La ortodoncia digital a gran escala: lo que hemos aprendido del mayor laboratorio de ortodoncia del Reino Unido

A orillas del Lago Corrib en Irlanda se sitúa el castillo de Ashford, una construcción medieval del siglo XIII. En la actualidad aloja un hotel de cinco estrellas que ha atraído a una larga lista de invitados ilustres, desde príncipes y reinas hasta actores y presidentes estadounidenses. Inspirado por su personalidad única, su encanto y su extraordinario servicio de atención al cliente, Sean Thompson decidió poner el nombre del castillo de Ashford a su laboratorio de ortodoncia con el objetivo de trasladar dichos valores a su sector.
Tras haber trabajado varios años en el departamento de ortodoncia y cirugía maxilofacial del Sunderland Royal Hospital, Sean se dio cuenta de que había una demanda creciente de ortodoncistas que, sin embargo, chocaba con la falta de laboratorios de alta calidad capaces de ofrecer servicios técnicos especializados de ortodoncia.
Así, Sean fundó Ashford Orthodontics en su garaje en 2001 y tras darse cuenta de que su clientela empezaba a crecer rápidamente, Craig Stevens y Graeme Winyard se unieron al proyecto. Hoy, estos tres técnicos especializados en ortodoncia gestionan el laboratorio de ortodoncia más grade del Reino Unido con unas instalaciones de 12 000 pies cuadrados (1100 metros cuadrados) y más de 50 empleados.
Sean siempre se ha esforzado para mantener el laboratorio a la vanguardia del sector, algo que hoy es más importante que nunca, ya que la ortodoncia está experimentando la revolución tecnológica más importante hasta la fecha con el paso de los procesos de trabajo tradicionales a las tecnologías digitales.
Sigue leyendo para saber cómo Ashford creó un departamento digital desde cero que ahora produce 1200 alineadores y retenedores transparentes al mes con un parque de 12 impresoras 3D, cuya ventaja económica ha conseguido que el laboratorio crezca y atraiga nuevos clientes.
Descubre el laboratorio de Ashford Orthodontics y lee la entrevista de Sean para aprender cómo se pasaron al trabajo digital.
Inicios y crecimiento de un departamento digital
Ashford Orthodontics empezó a experimentar con la ortodoncia digital hace cinco años.
"Sabíamos que teníamos que empezar a trabajar con la ortodoncia digital. No podíamos permitirnos no hacerlo si queríamos desempeñar un papel importante en el sector de la ortodoncia", añadió Sean. "Queríamos ser de los primeros en ponernos manos a la obra. Todas las empresas tienen planes de cuatro o cinco años y nadie quiere quedarse atrás mientras los demás avanzan".
Al principio, el laboratorio adquirió dos impresoras 3D Stratasys Objet30, máquinas industriales que se comercializaban especialmente para el sector de la ortodoncia. Así, empezaron a ganar experiencia con los procesos digitales y a trabajar con proyectos digitales de médicos, pero dado el alto coste y la complejidad para manejar estas impresoras 3D de gran escala, el laboratorio tuvo dificultades a la hora de justificar la viabilidad del trabajo digital en su negocio.
"Tenías que invertir mucho dinero en actualizar software y mantener y calibrar las máquinas, hasta el punto de que cuando tenías en cuenta el coste real de las resinas, ya no podías fabricar un modelo por el precio que queríamos y mucho menos en las cantidades que pretendíamos", nos contó Sean.
"Además, como con cualquier impresora, si construyes tu empresa en base a ella, no puedes tener solo una, sino que necesitas dos y tienes que tenerlas en funcionamiento al 50 %". Si una se estropea, siempre puedes aumentar el funcionamiento de la otra al 100 %". Con las máquinas Stratasys, resultaba muy costoso mantener un parque de ese tipo de impresoras, así que decidimos adquirir una impresora más pequeña que, si bien al principio podía suponer mucho trabajo para nosotros, después nos permitiría seguir añadiendo capacidades. Así fue como nos decidimos por Formlabs y no nos hemos arrepentido", concluyó Sean.
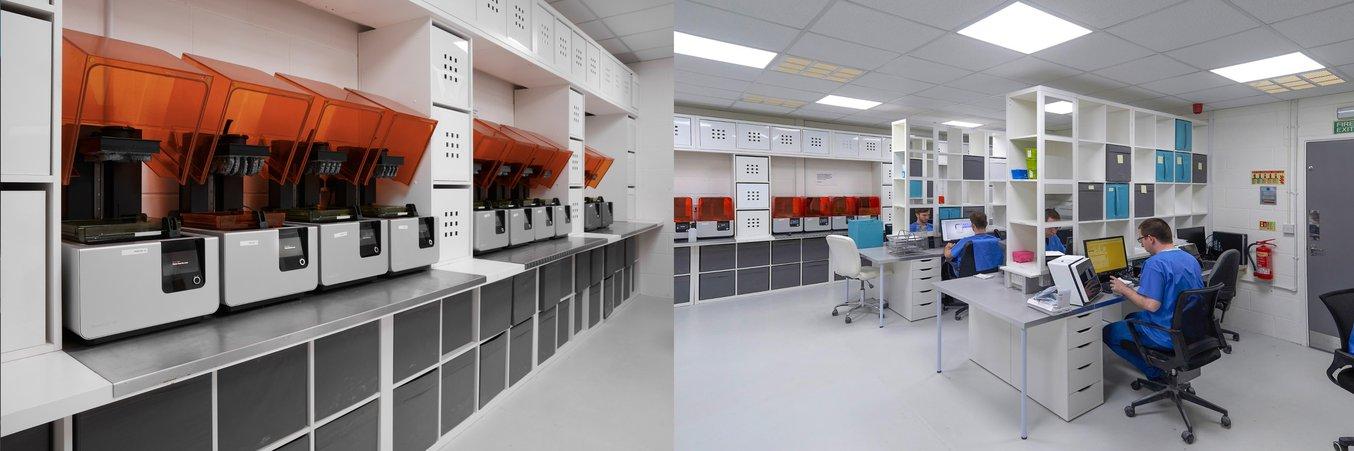
En la actualidad Ashford cuenta con un parque de 12 impresoras 3D de estereolitografía (SLA) Form 2 y emplea a ocho técnicos en su departamento digital.
El laboratorio empezó a funcionar con una sola impresora para pasar rápidamente a un parque de dos impresoras, después de cuatro y finalmente a uno de 12 impresoras Form 2. Al mismo tiempo, el número de trabajadores del departamento digital ha pasado de un solo técnico a un equipo de ocho expertos en tecnologías digitales, que incluye técnicos cualificados y expertos en informática.
"La Form 2 es muy fiable. La llamamos "caballo de batalla". Cuando nos vamos a casa por la noche sabemos que cuando lleguemos por la mañana todo estará impreso. No nos vamos a encontrar ningún fallo, todo va a estar ahí. Por ese motivo, podemos desarrollar nuestro negocio en torno a Formlabs", nos contó Sean.
Presentación del turno de noche
Ashford sigue un horario diario muy bien estructurado que se adaptó fácilmente la proceso de trabajo digital. El laboratorio cierra cada día alrededor de las 3 p.m. Durante la jornada se dedican a revisar las nuevas imágenes escaneadas que les envían los clientes y a planificar los tratamientos. Por la noche, dejan que se impriman en 3D los modelos digitales. Por la mañana temprano, uno de los técnicos limpia y seca las piezas impresas en 3D y un poco más tarde otro técnico produce los alineadores transparentes mediante termoformado en los modelos acabados. Cuando la mayoría de los técnicos llegan al laboratorio, los alineadores ya están listos para el posacabado.
"Cuando dispones de un modelo sobre el que trabajar, hay muy poca diferencia. Si estás en un laboratorio tradicional y quieres ir más allá y adaptar el trabajo digital, cuando ya has pasado por la fase de aprendizaje, el proceso de fabricación te resultará muy similar", nos contó Sean.
Por la tarde, los técnicos empaquetan y envían las piezas acabadas, de forma que los médicos las reciben en un plazo de 48 horas. En general, el proceso de trabajo digital ahorra 24 horas, ya que las imágenes escaneadas llegan al laboratorio de manera inmediata, lo que permite que Ashford elabore los encargos de manera más rápida y acepte más trabajo.
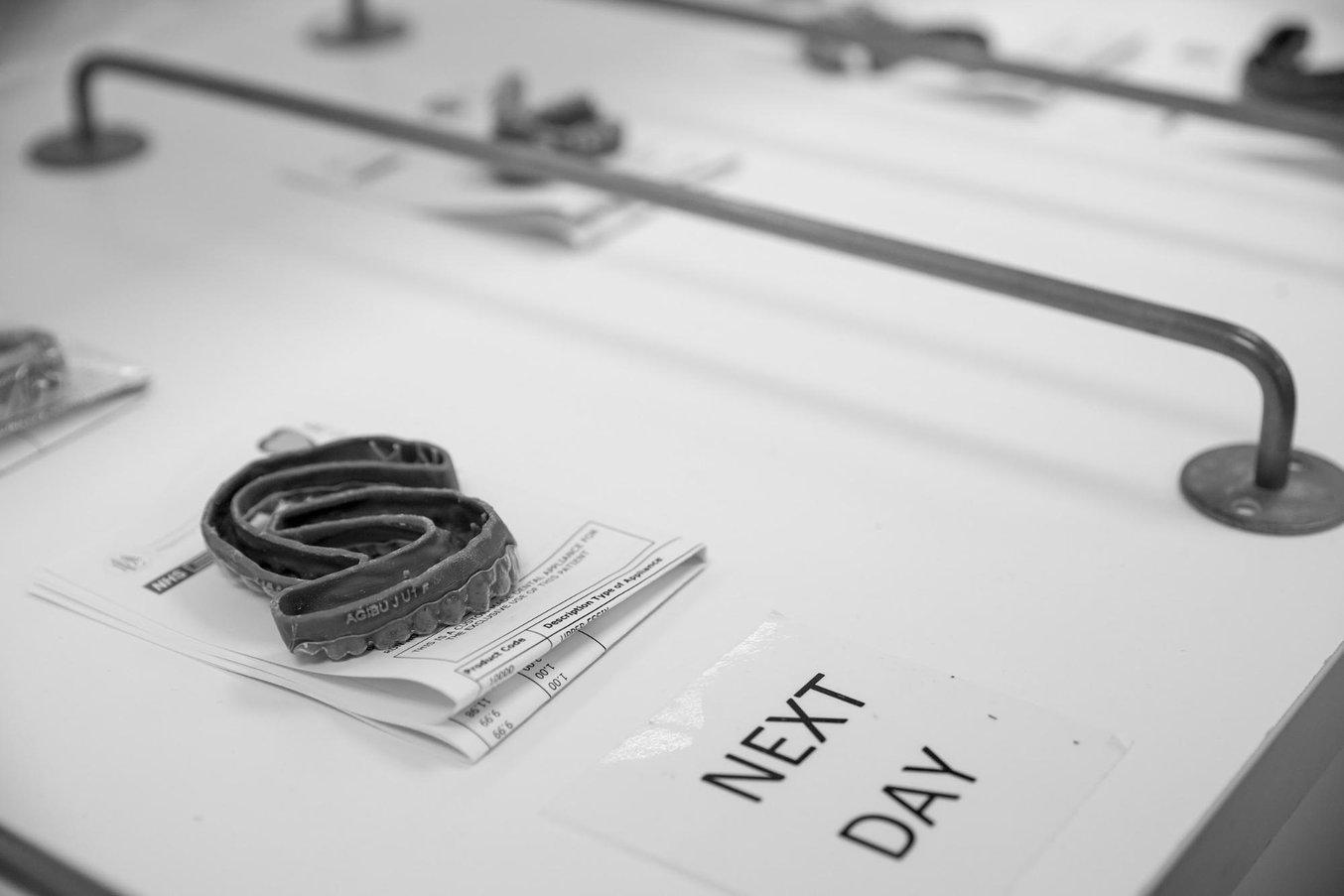
El proceso de trabajo digital te ahorra 24 horas: los médicos reciben las piezas finales en un plazo de 48 horas desde el envío de las imágenes escaneadas.
"Funciona perfectamente para nosotros. Encendemos las impresoras justo antes de volver a casa del trabajo: así es nuestro turno de noche. Cuando regresamos por la mañana, el turno de noche ya ha terminado su cometido. No importa si tardan dos, cuatro o seis horas: está hecho. Dependemos totalmente de eso cuando llegamos por la mañana, así que lo que nos importa realmente es la calidad y la fiabilidad de la impresión", nos explicó Sean.
El laboratorio también ha aprendido a aprovechar las múltiples impresoras y la gran base de impresión de la Form 2.
"Resulta muy sencillo distribuir varios modelos entre 10 o 12 impresoras e imprimirlos en un par de horas. Si necesitamos hacer lotes rápidos, podemos distribuirlos entre todas las impresoras en vez de utilizar solo una para todas las piezas. Nos hemos dado cuenta de que este modelo funciona muy bien para nuestra empresa", añadió Sean.
Encontrando soluciones con las tecnologías digitales
La tecnología digital también permite que el laboratorio almacene y acceda a los modelos digitales a cualquier hora en línea, lo que ha demostrado ser beneficioso para fabricar retenedores de reemplazo.
"No se producen retrasos cuando un niño rompe o pierde su retenedor, ya que no tiene que ir al dentista para capturar una nueva impresión. Los dientes se mueven todo el rato y es normal que se produzcan recaídas. Ahora podemos descargar el archivo de la nube (donde los guardamos de manera gratuita), imprimir el modelo, crear la pieza e incluso enviársela directamente al paciente", explicó Sean.
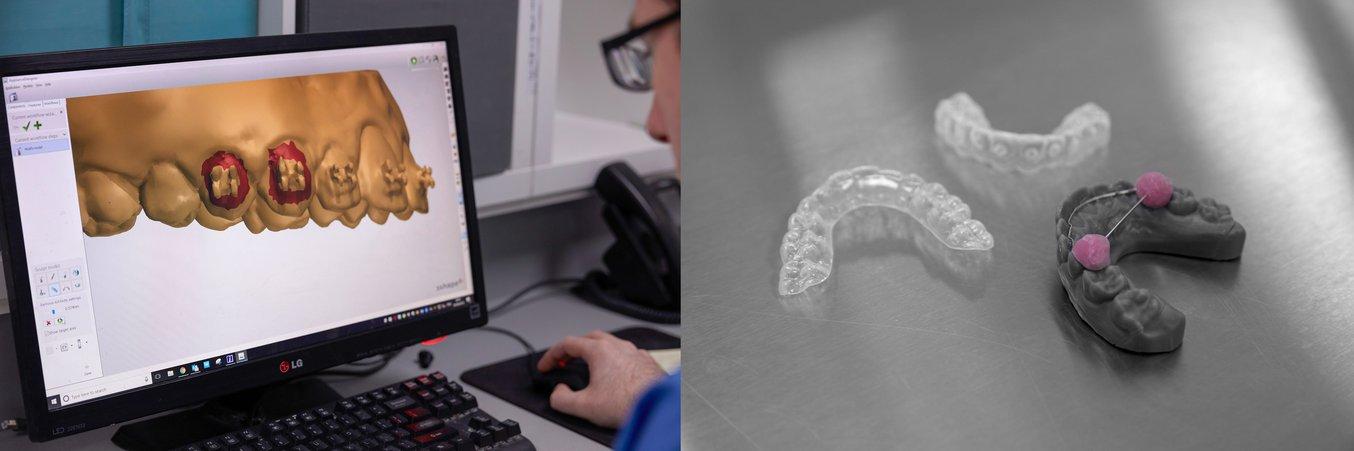
Además, con el proceso de trabajo digital, los técnicos pueden quitar brackets de manera virtual y crear múltiples piezas a partir del mismo modelo impreso en 3D.
Uno de los grandes beneficios de la tecnología digital, especialmente para ortodoncistas, es el hecho de que el laboratorio pueda reutilizar los modelos impresos en 3D para crear múltiples instrumentos.
"Una tendencia habitual hoy en día es despegar los brackets y colocar al momento todos los aparatos de retención en la consulta. Al eliminar los brackets de forma digital, podemos fabricar retenedores removibles, retenedores fijos, placas de Hawley o férulas de blanqueamiento en un mismo modelo, algo que no podríamos lograr a través de los métodos tradicionales o con los modelos de escayola", añadió Sean.
Un generador de confianza para atraer nuevos clientes
Sean cree que la tecnología digital sólo puede superar los procesos de trabajo tradicionales si resulta rentable. Dado que el ahorro también repercute en sus clientes, están acercando el mercado digital a cada vez más médicos clínicos: Sean considera que este es el camino que todo el mundo debería seguir.
"No debería costarte más prestar tus servicios a tus clientes y pacientes a través de la vía digital que a través de los métodos tradicionales de impresión. Por eso, lo que hemos hecho ha sido cambiar el coste de los modelos de escayola (que ya no necesitamos) por el coste de los modelos de resina. Por lo tanto, la factura que llega al laboratorio sigue siendo la misma, ya trabajes con procesos tradicionales o digitales, con la excepción de que puedes obtener tus productos con 24 horas de antelación", continuó Sean.
Esta propuesta de valor ha demostrado ser un éxito a la hora de atraer nuevos clientes del Reino Unido y de otras partes del mundo. Si bien el laboratorio tan solo obtiene pequeños márgenes de beneficios con los retenedores removibles y los modelos digitales, suponen un valor añadido considerable como generadores de confianza.
"Todos los días nos llegan nuevos clientes que nunca han trabajado con nosotros, así que no saben si la calidad va a ser buena o si el servicio de atención al cliente va a ser fiable. Cuando se dan cuenta de que los productos que fabricamos son de muy alta calidad, confían en nosotros para desarrollar instrumentos más complejos. Por lo tanto, siempre sucede que dos meses después de conseguir un nuevo cliente que quiere utilizar nuestros servicios de ortodoncia digital, nos empieza a preguntar si podemos fabricar bloques gemelos, aparatos fijos o aparatos funcionales. Antes de que podamos darnos cuenta, nos envía enormes cantidades de trabajo, porque podemos dar respuesta a todas sus necesidades", comentó Sean.
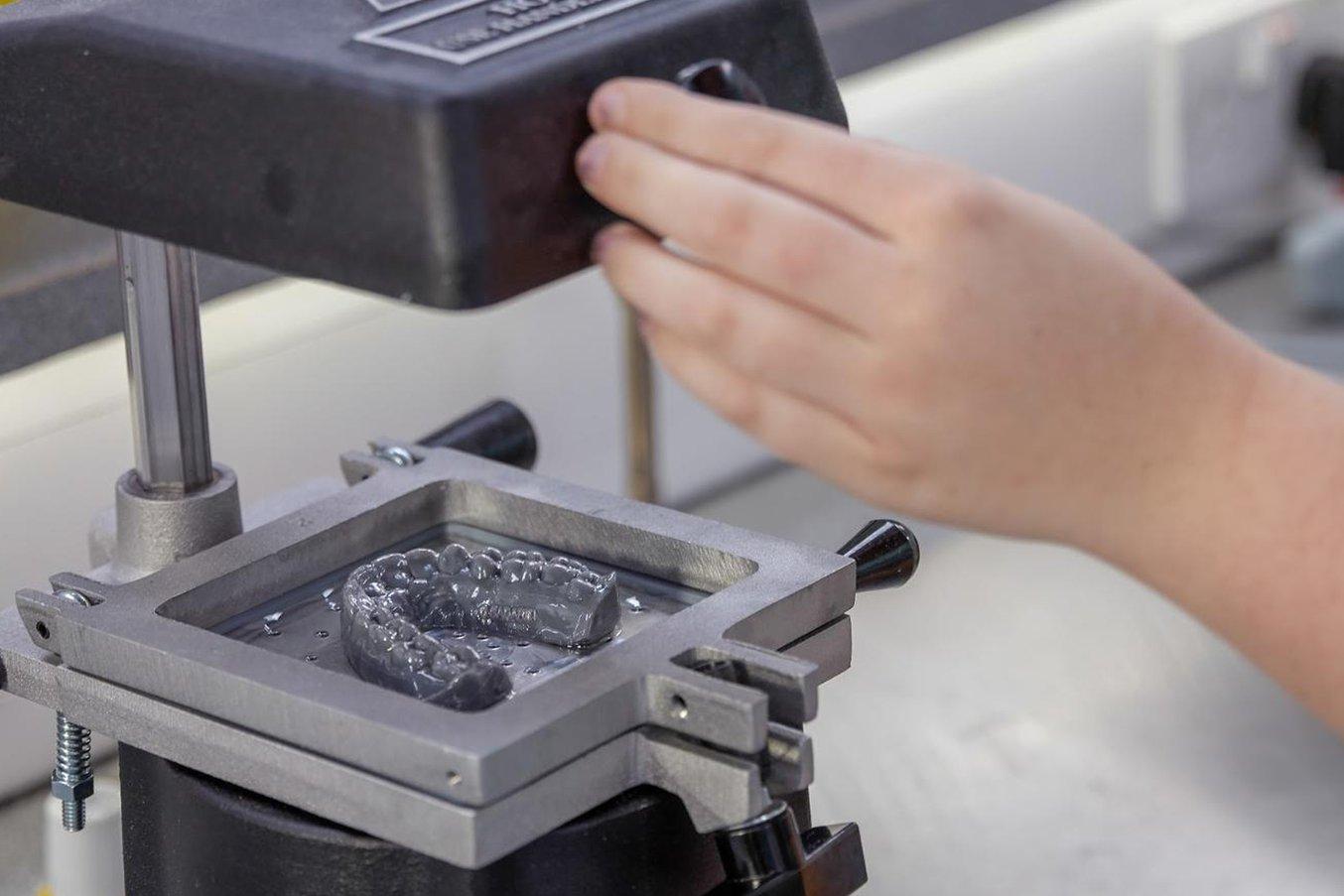
Los alineadores y retenedores termoformados funcionan como generadores de confianza. Esperan que los clientes empiecen a pedir instrumentos más complejos pronto, con los cuales el laboratorio generará más márgenes de beneficio.
En la actualidad, el laboratorio proporciona servicios completamente digitales a tres clínicas que no disponen de ningún material de impresión en sus oficinas. Se pueden permitir esa opción porque Ashford es capaz de satisfacer todas sus necesidades a través de métodos digitales.
"Cuando empezamos a adoptar el trabajo digital, este suponía alrededor del 2 % de nuestro negocio. El mes pasado alcanzó el 15 % y se trata de sector que más rápido está creciendo dentro del laboratorio", explicó Sean.
"En este momento, utilizamos técnicas tradicionales con una pequeña parte digital, pero en cuestión de dos o tres años, vamos a pasar a emplear técnicas digitales con una pequeña parte tradicional. Cuando eso ocurra, este sistema se convertirá en el motor de nuestro departamento de cara al futuro".
Cómo fabricar alineadores y retenedores termoformados a partir de modelos impresos en 3D
Descarga la guía de aplicación de Formlabs para consultar un tutorial paso a paso sobre cómo fabricar alineadores y retenedores termoformados a partir de modelos impresos en 3D con un proceso de trabajo digital, solicita una muestra gratuita de una pieza de ortodoncia y aprende más acerca de las herramientas y materiales necesarios y de los beneficios de pasarse a la ortodoncia digital.