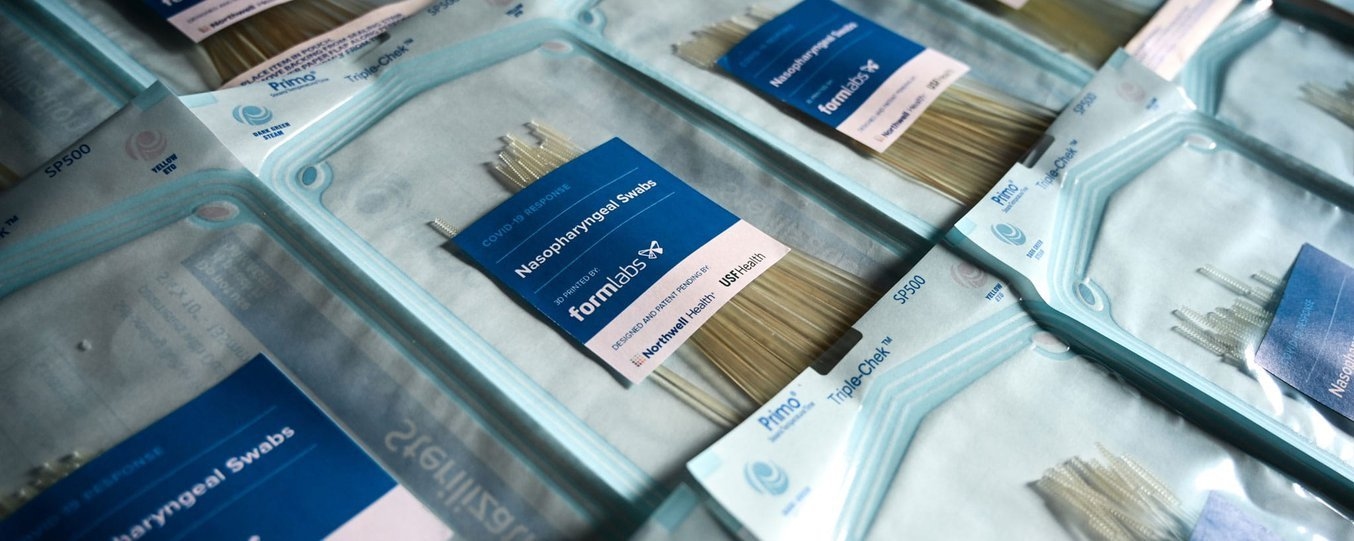
Considerations for Producing Safe and Effective Medical Devices
Formlabs has received hundreds of inquiries from clinicians and users in the 3D printing community who are eager to use our technology to respond to medical equipment shortages created by the COVID-19 pandemic. This article looks at the regulatory landscape for 3D printing in healthcare and how the technology can be responsibly used to have the highest impact on patient care.
History of 3D Printing in Healthcare
For years, users in the medical industry have successfully applied 3D printing technology to advance patient care. Some proven and documented applications include anatomical models, surgical guides, and medical devices. 3D printing offers a solution that can be adaptable to the change in needs, executed at the point of care, and trusted to deliver consistent, safe care to patients and clinicians - all qualities which are crucial in this time of uncertainty.
Formlabs’ Proven Commitment to Medical
Throughout the historical adoption of 3D Printing in the medical industry, Formlabs has been a proven partner to innovators adopting the technology for the first time and an active participant in working groups and advisory boards determining the application of regulations to keep patients safe. To advance new applications, Formlabs acquired an ISO 13485 certified resin manufacturing facility for production of new biocompatible materials, adjusted our own technology to ensure we could meet Quality Management System requirements, and conducted studies to provide information needed by medical professionals (ex. sterilization). This ongoing commitment to healthcare now lays the groundwork for Formlabs to play an instrumental role in the response to the unprecedented needs created by the COVID-19 pandemic.
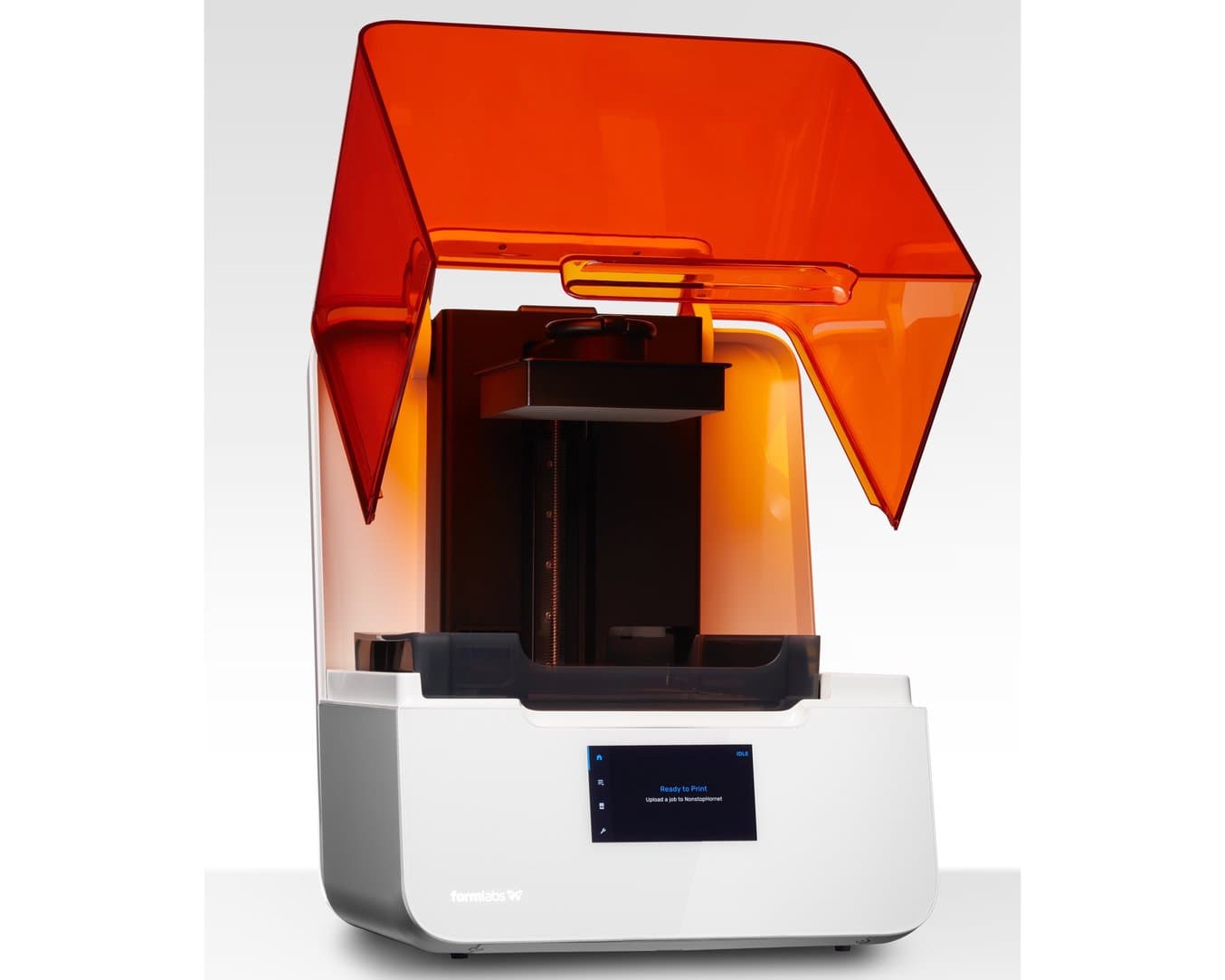
Regulatory Landscape for 3D Printing
Regardless of manufacturing technology, the expectations for device classification and approval remains the same. Additional guidance on regulatory approval processes can be found on the FDA's Medical Device webpage. In 2017, the FDA published specific guidance on 3D printing in Technical Considerations for Additive Manufactured Medical Devices. In response to the current needs, the FDA has a page addressing FAQs for 3D printing medical devices, accessories, and components during the COVID-19 pandemic. Formlabs recommends you consult each of these sources before using any 3D printing technology to produce medical equipment.
Ensuring Quality in the 3D Printing Process
It is a manufacturers responsibility to ensure the device, including the validation of design, materials, and post-processing, is safe and effective for use. It is also imperative that the facility that the devices are produced in is acceptable for production. The remainder of this article will focus on additional considerations for the process of 3D printing medical devices.
Establish process control
Prior to production, it is important to validate your process. This should consist of qualifying your machine’s capability to reproduce parts identical to the design specifications. Consider the following questions:
-
What factors may affect the outcome of your print? These factors may include machine setup/environment, design of the build platform, etc.
-
How can you control for each of these factors to ensure each part is manufactured according to specifications?
This pre-print planning will help you sustain a successful operation.
Maintain process control
Consider the ways in which you can control factors critical to your prints. Below are a few examples of how this may be accomplished:
-
Create a Standard Operating Procedure (SOP) for printing and post-processing. This may include the following:
-
Standard .STL file
-
Standard pre-print checks (resin preparation, printer leveling, etc)
-
Standard post-printing activities (minimum time from print finish to first wash, standard wash and cure times/positions, etc.)
-
-
Consider planned periodic activities required to keep your equipment and process in a capable condition. This may include tank replacement, IPA/wash fluid replacement, or printer checks. Document your plans and the execution of the planned activities.
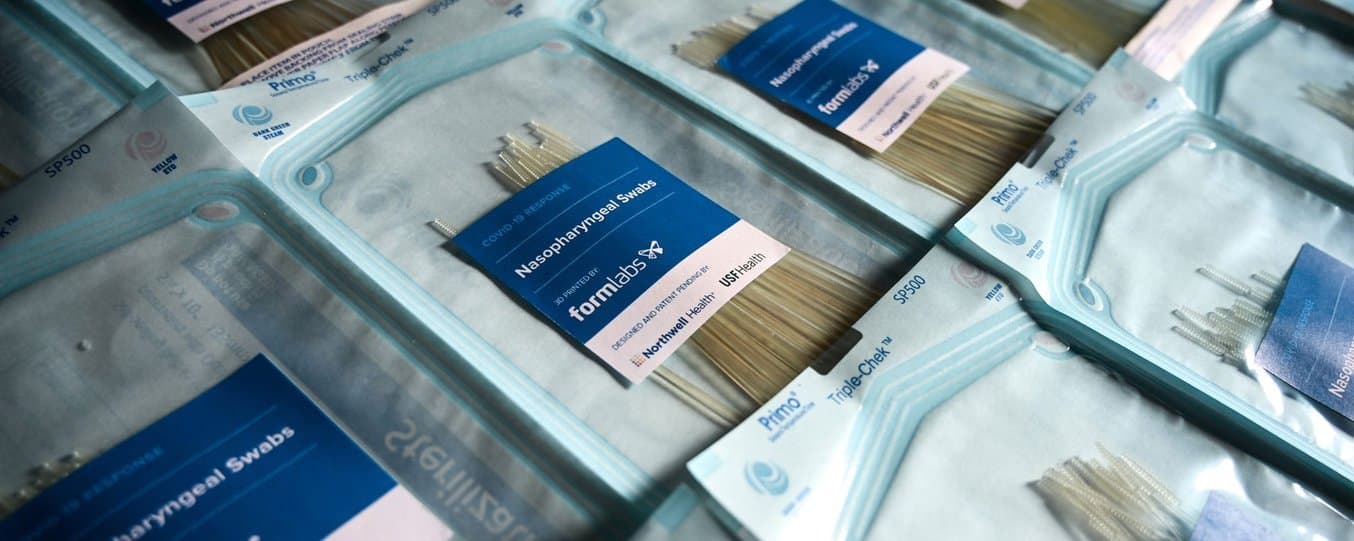
Quality Checks
Determine how you will ensure completed parts are acceptable for use. To do this you will need to choose a method and a frequency for inspection.
-
Example frequencies: Inspecting a few parts per build, all parts on every few builds, all parts every build.
-
Example method: Comparison to a specification, such as measuring the length and comparing to the specified length, and comparison to a standard, such as comparing a sample part to a known good part to determine if the length is acceptable.
Remember to have a quality control plan for each essential element of the product (dimensional, mechanical, functional). Different elements can have different QC frequencies and methods.
Expect the Unexpected
Even the most understood processes often behave in unexpected ways. Make plans to allow you to respond appropriately and protect patients from potentially unsafe products. A few common processes to allow appropriate response:
-
Create a batch record to segment and uniquely identify each build. For each build, document information such as the resin batch, tank, any errors encountered in printing, post-processing equipment, etc. If you encounter an unfamiliar issue, this information may be crucial in determining root cause and appropriately bracketing the good devices from the bad.
-
Have a reaction plan. Consider the things that can go wrong in the printing process and determine how you will react:
-
If a few parts on your build platform fail, what will you do? Will you discard all parts, or only those that are visibly not acceptable?
-
If your print encounters an error, will you restart or abort the print?
-
Having a plan of how you will react to common scenarios will help you remain consistent in your actions.
Disclaimer
Formlabs has created this website and has become involved in varying degrees with the projects described here during a global medical crisis. Formlabs is working on many projects to address global healthcare-related supply shortages around the world, but in trying to mitigate these shortages, patient safety is still Formlabs’ top concern. We must remind those who are helping to alleviate these shortages that masks, swabs, face shields, and other 3D printed products intended to prevent or treat COVID-19 are medical devices. These devices must be safe for their intended purpose and anyone considering the manufacturing of these products should consider the following items:
-
Formlabs is a manufacturer of 3D printing materials capable of fabricating finished devices according to their labeling and any other product manufactured from these materials should be verified and validated according to their intended purpose.
-
You may be fabricating a device that does not have the required regulatory approvals and clearances. If you are fabricating devices, follow the guidelines on the label for each material. You may seek to obtain reliable regulatory advice.
-
Please consider local regulations, material safety data sheets, software capabilities, sterilization requirements, and institutional requirements before 3D printing medical devices.
-
Regulatory agencies (such as the FDA) may consider expedited review of manufacturing information and/or premarket submissions.
Formlabs cannot warrant that any products not manufactured by Formlabs are suitable for their intended purpose.