Comment concevoir et imprimer en 3D des assemblages par encliquetage pour les enceintes, les boîtes, les couvercles, etc.
Les assemblages par encliquetage sont si courants dans les productions quotidiennes que de nombreuses personnes ne savent peut-être même pas que les éléments qu'elles utilisent en permanence sont des pièces encliquetables. Ce type de conception se retrouve dans les produits de consommation et les applications industrielles qui nous entourent : des couvercles de récipients alimentaires aux ceintures de sécurité, en passant par les verrous de portes, les assemblages par encliquetage sont omniprésents.
L'impression 3D étant devenue plus puissante et plus accessible, un plus grand nombre de personnes sont maintenant en mesure de concevoir leurs propres prototypes fonctionnels ou pièces finales, et ont besoin de découvrir comment créer un assemblage par encliquetage fonctionnel de haute qualité. Dans le guide suivant, nous allons voir ce qui définit un assemblage par encliquetage, quand et comment ils sont le plus utiles, les instructions de conception pour un encliquetage réussi, et les types de technologies et de matériaux d'impression 3D pour obtenir les meilleures performances.
Pour voir le pas à pas de la conception et de l'impression 3D d'un assemblage par encliquetage, regardez notre webinaire à la demande ici.
Introduction aux pièces encliquetables dans l'impression 3D
Qu'est-ce qu'un assemblage par encliquetage ?
La partie rouge est la composante saillante, également connue sous le nom de mâle, crochet, bord ou tête, qui doit subir une légère sollicitation à la base pour s’accrocher à la partie négative turquoise, ou à la partie en creux.
Un assemblage par encliquetage est un moyen courant, économique et facile d'assembler deux pièces ou composants. Bien qu'il existe différents types de pièces encliquetables, elles ont toutes en commun d'avoir une caractéristique saillante sur un composant qui s'accroche à une caractéristique déprimée ou négative (appelée contre-dépouille) sur l'autre composant. La partie saillante peut également être appelée crochet, perle ou tête. Certaines pièces encliquetables sont inséparables une fois assemblées, tandis que d'autres peuvent se séparer et s'assembler plusieurs fois, en fonction de la forme de la contre-dépouille et de la force nécessaire pour déformer la protubérance afin de la « désencliqueter » de la contre-dépouille.
Les pièces encliquetables sont des moyens faciles de créer des assemblages car, en particulier pour les plastiques, elles ne nécessitent qu'un léger ajustement pour la partie saillante de l'assemblage et peuvent généralement être démontées facilement.
Types d'assemblages par encliquetage et applications
Avant de commencer la conception d'un assemblage par encliquetage, il faut d'abord décider du type d'assemblage par encliquetage à utiliser : il existe quatre types d'assemblage par encliquetage courants.
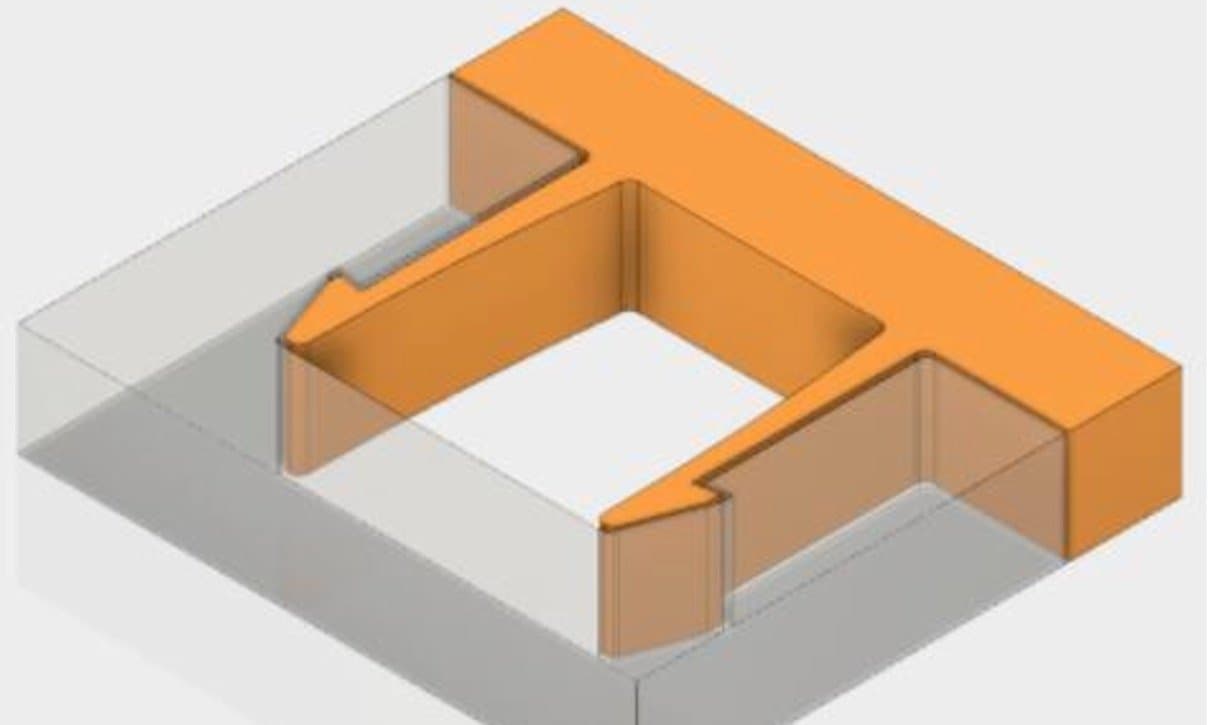
Pièces encliquetables en porte-à-faux
- Bras en porte-à-faux avec élément de verrouillage au niveau de l'extrémité libre
- Le bras en porte-à-faux se déforme à travers la cavité, s'enclenche à la fin et revient à sa forme initiale sans contrainte.
- Assemblage par encliquetage le plus courant
- Exemple : Boucles de siège ou de sac à dos
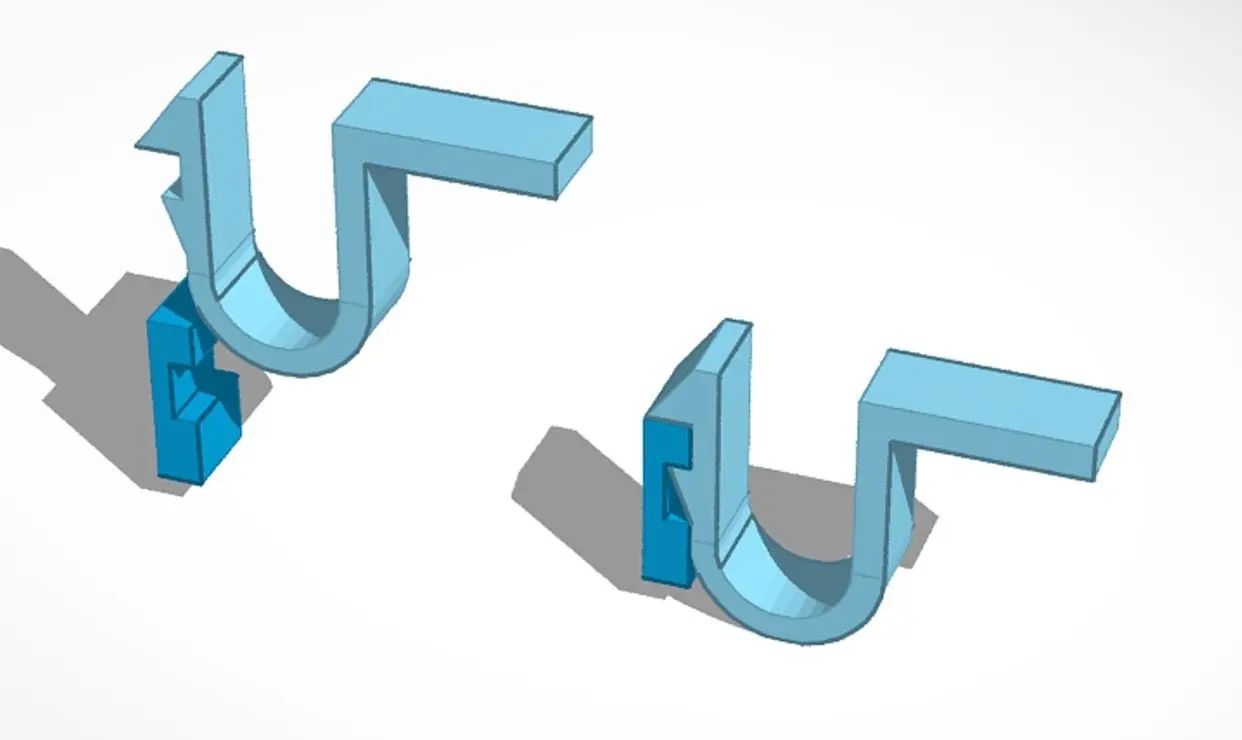
Pièces encliquetables en forme de U
- Comme dans le cas d'une articulation en porte-à-faux, si le bras est replié sur lui-même
- Exemple : Boîtiers électroniques
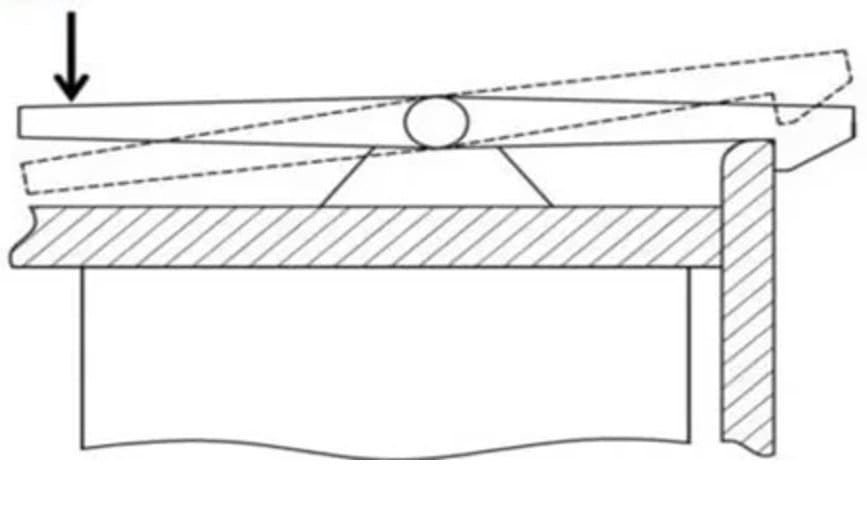
Pièces encliquetables de torsion
- Semblable à l'assemblage par encliquetage en porte-à-faux, mais le bras de l'élément en porte-à-faux est maintenu en position par une force de torsion exercée par un ressort ou un levier.
- Exemple : Roues de poussette ou de panier verrouillables
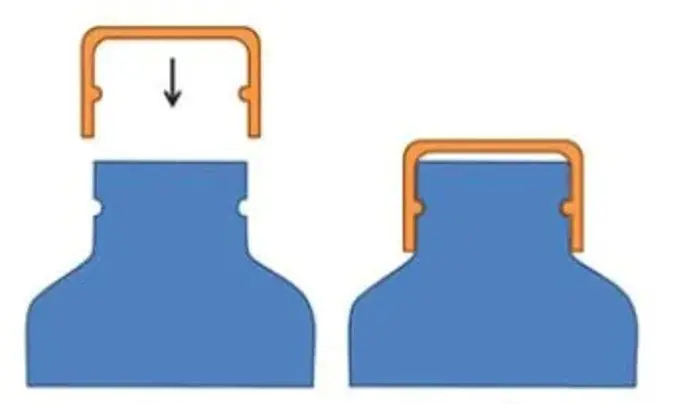
Pièces encliquetables annulaires
- Presque toujours pour des formes cylindriques ou circulaires
- Un anneau légèrement plus flexible est comprimé sur un composant d'anneau plus rigide avec une arête qui s'accroche et palpe le composant flexible, le contenant par tension
- Exemple : Bouchons de bouteilles
Pour explorer en détail les pièces encliquetables et savoir comment les concevoir pour l'impression 3D, téléchargez le guide de conception du MIT.
Impression 3D de pièces encliquetables
Les plastiques sont très bien adaptés aux pièces encliquetables en raison de leur grande flexibilité, c'est pourquoi les polymères de l'impression 3D excellent pour créer ce type d'assemblages simples. La fabrication rapide de ces pièces plastiques encliquetables est assez simple une fois que l'on a compris les instructions de conception et les paramètres d'impression de base.
Les méthodes d'impression 3D les plus courantes ont leurs propres forces et faiblesses, notamment en ce qui concerne les pièces encliquetables, qui nécessitent des tolérances serrées et une grande résistance mécanique.
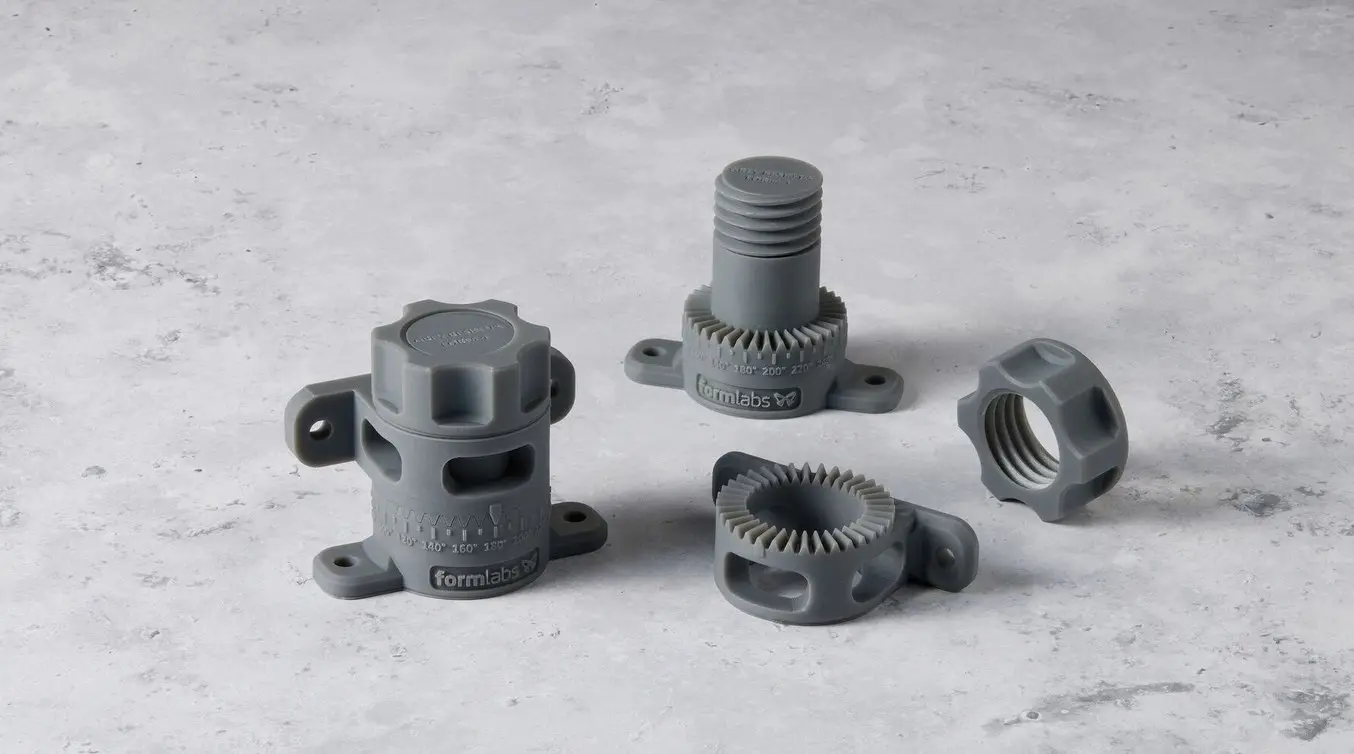
Commander un échantillon gratuit
Examinez et constatez par vous-même la qualité Formlabs. Nous enverrons un échantillon SLA gratuit à votre bureau.
Comment imprimer en 3D des pièces encliquetables
Choix d'un processus d'impression 3D pour les pièces encliquetables
Les trois procédés d'impression 3D les plus courants pour les matières plastiques, à savoir le dépôt de fil fondu (FDM), la stéréolithographie (SLA), et le frittage sélectif par laser (SLS), peuvent tous produire des assemblages par encliquetage fonctionnels pour des assemblages 3D faciles à réaliser. Mais lorsque vous vous demandez quelle technologie et quel matériau choisir pour votre application spécifique, il est important de remarquer les différences entre ces méthodes.
Le tolérancement est très important, tout comme la finition de surface, car les deux pièces encliquetables doivent s'ajuster étroitement l'une à l'autre, tout en laissant une marge de manœuvre pour se placer. Les imprimées SLA produisent généralement des pièces présentant la meilleure finition de surface, mais dans le cas des pièces encliquetables, la surface légèrement granuleuse des pièces SLS peut en fait contribuer à la sécurité de l'ajustement.
Adéquation des procédés d'impression 3D courants à l'impression 3D de pièces encliquetables :
-
FDM : acceptable, selon l'orientation (oriente les pièces pour la résistance dans le plan XY, pas Z). Les pièces imprimées par FDM ont généralement des tolérances légèrement plus mauvaises que celles imprimées par SLA ou SLS, ainsi que des lignes de couches plus visibles qui peuvent interférer avec l'assemblage par encliquetage.
-
SLA : Les bonnes tolérances, les tolérances serrées et les vitesses d'impression rapides permettent une itération rapide et très précise. Les imprimantes 3D SLA permettent également une gamme de matériaux et de propriétés mécaniques, ce qui facilite l'optimisation de la résistance, de la rigidité ou de la flexibilité, en fonction des objectifs de l'articulation encliquetable (par exemple, si vous voulez qu'elle soit détachable ou permanente).
-
SLS : Les excellentes propriétés des matériaux utilisés dans les utilisations finales confèrent aux assemblages par encliquetage robustes une grande longévité. La surface légèrement granuleuse des pièces imprimées 3D SLS peut rendre un assemblage par encliquetage encore plus solide, car le frottement ajouté le fait palier plus sûrement. En outre, les matériaux SLS sont des thermoplastiques standards du secteur, tels que le nylon, les composites de nylon et le TPU. Les propriétés mécaniques étant déjà connues et prédéterminées, vous pouvez utiliser le SLS pour réaliser des pièces encliquetables faisant partie d'assemblages plus importants, avec des réactions prévisibles et fiables aux facteurs de stress.
Voici un résumé des principaux facteurs à prendre en compte pour choisir entre les imprimantes 3D FDM, SLA et SLS.
Dépôt de fil fondu (FDM) | Stéréolithographie (SLA) | Frittage sélectif par laser (SLS) | |
---|---|---|---|
Résolution | ★★☆☆☆ | ★★★★★ | ★★★★☆ |
Précision | ★★★★☆ | ★★★★★ | ★★★★★ |
Finition de surface | ★★☆☆☆ | ★★★★★ | ★★★★☆ |
Volume de production | ★★★☆☆ | ★★★★☆ | ★★★★★ |
Conceptions complexes | ★★★☆☆ | ★★★★☆ | ★★★★★ |
Facilité d’utilisation | ★★★★★ | ★★★★★ | ★★★★☆ |
Avantages | Machines et matériaux grand public à faible coût Rapide et facile pour les petites pièces simples | Excellent rapport qualité prix Haute-précision Finition de surface lisse Grande vitesse d'impression Large gamme d'applications fonctionnelles | Pièces fonctionnelles solides Liberté de conception Pas besoin de structures de support |
Inconvénients | Faible précision Faible niveau de détail Liberté de conception limitée | Certains matériaux sont sensibles à une exposition prolongée aux UV | Finition de surface légèrement irrégulière Choix réduit de matériaux |
Applications | Modélisation conceptuelle Prototypage rapide Prototypage fonctionnel Aides à la fabrication | Modélisation conceptuelle Prototypage rapide Prototypage fonctionnel Outillage rapide Aides à la fabrication Fabrication de petites séries, de pièces provisoires ou sur mesure Modèles et dispositifs dentaires Modèles et dispositifs médicaux Prototypage et moulage de bijoux Modèles et accessoires | Prototypage rapide Prototypage fonctionnel Fabrication de petites séries, de pièces provisoires ou sur mesure Aides à la fabrication durables Dispositifs médicaux, prothèses et orthèses |
Volume d’impression | Jusqu’à 300 x 300 x 600 mm (imprimantes 3D de bureau et d’atelier) | Jusqu’à 353 x 196 x 350 mm (imprimantes 3D de bureau et d’atelier) | Jusqu’à 165 x 165 x 300 mm (imprimantes 3D d’atelier industrielles) |
Matériaux | Thermoplastiques standard, tels que l’ABS, le PLA et leurs variantes. | Variantes de résines (plastiques thermodurcissables). Standard, technique (type ABS, type PP, flexible, résistant à la chaleur, rigide chargé de verre), coulable, et dentaire et médical (biocompatible). Silicone et céramique purs. | Thermoplastiques techniques. Nylon 11, nylon 12, composites en nylon à charge de verre ou de carbone, polypropylène, TPU (élastomère). |
Formation | Formation minimale sur la configuration de l'impression, le fonctionnement de l'appareil et la finition ; formation modérée sur la maintenance. | Plug and play. Formation minimale sur la configuration de l'impression, le fonctionnement de l'appareil et la finition, la maintenance. | Formation modérée sur la configuration de l'impression, le fonctionnement de l'appareil et la finition, la maintenance. |
Environnement de travail requis | Local avec climatisation ou, de préférence, ventilation sur mesure pour appareils de bureau. | Les appareils de bureau et d'atelier peuvent fonctionner dans des bureaux. | Les systèmes d'atelier requièrent peu d'espace. |
Équipements auxiliaires | Système de retrait des supports pour les machines à supports solubles (automatisé en option), outils de finition. | Station de lavage et de post-polymérisation (les deux peuvent être automatisés), outils de finition. | Stations de post-traitement pour la gestion des poudres et le nettoyage des pièces. |
Coût de l'équipement | Les imprimantes et les kits d'impression 3D entrée de gamme commencent autour de 200 €. Les imprimantes FDM de bureau professionnelles commencent entre 2000 et 8000 €, et les systèmes industriels autour de 15 000 €. | Les imprimantes 3D résine bas de gamme sont disponibles entre 200 et 1000 €, les imprimantes 3D SLA professionnelles entre 2500 et 10 000 € et les imprimantes 3D résine grand format entre 5000 et 25 000 €. | Les imprimantes 3D SLS industrielles d'atelier commencent à un peu moins de 30 000 € pour l'imprimante et à 60 000 € pour l'ensemble de l'écosystème, y compris les stations de gestion et de nettoyage des poudres. Les imprimantes SLS industrielles traditionnelles coûtent environ 200 000 €. |
Coûts des matériaux | 50 à 150 €/kg pour la plupart des filaments standard, et 100 à 200 €/kg pour les matériaux de supports ou les filaments techniques. | 100 à 200 €/L pour la plupart des résines standard et techniques, 200 à 500 €/L pour les matériaux biocompatibles. | 100 €/kg pour le nylon. Le procédé SLS ne requiert pas de supports et la poudre non fondue peut être réutilisée, ce qui diminue les coûts des matériaux. |
Besoins en main d'œuvre | Retrait manuel des supports (il peut être pratiquement complètement automatisé pour les systèmes à supports solubles). Un post-traitement assez long peut être nécessaire pour obtenir une finition de haute qualité. | Lavage et post-polymérisation (les deux pouvant être presque entièrement automatisés). Post-traitement simple après l'impression pour enlever les traces de supports. | Flux de travail simple et semi-automatique pour le nettoyage des pièces et la récupération de la poudre. |
Les imprimantes 3D SLA de la série Form et SLS de la série Fuse de Formlabs peuvent produire des assemblages par encliquetage dans une vaste gamme de matériaux, assez rapidement et à un prix abordable. Leur vitesse et leur faible coût par pièce vous permettent également de tester et d'itérer rapidement vos conceptions de pièces encliquetables, afin d'optimiser la résistance et les performances de votre assemblage.
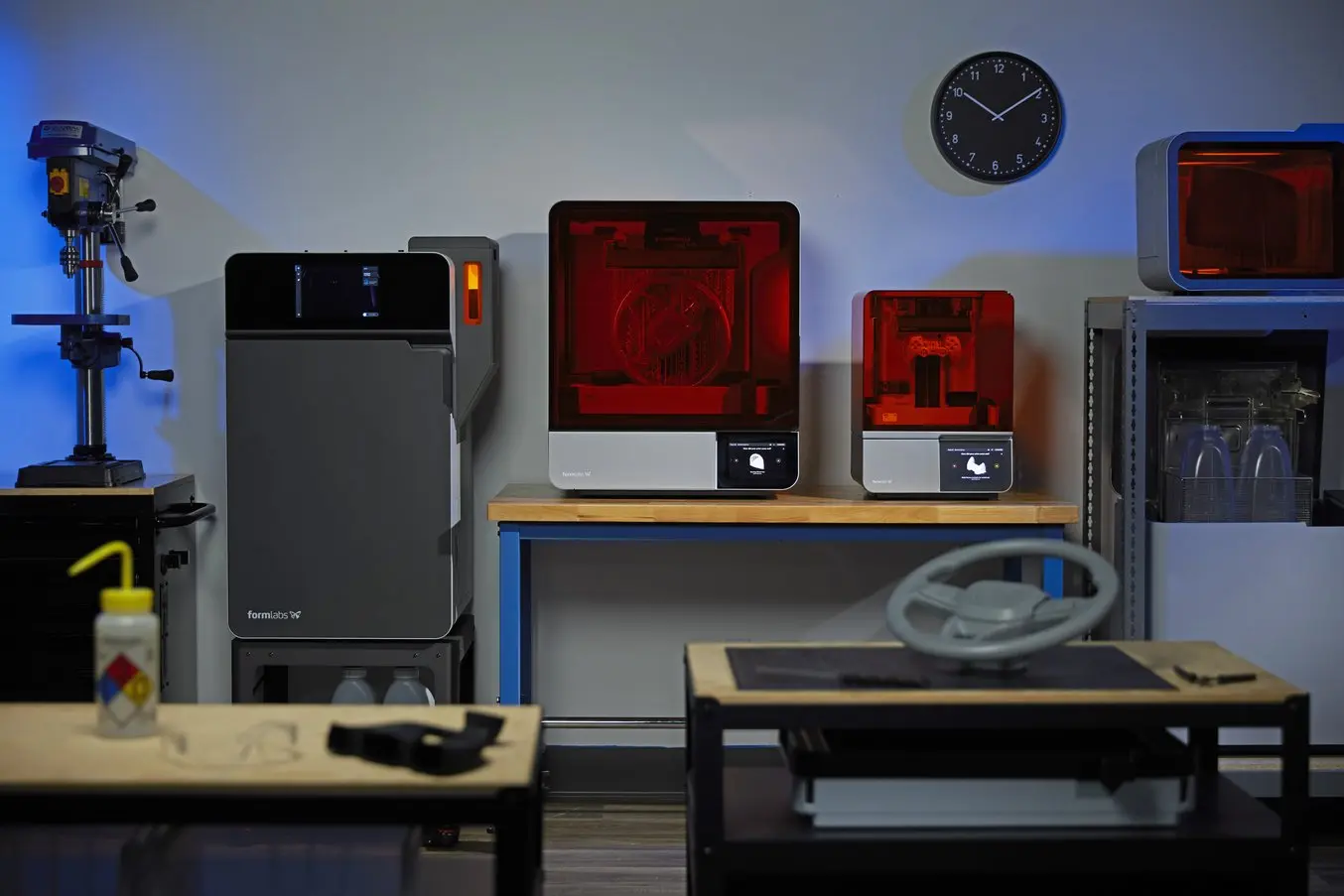
De gauche à droite : L'imprimante 3D SLS Fuse 1+ 30W de Formlabs, l'imprimante 3D SLA grand format Form 4L, l'imprimante 3D SLA de bureau Form 4, et les solutions de post-traitement SLA Form Cure L (en haut) et Form Wash L (en bas).
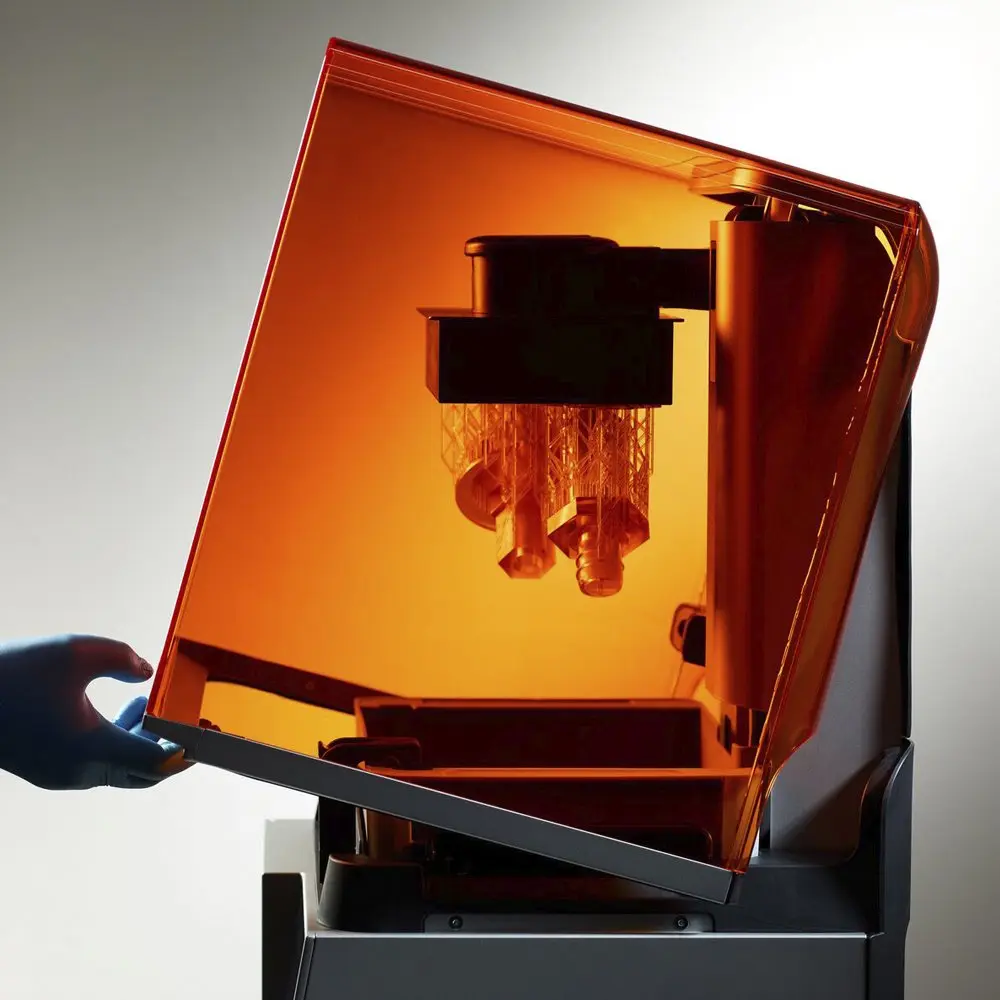
Introduction à l’impression 3D avec la stéréolithographie de bureau (SLA)
Vous cherchez une imprimante 3D pour produire rapidement des modèles haute résolution ? Téléchargez notre livre blanc pour découvrir comment fonctionne l’impression SLA et pourquoi elle est tant utilisée pour créer des modèles aux détails incroyables, une grande précision dimensionnelle et une excellente finition de surface.
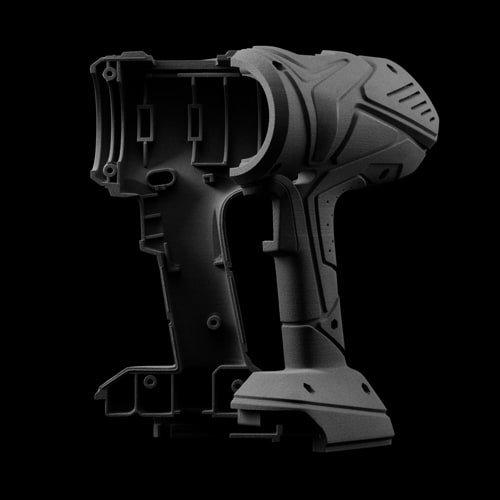
Introduction à l’impression 3D à frittage sélectif par laser (SLS)
Vous cherchez une imprimante 3D pour réaliser des pièces solides et fonctionnelles ? Téléchargez le livre blanc pour savoir comment fonctionne l’impression 3D SLS et les raisons de sa popularité pour le prototypage fonctionnel et la production de produits finis.
Matériaux pour l'impression 3D de pièces encliquetables
Lors de la conception d'un joint encliquetable, soit le matériau a déjà été choisi (avec une contrainte acceptable prédéfinie) et vous devez modifier les dimensions de votre conception d'encliquetage pour tenir compte de cette contrainte, soit vos dimensions sont définies à l'avance et vous devez choisir un matériau qui aura les performances nécessaires avec ces dimensions.
Pour choisir un matériau, il faut d'abord choisir sa technique d'impression 3D : FDM, SLA ou SLS. Pour les pièces imprimées en 3D FDM, la résistance varie selon l'axe ; si le porte-à-faux ne peut être créé que dans l'axe Z (la contrainte étant appliquée le long des lignes de couche), l'allongement à la rupture est réduit d'environ 50 % et la résistance à la traction d'environ 20 à 30 %. Les pièces imprimées avec la technologie SLA sont anisotropes et l'élément en porte-à-faux peut être imprimé dans n'importe quelle orientation. Les pièces imprimées 3D SLS sont anisotropes, mais avec seulement un faible degré de variation entre les axes XY et Z, à l'exception des poudres chargées de fibres de carbone comme Nylon 11 CF Powder, qui a sa plus grande résistance dans l'axe X (en suivant la direction dans laquelle les fibres de carbone sont disposées par le recouvreur de poudre).
Une contrainte acceptable peut être déterminée en examinant les courbes de contrainte/déformation pour différents matériaux. Si la contrainte acceptable est plus faible, les dimensions telles que la longueur du porte-à-faux et la largeur de la racine doivent être modifiées en conséquence. Avec une contrainte acceptable plus élevée, il est possible de réaliser un porte-à-faux plus long ou une base plus fine, tout en créant un assemblage par encliquetage fonctionnel. Examinez les tracés de contrainte et de contrainte suivants, en tenant compte du fait que ces essais sont terminés sur des barres ASTM de type I, et non sur des pièces encliquetables. Des considérations de conception appropriées peuvent permettre de surmonter les faiblesses ou d'abaisser les contraintes acceptables dans un matériau, bien que ces tracés soient d'excellentes ressources si vous êtes limité dans vos variations dimensionnelles et que vous recherchez simplement le matériau le plus fonctionnel.
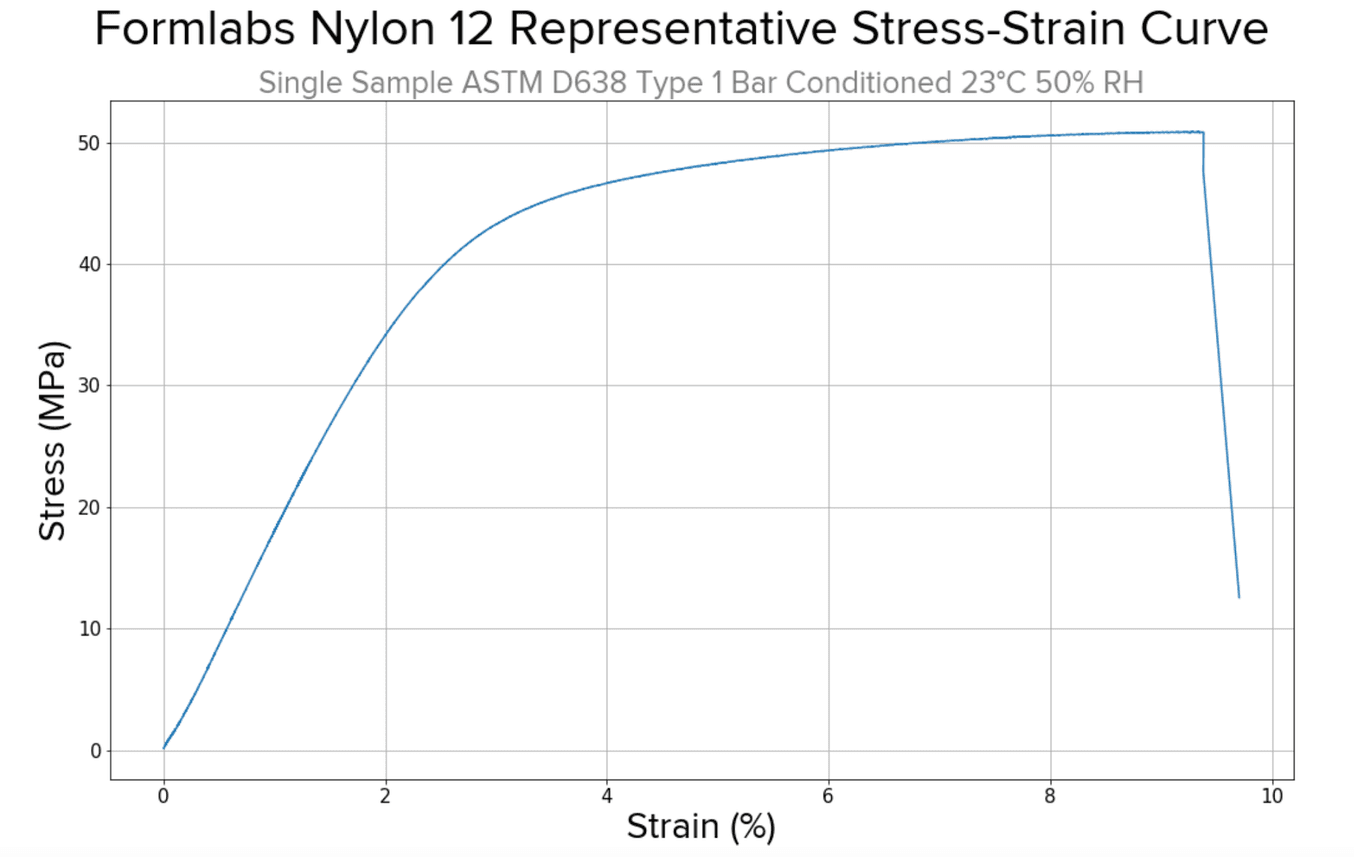
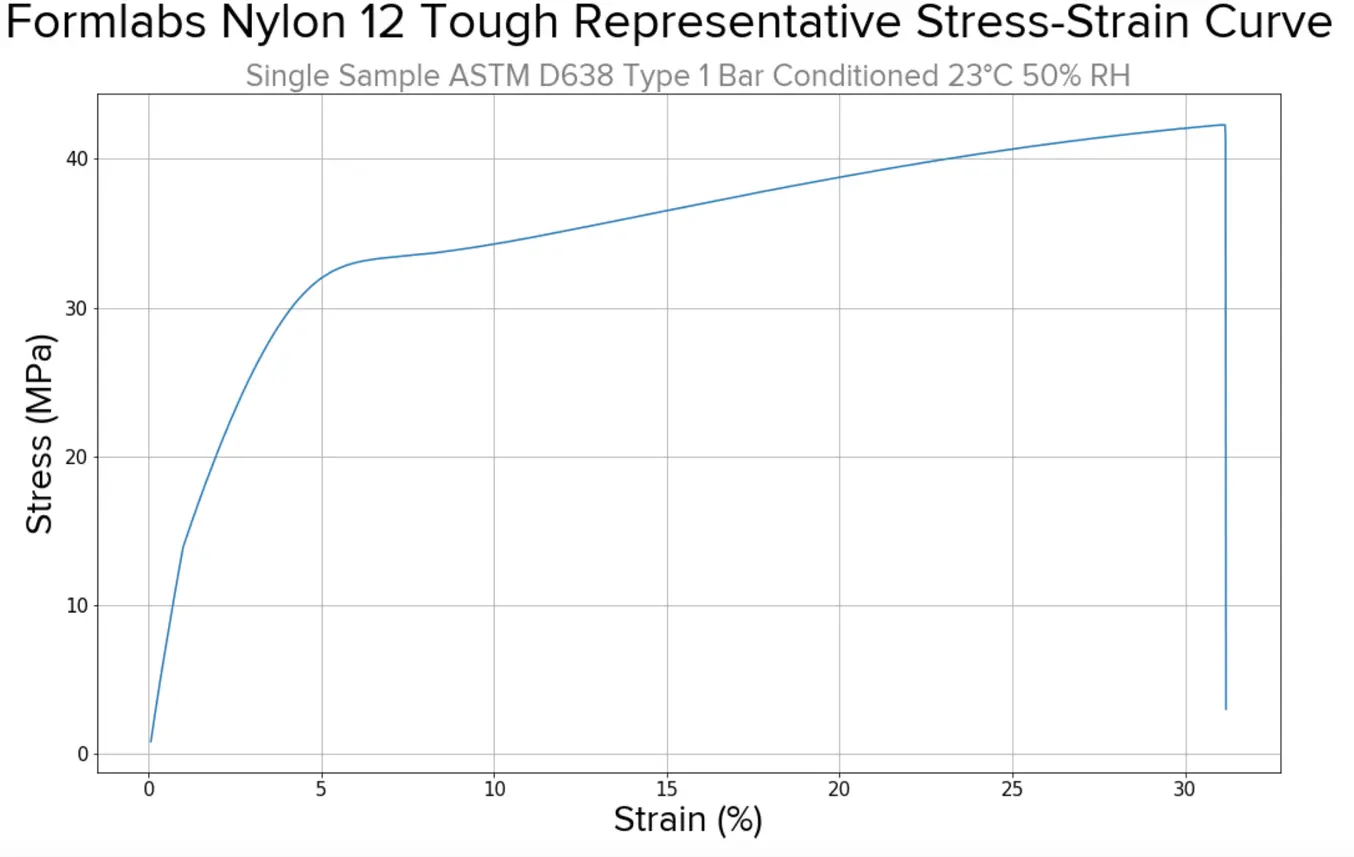
En ce qui concerne les résines SLA, voici un tableau comparant trois types de résines : les résines standard (principalement utilisées pour le prototypage) et les résines tenaces et durables (utilisées pour des assemblages plus fonctionnels ou à cycle plus élevé).
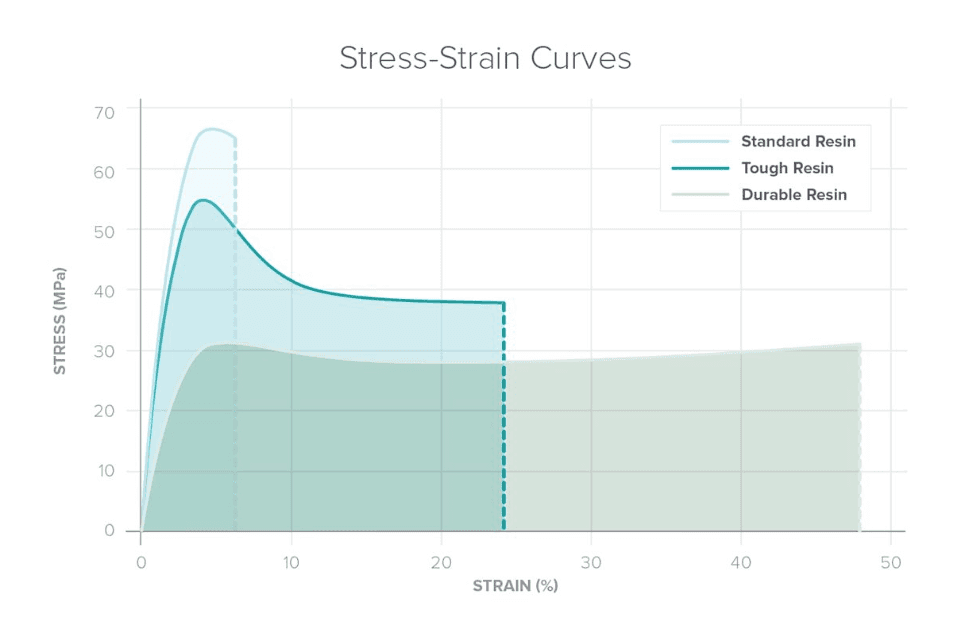
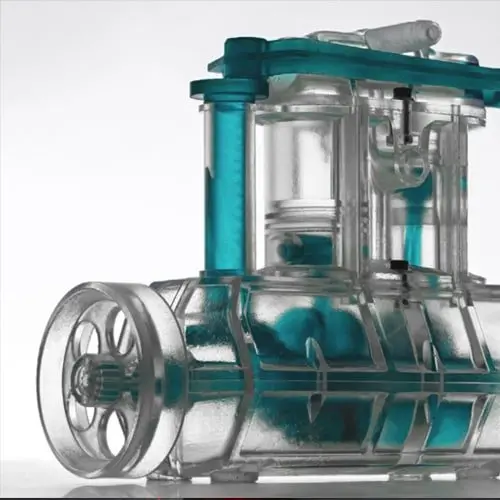
Optimisation de la conception d’assemblages imprimés en 3D
Concevoir avec les bonnes tolérances et un bon ajustement à l'esprit réduisent le temps passé au post-traitement, facilite l'assemblage et réduit les coûts de matériaux et d'itérations. Téléchargez notre livre blanc pour en savoir plus sur la tolérance et l’adéquation dans la conception d’assemblages fonctionnels imprimés en 3D.
Meilleures pratiques pour la conception d'assemblages par encliquetage pour l'impression 3D
Il n'existe pas de dimensions exactes « correctes » pour un assemblage par encliquetage : la largeur, la longueur et la forme optimales des différents composants de votre assemblage par encliquetage varient en fonction du type de matériau et de la dimension globale. Il existe toutefois quelques notions de base que les ingénieurs suivent lors de la conception de pièces encliquetables, en particulier pour l'impression 3D.
- Un crochet plus long réduit la contrainte sur la base.
- Une hauteur inférieure réduit la contrainte et l'ajustement pour l'assemblage et le désassemblage des pièces encliquetables.
- La largeur de la base n'a aucune influence sur la tolérance à la contrainte de la structure globale.
- Amincissez le crochet ou créez un crochet trapézoïdal allongé plutôt qu'un crochet droit, parallèle ou rectangulaire.
- Optimisez les courbes sur les bords de votre crochet plutôt que les filets.
- Il n'existe pas de jeu parfait pour un assemblage – certaines applications peuvent nécessiter plus de force que d'autres pour retirer le crochet de la contre-dépouille, ce qui est une bonne chose, d'autres peuvent être conçues spécifiquement pour se démonter facilement.
- En cas de doute, essayez et itérez !
Pas à pas : Conception et impression 3D d'un boîtier personnalisé pour Raspberry Pi
Étape 1 : Préparation de la conception personnalisée
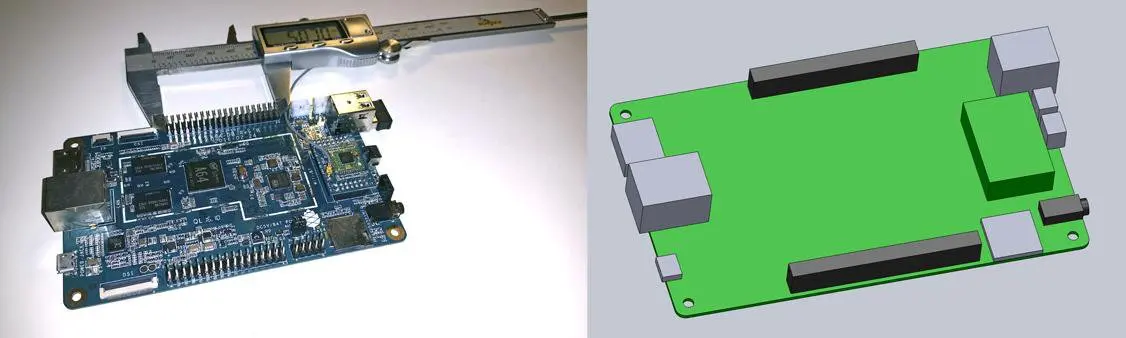
Mesure de composants électroniques (à gauche). Première phase du modèle 3D avec les blocs de base (à droite).
Pour ce projet, nous allons créer un boîtier pour un ordinateur monocarte Pine 64 (téléchargez le fichier STL sur Pinshape pour suivre les étapes). Ce tutoriel utilise SolidWorks en raison de sa popularité dans la conception de produits et l'ingénierie, mais vous pouvez utiliser un logiciel CAO similaire.
Tout d'abord, nous utilisons un calibre numérique ou une règle pour mesurer les composants électroniques. Nous commençons la conception du boîtier par un exercice complet d'ingénierie inverse sur la carte de circuit imprimé, en mesurant la carte, la position des trous de montage et tous les ports ou prises qui doivent être accessibles à travers le boîtier. Il est recommandé de mesurer les dimensions maximales de l'objet entier en le visualisant comme une boîte afin de comprendre exactement où les principaux éléments doivent être placés. Dans Solidworks, nous reproduisons ces mesures sous la forme d'un groupe de boîtes simples sur un seul fichier.
Étape 2 : S'assurer que les caractéristiques sont imprimables et orientées de manière optimale pour la technique d'impression 3D choisie
Lorsque vous imprimez des pièces à encliqueter comme ce boîtier avec des imprimantes 3D SLA, vous disposez d'une tolérance dimensionnelle plus que suffisante pour créer les petits alésages et les caractéristiques requis par la conception. Si vous n'êtes pas sûr de votre pièce, consultez le guide de conception, comme ce Guide de conception pour la Form 4 pour l'imprimante 3D SLA de Formlabs et ce Guide de conception de la série Fuse pour la série Fuse.
L'orientation de l'impression a une incidence non seulement sur la qualité des pièces et l'imprimabilité, mais aussi sur les propriétés mécaniques, le temps de post-traitement lors du retrait des supports et le temps d'impression. Les pièces encliquetables imprimées en SLA doivent être orientées légèrement en biais par rapport à la plateforme de fabrication afin de réduire les forces de décollement susceptibles d'entraîner une déformation de la pièce ou une baisse de la précision. Les pièces encliquetables imprimées par SLS sont autoportantes, mais pour certains matériaux, comme Nylon 11 CF Powder, elles doivent être orientées de manière à ce que la direction de la contrainte soit parallèle au haut de la chambre de fabrication, afin que les fibres de carbone soient enroulées dans cette direction et que la résistance globale soit maximisée.
Étape 3 : Conception du fond du boîtier
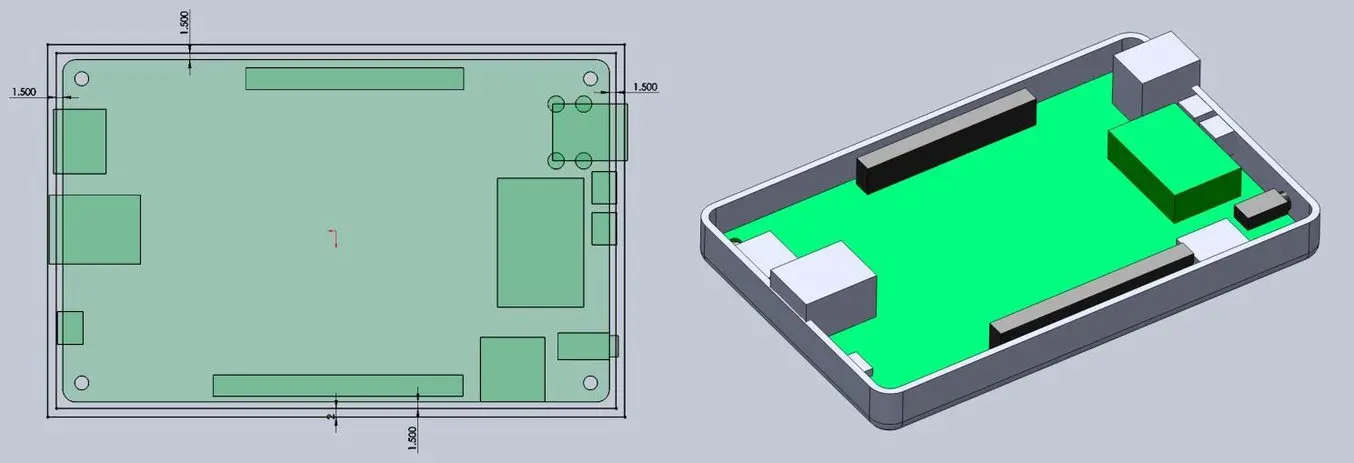
Laissez un espace entre le périmètre de vos composants électroniques et le boîtier (à gauche). Intégrez les parois de la partie inférieure du boîtier dans le modèle 3D (à droite).
Concevez votre boîtier encliquetable comme un assemblage, chaque moitié du boîtier étant modélisée comme une partie distincte. Suivez les conseils ci-dessous :
-
Quelle est la tolérance entre le périmètre de la carte de circuit imprimé et le boîtier ? Les imprimantes 3D SLA et SLS de Formlabs peuvent facilement atteindre une tolérance de 0,4 mm, tandis que les pièces imprimées en 3D FDM peuvent se déformer légèrement, et une tolérance plus proche de 1,5 mm à 2,0 mm peut être préférable.
-
Entaille des ouvertures de port, en tenant compte du besoin spatial de matériaux pour les câbles autour de l'ouverture du port ainsi que du port lui-même. Un supplément de 2,0 mm tout autour de l'ouverture du port est un bon point de départ.
-
Choisissez de créer une moitié inférieure du boîtier plus large où tous les ports s'ajustent à l'intérieur, ou une moitié comme l'image ci-dessus, où certains ports dépassent un peu. Dans ce cas, nous avons réalisé une moitié inférieure moins profonde, de sorte que les câbles ne doivent parcourir qu'une courte distance à l'intérieur, et nous comptons sur la moitié supérieure pour couvrir le reste des portes saillantes.
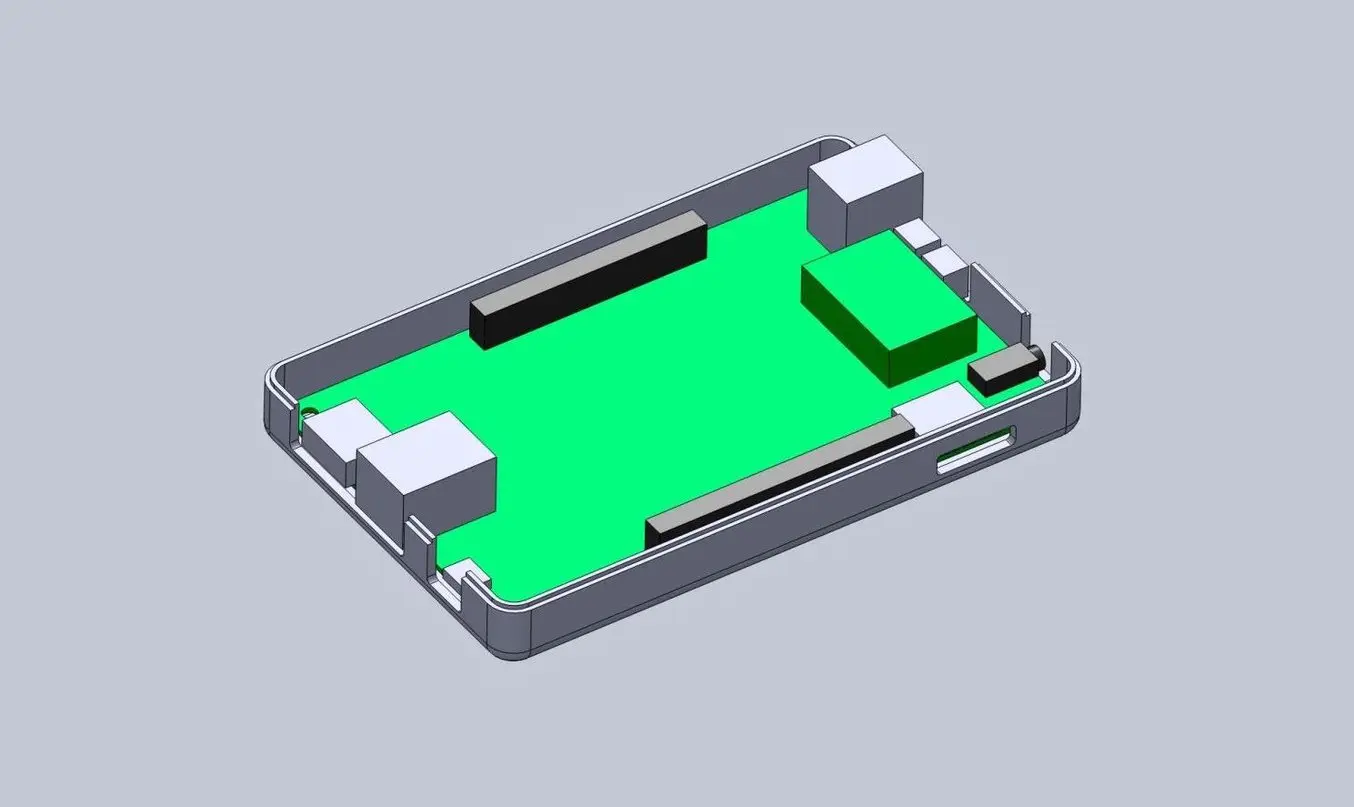
Ajoutez des ouvertures et des trous extrudés en bas pour accueillir des portes.
Étape 4 : Conception de la partie supérieure du boîtier
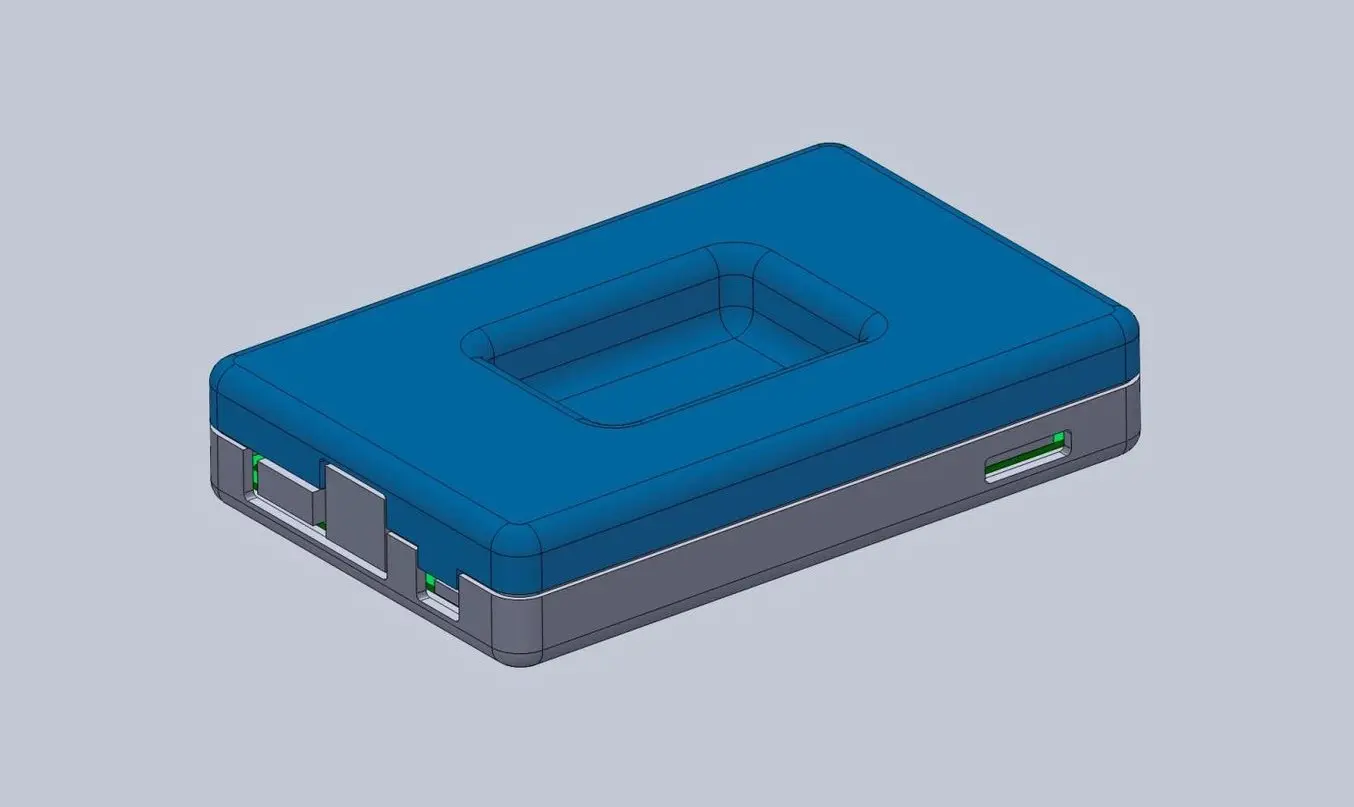
La moitié supérieure du boîtier est une image miroir de la moitié inférieure.
La partie supérieure présente les mêmes ouvertures pour accueillir les portes les plus hautes et du matériel supplémentaire pour combler les espaces vides dans la moitié inférieure. La partie enfoncée au milieu est facultative, mais elle ajoute un détail visuel légèrement plus organique et intéressant.
Étape 5 : Conception du joint
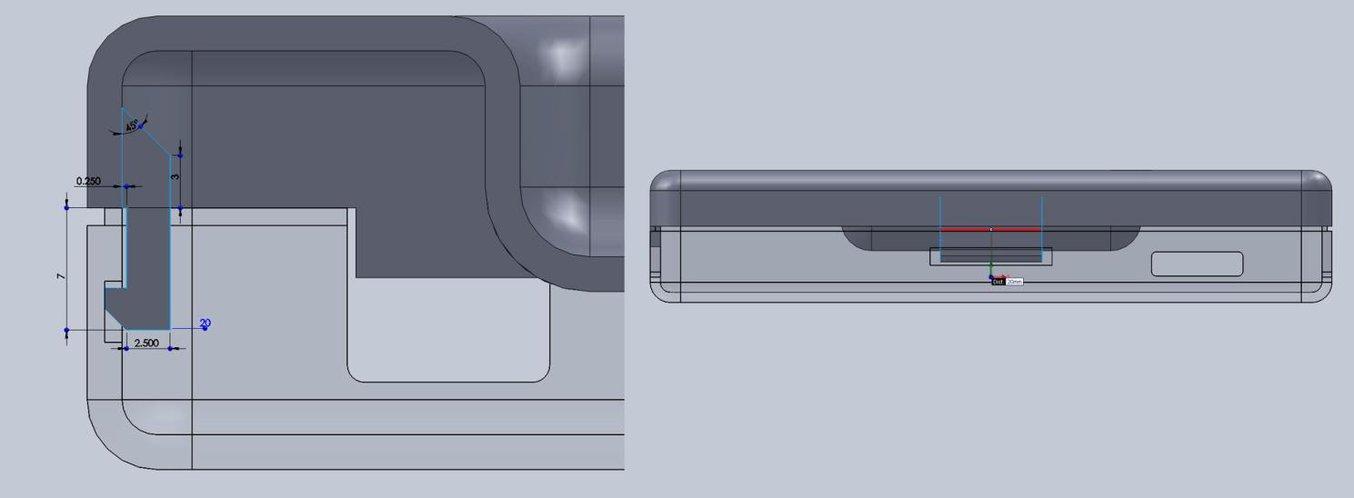
Avec un simple joint en porte-à-faux, la quantité de plastique qui s'insère à l'intérieur peut être augmentée, ce qui permet d'obtenir un loquet plus solide.
Vous pourriez utiliser n'importe quel type d'assemblage par encliquetage présenté précédemment, mais dans ce cas, nous avons opté pour le plus simple : un joint en porte-à-faux interne, qui offre une grande résistance avec une consommation minimale de matériaux. La conception de l'assemblage par encliquetage est la même des deux côtés du boîtier. Pour renforcer la solidité de l'assemblage par encliquetage, vous pouvez allonger la protubérance de manière à ce qu'il faille plus de résistance pour la retirer de la cavité.
Dans cet assemblage par encliquetage, il n'y a que 1,2 mm, mais 2 mm ou plus rendraient l'encliquetage beaucoup plus étanche : il n'y a pas de bonne réponse, cela dépend simplement de votre cas d'utilisation idéal et de la facilité avec laquelle vous souhaitez désassembler l'encliquetage.
Dans cette conception, les broches de la carte de circuit imprimé occupent beaucoup d'espace, de sorte que la fermeture de l'assemblage par encliquetage est capable de s'insérer dans le peu d'espace restant tout en préservant la force nécessaire pour maintenir le boîtier assemblé. Le joint en porte-à-faux est extrudé sur une longueur de 20 mm, ce qui en augmente la résistance.
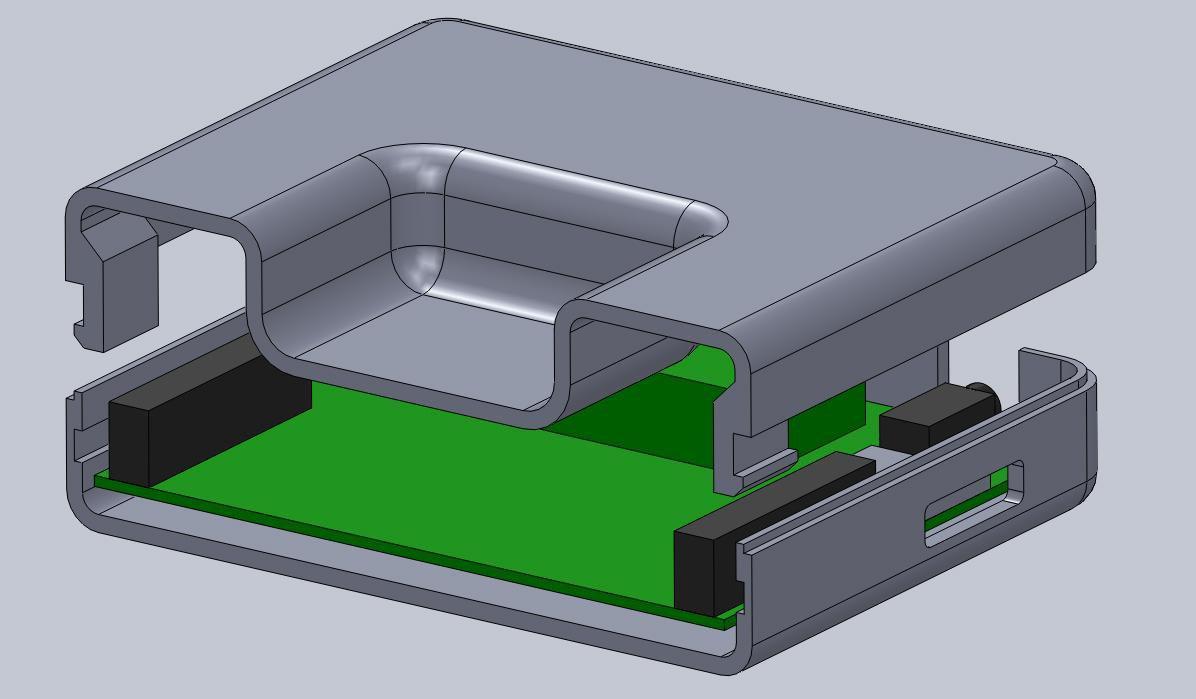
Sur cette vue éclatée, vous pouvez voir les détails de l'encliquetage des deux côtés.
Ci-dessus, nous montrons une section éclatée avec des détails sur le loquet, le circuit imprimé et la position des broches (en noir) qui limitent la taille des joints en porte-à-faux. Au lieu d'avoir une cavité cachée à l'intérieur de la partie inférieure du boîtier, ce détail pourrait être découpé à l'extérieur, ce détail peut être découpé à travers l'extérieur, ce qui permet d'allonger vos éléments d'encliquetage.
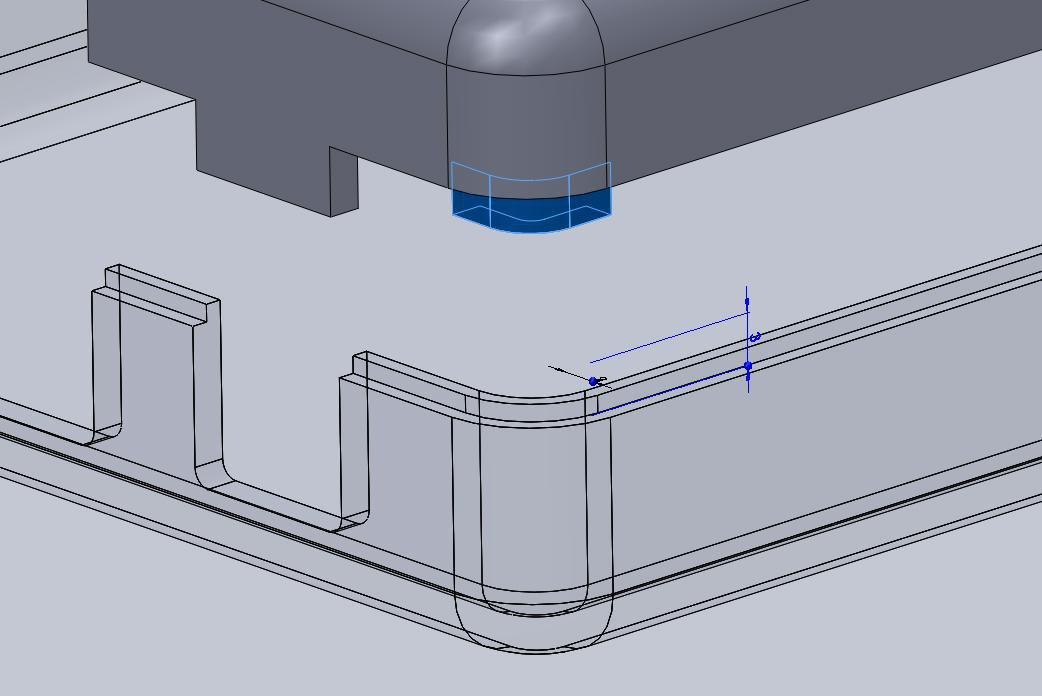
Les ailettes sont de petites extrusions qui s'insèrent dans les tiges opposées du boîtier afin de sécuriser les deux moitiés du boîtier.
Il est possible d'ajouter des ailettes au design, c'est-à-dire de petits éléments extrudés qui s'insèrent dans l'autre moitié du boîtier, pour maintenir les deux moitiés ensemble. Comme nous avons créé deux joints sur des côtés opposés, vous n'en aurez besoin, le cas échéant, que sur les deux côtés libres. Dans ce cas, nous les avons placés dans les coins. L'extrusion n'est que de 3 mm vers le bas, mais cela suffit à empêcher le mouvement des pièces imprimées en 3D interconnectées.
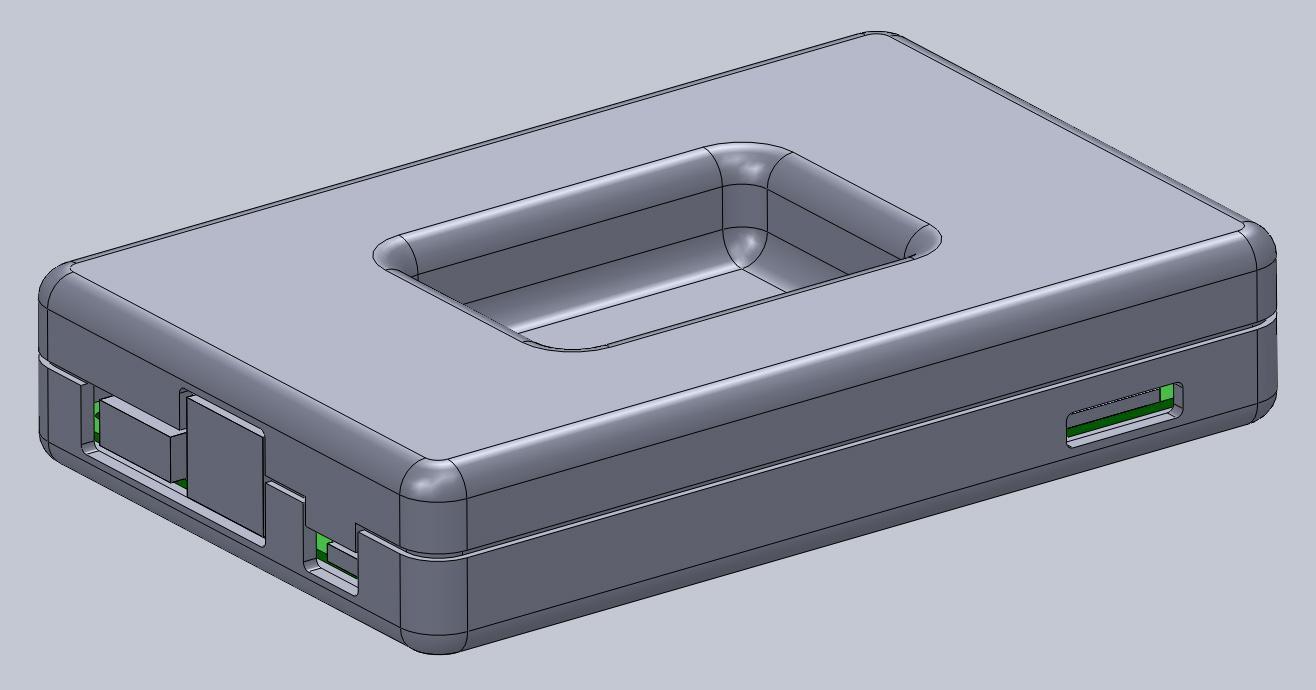
Ce simple boîtier encliquetable peut être adapté à pratiquement n'importe quel type de composant électronique.
Étape 6 : la touche finale
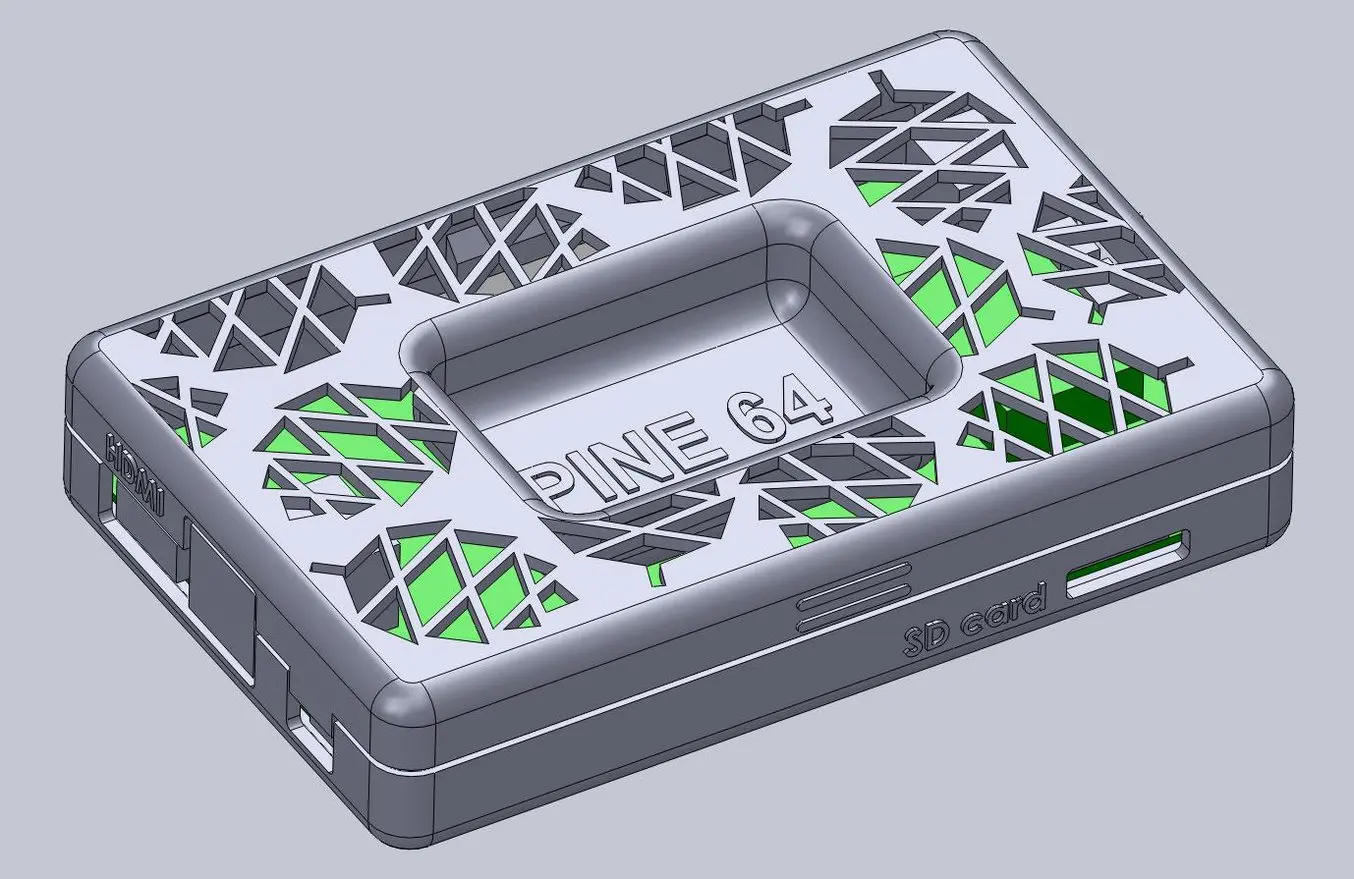
Le modèle final, outre les éléments d'encliquetage, comporte désormais des détails uniques et est prêt à être imprimé en 3D.
Même si ce n'est pas nécessaire, ajouter des détails qui vont au-delà de la fonctionnalité du joint peut rendre le design plus agréable sans trop d'efforts supplémentaires. Une fois votre pièce finalisée dans votre logiciel de conception 3D, exportez-la vers PreForm, et choisissez votre technologie d'impression et votre matériau.
PreForm, le logiciel de préparation d'impression de Formlabs pour les technologies SLA et SLS, intègre de nombreuses fonctionnalités, telles que l'ajout de textures, l'extrusion de noms de produits ou d'étiquettes pour les travaux itératifs, etc. Une fois que vous avez configuré votre impression (manuellement ou en utilisant les outils de préparation à l'impression automatisés de PreForm, tels que les supports générés automatiquement pour SLA ou l'emballage généré automatiquement pour SLS), vous pouvez ajouter des détails supplémentaires ou modifier l'orientation et les structures de support.
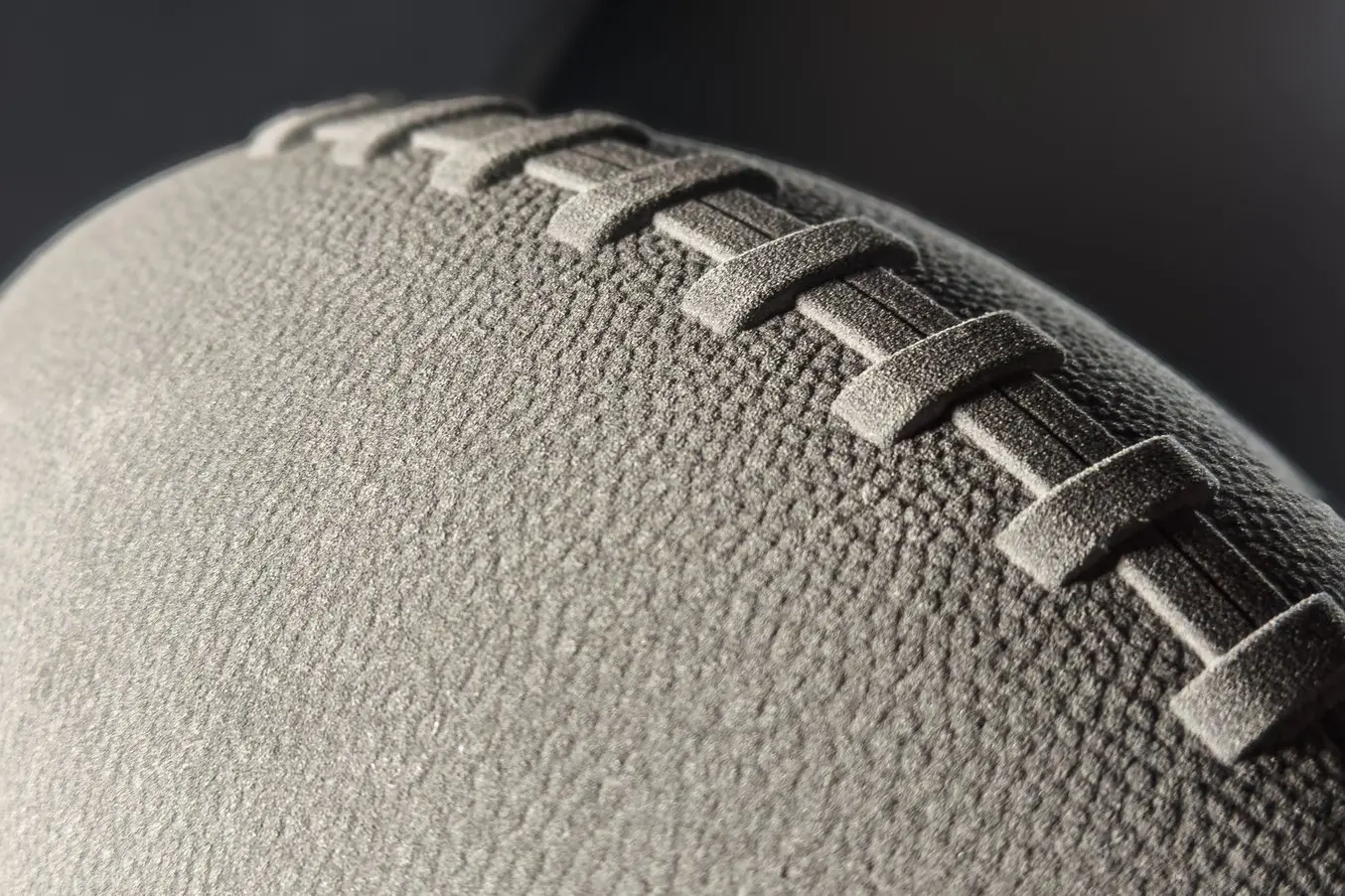
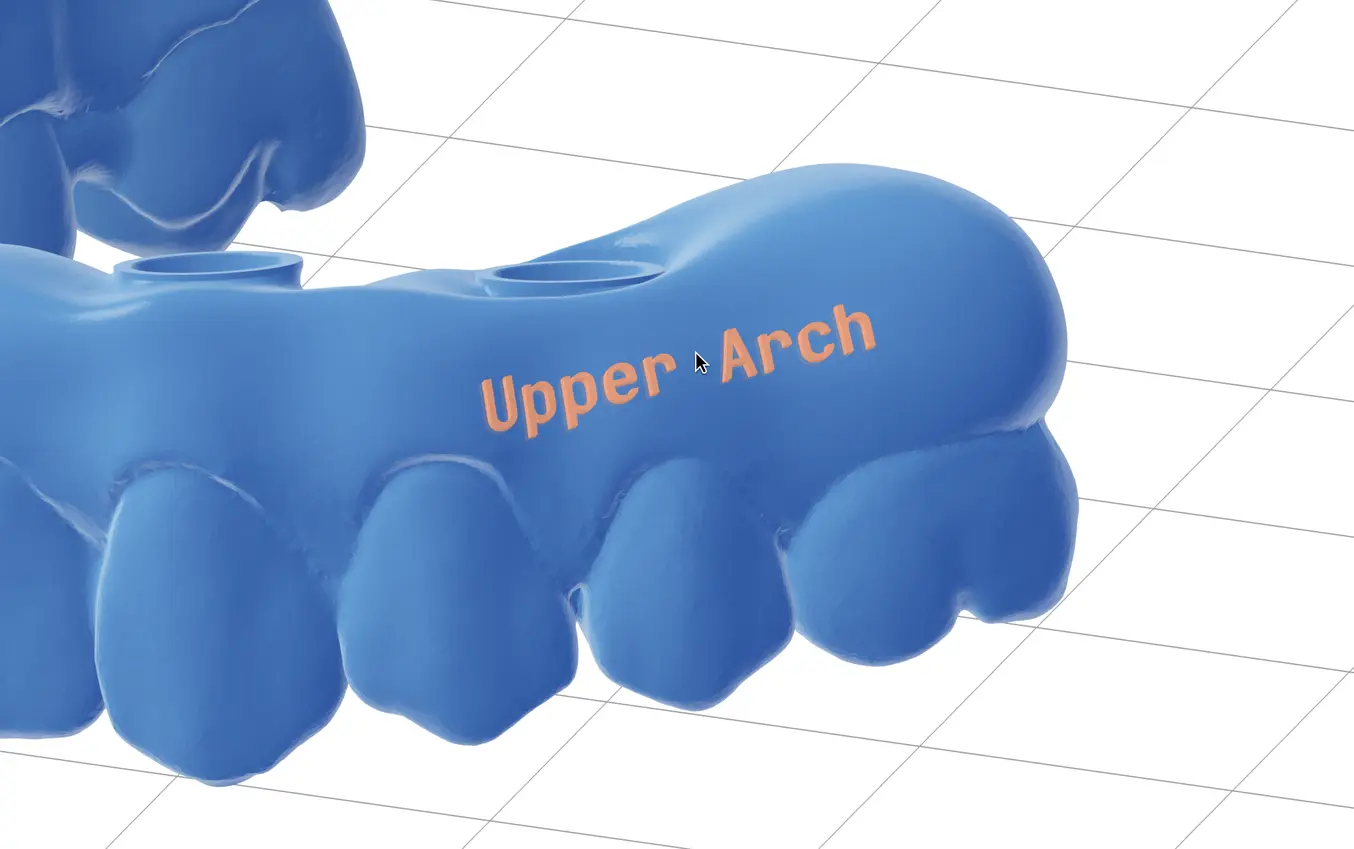
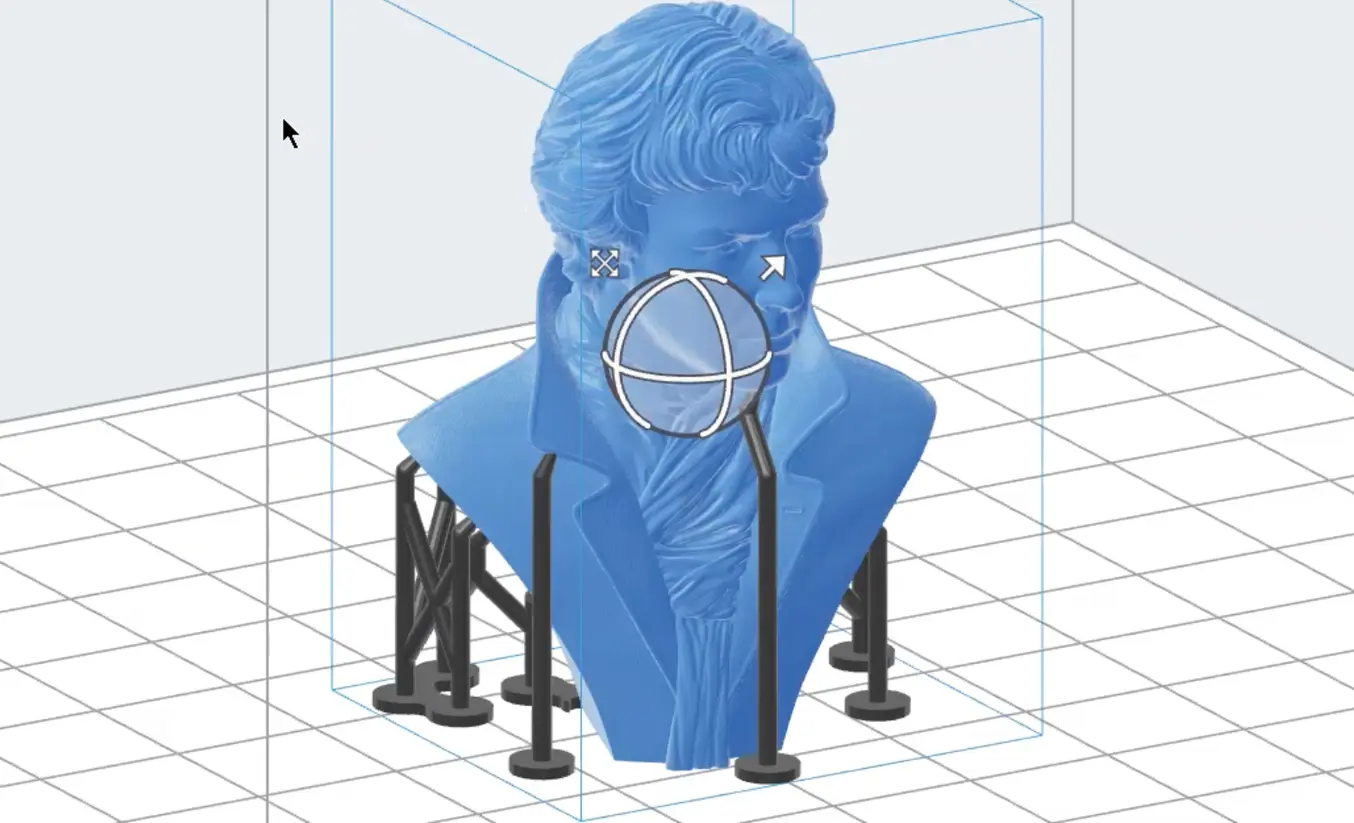
Étape 7 : Impression 3D et post-traitement de votre boîtier encliquetable
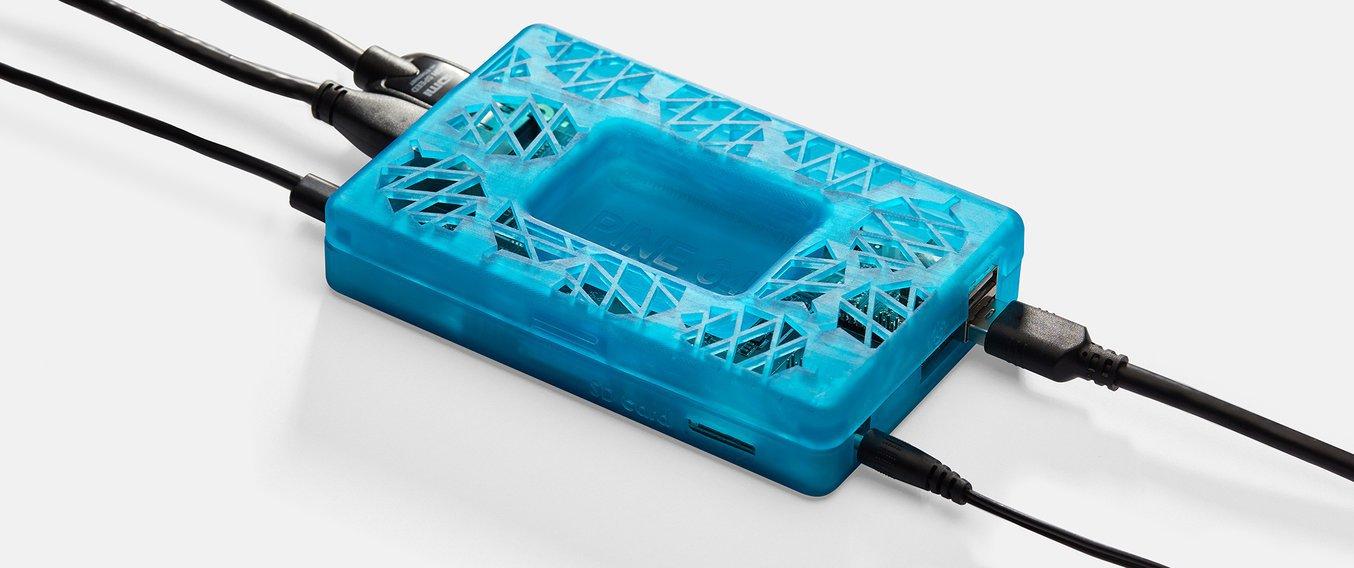
Une fois que votre pièce est prête à être imprimée, envoyez-la aux imprimantes de la série Form ou de la série Fuse par l'intermédiaire de PreForm. Lorsque l'impression est terminée, il faut la post-traiter en retirant les supports, en lavant et en post-polymérisant les pièces (SLA) ou en retirant la poudre, en procédant au mélange abrasif et au polissage (SLS). D'autres techniques avancées de post-traitement telles que le revêtement, le placage, le lissage à la vapeur et la teinture sont possibles et peuvent donner à vos pièces un aspect plus proche de celui des produits de consommation complets. Certains procédés, comme le revêtement, peuvent affecter les tolérances et l'assemblage par encliquetage. Il convient donc d'en tenir compte dans vos conceptions initiales.
Impression 3D d'assemblages par encliquetage pour les boîtiers et bien plus encore
L'impression 3D offre une série d'avantages pour la fabrication de pièces d'assemblage par encliquetage comme les enceintes, les boîtes, les couvercles et les assemblages fonctionnels. La capacité des imprimantes 3D et des matériaux avancés à créer des formes organiques complexes présentant des tolérances serrées, des caractéristiques fines et des finitions de surface lisses en fait une technologie idéale pour la fabrication de ces pièces. Les matériaux imprimés en 3D sont devenus plus industriels et plus durables, ce qui rend possible l'utilisation à long terme des pièces encliquetables, même en cas d'usage répété.
Pour en savoir plus sur les différents matériaux d'impression 3D disponibles, visitez notre gamme de matériaux ou demandez un échantillon.