restor3d a pour mission d'aider les chirurgiens et les prestataires de soins de santé qui guérissent et restaurent le corps humain. L'entreprise a adopté une approche basée sur la fabrication additive, dont la grande liberté de conception et le coût abordable lui permettent de dépasser les concurrents sur le marché du médical.
L'équipe de restor3d innove dans le domaine de la chirurgie de précision en modifiant la façon dont les implants, les instruments chirurgicaux et les modèles préopératoires sont développés et utilisés. Les instruments fabriqués de manière traditionnelle sont lents à produire, exigent des coûts initiaux importants et présentent souvent des complications dans le flux de travail chirurgical. restor3d exploite les capacités d'impression 3D pour améliorer radicalement la qualité des soins chirurgicaux en imprimant des implants métalliques et des instruments spécifiques à la procédure et souvent au patient.
Avec un parc de plus de 25 imprimantes 3D Formlabs dans sa ligne de production, restor3d imprime déjà la prochaine génération d'outils chirurgicaux. Leurs produits contribuent à :
- Remplacer les plateaux chirurgicaux volumineux et coûteux par des outils à usage unique spécifiques à la procédure.
- Réduire radicalement les coûts de la chaîne d'approvisionnement et de la stérilisation pour les hôpitaux.
- Rendre les systèmes de navigation préopératoire superflus grâce à des instruments spécifiques aux patients.
Lisez la suite pour apprendre de l'équipe de restor3d et des chirurgiens eux-mêmes comment l'impression 3D permet de créer des dispositifs médicaux accessibles et entièrement personnalisés.
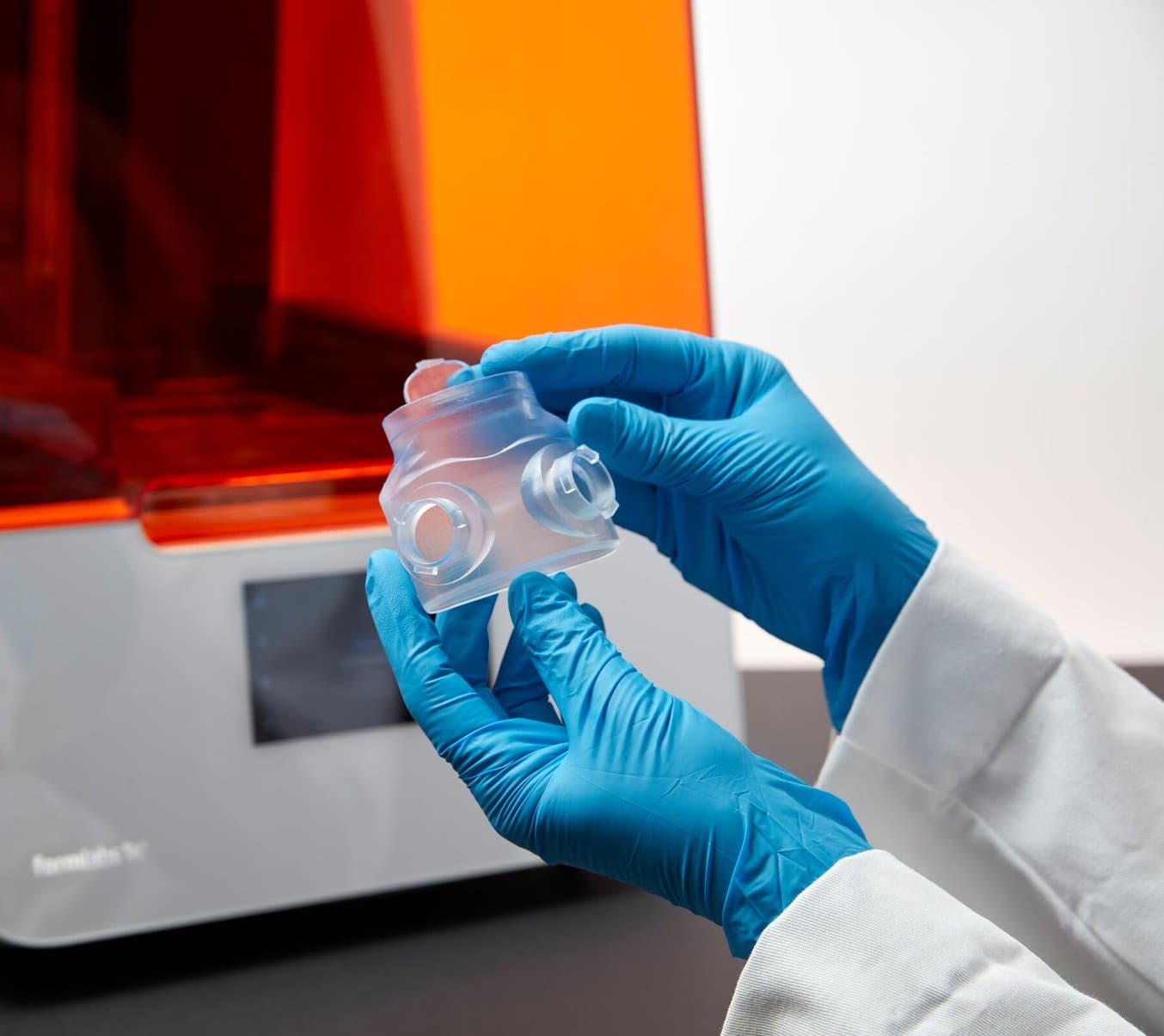
Utilisations éprouvées de la fabrication additive par de grandes sociétés de dispositifs médicaux
Découvrez comment la fabrication additive apporte plus d'avantages aux entreprises de dispositifs médicaux que les processus traditionnels lors de cette table ronde avec Enovis Surgical et restor3d.
De nouveaux horizons dans le domaine des instruments chirurgicaux
restor3d est composé d'une équipe d'ingénieurs biomédicaux et de spécialistes des matériaux hautement qualifiés qui se sont d'abord concentrés sur les implants imprimés en 3D pour les chirurgies de la colonne cervicale. En développant ces nouveaux implants, l'équipe a été confrontée à un problème récurrent : les instruments en acier inoxydable fabriqués de façon traditionnelle.
Cambre Kelly, Chief Technology Officer, a expliqué la situation en déclarant : « Nous développions un implant innovant dont les caractéristiques n'étaient réalisables qu'avec l'impression 3D, mais nous nous attendions à ce que les chirurgiens utilisent un système d'instruments traditionnel pour poser l'implant. Nous avons donc rapidement réalisé qu'il serait extrêmement intéressant de faire évoluer l'offre d'instruments tout en commercialisant des implants innovants. »
Le problème, c'est que le coût élevé des plateaux d'instruments traditionnels dissuade les hôpitaux de personnaliser leur flux de travail, de faire évoluer leur stratégie ou d'essayer de nouvelles tactiques.
« Les plateaux d'instruments traditionnels sont généralement usinés en acier inoxydable et coûtent plus de 50 000 € par plateau. En tant que fabricant de dispositifs médicaux, si vous investissez dans l'achat de 10 plateaux d'instruments à 50 000 € l'unité, vous serez obligé de les utiliser pendant très longtemps. Vous n'êtes pas du tout enclin à modifier la conception, à jeter un plateau et à repartir de zéro ou à changer des caractéristiques apparemment de moindre importance », explique M. Kelly.
restor3d a tiré parti de la puissance de la fabrication additive en interne et propose désormais des instruments et des plateaux à un prix défiant toute concurrence, afin que les hôpitaux puissent gagner en flexibilité et personnaliser leurs traitements à petit prix. La création d'outils spécifiques à une procédure et à usage unique a nécessité un processus flexible qui permet d'intégrer les retours d'information des chirurgiens dans le développement de produits d'une façon jamais vue jusqu'à présent.
« Nous sommes à présent en mesure de fournir des produits en flux tendu grâce à notre chaîne de fabrication en interne et à notre capacité à adapter rapidement la conception et la géométrie en fonction des retours d'information. Grâce à l'impression directe d'instruments à usage unique, nous sommes en mesure d'itérer et de modifier nos conceptions très rapidement », explique M. Kelly.
Permettre de nouveaux flux de travail cliniques grâce au développement rapide de produits
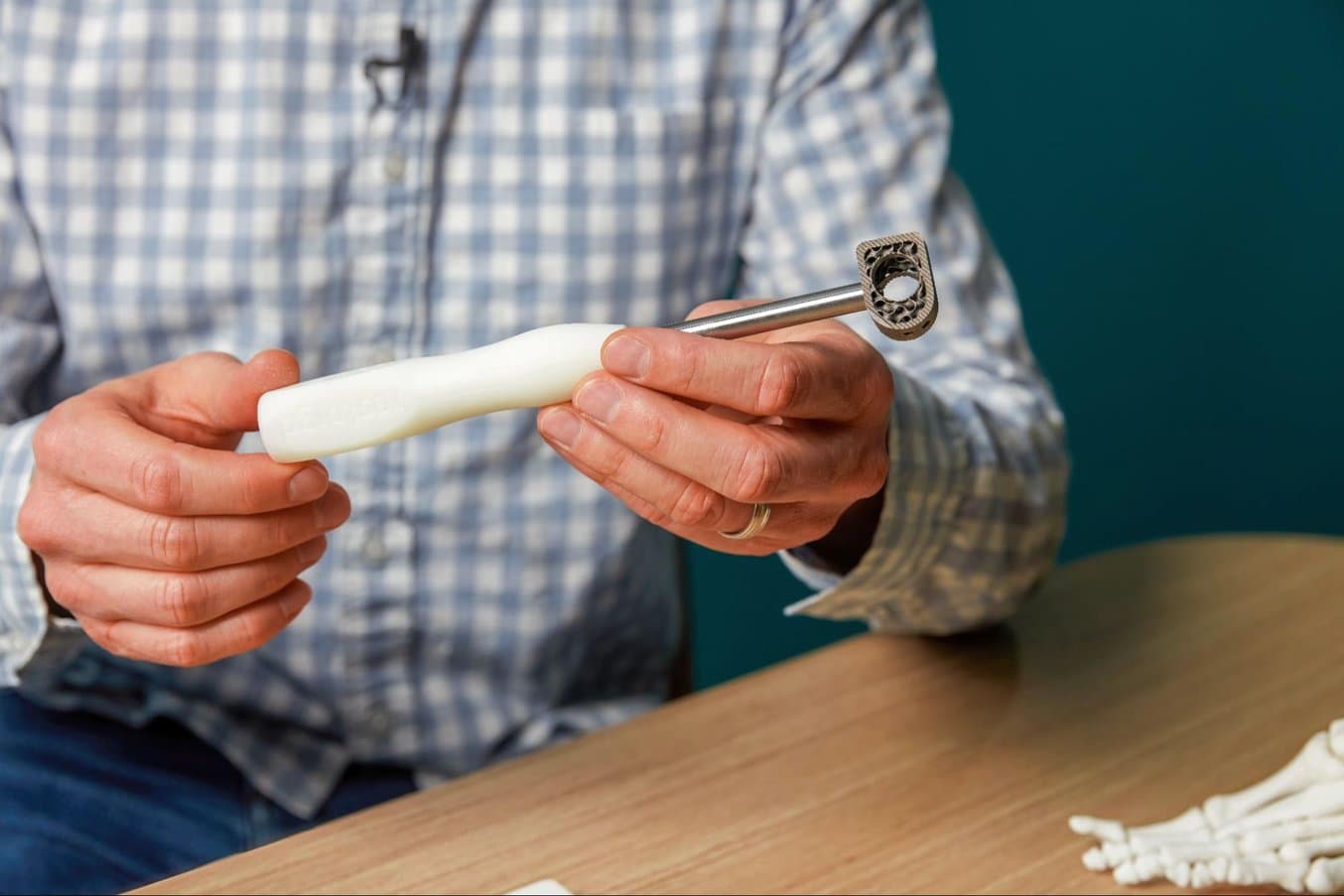
Les outils à usage unique de restor3d sont spécifiques à une procédure et combinent des composants imprimés en 3D en métal et en polymère.
Nathan Evans, vice-président principal du développement de produits, a déclaré : « Les chirurgiens sont plus à l'aise avec ce qu'ils ont appris pendant leur formation. Et s'ils ont été formés il y a 20 ou 30 ans, cette technologie n'était sans doute pas disponible. Nous constatons que les chirurgiens commencent vraiment à s'enthousiasmer lorsqu'ils entendent parler des cas de leurs collègues et voient les résultats obtenus avec une nouvelle technologie qui ouvre la voie à de nouvelles approches ou à de nouveaux flux de travail cliniques. »
Pour obtenir un point de vue clinique, Formlabs s'est entretenu avec le Dr Erik Westerlund, un chirurgien orthopédique spécialisé dans la colonne vertébrale. Le Dr Westerlund a été très impressionné par le système de discectomie cervicale antérieure avec fusion (ACDF) de première génération créé par l'équipe de restor3d, déclarant : « Le processus de développement actuel est le même depuis 20 ans. Une entreprise propose un nouveau système d'implant et/ou d'instrument. L'entreprise se présente, réalise des prototypes et, quelques jours ou semaines plus tard, on peut jeter un œil au design. Quelques semaines plus tard, un instrument bêta apparaît. Aujourd'hui, restor3d ne produit plus un prototype en quelques semaines, mais un véritable instrument en quelques jours à peine. Pour moi, cela change complètement la donne. »
Il poursuit : « Ce ne sont pas seulement les implants qui sont importants, mais la technique d'implantation également. C'est ce qui fait qu'une procédure réussit. Cette nouvelle approche de restor3d est une approche systémique. Grâce à la fabrication additive, l'implant et l'instrument sont mis sur un pied d'égalité : nous pouvons modifier les deux pour créer le meilleur résultat pour le patient. »
restor3d crée ses dispositifs médicaux en travaillant directement avec les chirurgiens. Dans des domaines tels que l'oncologie orthopédique, chaque opération est unique. Contrairement aux opérations orthopédiques normales où l'objectif de la chirurgie est d'adapter le patient aux implants existants, le cancer provoque des lésions osseuses distinctes chez chaque patient. restor3d doit donc travailler en étroite collaboration avec les chirurgiens du début à la fin pour fournir un outillage spécifique à la procédure.
« Les chirurgiens nous font constamment part de leurs commentaires. L'impression 3D nous permet de modifier rapidement la conception afin de prendre en compte les commentaires des chirurgiens et de fournir rapidement une nouvelle solution. »
Nathan Evans, premier vice-président du développement des produits, restor3d
Ben Wesorick, vice-président de Patient Specific Engineering, ajoute : « Nous commençons par réaliser des tomodensitogrammes, ou parfois des radiographies. Nous en discutons avec un médecin, puis faisons passer l'outil de la phase de conception jusqu'à la salle d'opération. Il s'agit donc d'un processus de bout en bout pour lequel nous sommes en contact permanent avec les médecins, depuis le scan du patient jusqu'à la réalisation de l'outil. »
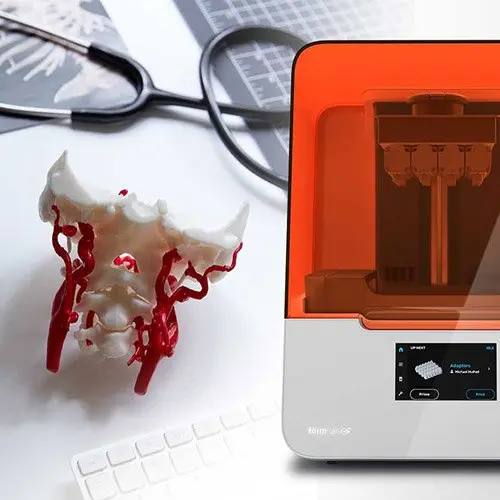
Introduction à l'impression 3D médicale
Rejoignez cette introduction de Formlabs pour apprendre les meilleures pratiques en matière d'impression 3D médicale et découvrir l'écosystème médical de Formlabs, avec plusieurs nouveaux produits de qualité médicale !
Une planification et des outils pour une opération parfaite
La phase de planification d'une intervention chirurgicale complexe est essentielle. Elle est devenue une part importante de la valeur ajoutée que restor3d apporte aux chirurgiens et comprend généralement la création de modèles anatomiques et de guides de coupe spécifiques au patient.
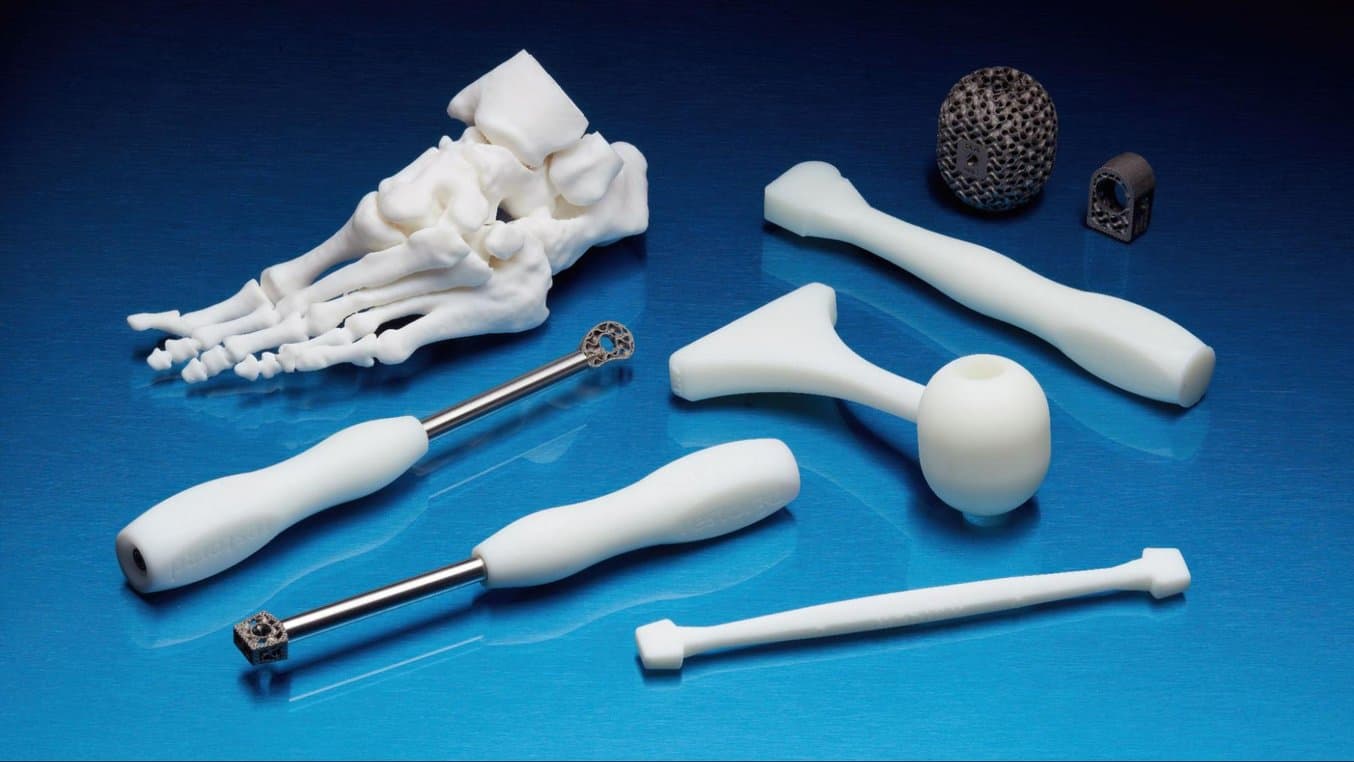
Outre les implants et les outils spécifiques à la procédure, restor3d fournit des modèles anatomiques et des guides de coupe spécifiques au patient pour faciliter la planification et la procédure.
La planification est une étape cruciale, même pour les opérations courantes que les médecins connaissent sur le bout des doigts. Chaque patient possède une anatomie unique, et même si l'implant lui-même est parfaitement conçu, le processus de mise en place est différent pour chaque patient. L'équipe de restor3d en est consciente et fournit des éléments supplémentaires pour le processus de planification afin d'assurer le succès de l'opération. « Nous pouvons fabriquer un implant parfaitement conçu destiné à s'insérer dans un trou spécifique, mais si ce trou ne se trouve pas au bon endroit, tout cela ne sert à rien. Les gabarits et les instruments de coupe que nous fournissons sont donc essentiels pour que tout se déroule de la meilleure des façons », explique Wesorick.
Pour bien comprendre l'impact qu'a restor3d sur le processus de planification, nous nous sommes entretenus avec Will Eward, MD, DVM, chirurgien oncologue orthopédique à Duke Health. Lorsque nous lui avons demandé ce qu'il y avait d'unique dans la planification préopératoire avec restor3d, il a répondu : « Ce qui est formidable, c'est que restor3d nous fournit des modèles en polymère non seulement du corps du patient, mais aussi de l'implant, des guides de coupe et de l'ensemble des instruments, depuis les manchons de guides jusqu'aux trous de vis".
L'ensemble des outils de planification permet aux chirurgiens de préparer et même de s'exercer sur des modèles anatomiques avant de travailler directement avec le patient. Cette préparation préopératoire réduit le temps d'opération et améliore la confiance des chirurgiens, ce qui se traduit par de meilleurs résultats et une récupération plus rapide.
« Depuis que je travaille avec restor3d, j'utilise beaucoup moins notre système de navigation peropératoire. La raison en est la qualité des guides de coupe. En chirurgie, la navigation assistée par ordinateur est une excellente chose. C'est fascinant à voir. Les étudiants en médecine l'adorent, mais cela rallonge de beaucoup le temps d'opération et force le patient à recevoir plus de radiations. Si nous pouvons obtenir les même résultats avec des guides de coupe bien conçus, tout le monde en sort gagnant. »
Will Eward, MD, DVM, chirurgien oncologue orthopédique à Duke Health.
Comment Formlabs aide restor3d à réaliser ses objectifs
Si restor3d parvient à créer des kits de planification préopératoire aussi détaillés et personnalisés, c'est grâce à son parc d'impression 3D interne. La gamme de matériaux disponibles, la précision des imprimantes et leur capacité à répondre aux demandes des chirurgiens à la demande permettent de fournir un produit personnalisé extrêmement rapidement.
« Dans la plupart des cas, nous fournissons entre un et trois implants métalliques et entre six et huit composants Formlabs. Les instruments de Formlabs sont donc vraiment essentiels pour la plupart de nos activités.
Ben Wesorick, Vice President of Patient Specific Engineering, restor3d
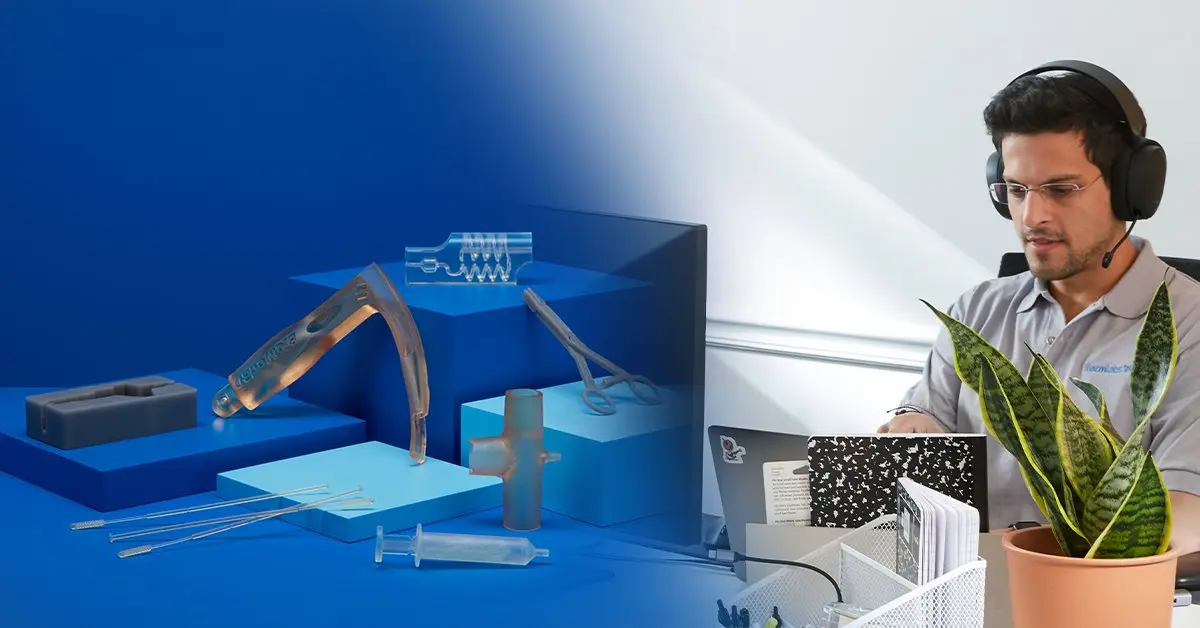
Discutez avec notre équipe commerciale médicale
Que vous deviez fabriquer des outils chirurgicaux adaptés aux patients ou un prototype de dispositif médical cardiaque, nous sommes là pour vous aider. L'équipe de Formlabs Medical est composée de spécialistes dévoués qui savent exactement comment vous soutenir et répondre aux besoins de votre entreprise.
Rapide, précis et facilement adaptable
restor3d dispose d'une gamme impressionnante d'imprimantes 3D métal qui permettent de créer des outils et des implants en alliages de cobalt, de chrome et de titane. Outre des imprimantes métal de grande taille, l'entreprise dispose d'un parc d'imprimantes de la série Form et d'autres machines à polymères.
Elena Tercheria, responsable de la fabrication additive, est spécialisée dans la production de pièces en polymère. Elle et son équipe s'appuient sur leur parc d'imprimantes Formlabs pour 90 % de leurs pièces en polymère, qu'il s'agisse d'instruments à usage unique ou de pièces sur mesure spécifiques au patient. Certaines d'entre elles sont imprimées à partir d'une résine spécialement formulée que les équipes chirurgicales peuvent voir sur les radiographies.
Lorsque Mme Tercheria et son équipe ont intégré la Form 4B, ils ont très vite compris que l'imprimante allait bouleverser leurs méthodes de travail, notamment en termes de vitesse d'impression. Mme Tercheria explique : « La vitesse de la Form 4B est comparable, voire supérieure, à celle des imprimantes DLP industrielles. »
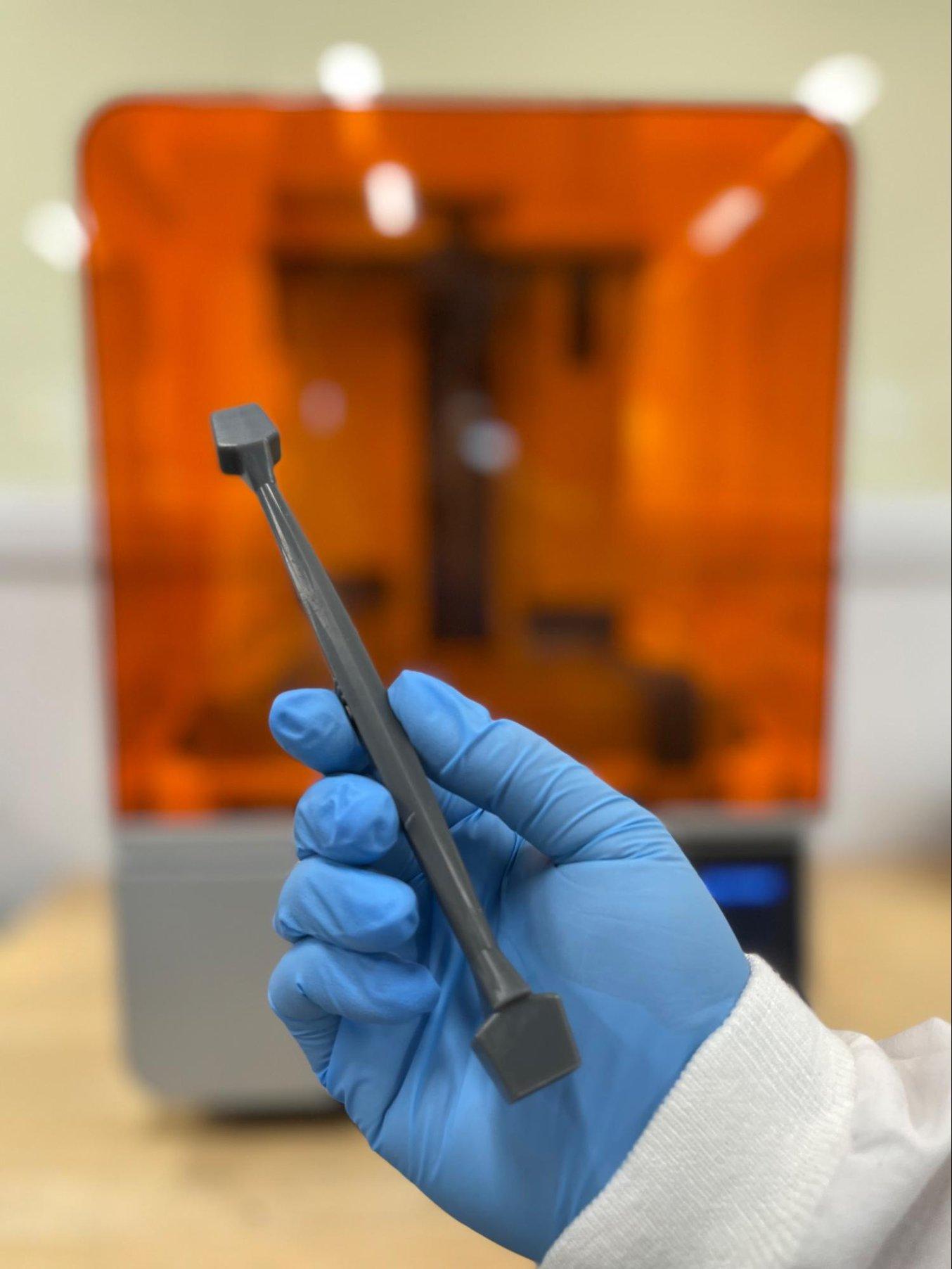
L'équipe de Mme Tercheria a constaté que les pièces imprimées sur la Form 4B ont des parois lisses, ce qui réduit le besoin de les post-traiter.
Lorsqu'on travaille avec des professionnels de la chirurgie qui se préparent à opérer, l'agilité est essentielle. « Parfois, des pièces se cassent avant d'être envoyées. Parfois, il faut envoyer des pièces supplémentaires. Parfois, un client demande simplement une nouvelle conception de la pièce. Le temps d'impression accéléré [de la Form 4B] nous aidera à réagir de manière beaucoup plus agile à de telles situations. » Le fait que certaines impressions puissent se terminer beaucoup plus rapidement détermine si les pièces seront envoyées le même jour ou finiront d'être imprimées pendant la nuit. En réduisant de deux heures la durée d'une impression, il est possible d'imprimer deux tâches dans le temps que d'autres imprimantes mettraient à en imprimer une, ce qui permet de doubler la capacité.
L'équipe de Mme Tercheria est ravie que la précision de l'affichage de la durée d'impression ait été améliorée sur la Form 4B. « Cela peut sembler futile, mais savoir combien de temps dure une impression libère de la main-d'œuvre pour des tâches plus importantes. Voir l'imprimante mélanger chaque couche tout en obtenant une réduction drastique du temps d'impression est vraiment impressionnant. C'est un pas de géant pour nous, car cela nous permet de planifier de manière fiable et d'anticiper la disponibilité des appareils. »
Pour ce qui est de la rapidité, le post-traitement est l'un des principaux facteurs qui détermine le délai d'exécution. Les pièces imprimées sur la Form 4B ont une finition de surface lisse et ont besoin de moins de supports, ce qui permet de gagner du temps et d'augmenter la précision de la production.
La réduction des structures de support signifie que moins de pièces doivent passer par le post-traitement, ce qui permet d'économiser du temps et des ressources.
Les imprimantes Formlabs sont une solution idéale pour le flux de travail unique de restor3d en raison de leur vitesse, de leur précision et de leur gamme d'options de matériaux. Un autre avantage est la possibilité d'évoluer à sa guise en ajoutant des imprimantes supplémentaires à son parc d'impression 3D au fil du temps. Les imprimantes de la série Form sont des machines prêtes à l'emploi qui permettent à restor3d d'accroître ses capacités de production en fonction de la demande, au lieu d'avoir à investir des capitaux de départ importants avec un long retour sur investissement. Deuxièmement, le fait qu'elle utilise la même machine et le même matériau au cours du processus de développement permet à l'équipe d'utiliser ses machines pour la production lorsque c'est nécessaire.
Pour être honnête, il n'y a presque pas de lignes de couche. Les parois latérales sont extrêmement lisses, presque comme si elles n'avaient pas été imprimées en 3D. »
Elena Tercheria, responsable de la fabrication additive, restor3d
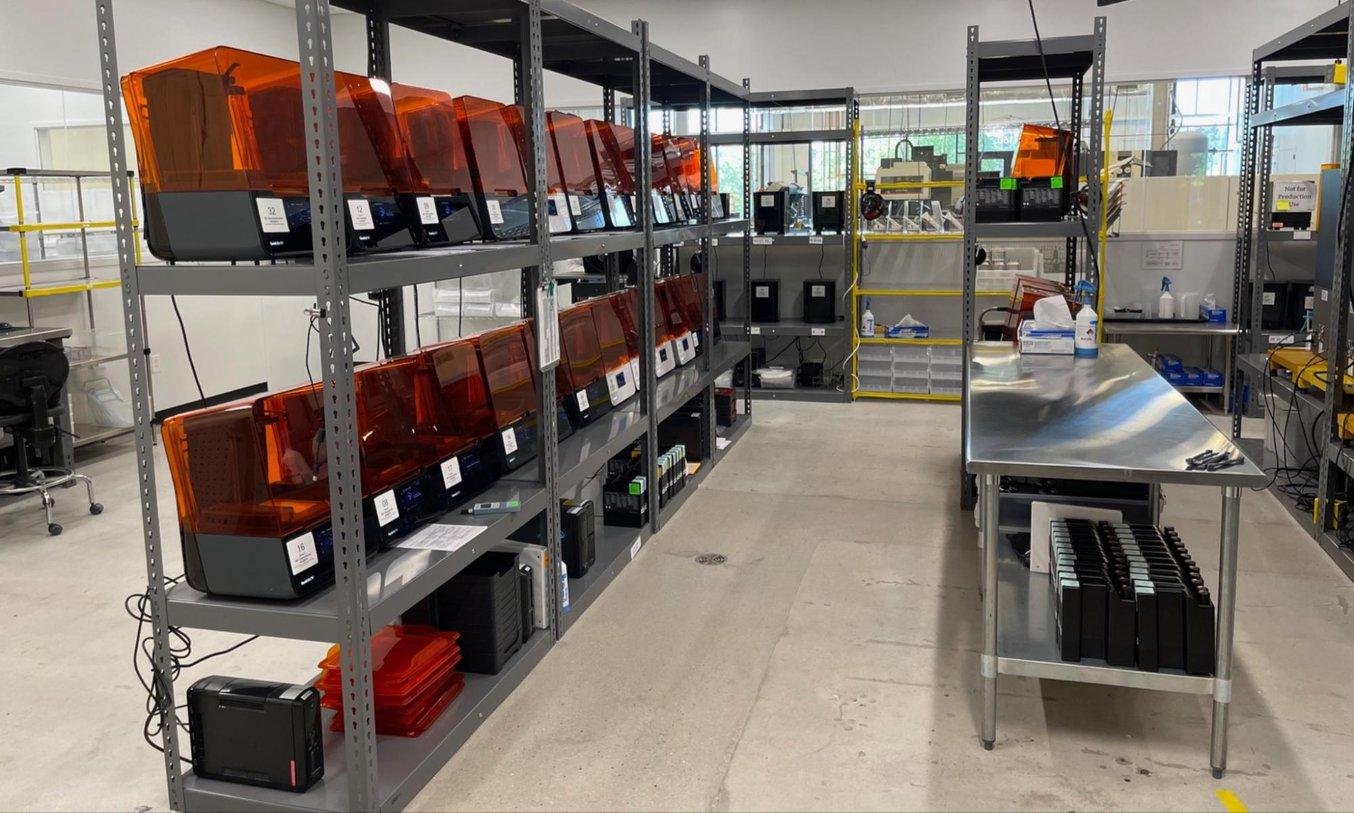
restor3d exploite un parc de 28 imprimantes 3D SLA Formlabs.
M. Kelly l'a résumé en disant : « Les deux raisons pour lesquelles nous sommes restés fidèles à Formlabs sont la flexibilité de la production et la capacité à s'adapter progressivement. L'investissement dans une imprimante Formlabs est nettement inférieur à celui d'un demi-million de dollars pour l'achat d'une imprimante métal. Ainsi, au fil du temps, nous pourrons continuer à augmenter notre parc de machines Formlabs en fonction de nos besoins, sans devoir dépenser de sommes extravagantes. »
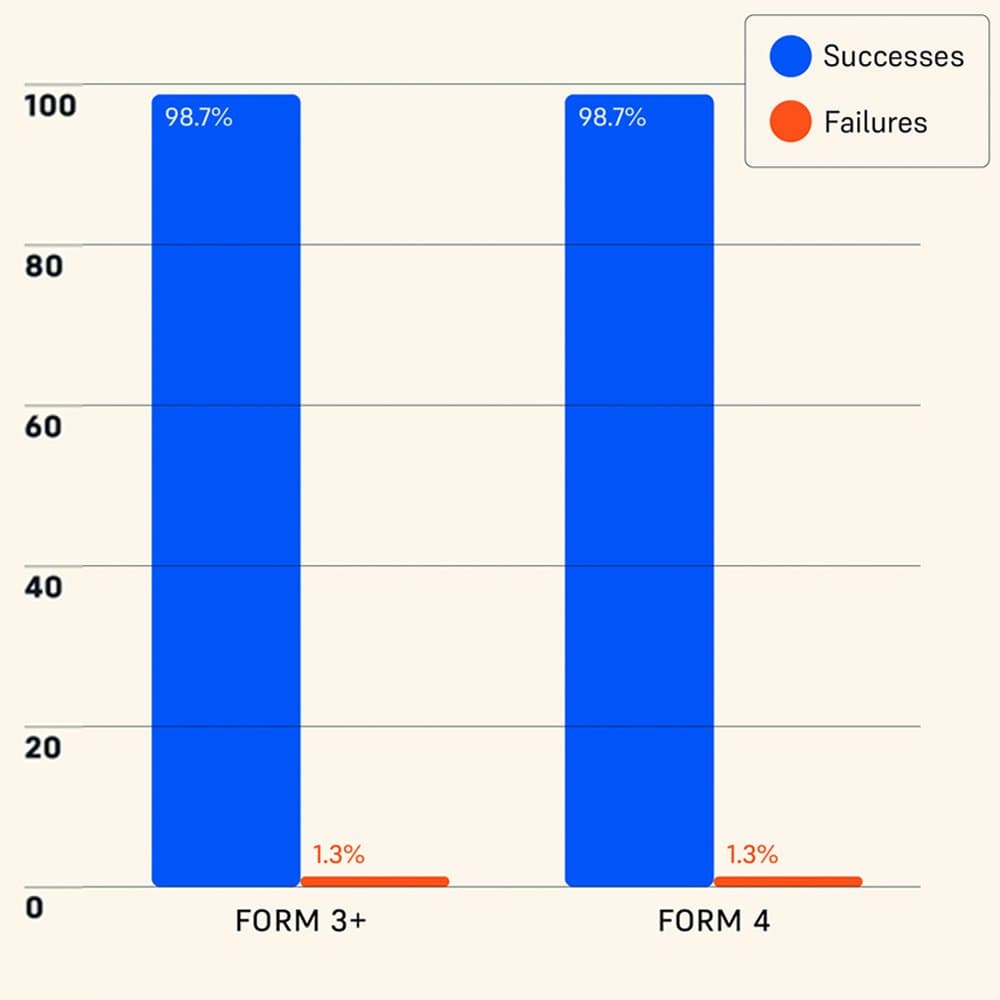
Fiabilité de la Form 4 et d’autres imprimantes 3D résine testées de manière indépendante
Une importante société indépendante de test de produits a mesuré un taux de réussite d’impression de 98,7 % pour la Form 4 de Formlabs. Lisez une description complète de la méthodologie d’essai et consultez les résultats dans notre livre blanc.
Des matériaux puissants
Les outils chirurgicaux de restor3d combinent des pièces en métal et en polymère qui remplacent les instruments en acier inoxydable que de nombreux chirurgiens ont utilisés pendant toute leur carrière. L'équipe d'ingénieurs évalue la gamme de matériaux afin de trouver un polymère capable de supporter des filets de vis et de résister à une procédure chirurgicale après une stérilisation aux rayons gamma ou à la vapeur.
Formlabs propose une gamme de plus de 30 matériaux, dont une large gamme de matériaux biocompatibles destinés aux professionnels de la santé. M. Wesorick a constaté que les performances des résines avancées étaient impressionnantes : « La raison pour laquelle nous apprécions les résines de Formlabs, ce sont leurs caractéristiques inter-opératoires. Tout d'abord, elles sont résistantes. Elles nous permettent d'imprimer ce que nous voulons sans devoir nous soucier de l'amincissement ou de la rupture du matériau. Nous avons constaté qu'elles étaient assez résistantes pour des objets tels que les impacteurs, les outils de coupe et les guides de forage. Elles permettent donc aux chirurgiens d'avoir un très bon retour d'information tactile. Je dirais que l'autre avantage de ces matériaux pour nous est qu'ils ne demandent pas une phase de conception trop complexe. »
L'équipe de restord3d soumet chaque instrument et implant à des tests rigoureux afin de s'assurer que le produit livré aux chirurgiens est de la plus haute qualité et qu'il peut être utilisé même dans des environnements soumis à de fortes contraintes. Ils effectuent des tests de flexion, d'impact, de torsion et d'utilisation clinique simulée avec des chirurgiens pour s'assurer que leurs outils résisteront aux conditions d'une salle d'opération.
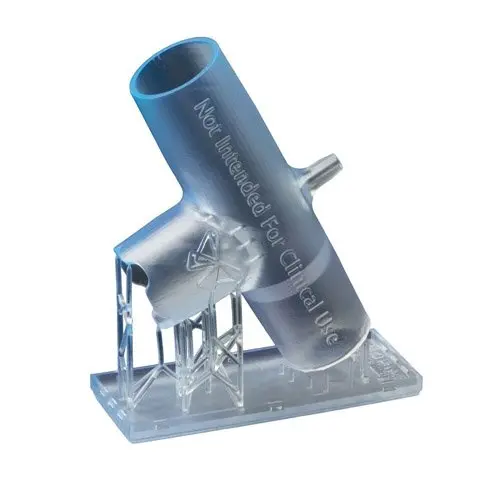
Commander un échantillon gratuit
Examinez et constatez par vous-même la qualité Formlabs. Nous enverrons un échantillon gratuit à votre bureau.
Liberté de conception
L'impression 3D résine de certains composants permet à l'équipe de restor3d d'essayer de nouvelles orientations, de nouveaux matériaux et de nouveaux types de caractéristiques de conception.
« Ce que nous apprécions vraiment dans l'utilisation des imprimantes Formlabs, c'est la flexibilité qu'elles nous offrent au niveau de la conception. Avec Formlabs, nous sommes presque toujours en mesure de répondre à la demande d'un chirurgien, ce qui n'est pas le cas avec les autres méthodes d'impression que nous utilisons », explique M. Wesorick.
Lors de la conception d'implants en titane, de nombreuses considérations liées à la conception pour la fabrication (DfAM) doivent être prises en compte, comme l'orientation de la plaque et tous les aspects liés à l'impression 3D.
« Par rapport à l'impression 3D du titane, Formlabs est beaucoup plus adaptée et nous permet d'être flexibles. L'un des avantages est que si nous ne pouvons pas produire une pièce en métal, il y a de fortes chances que nous puissions la fabriquer en résine et obtenir la fonction dont nous avons besoin grâce à la flexibilité du processus d'impression. »
Ben Wesorick, Vice-président de Patient Specific Engineering
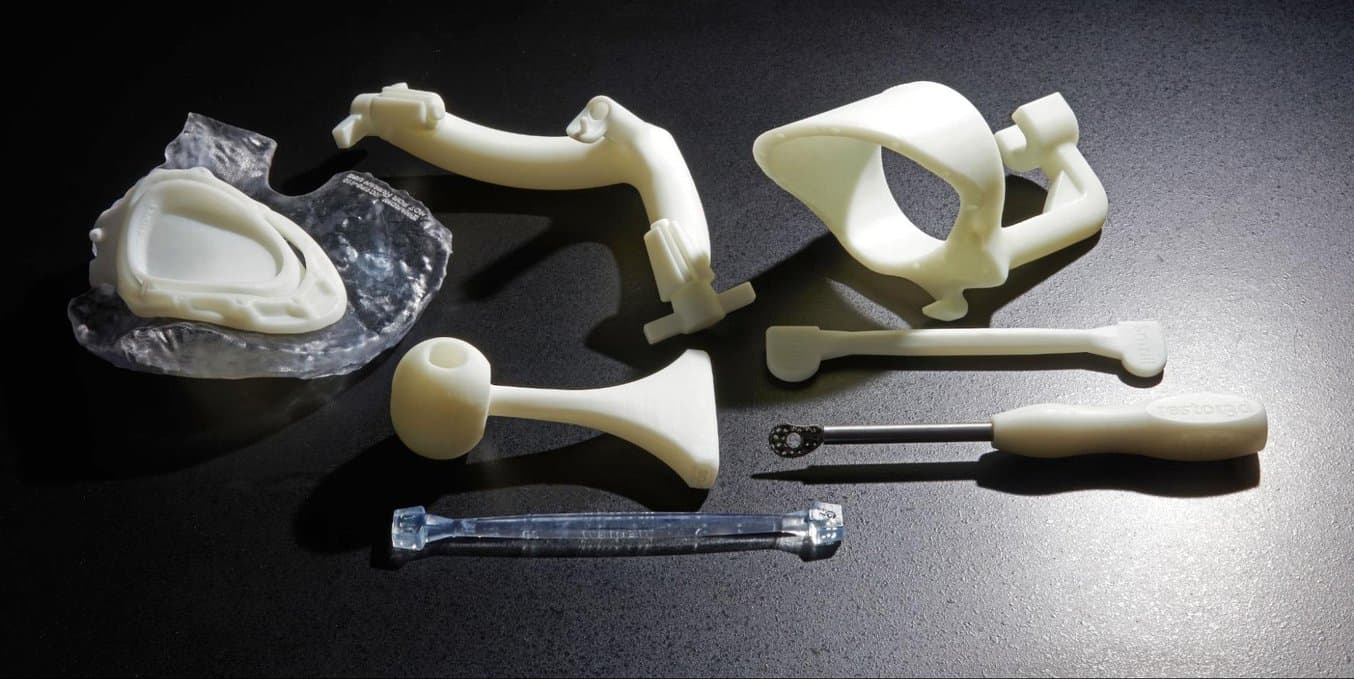
La liberté de conception offerte par l'impression 3D résine permet à restor3d de créer de nouvelles caractéristiques de conception complexes, telles que des coupes rondes ou des coupes géométriques très précises dans l'os, avec moins d'exposition et de dissection.
Biocompatible
Pour réduire encore les coûts et les délais de commercialisation, Formlabs propose aux fabricants de dispositifs médicaux plusieurs matériaux SLA et SLS biocompatibles. Les résines BioMed de Formlabs sont conçues pour les professionnels de la santé qui recherchent des matériaux de qualité médicale pour des applications exigeant performance et biocompatibilité. Ces matériaux sont développés et fabriqués dans une installation certifiée ISO 13485 et sont compatibles avec les méthodes courantes de désinfection et de stérilisation.
M. Evans nous explique les avantages qu'il y a à travailler avec un fournisseur de matériaux doté d'un solide système de gestion de la qualité : « Lorsqu'un fournisseur dispose déjà d'approbations et de tests de biocompatibilité tels que les tests ISO 10993, c'est très utile, en particulier pour les petites entreprises qui souhaitent éviter les délais et coûts importants associés à ces tests. Le fait de disposer de ces tests nous permet à la fois de commercialiser nos produits plus rapidement et de ne devoir réaliser que certains tests précis. C'est un élément essentiel pour Formlabs. »
À suivre : résoudre des problèmes dans l'ensemble du corps humain
restor3d s'est imposé comme un leader dans l'utilisation de l'impression 3D pour booster l'innovation dans la salle d'opération. Leur kit de planification préopératoire de pointe, leurs implants très précis et innovants ainsi que la solution de bout en bout fournie par leur kit d'instruments ont aidé les hôpitaux à réduire leurs coûts et à améliorer l'expérience des patients.
M. Kelly pense que l'entreprise n'en est qu'à ses débuts : elle songe à créer des instruments pour les opérations du pied et de la cheville, ainsi que pour différentes opérations de la colonne vertébrale. D'autres applications orthopédiques telles que la traumatologie, les extrémités supérieures et la médecine sportive sont également envisagées. « Nous faisons tout pour disposer de l'infrastructure et des plateformes technologiques qui nous permettront de résoudre des problèmes sur l'ensemble du corps et dans plusieurs domaines de la médecine.
L'entreprise a récemment emménagé dans un immense complexe de bureaux flambant neuf pour l'aider à prendre de l'ampleur, tant au niveau de l'entreprise que de la production. Le nouveau bureau soutiendra la croissance des lignes de produits actuelles et permettra de développer de nouvelles spécialités.
M. Wesorick a conclu en disant : « Certaines entreprises combinent déjà l'impression 3D et l'orthopédie, mais très peu d'entre elles fabriquent leurs produits complètement en interne. Ce que l'internalisation nous permet de faire, c'est d'améliorer nos produits et d'être les plus rapides sur le marché. C'est évidemment plus facile à dire qu'à faire, mais nos nouveaux bureaux vont vraiment nous permettre d'aller d'un bout à l'autre du processus, de la résine ou de la poudre à la pièce finie, ici, à Durham, en Caroline du Nord. »
Découvrez comment l'impression 3D peut être utilisée pour des applications médicales et explorez la gamme de matériaux médicaux biocompatibles de Formlabs.