9 aplicaciones de la impresión 3D en el sector aeroespacial
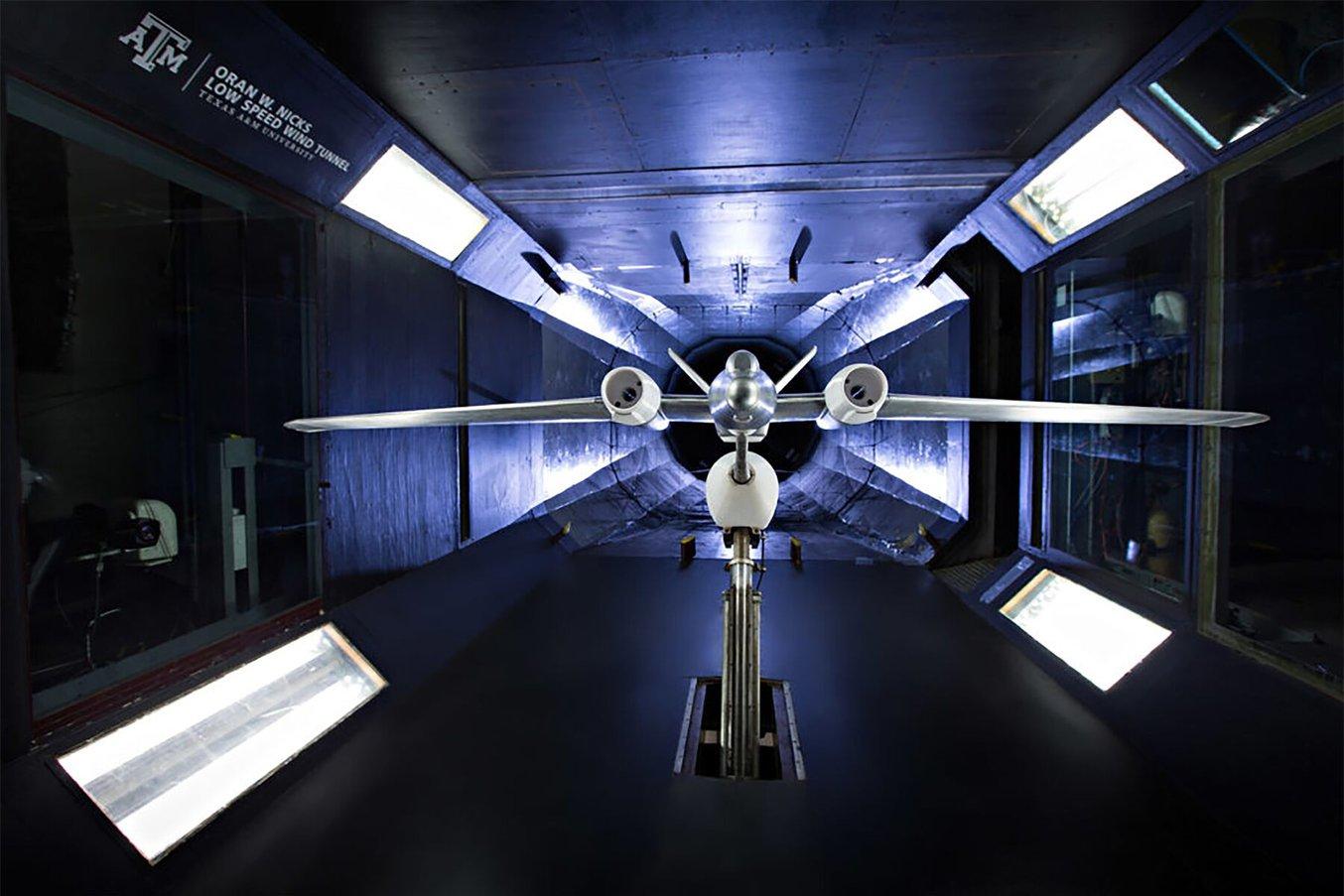
La fabricación aditiva, también conocida como impresión 3D, tiene muchas aplicaciones en el sector aeroespacial, desde el diseño hasta la fabricación y más allá.
La industria aeroespacial fue uno de los primeros sectores comerciales en adoptar la impresión 3D o fabricación aditiva cuando se inventó. En efecto, muchos fabricantes, proveedores y organismos gubernamentales llevan décadas usando la impresión 3D, y las generaciones más modernas de aviones comerciales vuelan con más de 1000 piezas impresas en 3D.
Sin embargo, las impresoras 3D industriales tradicionales son prohibitivamente caras, estando solo al alcance de las organizaciones más grandes y con mayor financiación. En los últimos 10 años hemos visto una disminución drástica en el precio de incluso las impresoras 3D de alto rendimiento, así como innovaciones en la ingeniería de los materiales que posibilitan muchas aplicaciones de aún más alto rendimiento. Cuando tienen un precio accesible, las impresoras 3D pasan a ser una opción para organizaciones pequeñas, pero también para las nuevas sucursales de organizaciones grandes, en las que las impresoras 3D habrían quedado limitadas a talleres centralizados de prototipado. Al llevar la tecnología aditiva a más usuarios finales, las impresoras 3D de Formlabs están dando a más ingenieros e investigadores aeroespaciales la oportunidad de expandir las fronteras de su sector.
Sigue leyendo para conocer nueve formas de las que la impresión 3D impulsa la innovación en la industria aeroespacial, desde el diseño hasta la fabricación y más allá.
Impresión 3D para el desarrollo de productos aeroespaciales
1. Prototipos rápidos impresos en 3D para ensayos funcionales de cohetes
Gravity Industries está desarrollando trajes voladores que parecen cosa de ciencia ficción. Sus trajes autopropulsados, que llaman "jet suits", están pensados para situaciones como esfuerzos de búsqueda y rescate en lugares a los que un helicóptero no puede llegar o en los que no puede aterrizar con seguridad. Usar varios tipos de tecnologías de impresión 3D ha acelerado su proceso de prototipado y ensayo, que incluye algunas pruebas en las que la resina fotopolimerizable termoendurecible era la mejor opción disponible.
Sam Rogers, piloto de pruebas y jefe de diseño del traje, usó piezas hechas con la Clear Resin en la Form 3 para desarrollar el diseño de un dispositivo de encendido para un motor de cohete con refrigeración Vortex. El material transparente era excelente para el entorno de ensayo, ya que permitía a Rogers observar los patrones de combustión en el interior del sistema de ensayo.
Durante los ensayos de diseño, Rogers diseñó la cámara para que fuera modular, de modo que se pudieran mezclar y combinar diferentes versiones tanto de la cámara como de la boquilla. Con un "escudo de oxígeno arremolinado" que mantenía el calor más intenso lejos de las paredes de la cámara, las piezas de resina podían durar varios segundos cada una. Era un tiempo suficiente, ya que cada disparo de ensayo solo tenía que ser lo bastante largo como para observar el patrón de ignición.
Si Rogers hubiera hecho sus decenas de diseños diferentes con metal, habría resultado carísimo. En cambio, al ser las pruebas cortas y tener las piezas costes de material muy bajos, se decidió por un diseño de alto rendimiento con un gasto y un tiempo de espera mínimos.
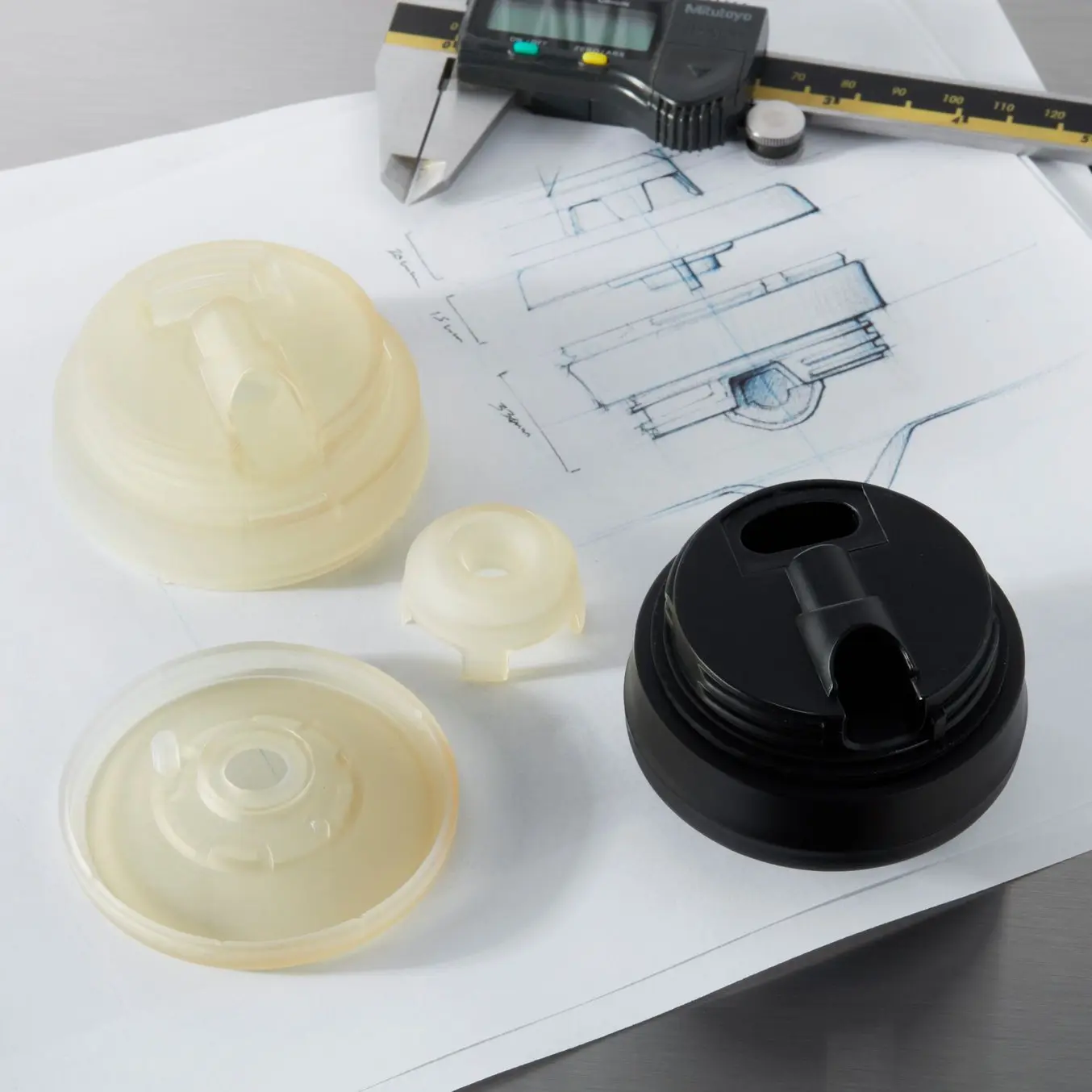
Guía de prototipado rápido para el desarrollo de productos
En esta guía, descubrirás cómo el prototipado rápido puede integrarse en el proceso de desarrollo de productos, cuáles son sus aplicaciones y qué herramientas de prototipado rápido están disponibles actualmente para los equipos de desarrollo de productos.
2. Crea piezas de cohetes complejas con la impresión 3D
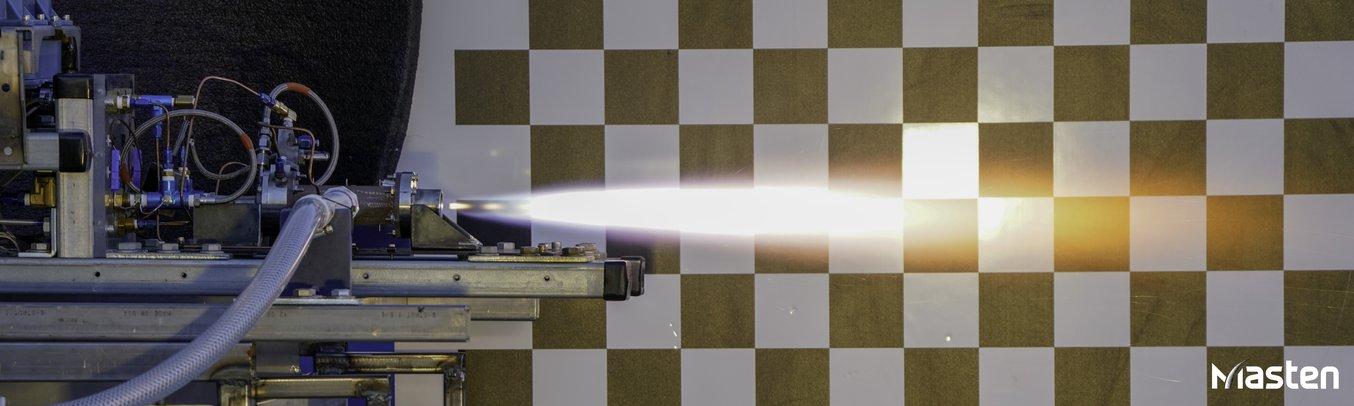
Masten Space Systems produce piezas de cohetes complejas mediante la impresión 3D.
Masten Space Systems es un fabricante especializado en cohetes de despegue y aterrizaje vertical. Masten empezó a imprimir en 3D motores de cohetes en 2014, empezando con pequeños propulsores de prueba y escalando después su producción a un motor Broadsword de 111 000 newtons de fuerza en 2016. Su experiencia en fabricación aditiva incluye tanto plásticos como metales. Según Kimberly Devore, ingeniera de investigación y ensayo de Masten, la empresa ha utilizado tanto el mecanizado tradicional como la impresión 3D para producir motores de cohetes. Aunque Masten sigue utilizando algo de fabricación tradicional en sus motores más antiguos, ha adoptado la impresión 3D para aumentar la flexibilidad del diseño y la velocidad de producción.
"Lo bueno que tiene [la impresión 3D] es que puedes modelar las piezas exactamente como las quieres. Y no requiere el mismo nivel de iteraciones que realizar un mecanizado tradicional. La verdad es que puedes diseñar las piezas para que se ajusten exactamente a tus necesidades", dijo Devore. "Muchas veces, con el mecanizado tradicional probablemente necesites hacer que el diseño sea bastante básico. Cada detalle que se agrega supone un dinero adicional que va a haber que pagar".
Sin embargo, con la impresión 3D, añadir complejidad para mejorar el rendimiento no tiene un coste adicional, ni tampoco lo tiene asumir riesgos. Dado que es relativamente rápido y barato hacer múltiples unidades de las piezas, se pueden probar cosas nuevas. "Poder realizar rápidamente iteraciones de ese tipo de cosas tiene un impacto tremendo".
3. Prototipado de herramientas aeroespaciales con la impresión 3D
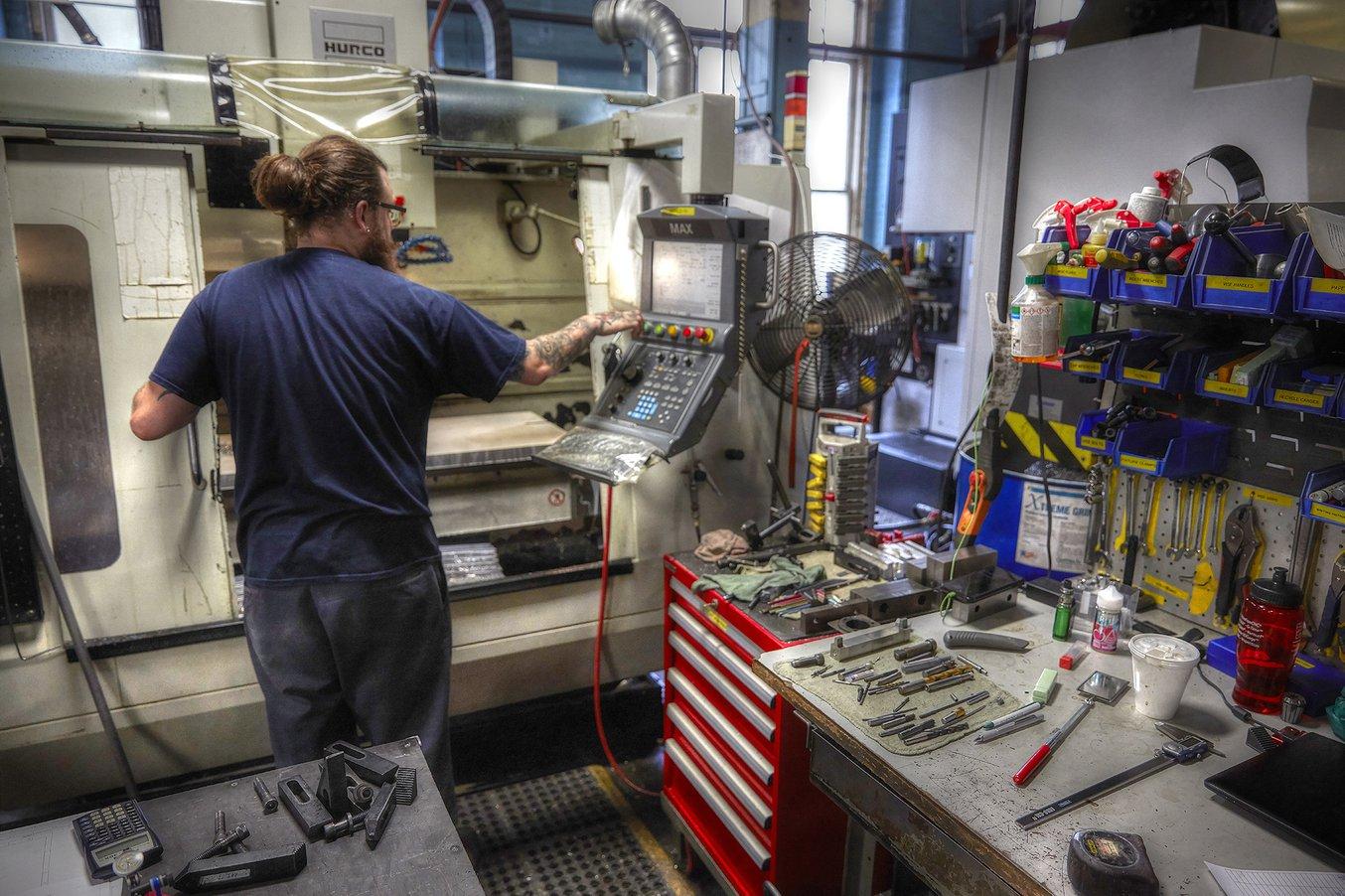
Para programar una fresadora de CNC, es necesario contar con las habilidades necesarias y disponer de tiempo. Si no hace falta que una pieza sea de metal, la impresión 3D puede ser una herramienta práctica para crear prototipos o herramientas de producción de manera mucho más rápida y por menos dinero.
A&M Tool and Design produce piezas y máquinas personalizadas para los sectores de la industria aeroespacial, la óptica y la robótica. El taller se ha modernizado con el paso del tiempo para incluir una variedad de nuevos equipamientos, que incluyen la impresión 3D, tecnologías tradicionales y fiables y soluciones reacondicionadas. Ryan Little, ingeniero mecánico en A&M Tool, investigó qué impresora 3D podía satisfacer mejor sus necesidades y optó por las impresoras 3D de Formlabs.
Para el prototipado, el taller empezó a utilizar las impresiones 3D con el fin de someter a ensayo el ajuste y la funcionalidad. La impresión 3D permite que Little y su equipo impriman las piezas mucho más rápido y aprovechen todas las horas del día, ya que configuran las impresiones de forma que se produzcan durante la noche y las puedan usar al día siguiente. La impresión es especialmente útil para geometrías costosas y que se tarda mucho en producir con una fresadora de CNC.
"Casi parece que la impresora es una herramienta auxiliar además del diseño asistido por ordenador", comentó Little. "Fabricamos un montón de prototipos para distintos tipos de utillaje. Si no tuviésemos la Form 2, muchos de los prototipos se quedarían en el software de diseño asistido por ordenador (CAD) hasta que tuviésemos la máquina preparada y algunos proyectos no se completarían ni se diseñarían nunca porque no resultaría práctico".
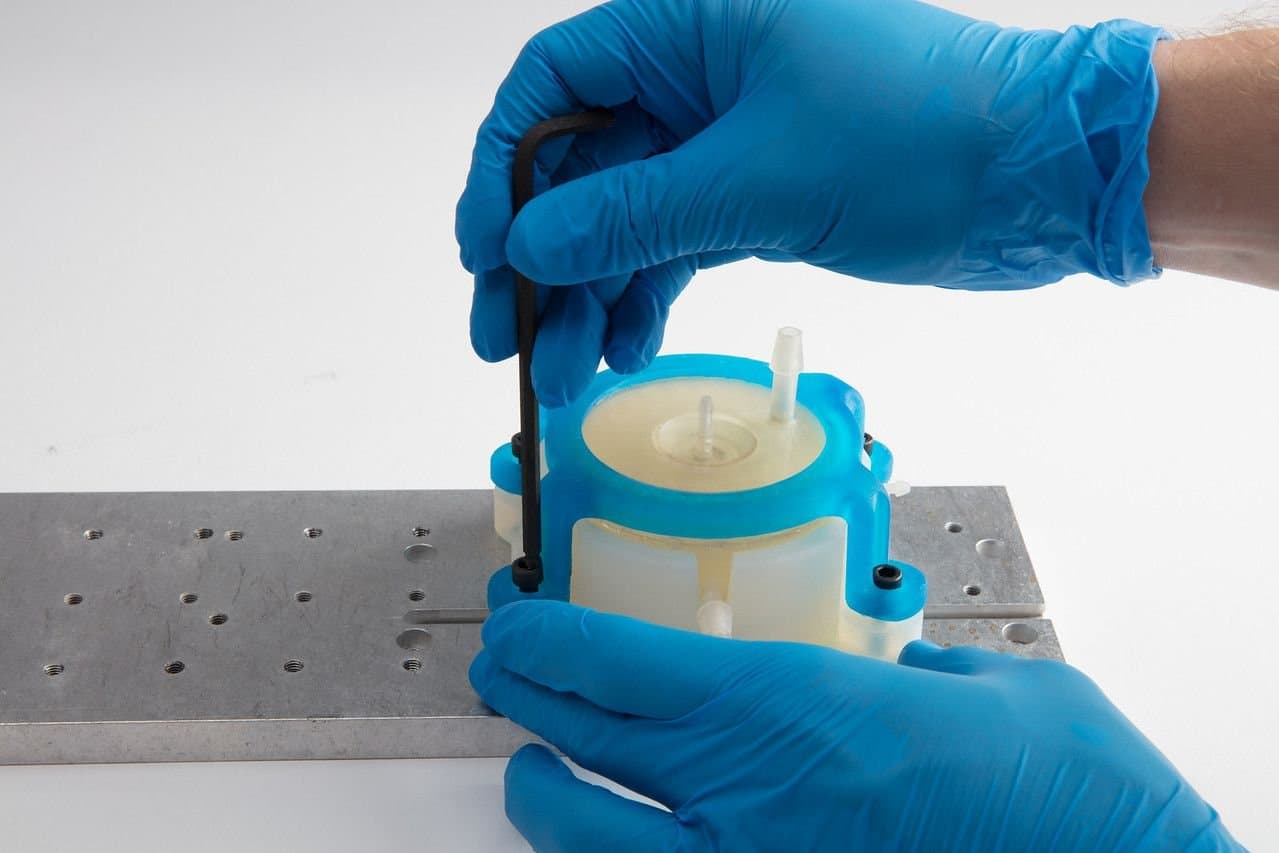
Diseño de sujeciones con guía y fijaciones mediante impresión 3D
Para los fabricantes, maximizar la velocidad de producción sin perder la alta calidad de las piezas es esencial para el éxito. Las sujeciones con guía y fijaciones se utilizan para simplificar los procesos de fabricación y montaje y hacerlos más fiables y eficientes, reduciendo los tiempos de ciclos y mejorando al mismo tiempo la seguridad de los trabajadores.
Impresión 3D para la fabricación aeroespacial
4. Ahorro de dinero con utillaje personalizado impreso en 3D para piezas de aeronaves
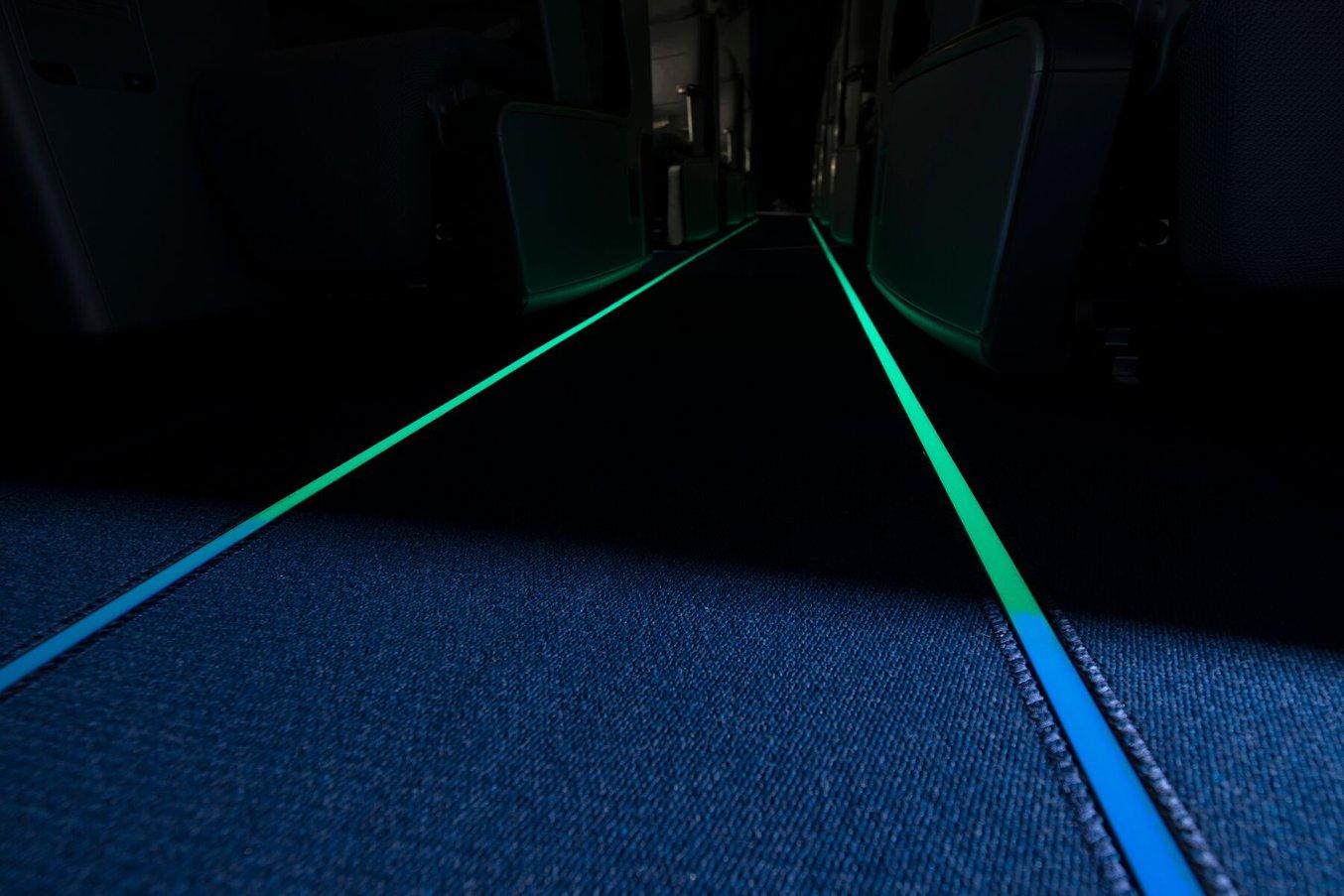
Lufthansa Technik imprimió en 3D la boquilla extrusora para producir estos marcadores de vías de evacuación que se iluminan por sí solos
Lufthansa Technik es uno de los mayores proveedores del mundo en lo que respecta a servicios de mantenimiento, reparación y mejora en el sector de la aviación. Sus marcadores Guide U para las vías de evacuación están diseñados para su instalación en cabinas de aviones en la fase de la posventa. Estos innovadores marcadores para el suelo son fotoluminiscentes, lo que quiere decir que están equipados con pigmentos luminiscentes que se cargan con la luz normal de la cabina y continúan brillando en la oscuridad si hay una emergencia en la que no hay electricidad.
Antes de fabricarlos, se sometieron a ensayo varios materiales y procesos de fabricación para el utillaje. Imprimir en 3D boquillas de extrusión a medida resultó ser el método de fabricación más rentable y flexible. "En teoría, también podríamos moldear nuestras piezas por inyección. Pero nunca habríamos tenido tanta flexibilidad para dar forma a la boquilla y realizar modificaciones. Esa es la gran ventaja que veo yo en la impresión 3D", explica Ulrich Zarth, ingeniero de proyectos de Guide U.
Esta herramienta de producción se imprimió en la Form 3L en colaboración con myprintoo, uno de los socios de Formlabs. La gran superficie de la base de impresión de la Form 3L permitió producir 72 boquillas en una sola impresión. Se sometieron a ensayo varios materiales de Formlabs y el elegido fue la Clear Resin, que, además de ofrecer la estabilidad y la calidad de la superficie adecuadas, ayuda a Lufthansa Technik a optimizar constantemente su proceso de producción.
"Si quieres geometrías precisas, especialmente en el sector de los plásticos, y las quieres rápido, yo siempre usaría la impresión 3D".
Ulrich Zarth, ingeniero de proyectos de Lufthansa Technik AG
Zarth y su equipo ahorraron una enorme cantidad de tiempo y dinero en su proceso de producción al imprimir este pequeño componente en sus propias instalaciones. En comparación con los métodos convencionales para fabricar utillaje de este tipo, también pudieron evitar cantidades mínimas demasiado altas en los pedidos y su optimización de los procesos se mantuvo considerablemente más flexible.
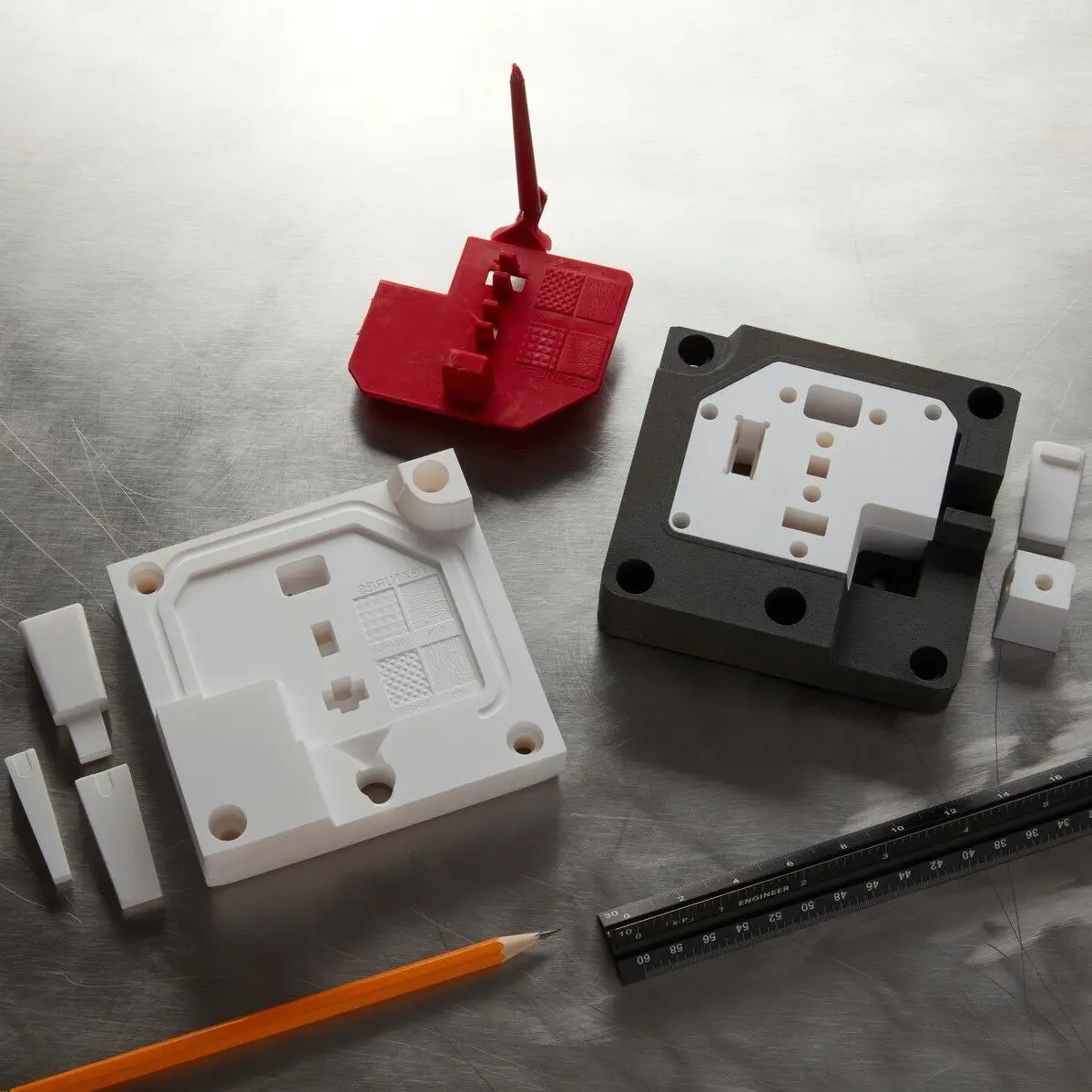
Guía de utillaje rápido
En este libro blanco, aprenderás a combinar las herramientas rápidas impresas en 3D con procesos de fabricación tradicionales como el moldeo por inyección, el termoformado o la fundición.
5. Ahorro de tiempo en la fabricación aeroespacial con sujeciones con guía para enmascaramiento impresas en 3D
El Grupo Integrado de Fabricación del AMRC trabaja con socios industriales para combinar tecnologías avanzadas y desarrollar sistemas integrados. El grupo de investigación trabajó en un proyecto para Airbus, el mayor fabricante aeroespacial de Europa, que incluía procesos de perforación y mecanizado de componentes de fibra de carbono, aluminio y titanio. "Después de taladrar un agujero y pasar al siguiente, teníamos que cubrir el primero de los dos, para que los residuos generados no contaminaran el segundo agujero", dijo George Sleath, ingeniero de proyectos del AMRC.
Lo primero que intentó el equipo fue utilizar una pieza de aluminio con una pequeña junta tórica de goma, pero eso no era una solución suficiente para el problema. Y había dos inconvenientes añadidos: se necesitaban tapas protectoras de muchos tamaños y solo tenían dos días para conseguir 500 si querían cumplir sus plazos.
Con un plazo tan ajustado para hacer productos personalizados, habría resultado imposible para prácticamente cualquier opción de fabricación que no fuera la impresión 3D. En ese momento, Sleath no estaba seguro de qué capacidades tenía el AMRC en sus propias instalaciones y solicitó presupuestos de tres servicios de impresión externos, pero los precios eran caros.
"Entonces, hablé con Mark Cocking en nuestro Grupo de Diseño y Prototipado y le pregunté si podíamos fabricar algo nosotros mismos. No tuve respuesta durante 24 horas, pero cuando la recibí, dijo "sí, ya tenemos más de la mitad impresa". Fabricar 250 de esas tapas protectoras para perforación fue un resultado impresionante", dijo Sleath.
Al final, Cocking consiguió tener todos los componentes fabricados en dos días, y las tapas funcionaron en situaciones reales tal y como se esperaba. "Las opiniones que recibía de los operarios que las estaban instalando eran fantásticas. La gran mayoría de las piezas funcionó exactamente como se habría previsto y ninguna de ellas se rompió durante su funcionamiento", dijo Sleath.
6. Piezas aeroespaciales de uso final impresas en 3D con galvanizado
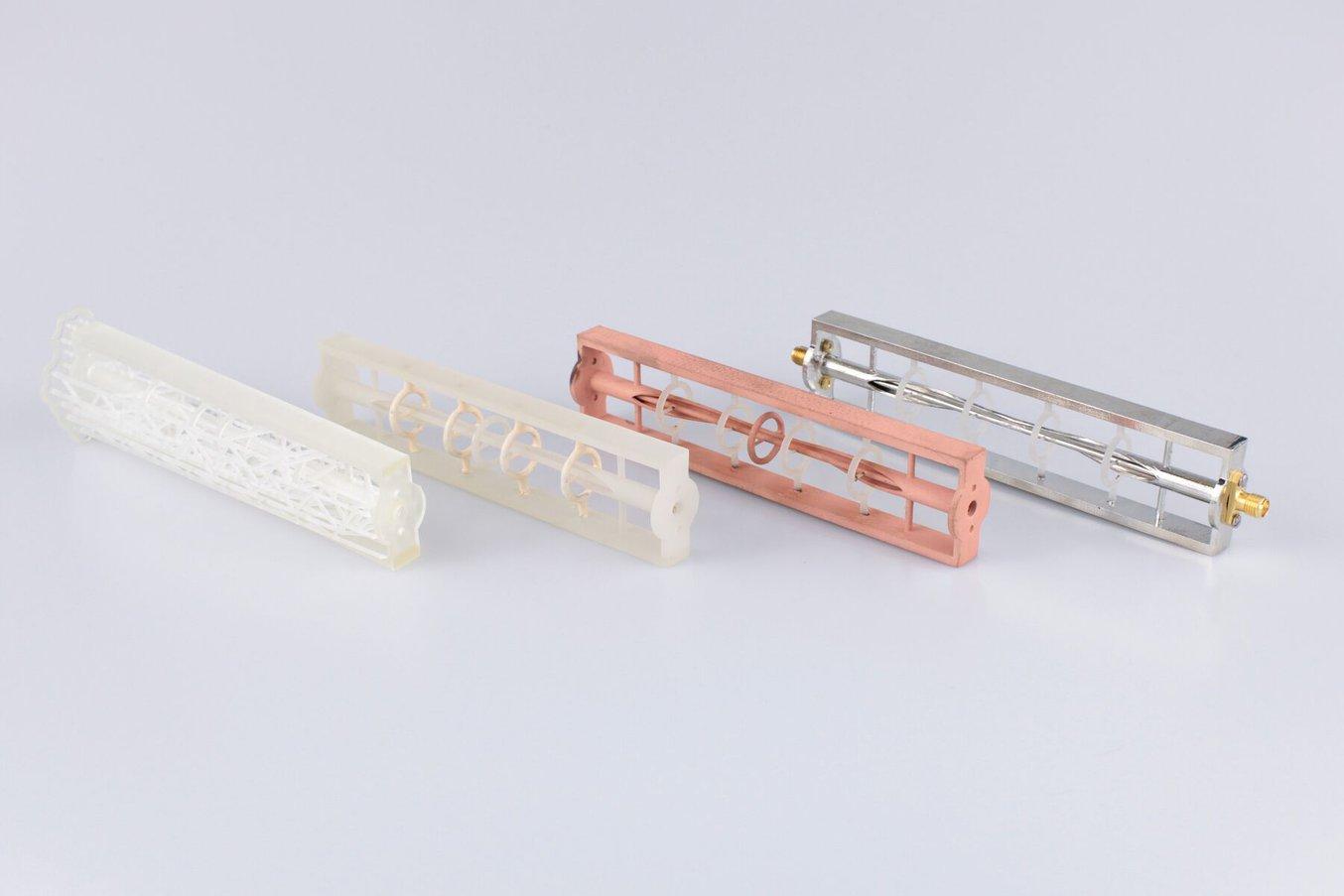
Imprimir en 3D piezas de uso final permite a Elliptika crear diseños novedosos para antenas a mayor velocidad y ahorrar dinero en el proceso.
Elliptika es una empresa especializada en el diseño y desarrollo de productos y soluciones de radiofrecuencias (RF) y microondas. La empresa diseña antenas y filtros personalizados que se utilizan para la investigación y el desarrollo en sectores como la industria automovilística, la defensa, la medicina y la educación. Los diseñadores de radiofrecuencia Gwendal Cochet y Alexandre Manchec necesitan conseguir geometrías complejas, mantener los costes reducidos y entregar los diseños con rapidez. Para obtener estos parámetros tan exigentes, han aprendido a ir más allá de las técnicas de fabricación tradicionales.
El equipo de Elliptika ha trabajado con diferentes procesos de fabricación aditiva y ha descubierto que la impresión 3D por estereolitografía (SLA) es la mejor opción para el galvanizado, debido a las superficies lisas que tienen las piezas impresas. "Después de imprimir la pieza en 3D, necesitamos retirar el soporte, limpiar la superficie y curarla. Luego, la pieza impresa se somete a un proceso químico para recubrir una capa delgada de cobre (aproximadamente 3 µm). Por último, la pieza puede recibir un acabado superficial, como una capa más gruesa de estaño".
Elliptika rentabilizó su impresora 3D de Formlabs con solo dos trabajos. Obtener una pieza hecha por un proveedor externo cuesta unos 3000 €, mientras que el material y la mano de obra para imprimir en 3D y galvanizar una antena en sus propias instalaciones cuesta solo 20 €.
Y el ritmo de su trabajo también se aceleró. Con las técnicas de fabricación tradicionales, fabricar una antena podía llevar hasta tres meses. "Gracias a poder imprimir en 3D en nuestra propia empresa, podemos tener piezas en dos días. Un día para imprimir, otro para recubrir, y listo. Es mucho más rápido", dijo el Sr. Cochet.
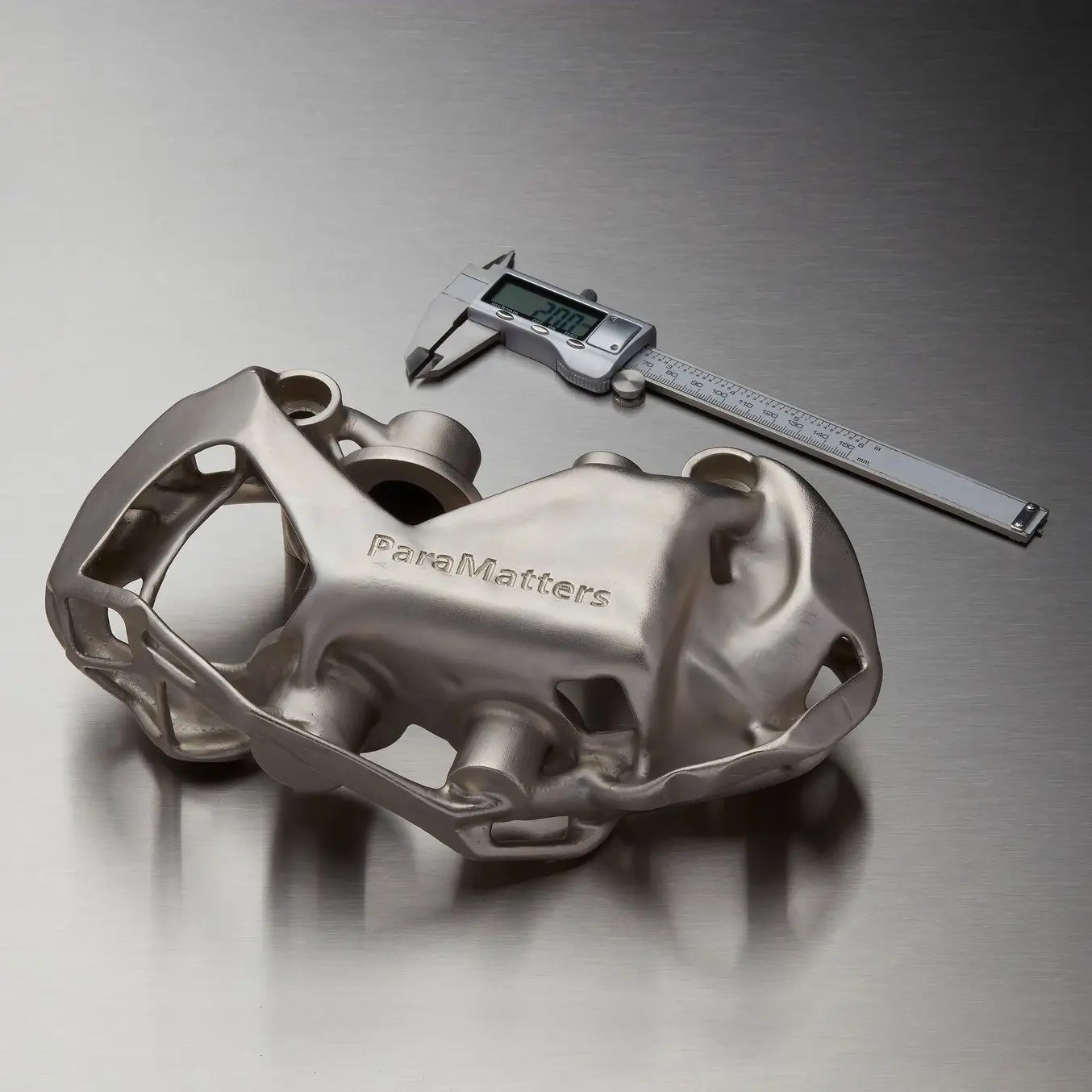
Resistencia del metal: Estrategias y casos de uso de las piezas impresas mediante SLA y galvanizadas
Sigue leyendo para descubrir cómo los ingenieros añaden metal a las impresiones 3D de resina y por qué las piezas de metal híbridas pueden abrir nuevas puertas a una sorprendente variedad de aplicaciones, entre las cuales se incluyen la resistencia y durabilidad para uso final.
La impresión 3D en la formación y la investigación aeroespacial
7. Ensayo en el espacio de piezas impresas en 3D
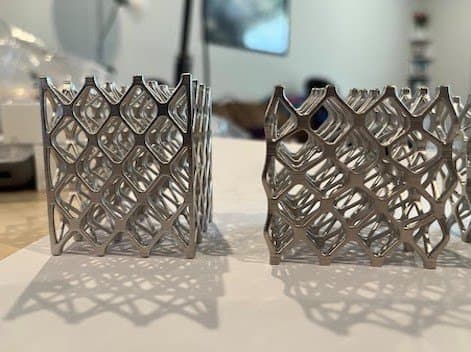
Muestra de compresión de una celosía hecha con la Rigid 10K Resin y galvanizada antes del ensayo (izquierda) y muestras posteriores al ensayo (derecha) que se cargaron desde la parte superior.
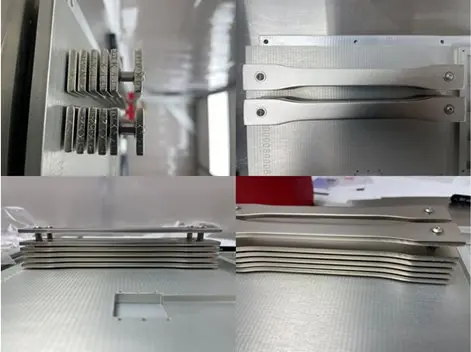
Piezas impresas en 3D con la Rigid 10K Resin y galvanizadas que se han enviado a la EEI.
Los investigadores de la NASA están estudiando cómo rinden en el espacio las piezas impresas mediante SLA y galvanizadas. Ingenieros del Centro de Vuelo Espacial Goddard de la NASA diseñaron soportes que se imprimieron en 3D en impresoras de Formlabs, se galvanizaron y se enviaron al espacio a bordo de una misión de reabastecimiento comercial (CRS-25) a la Estación Espacial Internacional (EEI).
Mediante la plataforma de pruebas de Alpha Space en la Estación Espacial Internacional, llamada Experimento de Materiales de la Estación Espacial Internacional (MISSE-16), las muestras se someterán al entorno del exterior de la estación espacial y, posteriormente, volverán a la Tierra, donde se llevarán a cabo ensayos adicionales. Los resultados podrían mostrar cómo la NASA y, posiblemente, otros fabricantes del sector aeroespacial podrían incorporar el galvanizado y la fabricación aditiva a futuros planes potenciales de productos.
8. Piezas de ensayo impresas para el túnel de viento
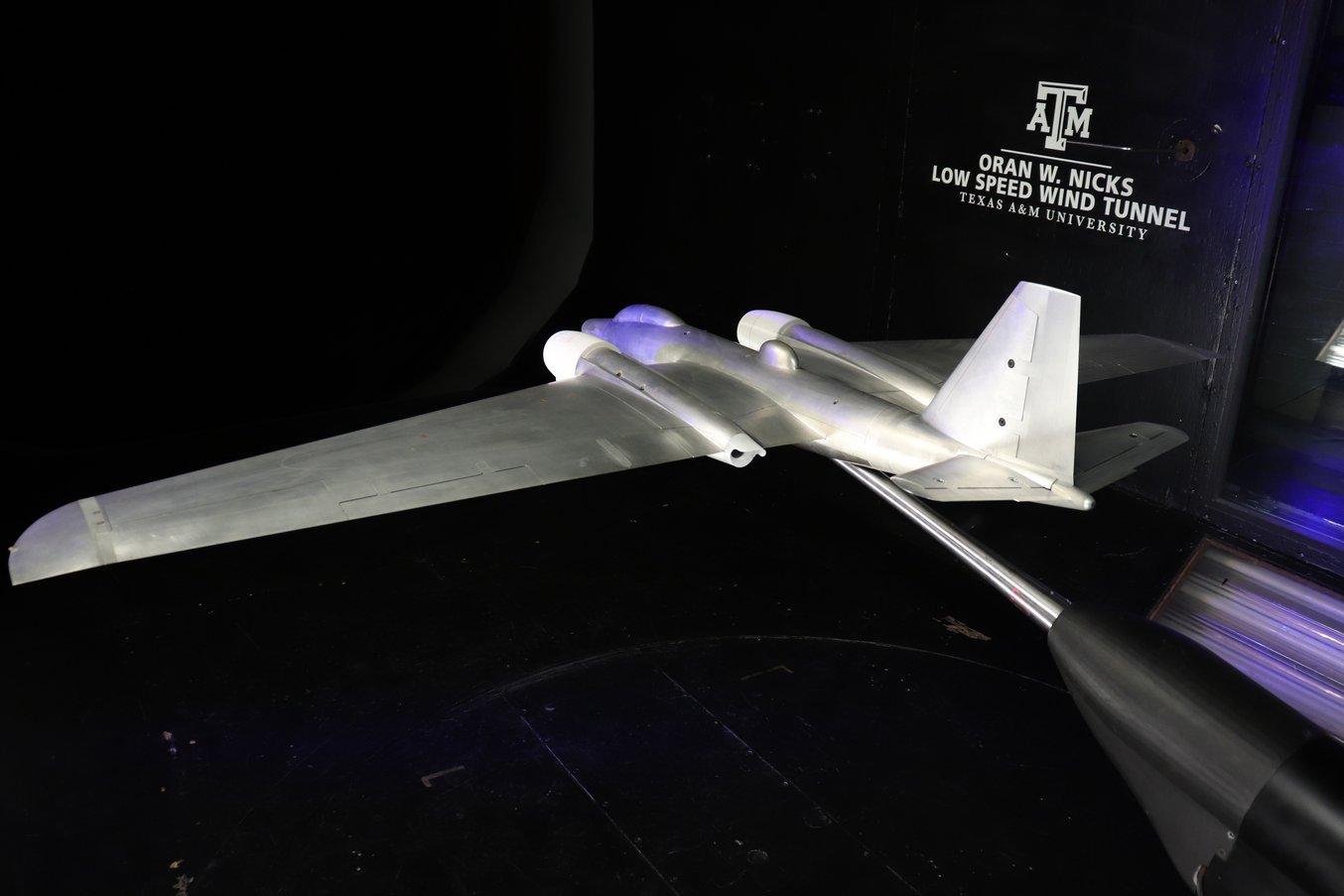
Los componentes impresos en 3D de alto rendimiento se pueden montar en modelos de aviones a escala en un túnel de viento.
Profesores y estudiantes de todo el mundo están usando impresoras 3D de Formlabs en pruebas de túnel de viento para potenciar su investigación.
El Túnel de Viento de Baja Velocidad Oran W. Nicks de la Universidad A&M de Texas realiza ensayos de túnel de viento para un amplio abanico de proyectos. Lisa Brown, directora e ingeniera del túnel de viento de la Universidad A&M de Texas, ayuda a los investigadores a desarrollar sus planes de ensayo, a diseñar los modelos y a crear el código que los ayuda a recopilar datos relevantes. Su equipo usa la impresión 3D para crear modelos a escala con los que probar diversos objetos.
Brown recuerda un proyecto en el que el equipo investigó una pala del rotor de un helicóptero con aleteo e incorporó la impresión 3D en el ensayo. Si vamos lo bastante rápido y las palas aletean a la suficiente velocidad, el borde delantero de esas palas llega a producir ondas de choque, y eso no es lo que se quiere en un helicóptero. De hecho, pudimos ver cómo se daban esas ondas de choque en nuestro túnel de baja velocidad, fue muy emocionante", dijo Brown. "Colocamos un pequeño inserto impreso en ese borde delantero con algunos sensores en su interior. Por eso, el modelo era un ala de aluminio con un pequeño inserto que podíamos reemplazar".
Para descubrir qué material eligió Brown y por qué, lee nuestro caso de estudio.
Al otro lado del Atlántico, el túnel de viendo del Instituto de Tecnología de Karlsruhe también pone a prueba piezas impresas en 3D. El estudiante de doctorado Lars von Deyn estudia métodos para predecir flujos turbulentos. Su trabajo tiene el potencial de dar más información a los fabricantes cuando se enfrenten a decisiones de materiales y diseño para reducir la fricción en la movilidad.
Para crear sus piezas de ensayo, von Deyn recurrió a la impresión 3D. "Me gustaría examinar estructuras que son muy difíciles de producir mediante procesos de mecanizado", nos dijo. Eligió la Form 3L porque su gran área de impresión le permitía cubrir el área de ensayo del túnel de viento con menos piezas y de este modo, crear menos interrupciones en el patrón del viento.
Encontrarás los resultados de sus experimentos en nuestro caso de estudio.
9. La impresión 3D como herramienta para formar a la próxima generación de ingenieros
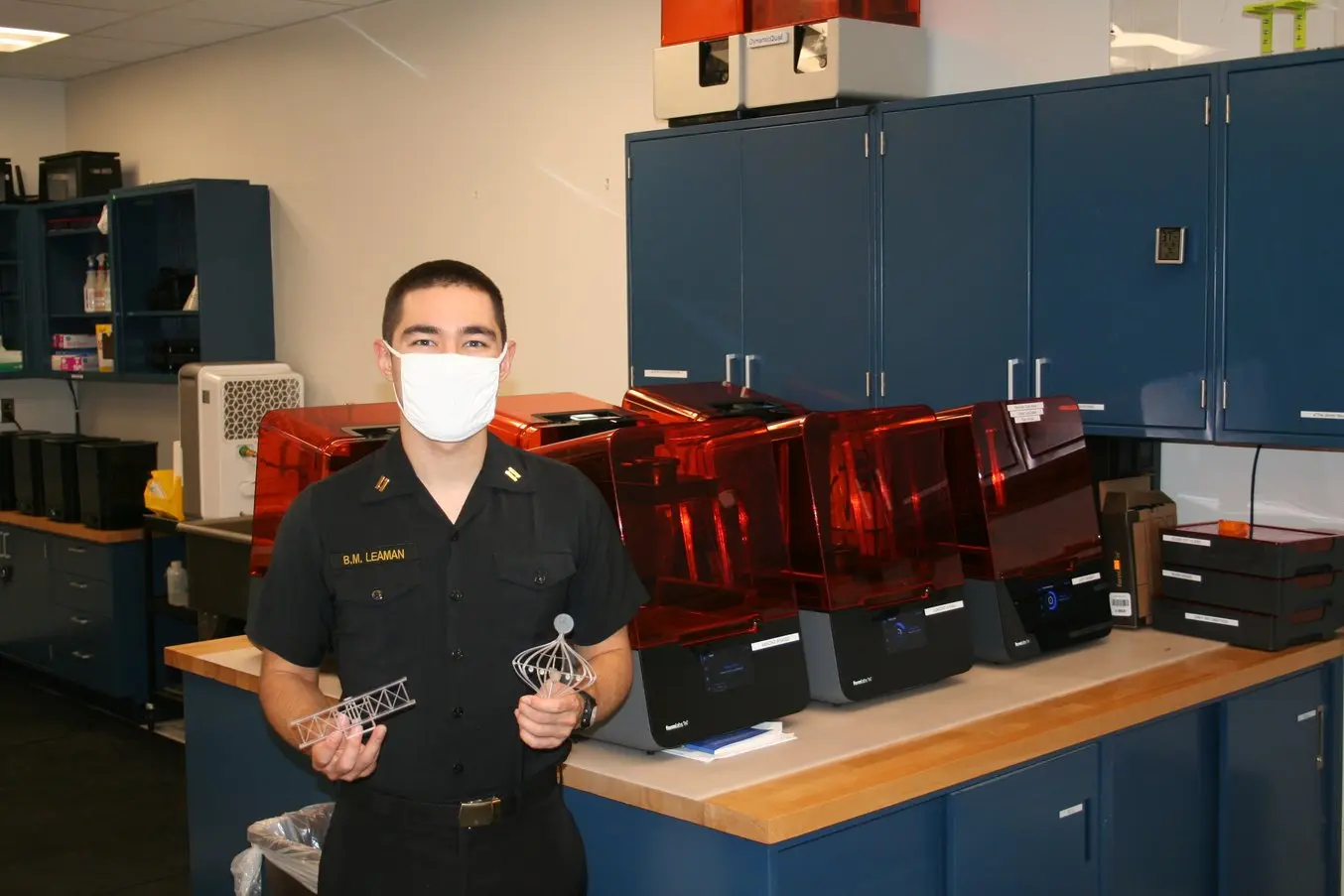
El alférez de primera clase Ben Leaman, estudiante de Arquitectura Naval en la USNA, mostrando las impresiones galardonadas que hizo con las impresoras Form 3 de Formlabs durante un desafío de las Olimpiadas de Fabricación Aditiva de 2021.
La Academia Naval de Estados Unidos (USNA) prepara a hombres y mujeres jóvenes para convertirse en oficiales profesionales de los cuerpos de la Armada y de la Marina de los Estados Unidos. El capitán Brad Baker, un profesor asociado de la USNA, se dio cuenta de que el proceso de iteración de sus estudiantes de ingeniería, y por tanto su ritmo de aprendizaje, estaba obstaculizado por la falta de capacidad para fabricar. Incluso con un taller de mecanizado dedicado a los proyectos de fin de carrera de los estudiantes, cada individuo o equipo no era capaz de hacer más de tres o cuatro iteraciones a lo largo del año.
El capitán Baker no era el primer profesor en el campus que ofrecía impresoras 3D a los estudiantes para sus trabajos académicos, pero consiguió centralizar el diseño y la capacidad de fabricación en un único lugar cuando puso en marcha MakerSpaceUSNA. Con solo un par de impresoras de modelado por deposición fundida (FDM) para empezar, comenzó por integrar la maquinaria en el currículo de ingeniería mecánica y poniéndola a disposición de los estudiantes para que pudiesen completar sus proyectos de fin de carrera.
Cuando los estudiantes entran en el currículo de ingeniería, lo primero que aprenden es a usar software CAD, luego a manejar impresoras FDM, más tarde avanzan a la estereolitografía (SLA) y finalmente se abren paso hasta las impresoras 3D de sinterizado selectivo por láser (SLS). Ahora incluso aprenden escaneo 3D y pueden completar proyectos enteros de ingeniería inversa usando todas las herramientas que han aprendido.
Disponer de impresoras fiables de alta calidad con las tecnologías FDM, SLA y SLS permite al MakerSpaceUSNA ofrecer a todos y cada uno de los estudiantes de la USNA experiencia con una gran variedad de tecnologías de fabricación aditiva. La filosofía del capitán Baker sobre la formación práctica y un enfoque en el aprendizaje mediante el error lleva esa exposición aún más lejos para los estudiantes de ingeniería y los prepara para carreras de servicio en la Armada de los Estados Unidos y más allá.
¿Qué nos depara el futuro en el sector aeroespacial?
Con tecnologías aditivas más potentes y accesibles que nunca, el sector está en disposición de recibir contribuciones de un abanico más amplio de ámbitos. Es difícil saber si los mayores avances de los próximos cinco a diez años provendrán de los fabricantes, los proveedores, organismos públicos, empresas emergentes o instituciones académicas, pero al familiarizarse más gente que nunca con la impresión 3D, esas innovaciones llegarán más rápido que nunca.
A medida que la comprensión de la impresión 3D siga extendiéndose por la industria aeroespacial, y que la tecnología y la base de materiales disponibles sean cada vez más versátiles, la fabricación aditiva continuará revolucionando el modo de construir y mantener aeronaves y naves espaciales.