Comment le fabricant de lunettes Plastinax utilise les techniques SLA et SLS pour réduire les délais de 40 %
Depuis 1976, Plastinax fabrique des lunettes pour certaines des plus grandes marques mondiales. Ils travaillent avec des clients internationaux pour concevoir des lunettes de soleil, des montures optiques et des montures de sécurité, puis passent à la production en grande série et moulent par injection jusqu'à 80 000 à 100 000 montures par mois. Les délais et la réactivité sont de la plus haute importance : pour rester compétitif sur le marché, Plastinax doit accélérer les processus de conception et de fabrication afin que ses montures puissent être transportées de ses installations de l'île Maurice à ses clients sur tous les continents.
Plastinax, qui appartient au groupe ENL, utilise les imprimantes 3D stéréolithographiques (SLA) et à frittage sélectif par laser (SLS) de Formlabs afin de produire des prototypes fonctionnels de petites séries de montures pour que leurs clients puissent les évaluer et donner leur avis avant de passer à l'étape de l'outillage. Ils se sont également lancés dans l'impression 3D d'outils pour la production de petites séries de montures et de composants de lunettes en utilisant l'imprimante 3D SLS Fuse 1 et Nylon 12 Powder.
Le flux de travail de l'impression 3D a également augmenté leur capacité de réaction et élargi la gamme de conceptions qu'ils peuvent produire. Steeven Devasagayaum, ingénieur concepteur chez Plastinax, nous a parlé de l'intégration des produits Form 2 et Fuse 1 dans son flux de travail, et de la façon dont l'impression 3D a modifié les processus de conception et de fabrication dans la société.
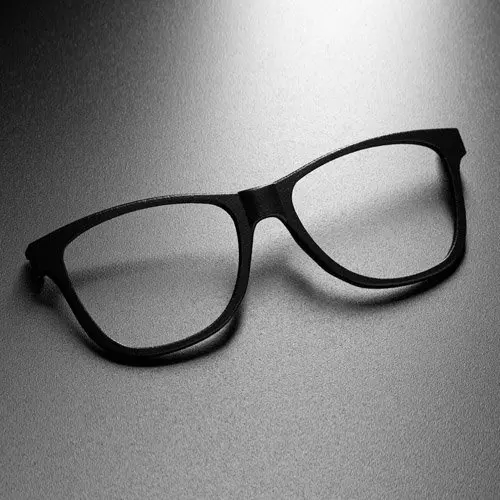
Production de lunettes imprimées en 3D sur l'écosystème SLS de la série Fuse de Formlabs
Dans ce livre blanc, nous aborderons les considérations relatives à la conception et aux matériaux et vous présenterons des fabricants qui exploitent le potentiel de l'impression 3D dans ce secteur.
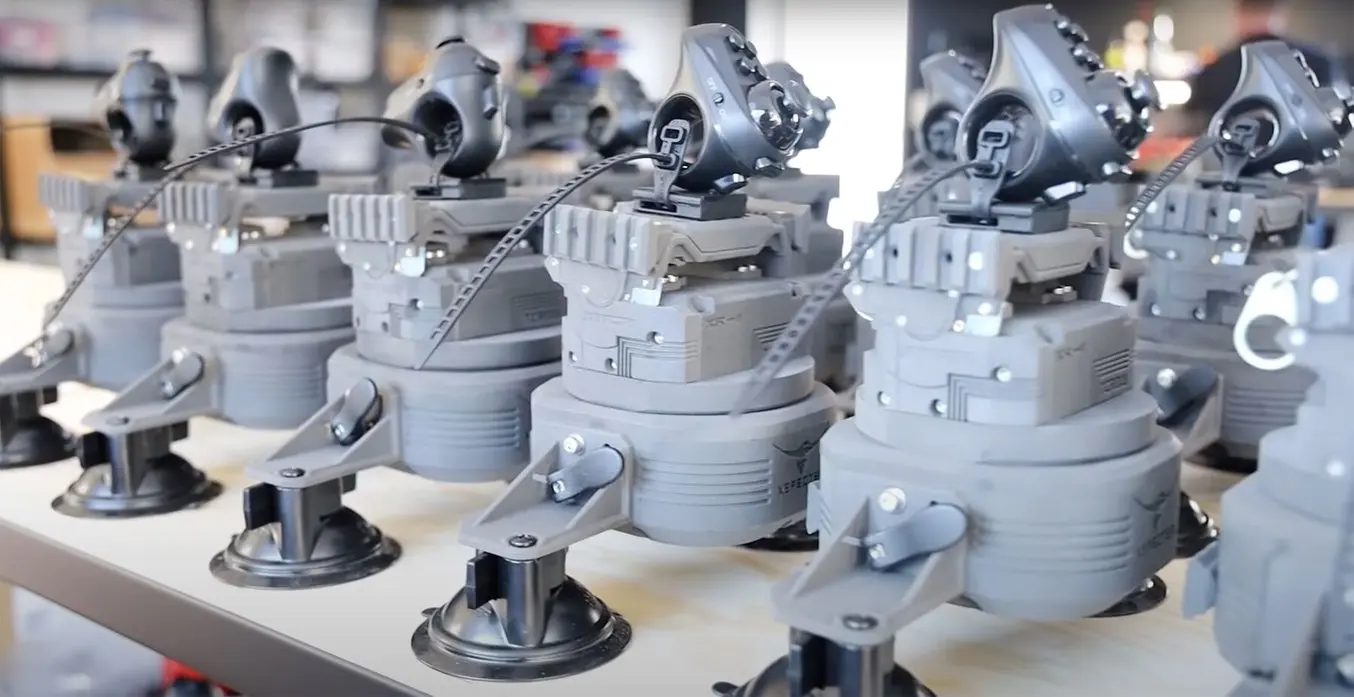
Le SLS pour la production finale
L'impression 3D pour la production finale n'est pas seulement accessible : elle est aussi plus abordable, plus agile et plus évolutive que jamais grâce à l'écosystème SLS Fuse. Explorez notre page dédiée à la production SLS pour comparer les différentes méthodes de fabrication, consulter les tarifs des poudres en vrac et découvrir comment 15 fabricants exploitent actuellement les imprimantes de la série Fuse.
Fabrication à grande échelle à l'île Maurice
Plastinax a commencé à fabriquer des montures de lunettes dans les années 1970 pour de grandes marques aux États-Unis, en Europe et dans le monde entier. À l'instar d'autres secteurs d'activité à l'époque, le processus de conception était plus lent et plus manuel, même si, dès le début, l'objectif était d'innover et de se différencier par le biais de conceptions complexes ou d'un branding distinct.
Lorsque M. Devasagayaum a rejoint l'entreprise en 2006, il a aidé l'équipe à passer de la fabrication manuelle de prototypes à l'impression de modèles en 3D par l'intermédiaire de sous-traitants. Ce nouveau flux de travail a permis de rapprocher les modèles des premières itérations du produit final moulé par injection et d'accélérer le processus de conception : ils ont ainsi pu passer d'une esquisse ou d'un dessin technique à un prototype fait à la main, puis au scan 3D et au dessin 3D réalisés par des sous-traitants.
L'impression 3D de modèles a permis d'obtenir des prototypes plus proches des pièces finales, mais posait tout de même des problèmes si un client demandait d'autres modifications : l'arrivée d'une série supplémentaire de prototypes pouvait prendre une semaine ou plus. L'allongement des délais a empêché Plastinax de rester compétitif.
Intégrer l'impression 3D en interne
L'équipe de recherche et développement de Plastinax s'est mise à la recherche d'une imprimante 3D SLA pour l'intégrer en interne et réduire les délais. Cependant, les machines disponibles sur le marché étaient coûteuses, et l'externalisation des prototypes rapides était alors plus rentable que d'investir dans les machines disponibles à l'époque.
En 2016, Plastinax a décidé d'intégrer l'impression 3D en interne avec une Form 2. Une deuxième unité a suivi un an plus tard pour répondre à la demande croissante de prototypes rapides. « Ces machines ont changé la donne. Du jour au lendemain, j'ai été capable de concevoir et d'obtenir un prototype rapide en quelques heures. Nous sommes devenus plus réactifs, et nous avons pu apporter des changements aux conceptions de nos clients en une semaine à peine. Ces imprimantes ont le meilleur rapport qualité-prix et surtout, elles sont fiables », nous dit M. Devasagayaum.
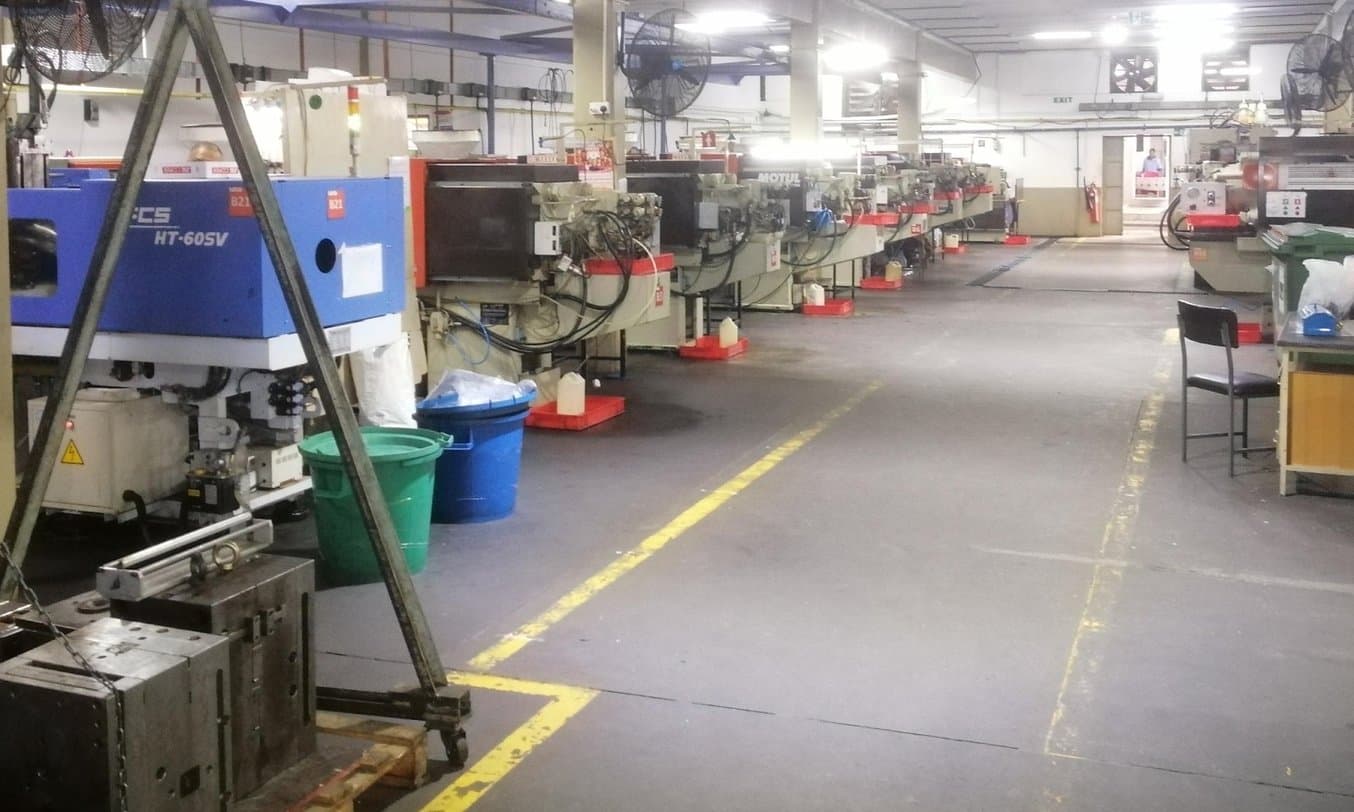
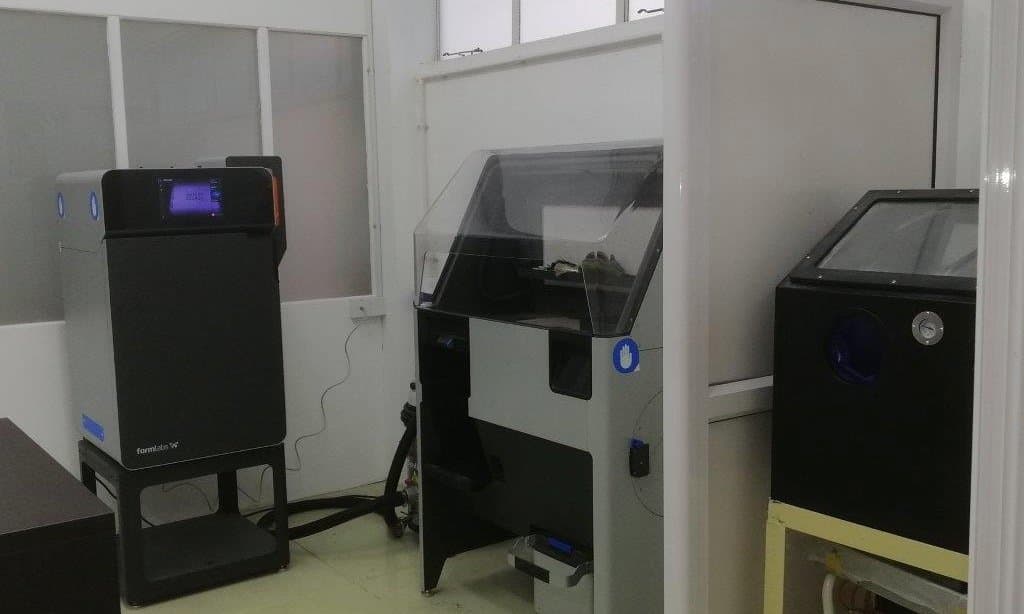
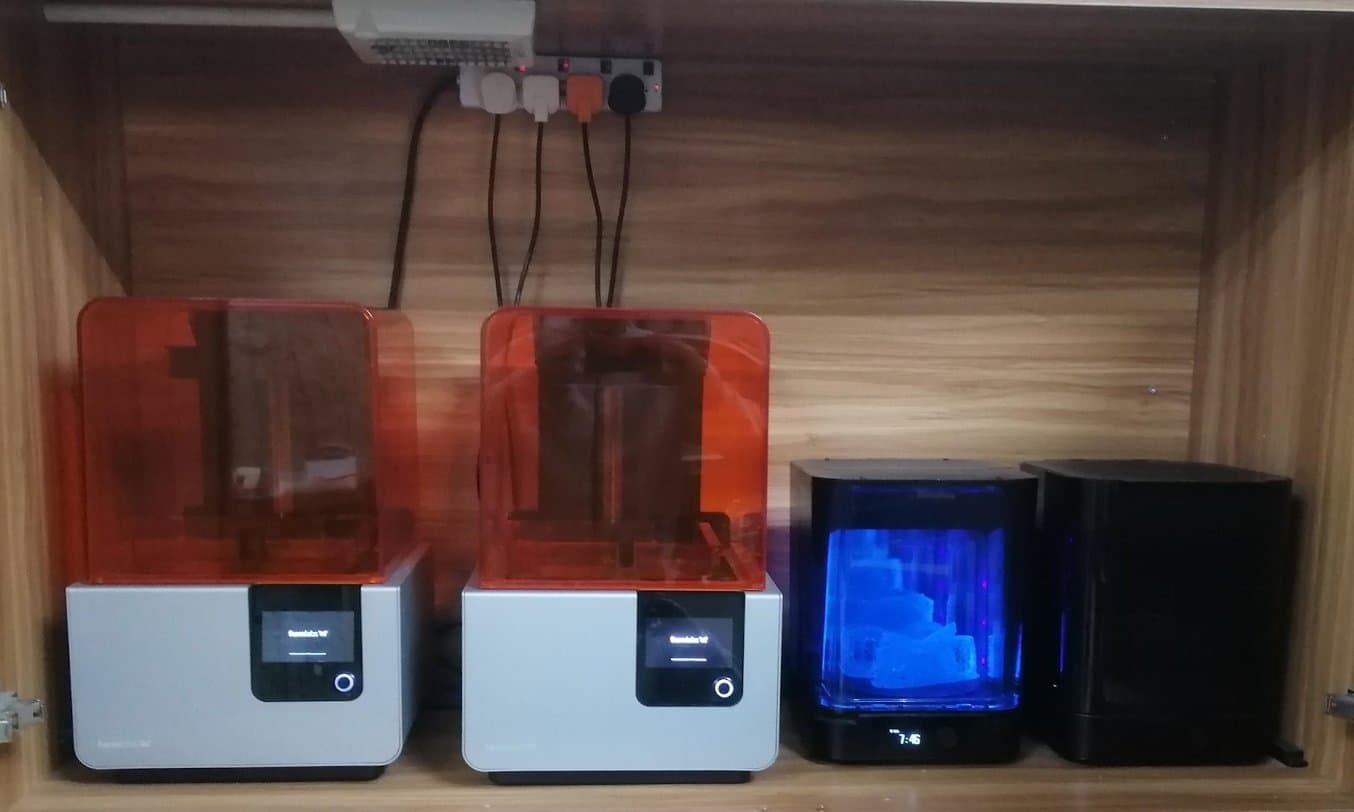
En s'appuyant sur la puissance industrielle de leurs installations à grande échelle (à gauche), Plastinax produit plus d'un million de paires de lunettes par an. L'intégration d'imprimantes 3D en interne comme celles de la série Fuse (au centre) et la Form 2 (à droite) leur permet d'itérer plus rapidement et de continuer à développer leur activité.
Augmenter le rendement avec le SLS
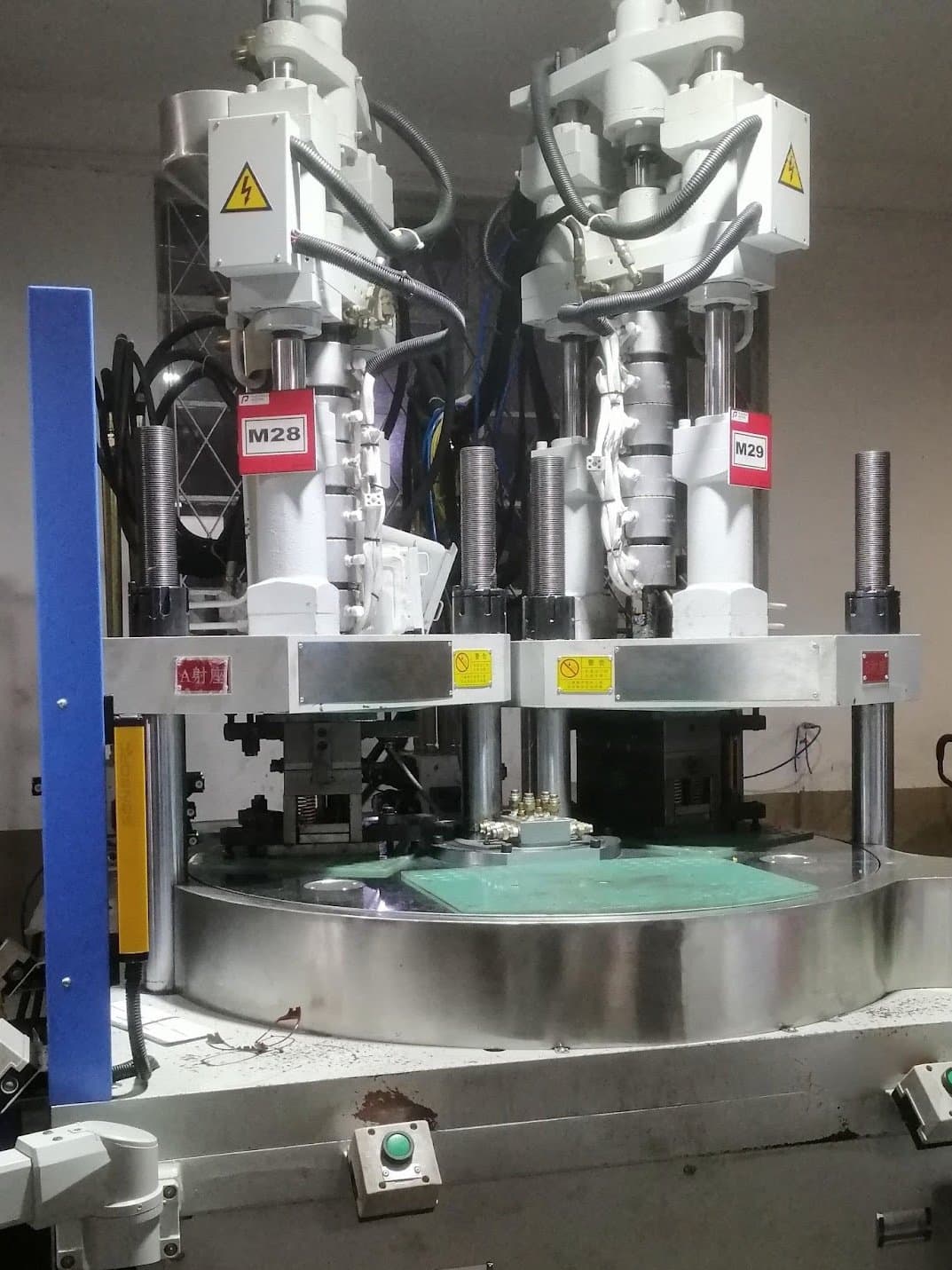
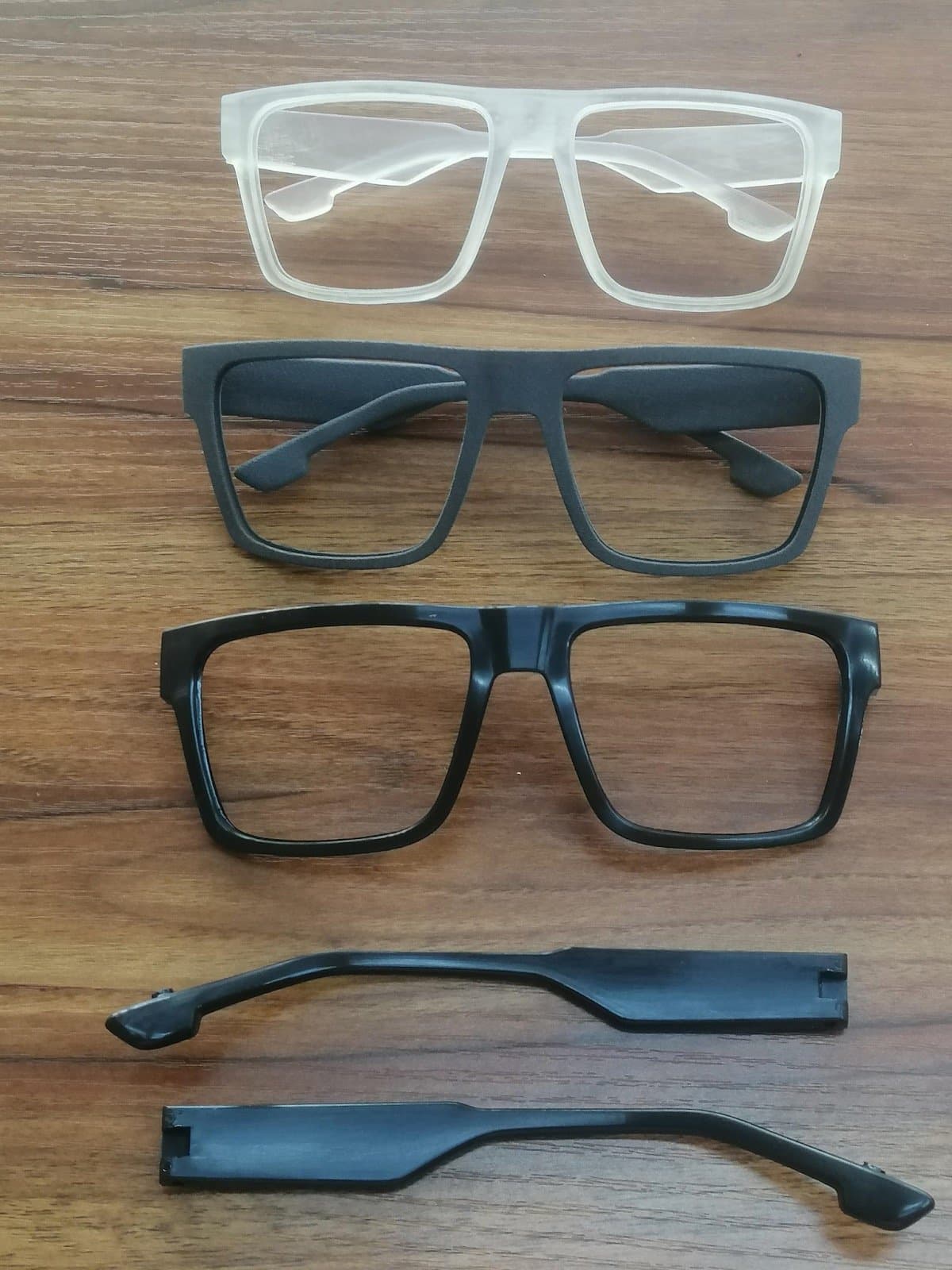
Plastinax a désormais la capacité de mouler par injection avec ses machines industrielles (à gauche) et d'imprimer en 3D avec des matériaux SLA et SLS (à droite, en haut et au milieu) pour obtenir des montures qui présentent l'aspect et la fonctionnalité du produit final (à droite, en bas).
Plastinax s'est développé, augmentant le nombre de résines utilisées : de Clear Resin pour les montures design translucides à Grey Pro Resin pour les tests fonctionnels. Puis, en 2021, un client leur a montré des prototypes en nylon imprimés en 3D par un concurrent d'Asie de l'Est et a démontré à quel point ils étaient solides. « Nous nous sommes mis à la recherche d'une machine capable de produire de telles pièces. Nous avons dû innover en nous dotant d'équipements fiables et performants afin d'être le plus compétitif possible. Nous travaillions avec Formlabs depuis six ans. L'assistance et le service étaient excellents ; nous avons donc décidé d'opter pour la Fuse 1 », explique M. Devasagayaum.
Les petits ruisseaux font les grandes rivières
Pour un fabricant sous contrat international comme Plastinax, le succès dépend de sa capacité à s'assurer la confiance d'un client et à prouver la supériorité de son produit final. Envoyer aux clients un seul design dans un matériau de haute qualité peut s'avérer insuffisant. Steeven Devasagayaum s'appuie sur la Fuse 1 pour adapter la conception à la moindre exigence du client.
« Dans le domaine de la lunetterie, les petites différences sont d'une importance capitale. Il ne s'agit parfois que de quelques dixièmes de millimètre. On m'a par exemple demandé de faire varier l'angle de l'arête du nez d'un degré, et ces imprimantes peuvent le faire. Ensuite, j'envoie les différentes versions au client », explique M. Devasagayaum.
Le lit de poudre autoportant de la technologie SLS au coeur de la Fuse 1 permet aux utilisateurs d'agencer les pièces efficacement, en les emboîtant ou en les empilant pour tirer le meilleur parti de chaque grain de poudre. Il est désormais possible d'imprimer plus de 10 montures à la fois. Cela simplifie le flux de travail et facilite le post-traitement dans la Fuse Sift. Le fait de pouvoir proposer plusieurs variantes à la fois a permis à Plastinax de recevoir des commandes après une seule conversation. Pour l'une d'elles, un concurrent avait fabriqué les montures mais les avait envoyées avec la mauvaise taille de verre. Heureusement, Plastinax a pu intervenir. « En quelques heures, nous avons pu trouver la bonne taille, imprimer les montures en 3D et leur envoyer le nouveau modèle dès le lendemain », explique M. Devasagayaum.
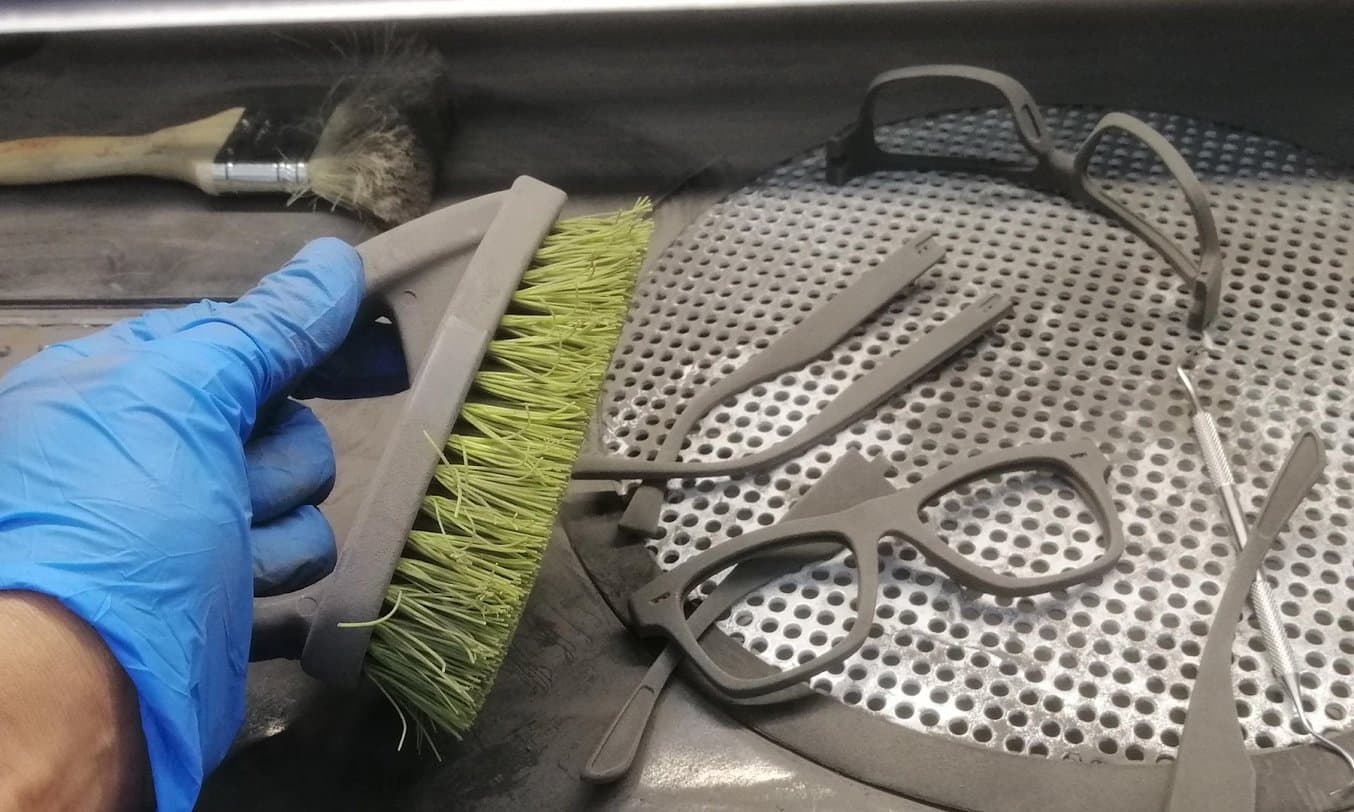
La Fuse Sift optimise le flux de travail de Plastinax et permet la production rapide de prototypes pour tester l'ajustement, la fonctionnalité et le style.
Flux de travail simplifié pour le SLA et le SLS
Le fait de disposer en interne d'une solution industrielle performante contribue à l'efficacité du flux de travail. M. Devasagayaum utilise à la fois la SLA et la SLS dans son processus de conception, et la petite taille des deux imprimantes permet de passer facilement d'une technologie à l'autre au cours d'une journée. Alors que la Fuse 1 fabrique des prototypes fonctionnels reproduisant avec précision de minuscules différences de mesure, la Form 2 peut imprimer deux montures en Clear Resin qui seront peintes pour mieux évaluer les options esthétiques du produit final.
« Les deux technologies m'aident dans mon processus de conception. Nylon 12 Powder est similaire au polyamide final avec lequel les montures seront moulées par injection. Du vernis et des motifs peuvent être appliqués aux pièces en Clear Resin afin qu'ils puissent voir quelles finitions nous pouvons réaliser. Nous avons ainsi le meilleur des deux mondes : la qualité de surface du SLA d'un côté, la résistance et la durabilité du nylon de l'autre. »
Steeven Devasagayaum, ingénieur de conception chez Plastinax
La similitude entre le nylon et le polyamide permet aux clients de se faire une idée du poids et de la résistance de leurs montures moulées par injection. Un client souhaitait concevoir des lunettes de protection, et Devasagayaum a imprimé plusieurs prototypes rapides pour les montrer à l'équipe marketing du client. Les lunettes de protection devaient être durables, résistantes aux chocs et légèrement flexibles : le SLS était donc la solution idéale. « Nous avons pu les vernir rapidement, et elles ressemblaient aux versions finales injectées avec du plastique », explique Devasagayaum.
La flexibilité des pièces en Nylon 12 Powder facilite également le montage et le démontage des lentilles sur les prototypes. Plastinax peut fabriquer des prototypes entièrement fonctionnels avec des verres de différentes épaisseurs pour toute une série de montures, ce qui lui permet de fournir au client un modèle qui ressemble et se comporte exactement comme les montures moulées par injection.
Plastinax peut désormais imprimer 28 prototypes à la fois sur la Fuse 1 lorsque des quantités plus importantes sont nécessaires, par exemple lors d'un salon professionnel. « Nous pouvons facilement fabriquer en interne des prototypes rapides qui ressemblent au produit fini. Si nous avions dû les sous-traiter, cela aurait pris dix jours ou plus », explique M. Devasagayaum.
En plus du prototypage, la série Fuse donne également accès à de nouveaux flux de travail d'outillage pour Plastinax. La légère flexibilité du nylon et sa grande précision dimensionnelle offrent la possibilité de concevoir, de tester et de produire des outils durables pour aider les lignes de production. Par exemple, Devasagayaum imprime des formes et des bases pour la découpe des lentilles, ainsi que des bases pour insérer des charnières métalliques flexibles sur les éléments de la branche ou pour maintenir les montures pendant le perçage de cavités, ce qui permet d'apposer des logos métalliques personnalisés.
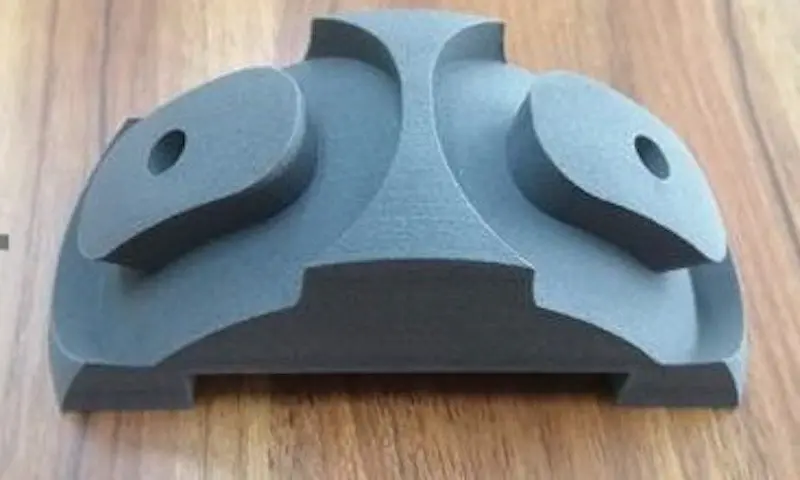
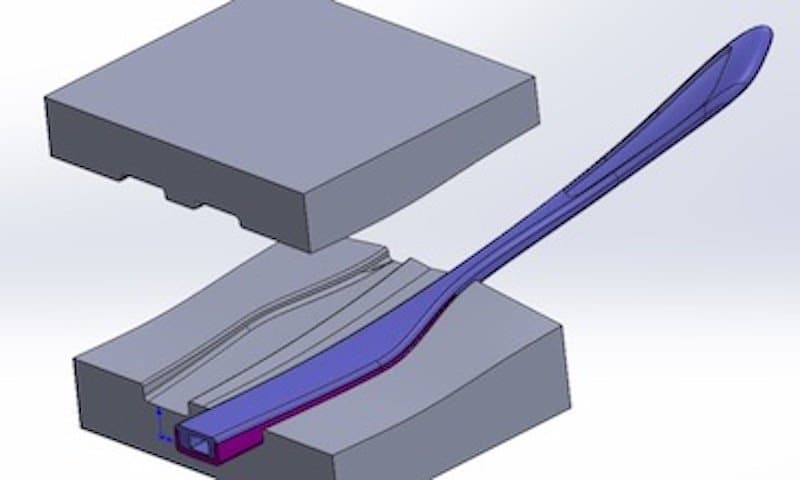
Plastinax crée des outils de formage des verres (à gauche) ou des bases pour l'insertion de charnières métalliques flexibles dans les branches d'une paire de lunettes, ou pour le perçage CNC de cavités sur les montures pour des logos métalliques personnalisés.
Un regard vers l'avenir
Le secteur de la lunetterie est en passe de devenir un pionnier de la personnalisation. Les lunettes sont l'un des seuls produits utilisés à la fois comme un élément de mode et comme un élément nécessaire à la vie de millions de personnes qui ont besoin de verres correcteurs. Les deux parties du secteur peuvent bénéficier de la personnalisation basée sur la forme du visage et sur les choix esthétiques du client.
Plastinax sait que la personnalisation prendra de plus en plus d'ampleur à l'avenir, et peut maintenant compter sur l'intégration du SLA et du SLS dans son flux de travail. L'outillage rapide imprimé en 3D par SLA pour le moulage par injection avec des matériaux tels que Rigid 10K Resin offre une alternative à l'outillage métallique, et l'impression directe de petites séries de montures finales sur le Fuse 1 est déjà envisagée par M. Devasagayaum. « Les possibilités sont infinies. La Form 2 a changé la donne en 2016 et la Fuse 1 a fait de même », nous a-t-il confié.
Pour en savoir plus sur l'impression 3D de montures de lunettes, consultez notre guide d'application ou contactez notre équipe commerciale pour en savoir plus sur l'intégration de l'impression 3D SLS et SLA en interne.