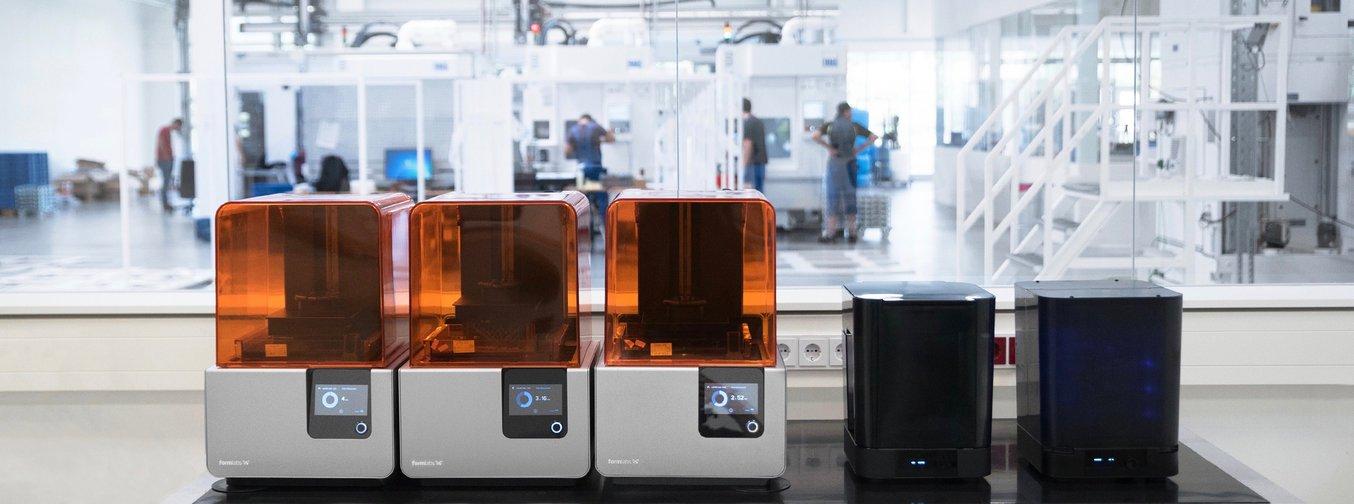
Qu’est-ce que des voitures de Formule 1 et Marine One peuvent avoir en commun? De nombreuses pièces de leurs transmissions et de leurs moteurs hautes performances ont été fabriquées à Kapfenberg, une petite ville tranquille des Alpes autrichiennes.
Pankl Racing Systems est une entreprise spécialisée dans le développement et la fabrication de pièces de moteur et de transmission pour voitures de course, véhicules à hautes performances et pour l'aérospatial. Elle emploie plus de 1 500 personnes et possède des filiales en Autriche, en Allemagne, au Royaume-Uni, aux États-Unis, en Slovaquie et au Japon.
Chacune des pièces fabriquées par Pankl nécessite toute une série d’outils et d’accessoires porte-pièces et supports, conçus et fabriqués spécifiquement pour cette pièce. Il en résulte une prolifération de ces outils spécifiques, qui ajoute de la complexité et des coûts importants au processus de fabrication.
Pour arriver à tenir des délais de production très serrés, l’ingénieur process Christian Joebstl et son équipe ont introduit l’impression stéréolithographique pour fabriquer directement des porte-pièces sur mesure et d’autres pièces de faible volume, nécessaires sur la ligne de production de leur toute nouvelle usine de pointe, dont l’installation a coûté 36 millions.
Pas le temps de lire cet article ?
Téléchargez l'étude de cas détaillée
Malgré le scepticisme qui a accueilli cette décision, l’impression 3D s’est avérée idéale en remplacement de l’usinage de nombreuses pièces et a même surpris les ingénieurs les plus exigeants. Dans un cas précis, l’impression 3D a permis de réduire de 90% le délai de production de porte-pièces, le faisant passer de 3 semaines à moins d’une journée. Les coûts ont été réduits de 80 à 90%, réalisant une économie de 150 000 €. Dans la suite, est expliqué comment Joebstl et son équipe ont mis en œuvre le nouveau process avec impression 3D.
Pankl travaille dans ce secteur depuis plus de 30 ans. L’impression 3D fait-elle partie de vos pratiques depuis longtemps ?
Étonnamment, pas du tout. Nous travaillons avec des imprimantes 3D depuis moins d’un an seulement. Un de mes collègues avait besoin d’un capot sur mesure pour protéger certaines surfaces des impacts dans une grenailleuse. Nous avions l’habitude de nous procurer ce type de pièce auprès d’un fournisseur externe, et cet outillage coûtait environ 1 200 €. Je me disais qu’il devait exister un autre moyen.
Familiarisé avec l’impression 3D pendant mes études, j’ai commencé à chercher et j’ai trouvé l’imprimante 3D Form2en lisant des revues en ligne. Mes collègues ont maintenant compris la valeur de l’impression 3D, mais, au début, ils étaient extrêmement sceptiques. Ils considéraient l’imprimante 3D plutôt comme un jouet.
Dans notre secteur, nous nous attendons à ce qu’un bon équipement soit obligatoirement coûteux. Le prix de la plupart de nos machines est d’au moins 100 000 € et peut dépasser cette somme de beaucoup. Lorsque mes collègues ont vu que la Form 2 ne coûtait que 3 900 €, ils m’ont demandé pourquoi nous avions acheté « un jouet ».
Nous avons commandé des échantillons de très nombreuses pièces sur mesure pour faire des tests, et il s’est avéré que les pièces imprimées présentaient les propriétés demandées. Les intervalles de tolérance pour les orifices et les longueurs étaient bien de ±0,1 mm. En me renseignant sur les coûts des résines pour faire des calculs d'amortissement, j’ai découvert qu’imprimer en 3D un ensemble d’outillage pour le grenaillage coûterait seulement 45 €. J’ai résumé toutes ces caractéristiques pour les exposer à la direction et j’ai apporté les pièces à la réunion de lancement de notre nouvelle usine. Ils ont finalement été convaincus et nous avons décidé de l’achat de notre première Form 2, puis rapidement des deux autres.

Dans quels cas l’impression 3D a-t-elle permis de réduire les délais de production et les coûts ?
Pankl a été choisie pour fabriquer les ensembles complets de boites de vitesses pour plusieurs lignes de fabrication de motos en 2016 et a rapidement commencé à mettre en place la nouvelle usine. Le processus de fabrication de ces engrenages est particulièrement délicat. Les pièces forgées en acier passent par de multiples phases d’usinage réalisées par des tours automatiques, puis subissent un recuit de détente des contraintes et d’autres traitements thermiques.
Chacune des phases d’usinage dans les machines de tournage requiert des porte-pièces spécifiques à chacun des types d’engrenages. L’usinage de ces pièces est coûteux et augmente significativement la complexité et les risques associés au processus de fabrication.
Notre calendrier était serré parce que nous devions produire plus de types d’engrenages que prévu. Au moment où nous devions concevoir et commander l’outillage nécessaire, nous aurions dû déjà commencer à produire les premiers lots d’essai. Nous ne pouvions juste concevoir les porte-pièces et en disposer le jour suivant. Si nous les avions faits faire par des fournisseurs externes, nous aurions dû attendre encore six semaines avant de pouvoir commencer la production. Nous avons donc décidé de les produire en interne sur nos imprimantes Form 2.

En les imprimant en 3D, il suffit de prendre le même modèle de conception, de l’envoyer à l'imprimante et la pièce finie est disponible le lendemain matin. Cela laisse le temps de l’essayer sur la ligne de fabrication et de la modifier si nécessaire. L’impression 3D simplifie également la phase de conception, parce qu’elle permet de fabriquer des porte-pièces de n’importe quelle forme. La conception adaptée à l’usinage traditionnel avec machines de fraisage ou de tournage à commande numérique est limitée par les contraintes des machines, et ajouter une courbe, un orifice ou un chanfrein complique sérieusement le processus.

Nous pouvons maintenant imprimer un porte-pièce unique en 5 à 9 heures et demie sur une Form 2, et environ 40 porte-pièces dans la même semaine sur les 3 imprimantes 3D Form 2.
Un porte-pièce unique usiné revient à 40-50 €, mais des pièces plus complexes peuvent coûter jusqu’à 300 €. L’impression 3D réduit ces coûts directs à 8,5-25 €, ainsi que les coûts supplémentaires de conception, d’achat et de stockage, ce qui aboutit finalement à des économies globales de l’ordre de 90%. En considérant que nous devrons fabriquer plus de 1000 porte-pièces sur l’ensemble de la production, l’impression 3D nous permettra d’économiser plus de 150 000 €.
Comment ces pièces imprimées se comportent-elles sur la ligne de production ?
Nous avons eu beaucoup de problèmes auparavant, parce que le produit de refroidissement utilisé dans le tour était très agressif pour les pièces en plastique, qui devenaient friables après un certain temps. Les pièces imprimées en résine Haute Résistance ont bien résisté à ce produit et présentent la solidité suffisante par rapport à la charge qu’elles doivent supporter de façon intermittente. Les intervalles de tolérance pour les orifices et les longueurs sont de ± 0,1 mm, ce qui satisfait les exigences s’appliquant à nos porte-pièces.

Nous avons déjà fabriqué plus de 300 porte-pièces imprimés en 3D pour la fabrication de lots de 200 pièces de chaque modèle d’engrenage, pour l’opération de test de fabrication. La production va bientôt passer à des lots de 1000 à 2000 pièces et la capacité de production de l’usine atteindra plus de 1,5 million d’engrenages.
Pour quelles autres applications avez-vous utilisé l’impression 3D ?
Le prototypage, le grenaillage, le masquage et la fabrication de différents porte-pièces et outillages. Lorsque nous concevons une nouvelle bielle, par exemple, nous utilisons des prototypes imprimés en 3D pour discuter des caractéristiques complexes de la pièce. C’est beaucoup plus facile lorsqu’il est possible d'examiner la pièce, de la tenir en main.
Nous devions par exemple concevoir une bielle pour un client, qui voulait vérifier qu’elle tenait bien dans la chambre du cylindre, sans heurter la chemise ou la culasse lorsqu’elle tournait. Nous avons imprimé un prototype en 3D et leur avons envoyé. Après avoir reçu leur confirmation, nous avons pu commencer la production en toute confiance. Si nous n’avions pas eu cette possibilité, nous aurions dû faire fabriquer la pièce usinée, ce qui aurait coûté beaucoup plus cher au client et demandé huit semaines de délai.
L'AJUSTEMENT EN INGÉNIERIE : OPTIMISER LA CONCEPTION POUR DES ASSEMBLAGES FONCTIONNELS IMPRIMÉS EN 3D
Un tolérancement dimensionnel correct à la conception va diminuer le temps de traitement après fabrication, faciliter l’assemblage et réduire les coûts en matériau en cas d’itération
En savoir plus
Nous avons aussi imprimé des adaptateurs spéciaux pour des pinces d’un robot manipulateur. Pour que la pince saisisse parfaitement la pièce, il faut prendre le négatif de la pièce et dessiner les doigts de la pince en fonction de la forme de la pièce à saisir. Habituellement, nous l’aurions fait par fraisage ou fonderie, ce qui aurait coûté bien plus cher.
Récemment, nous avons utilisé la résine Flexible dans une grenailleuse, afin d’augmenter le frottement entre les porte-pièces autonettoyants et d’autres pièces. En effet, le frottement entre les pièces métalliques était trop faible pour transmettre le mouvement de rotation. J’ai ajouté des freins élastiques imprimés en 3D pour augmenter le frottement, de façon à ce que le mouvement de rotation soit bien transmis de bas en haut. Cela aurait pris des semaines s’il avait fallu fabriquer ces pièces en externe.
Avez-vous d’autres projets d’impressions 3D au sein de Pankl ?
L’un de mes objectifs est d’obtenir des commandes de la part d’autres départements de Pankl. Nous avons eu de bons résultats en imprimant en 3D des pièces pour notre ligne de production et je pense à bien d’autres applications intéressantes de cette technique. Je souhaite montrer aux autres ingénieurs les pièces que nous avons réalisées et expliquer à quoi elles servent, pour qu’ils sachent que cette technique est disponible en interne.
J’ai démarré ce projet au moment où d’autres collègues montraient de l’intérêt pour nos nouveaux process. J’ai diffusé les informations sur les résines pour l’impression 3D, notamment leurs propriétés mécaniques, leur aspect et les différents usages auxquels elles conviennent. J’ai aussi imprimé des échantillons pour d’autres départements avec une description de leurs caractéristiques de conception. J’ai expliqué comment pouvaient se faire les commandes.
Découvrez ce que vous pouvez créer avec une Form 2
Exporez notre sélection de matériels pour toruver celui qui vous convient.
Demandez un échantillon
Nous avons déjà imprimé des pièces pour les départements aérospatial et transmissions. Ils nous ont envoyé les plans de conception, nous avons imprimé les pièces et ils les ont reçues finies et prêtes à l’emploi dans leurs machines. Mais Pankl est une grande entreprise, ce qui ralentit le processus. Nous avons à dépasser les mêmes réticences qui existaient au début dans notre département face à l'impression 3D, et je pense que c’est la même chose dans de nombreuses entreprises. Mais je suis sûr que les résultats que nous avons obtenus vont leur permettre d’en reconnaitre la valeur.