Introducción a la fundición de metal y formas de combinar la impresión 3D con los procesos de trabajo de fundición
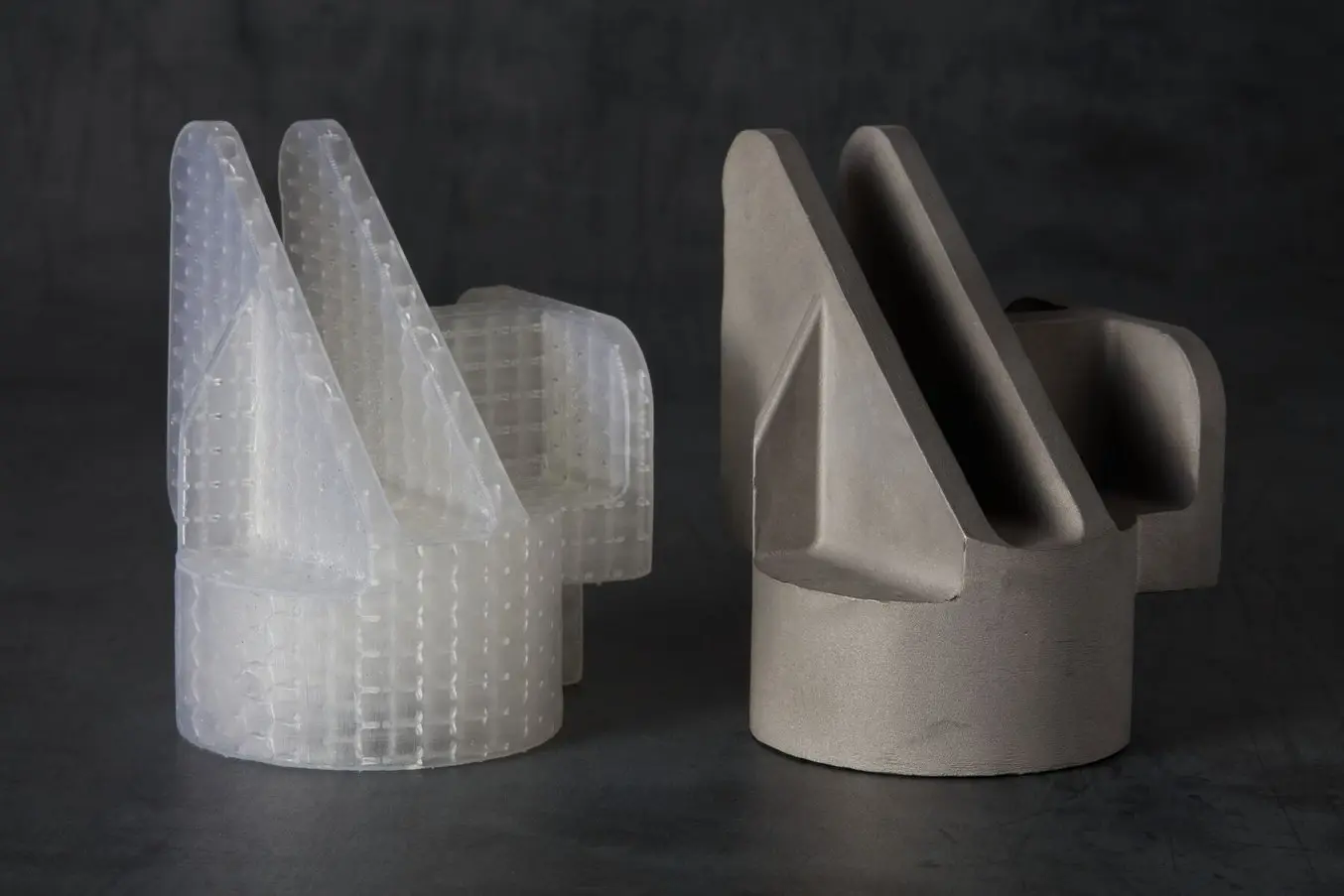
Un patrón para fundición a la cera perdida impreso en 3D con la Clear Cast Resin y la pieza fundida en metal.
La fundición de metal es un proceso metalúrgico milenario en el que se enfría y solidifica metal fundido dentro de un molde para formar piezas metálicas. A pesar de tener un origen tan antiguo, sigue siendo uno de los procesos más populares para las empresas que desean producir piezas de metal.
Este artículo explicará qué es la fundición de metal, cómo funciona, en qué consisten los procesos más comunes de fundición de metal y las ventajas de las que pueden disfrutar los fabricantes al combinar herramientas digitales modernas como la impresión 3D con procesos de trabajo tradicionales para la fundición.
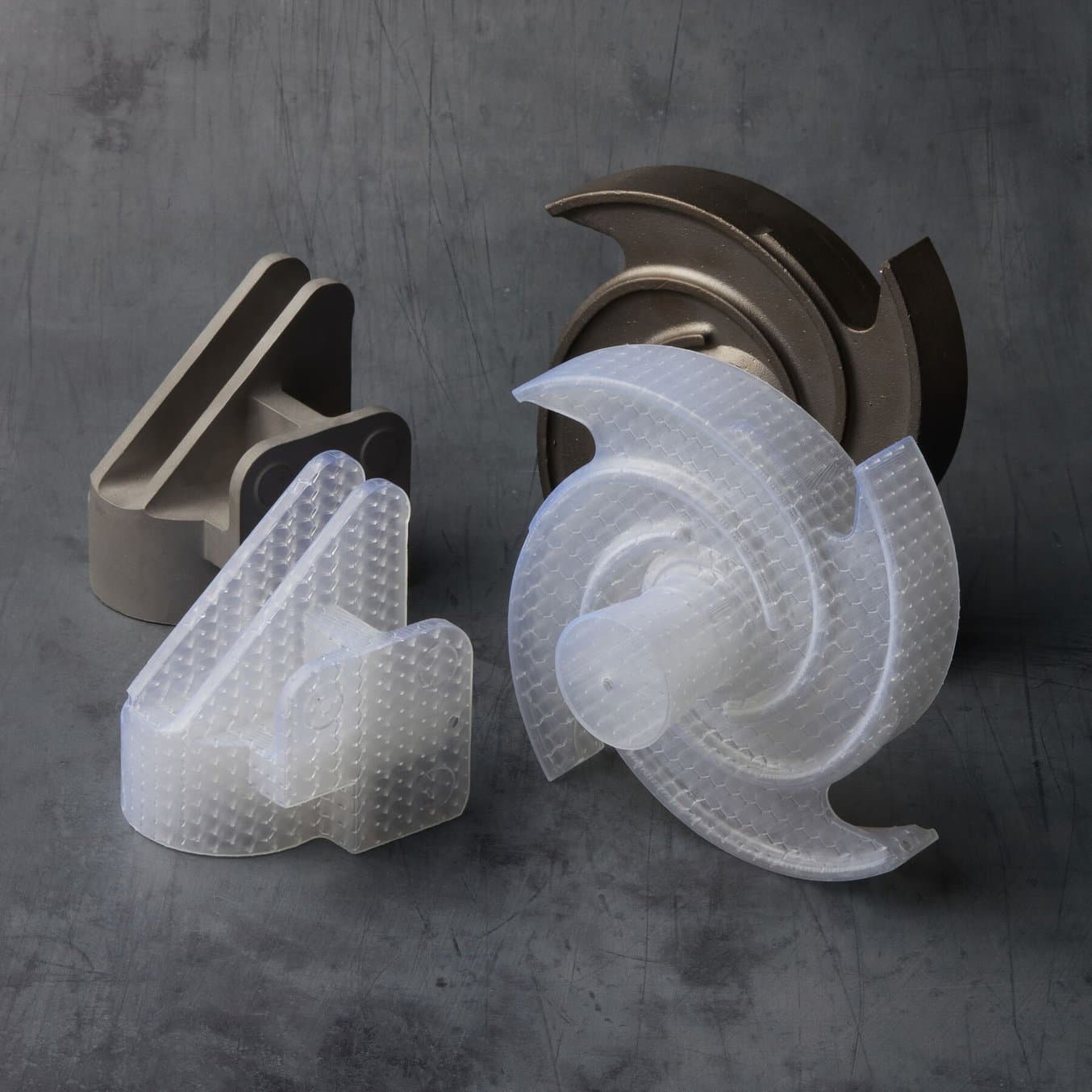
Precisión y rentabilidad en la fundición: Impresión 3D para piezas de metal
Este seminario web te mostrará los métodos que varias fundiciones con una larga trayectoria pudieron usar para fundir piezas metálicas con patrones impresos en 3D en las impresoras 3D de Formlabs. Descubre cómo las fundiciones están reduciendo sus costes, acortando las esperas y mejorando la calidad de sus piezas de metal al integrar la Clear Cast Resin de Formlabs y el módulo de celosías Lattice de Materialise Magics con los métodos de fundición tradicionales.
Resumen del proceso de la fundición de metal
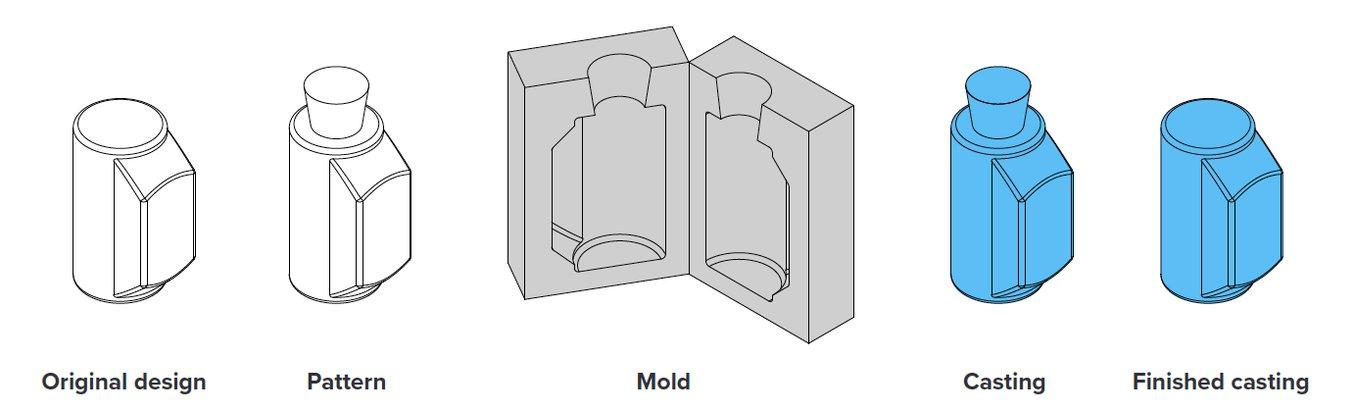
La fundición de metal paso a paso, desde el diseño original hasta la pieza fundida final.
Desde los inicios de la fundición de metal, sus métodos han evolucionado y cambiado. Sin embargo, sus técnicas básicas se han mantenido constantes. Este es un proceso general de fundición de metal, explicado paso a paso:
Paso 1: Creación de patrones
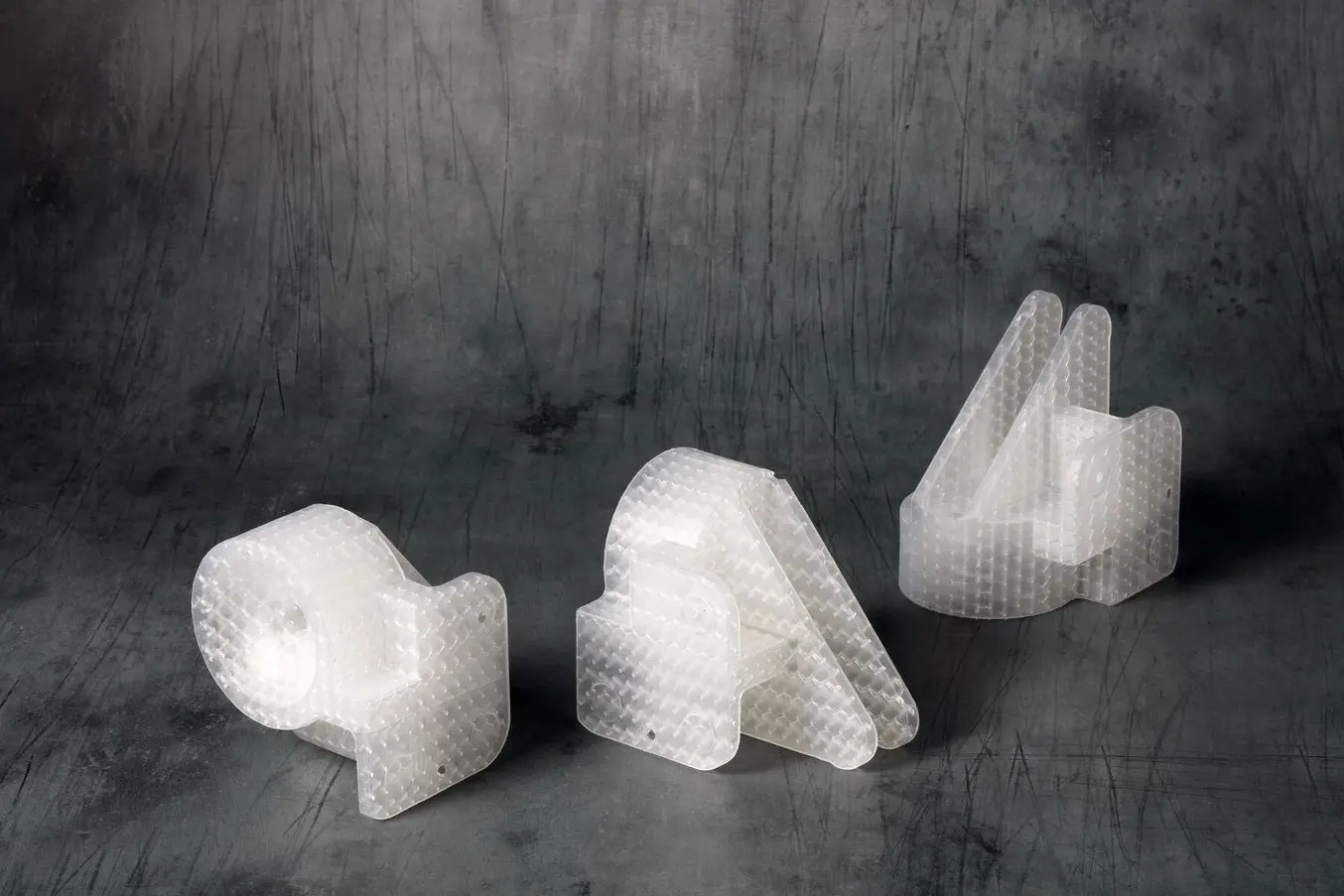
Patrones para fundición a la cera perdida industrial, impresos en 3D con la Clear Cast Resin.
Para comenzar el proceso de fundición de metal, un fabricante debe empezar por desarrollar una representación del patrón deseado. Este patrón es esencial para diseñar el molde que se usa la fundición. Tradicionalmente, se fabrica con madera, espuma, plástico o cera, y hace que el molde produzca la pieza de metal final con precisión. Hoy en día, la impresión 3D es otro método común para producir patrones, que permite a los diseñadores crear patrones precisos directamente desde herramientas digitales de software CAD.
Un patrón no es una réplica exacta de la pieza deseada. Contiene elementos adicionales que hacen posible el proceso de fundición, como entradas que permiten que el metal fundido fluya a un ritmo constante y respiraderos que dejan escapar el gas. Además, los patrones son más grandes que las piezas a las que representan, para compensar la contracción que se produce durante el enfriamiento.
Cuando la pieza fundida está hueca, el fabricante también crea un macho de arena o de metal que dé forma a su interior. Este macho se retira cuando se completa la fundición.
Paso 2: Fabricación de moldes
El siguiente paso es crear un molde de fundición, que puede ser reutilizable (no desechable) o no reutilizable (desechable). Los moldes no reutilizables se suelen fabricar con arena, yeso, cera o mediante la impresión 3D, y como su nombre sugiere, se destruyen durante el proceso de fundición. Los moldes reutilizables se fabrican con metal y con otros materiales resistentes, y se pueden reutilizar en múltiples ciclos de fundición.
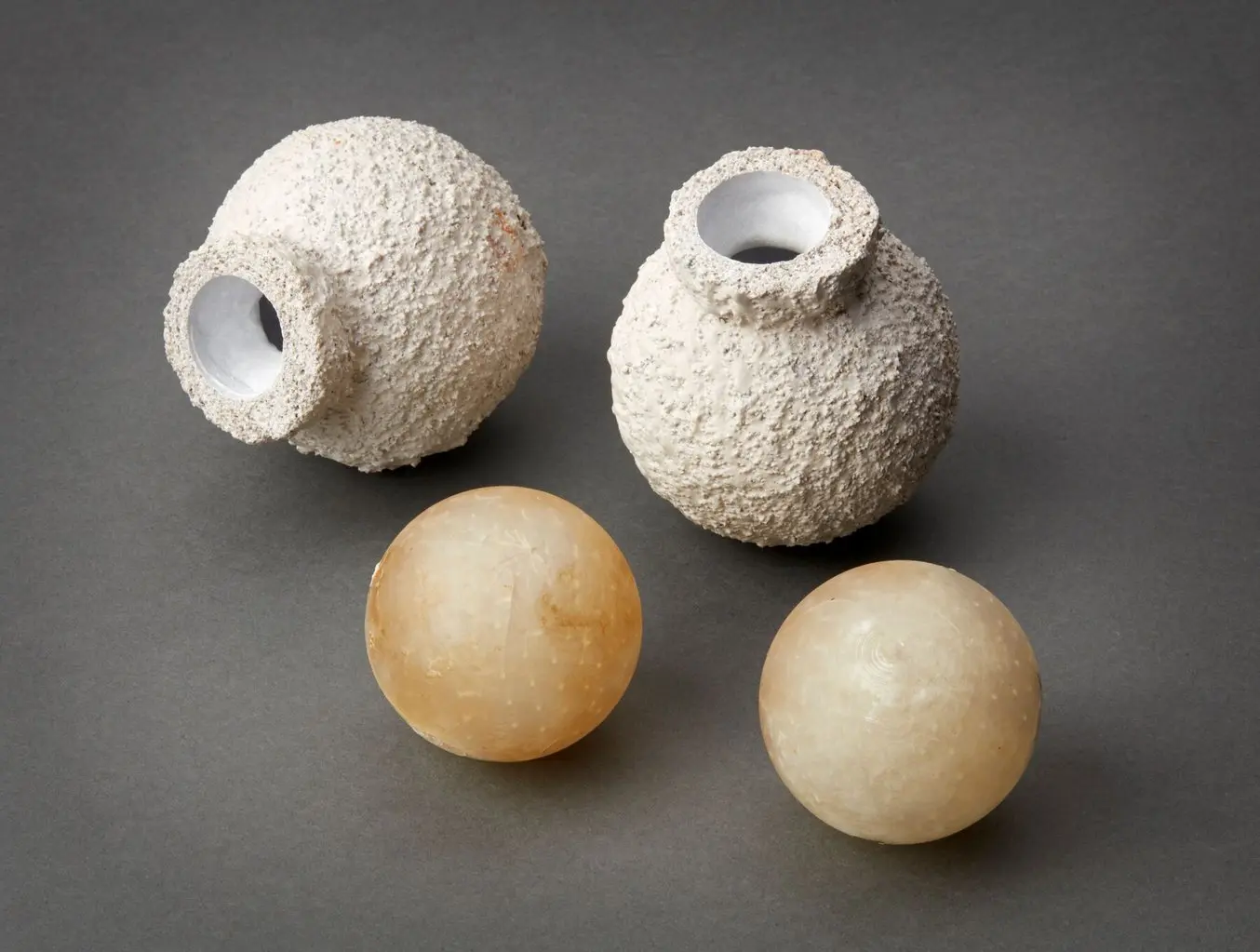
Coquillas cerámicas tras el quemado y patrones impresos en 3D con la Clear Resin.
Paso 3: Fusión y vertido del metal fundido
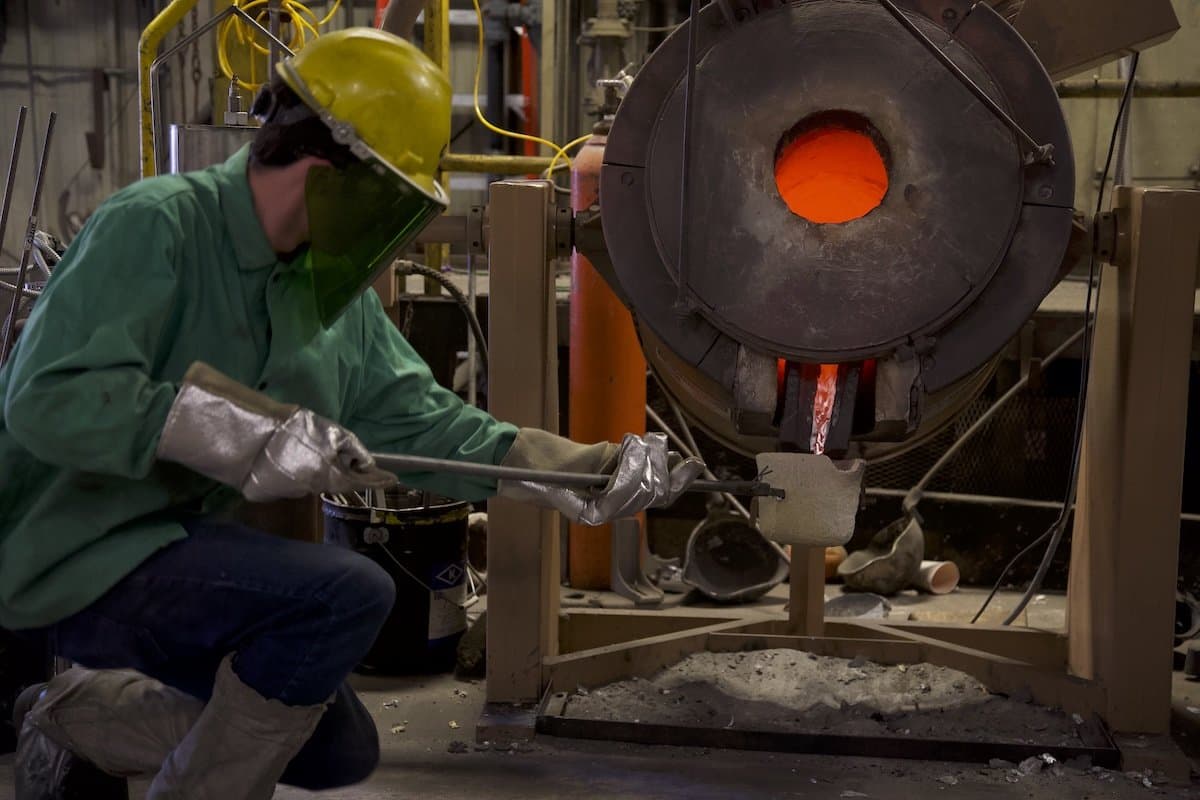
Vertido del aluminio fundido en un revestimiento hueco.
Durante este paso, el metal se calienta en un horno hasta que se funde. En función de la aplicación que se va a dar a la pieza final, los fabricantes pueden usar diversos metales, siendo los más comunes el hierro, el aluminio, las aleaciones de aluminio, el acero, el cobre y el zinc, así como metales preciosos como el oro y la plata. Cuando el metal está fundido, el fabricante lo vierte dentro de la cavidad del molde y deja que se enfríe y se solidifique.
Paso 4: Retirada del molde y limpieza
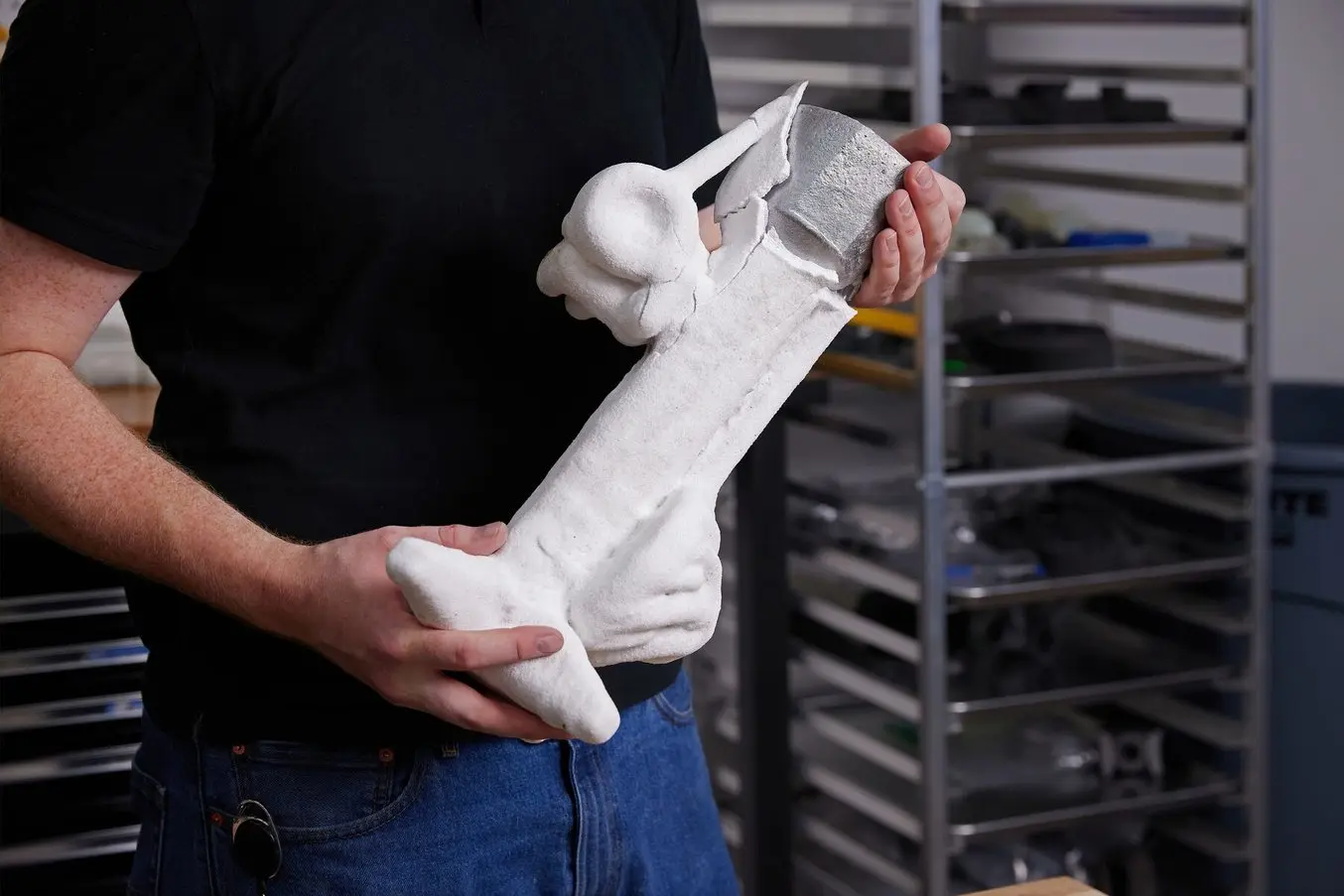
Fundición de metal después de la producción.
Cuando el metal se ha enfriado y solidificado, las piezas se retiran del molde. En función del tipo de molde, esto se puede hacer aplicando vibraciones para desprender el material, quitando el revestimiento con un lavado o usando pernos de expulsión. A continuación, se retira de las piezas el material sobrante, como los respiraderos, las entradas y las mazarotas. Por último, las piezas se liman, se rallan, se mecanizan o se arenan para alisar la superficie y obtener los requisitos finales de forma.
Tipos de procesos de fundición de metal
Aunque todas las técnicas de fundición de metal comparten un mismo proceso principal, hay algunos métodos que se ajustan mejor a ciertas aplicaciones. Algunos de los métodos más comunes son la fundición a presión, el moldeo por inyección y el moldeado en arena.
Fundición a presión
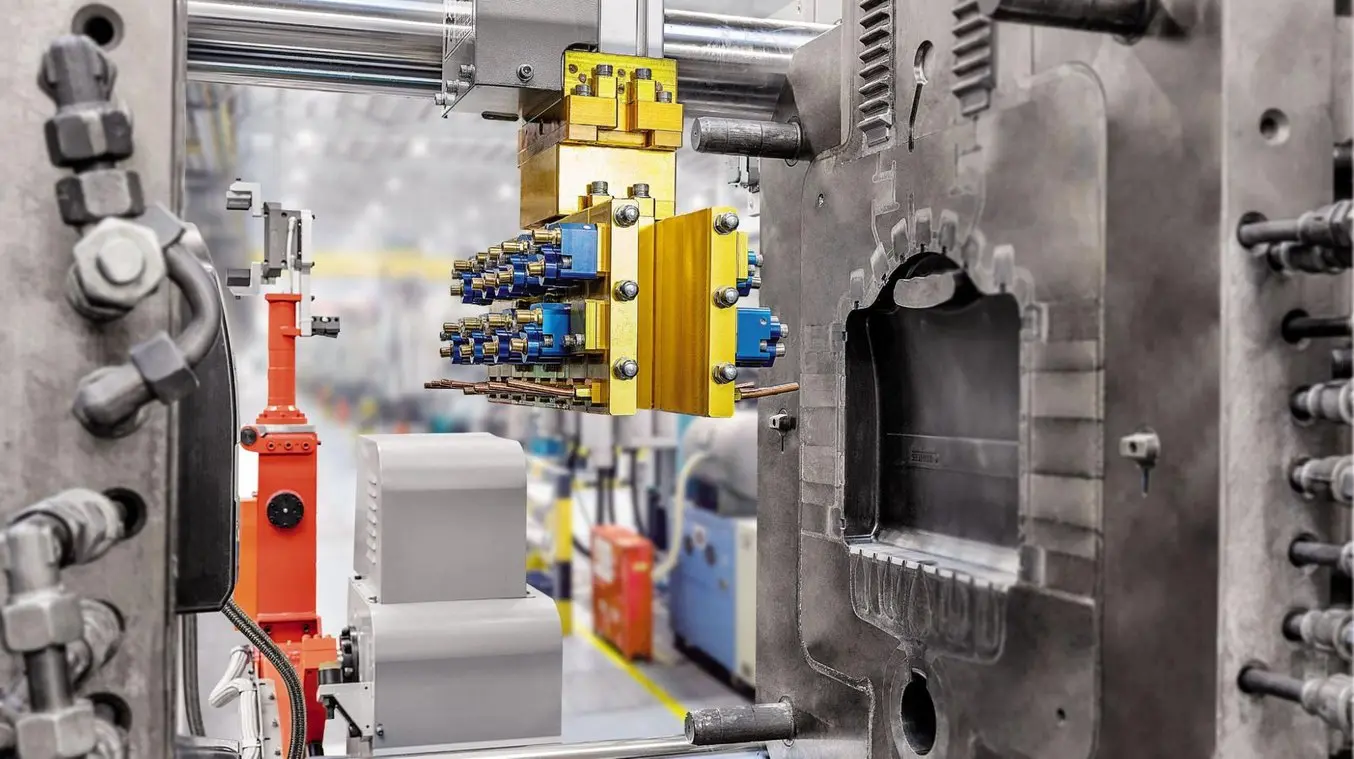
La fundición a presión utiliza un molde de acero y alta presión. (Fuente: buhlergroup.com)
La fundición a presión es un proceso de fundición de metal en el que un fabricante empuja a alta presión metal fundido dentro de una cavidad de un molde de acero para producir rápidamente piezas de metal. En la fundición a presión, el fabricante une dos mitades de un troquel o de un molde reutilizable y usa una boquilla para inyectar metal fundido presurizado en el interior del troquel. Cuando el metal se enfría, el troquel se abre y los pernos de expulsión empujan fuera la pieza fundida.
Los dos procesos de fundición a presión más comunes son la fundición en cámara caliente y la fundición en cámara fría. Aunque los detalles específicos de estos procesos varían, hay varias características generales que comparten las diversas modalidades del proceso de fundición a presión.
Fundición a presión en cámara caliente
La fundición a presión en cámara caliente es el más común de los dos procesos principales de fundición a presión. Las máquinas de fundición a presión en cámara caliente tienen un horno integrado para calentar el metal dentro de la máquina. Cuando el metal alcanza un estado fundido, la máquina baja una cámara cilíndrica dentro del mental. La forma de cuello de cisne del sistema de inyección de metal permite a la cámara llenarse rápidamente y después introducir el material en el molde con la presión del aire o con un pistón.
Sumergir el mecanismo de inyección para llenarlo permite que este proceso de fundición tenga una inyección en el molde rápida y optimizada. Sin embargo, al estar la cámara sometida a un calor directo procedente del metal fundido, los sistemas de fundición a presión en cámara caliente tienen un riesgo de corrosión, lo que los hace una opción menos viable para metales con un punto de fusión elevado. Es una opción más adecuada para materiales con puntos de fusión bajos y una gran fluidez, como el plomo, el magnesio, el zinc y el cobre.
Fundición a presión en cámara fría
En contraposición, el proceso de fundición a presión en cámara fría funciona de forma más lenta para evitar la corrosión. Con este método, un trabajador de la fundición introduce el metal fundido en el sistema de inyección y un pistón se ocupa después de empujar el metal al interior del molde.
Este proceso limita la corrosión que se da con más frecuencia en la fundición a presión en cámara caliente. Es una opción ideal para metales con puntos de fusión elevados, como el aluminio y sus aleaciones.
Ventajas de la fundición a presión
El proceso de fundición a presión es rápido y produce piezas muy detalladas. Es idóneo para producir grandes cantidades de piezas complejas y también puede producir piezas resistentes con un acabado de la superficie liso. La capacidad que tiene la fundición a presión de producir grandes cantidades de piezas la convierte en un proceso crucial en el sector automovilístico y en la industria aeroespacial.
Desventajas de la fundición a presión
Dado que las herramientas y el equipamiento de la fundición a presión son caros, este proceso no resulta rentable para remesas de producción pequeñas. Además, la maleabilidad de los metales que se usan en el proceso puede afectar a la complejidad del producto.
Fundición a la cera perdida
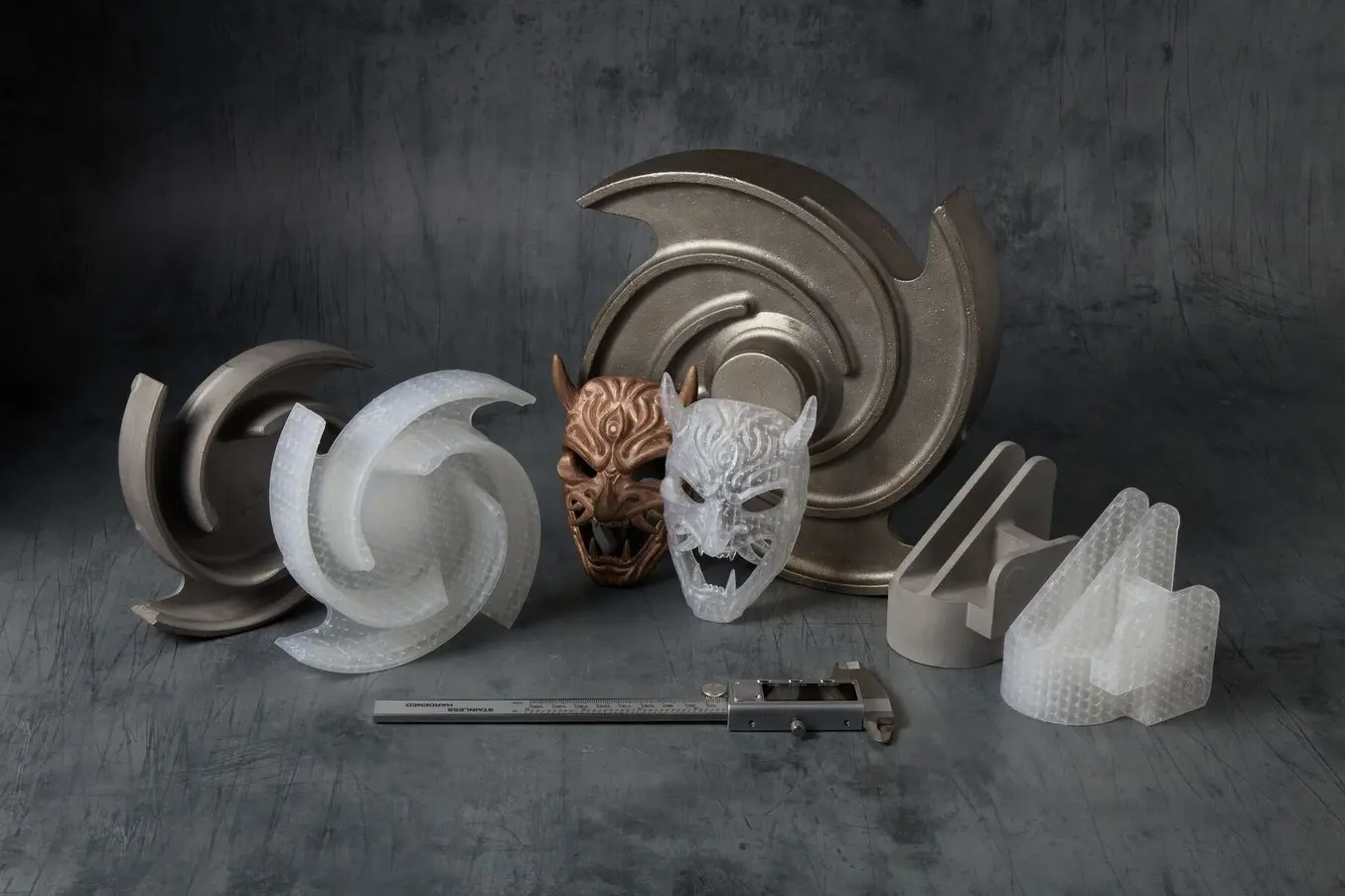
Piezas fundidas a partir de patrones impresos en 3D con la Clear Cast Resin en una impresora 3D de resina de Formlabs.
La fundición a la cera perdida es un proceso que usa cera, una lechada o mezcla de revestimiento y moldes para producir piezas complejas. Se trata de una de las técnicas de fundición de metal más antiguas, pero se sigue valorando por su capacidad para crear piezas de metal precisas con formas complicadas.
Este proceso se sigue utilizando mucho en la producción de joyas, aparatos dentales y arte. En su forma industrial, es un modo común de crear piezas metálicas de precisión para la ingeniería y la fabricación.
Los patrones para la fundición a la cera perdida suelen estar hechos de cera o de polímeros impresos en 3D. Los patrones se acoplan a una estructura parecida a un árbol y se sumergen en una lechada de sílice o se introduce en una caja de moldeo y se rodea con el revestimiento líquido. Después de que el material de revestimiento se seque, la caja de moldeo se coloca boca abajo en un horno, que funde el patrón dejando una cavidad negativa con la forma del modelo original. El metal se funde y después se vierte, usando la gravedad o la presión del vacío para introducir el metal en la cavidad. Las piezas fundidas se liman, se muelen, se mecanizan o se arenan para conseguir la geometría y el acabado final.
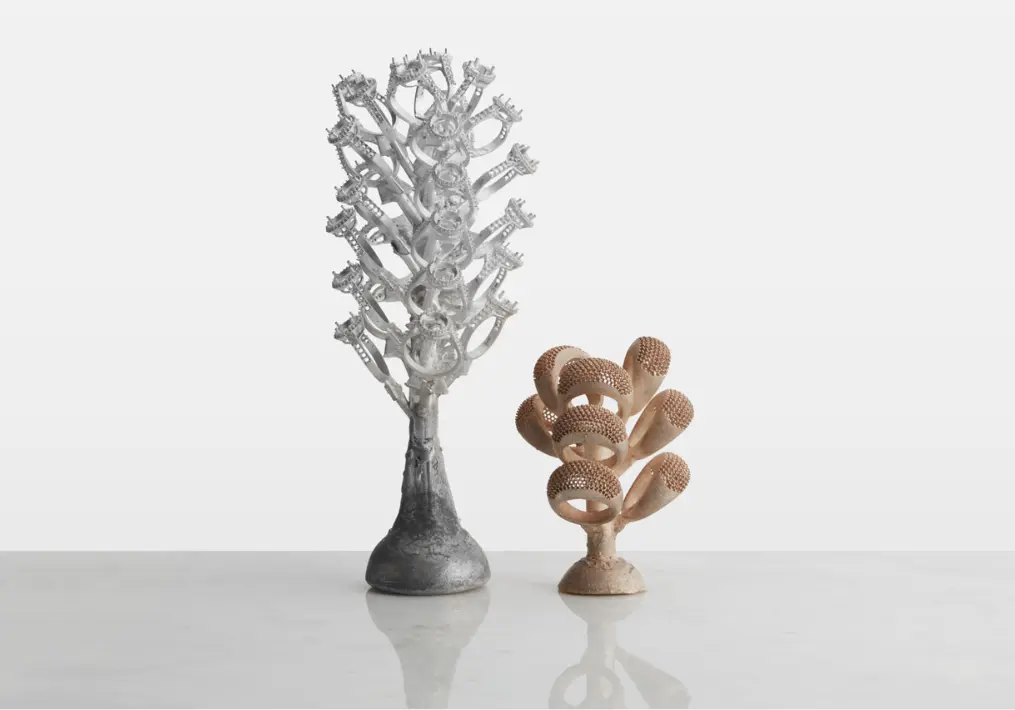
Árboles de fundición con anillos.
Los materiales de Formlabs que pueden utilizarse para imprimir en 3D piezas para la fundición a la cera perdida son la Clear Cast Resin, la Castable Wax Resin, la Castable Wax 40 Resin y la True Cast Resin, pero determinar cuál de estas resinas es la más adecuada es algo que depende de las características de cada pieza. La Castable Wax Resin es adecuada para joyas de peso ligero a medio, la True Cast Resin para joyas de peso medio y componentes de ingeniería de hasta 5 mm de grosor y la Clear Cast Resin para piezas de más de 3 mm de grosor.
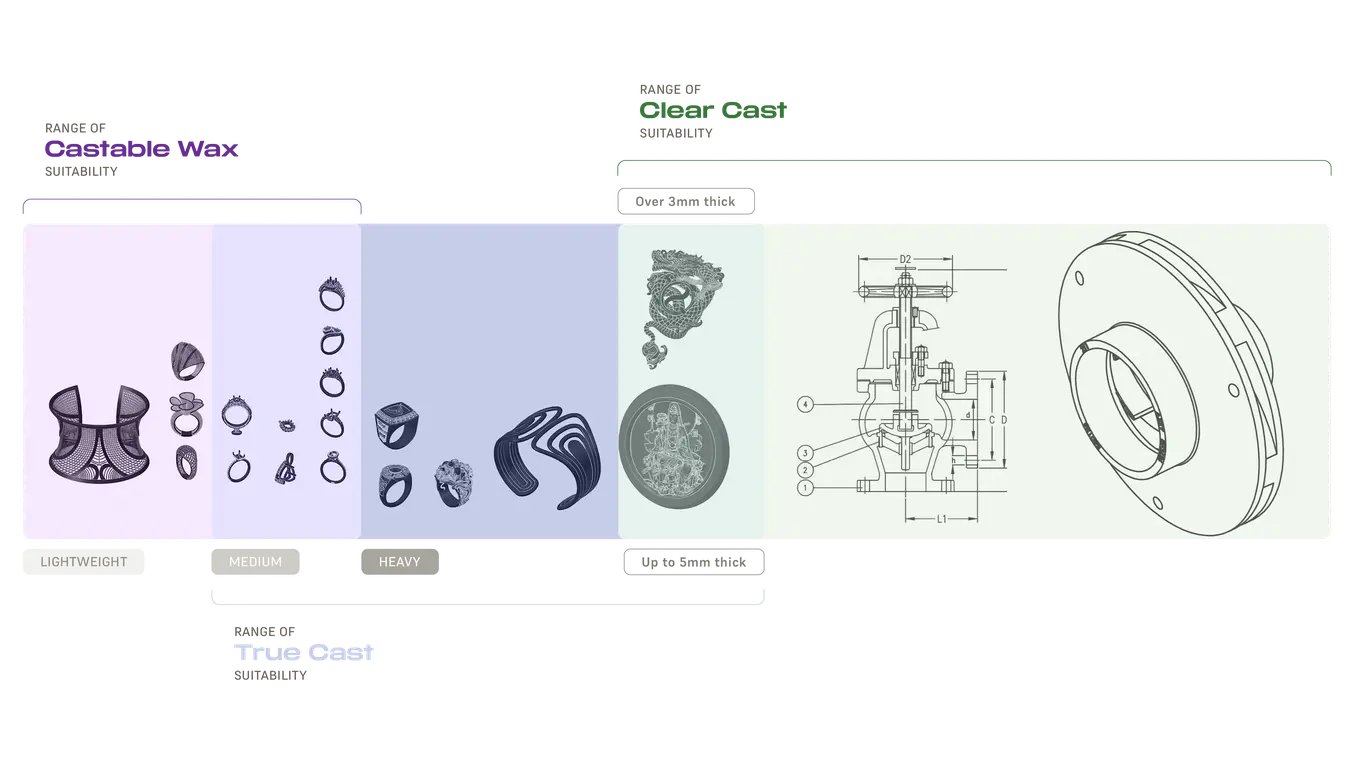
Ventajas de la fundición a la cera perdida
La fundición a la cera perdida es un proceso versátil. Permite a los fabricantes producir piezas precisas y repetibles a partir de casi cualquier metal disponible para la fundición, así como formas complicadas que serían difíciles o imposibles de fabricar con otros métodos de fundición. Las piezas fundidas también tienen una calidad de la superficie excelente y tolerancias reducidas, además de requerir un acabado de la superficie o un mecanizado mínimos.
Estas características hacen que la fundición a la cera perdida sea ideal para piezas complejas en aplicaciones automovilísticas, aeroespaciales e industriales; herramientas médicas, implantes dentales, joyería fina y arte.
Desventajas de la fundición a la cera perdida
La fundición a la cera perdida es un proceso complejo y laborioso. Fabricar un molde requiere equipamiento especializado, materiales refractarios y aglutinantes costosos y muchas operaciones manuales. Fundir piezas que necesiten machos puede ser difícil y el proceso es más adecuado para piezas pequeñas.
Moldeado en arena
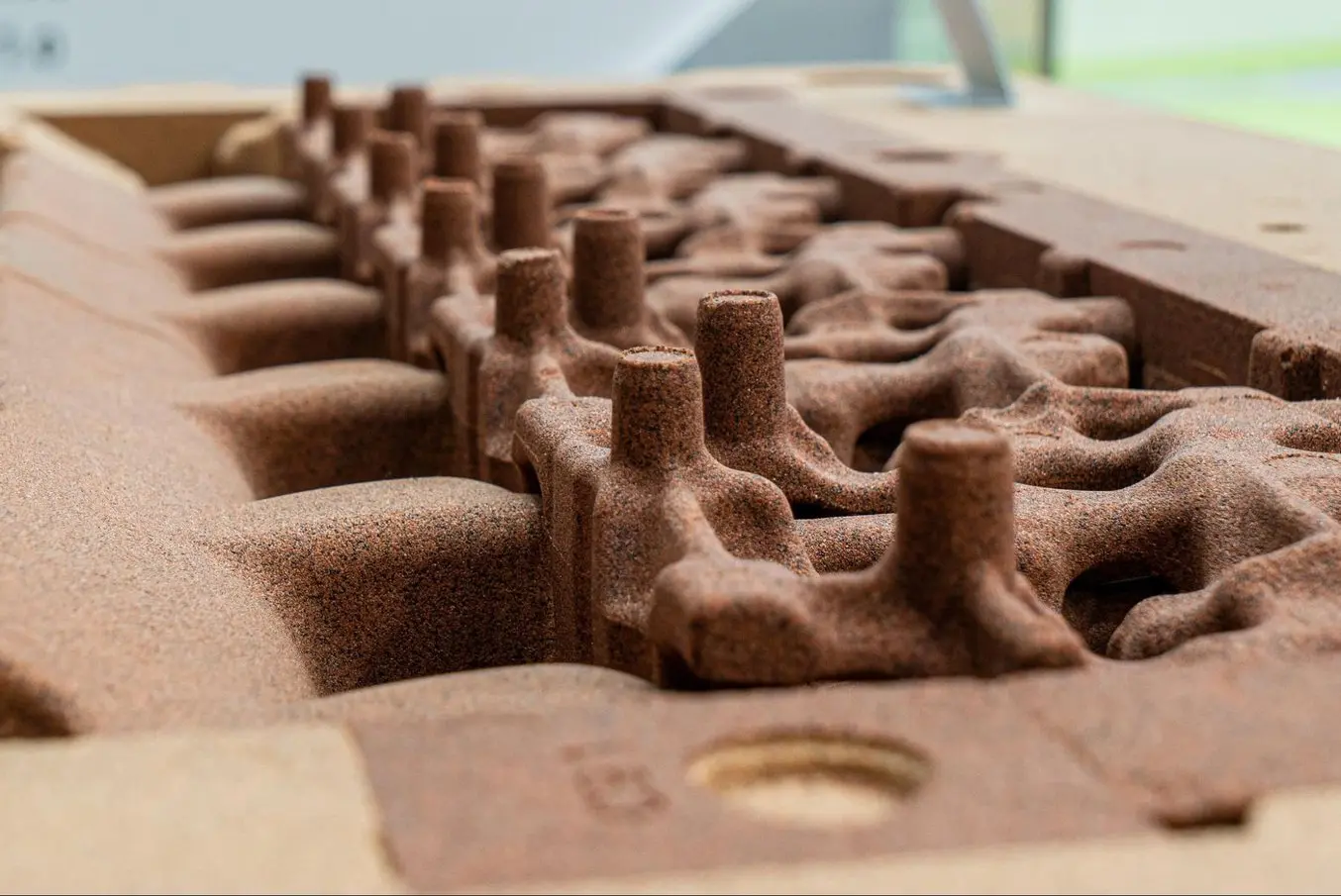
Una mitad de un molde para moldeado en arena.
El moldeado en arena es un método de fundición de metal que se usó por primera vez hace 3000 años, pero sigue siendo el método de fundición más utilizado hoy en día. Este proceso permite a los fabricantes fundir metal sin depender del mecanizado.
En el proceso de moldeado en arena, el fabricante crea en primer lugar un patrón de fundición o réplica de la pieza que se quiere fundir, que normalmente se hace con madera o plástico. El patrón se hace más grande de la cuenta para compensar la contracción. Las piezas con detalles en un lado solo necesitan un molde abierto. En el caso de las piezas que tienen varias superficies detalladas, el fabricante separa el patrón de fundición en dos cajas de moldeo para formar un molde de cavidad cerrada. Las dos mitades de ese molde se conocen como caja de moldeo superior y caja de moldeo inferior.
Cuando el fabricante ya ha creado el patrón, lo rodea de arena bien compactada. Después, añade bebederos y entradas para asegurarse de que el metal fundido fluya sin obstáculos por la cavidad del molde. El fabricante retira el patrón y cierra las dos mitades del molde de arena. Cuando el metal alcanza un estado fundido, se vierte dentro del molde y se deja enfriar. A partir de entonces, el molde de arena se retira usando vibraciones o agua a alta presión. Por último, el fabricante refina la pieza quitando los bebederos y las entradas y puliendo la pieza de metal fundida.
Ventajas del moldeado en arena
El moldeado en arena es un proceso adaptable que funciona fuera de las limitaciones de la maquinaria. Por eso, puede crear piezas complejas de prácticamente cualquier tamaño. La arena es barata y abundante, lo que reduce el coste de instalación y hace posible realizar modificaciones. Es la única forma práctica o económica de producir piezas fundidas muy grandes. Las esperas del moldeado en arena también son cortas, lo que lo convierte en un proceso viable para remesas de producción cortas.
La versatilidad del moldeado en arena hace que sea una opción de fabricación que sirve para sectores muy diversos. Puede producir equipamiento médico, componentes automovilísticos, equipamiento electrónico, depósitos de combustible, bloques motores y más.
Desventajas del moldeado en arena
El moldeado en arena crea metales muy porosos con texturas. La contracción y lo áspero que es el acabado de la superficie también reducen la precisión dimensional de las piezas. El resultado es un producto final de baja resistencia que requiere un posacabado lento para obtener un acabado de mayor calidad.
Cómo elegir el proceso de fundición de metal adecuado
A la hora de elegir el proceso de fundición de metal industrial adecuado, se deben tener en cuenta varios factores. Hemos creado esta tabla comparativa para ayudarte a comparar la fundición a presión, la fundición a la cera perdida y el moldeado en arena en cuanto a los tipos de metales que usan, su volumen de producción, sus costes, su tiempo de producción, la complejidad de las piezas que producen y para qué sectores se suelen usar.
Fundición a presión | Fundición a la cera perdida | Moldeado en arena | |
---|---|---|---|
Metales compatibles | Aluminio, cobre, plomo, magnesio, zinc | La mayoría de los metales | La mayoría de los metales |
Volumen de producción | Alto volumen | Volumen bajo a alto | De modelos únicos a volumen medio |
Coste por unidad | Baja | Moderado a alto | Moderado |
Costes de utillaje | Alta | Moderado | Baja |
Tiempo de ciclo | Rápido | Largo | Moderado |
Sectores | Automoción, industria aeroespacial, productos de consumo, mobiliario, herramientas eléctricas | Automoción, industria aeroespacial, joyería, medicina, odontología, arte | Automoción, industria aeroespacial, equipamiento industrial, electrónica, productos de consumo |
Fundición de metal con la impresión 3D
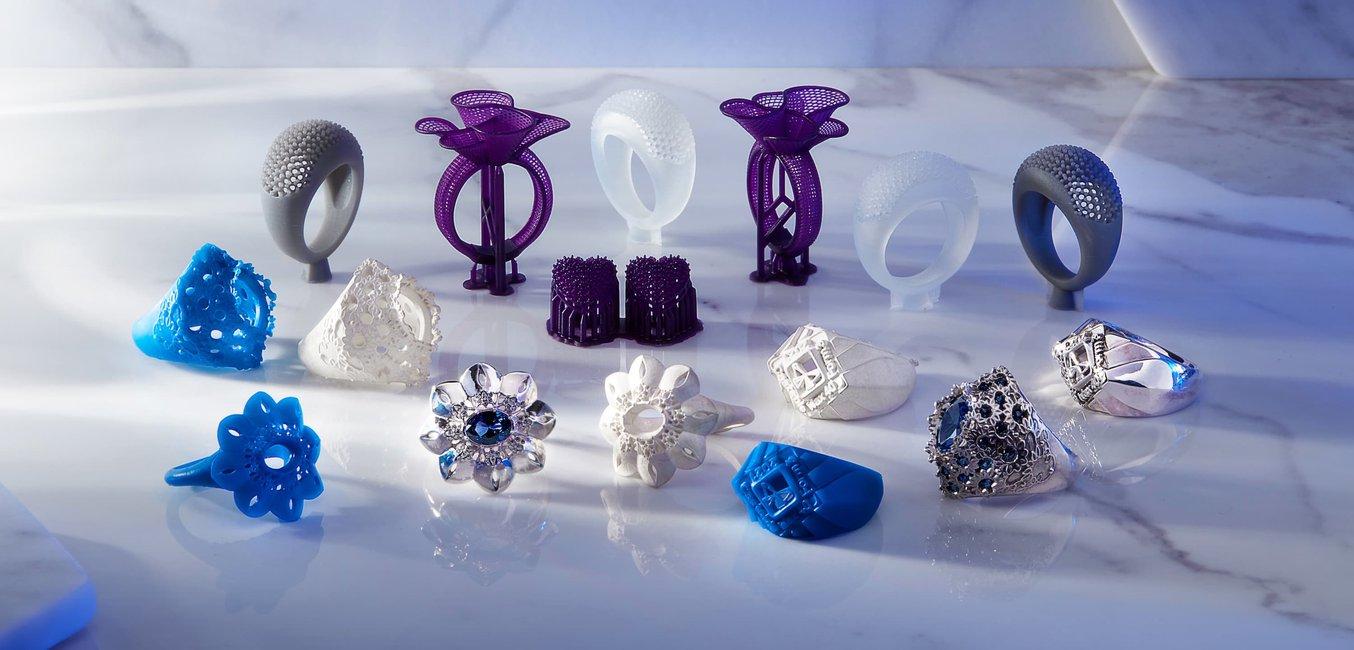
Patrones de joyería impresos en 3D y anillos fundidos con metal.
Los ingenieros, los diseñadores, los joyeros y los aficionados pueden aprovechar la velocidad y la flexibilidad de la impresión 3D combinando procesos de fundición como la fundición indirecta a la cera perdida, la fundición directa a la cera perdida, la fundición de peltre y el moldeado en arena con patrones impresos en 3D o vertiendo el metal en moldes impresos en 3D. Las piezas de metal fundido para las que se utiliza utillaje rápido impreso en 3D se pueden producir en un tiempo inferior al que se invierte en la fundición tradicional y por un coste considerablemente menor que el de la impresión 3D de metal.
Las impresoras 3D de estereolitografía (SLA) ofrecen una alta precisión y su amplia oferta de materiales las hacen adecuadas para procesos de trabajo de fundición que pueden producir piezas de metal a bajo coste, con una mayor libertad de diseño y en menos tiempo que con los métodos tradicionales.
Fundición indirecta a la cera perdida
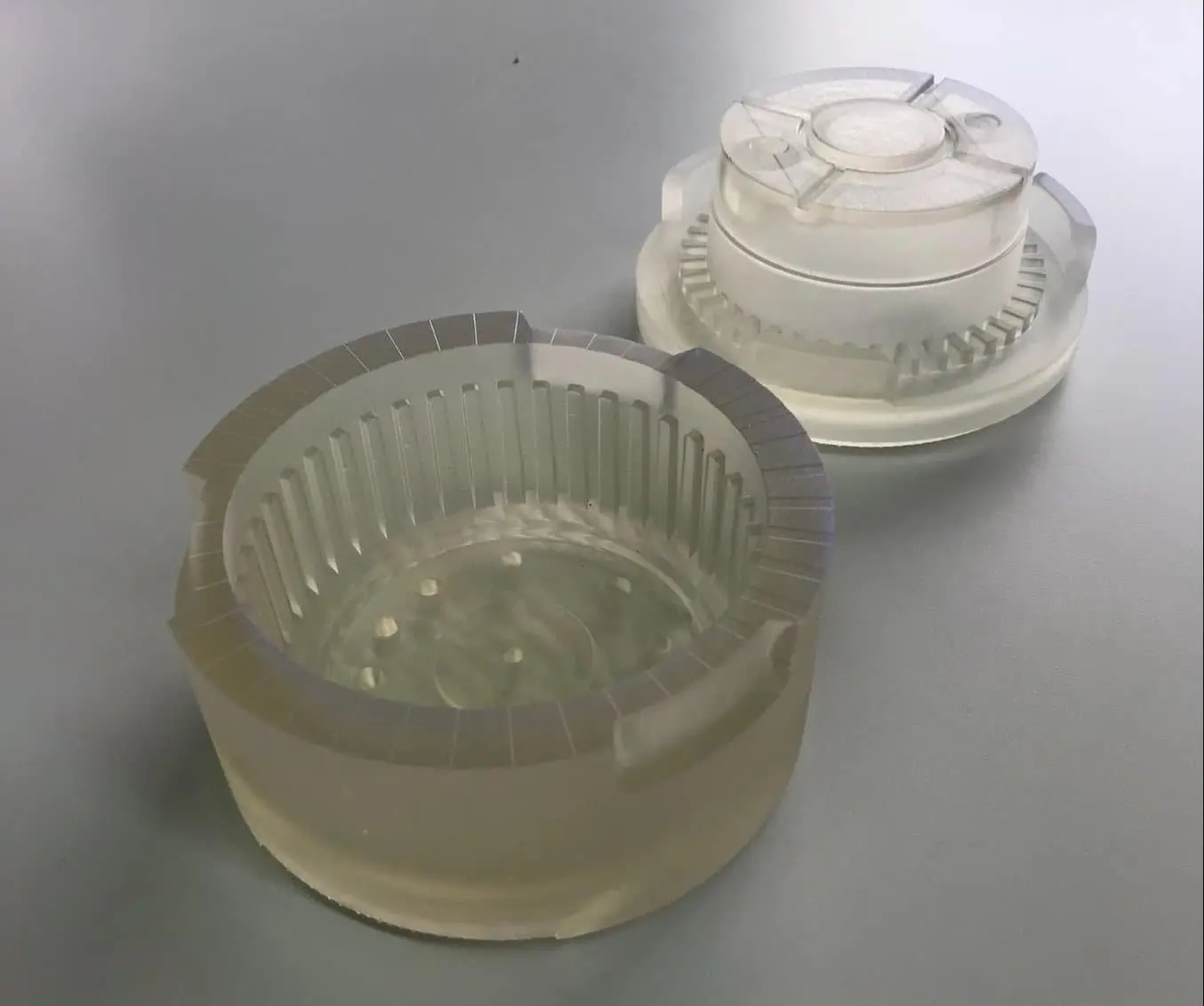
Un molde para inyección de cera impreso en 3D con Clear Resin.
El proceso de creación de modelos a partir de moldes o utillaje se denomina fundición indirecta a la cera perdida porque requiere crear moldes para producir los modelos además de los moldes de fundición finales.
Los moldes rígidos para cera (a menudo denominados "herramientas"), se suelen fabricar sometiendo aluminio o acero a un proceso de mecanizado. La producción de moldes de metal mecanizado cuesta miles de euros y hacen falta semanas de trabajo de mecanizado y acabado para poder hacer las primeras pruebas y crear los patrones para las piezas en un proceso de fundición.
Con la impresión 3D, los fabricantes pueden imprimir en 3D directamente el molde para su patrón utilizando materiales como la High Temp Resin o la Rigid 10K Resin, resinas con una gran resistencia a la temperatura. Para obtener un acabado de la superficie óptimo para las piezas moldeadas, da un tratamiento de lijado y de pulido a las superficies interiores del molde o un tratamiento de chorreado con microesferas de vidrio si deseas un aspecto mate uniforme. Para asegurarte de que las piezas finales tienen la precisión dimensional necesaria, compensa la contracción agrandando el molde impreso. El grado de contracción exacto de la cera y el proceso de fundición se pueden obtener de las especificaciones del proveedor.
Los moldes impresos en 3D para la fundición de metal acortan el tiempo entre el concepto y las primeras pruebas a una cuestión de días, porque los fabricantes pueden imprimir directamente el utillaje necesario para crear y evaluar las piezas.
Aunque las piezas moldeadas deben seguir las reglas de diseño para ser moldeables (p. ej., no tener socavados, dejar un mayor ángulo de desmoldeo es positivo, etc.), puedes conseguir una mayor complejidad de los patrones usando sujeciones con guía para combinar múltiples componentes en una única estructura.
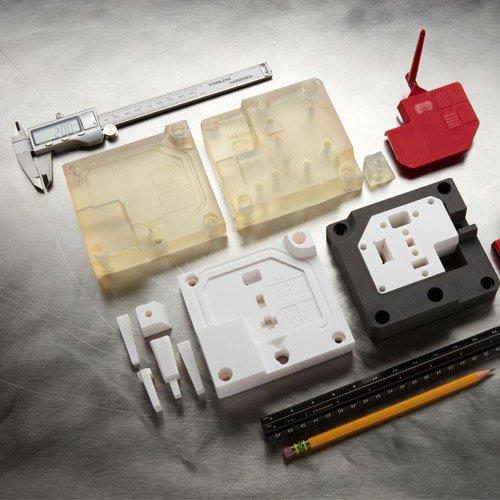
Fabricación de moldes con impresiones 3D: Técnicas para el prototipado y la producción
Descarga nuestro libro blanco para conocer seis procesos de fabricación de moldes que son posibles con una impresora 3D SLA en tus instalaciones, como el moldeo por inyección, el moldeo en vacío, el moldeo con silicona y más.
Fundición directa a la cera perdida
La fundición directa a la cera perdida es una versión de la fundición a la cera perdida donde el proceso pasa directamente de crear el patrón a rodearlo del material de revestimiento. Es ideal para producir piezas con geometrías demasiado complejas para moldearlas o piezas con amplios socavados y detalles finos en la textura de su superficie, en las que el moldeo es posible, pero conlleva altos costes de utillaje.
Tradicionalmente, los modelos para la fundición directa a la cera perdida se esculpen a mano o se mecanizaban, si la pieza es única o se espera que solo se produzca un puñado de unidades. En cambio, con la impresión 3D, los fabricantes pueden imprimir los patrones directamente en 3D, eliminando las limitaciones de diseño y de tiempo que son habituales en otros procesos.
Con las impresoras 3D, los ingenieros, diseñadores y joyeros pueden imprimir en 3D directamente los patrones de fundición para acortar los tiempos de espera y obtener una libertad de diseño que supere los límites de fabricabilidad de los procesos de moldeo. Formlabs ha desarrollado varios materiales de impresión 3D para fundición que son adecuados para la fundición directa a la cera perdida, especialmente para la fundición a la cera perdida industrial y la fundición de joyería.
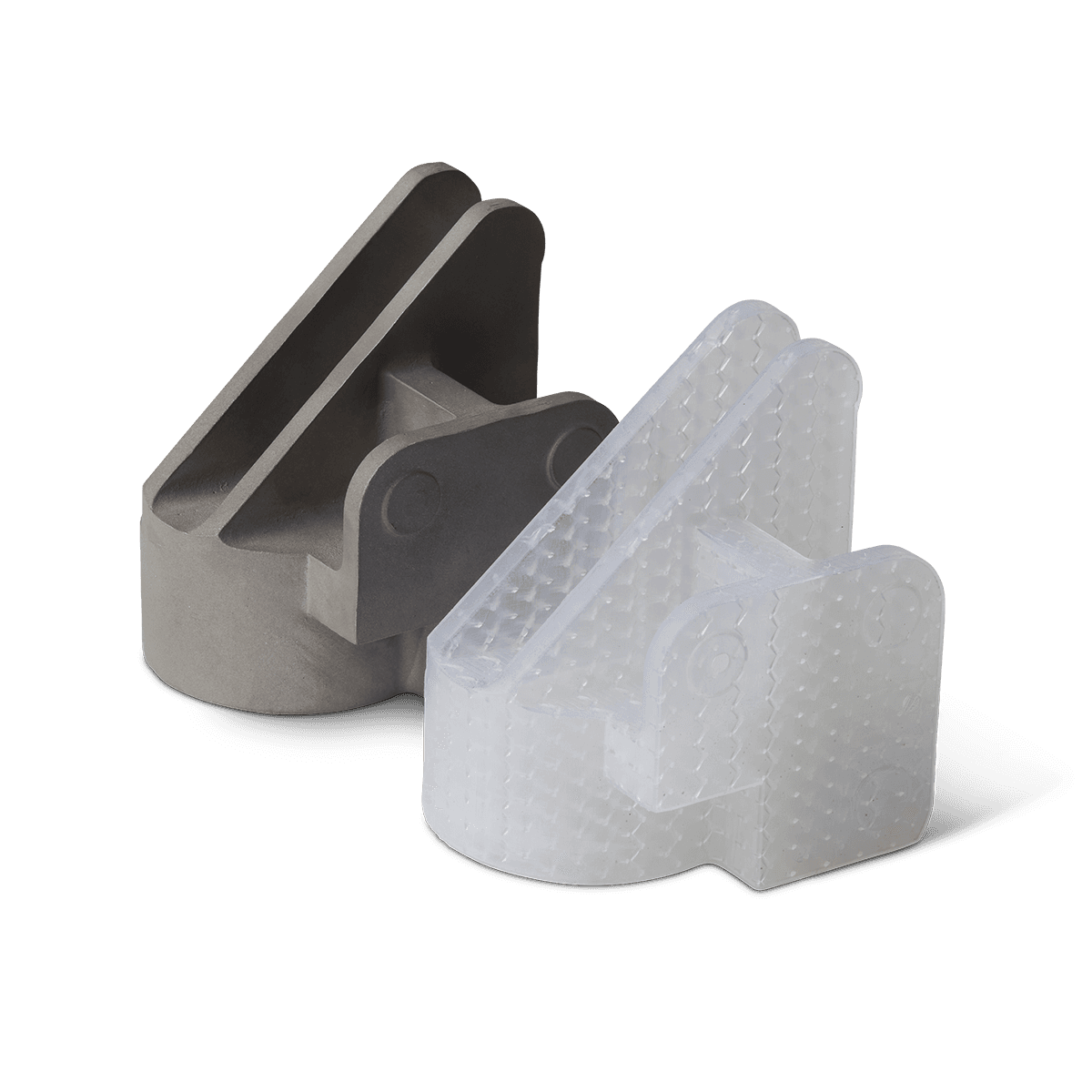
Fundición a la cera perdida industrial con patrones impresos en 3D con la Clear Cast Resin de Formlabs
Este libro blanco presenta los métodos que varias fundiciones con una larga trayectoria pudieron usar para fundir piezas metálicas con patrones impresos en 3D en las impresoras de estereolitografía (SLA) de Formlabs.
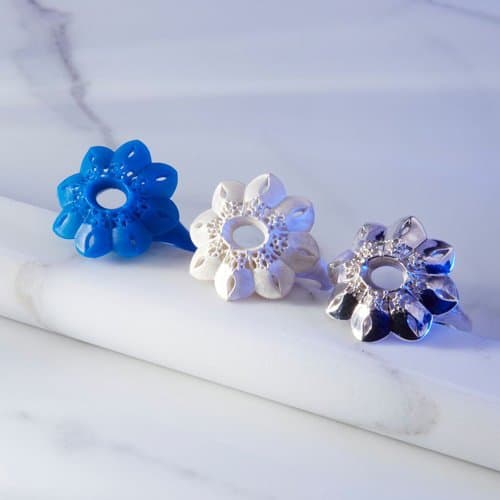
Introducción a la fundición para patrones de joyería impresos en 3D
La forma de la que trabajan los joyeros está cambiando, y en la vanguardia de dicho cambio están las resinas fotopolimerizables. En esta guía, aprenderás a fundir piezas de joyería fina a partir de patrones impresos en 3D con impresoras de Formlabs.
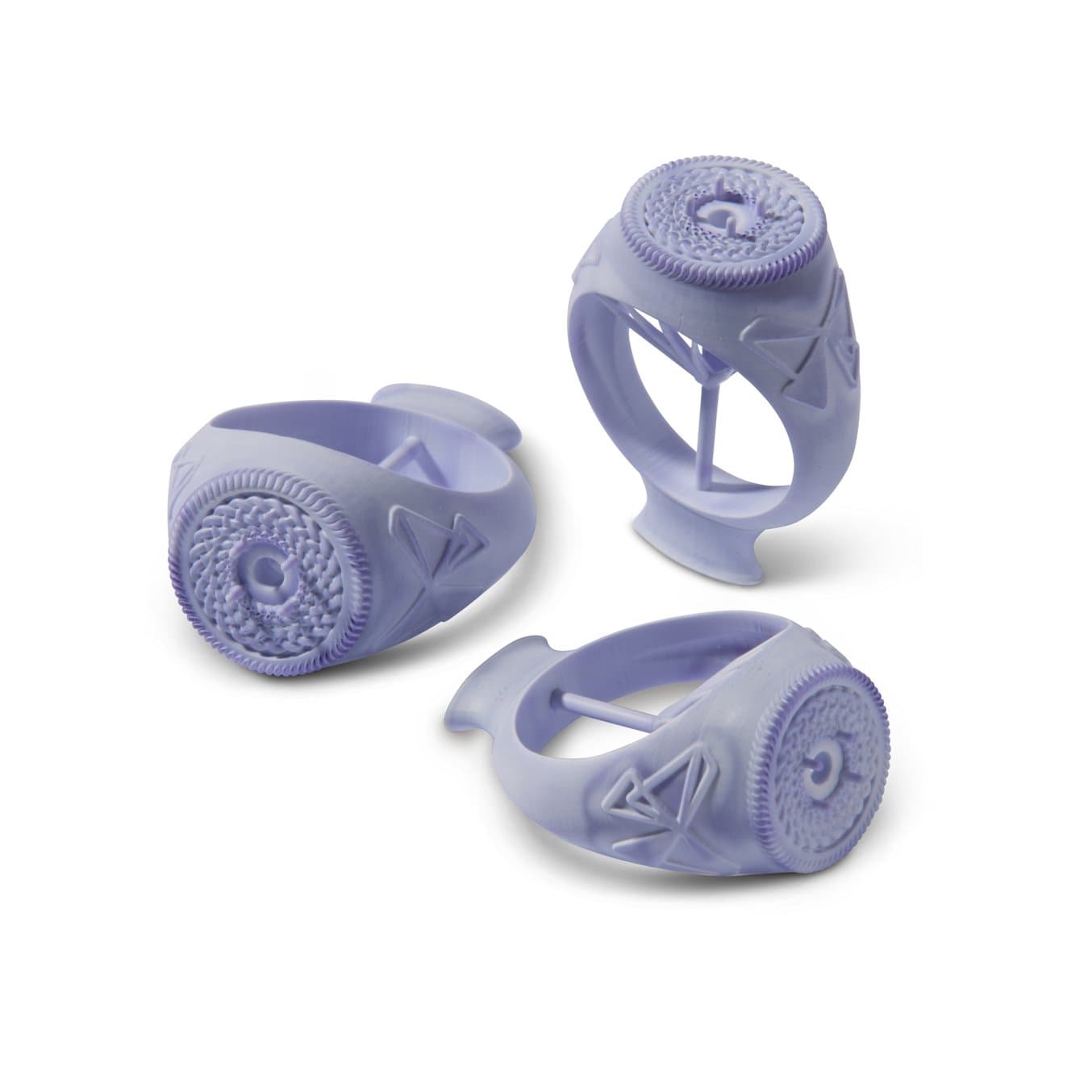
Solicita una pieza de muestra gratuita
Experimenta la calidad de Formlabs de primera mano. Enviaremos una pieza de muestra gratuita a tu lugar de trabajo.
Moldeado en arena
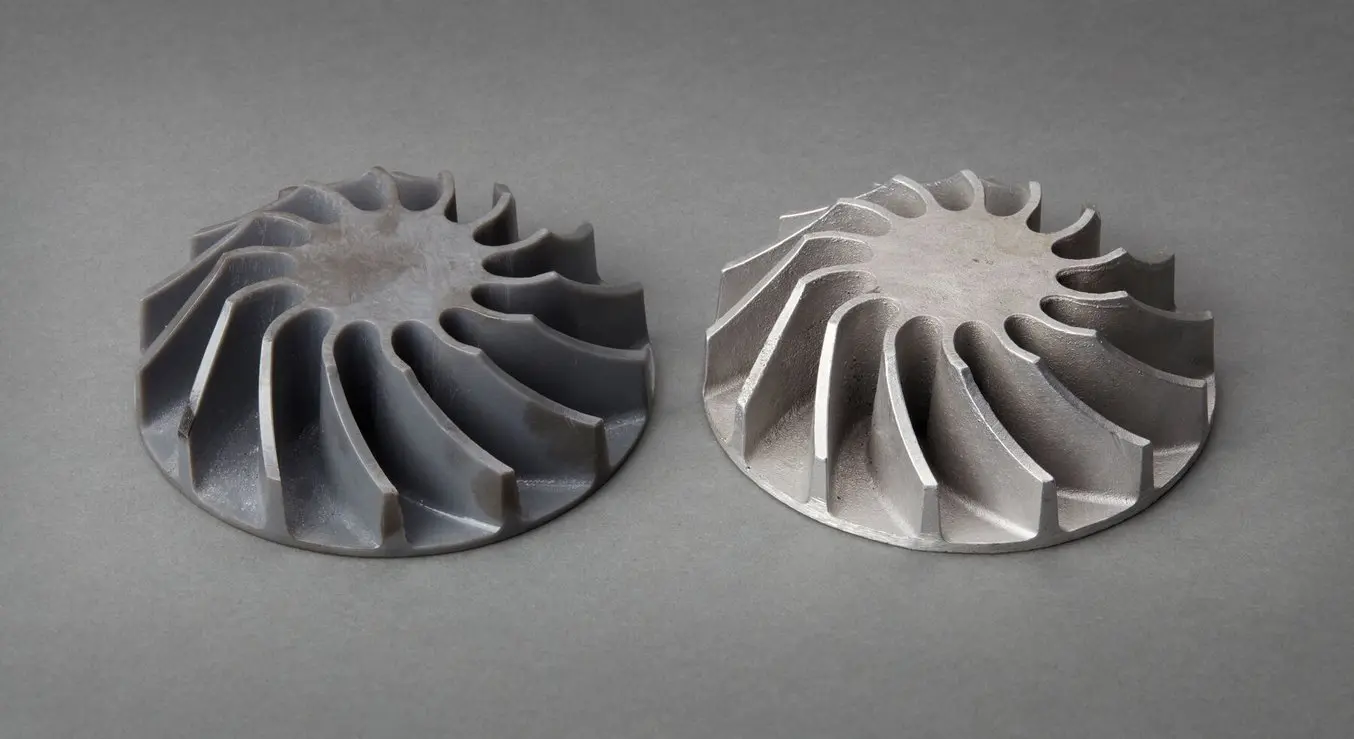
Modelo impreso con la Grey Resin y una pieza fundida de aluminio acabada a partir de un molde de arena abierto.
De forma parecida a la fundición a la cera perdida, la impresión 3D se puede utilizar para crear patrones para el moldeado en arena.
En comparación con materiales tradicionales como la madera, la impresión 3D permite a los fabricantes crear formas complejas y pasar directamente del diseño digital a la fundición.
Fundición de peltre
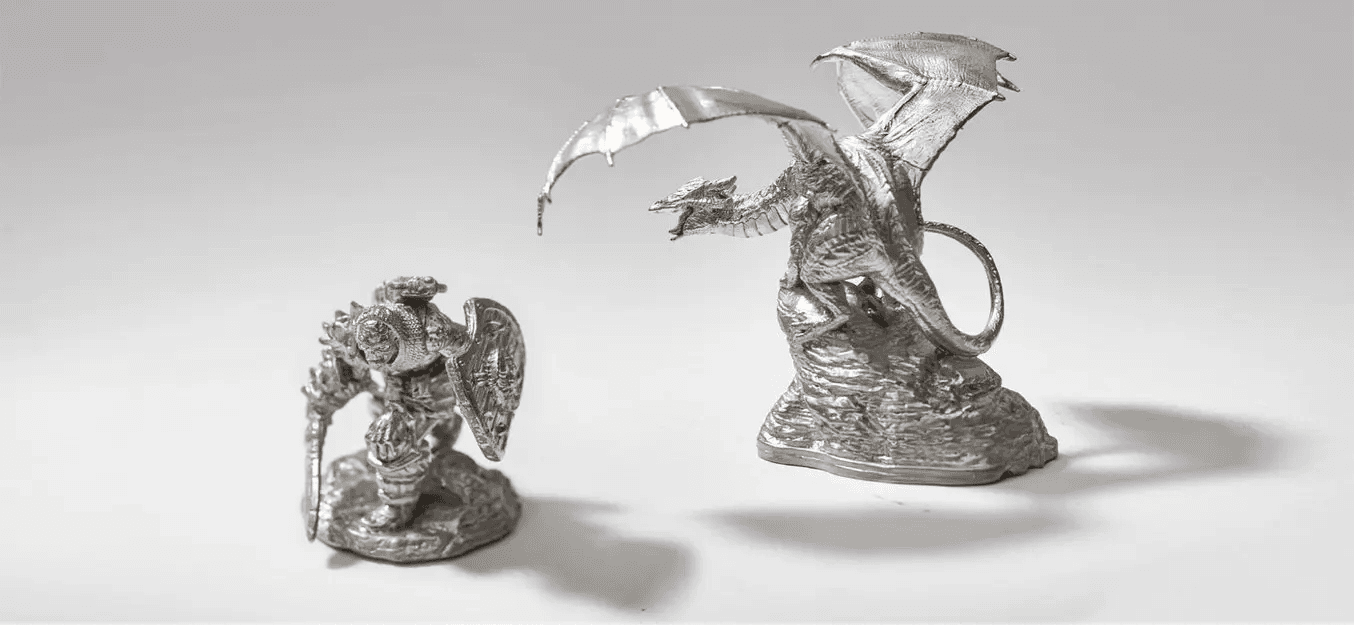
Figuras de Metal Miniatures hechas mediante fundición de peltre e impresión 3D.
El peltre es una aleación de metales con un punto de fusión bajo que se puede utilizar para fabricar objetos completamente metálicos para aplicaciones como las miniaturas de metal, la joyería, los modelos a escala y las réplicas de antigüedades.
Con los avances recientes en los materiales de impresión 3D resistentes a la temperatura como la High Temp Resin para las impresoras 3D SLA de Formlabs, ahora es posible imprimir moldes para la fundición directa del peltre.
Hay dos opciones para diseñar moldes: moldes desechables o moldes separables. Un molde desechable tiene una cáscara diseñada para romperse en el proceso. Los moldes separables tienen mitades que se pueden abrir para reutilizar el molde.
En comparación con la impresión directa del metal, fundir el peltre en moldes impresos en 3D ofrece un mejor nivel de detalle y acabado por un precio notablemente inferior. En comparación con la fundición con cera, imprimir un molde en 3D tiene menos pasos, requiere menos esfuerzo y conserva todo el nivel de detalle posible.
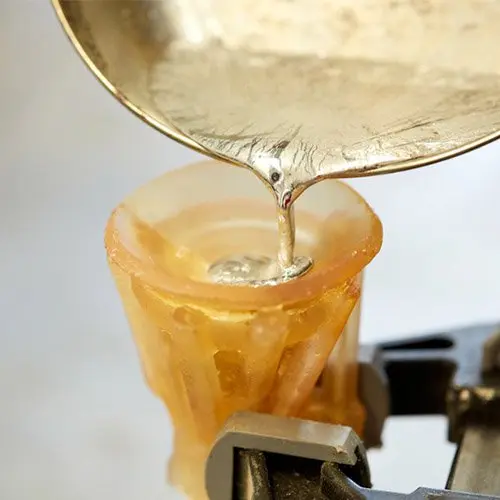
Metal, cerámica y silicona: Uso de moldes impresos en 3D en procesos de trabajo híbridos avanzados
Consulta nuestro seminario web para descubrir cómo la creación de moldes maestros impresos en 3D y moldes reutilizables o sacrificables puede permitirte producir piezas de porcelana, metales preciosos y no preciosos, silicona, materiales flexibles biocompatibles, etc.
Cuándo combinar la impresión 3D y la fundición de metal
La fundición de metal con la impresión 3D es una buena opción para as empresas que quieran potenciar la libertad de diseño o reducir los costes y los tiempos de producción.
Ciertos tipos de fundiciones de metal complejas, como las formas de gran tamaño con secciones transversales y piezas con múltiples machos, son difíciles de crear usando métodos de fundición de metal tradicionales. La impresión 3D permite a los fabricantes producir estos diseños complejos. Por ejemplo, las fundiciones o los joyeros pueden crear diseños complejos y hechos a medida que serían imposibles sin un patrón impreso en 3D.
La impresión 3D también elimina la dependencia de varias máquinas o proveedores de servicios para crear piezas. Las empresas solo necesitan un archivo digital, una impresora 3D y material de impresión. Esto puede ayudar a reducir los costes y el desperdicio, ya que todo el material que se utiliza acaba en el producto final.
Por último, combinar la impresión 3D con la fundición de metal puede reducir los costes y los tiempos de espera. En vez de tener que esperar semanas a que lleguen herramientas caras para poder fundir un producto final, una impresora 3D puede crear un patrón o molde en cuestión de horas.
Diversified Metalsmiths, Inc. ha incorporado las tecnologías modernas en su proceso de trabajo para la fundición de metal y ha logrado así reducir sus costes, mejorar los tiempos de espera y aumentar su agilidad. Con las impresoras 3D de estereolitografía (SLA) de la serie Form y la nueva Clear Cast Resin, Diversified Metalsmiths ha podido imprimir patrones de fundición en sus propias instalaciones de forma rápida y asequible, sin cambiar su proceso de trabajo para fundición o depender de proveedores externos.
"Nuestro principal motivo para comprar la Form 3L fue el coste de los patrones... En lo que respecta a amortizar la Form 3L y el equipamiento asociado, como mínimo cubriremos los costes en nuestro pedido actual y ahorraremos más de 200 $ por pieza en los pedidos que vengan después. Hay muy poca diferencia en nuestro proceso entre los patrones de acrílico y los patrones de Clear Cast Resin impresos mediante SLA, tanto antes como después de la fundición".
John Farr, vicepresidente de Tecnología de Diversified Metalsmiths
Impresora 3D para fundición de metal
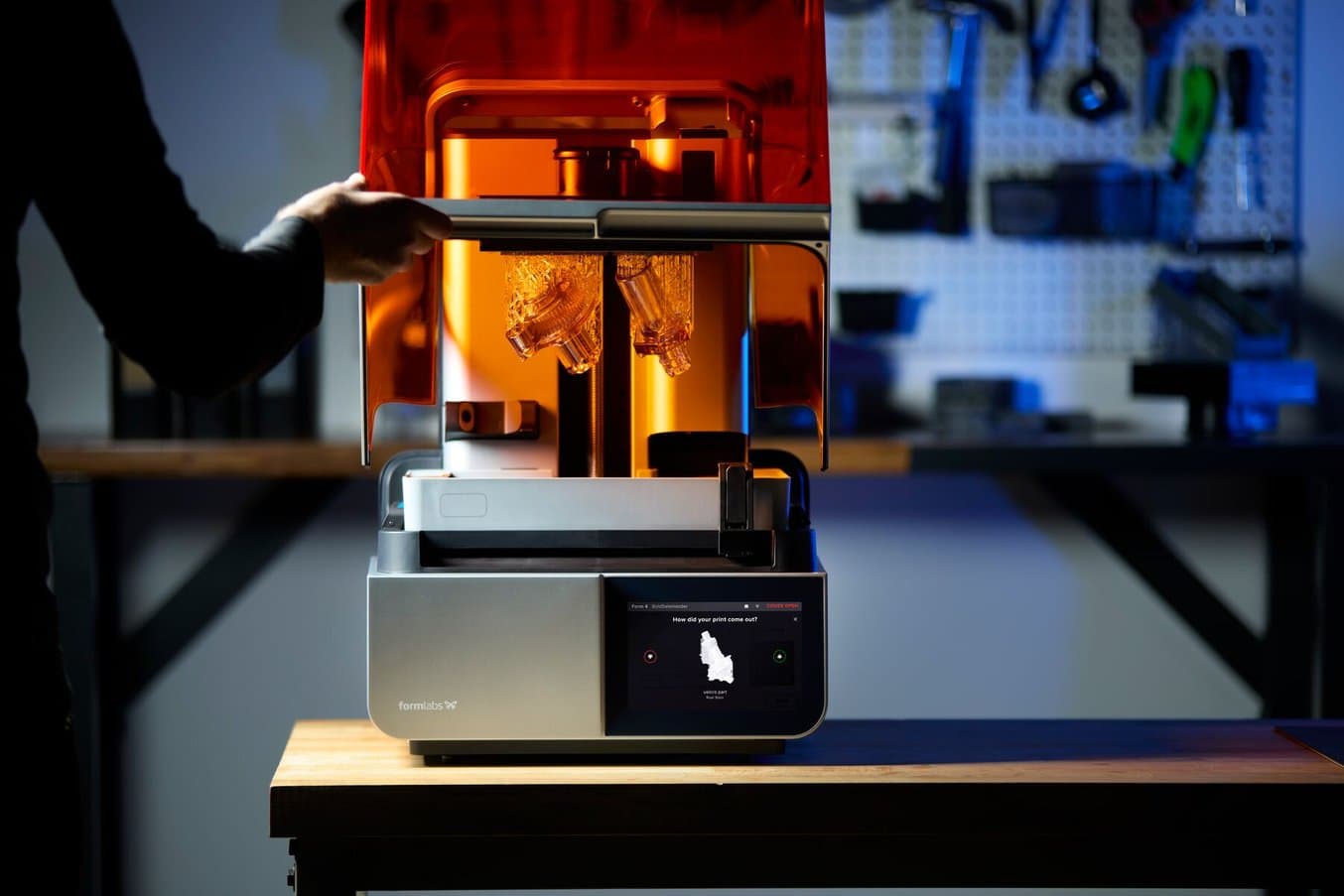
Combinar la fundición de metal y la impresión 3D ayuda a las empresas a crear piezas de metal de forma rápida y eficiente. Con una impresora 3D SLA de Formlabs, el proceso de la fundición de metal se puede acelerar y los costes se pueden reducir al mismo tiempo.
Infórmate sobre las impresoras 3D de resina de Formlabs o contacta con nuestros expertos en impresión 3D si tienes alguna pregunta.