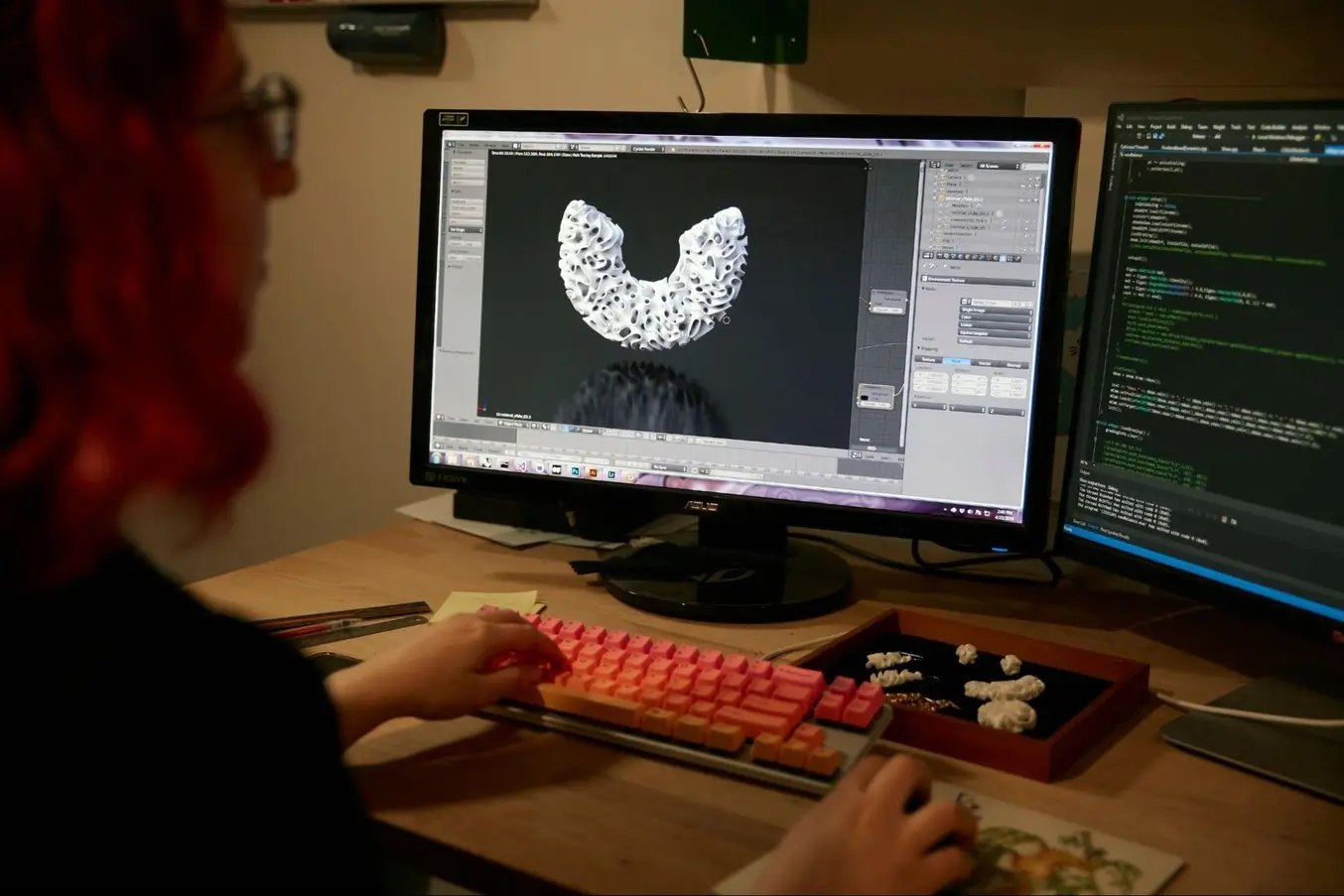
Digital design processes supported by CAD software have transformed the jewelry industry and taken their definite place in the jewelry designers’ workflow. Together with 3D printing, these digital technologies enable unlimited creative possibilities and customization.
From general CAD tools to proprietary jewelry design software, there are now dozens of viable alternatives, each with its own pros and cons, modeling approaches, and niche uses. Let’s take a look at the offerings so that you can make the right choice in selecting a virtual jewelry design environment that might stay with you for an entire career.
Introduction to Digital Jewelry
Jewelry design has traditionally involved a deep sense of craftsmanship and understanding of processes such as wax sculpting, soldering, bending, weaving, and stone setting, but in this age of digital transformation things have been changing. Designs can be fully prepared using modern computer-aided design (CAD) systems and converted to physical models by 3D printers for rapid prototypes, try-on models, and investment casting.
While manual artisanship will still be required for multi-material techniques involving inlays, drusy, or mokumé gané, coloring effects such as sgraffito, selective oxidation, multicolor anodizing, and champlevé enameling, or cloisonné with wires as thin as a quarter of a millimeter, digital jewelry design and 3D printing champions sharp and intricate designs with limitless geometrical possibilities such as filigree meshes, interlocking parts, mechanical joints, and complex mathematical shapes.

Digital jewelry designs can be 3D printed and directly cast.
Instant 3D previews and same-day fitting models help place the customer in the driver’s seat, which shortens development times for custom jewelry and increases customer satisfaction. Customization enables serving niche markets, which has resulted in an explosion of online jewelry brands, while jewelers can gain self-sufficiency by learning how to design for in-house manufacturing.
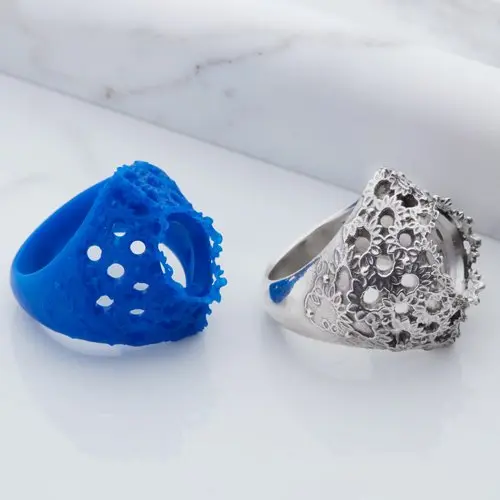
Introduction to Casting for 3D Printed Jewelry Patterns
In this white paper, learn how to cast fine jewelry pieces from 3D printed patterns and how direct investment casting, or lost wax casting, works as a moldmaking technique.
Types of Jewelry Designer (CAD) Software
A jewelry designer who has decided to jump onto the digital bandwagon has a plethora of choices when it comes to assistive jewelry CAD software. Dictating factors will be the accessibility of the user interface and suitability to the design genre. There are free entry-level solutions such as Tinkercad, CAD environments specifically dedicated to jewelry design such as 3Design and Firestorm, as well as all-purpose modelers such as SolidWorks, Rhinoceros, and Fusion 360 that are geared to a wide range of design work including jewelry.
A major benefit of solid modelers is that designs are fully parametric and all modeling operations are stored in a history tree. In constraint-based modeling, all features are determined by dimensioned sketches, leaving the entire design modifiable without having to remodel any major parts. Additionally, it will automatically update the entire geometry in case different base sizes or product variants are required. Other perks of these systems are their integration with renderers like Keyshot, and 3D print preparation software such as PreForm. The main disadvantage with using solid modelers for jewelry design is that models tend to come out too geometrical, lacking the smooth surface transitions and details that can uplift jewelry design to the next level.
For that reason, the preferred CAD software solutions for creating organic jewelry designs are polygonal modelers. Rather than a set of mathematically constructed solids and surfaces, geometry is stored like a mesh consisting of vertices, edges, and faces. These can be individually manipulated using low-level commands or high-level modifiers that globally affect the object. Mesh modelers like Maya and Modo offer limitless potential for designing organic shapes, while Blender and ZBrush add advanced sculpting capabilities.
A jewelry designer will encounter less steep of a learning curve with industry-specific solutions such as 3Design, Firestorm, and JCD. While a wizard-like user interface can impede the construction of truly custom geometry, they allow the designer to focus less on the technical and more on the creative aspect, while still leaving a vast design territory to explore. Being dedicated to the creation of all types of rings, bracelets, earrings, pendants, or colliers, they include options for automatic gemstone insertion as well as advanced duplication patterning, crown and prong settings, 3D texturing, scoop hollowing, multipipe torsades, embossings, and other special effects characteristic to great jewelry design. This dramatically speeds up the workflow leaving the software ideal for creators who like to work directly with the end customer.
The benefits of CAD integration across the jewelry development process are:
-
Rapid concept development: Envisioned designs can be accurately sketched for early visualization and 3D printed try-out models before casting.
-
Visualization: Impress clients and customers with cutting-edge 3D renderings, animations, and virtual reality experiences of works-in-progress. Photorealistic engines empower designers to optimize their compositions by simulating refraction, aberration, chatoyancy, interreflection, and other effects between precious metals and gems.
-
Geometrical freedom: Complex shapes, textures, and patterns are possible that could only be dreamt of when using traditional techniques.
-
Product customization: Models can be adapted to create variants for niche markets or individual customers.
- Rapid manufacturing: Products can be brought to production faster using in-house digital manufacturing technologies like 3D printing that eliminate the need for manual mold making. Master models can be reprinted preventing the loss of detail across production runs.
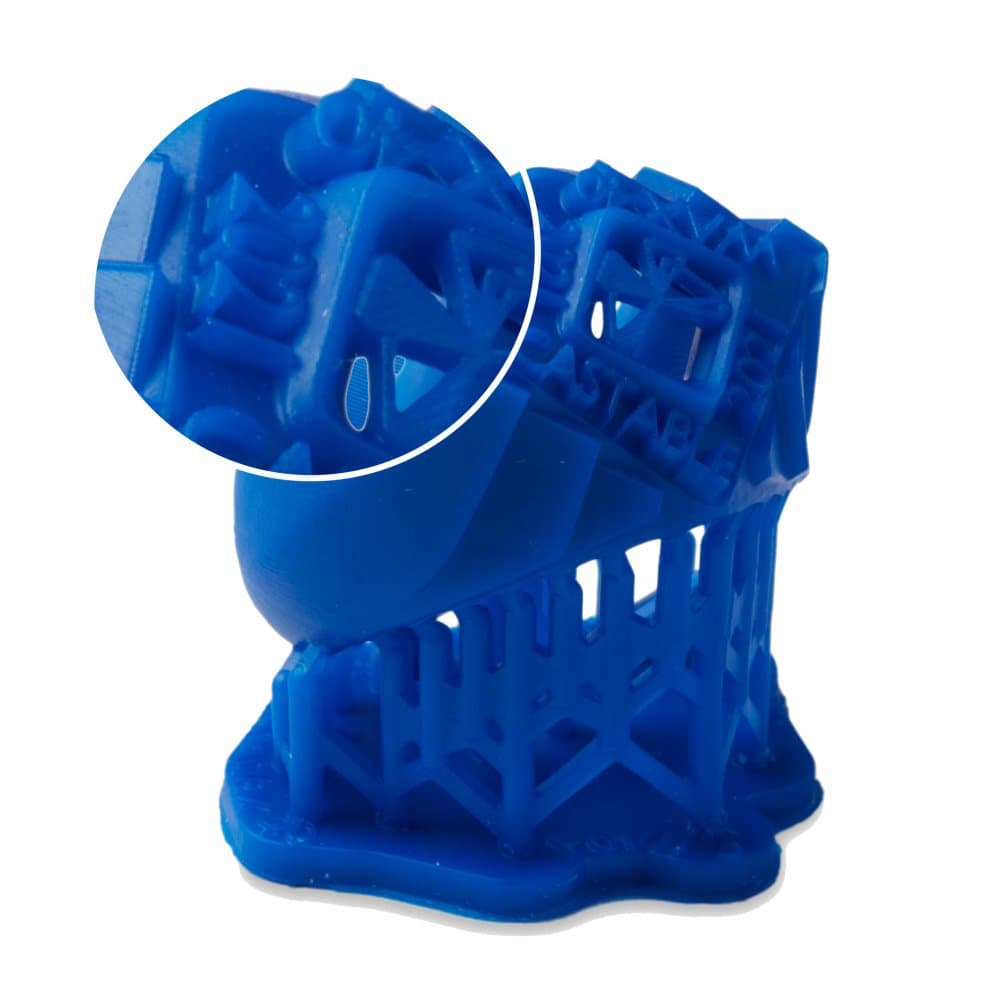
Request a Free 3D Printed Sample Part
Curious to see 3D printed jewelry patterns firsthand? Click here and we'll ship you a free jewelry sample part printed on our 3D printer.
Choosing the Best Jewelry Design Software
The prime factors in choosing the right 3D jewelry design software environment are the fit to the intended geometry, richness in jewelry-specific features, scale-up and customization possibilities, ease-of-use, and budget.
Starting with the suitability to create specific product geometry, solid or surface modelers like SolidWorks and Rhinoceros are great at geometric shapes and smooth, tightly controlled surfaces. They will let the designer numerically define all feature dimensions. Polygonal or mesh modelers offer some parametric control but mostly allow the designer to directly manipulate shapes, which can streamline the workflow towards organic designs. They are generally less precise and intuitive, and sometimes sloppier modeling can result in just the necessary level of imperfection to give jewelry a more authentic character. For artistic models involving realistic ornaments of plants, portraits, animals, and the like, freeform sculpting environments are often the best choice. Some CAD environments offer a hybrid between these different approaches. For example, ZBrush will allow for the most intricately decorated designs while being able to incorporate gem settings. When complex pavé, basket, or halo gem settings are required, 3Design will perform better. Rhino’s Grasshopper plug-in allows for mathematically or biologically inspired shapes and patterns unachievable in any other environment.
Since entering a digital workflow can be a massive transition for jewelers, a short learning curve and efficient modeling workflow will be of chief importance. In companies requiring high throughput, working with mesh modelers can become tedious unless there are intuitive sculpting features and wizards to guide the user rapidly from scratch towards the first 3D print. Whereas some CAD programs empower the designer to automatically layout gems along curves, Rhinoceros and 3Design expand that capability with the option to gem-encrust three-dimensional surfaces. These are key features that can save hours of manual modeling work.
The last main selection criterion is price, and since upper-tier propositions like 3Design, Firestorm, JCD, and Maya cost thousands of dollars, it is worth considering low-budget solutions. TinkerCAD is free and only allows working with primitive shapes, yet it is an opportunity to start with digital jewelry design. Wax models can be created from exported files, and in case of lacking detail, they can be carved by hand into something spectacular. Under one thousand dollars, Rhinoceros is an affordable package that has become the jewelry industry’s standard. Depending on the individual case, more costly plug-ins such as MatrixGold and Panther can be worth the investment. Fusion 360 is free for students, startups, and non-commercial users and offers a surprisingly comprehensive set of features for building jewelry models, as well as a direct coupling to PreForm 3D print preparation software.
Our overview chart of jewelry CAD software lists each program’s feature-richness for organic and parametric modeling, its inclusion of features typical to jewelry design, the overall user experience including ease-of-use and learning curve, possibilities for creating customized parts and variations from a base model, and cost.
Organic | Parametric | Jewelry-specific | UX | Customization | Price | |
---|---|---|---|---|---|---|
3Design | ★★★☆☆ | ★★☆☆☆ | ★★★★★ | ★★★★☆ | ★★★★☆ | ★☆☆☆☆ |
Blender | ★★★★☆ | ★☆☆☆☆ | ☆☆☆☆☆ | ★☆☆☆☆ | ★☆☆☆☆ | ★★★★★ |
Firestorm | ★★☆☆☆ | ★★★☆☆ | ★★★★☆ | ★★★☆☆ | ★★★★☆ | ★☆☆☆☆ |
Fusion 360 | ★☆☆☆☆ | ★★★☆☆ | ☆☆☆☆☆ | ★★★★☆ | ★★★☆☆ | ★★★★☆ |
JCD | ★★☆☆☆ | ★★★★☆ | ★★★★★ | ★★★☆☆ | ★★★★★ | ★☆☆☆☆ |
Maya | ★★★★★ | ★☆☆☆☆ | ☆☆☆☆☆ | ★★☆☆☆ | ★☆☆☆☆ | ☆☆☆☆☆ |
Modo | ★★★★☆ | ★☆☆☆☆ | ☆☆☆☆☆ | ★★★☆☆ | ★★★☆☆ | ★★☆☆☆ |
Rhinoceros | ★★★★☆ | ★★★★☆ | ★★★☆☆ | ★★☆☆☆ | ★★★☆☆ | ★★★☆☆ |
SolidWorks | ★☆☆☆☆ | ★★★★☆ | ☆☆☆☆☆ | ★★★☆☆ | ★★★☆☆ | ☆☆☆☆☆ |
TinkerCAD | ☆☆☆☆☆ | ★☆☆☆☆ | ☆☆☆☆☆ | ★★★★★ | ☆☆☆☆☆ | ★★★★★ |
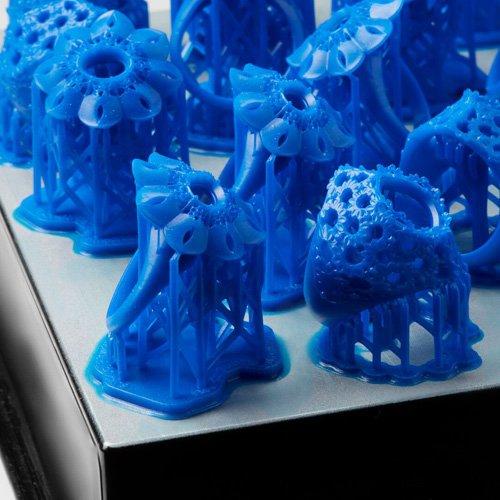
Demo Session: Casting With Castable Wax 40 Resin
Formlabs is excited to introduce Castable Wax 40 Resin, our 40% wax-filled material specifically formulated for the jewelry industry. Join Patrick Diggins, jewelry vertical manager at Formlabs, for a Castable Wax 40 Workflow Demo Session.
Jewelry CAD Software Solutions Compared
3Design
Developer: Type3
Released: Late 1990s
Platforms: Windows, macOS
Ideal for: Professional jewelers, CAD as a sales tool
Price: $6,950
3Design is a digital studio completely tailored to jewelry design. Features include custom loft profiles, twisted lofts, advanced multi-rail sweeps, multi-pipe torsades and braids, special effects, size ranges, a variety of pavé settings, drill holes, technical drawings, scoop hollowing, and sophisticated 3D texturing based on image or mesh input or the built-in texture generator. Over twenty modifiers exist to organically deform objects by means of bending, twisting, tapering, shearing, stretching, squashing, rippling, and more. Notable is the envelope deformer which allows the designer full freeform control for deformations across the entire shape. When extended with 3Shaper Pro, freedom in design is augmented with a freeform sculpting toolkit. And because 3Design is parametric, gem settings will seamlessly scale along and can be modified at any time in the process.
The user interface is embedded in the viewport for a full-screen experience. The icon-based controls are easy to learn and guide the user through the various steps of jewelry development. As the wizard-like interface works fast and is easy to learn, 3Design is the 3D jewelry design program of choice for businesses that prefer to co-design pieces together with clients. A downside of this architecture is that it can feel a bit rigid in limiting the designer’s creativity to traditional routines and shape libraries.
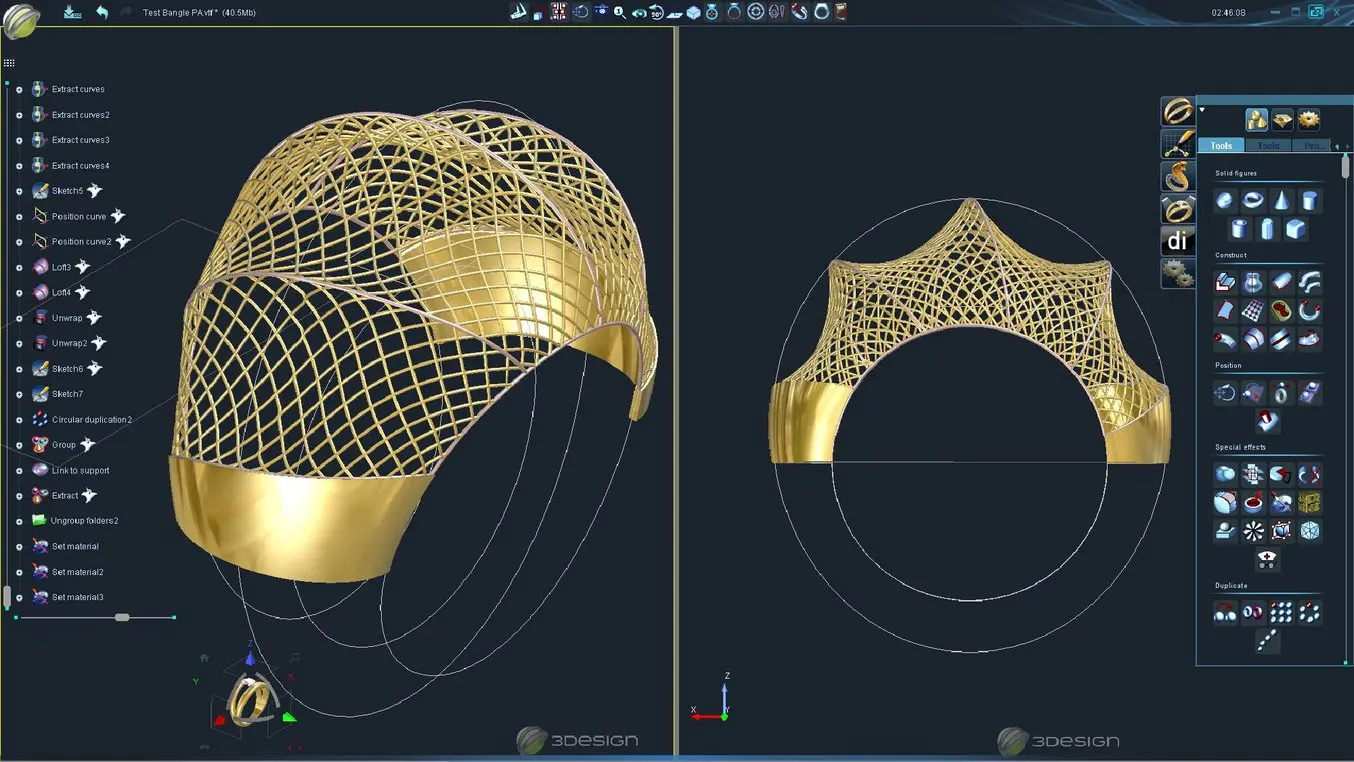
3Design is a complete jewelry CAD solution that combines parametric and direct modeling in an intuitive user interface.
Jewelry CAD Dream
Developer: Jewelry CAD CAM Masters (JCCM, LLC)
Released: 2011
Platforms: Windows
Ideal for: Professional jewelers, gemstone arrays
Price: $5,850
With one of the most powerful engines under the hood, Jewelry CAD Dream lives up to its name with a winning blend of modeling strategies optimal for jewelry creation. It offers standard solid and surface modeling tools, and lets the user edit faces, offsets, dimensions, and other features directly inside the viewport. Morphing tools can be applied for creating flowing organic shapes. Alternatively, hundreds of base models are available from the built-in library.
But most of all, JCD is the most robust parametric modeling system in the industry, and with a proprietary feature history system just about the only software that will smoothly run models with 500+ gemstones such as multi-row choker colliers or lavaliere pendants. Critical design parameters can be defined and transferred onto an input panel for end-user customization that enables designers to change the most important aspects at any time. The model will update without any glitches, even when editing complex surface curvatures that hold gemstone arrays.
There is a myriad of jewelry-specific tools and wizards for different types of pavé settings such as jelly, springs, and micro pavé as well as spherical patterns, baguette arrays, halos, azure and honeycomb cutters, prong, bezel, and wire settings, chains, pendant bails, braids, textures, pierce work, milgrain, advanced text embossing, and a ring sizer. Textures can be created by importing an image to use as relief, or importing a mesh to morph and multiply along a surface.
JCD will generate and fix 3D print files and add sprues for casting trees when required. There is a photorealistic renderer on board with 3D props available to add some glamour to the scene. And despite its feature-richness and parametric depth, the user interface remains clear and relatively easy to learn.
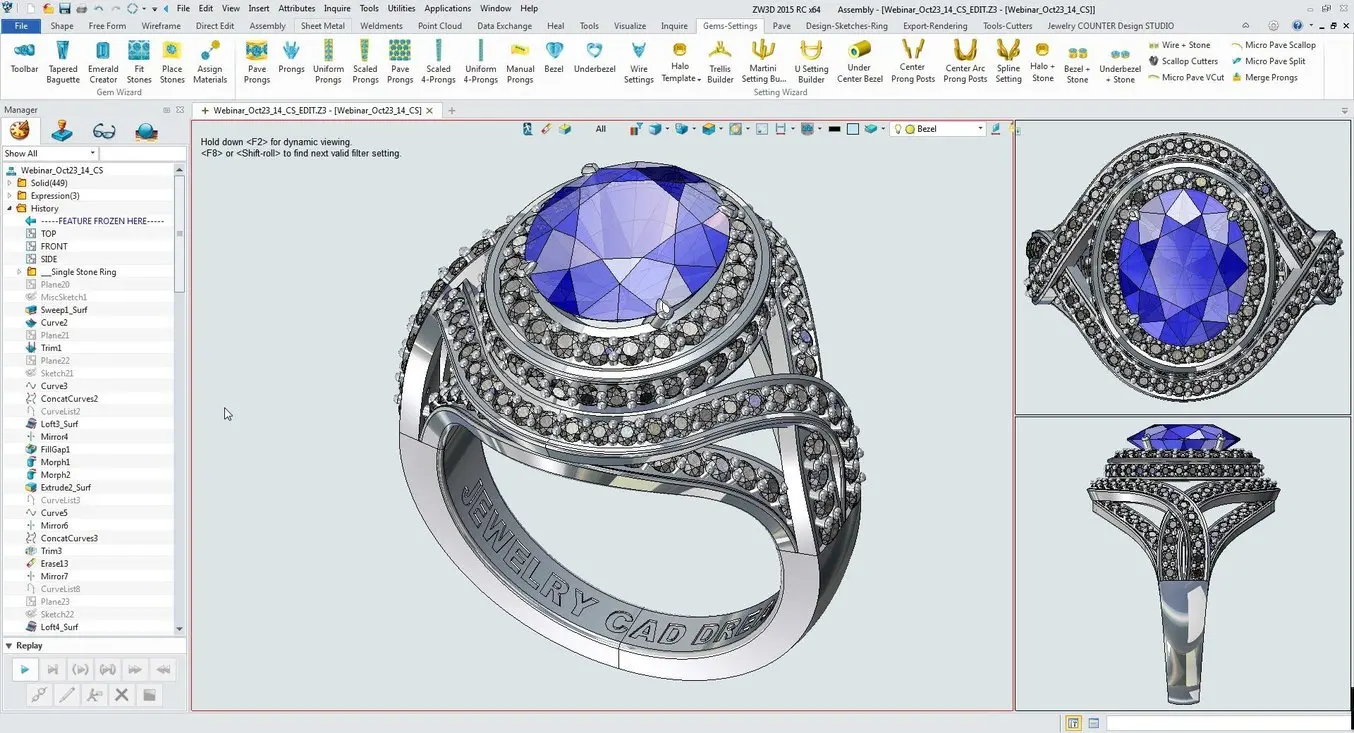
JCD is one of the most powerful and jewelry-specific modeling environments available to industry professionals.
Rhinoceros
Developer: Robert McNeel & Associates
Released: 1998
Platforms: Windows, macOS with limited features
Ideal for: Professional designers, complex geometry, computational design
Price: $995, $195 for students
Rhino3D is a freeform NURBS-based surface modeler especially suited for creating complex shapes. With a nearly endless list of features, it allows for sophisticated surface sweeping and lofting routines. For these reasons, Rhino is also used in the automotive, consumer product, and maritime industries. Since the program does not store any modeling history besides the Undo command, making modifications can be tedious and will require a serious level of professionalism on the part of the designer.
The user interface is fairly complex and difficult to learn. Those new to CAD modeling can expect to be immersed in manuals and tutorials for a good number of weeks only to get the basics down. But the rewards in terms of design quality can be vast. As the user’s expertise grows, so will their familiarity with hotkeys and textual input methods which will drastically speed up the workflow. It is even possible to create and implement scripts for custom functionalities and action sequences.
As a jewelry industry standard, there is an active online community and a great offering of third-party plugins. Most notable is MatrixGold, and not just because of its seven thousand dollar price tag. It makes use of Rhinoceros’ engine for creating complex flowing surfaces while adding automatic functionalities to create jewelry pieces. There are advanced options for text, pavé settings, prongs, crowns, bezels, and cutters. Going well beyond the capabilities of Rhinoceros, MatrixGold adds mesh modifiers for twisting, shearing, and tapering sections, a 3D texturizer based on bump maps that can be smartly scaled to a surface, a signet ring builder, a rendering studio, a profile editor, advanced rail sweeps, and the ‘Jali’ tool for adorning a piece with milgrain, rope, or pipes. In contrast with Rhinoceros, MatrixGold has a parametric history that allows lossless modification and resizing of pieces at any time during the creation process. To extend MatrixGold with CounterSketch, a user-friendly product customizer for over-the-counter sales, sets the buyer back another five thousand dollars, while the sculpting module Clayoo comes just under the one thousand dollar mark.
An alternative add-on is Panther3D, a third of the price and still a comprehensive toolset for creating all categories of rings and other jewelry items. It guides the user in creating gem settings, prongs, cutters, and size ranges, while making use of Rhinoceros’ advanced surfacing tools for designing custom base shapes and details.
At $660, RhinoJewel is a less costly plug-in that offers interesting functionalities such as a gemstone library, gem settings along curves and surfaces with various array tools, and weight estimation.
2Shapes is another interesting software proposition that can be integrated with Rhino as well and starts at 500 Euros. It converts Rhinoceros into an over-the-counter sales tool for product customization based on a library of 1,200 models that include cathedral, split shank, bypass, eternity, filigree, text, and signet rings and can be tweaked to the customer’s wishes in terms of sizing, prongs, gem settings, a profile editor, and more.
Free Jewels is a free plugin that also adds a basic jeweler toolset to Rhinoceros. The best free Rhino plug-in is Grasshopper3D, especially when extended towards jewelry design with Peacock, Matrix, Lunchbox, and Grasshopper Gold. These add-ons incorporate many necessary tools for parametric jewelry design, such as cutters, bezels, prongs, pavé, gem-on-curve, chains, milgrain, signet rings, textures, and a wax tree generator. Grasshopper has a node-based flowchart interface in which complex models and patterns can be crafted by scripting. The mesh models can subsequently be returned to Rhinoceros’ main viewport for further optimization towards 3D printing. Just like Rhino itself, this requires some expertise on behalf of the jeweler.
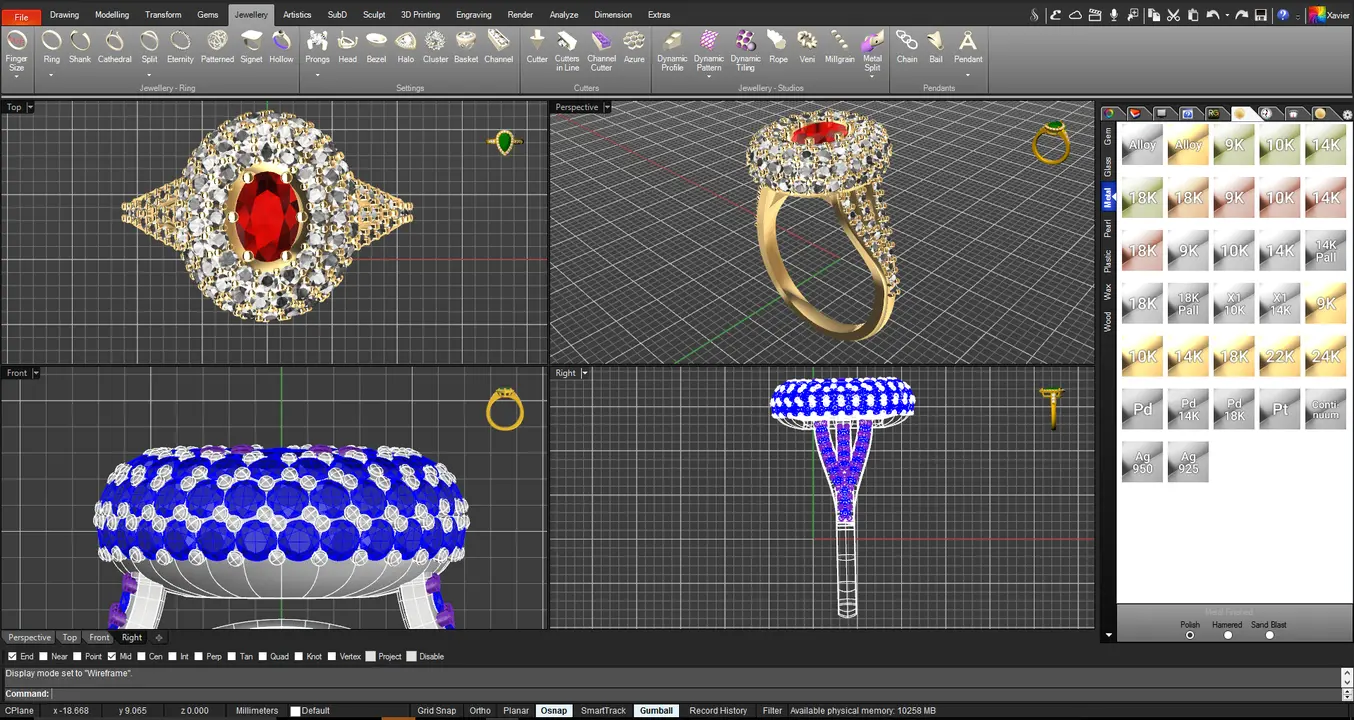
Rhino and its various plugins offer an almost endless list of features.
Firestorm CAD
Developer: 3D Space Pro
Released: 2008
Platforms: Windows
Ideal for: Ready-made designs
Price: $6,500
Firestorm feels like a stripped-down version of SolidWorks with extra functionalities for jewelry design. Most shaping is done by drawing 3D curves that can be turned into surfaces using blends and fills. Solids are created with the Pull tool which extrudes sketches into bodies that can subsequently be combined with Boolean operations. Direct manipulation of edges further speeds up the modeling process.
Instead of starting from scratch, Firestorm includes a massive library of 4,000+ jewelry-related base models. It offers most layout types for gems and makes it possible to automatically project these along curves or organic shapes. Text and images can be directly embossed onto the piece, and custom-made 3D widgets can be multiplied across a surface for sophisticated three-dimensional texturing.
By keeping things limited to essential tools and modifiers, the user interface is easy to learn. Despite not having a fully history-based feature tree, most aspects of the design can still be modified, turning Firestorm CAD into an effective over-the-counter sales tool. A disadvantage is that compared to industry leaders such as Rhinoceros and 3Design, there is a fairly limited user base and support system. Yet with the amount of available training videos and overall simplicity, professionals are empowered to realize their envisioned concepts within a matter of days.
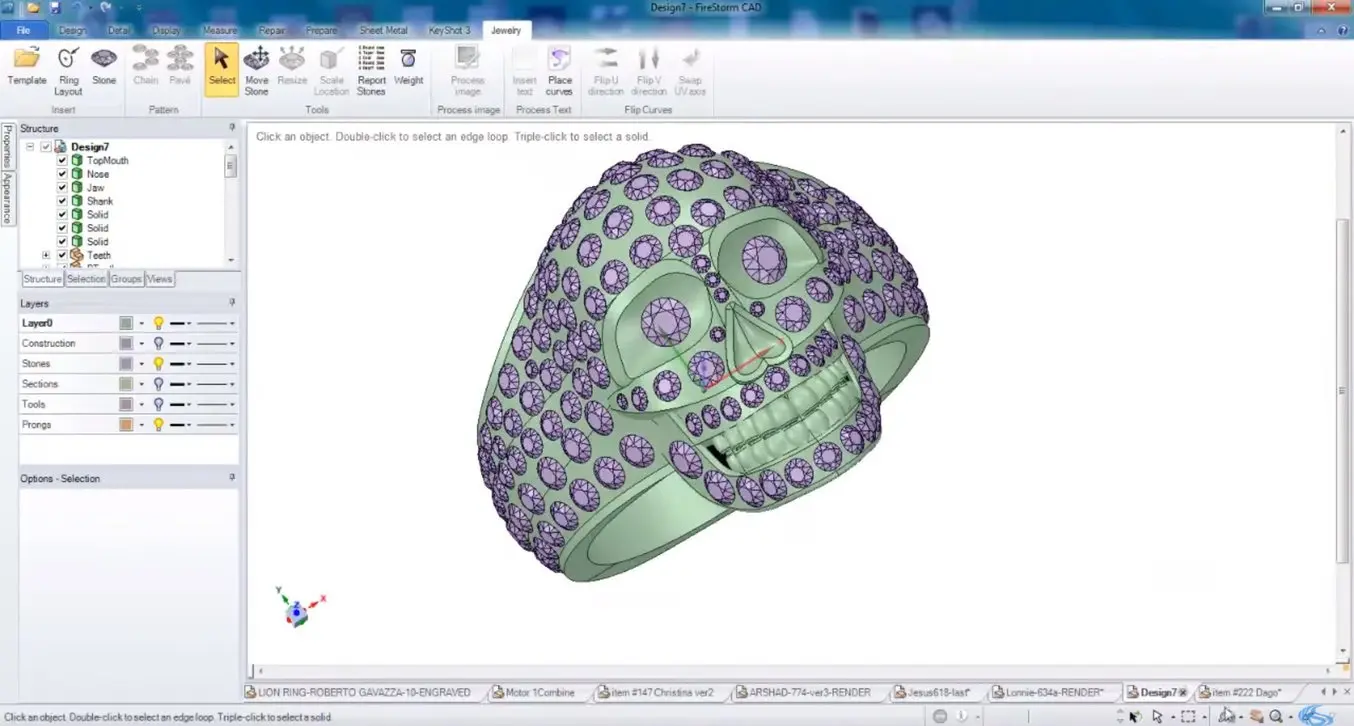
Firestorm achieves maximum modeling efficiency with minimum tool complexity while still allowing for fairly complex organic shapes and gem settings.
TinkerCAD
Developer: Autodesk
Released: 2011
Platforms: All WebGL-enabled browsers
Ideal for: Beginners
Price: Free
TinkerCAD is a free in-browser CAD solution that allows the creation, modification, and recombination of simple geometry. This block-building approach results in simplistic low-resolution shapes, yet it can be an interesting first step for the starting jeweler in adopting the digital workflow. Geometry can be numerically scaled to set up base models for jewelry pieces. Then, ornamentation and patterns can be manually modeled, scribbled, or imported from the cloud or the user’s own 3D library.
The drag-and-drop feature for adding geometry, a limited set of icon-based feature buttons, and navigation gizmo make TinkerCAD easy to use and accessible to the absolute beginner. With the omittance of history-based or parametric modeling, it is good to aim to get the model right the first time. Since TinkerCAD delivers ready-to-print STL or OBJ files, additional post-editing can be done in mesh editing or sculpting software such as MeshMixer or ZBrushCoreMini.
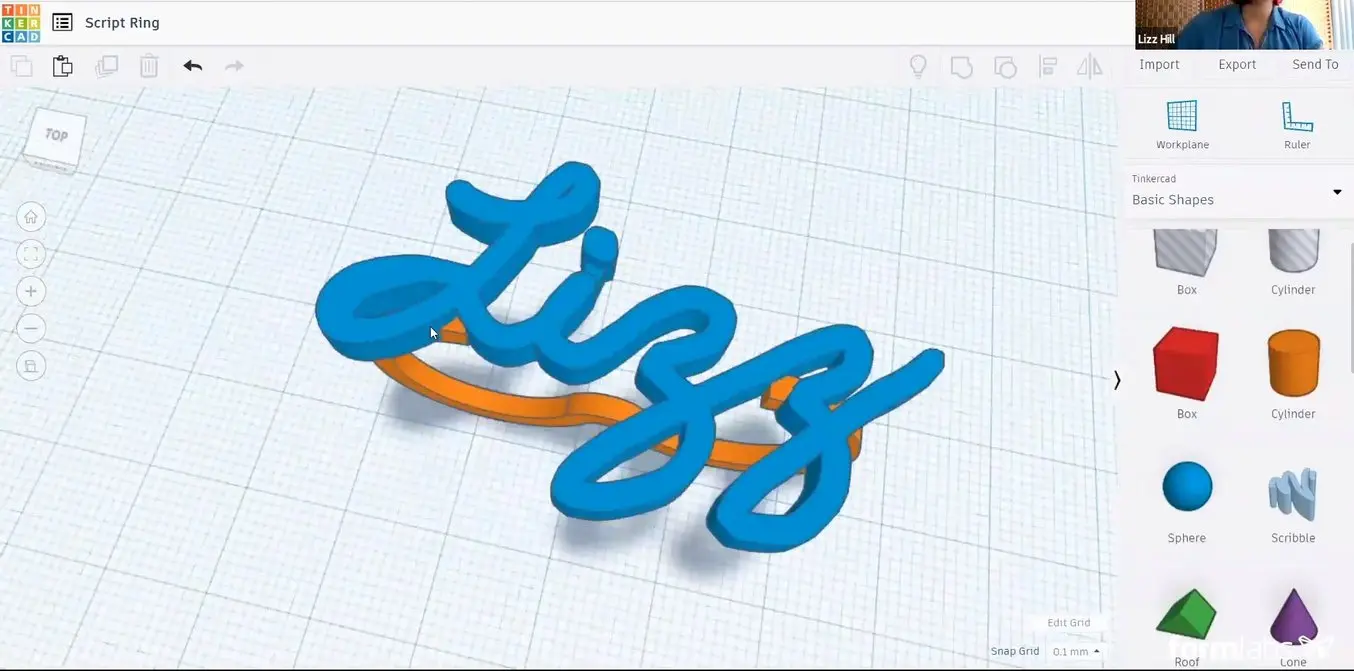
TinkerCAD offers a first taste of 3D modeling with simple operations, a scribbler, and a fun object library to tap into.
Fusion 360
Developer: Autodesk
Released: 2013
Platforms: Windows (x64), macOS
Ideal for: 3D Printing
Price: $495/year, free for students and startups
Fusion 360 is Autodesk’s cloud CAD solution and that is entirely free for students and startups. Models can be parametrically defined and the program includes a simplified history tree that can be disabled for direct modeling approaches. The key advantage of a cloud-based CAD platform is that resource-intensive operations happen on the network, independent of the local workstation’s processing power.
The modern user interface incorporates seven workbenches. In the Model workspace base models can be constructed and dimensionally constrained using standard surface and solid body operations. The Sculpt workbench then allows for freeform modifications, notably with the Edit Form tool. The user can now manipulate individual faces and vertices of the mesh while Fusion 360 ensures curvature smoothness across the shape. Another tool perfect for jewelry design is the Pipe command, which can automatically create organic filigree wire networks between the nodes of a mesh. The Refold Faces tool enables designers to convert flat models into bent shapes for rings or bracelets. Patterns are possible, but advanced gem settings and details will have to be modeled manually.
Additional workbenches are present for simulations, generative design, animations, renderings, and production drawings. Fusion 360 is easy to learn and is well suited for 3D printable parts with the direct PreForm integration, as you can see in our tutorial.
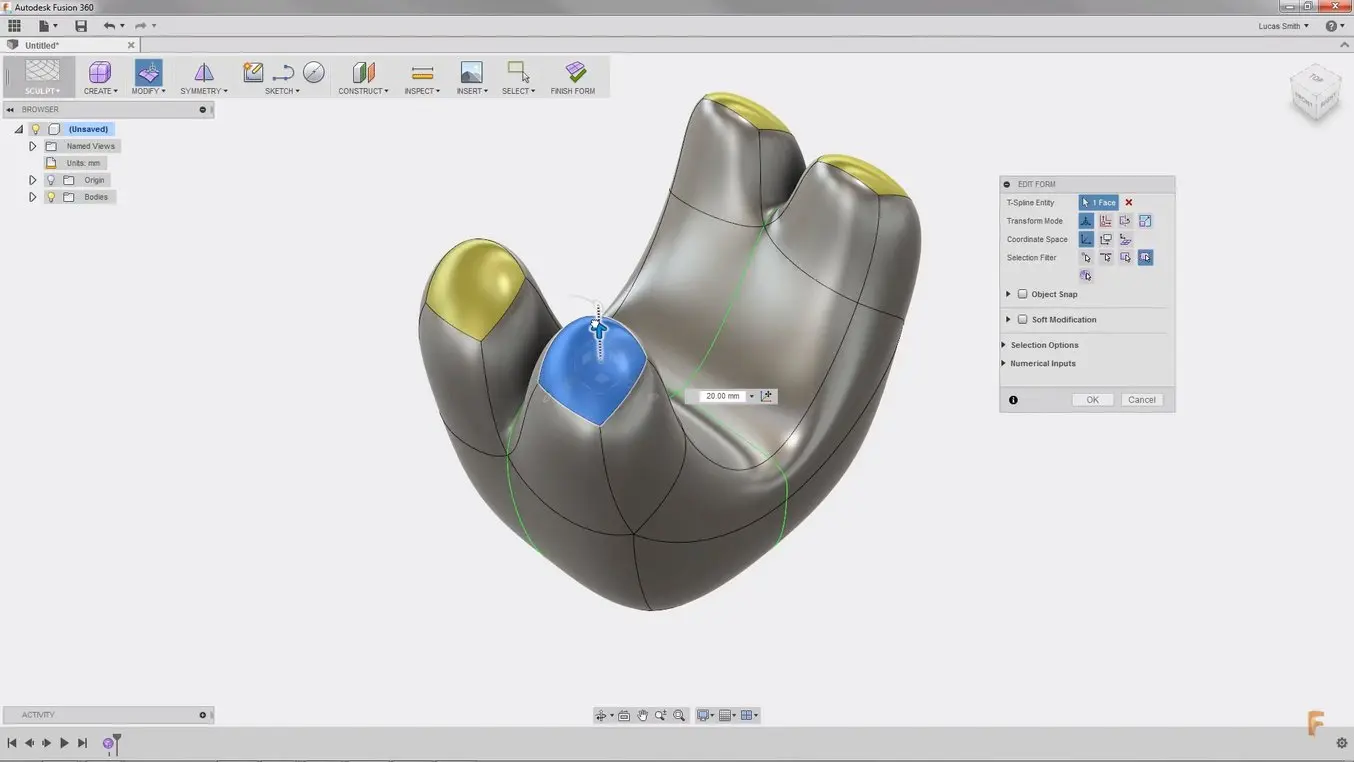
Fusion 360 has an intuitive user interface and all the basics needed for the beginning jewelry designer.
SolidWorks
Developer: Dassault Systèmes
Released: 1995
Platforms: Windows
Ideal for: Geometric designs
Price: $3,995+$1,295/year, $99/year for students
SolidWorks is the most widespread 3D CAD software on the planet. While it does offer more advanced surface and solid modeling tools than Fusion 360 such as boundary surfaces and curvature fillets, nothing can be directly manipulated or sculpted. With constraint-based modeling, all features are saved in a history tree along with their parameters. The primary advantage of this approach is that in case of revisions the model will dynamically update as the design requirements changed, and it is always possible to revert to an earlier state of the model. The procedural workflow requires an engineering mindset and careful planning as opposed to more exploratory approaches.
3D modeling environments cannot get less niche than SolidWorks; nothing in it is tailored specifically to jewelry design. And while there are some tools to create patterns along curves and on flat surfaces, on curved surfaces this will require a workaround. 3D text options are limited, and illustrations will often need to be redrawn in order to be added onto the model. Automatic embossing is confined to flat and cylindrical surfaces; for complex surfaces, these will also require a workaround. Parts can be imported so jewelry designers will want to establish their own libraries for gems and ornamental widgets.
In terms of user-friendliness, SolidWorks has found a very logical way of grouping all functionalities under the different menus and rows of tabs. Right-click menus, expert hotkeys, and the various interaction possibilities sound like a user interface circus, but in reality, they are surprisingly effective and easy to learn for the intermediate user. SolidWorks performs decently in exporting STL files for 3D printing, even if these need some post-editing work. For more information on the capabilities, read our SolidWorks tutorial for 3D printing.
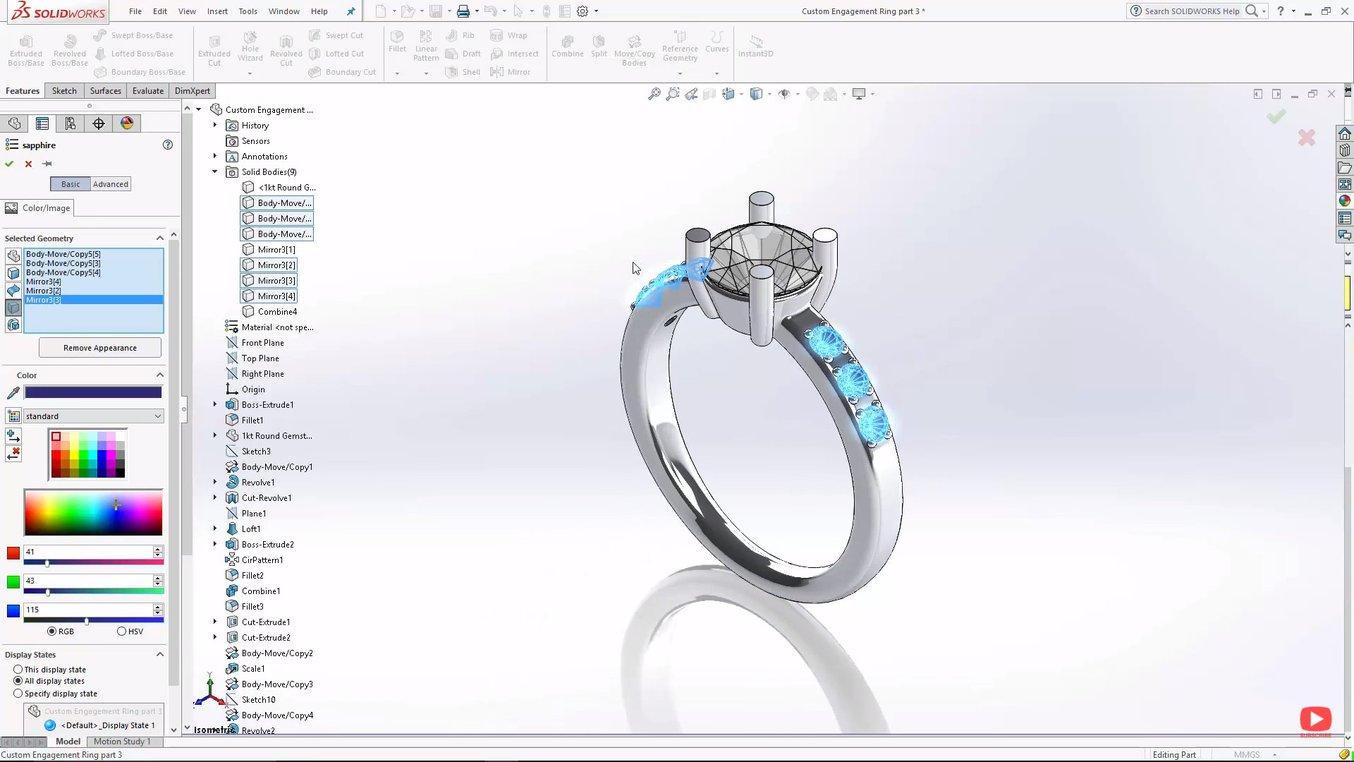
SolidWorks is ideal for geometric jewelry styles.
Blender
Developer: NeoGeo
Released: 1994
Platforms: Linux, macOS, Windows, Android, BSD
Ideal for: 3D Printing, rendering, best free CAD solution
Price: free
Blender’s combination of advanced mesh modeling and sculpting renders it attractive for jewelry designers and 3D printing enthusiasts. For beginners or those more mechanically inclined, the transition to Blender will entail a steep learning curve. In polygonal modeling, meshes can be precisely controlled to create the most complex forms and adornments. They can be deformed by bending, twisting, tapering, stretching, warping, smoothening, and waving.
Like 3Design, Blender has an envelope distorter as well as sculpting tools to allow for freeform shape manipulations. Noteworthy is the curve modifier, where a shape is morphed along a curve for a precise fit onto the jewelry piece. Because the modifier stack saves parameters for all modifiers employed, the geometry stays linked to the curve so it can be changed at any later point in time. Grasshopper-like generative design functionalities are possible in the new Geometry Nodes workspace which is great to create complex patterns that can be turned into gem settings or filigree lattices, taking full advantage of the possibilities with a 3D printer.
Compared to commercial alternatives, the open-source Blender is somewhat harder to learn, slightly more buggy when it comes to features such as Boolean operations, more limited in sculpting features, and overall more amenable for small projects. Nevertheless, it is a great start for paving the way toward an organic jewelry modeling workflow.
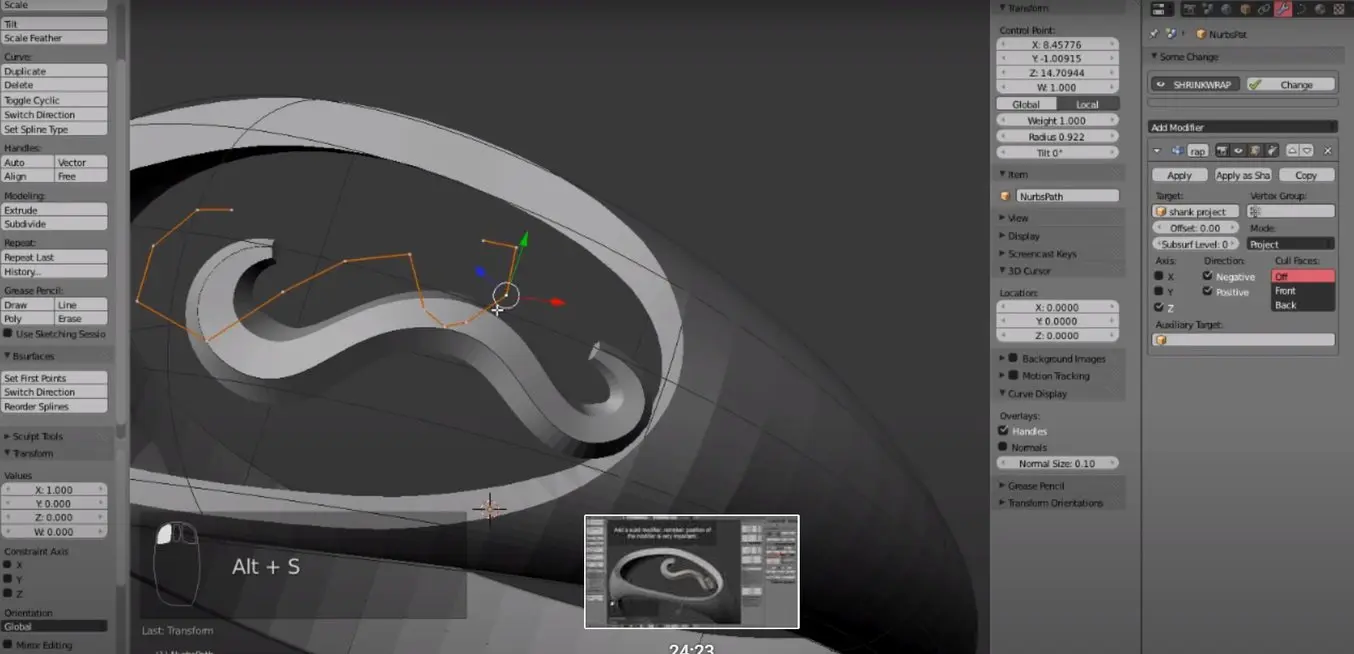
Blender offers advanced modifiers, empowering designers to generate organic shapes.
ZBrush
Developer: Pixologic
Released: 1999
Platforms: Windows, macOS
Ideal for: Sculpting, 3D textures, best value-for-money
Price: free, US$895 or US$360/year
ZBrush is the undisputed winner for creating sculpted designs such as flowers, reliefs, portraits, and animals. As a bonus, it offers extensive polygonal modeling tools for designs where precision is required. The designer can tweak modeling tools such as pinches, roundovers, bevels, and creases to gain just the right effect. Geometric primitives can be parametrically set up, say for different sizings, while the ruler and numerical input fields ensure accuracy where needed.
ZBrush is also unparalleled in creating 3D textures. It offers a library of ornamental brushes as well as creation of custom brushes for rapid texturizing across organic surfaces. Tunable texture randomization can be achieved with Nanomesh. In Curve Mode, geometry can be repeated and rotated along a spline which is useful for pavé settings and ornamentation. Import gemstones and prong settings directly with Gem Cut Studio, and directly export to Keyshot for rendering.
A program unlike any other, ZBrush comes with a learning curve, but once mastered it is the capstone of digital craftsmanship.
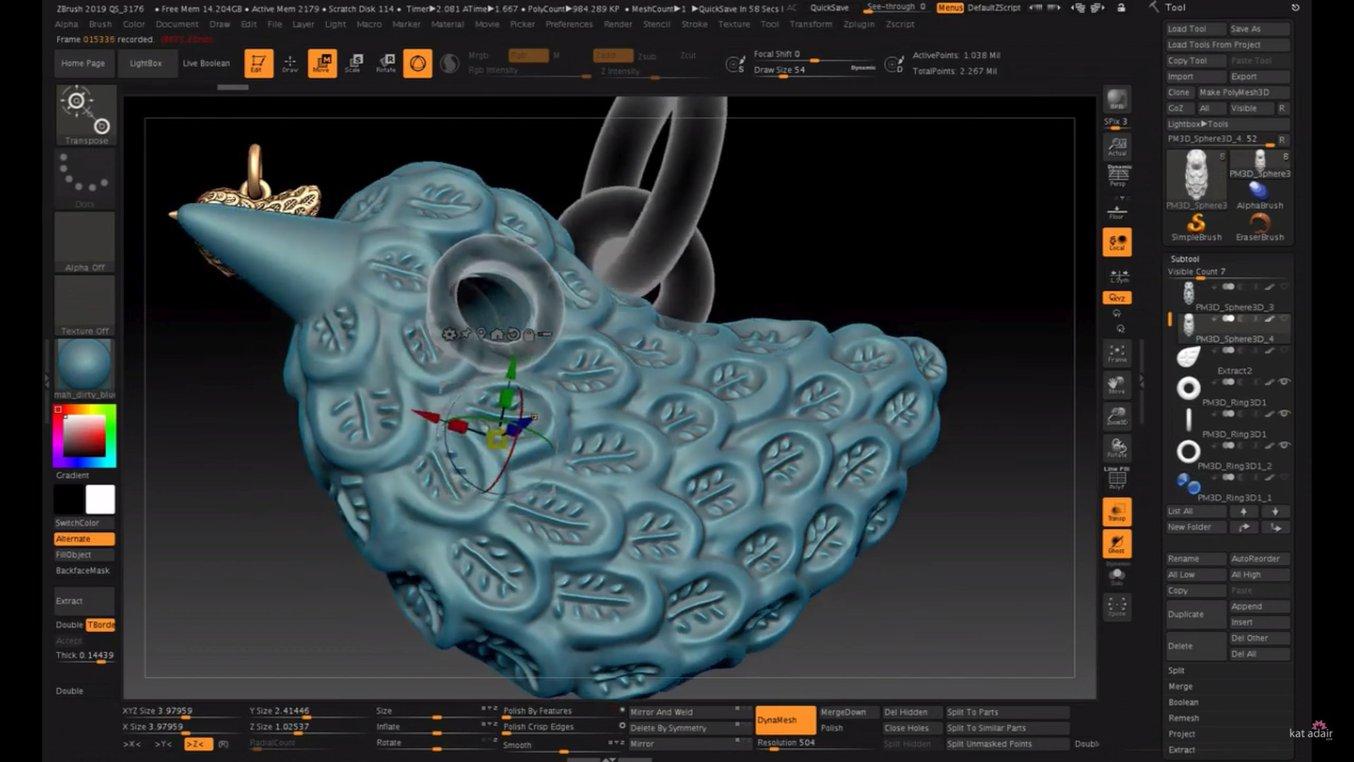
ZBrush, a winning interface between mesh modeling and freeform sculpting.
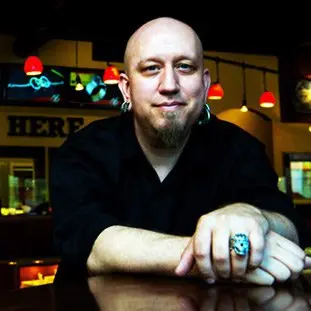
Intro to ZBrush for Jewelry: Design and 3D Print Intricate Organic Shapes
In this webinar, Tomas Wittelsbach, a digital sculptor will discuss how the fast iteration of designing, printing, and casting parts in-house has transformed his work process.
Maya
Developer: Autodesk
Released: 1998
Platforms: Windows, macOS, Linux
Ideal for: Organic, intricate designs
Price: $1,700/year
Originally targeted at the film and animation industry, Maya is increasingly used for 3D printed models, and is the most advanced polygon modeler at that. Besides sculpting tools and modifiers such as twist, flare, squash, taper, chamfer, bevel, bridge, and bend, it is possible to project curves onto shapes and create curve-based patterns. MASH is an additional toolkit to create intricate procedural shapes and patterns that can add plenty of visual interest to a jewelry piece.
As a direct modeler, Maya is not made for precision. But besides the geometry, it also stores its properties and interrelations in a node graph architecture that empowers the designer with a high-level overview of the modeling scene from where alterations can be made. Command history is also saved to some extent.
Having a customizable user interface speeds up the workflow, and while in Maya the sky is the limit, for jewelry designers patience is still required since most projects will involve loads of low-level operations in order to get to a workable design. Due to its advanced features and powerfulness, Maya is one of the hardest programs to learn—but in return, it can do almost anything.
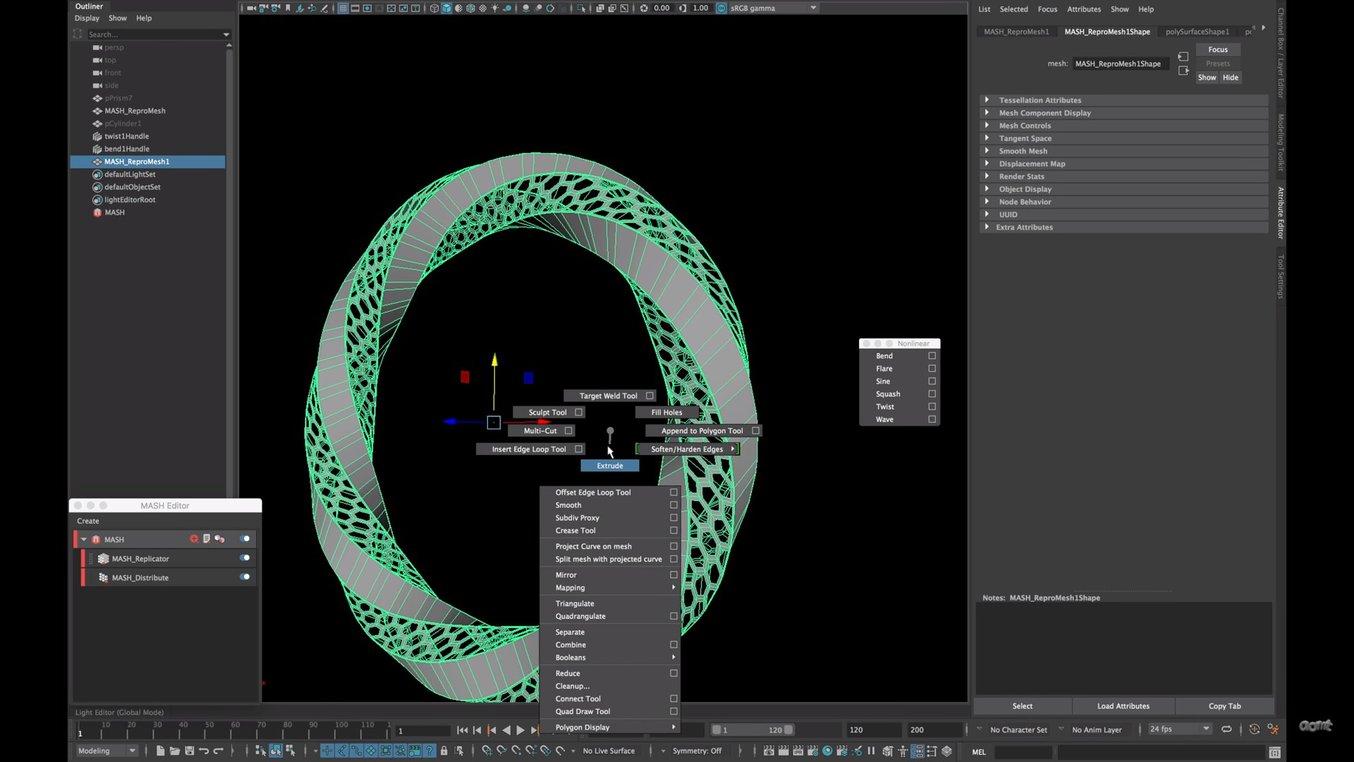
Maya, a polygon modeler great for organic, intricate designs.
Modo
Developer: Foundry
Released: 2004
Platforms: Windows, macOS, Linux
Ideal for: Concept design, freeform geometry
Price: $1,799
Modo is a polygonal modeler perfect for creative explorations without having to enter the engineering arena. The designer typically starts with a box and drags out its vertices to approximate the intended shape. Then using smoothing and creasing techniques, sharp and soft areas are defined. Using polygonal techniques such as offsets, bevels, bridges, and edge slices, details are added, and the resulting shape is further optimized using subdivision tools. The overall workflow feels like a happy amalgamation between sculpting and solid modeling.
Like other direct modelers, Modo has an inventory of deformers such as twist, bend, vortex, swirl, lattice, taper, bulge, thicken, wrap, push, and smooth. An important concept here is edge weighting. Besides deforming an entire object, it is possible to select certain areas and attach weights to these that determine how much of an effect the modifier has in that specific area. With the Falloff tool, this is automated in that the modifier tool affects elements based on a gradient that lies along a user-chosen line, curve, or spatial volume. This results in nicely smooth surface transitions as is desirable for eye-catching jewelry designs.
Another key benefit of Modo lies in its ability to 3D paint and generate image-based textures. The user interface looks somewhat like Blender’s yet is simpler, more visual, highly customizable, and easier to grasp. Most commands have their own hotkey for the expert user. Plug-ins exist for coupling SolidWorks, Thingiverse, Sketchfab, as well as some 3D printers.
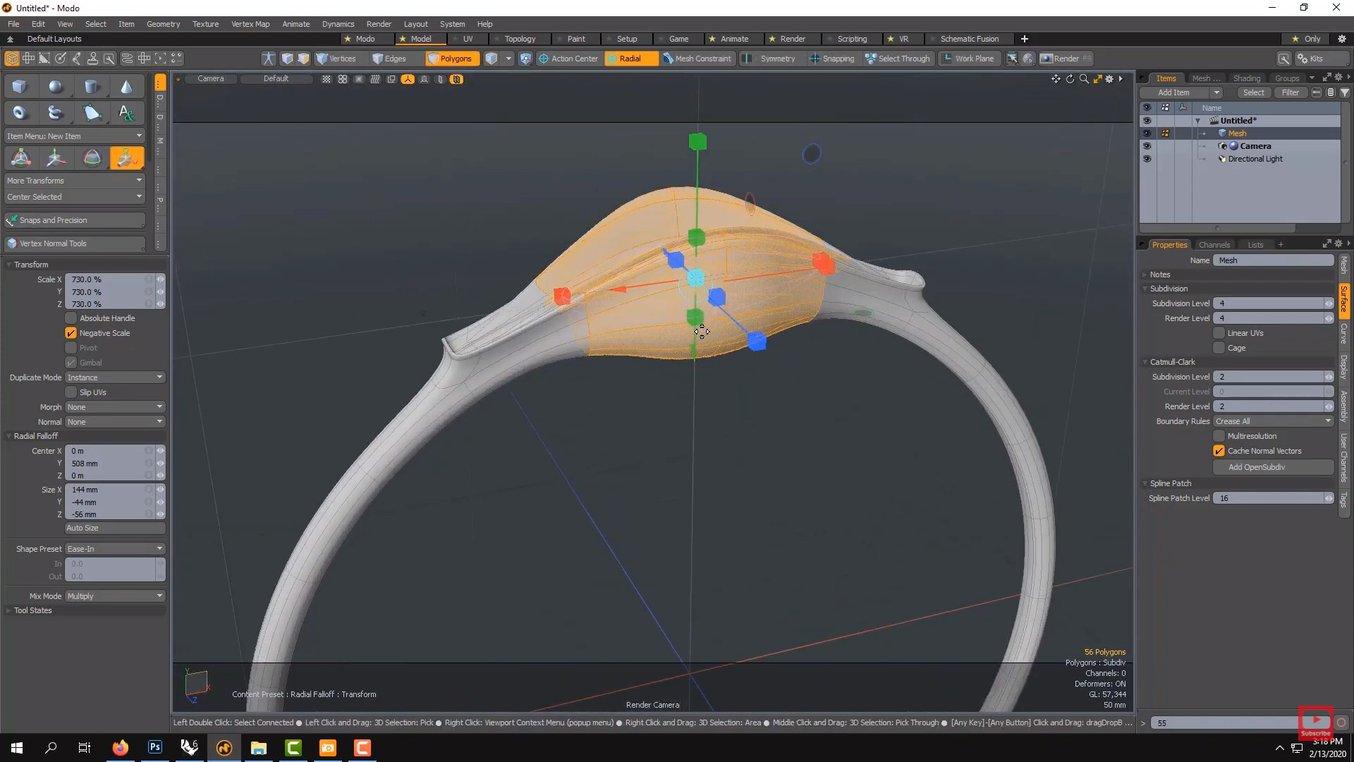
Modo offers advanced control over mesh deformers such as seen in this scaling operation with elliptical falloff.
Realizing Your Jewelry Design With 3D Printing
Beyond digital design, introducing a stereolithography 3D printer can be the start of digitally transforming your jewelry business. Formlabs Grey Resin is perfect for rapid design iterations to verify aesthetics and proportion. And having a prototype at hand enables consultative client sessions. Seeing and trying on the piece in real life increases customer satisfaction and confidence, while more feedback can be gained in order to improve the product in terms of design, fit, and wearing comfort.
Custom jewelry needs to be uniquely meaningful and last for generations, so early prototypes are crucial to hit the spot where the design is ‘just right.’ The excitement of a try-on meeting is also the prime opportunity to introduce a ‘reach option’ that stretches the budget towards incorporating a more exclusive center stone and more elaborate design options, which can drive up the retail sale. And for those ready-while-you-wait situations, consider using Draft Resin which prints up to four times as fast.
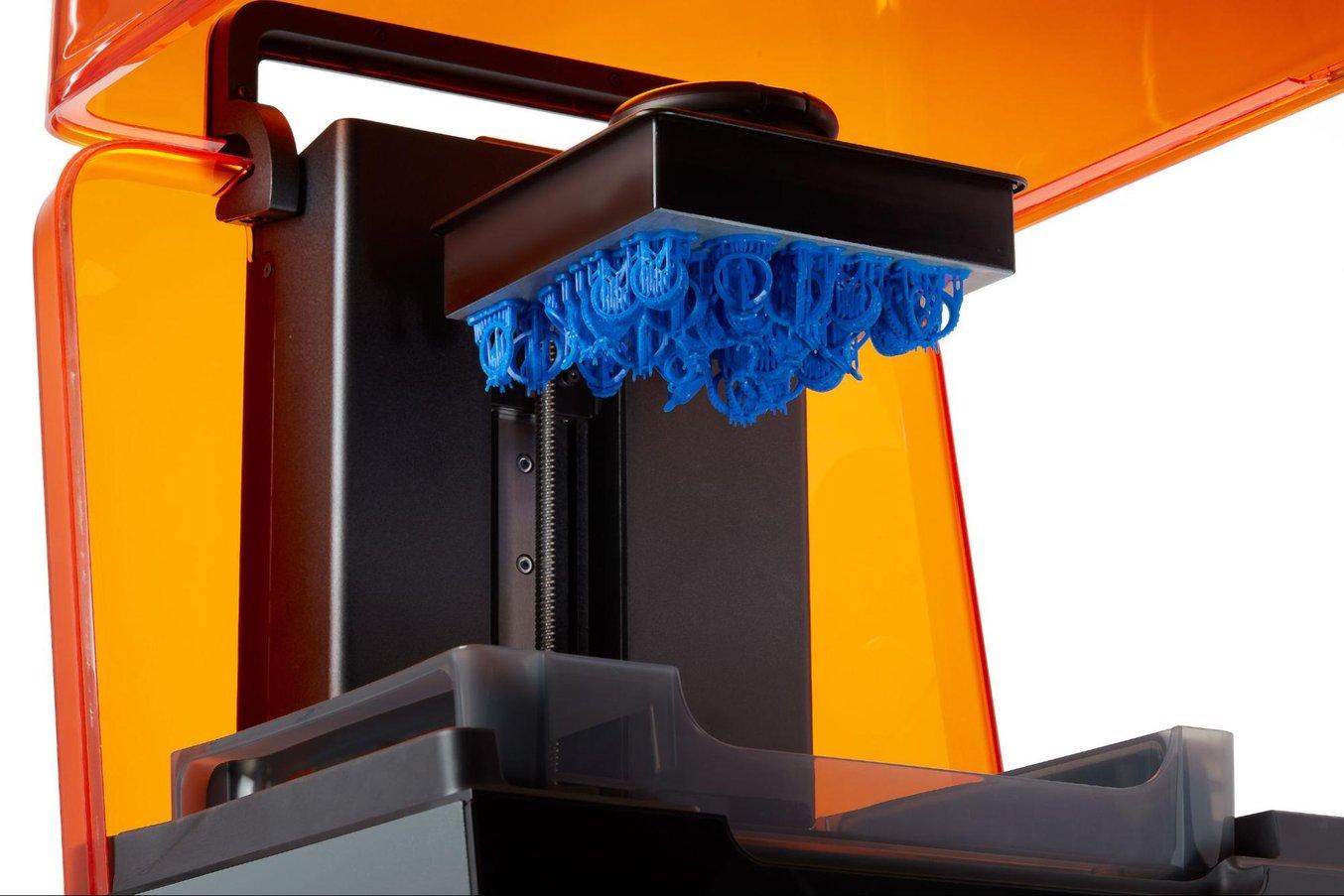
3D printing is the fastest and easiest way to realize digital jewelry designs.
When entering the production phase, one-offs can be made using direct investment casting, or lost-wax casting. The design can be directly printed in wax-filled resins, immersed in a refractory casting material, burned out, and cast just like traditional wax patterns. Castable Wax Resin results in a clean, ash-free burnout while capturing the most intricate of features such as wire filigree. Castable Wax 40 Resin contains 40% wax to ensure successful burnout and provide the easiest workflow.
Rubber molding is the next stop on the avenue towards volume production. One or more 3D printed master models are encapsulated in rubber for repeatable casting of wax patterns that are subsequently used for investment casting. Master models printed at ultrahigh resolution in standard resins will be useful for RTV silicone molding. Natural rubber, which with its high tear strength is more suitable for thick-walled pieces and durable molds, vulcanizes at 155°C. Heat-vulcanized silicone rubber completes hardening at 175°C and is more suited to pieces with intricate details. Use High Temp Resin for these cases as it resists temperatures up to 238°C after post-curing.
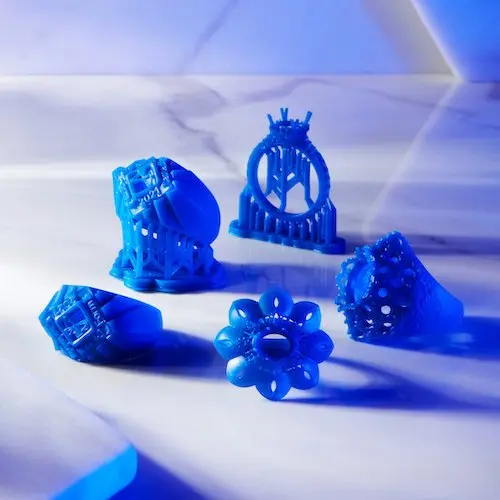
From Heavy Class Rings to Intricate Jewelry: Easy Casting With Our Latest Material
In this webinar, Patrick Diggins, our Jewelry Vertical Manager, will teach you how Castable Wax 40 can help you push the boundaries of design and production efficiency.
Get Started With Digital Jewelry Design and 3D Printing
The jewelry industry is historically characterized by family-owned businesses that have taken decades or even centuries in order to develop their knowledge and craft. While digital workflows involving CAD and 3D printing can mean a leap in design and production speeds, product customization possibilities, customer involvement, the exploration of new creative horizons and addressing of new markets, they will augment rather than replace the traditional workbench.
There is no magical one-click solution to successful jewelry designs, however CAD solutions like 3Design and Firestorm come close with specific design wizards and libraries of gems and base models. JCD shines in its handling of multi-gem arrays and parametric design while a plugin-cladded version of Rhinoceros handles most aspects of jewelry design just as well, even if requiring a higher level of modeling expertise. With Grasshopper, designs are set up parametrically while its data-driven approach sprouts complex geometries that truly open up new frontiers in ultra-customized jewelry design.
For smaller companies and independent designers who are just getting their feet wet in 3D design, polygonal modelers such as Blender and Modo are reasonable choices. Designers with a broader focus besides jewelry can get away with solid modelers like Fusion 360 and SolidWorks. Even Tinkercad proves to have some potential for simple and customized 3D designs. The best value, especially for organic models, is offered by ZBrush which integrates advanced sculpting and texturing with polygonal modeling as well as gem libraries and advanced 3D rendering.
All in all, there is no perfect CAD solution since it will depend on the preferred modeling approach, expertise, and project scope of each individual designer or business. The different solutions are strongly directed to specific genres of jewelry design. We hope this guide has been helpful as a source of awareness of different digital tools and 3D printing applications for jewelers looking to step to 3D.