabs : il est recommandé d'imprimer avec une épaisseur de couche de 50 μm. Orientez les pièces pour que les surfaces internes ne présentent aucune trace de support.
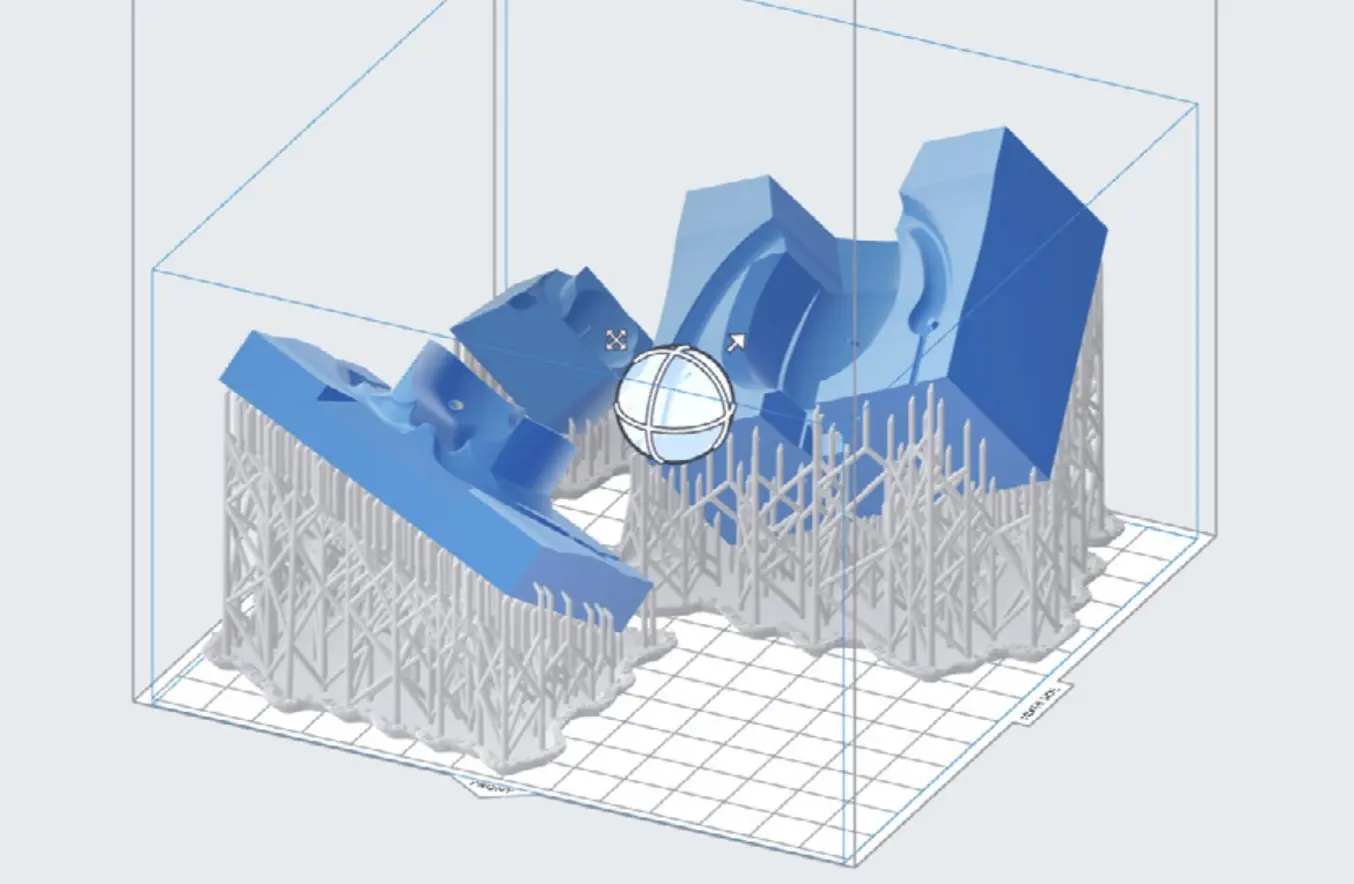
2. Lavez et post-polymérisez le moule, puis enlever les supports : Lavez minutieusement avec de l’alcool isopropylique jusqu’à ce que les pièces ne soient plus collantes. Une polymérisation à 60 °C pendant 15 minutes est recommandée pour Clear Resin. Polir l’extérieur du moule pour un fini parfaitement transparent peut être pratique.
3. Préparez le silicone au moins une heure avant le moulage de l'insert : Remplissez chaque côté de la cartouche à époxy avec un produit (A ou B), en utilisant une seringue différente pour chaque liquide. Maintenez-la en position verticale et laissez l’air s’échapper lentement pendant au moins une heure et au plus une journée. L’ajout de colorant est une étape optionnelle à effectuer ici. Le cas échéant, ajoutez le colorant au côté A ou B de la cartouche et mélangez minutieusement.
4. Appliquez le produit de démoulage (facultatif) : Appliquez une couche très fine de vaseline sur les surfaces internes du moule avec un petit pinceau. Cette technique de surmoulage en silicone fonctionne aussi sans agent démoulant.
5. Orientez l'appareil : Les chevilles d’alignement sur le moule sont là pour aider à ajuster l’appareil.
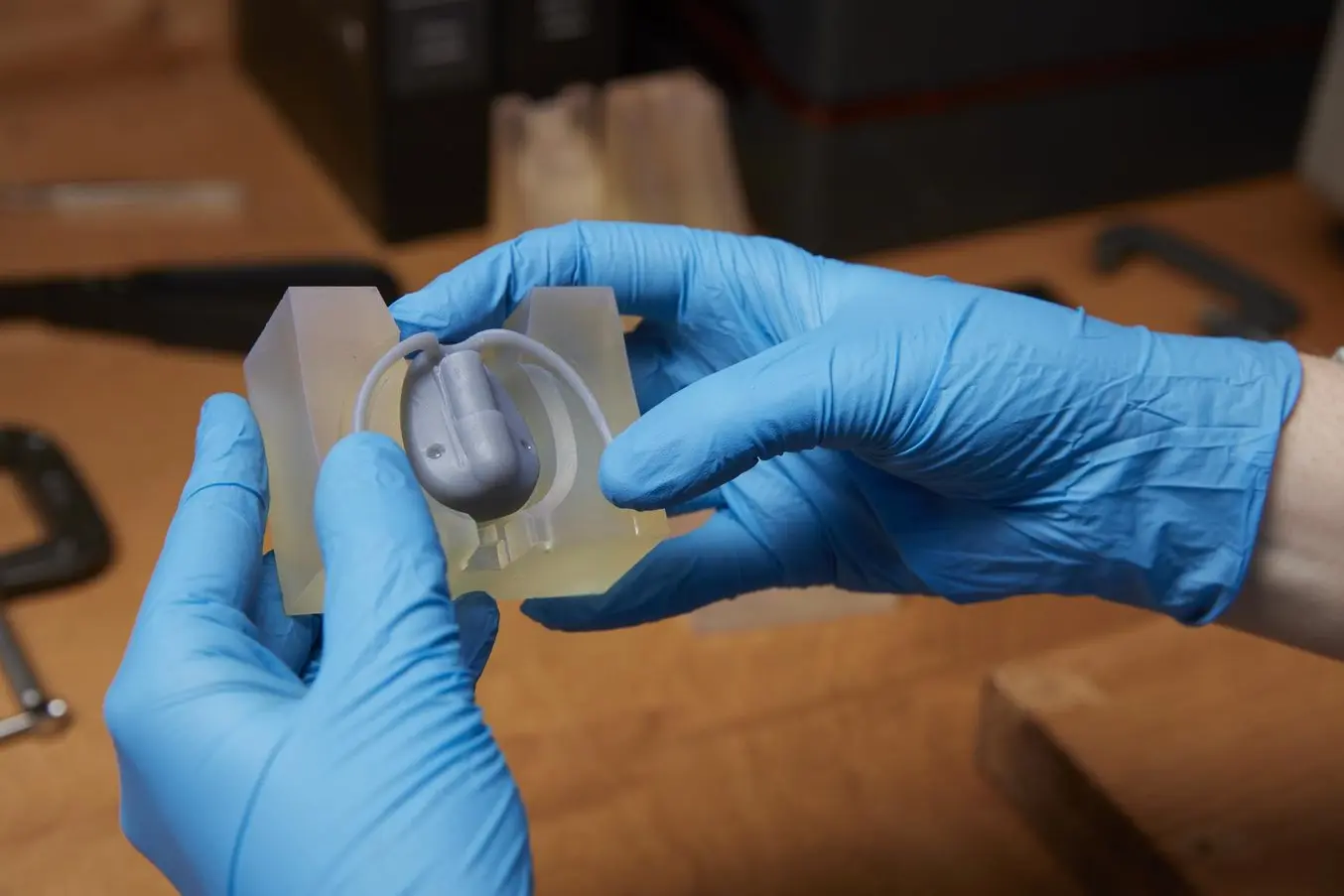
6. Fermez le moule et comprimez-le à la main : Vérifiez la position et l’alignement de l’appareil à travers l’extérieur du moule. S’il semble ne pas être aligné correctement, répétez les étapes cinq et six.
7. Serrez le moule : Commencez par un serrage dans « l’axe de dépouille », soit perpendiculaire à la ligne de jonction principale du moule. C’est un bon moment pour vérifier une nouvelle fois l’alignement, car le serrage peut avoir déplacé l’appareil interne. Sceller les bords du moule avec du ruban adhésif avant de le mettre sous presse contribue à réduire toute fuite de matériau et toute bavure qui pourrait se produire lors de la fabrication de moules par vulcanisation à température ambiante.
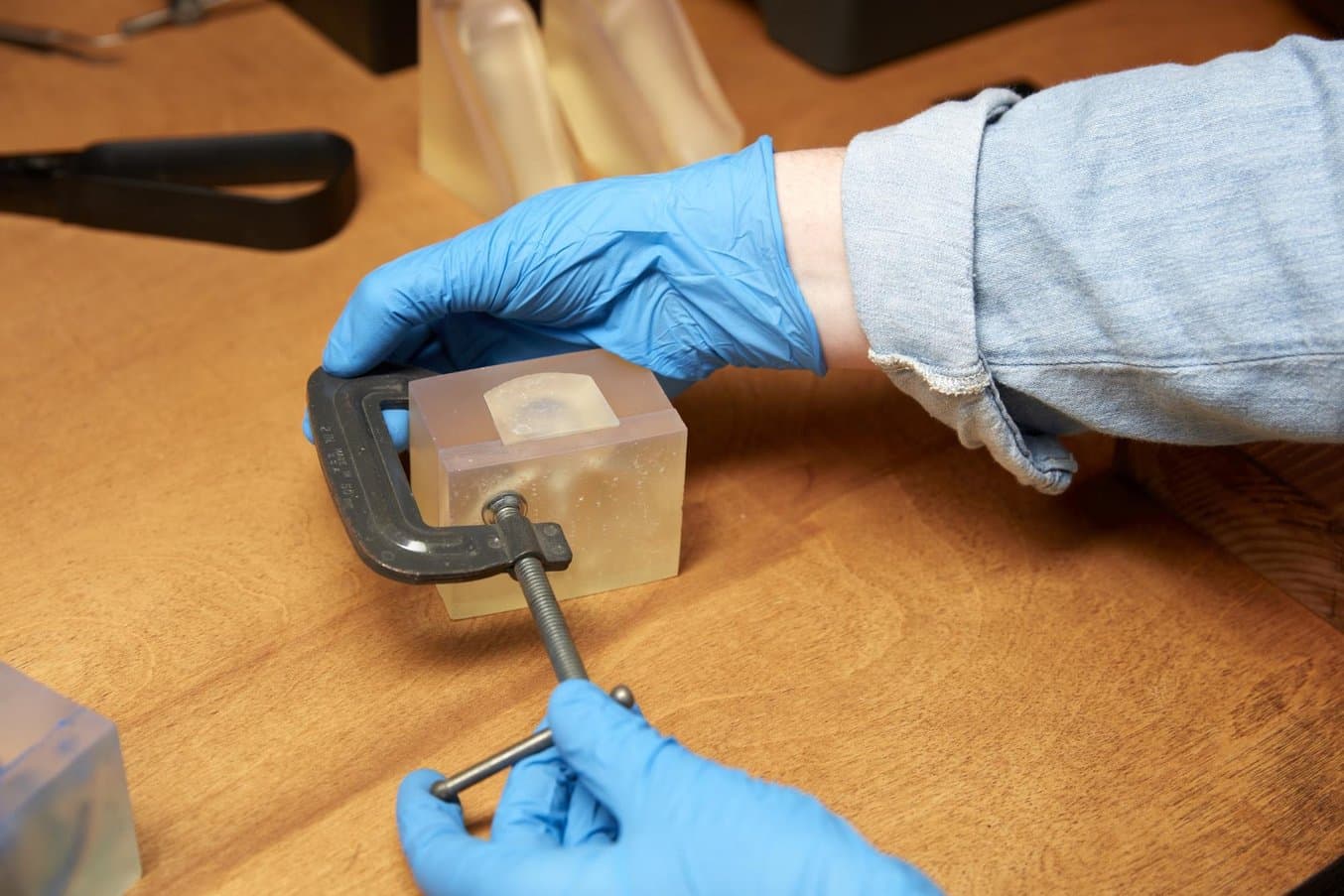
8. Assemblez le pistolet à époxy : Insérez les cartouches dans le pistolet et vissez la buse mélangeuse. Il est conseillé de faire couler un peu de liquide à ce stade pour vous assurer que le mélange se fait correctement.
9. Injectez le silicone dans le moule : Insérez l’embout de la buse mélangeuse dans l’ouverture du moule et appuyez doucement sur la gâchette. Regardez le silicone se répandre dans le moule, et continuez à pomper jusqu’à ce que le moule soit plein et que le silicone ressorte par tous les évents. Une fois que vous avez arrêté, le silicone peut continuer à descendre dans le moule à cause de la décantation des bulles d’air ou de l’écoulement du matériau sur les lignes de jonction. Vous devrez peut-être en rajouter un peu à plusieurs reprises après le remplissage initial. Après le remplissage, tenir un appareil vibrant (comme une ponceuse à main) contre la surface du moule peut encourager l’évacuation des bulles d’air.
10. Attendez que le silicone durcisse : Vérifiez la durée de polymérisation recommandée sur la notice de votre silicone. C’est le moment idéal pour commencer à ébavurer.
11. Démoulez le prototype Découpez d’abord tout le silicone en excès à l’extérieur du moule. Puis ouvrez le moule avec la spatule Formlabs ou un tournevis à tête plate. Faites attention aux minces fils de silicone qui se forment dans les évents du moule. Prenez le temps de les découper individuellement pour éviter qu’en restant fixés au moule, ils arrachent la coque en silicone de votre appareil. Il peut aussi être utile de découper une partie des bavures avant de libérer complètement l’objet.
12. Découpez, finissez et nettoyez le prototype: Il y aura toujours quelques bavures à découper avec la pince coupante Formlabs ou une lame acérée. Si des bulles d’air ont formé des creux à la surface, vous pouvez les colmater en repeignant avec du silicone liquide et en le laissant polymériser. Les prototypes doivent être nettoyés suivant les recommendations particulière du secteur avant d’être confiés à des testeurs.
Le moule peut être réutilisé plusieurs fois, mais vous devrez peut-être préalablement nettoyer les évents avec un objet pointu comme un trombone ou un foret.
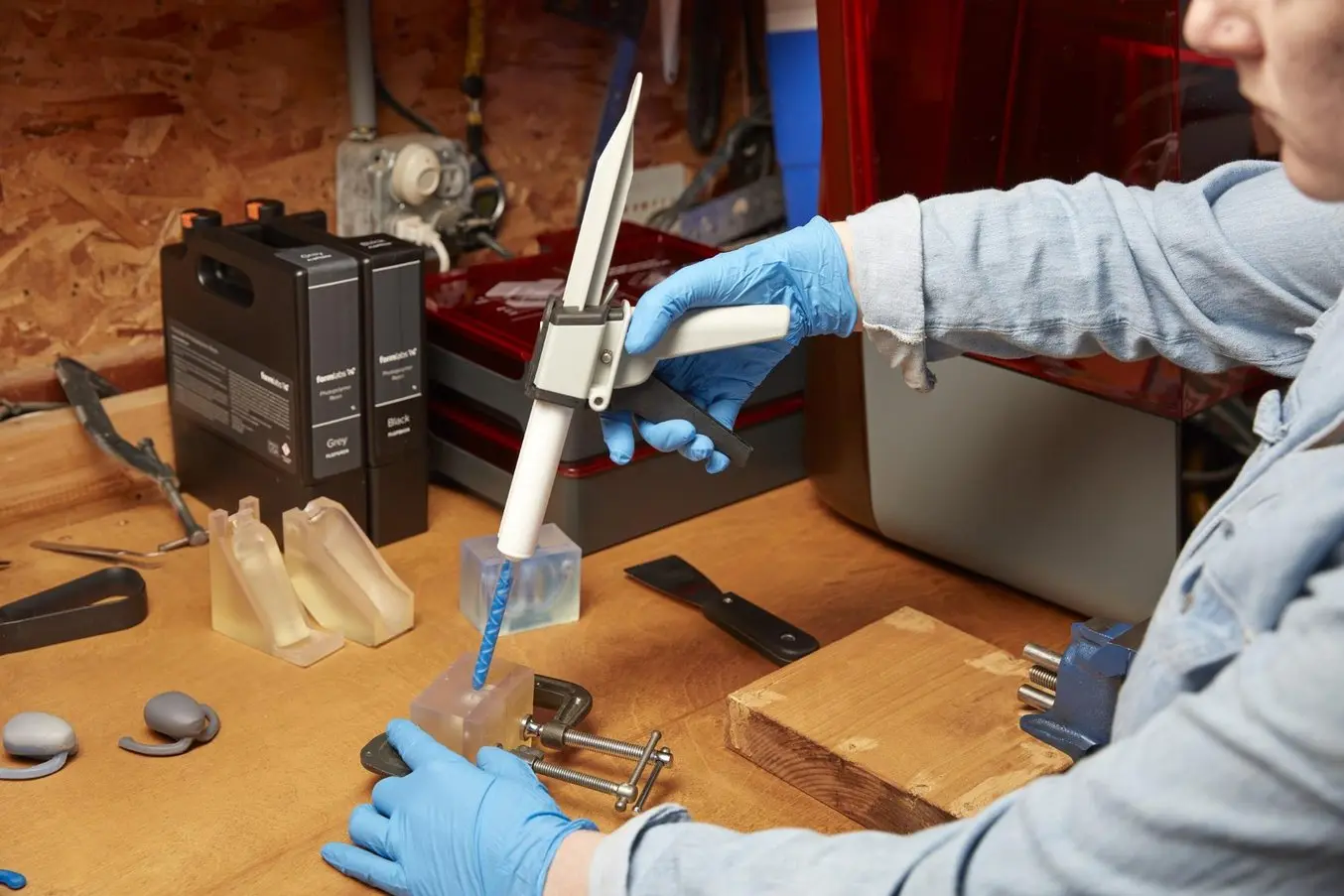
Obtenez plus de conseils et d’idées pour la fabrication et le prototypage
Vous souhaitez apprendre davantage de meilleures pratiques concernant le moulage ? Notre livre blanc,Moulage en silicone pour la conception de produits, offre d’autres recommandations et méthodes éprouvées pour le moulage en silicone, le moulage par insertion, le surmoulage et le moulage par compression.