Los moldes impresos en 3D crean nuevas categorías de productos de poliuretano en Kastalon
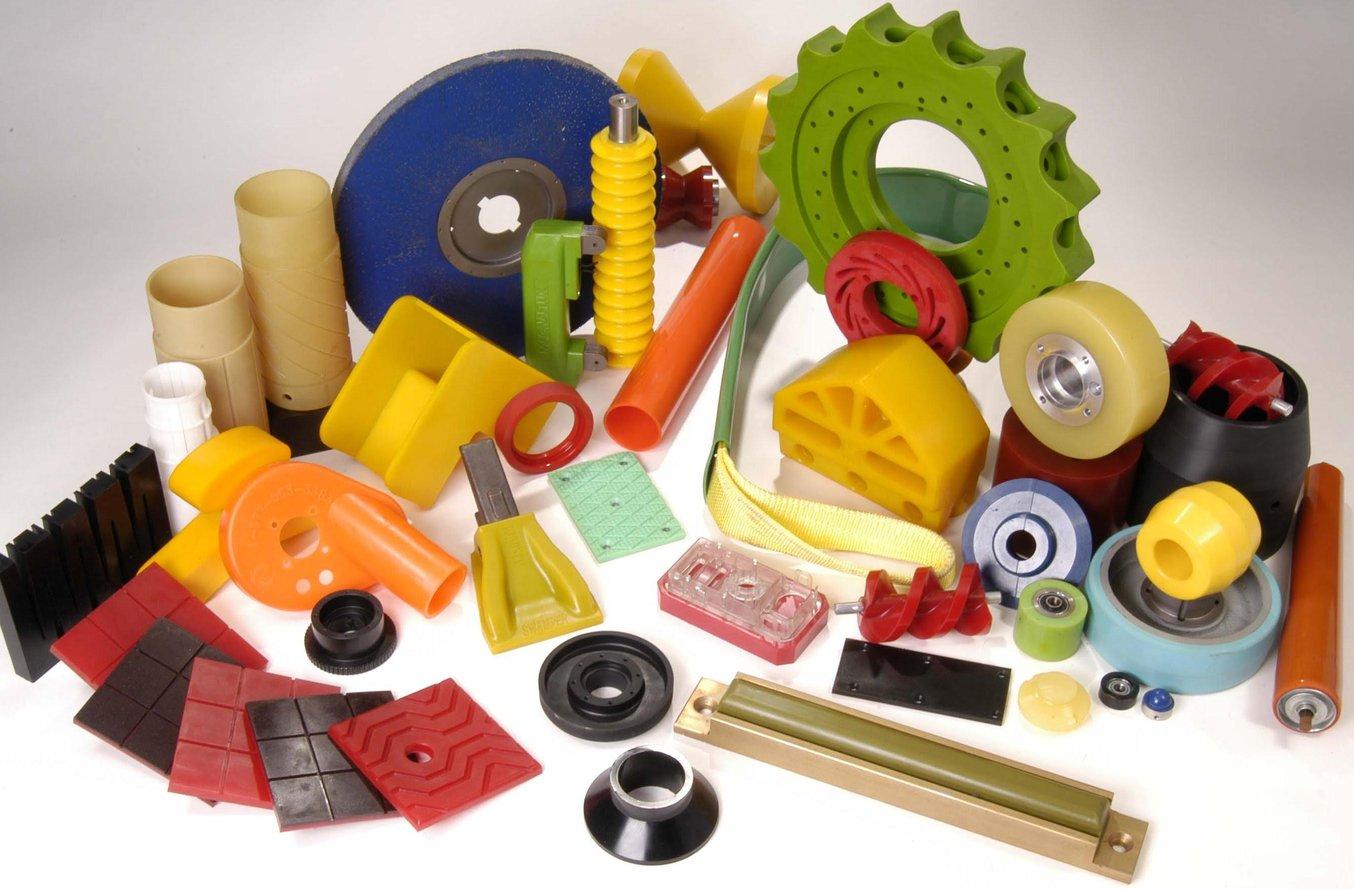
Son cruciales, pero a menudo no se ven: rodillos para las cintas transportadoras de cadenas de montaje, pastillas de freno para montañas rusas y calzos para las ruedas de aviones de combate que los mantienen en su sitio... Las piezas de poliuretano son esenciales para el funcionamiento de los sistemas, aunque no sea el primer material que venga a la cabeza cuando miramos un producto. Para funcionar bien como parte de conjuntos mayores, las piezas de poliuretano se tienen que diseñar para optimizar el uso del material, tolerancias ajustadas y soportar cargas o deformaciones de forma prolongada.
Kastalon, un fabricante de poliuretano en Illinois, lleva décadas resolviendo problemas para producir miles de piezas de poliuretano personalizadas capaces de cumplir este diverso abanico de requisitos. El ingeniero de productos Brian Baer nos ha hablado acerca de cómo la impresora de estereolitografía (SLA) de gran formato Form 3L crea nuevas oportunidades para utillaje, accesorios para la fabricación y la investigación y desarrollo de nuevos productos.
"Poder imprimir en 3D un molde totalmente nuevo es una gran ventaja cuando hay que realizar pequeños cambios y ajustes. También nos viene muy bien poder alcanzar una tolerancia de +/- 0,01. Hemos hecho cosas que antes no podíamos hacer y el volumen no deja de crecer".
Brian Baer, ingeniero
Cómo Kastalon combina la impresión 3D con el mecanizado tradicional
Kastalon diseña y fabrica cientos de moldes personalizados para producir cientos de miles de piezas de poliuretano. La forma tradicional de llevar a cabo de este proceso es que cuando los clientes solicitan piezas de uso final, el equipo de Kastalon evalúa la viabilidad de moldear la pieza antes de mecanizar el molde a partir de aluminio o acero.
Antes, el coste y la complejidad del proceso de mecanizado a veces obligaba a Kastalon (como a muchos fabricantes de plásticos) a rechazar piezas que eran demasiado complicadas de moldear o no resultaban rentables para remesas cortas de piezas o para el prototipado. Los moldes con demasiados elementos entrecruzados, canales pequeños o pernos a menudo resultaban poco eficientes de diseñar, mecanizar y a veces, modificar por completo. A pesar de ello, era difícil rechazar oportunidades de negocio, y al haber trabajado con diversas tecnologías de impresión 3D cuando estudiaba, Baer empezó a investigar otras formas de fabricar moldes.
Una incursión en el ámbito de la impresión 3D años antes había dejado un mal sabor de boca al equipo, por lo que Baer tenía requisitos específicos en mente mientras realizaba su investigación. Necesitaban una máquina capaz de lidiar con tolerancias de +/- 0,01 cm, materiales que pudieran soportar temperaturas de moldeo de 80-150 °C y un sistema con un precio económico.
"No fue hasta que encontré Formlabs y vi su abanico de materiales que soportan temperaturas elevadas y hacen cosas muy concretas que me di cuenta de que esta impresora sí se puede aplicar a [los] tipos de cosas que hacemos".
Brian Baer, ingeniero
A finales de 2022, la Form 3L llegó a la oficina de Kastalon, pero hicieron falta varios ensayos para convencer a toda la empresa. Los compañeros de Baer mantuvieron su escepticismo respecto a los materiales y las tolerancias que eran posibles hasta que Baer imprimió algunas piezas de prueba. "Imprimí una pieza para el taller de mecanizado y realizaron una prueba de rugosidad media (RA). Al responsable del taller le impresionó mucho que pudiera adaptarse a las especificaciones que le había dado y lo lisa que era la pieza", dice Baer.
De hecho, Baer continúa diciendo que ahora el responsable del taller de mecanizado es el primero que le envía piezas para que las imprima en 3D en vez de mecanizarlas. "Es de los primeros que sugiere la impresión 3D cuando hay trabajos a los que se pueda aplicar. El taller de mecanizado está saturado con proyectos mayores, así que si hay algo más pequeño que se puede imprimir, quiere que nos lo quedemos y le demos más margen", dice Baer.
Nuevas oportunidades en cuanto a la geometría, los ensayos y las operaciones
La impresión 3D crea nuevas posibilidades para moldear piezas de poliuretano. El equipo de ingeniería de Kastalon puede probar nuevos elementos de diseño y geometrías con los que los moldes de metal simplemente no pueden competir, o hacer pequeños cambios a los diseños sin preocuparse de desperdiciar un molde mecanizado. El equipo puede proponer diseños nuevos con confianza porque pueden hacer ensayos e iteraciones de forma exhaustiva sin miedo de saturar el taller de mecanizado con pequeños cambios.
Molde de abrazadera de cortadora de cola: Posible gracias a la impresión 3D
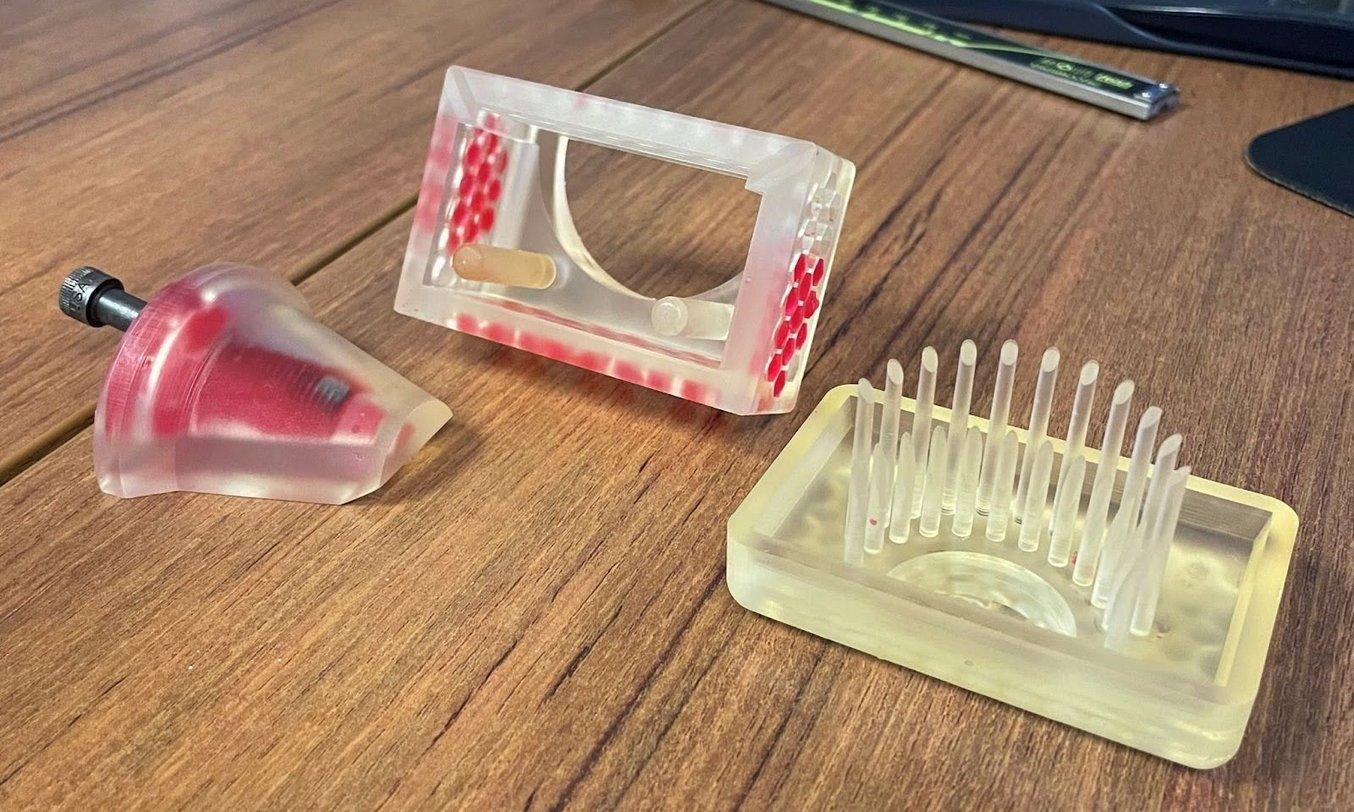
Kastalon tuvo que decir que no a un cliente que pidió una pieza con 24 agujeros ciegos desplazados de la superficie superior, ya que el molde simplemente sería demasiado difícil de mecanizar.
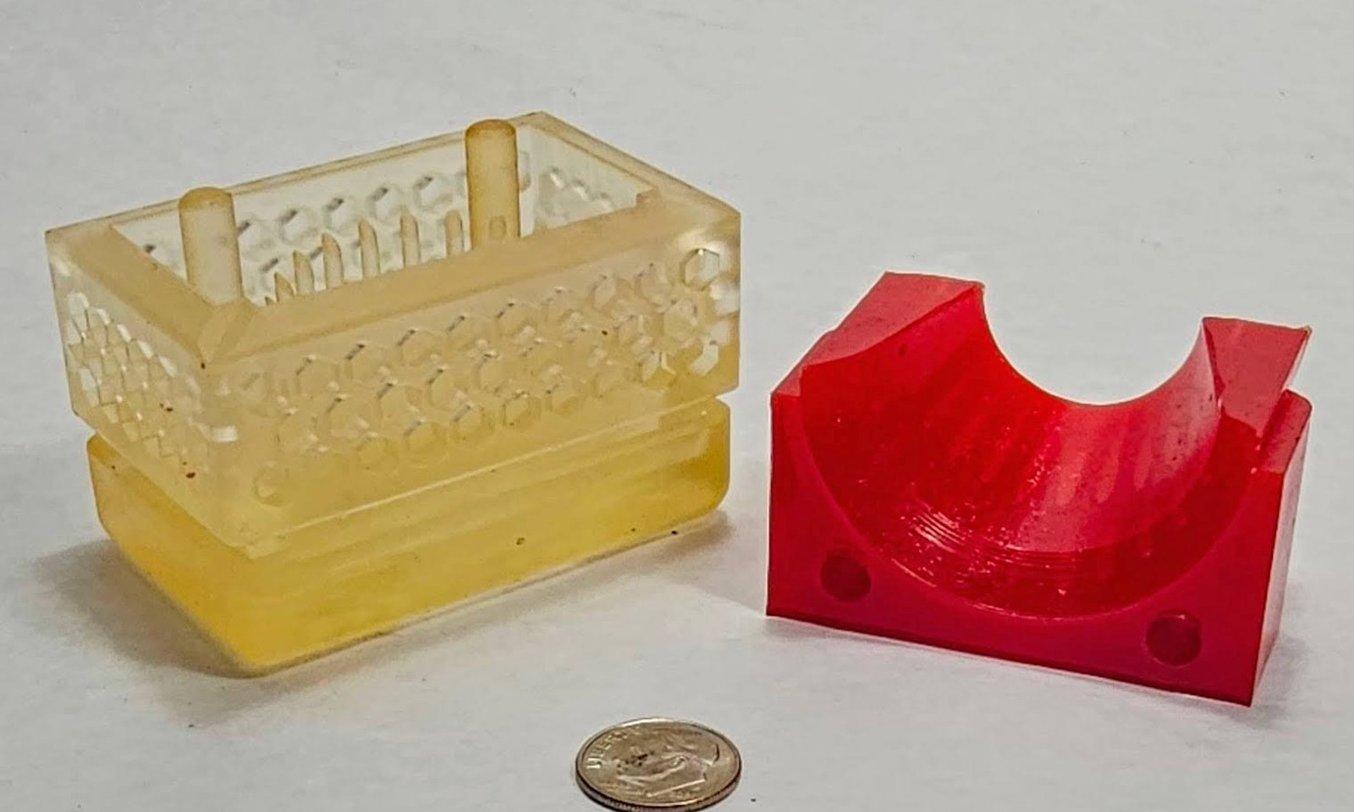
Con la Form 3L y la High Temp Resin, Baer pudo imprimir y fundir la pieza de poliuretano acabada (derecha) en menos de un día.
Antes de que llegara la Form 3L, el equipo de Kastalon tuvo que decirle a un cliente que no podía aceptar el pedido de la pieza del molde de la abrazadera de cortadora de cola. Aunque podría haber sido posible tras mucho ensayo-error, el juego de 24 pinchos altos no llega hasta el final y el espacio entre ellos es de 0,079375 cm.
Ese margen de espacio y que todos los agujeros sean ciegos y acaben distanciados de la superficie superior hacen que esta pieza requiera un mecanizado extremadamente difícil con utensilios de corte muy delicados y largos. La otra opción sería hacer cada pincho individualmente y después enchavetarlo para que se alinee en la orientación correcta... pero cuando el pincho solo tiene 0,264 cm de diámetro, no es tarea fácil.
Después de evaluar estos distintos de procesos de fabricación posibles, el equipo tuvo que negarse a aceptar el pedido. "Pasamos mucho tiempo discutiendo si sería posible y fue una decisión difícil decir que no al cliente", dice Baer.
Solo unas semanas después, llegó la Form 3L, y Baer diseñó e imprimió el molde en medio día para demostrar la viabilidad empresarial de imprimir en 3D geometrías complejas como estas. El coste de los materiales era de poco más de 30 € y el diseño le llevó unas dos horas. "Todo el mundo sintió al momento mucho respeto por la impresión 3D. Abrió los ojos de muchos de nuestros trabjadores de la fábrica para que dijeran: "Podemos aceptar más pedidos porque ahora podemos hacer cosas como esta", dice Baer.
Rueda antiaplastamiento
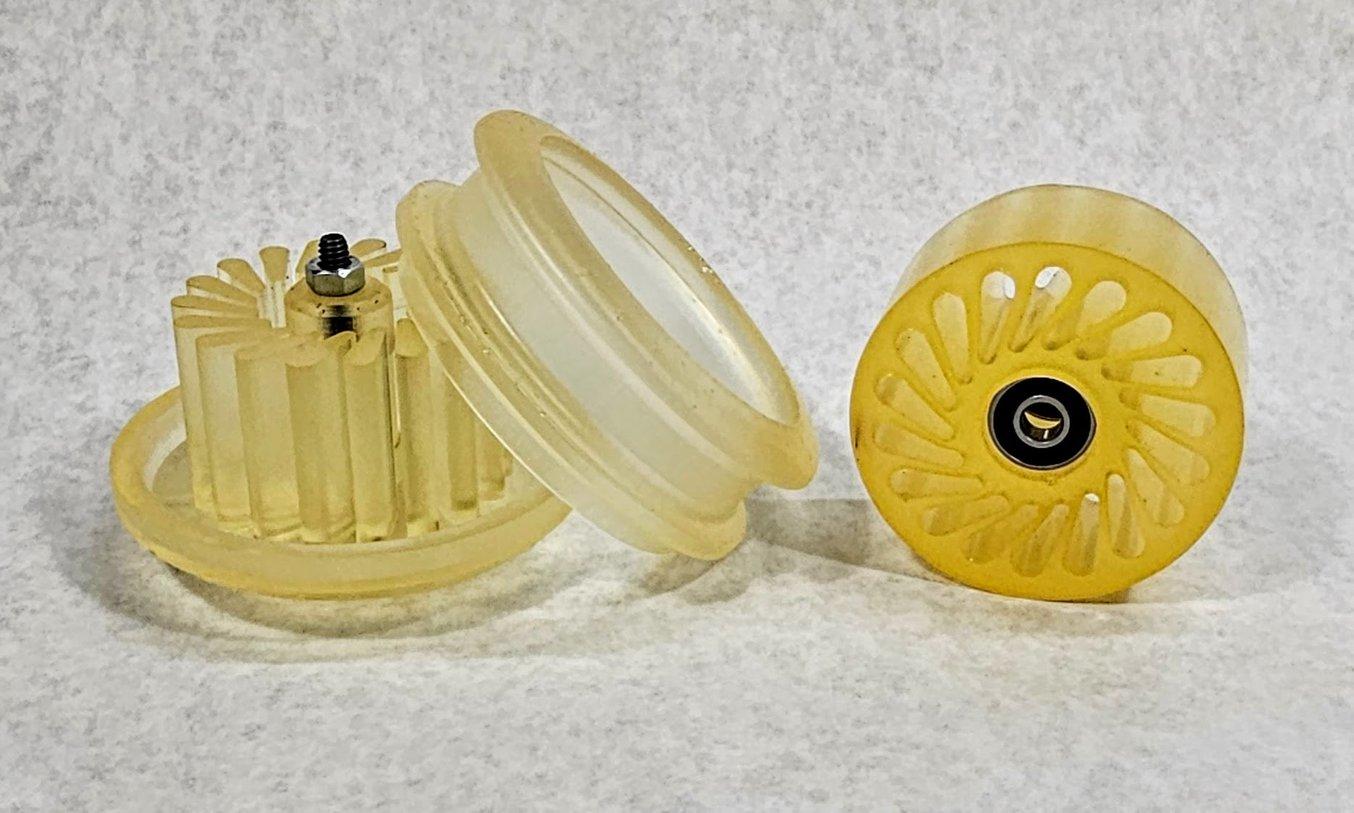
Estos moldes de rueda (izquierda, arriba y abajo) y las ruedas (derecha) están diseñados para deformarse de forma uniforme en caso de sobrecarga: la abertura en forma de lágrima distribuye el peso de forma uniforme para que la rueda no aplaste el producto.
La Form 3L destaca cuando los detalles pequeños hacen que un molde sea demasiado difícil de mecanizar. Estas pequeñas ruedas antiaplastamiento, que se usan para sujetar productos blandos (como embalajes de cartón) en sistemas de cintas transportadoras, hacen las veces de conjuntos de resorte. En vez de que un brazo de resorte haga presión sobre el cartón, la misma rueda se deforma de forma uniforme para sujetar el cartón en su sitio.
Sin embargo, los moldes de las ruedas tienen un espacio de margen increíblemente pequeño entre las "aletas" que se usan para moldear las aberturas en forma de lágrima en las ruedas, lo que hace que sea casi imposible fabricar el molde.
Las ruedas tienen 5 cm de ancho y el grosor de la pared entre las aletas es de 0,3175 cm. "Cinco centímetros de profundidad con un espacio de 0,3175 cm podría ser posible, pero va a enfadar a muchos mecanizadores si intentas mandar ese diseño", dice Baer.
Además del nivel de dificultad del mecanizado, un molde de aluminio de varios componentes haría que el proceso de montaje fuera más complicado. Hay dos opciones: mecanizar el molde con las aletas como una sola pieza (como se muestra en la imagen de arriba) y hacer que el espacio entre los componentes sea extremadamente difícil de hacer para los mecanizadores, o hacer todas las aletas individualmente y después ensamblarlas, lo que requeriría más trabajo de preparación y más montaje de piezas pequeñas, añadiendo trabajo manual e irritación a las tareas de los mecanizadores.
La impresión 3D se convirtió en la solución lógica a estos problemas y Baer diseñó fácilmente en SolidWorks un molde de dos componentes con un rodamiento extraíble antes de imprimirlo con la High Temp Resin y la Rigid 10K Resin en la Form 3L. El equipo usó la Rigid 10K Resin para fundir 25 ruedas para el cliente por un coste inferior al que habría supuesto trabajar con un molde mecanizado. "Hemos hecho ruedas muy pequeñas de muchos tipos y estilos, algo que no podíamos hacer antes de la Form 3L porque no nos salía rentable", dice Baer.
Mecanizado | Impresión 3D | |
---|---|---|
Número de componentes | 21 | 3 |
Tiempo de diseño | 7 h | 3 h |
Tiempo de preparación | 5 h | - |
Tiempo de fabricación | 35 h | 12 h |
Tiempo total | 47 h | 15 h |
Modelos para ensayos internos de muelles de gran tamaño
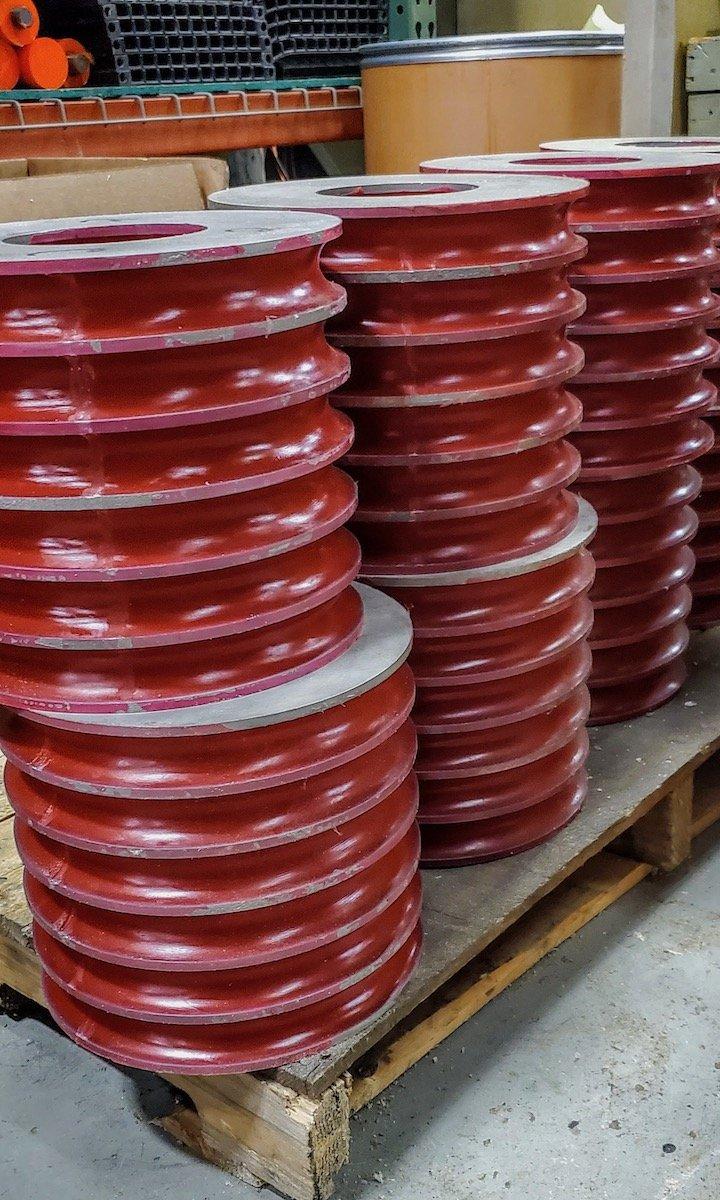
Tradicionalmente, las piezas de poliuretano como estos muelles rojos se funden a partir de grandes moldes de aluminio.
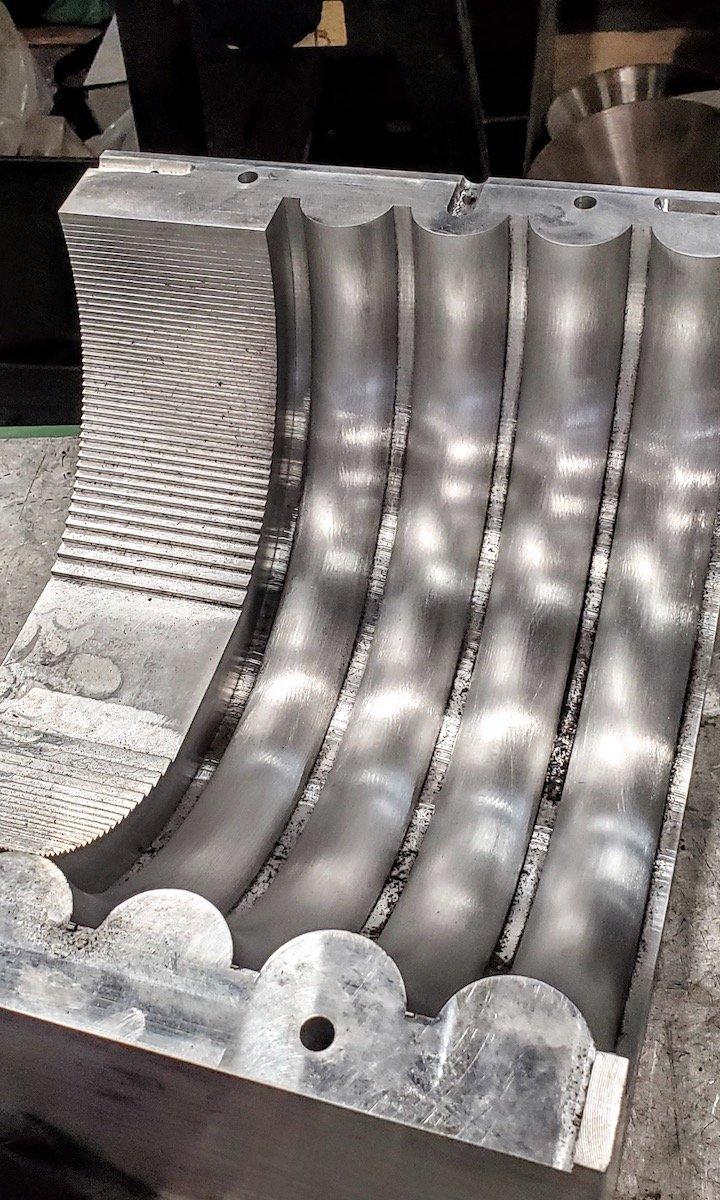
Estos moldes de aluminio (o en algunos casos, de acero) son caros y lentos de mecanizar.
El estadio de béisbol de los Astros de Houston tiene una cúpula retraíble como protección contra las inclemencias del tiempo y Kastalon es el fabricante responsable de los muelles que mantienen dicha cúpula tensa y en funcionamiento, incluso con vientos huracanados.
Antes de fabricar moldes como los que hacen falta para muelles del tamaño de los del estadio, el equipo de Kastalon realizó ensayos exhaustivos para probar el diseño y el material con versiones a escala reducida de las piezas. Cambiar ligeramente el diseño y poner a prueba los cambios en la relación elástica del muelle con diferentes geometrías y formulaciones de poliuretano les permitió optimizar su producto final para períodos prolongados de esfuerzos intensos.
Sin embargo, a pesar del cambio de tamaño, cada uno de los moldes de aluminio seguía siendo caro, especialmente si solo se utilizaba para ensayos del fabricante. Ahora, la Form 3L permite al equipo probar muchos diseños de muelles diferentes por un coste mucho menor y sin ocupar el tiempo del taller de mecanizado.
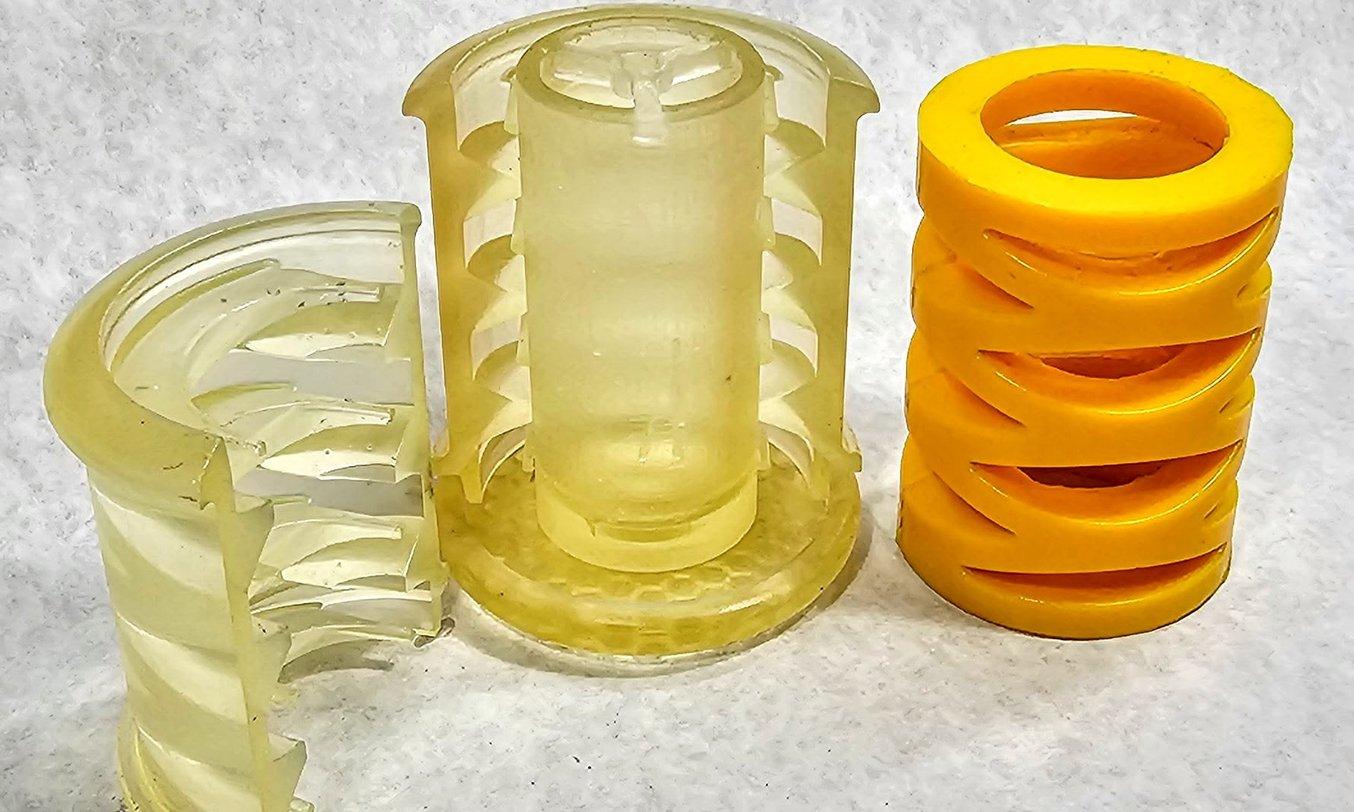
Estos moldes (de High Temp Resin, a la izquierda) y los muelles de poliuretano (en naranja, a la derecha) son prototipos con una geometría diseñada para reproducir muelles de disco apilados.
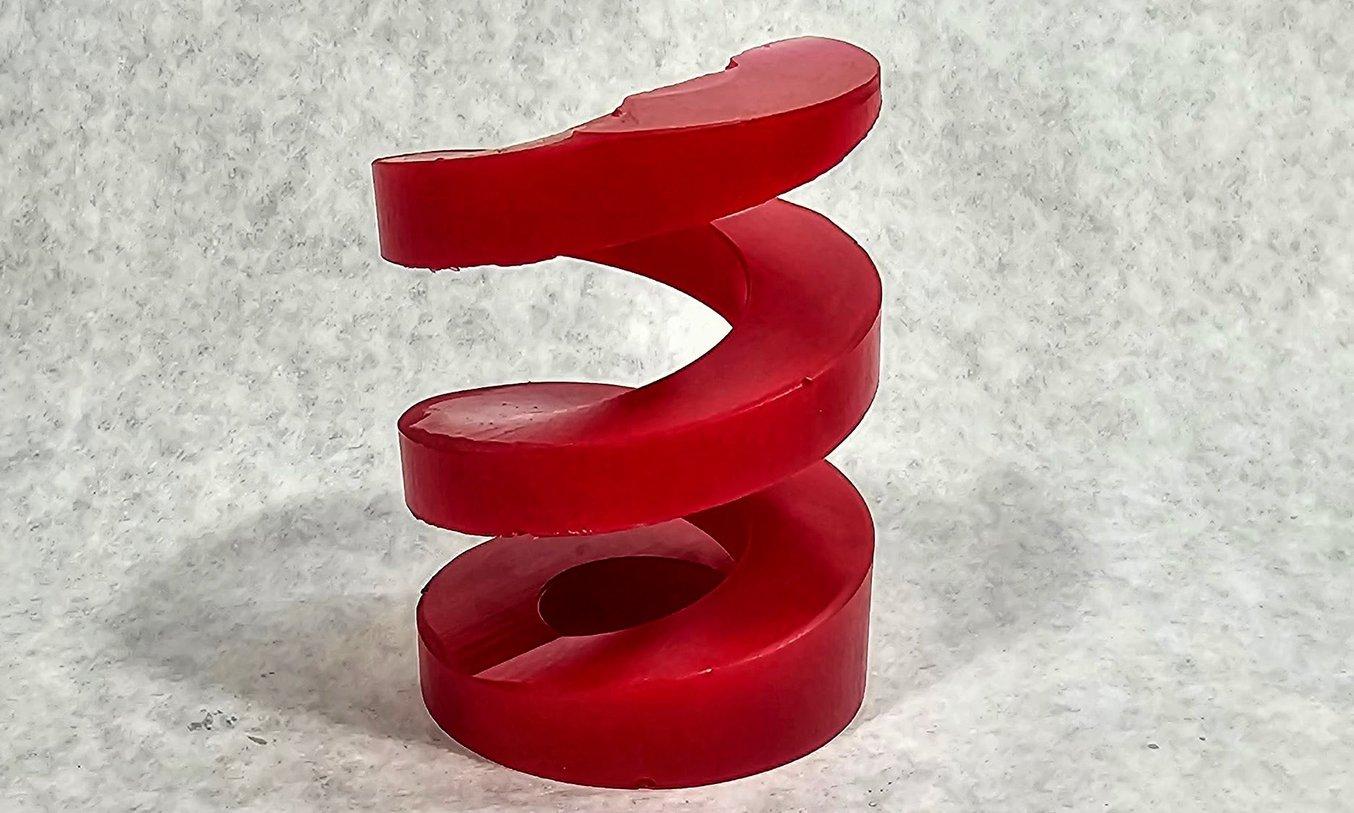
La impresión 3D permite a Baer y al equipo experimentar con nuevas geometrías y diseños, sin añadir más trabajo para el taller de mecanizado.
"Ahora podemos imprimir y poner a prueba muchas formas y geometrías extrañas que antes habrían costado una cantidad ingente de dinero solo para probarlas o para la investigación y el desarrollo", dice Baer. Someter a ensayo formas y geometrías nuevas y complicadas sin añadir los costes elevados de los materiales y la mano de obra del mecanizado permite a Kastalon no solo expandir su cartera de clientes, sino también hacer piezas mejores para sus clientes actuales.
Moldes de rodillo: Evita el mecanizado del poliuretano blando
Para los rodillos con revestimiento o las mangas para rodillos, el proceso de trabajo tradicional incluía un molde cilíndrico de poliuretano con paso de mecanizado adicional para reducir el diámetro exterior al tamaño y el acabado de la superficie deseados. El paso adicional de mecanizar las muescas se puede realizar con diversos estilos y tamaños en función de la aplicación que se vaya a dar al rodillo. En este caso concreto, mecanizar muescas largas horizontales en el poliuretano blando se convirtió en una tarea problemática. Para los pedidos grandes, este paso de mecanizado con mucho trabajo manual reducía los beneficios derivados del pedido y ocupaba horas del tiempo del taller de mecanizado. "Mecanizar el poliuretano blando es un engorro, porque no siempre da un buen resultado y no siempre genera un acabado excelente al cortar", dice Baer.
Mecanizar las muescas directamente llevaría unas tres horas por cada rodillo, pero mecanizar un único molde de metal era demasiado caro y arriesgado, sobre todo cuando no se había hecho nunca un molde con esta geometría y no se sabía si funcionaría. Para fabricar un molde de metal, el equipo requeriría una varilla de ataque o un torno con un cabezal indexador, que son ambos elementos de equipamiento costosos que están muy especializados para determinadas geometrías y aplicaciones.
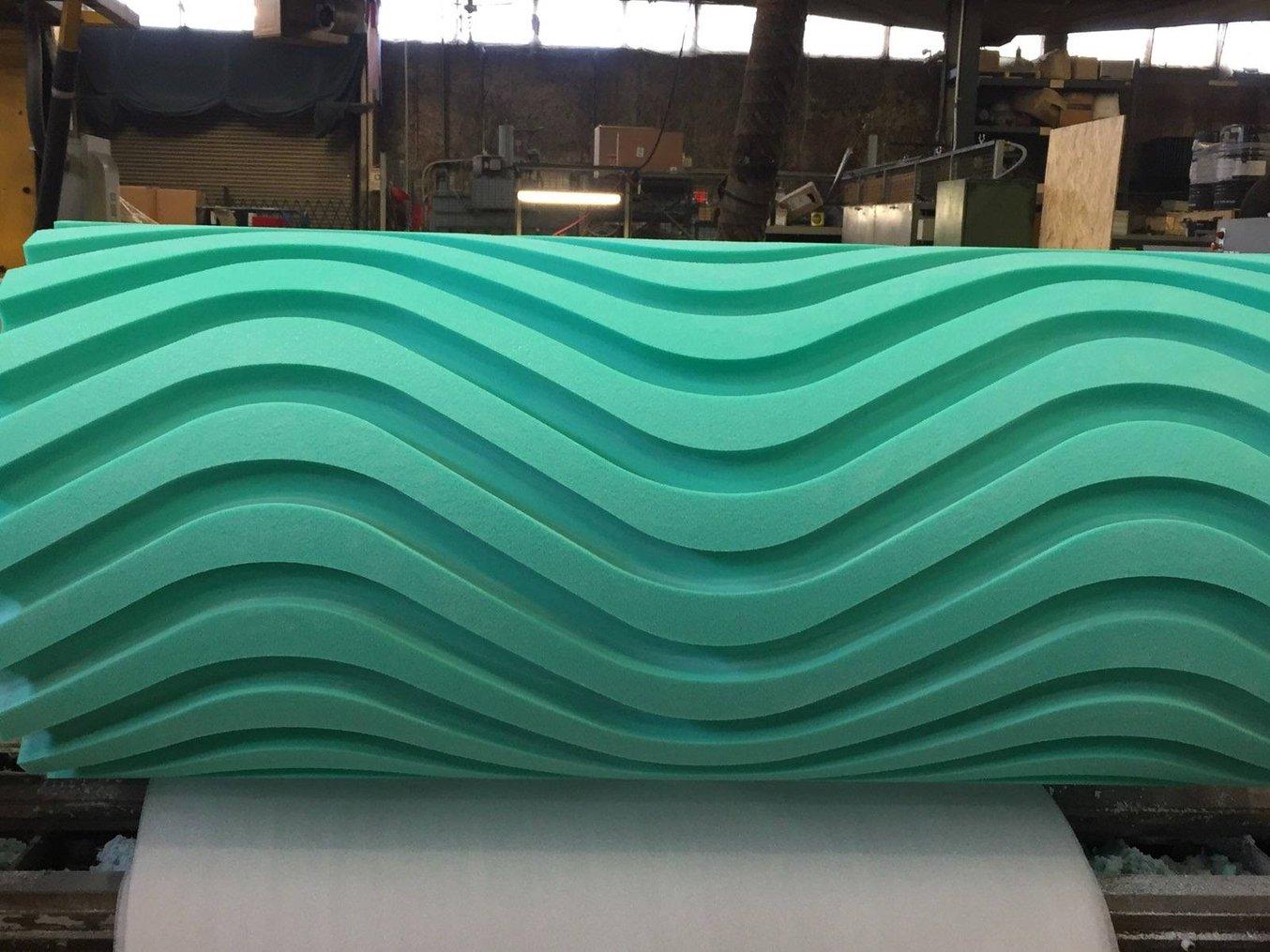
Mecanizar el poliuretano blando es un proceso que puede ser lento y engorroso, especialmente con piezas grandes como este rodillo, que se funde como un cilindro y después se mecaniza para hacer la forma final.
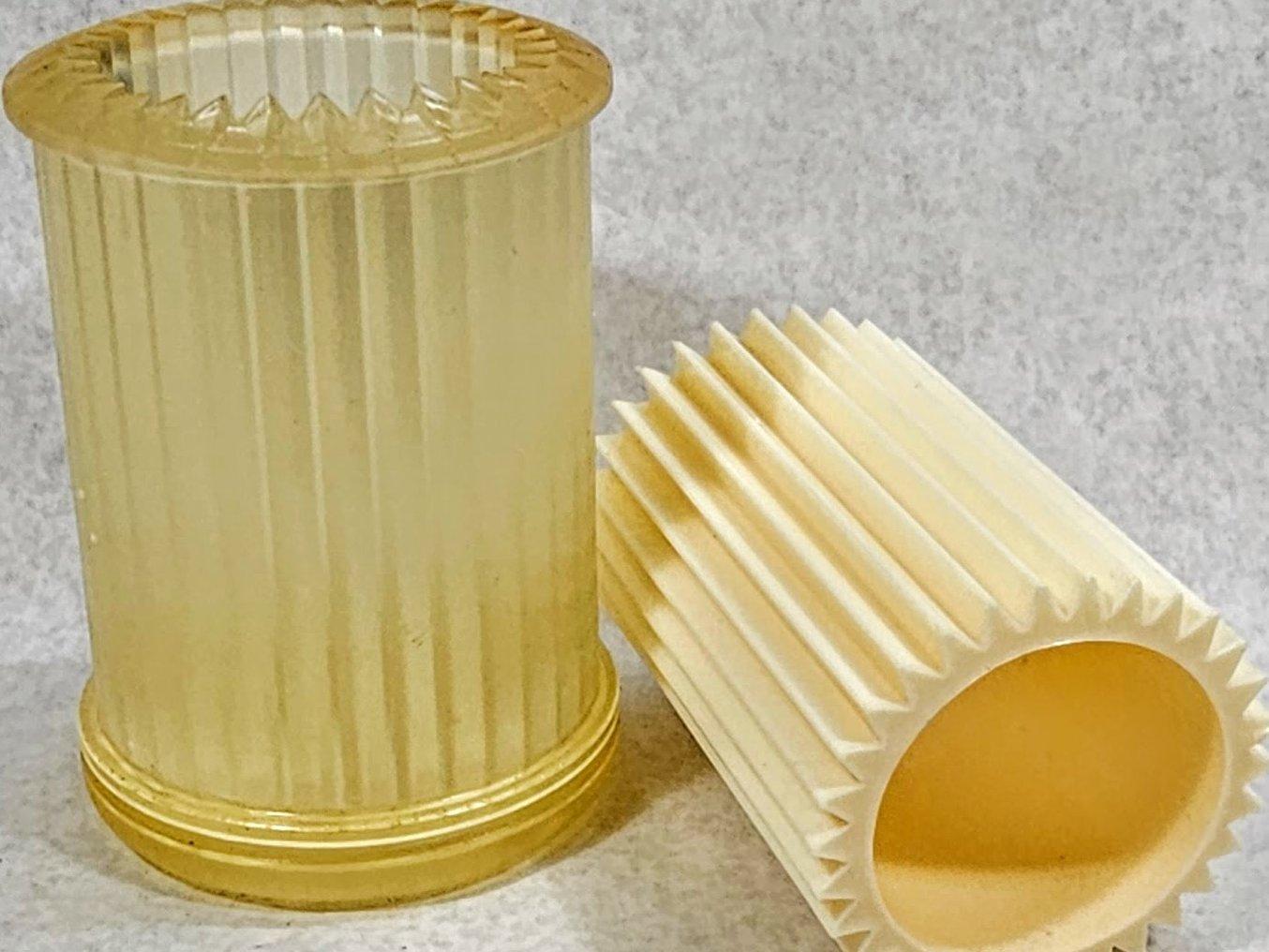
Cuando las piezas son pequeñas, mecanizar las muescas pequeñas puede ser casi imposible. Baer ha empezado a imprimir moldes con las muescas ya aplicadas, para que cada uso cree una pieza completa sin que haga falta un mecanizado adicional.
Baer reconoció la situación y se propuso intentar algo nuevo. Diseñó e imprimió un molde que daría al poliuretano la forma con muescas que necesitaban. Imprimirlo directamente en la Form 3L con la High Temp Resin o la Rigid 10K Resin ofrecía una solución rentable que eliminaba horas de trabajo manual.
Cuando se elige un material, Baer considera la resolución, la altura de capa, el coste por litro, la resistencia y el color/transparencia, para acabar eligiendo entre la High Temp Resin y la Rigid 10K Resin la mayor parte del tiempo. Para los prototipos, las piezas únicas o las aplicaciones de moldeo de muy bajo volumen, la High Temp Resin se usa por su menor coste y su transparencia; de hecho, resulta útil para los prototipos poder ver qué pasa dentro de ellos para evaluar si hay que cambiar algo. No obstante, para las piezas que se van a fundir en cantidades mayores, el equipo recurre a las propiedades mecánicas avanzadas de la Rigid 10K Resin. "Hemos estado usando la Rigid 10K Resin últimamente, principalmente porque puede soportar mejor el desmoldeo".
Mecanizado | Molde impreso en 3D | |
---|---|---|
Piezas por año | 40 | 40 |
Preparación del molde | 1 h | 1 h |
Trabajo manual por pieza después del moldeo | 3 h | 0 h |
Tiempo total | 160 h | 40 h |
Mayor capacidad y mejores productos
En menos de un año, la Form 3L ha transformado el proceso de toma de decisiones en Kastalon. Al no verse limitado ya por las restricciones tradicionales del mecanizado, el equipo de ingeniería puede aceptar pedidos que antes ni habría intentado y optimizar procesos que antes costaban miles de dólares en cuanto a mano de obra y materiales.
"Nuestro volumen de piezas ha ido creciendo. Hemos ido ganando mucha confianza y el número de pedidos para la Form 3L no ha dejado de subir. Podemos probar cosas nuevas y ayudar al equipo de ventas a dar a los clientes lo que quieren, incluso en cantidades pequeñas, solo para ver si es posible".
Brian Baer, ingeniero
Los mecanizadores de Kastalon se han labrado una reputación basada en la precisión, la fiabilidad y la excelencia. Al principio, costó convencer a la empresa de añadir moldes impresos en 3D al proceso, pero los resultados hablan por sí solos. Al haber demostrado las propiedades mecánicas, las tolerancias y la libertad de diseño posibles con la estereolitografía, hasta el responsable del taller de mecanizado está enviando piezas a la impresora.
Para saber más acerca del utillaje rápido, visita nuestra página de aplicaciones. Para ver la Form 3L, visita nuestra página de productos.