Comment Flame Retardant Resin ouvre de nouvelles possibilités pour Avance Design
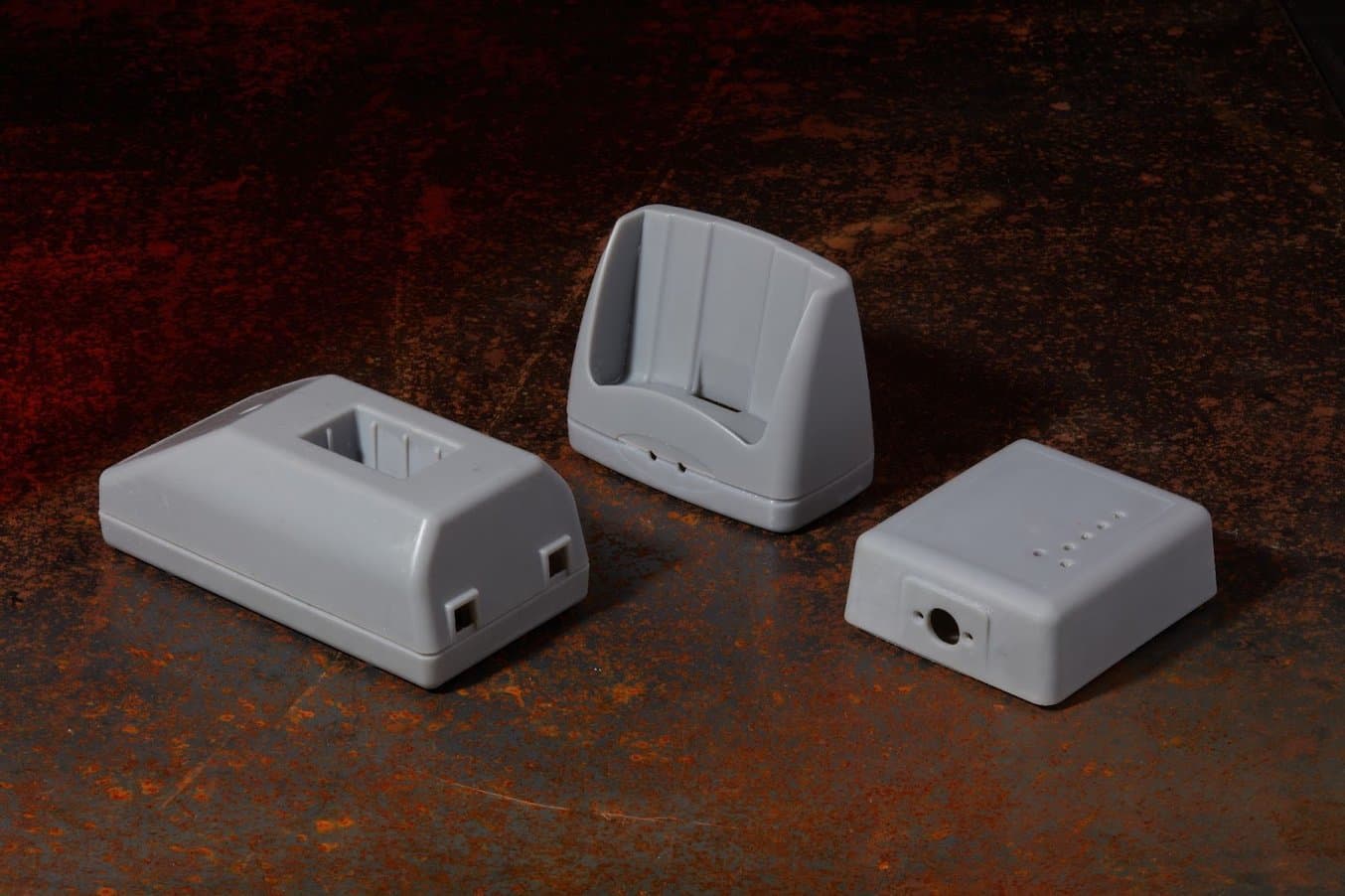
Avance Design, une société de conseil en ingénierie et en développement de produits située à Indianapolis dans l'Indiana (États-Unis), utilise l'impression 3D depuis plus de vingt ans. Chaque nouveau matériau d'impression 3D mis sur le marché lui ouvre de nouvelles possibilités.
Outre le moulage, l'usinage et l'impression FDM, Avance utilise trois imprimantes SLA Form 3+ et deux Form 3 pour développer des produits destinés aux secteurs de la médecine, de la robotique, de l'architecture et de l'électronique. Depuis que la compagnie utilise la nouvelle Flame Retardant Resin de Formlabs, Avance a raccourci son cycle de développement et réduit les coûts et la main-d'œuvre associés à la production de pièces certifiées UL 94.
Tony Parker, directeur d'Avance, nous a parlé de la production de petites séries, de la personnalisation de masse et d'une série de pièces réussie pour un client grâce à Flame Retardant Resin.
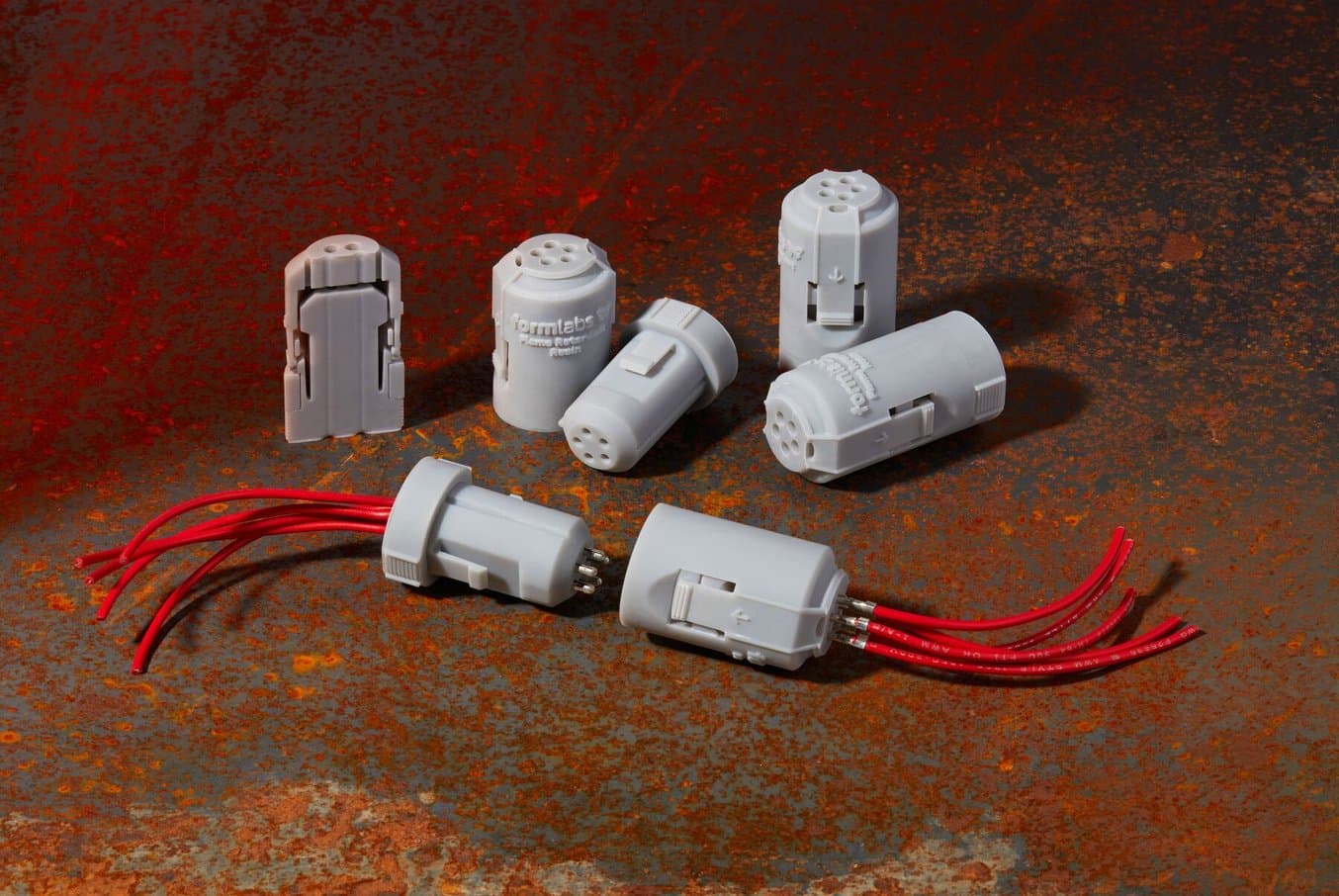
Comment Flame Retardant Resin ouvre de nouvelles possibilités pour Avance Design
Découvrez comment vous pouvez utiliser Flame Retardant Resin pour imprimer facilement en 3D des pièces ignifugées, rigides et capables de résister à la chaleur ou au fluage qui peuvent être utilisées à long terme dans des environnements intérieurs et industriels avec des températures élevées ou des sources d'inflammation.
Des séries de pièces directement imprimées en une semaine au lieu de trois
L'un des clients d'Avance Design est Energy Access, un fabricant de solutions personnalisées de chargement de batteries pour des équipements électroniques dans les secteurs de la médecine, de la défense, de l'industrie lourde, de la sécurité et de la robotique. Energy Access fait appel à l'équipe d'Avance pour l'aider à concevoir des solutions de recharge adaptées à des batteries fabriquées sur mesure. « Mon travail consiste à concevoir un boîtier permettant d'abriter et de protéger la batterie, et à concevoir une pochette permettant de la connecter à la solution de chargement », explique M. Parker.
Pour Avance, la conception et le développement de produits pouvant s'intégrer à des équipements personnalisés est la partie la plus facile. Les problèmes surviennent lorsqu'il s'agit de faire correspondre les propriétés des matériaux de la pièce imprimée en 3D avec ceux des composants produits en série et moulés par injection.
Energy Access a fait de la certification UL 94 une norme pour l'ensemble de l'entreprise, afin de se prémunir contre tout risque d'incendie. Avance doit donc être en mesure de fournir des pièces répondant parfaitement à ces standards. « Nous souhaitions que nos matériaux présentent les mêmes propriétés pour que nos pièces soient mieux adaptées à leur assemblage final et pour faciliter l'intégration de ces caractéristiques mécaniques dans leur produit final », explique M. Parker.
Pour obtenir ces propriétés matérielles (résistance, surface lisse et respect de la norme d'inflammabilité UL-94), Avance devait auparavant mouler des pièces en polyuréthane. M. Parker imprimait en 3D ou usinait un modèle de moule, fabriquait un moule en silicone autour de celui-ci, trouvait un polyuréthane classé UL disponible dans le commerce et le coulait dans le moule en silicone, puis extrayait la pièce en polyuréthane coulée et la post-traitait. « Cela prenait plusieurs jours pour chaque pièce, et si nous devions en commander 20, cela prenait environ trois semaines », explique M. Parker.
Désormais, grâce à Flame Retardant Resin de Formlabs, M. Parker peut supprimer de nombreuses étapes et passer de la conception CAO à la pièce finie beaucoup plus rapidement. « Le fait de pouvoir imprimer directement en 3D cette pièce en Flame Retardant Resin permet de réduire les délais à une semaine à peine pour l'ensemble des 20 pièces », explique M. Parker.
Comparaison des méthodes de fabrication d'un boîtier en Flame Retardant Resin
Étapes | Délai de production pour 20 pièces | Coût par pièce | |
---|---|---|---|
Flame Retardant Resin, SLA | Impression, lavage, post-polymérisation, retrait des supports, peinture | 4 – 5 jours | 19,80 $ (6,50 $ pour les matériaux, 13,30 $ pour la main-d'œuvre*) |
Filament FDM | Impression, dissolution des supports, nettoyage, ponçage, apprêt, peinture | 5 – 6 jours | 42 $ (7 $ pour les matériaux, 35 $ pour la main d’œuvre*) |
Moulage de polyuréthane | Impression, lavage, post-polymérisation, retrait des supports, remplissage des moules en silicone, moulage, nettoyage, peinture | 21 jours | 85 $ (25 $ pour le modèle, le moule et l'uréthane, 60 $ pour la main-d'œuvre*) |
Moule d'injection traditionnel | Sous-traiter l'outillage et le moulage | 20 – 30 jours | 250 $ (5 000 $ d'outillage, 0,50 $ par pièce ensuite) |
*Labor costs are calculated at $80/hour.
Finition de surface et usinabilité
Ce flux de travail plus court a eu un impact sur le processus de développement de M. Parker, mais ce n'est pas le seul avantage. Après tout, l'impression 3D FDM propose depuis des années des matériaux certifiés UL. Les pièces devaient présenter une finition de surface de qualité, sans les lignes de couche que l'on trouve sur les pièces imprimées avec des imprimantes FDM. « J'ai été très impressionné par la qualité de la surface obtenue avec Flame Retardant Resin. Les pièces ont presque l'air d'avoir été recouvertes d'une couche d'apprêt, et elles se poncent comme telles. Il est facile de les post-traiter et de les peindre, ce qui est un réel avantage pour nous », déclare M. Parker.
L'équipe d'Avance doit également s'assurer que ces pièces peuvent faire partie d'un assemblage plus important, ce qui nécessite qu'elles puissent accueillir des inserts vissés. « Les inserts à enfoncer ont des paramètres spécifiques, mais nous avons simplement suivi les recommandations relatives à la taille de trou souhaitée, puis nous avons utilisé une petite presse pour remplir un insert de base, et la pièce a très bien résisté. Il n'y a eu aucun problème, et les pièces imprimées ont très bien accueilli les inserts », déclare M. Parker.
Cette facilité d'intégration fait toute la différence pour les processus d'assemblage en aval de la chaîne. M. Parker peut compter sur les pièces imprimées avec les produits Formlabs pour passer les tests UL, obtenir les mêmes résistance et qualité de surface que le reste du chargeur de batterie, et intégrer systématiquement des fixations filetées. Bien qu'elles soient imprimées en 3D, les pièces en Flame Retardant Resin peuvent s'intégrer sans problème dans les méthodes d'assemblage de ses clients. « Les membres de l'équipe d'Energy Access ont été très impressionnés : ils ne voulaient pas recourir à l'impression FDM ou au moulage pour obtenir des pièces ignifugées. Ils ont aimé l'idée de développer, d'apporter des modifications et de pouvoir conserver le même matériau tout au long du processus de conception et de fabrication », explique M. Parker.
Pouvoir imprimer en 3D une pièce qui simule un thermoplastique et qui présente une bonne finition, des détails fins et un comportement mécanique similaire à celui des pièces moulées est un énorme gain de temps et un grand avantage. Avec Flame Retardant Resin, nous pouvons passer de la conception CAO à la pièce finie en nous épargnant le travail supplémentaire que nous devions effectuer avec d'autres méthodes.
Tony Parker, Directeur général d'Avance Design
Exploiter plusieurs matériaux pour la production
Avance Design travaille sur de nombreux autres projets ne requérant pas de matériaux homologués UL. Chaque projet commence par une discussion et une analyse des caractéristiques les plus importantes pour le client, et généralement, M. Parker trouve une résine Formlabs adaptée. « Nous disposons toujours de 20 à 30 cartouches de résine », explique-t-il. Un projet récent avec un client nécessitait un matériau flexible pour des dispositifs de simulation destinés à l'enseignement médical. M. Parker a conçu des pièces en Flexible 80A Resin qui seront utilisées dans le dispositif. Les pièces ont rencontré un franc succès et Avance en a imprimé plus de 1000 sur les imprimantes Form 3+, démontrant ainsi les avantages d'une production en petite série.
Le secteur de l'architecture offre d'autres opportunités, car il faut souvent y produire de petites séries de pièces (par exemple, des éléments de porte devant correspondre au style et à la décoration du lieu). Les clients se tournent vers Avance pour des articles tels que des boîtiers personnalisés pour l'électronique qui s'harmonisent avec le décor et le style d'un bâtiment. Pour répondre aux exigences de résistance et de forme d'une application finale et éviter les coûts de moulage ou d'usinage, M. Parker utilise la Form 3+ et la Form 3 pour produire de petites séries de pièces finales.
De nouveaux horizons en vue
Avec un nouveau matériau ajouté à son arsenal, M. Parker est enthousiaste quant aux opportunités qui s'offrent à lui pour les applications de Flame Retardant Resin. « Les gens sont habitués aux pièces moulées ou aux technologies d'impression FDM, mais lorsqu'ils verront que cette résine est disponible, ils réaliseront toutes les possibilités qu'elle renferme. C'est un moyen plus rapide et moins coûteux d'obtenir une pièce finale ignifugée », explique M. Parker.
M. Parker pense que la complexité du processus de moulage a dissuadé certains de ses clients d'utiliser l'impression 3D dans des applications médicales, d'ingénierie ou de robotique. « Je suis sûr que certains clients s'y sont intéressés et se sont finalement dit que cela ne valait pas la peine de passer par le processus de moulage. Mais maintenant qu'il existe un moyen d'imprimer directement les pièces en 3D pour les secteurs qui en ont besoin, je suis impatient de voir les possibilités qui s'offrent à nous », déclare M. Parker.
Pour découvrir les avantages que Flame Retardant Resin peut vous offrir, visitez la page produit ou contactez notre équipe commerciale pour discuter de votre application unique.