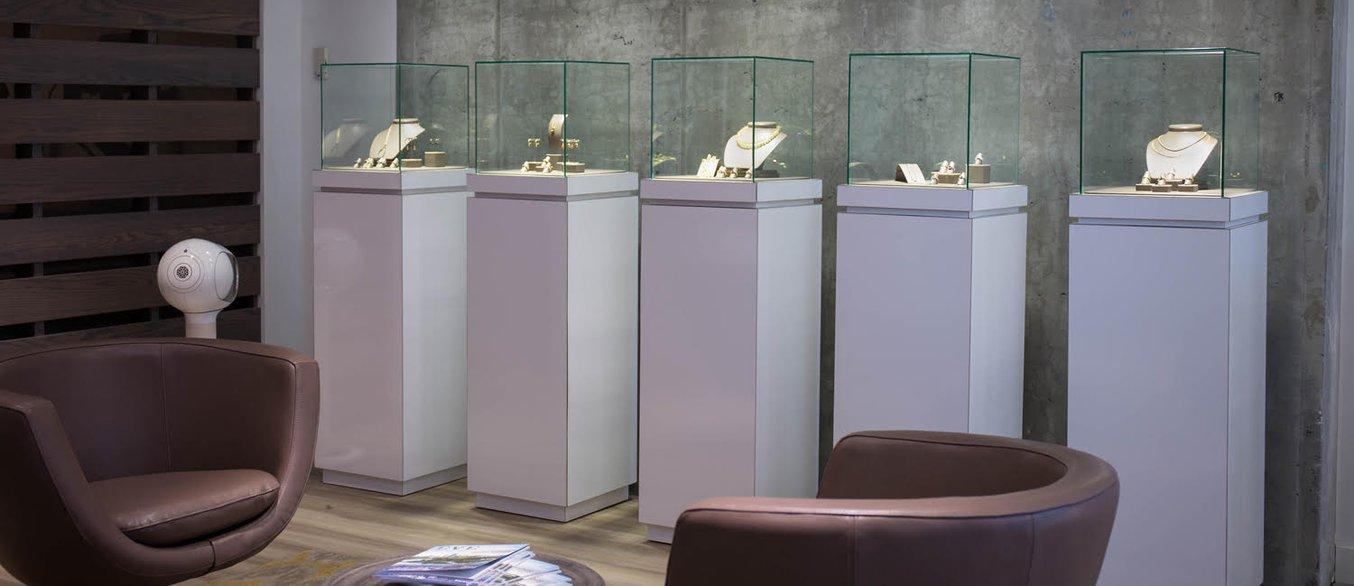
At Davidson Jewels, customization is more than a business plan: it’s a philosophy. This jewelry design studio, based in Calgary, designs and builds custom jewelry and engagement rings, working with clients from concept to final piece to create jewelry that “is as unique as that special person in your life.”
The custom jewelry design and development process begins with listening. Once Davidson & Co. has worked to understand a client’s needs, the next step is design. The studio uses computer-aided design (CAD) software and a Formlabs Form 2 3D printer to prototype pieces for clients to test, making sure that the concept and fit are perfect before moving on to source the gemstone and materials from their global suppliers.
We interviewed designer Ian Davidson about how he became interested in jewelry, how prototyping tools have evolved the industry, and how he uses Formlabs Black Resin and Castable Resin to prototype and finalize his custom pieces.
How did you get involved with jewelry?
I attended art school in the late 1960s and early 1970s studying painting. My first introduction to jewelry was as an option in art school. After college, it was a simple way to earn money to support myself by selling my pieces at craft fairs. I soon learned that it was a good fit with my creativity and ability to work with people. I also loved tools and figuring out how things were made.
How does your jewelry fit in with the broader landscape of the industry?
I work today from my streetfront jewelry design studio, where I present a small collection. But I mostly work with retail clients on individual projects that they bring to me.

How did you first start working with CAD and bringing technology into the process?
I bought my first CAD system in 1989, a 2D CAD program called Power Draw, a Mac computer, and a pen plotter to output the drawings. I knew something was going to happen with computers and jewelry design, and wow, did it ever. I bought into Gemvision’s software, Matrix, at version 3 to explore design possibilities with my clients and to be able quickly make design changes. But 3D output was not readily available, so most of the time I hand-carved the wax model by hand.
I bought the first version of a printer that used digital light projection (DLP). It was nice to be able to print in 3D, but I paid the price for early adoption, as it was difficult to get good, consistent prints. A dream came true when I purchased a Form 1+. True plug-in and print at a great price, and the same for my Form 2, which is even more consistent.
The Form 2 has the biggest “cool” factor for my customers. They have all heard about 3D printing and how it’s going to change their lives, but have never seen one. The Form 2 is located in the public area of the studio and it gets a lot of attention.
The Form 2 3D printer uses stereolithography (SLA) to precisely cure parts from a liquid resin. Learn more about the differences between SLA and DLP.
What have been some of the biggest challenges in moving from prototype to production?
In the beginning, I used 3D printing as a proof of concept tool with clients. After getting approval, I would send an STL file to an outside service bureau to be grown again and cast. Today, I do all of that in house. The biggest problem I faced moving from prototype to production was curing the resin. Resin that is cured properly makes casting easy.
How does prototyping jewelry pieces ahead of time in Black Resin help you?
I like using Black Resin to help my clients see exactly what their new piece is going to look like. If they are going to take the model home to share it with their partner or think further on the design, it’s hard, durable, and wearable.
What’s your experience been like with Castable Resin? What is your casting workflow?
I find that Castable Resin works very well when the material is cured properly. After curing the resin, I invest it with a St. Louis vacuum investment mixer and follow Formlabs’ burnout instructions. I burn out overnight, casting in the morning with a Schultheiss VPC 040 casting machine. I get great results with castings that clean up quickly only using sandpaper (and a file on the sprue).

What does the future of jewelry look like? How will technology like 3D printing change the industry?
I think that the future looks bright for jewelry designers who master the use of 3D design software and printers. 3D printing technology makes it possible to quickly design, explore, change, and produce accurate and complex models that may have taken days to create by hand, with no possibility of change without scrapping many hours of work.
Selling Custom Jewelry
Custom design is the future of the jewelry industry, and your business needs the best tools to adapt. Download our tip sheet to learn how to approach the custom sales experience, from recommended workflows to where 3D printing fits in.