Systèmes de refroidissement imprimés en 3D avec la résine High Temp (haute température)
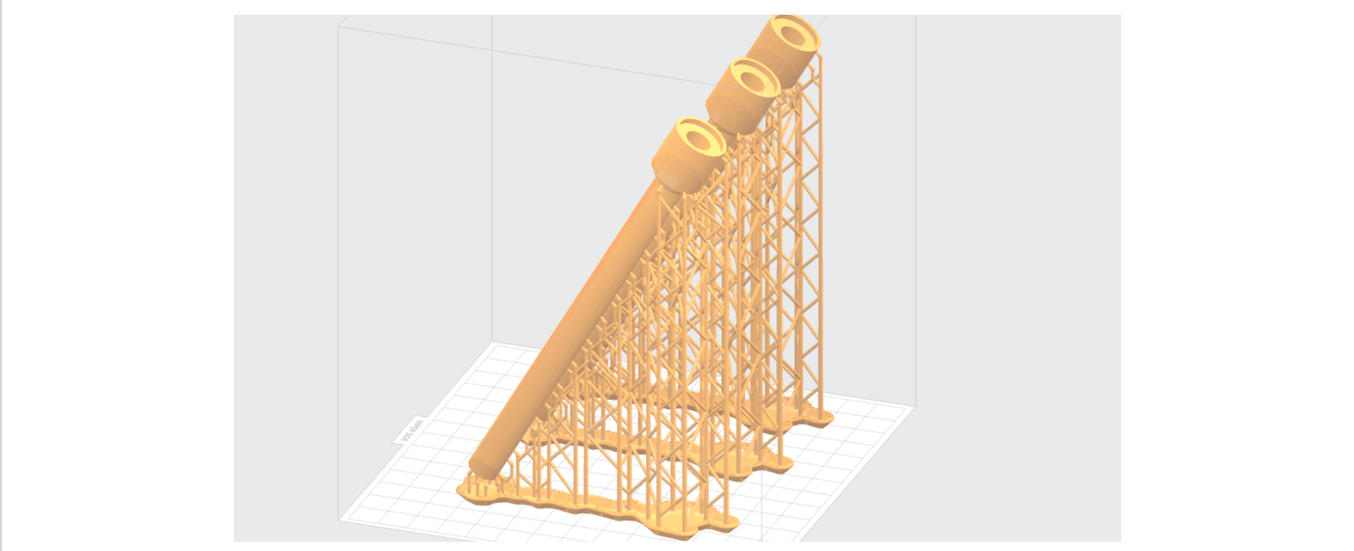
Introduction
Largement répandue pour la réalisation de prototypes dits “visuels”, la fabrication additive se démocratise de plus en plus pour la production de pièces entièrement fonctionnelles, voire de produits finis. En effet, avec la diversification des technologies d'impression 3D et des matériaux, il est désormais possible d'imprimer des pièces à la géométrie complexe disposant d'une variété de propriétés mécaniques, afin de répondre à bon nombre d'applications qui nécessitaient jusque là des pièces usinées.
Si le dépôt de fil fondu (FDM) est utilisé depuis de nombreuses années en prototypage rapide, l'émergence de nouveaux matériaux et technologies telle la stéréolithographie (SLA) permet de grandes avancées dans le prototypage fonctionnel. Le SLA offre notamment une large gamme matériaux haute performances aux propriétés mécaniques variées (résistance à la chaleur, aux chocs, flexibilité, biocompatibilité), ainsi que la fabrication de pièces haute précision entièrement isotropes, le tout sur des machines de bureau. Il est ainsi possible de développer en interne des pièces soumises à des contraintes importantes, tels que des systèmes de refroidissement.
Cet article est tiré du webinaire “Matériaux d'ingénierie pour la R&D industrielle : impression 3D de caloducs avec la résine High Temp”.
Il présente les travaux de Thomas Joffre, chef de projet recherche en fabrication additive au Centre Technique et Industriel de la Plasturgie et des Composites (CTIPC) et Valérie Sartre, maître de conférences à l'INSA et chercheuse au Centre de Thermique et d'Énergétique de Lyon (CETHIL) ainsi que de leurs collègues, sur la problématique des caloducs et leurs recherches sur la création de systèmes de refroidissement en polymères via la fabrication additive.
Visionner gratuitement le webinaire complet
Qu'est ce qu'un caloduc ?
Le terme caloduc (heat-pipe en anglais), du latin calor qui signifie “chaleur” et ductus qui signifie “conduite”, désigne un élément conducteur de chaleur utilisant un fluide qui change de phase (chaleur latente).
Fonction et fonctionnement d'un caloduc
Traditionnellement fabriqués en cuivre, ces dispositifs se présentent sous la forme d'un tube hermétique, vide d’air, dans lequel circule un fluide caloporteur (eau, éthanol, méthanol par exemple), permettant un transfert de chaleur particulièrement efficace grâce à une succession de cycles d’évaporation-condensation du fluide.
Le caloduc absorbe la chaleur à l'une de ses extrémités (évaporateur), où le liquide s'évapore et circule ensuite jusqu’à l'autre extrémité (condenseur), où il revient à l’état liquide. Le retour du liquide du condenseur vers l’évaporateur s’effectue sous l’effet des forces de gravité ou de capillarité, via une structure capillaire poreuse.
Les caloducs remplissent deux fonctions principales :
- Le transport de chaleur d'une source chaude vers une source froide (situées à chaque extrémité du caloduc) avec une faible différence de température. La partie évaporatrice peut être de très petite dimension, et permet ainsi l'extraction de fortes densités de flux thermiques dissipées dans des zones confinées.
- Homogénéisation de la température de surface par élimination des “points chauds”. Le caloduc peut diffuser la chaleur, dissipée par une source chaude de petite taille vers une source froide de plus grande taille, ce qui permet de réduire la température de la source chaude. Ou alors, appliqué sur une surface dont la distribution de températures est non homogène, le caloduc diffuse le flux thermique des zones chaudes vers les zones froides, ce qui réduit les gradients de températures néfastes dans certaines applications.
Différents types de caloducs
S'ils fonctionnent tous selon le même principe de base énoncé ci dessus, il existe différents types de caloducs qui diffèrent par leur forme, ou encore par les structures capillaires dont ils sont équipés à l'intérieur.
1.Caloduc tubulaire classique (cylindrical heat pipe) et thermosiphon :
Ce sont de simples tubes pourvus d'un condenseur à une extrémité et d'un évaporateur à l'autre. Le caloduc tubulaire classique est équipé d'une structure capillaire intérieure, qui va permettre de drainer le liquide vers l'évaporateur, tandis que le thermosiphon fonctionne par gravité, l'évaporateur se trouvant dans ce cas forcément en dessous du condenseur, pour permettre au liquide de s'écouler de l’évaporateur vers le condenseur.

→ Les caloducs tubulaires sont adaptés à la fonction de transport de chaleur sur de petites distances. De faible coût et de technologie bien maîtrisée, ils sont utilisés par exemple dans les échangeurs récupérateurs de chaleur des VMC, les ordinateurs portables, etc. | → Les thermosiphons, de fabrication plus simple, donc de coût plus bas, sont privilégiés lorsque la source chaude est localisée à une altitude inférieure à celle de la source froide quelles que soient les conditions de fonctionnement, car ils présentent de meilleures performances thermiques que les caloducs tubulaires. |
2.Chambre de vapeur / diffuseurs thermiques diphasiques (Flat plate heat pipe / vapor chamber)
Ce caloduc plat, généralement de forme parallélépipédique, a la particularité de transférer la chaleur de l'évaporateur vers un condenseur de plus grande taille. Les sources de chaleur peuvent être multiples. Le condenseur peut être localisé sur la même paroi que l’évaporateur, ou sur la paroi opposée, ou même aux extrémités.

→ Les caloducs plats sont adaptés à la fonction homogénéisation de température. Par exemple, ils sont actuellement insérés dans la base de certains radiateurs à ailettes destinés au refroidissement de puces électroniques : en diffusant la chaleur dissipée par la puce vers l’ensemble des ailettes, l’efficacité de la surface ailetée est ainsi améliorée. |
3.Boucle diphasique (Loop heat pipe)
Dans le cas des boucles diphasiques à pompage capillaire, la structure capillaire est localisée uniquement dans l'évaporateur et le liquide et la vapeur circulent dans des conduites séparées.

→ Ce type de caloduc permet de transférer la chaleur sur de plus grandes distances que le caloduc tubulaire classique, car les pertes de pression lors de l’écoulement du fluide sont réduites. Ils sont essentiellement utilisés dans l’industrie spatiale, pour le contrôle thermique d’appareils de mesure, d'instruments optiques et de batteries à bord de satellites. |
4.Caloduc oscillant (Pulsating heat pipe)
Il s'agit d'un simple tube capillaire de petit diamètre, en forme de serpentin, dans lequel oscillent des bouchons de liquide et de vapeur qui assurent le transport de chaleur.

→ Malgré ses nombreux avantages (fabrication facile, faible coût, sensibilité moindre à la gravité, performances thermiques élevées), ce caloduc n’est pas encore industrialisé car son fonctionnement chaotique est encore mal maîtrisé. |
Les structure capillaires des caloducs

Au sein de la plupart de ces variantes de caloducs, nous retrouvons une structure capillaire qui sert à drainer le liquide du condenseur vers l'évaporateur. Celles ci peuvent être composées de rainures, de toiles métalliques (mèches), ou encore de poudres frittées.
Les toiles métalliques sont les structures capillaires les moins utilisée actuellement car elles ne se prêtent pas à la fabrication industrielle en grande série et introduisent des pertes de charge importantes.
Le rainurage intérieur du tube permet une production de masse à faible coût, notamment lorsque la matière de la paroi du caloduc est compatible avec les procédés d’extrusion. Les forces capillaires sont cependant plus faibles dans les rainures que dans une structure frittée, ce qui fait que les caloducs rainurés sont principalement utilisés dans les applications spatiales, où l’absence des forces de gravité pouvant s’opposer aux forces capillaires permet le fonctionnement correct de ces systèmes.
Les progrès réalisés dans les techniques de frittage (utilisation de poudres de différentes granulométrie, de porogènes, …) permettent actuellement de fabriquer des caloducs frittés très performants, à des coûts raisonnables, pour les applications terrestres.
Exemples d’application des caloducs
Utilisation des caloducs en électronique
Les caloducs sont très fréquemment utilisés pour le contrôle thermique des systèmes électroniques dissipatifs (comme par exemple les cartes électroniques). On utilise généralement des caloducs tubulaires ou des boucles diphasiques placés dans le boîtier électronique, à la surface du composant ou de la carte électronique. La chaleur est ainsi dissipée vers l'air extérieur par des ailettes intégrées au boîtier.
Utilisation des caloducs en aéronautique
Les caloducs oscillants peuvent être utilisés en aéronautique, afin d'homogénéiser la température des tuyères à l'échappement d'un moteur d'avion, soumises à d’importants gradients de températures.

Problématique
Dans le domaine de l'électronique notamment, les systèmes de refroidissement actuels sont insuffisants. L'augmentation de la densité de flux thermiques dissipées par les composants ainsi que leur miniaturisation entraînent des surchauffes très importantes au niveau de la jonction des semi-conducteurs. Ces surchauffes génèrent des défaillances dans les appareils électroniques et réduisent notablement leur durée de vie.

On constate que la majorité des causes de défaillances des composants électroniques (55%) est due à un problème de contrôle de la température. Il est donc nécessaire de trouver des systèmes plus efficaces pour dissiper la chaleur vers une source froide, tels que les caloducs.
Contraintes de fabrication d'un caloduc
Un caloduc est un dispositif simple mais pour qu'il fonctionne correctement, le matériau constitutif de l’enveloppe doit cependant respecter un certain nombre de contraintes :
1. Tenue mécanique du matériau : Le volume intérieur du caloduc étant vide d’air, la pression interne qui règne en son sein dépend de la nature du fluide et de la température. Il existe alors une différence de pression entre le volume intérieur et l’extérieur (dépression ou surpression), sous laquelle l’enveloppe du caloduc doit pouvoir conserver sa forme et son étanchéité.
2. Étanchéité : Contenant un fluide diphasique, le caloduc doit être parfaitement étanche à la vapeur, de sorte à ne pas perdre sa charge en fluide. Il doit être également étanche à l’air, car l’introduction de gaz incondensables dans le volume intérieur perturbe le fonctionnement du caloduc.
3. Stabilité chimique et thermique : Le matériau de l’enveloppe doit être chimiquement compatible avec le fluide, dans la gamme de températures de fonctionnement envisagée. En effet, toute incompatibilité génère des gaz incondensables qui s’accumulent dans le volume intérieur du caloduc.
4. Faible résistance conductive : À l’évaporateur et au condenseur, le flux thermique doit être transféré par conduction à travers la paroi du caloduc. Par rapport à un matériau conducteur, une paroi de faible conductivité thermique (isolante) augmente la différence de température entre les sources. Il en résulte de plus faibles performances thermiques.
5. Stabilité de ses caractéristiques dans le temps : Ces dispositifs étant amenés à fonctionner pour des applications nécessitant des durées de vie importantes, allant de quelques mois à plusieurs dizaines d'années, les caractéristiques mentionnées précédemment doivent rester stables dans le temps.
Fabrication traditionnelle de caloducs
Traditionnellement, les caloducs sont fabriqués en métal (cuivre, aluminium, acier inoxydable, …). Les procédures de fabrication des caloducs font partie du savoir-faire des industriels et relèvent, à ce titre, du secret de fabrication. La qualité de fabrication est tout à fait déterminante dans la durée de vie du caloduc, tout au long du processus dont les principales étapes sont les suivantes :
- Fabrication de l’enveloppe et de la structure capillaire
- Dégraissage et décapage de l’enveloppe et de la structure capillaire
- Purification du fluide
- Dégazage de l’enveloppe et du fluide
- Transfert du fluide dans l’enveloppe
- Fermeture du caloduc
Fabrication en polymères
Pourquoi choisir de concevoir des caloducs en polymères via l'impression 3D stéréolithographique (SLA) ?
1. Poids : cela permet un allègement des équipements par rapport à des composants en métal (par exemple pour des applications avec une contrainte de poids tels que des avions électriques). La conductivité est cependant moindre qu'avec le métal, on doit donc augmenter la surface d'échange pour compenser cela.
2. Liberté de conception : L'impression 3D permet des pièces complexes avec une grande surface d'échange.
3. Isotropie: La SLA produit des pièces complètement isotropes après post-traitement.
4. Précision/tolérance: La Form 2 permet une précision jusqu'à 25µ d'épaisseur de couche et délivre des pièces avec un haute exactitude et tolérance.
5. Étanchéité : Les pièces imprimées en SLA sont étanches (selon l’épaisseur de la paroi)
La stéréolithogrpahie (SLA) est une technologie de fabrication additive qui fonctionne à partir d'une résine photosensible durcie à l'aide d'un laser UV.
Ce mode de production permet de nombreux avantages :
- Matériaux aux propriétés mécaniques et thermiques variées
- Pièces isotropes : la réticulation complète entre les couches permet des pièces étanches et résistantes
- Géométries complexes : pas de contraintes de coûts liées à la complexité de la pièce
- Qualité professionnelle : finitions semblables à des produits finis et entièrement fonctionnels
- Accessible : machines de bureau à moindre coût pour une qualité professionnelle
En savoir plus sur la stéréolithographie
Démarche de fabrication d'un caloduc en fabrication additive
Afin de comprendre les règles de design en fabrication additive, Thomas Joffre et son équipe ont commencé par réaliser une impression benchmark. Ils ont imprimé un modèle de pièce qui leur sert à tester :
- Les épaisseurs de paroi, en négatif ainsi qu'en positif
- Les formes (rectangles, sphères)
- Les plafonds (pour voir la rugosité en fonction de l'orientation)
- Les angles, rayons
- La précision géométrique (contrôlée avec un bras faro)
La pièce a été imprimée à plusieurs orientations pour connaître les paramètres d'impression optimum.

Ils ont ensuite conçu le caloduc en commençant par une pièce simple, pour tester la tenue en température et les effets de refroidissement. La pièce se compose des éléments suivants :
- Une tête hexagonale pour tester le taraudage
- Un tube avec une épaisseur de paroi variables, le but étant d'essayer de faire une paroi la plus fine possible pour la légèreté et la conductivité
- Un bout arrondi avec zone renforcée pour éviter les supports sur la pièce
Procédure de fabrication d'un caloduc en fabrication additive
Matériau : Résine High Temp de Formlabs
- Hauteurs de couche de 100, 50 ou 25µ
- Température de fléchissement sous charge à 0,45MPa : 238ºc
- Matériau rigide
Téléchargez la fiche technique complète
Ce matériau est généralement utilisé pour des tests de flux de fluides, d'air chaud ou de gaz, des supports, boîtiers et fixations résistants à la chaleur, ou encore des moules et inserts et toutes sortes d'applications en haute température.
Paramètres
- Hauteur de couche choisie : 50 microns (meilleur compromis entre qualité de pièce et temps de fabrication).
- Angle : Essais à 0 º, 30 º et 45 º degrés. Les propriétés du fonctionnement du caloduc vont dépendre de l’orientation lors de la fabrication. Le but final étant de réaliser des formes complexes, il est nécessaire d’établir l’impact de l’orientation sur la fabricabilité et les performances d’un caloduc élémentaire.
- Épaisseur de Paroi : tests effectués avec des parois entre 0.4 et 1.2 mm (les parois inférieures à 0.4mm créent des pièces non étanches).
Conception
- Création d'un modèle 3D sur SolidWorks
- Ajout des supports dans le logiciel gratuit de préparation à l'impression Preform, et modification manuelle afin d'éviter les supports internes

Impression
- Envoi du fichier vers la Form 2
- Insertion du bac et de la cartouche
- Lancement de l'impression
Post-traitement
- Lavage dans FormWash (6 min dans de l'alcool isopropylique) pour éliminer l'excès de résine non durcie
- Réticulation dans FormCure (1h à 60cº) afin de finaliser la réticulation et permettre à la pièce d’atteindre ses propriétés mécaniques maximales
Préparation et instrumentation des caloducs
Les tubes sont munis d’un embout taraudé dans lequel est inséré un tube en forme de T, relié d’une part à un capteur de pression, d’autre part à une pompe à vide.
Trois thermocouples sont installés au moyen d’adhésifs sur la surface extérieure de l’enveloppe, à différentes hauteurs pour mesurer les variations de température le long du caloduc.
Un fil chauffant est enroulé en spires jointives à la base du tube, préalablement enduite de pâte thermique conductrice, et couplé à une alimentation électrique. Le condenseur, situé à l’autre extrémité du tube, est simplement refroidi par convection naturelle avec l’air ambiant. De la peinture noire d’émissivité connue est appliquée sur un côté et toute la longueur du tube, pour permettre des mesures de températures par caméra infra-rouge.
Trois thermocouples sont installés pour mesurer les variations de température le long du caloduc.

Résultats
On constate que le taraudage fonctionne très bien et que le caloduc se connecte bien à l'embout.
Test 1 : Étanchéité à l'air
Il est important que le caloduc fonctionne en l'absence de gaz incondensables car cela affecterait négativement ses performances thermiques.
Étapes :
- Mise sous vide des tubes avec une pompe à vide (durée variable de pompage, 30 min à 2 heures)
- Découplage des tubes et de la pompe
- Mesure de la pression interne avec le capteur de pression durant plusieurs jours. Les courbes se stabilisent à la pression de 25 millibars, quelle que soit la durée de pompage. Il s’agit d’un vide satisfaisant pour cette application.

Test 2 : Fonctionnement en tant que caloduc
Étapes :
- Chauffage de la partie évaporateur avec le fil chauffant
- Mesure du champ de températures de l'évaporateur avec la caméra infrarouge
- Photographie du condenseur
Paramètres :
- Épaisseurs de paroi : 0,4 mm / 0,8 mm
- Volumes de fluide : 4 ml / 3 ml
- Puissances : 2,44 W / 1,8 W
- Fluides testés : Eau / éthanol
Observation 1
Les tubes se comportent très bien lors du chauffage de la zone évaporateur. On ne constate pas de déformation à l’oeil nu.
Le champ de température n'est pas uniforme à l'évaporateur (présence de zones chaudes) car le matériau a une faible conductivité.

Observation 2 :
Lorsque la surface interne du condenseur est texturée de manière oblique, des gouttelettes de fluide se forment au niveau du condenseur, ce qui indique que le caloduc fonctionne.
Les gouttes ne sont pas visibles lorsque la surface est texturée verticalement. Il semblerait que le fluide soit drainé vers l'évaporateur par le biais des micro rainures longitudinales liées à ce type d’état de surface. La direction de fabrication pourrait jouer sur le régime de condensation et donc sur les performances du caloduc.
Test 3 : Puissance variables
Les caloducs ont été soumis à des échelons de puissance croissants (0,14 - 2,7 W). A chaque échelon, la stabilisation de la température moyenne de l’évaporateur au niveau de la source chaude montre que le régime permanent est obtenu. Toutefois, des oscillations de température sont détectées à partir de 1,48 W.
Les températures ont ensuite été comparées avec celles des caloducs vides (sans fluide). Elles sont plus faibles lorsque le caloduc est chargé en fluide que lorsqu’il est vide, ce qui atteste que le transfert de chaleur par changement de phase liquide-vapeur a lieu au sein du caloduc. En l’absence de fluide, le transfert de chaleur s’effectue par conduction thermique le long de la paroi du tube. Comme la conductivité thermique du matériau est constante, la température évolue linéairement avec le flux thermique.


Les températures ne sont que faiblement modifiées lorsque l'épaisseur de la paroi varie de 0,4 à 0,8 mm. Une épaisseur de 0,8 mm peut donc être sélectionnée, car elle permet une meilleure tenue mécanique de l’enveloppe.
Conclusion et Perspectives
En conclusion, au cours de cette expérience, nous avons obtenu les résultats suivants :
- Un caloduc imprimé en polymère entièrement fonctionnel
- Une étanchéité satisfaisante pour permettre le fonctionnement du caloduc
- Une tenue en température de l’enveloppe du caloduc à 100 ºc
- Une grande influence de la direction de fabrication sur le mode de condensation et donc sur les performances du caloduc
Perspectives
Pour aller plus loin dans la réflexion, il faudrait se pencher sur les points suivants :
- Quantifier de façon plus précise les performances en termes de résistances thermiques
- Tester les limites de fonctionnement du caloduc en augmentant la puissance de chauffe
- Essayer le caloduc avec d'autres fluides caloporteurs
- Vérifier la tenue dans le temps
Modèle de caloducs à ailettes
L’étude précédente a pour objectif de tester les performances d'un dispositif à ailettes creuses intégrées (également réalisé en fabrication additive de polymères) constitué d'un évaporateur plan (en bas) et d'un condenseur à ailettes creuses. La réduction de l'efficacité des ailettes causée par la faible conductivité de la paroi serait compensée par la condensation du fluide au sein même des ailettes. De plus, étant une pièces unique, il n'y aurait pas la résistance de contact usuelle entre le caloduc et l'échangeur à ailettes.
Cette recherche à été conduite par :
CETHIL :
- Valérie Sartre, Maître de Conférences
- Stéphane Lips, Maître de Conférences
- Antoine Voirand, Post-doctorant
- Skander Mani, Chef de projet recherche
CT-IPC :
- Thomas Joffre, Chef de projet recherche en fabrication additive
- Julien Bajolet, Responsable recherche fabrication additive
Découvrez la résine High Temp par vous-même en commandant un échantillon gratuit imprimé sur la Form 2, et testez-la en conditions réelles.
Commander un échantillon gratuit Acheter High Temp Resin