Comment Brose s'appuie sur les technologies SLA et SLS pour booster la production automobile
Aujourd'hui, un véhicule sur trois qui sort de la chaîne de montage contient au moins un composant fabriqué par Brose, l'un des cinq plus grands constructeurs automobiles familiaux au monde. Fondée il y a plus d'un siècle à Berlin par Max Brose, l'entreprise était à l'origine spécialisée dans le commerce d'accessoires automobiles, avant de devenir un leader du marché des systèmes mécatroniques. Les produits de Brose, tels que les sièges, les hayons et les portes, sont conçus et fabriqués pour les plus grandes marques automobiles : BMW, Volvo, Ford, Mercedes, Jeep et autres.
Le développement constant de Brose et les collaborations fructueuses à long terme avec ces équipementiers sont dus en partie à l'engagement de l'entreprise en faveur de l'innovation et de l'amélioration continues. L'impression 3D joue un rôle clé dans de nombreux processus de conception et de production finale et permet à l'entreprise de s'adapter aux changements rapides de l'industrie automobile.
Nous avons visité Brose North America, le siège de la société, situé à Auburn Hills (Michigan), et Brose New Boston à New Boston (Michigan), l'une de ses plus grandes installations de production finale, pour découvrir comment sont utilisées les puissantes imprimantes 3D stéréolithographiques (SLA) et à frittage sélectif par laser (SLS) de la société. Matthias Schulz, responsable de la division prototypage de sièges et de l'équipe de technologie additive dans cette région, a expliqué comment Brose utilise l'impression 3D tout au long du processus, de la conception à la production de pièces finales, tout en respectant les délais serrés exigés par les équipementiers.
« Au cours des cinq dernières années, nous avons assisté à des changements rapides dans le secteur automobile. Les délais de développement des nouveaux produits se sont considérablement raccourcis, ce qui nous oblige à nous adapter : nous devons intégrer de plus en plus de technologies additives, qui non seulement réduisent les délais de production des outils, mais nous permettent également d'accélérer la livraison des pièces. »
Matthias Schulz, responsable du prototypage des sièges, Brose North America
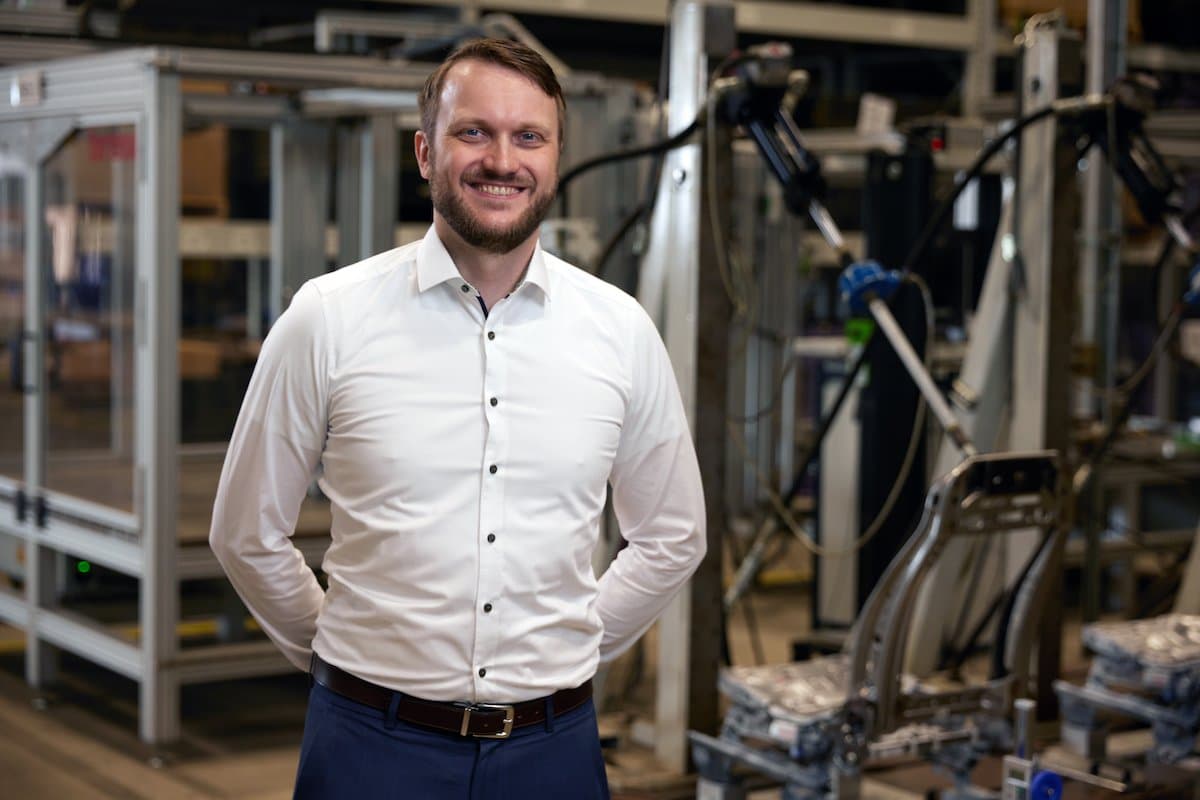
Webinaire à la demande : SLS chez Brose pour la production de pièces automobiles finales
Dans ce webinaire à la demande, Matthias Schulz, responsable du prototypage de sièges chez Brose North America, montre comment l'entreprise utilise les technologies SLA et SLS pour tout, de la production rapide de gabarits de soudage à la production en série de 250 000 pièces finales.
Quand le prototypage dépasse les pièces uniques
Le prototypage est l'une des applications les plus courantes et les plus adaptées à l'impression 3D. Bien que Brose utilise diverses imprimantes 3D à dépôt de fil fondu (FDM), SLA et SLS pour les prototypes, les volumes produits ne sont pas ce à quoi on ont pourrait s'attendre dans le cas de preuves de concept. Pour Brose, un volume typique de prototypes est plus proche de 500 ou 1000 unités.
« Nous utilisons l'impression 3D à plus grande échelle. Pour nous, « prototyper » signifie produire plusieurs centaines de pièces, notamment en fonction du nombre de tests à effectuer. Outre le respect des normes internes et externes, nous nous conformons également aux exigences fédérales. Ces derniers nous obligent en effet à imprimer un certain nombre de pièces, ce qui équivaut généralement à 700 – 800 pièces pour un prototype », explique M. Schulz.
Les quantités minimales élevées font de SLA le meilleur choix : amortisseur de siège en caoutchouc
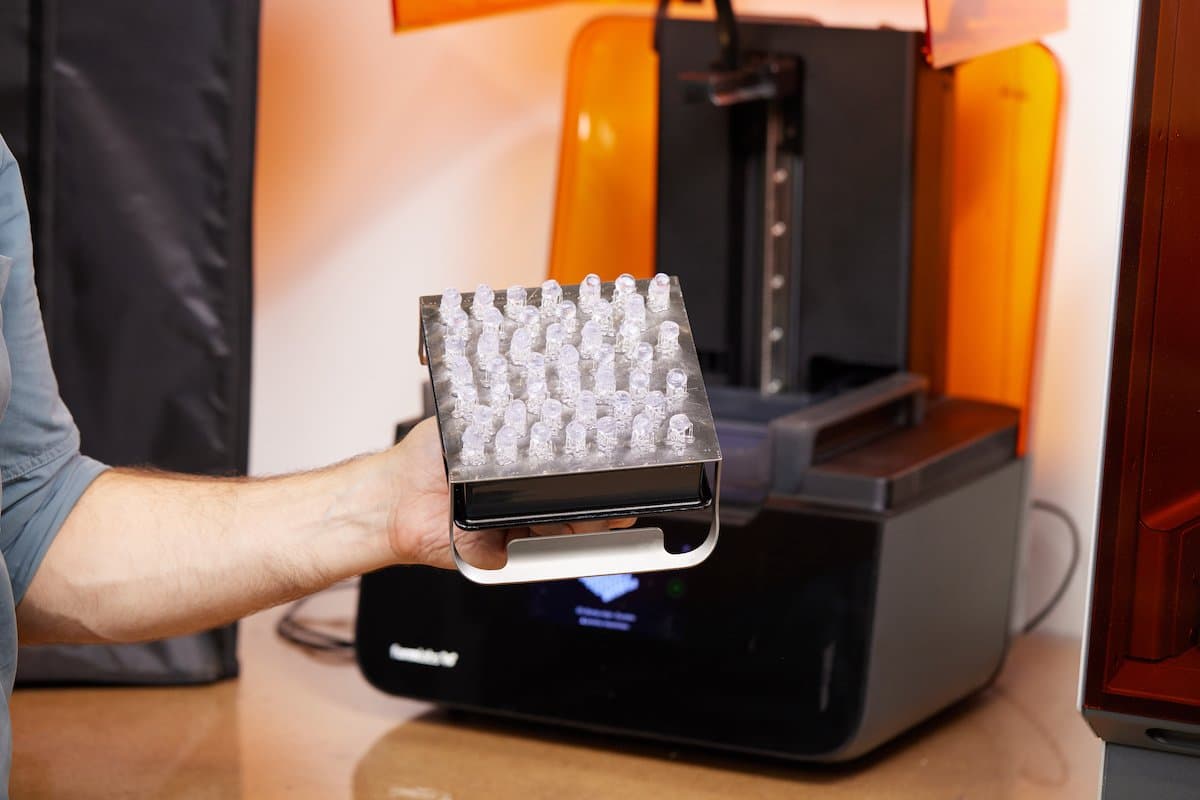
Ces prototypes sont de petits amortisseurs conçus pour réduire le bruit et améliorer le retour tactile du siège métallique sur le châssis. La sous-traitance aurait nécessité une commande minimale de plusieurs millions d'unités. M. Schulz et son équipe ont donc décidé d'utiliser des imprimantes de la série Form pour les essais.
Pour un projet, l'équipe de prototypage devait utiliser un amortisseur en silicone souple installé à l'intérieur d'un siège. Cette pièce permet de réduire le bruit lors du mouvement du siège sur le châssis, et d'améliorer le retour tactile et acoustique du mouvement de l'ensemble du siège. Pour commander ces pièces auprès d'un fournisseur étranger, la quantité minimale à commander était de plusieurs millions, alors que Brose n'avait besoin que de quelques centaines de pièces pour un essai de conception préliminaire.
Outre le coût élevé de l'achat et de l'expédition de millions de pièces, les délais de production étaient de plusieurs semaines, avec le risque de devoir stocker de nombreuses pièces inutiles qui deviendraient ensuite des déchets. Au lieu de commander la pièce, le logiciel CAO existant a été utilisé pour imprimer rapidement plusieurs centaines de pièces sur la Form 4, l'ensemble étant terminé en une semaine. Cette solution a permis de réduire à la fois le coût global et le temps de production du projet.
« Nous avons pu les imprimer avec une Form 4 à un coût bien inférieur à celui que nous aurions dépensé en les faisant venir de l'étranger et en commandant une quantité minimale, ce qui nous aurait obligés à commander plusieurs millions de pièces. Ils ont été disponibles rapidement et nous n'avons pas eu à attendre. »
Matthias Schulz, responsable du prototypage des sièges, Brose North America
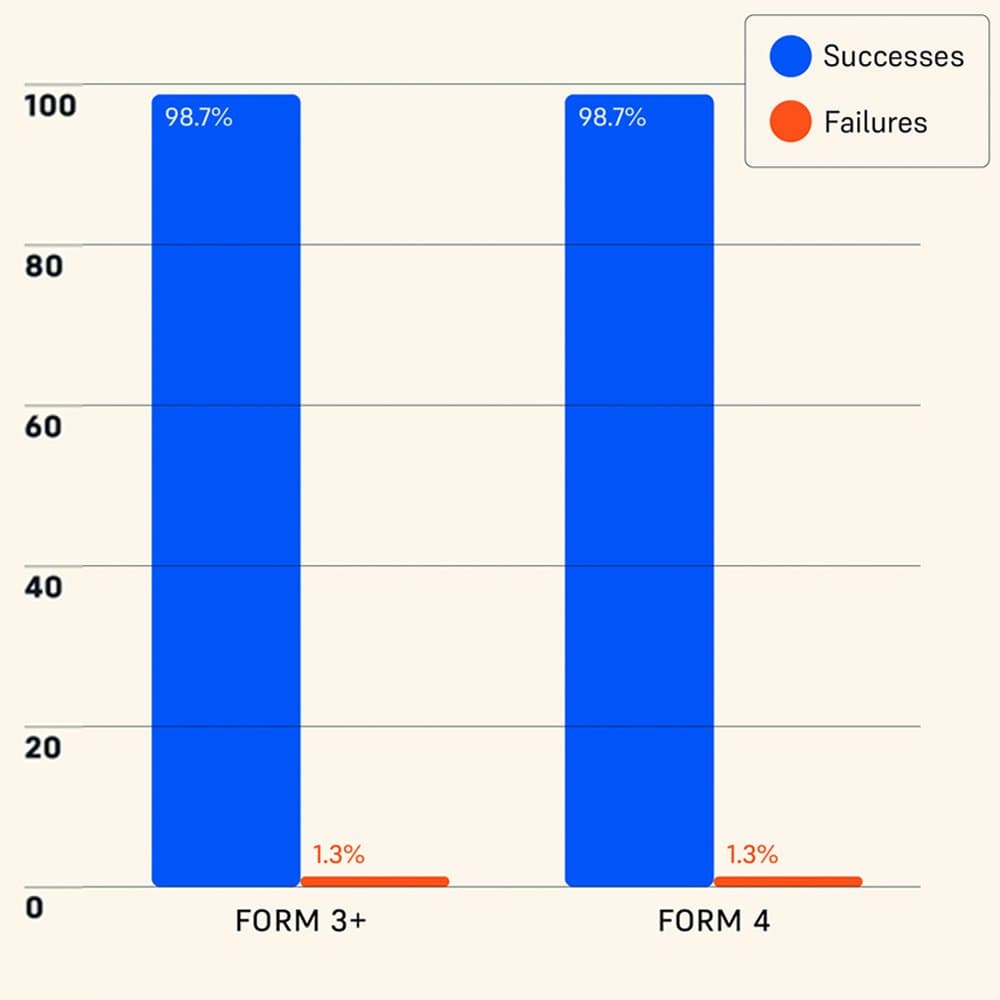
Fiabilité de la Form 4 et d’autres imprimantes 3D résine testée de manière indépendante
Une importante société indépendante de test de produits a mesuré un taux de réussite d’impression de 98,7 % pour la Form 4 de Formlabs. Lisez une description complète de la méthodologie d’essai et consultez les résultats dans notre livre blanc.
Combinaison des techniques SLA et SLS pour les grands volumes de prototypes
Lorsque les composants sont plus complexes, plus grands et plus encombrants, Brose se tourne vers son parc de trois imprimantes 3D SLS de la série Fuse pour le prototypage et la production. L'impression 3D SLS, grâce à son lit d'impression autoportant, permet des volumes de production importants. En outre, la résistance et les propriétés mécaniques du nylon fritté rendent cette technologie idéale pour les composants finaux. Dans le cadre d'un projet récent, l'équipe de technologie additive de Brose a utilisé les technologies SLA et SLS pour développer le prototype d'une grille de rembourrage de siège.
Les pièces translucides et flexibles ont été imprimées en Durable Resin à l'aide d'imprimantes 3D SLA de la série Form, tandis que les tubes de connexion en treillis ont été fabriqués en poudre de Nylon 12 GF Powder à l'aide d'imprimantes de la série Fuse. Chaque tapis prototype comprenait six pièces SLS et trois pièces SLA, mais au total, l'équipe a assemblé 150 de ces tapis complets pour les essais dans le cadre d'assemblages de sièges complets.
En utilisant ses propres outils de prototypage rapide, Brose a été en mesure de concevoir, de tester et d'améliorer un composant essentiel de l'assemblage du siège sans avoir à recourir à l'outillage ou à la sous-traitance. « Parfois, la combinaison du SLA et du SLS est la solution idéale, comme dans le cas du tapis de suspension du siège. Les surmoules sont des outils très complexes et coûteux, c'est pourquoi nous avons conçu les pièces SLS pour qu'elles se referment sur le câble et avons installé les pièces SLA à l'état brut sur le câble avant de les post-polymériser », a expliqué M. Schulz.
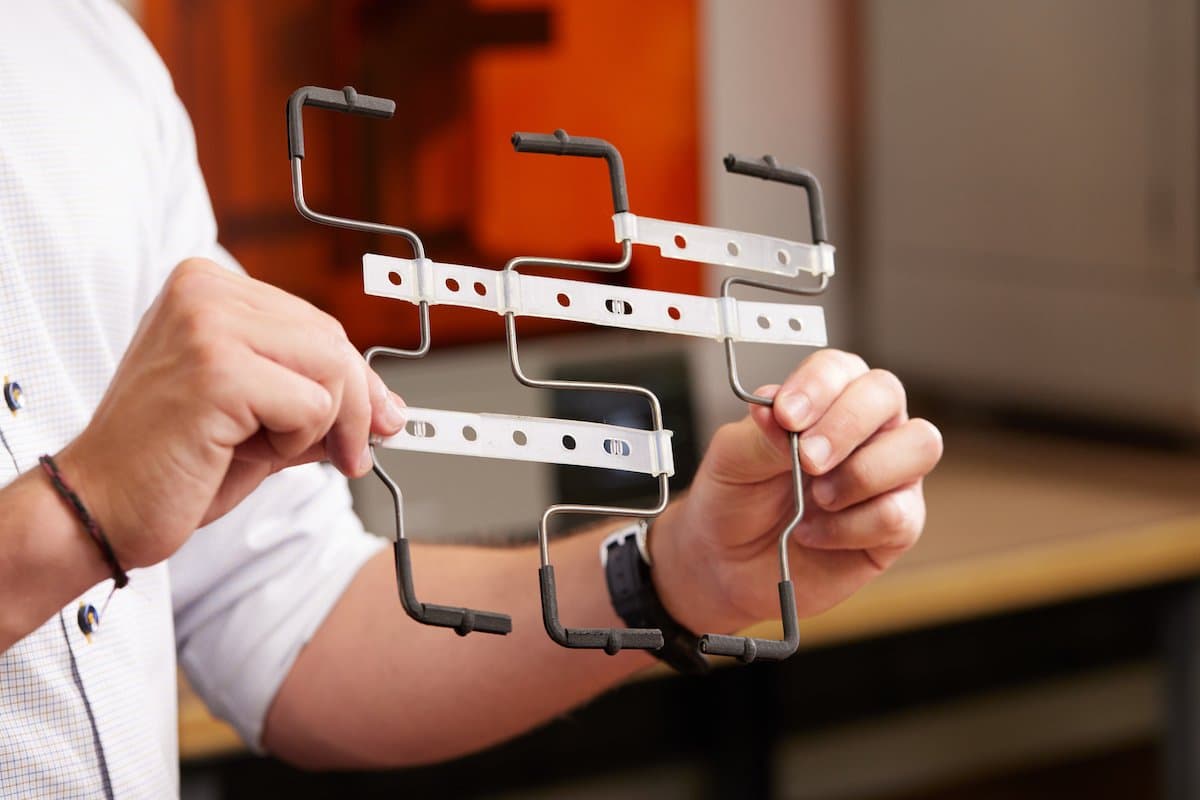
Ce tapis de suspension de siège comprend à la fois des pièces SLA (en Durable Resin, un matériau translucide) et des pièces SLS (en Nylon 12 GF Powder, un matériau gris foncé). Pour les essais, 150 assemblages complets ont été nécessaires, comprenant 900 pièces SLS et 450 pièces SLA.
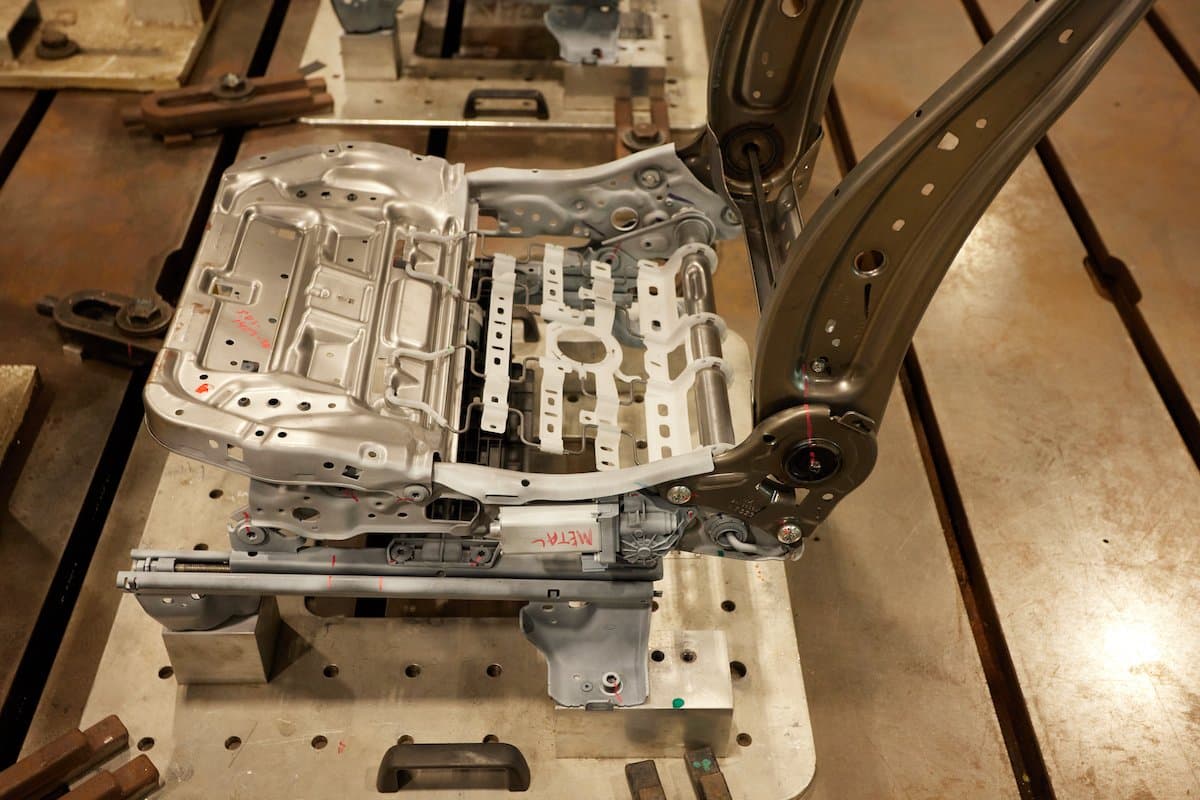
Les prototypes et les versions finales des pièces (comme celle-ci) sont soumis à des tests de fatigue simulant des années d'utilisation.
Simplifier le processus de production grâce aux aides à la production
La fabrication additive n'est pas seulement utilisée comme outil de prototypage : Brose intègre la technologie dans tous les départements de l'entreprise, suivant ainsi leur initiative Plant Goes Additive, qui a débuté en 2022. La production de composants automobiles est continue et hautement contrôlée : chaque partie du processus a été optimisée pour garantir l'efficacité, la sécurité et l'excellence du produit.
Des fixations de soudage robotisées prêtes à être imprimés le jour même avec la Form 4L
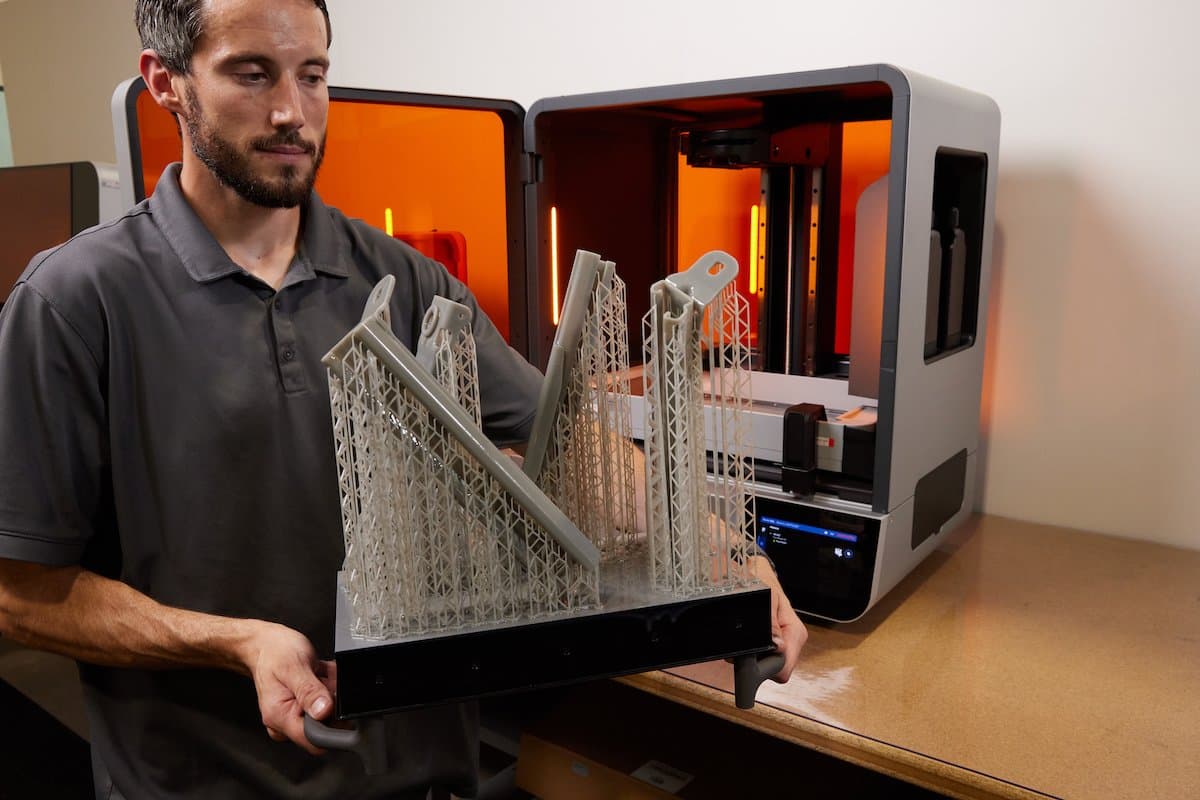
La Form 4L permet d'imprimer de grandes pièces en une journée, comme cette fixation de soudage réalisée avec Fast Model Resin.
À chaque étape de la chaîne d'approvisionnement automobile, les pièces métalliques sont des composants essentiels du produit global, et le soudage est une étape clé du processus d'assemblage. Chez Brose North America, où l'équipe de technologie additive gère un parc d'imprimantes SLA et SLS, l'équipement de soudage doit s'adapter en permanence aux différentes lignes de produits. Dans une usine, les machines à souder restent programmées pour une seule ligne de produits, mais au siège, deux machines robotisées se chargent du soudage des prototypes de sièges de toutes les différentes lignes.
Chaque fois que l'unité passe à une nouvelle ligne de produits, le service de soudage doit reprogrammer les paramètres. La programmation d'un dispositif de soudage robotisé à l'aide de rails métalliques implique des dépenses considérables et, très souvent, ces composants ne sont pas disponibles lorsque le poste de soudage est prêt à former le dispositif. L'impression 3D apporte une solution rapide et économique à ce problème, car la vitesse et la précision dimensionnelle sont précisément ce qui est requis pour ce type de pièce.
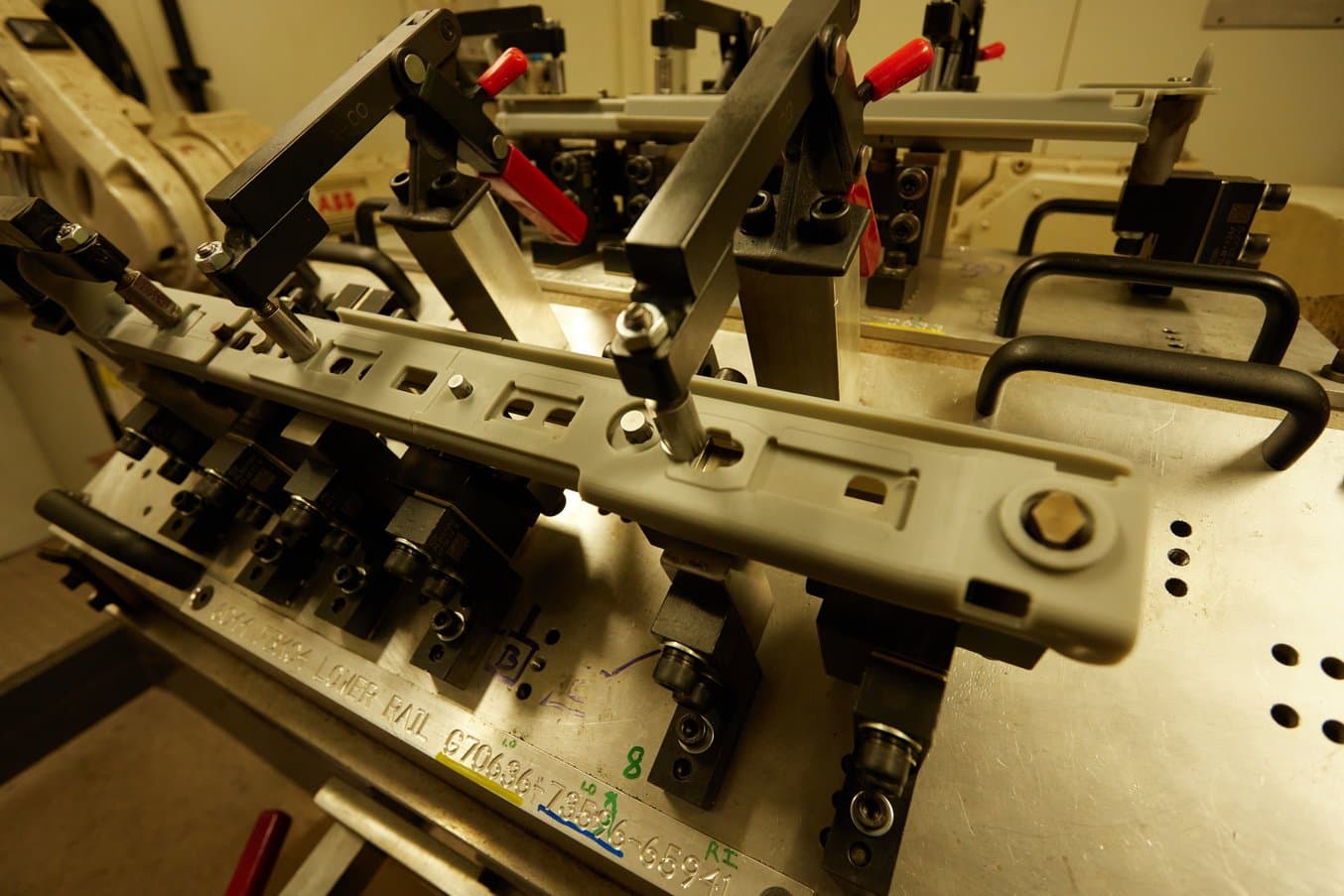
Cette pièce de siège a été imprimée sur la Form 4L avec Grey Resin, puis lavée, post-polymérisée et assemblée dans la machine à souder robotisée en moins de trois heures. L'équipe est ainsi en mesure d'ajuster rapidement le robot aux mouvements nécessaires.
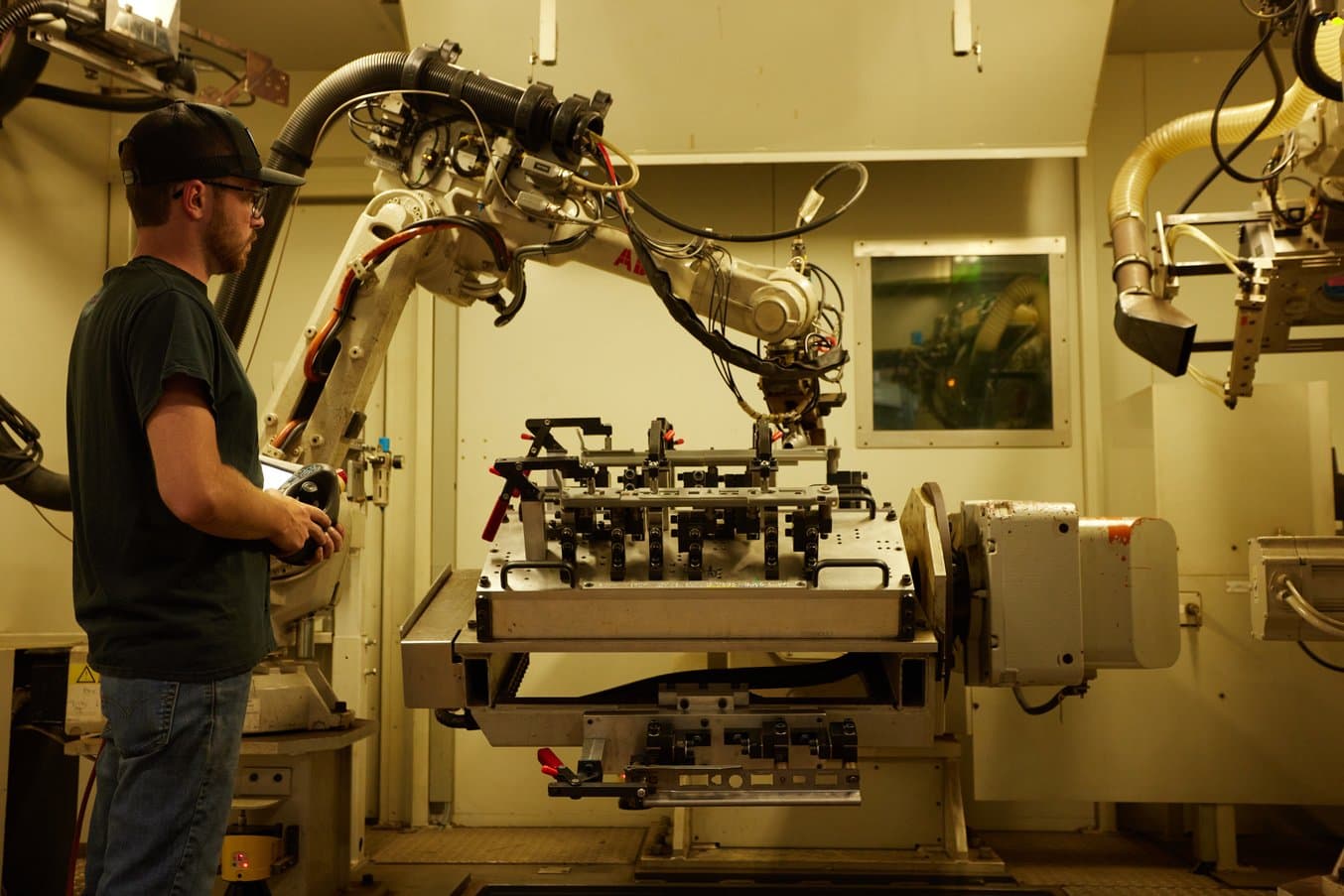
Les fixations de ce type permettent à l'équipe de soudage de passer rapidement et efficacement d'une ligne de produits à l'autre. Ces fixations sont extrêmement précises, rentables et reproductibles à l'infini en cas de modifications ou de remplacements.
L'équipe de Brose a récemment reçu une imprimante 3D résine grand format Form 4L. L'installation a été réalisée en 30 minutes seulement, après quoi le personnel a commencé à imprimer des pièces grand format pour le dispositif de soudage à l'aide de Fast Model Resin. Les pièces, divisées en quatre parties, remplissent la quasi-totalité du volume d'impression. Malgré leur taille, la Form 4L les a imprimées en moins de deux heures, et 45 minutes à peine après le lavage et la post-polymérisation, elles étaient déjà montées sur le dispositif robotisé.
« La nouvelle Form 4L de Formlabs nous permet d'imprimer rapidement des pièces de grand format. Par exemple, nous utilisons la Form 4L pour créer des pièces de réglage pour les cellules de soudage en quelques heures plutôt qu'en une nuit. Cela permet à l'équipe de soudage de Brose de programmer le dispositif robotique avant l'arrivée des composants d'estampage. Avec la nouvelle Fast Model Resin, nous obtenons le niveau de détail et la rigidité dont nous avons besoin en un temps record. »
Matthias Schulz, responsable du prototypage des sièges, Brose North America
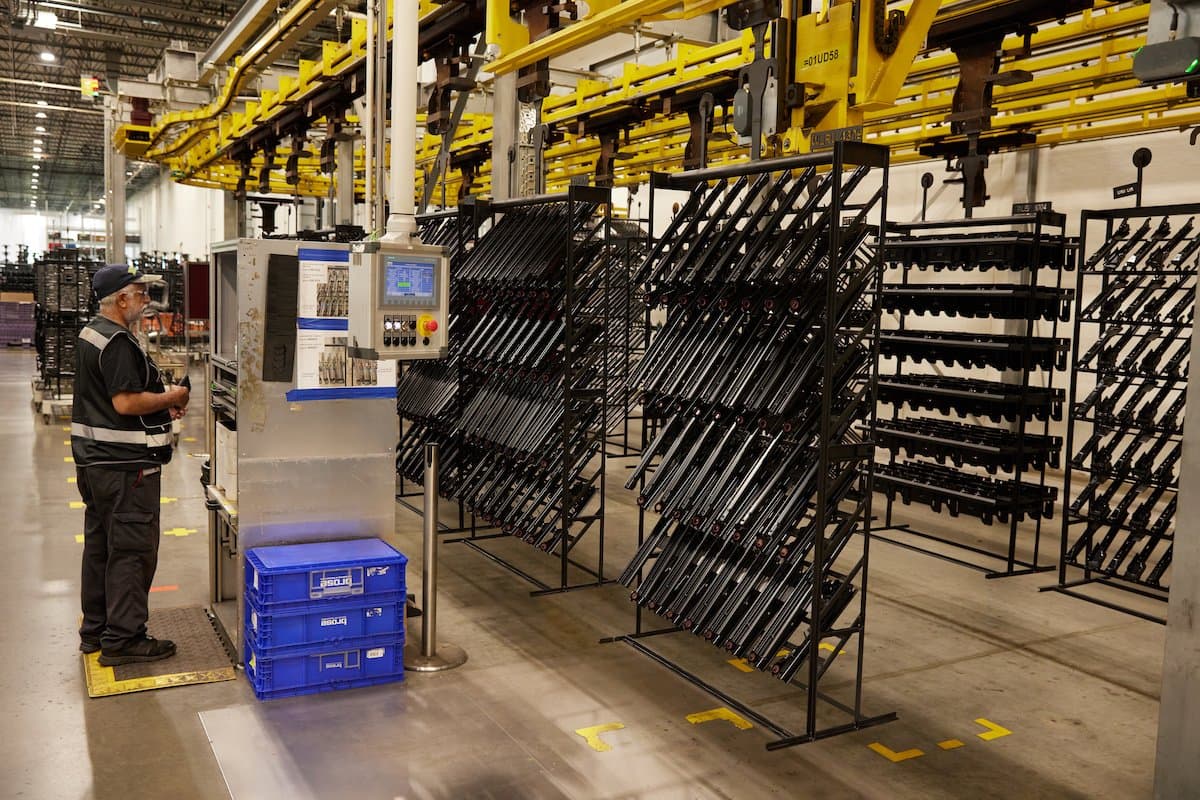
Dans l'usine de Brose New Boston, des milliers de rails de siège, visibles sur la photo, sont soudés ensemble pour créer la base de l'assemblage du siège. Le contrôle des paramètres de soudage est une étape fondamentale du processus de production.
Les paramètres de soudage définis au siège de Brose North America à l'aide de prototypes et de montages imprimés en 3D seront ensuite utilisés pour la production en série des cadres de siège soudés. Les rails du siège, visibles sur la photo précédente, seront assemblés dans l'usine de Brose New Boston à l'aide d'un grand équipement de soudage robotisé.
Réduction des coûts d'exploitation grâce aux connecteurs de fin de ligne chez Brose New Boston
Dans l'usine Brose New Boston, située à une trentaine de minutes du centre-ville de Détroit, l'équipe utilise l'impression 3D pour créer des substrats de production personnalisés qui simplifient le processus d'assemblage. Les pièces imprimées en 3D doivent être rigoureusement testées avant d'être intégrées dans la production, mais une fois que c'est fait, elles permettent de réduire les déchets, d'améliorer les délais et d'assurer le bon fonctionnement des appareils.
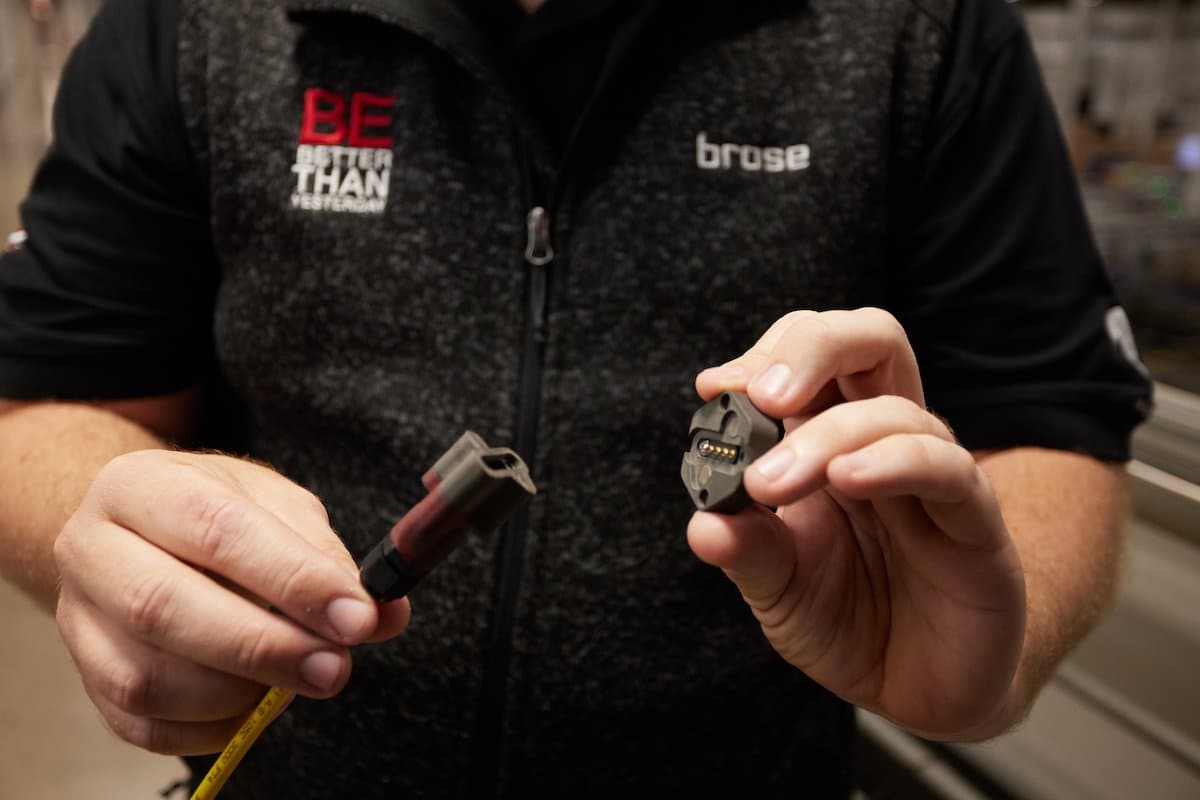
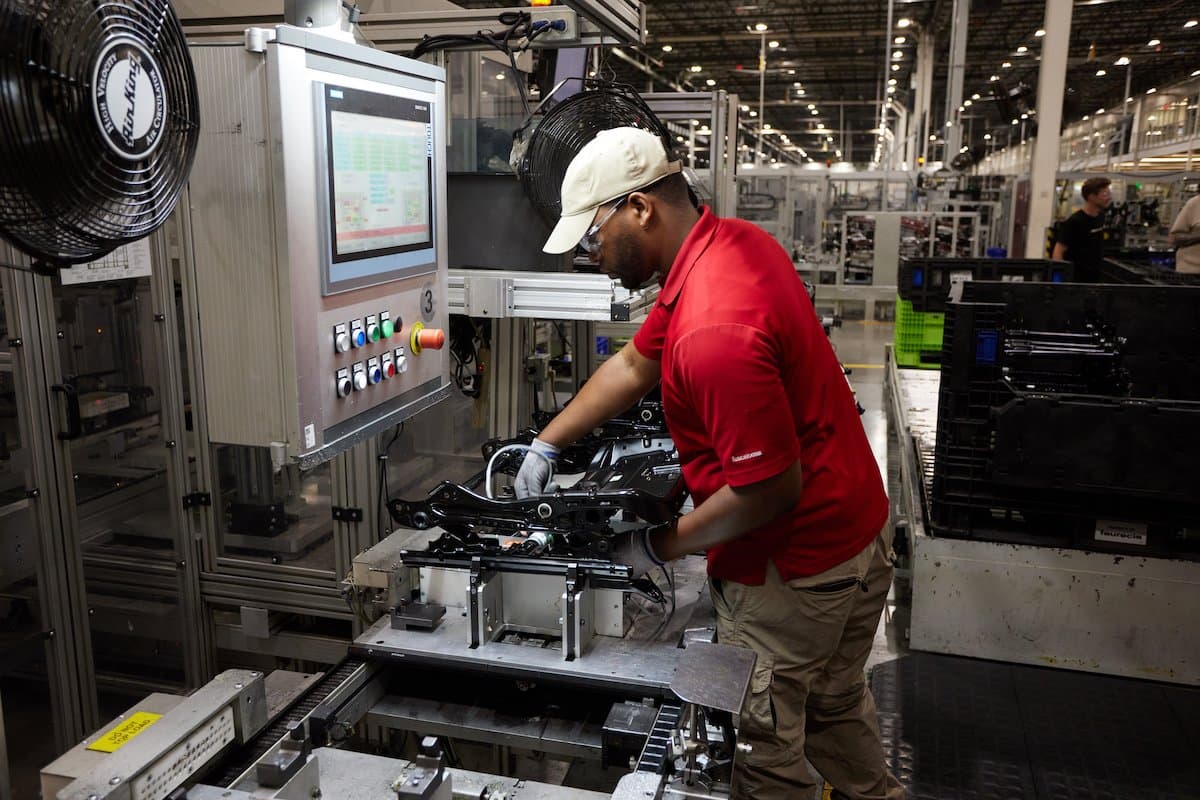
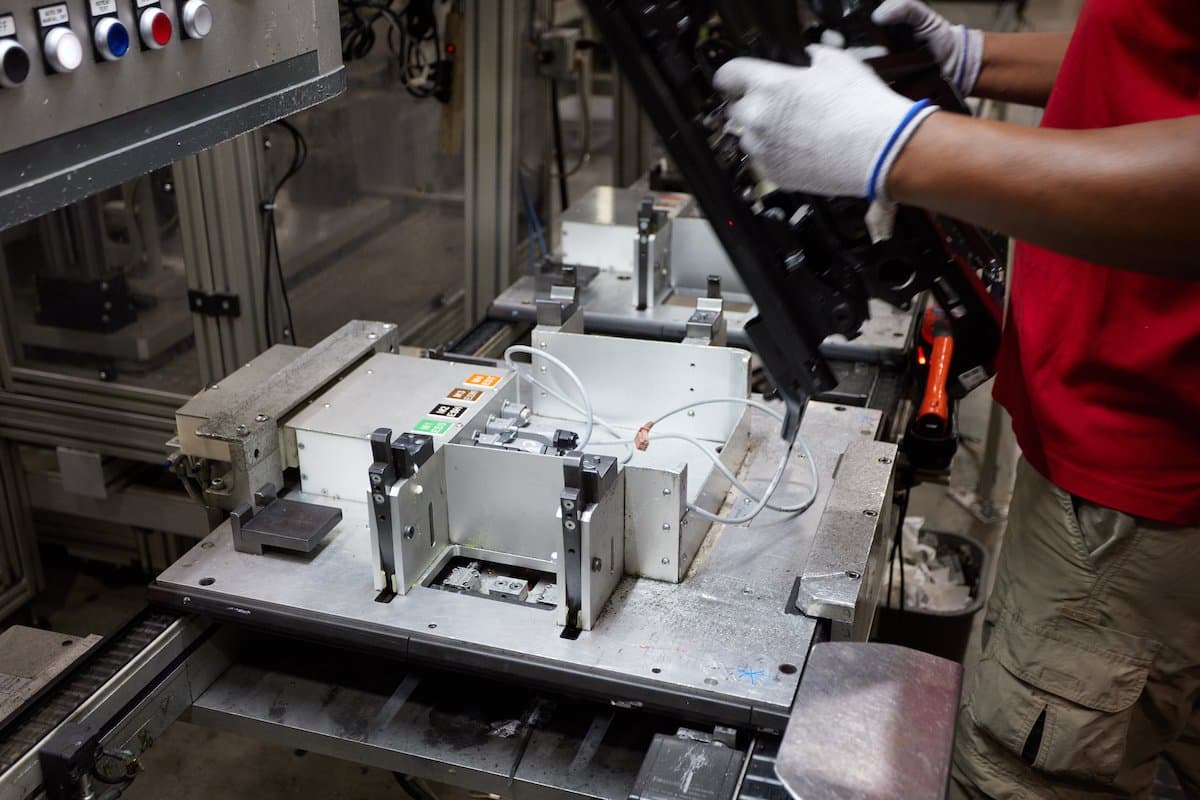

Ce connecteur de fin de ligne a été mis en place lors de la dernière étape du processus d'assemblage du siège. Après avoir branché l'armature du siège à la prise électrique et effectué le contrôle final, le personnel technique retire le siège pour passer à l'étape suivante du processus. Il arrivait souvent que la connexion électrique soit oubliée et qu'en retirant le siège, le câble se rompe, causant quelques centaines de dollars de dommages à la chaîne de montage et entraînant l'arrêt de la production.
L'équipe de technologie additive a collaboré avec l'équipe de Brose New Boston pour concevoir une ligne de connexion magnétique qui se fixe facilement à la ligne et au cadre du siège, mais qui se détache tout aussi facilement si le personnel technique retire le cadre du siège sans déconnecter manuellement le câble. « Nous utilisons des supports de production imprimés en 3D pour réduire l'usure des machines. Ils nous permettent d'effectuer des réparations plus rapides sur la ligne de production. Cela permet de réduire les temps d'arrêt et d'augmenter la productivité globale », a déclaré M. Schulz.
Production en série de gammes de pièces pour l'industrie automobile
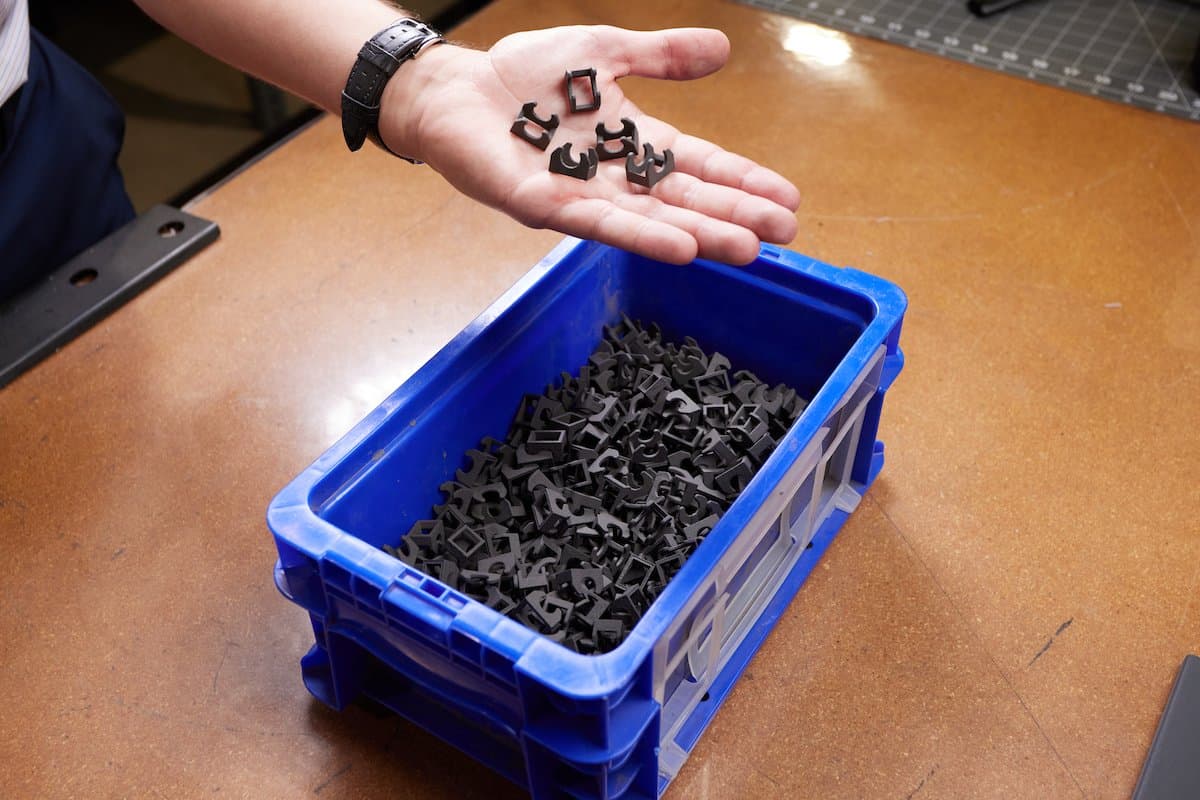
Brose imprimera en 3D 250 000 de ces clips de siège pour la BMWX7.
Selon M. Schulz, le secteur automobile a connu une évolution rapide, en particulier au cours des cinq dernières années. L'essor des véhicules électriques, la demande accrue de caractéristiques personnalisées et les préoccupations liées à la chaîne d'approvisionnement ont incité les fabricants de composants à investir davantage dans la fabrication additive en tant que moyen de production alternatif fiable.
« Nous avons de plus en plus de clients qui demandent la technologie additive. Cette technologie est également essentielle pour répondre aux besoins de l'utilisateur final, qui souhaite une personnalisation accrue des véhicules. Par conséquent, la technologie additive est de plus en plus demandée par les fabricants de composants », a déclaré M. Schulz.
Il n'a pas toujours été possible d'imprimer en 3D des pièces destinées à une utilisation finale, en particulier dans le secteur automobile, qui est soumis à des exigences réglementaires strictes. Brose et son équipe de fabrication additive n'ont veillé à adopter cette technologie que lorsque la qualité du matériel et des matériaux a permis de produire de manière fiable des pièces très performantes.
« Nous avons choisi d'utiliser l'équipement Formlabs parce que la disponibilité des matériaux et l'uniformité des impressions se sont tellement améliorées que la technologie est prête pour l'industrie automobile. Cependant, nous essayons toujours de résoudre les problèmes de sécurité et de résistance, en particulier avec les équipementiers. Avec Formlabs, nous avons prouvé que nous pouvions mettre en œuvre des pièces comme nous le faisons sur l'actuel BMW X7. »
Matthias Schulz, responsable du prototypage des sièges, Brose North America
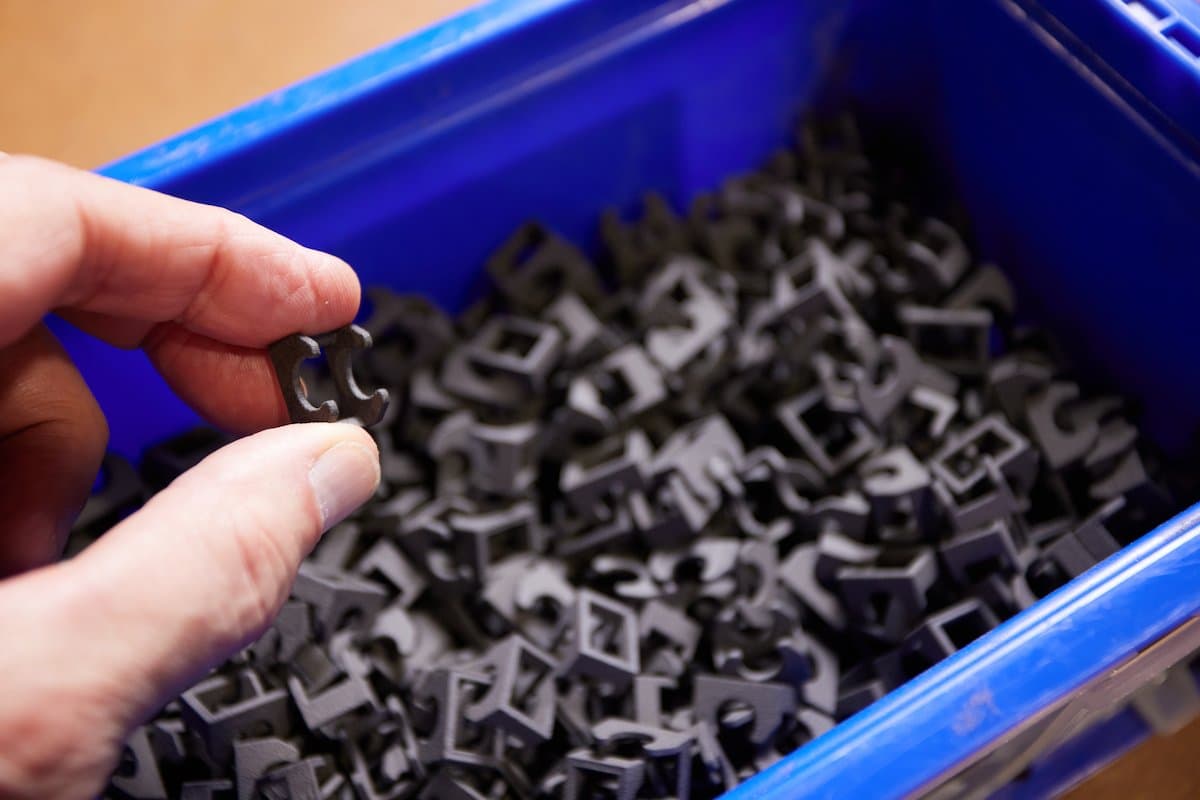
Application : pièces de siège de BMWX7
Processus de travail : Scan 3D, itération, puis impression 3D sur les imprimantes 3D SLS de la série Fuse pour la production finale.
Volume : 250 000
Détails de l'impression :
- Imprimante : Fuse 1 et Fuse 1+ 30W
- Matériaux : Nylon 12 GF Powder
- Volume d'impression : 1440 unités par chambre d'impression
- Pièces par mois : 16 000
Pourquoi l'impression 3D ?
- Pour combler la période de transition nécessaire à la disponibilité de l'équipement
Brose utilise l'impression 3D pour la production de produits finis comme une alternative abordable et rapide à la fabrication traditionnelle. Lorsqu'une entreprise de fabrication de composants a besoin d'une pièce ou de la modification d'une pièce existante, pour laquelle l'outillage ne peut pas être fabriqué ou qui ne peut pas être produite en masse rapidement, l'équipe de technologie additive de Brose évaluent si elle se prête à l'impression 3D. La rétro-ingénierie et le scan des composants existants en constituent une partie importante.
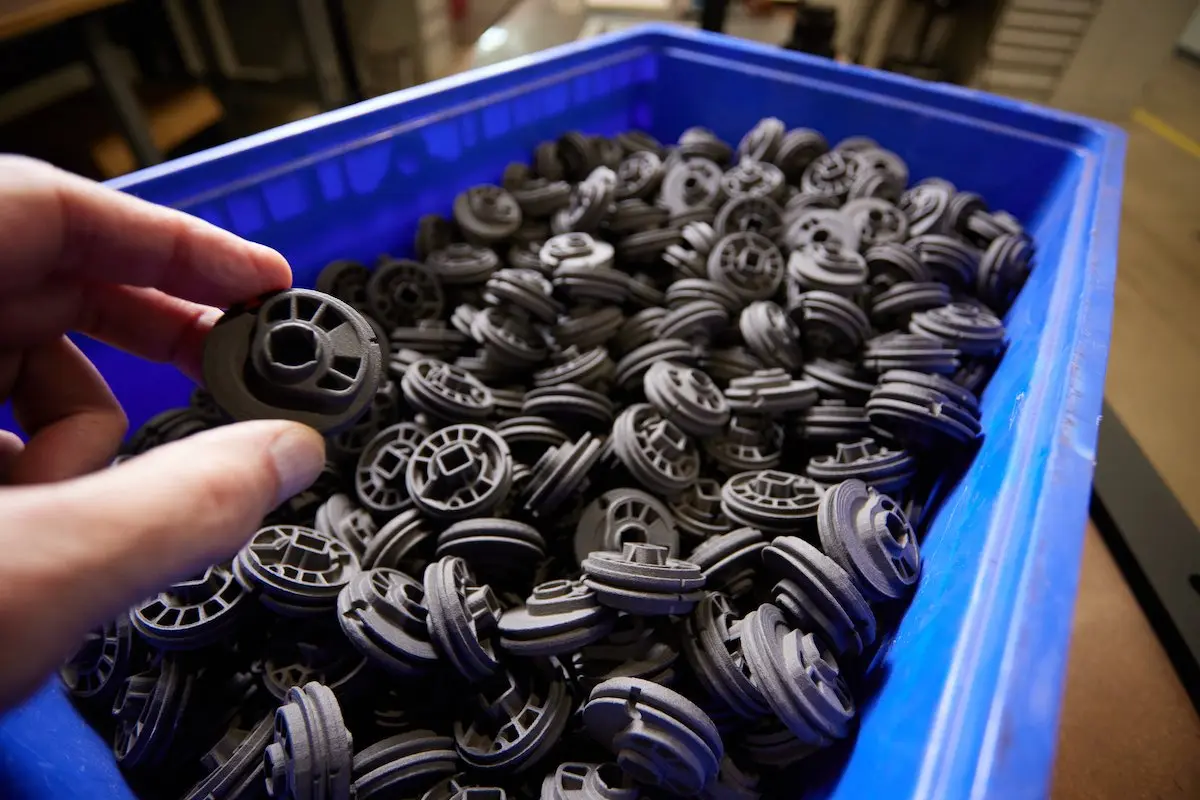
Application : roulements de câbles Bowden
Processus de travail : Scan 3D, itération, puis impression 3D sur les imprimantes 3D SLS de la série Fuse pour la production finale.
Volume : 20 000
Détails de l'impression :
- Imprimante : Fuse 1 et Fuse 1+ 30W
- Matériaux : Nylon 12 GF Powder
- Rendement : 144 pièces par chambre, 1000 pièces par semaine
Pourquoi l'impression 3D ?
- Pour combler la période de transition nécessaire à la disponibilité de l'équipement
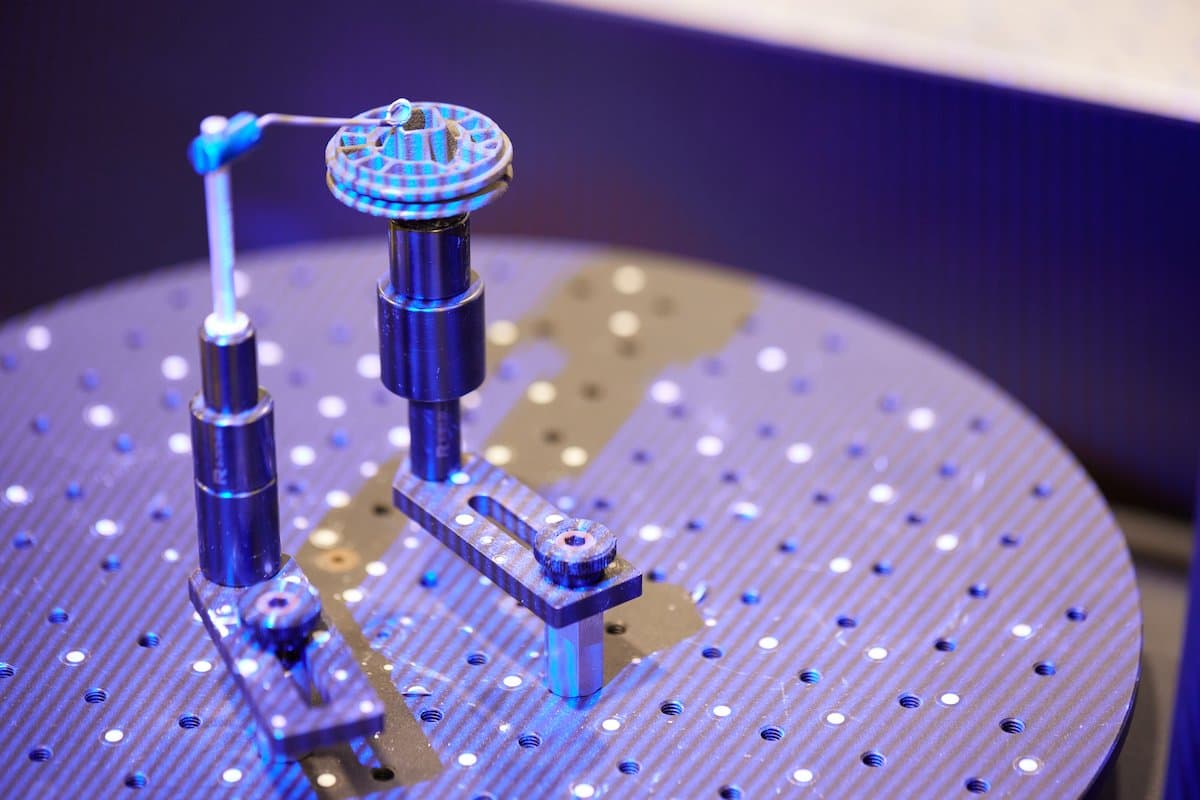
Brose scanne souvent les composants existants ou les itérations précédentes, de sorte que les modifications peuvent être apportées dans le logiciel de CAO et la version mise à jour imprimée en 3D le même jour.
Ce composant est un roulement de câbles Bowden : 20 000 de ces pièces seront produites avec le parc d'imprimantes 3D SLS de la série Fuse de Brose, et seront incluses dans l'assemblage final du siège pour un équipementier majeur et renommé.
« Brose a décidé d'intégrer la technologie SLS de Formlabs parce qu'elle nous permet d'imprimer en 3D rapidement, avec moins d'exigences de post-traitement que la technologie SLA. Nous pouvons imprimer des volumes très importants, ce qui est nécessaire pour permettre l'impression de transition ou fabriquer d'autres pièces d'utilisation finale pour les équipementiers », a déclaré M. Schulz.
Avec trois imprimantes 3D de la série SLS Fuse fonctionnant en continu pour produire des prototypes, des aides à la fabrication et des centaines de milliers de composants finaux, la fiabilité et la cohérence sont primordiales. L'équipe utilise Nylon 12 GF Powder en raison de sa précision dimensionnelle et de sa similitude avec le nylon moulé par injection, même en cas de production en grande quantité. À la fin de chaque cycle d'impression, un entretien rapide de la Fuse 1 ou de la Fuse 1+ 30W ne prend qu'une quinzaine de minutes, ce qui garantit une production continue et efficace.
« Formlabs sait comment concevoir une imprimante facile à entretenir. Les appareils sont extrêmement fiables et les erreurs d'impression sont rares, ce qui nous permet d'imprimer des volumes de pièces plus importants en toute confiance pour passer à la production », a déclaré M. Schulz.
Accélération de la production dans l'industrie automobile grâce aux imprimantes 3D
L'engagement de Brose en faveur de l'amélioration continue a conduit l'entreprise à investir dans de nouvelles technologies, telles que la fabrication additive et l'automatisation, dans le but de simplifier les processus et d'offrir des solutions innovantes aux clients. L'impression 3D joue un rôle de plus en plus important au sein de l'entreprise, et des dirigeants comme M. Schulz s'attachent à trouver de nouveaux moyens d'exploiter ses délais de production rapides et ses coûts souvent inférieurs.
Grâce à des outils rapides et puissants tels que la Form 4, la Form 4L et la série Fuse, les prototypes, les aides à la fabrication et les composants finaux peuvent être produits en quelques heures ou quelques jours, au lieu de semaines ou de mois. « Formlabs est le partenaire idéal pour nous. Nous avions besoin d'une solution prête à l'emploi qui nous permettrait de produire des volumes de pièces plus importants avec moins d'assistance technique. Les logiciels, l'assistance et les imprimantes de Formlabs sont parfaits pour cela. »
Pour en savoir plus sur l'impression 3D dans le secteur automobile, consultez notre site internet. Pour vous rendre compte par vous-même de la qualité de l'impression 3D SLA ou SLS, commandez un échantillon.