Comment résoudre les problèmes des laboratoires grâce à l'impression 3D
L'une des plus grandes chaînes de laboratoires de Norvège, SINTEF Norlab, est spécialisée dans les mesures environnementales, l'eau potable, les analyses microbiologiques et chimiques ainsi que les essais de matériaux. L'entreprise existe depuis 1955 et emploie actuellement 110 personnes réparties dans 13 laboratoires à travers le pays.
Jørn Røssvoll travaille depuis un peu plus de 20 ans au siège de Mo I Rana, une petite ville située juste en deçà du cercle arctique. Son travail consiste à effectuer des examens avec des microscopes électroniques à balayage (MEB) et à veiller au bon fonctionnement des systèmes informatiques et de divers instruments, tels que les appareils à rayons X et les MEB. Dans le cadre de son travail (qui est aussi sa passion), M. Røssvoll aime inventer de nouveaux outils et appareils pour accélérer et simplifier l'exécution de ses tâches.
Ces divers projets nécessitent de nombreuses pièces personnalisées, qu'il créait auparavant à l'aide de tours et de moules. Cependant, en 2016, il a découvert la conception CAO et a convaincu l'entreprise d'acheter une imprimante 3D stéréolithographique (SLA) Form 2 pour accélérer le travail. Depuis lors, il a élargi son parc avec une nouvelle Form 3 et a lancé environ 328 impressions sur les deux imprimantes pour créer plus de 2600 pièces.
Lisez la suite pour découvrir comment Jørn Røssvoll crée des appareils complexes et personnalisés qui permettent de résoudre les problèmes quotidiens des laboratoires.
Pourquoi utiliser l'impression 3D dans un laboratoire ?
Pour entretenir ses différents instruments et appareils de mesure et les adapter aux exigences de projets spécifiques, M. Røssvoll a souvent besoin de pièces sur mesure ou de pièces de rechange.
« Dans le nord de la Norvège, nous sommes loin de tout. Trouver des pièces de rechange peut s'avérer compliqué. En particulier dans le secteur des laboratoires : si vous devez commander des pièces spéciales, elles peuvent vous coûter les yeux de la tête. Une fois, nous avons dû acheter 15 petits cônes en plastique avec des fils, et ils coûtaient environ 100 dollars pièce. Je me suis dit : "Hmm, ça ne doit pas être sorcier". J'ai reproduit la pièce et me suis rendu compte que le matériel nécessaire ne coûtait que deux dollars et demi », a déclaré M. Røssvoll.
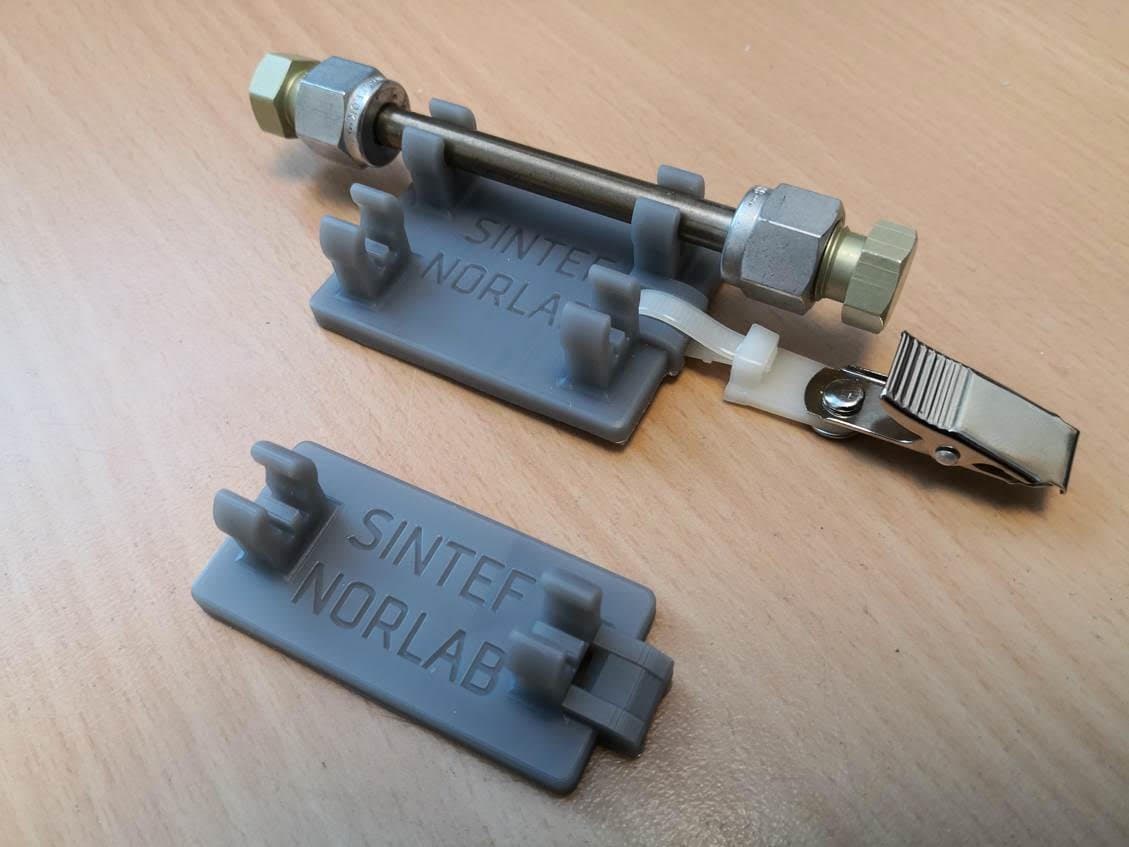
Ce support s'attache à la poche d'un travailleur et sert à transporter des tubes en acier contenant des produits chimiques pour mesurer les hydrocarbures. Les supports originaux étaient souvent perdus et leur remplacement était coûteux. Les pièces de rechange imprimées en 3D coûtent moins d'un dollar à fabriquer.
L'impression de la plupart des pièces ne prend que quelques heures. Si M. Røssvoll devait les commander, certains instruments pourraient rester hors service pendant plusieurs semaines. Lorsque les pièces sont expédiées de l'étranger, elles doivent passer par les douanes, ce qui peut être un processus fastidieux. Il est souvent plus facile et moins cher de simplement les fabriquer soi-même.
« Avant l'arrivée de l'impression 3D, je devais fabriquer la plupart des pièces avec un tour, ou je devais créer un moule en silicone pour pouvoir les couler en époxy. Cela prenait beaucoup de temps. Lorsque les imprimantes SLA sont devenues abordables, j'ai donc rapidement obtenu l'accord de mon patron pour acheter une imprimante Form 2. Le principal avantage de la méthode SLA est qu'elle permet de fabriquer des pièces isotropes, qui présentent donc les mêmes propriétés dans toutes les directions », explique M. Røssvoll.
« J'ai parfois dû imprimer beaucoup de pièces en peu de temps, parce que nous avions un gros contrat avec une entreprise et que nous devions préparer tout le matériel avant de l'envoyer à une date fixée. » Je n'avais pas beaucoup de temps pour tout imprimer. Quand je n'avais encore que l'imprimante Form 2, je devais parfois venir à 2 heures du matin pour retirer des pièces et lancer une impression. Pour pouvoir doubler la production, j'ai vite obtenu l'autorisation d'acheter une imprimante Form 3 », a déclaré M. Røssvoll.
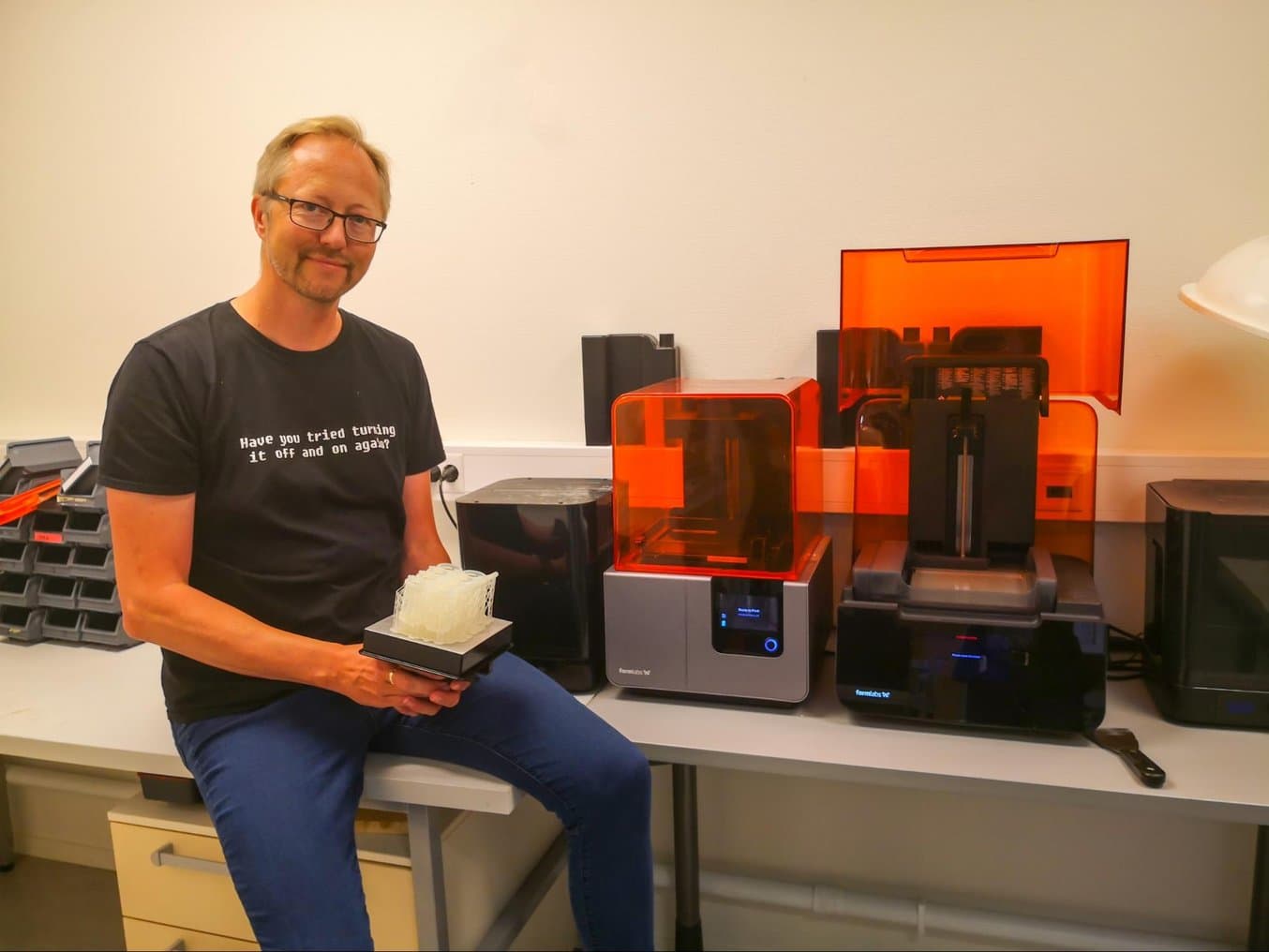
M. Røssvoll possède deux imprimantes 3D SLA dans son bureau : une Form 2 et une Form 3. Il a imprimé plus de 2600 pièces pour plus de 100 projets différents.
« Je les apprécie beaucoup parce que les erreurs sont rares et que les résultats sont fiables. Elles sont vraiment performantes. Parfois, je ne les utilise pas pendant une semaine ou deux, mais dès qu'une commande arrive, elles fonctionnent presque 24 heures sur 24, 7 jours sur 7, pendant une semaine ou deux. Il y a des intermittences, mais on les utilise beaucoup », a déclaré M. Røssvoll.
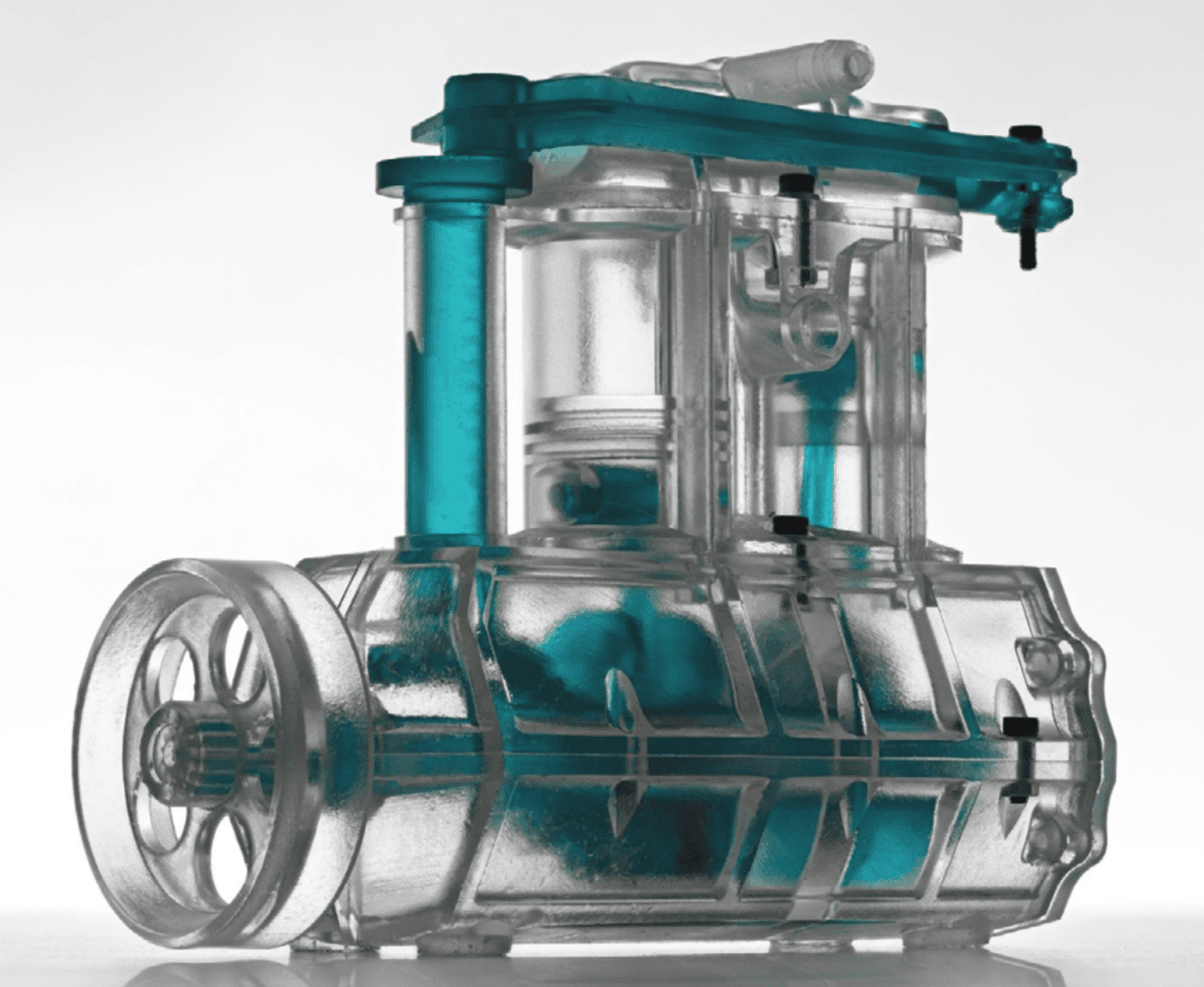
Optimisation de la conception d’assemblages imprimés en 3D
L'impression 3D SLA propose une large gamme de matériaux techniques, depuis des résines utilisables à haute température pour réaliser des moules, à celles qui supportent des contraintes et des déformations importantes ou résistent à l'usure. Téléchargez notre livre blanc pour connaître les tolérances de conception spécifiques recommandées.
Télécharger le livre blancApplications et inventions aux laboratoires de SINTEF Norlab
Les travailleurs des 13 laboratoires de SINTEF Norlab viennent trouver M. Røssvoll quand ils ont des problèmes à résoudre. Découvrez certains des outils les plus intéressants et les plus innovants qu'il a créés au fil des ans.
Machine pour assembler des bouchons et des plaques
Dans le laboratoire de SINTEF Norlab à Oslo, les analystes ont besoin pour leurs tests de bouchons en plastique renforcés d'une plaque, au milieu desquels ils insèrent une aiguille. Quand l'entreprise achète ces pièces, les bouchons et les plaques arrivent dans des sacs séparés, et les analystes doivent utiliser leurs pouces pour enfoncer les plaques dans le bouchon avant de les utiliser. Devoir assembler des milliers de bouchons manuellement est non seulement fastidieux, mais aussi douloureux pour les pouces.
Un des collègues de M. Røssvoll au laboratoire lui a demandé s'il pouvait créer quelque chose qui faciliterait ce processus. Il a commencé de concevoir un dispositif dans Fusion 360, qui au bout de quelques mois est devenu une machine d'assemblage miniature compacte mais complexe pouvant tenir sur une table. Elle se compose d'un ensemble de pièces imprimées en 3D et de roulements unidirectionnels récupérés dans le chargeur de feuilles d'une vieille imprimante à jet d'encre démantelée.
« J'ai compris qu'en utilisant les roulements unidirectionnels, je pouvais transformer le mouvement de va-et-vient de la poignée en un mouvement circulaire. Le premier roulement arrête le mouvement dans un sens, et le second dans l'autre. Les deux roues que j'ai fabriquées ne peuvent donc tourner que dans un sens », explique M. Røssvoll.
« Les plaques doivent sur les trous, mais pas passer à travers. J'ai donc ajouté des petites languettes en bas pour les retenir. Mais puisqu'elles sont flexibles, le piston les pousse à travers le trou, et elles finissent dans les bouchons. J'ai également ajouté des encoches autour de l'axe : une bille en acier s'insère dans l'encoche pour que les deux roues s'arrêtent exactement au bon endroit », a déclaré M. Røssvoll.
« Cela a demandé plus de temps et d'efforts que je ne le pensais au début, mais ils en sont très contents et l'utilisent depuis quelques mois. Ils disent qu'ils l'adorent », a déclaré M. Røssvoll.
Outil de rinçage pour le nettoyage de tubes
Certains clients du laboratoire doivent ajouter du calcaire broyé aux rivières ou aux lacs pour équilibrer l'acidité. Chaque fois qu'un nouveau type de calcaire est utilisé, ils doivent effectuer des tests pour évaluer les niveaux de pH à différentes profondeurs. Pour ce type d'analyse, M. Røssvoll a fabriqué un ensemble de cinq énormes tubes, d'environ 20 centimètres de diamètre et de deux mètres et demi de haut, qui peuvent contenir 69 litres d'eau. Les tests sont effectués en prélevant des échantillons à différentes profondeurs dans la colonne d'eau.
Lorsque les tests sont terminés, des résidus de calcaire restent collés à l'intérieur des tubes en polycarbonate, ce qui rend difficile la lecture des marqueurs. Comme les tubes sont très hauts et qu'ils sont proches du plafond, nettoyer l'intérieur des tubes avec une brosse serait assez compliqué. M. Røssvoll a donc conçu un outil pour simplifier le processus.
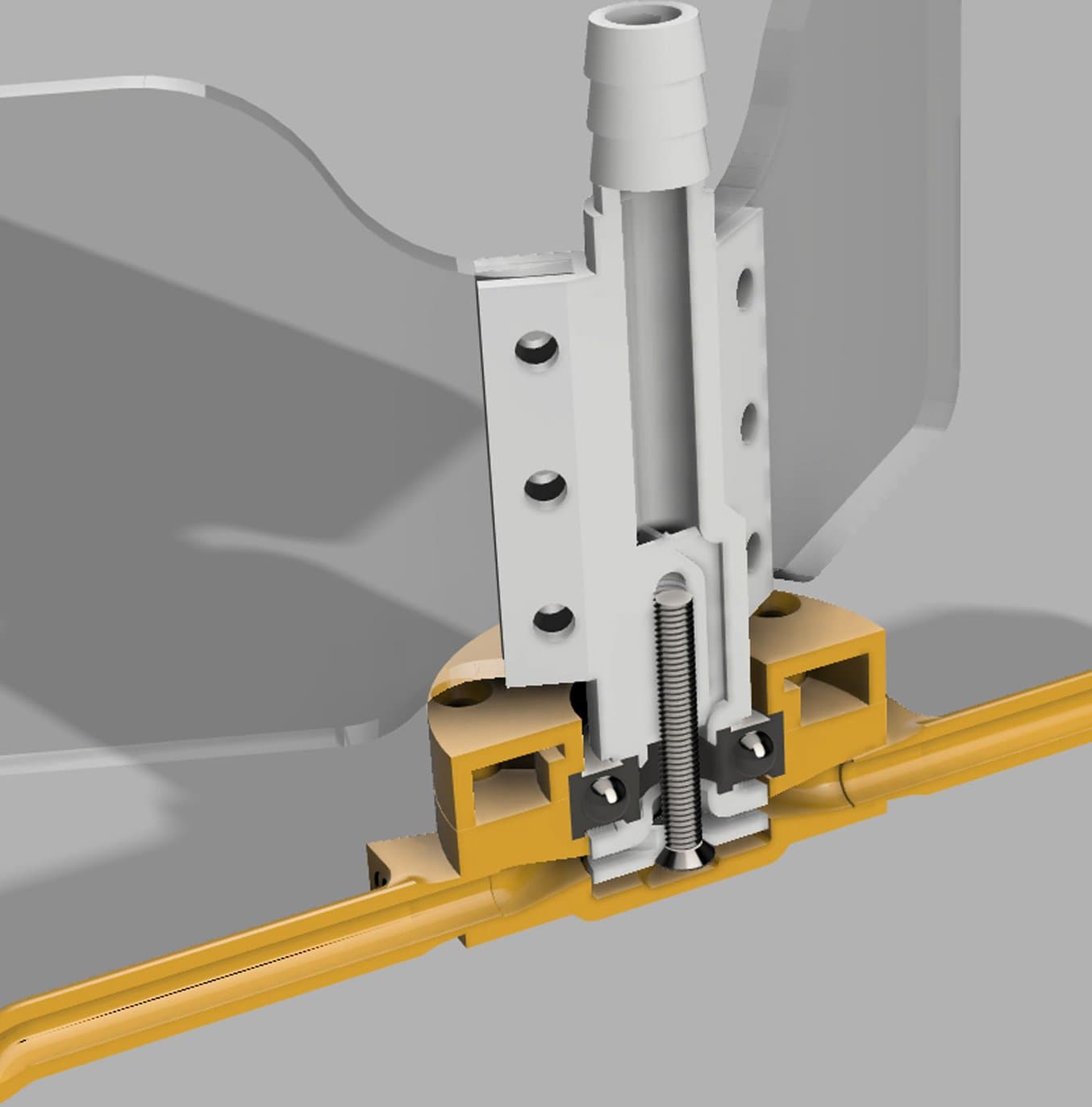

L'appareil est maintenu au centre du tube par des ailettes et projette de l'eau par ses extrémités rotatives, nettoyant ainsi l'intérieur du tube.
« Nous connectons simplement un tuyau à la sortie d'eau, et les ailettes le maintiennent au centre du tube. Lorsque l'eau commence à couler, les extrémités tournent et rincent l'intérieur du tuyau avec de l'eau propre. La partie la plus délicate a été de faire fonctionner le roulement à billes et de faire passer l'eau par le centre en même temps. Ça a demandé un peu de réflexion, mais cela prouve bien qu'on peut vraiment tout faire avec l'impression 3D. L'appareil fonctionne parfaitement », a déclaré M. Røssvoll.
Support d'ampoule à verrou tournant et de filtre à air
L'équipe de SINTEF Norlab teste souvent la qualité de l'air pour détecter d'éventuels contaminants. L'un de ces tests exige que l'air passe d'abord par un filtre, puis par une petite ampoule en verre remplie de produits chimiques qui réagissent à la présence d'hydrocarbures.
Ces produits chimiques ne peuvent pas être exposés aux rayons UV du soleil pendant le mesurage, et il doit y avoir une liaison étanche entre le filtre et l'ampoule. Les analystes utilisent normalement des tuyaux en silicone et du ruban adhésif pour attacher les pièces. Mais puisque l'échantillonnage peut prendre d'une à deux heures et que les travailleurs transportent l'appareil pendant qu'ils travaillent, les pièces se détachent souvent, rendant les tests invalides.
« Après y avoir mûrement réfléchi, j'ai imaginé un porte-ampoule à verrou tournant sur le boîtier du filtre, où des joints toriques assureraient l'étanchéité. Tout est imprimé en 3D avec Durable Resin, et le dispositif fonctionne parfaitement. J'en ai fabriqué environ 50 et nous les avons expédiés aux clients. Ils les utilisent principalement sur les plateformes de la mer du Nord pour prendre des mesures sur le lieu de travail. Ils n'ont eu aucun incident depuis qu'ils ont commencé à les utiliser », a déclaré M. Røssvoll.
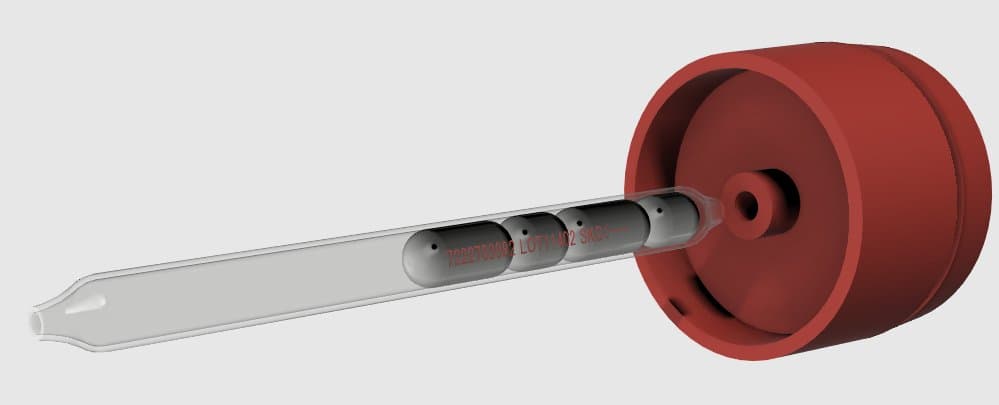
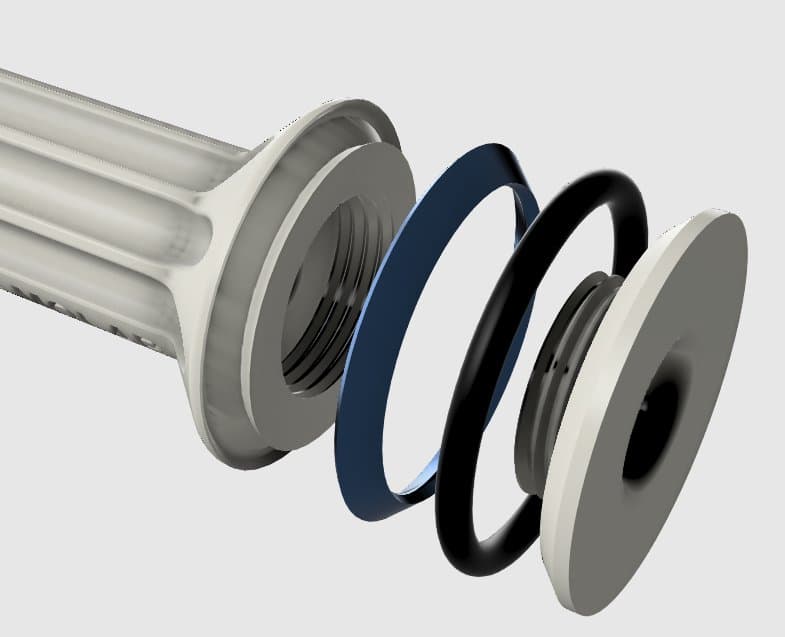
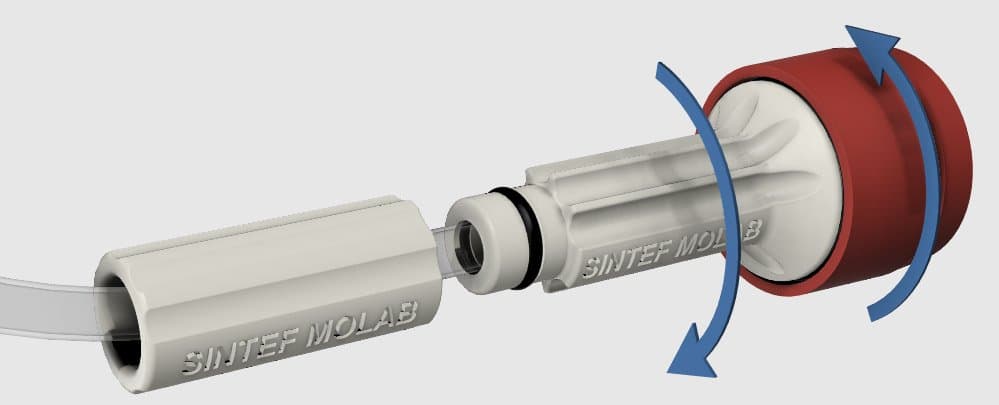
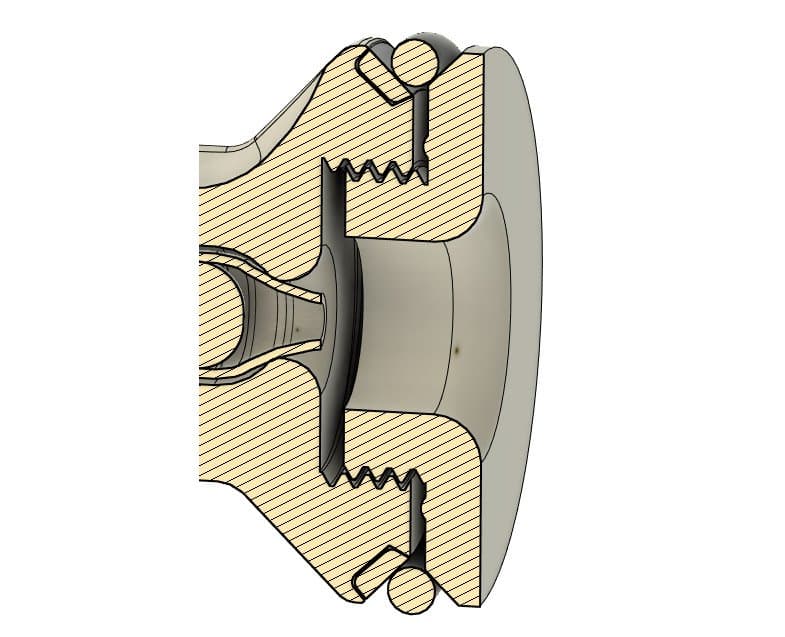
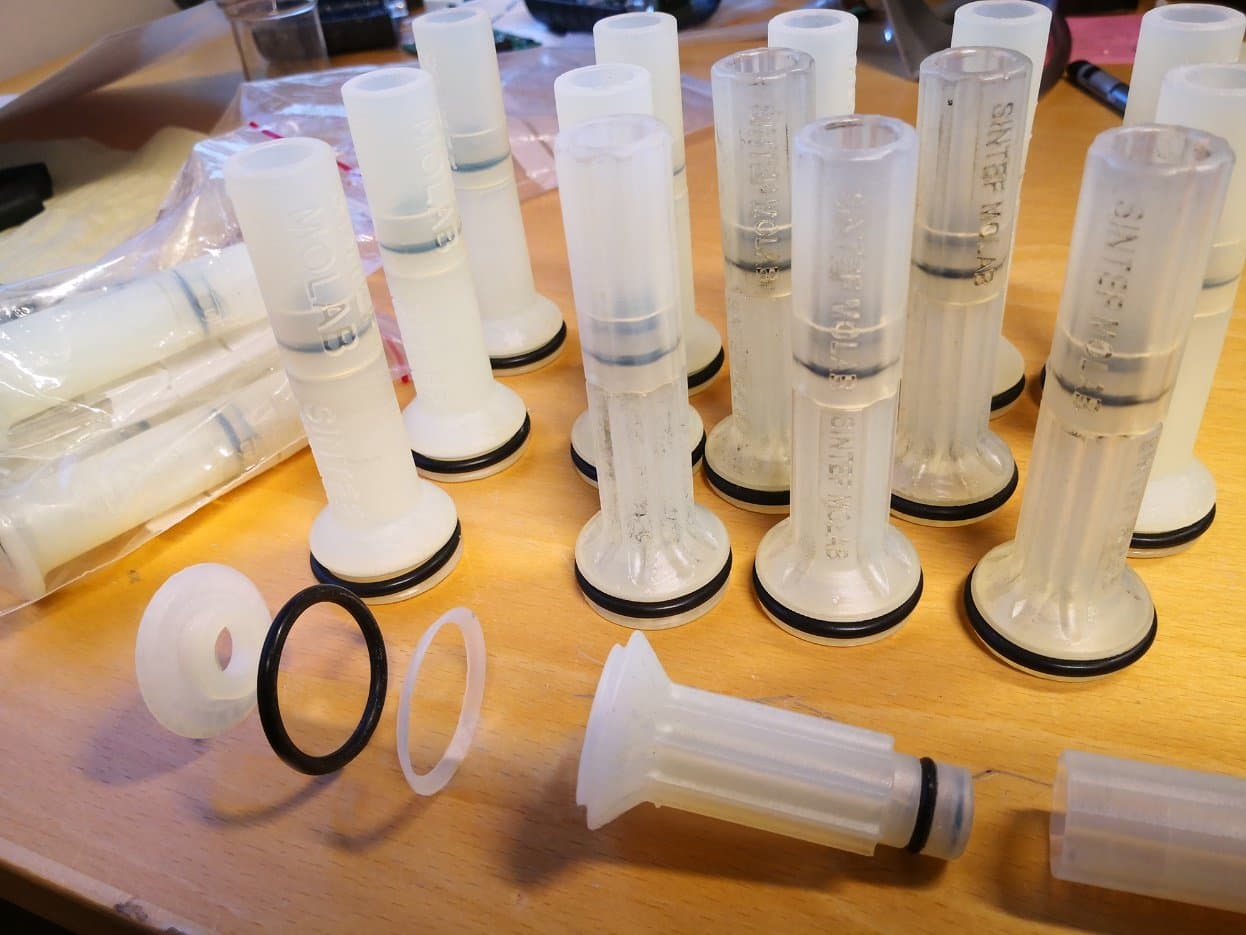
Un joint torique est placé sur le porte-ampoule, empêchant la partie inférieure de tourner lorsqu'elle est insérée dans le fond du filtre. Cela permet de fixer facilement le boîtier du filtre à l'extrémité. Lorsqu'il est serré, le joint torique se dilate et appuie sur la paroi intérieure du boîtier du filtre pour établir une liaison solide. Une fois l'échantillonnage terminé, les analystes n'ont qu'à le faire tourner dans l'autre sens pour retirer le boîtier du porte-ampoule.
+1 : imprimer en 3D les parties manquantes d'un squelette de baleine
Bien sûr, un article sur la Norvège ne serait pas complet sans une petite touche locale.
L'année dernière, M. Røssvoll a été contacté par un musée de Mo I Rana possédant un petit squelette de baleine de Minke auquel certains os manquaient.
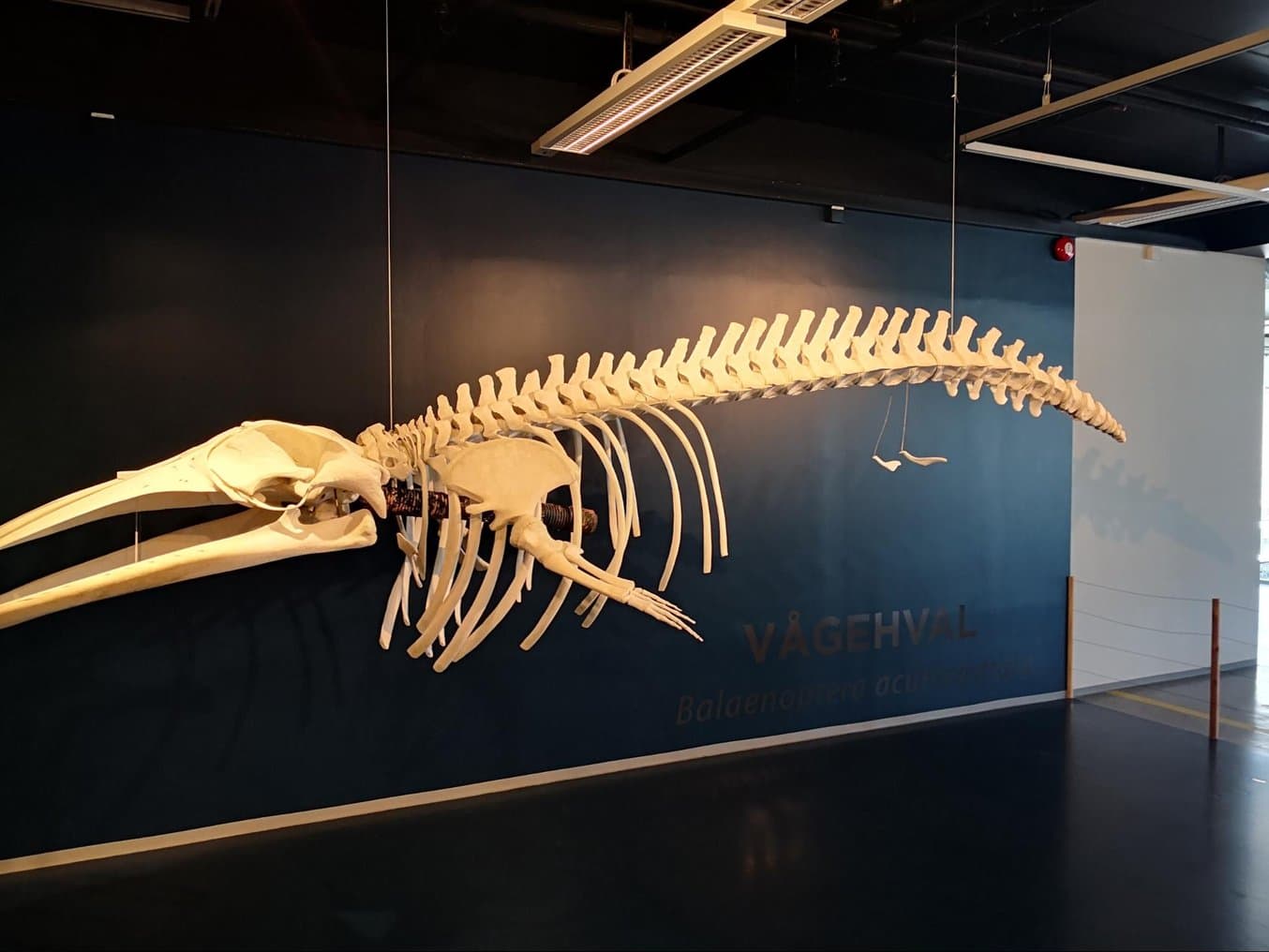
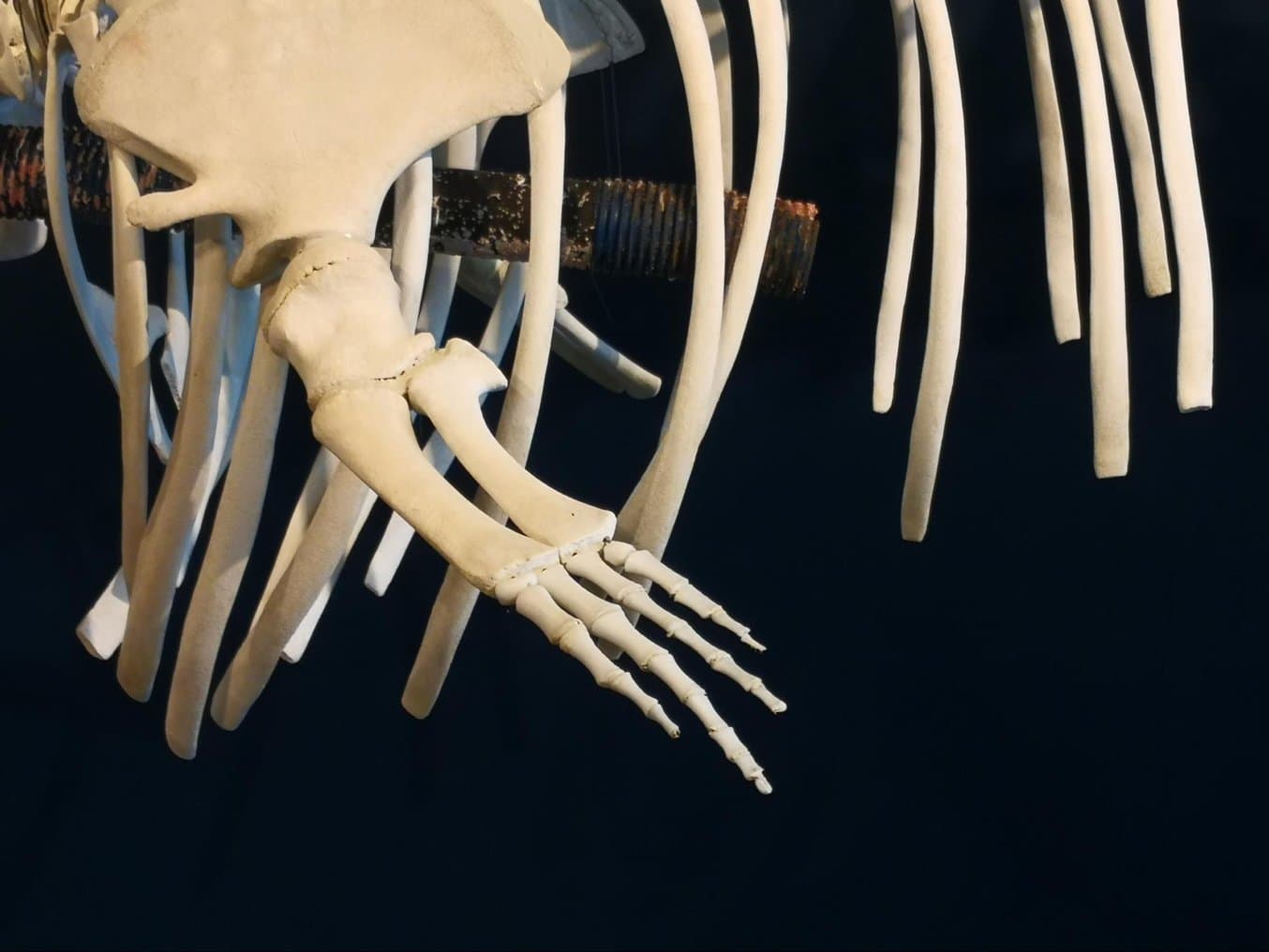
Les petits os des nageoires de ce squelette de baleine ont tous été imprimés en 3D.
Pour imprimer les parties manquantes, le musée a obtenu les scans 3D d'un autre squelette de baleine situé à Copenhague. Après avoir apporté quelques retouches aux scans 3D pour enlever les lignes de scannage, M. Røssvoll a imprimé 57 pièces, dont deux ensembles complets d'os de nageoires et deux os pelviens.
« J'ai utilisé Rigid Resin pour imprimer les os. La couleur est presque identique à celle des os de baleine, il est donc impossible de voir la différence », a déclaré M. Røssvoll.