How 3D Printing Boosts Efficiency and Spurs Innovation in Assembly Processes
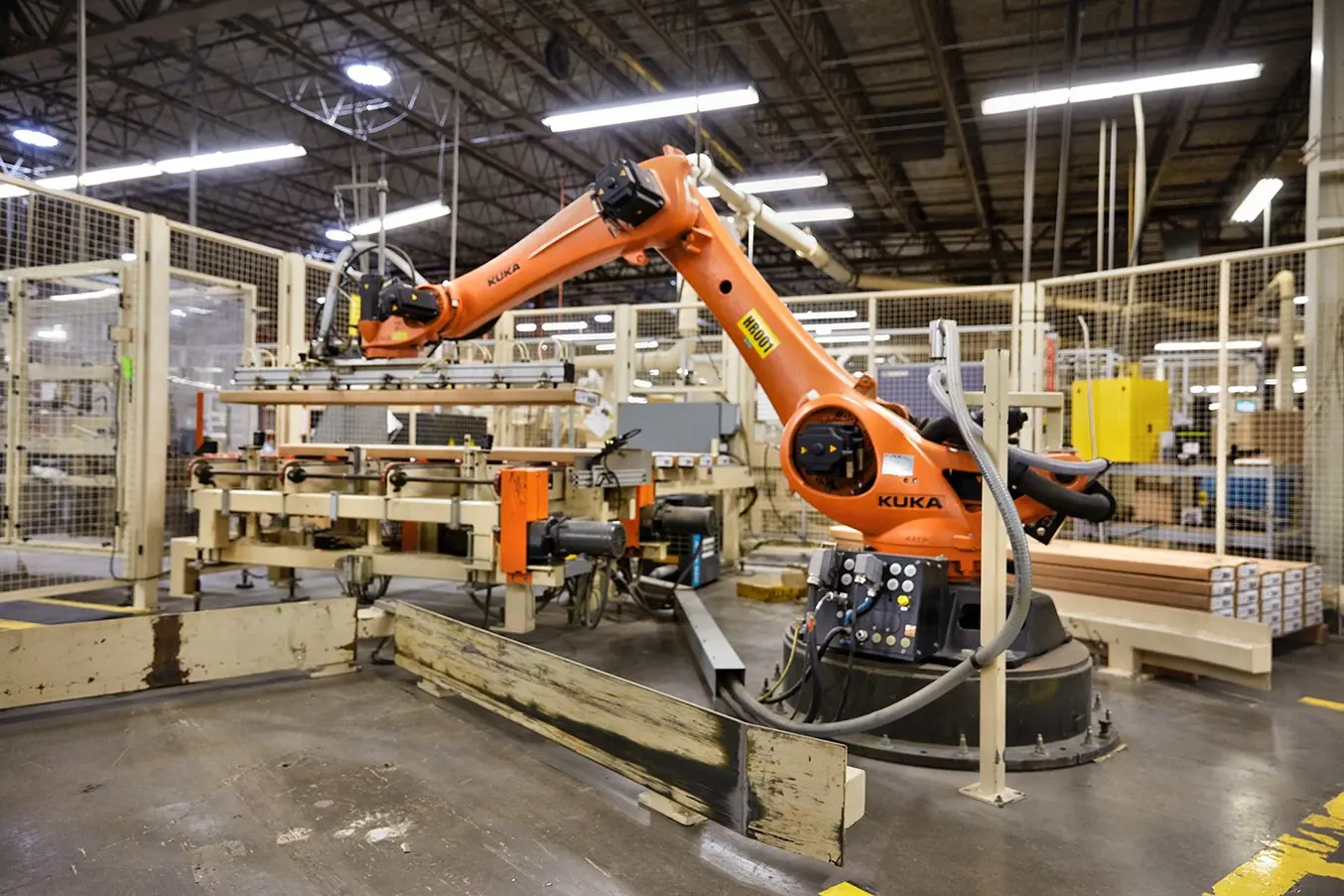
For products with any degree of complexity, at some point, individual components manufactured with different processes must be brought together into final assemblies.
Methods for manufacturing and assembling products have gone through many revolutions, each time driven by new technologies extending what is possible to build. Early joinery techniques helped carpenters build objects larger than a naturally occurring segment of lumber, with nails and screws reducing the time and skill required to build large structures from wood. Later, the introduction of manufactured metal fasteners like machine screws, bolts, and rivets provided strong, reliable mechanical joints for metal and plastic assemblies at a low cost.
Looking to assemble 3D printed parts? Learn how in our guide to using screws in 3D printed SLA parts.
Each era of development in fastening technology has been pushed forward by varied economic and design needs. The limited availability of craftspeople skilled in traditional joinery spurred the development of nails and screws; the desire to build structures that exceeded the capabilities of wood propelled efforts in riveting to create structural joints in tall steel-framed buildings like the Eiffel Tower.
The pressures driving innovation in the assembly methods are energy, speed, and labor costs. In each of those areas, 3D printing is helping to make assembly faster, use less energy, and create more efficient assemblies.
Energy Efficiency
Market and regulatory pressures for greater energy efficiency impacts supply chains as well as design and engineering choices for final products. For manufacturers and assemblers, this means using all of the technologies and advanced materials available to make assemblies lighter while also meeting efficiency requirements.
Lighter materials use less energy to handle and transport to final customers. Lighter vehicles consume less fuel, increasing mileage per gallon for traditional vehicles, and exteend the range for electric vehicles. The engineering practice of redesigning parts and assemblies for reduced weight and increased efficiency is known as lightweighting; the topic is popular enough to have entire trade journals and conferences are devoted to it.
The practice of lightweighting has a longer history in high performance applications like racing and aerospace, but the advantages of the practice and the increased use of fabrication techniques like 3D printing opens up use cases for more accessible consumer products like cars, bicycles, and even shoes.
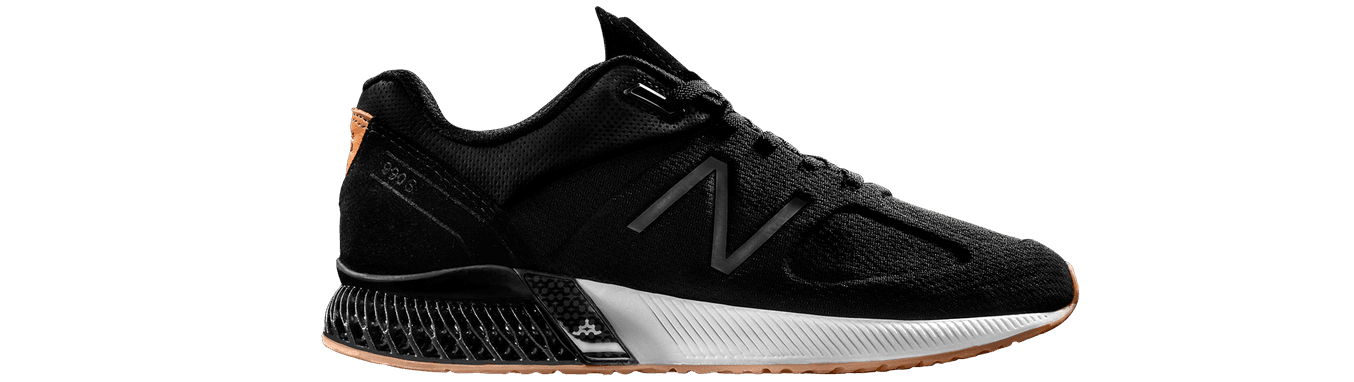
While changes in part design can provide gains in structural efficiency for weight reduction, the actual methods for joining individual parts together is another area to look for opportunities for lightweighting. Advances in structural adhesives along with more efficient mechanical fasteners like self-clinching rivets and multi-functional molded parts have helped product engineering teams build robust assemblies even while cutting weight.
The automotive industry has been steadily replacing metal parts with lighter plastic components for decades. Plastic parts reduce overall vehicle weight and improve fuel efficiency, and when assemblies can be replaced with individual parts, weight is cut further by avoiding the use of mechanical fasteners.
3D printing can also be highly energy-efficient for producing lightweight parts in small and medium volumes that would typically be machined but require significant material removal to arrive at net geometry and low part weight.
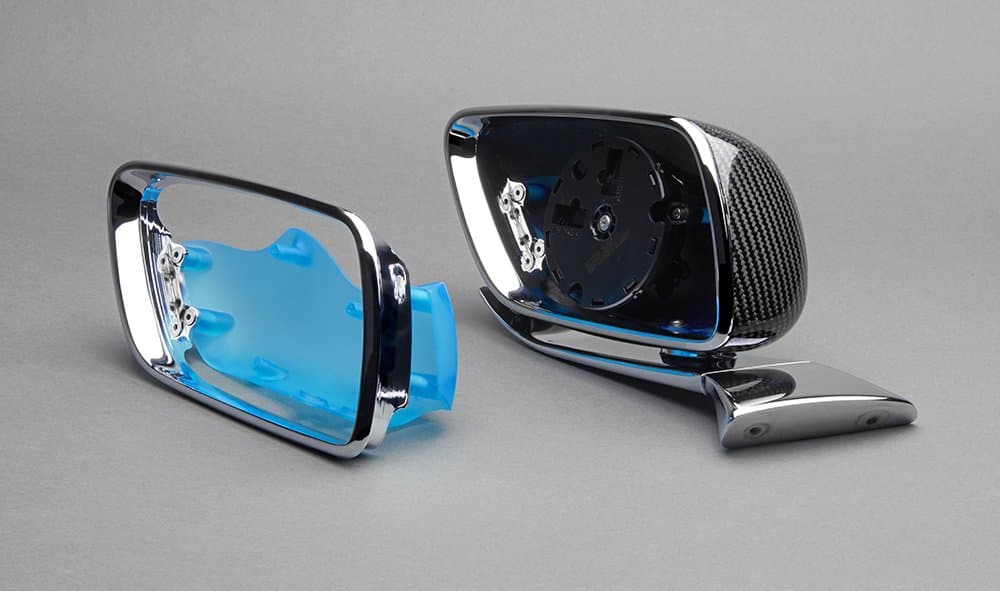
Labor, Automation, and Speed
Labor costs continue to rise globally, and assembly process steps are often a significant contributor to the labor cost involved in manufacturing a final product.
Reducing labor while maintaining or increasing throughput requires a multi-pronged approach leveraging automation, improved organizational practices, and customized tools to meet the needs of the job at hand.
Most modernizing efforts in manufacturing and assembly processes involve some degree of automation, typically via the use of robotics. While advances in robotic capabilities and decreased cost makes them appealing for a growing range of manufacturing applications, many assembly processes still require the deftness and flexibility of human hands.
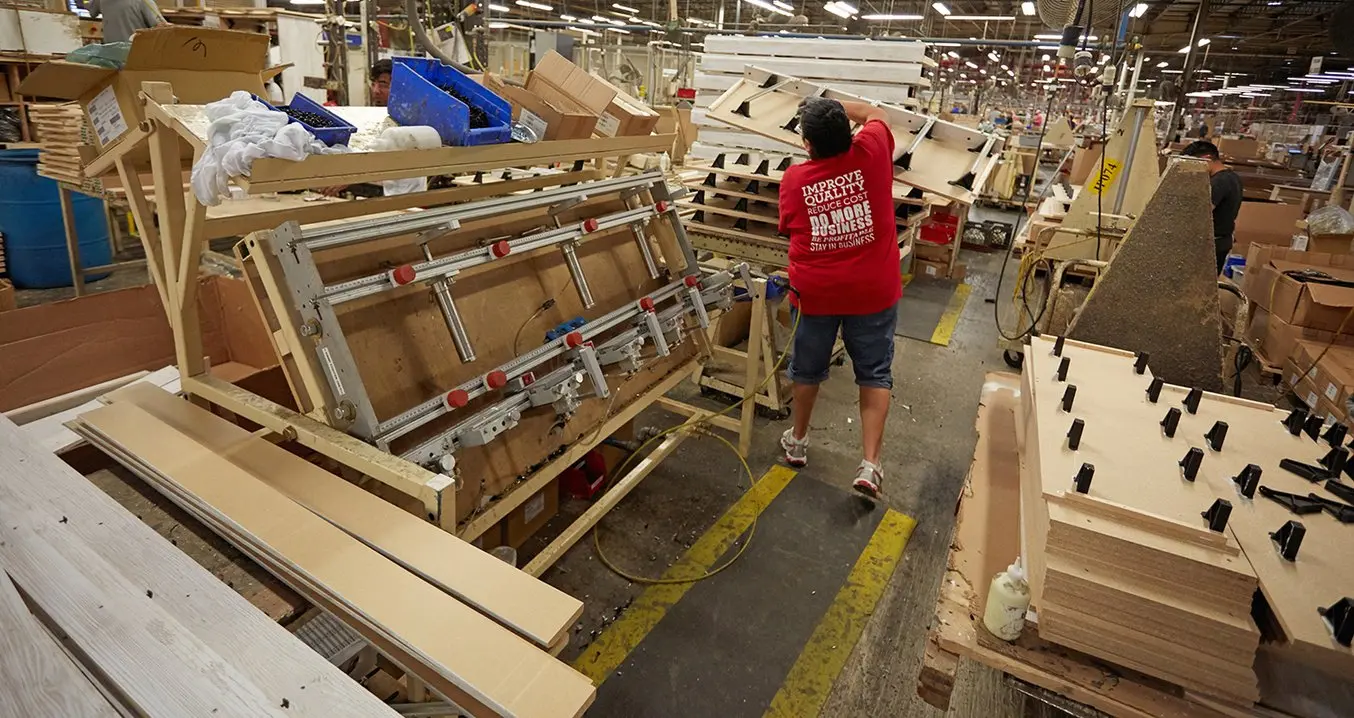
Manufacturers that perform assembly tasks have used auto-feeding systems for fasteners and torque-limited screwdrivers for decades, but true customization of assembly tools helps hone processes specific to a given manufacturer or product line, further optimizing cycle times and maintaining high quality. 3D printing makes such customization more accessible and cost-effective.
The use of customized toolheads or adapters improves the speed of fastener dispensing, repeatability of fastener location, and ultimately, the predictable look, feel, and function of a fully assembled product.
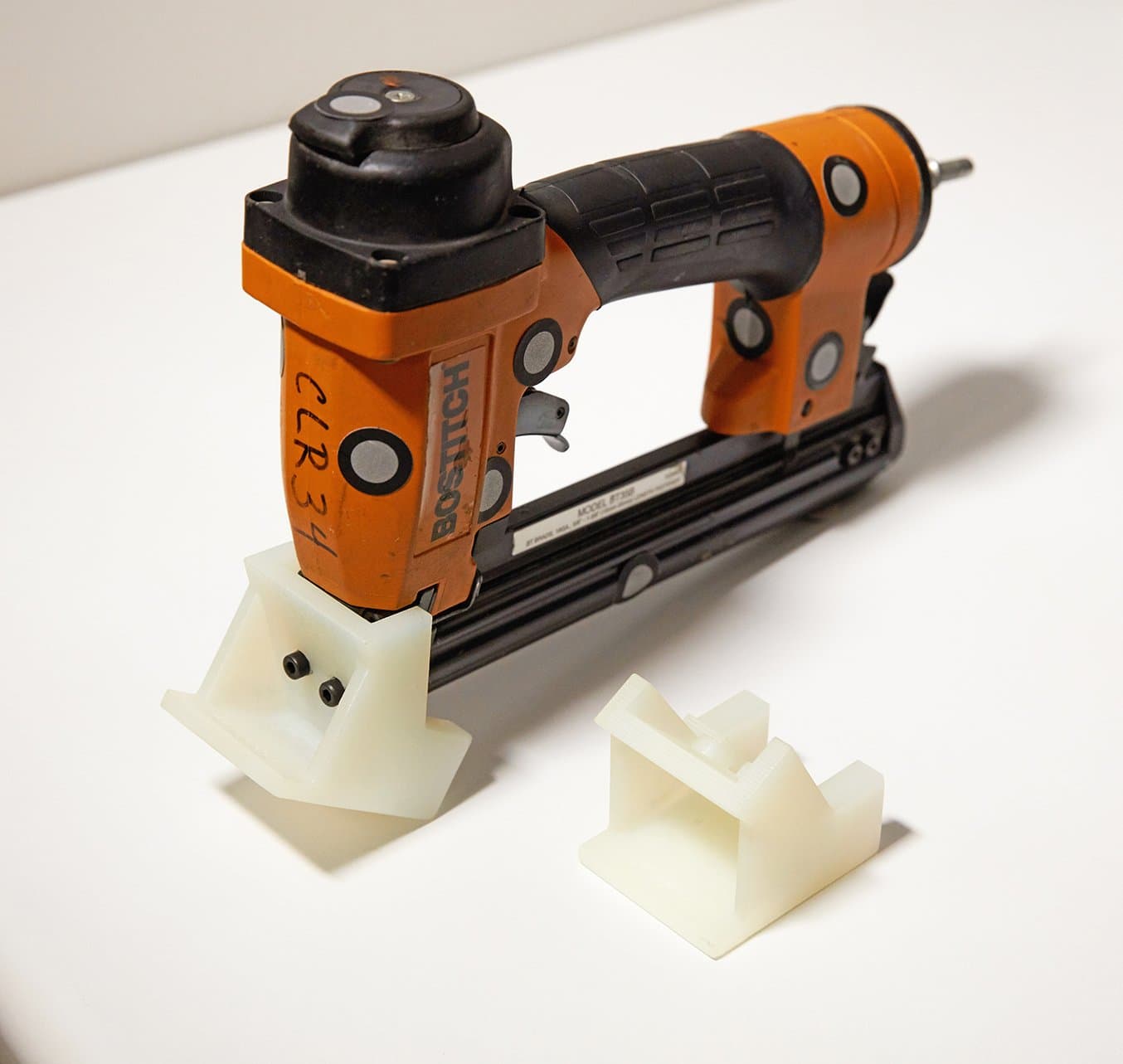
Part Consolidation and Digital Assembly
Increasingly, companies are thinking about how they can consolidate parts and reduce the use of mechanical fasteners to decrease manufacturing time, product weight, and assembly time.
Investment casting has the ability to create complex geometries with undercuts and pass throughs. It has long been used to consolidate multiple parts of an assembly into a single, unified part, and the rise of 3D printing and topology optimization software are making the process even more powerful.
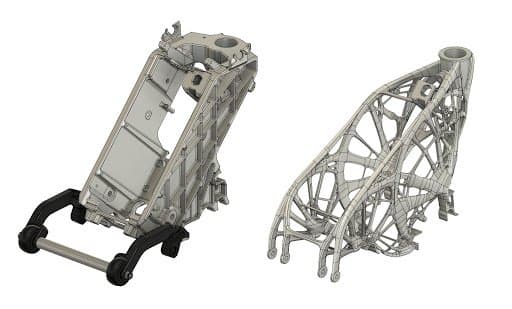
Learn More About 3D Printing
Today’s manufacturing and assembly needs are more complicated than ever before. For businesses to meet customer and application demands, engineers must be aware of and ready to deploy the latest in technologies and methods for assembly.
Learn more about how manufacturers are using 3D printing to save time and money, or evaluate our materials for yourself by requesting a sample of one of Formlabs Engineering Resins.