Cómo IGESTEK desarrolla piezas de materiales compuestos con la impresión 3D y el utillaje rápido
IGESTEK es una empresa de la ciudad española de Bilbao que se especializa en el desarrollo de soluciones ligeras para el sector automovilístico, usando plásticos y materiales compuestos.
La compañía desarrolla e integra diferentes técnicas de procesamiento híbrido para fabricar componentes con materiales compuestos, que los proveedores automovilísticos de primer nivel y los fabricantes de equipo original pueden utilizar para producir piezas destinadas a coches y motocicletas de alta gama.
El equipo de IGESTEK utiliza la impresión 3D a lo largo del proceso de desarrollo del producto desde la fase de diseño conceptual (para verificar las geometrías) hasta la fase de diseño detallado, con el fin de fabricar prototipos funcionales. También utiliza la impresión 3D para fabricar utillaje rápido, como insertos para moldes de inyección de plástico o herramientas de termoformado para materiales compuestos.
Sigue leyendo para averiguar cómo IGESTEK mejora la velocidad del desarrollo, reduce los costes y permite ofrecer una respuesta ágil a los posibles problemas que surjan.
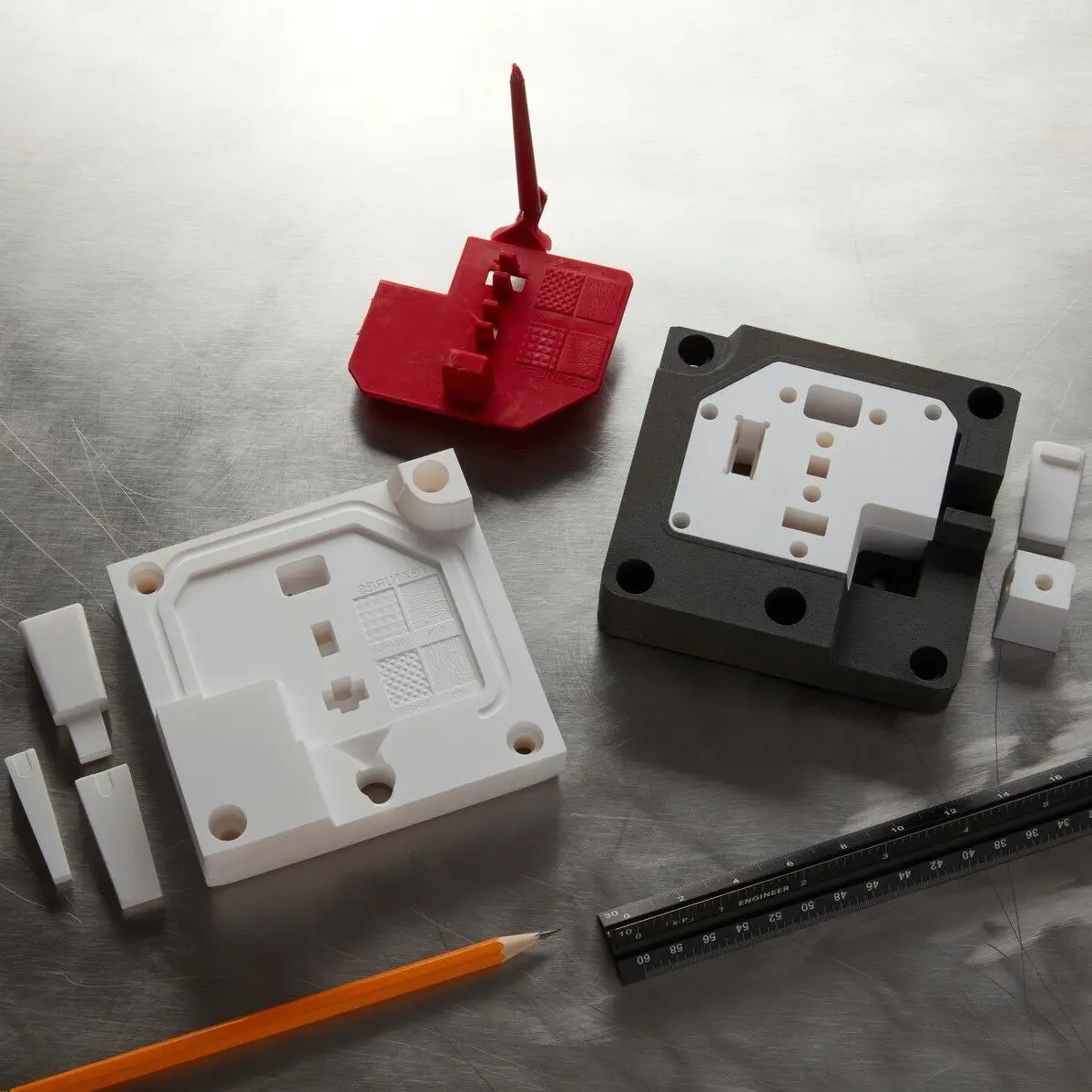
Guía de utillaje rápido
En este libro blanco, aprenderás a combinar las herramientas rápidas impresas en 3D con procesos de fabricación tradicionales como el moldeo por inyección, el termoformado o la fundición.
Iteraciones de un componente automovilístico con diseño generativo en la Form 3L
Uno de los últimos proyectos innovadores de IGESTEK es un Soporte Amortiguador de Suspensión Estos componentes forman parte del sistema de suspensión de un vehículo, cuya función es reducir las vibraciones que se producen durante el movimiento del vehículo para aumentar la comodidad de los pasajeros.
El soporte amortiguador se desarrolló con el software de diseño generativo Fusion 360 de Autodesk, que ofrece múltiples soluciones en función de una serie limitada de requisitos.
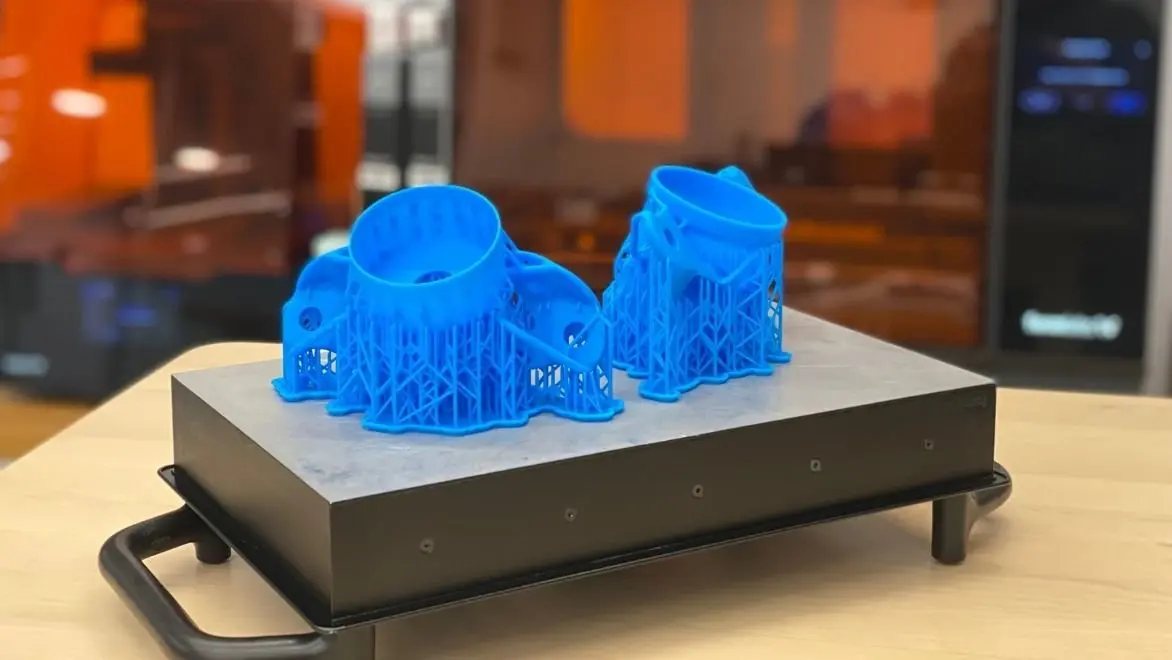
El gran volumen de impresión de la Form 3L permitió a IGESTEK imprimir múltiples iteraciones del componente al mismo tiempo.
A continuación, el equipo imprimió en 3D in situ los diseños más prometedores en su impresora 3D de estereolitografía (SLA) de gran formato Form 3L para validar la geometría, aprovechando su gran volumen de impresión para imprimir hasta tres iteraciones diferentes al mismo tiempo. Gracias a la impresión 3D SLA, se han podido realizar las geometrías complejas que se obtuvieron mediante el diseño generativo y validar los procesos de montaje y cinemáticos con prototipos funcionales sin invertir en herramientas caras.
El resultado final del proceso de I+D fue una arquitectura de múltiples materiales que combina la impresión 3D de metal basada en geometrías generativas y materiales compuestos más ligeros para ofrecer un rendimiento óptimo, en un paquete un 40 % más ligeros que las soluciones actuales del mercado.
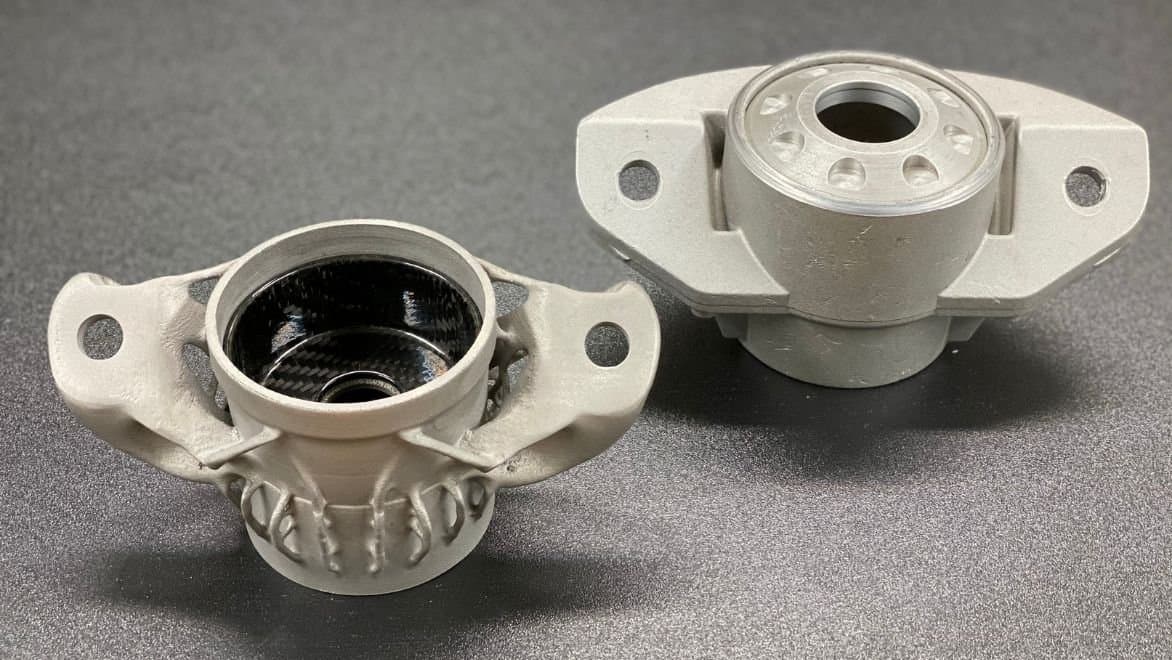
El resultado final, construido con una combinación de impresión 3D de metal y materiales compuestos.
Cómo usar los materiales de impresión 3D SLA para crear una herramienta de termoformado
El equipo de IGESTEK también utiliza la impresión 3D más allá de la creación de prototipos, para producir utillaje rápido con el que fabricar piezas de materiales compuestos, como por ejemplo, el termoformado de preimpregnados de carbono.
"Las resinas de Formlabs, como la Rigid 10K Resin y la High Temp Resin son muy útiles para aplicaciones de ingeniería. Solemos trabajar con tecnologías de termoformado por compresión de materiales compuestos. Para trabajar con una prensa, la herramienta necesita ser rígida y resistente al calor, porque se utiliza presión (para dar formar a las piezas de materiales compuestos) y también altas temperaturas, que normalmente son de 180 o 200 grados", nos dijo Nerea Romero, directora de innovación en IGESTEK.
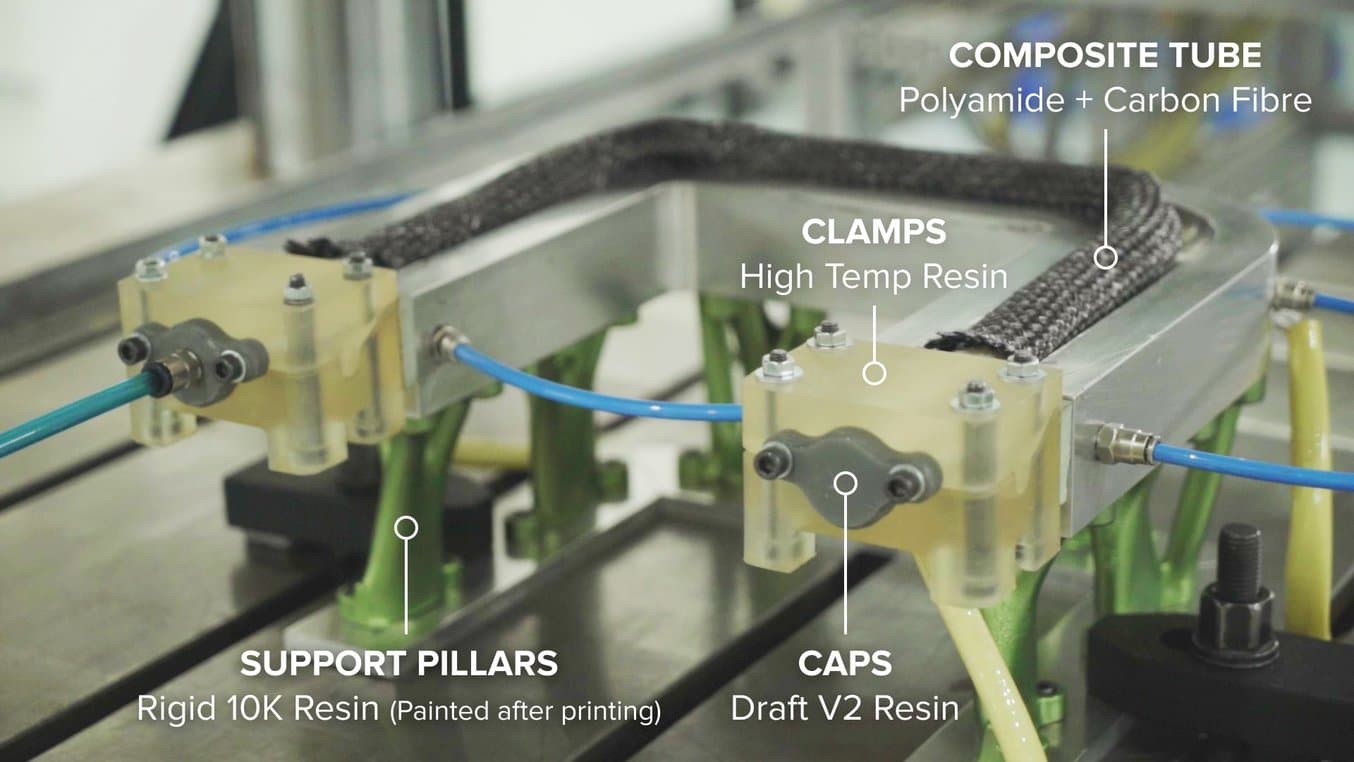
Este equipo de termoformado para tubos de materiales compuestos se construyo con diversas piezas impresas en 3D.
Un ejemplo reciente es una herramienta que el equipo desarrolló para fabricar tubos de materiales compuestos. Utilizaron la Rigid 10K Resin para fabricar los pilares de apoyo de un equipo que requería una gran rigidez, la High Temp Resin para producir las sujeciones que debían soportar altas temperaturas y presiones del aire y la Draft Resin para fabricar rápidamente topes para la herramienta.
"[Si no tuviéramos acceso a la impresión 3D], tendríamos que fabricar con metal, lo que obviamente requiere más tiempo y es más caro. Con la impresión 3D, disponemos de una respuesta rápida para lo que investigamos. Si algo no funciona, simplemente podemos imprimir otro prototipo y mejorarlo", explicó Romero.
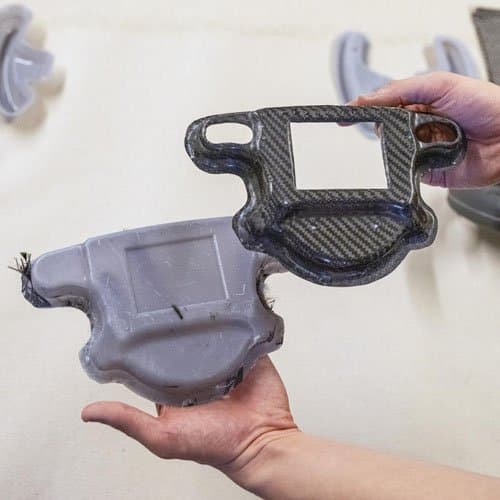
Fabricación de piezas de fibra de carbono con moldes impresos en 3D
Descarga este libro blanco con guías para diseñar moldes compuestos y directrices paso a paso para los métodos de preimpregnado (prepreg) y de laminado manual para crear piezas de fibra de carbono.
Moldeo por inyección con insertos de moldes impresos en 3D
El equipo de IGESTEK también utiliza la impresión 3D para crear insertos de moldes para el moldeo por inyección de piezas de plástico. Antes, mecanizarían estos insertos a partir de aluminio y acero (in situ para piezas simples y externalizándolos para moldes más complejos), pero esto conlleva costes elevados y plazos de entrega largos, especialmente para prototipos únicos o remesas de prototipos de bajo volumen.
Con un ejemplo reciente de un inserto de molde de inyección para fabricar un componente para la cubierta exterior de un coche, la impresión 3D permitió al equipo reducir los costes y los plazos de producción a menos de un tercio de los originales.
Inserto de molde de inyección | Impreso en 3D | Mecanizado en metal |
---|---|---|
Coste | 300 € | 1000 € |
Plazo de producción | 10 horas | 30 horas |
El molde tiene dos cavidades: una cavidad está hecha de un inserto de metal y la otra cavidad es un inserto impreso en 3D a medida que contiene el negativo del diseño. Esto es ideal para la creación de prototipos, ya que el equipo puede cambiar con facilidad los insertos impresos en 3D y someter a ensayo diferentes iteraciones con rapidez.
"En la fase de prototipos, solo hacen falta algunos componentes que se montarán con otros componentes para poner a prueba la simetría de todo. Con 20 o 50 componentes, basta para demostrar que lo que hacemos funciona", nos dijo Romero.
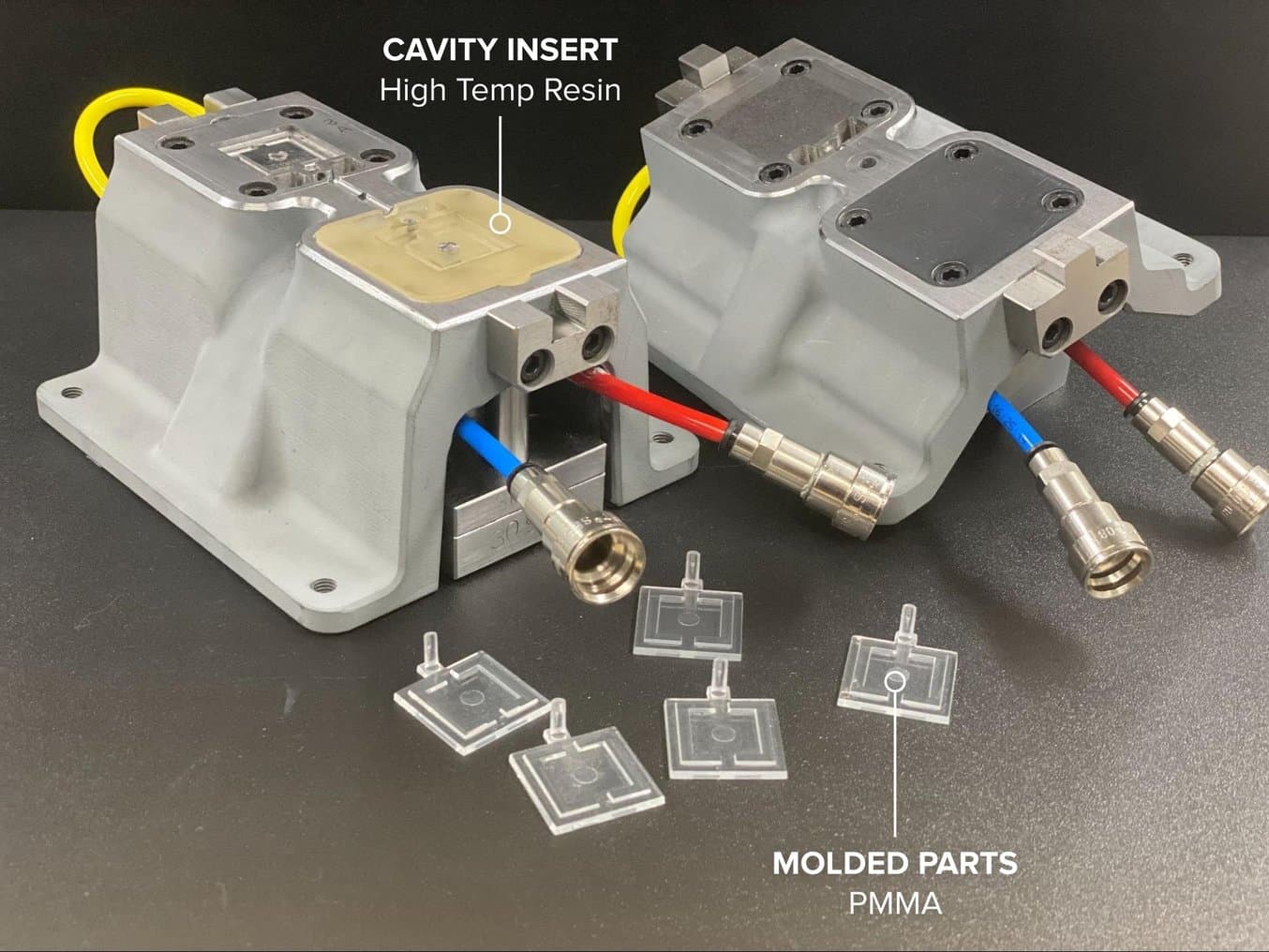
Conjunto de moldeo por inyección para un componente automovilístico hecho con acrílico, utilizando insertos de molde de High Temp Resin.
El número de piezas moldeadas que se pueden obtener con un inserto impreso en 3D depende principalmente de tres factores: el material de moldeo, el sistema de inyección y los parámetros del proceso de moldeo.
"Depende en gran medida de qué tipo de material se utilice para el moldeo por inyección o para el compuesto. Porque, por ejemplo, para el moldeo por inyección, si se usa un plástico reforzado con fibras, el proceso es mucho más agresivo que con materiales más convencionales. El inserto quedará dañado antes. Tal vez se puedan obtener 20 componentes, pero si se quiere producir más, hay que ir cambiando los insertos para continuar con la fabricación", nos dijo Romero.
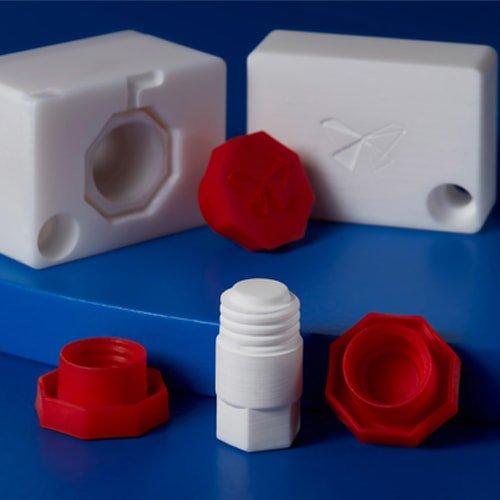
Moldeo por inyección rápido de bajo volumen con moldes impresos en 3D
Descarga nuestro libro blanco para encontrar recomendaciones sobre el uso de moldes impresos en 3D en el proceso de moldeo por inyección para reducir costes y el plazo de producción. También podrás ver estudios de casos reales con Braskem, Holimaker y Novus Applications.
Rumbo al siguiente gran proyecto
Incluso mientras sigue innovando el equipo de IGESTEK ya está pensando en cómo puede poner a prueba los límites de lo que es posible con la impresión 3D en sus próximos proyectos.
Algunos de los próximos proyectos incluyen la creación de herramientas de termoformado de gran tamaño, el aprovechamiento del volumen de impresión de su Form 3L y la experimentación con otros materiales como la Flexible 80A Resin y la Elastic 50A Resin, que aportan nuevas capacidades al utillaje.