Impression 3D de joints de connecteurs automobiles finaux en silicone
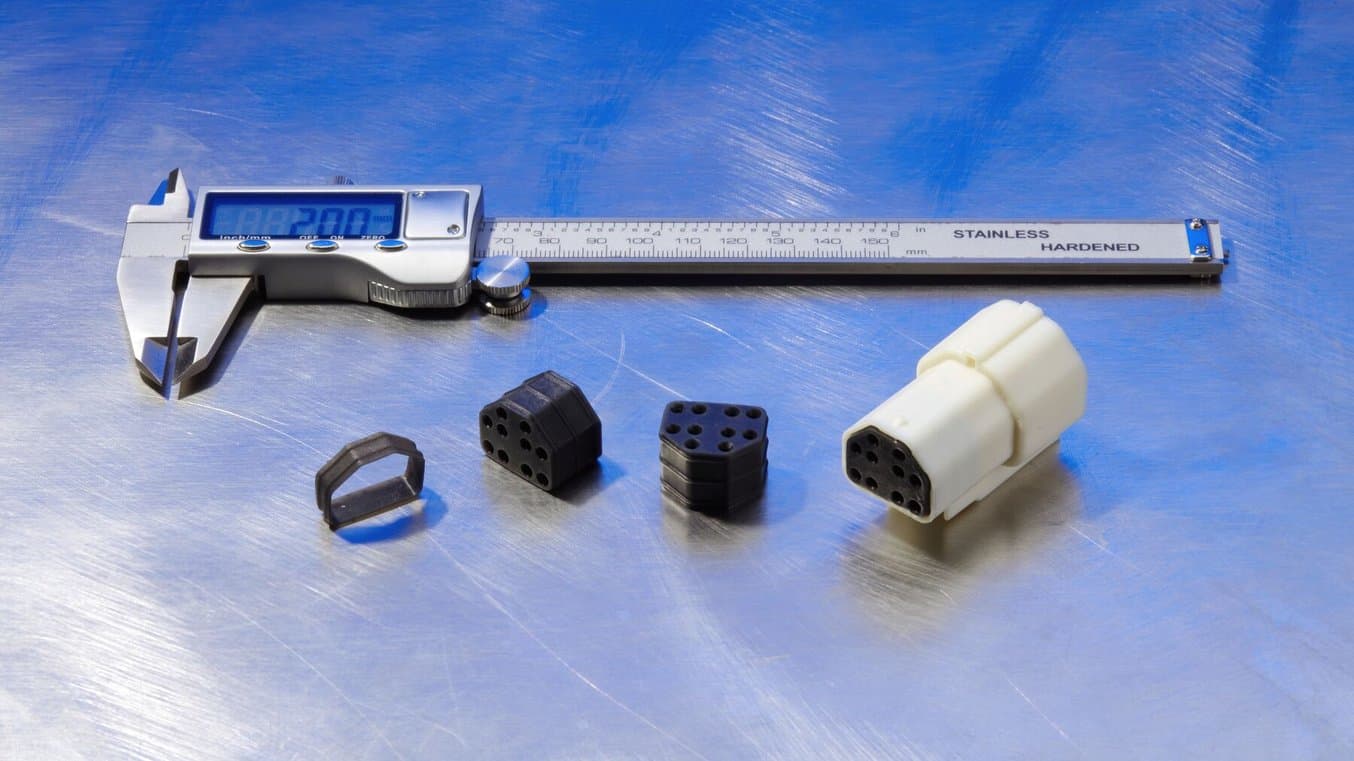
Joints de connecteurs de HGM Automotive Electronics imprimés en 3D avec Silicone 40A Resin.
HGM Automotive Electronics est un fabricant spécialisé qui conçoit et fournit des systèmes électroniques de pointe pour le marché secondaire de l'automobile.
Selon Guy Cardwell, directeur de la recherche et du développement chez HGM Automotive Electronics, le plus grand défi de l'entreprise est de trouver des pièces permettant d'entretenir ou de réparer leurs moteurs, étant donné que de nombreux véhicules sur lesquels ils travaillent sont des voitures anciennes. Les connecteurs et autres composants électriques sont de plus en plus difficiles à trouver, d'autant plus que la production des pièces originales s'arrête progressivement.
Ils se sont tournés vers l'impression 3D pour le prototypage et la production de petites séries, car il s'agit de la meilleure option pour fabriquer des pièces à la demande en interne. Toutefois, il s'agit d'une industrie réglementée qui doit respecter des exigences spécifiques telles que l'indice de protection (IP) et la résistance aux produits chimiques, d'où l'importance du choix du matériau. Le matériau le plus couramment utilisé pour les joints de connecteurs automobiles est généralement le silicone souple, mais les possibilités de production sont vraiment très limitées. Si le moulage par injection est trop coûteux pour produire de petites séries, le moulage traditionnel de silicone prend quant à lui beaucoup de temps.
Depuis l'introduction de Silicone 40A Resin, le premier matériau d'impression 3D accessible 100 % en silicone pour des pièces souples, flexibles et durables, M. Cardwell déclare avoir trouvé « exactement ce qu'il leur fallait. » Grâce à des essais chimiques et mécaniques rigoureux, ils ont démontré que ce nouveau matériau possède d'excellentes propriétés mécaniques et une résistance aux produits chimique parfaite pour des pièces automobiles finales. L'entreprise a participé au programme bêta pour les nouveaux matériaux et les a utilisés pour le prototypage, mais son objectif principal est à présent de commencer à produire de petites séries de pièces finales.
« Silicone 40A Resin est parfaite. Elle ressemble beaucoup au matériau original qui aurait été utilisé par le fournisseur. »
Guy Cardwell, directeur de la recherche et du développement chez HGM Automotive Electronics
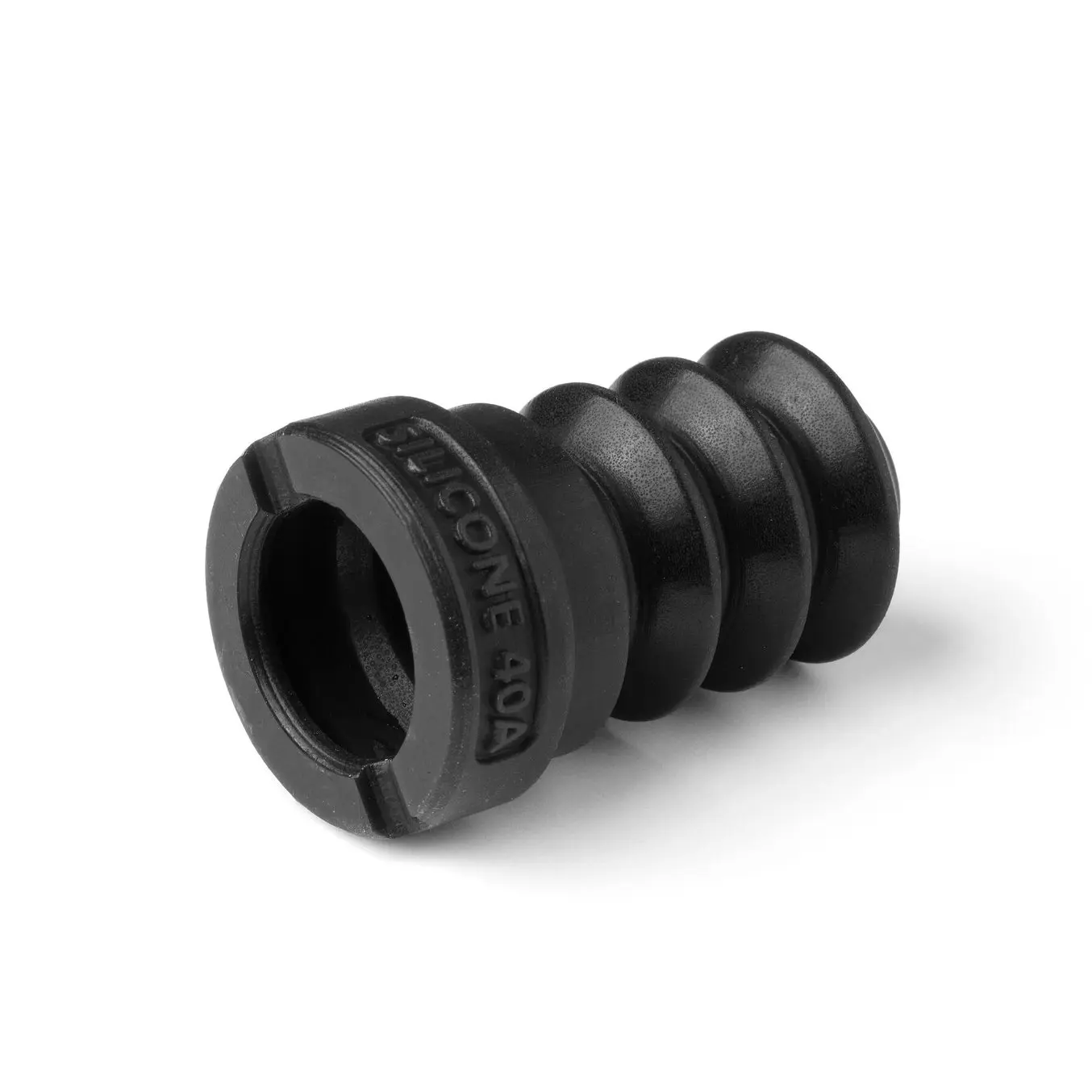
Commander un échantillon gratuit
Examinez et constatez par vous-même la qualité Formlabs. Nous enverrons un échantillon gratuit imprimé avec Silicone 40A Resin à votre bureau.
Améliorer le design d'un joint de connecteur avec Silicone 40A Resin
Méthode comparée | Avantages de l'impression 3D avec Silicone 40A Resin |
---|---|
Sous-traitance du moulage par injection | Réduction du délai d'exécution de 90 % Réduction des coûts de 98 % |
Moulage de silicone en interne | Géométries complexes et exigeantes avec une résolution fine des caractéristiques Réduction de la main-d'œuvre, des risques d'erreur et des délais d'exécution Reproduisible et adaptable pour 10 à 1000 unités de production |
Après que ses connecteurs électriques ont rencontré un franc succès, HGM Automotive a commencé à expérimenter des joints d'étanchéité sur mesure. Il s'agit de composants difficiles à fabriquer, que l'on trouve rarement sur le marché et qui, le cas échéant, sont généralement de très mauvaise qualité. Faute d'un matériau élastomère suffisamment souple, il est difficile de développer des joints sur mesure pour les connecteurs. On pourrait certes fabriquer un moule à injection et utiliser un uréthane très souple pour produire ces pièces. L'inconvénient, c'est que ce moule coûterait entre 6000 et 10 000 €. Le coût serait justifié si l'entreprise avait besoin de 10 000 de ces pièces, mais la réalité est plus proche de 100 à 1000 pièces par an. En outre, une fois le moule réalisé, il est pratiquement impossible de modifier le design. Cela représente un véritable obstacle, en particulier pour les joints de connecteurs qui ont tendance à présenter des formes compliquées. « Il s'agit simplement d'une question de coût et de flexibilité », explique M. Cardwell.
Délai de production | Coût | |
---|---|---|
Sous-traitance du moulage par injection | 3 à 4 semaines | 10 000 € pour l'outillage 0,5 € par pièce |
Impression 3D avec Silicone 40A Resin en interne | 6 heures pour 25 pièces | 1 – 2 € par pièce |
Pour un volume de production de 100 unités de joints de connecteurs, HGM Automotive a réduit ses coûts de 98 % et ses délais de 90 %.
Au départ, les joints des connecteurs étaient imprimés avec Elastic 50A Resin de Formlabs, mais même ce matériau n'était pas assez flexible. Comme l'ajoute M. Cardwell, puisque les connecteurs sont assemblés manuellement, les fabricants de faisceaux de câbles mettent généralement deux à trois fois plus de temps à assembler un connecteur avec un matériau plus dur comme l'uréthane qu'avec un joint en silicone, « simplement parce qu'ils doivent travailler contre le matériau. »
Une autre option consistait à se tourner vers un moulage de silicone ordinaire, ce qu'ils ont déjà fait par le passé pour d'autres pièces. Cependant, ce connecteur est conçu pour que neuf fils pénètrent dans le joint, ce qui rend le design très complexe. Il présente des trous et une géométrie qui rendraient le démoulage difficile et, dans l'ensemble, un niveau de détail qui nécessite la précision de l'impression 3D.
« Il est possible de le fabriquer par moulage, mais il faut être extrêmement prudent [avec les géométries complexes,] et cela prend beaucoup de temps. Le simple fait de pouvoir l'imprimer en 3D par lots est donc un énorme avantage par rapport à tous les autres processus. »
Guy Cardwell, directeur de la recherche et du développement chez HGM Automotive Electronics
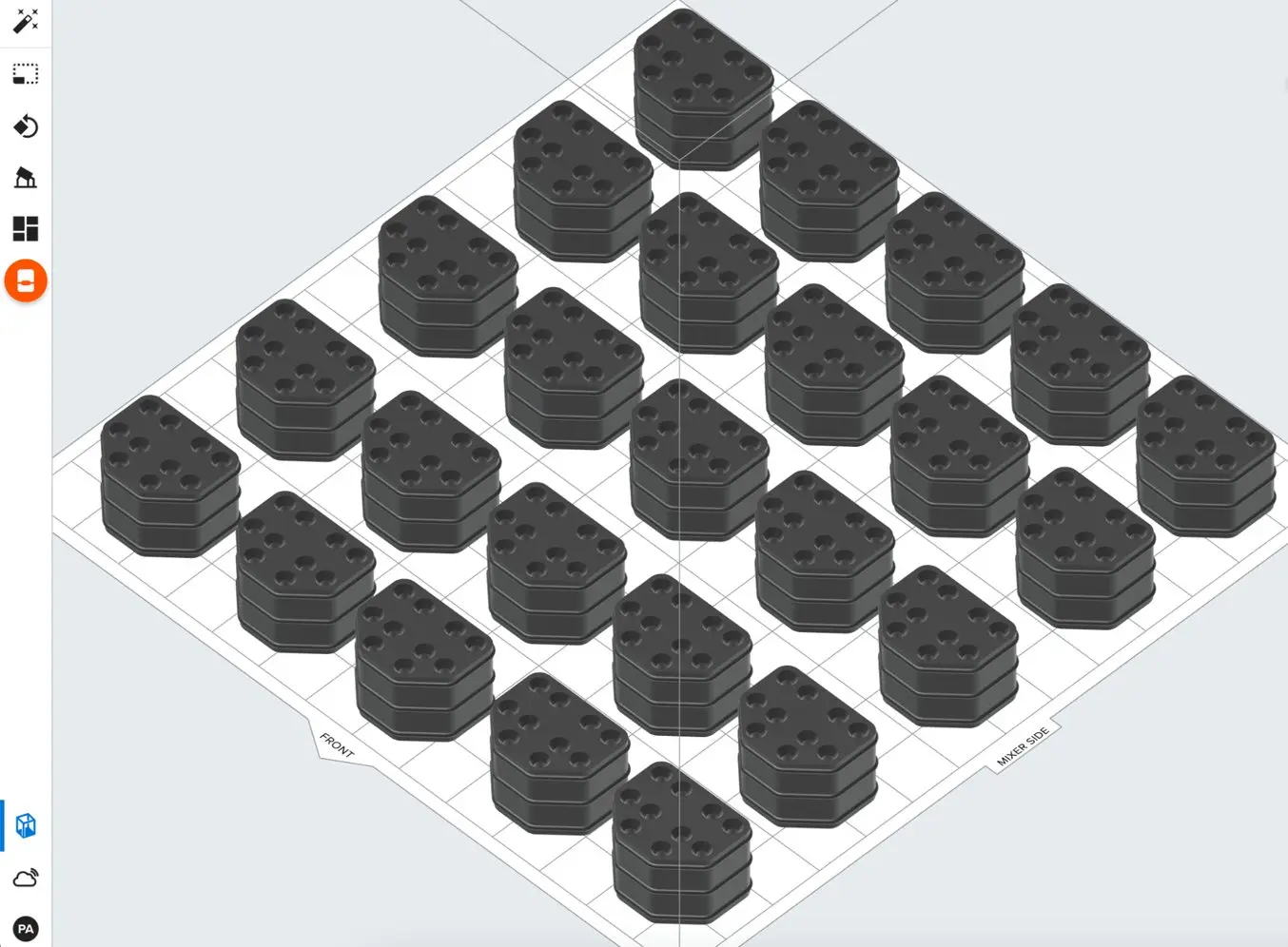
Fichier CAO des joints de connecteur de HGM Automotive Electronics chargé dans le logiciel PreForm. Neuf fils pénètrent dans le joint, qui fait environ un centimètre d'épaisseur. Comme il s'agit d'une géométrie complexe avec des détails fins, l'outillage requis par le moulage par injection ou le moulage de silicone est compliqué à réaliser. Les 25 connecteurs s'impriment en 4 heures et 30 minutes sur la Form 3+.
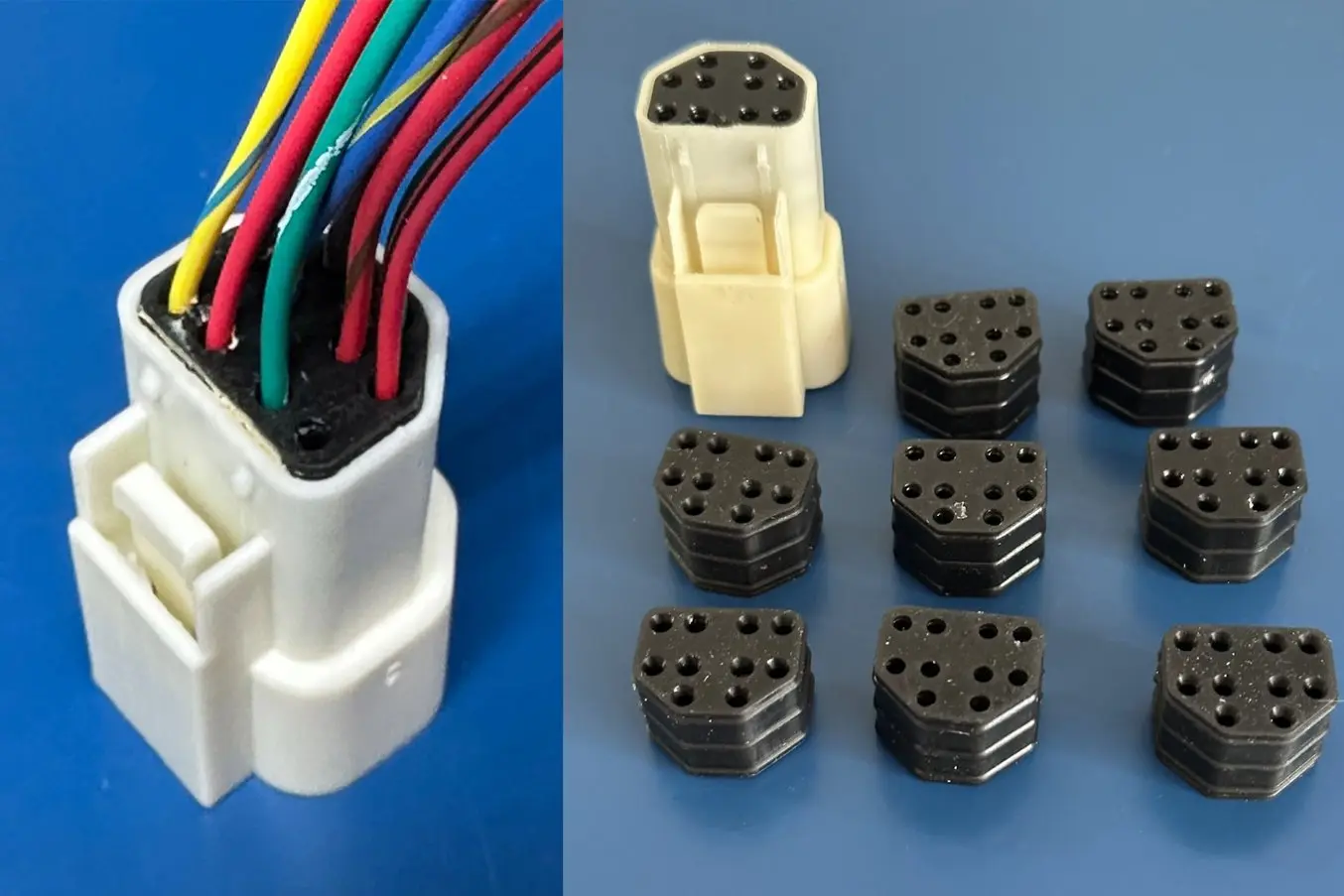
Joints de connecteurs imprimés et assemblés avec un boîtier et des composants électroniques.
« C'est vraiment un matériau idéal, parce qu'il ressemble beaucoup au matériau de production. »
Guy Cardwell, directeur de la recherche et du développement chez HGM Automotive Electronics
Silicone 40A Resin permet à HGM d'intégrer en interne tous les processus de fabrication pour la production de petites séries, et sa polyvalence représente également un grand avantage pour l'entreprise. L'équipe prévoit d'ores et déjà d'autres applications que des joints de connecteurs. Le principal avantage du nouveau matériau réside dans sa grande ressemblance avec le matériau de production final : il offre des propriétés idéales pour les applications de HGM Automotive Electronics, notamment en termes d'élasticité, de résistance à la déchirure et de flexibilité.
« Silicone 40A Resin me donne la possibilité d'explorer de nouveaux marchés et de fabriquer des pièces qui ne pouvaient auparavant être réalisées qu'avec un processus de moulage très coûteux et fastidieux. D'autres imprimantes 3D peuvent certes utiliser des matériaux élastiques, mais seules les imprimantes SLA Formlabs et Silicone 40A Resin peuvent réaliser des joints de connecteurs souples dont la qualité et la durabilité sont comparables à celles d'une pièce moulée en silicone ou en TPU. »
Guy Cardwell, directeur de la recherche et du développement chez HGM Automotive Electronics
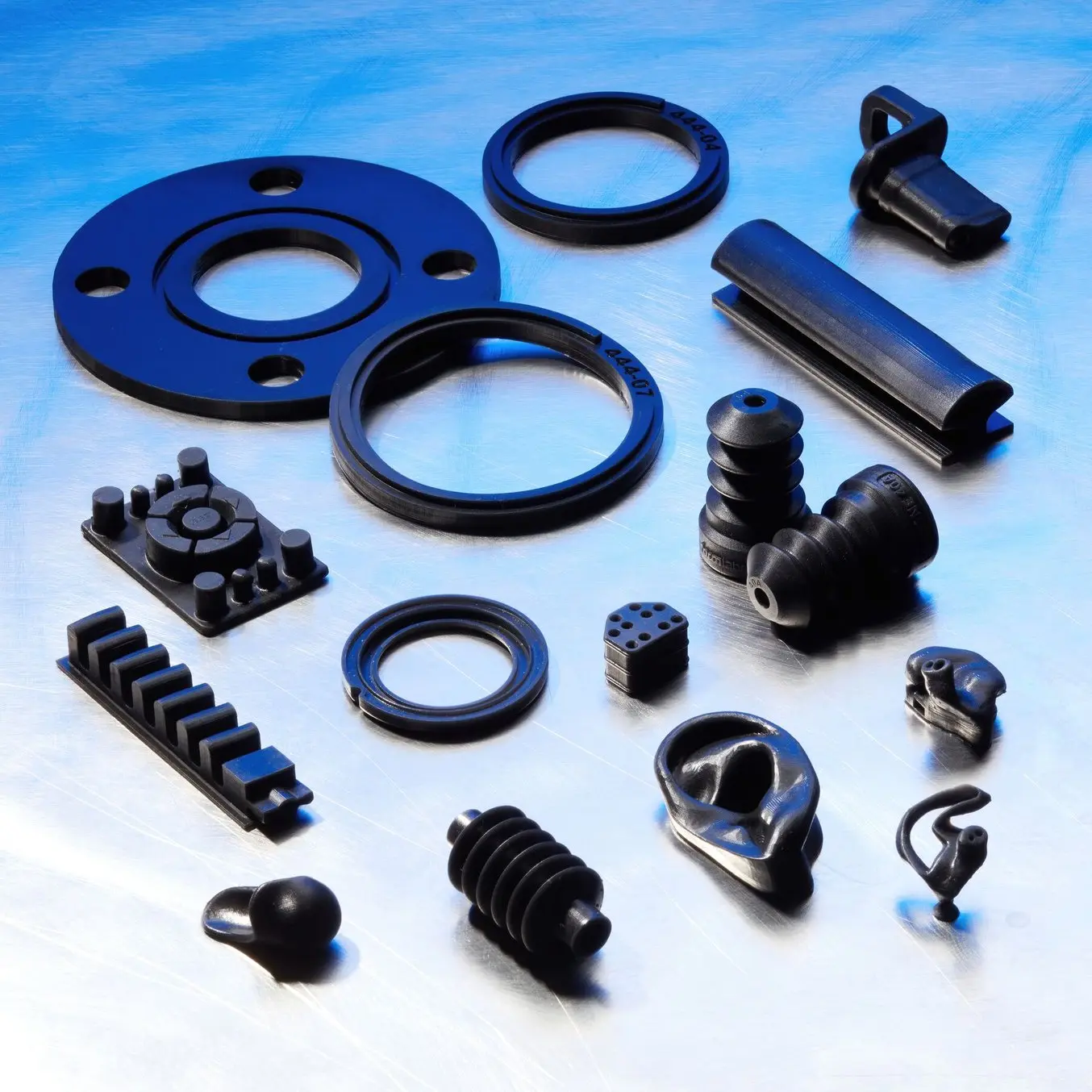
Présentation de Silicone 40A Resin
Au cours de ce webinaire, nos experts en impression 3D vous expliqueront les principaux avantages et applications de Silicone 40A Resin, et vous présenteront les flux de travail ainsi que les propriétés de ce matériau.
Du test à la confirmation : Silicone 40A Resin répond aux exigences du secteur en matière de résistance thermique et chimique
« Silicone 40A Resin possède toutes les propriétés nécessaires en termes de souplesse et de maniabilité dont nous avons besoin pour cette application. Lors de nos essais, la résistance chimique a jusqu'ici été conforme à ce que nous aurions attendu d'un silicone moulé utilisé pour cette application. »
Guy Cardwell, directeur de la recherche et du développement chez HGM Automotive Electronics
Dans les applications automobiles, il faut généralement des joints étanches capables de résister à une profondeur d'un, deux ou trois mètres, en fonction de l'application. En outre, des exigences en matière de résistance chimique s'appliquent à tous les fluides automobiles standard, dont les principaux sont l'eau, l'huile et le liquide de transmission. Pour tester les pièces, M. Cardwell a imprimé plusieurs échantillons et les a testés dans le compartiment moteur de sa voiture. Les échantillons de silicone imprimés ont été laissés dans le compartiment moteur dans des conditions de fonctionnement normales afin de tester leur résistance à la température et aux produits chimiques pendant plus de six semaines.
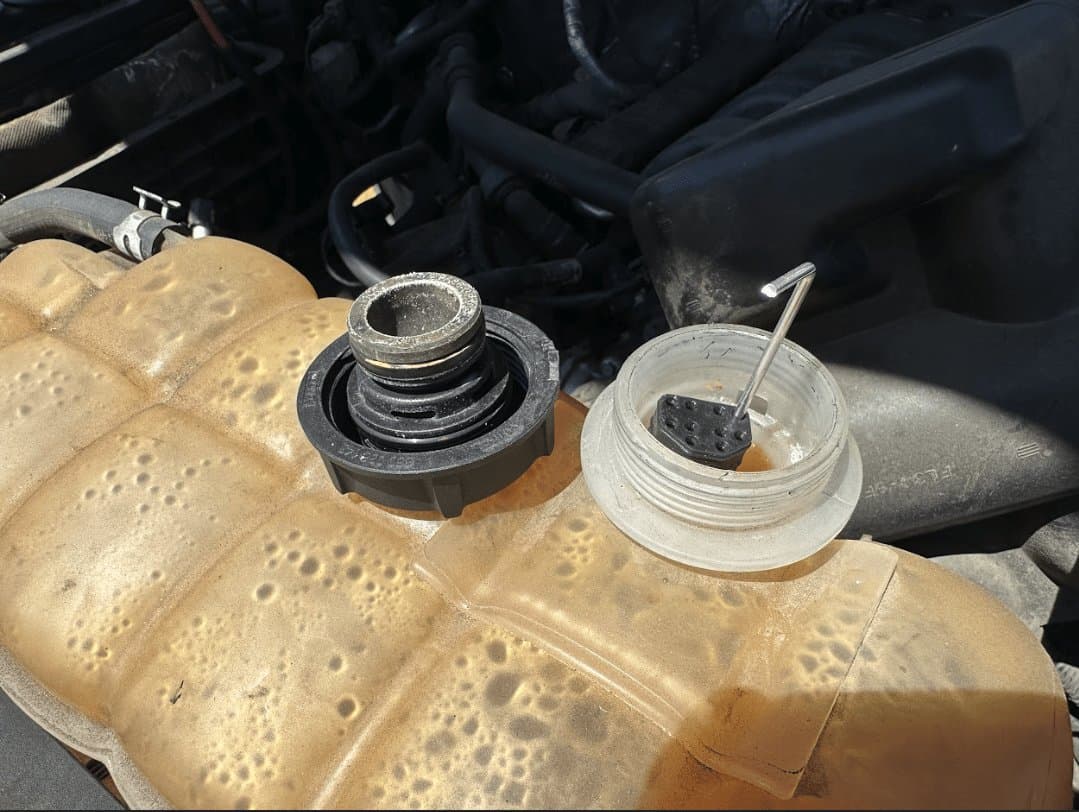
Les joints de connecteurs imprimés en 3D avec Silicone 40A Resin sont testés sur le terrain par HGM Automotive Electronics à l'intérieur d'un réservoir de liquide de refroidissement.
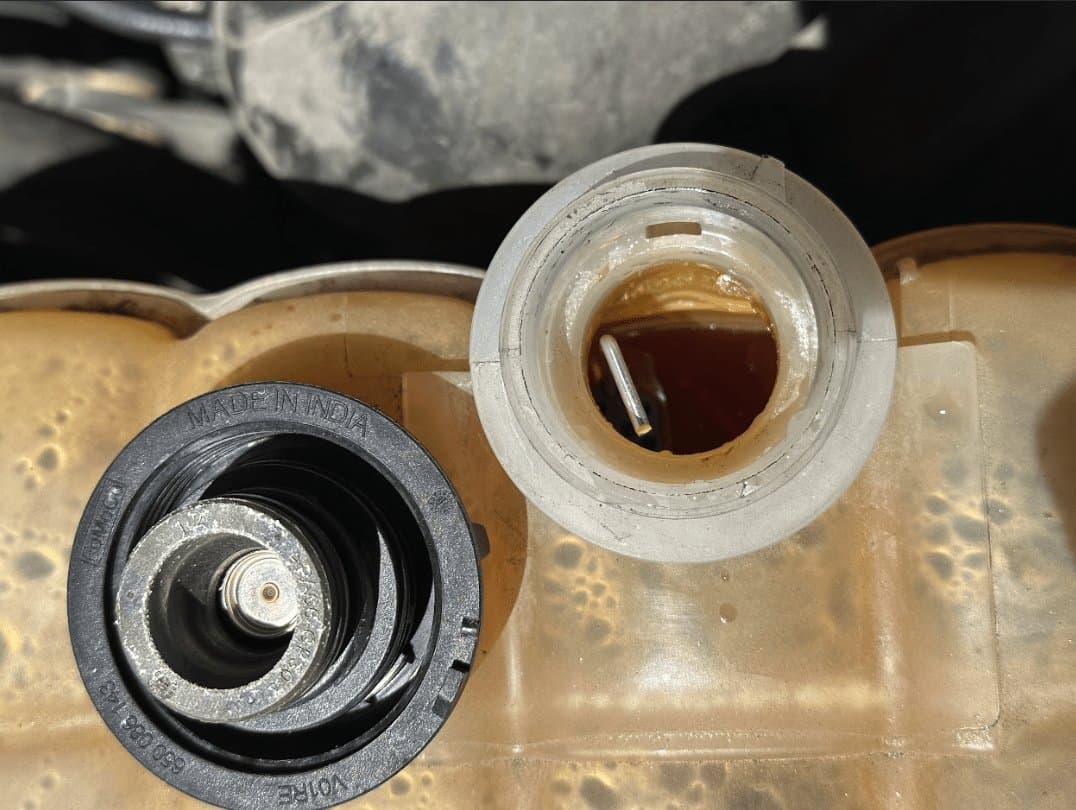
« Nous les avons laissés dans différents fluides pour tester la température. Nous avons effectué des tests avec de l'eau, et des tests statiques avec du liquide de transmission et de l'antigel », explique M. Cardwell. Il ajoute que « le principal liquide que ces joints empêchent d'entrer est généralement l'eau. » Après six semaines de cycles thermiques et d'expositions à divers fluides, M. Cardwell a pu confirmer l'étanchéité et la résistance à la température de Silicone 40A Resin. La température des composants électroniques de voitures peut aller de -40 °C à 105 °C. Avec sa température de transition vitreuse (Tg) à -107 °C et sa résistance à la température entre -25 °C et 125 °C, Silicone 40A Resin répondait parfaitement à leurs besoins en matière de résistance à la température. « J'ai procédé aux essais en partant du principe que ce matériau se comporterait de la même manière qu'un silicone moulé par injection », ce qui a été le cas. Les propriétés de Silicone 40A Resin ont répondu à toutes les attentes : elle a donc bien mérité sa place dans la gamme de matériaux de HGM.
Après avoir effectué des tests approfondis sur le terrain, l'équipe de HGM est très satisfaite de sa nouvelle résine 100 % silicone et de la façon dont elle répond à ses besoins. Ils ont l'intention de l'utiliser pour produire des joints de connecteurs finaux et comptent en fabriquer entre 500 et 1000 unités par an. M. Cardwell envisage d'utiliser la résine dans d'autres domaines et ajoute qu' « il y a au moins quatre produits pour lesquels ce matériau serait parfait, rien qu'au niveau des connecteurs ».
HGM Electronics : des innovations pour l'avenir
Silicone 40A Resin a donné à HGM Automotive la flexibilité de développer des conceptions qui ne pouvaient jusqu'ici être réalisées qu'avec des processus coûteux et chronophages, ce qui lui a permis d'explorer de nouveaux marchés.
« Je me souviens d'avoir distribué [des échantillons de pièces] aux différents employés de l'entreprise et tout le monde s'est exclamé : " Comment vous avez fait ça ? " Ce matériau nous intéresse donc au plus haut point. Et on ne sait pas quelles seront ses applications futures tant qu'on n'expérimente pas : ce n'est qu'alors qu'on comprendra vraiment son potentiel. Je ne pense pas que nous allons nous cantonner aux seuls connecteurs. Nous l'utiliserons pour un tas d'autres choses. Je n'ai aucun doute là-dessus. »
Guy Cardwell, directeur de la recherche et du développement chez HGM Automotive Electronics
M. Cardwell se réjouit de pouvoir dire à ses clients qu'il peut produire des pièces personnalisées en caoutchouc souple. Il envisage de développer différents types de joints et de sceaux sur mesure, ainsi que de nouvelles bottes isolantes en silicone pour des applications haute tension, que vous pouvez voir ci-dessous.

Capuchons de bougies d'allumage imprimés avec Silicone 40A Resin.
« Vous me demandez si je sais ce que je compte faire demain avec les silicones imprimés en 3D ? Non, mais j'ai hâte de le découvrir. »
Guy Cardwell, directeur de la recherche et du développement chez HGM Automotive Electronics