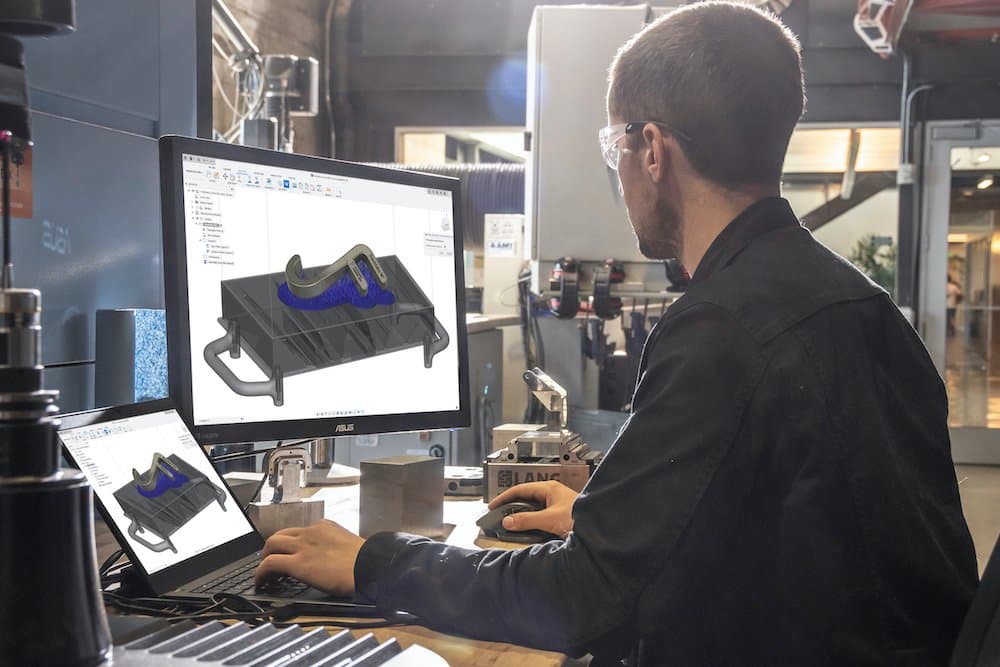
Formlabs et Fusion 360 d'Autodesk se sont associés pour optimiser vos procédures numériques grâce à de nouveaux outils CAO intégrant l’impression 3D. Nos imprimantes Form 3 et Form 3L sont les premiers appareils SLA à être inclus dans ce tout nouvel ensemble d'outils qui combine le meilleur du logiciel CAO polyvalent d'Autodesk avec des résultats d'impression 3D professionnels. Nous sommes ravis d'offrir cette nouvelle fonctionnalité aux utilisateurs Formlabs, qui peuvent maintenant imprimer leurs nouvelles idées en seulement quelques étapes.
L'intégration logicielle comprend une toute nouvelle interface, où les utilisateurs peuvent visualiser et ajuster la position de leurs pièces dans les Form 3 et Form 3L. Les concepteurs peuvent personnaliser un tableau de bord de conception pour l'adapter aux flux de travail d'impression 3D les plus fréquemment utilisés. Les équipes peuvent également optimiser la gestion des fichiers en exportant directement un fichier FORM à partir de Fusion 360 (un accès direct à PreForm sera bientôt disponible). Il n'est donc plus nécessaire de télécharger des fichiers STL individuels, ce qui permet aux concepteurs et aux fabricants de disposer d'un contrôle de version plus fiable.
« L'intégration des imprimantes Formlabs dans Autodesk Fusion 360 représente une grande avancée dans l'optimisation des flux de travail additifs, car elle permet de préparer la conception et la fabrication sur une seule plateforme unifiée. »
Sualp Ozel, Autodesk
Formlabs a travaillé en étroite collaboration avec les développeurs d'Autodesk pour donner vie à cette intégration. Selon Sualp Ozel, chef de produit senior, « l'intégration des imprimantes Formlabs dans Autodesk Fusion 360 représente une grande avancée dans l'optimisation des flux de travail additifs, car elle permet de préparer la conception et la fabrication sur une seule plateforme unifiée. Cela permet d'économiser de l'argent et d'obtenir des résultats de qualité, cohérents et professionnels en temps voulu. »
Nous avons été inspirés par notre large communauté d'utilisateurs présents dans le monde entier qui utilisent déjà Fusion 360 avec la Form 3. Leurs flux de travail numériques seront bientôt encore mieux adaptés à leurs besoins spécifiques. Lisez quelques-uns de leurs témoignages ci-dessous, et ne ratez pas nos prochaines études de cas !
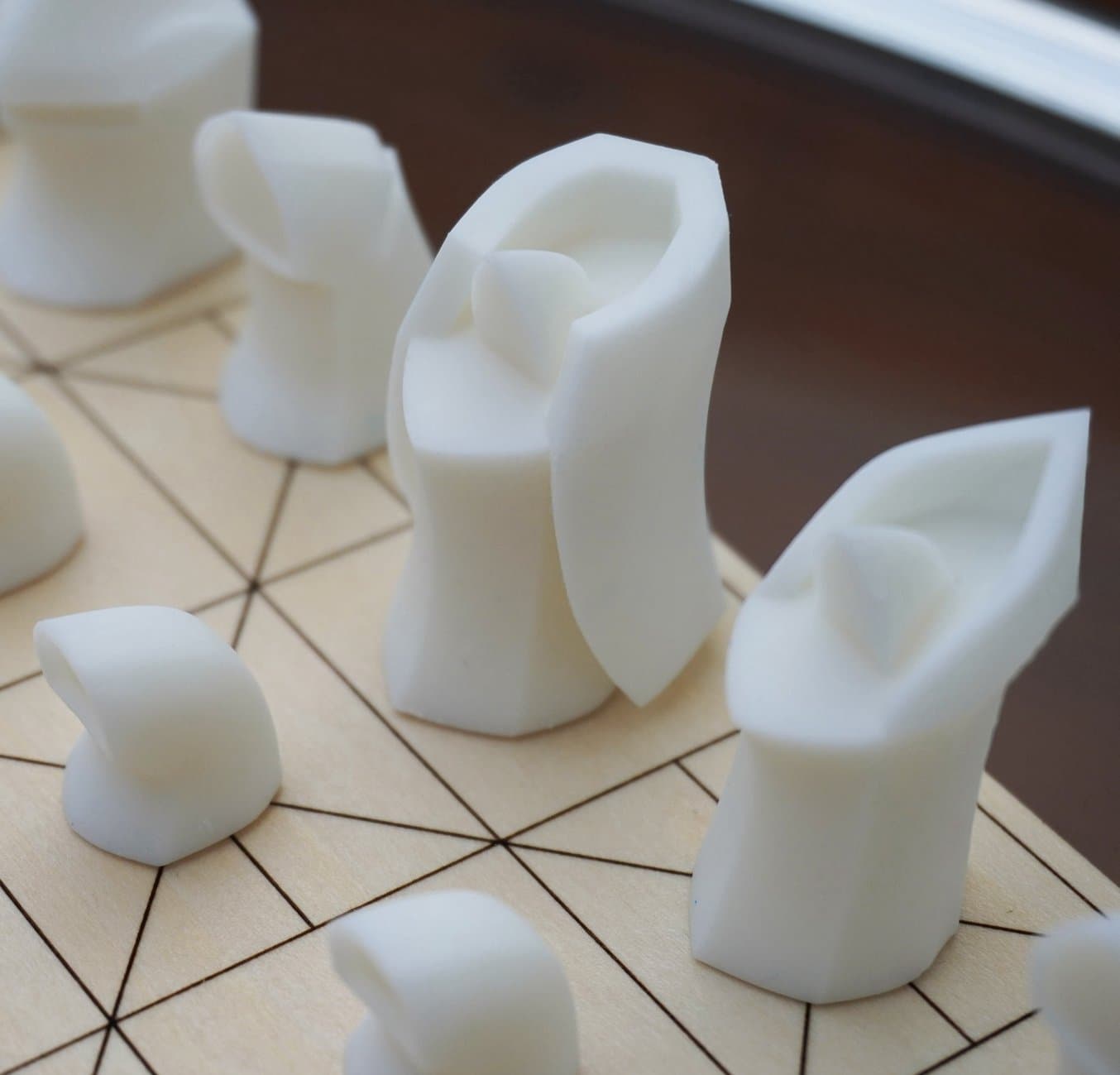
Intégration de Formlabs avec Fusion 360
Formlabs et Fusion 360 d'Autodesk se sont associés pour optimiser vos procédures numériques grâce à un nouveau logiciel CAO intégrant l’impression 3D.Visitez notre centre d'intégration pour découvrir les toutes dernières fonctionnalités de Fusion 360 pour l'impression SLA, lire d'autres témoignages d'utilisateurs et télécharger notre guide de conception. (En photo : jeu d'échecs de Will Qiu)
Étude de cas d'utilisateur : Cosm
Le PDG Derek Sham a fondé l'entreprise de dispositifs médicaux Cosm en 2018 pour s'attaquer à un problème médical extrêmement courant mais rarement abordé : le prolapsus utérin. Cette affection, causée par l'affaiblissement du périnée, touche près de 25 % des femmes dans le monde. Un traitement non chirurgical courant est le pessaire : une prothèse de soutien insérée dans le vagin. Cependant, de nombreuses patientes abandonnent le traitement en raison du faible choix de tailles et de formes standard disponibles. Cosm a remédié à cela en développant une toute nouvelle approche adaptée aux patientes.
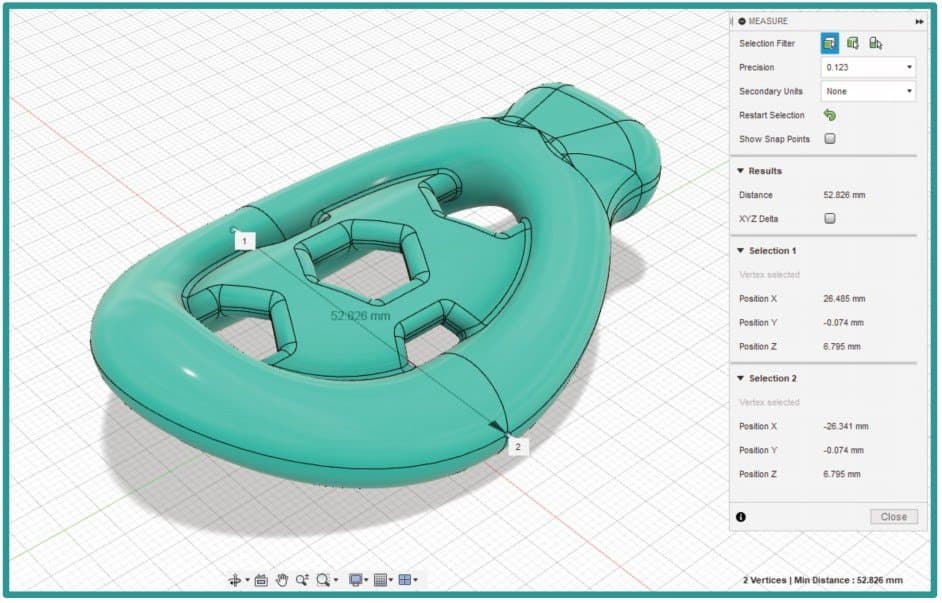
« Grâce à la résolution de la Form 3B, nous pouvons modifier nos dimensions d'une fraction de millimètre dans Fusion 360 et obtenir les propriétés dont nous avons besoin pour nos moules et nos pièces finales en silicone. »
Robert Lancefield, responsable de l'ingénierie de conception mécanique
Selon Aye Nyein San, directrice technique chez Cosm, « nous avons recours à la science des données, à l'apprentissage automatique et à l'intelligence artificielle. Grâce à cela, nous espérons offrir aux femmes une meilleure expérience lorsqu'elles sont traitées pour un prolapsus. » Elle a poursuivi en expliquant que la première phase de leur flux de travail implique une nouvelle technique d'imagerie par ultrasons. Les données du scan sont importées dans Fusion 360 pour concevoir un moule en forme de coque qui est ensuite imprimé sur la Form 3B. Enfin, ce moule est rempli d'un silicone biocompatible pour produire le pessaire sur mesure.
Fusion 360 et la Form 3B offrent à Cosm la précision dimensionnelle nécessaire pour donner des soins de qualité aux patientes.
Étude de cas d'utilisateur : Vertiball
Curtis Kennedy, fondateur et PDG de Vertiball, veut donner aux athlètes les moyens de gérer eux-mêmes le soulagement de leurs douleurs musculaires, leur rétablissement et la prévention des blessures. Découvrez la Vertiball : une boule de massage en rotation libre qui peut être montée sur une surface verticale, ce qui permet de cibler plus facilement la zone exacte à masser. L'innovation clé de Vertiball est une ventouse de qualité industrielle qui peut se fixer sur des surfaces lisses non poreuses comme les cloisons peintes, le métal ou le bois. L'avant de l'appareil contient une boule en rotation libre qui glisse et se verrouille sur le mécanisme de base.
Vu les nombreuses pièces mobiles et glissantes du produit, un prototype précis était essentiel. Curtis a pu compter sur Fusion 360 et la Form 3 pour l'obtenir. Pour la conception de chaque pièce d'assemblage, l'équipe de conception de Vertiball a effectué une analyse des contraintes dans l'environnement de simulation de Fusion avant d'engager des ressources matérielles dans un prototype imprimé avec la Form 3.
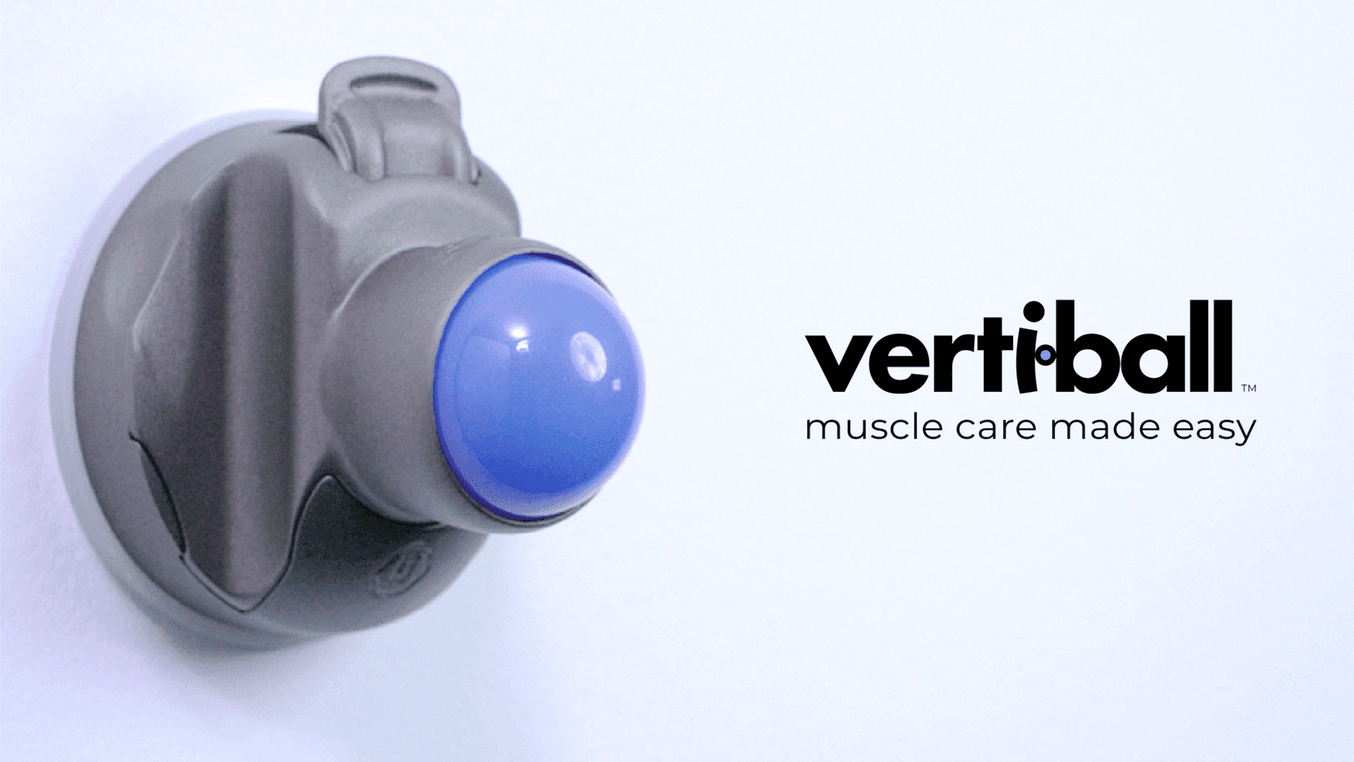
« Une nouvelle conception peut sembler géniale sur l'ordinateur, mais la seule façon d'en être certain est de la tester. Une fois que nous avons validé la fonctionnalité théorique d'une conception par simulation, nous passons directement au prototypage en utilisant la Form 3. »
Curtis Kennedy, président de Vertiball
Au cours du processus de développement, Curtis avait également besoin d'un matériau de prototypage à faible friction et résistant aux fissures semblable au polyamide 6 pour la fabrication du produit final. Pour cela, il s'est tourné vers la famille de résines Tough et Durable de Formlabs.
Étude de cas d'utilisateur : PrintCity
Mark Chester est un spécialiste du développement de produits au centre d'impression 3D PrintCity de l'université métropolitaine de Manchester. Avec un parc de plus de 65 imprimantes 3D FDM, SLA et métal acquises auprès d'Additive-X, le plus grand partenaire de Formlabs au Royaume-Uni, Mark aide les entreprises à mener des études de faisabilité sur les nouvelles technologies numériques.
United Utilities, la plus grande compagnie de distribution d'eau du Royaume-Uni, a voulu évaluer l'utilisation du scan optique et de l'impression 3D pour fabriquer de petites pièces de rechange à la demande. Cela pourrait leur éviter d'attendre des jours voire des semaines la livraison de pièces de rechange en cas de panne sur le terrain.
Le flux de travail proposé par Mark commence par la numérisation d'une pièce usée à l'aide d'un scanner laser. Les données brutes sont importées dans Fusion 360 puis nettoyées dans l'espace de travail de maillage, et les puissants outils de modélisation paramétrique de Fusion sont mis à profit pour recréer une pièce de remplacement précise par rétro-ingénierie. Enfin, les pièces sont envoyées directement de Fusion 360 à PreForm avant d'être imprimées sur la Form 3. Grâce à cette intégration entre Fusion 360 et PreForm, l'équipe de maintenance de United Utilities peut importer des scans, puis nettoyer et imprimer des pièces directement sans avoir à enregistrer des dizaines de fichiers STL pour des pièces à usage unique.
« Fusion 360 ne nécessite qu'un apprentissage léger pour les clients qui n'ont pas d'expérience préalable en CAO. Son coût est également avantageux. »
Mark Chester, spécialiste en développement de produits à PrintCity
Autodesk Fusion 360 et la Form 3 permettent à l'équipe de Mark d'identifier rapidement un flux de travail adapté et de le présenter aux clients, quelle que soit la taille de leur organisation.