Cómo fomentar la personalización y el ahorro de costes: Labconco y su salto estratégico a la impresión 3D
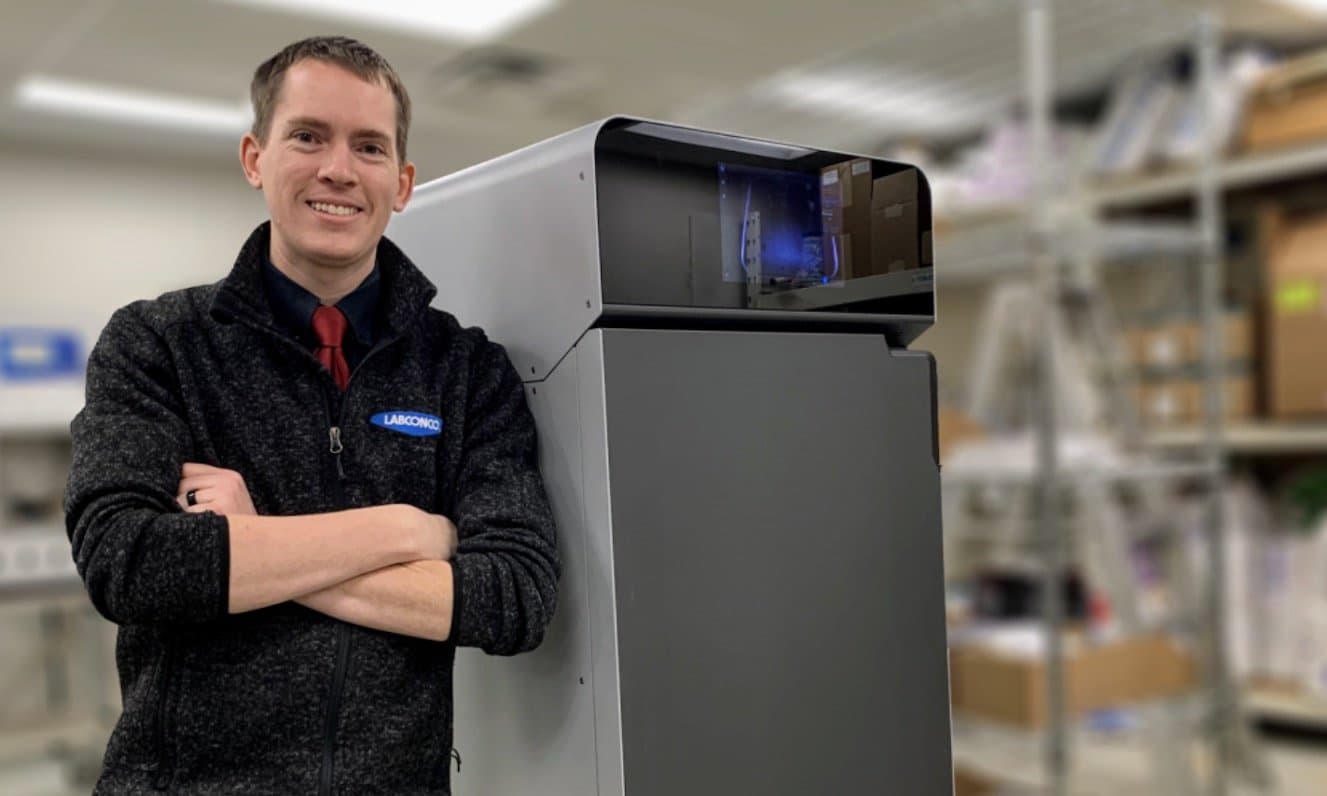
En la primera reunión de Brent Griffith en Labconco a principios de 2020, la impresión 3D entró en escena de forma espectacular. El equipo se había reunido en parte para hablar de un pequeño componente para su nuevo producto Logic Vue que se tenía que moldear por inyección. Dado que se trataba de un producto nuevo y no se habían establecido las cantidades del suministro, era posible que la herramienta necesaria para ello, valorada en más de 15 000 €, solo tuviera que producir 100 piezas en el primer año. Que el coste resultante fuera tan alto hizo que el grupo buscara nuevas soluciones. "Tomé la palabra y dije: 'Yo podría imprimir eso en 3D y tener todas esas piezas que esperamos para un año terminadas para mañana'. Todo el mundo se quedó callado", dice Brent Griffith, ingeniero de productos de Labconco.
En ese momento, Labconco no tenía ninguna impresora 3D propia. Cuando Griffith volvió al día siguiente con varias versiones del componente impresas en las impresoras que él mismo tenía en casa, la viabilidad de este uso de la impresión 3D quedó fuera de toda duda.
Hoy, Griffith supervisa un laboratorio en crecimiento con tres impresoras de sinterizado selectivo por láser (SLS) Fuse 1+ 30W, la Fuse Sift y la Fuse Blast, una impresora de estereolitografía (SLA) Form 3L y varias impresoras de modelado por deposición fundida (FDM) para Labconco, una empresa que fabrica equipamiento de laboratorio para diversos sectores, como el de las pruebas alimentarias, el del desarrollo farmacéutico, el de los diagnósticos oncológicos y el de la criminalística. Griffith ahora está imprimiendo cientos de piezas a la semana que son mejores que los anteriores componentes mecanizados o moldeados, que sirven como soluciones provisionales cuando los problemas en la cadena de suministro afectan a la producción y que ayudan en las fases de desarrollo de los muchos nuevos productos de Labconco.
La construcción del caso
Después de que Griffith demostrara la viabilidad del caso de uso de negocio con ese primer componente impreso en 3D, empezó a imprimir otras piezas para ingenieros de las oficinas con el fin de apoyar su trabajo de desarrollo, y pronto se formó una cola. "La cosa se puso movida muy rápido", dice Griffith.
Para averiguar qué más se podía hacer con la impresión 3D, él y otro ingeniero llamado Austin Orme se dispusieron a realizar una auditoría de las miles de piezas, herramientas y componentes que intervienen en la creación de los productos de Labconco. "Las instrucciones que recibimos fueron encontrar una máquina que tenga un volumen de impresión excelente y que produjera piezas de muy alta calidad que pudiéramos usar tanto para los prototipos como para la fabricación", dice Griffith. "Pronto descubrimos que no bastaría con solo una máquina para hacerlo, ya que no nos daría las capacidades y la flexibilidad que necesitábamos para alcanzar el éxito". El laboratorio acabó incorporando seis impresoras para empezar, entre las que se encontraban tres impresoras SLS Fuse 1+ 30W y una impresora SLA de gran formato Form 3L.
"Compramos la Form 3L porque queríamos acceder al catálogo de resinas de Formlabs. Sabía que nos aportaría flexibilidad y nos abriría las puertas a nuevas oportunidades. Hasta ahora, ha cumplido con exactitud esas esperanzas".
Brent Griffith, ingeniero de productos
Entre el abanico de materiales disponibles para la Form 3L y los volúmenes de producción medios a altos que se podían conseguir con tres impresoras de la serie Fuse, Griffith ha podido mejorar productos ya existentes, ahorrar decenas de miles de euros en costes de utillaje, acelerar el desarrollo de proyectos ya existentes y reemplazar piezas bajo demanda.
Reemplazar, mejorar, escalar: Las aplicaciones de la impresión 3D en Labconco
Sensor de nivel de líquido de SLS: Reemplazar un conjunto moldeado
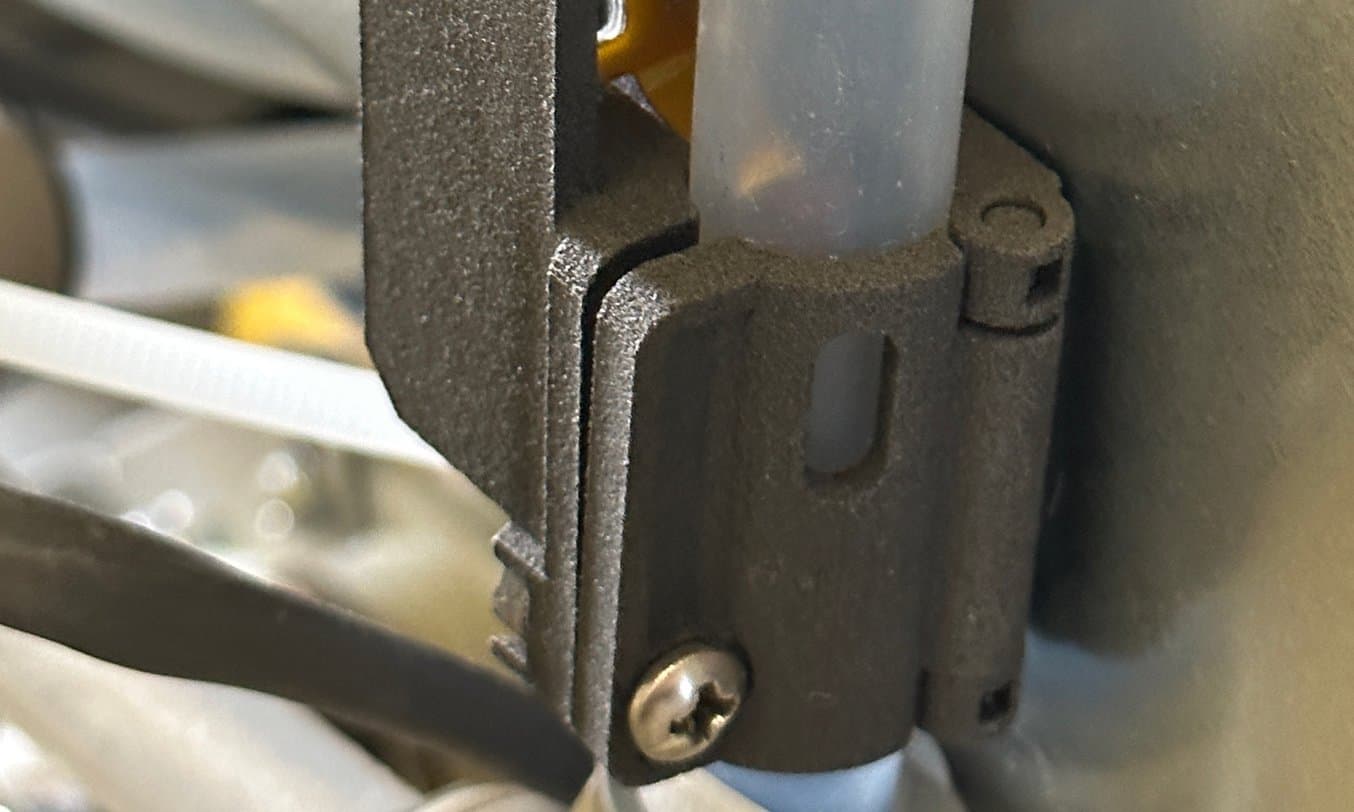
Este componente de sensor de nivel de líquido tiene un elemento de bisagra funcional que el ingeniero de productos de Labconco Tim Grove diseñó después de ver la muestra estándar del Nylon 12 Powder. El elemento permite que la pieza se imprima como un único componente en vez de como un conjunto de varias piezas, reduciendo el tiempo de trabajo manual y los costes de material.
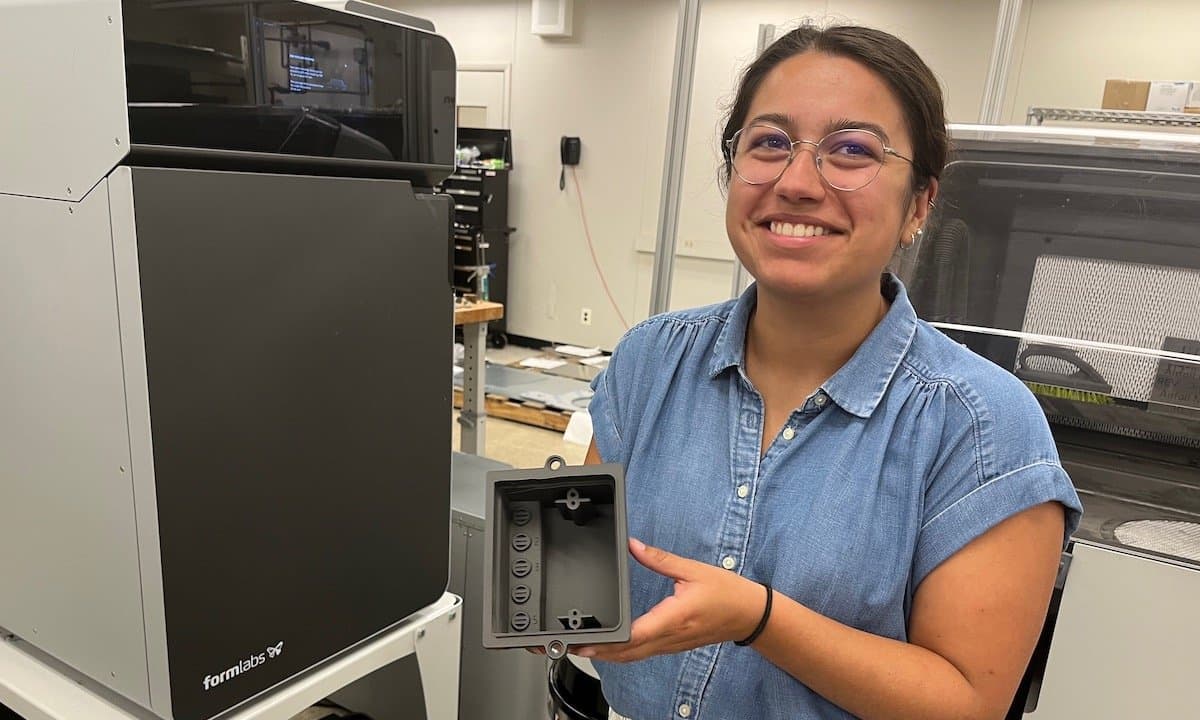
Al haber podido escalar el equipo de ingeniería de productos de Labconco su espacio de impresión 3D de forma tan eficaz, muchos miembros del equipo tienen acceso a tecnología industrial como la de las impresoras SLS de la serie Fuse. Griffith dice que ahora, varios departamentos de Labconco están empezando a pensar en cómo incorporar la impresión 3D en sus procesos de trabajo típicos para reducir costes, ganar flexibilidad y proteger su cadena de suministro.
La línea de lavadoras de recipientes de vidrio de Labconco incorpora avances de ingeniería de vanguardia, como componentes de fabricación aditiva. Uno de los componentes, un soporte para sensor de nivel de líquido, actúa como respaldo para la protección contra desbordamientos. En el proceso convencional, este componente se habría producido mediante el moldeo por inyección de dos piezas separadas, seguido de un ensamblaje en el que un pasador mantiene juntas las dos piezas.
Sin embargo, Tim Grove, un ingeniero de productos de Labconco, reconoció el potencial de ahorro de costes y tiempo que podría ofrecer la fabricación mediante la impresión 3D SLS. Inspirándose en el diseño de bisagra que aparece en la muestra estándar del Nylon 12 Powder de la misma Formlabs, Grove se dedicó a reimaginar el soporte del sensor de nivel de líquido, con el objetivo de optimizar el ensamblaje y eliminar los gastos asociados con hacer pedidos de múltiples herramientas.
Mediante una colaboración iterativa con Griffith, Grove pasó por múltiples versiones de la pieza, asegurándose de que tuvieran una funcionalidad sin defectos y un rendimiento sin inconvenientes.
"Sale de la impresora con la bisagra ya funcionando y lista para usar, lo que supone un ahorro de costes y nos da flexibilidad en la producción. El Nylon 12 Powder que se usa con la serie Fuse es un buen punto medio para nosotros en lo que respecta a los polímeros. Encontramos muchas aplicaciones para él y funciona de maravilla", dice Griffith.
Sensor de nivel de líquido de SLS | Número de componentes | Tiempo de trabajo manual de ensamblaje (con 50 componentes) | Coste por pieza acabada (con trabajo manual) | |
---|---|---|---|---|
Moldeado | 3 | 1 hora | 4,45 € cada uno + utillaje | |
Impreso en 3D por SLS | 1 | 0 | 2,56 € cada uno |
Rueda de ventilador de SLA: Soluciones para la obsolescencia de los suministros
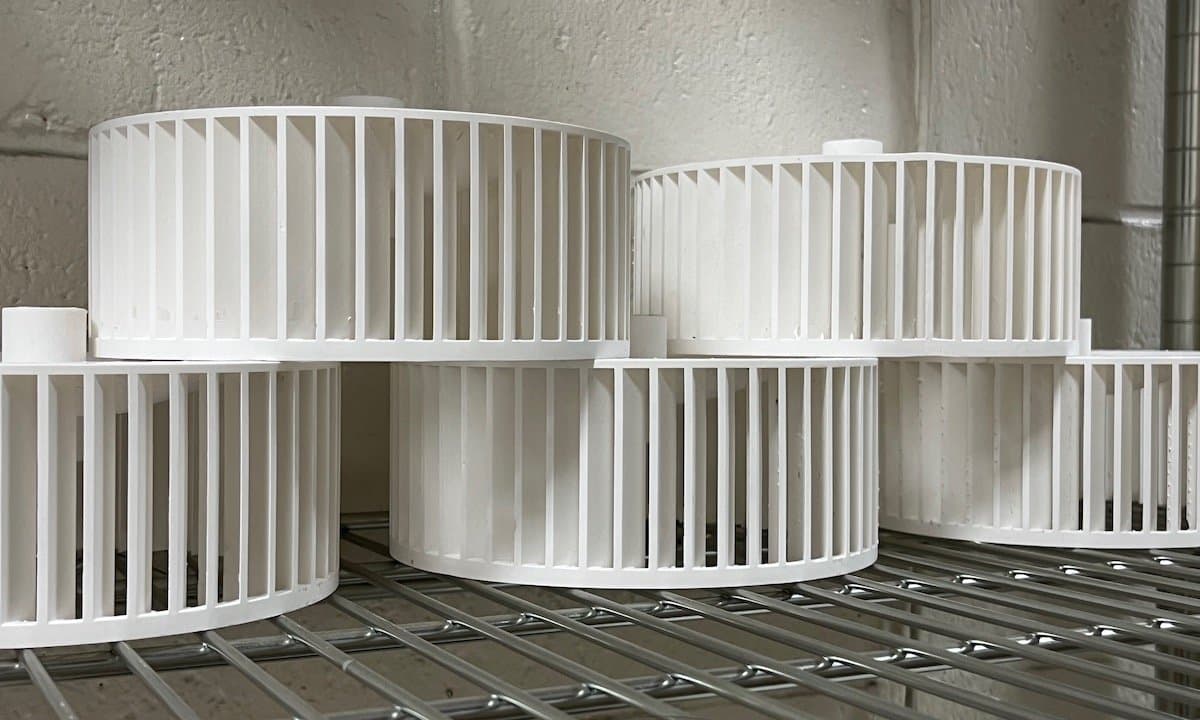
Este componente, que se utiliza en el analizador de grano Kjeldahl de Labconco, se compraba previamente a un proveedor externo, hasta que este decidió dejar de fabricar la pieza. Griffith aplicó ingeniería inversa al componente e imprimió la nueva versión en la Form 3L con la Rigid 10K Resin cada día durante más de un mes, volviendo a abastecer sus existencias de componentes de recambio y protegiéndose de problemas con la cadena de suministro en el futuro.
En lo que respecta al aparato Kjeldahl de Labconco, que se usa para analizar granos, el equipo estaba trabajando con un proveedor externo que producía una pieza para una rueda de ventilador crucial. Las cantidades eran bajas y el proveedor decidió dejar de fabricar la pieza cuando el utillaje alcanzó el final de su vida útil.
Labconco se enfrentaba a la búsqueda de un nuevo proveedor, a tener que esperar al diseño y a la producción de una nueva herramienta y una serie de moldeo y al alto coste de los materiales y la mano de obra. "Hemos examinado una docena de soluciones diferentes y ninguna se acerca a cumplir con nuestras especificaciones, particularmente en lo que respecta a la compatibilidad química. Por eso, acabé tomando una copia para aplicar ingeniería inversa al componente, optimizarlo e imprimirlo con la Rigid 10K Resin", dice Griffith. "Después de someterlo a ensayo para ver si aguantaría, decidimos que era la mejor solución".
Su nueva impresora de gran formato, la Form 3L, había llegado justo a tiempo. Imprimieron durante 40 días seguidos la rueda de ventilador que habían obtenido de la ingeniería impresa para reponer sus existencias de la pieza.
"La Rigid 10K Resin ha sido nuestra elección habitual para varios componentes. La compatibilidad química encajaba con lo que nos hacía falta en cuanto a ácidos; especialmente, en este caso, ácido sulfúrico vaporizado. Ahorramos cientos de horas de verificar proveedores y materiales que acaban no sirviendo al cambiar a la fabricación aditiva. En este sentido, es un caso de uso de negocio fuerte", dice Griffith.
Rueda de ventilador de SLA | Coste |
---|---|
Original, moldeada | 178,77 € |
Rediseñada e impresa con la Rigid 10K Resin | 52,65 € |
Separador de jaula de rodamientos de SLS: de 500 € a 20 €
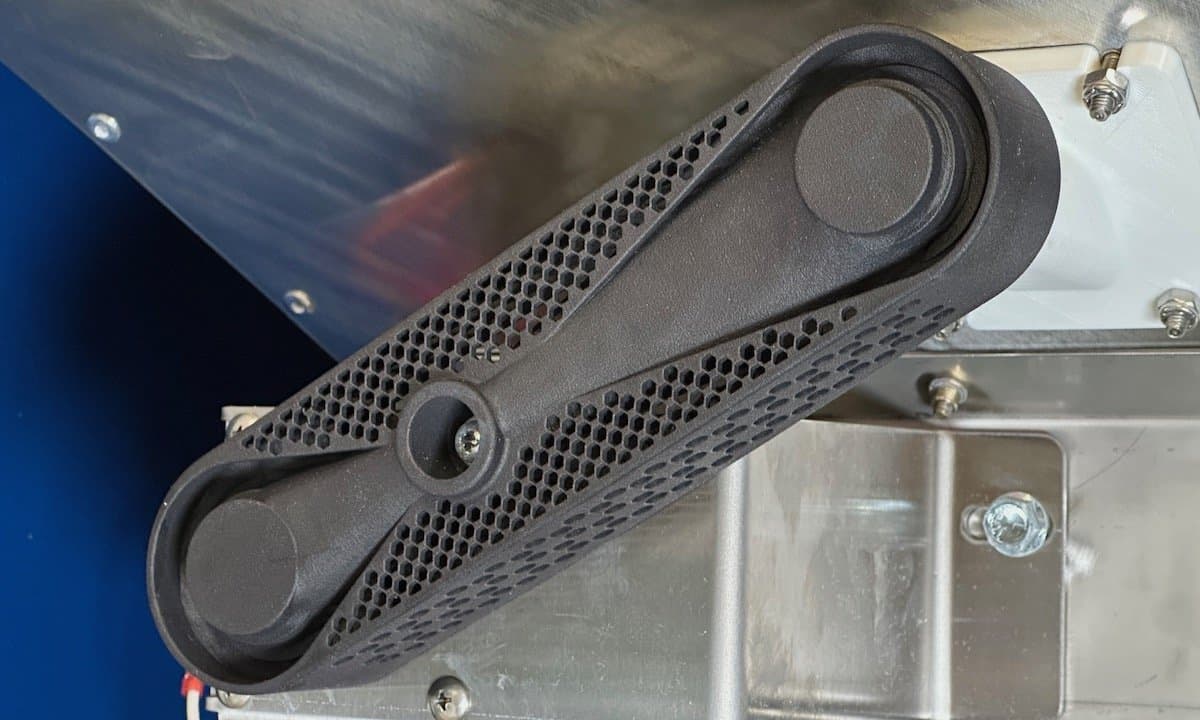
Griffith podría haber impreso esta pieza como una copia exacta del componente, que un mecanizador externo había presupuestado en alrededor de 500 €. En vez de eso, aplicó principios que había aprendido en el Programa de Diseño y Fabricación Aditiva de la Universidad Estatal de Pensilvania para rediseñar la pieza y aprovechar las posibilidades geométricas que ofrece la impresión 3D SLS. El nuevo componente cuesta a Labconco unos 21 €, ahorrándoles cientos de euros y reduciendo el tiempo de espera a menos de dos días.
Aunque algunos componentes pueden ser relativamente simples, fabricarlos mediante métodos tradicionales sigue pudiendo resultar caro. Un mecanizador presupuestó una pieza que separa dos rodamientos e impide que se vean atraídos entre sí en 500 €. La pieza era para un producto nuevo y Labconco ya había demostrado la viabilidad del caso de uso para su laboratorio de impresión 3D. Griffith empezó inmediatamente a imprimir el separador en la Fuse 1+ 30W y bajó el precio a unos 45 €, que se acerca a ser una décima parte de lo que costaría externalizar la pieza al mecanizador.
El proceso de mejora no se detuvo ahí. Griffith aplicó los principios que había adquirido durante su trabajo con el Programa de Diseño y Fabricación Aditiva de la Universidad Estatal de Pensilvania y convirtió lo que en principio era una mera sustitución del método anterior en una optimización completa.
"Era justo lo que yo había estado aprendiendo, cómo aplicar las oportunidades y las restricciones que conlleva la fabricación aditiva. En vez de preguntarnos si podemos hacer algo con la fabricación aditiva, la pregunta debería ser "¿deberíamos hacerlo con ella?" En este caso, podíamos realizar una sustitución directa, 1:1, pero de hacer eso, no habríamos aprovechado las oportunidades que ofrece la fabricación aditiva. Ya que disponíamos de estas impresoras de la serie Fuse, que tienen muy pocas restricciones reales en cuanto a la geometría de las piezas, podía desmelenarme un poco y probar cosas nuevas".
Brent Griffith, ingeniero de productos
Experimentó con reducir el material en toda la pieza mediante el diseño generativo, sin descuidar los elementos de seguridad del separador que protegen a los operarios. En un día, ya tenía un diseño revisado y optimizado, y Labconco empezó a imprimir en 3D mediante SLS las piezas en sus propias instalaciones por unos 20 € cada una.
"La impresión 3D ofrece grandes ventajas en cuanto a lo que se puede hacer con la geometría. Si se aligera una pieza o se aplican técnicas de diseño diferentes, se pueden combinar componentes de formas de las que no se han combinado anteriormente. Podemos realizar la fabricación in situ y ahorrar mucho dinero", dice Griffith.
Separador de jaula de rodamientos de SLS | Coste (incluyendo el de mano de obra) | Tiempo de espera |
---|---|---|
Mecanizado | 485,92 € | 2-3 semanas |
Sustitución SLS 1:1 | 43,50 € | 29 horas |
Optimizado para el SLS | 21,08 € | 28 horas |
Ensayos con piezas de SLS: Reducción de las cantidades de componentes y mejora de la funcionalidad
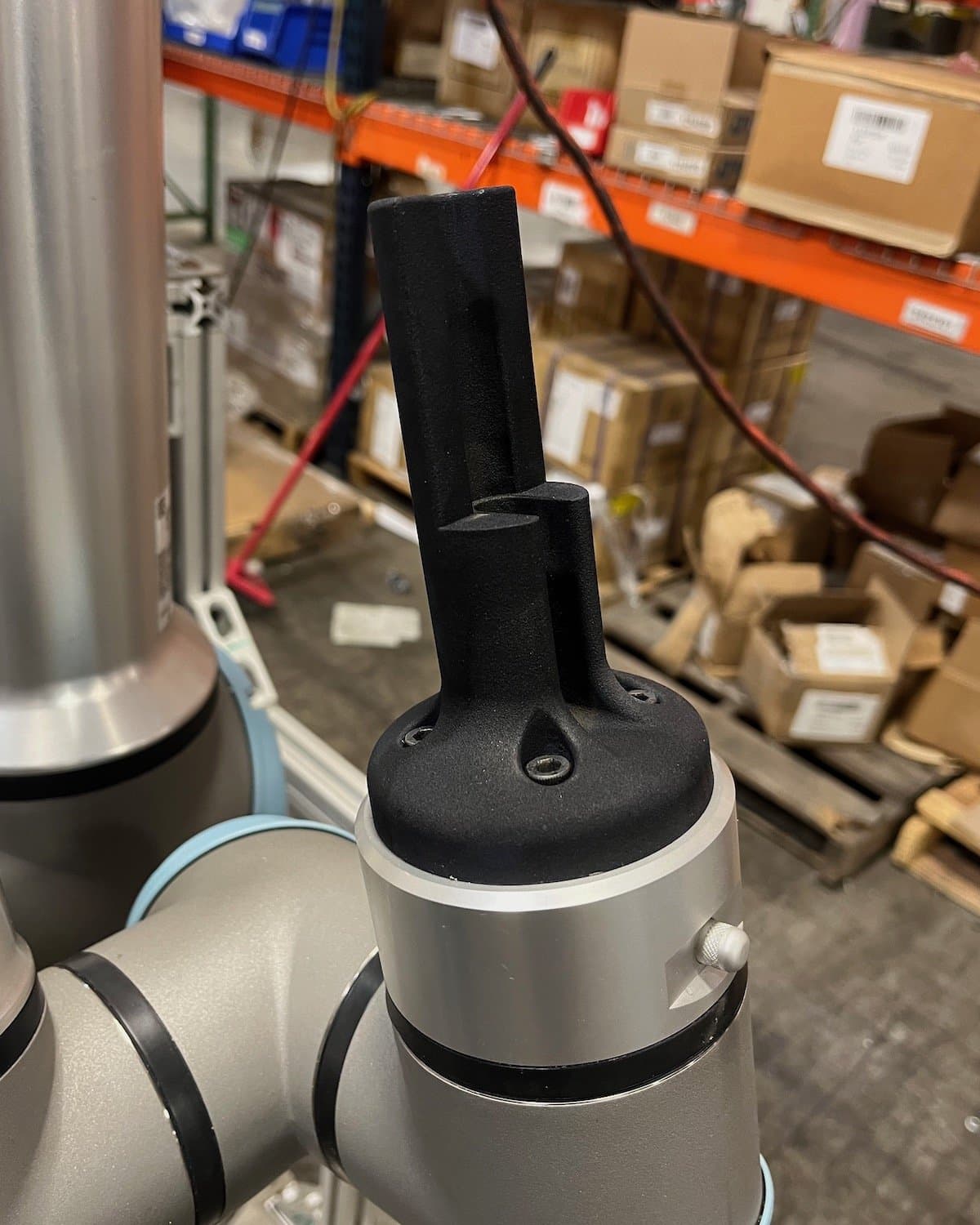
Para ayudar a que Labconco tenga una transición fluida a un proceso de trabajo híbrido que combine tareas manuales y accionadores robóticos, Griffith y el equipo diseñaron herramientas y efectores a medida y los imprimieron con el Nylon 12 Powder en sus impresoras de la serie Fuse.
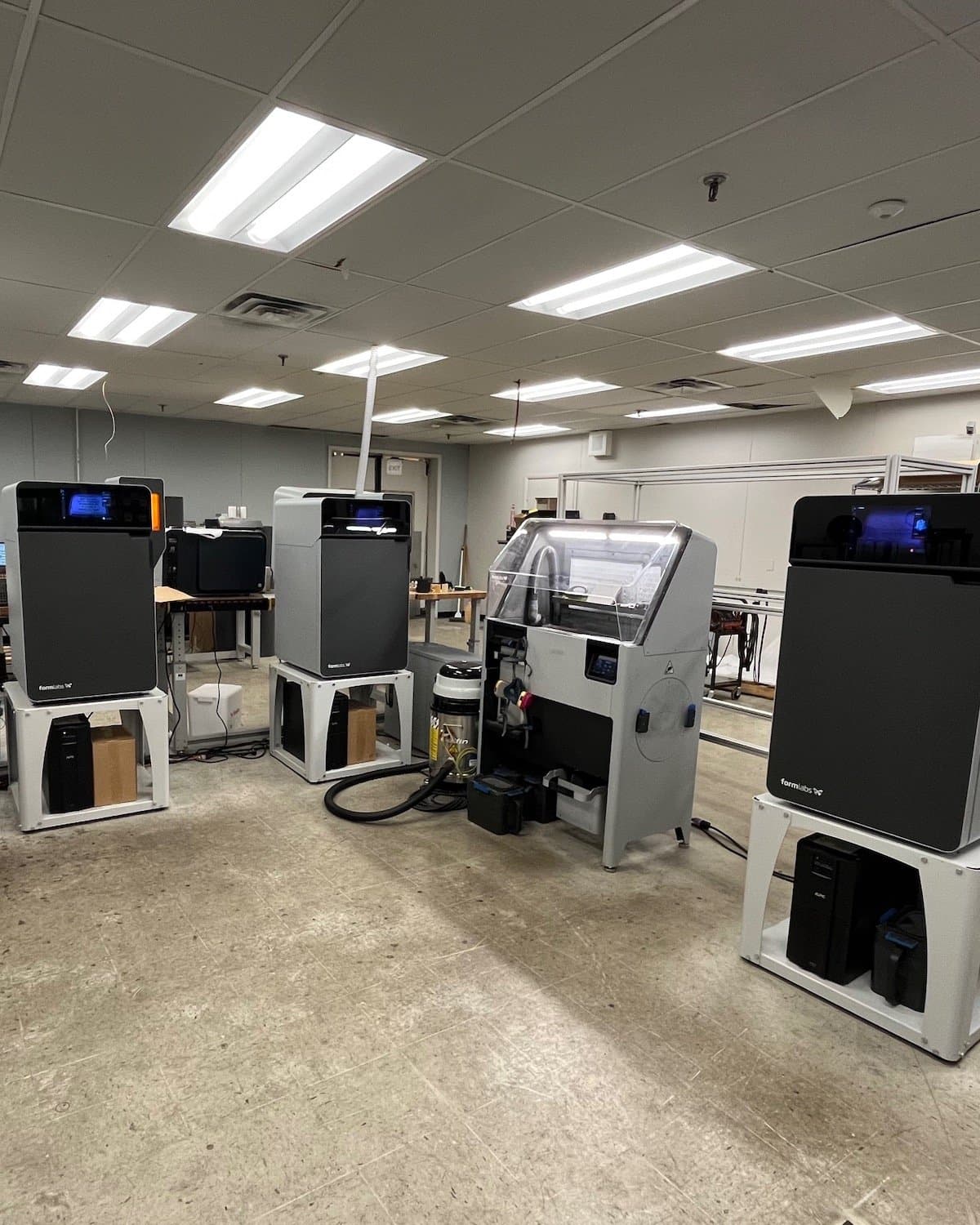
El tamaño compacto y la escasa huella energética de las impresoras 3D SLS de la serie Fuse hace que, a medida que Griffith y su equipo expanden su abanico de aplicaciones para piezas de SLS resistentes y duraderas, puedan seguir el ritmo de esa expansión escalando su trabajo de SLS.
La incansable búsqueda de la excelencia en Labconco llega hasta los ensayos de componentes importantes de uno de sus productos estrella: los armarios de seguridad biológica. Estos armarios son esenciales para proteger al personal y a los productos que se manipulan en su interior, gracias a patrones específicos del flujo de aire y a filtros HEPA. Para asegurar que su nivel de rendimiento es el máximo, estos filtros pasan por rigurosos ensayos y certificaciones antes de que se puedan marcar como completos.
Anteriormente, este proceso de ensayo dependía en gran medida de operarios humanos, lo que introducía posibles variaciones y limitaciones. No obstante, Labconco ha adoptado un enfoque transformador que emplea sistemas robóticos para automatizar el escaneado de cada filtro con una precisión impecable. Este paso a la automatización requería desarrollar utillaje y efectores terminales hechos a medida para los brazos robóticos encargados de realizar los ensayos. Los métodos tradicionales de fabricación resultarían exorbitantemente caros y podrían tardar meses, por lo que al necesitar un bajo volumen de piezas, imprimir en 3D estas piezas con las máquinas de la serie Fuse era una parte importante de la transformación.
Con las piezas de SLS que produce en sus propias instalaciones con la Fuse 1+ 30W, Labconco ha alcanzado un uso diario notable de estos componentes, que eleva la precisión y la fiabilidad de sus ensayos de seguridad de los productos. Esta adopción tan importante de la fabricación aditiva no solo ha optimizado las operaciones, sino que también ha dado a Labconco la capacidad de asegurar fuera de toda duda la seguridad y el rendimiento de sus productos.
Componentes del efector | Coste |
---|---|
Mecanizado | 508,32 € |
Impreso en 3D por SLS | 73,44 € |
Componente de campana extractora de humos: Producción SLS de volumen medio para un trabajo más ágil
Labconco fue la primera empresa en comercializar la producción de campanas extractoras de humos para laboratorios y ahora es una de sus divisiones de productos más importantes. Las campanas extractoras de humos son indispensables para las instalaciones químicas, farmacéuticas o agrícolas a gran escala.
Un componente, un tope mecánico que impide que los usuarios abran la puerta de la campana más allá de un punto concreto (ahorrando así energía), se fabricaba antes mediante moldeo por inyección. Pedir grandes cantidades de una única herramienta limitaba la capacidad de Labconco para hacer cambios o personalizar los pedidos para los clientes de gran envergadura. Las herramientas se desgastan y en ocasiones los proveedores se vuelven menos fiables a la hora de reemplazarlas. Para contrarrestar los problemas en la cadena de suministro, empezaron a imprimir estos topes para las puertas en la Fuse 1+ 30W y ahora Griffith produce entre 50 y 100 de estos componentes cada semana con el Nylon 12 Powder.
"Si se moldea la pieza, no es fácil hacer revisiones. Es tan raro que ocurra como cabría esperar, pero ha habido componentes que hemos moldeado por inyección y nos ha acabado perjudicando porque al ponerlos en práctica después de que nos los entreguen, se empiezan a romper o no funcionan como esperamos. Ahora los ingenieros saben que si pasamos a hacer algunas piezas con la impresión 3D, rediseñarlas supone mucho menos esfuerzo y hay más cambios que se pueden realizar en ellas. Es algo que no siempre se puede cuantificar con dinero y la fabricación aditiva tiene ventajas "intangibles" que en mi opinión, a menudo se pasan por alto", dice Griffith.
Otra ventaja de traer la tecnología de impresión 3D a nuestra empresa es la confianza que da a los empleados jóvenes que acaban de empezar su carrera profesional. Sin tener la carga de que el diseño deba ser absolutamente perfecto para pedir una nueva herramienta, están más dispuestos a probar cosas nuevas o a pensar en nuevas ideas. "Los ingenieros más jóvenes no tienen los 20 años de experiencia que permiten mirar una pieza y decir 'funcionará'. Poder imprimir en 3D y probar una cosa (o incluso muchas) y que falle sin que suponga un problema es estimulante", dice Griffith. "Permitir que se centren en encontrar la mejor solución, la más creativa, para un problema dado es la mentalidad que queremos que tengan, y la impresión 3D es una parte que influye mucho en ello".
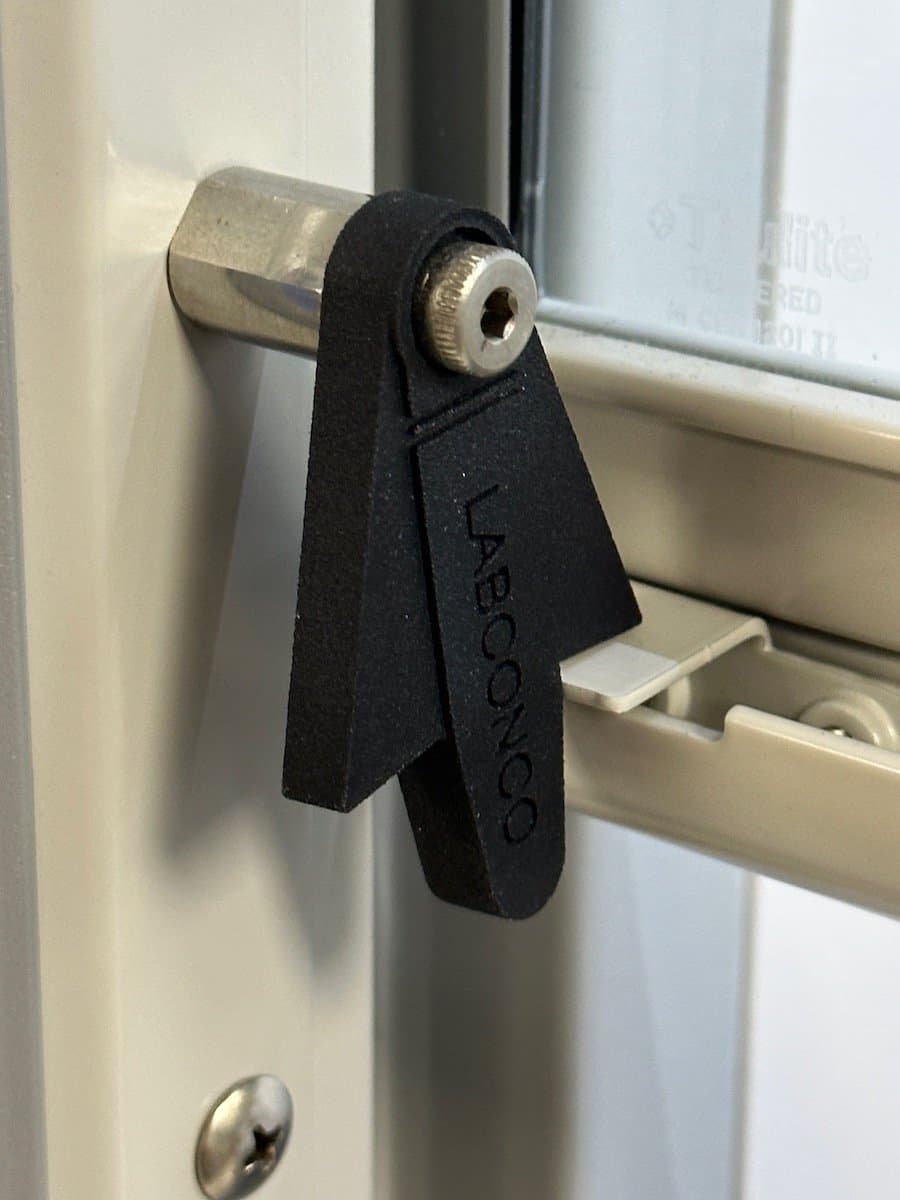
Griffith produce entre 50 y 100 de estos topes de puertas cada semana con el Nylon 12 Powder en la Fuse 1+ 30W, evitando tanto los costes como los riesgos de quedarse bloqueado en el proceso de trabajo de una herramienta.
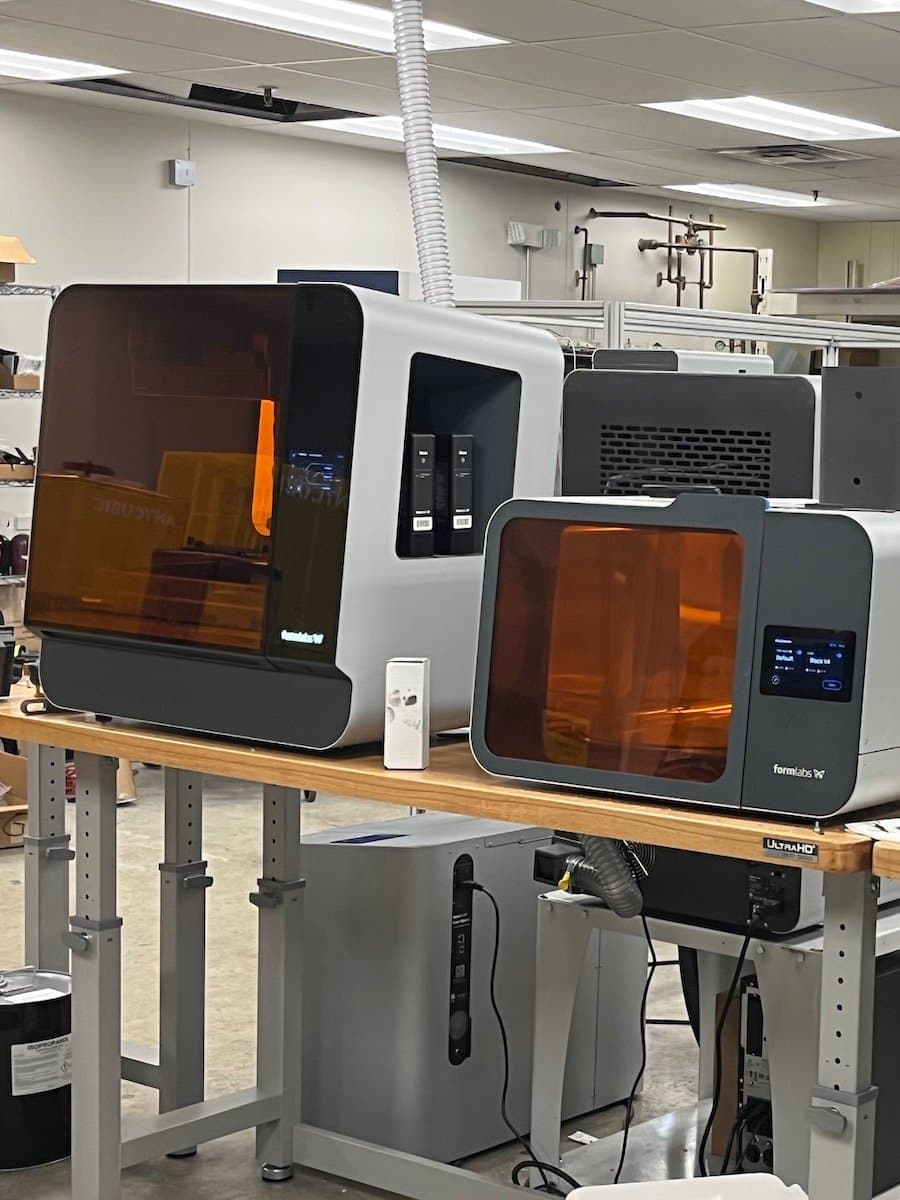
La facilidad de uso de las impresoras SLS y SLA (como la Form 3L y la Form Cure L que mostramos aquí) hace que los empleados jóvenes que acaben de empezar sus carreras profesionales puedan ganar confianza con nuevas tecnologías y sentirse capacitados para crear nuevas ideas.
La Fuse Blast de Labconco completa su ecosistema para SLS
Con volúmenes de producción de más de cien piezas de SLS a la semana, los pasos de posacabado manual como el granallado y la limpieza requerían horas de trabajo manual, un tiempo que habría estado mejor empleado en tareas de diseño e ingeniería más importantes. "La empresa quiere que nos centremos en encontrar nuevas oportunidades, rediseñar componentes para mejorarlos y reducir costes en vez de tenernos aquí parados, limpiando manualmente todas estas piezas", dice Griffith.
Por lo tanto, Labconco completó su ecosistema SLS Fuse con la Fuse Blast y con otro sistema de granallado automático de mayor coste. Después de una preparación de diez minutos, Griffith podía automatizar la limpieza y el granallado de dos cámaras de impresión enteras de la serie Fuse. "La instalación fue sencillísima... tiene casi el mismo tamaño que nuestro sistema de granallado manual. Por eso, si alguien tiene espacio para un sistema de granallado manual, como debería tenerlo cualquier empresa que utilice el SLS, tendrá espacio para una Fuse Blast sin problemas", dice Griffith.
Mejora de la calidad y el rendimiento de las piezas
Los equipos que hacían pedidos al taller de Labconco notaron inmediatamente la diferencia en cuanto a la lisura de la superficie y la calidad de las piezas.
"La diferencia que marcó la Fuse Blast fue considerable. Todos los ingenieros a los que empecé a darles prototipos empezaron a darse cuenta de que las piezas habían cambiado sin que yo tuviera que decirles que habíamos automatizado el posacabado. Notaron inmediatamente que había menos polvo residual en las piezas, que eran más lisas, que tenían un tacto más agradable y que su aspecto había mejorado. La diferencia que ha supuesto para la calidad de las piezas es notable".
Brent Griffith, ingeniero de productos de Labconco
Las superficies lisas y la ausencia de residuos de polvo tuvo un efecto inesperado en el rendimiento de las piezas: las máquinas funcionaban mejor cuando sus componentes impresos mediante SLS se habían limpiado en la Fuse Blast. "De hecho, mejoró ligeramente el rendimiento de algunos de los componentes que fabricábamos porque estaban bastante más limpios, especialmente en las series iniciales de encargos para uno de nuestros productos.
Los resultados eran prácticamente idénticos a los de las piezas limpiadas en su otro sistema automatizado de granallado, que tiene un coste más elevado. "No puedo decir que vea una gran diferencia entre los dos. [La Fuse Blast] sin duda da resultados que están muy por encima de su categoría", siguió explicando Griffith.
Menos tiempo dedicado al posacabado y más tiempo para optimizar los diseños
La automatización de la Fuse Blast no solo elimina la necesidad de pasar tiempo granallando piezas a mano, sino que reduce la cantidad de tiempo que Griffith y el equipo tienen que pasar manipulando la Fuse Sift. Antes, pasar más tiempo con la Fuse Sift salía a cuenta porque acortaba el tiempo de granallado. Ahora, la Fuse Blast lleva a cabo los ciclos de forma automática y produce piezas limpias, incluso si empiezan estando enterradas en polvo. "Ahora me importa menos cuánto polvo logramos quitar [con la Fuse Sift] porque sé de lo que es capaz la Fuse Blast. Limpiar piezas a fondo en la Fuse Sift ya no es sinónimo de ahorrar tiempo. El poco polvo extra que habríamos recuperado siendo más exhaustivos en la Fuse Sift no está justificado por el trabajo manual adicional que requiere obtenerlo", dice Griffith.
Para una pieza que tiene un ritmo de producción constante de unas 50 piezas a la semana, el equipo de Griffith estaba realizando el granallado de forma manual y tenía que limpiar tres agujeros por pieza con un cepillo para tubos. Con la Fuse Blast, puede configurar un ciclo automatizado, irse y volver después de 20-30 minutos para recoger un juego de piezas perfectamente limpias. "La Fuse Blast es una máquina genial. Se le da de maravilla limpiar los agujeros, que es una de las cosas que más tiempo nos ahorra", dice Griffith.
Escalado de las operaciones de impresión 3D
Griffith y sus compañeros adoptaron un enfoque sistemático respecto a la impresión 3D y su auditoría demostró la viabilidad del caso de uso para las primeras seis máquinas que incorporaron. A medida que seguían encontrando formas de ahorrar en costes, reducir el trabajo manual y mejorar los diseños de su amplio catálogo de componentes, empezaron a plantearse expandir sus capacidades de impresión 3D.
"Cada vez que llega una pieza a mi escritorio, me pregunto: '¿podemos mejorarla un poco con la fabricación aditiva?' Yo creo que estar atentos a esas oportunidades es lo que más nos ha permitido brillar y ahorrar más dinero o reducir más costes para muchos componentes", dice Griffith.
Las ventajas están claras para toda la empresa, ya que los equipos que trabajan con clientes que tienen aplicaciones específicas pueden ofrecer con confianza soluciones rentables gracias al poder de la fabricación de bajo volumen. "Podemos satisfacer de forma rentable la demanda, incluso para los clientes que solo necesitan cinco, diez o 50 unidades de una pieza personalizada. Podemos responder rápidamente a lo que necesita el mercado", dice Griffith.
Desde el primer ejemplo que dejó muda de asombro a toda una reunión, Griffith ha elaborado un caso de uso de negocio para fabricantes de todos los tamaños. La producción in situ con la impresión 3D SLA y SLS puede hacer posibles nuevas aplicaciones, aumentar el éxito empresarial, optimizar el rendimiento de los productos, prevenir problemas en la cadena de suministro y reducir costes.
Para saber más acerca de cómo incorporar el SLS y la SLA en tu empresa, programa una consulta con nuestro equipo de ventas para la fabricación.