Holimaker produit des centaines de pièces prototypes et de pré-production avec des moules à injection imprimés en 3D
La start-up française Holimaker veut permettre au plus grand nombre d’accéder à la fabrication plastique en réalisant des outils de micro-industrie pour la transformation du plastique. HoliPress, leur produit phare, est une presse de moulage par injection manuelle qui permet aux ingénieurs et aux concepteurs de produits de réaliser, sur leur bureau, des pièces plastiques en petite série pour les prototypes, une production expérimentale, voire une quantité limitée de pièces finales.
Holimaker propose des études de faisabilité à ses clients, en utilisant des moules imprimés en 3D pour une production rapide et abordable. Cela permet à ses clients de concevoir des prototypes rapidement et à moindre coût, ainsi que de valider les conditions de fabrication finales au cours de la phase de production expérimentale du lancement d’un nouveau produit. Utilisant une méthode de fabrication identique, notamment en ce qui concerne les matériaux et la conception des moules, ces pièces peuvent être testées sur le terrain et assurer que les modèles soient prêts à être produits à grande échelle. Les modèles de moules imprimés en 3D peuvent ensuite être facilement adaptés pour l’acier forgé au cours de la production en série.
Holimaker utilise des moules imprimés en 3D dans 80 à 90 % de ses projets actuels. Nous avons rencontré Aurélien Stoky, son gérant, et Vivien Salamone, son directeur adjoint, pour comprendre comment ils combinent les deux technologies.
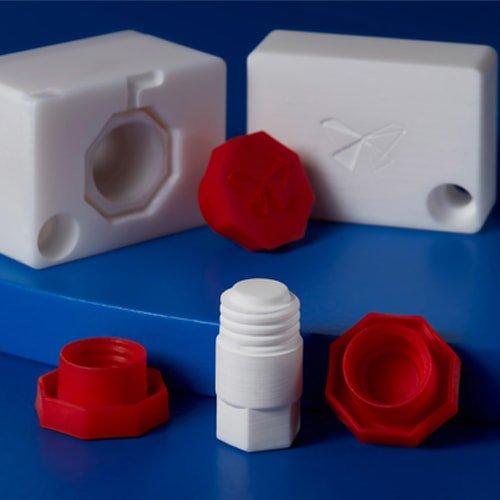
Le moulage par injection rapide en petite série avec des moules imprimés en 3D
Téléchargez ce livre blanc pour connaître les recommandations d’utilisation de moules imprimés en 3D dans le processus de moulage par injection afin de réduire les coûts et délais de production. Vous y trouverez des études de cas réels, réalisées chez Braskem, Holimaker et Novus Applications.
Pourquoi imprimer en 3D des moules à injection ?
Traditionnellement, les moules à injection sont fabriqués au moyen de méthodes industrielles coûteuses telles que l’usinage CNC ou l’électroérosion par enfonçage (EDM). Cependant, pour les plus petites quantités de pièces, le coût, la durée, l’équipement spécialisé et la main-d’œuvre qualifiée nécessaires pour fabriquer le moule à partir de métaux d’usinage ordinaires avec ces méthodes de production traditionnelles entravent le processus, ce qui rend souvent le moulage par injection à cette échelle inaccessible à de nombreuses entreprises. Le fait de s’appuyer sur l’impression 3D pour fabriquer des moules à injection pour le prototypage et la production en petite série permet de considérablement atténuer ces obstacles par rapport aux moules métalliques, tout en continuant de produire des pièces reproductibles et de qualité.
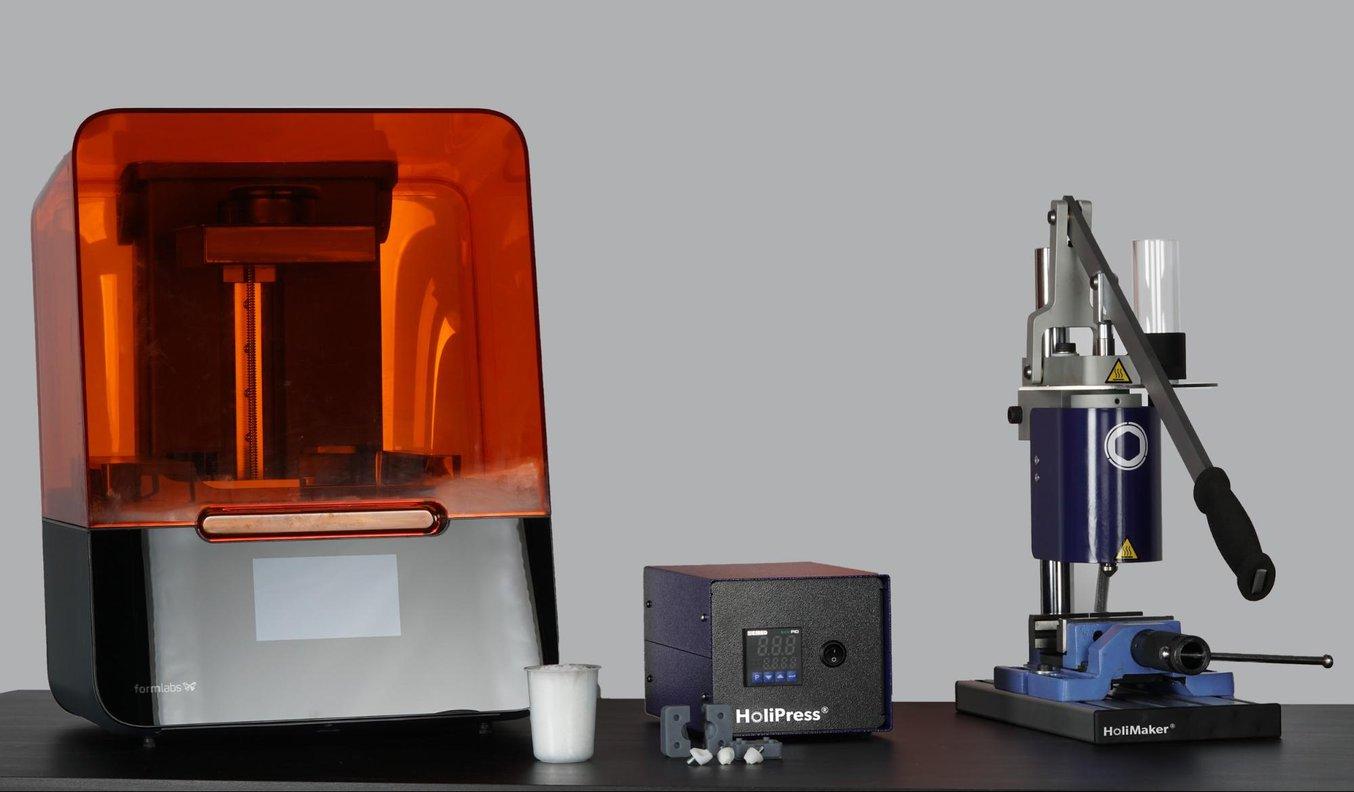
La Holipress à côté de l’imprimante Form 3.
« Dans le moulage par injection, le point de blocage, c’est la fabrication du moule. Pour démocratiser le moulage par injection et le rendre accessible au plus grand nombre, nous avons dû trouver une technologie complémentaire pour produire notre moule. L’impression de bureau était la clé du problème. Nous associons la flexibilité de l’impression 3D à la productivité et la qualité des plastiques moulés par injection », déclarent Stoky et Salamone.
Le principal intérêt de ce procédé alternatif est de permettre de raccourcir le délai entre le concept et la production, tout en fabriquant une série de pièces en thermoplastique traditionnel. Grâce à la machine Holipress, il est possible de produire de petites séries de prototypes et de pièces de pré-production pour tester le matériau définitif et la chaîne qui seront utilisés pour la production en série, voire même de produire des quantités limitées de pièces finales. Et, grâce à l’impression 3D par stéréolithographie (SLA) de bureau, il devient possible de le faire en quelques jours, avec un équipement très limité et sans recourir à des opérateurs qualifiés.
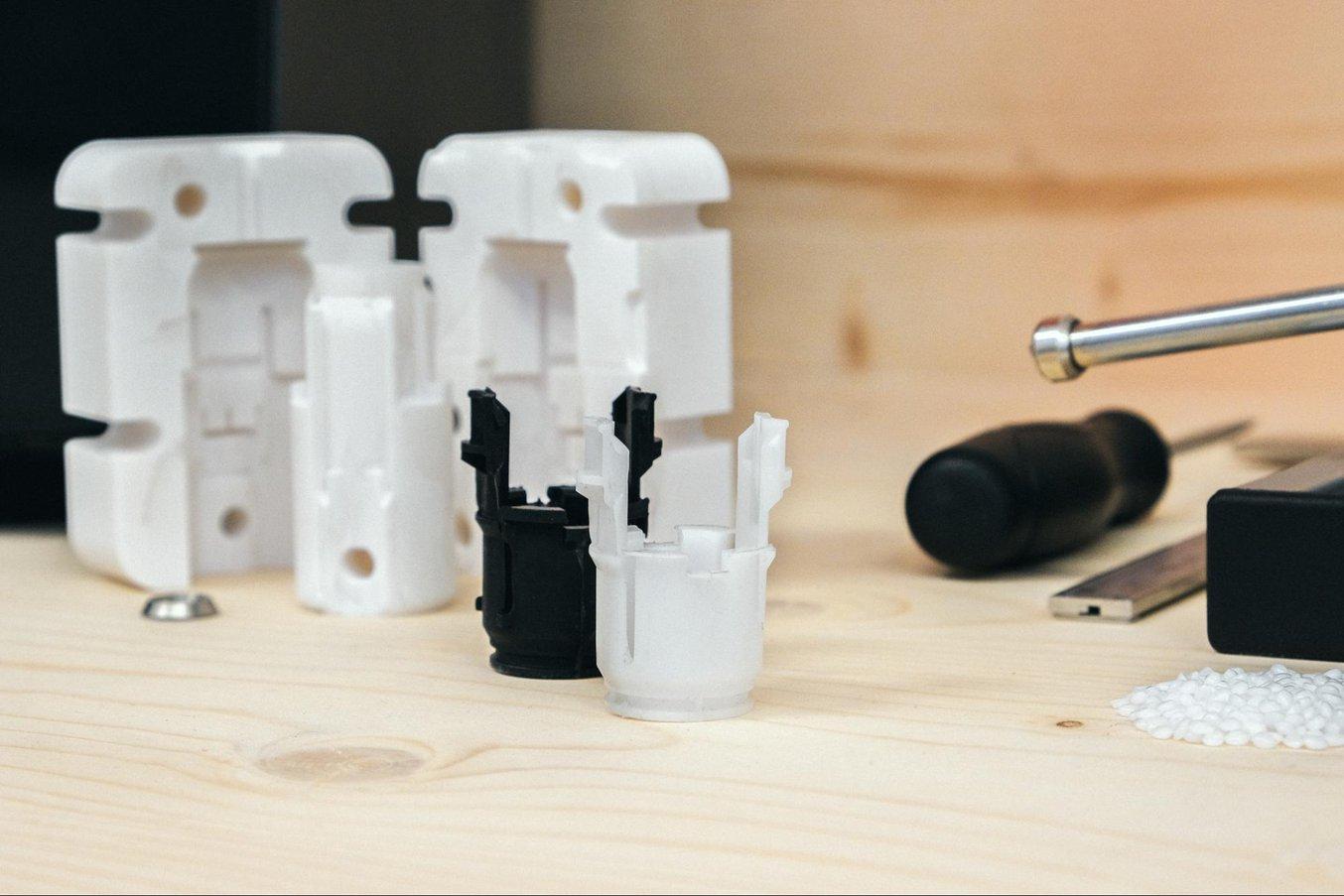
Holimaker a utilisé des moules imprimés en 3D pour mouler par injection des prototypes d’une pièce de connecteur de vanne pour un client qui devait effectuer des tests de résistance à la pression de l’eau.
Grâce à l’impression 3D des moules, Holimaker peut réduire de façon spectaculaire le délai de production et itérer les modèles pour en optimiser la forme dans la journée.
« Nous concevons souvent le moule le matin, nous l’imprimons en cours de journée, puis nous pouvons tester l’injection dans l’après-midi pour modifier le modèle CAO et lancer une seconde impression de nuit. Avec la méthode traditionnelle, nous serions obligés d’usiner le moule à nouveau et cela prendrait des semaines », ajoute Stocky.
Holimaker a aussi exploré d’autres méthodes de réalisation de moules. Pour les commandes supérieures à mille pièces, la start-up utilise un moule en aluminium usiné, mais pour les plus petites quantités, la presse fonctionne avec des moules imprimés en 3D. Dans certains cas, les deux procédés sont combinés. Pour de grandes quantités de pièces à géométries exigeantes, l’extérieur du moule est usiné et l’insert est imprimé en 3D et remplacé au cours de la production.
Disposer de l’impression 3D en interne leur a aussi permis de s’aventurer au-delà des limites imposées par les techniques d’usinage. Pour de nombreux projets, il leur a été possible de réussir des modèles de moules très complexes, difficiles à fabriquer de manière traditionnelle, permettant ainsi à leurs clients d’innover encore plus.
« En termes de formes, certains de ces projets étaient irréalisables sans l’impression 3D », reconnaît Stoky.
Le processus étape par étape
Conception
Généralement, l’équipe développe trois à quatre modèles par projet afin d’en parfaire la conception. Elle suit les recommandations générales en matière de moulage et de conception pour la fabrication, comme par exemple l’utilisation d’angles de dépouille. Elle travaille surtout sur de petites pièces et y ajoute des évents de 0,1 mm et des canaux de 0,5 mm.
L’équipe respecte également quelques règles d’impression 3D, telles que la création de chanfreins sur la pièce pour faciliter son retrait de la plateforme de fabrication, la création de tenons de centrage pour aligner les moitiés du moule et l’ajout d’encoches pour permettre l’ouverture du moule avec un tournevis. Elle utilise généralement des moules de 10 mm d’épaisseur et évite les sections transversales trop fines. Les parties ne dépassant pas 1 à 2 mm d’épaisseur ne peuvent pas résister aux températures élevées.
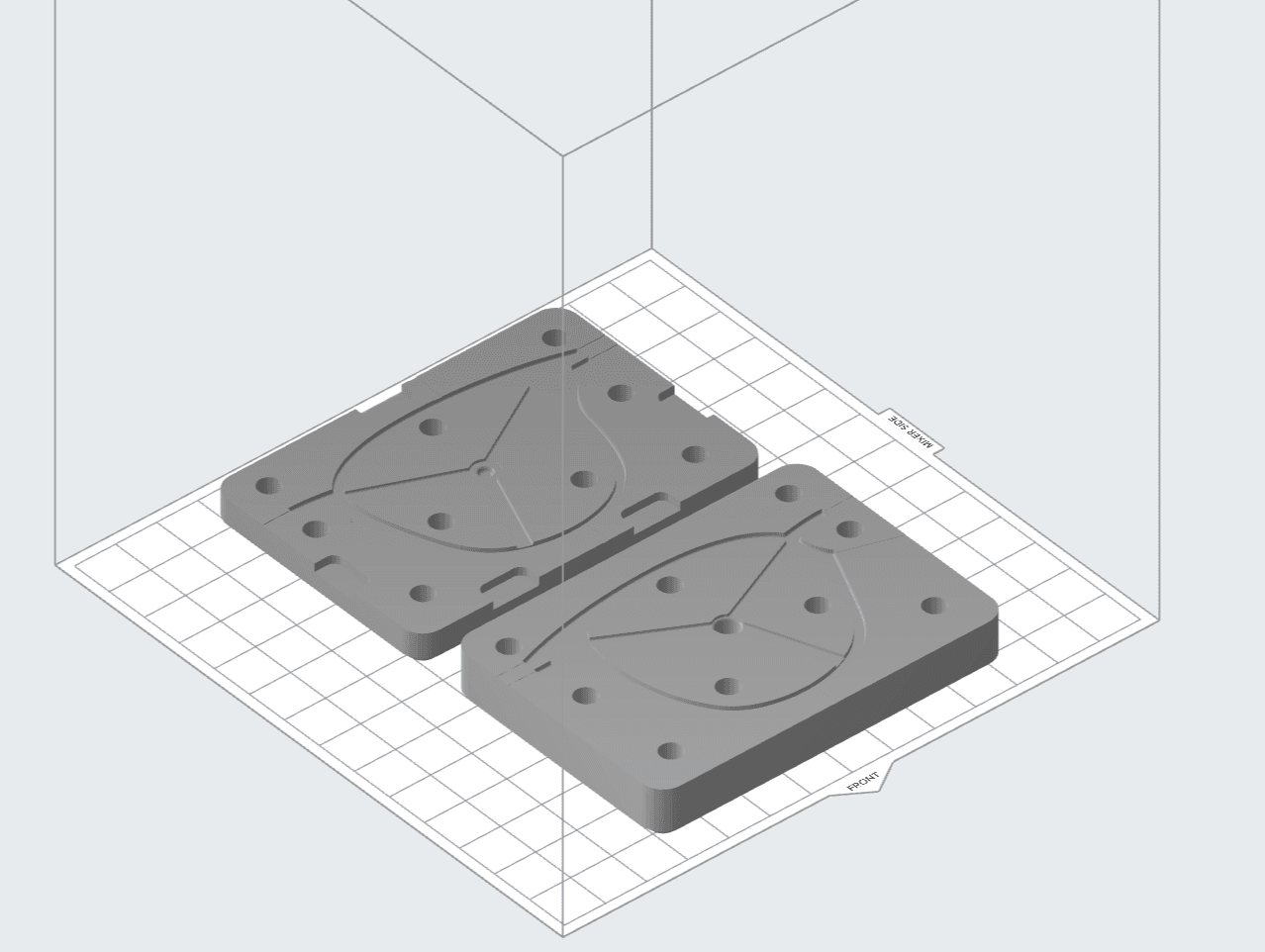
Divers modèles de moules à injection dans le logiciel de préparation d’impression PreForm de Formlabs.
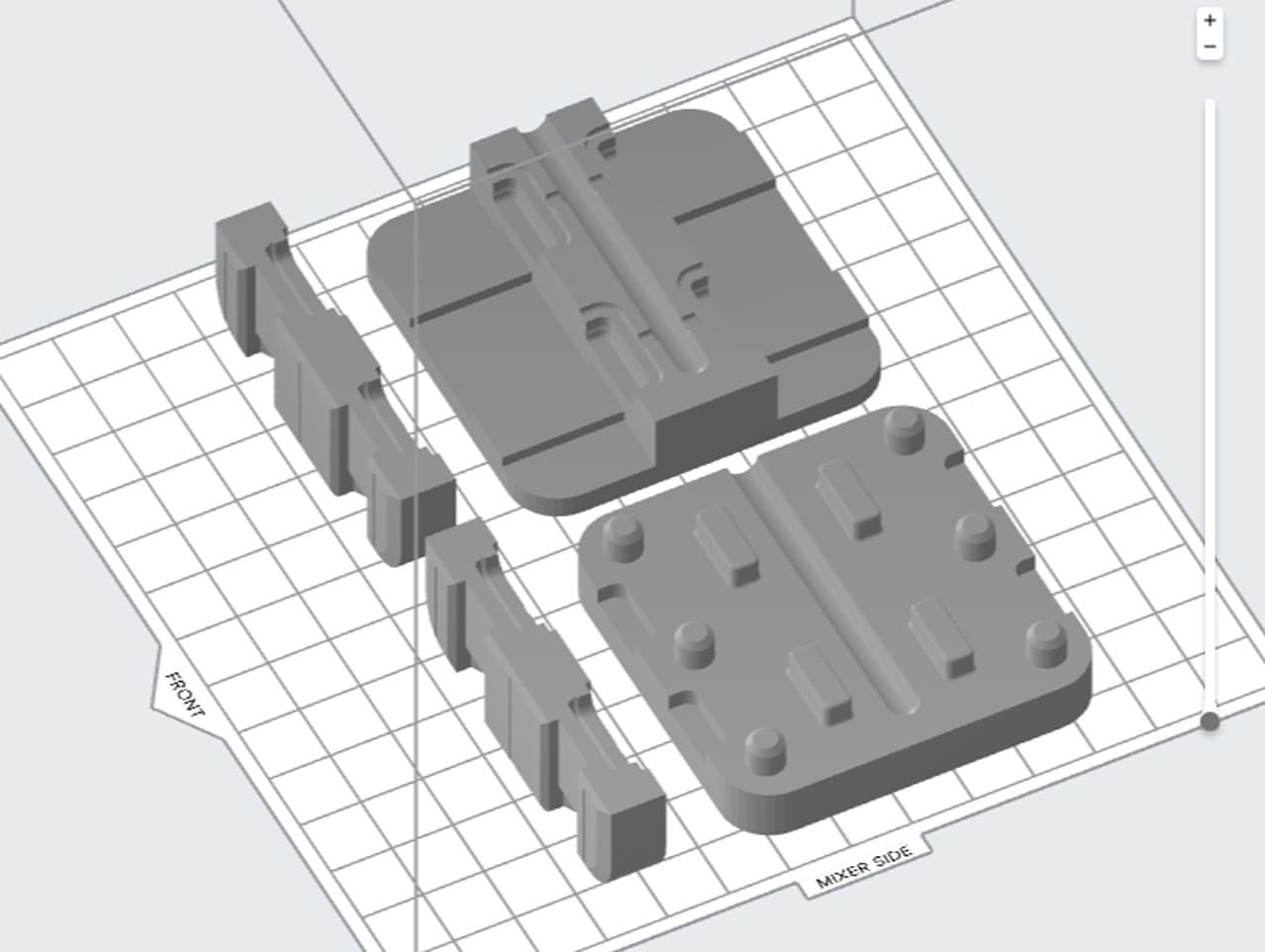
Le passage d’un moule imprimé en 3D pour les faibles volumes de production à un moule métallique usiné pour la production en série se fait sans heurt. Il se peut que de simples modifications des dimensions des évents d’aération, des canaux d’injection et des angles de dépouille soient nécessaires.
Impression 3D
L’équipe de Holimaker imprime les moules directement sur la plateforme de fabrication, à 50 microns d’épaisseur de couche. Cette orientation économise du temps d’impression et de la résine en évitant l’ajout de structures de support. En cas d’erreur en matière de dimensions, celle-ci se situe généralement à l’extérieur du bloc, qui est post-traité par ponçage manuel pour s’ajuster aux cadres du moule métallique standard offrant un soutien supplémentaire.
En général, Formlabs recommande d’utiliser Rigid 10K Resin et High Temp Resin pour le moulage par injection, mais Grey Pro Resin peut être une option en cas de rupture du moule en raison de ses formes trop exigeantes. Si le refroidissement n’est pas une priorité, Grey Pro Resin représente une bonne option pour prolonger la durée de vie du moule.
Holimaker privilégie Grey Pro Resin pour la plupart de ses études. Ce matériau possède une thermorésistance moins élevée que High Temp Resin et Rigid 10K Resin, mais il est moins fragile et permet un nombre plus élevé de cycles pour les formes géométriques complexes. Le matériau Grey Pro Resin peut également être foré et manipulé à plusieurs reprises et il convient à une utilisation sur presse à injection standard.
Le moulage par injection
L’équipe a utilisé la machine d’injection Holipress dans toutes ses études. C’est une petite presse à injecter manuelle, facile à utiliser et disponible pour un dixième du prix d’une presse industrielle.
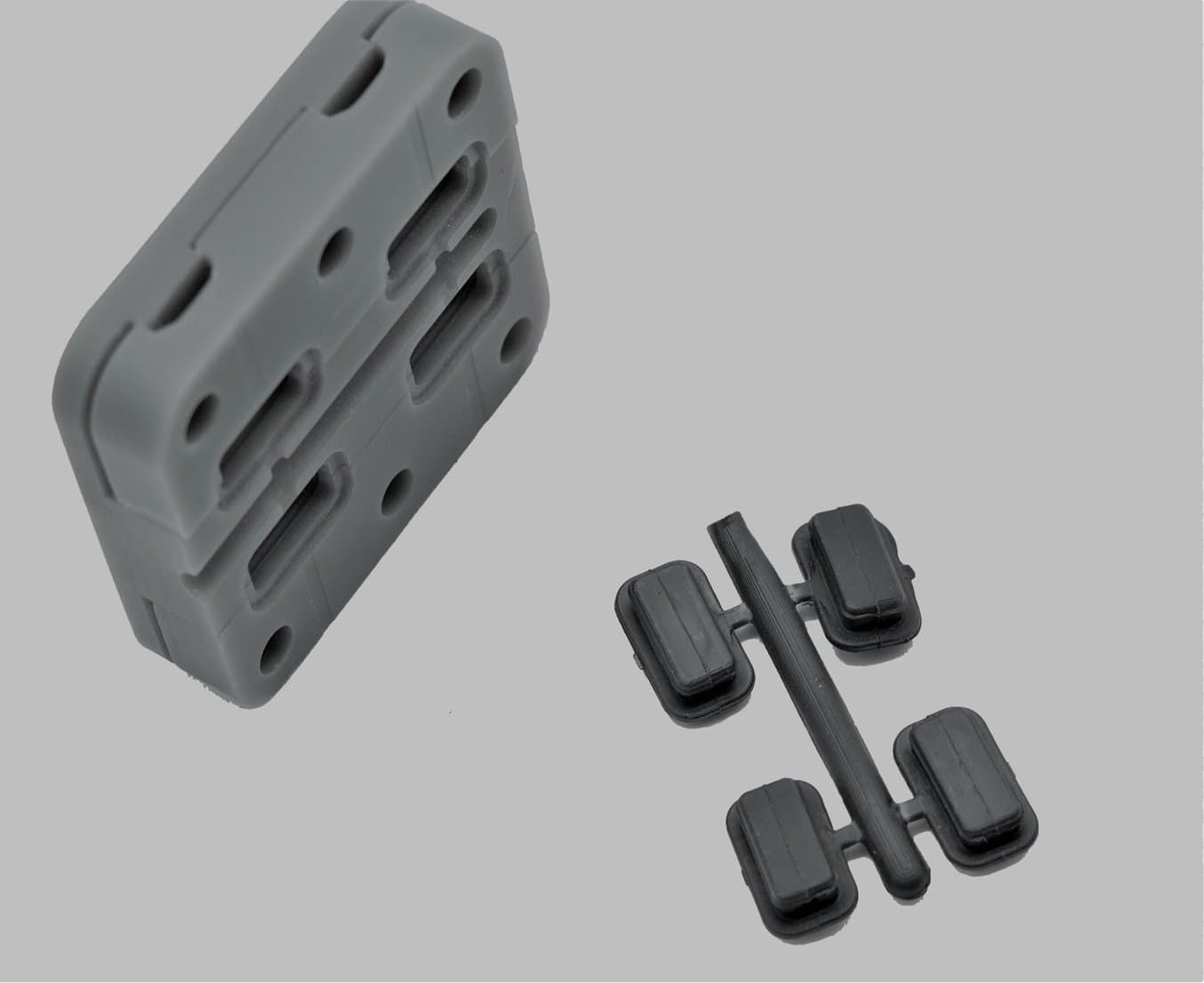
Ces fermoirs pour écran facial ont été moulés par injection avec du polypropylène (qualité alimentaire, 220 °C).
Les moules sont placés dans un cadre en aluminium fabriqué préalablement qui résiste mieux à la pression et garantit que la buse d’injection n’est pas en contact direct avec le moule imprimé.
Avec des moules imprimés en résine Formlabs, Holimaker injecte une large gamme de thermoplastiques de duretés différentes allant de Shore 40A à 90A, avec des durées de cycle de trois à cinq minutes. Le nombre de cycles par moule varie d’environ 10 pièces pour du PA injecté à 270 °C à des centaines de pièces pour du PP, du TPE ou du POM, injectés à des températures inférieures. Holimaker est en train de développer un système de refroidissement intégré pour contribuer à réduire le temps de refroidissement avant démoulage.
Résultats
L’équipe a choisi la technologie d’impression 3D SLA de Formlabs pour sa facilité d’utilisation et la qualité des pièces qu’elle produit.
« La qualité de nos pièces injectées est très bonne parce que les moules sont de très bonne qualité. Et quand je lance une impression le soir, je suis quasiment certain d’avoir un moule réussi, prêt à servir le lendemain matin », déclare Stoky.
Auparavant, Stoky et Salamone, les gérants de Holimaker, utilisaient une autre technologie d’impression de bureau, mais ils ont abandonné celle-ci après avoir constaté trop de déformations des impressions, y compris avant l’injection.
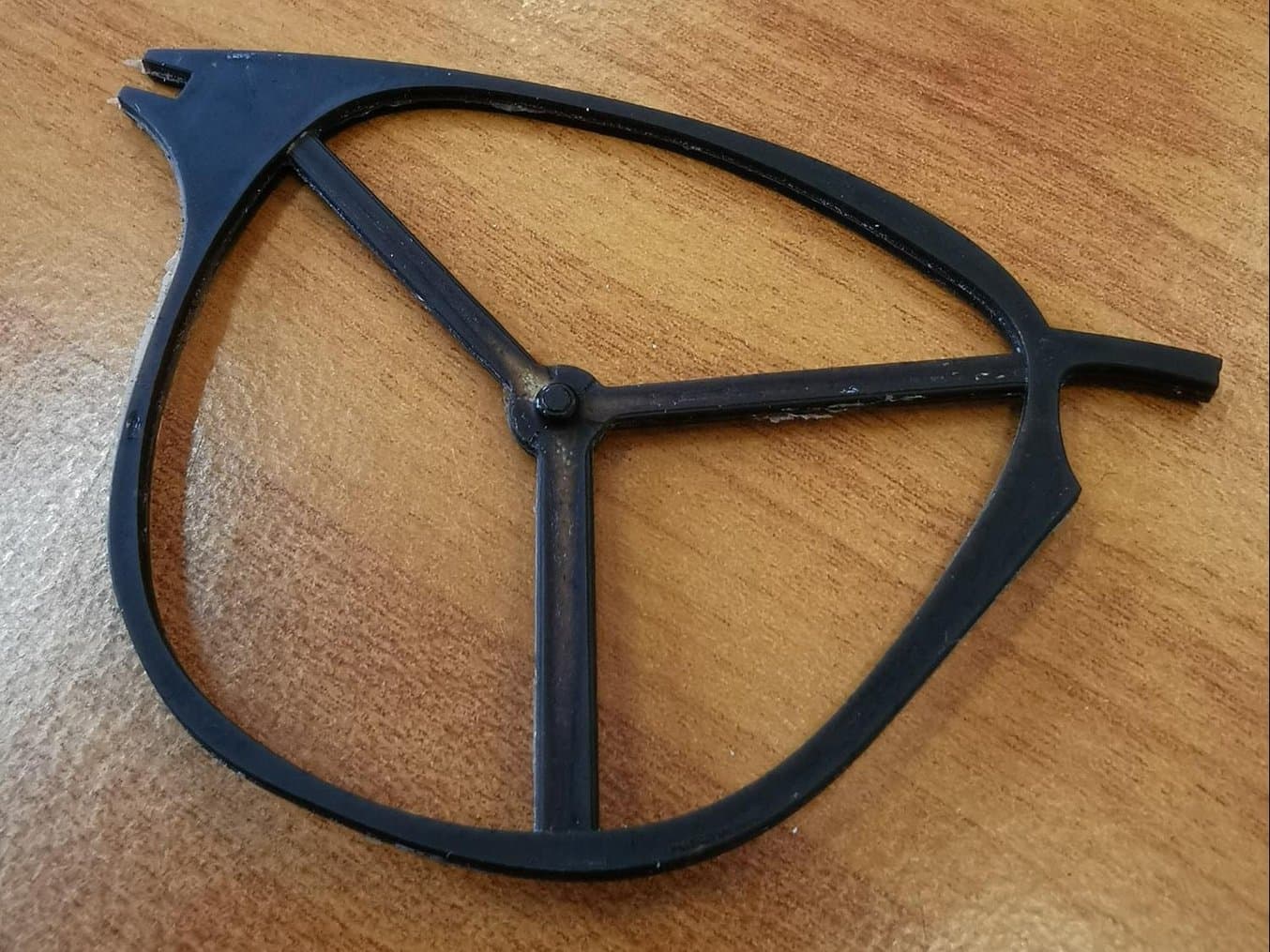
Une monture de lunettes fabriquée avec des moules imprimés en 3D.
« Les pièces Formlabs offrent une grande précision dimensionnelle et une finition de surface impeccable. Si une erreur dimensionnelle se produit, elle est très minime et uniforme dans les trois axes, donc nous pouvons l’anticiper et la compenser au post-traitement. Avec les autres imprimantes de bureau, nous ne pouvions pas contrôler la déformation », explique Stoky.
L’équipe apprécie aussi la simplicité et la facilité de mise en œuvre et de maîtrise du processus, comportant la Form Cure et la Form Wash qui automatisent complètement le processus de polymérisation et de lavage.
Holimaker a partagé avec nous quelques cas de leur clientèle pour mieux illustrer les types de pièces, les conditions de moulage et les résultats de leurs études de faisabilité.
Société | Smart Power | FERME 3D | Lunetier | |
---|---|---|---|---|
Produit | Crampon de football | Fermoir pour écran facial | Monture de lunettes | |
Besoin | Réaliser une pré-production de prototypes dans différents thermoplastiques pour les tester en conditions réelles et choisir le matériau final pour une production de masse. | Tester une solution pour produire une série de plusieurs dizaines de milliers de pièces dans un court laps de temps. | Tester la compatibilité des matériaux de dispositifs optiques avec les moules imprimés pour produire une série de 200 montures. | |
Matériaux injectés | POM (180°C), PA 6.6 (270°C), PP (210°C) | PP (food-grade, 220°C) | ASA (240°C), PA (240°C) | |
Nombre de pièces pour un moule | 60 | 100 | 70 | |
Délai de | 2 minutes | 2 minutes | 2 minutes | |
Délai de production du projet | 1 semaine | 1 semaine | 2 semaines |
Gain de temps et économies grâce à l’impression 3D des moules à injection
L’utilisation de moules imprimés en 3D en interne a considérablement diminué les coûts et les délais par rapport aux moules en métal usinés par un sous-traitant.
Moule usiné en métal par un sous-traitant | Moule imprimé en 3D en interne | |||
---|---|---|---|---|
Équipement | Holipress, thermoplastiques | Holipress, thermoplastiques, imprimante Form 3, Grey Pro Resin | ||
Temps de production du moule | 3 à 5 semaines | 1 semaine | ||
Coût de production du moule | 4-5 X | 1 X |
Un usinage rapide alliant le moulage par injection et l’impression 3D de bureau permet à Holimaker de produire rapidement de petits lots de pièces thermoplastiques sur demande.
« Le délai entre la conception de l’objet et la fabrication de la pièce par injection a été écourté. Nous gagnons en flexibilité, en temps et en coûts », ajoute Stoky.
Téléchargez gratuitement ce livre blanc ou regardez ce webinaire pour connaître les détails du processus de travail, les instructions de conception et les bonnes pratiques relatives à l’utilisation de moules imprimés en 3D pour le processus de moulage par injection. Vous y trouverez d’autres études de cas réels, réalisées chez Braskem et Novus Applications.