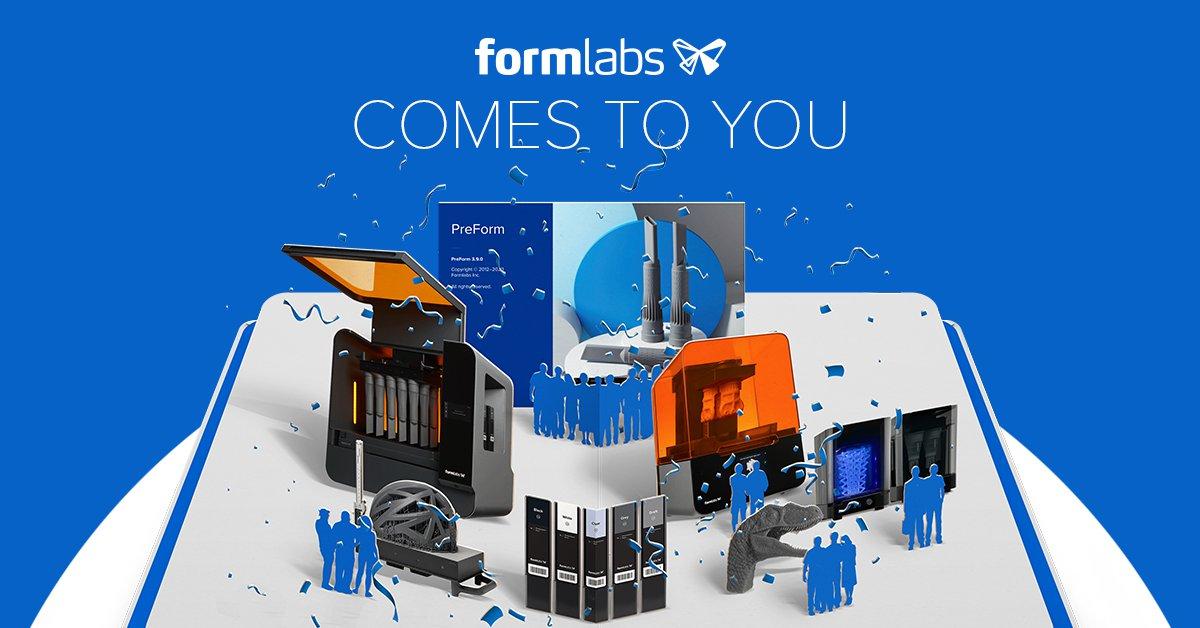
As 2020 draws to a close, it’s time to reflect on what has been an event-filled and unpredictable year. Challenging times call for innovative solutions and the 3D printing community has provided exactly that.
For this annual review, we’ve curated a selection of our most popular Formlabs Comes To You virtual sessions, highlighting some of the ways our customers have been driving impact across their industries.
This year, we went behind the scenes at United States Naval Academy, learned how a TedX speaker uses 3D printing to explore the connection between neuroscience and the body, shared how organizations are using additive manufacturing to adapt and evolve for a brighter 2021, and much more.
1. How Exactech and University of Florida Partnered to Use 3D Printing in the Fight Against COVID-19
No review of 2020 would be complete without addressing the impact and disruption caused by the global pandemic. Determined to offer support to the medical community and help those in critical need of testing, PPE, and medical equipment, Formlabs and its users acted quickly to establish a COVID-19 response initiative - collaborating with healthcare providers and government agencies around the world.
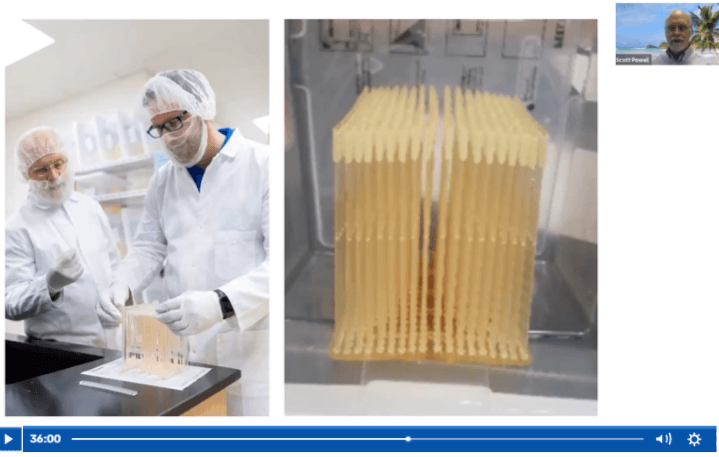
A powerful example of this was when the University of Florida and Exactech combined a fleet of Formlabs 3D printers, FDA-compliant facilities, and medical expertise to validate a nasal swab design and quickly scale production. The session explores how the two organizations had been using 3D printing technology prior to the pandemic, and during their new partnership.
“When the pandemic hit, we pivoted to produce nasal swabs. Equipped with the validated STL file from Formlabs and Northwell Health, we partnered with Exactech for their extensive experience in developing medical equipment in ISO approved facilities, rallied together our Formlabs printers, and ramped up production.”
Scott Powell, Operations Manager, University of Florida
2. CAPT Brad Baker on 3D Printing at the US Naval Academy
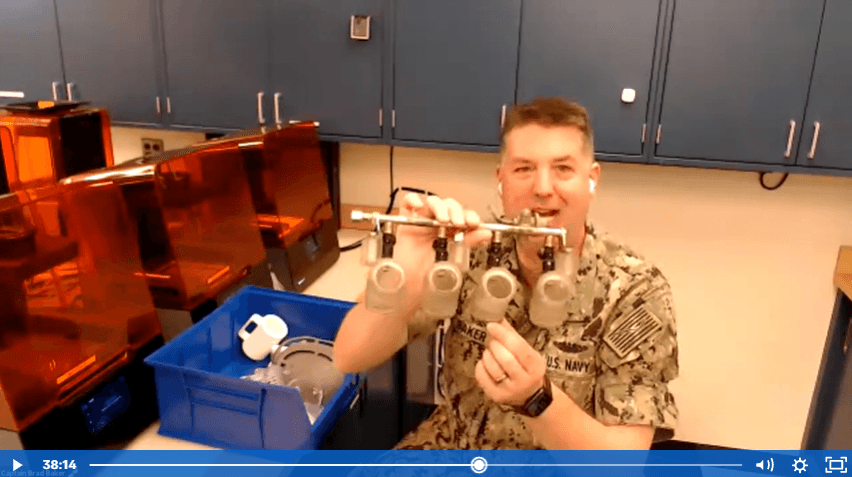
It’s not every day that you get to go behind the scenes and look at the additive manufacturing tools used by a federal service facility. In this tour of their world-class makerspace, United States Naval Academy’s Associate Professor, CAPT Brad Baker, discusses how he utilizes SLA printing within his mechanical and nuclear engineering teaching programs. With 16+ years of experience in the submarine force and a PhD in Mechanical Engineering, you’ll want to hear his advice for creating robust end-use parts.
“At the makerspace we have a wide range of filament, powder, and resin-based 3D printers for the USNA students to access. Our six Formlabs printers, or ‘precision printers’ as we call them, are used primarily for projects that require high accuracy, specific tolerances and fine details.”
Captain Brad Baker, MakerSpace Lab Director at USNA
3. Building BIG Structures with Monster City Studios
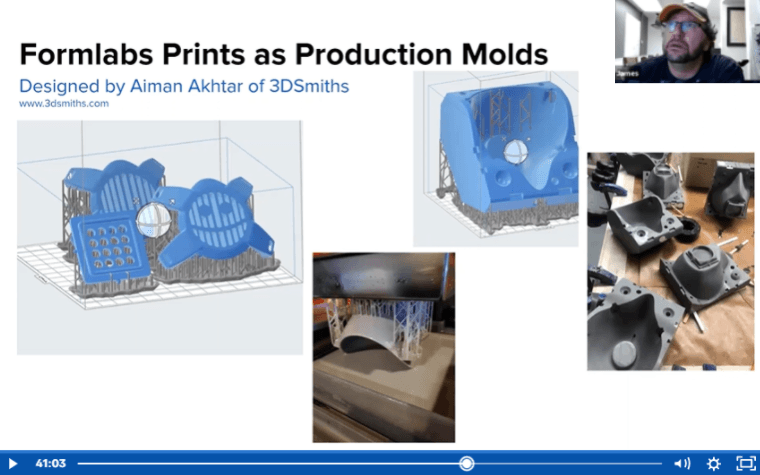
“Metal injection molding tools are extremely expensive and the one we wanted to create would have cost around €25,000. With Formlabs technology we were able to print a mold for a few hundred euros and inject silicone rubber into it. It works just like an aluminium or steel tool - we just use it for lower runs.”
James Powell, Founder, Monster City Studios
4. The Closest Thing to Metal 3D Printing With a €3300 Printer
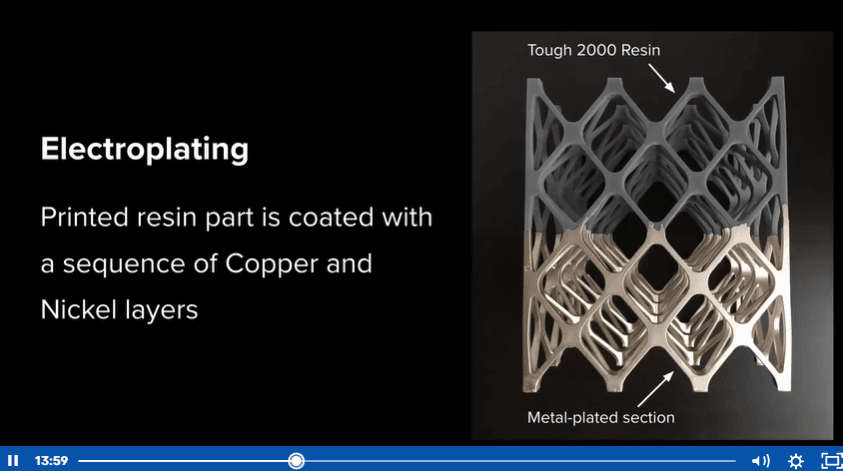
Metal 3D printing or machining metal parts can be a costly process, but it doesn’t have to be this way. During this session President and Founder of RePliForm Sean Wise looks at using hybrid techniques, like using electroplating with his Formlabs Form 3 printer, to achieve high detail, metallike parts at an affordable price. Sean discusses the science behind the electroplating process and how it can enhance the mechanical properties of the print. If you’re interested in exploring this topic, this is the video for you.
“RepliForm specializes in electroplating 3D printed parts to enhance their mechanical performance: with this technique we can increase the stiffness, strength and durability of photopolymer parts, without having to use a metal printer.”
Sean Wise, President and Founder of RePliForm
5. Designing for Humans with Product Designer and TedX Speaker, Dani Clode
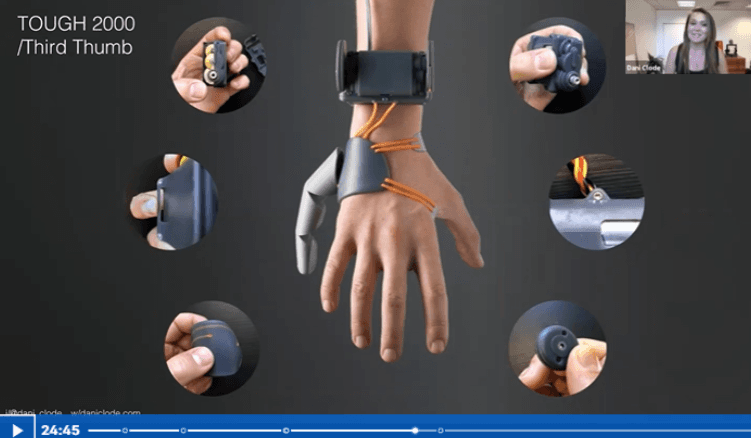
Designing functional parts for the human body is no easy feat. This virtual session explores the topic of augmentation and prosthetic extension, with product designer and TedX speaker, Dani Clode. During this highly-visual presentation, Dani talks about using the Form 3 when founding ‘The Third Thumb’ - a neuroscientific research project in collaboration with University College London. She also shares insights from working with Formlabs Tough 2000 Resin.
“The Third Thumb Project is designed around a 3D printed extension for your hand. It’s a catalyst for discussion, a bridge between design and neuroscience, and a truly unique experience.”
Dani Clode, Founder of The Third Thumb Project
6. Running a Print Farm with Christina Perla, Co-Founder & CEO of Makelab
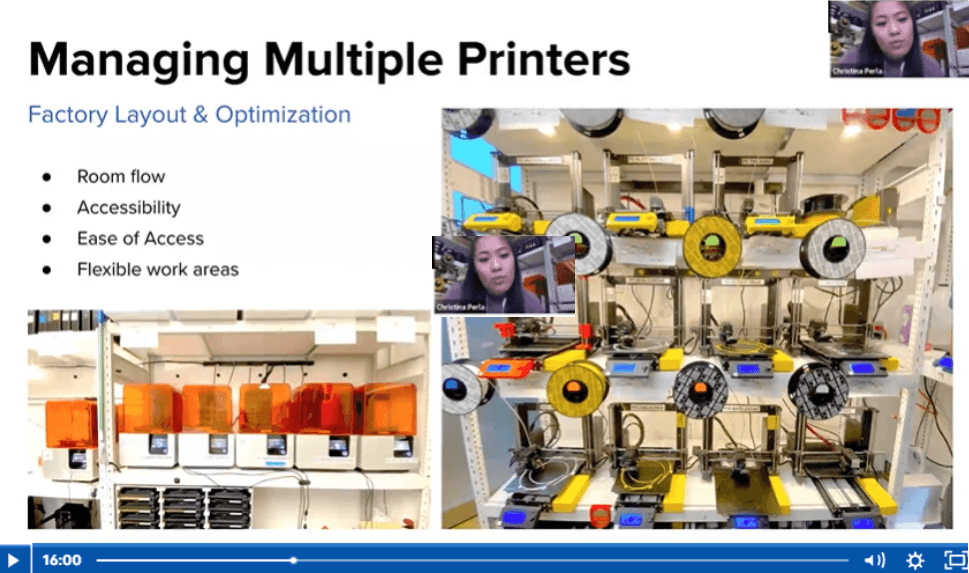
Another user benefiting from the enhanced production power of a fleet of 3D printers, is Formlabs Ambassador Christina Perla. In this session, Christina shares how she scaled her fabrication capabilities with Formlabs technology at her NYC based service bureau, Makelab. Hit play for tips and advice on keeping 20+ Form 3s running efficiently.
“When we scaled from one Formlabs 3D printer to seven, fourteen, then twenty, I learned quickly that factory layout and optimization was key. We’re based in Brooklyn, NY and space is hard to come by - so we decided that we needed to go vertical to get the most from our setup.”
Christina Perla, Co-Founder & CEO of Makelab
7. The Product Development Process that Helped This Startup Raise €475k
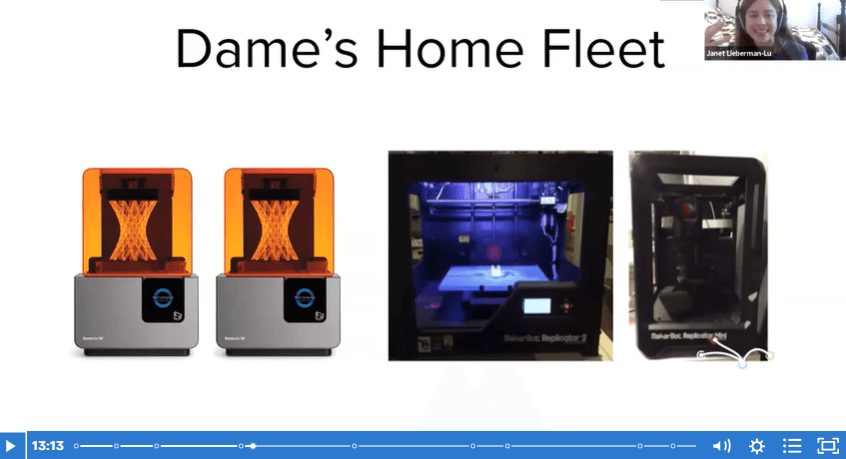
“The time and money saved by being able to immediately 3D print your ideas can be really transformative in how you think about the value proposition of prototypes."
Janet Lieberman-Lu, Co-founder of Dame Products
8. Designing and 3D Printing Jewelry with Rhino and Formlabs
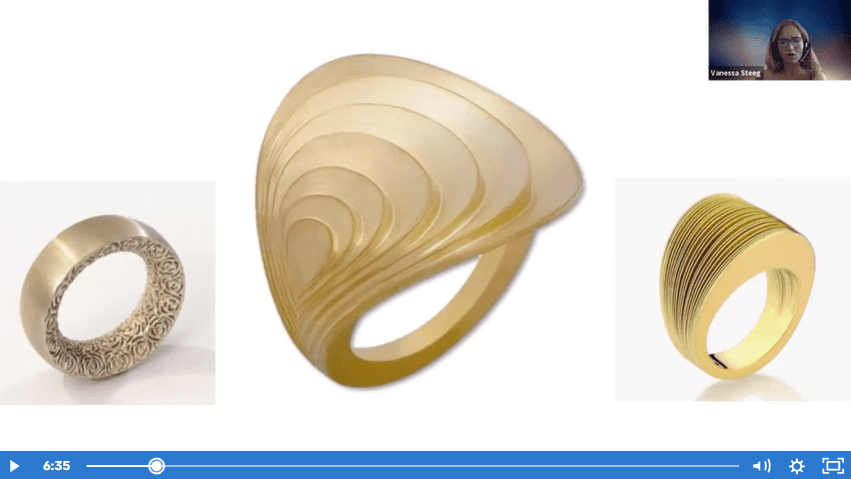
“Surface modeling is a spline-based geometry that is very powerful and versatile for creating the organic and complex shapes that are synonymous with jewelry.”
Vanessa Steeg, Rhino Tech & Trainer at McNeel
9. SLA Masterclass: Getting the Most From Your Prints With a Formlabs Pro Services Trainer
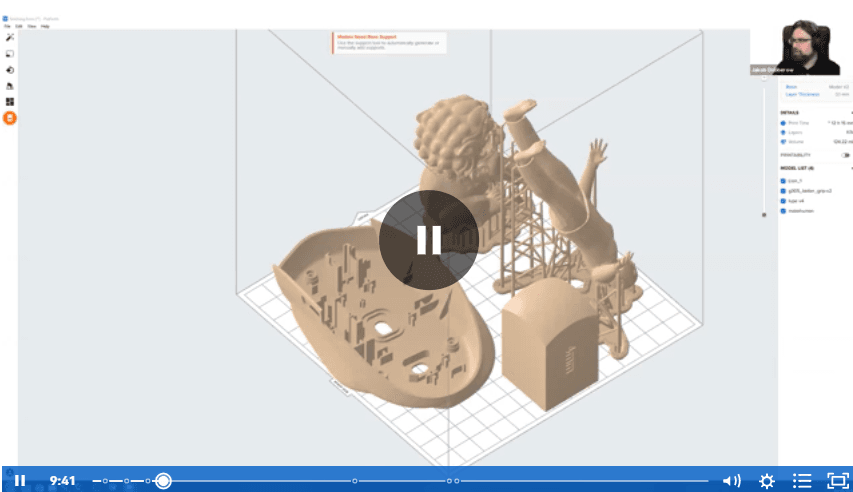
“The beauty of resin-based printing is that it allows you to create a very precise straight edge at any layer height. Therefore with designs that are tall on the Z-direction, you can speed up the print process without compromising accuracy by increasing the layer height.”
Jakob Dobberow, Pro Services Trainer at Formlabs
10. Innovation for Good: Accelerating Product Development Post COVID-19
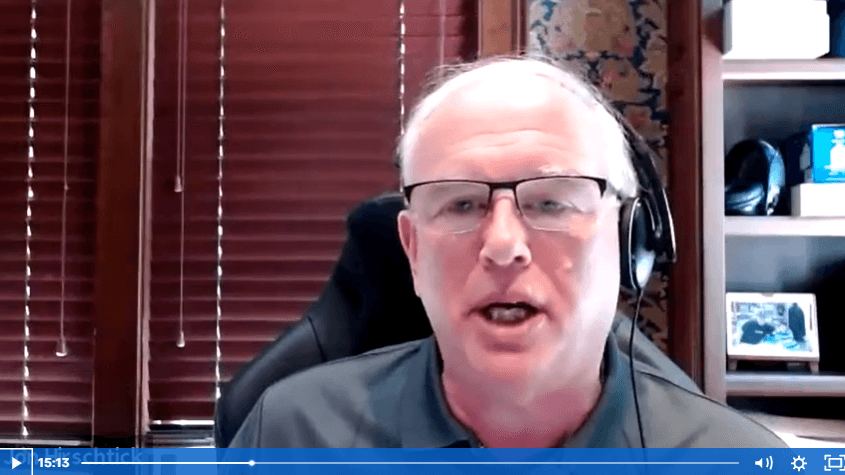
“The Covid-19 crisis has turned everyone into an entrepreneur in a sense - those who were negatively affected had to rethink and adapt, those who provided crucial resources had to keep up with demand, and others had to pivot quickly to seize opportunities.”
John Hirshtick, President, Software-as-a-Service (SaaS) Division, PTC
Wait, There's More
It wasn’t just manufacturing processes that digitized in 2020. The annual Formlabs User Summit evolved into a two-day, entirely virtual event, with over 5,000 of you tuning in from 100+ countries worldwide. Visit the event archive to hear how brands like Marvel, Ford, TaylorMade, Lush Cosmetics, and more are using 3D printing as a catalyst for change.
In the meantime, we’d like to take this opportunity to thank our customers, colleagues, and the community for driving impact in 2020, we look forward to what the new year has to bring.
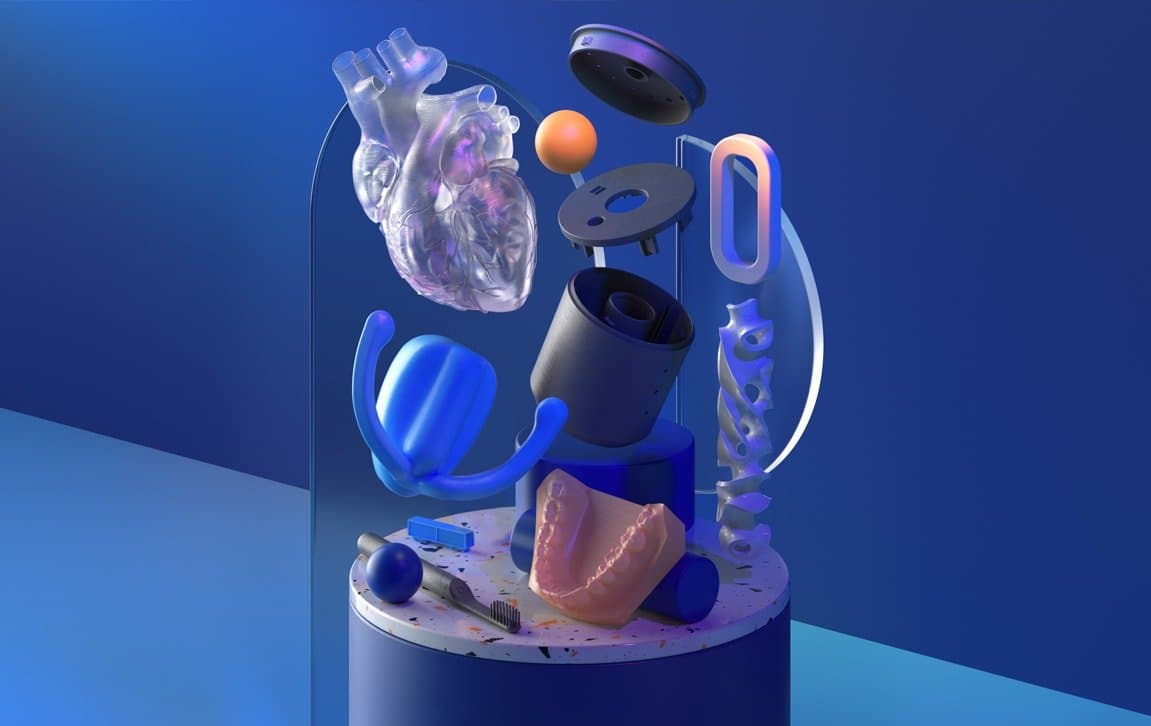
Formlabs User Summit 2020
Revisit the most memorable momebts from Formlabs User Summit 2020, with this video archive of 50+ recorded sessions.