With the release of the Fuse 1, Formlabs has expanded access to high-quality selective laser sintering (SLS) technology with an incredibly capable and low-cost machine. As part of its commitment to continuous improvement of its products, Formlabs has launched an updated 3D packing function to help you achieve production-ready parts and highly functional protoypes in-house, as efficiently as possible.
In SLS printing, the best way to achieve high throughput and use material efficiently is to fill as much of each build volume as possible with printed parts. This is a concept known as packing density, and a higher packing density means less leftover powder with each print and a lower cost per part. Usually, achieving a high packing density requires hours of manual work fitting parts together in print preparation software, or the usage of expensive software tools which automate this process.
Formlabs is committed to continuous improvement of its products through software, and as part of this commitment, the free PreForm 3.20.0 update includes a completely redesigned 3D packing algorithm built to achieve the highest packing density possible on the Fuse 1.
Reducing Print Costs and Manual Preparation Time
PreForm’s new 3D packing algorithm has been in use by Formlabs’ internal teams for about a month before it launched, and we estimate it collectively reduced the cost of prints run during this time by 29%. The algorithm was developed and tested against thousands of print jobs in simulated prints as well, and proved competitive with the leading 3D packing software solutions on the market.
Here are some example builds that showcase the value of optimized 3D packing in different scenarios:
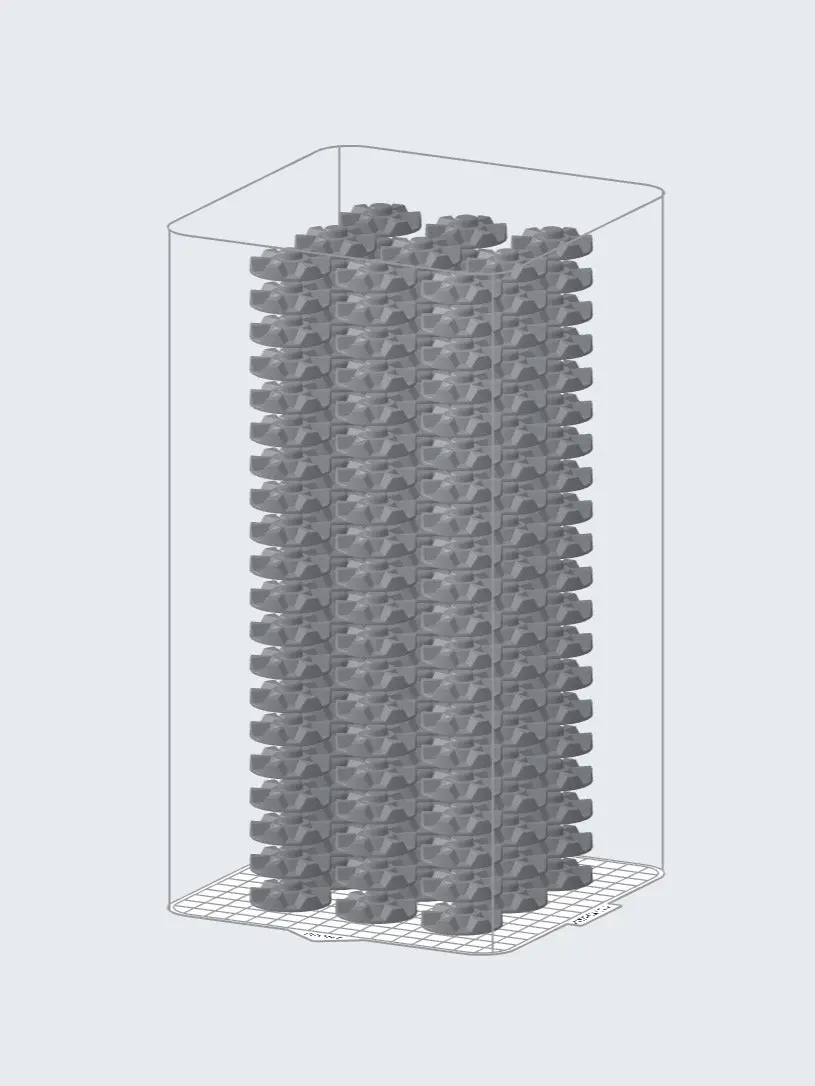
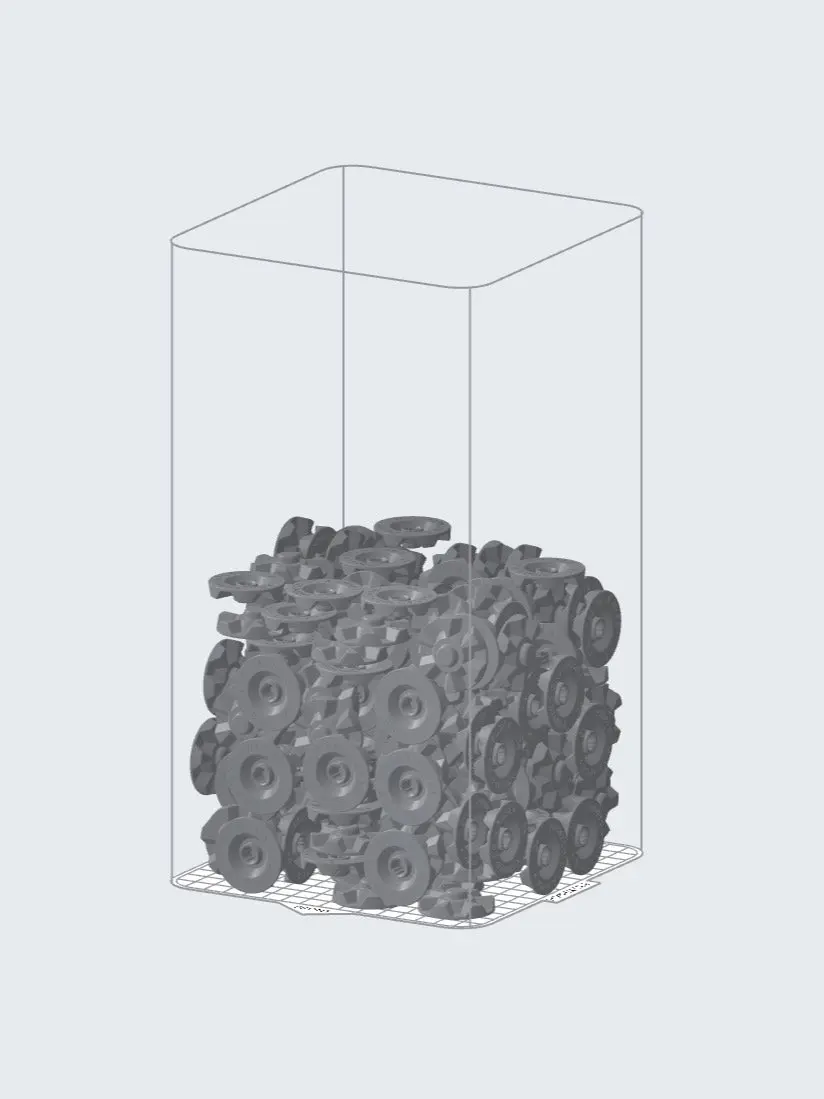
Form Cure Turntable Coupling
108 arrayed Form Cure turntable couplings, which highlights the value of packing for a production scenario.
Print time before: 32h 14m
Density before: 13%
Print time after: 26h 35m
Density after: 24%
Materials saving: 5.07kg - 2.73kg = 2.34kg (46%)
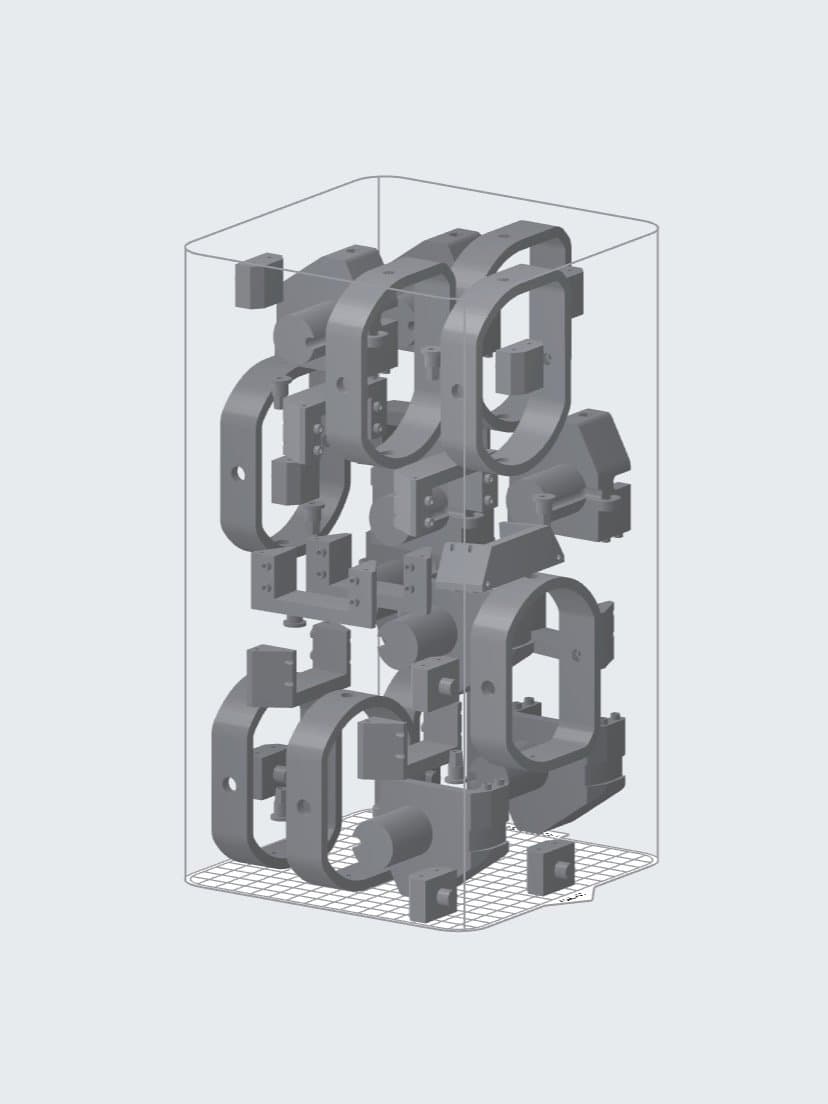
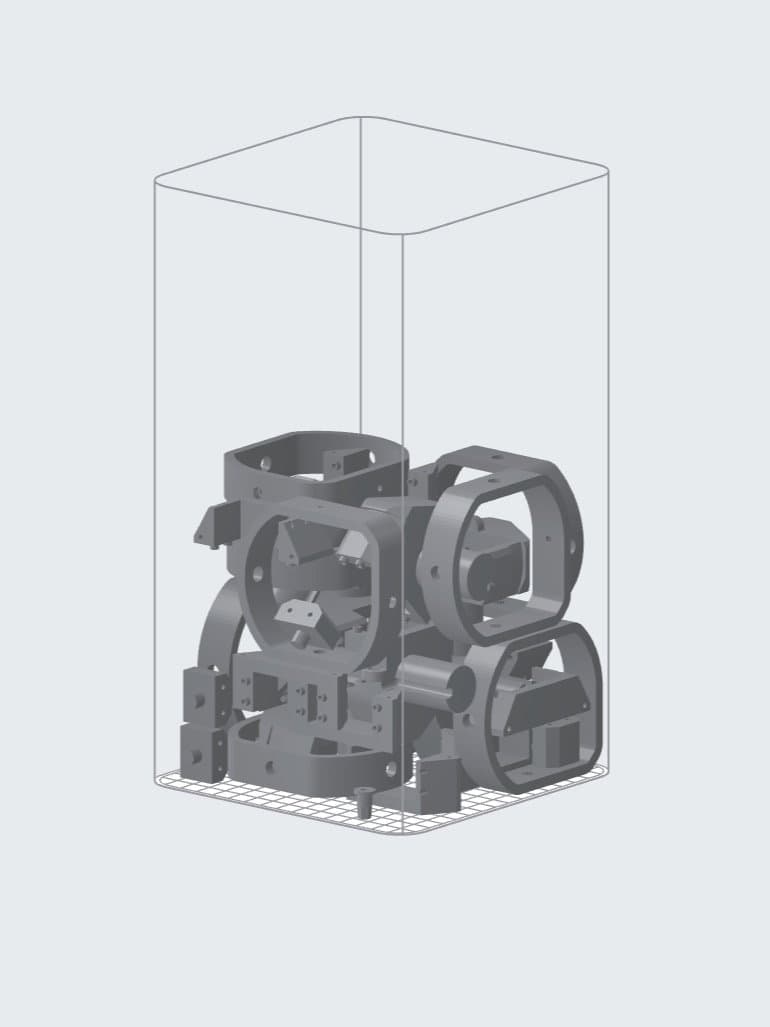
Spotlight Control Assemblies
Assembly for an internal project, which showcases a use case where packing can quickly get an optimal layout to save time without any effort needed.
Print time before: 33h 34m
Density before: 17%
Print time after: 24h 12m
Density after: 29%
Materials saving: 5.30kg - 3.05kg = 2.25kg (42%)
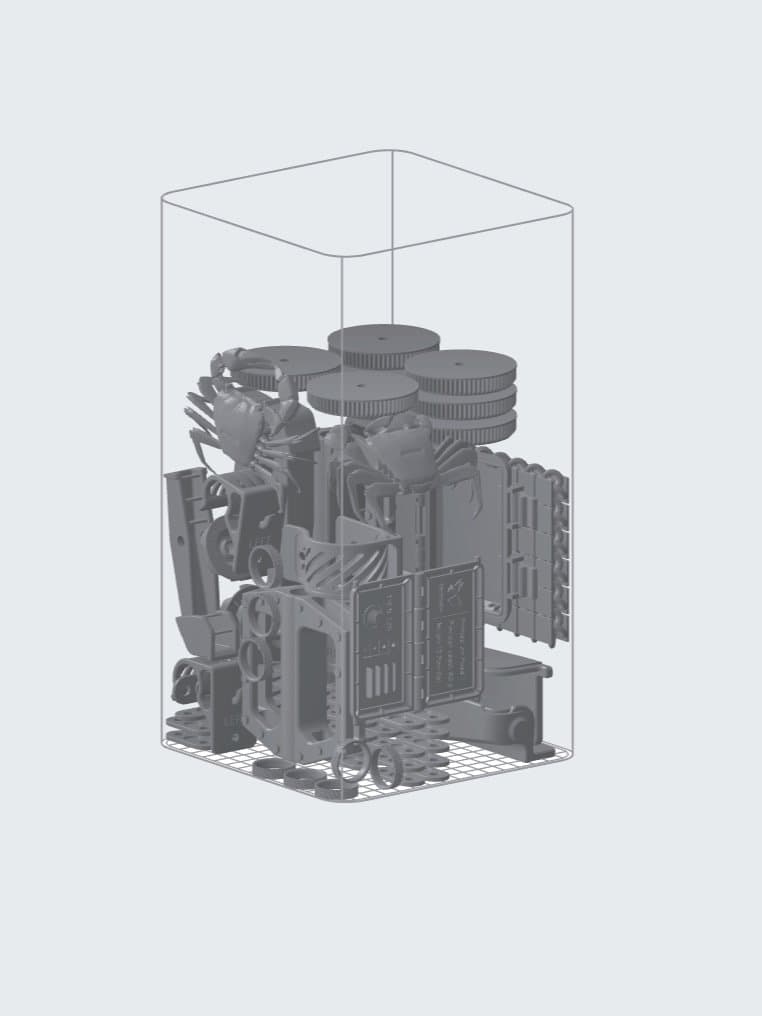
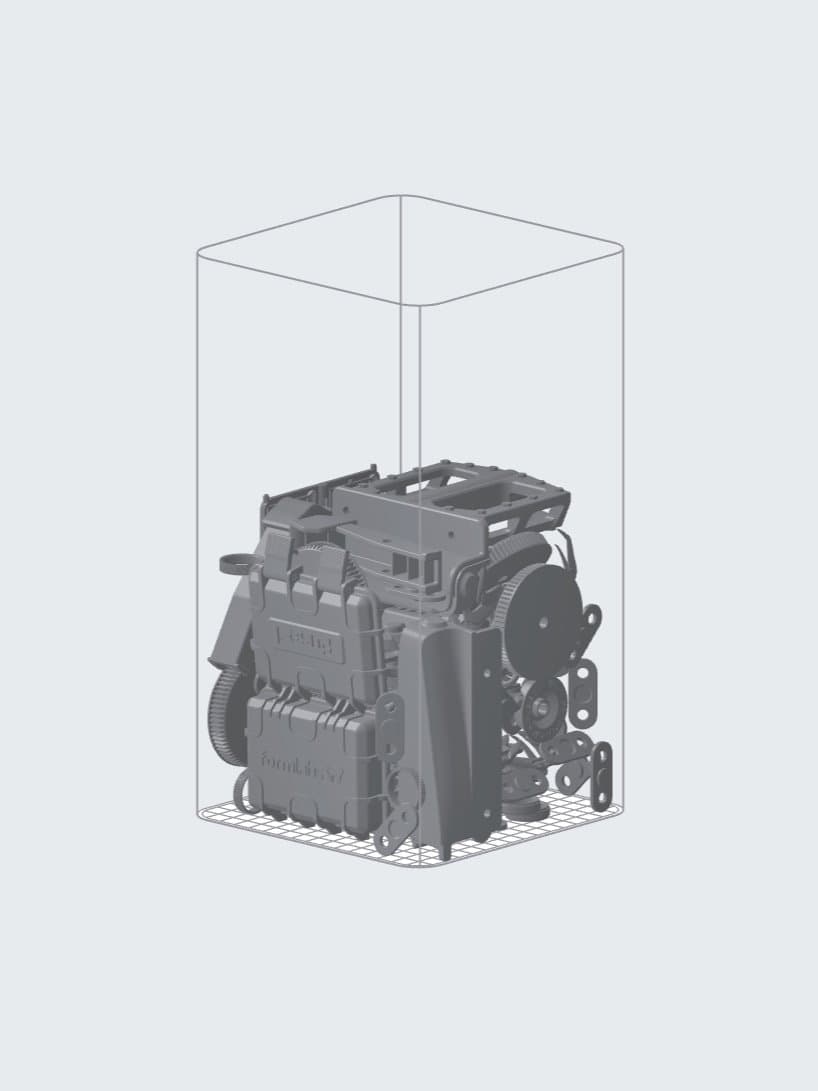
Engineering Parts and Assorted Test Models
Batch of engineering parts and assorted test models to print for various internal clients.
Manual setup time: ~30m
Print time before: 31h 41m
Density before: 19%
Packing time: 50s
Print time after: 28h 7m
Density after: 24%
Materials saving: 4.11kg - 3.23kg = 0.88kg (21%)
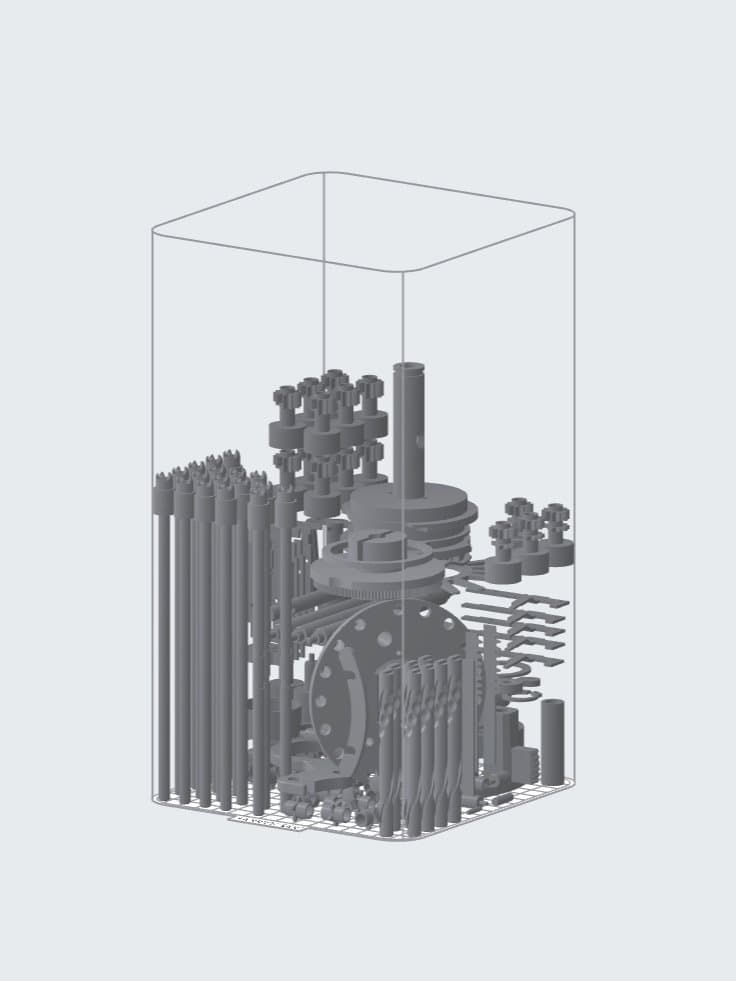
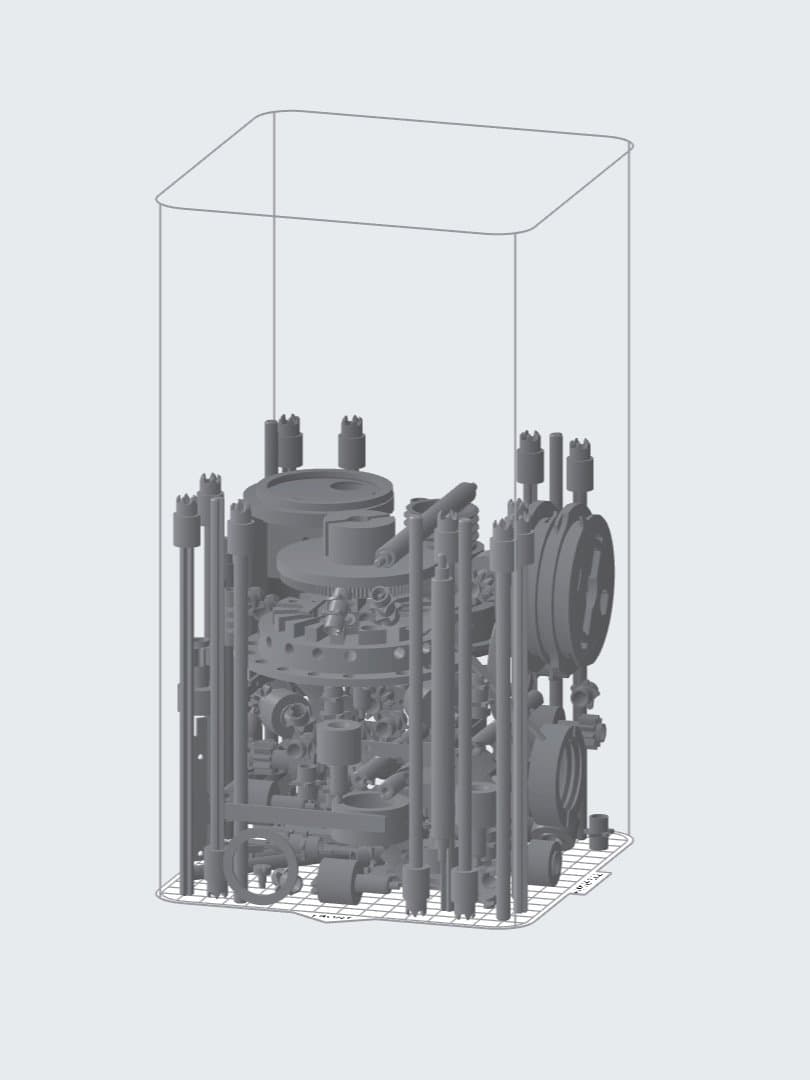
Curta Mechanical Calculator Assembly
138 components of a mechanical calculator, manually packed before packing improvement.
Manual layout time: ~2h
Print time before: 28h 56m
Density before: 16%
Packing time: 55s
Print time after: 26h 34m
Density after: 20%
Materials saving: 3.94kg - 3.17kg = 0.77kg (20%)
In internal usage, the new packing algorithm has also reduced the average preparation time for Fuse 1 jobs by 73% and saved our Berlin print farm three hours of working time each day.
When setting up print jobs, you can either give the packing algorithm full control of model orientations, or lock orientations of models before packing. The feature also gives the option to pack only specific models while keeping others locked in place.
Try the New 3D Packing Function Now
Download PreForm 3.20.0 today to try these updates for yourself and see how our updated packing function can help you maximize your SLS production, and contact our sales team to see how Fuse 1 can fulfill your in-house printing needs.