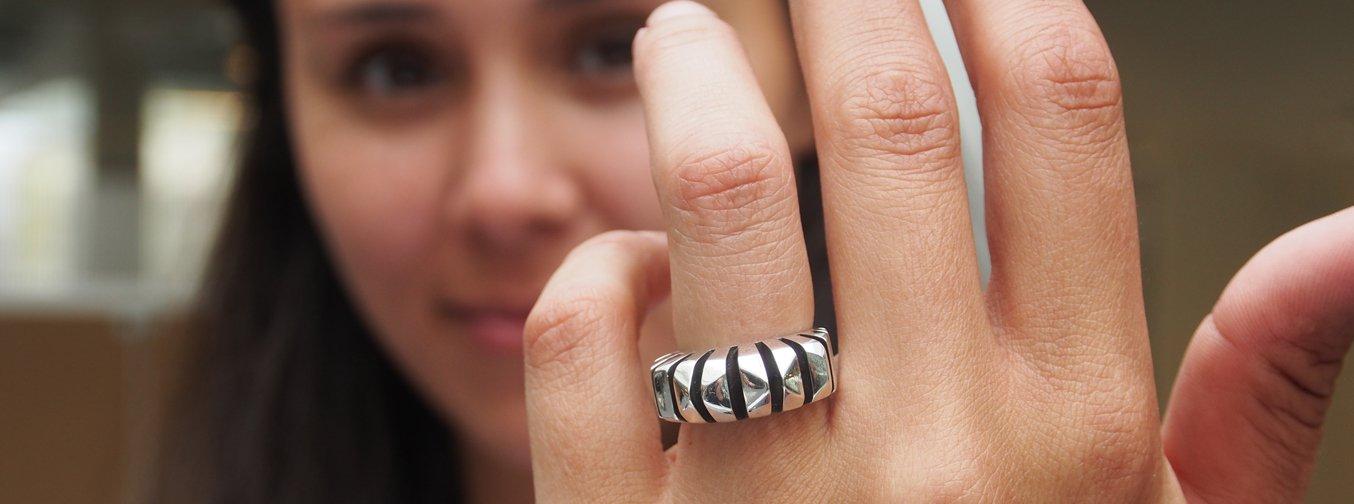
Jewelry is a traditional craft, passed from master to apprentice over hundreds of years. With the emergence of digital technologies, the industry is going through a rapid transformation. Where do tomorrow’s jewelry designers learn their craft today?
Lars Sögaard Nielsen, a goldsmith by trade, is one of the teachers who run the Jewelry, Technology, and Business program for undergraduates at Copenhagen School of Design and Technology (KEA) in Denmark. The course covers all the steps of modern jewelry design and manufacturing, from CAD design to 3D printing, moldmaking, and casting.
Using digital tools in addition to traditional techniques, the program’s students stay above the curve in the industry and learn how to ultimately grow their business.
Designing a Jewelry Education Program from the Ground Up
Nielsen comes from a traditional jewelry background but has long seen the value in digitizing the industry. He joined the Jewelry, Technology, and Business program to teach aspiring jewelers how to work digitally, learning tools that will be essential for growing and scaling their businesses later on.
“Experience with digital technologies is a big advantage today. When you see job offers, and you mention that you know how to work in 3D modeling and 3D printing, you are in a much better position than the person without this knowledge,” Nielsen says.
KEA’s curriculum is now in its fifth year and evolves continuously. Students first learn 3D modeling with Rhino software, then how to produce ready-to-cast pieces using 3D printing. They get hands-on experience with casting and moldmaking to manufacture jewelry. Finally, they master the craft of finishing and polishing jewelry.
Nielsen found significant differences between teaching traditional jewelry work using wax compared with digital tools. The traditional process of making pieces by hand can take several days. Time is limited in a classroom setting, and this would shorten students’ exposure to learning new processes and adapting to changes in the design.
With digital design, students can create a design in CAD and have a 3D printed piece in hours ready for same-day casting. Then, the students can look at the finished pieces and easily iterate on their designs. “The time savings are incredible,” Nielsen says.
Choosing the Right Tools for Jewelry
Nielsen wanted to pick the tools that he knew his students could use once they graduate.
“I had access to a small DLP 3D printer, but that was a battle in itself: it comes with small cartridges, and the build platform is really small, not to mention the castable resin made lousy prints. I’ve also used professional wax 3D printers, which would produce very good prints, but required fixing and calibrating all the time, and come with exorbitant costs. When you’re starting a company, you do not have tens of thousands of Euros to buy a printer. Nobody has,” Nielsen says.
He learned about Formlabs’ Form 2 stereolithography (SLA) 3D printer after a fellow goldsmith in Copenhagen recommended it for casting, and ultimately he chose it for the new jewelry program for its combination of ease of use, quality, and affordable price.
“When you have a 3D printer on your desk, you can really test things out,” Nielsen says. “It has become much easier to teach about 3D printing as the technology is getting easier to use, and the Form 2 is a great example of this. The more the students put into learning the technology, and the more they embrace making mistakes, the more they get out of it in the end.”
Formlabs collaborated with Nielsen and KEA to document the optimal casting process for 3D printed jewelry. Download the Recommended Burnout Process and Casting Guide to learn more.
The Program’s Crown Jewel
Madeleine Le Kruse Madsen and Astrid Ann Landt are third-year students of the Jewelry, Technology, and Business program. In the last semester, their main project was taking all they’ve learned and applying it in practice. As part of the course, they set up a company, designed a collection, prototyped and produced jewelry pieces using digital tools and investment casting, then sold the pieces to customers.
The theme of the project was Jewelry for Change: creating a collection that would change something for the wearer. The project began with interviewing women aged between 45-65. The students learned that there could be pressure from society to be young and cool, and to look attractive in comparison with young mothers. Madsen interpreted this into a hypothesis for a collection that talks positively about the natural changes in life. To confirm her hypothesis, she made pro kits, which are similar to focus groups, where she would ask users questions to learn about the type of jewelry and the shapes and geometries that would most appeal to this customer group.

After Madsen confirmed her hypothesis, she began prototyping models, 3D printed them in Black Resin, and spray painted them to mimic a silver piece. She used these prototypes to collect feedback from customers who tried on multiple versions of the pieces before she was able to get the best result. The final models were then printed with Castable Resin and cast into gold and silver. Their business plan included everything needed to start a business, from developing a business model to packaging and branding. The project lasted three months, and they came out with sizable revenues of €13,000.

The students highlighted the benefits of a digital workflow for jewelers.
“It was easy for me to learn to draw in 3D. The things that we’ve made for this project, I could have never done by hand. I think the possibilities of creating something unique and more advanced is so much greater when we can design and 3D print,” Madsen says. “Learning how to make jewelry digitally gives you a different toolset to choose from. It looks great on your job application and is an advantage you have when working with jewelry manufacturers. For example, if they want someone who understands the digital process and can communicate this to manufacturers in India, we would be equipped to do so.”
“We chose KEA because the program combines theory with practice. We learned not only how to draw in CAD, print, and cast, but how to think like an entrepreneur and put these learnings to use. It was a surprise, but we were even profitable with our Jewelry for Change project! So we essentially set up a business within our education,” says Madsen.
The Future of Jewelry Education
Nielsen believes that in the jewelry industry, digital technology, and traditional craft can coexist in harmony, supplementing each other.
“Some people say that 3D printing is replacing the art of a goldsmith’s work, but what I would say back to them is that if I can offer students a tool to help them realize their ideas, then I will give them that chance to learn it. If I can get a better hammer, I will get it. It’s not replacing your craft as a goldsmith, who still needs to understand casting, stone setting, and finishing. It’s a tool that brings you further,” says Nielsen.
Find out more about digital modeling and 3D printing and get familiar with the basics of digitally designing jewelry for best results in both printing and casting from our white paper.