Réduction des coûts et personnalisation : le passage stratégique de Labconco à l'impression 3D
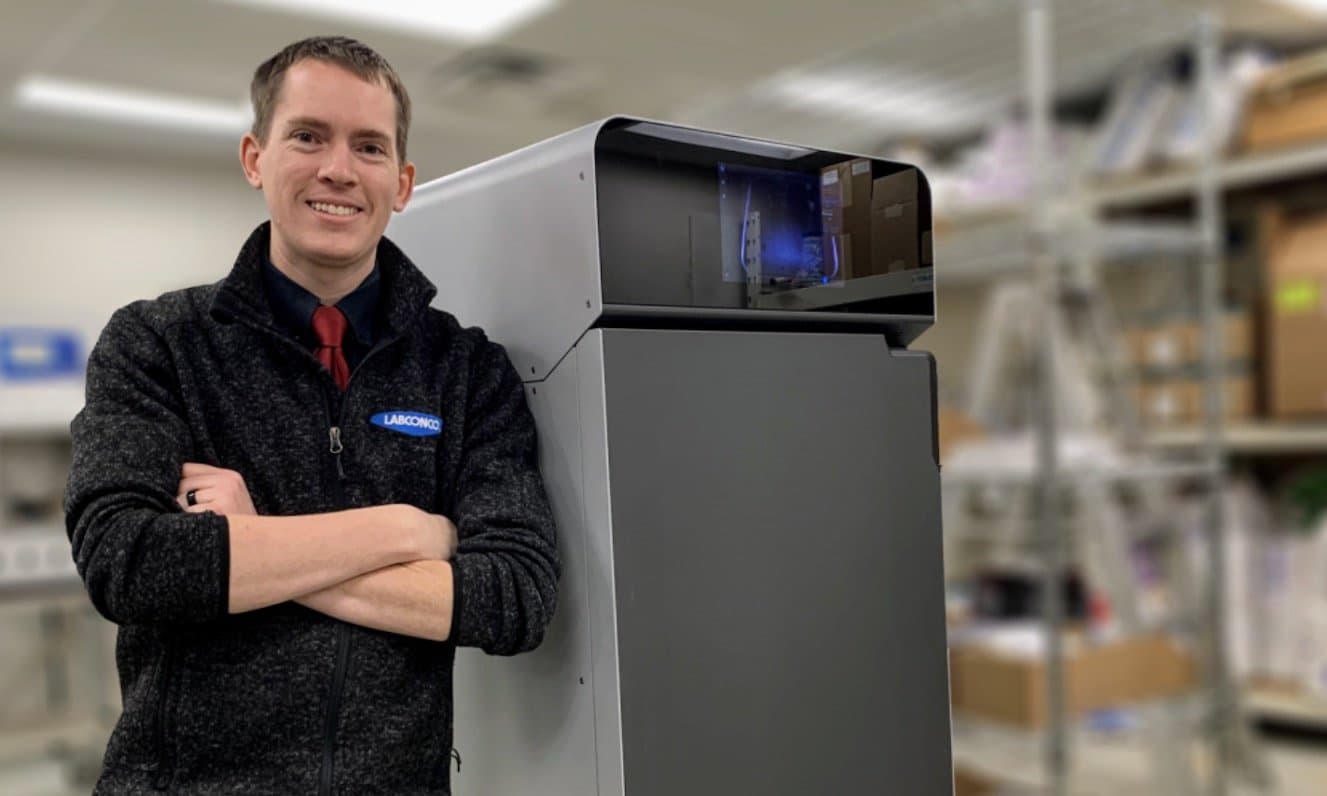
Lors de sa première réunion à Labconco début 2020, Brent Griffith a fait taire la salle quand il a proposé d'avoir recours à l'impression 3D. La réunion avait notamment pour objet la fabrication d'un petit composant pour le Logic Vue, un nouveau produit de Labconco, qui devait être moulé par injection. Comme le produit était nouveau et que les quantités à fournir n'étaient pas encore fixées, il se pouvait très bien que cet outil de moulage coûtant plus de 15 000 € ne produise que 100 pièces la première année. Le coût par pièce élevé qui en résultait a incité le groupe à rechercher de nouvelles solutions. « J'ai pris la parole et j'ai dit : "Je pourrais imprimer cela en 3D et avoir dès demain le nombre de pièces que nous prévoyons de fabriquer en un an." Tout le monde s'est tu » affirme Brent Griffith, ingénieur produits chez Labconco.
À l'époque, Labconco ne disposait pas d'imprimantes 3D en interne. Lorsque M. Griffith est revenu le lendemain avec plusieurs versions du composant qu'il avait imprimées chez lui avec ses propres imprimantes, la rentabilité de l'impression 3D s'est imposée d'elle-même.
Aujourd'hui, M. Griffith supervise un laboratoire en pleine expansion qui compte trois imprimantes à frittage sélectif par laser (SLS) Fuse 1+ 30W, la Fuse Sift et la Fuse Blast, une imprimante stéréolithographique (SLA) Form 3L et plusieurs imprimantes à dépôt de fil fondu (FDM). Labconco fabrique des équipements de laboratoire pour toute une série de secteurs, des tests alimentaires au développement pharmaceutique, en passant par les diagnostics en oncologie et la médecine légale. M. Griffith imprime désormais chaque semaine des centaines de pièces au lieu de les mouler ou de les usiner. Elles servent de remplacement lorsque des problèmes de chaîne d'approvisionnement affectent la production, et aident à développer les nouveaux produits de Labconco.
Arguments à l'appui
Une fois que M. Griffith a démontré les avantages de cette première pièce imprimée en 3D, il a commencé à imprimer d'autres pièces pour aider les ingénieurs du bureau dans leur travail de développement, et les demandes ont tôt fait de se multiplier. « La nouvelle s'est répandue comme une traînée de poudre », explique M. Griffith.
Pour découvrir les autres possibilités offertes par l'impression 3D, son collègue ingénieur Austin Orme et lui se sont mis à auditer les milliers de pièces, d'outils et de composants entrant dans la fabrication des produits Labconco. « Nos instructions spécifiques étaient de trouver une machine offrant un excellent volume d'impression et produisant des pièces de très haute qualité que nous pourrions utiliser à la fois pour les prototypes et la production », explique M. Griffith. « Nous avons rapidement constaté qu'une seule machine ne suffirait pas pour accomplir un tel travail, car elle ne nous offrirait pas les capacités et la flexibilité dont nous avions besoin pour réussir. » Le laboratoire a fini par ajouter six imprimantes pour commencer, dont trois imprimantes SLS Fuse 1+ 30W et une imprimante SLA grand format Form 3L.
« Nous avons acheté la Form 3L parce que nous voulions avoir accès à la gamme de résines de Formlabs. Je savais que cela nous donnerait de la flexibilité et nous ouvrirait de nouvelles perspectives. Et c'est exactement ce qui s'est produit. »
Brent Griffith, ingénieur produits
Grâce à la gamme de matériaux compatibles avec la Form 3L et aux volumes moyens ou élevés fabriqués par les trois imprimantes de la série Fuse, M. Griffith a pu améliorer les produits existants, économiser des dizaines de milliers de dollars sur les coûts d'outillage, accélérer le développement de projets existants et remplacer des pièces à la demande.
Remplacer, améliorer, augmenter : les applications de l'impression 3D chez Labconco
Capteur de remplissage SLS : remplacement d'un assemblage moulé par injection
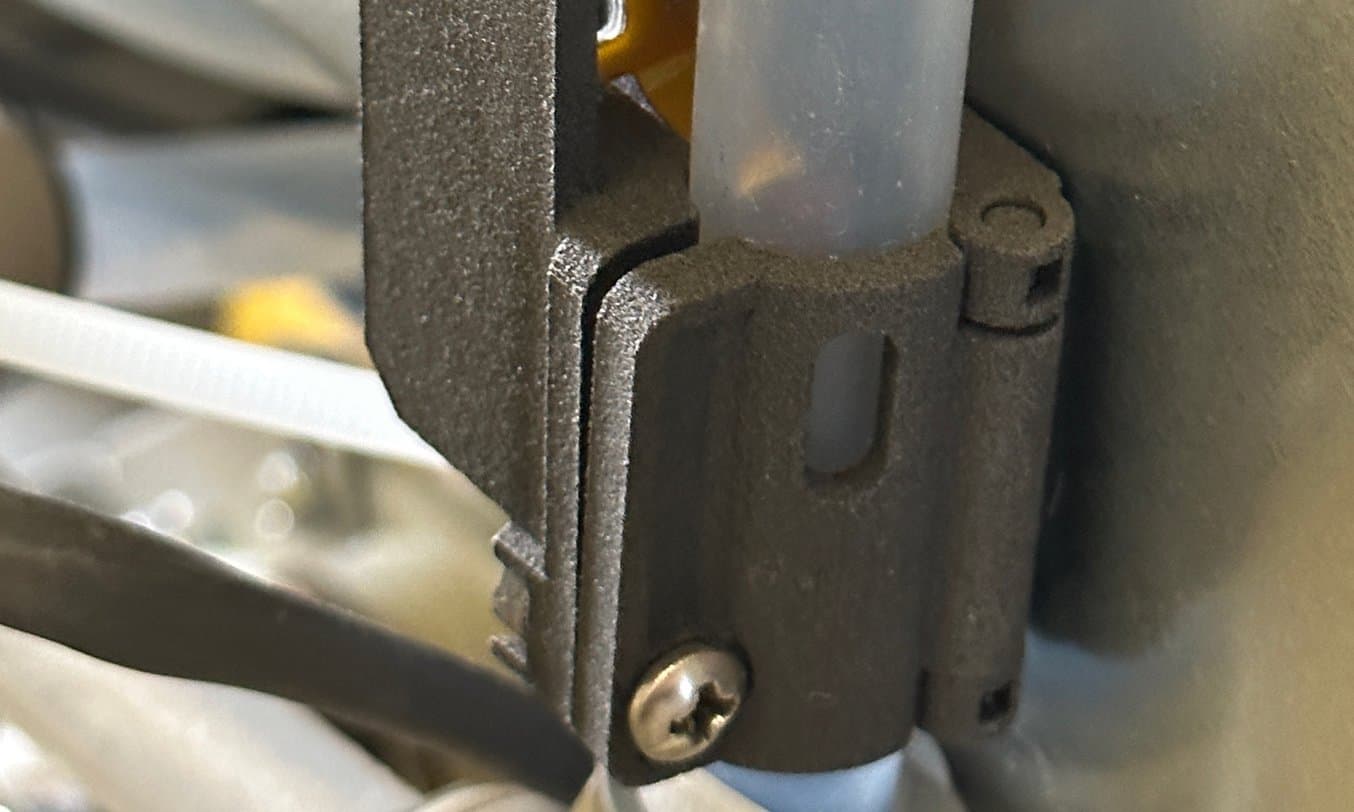
Ce composant du capteur de remplissage est doté d'une charnière fonctionnelle que Tim Grove, ingénieur produits chez Labconco, a conçue après avoir vu l'échantillon standard en Nylon 12 Powder. Cette fonction permet d'imprimer la pièce en une fois au lieu de créer un assemblage en plusieurs parties, ce qui réduit le temps de travail et le coût des matériaux.
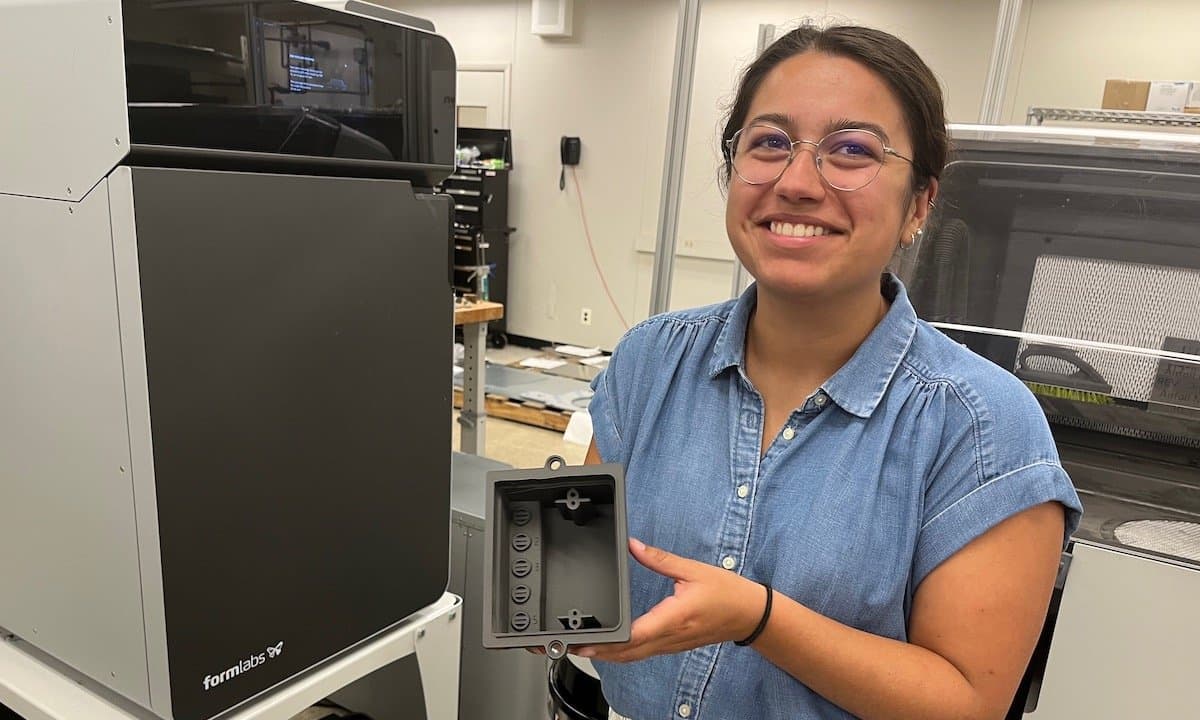
Comme l'équipe de développement de produits de Labconco a réussi à faire évoluer efficacement son installation d'impression 3D, de nombreux membres de l'équipe ont désormais accès à des technologies industrielles telles que les imprimantes SLS de la série Fuse. Selon M. Griffith, de nombreux départements de Labconco commencent à réfléchir à la manière d'intégrer l'impression 3D dans leurs processus de travail habituels afin de réduire les coûts, de gagner en flexibilité et de protéger leur chaîne d'approvisionnement.
La ligne de produits Glassware Washer de Labconco intègre des avancées techniques de pointe, notamment des composants imprimés en 3D. L'un des composants, un support de capteur de remplissage, sert à éviter les débordements. Dans une approche conventionnelle, ce composant aurait été moulé par injection en deux pièces séparées, et une goupille aurait maintenu les deux pièces ensemble.
Cependant, Tim Grove, ingénieur produits chez Labconco, a compris le potentiel qu'offrait l'impression 3D SLS pour réduire les coûts et les délais. Inspiré par la conception de la charnière présente dans l'échantillon standard de Nylon 12 Powder de Formlabs, M. Grove a réimaginé le support du capteur de remplissage pour optimiser l'assemblage et éviter les dépenses qu'aurait entraînées la commande de plusieurs outils.
Dans le cadre d'une collaboration itérative avec M. Griffith, M. Grove a travaillé sur plusieurs versions de la pièce pour garantir une fonctionnalité sans faille et des performances à toute épreuve.
« Elle sort de l'imprimante avec la charnière immédiatement prête à l'emploi. Ce procédé permet donc de réaliser des économies et d'assouplir la production. Nylon 12 Powder est un bon polymère qui nous convient parfaitement. Nous lui trouvons de nombreuses applications et obtenons des résultats époustouflants », explique M. Griffith.
Capteur de remplissage SLS | Nombre de composants | Temps de travail pour l'assemblage (50 composants) | Coût par pièce finie (avec main d'œuvre) | |
---|---|---|---|---|
Moulé par injection | 3 | 1 heure | 4,45 €/pièce + outillage | |
Imprimé en 3D par SLS | 1 | 0 | 2,56 €/pièce |
Roue de soufflerie SLA : la solution quand un fabricant arrête la production d'une pièce
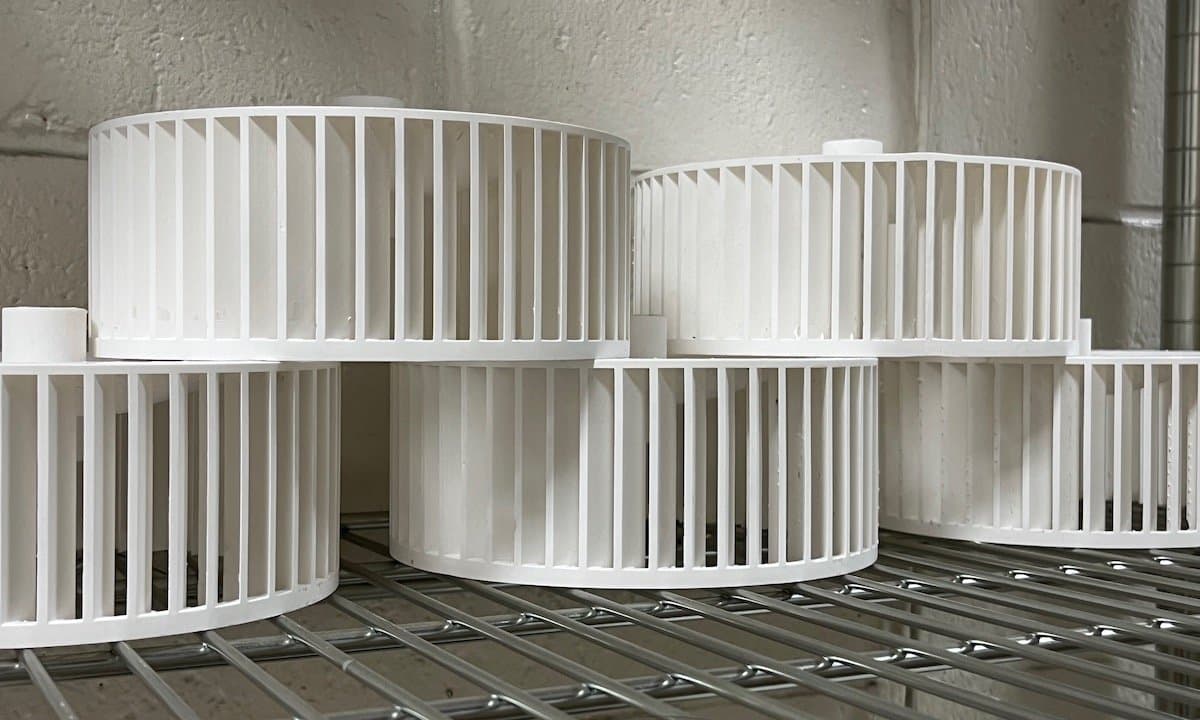
Ce composant utilisé sur le produit d'analyse des grains Kjeldahl de Labconco était auparavant commandé auprès d'un fournisseur externe, jusqu'à ce qu'il arrête de le produire. M. Griffith a procédé à une rétroconception du composant, puis a imprimé la nouvelle version en Rigid 10K Resin sur la Form 3L tous les jours pendant plus d'un mois, ce qui a permis de constituer un stock de composants de remplacement et de se prémunir contre les problèmes de chaîne d'approvisionnement.
Dans le cas de l'appareil d'analyse de grains Kjeldahl de Labconco, l'équipe travaillait avec un sous-traitant externe qui fabriquait un composant essentiel de la roue de soufflerie. Les quantités étaient faibles, et le fournisseur a décidé d'arrêter de fabriquer cette pièce lorsque l'outillage a atteint la fin de sa durée de vie.
Labconco a dû à la fois rechercher un nouveau fournisseur, attendre la conception et la production d'un nouvel outil moulé par injection, et faire face au coût élevé des matériaux et de la main-d'œuvre. « Nous avons essayé une douzaine de solutions différentes, mais aucune n'était en mesure de répondre à nos spécifications, notamment en ce qui concerne la compatibilité chimique. J'ai d'abord pris une copie et fait une rétro-ingénierie du composant, puis je l'ai optimisé et imprimé en Rigid 10K Resin », explique M. Griffith. « Après avoir testé sa résistance, nous avons décidé qu'il s'agissait de la meilleure solution. »
Leur imprimante SLA grand format, la Form 3L, est arrivée à point nommé. Ils ont imprimé cette roue de soufflerie rétroconçue pendant 40 jours d'affilée pour reconstituer leur stock de pièces.
« Nous avons utilisé Rigid 10K Resin pour plusieurs composants. La compatibilité chimique correspondait à ce dont nous avions besoin pour les acides, en particulier pour l'acide sulfurique vaporisé. Le passage à la fabrication additive nous permet d'économiser des centaines d'heures, que nous passions auparavant à passer en revue les fournisseurs et les matériaux. Si cela ne suffit pas à vous prouver l'utilité de cette technologie, je ne sais pas ce qu'il vous faut », déclare M. Griffith.
Roue de soufflerie SLA | Coût |
---|---|
Original moulé | 178,77 € |
Optimisée et imprimée en Rigid 10K Resin | 52,65 € |
Séparateur de roulement SLS : de 500 € à 20 € par pièce
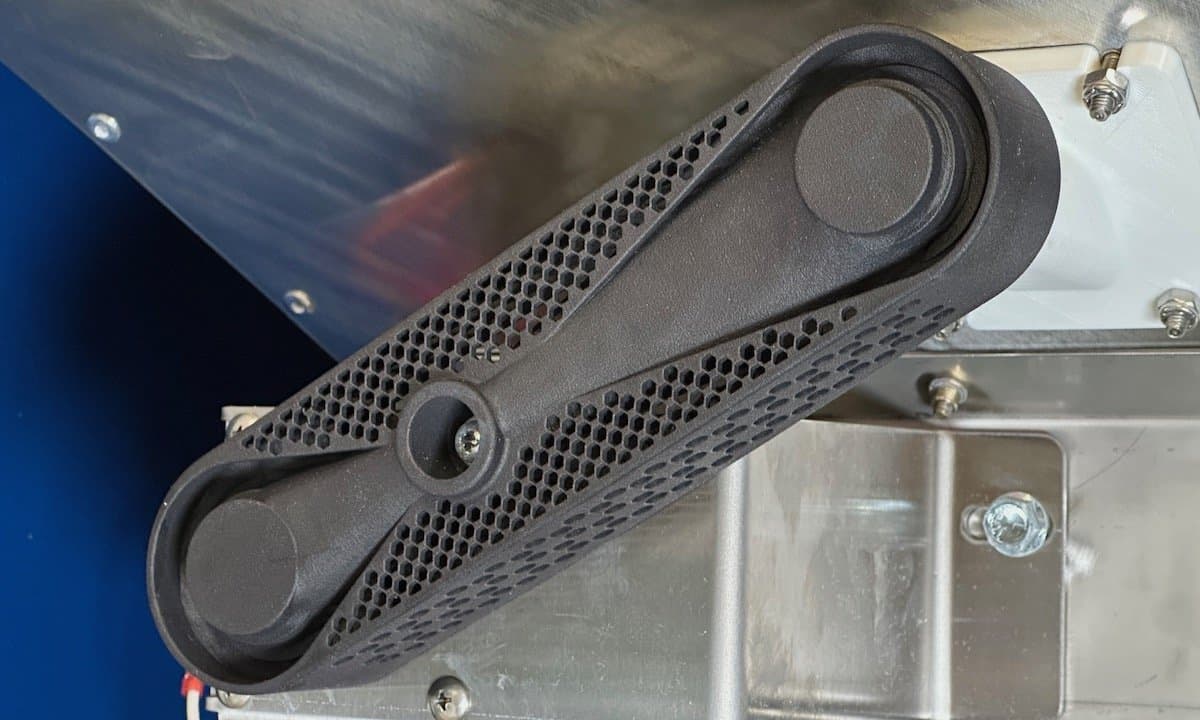
M. Griffith aurait très bien pu imprimer cette pièce en réalisant une copie exacte du composant qu'un sous-traitant avait usiné pour 500 €. Il a préféré mettre en pratique ce qu'il avait appris dans le cadre du programme de fabrication et de conception additives à l'Université d'État de Pennsylvanie, et a reconçu la pièce pour tirer parti des possibilités géométriques offertes par l'impression 3D SLS. Le nouveau composant coûte environ 21 € à Labconco, ce qui lui permet d'économiser des centaines d'euros et de réduire le délai d'exécution à moins de deux jours.
Si certains composants sont relativement simples à réaliser, les méthodes traditionnelles de fabrication servant à les produire peuvent s'avérer coûteuses. Un sous-traitant proposait d'usiner cette pièce – un séparateur empêchant les roulements d'entrer en contact – pour environ 500 € l'unité. Cette pièce était destinée à un nouveau produit, et Labconco avait déjà prouvé l'utilité de son laboratoire d'impression 3D. M. Griffith a immédiatement commencé à imprimer le séparateur sur la Fuse 1+ 30W et a baissé le prix à environ 45 €, soit un dixième de ce qu'exigerait un sous-traitant.
Mais ce n'est pas tout. M. Griffith a mis en pratique ce qu'il avait appris dans le cadre du programme de fabrication et de conception additives à l'Université d'État de Pennsylvanie, et est passé d'un simple remplacement de pièce à une optimisation complète.
« C'est exactement ce que j'avais appris : comment appliquer les aspects opportunistes et restrictifs de la fabrication additive. La question n'est pas de savoir si nous pouvons imprimer une pièce en 3D, mais si nous le devons. Dans ce cas précis, nous aurions pu simplement copier et remplacer la pièce, mais nous aurions alors manqué une magnifique occasion d'exploiter les possibilités de la fabrication additive. Comme nous disposions des imprimantes de la série Fuse qui offrent très peu de contraintes géométriques, j'ai pu laisser libre cours à mon imagination et essayer de nouvelles choses. »
Brent Griffith, ingénieur produits
Il a eu recours à la conception générative pour réduire les besoins en matériaux de l'ensemble de la pièce, tout en préservant les fonctions de sécurité du séparateur de roulements. En l'espace d'une journée, il disposait d'une conception optimisée, et Labconco a commencé à imprimer en 3D les pièces SLS en interne pour environ 20 € l'unité.
« L'impression 3D nous offre d'énormes avantages en termes de géométrie. En créant une version allégée d'une pièce ou en utilisant différentes techniques de conception, il est possible de combiner des composants de manière inédite. Nous pouvons tout produire en interne et économiser beaucoup d'argent », explique M. Griffith.
Séparateur de roulements SLS | Coût (y compris celui de la main-d'œuvre) | Délai de production |
---|---|---|
Usinage | 485,82 € | 2 – 3 semaines |
Remplacement SLS 1:1 | 43,50 € | 29 heures |
Optimisé pour le SLS | 21,08 € | 28 heures |
Des pièces SLS à l'essai : moins de composants pour une meilleure fonctionnalité
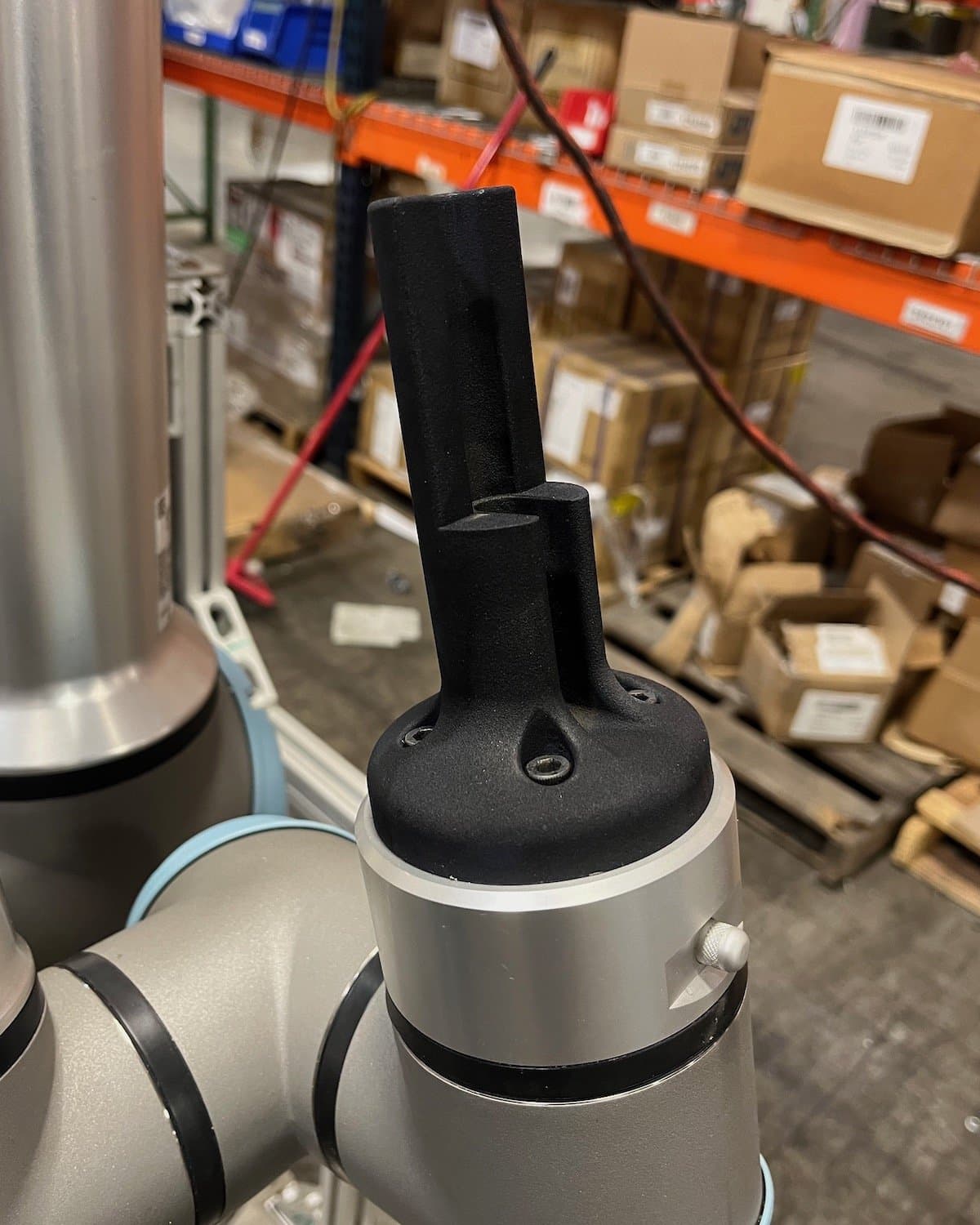
Pour aider Labconco à passer facilement à un flux de travail hybride combinant des tâches manuelles et des actionneurs robotiques, M. Griffith et son équipe ont conçu des outils et des effecteurs personnalisés, puis les ont imprimés avec Nylon 12 Powder grâce à leur parc d'imprimantes de la série Fuse.
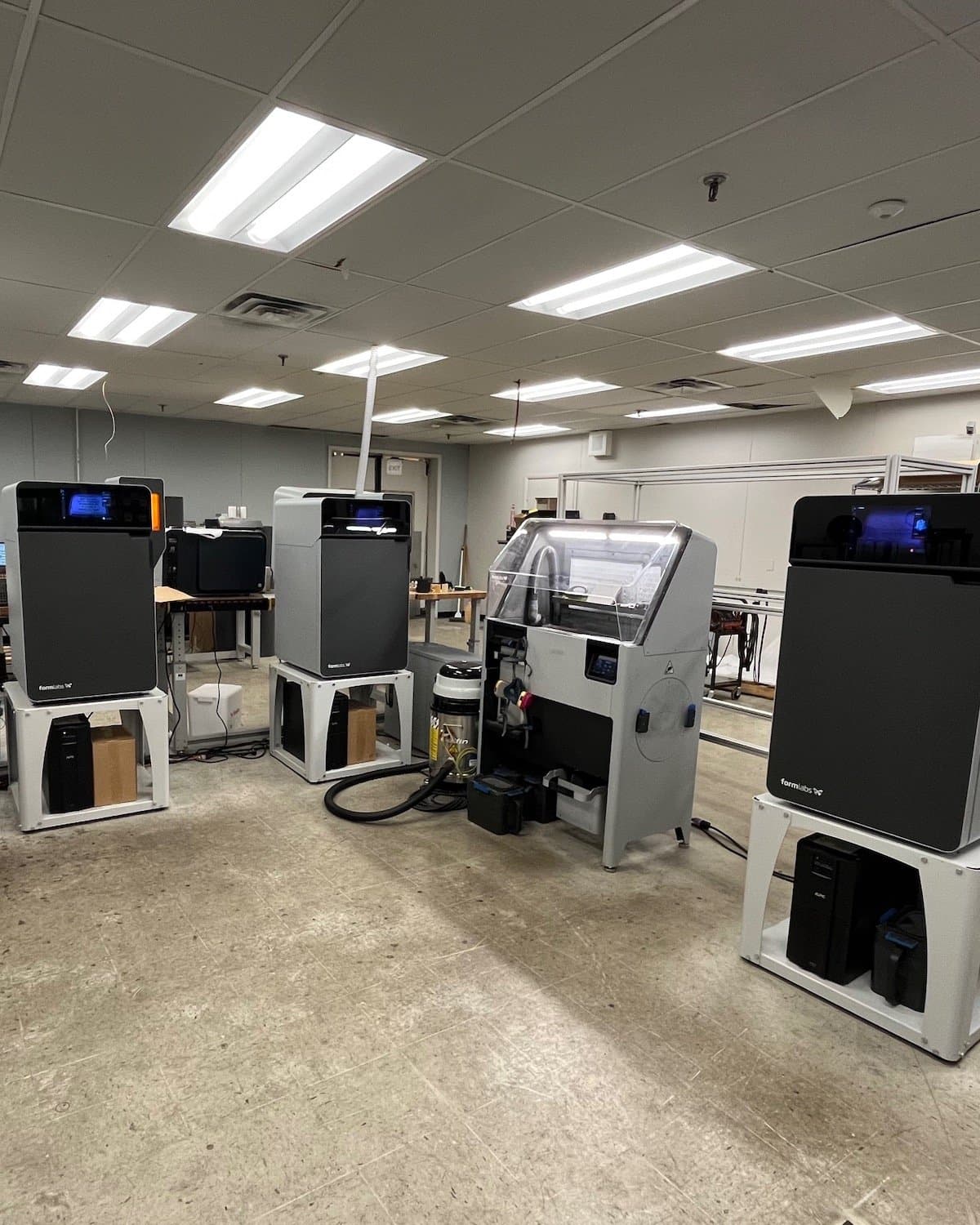
La taille compacte et la faible consommation énergétique des imprimantes 3D SLS de la série Fuse ont permis à M. Griffith et à son équipe de faire évoluer leurs opérations SLS à mesure qu'ils étendaient leur gamme d'applications pour des pièces SLS robustes et durables.
La recherche d'excellence de Labconco s'étend aux tests des composants critiques utilisés dans l'un de ses produits phares, les armoires de sécurité biologique. Ces armoires jouent un rôle essentiel dans la protection du personnel et des produits qu'ils traitent, et sont basées sur des modèles de flux d'air et des filtres HEPA spécifiques. Afin de garantir le plus haut niveau de performance, ces filtres sont soumis à des tests et à des processus de certification très stricts avant d'être déclarés prêts à l'emploi.
Auparavant, ce processus de test dépendait fortement des opérateurs humains, ce qui impliquait une variabilité et des limitations potentielles. Mais Labconco a adopté une approche innovante exploitant la puissance des systèmes robotiques pour automatiser le scan de chaque filtre avec une précision incroyable. Ce passage à l'automatisation a nécessité le développement d'outils et d'effecteurs personnalisés pour les bras robotisés chargés d'effectuer les tests. Avec les méthodes de fabrication traditionnelles, ce projet aurait été extrêmement coûteux et aurait pris des mois. Compte tenu du faible nombre de pièces nécessaires, l'impression 3D de ces pièces sur les imprimantes de la série Fuse a constitué une étape importante dans cette approche innovante.
Grâce aux pièces SLS produites en interne sur la Fuse 1+ 30W, Labconco a obtenu des composants d'une résistance remarquable et a augmenté la précision et la fiabilité de ses tests de sécurité. Cette adoption de l'impression 3D a non seulement rendu les opérations plus efficaces, mais a également permis à Labconco de garantir une sécurité et une performance optimales pour ses produits.
Composants de l'effecteur | Coût |
---|---|
Usinage | 508,32 € |
Imprimé en 3D par SLS | 73,44 € |
Composant de hotte : produire des volumes moyen par SLS pour plus d'agilité
Labconco a été la première entreprise à commercialiser la production de hottes, et c'est aujourd'hui l'une de ses classes de produits les plus importantes. Les hottes sont indispensables dans les installations chimiques, pharmaceutiques ou agricoles à grande échelle.
L'un des composants – une butée mécanique qui empêche les utilisateurs d'ouvrir la guillotine de la hotte au-delà d'un certain point (ce qui permet d'économiser de l'énergie) – était auparavant moulé par injection. La commande de volumes importants fabriqués avec un seul outil limitait la capacité de Labconco à apporter des modifications ou à personnaliser les commandes pour les gros clients. Les outils s'usent, et les fournisseurs peuvent rencontrer des difficultés pour les remplacer. Pour résoudre les problèmes liés à la chaîne d'approvisionnement, ils ont commencé à imprimer ces butées sur la Fuse 1+ 30W. Aujourd'hui, M. Griffith produit entre 50 et 100 de ces composants chaque semaine avec Nylon 12 Powder.
« Si vous moulez cette pièce par injection, vous ne pouvez pas la modifier facilement. C'est heureusement assez rare, mais nous avons déjà eu par le passé des composants pour lesquels le choix du moulage par injection nous a coûté cher, parce que lorsque nous les avons reçus et utilisés, ils se sont cassés ou n'ont pas fonctionné comme prévu. Les ingénieurs sont désormais conscients que l'impression 3D de certaines pièces rend la rétro-ingénierie beaucoup moins fastidieuse et offre davantage d'options d'adaptation. Il n'est pas toujours possible d'attribuer une valeur monétaire à cela, et la fabrication additive présente d'autres avantages importants qui, à mon avis, sont souvent oubliés », déclare M. Griffith.
Un autre avantage de l'intégration de la technologie d'impression 3D en interne est la confiance qu'elle inspire aux jeunes employés qui commencent leur carrière. N'étant pas soumis à la pression de devoir commander un outil parfait, ils sont plus enclins à essayer d'autres choses ou à proposer de nouvelles idées. « Les jeunes ingénieurs n'ont pas les 20 ans d'expérience qui leur permettraient de regarder une pièce et de dire si elle va fonctionner ou pas. La possibilité d'imprimer en 3D et d'essayer des tas de choses sans craindre d'éventuelles erreurs les rend plus confiants », explique M. Griffith. « Nous voulons leur permettre de se concentrer sur la recherche de la meilleure solution à un problème donné, et l'impression 3D contribue à cela. »
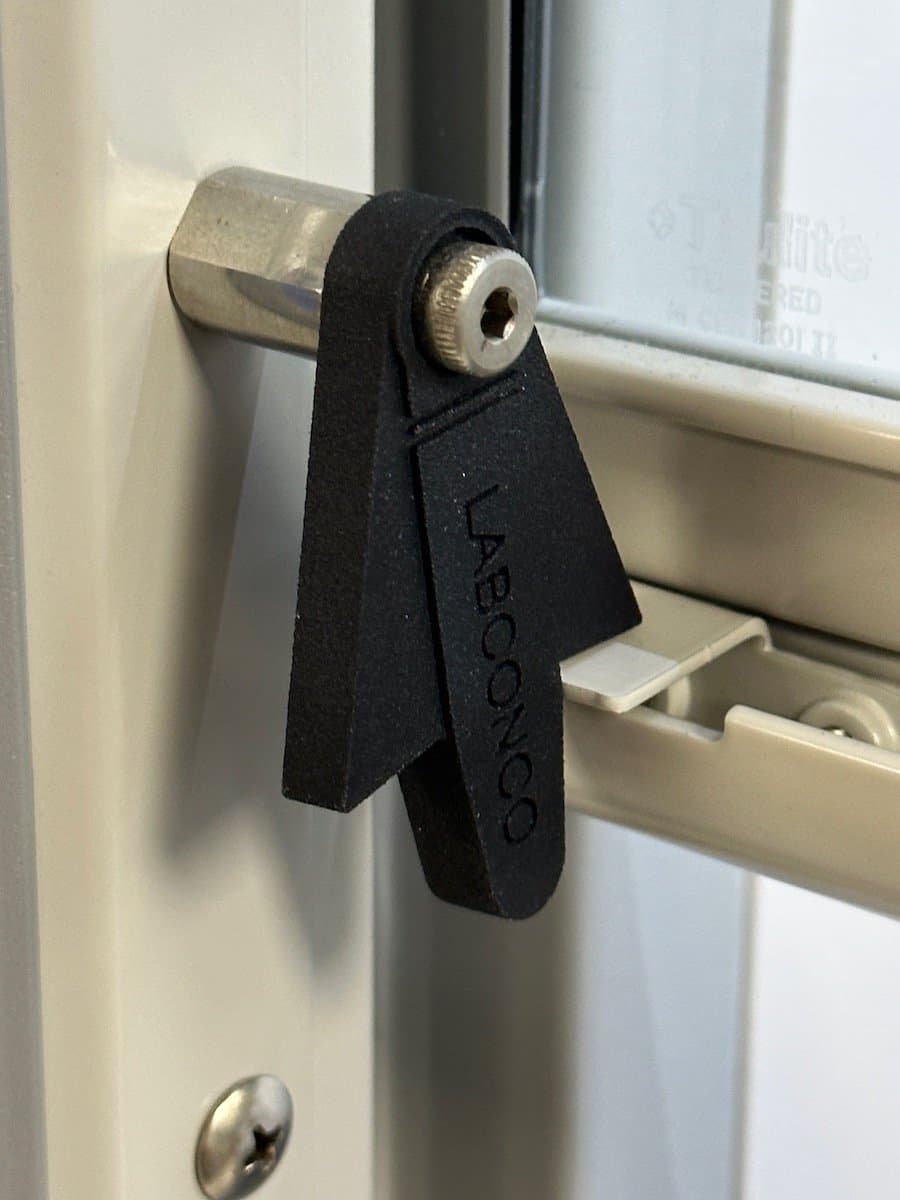
M. Griffith produit chaque semaine entre 50 et 100 de ces pièces en Nylon 12 Powder sur la Fuse 1+ 30W, ce qui lui permet d'éviter les coûts et les risques liés à l'utilisation d'un seul outillage.
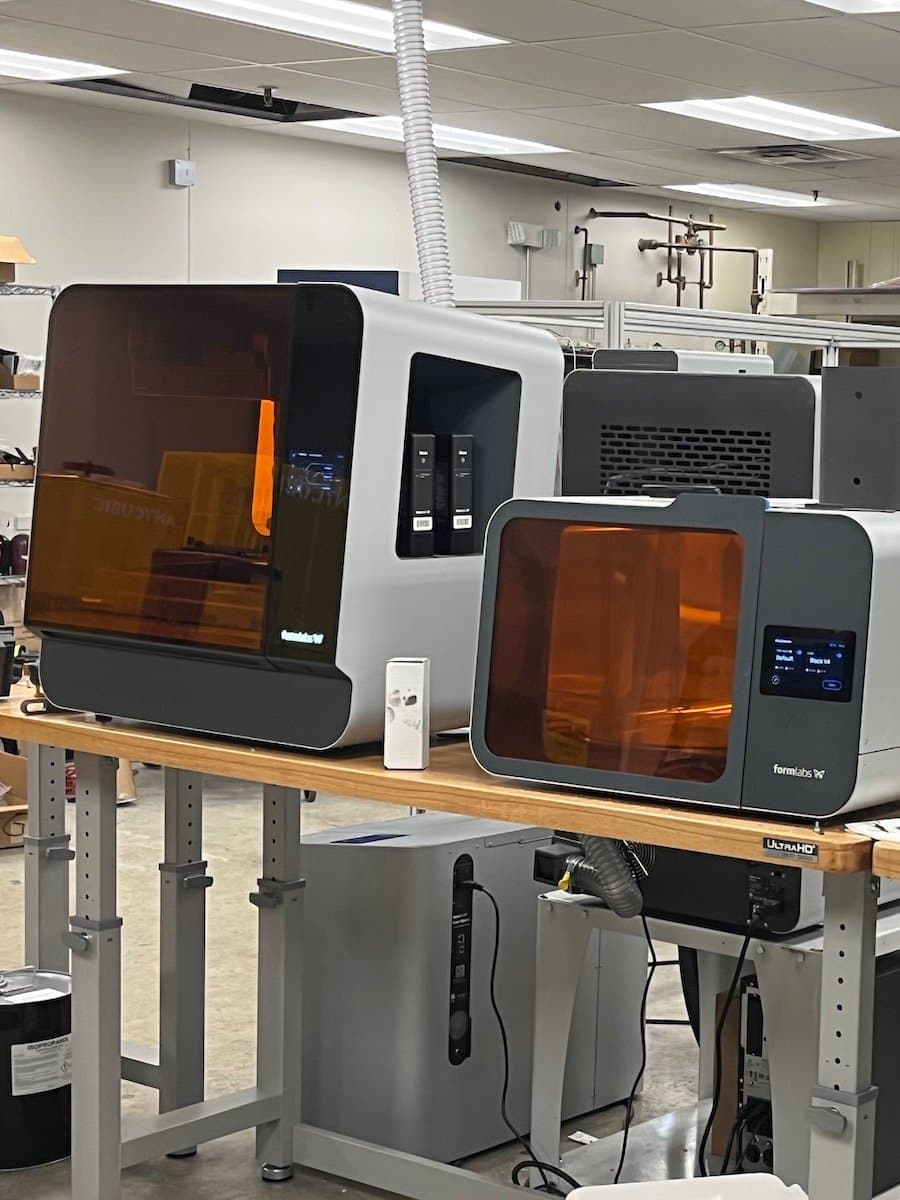
La facilité d'utilisation des imprimantes SLS et SLA (comme la Form 3L et la Form Cure L présentées ici) permet aux jeunes employés qui commencent leur carrière de se familiariser avec les nouvelles technologies et de proposer de nouvelles idées.
La Fuse Blast de Labconco vient compléter leur écosystème SLS
Avec des volumes de production atteignant plus d'une centaine de pièces SLS par semaine, les étapes manuelles de post-traitement telles que le sablage et le nettoyage nécessitaient jusqu'ici des heures entières de travail manuel qui auraiet pu être mises à profit pour des tâches de conception et d'ingénierie plus importantes. « L'entreprise souhaite que nous nous concentrions sur la recherche de nouvelles opportunités, la rétro-ingénierie des composants et la réduction des coûts, plutôt que de rester au bureau à nettoyer manuellement toutes ces pièces », explique Brent Griffith.
Ayant déjà acheté un système de sablage automatisé très coûteux, Labconco a ajouté la Fuse Blast pour compléter son écosystème Fuse SLS. Après une installation de dix minutes, M. Griffith a pu automatiser le nettoyage et le sablage de deux chambres de fabrication complètes de la série Fuse. « L'installation a été un jeu d'enfant... la Fuse Blast est presque de la même taille que notre système de sablage manuel. Si vous disposez d'un espace pour un système de sablage manuel, ce qui est le cas de toutes les entreprises qui utilisent le SLS, vous pourrez sans problème utiliser la Fuse Blast », explique M. Griffith.
Des pièces de meilleure qualité et plus performantes
Dès le début, les équipes de Labconco ont remarqué une différence dans le lissage de la surface et la qualité des pièces.
« La Fuse Blast a immédiatement fait une énorme différence, et les ingénieurs ayant reçu des pièces pour le prototypage ont tout de suite remarqué que les pièces avaient changé, sans même que je leur dise que nous avions automatisé le post-traitement. Ils ont immédiatement remarqué qu'il y avait moins de résidus de poudre sur les pièces, qu'elles étaient plus lisses, plus agréables au toucher et plus belles. Cela fait une grosse différence dans la qualité des pièces. »
Brent Griffith, ingénieur produits chez Labconco
Les surfaces lisses et l'absence de résidus de poudre ont eu un effet inattendu sur les performances des pièces : les machines fonctionnent mieux lorsque leurs composants imprimés par SLS ont été nettoyés dans la Fuse Blast. « Nous avons en fait obtenu des performances légèrement supérieures sur certains des composants que nous fabriquions parce qu'ils étaient beaucoup plus propres, en particulier lors des premiers cycles de mise en service pour l'un de nos produits », explique M. Griffith.
Les résultats étaient pratiquement identiques à ceux obtenus avec leur autre système de sablage automatisé très coûteux. « Je ne peux pas dire que je remarque une grande différence entre les deux. [La Fuse Blast] est bien plus performante que nous le pensions », a poursuivi M. Griffith.
Moins de temps pour le post-traitement, plus de temps pour l'optimisation de la conception
L'automatisation de la Fuse Blast ne permet pas seulement de libérer le temps qu'il fallait auparavant consacrer au sablage manuel des pièces : elle réduit aussi le temps que M. Griffith et son équipe doivent passer sur la Fuse Sift. Le fait de passer plus de temps sur la Fuse Sift permettait jusqu'ici de réduire la durée du sablage manuel. À présent, la Fuse Blast effectue des cycles automatisés et produit des pièces propres, même si les pièces placées dans le panier sont encore pleines de poudre. « Maintenant, je dois beaucoup moins me soucier de la quantité de poudre que je retire [avec la Fuse Sift], car je sais de quoi la Fuse Blast est capable. Dorénavant, il ne faut plus nettoyer les pièces dans la Fuse Sift pour accélérer le sablage. Et la petite quantité de poudre que nous pourrions récupérer en procédant à un dépoudrage minutieux dans la Fuse Sift ne vaut pas les coûts de main-d'œuvre supplémentaires qu'elle impliquerait », explique Griffith.
Dans le cas d'une pièce produite environ 50 fois par semaine, l'équipe de M. Griffith procédait à un sablage manuel et devait nettoyer trois trous par pièce à l'aide d'un cure-pipe. Grâce à la Fuse Blast, il peut désormais programmer un cycle automatisé et s'en aller, puis revenir au bout de 20 à 30 minutes et trouver un lot de pièces parfaitement propres. « La Fuse Blast est une machine phénoménale. Elle fait un travail fantastique pour dégager les trous, ce qui est probablement l'un des plus grands gains de temps pour nous », déclare M. Griffith.
Adapter la taille de votre parc d'impression 3D
M. Griffith et son équipe ont procédé de manière systématique pour passer à l'impression 3D : le premier audit a démontré les avantages commerciaux des six premiers appareils achetés. Maintenant que l'équipe a identifié d'autres économies de coûts et de main-d'œuvre et qu'elle a optimisé les conceptions pour un catalogue complet de composants, elle souhaite augmenter ses capacités d'impression 3D.
« Chaque fois qu'une pièce arrive sur mon bureau, la première question que je me pose est la suivante : "Pouvons-nous encore un peu l'améliorer grâce à l'impression 3D ?" Je pense que c'est en recherchant ces opportunités que nous avons pu devenir ce que nous sommes, économisé le plus d'argent et réduit le coût des composants », déclare M. Griffith.
Les avantages sont évidents pour l'ensemble de l'entreprise : les équipes qui travaillent avec des clients ayant des applications spécifiques ou de niche peuvent proposer des solutions rentables en produisant de petites séries en interne. « Même si les clients n'ont besoin que de cinq, dix ou cinquante pièces d'une pièce fabriquée sur mesure, nous pouvons généralement répondre à leur demande à bas coût. Ainsi, nous sommes en mesure de répondre rapidement aux besoins du marché », explique M. Griffith.
Depuis sa première réunion où il a laissé toute la salle sans voix, M. Griffith a élaboré une analyse de rentabilité pour les fabricants de toutes tailles : avec l'impression 3D SLA et SLS, la production en interne permet d'avoir accès à de nouvelles applications et d'améliorer la réussite commerciale, ainsi que d'optimiser les performances des produits, de se protéger des problèmes de chaîne d'approvisionnement et de réduire les coûts.
Pour en savoir plus sur l'intégration des procédés SLS et SLA en interne, prenez rendez-vous avec notre équipe de vente.