Atteignez de nouveaux sommets grâce à une imprimante de pointe : la Form 4 chez Black Diamond
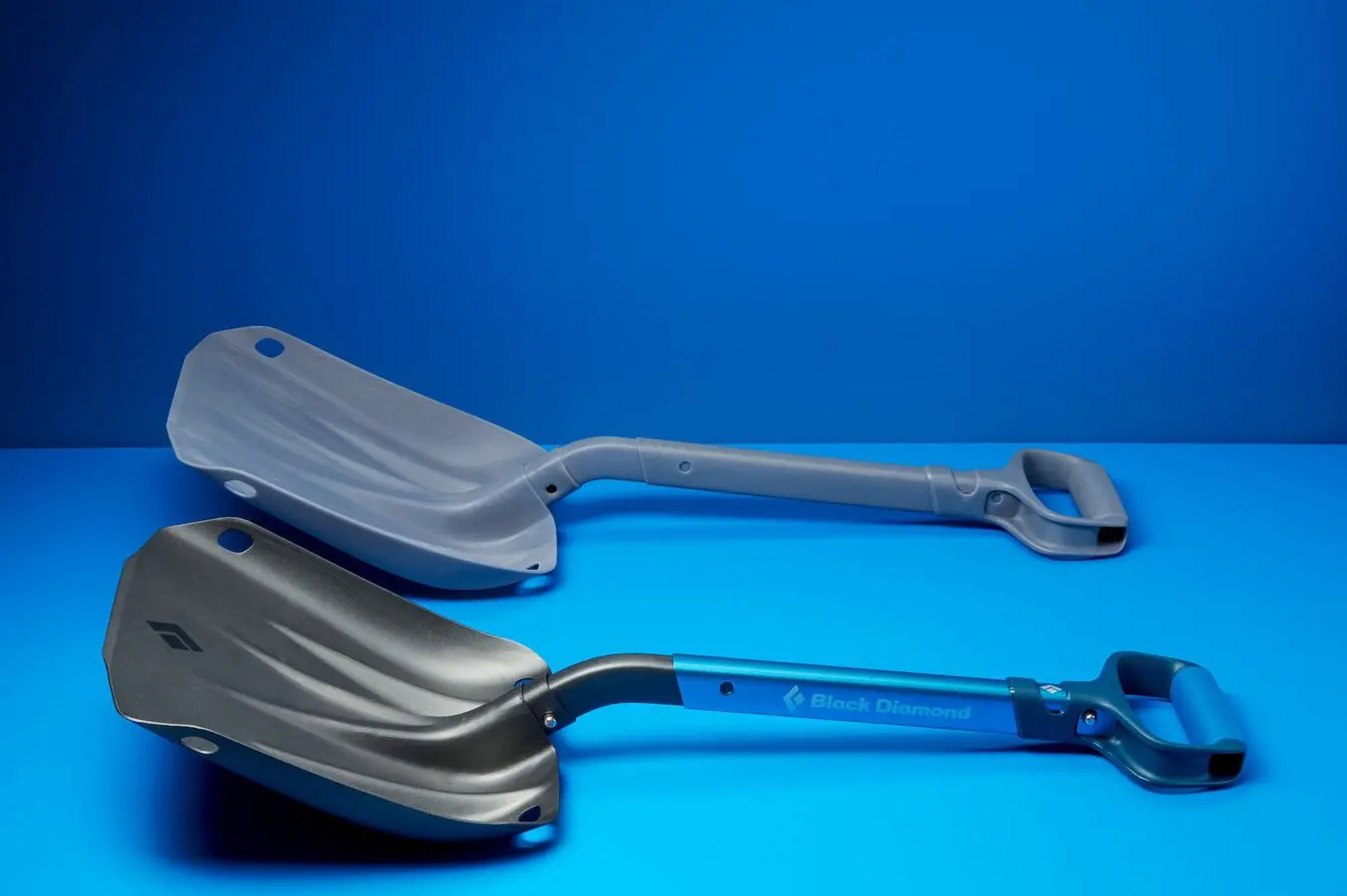
Black Diamond Equipment n'impose à son équipe de designers qu'une seule condition indispensable : un enthousiasme inconditionnel et contagieux pour l'équipement qu'ils créent. Les passionnés de sports d'extérieur et d'alpinisme qui travaillent chez Black Diamond ne demandent pas mieux.
L'équipe de conception de Black Diamond est obsédée par les détails et est extrêmement exigeante en ce qui concerne son matériel. Elle crée ainsi des équipements fiables et performants qui garantissent à tous sécurité et plaisir sur les pentes. L'équipe est tout aussi exigeante en ce qui concerne les outils utilisés pour la conception. Au fil des années, son parc d'imprimantes 3D s'est agrandi et comprend désormais des imprimantes 3D résine grand format, un parc d'imprimantes résine de bureau et à frittage sélectif par laser (SLS).
Matt Tetzl, directeur du laboratoire de conception de produits, a discuté avec nous du processus de conception de Black Diamond et a expliqué comment la Form 4, la Form 3L et les imprimantes de la série Fuse ont aidé l'équipe à passer plus de temps à tester les produits dans les montagnes Wasatch, plutôt que d'attendre dans le laboratoire que les impressions soient terminées.
Impression à haut rendement et contrôle des équipements
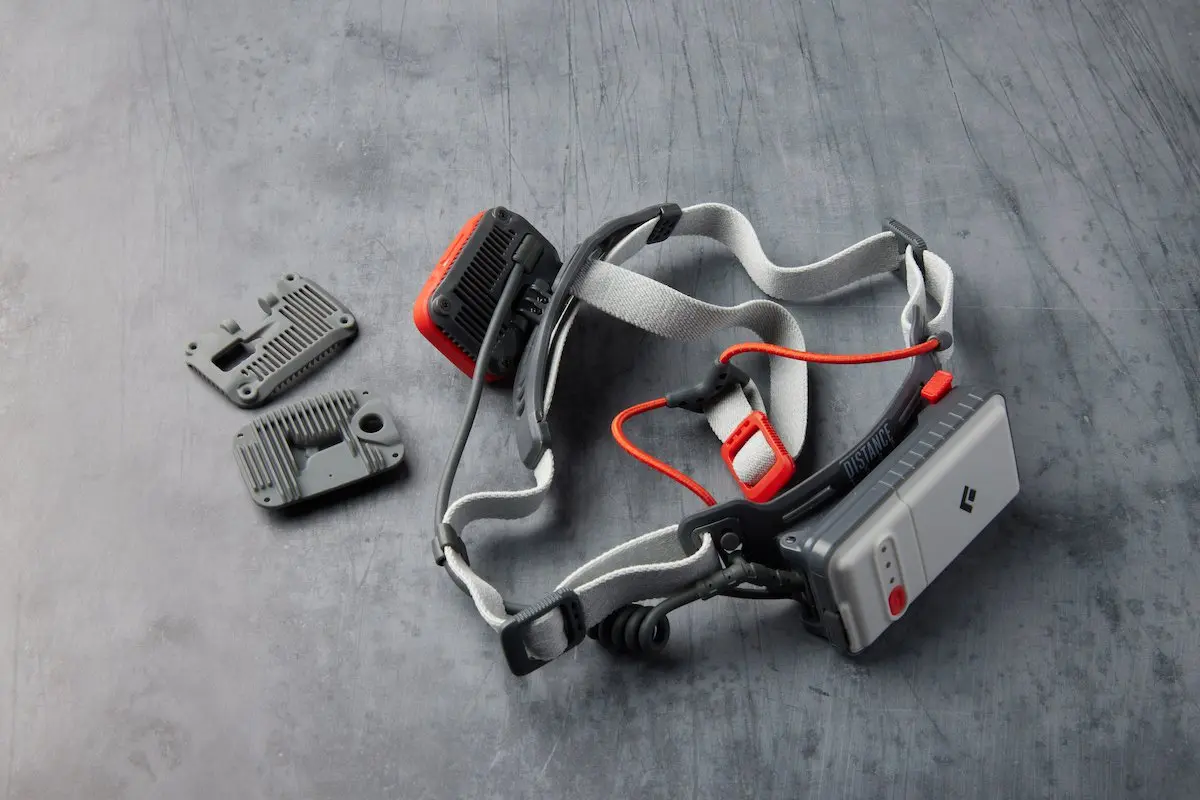
La rapidité de la Form 4 a permis à M. Tetzl de créer trois itérations de ce composant de lampe frontale (à gauche, Grey Resin V5) en une journée.
L'équipe de conception de Black Diamond doit s'assurer que ses produits sont à la hauteur du défi qui consiste à donner un sentiment de sécurité aux débutants en escalade et à aider les professionnels à battre de nouveaux records. De telles exigences nécessitent des tests approfondis, voire des millions de cycles pour certains produits. Pour faire face à cette quantité de tests, le laboratoire d'impression 3D fonctionne 24/24. « Nos imprimantes, aussi bien SLA que SLS, fonctionnent tous les jours », explique M. Tetzl. « Ma promesse à l'équipe est d'être capable de livrer les pièces pour le lendemain. »
M. Tetzl traite les demandes de plusieurs équipes, qu'il s'agisse d'impressions en résine ou en poudre. Pour cela, il utilise Dashboard, le logiciel de gestion d'impression basé sur le web pour les imprimantes 3D Formlabs. Jusqu'à présent, il envoyait la plupart des pièces destinées aux tests fonctionnels à la série Fuse, afin d'exploiter la résistance et la durabilité de Nylon 12 Powder. Mais la Form 4 l'a incité à revenir à l'impression 3D résine pour de nombreuses pièces. « Nous utilisons la Fuse tous les jours depuis qu'elle a été livrée, mais grâce à la Form 4, nous faisons à nouveau plus d'impressions résine. Je peux désormais fournir des pièces le jour même où elles sont demandées. »
Pouvoir réaliser des prototypes ou des pièces de test fonctionnelles en une journée est un immense avantage pour l'équipe de conception. « Pour la validation de la conception, c'est vraiment génial. Au lieu de réserver un jour pour l'impression et un autre pour les tests ou les itérations, nous arrivons désormais à tout faire le même jour », rapporte M. Tetzl.
« Pour un projet de lampe en particulier, nous avons conçu et imprimé trois itérations en une seule journée afin d'avoir trois pièces différentes pour notre réunion de l'après-midi. »
Matt Tetzl, directeur du laboratoire de conception de produits, Black Diamond
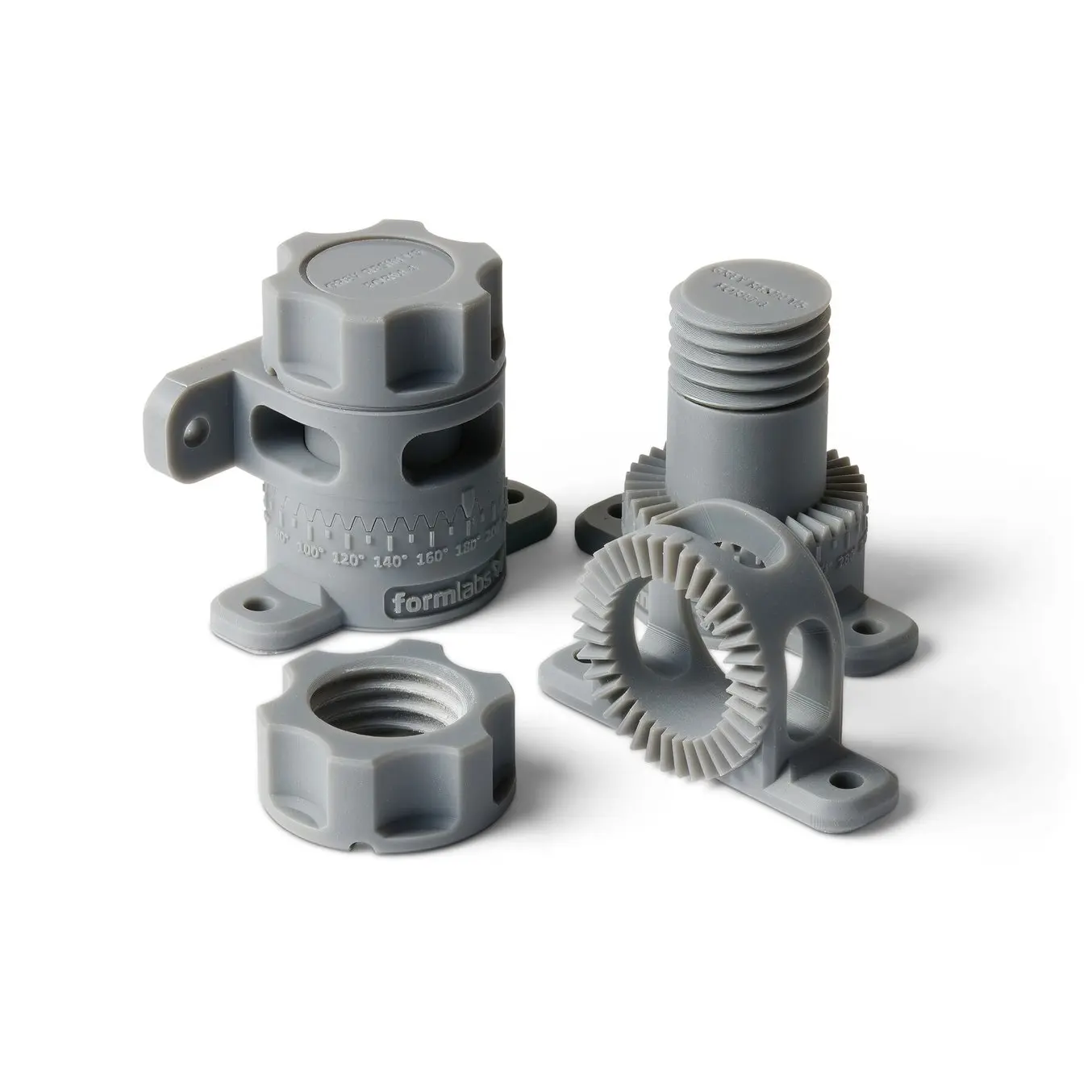
Commander un échantillon gratuit
Examinez et constatez par vous-même la qualité Formlabs. Nous enverrons un échantillon gratuit en Grey Resin V5 à votre bureau.
Fiable aussi bien en laboratoire qu'à flanc de montagne
Que l'on soit débutant en sports de montagne ou grimpeur expérimenté, on préfère toujours utiliser son énergie à planifier le parcours de randonnée ou la paroi rocheuse qui nous attend, et non à se demander si l'équipement résistera à la charge. Il en va de même pour la conception de cet équipement : M. Tetzl et son équipe mettent l'accent sur la conception ergonomique, le choix des matériaux, les tests de fatigue et toute une série d'autres facteurs qui ont leur importance pour concevoir un équipement de première classe. Ils ne doivent donc pas s'inquiéter de savoir si une impression sera réussie ou si les pièces imprimées respecteront les tolérances. Dès le premier jour, la Form 4 a permis à l'équipe de se concentrer entièrement sur le produit. « C'était vraiment du plug-and-play. Dès que vous connectez l'appareil au réseau, on retrouve l'écosystème bien connu de Formlabs : il ne reste qu'à télécharger les pièces, appuyer sur un bouton et récupérer les pièces finies », raconte M. Tetzl.
De son installation à son intégration dans le processus de travail, la Form 4 simplifie tous les processus. « C'était très intuitif. Juste après le déballage, on met l'imprimante à niveau et on se lance. Elle est aussi facile à utiliser que tous les autres systèmes Formlabs », déclare M. Tetzl.
La facilité d'utilisation et la fiabilité constantes de la Form 4 en font le choix évident pour de nombreuses pièces. « Dans 99 % des cas, je suis sûr de la réussite de l'impression. Et pour le reste, je sais que je peux résoudre le problème moi-même. Si une imprimante tombe en panne, je peux la remettre en service le jour même. Cette certitude est extrêmement satisfaisante », dit M. Tetzl.
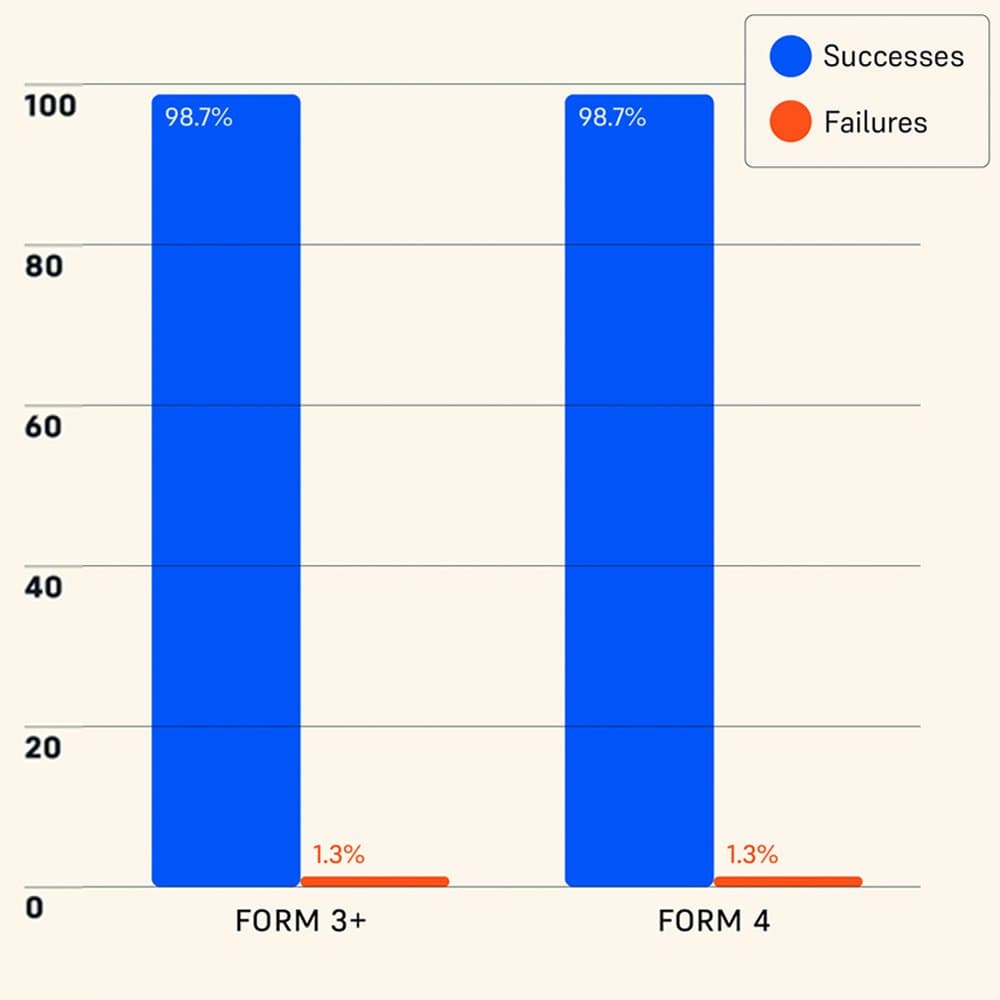
Fiabilité de la Form 4 et d’autres imprimantes 3D résine testée de manière indépendante
Une importante société indépendante de test de produits a mesuré un taux de réussite d’impression de 98,7 % pour la Form 4 de Formlabs. Lisez une description complète de la méthodologie d’essai et consultez les résultats dans notre livre blanc.
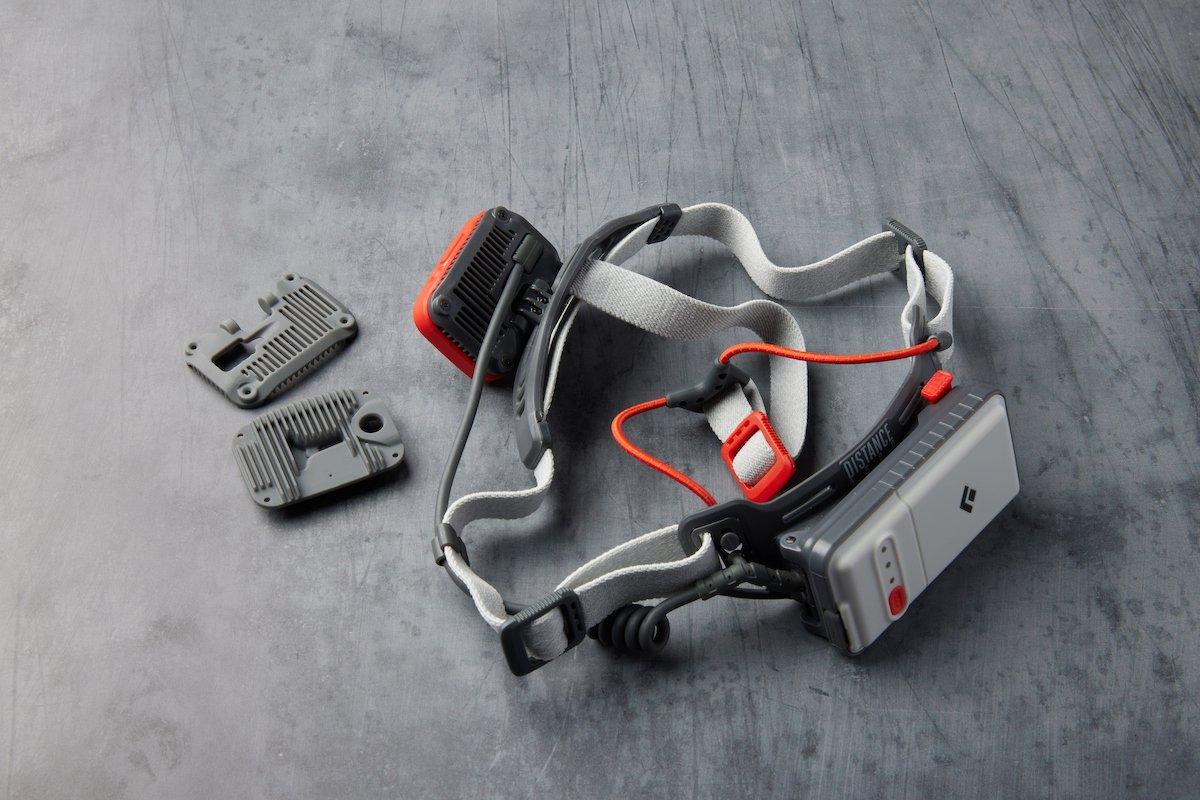
Guide de prototypage rapide pour le développement de produits
Dans ce guide, vous découvrirez comment le prototypage rapide s'intègre au processus de développement de produits, ses applications, et les outils de prototypage rapide dont les équipes de développement de produits disposent aujourd'hui.
Rien ne vaut un bon matériau : polyvalence, précision et performance
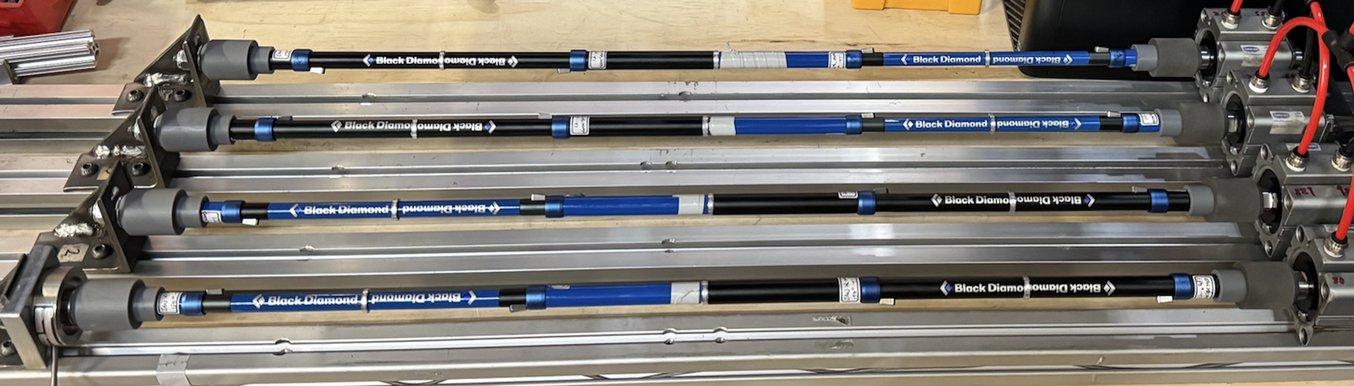
Cette configuration pour les tests de fatigue d'un bâton de trekking comprend des supports imprimés sur la Form 4 en Grey Resin V5 (à gauche) ou sur la Fuse 1+ 30W en Nylon 12 Powder (à droite).
Pour des produits aussi techniques que les équipements de Black Diamond, le processus de développement doit couvrir une large gamme de propriétés des matériaux ainsi que des tests approfondis. Dans le cycle de développement produit d'un bâton de trekking léger, la Form 4 et la nouvelle Grey Resin V5 ont récemment été mis à l'épreuve.
Auparavant, les composants du bâton de trekking avaient été testés dans une variante en Nylon 12 Powder de l'imprimante Fuse. « La plupart de nos tests fonctionnels sont effectués avec du nylon, mais nous avons réalisé cette fixation sur la Form 4 parce qu'elle nous permet d'essayer plusieurs conceptions en quelques heures », explique M. Tetzl.
Bien que l'équipe ait d'abord douté de la capacité de la résine SLA à résister à l'immense pression et aux tests de friction subis par le bâton de randonnée, les boutons en Grey Resin V5 du mécanisme du bâton ont résisté à plus d'un million de cycles avec une charge de 35 livres par cycle, puis à plus d'un million de cycles supplémentaires. « Cette version du produit est plus solide que les précédentes. Pour les casques, nous obtenons un niveau de détail plus élevé qu'avec la Form 3 », explique M. Tetzl.
Ce niveau de détail est essentiel pour les grands prototypes de casques que l'équipe réalise sur ses imprimantes de bureau et d'atelier : la Form 4 et la Form 3L. « La qualité de la surface est très bonne. L'équipe est vraiment impressionnée par toutes les pièces que nous avons imprimées en Grey Resin et Clear Resin sur la Form 4. »
La Form 3L repousse les limites du possible
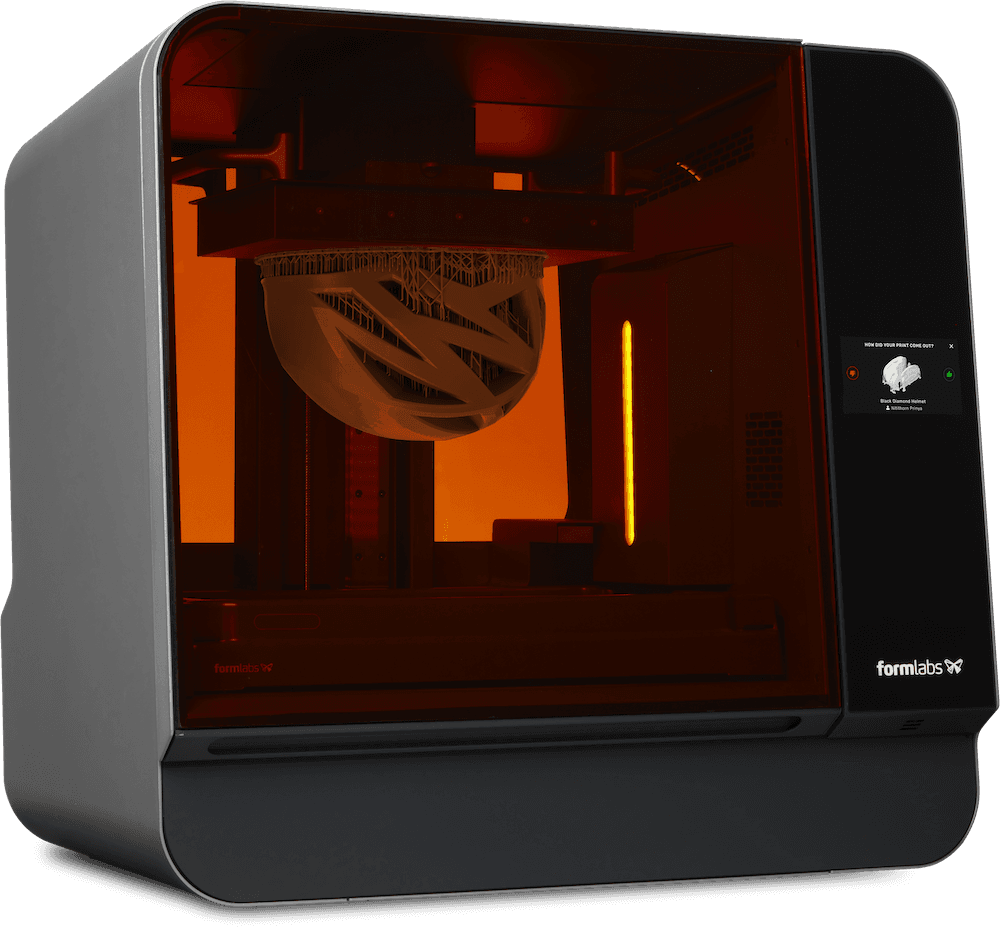
L'impression 3D résine d'atelier ouvre la voie au prototypage grandeur nature, sans pour autant transiger sur la qualité de surface et sur la diversité des matériaux.
La rapidité, le grand choix de matériaux et la qualité des surfaces permettent à l'équipe de conception de Black Diamond de fabriquer des prototypes plus rapidement tout en gardant un meilleur contrôle sur l'ensemble du processus. « Au départ, nous avions acheté la Form 3L uniquement pour réaliser des prototypes de casques. Nous avons alors réalisé que nous pouvions également l'utiliser pour un certain nombre d'autres projets nécessitant un volume d'impression important », explique M. Tetzl.
Il y a quelques années, Black Diamond a pris plusieurs mesures pour transférer en interne la phase de développement d'une catégorie de produits compétitive et très technique : les chaussures. L'équipe avait engagé un cordonnier en interne et a reconnu les possibilités que la Form 3L leur offrait lorsqu'elle a commencé à l'utiliser pour produire des casques. « Nous avons réalisé que nous pouvions réaliser des semelles intermédiaires en taille réelle avec un niveau de détail et une finition de surface élevés. L'équipe responsable apporte de nombreuses modifications vraiment minuscules au design des semelles intermédiaires, c'est pourquoi les capacités d'impression grand format de l'entreprise lui sont vraiment d'une grande aide », explique M. Tetzl.
Si la Form 3L était au départ une simple « imprimante à casque », elle est devenue en très peu de temps un outil polyvalent qui permet de réaliser les projets les plus divers. Lors des phases finales de développement d'un piolet, l'équipe a imprimé des prototypes grandeur nature à l'aide de la Form 3L afin de tester le toucher et la capacité d'accrochage sans risquer qu'un prototype assemblé en plusieurs parties ne se casse. Après quatre ans à essayer différentes versions de conception, les phases d'itération finales ont été énormément accélérées par l'impression 3D résine grand format en interne.
« Vous pouvez regarder un piolet toute la journée, mais au final, ce qui compte, c'est la sensation qu'il procure. Le fait de pouvoir l'imprimer en 3D et d'avoir une idée de la sensation de préhension et d'accrochage est très précieux », explique M. Tetzl.
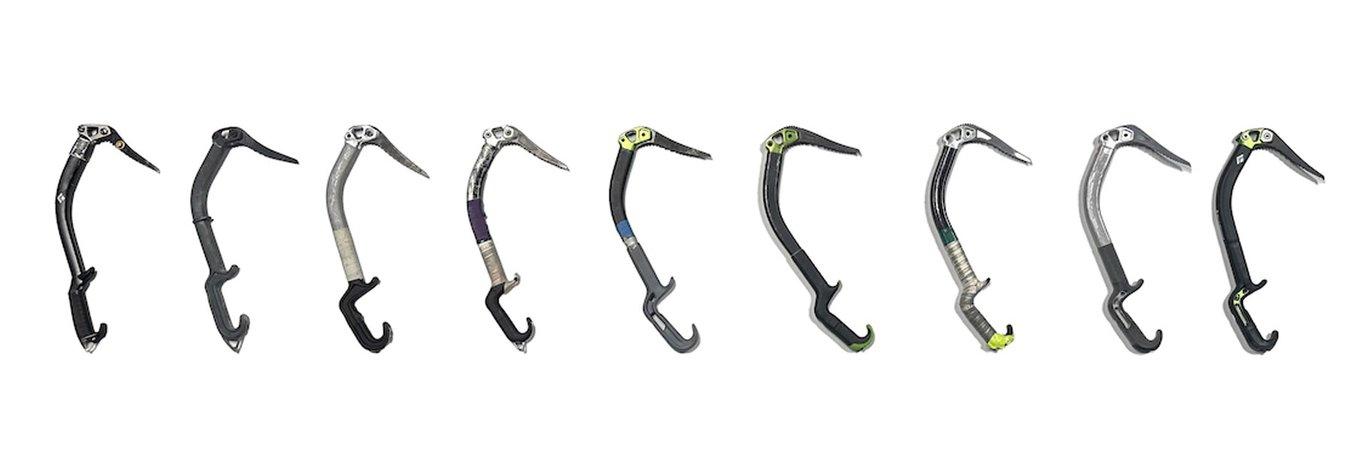
Grâce à l'impression 3D et aux capacités SLA et SLS de l'entreprise, l'équipe a pu créer des prototypes du piolet sans craindre que les composants assemblés n'affectent la sensation de la prise en main ou la force nécessaire pour le planter.
Le toucher des pièces dépend aussi des matériaux. M. Tetzl imprime la grande majorité de ses pièces en Grey Resin, mais utilise également Clear Resin pour la fabrication de moules d'uréthane en plusieurs parties. « Nous avons fait de la Form 3L notre plateforme pour les moules, en particulier lorsqu'ils sont composés de plusieurs pièces. Clear Resin donne de très bonnes pièces et il est pratique de pouvoir voir l'uréthane lors du remplissage de la cavité », explique M. Tetzl. Les moules en Clear Resin sont lavés, post-polymérisés, aspergés d'agent de démoulage uréthane et enfin remplis et laissés au repos pendant 15 minutes. Les moules imprimés en 3D en interne permettent de réaliser des prototypes parfaitement fonctionnels dans des matériaux plus souples et résistants aux UV tels que l'uréthane, sans avoir à sous-traiter la fabrication des outils.
Avant que l'équipe ne fasse appel à des capacités d'impression 3D à grande échelle, la sous-traitance des moules et des prototypes de grande taille tels que les casques représentait une dépense importante et allongeait encore la durée du processus de conception. Le contrôle accru du processus de développement des casques, des semelles intermédiaires et des moules permet désormais de réduire les coûts et de raccourcir d'autant les délais de production.
Des pièces en nylon fabriquées en interne pour effectuer des tests pratiques, et plus encore
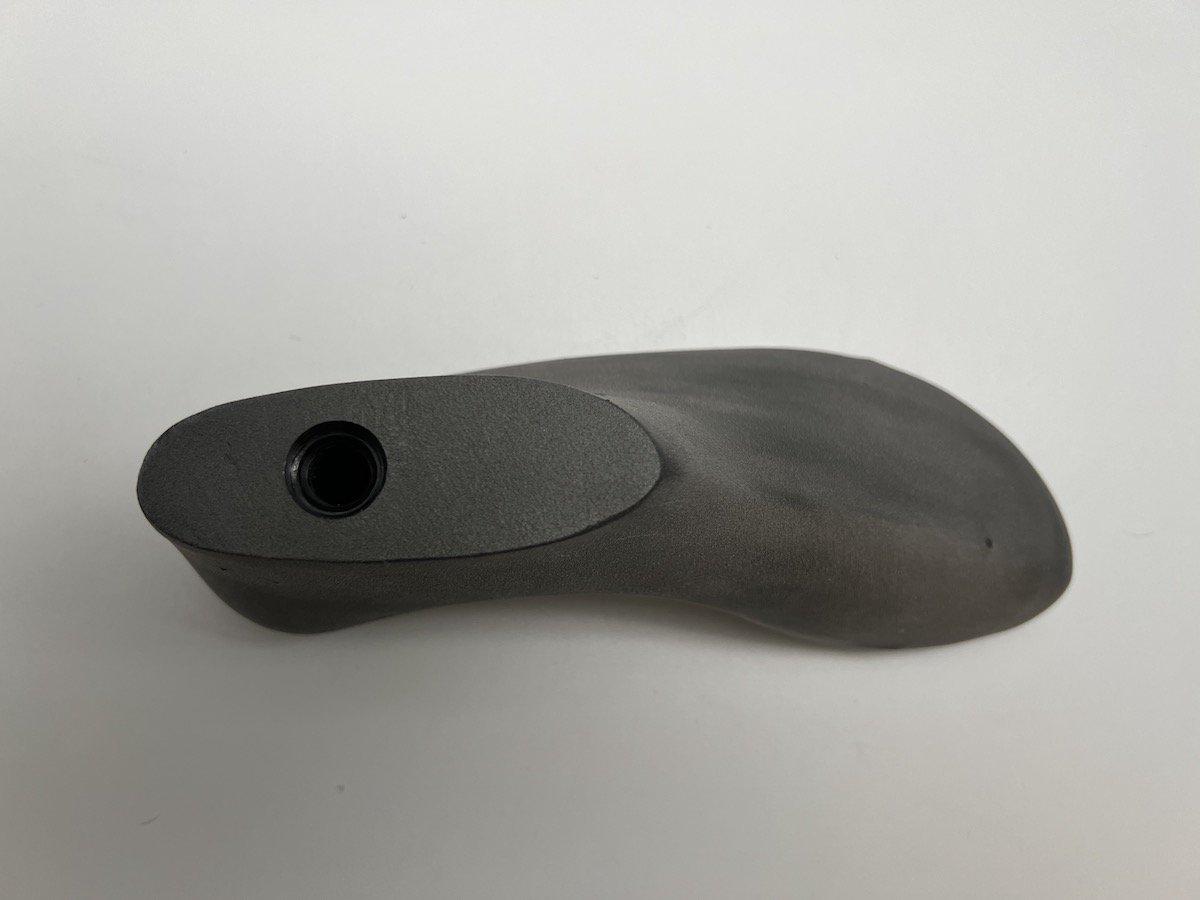
En imprimant ce modèle de chaussure en interne avec Nylon 12 Powder sur la Fuse 1+ 30W, l'équipe a pu réduire ses coûts. Une pièce en nylon coupée comme celle-ci pourrait coûter jusqu'à 2000 $ si elle était produite par un sous-traitant, alors que l'impression en interne ne coûte que 65 $.
En plus de l'impression 3D résine grand format, l'équipe de M. Tetzl a également intégré l'impression SLS dans ses locaux. Après la validation de la conception avec des pièces en résine, il a utilisé des matériaux plus robustes et adaptés à l'utilisation finale pour effectuer des tests fonctionnels.
Auparavant, M. Tetzl envoyait des pièces à un sous-traitant en impression 3D équipé d'une imprimante MJF, mais cela lui coûtait cher. « Il s'agissait du même processus avec les mêmes matériaux, il était donc logique de résoudre le problème en interne afin de travailler plus rapidement et à moindre coût. Le résultat était exactement ce que nous voulions : nous obtenons la plupart des pièces pour 80 % moins cher », rapporte M. Tetzl.
Dans le cas de prototypes de ce type destinés à des tests pratiques, il est important qu'ils puissent résister à de lourdes charges et à une utilisation intensive. La résistance et la durabilité de Nylon 12 Powder ont permis à l'équipe de Black Diamond d'utiliser les prototypes dans leur environnement préféré : en extérieur, sur une montagne. Lors des Championnats du monde d'escalade sur glace 2023 à Edmonton, au Canada, un participant a utilisé un piolet dont la poignée a été imprimée en Nylon 12 Powder sur la Fuse 1+ 30W. Le piolet a fait une chute de 24 mètres avant de se planter dans la glace en contrebas, mais il a résisté à l'impact sans aucune fracture ni dommage. « Nous avions déjà des composants fonctionnels dans les skis, nous avons fabriqué des composants internes pour un testeur de chute, qui doivent résister à une charge considérable de manière répétée. Nous pouvons enfin fabriquer en interne des pièces imprimées en 3D très résistantes », déclare M. Tetzl
La Fuse 1+ 30W aide également l'entreprise à réduire les coûts de développement des chaussures. Pour le moulage des chaussures ou des bottes, le cordonnier interne à l'entreprise utilise de grands moules, généralement fabriqués en nylon. L'équipe se procurait auparavant ces pièces grand format auprès d'un prestataire de services de fabrication, mais en les imprimant avec Nylon 12 Powder sur la Fuse 1+ 30W, elle a pu réduire ses coûts de 2000 $ à seulement 65 $ et raccourcir le délai de fabrication. « La Fuse nous a permis d'intensifier notre utilisation du nylon pour nos nouveaux projets de chaussures. »
En faisant fonctionner la Fuse 1+ 30W presque tous les jours à une densité de 15 à 20 %, Black Diamond peut faire évoluer efficacement et à moindre coût le développement de ses chaussures par impression 3D SLS et augmenter ses capacités de tests fonctionnels.
Une capacité accrue grâce à la Form 4
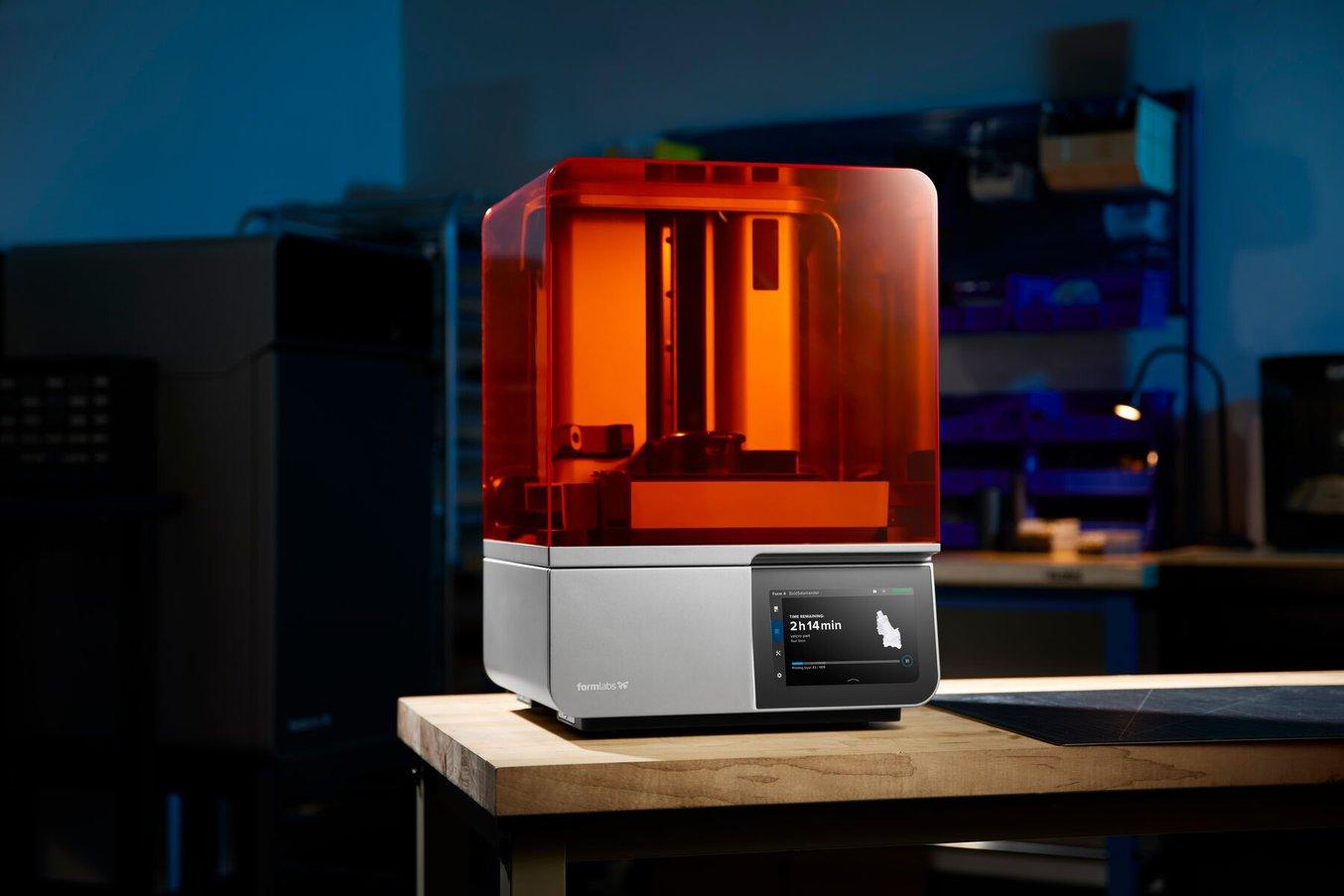
Sa fiabilité et sa rapidité font de la Form 4 un ajout précieux au parc d'imprimantes 3D de Black Diamond. Pouvoir imprimer plusieurs itérations par jour permet à l'équipe de passer moins de temps à attendre les pièces imprimées et plus de temps à créer la prochaine grande innovation en alpinisme.
Avec des centaines de produits et une file d'attente d'impression qui ne semble jamais diminuer, M. Tetzl a besoin de fiabilité, de rapidité et d'une qualité d'impression uniforme. Black Diamond a utilisé les imprimantes Formlabs à maintes reprises : son processus de travail s'est d'abord appuyé sur la Form 2, puis sur la Form 3, la Form3 +, la Form 3L, la Fuse 1+ 30W et maintenant la Form 4. Pour fabriquer des équipements auxquels les grimpeurs, les randonneurs et les alpinistes font confiance et qui peuvent même sauver des vies, l'équipe de conception de Black Diamond a besoin d'outils d'une fiabilité sans faille. L'équipe ne fait aucun compromis sur cette fiabilité, même en termes de rapidité ou de diversité des matériaux. Cependant, comme l'a fait remarquer M. Tetzl, la Form 4 offre le même système que celui avec lequel il est familier.
« Nous n'avons pas eu une seule erreur d'impression sur la Form 4. »
Matt Tetzl, directeur du laboratoire de conception de produits, Black Diamond
Grâce à la rapidité de la Form 4, l'équipe de Black Diamond passe moins de temps à attendre que les impressions se finissent et plus de temps à son activité favorite : tester ses produits dans la chaîne de montagnes Wasatch.