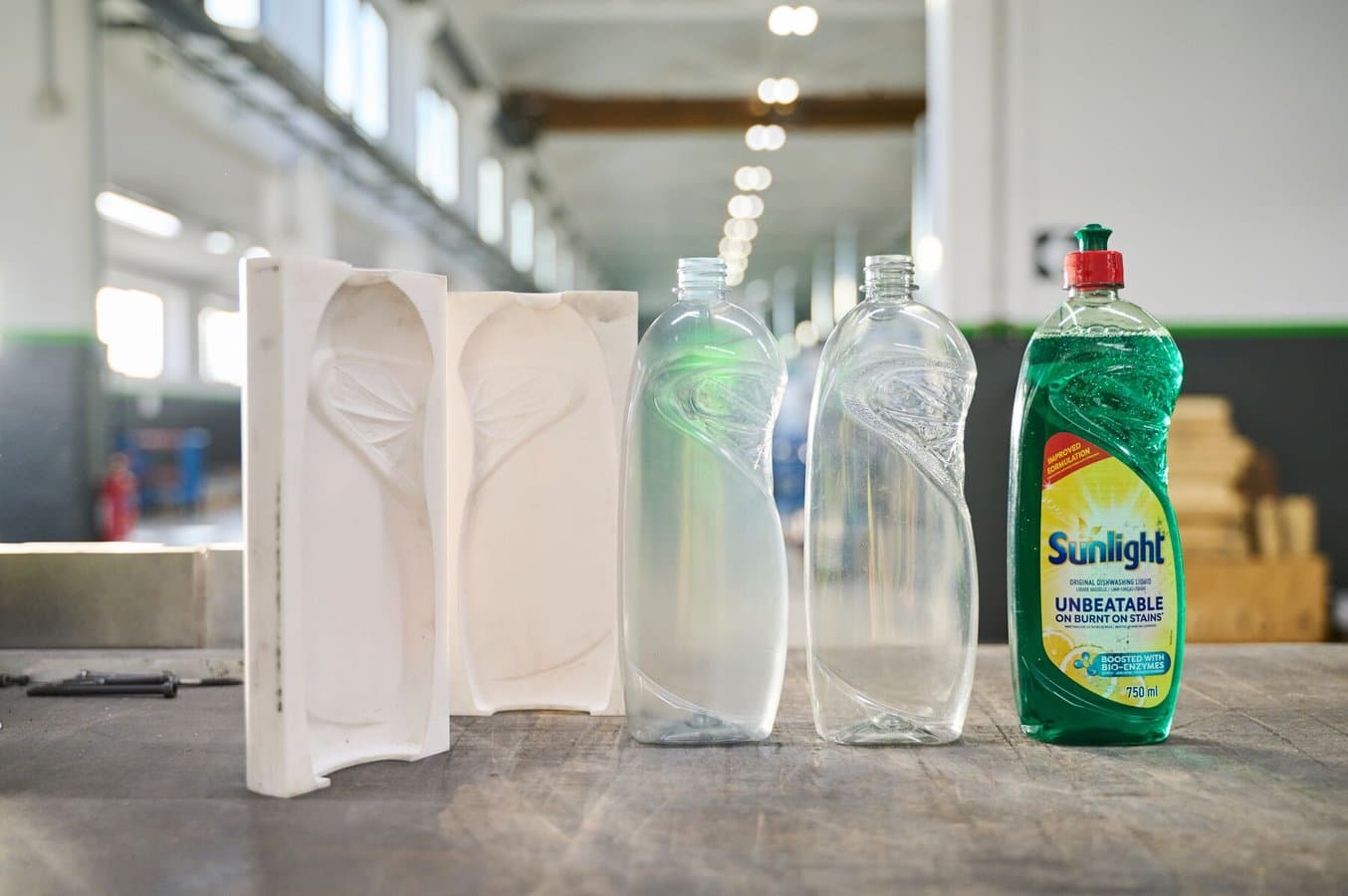
Al ser un proceso de fabricación moderno diseñado para producir piezas de plástico huecas a gran escala, el moldeo por soplado ha existido desde 1938, cuando los inventores estadounidenses Enoch Ferngren y William Kopitke registraron una patente para un "aparato para dar forma a artículos huecos a partir de material plástico orgánico". Sin embargo, los principios del moldeo por soplado han existido desde al menos el siglo I a.C., cuando se desarrolló el soplado de vidrio en la antigua Siria. Hoy, la impresión 3D y otras tecnologías de fabricación avanzadas están mejorando la eficiencia y la eficacia del moldeo por soplado de plásticos, así como haciéndolo más accesible para un amplio abanico de fabricantes.
Los tres tipos principales de moldeo por soplado, que son el moldeo por extrusión-soplado (EBM), el moldeo por inyección-soplado (IBM) y el moldeo por inyección, soplado y estiramiento (ISBM), implican usar aire para inflar una preforma de plástico calentada y que se ajuste a los contornos de un molde. Aunque el EBM suele conseguir el menor coste por pieza, el IBM y el ISBM son capaces de producir productos que sean más complejos y pueden alcanzar hitos de funcionalidad que están fuera del alcance de las piezas producidas mediante EBM. En particular, el ISBM se usa con frecuencia para crear productos que requieran grados elevados de resistencia y transparencia.
Este artículo da una descripción detallada de los diferentes tipos de procesos de moldeo por soplado de plásticos, los polímeros más comunes que se usan para los productos moldeados por soplado y cómo puedes empezar a moldear por soplado.
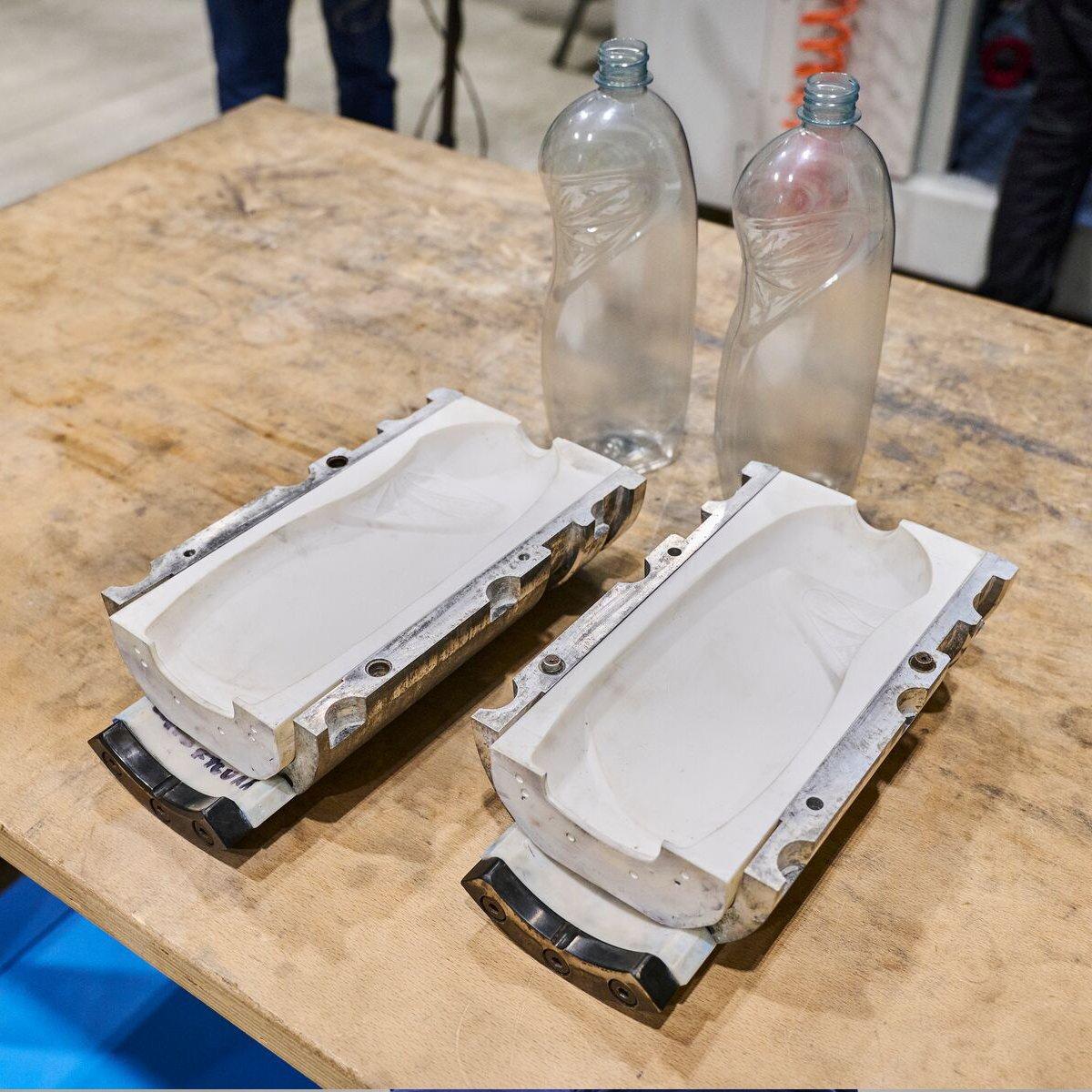
Moldeo por soplado y estiramiento rápido de bajo volumen con moldes impresos en 3D
Este libro blanco proporciona métodos y recomendaciones para usar en el proceso de SBM moldes impresos en 3D mediante SLA, para reducir los costes y los tiempos de espera durante la preproducción. Detalla el estudio de viabilidad que realizaron dos expertos del sector, Unilever y Serioplast. Los pormenores de este estudio abarcan desde consideraciones respecto al diseño y el proceso de trabajo hasta las condiciones de moldeo.
¿Qué es el moldeo por soplado?
El moldeo por soplado es un proceso de fabricación industrial que se usa para crear piezas de plástico huecas. Muchos sectores diferentes utilizan el moldeo por soplado de plástico, entre los que se encuentran la industria automovilística (para depósitos, conjuntos de admisión y conductos, entre otros componentes) y el sector agrícola (para contenedores a granel, piezas de regadío y depósitos de fluidos). Pero quizás el uso más conocido del moldeo por soplado esté en el sector de los envases, donde el proceso se utiliza para hacer botellas de plástico y otros contenedores para todo tipo de sustancias: agua, productos de belleza, soluciones de limpieza, etc.
El moldeo por soplado de plástico ofrece un método fiable y asequible para crear piezas de plástico en grandes cantidades. Como ocurre con muchos procesos de fabricación, los costes iniciales pueden ser elevados, por lo que el moldeo por soplado a menudo empieza a ser conveniente económicamente solo cuando un fabricante necesita crear miles de unidades de la misma pieza. Aunque algunas metodologías permiten diseñar con mayor complejidad que otras, lo más probable es que el moldeo por soplado sea la más eficaz para formas huecas con paredes delgadas.
En comparación con el moldeo por inyección, el moldeo por soplado de plásticos suele tener un coste de utillaje más bajo. Del mismo modo, el moldeo por soplado admite muchos materiales diferentes, lo que lo hace apropiado para una gran variedad de aplicaciones.
Por lo tanto, la fabricación en lotes pequeños y el diseño iterativo de productos suelen beneficiarse más de herramientas con costes iniciales más bajos y una mayor versatilidad en los diseños, como las impresoras 3D. No obstante, algunos líderes de sector están empezando a usar ambas tecnologías en sus procesos de fabricación diseñando moldes de soplado con impresoras 3D de estereolitografía, reduciendo el coste del utillaje y mejorando la calidad del producto final.
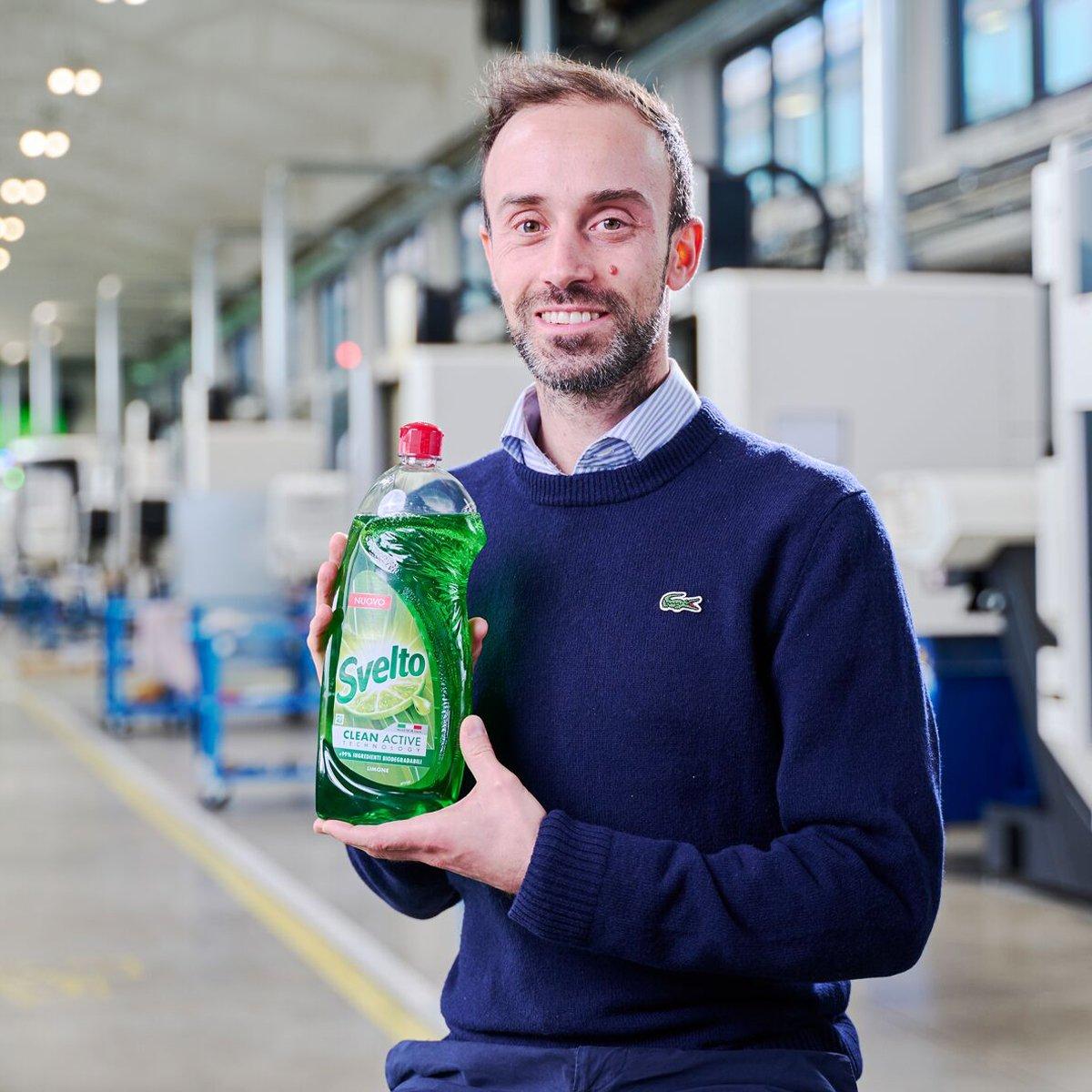
Reduce los costes y el tiempo dedicado a los ensayos piloto de embalajes con el moldeo por soplado rápido
En este seminario web, el experto en moldeo por soplado Flavio Migliarelli explicará el proceso de trabajo y el método paso a paso, además de hablar de las ventajas clave y las posibles aplicaciones de usar moldes impresos en 3D para realizar un moldeo por soplado y estiramiento rápido.
¿Cómo funciona el moldeo por soplado?
En el proceso de moldeo por soplado, se usa una boquilla para introducir aire presurizado en una preforma de plástico calentada, que se expande para encajar con los contornos de un molde. Mediante este proceso, se forma una pared de plástico delgada con la forma de un molde, dejando una cavidad hueca. A continuación, el plástico se enfría hasta que ya no necesite el molde para conservar su forma. Por último, el molde se retira, se recorta el plástico sobrante y la pieza de plástico se somete a ensayos para comprobar su calidad antes de enviarla a los clientes.
1. Calentamiento de la preforma
El modo en que se crea una preforma varía entre los tres principales procesos de moldeo por soplado: el EBM, el IBM y el ISBM. Este artículo describirá esas diferencias con detalle en el apartado "Tipos de proceso de moldeo por soplado".
Cuando se crea la preforma, se debe calentar hasta una temperatura específica que le permita mantener su integridad mientras se llena de aire presurizado. En función del proceso y del tipo de plástico que se utilice, es posible que la preforma ya esté calentada hasta una temperatura que le permita expandirse para ajustarse al molde. En otros casos, se usan calentadores de banda o de anillo para llevar la preforma hasta el intervalo de temperatura termoelástico.
La temperatura adecuada varía en función del material, la metodología y el producto final que se desee. El tereftalato de polietileno (PET), un material que se usa con frecuencia para crear envases de bebidas, se suele calentar hasta alcanzar los 100 °C. Para obtener un grosor de las paredes uniforme y evitar dañar el producto final, es muy importante asegurarse de que la preforma se caliente de forma uniforme.
2. Moldeo
Cuando la preforma sea maleable, se introduce aire presurizado mediante una boquilla. La preforma se infla como un globo hasta que las paredes de plástico delgadas se ajusten a los contornos de la cavidad. Los moldes pueden dar a la botella diferentes formas y texturas, así como incluir letras y logotipos. Como ocurre con otros tipos de moldeo, entre los que se cuentan el moldeo por compresión y el moldeo por inyección, los moldes de soplado permiten que el plástico sobrante salga para que no crezca expresivamente la presión y garantizar un resultado uniforme.
El aire presurizado se debe introducir a un ritmo constante que permita que la preforma se expanda sin agrietarse o desgarrarse. Los moldes más complejos pueden aumentar el tiempo de producción por pieza, lo que a su vez conduce a un incremento del coste.
3. Enfriamiento y solidificación
Después de crear el cuerpo hueco, hay que enfriarlo hasta que salga del intervalo termoelástico y mantenga su forma al retirar el molde. Por consiguiente, un sistema de enfriamiento eficiente y eficaz puede tener un gran impacto en la eficiencia de cualquier proceso de moldeo por soplado.
Al igual que con el calentamiento y el moldeo, el enfriamiento y la solidificación se deben realizar de forma uniforme para evitar daños. Además, enfriar demasiado rápido puede provocar deformidades e irregularidades en la pieza final. Muchas máquinas de moldeo por soplado usan aire comprimido enfriado y/o canales de fluido de refrigeración para aumentar la eficiencia del proceso de moldeo por soplado.
4 Desmoldeo y posacabado
Cuando la temperatura haya bajado por debajo del intervalo termoelástico, el cuerpo hueco se podrá retirar del molde y trasladarlo a una cadena de producción donde se pueda quitar la rebaba, recortarlo, revisarlo en busca de fugas, evaluar su calidad y embalarlo para el envío.
En muchas cadenas de fabricación moderna, el desmoldeo y el posacabado puede estar automatizado casi por completo, incluso en los pasos de recorte y comprobación de fugas, aunque es posible que los diseños especialmente grandes o que estén hechos a medida requieran un acabado manual. Sin embargo, una supervisión humana sigue siendo una parte crucial de la mayoría de los procesos de moldeo por soplado, tanto para el control de calidad como para el embalaje final.
Tipos de proceso de moldeo por soplado
Hay tres tipos principales de moldeo por soplado: el moldeo por extrusión-soplado (EBM), el moldeo por inyección-soplado (IBM) y el moldeo por inyección, soplado y estiramiento (ISBM). Las principales diferencias entre estos tres tipos se encuentran en cómo se da forma a la preforma de plástico o paresón.
Moldeo por extrusión-soplado (EBM)
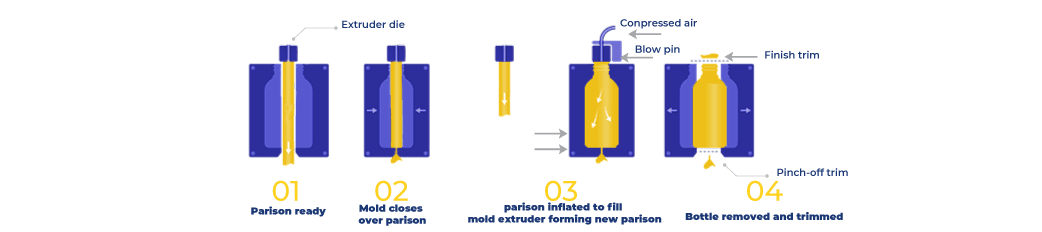
Fuente: GAP Polymers
El moldeo por extrusión-soplado (EBM) es el tipo de moldeo por soplado más común y también el más simple y económico. Sin embargo, los productos creados mediante EBM suelen tener limitaciones en cuanto a su complejidad estructural y su nivel de detalle.
En el EBM, se introduce plástico fundido a través de un extrusor, formando un tubo hueco: el paresón. A continuación, el molde se cierra en torno al paresón. Después, se usa aire presurizado para inflar el paresón hasta que llene por completo la cavidad del molde, encajando con sus contornos internos.
Después de que el paresón se haya inflado por completo, tiene lugar el proceso de enfriamiento y solidificación, que cuenta con frecuencia con la ayuda de canales de fluido de refrigeración o de aire comprimido. Sin embargo, al ser el EBM el tipo más básico de moldeo por soplado, algunas máquinas de EBM están hechas para que enfriamiento tenga lugar de forma natural, sin ayuda.
El moldeo por extrusión-soplado se usa a menudo con el polietileno, un plástico popular para depósitos agrícolas, envases de fluidos automovilísticos (como aceite para motor y refrigerante), botellas de champú y muchos otros productos comunes. El EBM también es el método más común para el moldeo por soplado de nylon.
Además de las restricciones que tiene en cuanto a la complejidad estructural y el nivel de detalle, los técnicos de fabricación pueden toparse con que no pueden obtener la variación del grosor de las paredes que requiere su producto y verse obligados a recurrir al IBM o el ISBM. Sin embargo, para usos como el de recipientes y botellas simples, el EBM es suficiente.
Además, aunque el EBM solo permite una proporción de inflado pequeña a mediana, la pieza final producida mediante EBM puede ser bastante grande, lo que lo convierte en el método preferido para producir productos como bidones industriales, maletines y depósitos de combustible.
Moldeo por inyección-soplado (IBM)
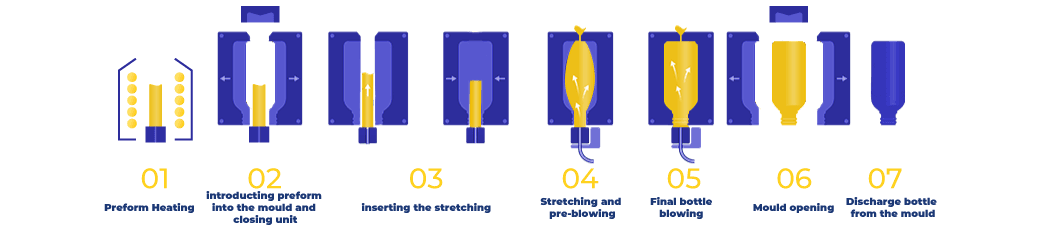
Fuente: GAP Polymers
El moldeo por inyección-soplado (IBM) combina el moldeo por inyección y el moldeo por soplado. En primer lugar, se crea la preforma inyectando plástico fundido en un molde y después se enfría para crear un paresón. A continuación, la preforma se traslada a la cavidad del molde de soplado, se recalienta y se llena con aire comprimido hasta que se expande para llenar la cavidad del molde. A partir de ese punto, el proceso es muy similar al EBM: el plástico moldeado se enfría, se retira del molde de soplado, se recorta y se envía.
Sin embargo, el paso de moldeo por soplado no siempre requiere que el paresón se caliente hasta la misma temperatura que cuando se moldeó por inyección. Esto hace que con frecuencia, el moldeo por inyección-soplado sea una opción superior para los fabricantes que trabajan con materiales que tienen un tiempo de secado largo, como el PET, el material más común para fabricar botellas de agua y de refrescos.
El IBM también es más adecuado que el EBM para formas complejas o para productos con tolerancias más ajustadas (por ejemplo, botellas de medicamentos que tengan una tolerancia estricta para su cuello). Por lo tanto, es probable que los fabricantes de los sectores de la cosmética y los productos farmacéuticos recurran al moldeo por inyección-soplado debido a su mayor precisión. No obstante, los varios pasos que conlleva el proceso y la mayor complejidad de los diseños hacen que las herramientas puedan ser mucho más caras y que el tiempo por pieza total sea superior al del EBM.
Moldeo por inyección, soplado y estiramiento (ISBM)

Fuente: GAP Polymers
Al igual que el IBM, el moldeo por inyección, soplado y estiramiento (ISBM) puede obtener una mayor complejidad de las piezas y una mayor precisión dimensional que el EBM. A menudo, sobre todo cuando se utiliza PET como plástico, el ISBM permite fabricar con un nivel de detalle incluso mayor y elementos de diseño más finos que el IBM. Como extra, algunos procesos de fabricación mediante ISBM reducen o eliminan el plástico sobrante, que crea menos desperdicio y un producto acabado más liso.
El ISBM es muy similar al IBM en el sentido de que es un proceso de dos pasos que comienza por usar el moldeo por inyección para crear la preforma. Sin embargo, una vez que la preforma se ha transferido al molde de soplado y se calienta, se alarga una barra vertical para estirar la preforma antes de inyectar el aire presurizado. Este paso adicional crucial hace que el ISBM sea capaz de producir formas ovaladas, cuadradas y poligonales que podrían dar problemas a otros métodos.
El ISBM conlleva un paso adicional respecto al IBM, el estiramiento, con lo que los tiempos de procesamiento son ligeramente más largos y, de media, tiene los costes más elevados de los tres métodos principales de moldeo por soplado de plásticos.
Materiales para el moldeo por soplado
Material | Características | Coste | Módulo de flexión (aproximado)* | Temperatura de flexión bajo carga (aproximada)* | Aplicaciones |
---|---|---|---|---|---|
Polietileno de alta densidad (PEAD) | Translúcido, de dureza moderada, fácil de teñir | € | 1170 MPa | 71 °C | Depósitos agrícolas, bidones industriales, maletines, botellas de fluidos automovilísticos, botellas de champú |
Polietileno de baja densidad (PEBD) | Translúcido, de dureza baja a moderada, fácil de teñir | €€ | 275 MPa | 60 °C | Botes dispensadores de plástico, defensas de embarcaciones, película soplada para bolsas de plástico |
Tereftalato de polietileno (PET) | Transparente, bastante duro, fácil de teñir, fuerte protección contra la humedad | €€ | 3400 MPa | 79 °C | Botellas de agua y refresco, jarras de plástico |
Polipropileno (PP) | Translúcido (pero algunas mezclas pueden ser casi transparentes), dureza moderada a alta, fácil de teñir, esterilizable en autoclave | € | 1030 MPa | 77 °C | Tubos para automóviles y electrodomésticos, recipientes para alimentos, cajones de almacenamiento de plástico |
Cloruro de polivinilo (PVC) | Transparente (pero fácil de teñir hasta darle opacidad), dureza muy variable, duradero | €€ | 2300 MPa | 79 °C | Fuelles, conos de tráfico, tuberías, racores |
Nylon (poliamida, PA) | Translúcido, de dureza moderada, fuerte, resistente a los impactos | €€€€ | 2900 MPa | 169 °C | Tubos y depósitos automovilísticos |
Policarbonato (PC) | Transparente, bastante duro, fácil de teñir, muy tenaz, resistente a los impactos | €€€ | 2350 MPa | 143 °C | Botellas de agua de gran tamaño, recipientes de almacenamiento de alimentos, jeringas |
Copolímero de olefina cíclica (COC) | Transparente, duro, esterilizable en autoclave, fuerte protección contra la humedad | €€€€ | 2480 MPa | 77 °C | Película soplada, envoltura retráctil, jeringas, almacenamiento médico (alternativa al vidrio) |
Acrilonitrilo butadieno estireno (ABS) | Opaco, duro, tenaz, resistente a los impactos | €€€ | 2680 MPa | 88 °C | Carcasas para componentes electrónicos, parachoques automovilísticos, maletines, tuberías y mangueras |
*los valores de temperatura de flexión bajo carga y módulo de flexión dependerán del equilibrio de ingredientes y del proceso de fabricación específico de una remesa dada
Desarrollo de productos para el moldeo por soplado con la impresión 3D
Debido a los elevados costes iniciales, a los procesos de utillaje complicados y caros y a la falta de pericia en la fabricación, muchas empresas que necesitan producir piezas moldeadas por inyección actualmente externalizan su diseño y su producción. Los moldes en sí mismos a menudo se hacen con aluminio, zinc o aleaciones de acero, materiales que resultan caros de mecanizar. Incluso si una empresa subcontratada es capaz de prototipar los moldes, los servicios de diseño traen consigo con frecuencia un precio elevado y un tiempo de entrega lento, con lo que un prototipado verdaderamente iterativo se vuelve inviable.
Sin embargo, la impresión 3D ahora puede dar a las empresas la capacidad de prototipar y diseñar sus moldes ellas mismas en sus propias instalaciones, reduciendo el coste y el tiempo de espera necesarios para desarrollar un embalaje de plástico hueco para su producto. Aunque muchas empresas siguen optando por externalizar la producción, la impresión 3D les da un mayor control sobre el producto final, con unos tiempos y unos costes más reducidos.
Unilever ha recurrido recientemente a la impresión 3D para reducir los costes y agilizar el proceso de diseño para los embalajes de productos de plástico. Junto con su socio de fabricación Serioplast, validaron los moldes impresos en 3D para el moldeo por soplado y estiramiento de bajo volumen usando la impresora 3D de estereolitografía (SLA) Form 3L de Formlabs y la Rigid 10K Resin de Formlabs.
"Con el molde impreso en 3D, podemos ahorrar hasta un 70 % de tiempo y un 90 % de costes respecto al molde estándar. Anteriormente, [los clientes] tenían que esperar hasta 12 semanas para recibir la pieza de un único diseño, mientras que ahora podemos hacer cinco diseños".
Flavio Migliarelli, director de diseño para I+D de Serioplast Global Services
Dado que una impresora 3D puede producir piezas en unas horas y los moldes cuestan menos que el utillaje de metal, las empresas ahora disponen de un grado de control mayor en el desarrollo de piezas de plástico huecas. Los diseños de moldes se pueden crear digitalmente mediante CAD y exportarlos a una impresora 3D, que puede producir utillaje rápido muy detallado usando materiales que son lo bastante fuertes y resistentes a las altas temperaturas como para usarlos en una máquina de moldeo por soplado. Esto permite a las empresas prototipar tanto el molde como la pieza final, y si hace falta realizar un cambio en el diseño, el molde rediseñado se puede imprimir de forma rápida y económica.
"Puedes tener una botella real antes de fabricar el molde real; así se puede identificar inmediatamente si el desarrollo está siguiendo el camino adecuado o si hace falta cambiar algo antes de cometer errores que salgan más caros.
Stefano Cademartiri, propietario de CAD y Prototipado de Unilever
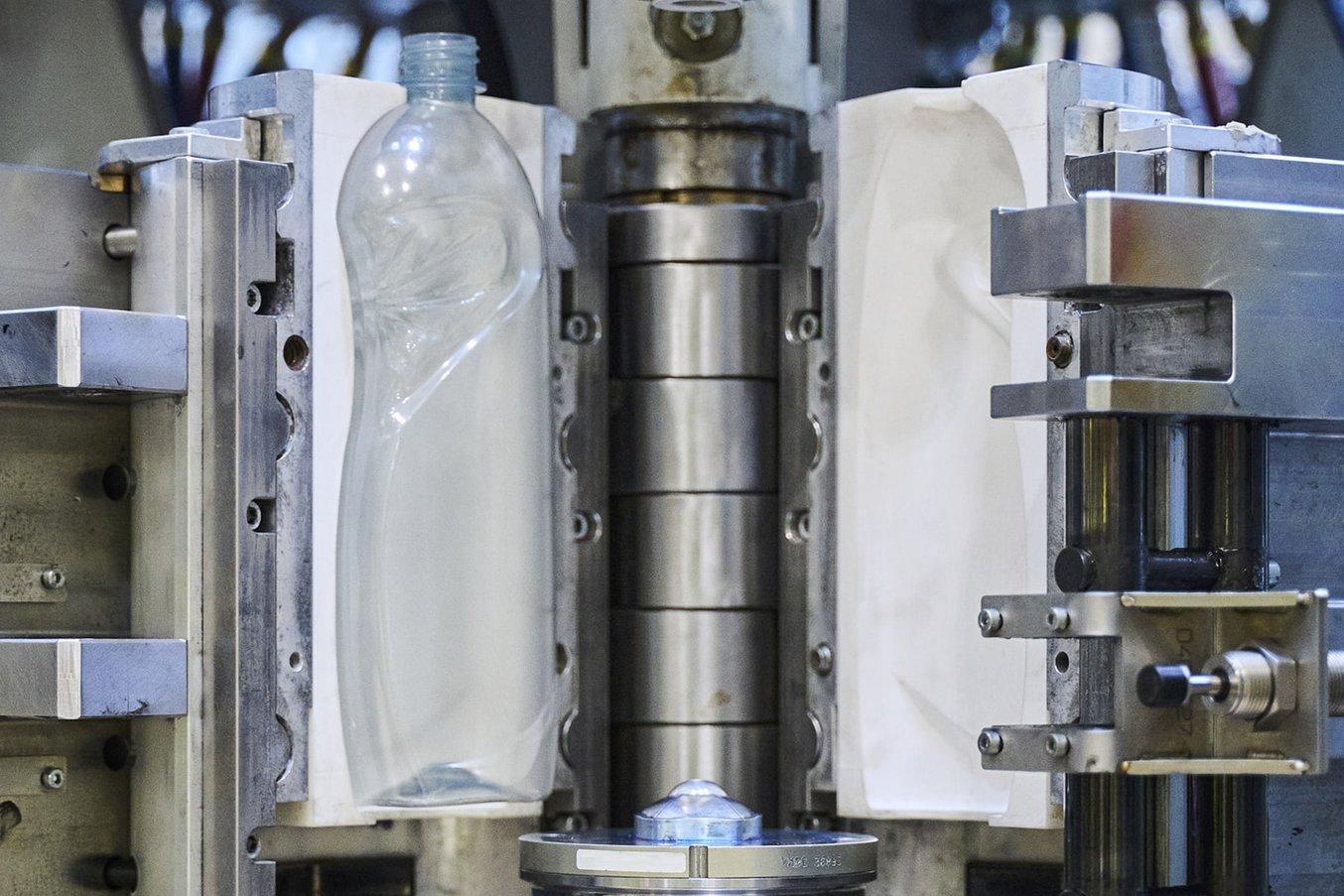
Molde impreso en 3D con la Rigid 10K Resin para una botella de 750 ml que Slice Design creó para Unilever, instalado en las abrazaderas que sujetan la cáscara del molde en la máquina. El equipo puede usar la misma ventana de proceso que con un molde piloto estándar, lo que permite someter a ensayo el proceso final de forma fiable.
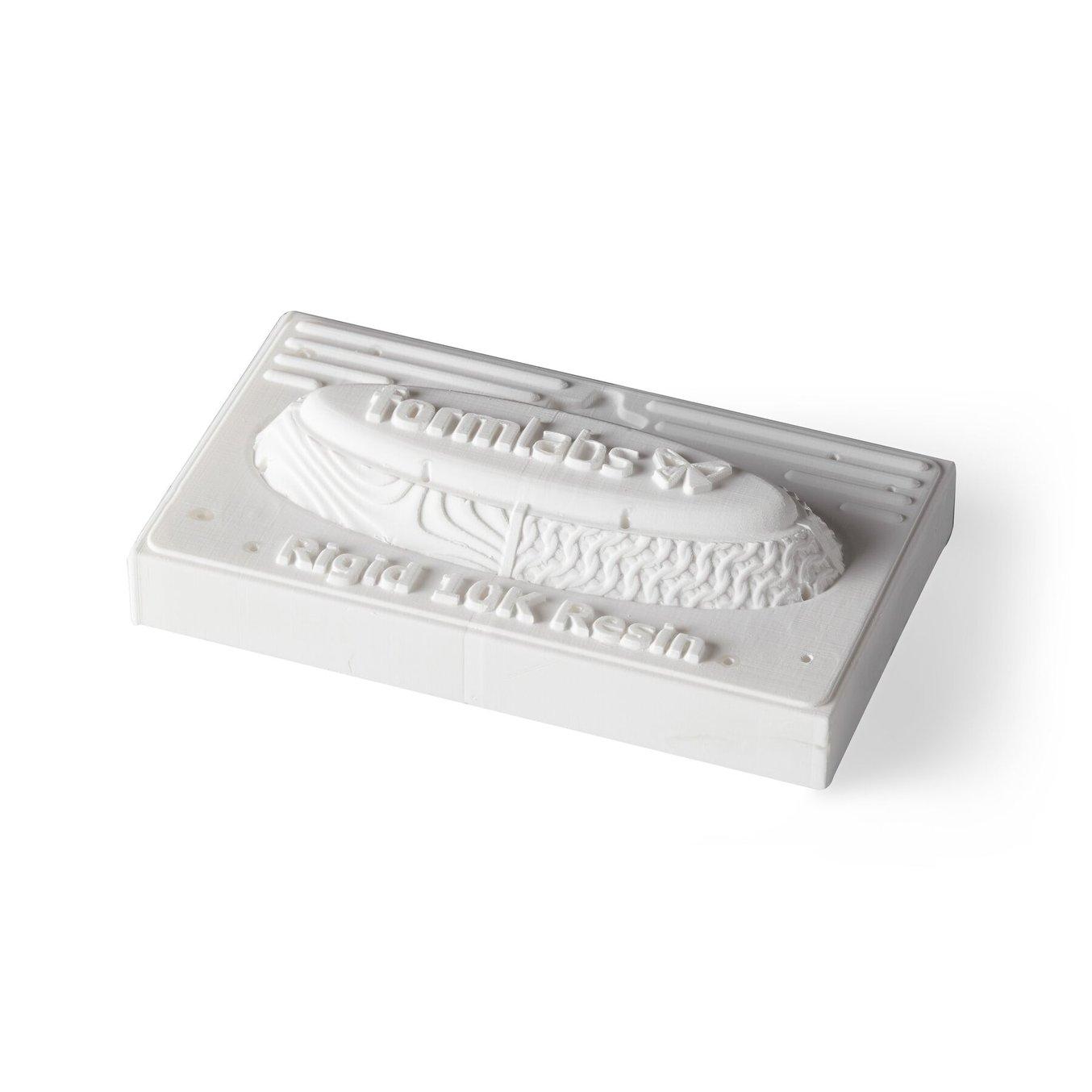
Solicita una pieza de muestra gratuita
Experimenta la calidad de Formlabs de primera mano. Enviaremos una pieza de muestra gratuita a tu lugar de trabajo.
Empieza a moldear por soplado
El moldeo por soplado de plásticos es un proceso de fabricación popular que se usa en un amplio abanico de sectores y admite diversos materiales populares. Fundamentalmente, el moldeo por soplado consiste en usar aire presurizado para inflar un plástico termoelástico y adaptar su forma a un molde. Cuando alcanza la forma deseada, se enfría, se posacaba y se envía al cliente.
Los materiales populares para el moldeo por soplado incluyen el polietileno (PE), el tereftalato de polietileno (PET) y el polipropileno (PP). Su versatilidad en cuanto a los materiales, su escalabilidad y su fiabilidad hacen que el moldeo por soplado sea una parte esencial de la fabricación de productos de embalaje, contenedores de almacenamiento y componentes de máquinas para los sectores de las mercancías embaladas, la automoción, la agricultura, los productos farmacéuticos y la cosmética, entre otros.
Hoy en día, tecnologías como la impresión 3D están reduciendo los obstáculos para que fabricantes tanto pequeños como grandes accedan al moldeo por soplado, principalmente al hacer posible un prototipado iterativo de los moldes. Los diseñadores de productos y los pequeños fabricantes que hayan tenido que externalizar el diseño y la producción de los moldes de soplado pueden usar la impresión in situ para obtener un mayor control sobre el proceso a un coste reducido.
En función del uso que se le dé, quien se inicie en el moldeo por soplado puede elegir entre el moldeo por extrusión-soplado (EBM), el moldeo por inyección-soplado (IBM) y el moldeo por inyección, soplado y estiramiento (ISBM). En general, el EBM ofrece tiempos de entrega más rápidos y una gama de tamaños más amplia, al mismo tiempo que limita el nivel de detalle y la complejidad de los diseños. El IBM hace posible un gran nivel de detalle en el diseño, pero el tamaño de la pieza final puede ser limitado. A su vez, el ISBM puede ofrecer un mayor abanico de opciones en cuanto a las formas. El EBM tiende a costar menos que el IBM y el ISBM.
¿Quieres aprender más acerca del moldeo por soplado con moldes impresos en 3D? Descarga nuestro libro blanco para disponer de recomendaciones detalladas para el uso de moldes impresos en 3D en el proceso de moldeo por soplado y para conocer en profundidad un caso de estudio real con Unilever y Serioplast.