Concevoir le fauteuil roulant du futur grâce à l’impression 3D
« J'avais même renoncé à aller à l'épicerie, qui ne se trouve qu'à deux pâtés de maisons de chez moi. »
Lorsque Satoshi Sugie, fondateur de WHILL, a entendu cette phrase, il a compris que beaucoup de personnes à mobilité réduite méritaient mieux. Aujourd'hui, il dirige une entreprise dont la mission est de rendre les déplacements en fauteuils roulants plus innovants et agréables.
Bâtir la prochaine génération de fauteuils roulants n'a pas été facile. Grâce aux imprimantes Formlabs et à la conception générative, les ingénieurs de WHILL ont pu repousser les limites et proposer un produit unique.
Lisez la suite pour découvrir le témoignage de M. Yasuhiro Hirata sur le développement du fauteuil roulant WHILL.
L'impression 3D pour accélérer le développement
Les startups sont confrontées à toutes sortes de problèmes, et notamment aux contraintes de temps et d'argent. C'est particulièrement vrai pour les startups de matériel informatique (nous sommes bien placés pour le savoir !) qui essaient souvent de résoudre un nouveau problème en partant de zéro. L'un des principaux défis de toute startup est de surmonter des obstacles imprévus, ce qui peut être coûteux et prendre du temps. Obtenir les pièces complexes nécessaires a été un vrai casse-tête pour WHILL, car les méthodes de fabrication traditionnelles sont souvent peu adaptées à la production de petits volumes. Pour que l'entreprise puisse survivre financièrement, elle devait trouver un moyen de réduire le coût de chaque fauteuil roulant.
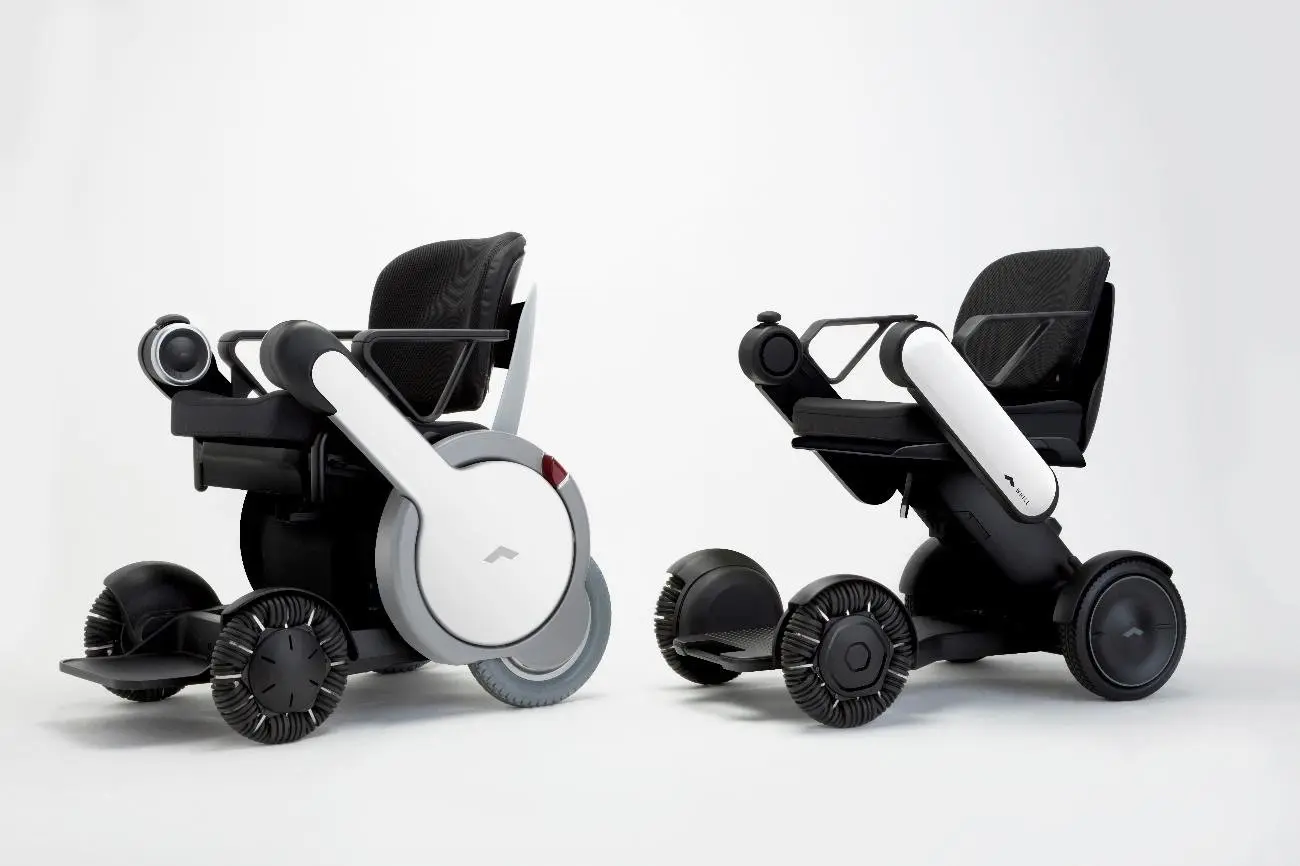
La décision a alors été prise de prototyper rapidement certaines pièces complexes, et de se tourner vers une société d'impression 3D externe. WHILL s'est rapidement rendu compte des problèmes de coûts et de délais qu'entraînait la sous-traitance de l'impression 3D ; cette solution n'était clairement pas envisageable à long terme pour l'équipe. M. Hirata savait que WHILL ne pourrait pas mener à bien son projet sans prototypes physiques, c'est pourquoi il a été décidé d'adopter l'impression 3D en interne.
« Si vous ne savez pas quelle forme est la meilleure, imprimez-la et voyez par vous-même. »
M. Hirata n'était pas satisfait des imprimantes à filament fondu (FFF) plus anciennes qu'il avait eu l'occasion d'utiliser auparavant. Mais, ayant suivi le succès de Formlabs, il a décidé d'investir dans l'une de nos machines. WHILL a présenté la première imprimante Formlabs à l'équipe en 2016. Depuis lors, elle a été utilisée pour divers projets et a permis d'obtenir exactement ce que l'équipe souhaitait : des prototypes rapides de haute qualité. Les prototypes des pièces entrant directement en contact avec les utilisateurs sont les plus importants. Ces prototypes doivent présenter un aspect et une sensation réalistes, et ne pas donner l'impression d'être bon marché ou creux. L'imprimante SLA de Formlabs a donné à M. Hirata exactement ce dont il avait besoin pour ses prototypes finaux : des pièces de haute qualité, détaillées et abordables.
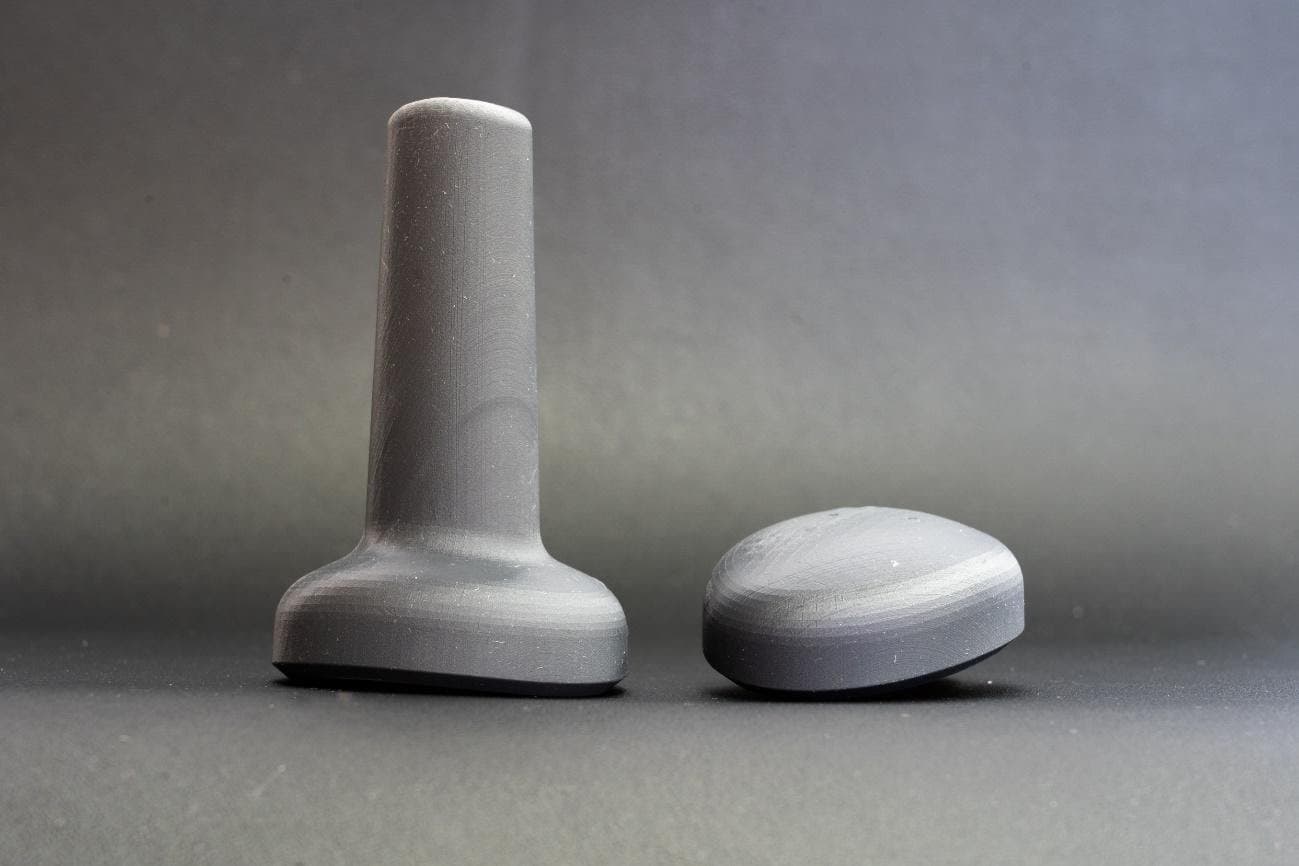
L'introduction d'une imprimante 3D haute définition au sein de l'équipe de développement de WHILL a été indispensable pour créer un produit final. Évaluer la sensation au toucher de certaines pièces n'est possible que si celles-ci sont d'une qualité au moins égale à celle des produits finaux. Pour WHILL, les pièces de Formlabs sont la solution parfaite, car elles permettent de réaliser à la fois des tests internes et des tests utilisateurs sur des prototypes de fauteuils roulants.
« Nous essayons de fabriquer et d'évaluer autant de prototypes que possible pour les parties que les utilisateurs touchent, comme par exemple les manettes. Si l'impression était externalisée comme par le passé, le nombre de prototypes à fabriquer et de points à examiner serait limité en raison des contraintes de budget et de calendrier. Avec la Form 2, Flexible Resin présente une sensation au toucher proche de celle des produits réels fabriqués en série, ce qui nous permet de modéliser et d'évaluer des prototypes de haute précision sans avoir à nous restreindre. »
Yasuhiro Hirata
L'équipe a utilisé différentes résines sur un même projet, démontrant ainsi de quoi est capable une seule imprimante Formlabs. Flexible Resin était idéale pour créer des pièces agréables au toucher, Clear Resin pour les pièces transparentes autour de l'écran du fauteuil roulant, tandis que Tough Resin a été utilisée pour les pièces nécessitant plus de résistance. Le fait de disposer d'une seule machine capable d'imprimer plusieurs pièces en différents matériaux adaptables a permis à la startup d'économiser énormément de temps et d'argent.
« En plus d'être précise, la Form 2 tombe rarement en panne. Grâce à cela, nous avons pu créer différents types de prototypes chaque jour et les examiner pour améliorer la qualité du produit. »
Yasuhiro Hirata
Conception générative
La conception générative désigne le processus qui consiste à utiliser des algorithmes pour créer des centaines, voire des milliers de conceptions optimisées en tenant compte des principaux objectifs de conception, des fonctions, des dimensions, des matériaux, des méthodes de fabrication et des contraintes de coût.
L'équipe de WHILLS voulait créer une pièce solide d'un seul tenant pour le centre du fauteuil roulant. Ils se sont tournés vers la conception générative et ont été en mesure d'analyser plusieurs conceptions à la fois. Le problème avec les conceptions complexes uniques, c'est qu'elles peuvent être coûteuses et presque impossibles à réaliser avec des flux de travail traditionnels.
« Si nous n'avions pas de contraintes de budget, nous pourrions utiliser un matériau léger comme le carbone, mais ce n'est pas envisageable. Alors que nous songions à réduire le poids du produit avec un matériau abordable, l'idée de tester la conception générative nous est apparue. Nous avions besoin de réaliser des prototypes complexes en moins de temps, et nous n'y serions sans doute pas arrivés sans les imprimantes 3D et les résines de Formlabs. »
Yasuhiro Hirata
La nouvelle pièce complexe a d'abord été imprimée en interne avec Castable Wax de Formlabs. L'équipe a utilisé Autodesk Fusion 360 pour concevoir de manière générative la pièce principale du corps du fauteuil roulant, avant de réaliser le prototype de la pièce en interne, ce qui a fortement impressionné l'équipe. Résultat final : WHILL a pu alléger de plus de 40 % le cadre du fauteuil roulant.
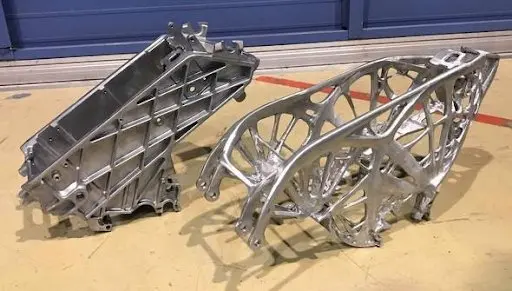
Prototypage en interne avec Formlabs
WHILL est l'une des nombreuses entreprises qui ont fabriqué des produits incroyables grâce au prototypage rapide en interne. Téléchargez notre livre électronique gratuit sur le prototypage rapide pour découvrir six autres entreprises qui ont changé leur façon de travailler après avoir acheté une imprimante Formlabs.