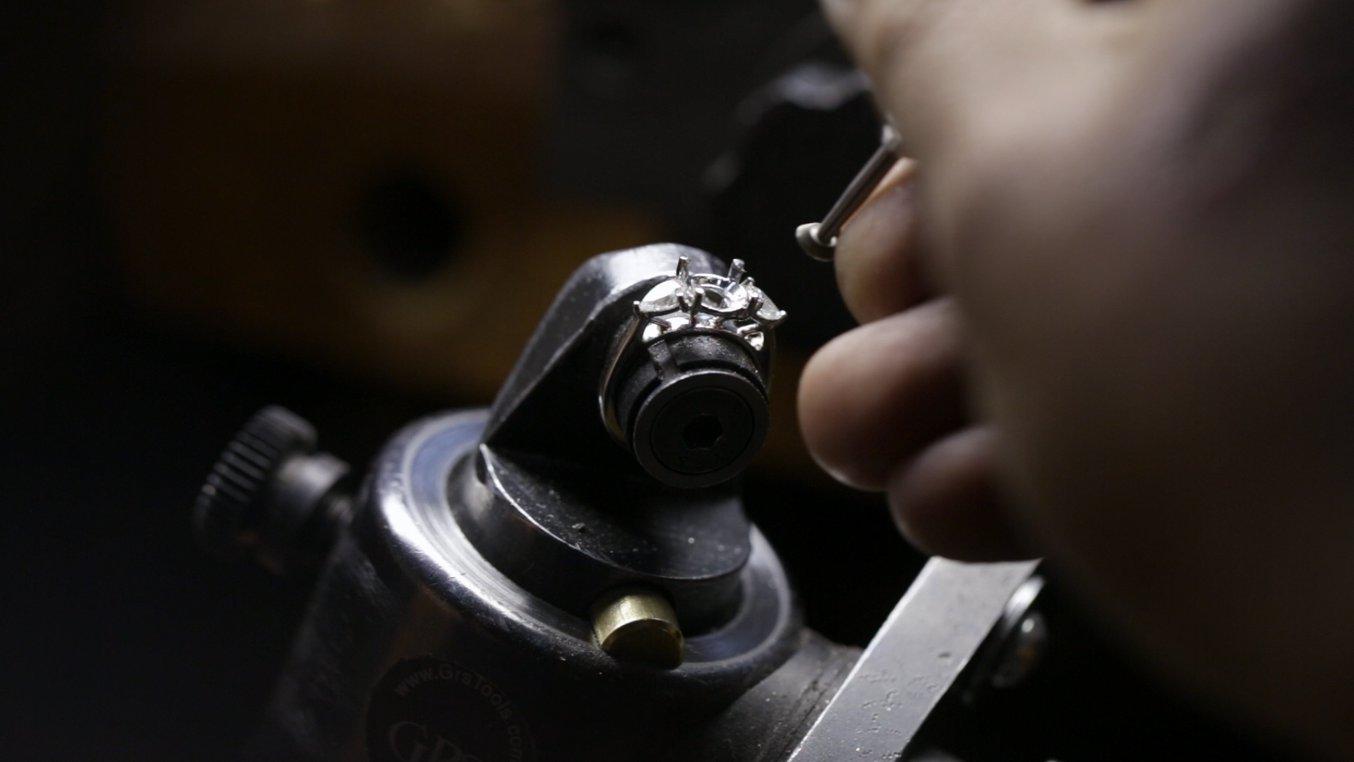
“I was really pleasantly surprised about Formlabs resin performance when it comes to casting. It burnt out very well.” – Jacob Yoon, Golden Century Casting
A bench jeweler joins rings printed on the Form 2 to a wax casting tree.
Not every family business adapts to new technology. Unlike the typical family-owned casting house, Golden Century Casting uses modern technology to make its tried-and-true services even better. For over 30 years, Golden Century has offered a full range of jewelry production services, including CAD design, casting, finishing, and setting. They specialize in fine custom jewelry for clients ranging from independent retailers to private designer labels and international brands.

When General Manager Jacob Yoon and his team first began to cast 3D printed rings, they had mixed results. “Casting photopolymer resin was definitely a monkey wrench that was thrown into the manufacturing process.” For fine jewelry, it’s essential to find materials that completely leave the mold during burnout. Because some photopolymers often fail to work as claimed, Jacob didn’t have high expectations for Formlabs resin. However, he says, “I was really pleasantly surprised about Formlabs resin performance when it comes to casting. It burnt out very well.”

Beyond producing professional results, working with Formlabs resin expands the number of clients that casting houses like Golden Century can serve. Jacob says, “Technology has forever changed this industry. I would say 99% of the stuff we create now has been 3D printed.” Now, jewelry designers working with Golden Century can produce their own castable designs on Formlabs 3D printers and send them in for casting, gem setting, and finishing.

With throughput of over 50 rings every 10 hours, the Form 2 brings a new level of automation and efficiency to the jewelry manufacturing industry. Jacob explains, “The advantage of using 3D printers for jewelry manufacturing is that when you design something, you press print and have it the next day.” The benefits include not only speed and quantity, but also quality. He says that with traditional wax modeling, “you can never make the right side of a shank look exactly like the left side of the shank by hand.” Whether for one piece or a run of a thousand, 3D printing brings detail and consistency to a new generation of jewelers.