Comment Braskem a utilisé l’impression 3D pour fabriquer des moules à injection pour des pièces finales
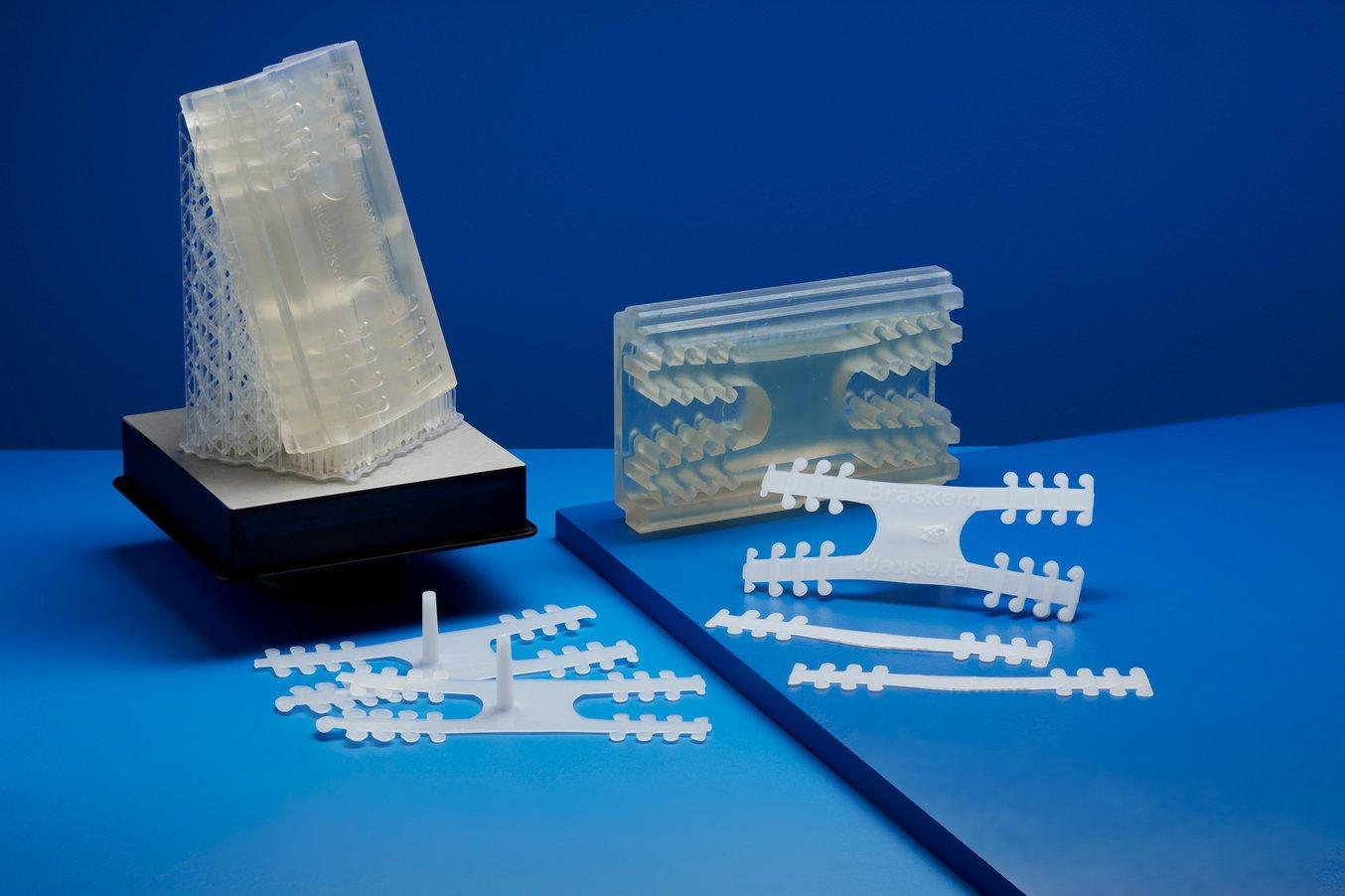
La fabrication de moules est utilisée dans toutes les industries par des concepteurs de produits, des entrepreneurs et des enseignants afin de créer des pièces identiques. Le moulage par injection, en particulier, est un procédé de moulage polyvalent qui est généralement utilisé pour produire ces pièces en grande quantité. Le moulage par injection à grande échelle est rentable, très performant, reproductible et produit des pièces de qualité. Cependant, pour les plus petites quantités, le coût et la durée nécessaires pour fabriquer le moule à partir de métaux d’usinage traditionnels entravent le processus, rendant souvent le moulage par injection à cette échelle inaccessible à de nombreuses entreprises.
Alors, que faire si vous recevez une demande urgente de produire quelques milliers de pièces identiques dans un délai d’une semaine ? S’appuyer sur des moules à injection imprimés en 3D pour une production en petites quantités réduit considérablement les coûts et les délais nécessaires par rapport aux moules métalliques réalisés par fraisage numérique, tout en permettant de produire des pièces reproductibles et de qualité.
Formlabs s’est entretenu avec Michelle Sing et Jake Fallon, ingénieurs de développement technologique, Collin Azinge, ingénieur en procédés de fabrication additive, et Fabio Lamon, responsable mondial des technologies de fabrication additive de Braskem, l’un des leaders mondiaux de la pétrochimie, afin qu’ils racontent leur première expérience de moulage par injection avec un moule imprimé en 3D.
Comment fabriquer rapidement des moules à injection pour petite série : panel de discussion en direct
Regardez ce panel de discussion pendant lequel des experts du secteur du moulage par injection expliquent comment l’impression 3D permet en quelques jours, à partir d’une simple idée, de fabriquer des moules en interne à la demande pour produire des centaines de pièces.
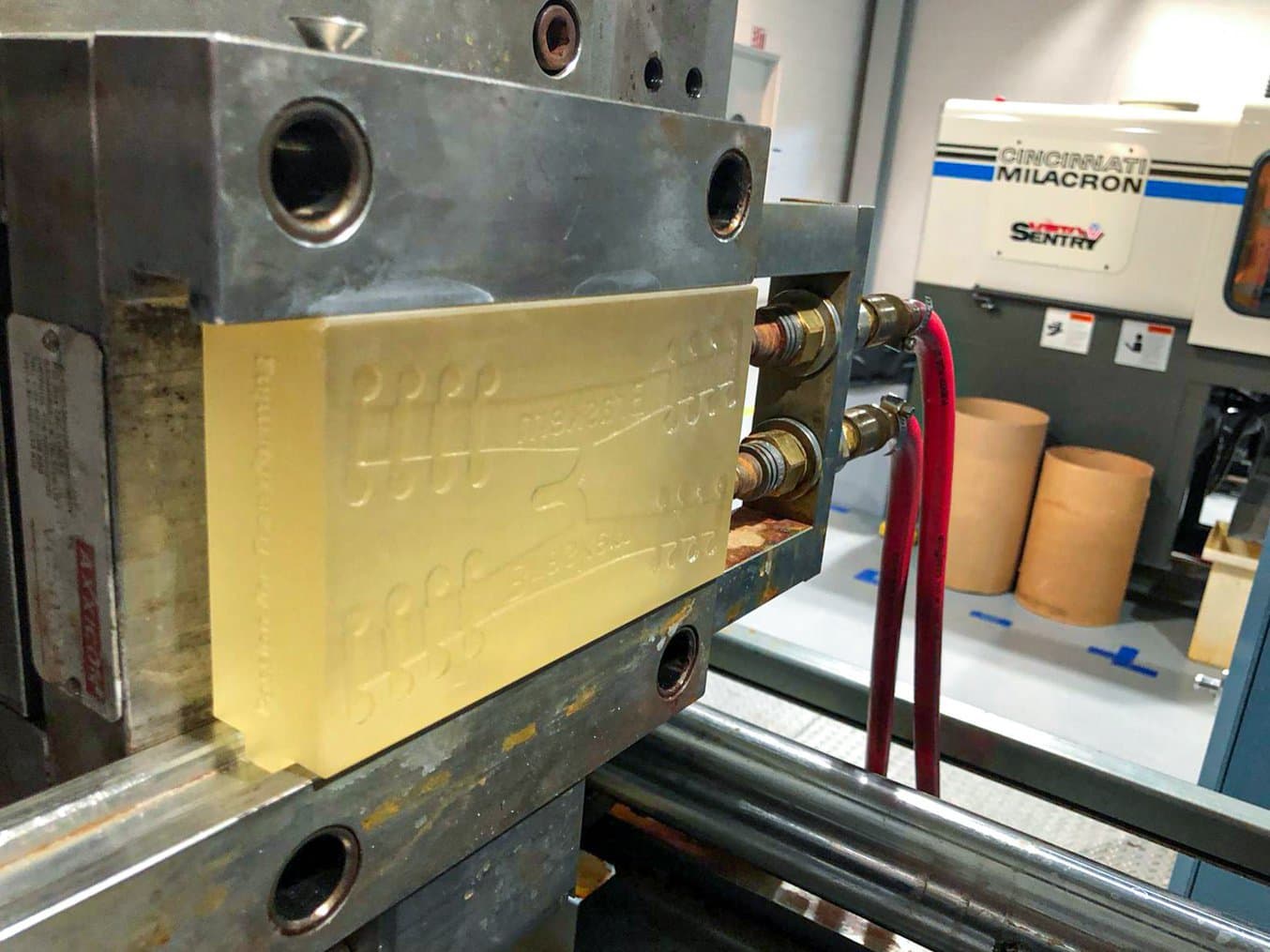
Impression directe ou moulage par injection ?
Jake Fallon a ouvert sa boîte mail pour y trouver un message urgent de la part d’un des vice-présidents de Braskem, en relation avec l’épidémie de COVID-19. La société devait produire des centaines de sangles pour des masques de protection pour tous leurs employés dans le monde. Que pouvait faire Jake en 48 heures avec l’équipement disponible chez Braskem ?
Lors de sa réunion avec ses collègues de l’équipe de fabrication additive, ils ont eu comme première idée d’imprimer les sangles en 3D, directement sur une imprimante à dépôt de fil fondu (FDM). Mais même si l’impression FDM est rapide, ils ont estimé la durée de fabrication à 17 minutes par sangle. Comme la demande portait sur plusieurs milliers de pièces, cela aurait pris bien trop de temps.
Outre des imprimantes FDM d’atelier, le Tech Center de Braskem à Pittsburgh dispose également d’une Form 3 de Formlabs et d’un équipement industriel de moulage par injection. Cela a fait germer une idée mais également de nombreuses questions.
Que peut apporter le moulage par injection ? Le moulage par injection est reconnu pour son efficacité et sa rapidité à produire des pièces en série, mais l’équipe s’est d’abord posé des questions sur la faisabilité d’un moule en plastique imprimé en 3D convenant à leur machine d’injection électrique Cincinnati Milacron Roboshot de 110 tonnes. Un moule plastique pouvait-il résister à la pression exercée par la machine ? Allait-il se casser après 50, 500 ou même 1000 injections ?
Braskem s’est tourné vers High Temp Resin, un matériau de Formlabs permettant d’imprimer des moules et des inserts pouvant être utilisés avec des processus exigeants tels que le moulage par injection pour produire des pièces à partir des matériaux de production finaux. High Temp Resin présente une température de fléchissement sous charge de 238 °C à 0,45 MPa. C’est un paramètre important car les mouleurs devaient garder la pression aussi basse que possible pour réduire le risque de rupture du canal d’injection. Cela imposait d’augmenter la température pour réduire la viscosité du matériau. High Temp Resin était le matériau idéal pour supporter les températures supérieures et les plus faibles pressions requises pour ce moule particulier.
L’équipe a conçu un moule produisant deux sangles par injection. Ils ont sorti leur premier moule imprimé de la Form 3, supprimé les supports et lui ont fait subir un ponçage élémentaire. Les sangles ont commencé à s’empiler au fur et à mesure des passages à l’injection. Un polypropylène souple de faible viscosité a été injecté à l’intérieur du moule pour réduire la pression dans la cavité et augmenter la durée de vie de la pièce imprimée en 3D.
La toute première version du moule a supporté 5 tonnes de force de serrage, pour une durée de cycle de 20 secondes, une vitesse d’injection de 1,27 cm/s et le maintien de la pression à 345 bars pendant environ 8 secondes. Les températures moyennes de moulage s’élevaient à environ 230 °C.
« Nous avons utilisé High Temp Resin V2 à une épaisseur de couche de 50 microns. La qualité était vraiment bonne et la résolution fantastique. En prenant une sangle au hasard, il était difficile de dire si elle avait été ou non fabriquée avec un moule en métal. »
Jake Fallon
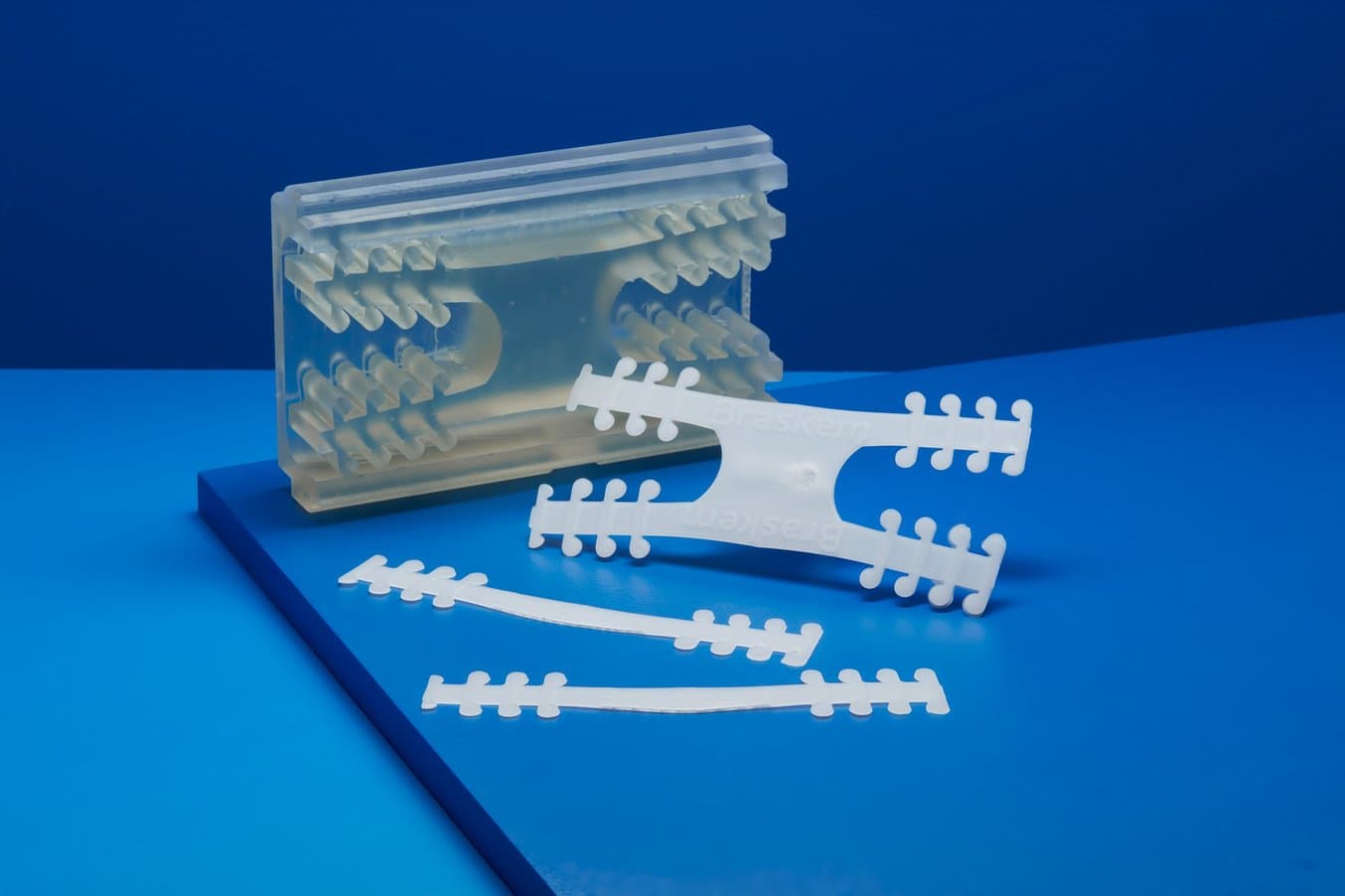
L’équipe a utilisé un spray standard de démoulage, qui supporte 40 à 50 injections. L’efficacité du spray a été améliorée en imprimant à 50 microns d’épaisseur de couche, créant ainsi une finition de surface lisse qui facilite l’extraction des pièces du moule. Un refroidissement supplémentaire du moule n’a pas été nécessaire. Aucun signe de réaction entre le matériau injecté et la résine imprimée n’a été observé.
Si Braskem n’avait pas disposé de l’impression 3D, la société aurait dû sous-traiter un moule en métal coûteux, et cela aurait représenté bien plus de temps et de coûts au niveau de l’équipe. L’impression 3D lui a permis de produire des milliers de sangles en une semaine, entre la réception du message du vice-président et leur expédition vers les bureaux du monde entier.
Itérations de conception et injections
« Nous avons réduit la consommation de matériau de 28 % pendant les itérations de conception. »
Jake Fallon
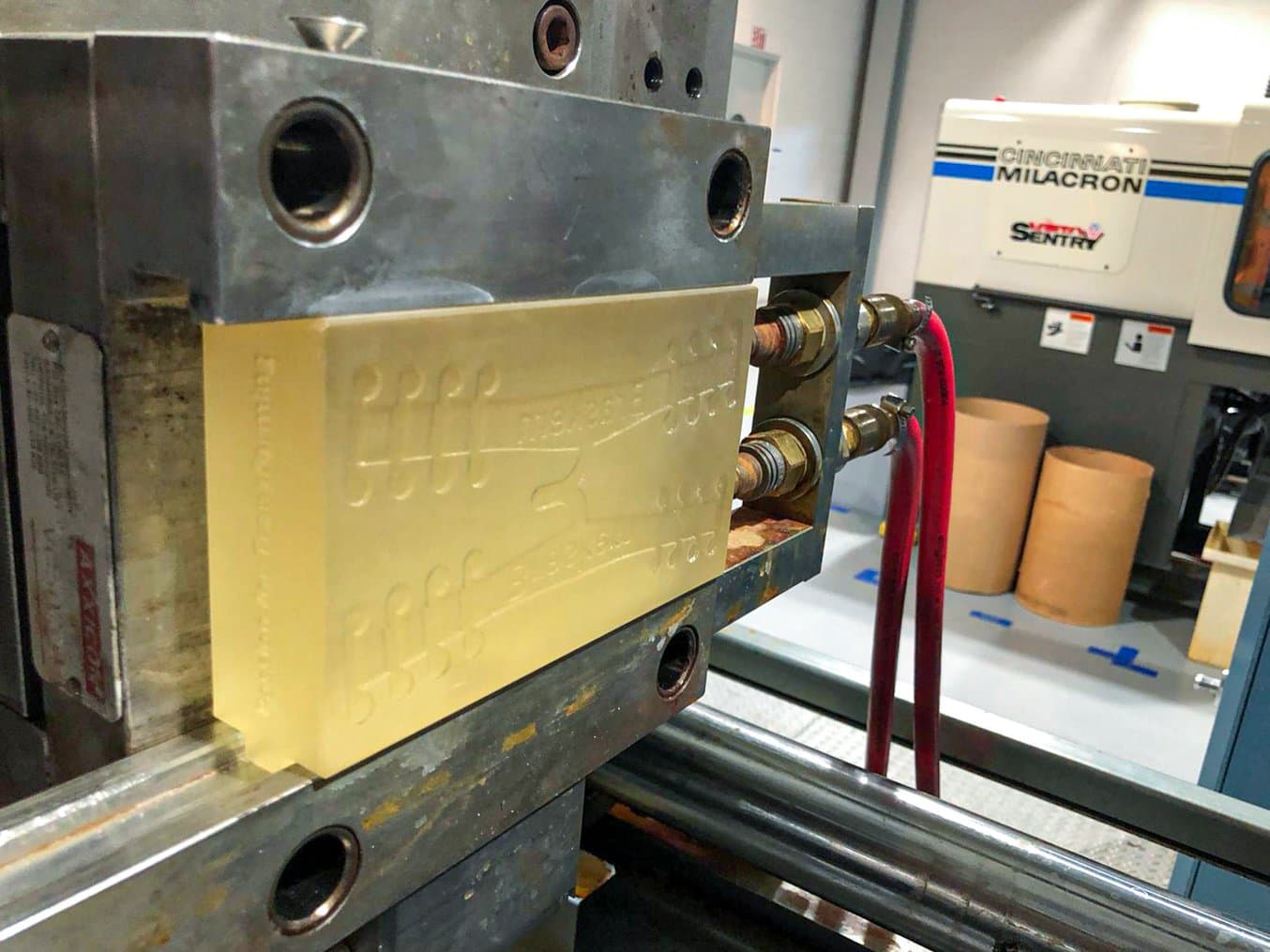
Pendant que la machine Roboshot fabriquait des sangles, Jake est retourné sur le logiciel CAO pour améliorer le modèle du moule, en s’efforçant d’élargir le canal d’injection. Jake voulait réduire la pression et améliorer le flux à l’intérieur de la cavité pour prolonger la durée de vie du moule et éviter les bavures. Au cours de l’amélioration du moule, il a pu également réduire la quantité de High Temp Resin utilisée pour imprimer le moule de 28 %, ce qui représente une économie pour la société et une réduction du temps d’impression.
Le moule V1 a bien fonctionné du premier coup, mais le moule V2, avec un canal d’injection plus grand, a été conçu pour supporter des milliers d’injections. Le nouveau moule pouvait supporter au moins 1500 injections avant d’être remplacé et il a permis à l’équipe de satisfaire les commandes de sangles. Ce moule amélioré pouvait imprimer quatre sangles par minutes, exactement ce qu’il fallait à l’équipe pour terminer sa tâche.
L’équipe de Braskem prévoit des dizaines d’applications potentielles de moules imprimés en 3D à l’avenir. Des moules imprimés en 3D peu coûteux, fabriqués pour moins de 100 dollars par pièce, peuvent aider des clients à rapidement produire des lots de petites quantités. Un exemple pourrait être un emballage thématique saisonnier, ce qui attirerait l’attention des clients. Auparavant, les petites entreprises n’auraient pas pu justifier le coût correspondant aux moules et à l’outillage. Mais des moules qui peuvent supporter des milliers d’injections pourraient ouvrir de nouvelles opportunités de marketing et d’image de marque.
En savoir plus
« L’avantage numéro 1 a été le temps. Nous avons testé le moule en une semaine et, en une journée, nous avons conçu un deuxième modèle qui apportait des améliorations significatives. »
Jake Fallon
L’équipe de Braskem a été surprise de voir comment le moulage par injection a permis d’étendre l’utilisation de son imprimante 3D au-delà du seul prototypage rapide jusqu’en production. Du fait de la disponibilité de centaines de matériaux pour le moulage par injection, Braskem est depuis longtemps un partenaire fiable pour les entreprises utilisant ce procédé pour la production de masse. L’entreprise vend également plus de 300 matériaux pour le thermoformage, le moulage par soufflage et d’autres procédés de fabrication qui peuvent tirer parti de moules imprimés en 3D.
L’équipe va prochainement s’intéresser aux possibilités offertes par le moulage par injection avec la Form 3L, en raison de sa capacité à fabriquer des pièces de grande taille. Selon Jake, « les dimensions du moule imprimé en 3D étaient à la limite du volume d’impression de la Form 3. Nous sommes impatients de connaitre les opportunités que va apporter la Form 3L. »
Téléchargez gratuitement ce livre blanc ou regardez ce webinaire pour connaître les détails du processus de travail, les instructions de conception et les bonnes pratiques relatives à l’utilisation de moules imprimés en 3D pour le processus de moulage par injection. Vous y trouverez d'autres études de cas réels, réalisées chez Novus Applications et Holimaker.