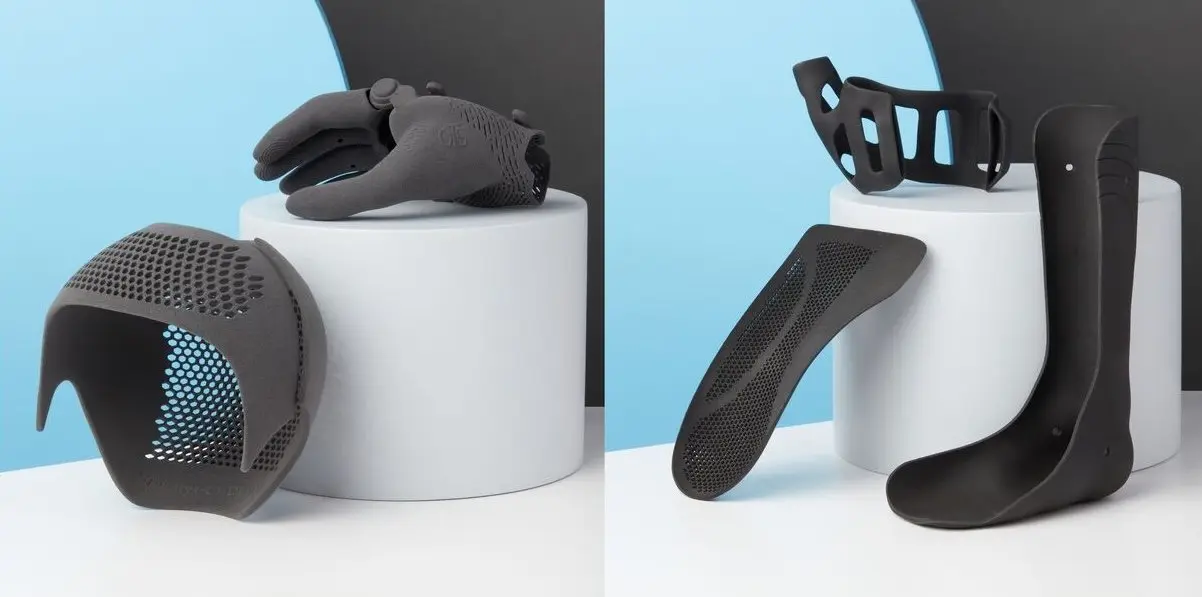
Las órtesis son productos sanitarios externos creados para tratar deformidades musculares o esqueléticas o darles apoyo. Además de proporcionar comodidad y apoyo, pueden ayudar a la movilidad o a la recuperación, aliviar el dolor y prevenir el desarrollo de problemas más permanentes.
Algunos ejemplos de órtesis comunes son los siguientes:
- Las rodilleras reducen la presión y la fuerza que soportan las rodillas durante la actividad física.
- Las órtesis de pie y tobillo estabilizan el pie y mejoran la marcha.
- Las órtesis de muñeca y mano dan apoyo a las articulaciones de estas regiones y al uso del miembro.
En la actualidad, el tamaño del mercado del sector de las órtesis es de aproximadamente 6500 millones de dólares y se prevé un índice de crecimiento anual del 4,2 %. El crecimiento de este sector sanitario está impulsado por la necesidad de mejorar la atención al paciente mediante soluciones hechas a medida. Sin embargo, los retos tradicionales de este sector incluyen que sus productos sean incómodos para el paciente y los problemas de salud causados por un ajuste deficiente en una solución estándar. La personalización alivia estas preocupaciones, permitiendo adaptar las soluciones al paciente, pero utilizar los métodos tradicionales de producción personalizada conlleva costes adicionales y largos tiempos de espera.
Muchos profesionales sanitarios están adoptando la impresión 3D de órtesis para producir soluciones ortopédicas personalizadas. Al seguir procesos de trabajo de eficacia probada, la impresión 3D puede ahorrar tiempo y recursos, permitiendo producir órtesis adaptadas a los pacientes en tiempo récord. Sigue leyendo para saber cómo las órtesis personalizadas impresas en 3D benefician tanto a la experiencia del paciente como a la eficiencia de la producción.
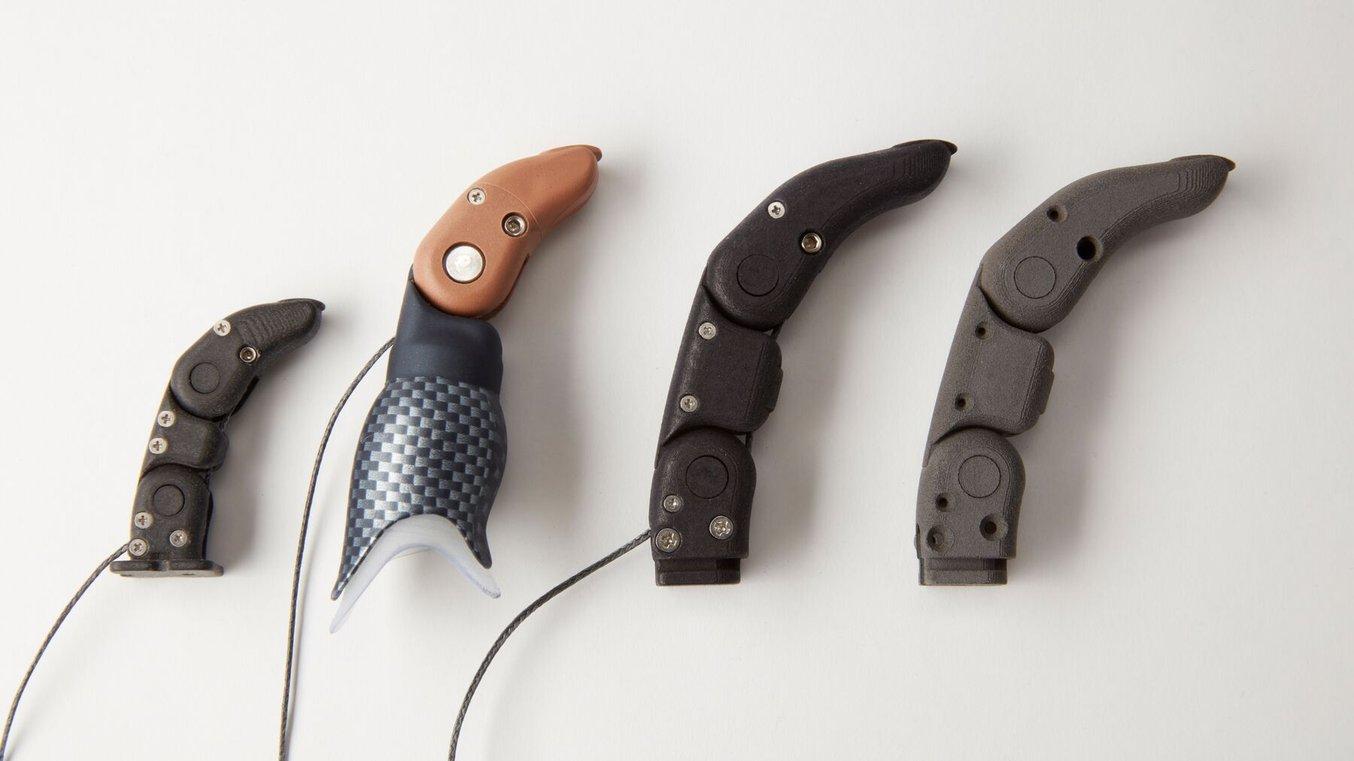
La impresión 3D en el sector de las órtesis y prótesis
Este libro blanco es una introducción al uso de la tecnología de impresión 3D para crear órtesis y prótesis de última generación.
Cómo la impresión 3D revoluciona las órtesis
El proceso tradicional para crear órtesis ha caído en una categoría de procedimientos del tipo "si no está roto, no lo arregles", como reza el dicho inglés. Los procesos de trabajo tradicionales, caracterizados por una gran exigencia de trabajo manual y de tiempo, producen las órtesis que esperan los pacientes, pero con costes añadidos, lo que indica que hay bastante que se puede mejorar.
Los procesos de trabajo digitales para las órtesis personalizadas engloban nuevas opciones de diseño, ensayo y fabricación para reducir los costes de la personalización y acelerar los ciclos de producción, con lo que se obtienen tiempos de espera menores, productos que se ajustan mejor a sus usuarios y resultados mejorados con los pacientes. Al ser conocida por su rapidez de producción y sus procesos relativamente asequibles, la impresión 3D ofrece a los interesados en el sector de las órtesis una solución eficaz que hace posible una personalización de forma rápida y económica.
Las órtesis tradicionales frente a las impresas en 3D
Las órtesis se fabrican de diversas formas, en función de cuál sea la pieza de uso final deseada. Para fabricar las órtesis se pueden utilizar procesos de fabricación tradicionales, como el moldeo en escayola, el moldeo en espuma, el mecanizado convencional, el termoformado y la fundición en cera.
Independientemente de los métodos que se utilicen, los procesos de trabajo básicos se pueden resumir de la siguiente forma:
- Se crea un mapa del paciente mediante una impronta o molde, dibujos técnicos y mediciones. Este proceso puede tardar hasta una hora en completarse.
- Se crea un modelo de desarrollo a partir del mapa topográfico. En función del proceso que se utilice, es algo que puede llevar de una a dos horas.
- El modelo se ajusta y esculpe para que se amolde al paciente. Este proceso puede requerir múltiples citas con el paciente a medida que se realizan ajustes en el modelo. Estas citas pueden durar varias horas a lo largo de varias semanas, en función del plan de tratamiento.
- Por último, la órtesis pasa por un posacabado y un acabado para prepararla para su uso.
Durante este proceso manual, los posibles errores pueden acumularse en cada fase del proceso de trabajo. Los errores a la hora de verter los moldes, las mediciones inexactas y los errores de diseño pueden alargar un proceso que ya de por sí es largo, trayendo consigo un exceso de trabajo manual, tiempos de producción prolongados y citas adicionales con los pacientes. Además, este proceso de trabajo requiere trabajo manual especializado en un entorno lleno de polvo y vapores químicos. En total, puede llevar de tres a seis semanas completar una sola personalización.
Ventajas de la impresión 3D para órtesis
El alto grado de personalización e individualización de las órtesis impresas en 3D aumenta la precisión biomecánica y la comodidad del paciente. Estos diseños se adaptan directamente a las necesidades del paciente, lo que permite ofrecer un tratamiento y una comodidad óptimos.
"Las órtesis se deben construir para una persona y deben tratar únicamente los síntomas en vez de ser soluciones estandarizadas e incómodas".
Matej Vlašič, aNImaKe
La eficiencia y asequibilidad de las órtesis impresas en 3D hacen que las soluciones hechas a medida sean accesibles a más pacientes y que resulten ventajosas para los fabricantes de ortopedia. Tras aprender los nuevos procesos de trabajo, adoptar la impresión 3D de órtesis ha demostrado una y otra vez que aumenta la productividad al tiempo que reduce los costes.
Ahorro de tiempo: Los procesos de trabajo digitales ahorran tiempo tanto para los ortesistas como para los pacientes. Los procesos de trabajo sencillos y eficaces permiten a los ortesistas y a su personal dedicar menos tiempo a crear modelos y posacabarlos y más tiempo a tareas más importantes. Los pacientes necesitan menos citas para ajustar las órtesis y menos tiempo durante las citas para recoger impresiones y mediciones.
Ahorro de costes: Al digitalizar y simplificar tu proceso de trabajo con la impresión 3D, reducirás los costes de producción, mano de obra, material, almacenamiento y transporte. Con los procesos de trabajo tradicionales, hacen falta materiales adicionales para la toma de improntas y la fabricación de moldes, por no hablar del almacenamiento de todos estos materiales. La impresión 3D elimina esta necesidad. Además, el posacabado de las órtesis impresas en 3D ahorra trabajo manual para aumentar la eficiencia.
Proceso de trabajo simplificado: Los procesos de trabajo digitales requieren menos trabajo manual e incluyen menos pasos, eliminando secuencias enteras de procesos manuales, como varias de las visitas de los pacientes para los ajustes de las órtesis. Además, la impresión por lotes permite imprimir varias órtesis a la vez, dependiendo del tamaño de los aparatos que se impriman y de qué tipo sean.
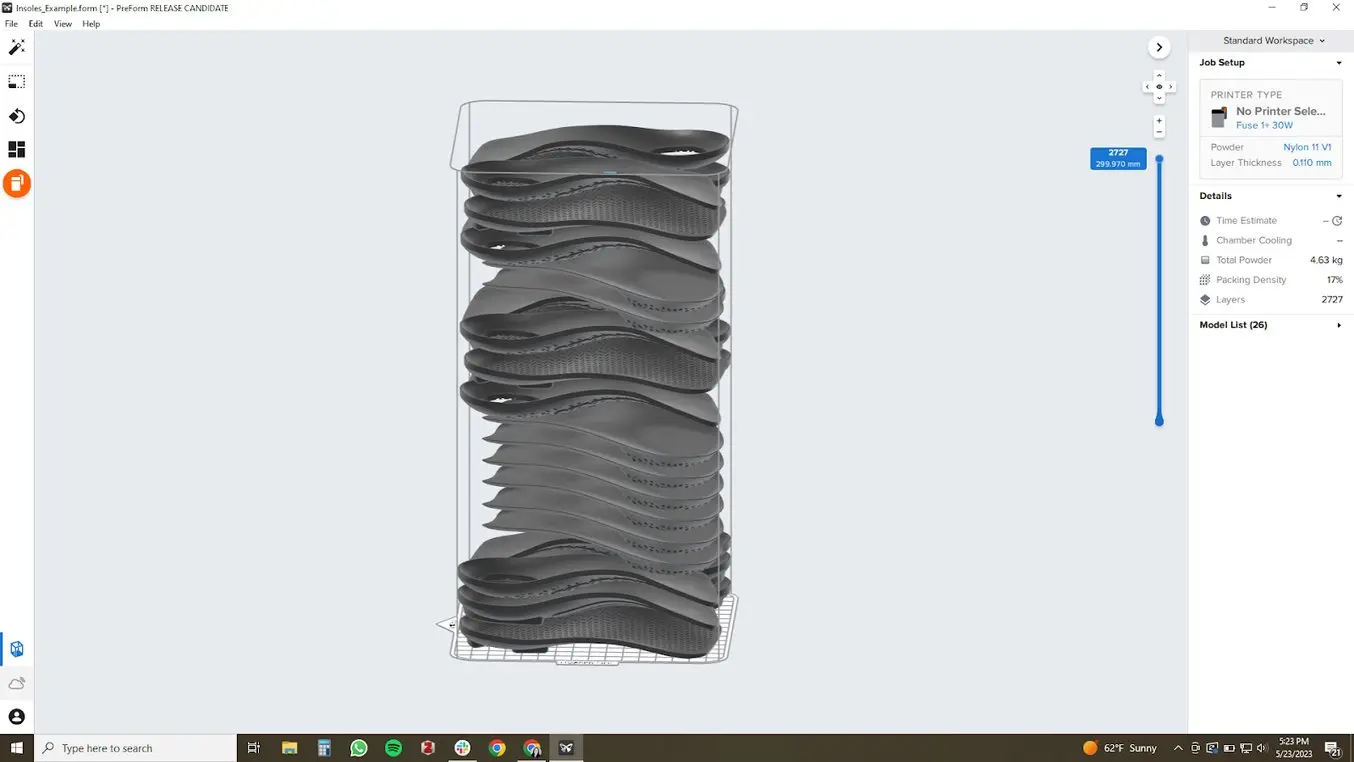
La impresión 3D SLS permite imprimir muchas piezas en una sola impresión, lo que aumenta la eficiencia y reduce los costes.
Logística mejorada: La digitalización simplifica la gestión logística. Se puede tomar un escaneo 3D en cualquier lugar y enviarlo a distancia para usarlo en el modelado y el diseño digital. Una vez diseñados, los archivos digitales se pueden enviar directamente a una impresora, independientemente de si esta se encuentra en las mismas instalaciones o fuera de ellas.
Sostenibilidad: Con el proceso de trabajo digital, se necesita mucha menos materia prima para producir el producto final, ya que se elimina la creación de una réplica o modelo físico. La impresión 3D mediante sinterizado selectivo por láser (SLS), que se utiliza para la producción de múltiples tipos de órtesis, permite reciclar el polvo de impresión en la siguiente impresión para reducir o incluso eliminar el desperdicio. A diferencia de los métodos tradicionales de producción, en los que hay que desechar modelos y plásticos, la impresión 3D minimiza el desperdicio y reduce el uso de productos químicos agresivos.
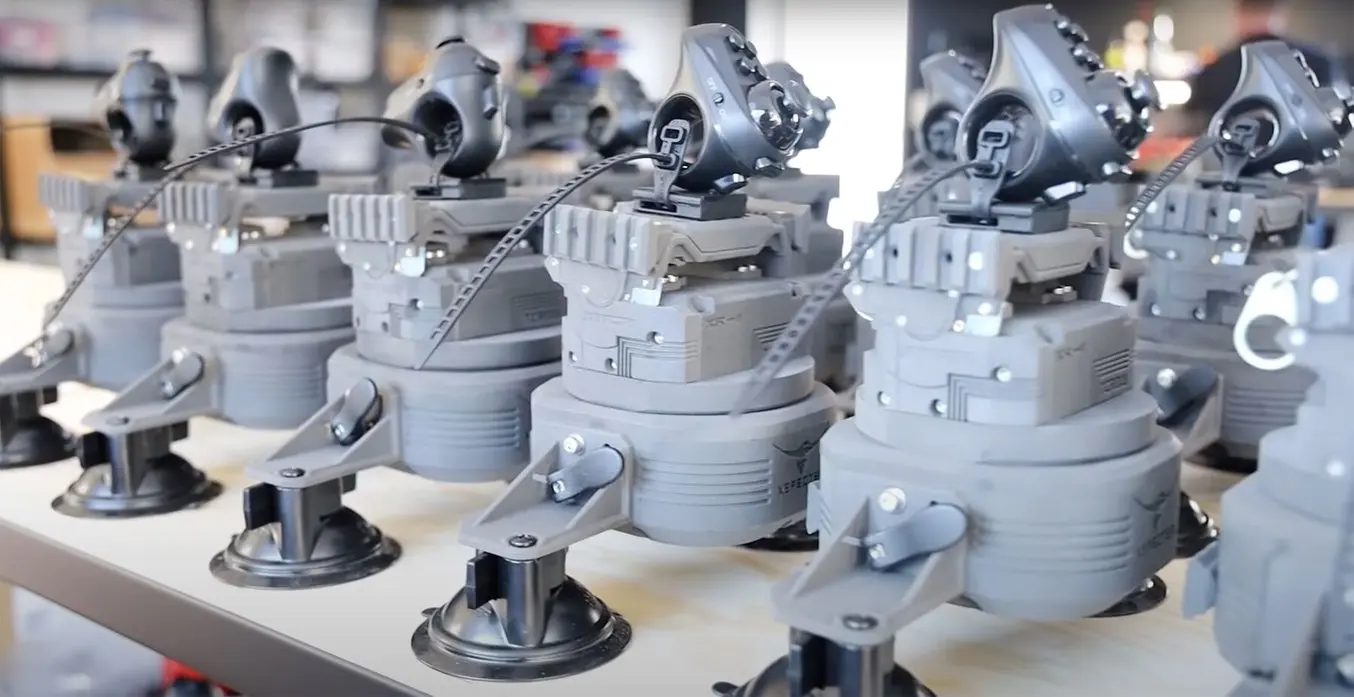
SLS para la producción de uso final
La impresión 3D para una producción de uso final no solo es posible, sino que es más asequible, ágil y escalable que nunca con el ecosistema SLS Fuse de Formlabs. Visita nuestra página de SLS para la producción, donde podrás comparar los métodos de producción, conocer los precios a granel del polvo de impresión y ver la producción en acción con 15 fabricantes diferentes que están usando actualmente la serie Fuse.
Aplicaciones de las órtesis impresas en 3D
Las órtesis pueden tratar diversos problemas. Las diferencias en el tamaño y la forma de la anatomía del paciente, además de los requisitos de cada órtesis, hacen que las órtesis estándar puedan resultar incómodas y no ajustarse bien, lo que puede afectar a su ponibilidad y eficacia, e incluso causar problemas secundarios. Las órtesis estándar son tradicionalmente menos caras que las soluciones personalizadas, ya que se producen en masa con tallas uniformes. Sin embargo, esto se hace a costa de la comodidad del paciente y, a menudo, de su eficacia. Por lo tanto, las órtesis personalizadas son necesarias para una serie de aplicaciones clave, como las siguientes.
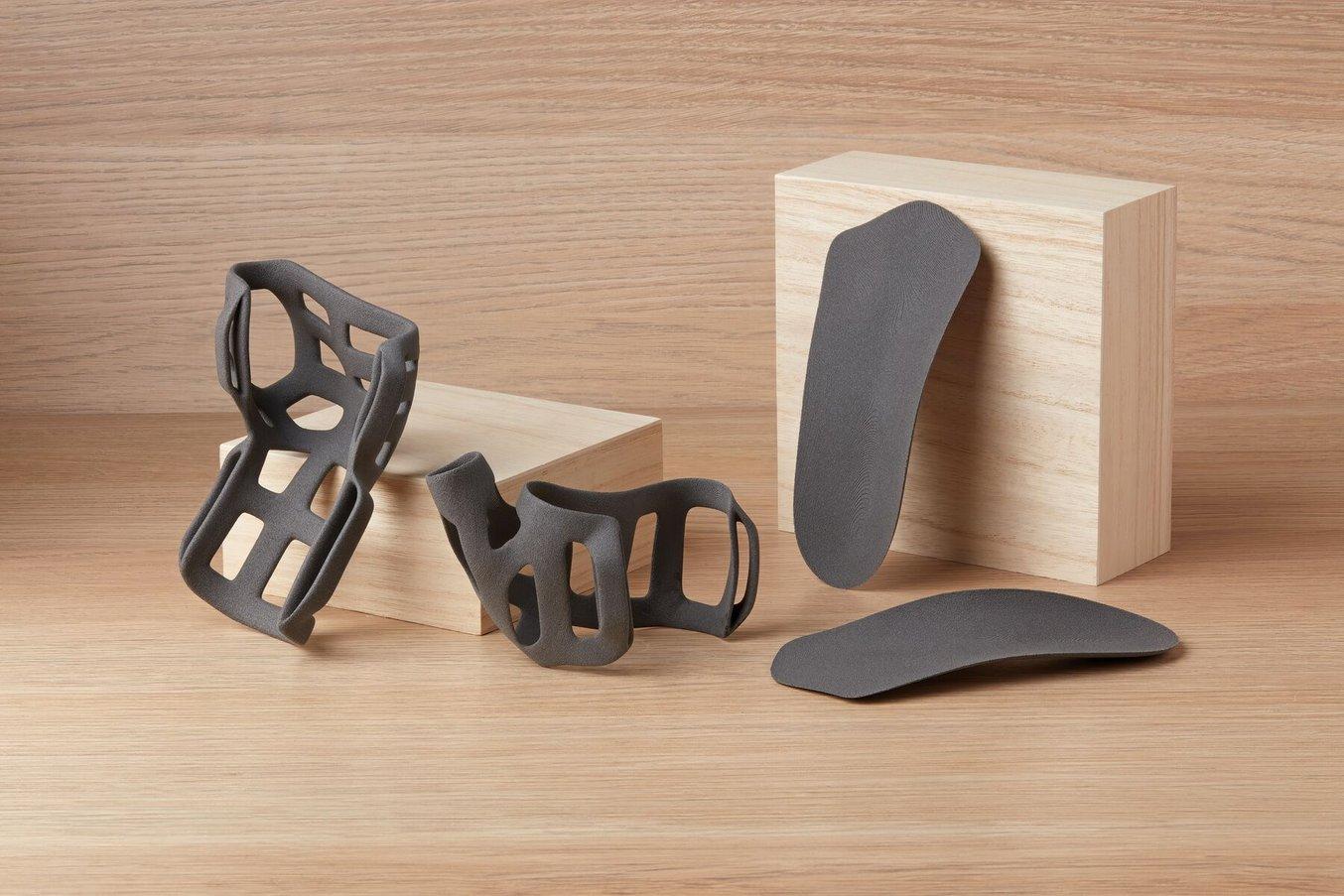
Ejemplos de una órtesis de muñeca, una órtesis de mano y plantillas ortopédicas impresas con la impresora SLS Fuse 1+ 30W.
Plantillas: Las plantillas ortopédicas u órtesis de pie se introducen en el zapato para dar apoyo. Pueden corregir problemas relacionados con los pies y reducir el dolor. A quienes sufren dolor o molestias por juanetes, artritis, pie cavo o fascitis plantar se les pueden prescribir plantillas ortopédicas.
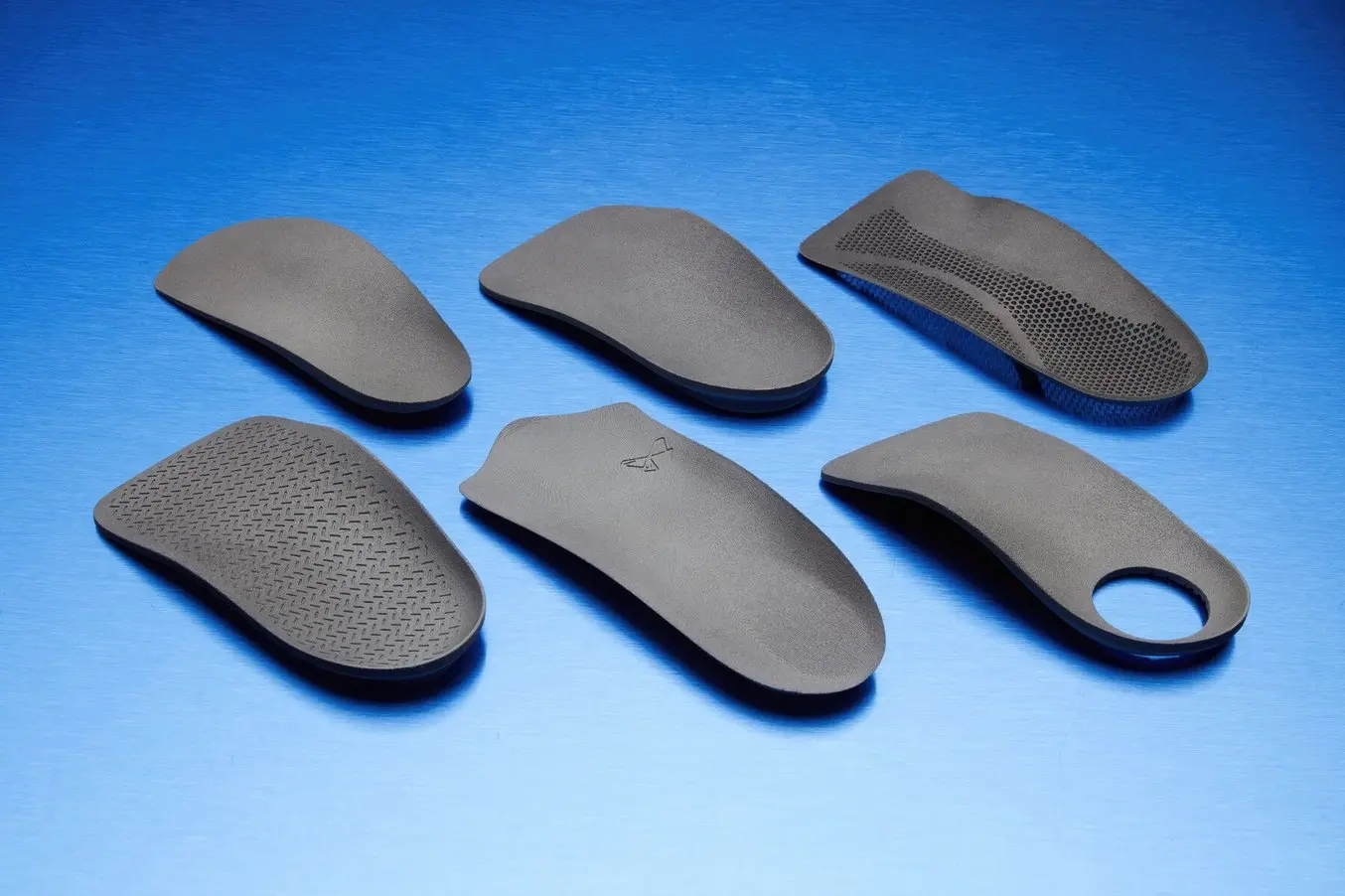
Revoluciona tu producción de plantillas con la Fuse 1+ 30W de Formlabs
Aumenta tu producción de plantillas al mismo tiempo que ahorras tiempo y dinero. En este seminario, hablamos de por qué la Fuse 1+ 30W es la solución perfecta para empezar a pasar a la fabricación digital o expandir tu producción de forma asequible y eficiente.
Órtesis de muñeca y mano: Las órtesis para muñeca y mano inmovilizan las articulaciones para el tratamiento de determinados problemas, como fracturas, artritis, lesiones de ligamentos, injertos de piel, deformidades, tendinitis y esguinces. Una órtesis puede limitarse a solo el pulgar o los dedos, a la mano, o abarcar toda la parte inferior del brazo, en función del plan de tratamiento.
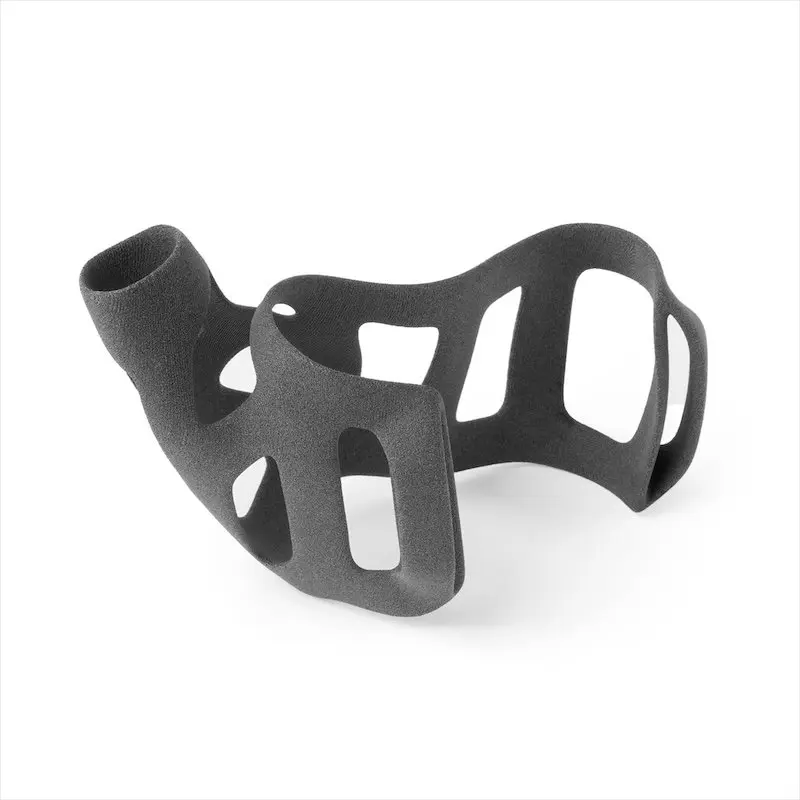
Órtesis de mano para inmovilizar el pulgar.
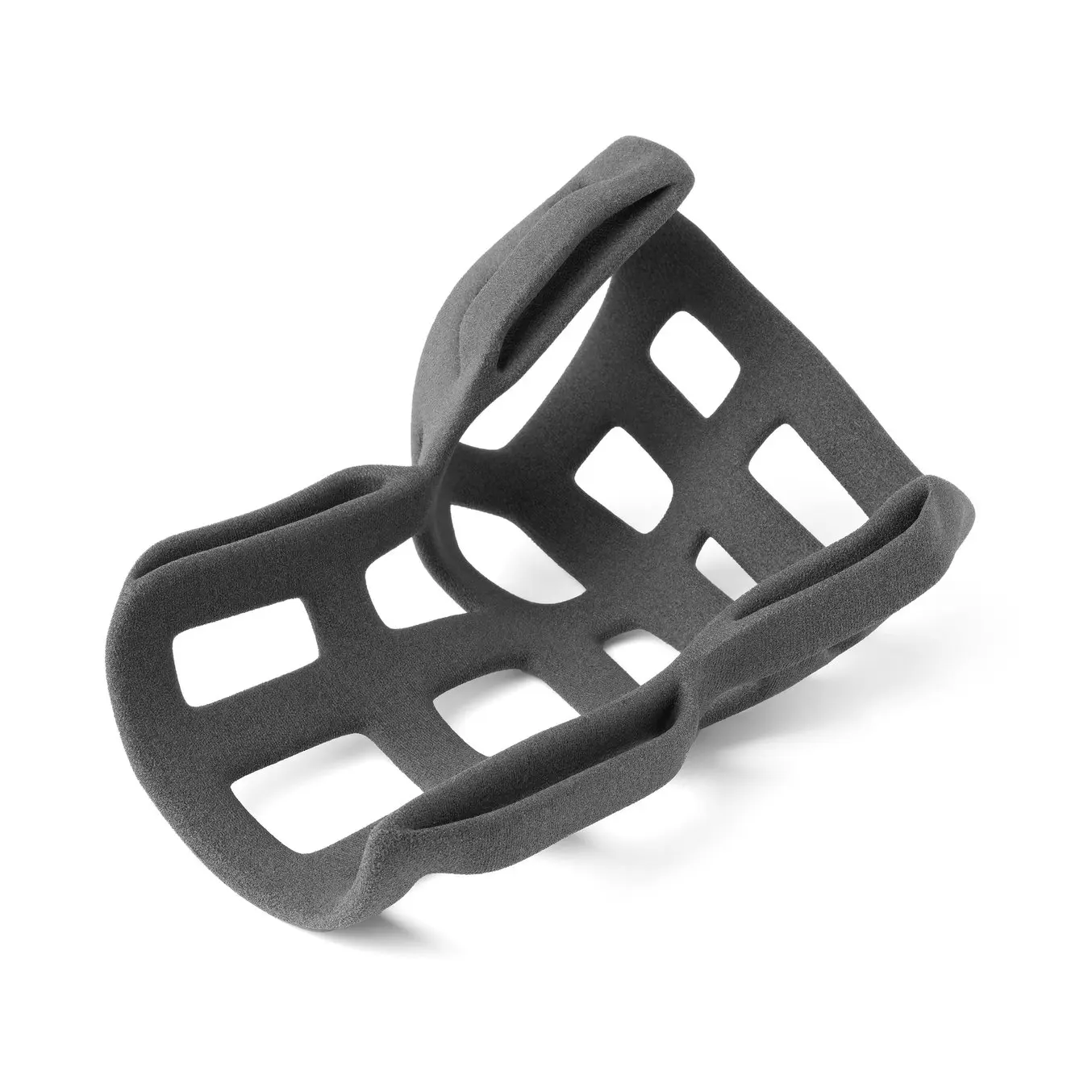
Órtesis de muñeca impresa con la impresora SLS Fuse 1+ 30W.
Ortesis de pie y tobillo: Para ayudar a la movilidad de los pacientes con problemas de control motor de las extremidades, se pueden prescribir órtesis de pie y tobillo para corregir la alineación o dar apoyo. Estas afecciones pueden deberse a diversos trastornos neurológicos y musculoesqueléticos, como un ictus, una parálisis cerebral y la esclerosis múltiple, y afectan a personas de todas las edades.
Cascos de remodelación craneal: Estas órtesis son aparatos similares a cascos para bebés menores de 18 meses con plagiocefalia o deformidades de la cabeza (en la mayoría de las ocasiones, causadas por pasar demasiado tiempo tumbados sobre la espalda) y sirven para corregir y proteger la cabeza. El Nylon 11 Powder, impreso con la impresora 3D Fuse 1+ 30W de sinterizado selectivo por láser (SLS), se puede utilizar para el componente exterior rígido. En el interior, se puede usar el TPU 90A Powder para crear una capa acolchada.
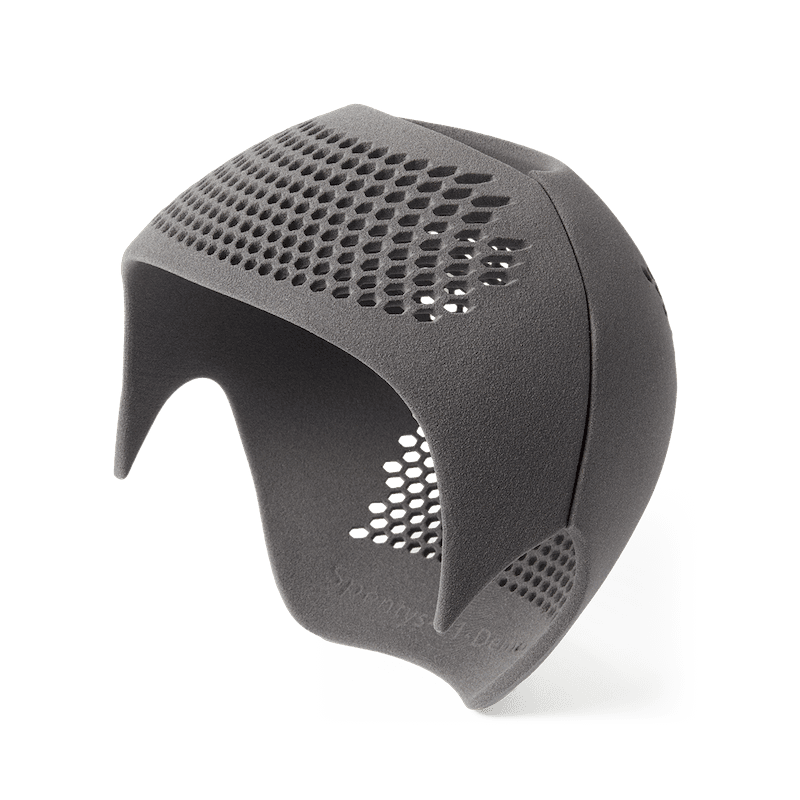
Un casco de remodelación craneal impreso en TPU 90A Powder.
Máscaras de protección de la nariz: Las máscaras para proteger la nariz o la cara se suelen prescribir tras fracturas de la nariz o de otras partes de la cara. Un método para producir máscaras de protección de la nariz es la impresión 3D SLS con el Nylon 11 Powder. Es posible imprimir máscaras transparentes (que se piden con frecuencia por motivos estéticos) con la impresión 3D por estereolitografía (SLA). Si imprimes mediante SLA, la BioMed Durable Resin es una opción transparente y resistente a los impactos para impresoras 3D SLA Form 3+/3L.
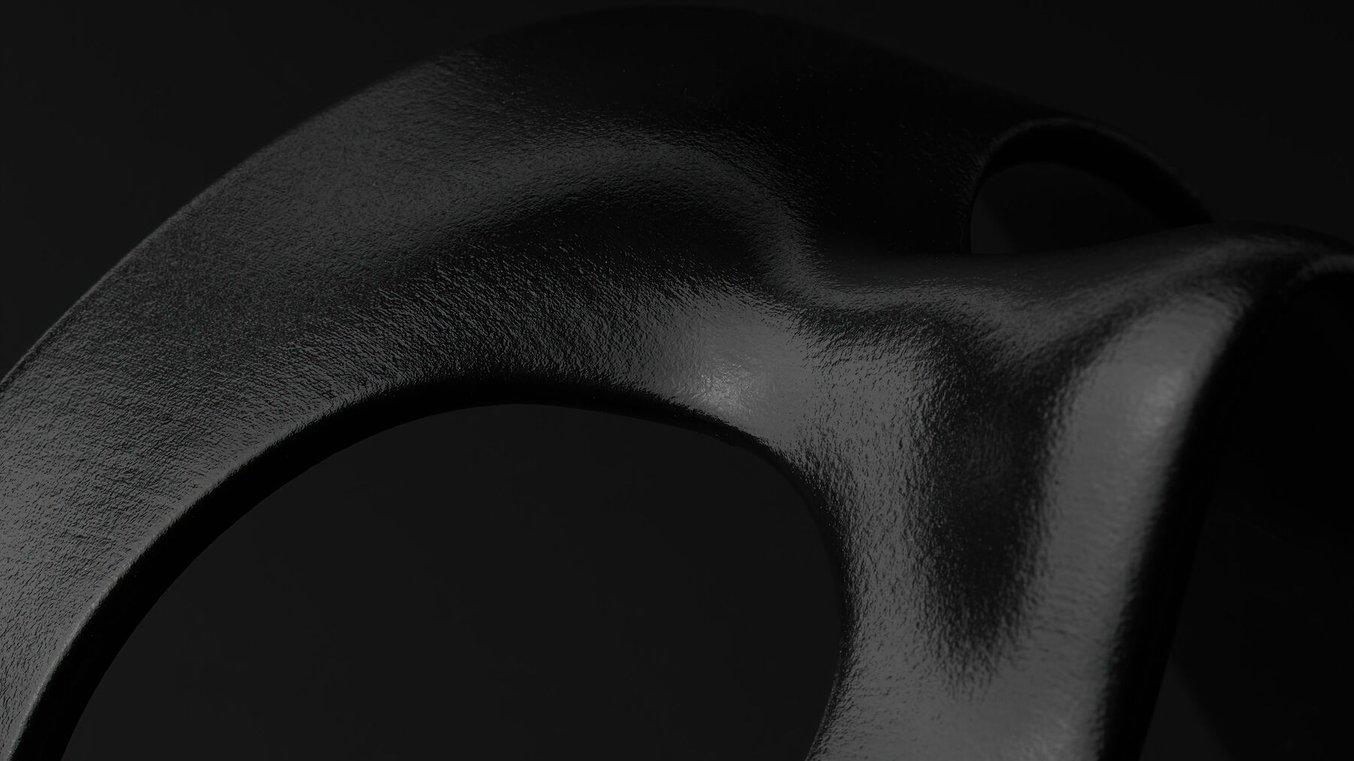
Primer plano de una máscara de protección de la nariz impresa con el Nylon 11 Powder que se ha posacabado alisándola con vapor.
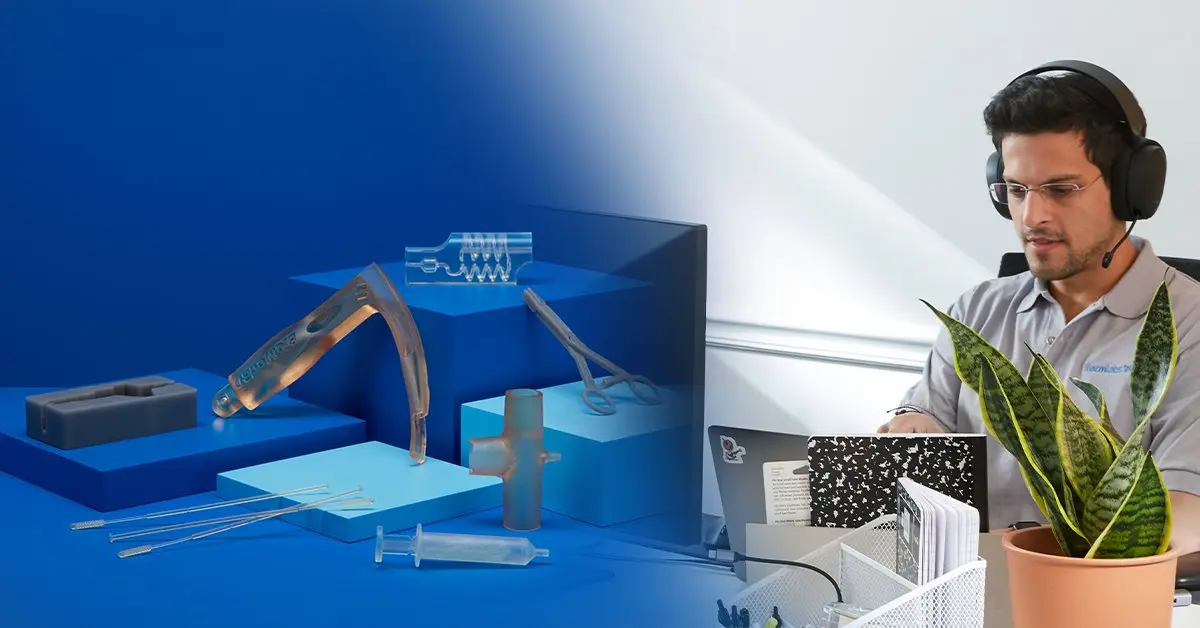
Habla con nuestro equipo de ventas para el sector médico
Independientemente de si lo que necesitas es fabricar herramientas quirúrgicas adaptadas a los pacientes o crear prototipos para un producto sanitario cardíaco, nosotros estamos aquí para ayudarte. El equipo Formlabs Medical es un grupo de especialistas que saben exactamente cómo ofrecer la asistencia que tu negocio y tú necesitáis.
Proceso de trabajo digitales para fabricar órtesis personalizadas con la impresión 3D
La fabricación de órtesis personalizadas mediante impresión 3D requiere un escáner 3D, un software CAD y una impresora 3D con un material compatible. Hay varias opciones para cada una de estas herramientas en función del tipo de órtesis, el volumen de producción, los usos previstos, el proceso de trabajo, el espacio y la inversión inicial. Sin embargo, utilizar la impresión 3D para crear órtesis personalizadas es ahora más accesible que nunca.
1. Escaneo
El primer paso para crear órtesis impresas en 3D es capturar una imagen o un escaneo de la anatomía del paciente que requiere la órtesis. A continuación, estos datos anatómicos se traducen en un modelo 3D digital, que se puede utilizar para diseñar la órtesis.
En comparación con los procesos tradicionales de toma de impresiones y creación de modelos, el escaneo 3D ofrece una gran precisión, una mayor velocidad de captura, una reducción del trabajo manual y flexibilidad a la hora de elegir ubicaciones de captura. Hay varios fabricantes de escáneres digitales que ofrecen soluciones para crear órtesis impresas en 3D. Los escáneres 3D para aplicaciones ortopédicas abarcan una amplia gama de precios y tecnologías, como LiDAR, TAC en carga, infrarrojos y láser. Encontrarás más información sobre las opciones disponibles específicamente para plantillas ortopédicas en esta guía.
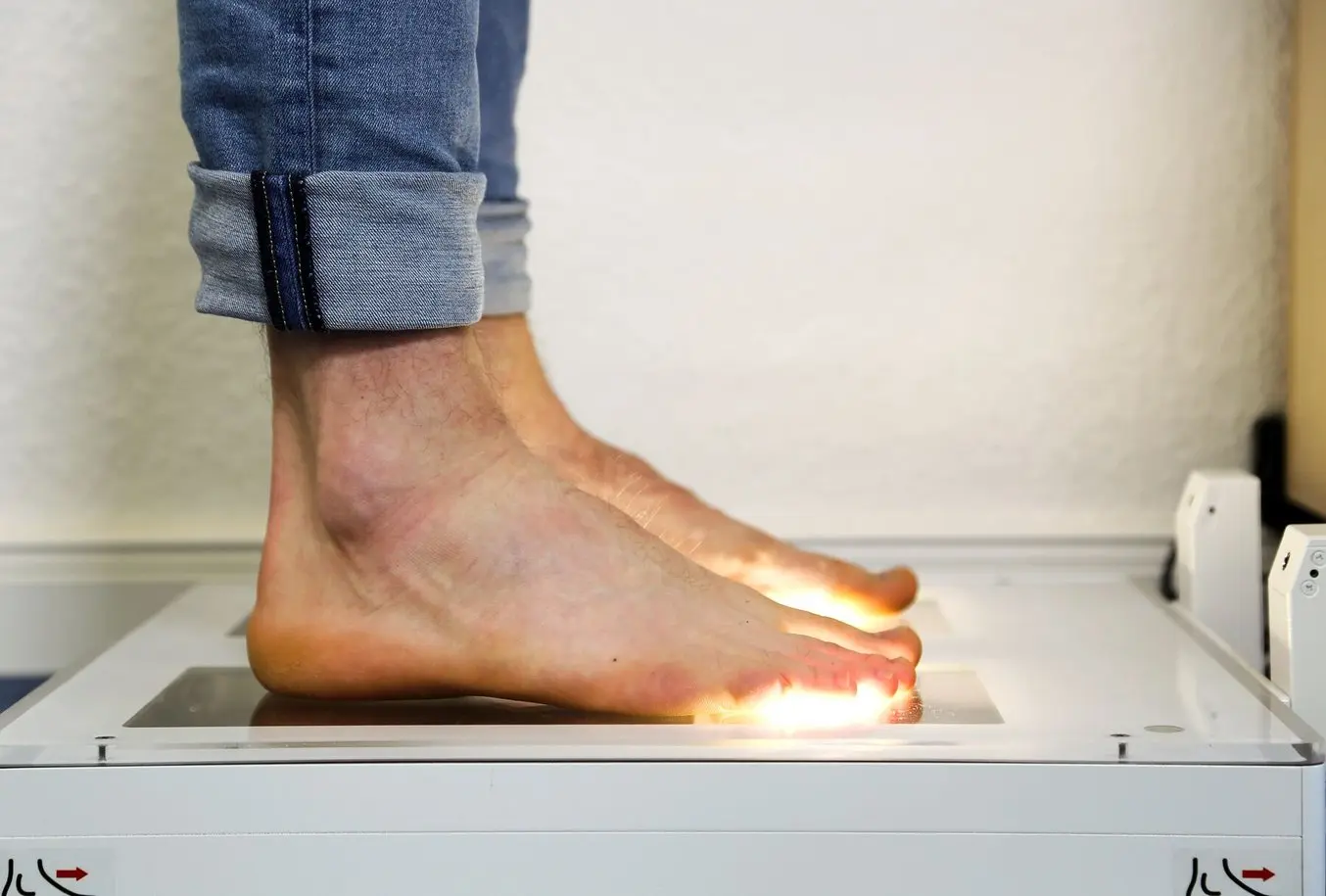
El escaneo 3D captura una impronta del pie más precisa y completa que los métodos tradicionales.
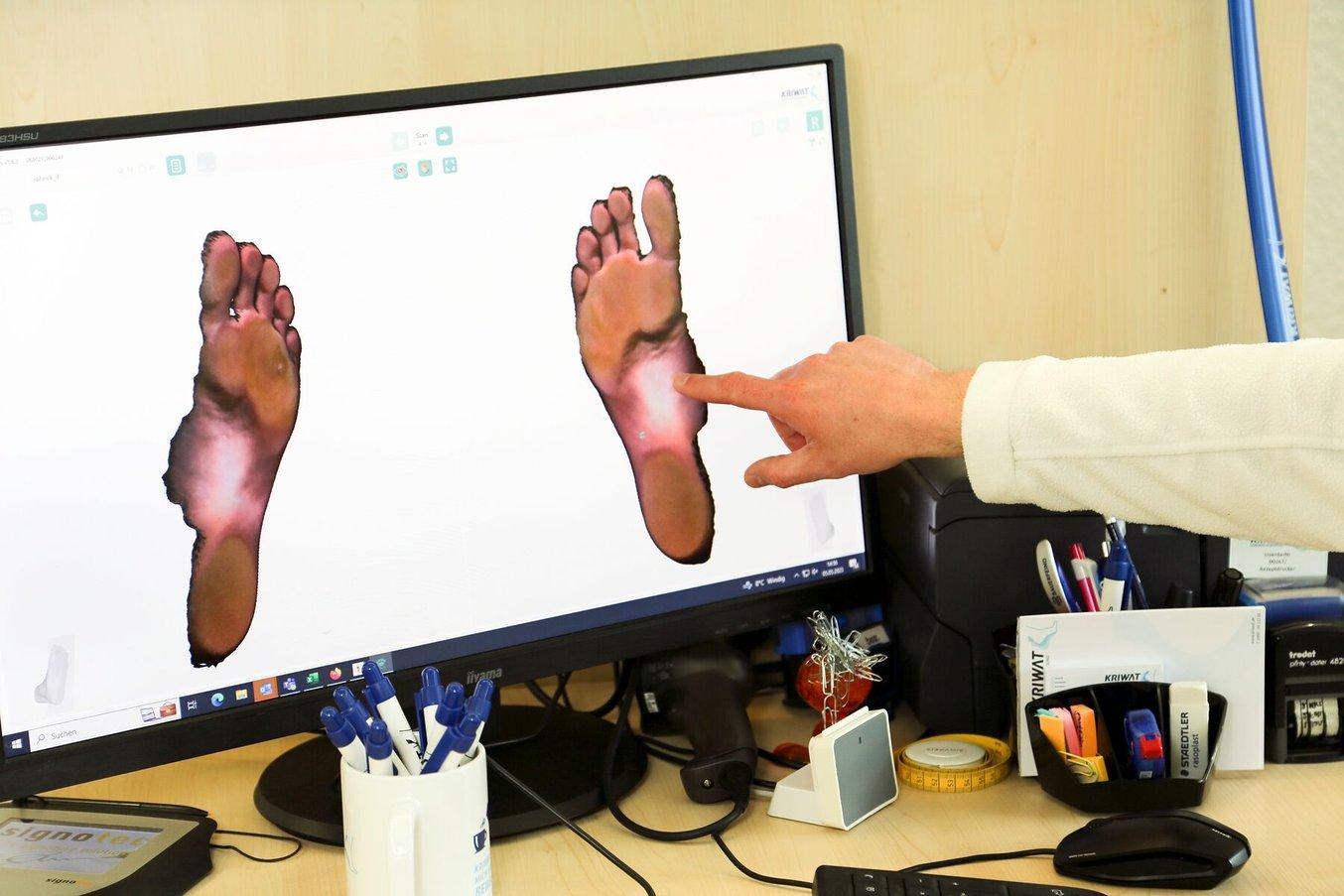
Escanear facilita el envío digital de los datos para su diseño e impresión.
2. Modelado digital
Una vez que el escaneo ha capturado los datos necesarios, hay que desarrollar un modelo preciso utilizando software CAD o CAM. Se pueden utilizar diversos programas para el diseño, en función del uso específico de la órtesis, y están disponibles en varios proveedores. Al estar centrados en la precisión, la facilidad de uso y la personalización, algunos de estos programas permiten diseñar una órtesis en cuestión de minutos. Si necesitas más información sobre los distintos programas de CAD disponibles para diseñar específicamente plantillas ortopédicas, lee nuestra guía.
En la mayoría de los casos, los datos adquiridos se deben modificar mediante reparaciones de la malla para desarrollar modelos imprimibles en 3D para la siguiente fase del proceso de personalización. Una vez completado el diseño, se guarda como un archivo STL, OBJ o 3MF, y se importa en un software de preparación de impresiones, como PreForm.
Para optimizar el proceso de trabajo, se pueden imprimir varios aparatos ortésicos en una sola impresión, dependiendo del tamaño y la orientación de los aparatos.
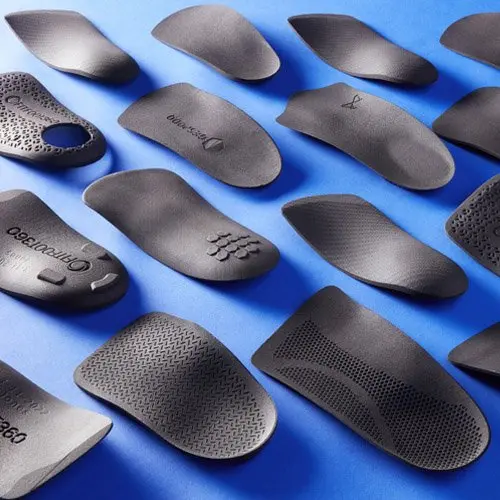
Impresión 3D de bases rígidas para plantillas ortopédicas
Descubre cómo producir bases fuertes y dúctiles para plantillas ortopédicas que superen los 4 millones de ciclos de flexión, con el ecosistema SLS compacto y asequible de Formlabs. Esta guía exhaustiva te ayudará a empezar a producir bases para plantillas ortopédicas con la Fuse 1+ 30W.
3. Impresión 3D de órtesis
Los proveedores de servicios ortopédicos y sanitarios pueden aprovechar la diversa tecnología de impresión 3D disponible para producir artículos acabados. La aplicación de la pieza de uso final, su tamaño, el volumen de producción y las complejidades del diseño son algunos de los criterios importantes que hay que tener en cuenta al elegir una tecnología de impresión.
La impresión 3D SLS es una solución rentable y de alta calidad para hacer órtesis personalizadas impresas en 3D. Las impresoras SLS tienen la capacidad de imprimir varias órtesis en una misma remesa de impresión y ofrecen una amplia gama de materiales biocompatibles, que incluyen opciones tanto flexibles como rígidas. Con el SLS se pueden fabricar órtesis resistentes y geometrías complejas con gran precisión. A diferencia de otros tipos de impresión 3D, el SLS no requiere estructuras de soporte y tiene un proceso de trabajo optimizado de principio a fin, desde la configuración hasta las piezas acabadas.
La impresión 3D por fusión multijet (MJF) es una alternativa similar al SLS. Aunque produce piezas de alta calidad, tiene unos costes de inversión inicial mucho más elevados que el SLS, por lo que únicamente es accesible para los mayores laboratorios y fabricantes de órtesis.
Para algunas aplicaciones, como los interiores de los cascos de remodelación craneal o cuando se requiere una máscara transparente de protección de la nariz, se suele utilizar la impresión 3D SLA. Por último, el modelado por deposición fundida (FDM) es una tecnología de impresión 3D de bajo coste que puede utilizarse para prototipado, pero carece de la durabilidad necesaria para las órtesis de uso final.
Habla con un experto en impresión 3D para saber qué tecnología es la mejor para alcanzar tus objetivos.
Selección de materiales para la impresión 3D de órtesis
Al seleccionar materiales para órtesis impresas en 3D con SLS, se deben tener en cuenta propiedades específicas en función de la aplicación de la órtesis y las necesidades del paciente, como la durabilidad, la flexibilidad, la elasticidad y la rigidez. Dos materiales del catálogo de Formlabs, el TPU 90A Powder y Nylon 11 Powder, son ideales para la producción de órtesis.
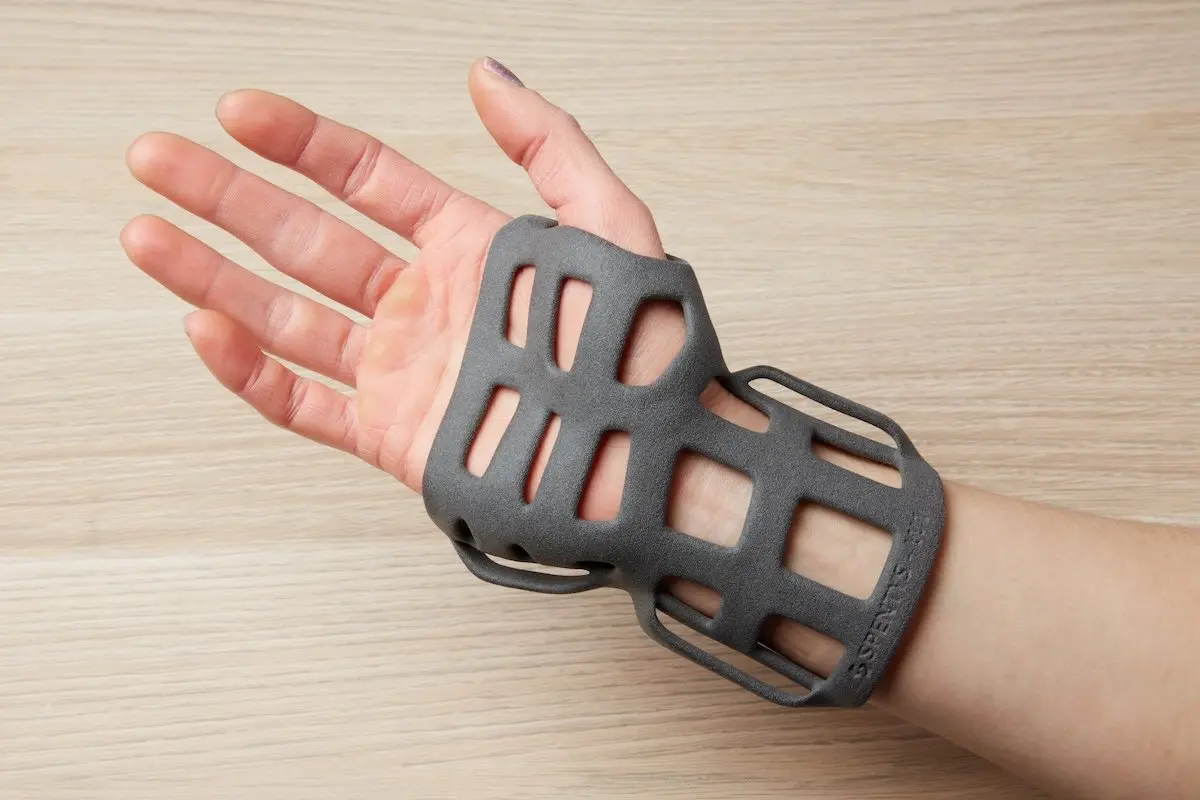
Una órtesis de muñeca impresa en la impresora 3D SLS Fuse 1+ 30W.
El TPU 90A Powder es un elastómero flexible que combina la alta resistencia al desgarro y el gran alargamiento de rotura de los materiales de goma con la libertad de diseño y la durabilidad de la impresión 3D SLS. El TPU o poliuretano termoplástico es un termoplástico elastomérico muy utilizado. En la ortopedia, este material seguro para la piel suele tener los siguientes usos:
- Prototipos de productos sanitarios y productos sanitarios y componentes de los mismos de uso final
- Almohadillas y cavidades ortopédicas
- Tecnología ponible
- Cascos de remodelación craneal
El Nylon 11 Powder es un material ideal para imprimir órtesis rígidas con gran ductilidad y estabilidad a largo plazo, entre las que se encuentran bases de plantillas ortopédicas. Además, las piezas impresas con el Nylon 11 Powder tienen una gran estabilidad ambiental, absorben muy poca humedad y son resistentes a la luz, el calor y los productos químicos. Las órtesis impresas con el Nylon 11 Powder están certificadas como compatibles pueden entrar en contacto con la piel, por lo que son ideales para las máscaras de protección de la nariz. Este material duradero y seguro para la piel suele tener los siguientes usos para órtesis y productos sanitarios:
- Plantillas deportivas y correctoras
- Órtesis de pie y tobillo
- Máscaras de protección de la nariz
- Férulas
- Prototipos de productos sanitarios y productos sanitarios y componentes de los mismos de uso final
Para demostrar la resiliencia del Nylon 11 Powder, se compararon las plantillas impresas con él en impresoras de Formlabs con plantillas de polipropileno fabricadas de forma tradicional. Las plantillas ortopédicas de Formlabs demostraron poseer una durabilidad excelente y resistencia a un uso intensivo, al mismo tiempo que mantiene una rigidez uniforme. En un ensayo de flexión dinámica en tres puntos, las plantillas de Formlabs impresas con el Nylon 11 Powder sobrevivieron al equivalente de 10 959 pasos diarios durante 365 días, lo que supera con creces los pasos dados por un adulto medio. Para ver los resultados completos del análisis del rendimiento mecánico, descarga el libro blanco.
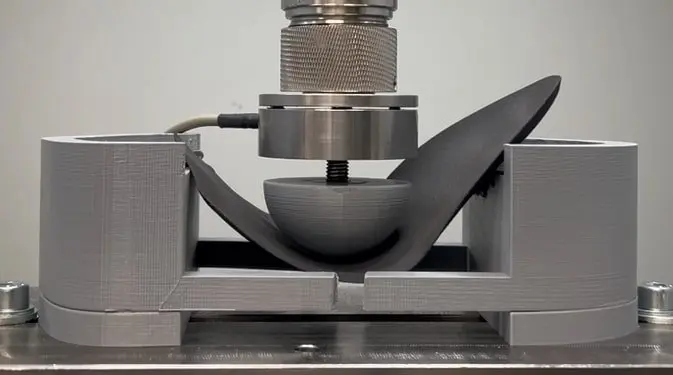
Análisis de rendimiento mecánico de bases de plantillas rígidas impresas en 3D y fabricadas de forma tradicional
Este estudio investiga las propiedades de los materiales y los métodos de fabricación utilizados para hacer plantillas ortopédicas personalizadas: la Fuse 1+ 30W y el Nylon 11 Powder de Formlabs, el HP 3D de alta reutilización PA 11 y el polipropileno fabricado de forma tradicional.
4. Acabado y posacabado
Las órtesis impresas en 3D requieren un posacabado y a menudo también se ensamblan con componentes disponibles en el mercado, como cubiertas y almohadillas. Los procesos de trabajo de posacabado varían en función tanto del tipo de impresión como del acabado deseado. También pueden añadirse correas, acolchados y tejidos, en función de los requisitos de la órtesis final.
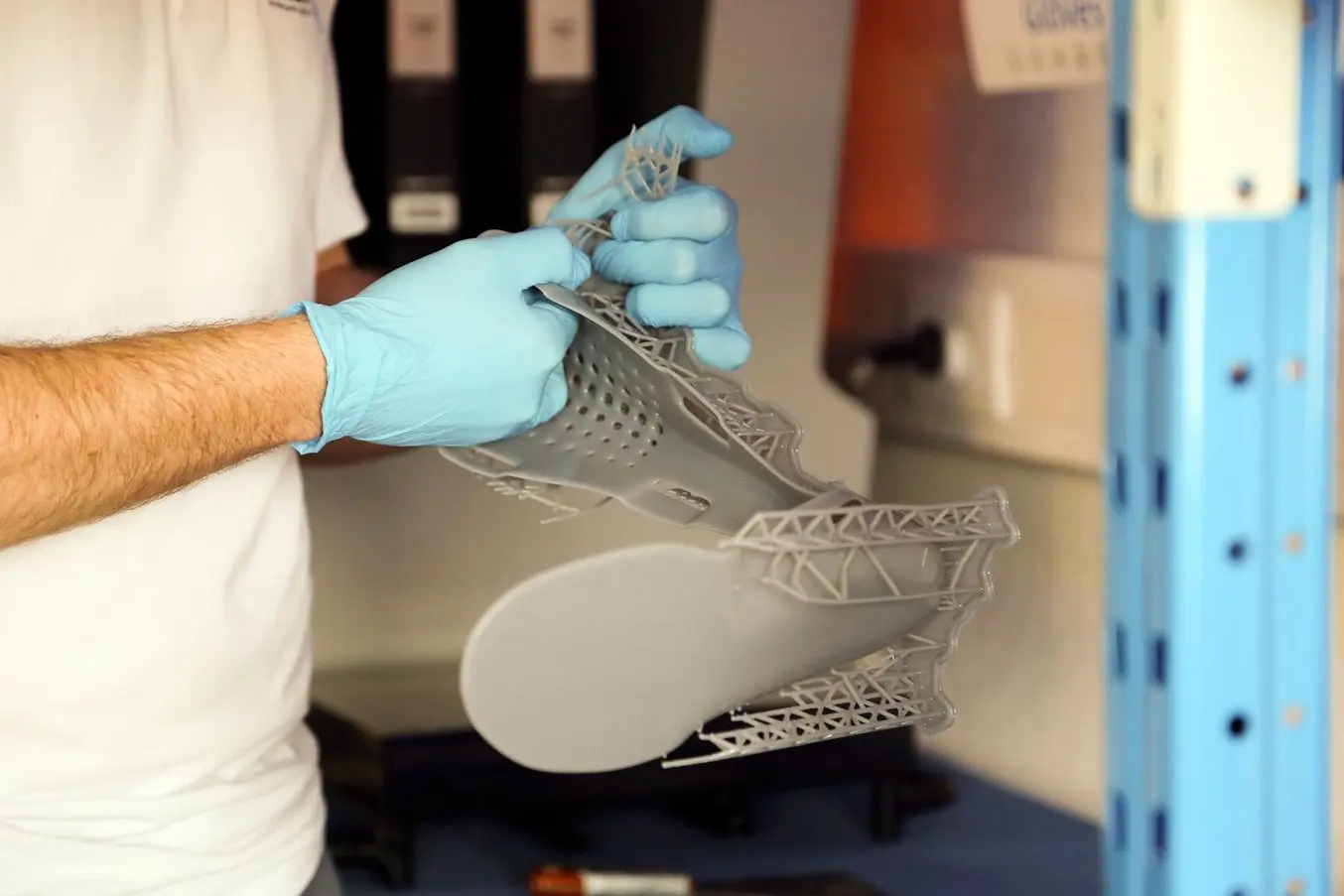
Eliminación de soportes de una órtesis impresa en una impresora 3D SLA Form 3BL.
Las órtesis impresas mediante SLA se lavan con alcohol isopropílico antes de eliminar los soportes impresos. A continuación, las impresiones se curan durante un tiempo determinado, en función de la resina utilizada para la impresión. Explora las instrucciones completas de posacabado para las impresoras SLA Form 3+/3BL aquí.
Para la impresión 3D SLS y con la Fuse 1+ 30W, la Fuse Sift ofrece un sistema de gestión del polvo todo en uno que puede ventilar y tamizar el polvo. Las piezas acabadas salen de la Fuse Sift con un acabado de la superficie ligeramente rugoso, ideal para aplicarle aditivos adhesivos y soluciones de revestimiento, que se pueden añadir para crear el producto final.
Si buscas una solución de limpieza y pulido totalmente automatizada, la Fuse Blast permite llevar a cabo una limpieza automática o manual, consiguiendo hacer que las impresiones estén limpias al tacto en tan solo 10 minutos con la limpieza automatizada. La función automatizada es totalmente automática e incluye rutinas preprogramadas para facilitar aún más la producción. Una función de pulido adicional también puede dar a las piezas un acabado liso.
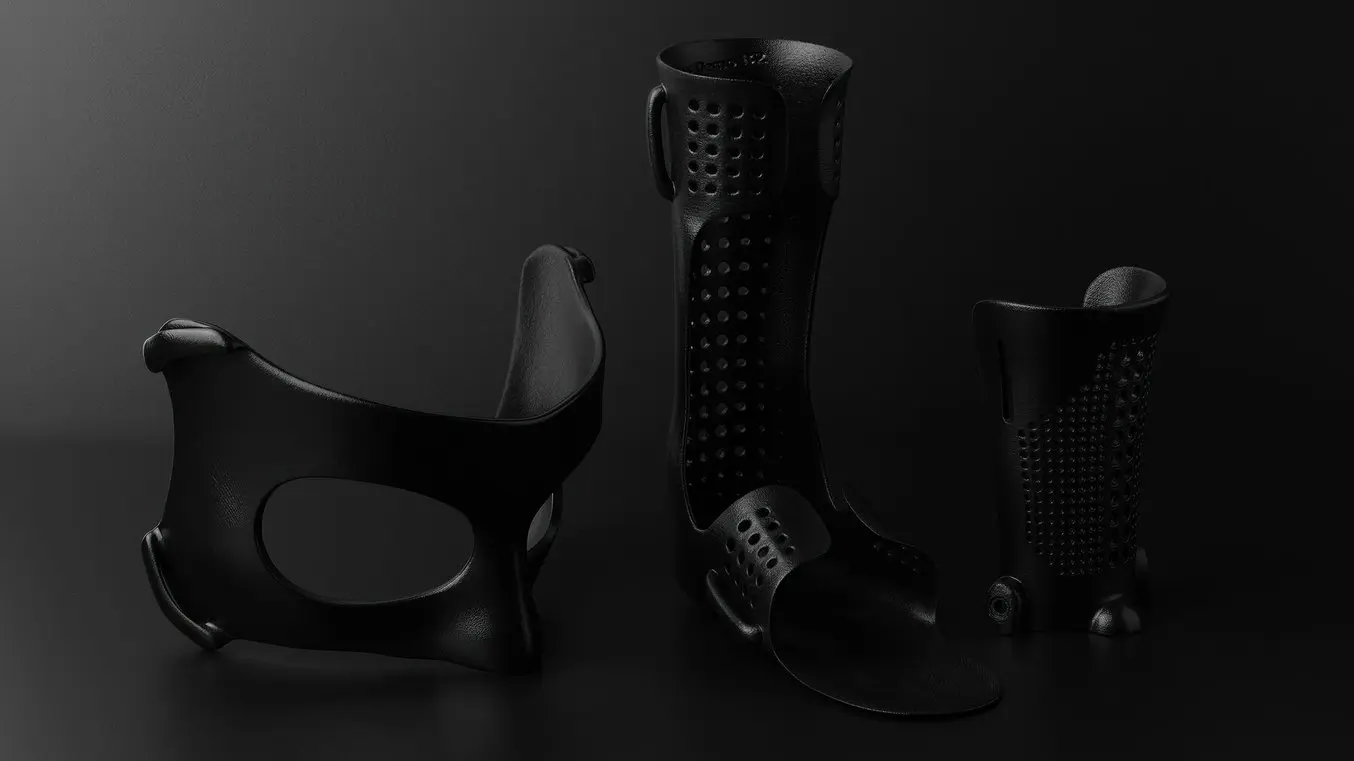
Órtesis impresas con el Nylon 11 Powder a las que se les ha dado un acabado mediante alisado con vapor.
Para las órtesis que requieren un acabado de la superficie liso, el alisado con vapor es un paso habitual del posacabado de las piezas impresas en 3D mediante SLS que puede mejorar la porosidad y reducir la rugosidad. El alisado con vapor también reduce en gran medida la fricción que pueden sentir los pacientes que llevan aparatos ortopédicos. Este proceso químico consiste en exponer la superficie de una pieza impresa en 3D mediante SLS a un disolvente vaporizado. Mediante el alisado con vapor, las impresiones SLS pueden obtener una calidad de la superficie y una durabilidad comparables a las de las piezas moldeadas por inyección, por no hablar de una reducción en la proliferación de bacterias y la absorción de humedad.
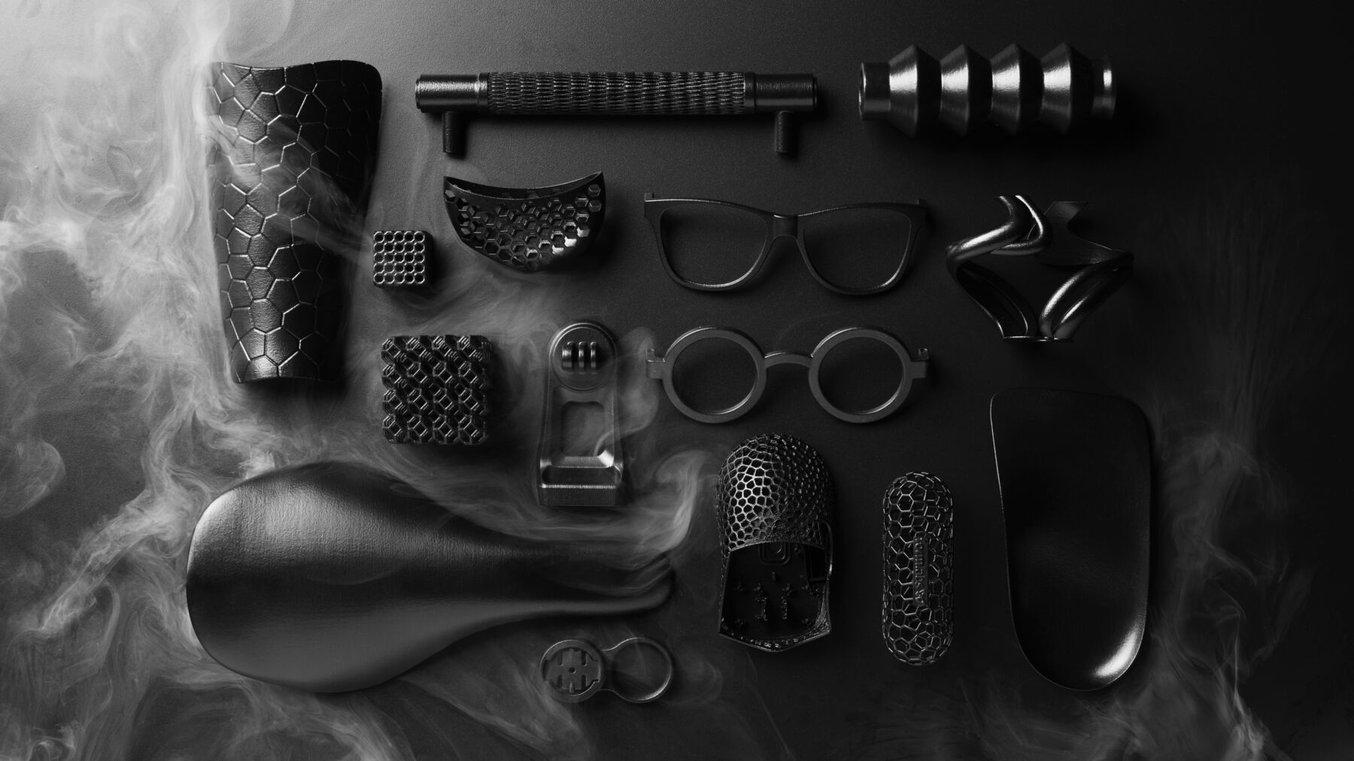
Mejora con el alisado con vapor de la calidad de la superficie de piezas impresas en 3D mediante SLS: Un estudio colaborativo de Formlabs y AMT
En este libro blanco, repasaremos las características y las ventajas del alisado con vapor y veremos los resultados de informes de ensayos de los polvos para SLS de Formlabs con el sistema de alisado con vapor de AMT.
Empieza a imprimir órtesis en 3D
La impresión 3D ha revolucionado el diseño de órtesis, permitiendo producir órtesis adaptadas a los pacientes con procesos de trabajo optimizados que ahorran tiempo y recursos. Para los pacientes, esto supone menos citas en la ortopedia, esperas más cortas y una personalización precisa que aumenta su comodidad, todo ello por un precio inferior al de los métodos tradicionales para producir órtesis personalizadas. Para los ortesistas y fabricantes, los procesos de trabajo en 3D ahorran tiempo y recursos, a la vez que fomentan un entorno de trabajo más cómodo.
La impresión 3D SLS ha demostrado ser un método fiable y eficaz para fabricar productos ortopédicos, y la impresora 3D SLS Fuse 1+ 30W de Formlabs combina potencia industrial con un proceso de trabajo asequible y accesible. Al ser una impresora SLS compacta y ocupar poco espacio, la Fuse 1+ 30W puede encajar fácilmente en un espacio de producción ya existente. Además, el catálogo de materiales de la Fuse 1+ 30W incluye el Nylon 11 Powder, un material resistente y flexible que imita fielmente las propiedades de los materiales de las órtesis de uso final actuales, y el TPU 90A Powder, un material elástico y seguro para la piel.
¿Quieres saber más? Para ver una descripción completa sobre los procesos de trabajo digitales y la impresión 3D en el sector de las órtesis y prótesis, descarga nuestro libro blanco o habla con un experto de Formlabs para encontrar la solución más adecuada para ti.